Hyd-Mech S20DSP User manual

YEAR OF MANUFACTURE: ______________
USE AND MAINTENANCE MANUAL
S20DSP
EN


Introduction and technical specifications 1---1......................
Foreword 1---1..........................................................
Machine presentation 1---1...............................................
Machine specification 1--- 2...............................................
Dimensions 1---4........................................................
F u n c t i o n a l p a r t s 2 --- 1............................................
S20DSP model 2---1.....................................................
Cutting head 2---2.......................................................
Vice 2 --- 3..............................................................
C o n t r o l Pa n e l 2 --- 3......................................................
Tu r n t a b l e 2 --- 4..........................................................
F i x e d p l a t f o r m 2 --- 4.....................................................
M o t i o n --- v a r i a t o r --- r e d u c e r u n i t 2 --- 5.......................................
Base 2 --- 6..............................................................
Safety and accident prevention 3---1................................
U s e o f t h e m a c h i n e 3 --- 1.................................................
General recommendations 3---2...........................................
Recommendations to the operator 3---3....................................
Machine safety devices 3---5..............................................
Reference standards 3---5................................................
Protection against accidental contact with the blade 3---6......................
Electrical equipment 3---6................................................
Emergency devices 3---7..................................................
Noise level of the machine 3---8...........................................
Noise level measurement 3---8............................................
Noise level values 3---8...................................................
Vibration emission 3---9..................................................
Electromagnetic compatibility 3---9........................................
Machine installation 4---1........................................
Packaging and storage 4---1...............................................
Anchoring the machine 4--- 4..............................................
Minimum requirements 4---4..............................................
C h e c k l i s t 4 --- 5..........................................................
Connection to the power supply 4---6.......................................
Description of machine operation 5---1.............................
Control panel description 5---1............................................
Basic instructions for carrying out a cutting operation cycle 5---3................
Manoeuvring the cutting head 5---3........................................
Clamping the work piece in the vice 5---3...................................
Rapid vice positioning 5---4...............................................
R a p i d v i c e t r a n s l a t i o n 5 --- 6...............................................
Wi d t h o f c u t 5 --- 6.......................................................
Preliminary check list for cutting operation 5---7.............................
Semi---automatic operating cycle 5---7......................................
Execution of inclined cuts 5---10............................................
Loading side rollerway position 5---10.......................................
Angled cuts 45˚to the left 5---11...........................................
Angled cuts 60˚to the left 5---12...........................................
Angled cuts 45˚to the right 5---14..........................................
Angled cuts 60˚to the right 5---15..........................................

Diagrams, exploded views and replacement parts 6---1................
Hydraulic diagram 6---2..................................................
How to read the wiring diagrams 6---3......................................
D2 --- Letter codes used to designate the type of component 6---5...............
Standardised Wiring Diagrams S20DSP (CENELEC Standard) 6---8............
IUD/IUV card 6---21.....................................................
Exploded views 6---22.....................................................
M o t o r u n i t 6 --- 2 2.........................................................
Driving pulley unit 6---24..................................................
Front flywheel assembly 6--- 26..............................................
F i x e d w o r k t a b l e 6 --- 2 8....................................................
Cutting head cover 6---30..................................................
C y l i n d e r s 6 --- 3 2.........................................................
Base assembly 6---34......................................................
C o n t r o l p a n e l 6 --- 3 6......................................................
Vice assembly 6---38......................................................
A d j u s t m e n t s 7 --- 1...............................................
Displaying and editing the set---up parameters 7---1..........................
Set language parameter 7---2..............................................
Set parameter for machine type 7---2.......................................
Semiautomatic---Dynamic and Manual operation setting (optional) 7---2.........
Pedal control setting (optional) 7---3.......................................
Optional inverter presence settings 7---3....................................
Blade speed proximity settings 7---3........................................
Minimal lubrication system settings 7---3....................................
FCTI / FCTA digital output enabling setting 7---3............................
Blade stop setting 7---3...................................................
Cutting vice opening setting 7---4..........................................
Cutting vice opening/closing time setting 7---4...............................
Machine maximum power input setting 7---4................................
Measurement unit setting 7---4............................................
Setting minimum blade tensioning 7---5.....................................
Display backlighting time setting 7---5......................................
Cutting head stroke 7---5.................................................
Software version and total use time of the machine 7---8......................
Adjusting the display brightness 7---8.......................................
Machine working pressures 7---9...........................................
Hydraulic pressure 7---9..................................................
Cutting head 7---10.......................................................
Blade tensioner slide play adjustment 7---10..................................
B l a d e g u i d e c o m p o n e n t s 7 --- 1 1.............................................
Blade guide heads 7---11..................................................
Blade steady buttons 7---11................................................
Blade guide plates 7---11..................................................
Blade 7 --- 1 4.............................................................
Tool changeover 7---14....................................................
Blade perpendicularity 7---16..............................................
Blade orthogonality 7---17.................................................
Front flywheel 7---18......................................................
Rear flywheel 7---18......................................................
Maintenance and choice of consumables 8---1.......................
The role of the operator 8---1.............................................

Maintenance requirements 8---2...........................................
General maintenance 8---2...............................................
Daily 8 --- 2.............................................................
Weekly 8 --- 2............................................................
Monthly 8---3...........................................................
Maintenance of working parts 8---3........................................
Consumable materials 8---3...............................................
Oils for oleopneumatic circuit 8--- 3........................................
Oil for lubricant/coolant fluid 8---4.........................................
Cutting speed and choice of tools 9---1..............................
Cutting speed 9---1......................................................
Standard machine 9---1..................................................
Choice of blade 9---2....................................................
Saw tooth pitch 9---2.....................................................
Cutting speed and downstroke speed 9---2..................................
Ty p e s o f s w a r f : 9 --- 3.....................................................
Lubricant/coolant fluid 9---4..............................................
Blade structure 9---4.....................................................
B l a d e t y p e s 9 --- 5........................................................
C o n v e n t i o n a l r a k e 9 --- 5..................................................
Po s i t i v e r a k e 9 --- 5.......................................................
Va r i a b l e p i t c h 9 --- 5......................................................
Variable pitch blades with 0˚cutting angle 9---6..............................
Variable pitch with positive rake (from 9 to 10 degrees) 9---6...................
Set: 9 --- 6...............................................................
Standard or splayed set 9---6..............................................
U n d u l a t e d s e t 9 --- 7......................................................
Alternating grouped sets 9---7.............................................
A l t e r n a t i n g s e t 9 --- 7.....................................................
Blade selection table relating to cutting speed and downstroke speed 9---8.......
Classification of steels 9---9...............................................
Classification of steels 9---10...............................................
Troubleshooting 10---1............................................
Troubleshooting blade and cutting problems 10---1............................
Troubleshooting 10---7....................................................
D i a g n o s t i c s s y s t e m 1 0 --- 8..................................................
Machine alarms and emergencies 10---10.....................................


1--1
Introduction and
technical
specifications
Foreword
Hyd---Mech in response to modern production techniques, has developed the new
S20DSP.
This work tool has been designed to satisfy the wide range of cutting needs of a
modern workshop with simplicity and reliability, while at the same time comply-
ing with all EEC safety standards.
The S20DSP is structurally rigid, silent and safe: it produces a minimum of waste
while its great versatility makes it suitable for cutting various materials such as
stainless steel light alloys, aluminium, copper and bronze at high speed and with
high precision.
Its high cutting capacity, combined with the possibility of making inclined cuts
from 60˚left to 60˚right, make this model the ideal solution for satisfying the
wide strange of cutting needs of machine shops, turneries, structural steel shops
and engineering workshops.
We congratulate our clients on having chosen this product, which will give
effective and faithful service for many years, especially if the instructions
contained in this use and maintenance manual are carefully followed.
This band saw has been exclusively designed to cut metals.
Machine presentation
Functioning is SEMI---AUTOMATIC.
In Semi---automatic mode, after setting the head cutting stroke on the control
panel and the head downstroke speed, the operator positions the vice 2÷3 mm
from the workpiece and presses the start button (or optional foot pedal if fitted)
on the control panel to start up the band saw. The vice then clamps the material,
the head lowers, cuts the piece and returns to its start position and the vice opens
again.
1.Thecuttervicecloses 2. The head lowers un-
til the cut is made
(FCTA)
3. The head returns to
start position (FCTI)
4. The cutter vice
opens
Warning
1

1--2 2
Use and maintenance manual S20DSP
Machine specification
Theanodisedaluminiumnameplateisrivetedonthesideofthemachine;the
same data are reproduced on the declaration of conformity included with this use
and maintenance manual.
bar bar
------ --
V
1PH AVA
3PH
model
air pressure
data code
oil pressure
HYD--MECH
The Rock Solid Solution
When communicating with the Technical Service department, the model, serial
number and year of manufacture of the machine must be quoted.
CUTTING SPEEDS
Blade rotation speed mt/min 15 100
BAND SAW
Rated size mm 4500 x 27 x 0,9
Max/min blade length mm 4500 ± 40
Blade height mm 27
Blade width mm 0,9
Band saw tension Kg 1250
When choosing the cutting tool, if its dimensions do not correspond to those
included in the ”Rated size” section, check that the dimensions at least fall
within the admissible max/min specifications.
RATED ELECTRICAL POWER
Head spindle motor KW 1.,5
Electric coolant pump motor KW 0,1
M1 power pack motor (optional) KW 0,37
Max installed power KW 1,97
WORKING PRESSURE
Working pressure blade tensioning/detensioning Kg 1250/900
Head working pressure in the ascent phase (optional) Bar 20
Vice working pressure during opening/closure phase (AV ver-
sion)
Bar 6
N.B.
Attention

1--3
3Introduction and technical specifications
LUBRICANT/COOLANT FLUID AND OIL
Oil for blade tensioner unit (optional) capacità Lt 8,5
Lubricant/coolant fluid (oil concentration 5---6%) capacità Lt 200
VICE
Vice max. opening mm 455
SPINDLE MOTOR
No.of poles Current (Volts) Absorption
(Amps)
Power (Kw) rpm
4 400 3,7 1,5 1410
Stator wound with enamelled copper wire, class H 200˚C.
Class F insulation (limit temperature TL 155˚C).
IP 55 protection rating (total against contact with live parts, water sprayed from all directions, with shaft oil
seal).
Conforming to CEI norms, publication: IEC 34 of 01/07/1985.
Example of class F insulation: in air--cooled machines at an ambient tempera-
ture of 40˚C (according to CEI 2--3 and IEC 85), the allowable overtempera-
ture is 100˚C (where 100ٛC represents the allowable DT).
ELECTROPUMP MOTOR
Single phase; Frequency 50 Hz.
Voltage (Volts) Absorption
(Amps)
Power (Kw) rpm Delivery rate
lt/min
Head (mt.)
230 0,30 0,09 2800 24 1,5
400 0,18 0,09 2800 24 1,5
Protection rating IP 55.
Conforming to CEI norms, publication: IEC 34 of 01/07/1985.
CUTTING CAPACITY
Section
0˚330 330 450x330
45˚a320 300 300x300
60˚a210 200 200x200
45˚'320 300 300x300
60˚'210 200 200x200
N.B.

1--4 4
Use and maintenance manual S20DSP
Dimensions
MACHINE INSTALLED
Work table height mm 880
Weight Kg 1110
12001300800
2260
1200 310230
880
2580
1200
3300
1300 800
1200 780600
650
PACKED WEIGHT
Wooden cage and pallet Kg 130
Wooden pallet Kg 70
2900
1800
1800

2--1
Functional parts
S20DSP model
In order for the user to move towards a full understanding of how the machine
works, which is described in detail in the chapter 5, this chapter deals with the
main units and their locations.
CUTTING HEAD
CONTROL
PANEL
VICE
TURNTABLE
BASE
2

2--2 6
Use and maintenance manual S20DSP
Cutting head
The oerating head is the element that performs the cut and is made up of a bow
made from a fusion of cast iron onto which the band, the band guide elements,
the band tensioning unit and the mechanical speed variator are mounted. The
operating head is restricted in its movements by the articulated joint on the
rotatng platform.
Motor
Blade guide heads
Belt tensioning wheel
Transmission box
Drive pulley
Idle pulley
Rear flywheel
Speed variator
Cutting head beam
Front flywheel
Blade casing

2--3
7Functional parts
Vice
The vice is the unit that clamps the workpiece during cutting. It consists of a vice
support, commonly known as a “lead nut”, fixed to the work table, and a lead
screw with a sliding support on which the mobile jaw is mounted. It can run
transversely with respect to the cutting surface, or lengthways, for opening and
closing, on the linear guides and slides with recirculation of pre---loaded spheres.
Theviceismanuallynearedtothematerialtobecutusingahand---wheeland
blocking is performed using a hydraulic cylinder (in the AV version).
Slideway
Handwheel
Vice support (lead nut)
Control Panel
The control panel has a protection rating of IP 54 and contains the electronic
equipment. Access to the control panel is protected by a safety panel mounted on
hinges and fastened with screws, specially designed to prevent tampering. The
control panel swivels on two articulated joints so that it can be positioned by the
operator for greater ease---of---use and safety.
Control panel
Articulated joints
Control console

2--4 8
Use and maintenance manual S20DSP
Turntable
Made from a fusion of cast iron it makes up the fulcrum of the cutting band. By
releasing the blocking lever on the fixed platform right and left rotation of the
bow is consented.
Fixed platform
It is made up of two parts, upper and lower, which close the rotating and platform
and support the cutting surface in interchangeable steel.
The lower part is the resting base of the rotating platform, cutting surface and
vice. It is free to run transversely on linear guides and slides with re---circulation
of pre---loaded spheres. It is integral to the base and the rear part has the
reference strokes for 60˚left and 60˚right cuts.

2--5
9Functional parts
Motion--variator--reducer unit
Rotation of the band is performed by a system made up of a motor connected to a
variator and a mechanical speed reducer.
This unit allows rotation of the band in a continuous adjustment range that goes
from 20 to 100m/min.

2--6 10
Use and maintenance manual S20DSP
Base
This unit features a large coolant collection surface which conveys the coolant to
the rear tank via the tank cover, and a swarf collection drawer. An electric pump
is housed inside the tank which draws the clean fluid from the filter system.
Lubricant/coolant tank
Electric pump housing
Swarf collection drawer
Hydraulic single box housing

3--1
Safety and accident
prevention
The S20DSP has been designed and produced in accordance with European
standards. Forthecorrectuseofthemachinewerecommendthattheinstruc-
tions contained in this chapter are carefully followed.
Use of the machine
The S20DSP band saw cutting machine is intended exclusively for cutting metallic
materials, ferrous or non---ferrous, in section or solid.
Other types of material and machining are not compatible with the specific
characteristics of the saw.
The employer is responsible for instructing the personnel who, in turn, are
obliged to inform the operator of any accident risks, safety devices, noise
emission and accident prevention regulations provided for by international
standards and national laws regarding the use of the machine. The operator must
be perfectly aware of the position and function of all the machine’s controls.The
instructions, warnings and accident prevention standards in this manual must be
respected without question by all those concerned.The following definitions are
those provided for by EEC MACHINES DIRECTIVE 98/37/CE :
H“Danger zone”: any zone in and/or around a machine in which the presence of a
person constitutes a risk for the safety and health of that person.
H“Person exposed”: any person finding himself either completely or partly in a
danger zone.
H“Operator”: the person or persons given the responsibility of installing, operating,
adjusting, maintaining, cleaning, repairing or transporting the machine.
The manufacturer declines any responsibility whatsoever, either civil or crimi-
nal, should there be unauthorised interference or replacement of one or more
parts or assemblies on the machine, or if accessories, tools and consumable
materials are used that are different from those recommended by the manu-
facturer itself or if the machine is employed in a plant system and its proper
function is thereby altered.
Attention
3

3--2 12
Use and maintenance manual S20DSP
General recommendations
LIGHTING
Insufficient lighting for the types of operation envisaged could constitute a safety
hazard for the persons concerned. For this reason, the machine user must provide
lighting in the working area sufficient to eliminate all shadowy areas while also
avoiding any blinding light concentrations. (Reference standard ISO 8995---89
“Lighting in work environments”).
CONNECTIONS
Check that the power supply cables and pneumatic feed systems comply with the
maximum machine absorption values listed in the “Machine Specification” tables;
replace if necessary.
EARTHING
The installation of the earthing system must comply with the requirements set out
in IEC STANDARD 204.
OPERATOR POSITION
The position of the operator controlling machine operations must be as shown in
the diagram below.

3--3
13 Safety and accident prevention
Recommendations to the operator
Always wear proper goggles or protective glasses.
Do not use the machine without the guards in position. Replace the poly-
carbonate windows , if subject to corrosion.
Do not allow hands or arms to encroach on the cutting zone while the
machine is in operation.
Do not wear oversize clothing with long sleeves, oversize gloves, brace-
lets, necklaces or any other object that may become entangled in the ma-
chine during working; long hair must be tied back and bunched.
Alwaysdisconnectthepowersupplytothemachinebeforecarryingout
any maintenance work whatsoever, including in the case of abnormal
operation of the machine.
Before starting cutting operations, support the material at both ends of
the machine using the support arm --- standard, or OPTIONAL acces-
sories such as the feed and discharge roller tables shown in the diagram
below. Before removing the devices supporting and moving the material,
fasten the latter in place using the machine’s clamping devices or other
suitable equipment.
mm. 1500 mm. 1500
FEED ROLLER TABLE DISCHARGE ROLLER TABLE
Arrange recovery/collection systems for the cut pieces, such as metal
baskets, for example.

3--4 14
Use and maintenance manual S20DSP
mm. 1500
FEED ROLLER TABLE COLLECTION BASKET
Any maintenance work on the hydraulic or pneumatic systems must be
carried out only after the pressure in the system has been released.
The operator must not perform any risky operations or operations not
required for the machining operation under way (e.g. remove swarf or
metal shavings from the machine while cutting).
Remove equipment, tools or any other objects from the cutting zone;
always keep the working area as clean as possible.
Before starting any cutting operations, ensure that the workpiece is
securely held in the vice and the machine has been set correctly. A
number of examples of how to clamp different profiles correctly in our
machines are shown below.
Do not use the machine to cut pieces that exceed the capacity of the
machine as listed in the machine specifications.
Never move the machine while it is cutting.
Do not use blades of different sizes to those recommended in the
machine specifications.
When cutting very short pieces, make sure that they are not dragged
behind the support shoulder, where they could jam in the blade.
Table of contents
Popular Cutter manuals by other brands
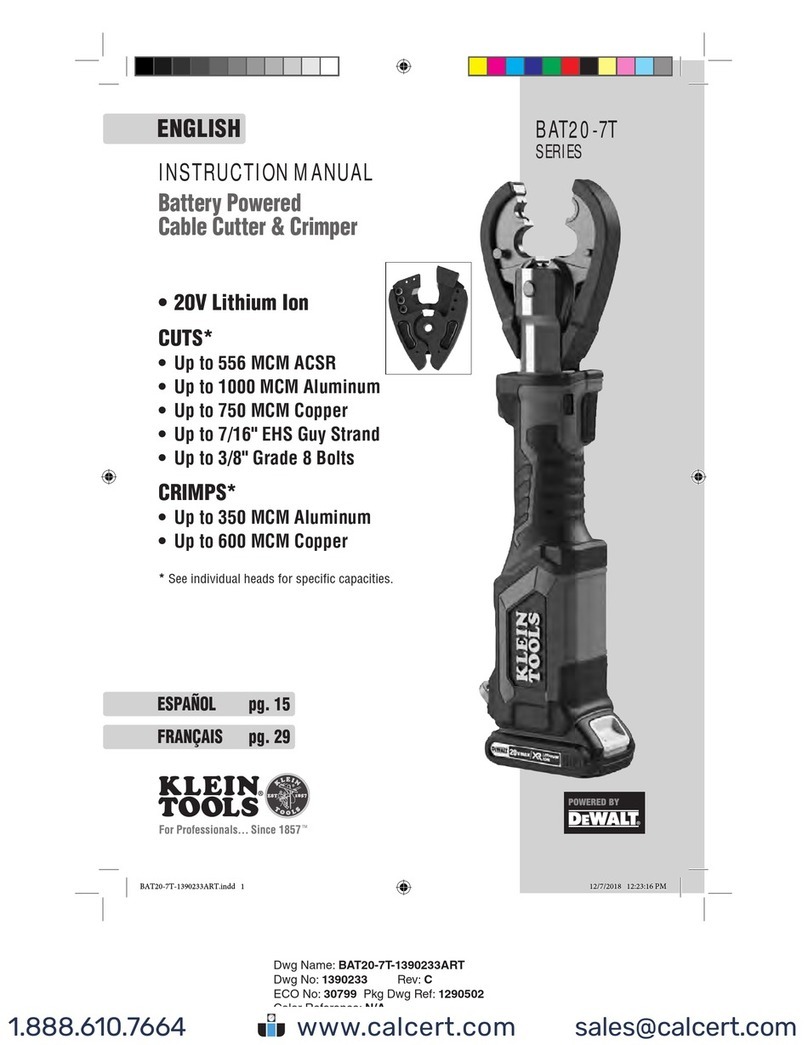
Klein Tools
Klein Tools BAT207T3 instruction manual

Westfalia
Westfalia TC 180 J 11 instruction manual
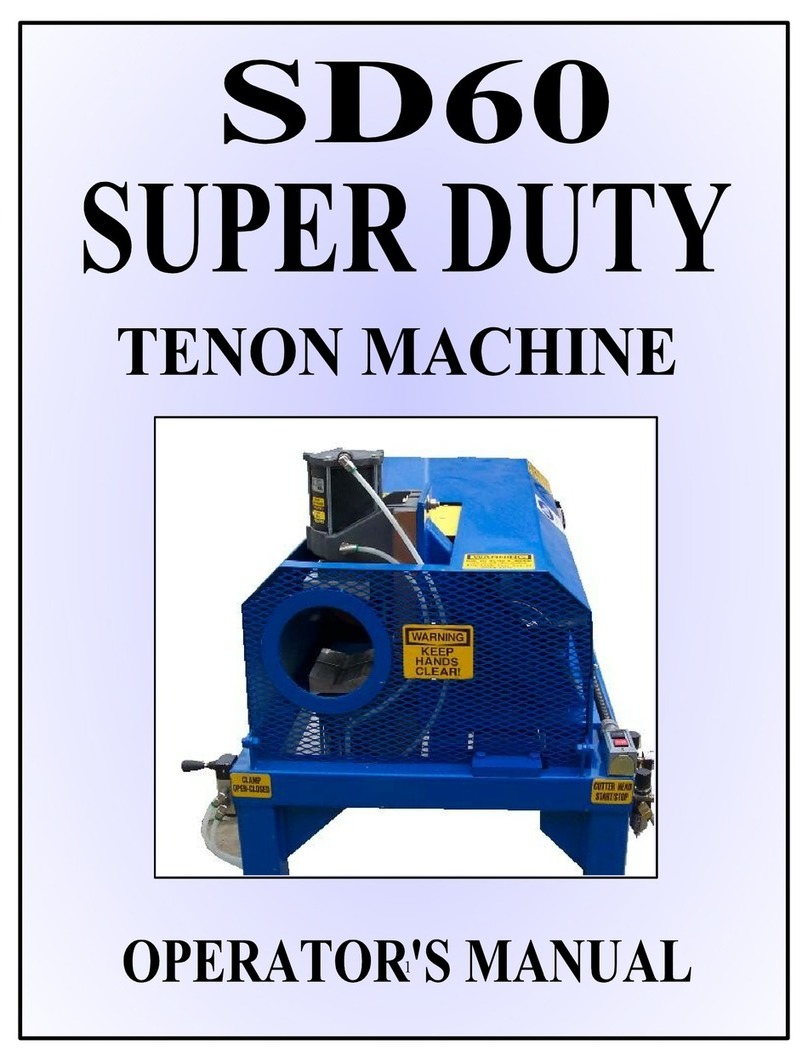
Dyna
Dyna SD 60 Operator's manual
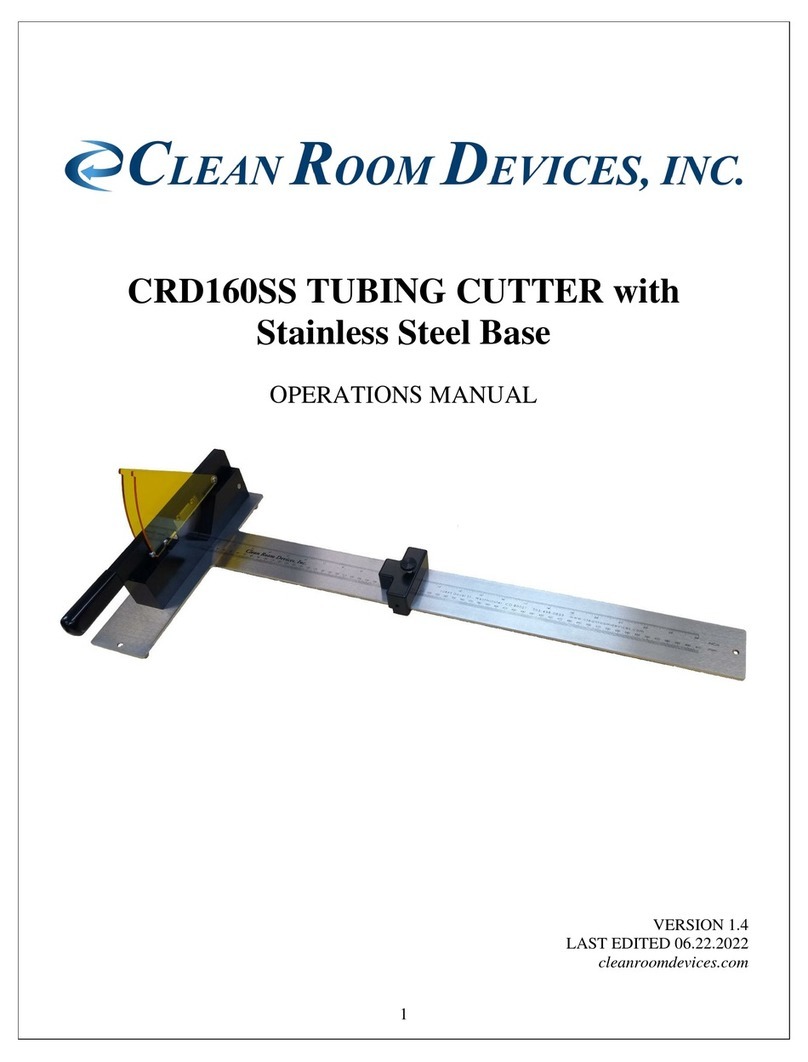
CLEAN ROOM DEVICES
CLEAN ROOM DEVICES CRD160SS Operation manual

Powermatic
Powermatic SLR12-700 instruction sheet
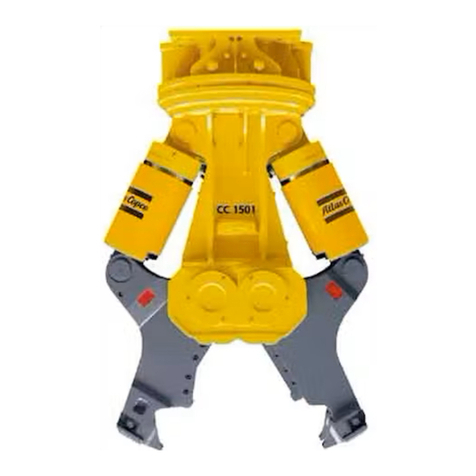
Atlas Copco
Atlas Copco CombiCutter CC 1501 operating instructions