Hydra-slide LP350 Manual

SKIDDING RIGGING HYDRAULICS
LOW PROFILE SKIDDING SYSTEM
MODEL:
LP350
March 2018
Hydra-Slide Ltd.
84 Royal Rd.,
Guelph, ON. N1H 1G3
Canada
hydra-slide.com
PLEASE READ OPERATING MANUAL BEFORE
USING THIS EQUIPMENT AND ADHERE TO ALL
SAFETY INSTRUCTIONS. FOR QUESTIONS
CONTACT HYDRA-SLIDE LTD. AT 519-830-7517.

Table of Contents
1 - GENERAL INFORMATION....................................................................................................................... 1
1.1 Original Instructions ................................................................................................................................ 1
1.2 Manufacturer Details ............................................................................................................................... 1
1.3 Machinery Description............................................................................................................................. 1
1.3.1 The Workstation ............................................................................................................................... 2
1.3.2 Intended Use ..................................................................................................................................... 2
1.4 Safety Precautions .................................................................................................................................... 2
1.4.1 General Safety Precautions and Potential Misuse ............................................................................ 2
1.4.2 Operator Training ............................................................................................................................. 3
1.4.3 Residual Risks and Protective Measures .......................................................................................... 3
1.4.4 In Case of Breakdown ....................................................................................................................... 4
1.4.5. Airborne Noise Emissions ............................................................................................................... 4
1.4.6 Non-Ionizing Radiation .................................................................................................................... 4
2 - ASSEMBLY AND SETUP .......................................................................................................................... 5
2.1 General Instructions ................................................................................................................................. 5
2.2 Track Plate Connection ............................................................................................................................ 5
2.3 Slider Plate Assembly .............................................................................................................................. 6
2.4 Slider Plate – Pusher Head Connection ................................................................................................... 7
3 – OPERATION ............................................................................................................................................... 9
4 - MAINTENANCE AND ADJUSTMENTS ................................................................................................ 11
4.1 Preventive Maintenance ......................................................................................................................... 11
4.2 Troubleshooting ..................................................................................................................................... 11
5 - TRANSPORTATION, HANDLING, AND STORAGE ........................................................................... 12
APPENDIX 1 – EC DECLARATION OF CONFORMITY ........................................................................... 13


1
ORIGINAL INSTRUCTIONS
HYDRA-SLIDE LP350 LOW PROFILE SKIDDING SYSTEM
1 - GENERAL INFORMATION
1.1 Original Instructions
The English version of this manual is the Original Instructions for the Hydra-Slide LP350 Low Profile
Skidding System. All other language versions are translations of the Original Instructions.
1.2 Manufacturer Details
Hydra-Slide Ltd.
84 Royal Road
Guelph, Ontario, Canada
N1H 1G3
(519)-900-1450
1.3 Machinery Description
Machinery Designation: LP350 Low Profile Skidding System
Hydra-Slide’s LP350 Low Profile Skidding System has been designed to move loads with a maximum
capacity of 350 tons (318 tonne). The system uses specially designed skid shoes and hydraulically
operated push cylinders to move loads horizontally along guiding tracks over a friction surface. The
hydraulic push cylinders are modified double acting cylinders which operate at 10,000 psi (700 bar).
The friction surface is a dry graphite lubricant film. The height of the load support section is 1.5” (38
mm), and all components are hand-portable, the maximum component weight being 125 lbs. (57 kg).
The following main components comprise a standard system:
16 x Track Sections
18 x Track Connector Plates
2 x Male Slider Plates
2 x Female Slider Plates
2 x Inner Slider Plates
2 x Push Cylinder Assemblies
2 x Pusher Heads
1 x Storage Box
Hardware kit including Allen wrenches, thread tap, coupler bleed tool, and touchup paint

2
The LP350 Low Profile Skidding System is designed to work with most 10,000 psi (700 bar) hydraulic
power units; however, it is recommended to be used with Hydra-Slide’s synchronous HYDRA-PAC
power units. The system comes with a steel storage box to store all system components and necessary
hardware to assemble and operate.
1.3.1 The Workstation
The LP350 Low Profile Skidding System is remotely operated. It is suggested that the operator set up
his/her workstation in a safe location, clear of the load to be skidded, and with as much visibility of the
load and skidding system as possible.
1.3.2 Intended Use
The LP350 Low Profile Skidding System is used to move heavy equipment up to 350 tons (318 tonne)
safely and in a controlled manner.
1.4 Safety Precautions
Set up and operate the LP350 Low Profile Skidding System only under the direction and supervision
of experienced and qualified personnel.
This section contains information required for the safe operation of the LP350 Low Profile Skidding
System. Please read and understand the instructions and safety warnings that come with the equipment.
Failure to comply with these safe operating recommendations could result in property damage or
personal injury. Always follow safe work practices.
The LP350 has been designed and manufactured for a maximum load capacity of 350 tons (318 tonne).
The maximum operating pressure of the push cylinders is 10,000 psi (700 bar). Do not exceed these
values at any time when using the system.
Use in any other manner or for any other purpose is not intended and is not recommended by the
manufacturer. The operational safety of the system is only assured if used as intended.
1.4.1 General Safety Precautions and Potential Misuse
Only qualified operators should install, operate, adjust, maintain, clean, repair or transport this
equipment.
Only use this equipment in accordance with its intended use and follow all instructions.
Never exceed recommended maximum pressure and stroke ratings. Good practice recommends
using only 80% of these ratings.
Always wear appropriate Personal Protective Equipment.
Protect all equipment from potential hazards such as fire, explosion, sharp surfaces, extreme
heat/cold, corrosives, and heavy impact.
Anticipate possible problems and take steps to avoid them. If in doubt, ask.
Never operate any equipment without all provided guards and safety devices in place and in good
working condition.
Lift and move slowly and check often. Control the load at all times.

3
Double-check track connections before loading the track.
Avoid standing in the line of force of hoses or any hydraulic components.
Lift or move equipment and components using only the provided lift lugs or handles, etc. and
only employ proper lifting equipment and techniques. Never lift by the hoses or hydraulic
fittings.
Never place any part of your body under the load unless the load is on a solid support.
Never place any part of your body between a moving load and a solid obstacle where there is
danger of crushing.
Take steps to keep all equipment clean and free from possible damage. This is particularly
important for hoses and couplers.
Don’t allow hoses to kink, twist, crush, cut or bend tightly. Bending radius should be at least 4½
inches. Inspect hoses and couplers before each use and remove from service if any signs of
damage are noted. Never attempt to repair a hose.
Never handle hoses or couplers while they are under pressure, even when wearing Personal
Protective Equipment. There is risk of serious personal injury from hose leaks, faulty or
improperly connected couplers.
Use safe practices to bleed a pressurized hose or coupler; use only a specially-designed coupler
bleed tool such as a CT-604 Safety Tool available through Hydra-Slide Ltd.
Always ensure that jacks and cylinders are used parallel and in line with their axis. Never use a
jack or cylinder at an angle or to “kick” or move a load sideways. Use only Hydra-Slide’s AS500
Alignment Shoes for these types of operations.
Do not apply any external forces to the load or track other than those from proper use of the
supplied hydraulic cylinder(s), i.e. do not use come-alongs, winches, etc. to push or pull the load
If jacking a load, always use appropriate blocking or cribbing to guard against a falling or out of
control load.
Do not use any lubricants on the system other than those provided and/or specified for use.
1.4.2 Operator Training
The operator should be experienced in the safe operation of high pressure hydraulic jacking systems.
The operator should also read and understand these Instructions in full prior to operating the system.
1.4.3 Residual Risks and Protective Measures
Observing the safety precautions indicated in these Instructions minimizes the risks associated with
using the LP350 Low Profile Skidding System, however residual risks remain in the event of loss of
control of the load while skidding. It is recommended to always use the provided stop blocks as
described in Section 3.3.

4
1.4.4 In Case of Breakdown
In case of equipment breakdown or other operational problems, cease operation immediately and take
any necessary steps to secure equipment and protect surroundings and personnel. Depressurize hoses
and all hydraulic components (use coupler bleed tool as required). Identify the problem. Jack up the
load to remove weight from skid system and secure it with blocking or other support. Correct the
problem and/or replace any broken or defective components. Jack down load onto skid system and
continue operations in accordance with these Instructions.
1.4.5. Airborne Noise Emissions
Operation of the LP350 Low Profile Skidding System does not produce airborne noise exceeding 70
dB(A).
1.4.6 Non-Ionizing Radiation
Operation of the LP350 Low Profile Skidding System does not produce non-ionizing radiation.

5
2 - ASSEMBLY AND SETUP
Before each use, inspect the system for any signs of damage or oil leaks. If any issues are found, do not
operate the LP350 until corrective measures have been taken.
2.1 General Instructions
Establish a clear path for the load to be moved.
Raise load (using other means) to a sufficient height to place skid system under.
Place track under load.
The track sections are bi-directional and symmetric; any two ends may be connected together.
Connect the track plate sections using the connector plates supplied and secure with the
countersunk screws. Hand tighten only and ensure that the Tracks are set up parallel and level.
It may be advantageous to have a slight incline in the direction of travel but never set up or
operate the system on a decline without an adequate external holdback.
Tracks must be oriented so the load will move in a straight line to the desired location.
Tracks must be positioned such that the ratchet slots are equidistant from the edge of the load so
the push cylinders will be able to extend in synchronization.
The track must be fully supported over its entire length. Excess deflection can cause severe
damage.
2.2 Track Plate Connection
The wedge design of the track connection requires that the ends of the track sections be in direct contact
so the feet of the connector plate can fit into the slots on the two adjacent track plate sections (see detail
figure below).
Set up two track sections end-to-end with track ends in full contact.
Place track connector plate over the two adjacent tracks ensuring bottom of connector plate is
sitting flat on the top face of the two track sections.
Once the connector plate is in place, pull the tracks apart so the inside faces of the feet on the
connector plate come into direct contact with the tracks.
Secure the track connector plate to the track sections using the supplied bolts (see figures below).

6
2.3 Slider Plate Assembly
Insert the skid shoe slider plates on the track under the load and connect the holes over the pins. Ensure
that the guide bars engage and that the slider plates move freely on the track.
The LP350 system has three different types of slider plates. This allows the system to be set up and
operated in several different configurations, depending on the size of the load being moved. The three
slider plate types are shown below.
The slider plates are connected to each other using male-female type connections (see above figures).
For moving longer, single-piece loads it is possible to divide the slider plates into front and rear sections.

7
For this configuration, it is necessary to ensure that the front and rear slider plates do not lose contact
with the load as they may become displaced; it is recommended to purchase additional pusher heads for
the rear end in order to maintain direct contact with the load.
When setting up and connecting the slider plates, ensure that the two slots on the ends of the male and
female slider plates are on the outsides of the slider plate assemblies so that the pusher heads can be
connected (see details in Section 2.4).
2.4 Slider Plate – Pusher Head Connection
Attach the pusher heads to one end of each slider plate assembly and engage the hinged locking
pins.
Ensure that the area on the bottom of the load where it will contact the slider plate assembly is
clear and is a suitable supporting surface.
Position the slider plate assembly under the load and ensure that the weight of the load will be
distributed evenly over the surface of the slider plates. Note:
o Do not exceed 30,000 lbs per foot of slider plate length used (44,000 kg per meter
of length)
o Do not point-load
o It is good practice to use a friction material such as wood or rubber between the
skid shoe and the load
The pusher heads must make direct contact with the load, otherwise the slider plates can bend
causing severe damage to the system.

8
Check to make sure that the track has been set up properly and is adequately supported.
Lower the load (by other means) onto the slider plate assembly and ensure that it is evenly
distributed over the surface of the skid shoe.
Check one final time to make sure that the track and slider plates are properly set up and
adequately supported, making any necessary corrections before operating the system.

9
3 – OPERATION
It is recommended that the cylinder rods be extended and retracted fully at least twice before connecting
to the system to verify their functionality.
Insert the push cylinder assemblies into the track and place the rod end into the pusher head slots.
Ensure that the cylinder’s base plate engages with the ratchet slots in the track.
Attach suitable 10,000 psi-rated hydraulic hoses to the cylinder quick coupler fittings. Unless
otherwise specified, the advance and retract ports have standard CR-400 female couplers.
Connect the other end of the hoses to a suitable hydraulic pump unit, ensuring that the bottom of
each cylinder is connected to the “advance port” and the top of each cylinder is connected to the
“return port”. These systems will function with most 10,000 psi double-acting hydraulic pumps
however we recommend use of a “synchronous” pump unit.
Ensure that all couplers are fully engaged and hand-tight, otherwise the hose check valves will
not open and the cylinders will not function properly.
Ensure a clear path for the hydraulic hoses and monitor continually to make sure they will not
become caught or entangled during the move.
The pump unit should be placed in a location which gives the operator an unobstructed view of
the push cylinders during operation. Personnel should be positioned at the back side or in any
area of operation that is not visible to the operator, and should be in continuous visual or radio
contact with the operator.
Apply hydraulic pressure and extend the push cylinders, one at a time, until they come into
contact with the load.
Check the complete system setup and ensure that the push cylinders are properly engaged and
that there are no hydraulic leaks.
Continue to extend the push cylinders to near full stroke making sure that they extend in unison
so they do not jam in the track, which could damage the system. If possible, avoid fully

10
extending the push cylinders, and avoid full pressurization when extended as this can cause
serious damage to the cylinder internals.
Retract the push cylinders until they rise up over the track slide plates and drop into the next slot.
Continue to extend and retract the push cylinders as above until the load reaches the desired position.
If the load has been moved too far, simply reposition the pusher heads to the opposite end of the slider
plates, and push the load back to the desired position.
As before during initial setup, ensure that the pusher heads make direct contact with the load, otherwise
the slider plates can bend causing severe damage to the system. To accomplish this it may be necessary
to raise the load and reposition the slider plate assemblies.
When the desired position is reached, raise the load (using other means) to a sufficient height to remove
the skid system, and then lower the load into place.

11
4 - MAINTENANCE AND ADJUSTMENTS
4.1 Preventive Maintenance
When not in use, store all of the skid system components in the supplied storage box, in a dry
location and protected from damage. Take special care of all hydraulic components and fittings.
Keep skidding surfaces clean, dry and completely covered with graphite. Reapply graphite as
needed depending on usage and storage conditions. Minor surface rusting should not affect the
system’s performance, and can be removed with a scouring pad before use.
Repair or replace any broken, worn or damaged components. Contact Hydra-Slide Ltd. For
replacement parts.
Keep cylinder rods fully retracted when not in use.
Keep coupler threads clean and well-lubricated, and secure the protective dust caps on all
couplers when not in use.
4.2 Troubleshooting
Symptom Probable Cause Recommended Action
Push cylinder will not extend, or
extends only partially
- Coupler is not fully engaged
- Load exceeds capacity
- Skid shoe is jamming in track
- Check and tighten all couplers
- Reduce load
- Realign track
Push cylinder will not extend and
oil is coming from pressure relief
valve or top of cylinder
- Coupler is not fully engaged - Check and tighten all couplers
Cylinders exhibit jerky, sporadic
movement when extending
- Air in hydraulic system - Bleed the hydraulic system
Push cylinder will not retract - Coupler is not fully engaged - Check and tighten all couplers
Load does not move straight - Track is not set up equidistant from
edge of load
- Cylinders are not extending in
unison
- Reposition track
- Use a synchronous pump unit or some
other means to provide equal oil flow.

12
5 - TRANSPORTATION, HANDLING, AND STORAGE
Individual components should be handled separately and with care. Weights are indicated on the
nameplates of each component part.
Lift all components using the attached handles; we recommend handling track sections with two
personnel, as
Transport and handle in a safe manner and always ensure that parts are properly secured and
prevented from unexpected movement.
When not in use, store the skidding system in a covered, dry location, protected from damage.
Take special care of all hydraulic components, hoses and fittings, etc.
Wipe clean the inside and outside of all hose couplers using a clean, non-fibrous cloth before
connecting; always replace protective caps when couplers are not in use.

13
APPENDIX 1 – EC DECLARATION OF CONFORMITY
Manufacturer
Hydra-Slide Ltd.
84 Royal Road
Guelph, Ontario, Canada
N1H 1G3
We declare that the Hydra-Slide LP350 Low Profile Skidding System is in accordance with the following
Harmonized Standards:
EN ISO 12100:2010 Safety of machinery – General principles for design -
Risk assessment and risk reduction
EN 4413:2010 Hydraulic fluid power – General rules and safety
requirements for systems and their components
And in accordance with the EC Guidelines of:
2006/42/EC – Machinery Directive
Documentation supporting this declaration is kept on file at the address listed above.
Hydra-Slide Ltd. February 18, 2017
Don Mahnke P. Eng
President

1
5
3
4
2
6
7
LP350 SYSTEM ASSEMBLY
SIDE VIEW
TOP VIEW
END VIEW
1"
25
11
2
"
38
A
48"
1219
48"
1219
141 3
8
"
3591
72"
1829
12"
305
13 1
4
"
337
91
2
"
240
63
8
"
162
12"
305
20"
503
25 5
8
"
650
30"
761
33
4
"
95
DETAIL A
CYLINDER MOUNT & PUSHER HEAD ASSEMBLY
ITEM No.
PART No.
DESCRIPTION
WEIGHT
1
LP350-01
Track Plate Assembly
120 lb
55 kg
2
LP350-02
Female Slider Plate Assembly
120 lb
55 kg
3
LP350-03
Male Slider Plate Assembly
120 lb
55 kg
4
LP350-04
Inner Slider Plate Assembly
120 lb
55kg
5
LP350-05
Track Connector Plate
5 lb
2.3 kg
6
LP350-06
Push Cylinder Assembly
100 lb
45 kg
7
LP350-07
Pusher Head Assembly
30 lb
14 kg
4
A
123
B B
A
2 134
LP350 GENERAL
ASSEMBLY DRAWING
01
LP350-GA
SHEET 1 OF 1
REV
DWG. NO.
B
SIZE
TITLE:
PROPRIETARY AND CONFIDENTIAL
THE INFORMATION CONTAINED IN THIS DRAWING IS THE SOLE
PROPERTY OF HYDRA-SLIDE LTD. ANY REPRODUCTION IN PART
OR AS A WHOLE WITHOUT THE WRITTEN PERMISSION OF
HYDRA-SLIDE LTD. IS PROHIBITED.
DRAWN BY:
R.Y.


HS3014 HYDRAULIC CYLINDER OPERATING INSTRUCTIONS
1.0 Contact Information
Hydra-Slide Ltd.
5617 4th Line RR # 3 Rockwood
Ontario, Canada
N0B 2K0
(519)-496-4008
2.0 General Instructions
This manual provides instructions on the safety, installation, operation, maintenance, and
troubleshooting for Hydra-Slide’s HS3014 Hydraulic Cylinders. Before any operation involving the use
or maintenance of the cylinders, please read this Manual carefully.
It is recommended that service work on the HS3014 Cylinders be provided by qualified technicians only.
It is advised that only spare parts recommended by Hydra-Slide Ltd. be used for repair. Hydra-Slide does
not accept responsibility for damages caused by the use of unsuitable spare parts.
Please contact Hydra-Slide if any problems occur during the operation of the HS3014 Cylinders or if any
spare parts are required for repair.
3.0 Receiving Instructions
Components should be visually inspected after receiving to ensure no damage to the equipment during
shipping. If any damage is present, please contact Hydra-Slide immediately.
4.0 Product Description
The Hydra-Slide HS3014 Cylinder is a 30 ton (27.2 tonne) capacity, double acting hydraulic cylinder.
•Maximum Operating Pressure: 10,000 psi (700 bar)
•Maximum Stroke Length: 14.5 inches (370 mm)
•Collapsed Height: 22.7 inches (575 mm)
•Cylinder Diameter: 4 inches (100 mm)
•Cylinder effective area
oPush: 6.488 in2(4185 mm2)
oPull: 2.514 in2(1620 mm2)
•Cylinder max force @ 10,000 psi
oPush: 64,000 lbs (29030 kg)
oPull: 25,000 lbs (11340 kg)

5.0 Safety
Always read and understand instructions and safety warnings that come with the equipment
and always follow safe work practices. Failure to comply with these safe operating
recommendations could result in property damage or personal injury.
•Only qualified operators should install, operate, adjust, maintain, clean, repair or
transport this equipment.
•Only use this equipment in accordance with its intended use and follow all instructions.
•Never exceed recommended maximum pressure and stroke ratings. Good practice
recommends using only 80% of these ratings.
•Always wear appropriate personal protective equipment.
•Protect all equipment from potential hazards such as fire, explosion, sharp surfaces,
extreme heat/cold, corrosives or heavy impact.
•Anticipate possible problems and take steps to avoid them. If in doubt, ask.
•Never operate any equipment without all provided guards and safety devices in place
and in good working condition.
•Lift/move slowly and check often. Control the load at all times.
•Avoid standing in the line of force of hoses or any hydraulic components.
•Lift or move equipment and components using only the provided lift lugs or handles,
etc. and only employ proper lifting equipment and techniques. Never lift by the hoses
or hydraulic fittings.
•Never place any part of your body under the load unless the load is on a solid support.
•Never place any part of your body between a moving load and a solid obstacle where
there is danger of crushing.
•Take steps to keep all equipment clean and free from possible damage. This is
particularly important for hoses and couplers.
•Don’t allow hoses to kink, twist, crush, cut or bend tightly. Bending radius should be at
least 4 ½ inch. Inspect hoses and couplers before each use and remove from service if
any signs of damage are noted. Never attempt to repair a hose.
•Never handle hoses or couplers while they are under pressure even when wearing
personal protective equipment. There is risk of serious personal injury from hose leaks,
faulty or improperly connected couplers.
•Never use unsafe practices to bleed a pressurized hose or coupler. Use only a specially
designed coupler bleed tool such as a CT-604 Safety Tool available through Hydra-Slide
Ltd.
Table of contents
Popular Lifting System manuals by other brands
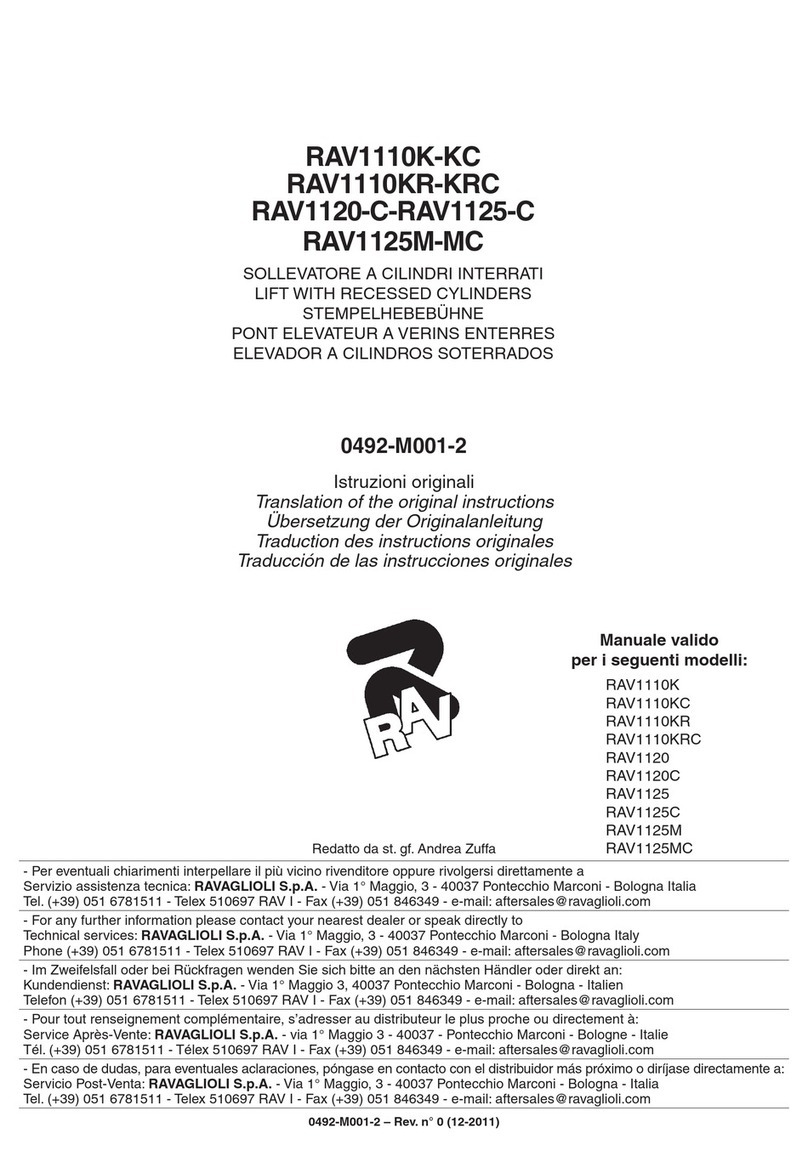
Ravaglioli
Ravaglioli RAV1110K instructions

Caliber
Caliber MOTO RampPro 13561 Assembly instructions
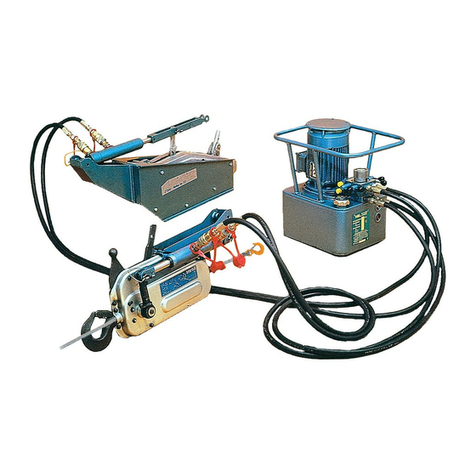
Tractel
Tractel Supertirfor TU16H Operating and maintenance instructions

Toyota
Toyota 7BPUE15 Service manual
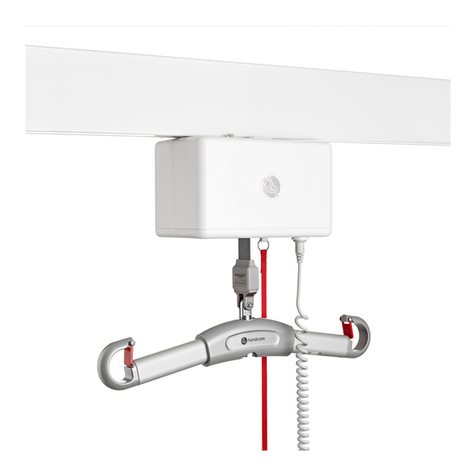
SystemRoMedic
SystemRoMedic RiseAtlas625M user manual
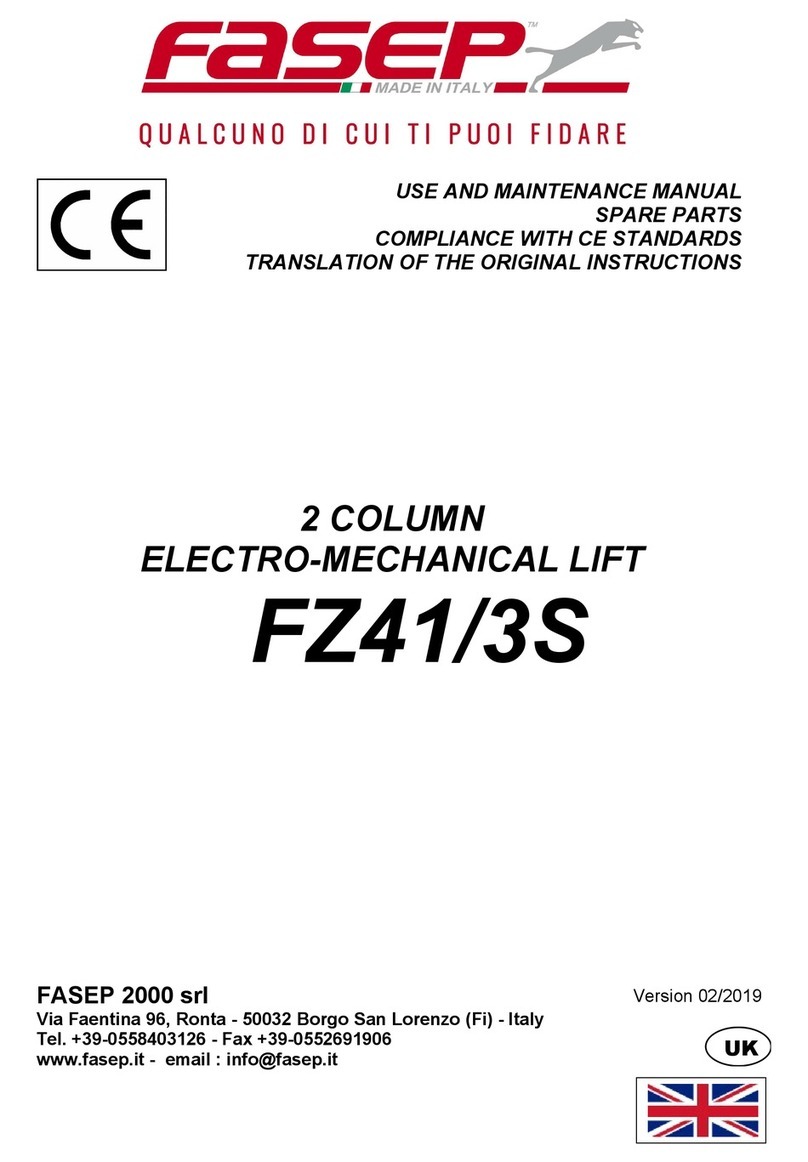
Fasep
Fasep FZ41/3S Use and maintenance manual, spare parts catalog