IBM 29 CARD PUNCH - User manual

a
"
*
.
D
3
Card
Punch
sve
&
Field
Engineering
Maintenance
Manual
$225-3357-3

II
Ina
Field
Engineering
Maintenance
Manual
D
Card
Punch
$225-3357-3

Preface
This
publication
provides
information
for
the
maintenance
of
the
IBM
29
Card
Punch.
The
manual
is
written
with
presupposition
that
the
reader
has
a
working
knowledge
of
the
machine.
As
much
applicable
information
as
possible
is
in
each
section
of
this
manual.
The
sections
are
numbered
for
easy
reference.
The
sections
are
presented
in
a
sequence
similar
to
the
card
path
through
the
machine.
Timing
adjustments
for
some
units
may
vary
among
machines
due
to
features
and
engineering
changes;
refer
to
the
individual
machine
wiring
diagram
for
accurate
timing.
Special
features
are
treated
individually
in
a
separate
manual,
Field
Engineering
Theory
—
Maintenance,
JBM
29
Card
Punch
Features,
[BM
29
Interpreting
Card
Punch,
Model
C,
Form
223-2926.
Other
related
manuals
are:
Field
Engineering
Theory
of
Operation,
JBM
29
Card
Punch,
Form
225-3358
Illustrated
Parts
Catalog,
JBM
29
Card
Punch,
Form
124-0085
Reference
Manual,
JBM
29
Card
Punch,
Form
A24-3332
Fourth
Edition
(April
1969)
This
a
major
revision
of,
and
obsoletes,
Form
225-335
7-2,
FE
Supplement
Form
$23-4035,
and
all
earlier
editions.
Significant
changes
have
been
made
throughout
this
manual,
including:
new
diagnostic
flowcharts,
Chapter
1;
a
new
chapter,
Chapter
2;
new
lubricant
specifications,
Chapter
3;
revised
starwheel
adjustments
and
revised
print
suppress
adjustments,
Chapter
4.
This
manual
should
be
reviewed
in
its
entirety.
Changes
are
periodically
made
to
the
specifications
herein;
any
such
changes
will
be
reported
in
subsequent
revisions
or
FE
Supplements.
This
manual
has
been
prepared
by
the
IBM
Systems
Development
Division,
Product
Publications,
Dept
B96,
PO
Box
390,
Poughkeepsie,
N.Y.
12602.
A
form
for
readers’
comments
is
provided
at
the
back
of
this
publication.
If
the
form
has
been
removed,
comments
may
be
sent
to
the
above
address.
©Copyright
International
Business
Machines
Corporation
1965,
1969

Chapter
1.
Reference
Data
and
Service
Aids
.
Section
1.
Reference
Data.
1.1
Operations
1.2
Sequence
of
Operations
1.2.1
Functions
.
Section
2.
Diagnostic
Techniques
1.3
Initial
Approach
.
1.4
Diagnostic
Flowcharts
.
1.4.1
Start
and
Run
Failures
.
1.4.2
Card
Transport
Failures
1.4.3
Interposer
Selection
Failures
1.4.4
Escapement
Failures
1.4.5
Punch
Drive
Cycle
Failures
.
1.4.6
Printing
Control
Failures
1.5
Machine
Service
Features
1.5.1
Motor
Switch
1.5.2
Test
Probe
1.6
Servicing
Techniques
1.6.1
Forcing
1.6.2
Interrupting
Machine
Operation
1.6.3
Jum
pering
1.6.4
Measuring
1.6.5
Cycling
Manually
1.6.6
Interchanging
Units
.
1.7
Difficult-to-Analyze
and
Intermittent
F
ailures
1.7.1
Left-Zero
Feature
1.7.2
Diagnosis
of
““Heavy”’
or
Stiff
Keyboards
1.7.3
Stacker
;
.
1.7.4
Starwheel
Adjustment
.
Chapter
2.
Console
and
Maintenance
Facilities
Section
1.
Basic
Unit
,
2.1
Installation
Procedures
.
2.1.1
Shipping
Material
2.1.2
Power
.
2.1.3
Keyboard
Operations
2.1.4
Program
and
Function
(Model
A).
2.1.5
Program
and
Function
(Model
B)
.
2.1.6
Final
Checkout
.
Section
2.
Features.
.
2.2
Installation
Procedures
.
2.2.1
Feature
Checkout
2.2.2
Final
Checkout
.
Chapter
3.
Preventive
Maintenance
.
Section
1.
Basic
Unit
3.1
Cleaning
.
3.2
Adjustment
3.3
Safety
.
3.3.1
Safety
Devices
3.3.2
Electrical
Hazards
3.3.3
Chemical
Hazards
3.4
Lubrication
Section
2.
Features
.
Chapter
4.
Checks,
Adjustments,
and
Removals
Section
1.
Basic
Unit
4.1
Base
4.1.1
Diodes
1-7
1-7
1-7
1-7
1-8
1-8
1-8
1-10
1-10
1-10
1-11
j-11
1-12
1-12
2-1
2-1
2-1
2-1
2-1
2-1
2-1
2-2
2-3
2-3
2-3
2-3
3-1
3-1
3-1
3-1
3-1
3-1
3-1
3-1
3-1
3-8
4-1
4-1
4-1
4-]
4.1.2
4.2
4.2.1
4.2.2
4.2.3
4.2.4
4.3
4.3.1
4.3.2
4.4
4.4.1
4.4.2
4.5
4.5.1
4.5.2
4.5.3
4.5.4
4.5.5
4.5.6
4.5.7
4.5.8
4.5.9
4.5.10
4.5.11
4.5.12
4.5.13
4.5.14
4.5.15
4.6
4.6.1
4.6.2
4.6.3
4.6.4
4.6.5
4.6.6
4.6.7
4.6.8
4.6.9
4.6.10
4.6.11
4.6.12
4.6.13
4.6.14
4.6.15
4.6.16
4.6.17
4.6.18
4.6.19
4.7
4.7.1
4.7.2
4.7.3
4.7.4
4.8
4.8.1
4.9
4.9.1
Contents
Arc
Suppressors
.
Drive
.
Drive
Motor
.
Drive
Motor
Belt
Adjustments
.
Backspace
Mechanism
Service
Check
.
Backspace
Mechanism
Adjustment
Friction
Drive
Friction
Drive
Service
Check
Friction
Drive
Torque
Adjustment
Escapement
Unit
Escapement
Unit
Service
Check
Escapement
Unit
Adjustments.
Card
Feed
Hopper
Adjustments
Feed
Clutch
Adjustment
Card
Feed
Latch
Magnet
Adjustments
Hopper-to-Prepunch
Bed
Service
Checks
.
Pressure
Rail
Adjustments
.
Card
Guide
Adjustments
Card
Registration
Service
Check
Pusher
Arm
Adjustment
Card
Stop
Cam
Adjustment
Pressure
Roll
Service
Check
Pressure
Roll
Adjustments
.
Registration
Adjustments
Feed
Wheel
Removal
and
Replacement
Card
Feed
Circuit
Breaker
Service
Check
.
Card
Feed
Circuit
Breaker
Adjustment
Punch
Drive
. .
Index
Pointer
Adjustment
.
Interposer
Magnet
Adjustment
Guide
Comb
and
Bumper
Adjustment
Punch
Interposer
Magnet
Assembly
Adjustment
Interposer
Bail
Contact
Assembly
Adjustment
Punch
Drive
Removal
and
Replacement
.
Clutch
Magnet
Adjustment.
Punch
Clutch
Service
Check
Punch
Clutch
Adjustments
.
.
High-Speed
CB
Assembly
Service
Check
.
High-Speed
CB
Assembly
Adjustment
High-Speed
Cam
Removal
.
Die
and
Stripper
Service
Check
Die
and
Stripper
Adjustment
Die
and
Stripper
Removal
and
Replacement
(With
Print
Feature)
.
Die
and
Stripper
Removal
and
Replacement
|
(Without
Print
Feature)
.
Punch
Penetration
Adjustments
Punch
Removal
and
Replacement
.
Pin
Bail
Drive
Link
Adjustment
Pin-Sense
Unit
Pin-Sensing
Unit
Service
Checks
Pin-Sensing
Unit
Adjustments
.
Pin-Sensing
Unit
Removal
and
Replacement
.
Sensing
Pin
Removal
Eject
Unit
.
Eject
Unit
Adjustments.
Stacker
Unit
.
.
Stacker
Unit
Adjustments
.
4-1
4-1
4-1
4-1
4-1
4-1
4-1
4-1
4-2
4-2
4-2
4-4
4-4
4-4
4-4
4-5
4-5
4-6
4-7
4-7
4-7
4-7
4-7
4-7
4-8
4-9
4-9
4-9
4-9
4-9
4-9
4-10
4-11
4-11
4-12
4-12
4-13
4-14
4-14
4-14
4-14
4-14
4-14
4-14
4-15
4-15
4-16
4-16
4-16
4-17
4-18
4-18
4-18
4-18
4-18
4-18
lit

4.10
Program
Drum
Unit
.
4.10.1
Sensing
Assembly
Service
Check
4.10.2
Sensing
Assembly
Adjustments
.
4.10.3
Sensing
Assembly
Removal
and
Replacement
4.10.4
Program
Cam
Contacts
Service
Check
4.10.5
Program
Cam
Contacts
Adjustment
4.10.6
Program
Drum
Interlock
Arm
(Split
Hub)
Adjustment
4.11
Print
Unit
.
4.11.1
Print
Assembly
Service
Checks.
4.11.2
Print
Assembly
Adjustments
.
4.11.3
Print
Assembly
Removal
and
Replacement
4.11.4
Ribbon
Feed
Pawl
Adjustment
4.11.5
Print
Drive
Adjustment
.
4.11.6
Print
Suppress
Magnet
Adjustment
4.12
Keyboard
.
.
4.12.1
Contact
Adjustments
4.12.2
Hook
Support
Bar
Adjustment
4.12.3
Permutation
Bar
Adjustment
4.12.4
Restoring
Magnet
Adjustment
.
Illustrations
Figure
Title
Chapter
1.
Reference
Data
and
Service
Aids
1-1
Characteristics
1-2
Operations
1-3.
Sequence
of
Operations
1-4
Diagnostic
Flowchart
Symbols
1-5
Start
and
Run
Failures
.
1-6
Card
Transport
Failures
1-7
Interposer
Selection
Failures
1-8
Escapement
Failures
(Part
1
of
2).
1-8
|Escapement
Failures
(Part
2
of
2).
1-9
Punch
Drive
Cycle
Failures
1-10
Print
Control
Failures
1-11
Test
Probe
1-12
Reed
Relay
Insertion
Chapter
2.
Console
and
Maintenance
Facilities
2-1
Program
Card
-
Model
A
2-2
Program
Card
—
Model
B
Chapter
3.
Preventive
Maintenance
3-1
Preventive
Maintenance
Routines
.
3-2.
~=Lubrication
—
Right
Front
.
3-3.
~Lubrication
—
Front
3-4
Lubrication
—
Front
(Machine
Bed
Tilted)
3-5
Lubrication
—
Rear
.
3-6
Punch
Unit
Lubrication
3-7
Keyboard
Lubrication
.
Chapter
4.
Checks,
Adjustments,
and
Removals
4-1
Friction
Drive
Adjustment
.
4-2
Escapement
Adjustment
(Part
1
of
2)
4-2.
Escapement
Adjustment
(Part
2
of
2)
4-3.
Hopper
Adjustment.
iV
4-20
4-20
4-20
4-22
4-22
4-22
4-22
4-22
4-22
4-29
4-33
4-36
4-36
4-36
4-37
4-37
4-38
4-38
4-38
Page
1-1
1-1
1-2
1-2
1-3
1-4
1-5
1-6
1-7
1-8
1-9
1-10
.
1-10
2-2
2-2
3-3
3-4
3-5
3-6
3-7
3-8
4-1
4-2
4-4
4.12.5
Upper
Permutation
Support
Adjustment
.
4.12.6
Key
Unit
Adjustment
4.12.7
Key
Unit
Removals
.
Section
2.
Features.
Chapter
5.
Power
Supplies
Section
1.
Basic
Unit
Section
2.
Features.
Chapter
6.
Locations
6.1
Keystem
Numbering
6.2
Reed-Relay
Card
6.2.1
Reed
Relays
.
6.3
Wire-Contact
Relays
6.4
Standard
Modular
System
(SMS)
.
6.4.1
SMS
Card
Receptacles
. .
6.4.2
SMS
Locations
and
Pin
Numbering
6.5
Location
Figures
Index
Figure
Title
4-4
CF
Clutch
Magnet
Adjustment
4-5
CF
Clutch
Adjustment
.
.
4-6
CF
Latch
Magnet
Adjustment
.
4-7
Pressure
Rail
Adjustment
4-8
Pressure Rail
—
Card-Lever
Contact
4-9
Card
Guide
—
Detail
Station
4-10
Card
Guide
—
Master
Station
4-11
Detail
Card
Registration
4-12
Pressure
Roll
Adjustment
. .
4-13
Master
Station
Registration
Adjustment
.
4-14
Armature
Pivot
Adjustment
.
4-15
Armature
Pivot
Adjustment
—
Side
View
4-16
Armature
Adjustment
.
4-17
Interposer
Unlatching
Clearance
4-18
Interposer
Relatching
Adjustment
4-19
Armature
Unlatching
Clearance
4-20
Interposer
Bail
Contact
Adjustment
4-21
Interposer
Bail
Contact
Rise
Adjustment
4-22
Print
Drive
Unit
Cam
Timing
4-23
Punch
Clutch
Magnet
4-24
Punch
Clutch
Components
.
4-25
Punch
Clutch
Adjustment
.
4-26
High-Speed
Circuit
Breaker
4-27
Punch
Bed
—
Front
View
4-28
Punch
and
Extension
4-29
Punch
Penetration
Adjustment
4-30
Sensing
Pin
Contact
Adjustment
4-31
Pin
Sensing
Adjustment
4-32
Stacker
Timing
4-33
Stacker
Adjustment
.
4-34
Traveling
Card
Guide
4-35
Timing
Tool
.
4-36
Program
Unit
Timing
Chart
4-39
4-39
4-40
4-41
5-1
5-1
d-1
6-1
6-1
6-1
6-2
6-3
6-3
6-3
6-3
6-5
Page
4-5
4-5
4-5
4-6
4-6
4-6
4-6
4-7
4-8
4-8
4-9
4-9
4-10
4-10
4-10
4-11
4-11
4-11
4-12
4-12
4-13
4-13
4-14
4-15
4-15
4-16
4-17
4-17
4-18
4-19.
4-19
4-20
4-21

Figure
4-37
Title
Method
of
Holding
Escapement
Wheel
4-38
Program
Cam
Contact
Adjustment
4-39
Overlay
for
Figure
4-40.
4-40
Code
Plate
Chart
E‘L’
4-41
Print
Interposer
Assembly
.
.
4-42
Punch
Drive
and
Yoke
Adjustments
.
4-43
Printing
Adjustment
4-44
Print
Interposer
Assembly
.
4-45
Vertical
Drive
Rod
Assembly
.
4-46
Character
Patterns
E‘L’.
4-47 Character
Patterns
E‘A’.
4-48
Test
Patterns.
4-49
Print
Drive
Unit
.
4-50
Print
Head
Removal.
4-51
Print
Wire
Replacement
4-52
Print
Suppression
Magnet
Adjustment
4-53
Keyboard
Adjustment
.
4-54
Keyboard
Permutation
Unit
—
Rear
4-55
Keyboard
Permutation
Unit
—
Bottom
A
ampere
alpha
alphabetic
AMP
amphenol
pin
auto
automatic
CB
circuit
breaker
CE
customer
engineer
CEM
Customer
Engineering
Memorandum
CF
card
feed
chat
character
ckt
circuit
col,
cols
column,
columns
ctrl
control
dc
direct
current
def
definition
dup
duplicate
FC
friction
clutch
HSS
high-speed
skip
Hz
Hertz
(cycles
per
second)
Page
4-21
4-23
4-25
4-27
4-29
4-29
4-30
4-30
4-31
4-32
4-33
4-34
4-34
4-35
4-36
4-36
4-37
4-38
4-39
Figure
Title
Page
4-56
Keyboard
Key
Unit
and
Permutation
Unit
4-40
4-57
Keyboard
Interlock
Disks
.
4-41
Chapter
5.
Power
Supplies
5-1
Power
Supply
.
5-1
5-2
Power
and
Receptacle
Requirements
.
5-2
Chapter
6.
Locations
6-1
Combination
and
Numeric
Keystem
Numbering
6-1
6-2
Locations
—
Relay
Board and
Relays
.
6-2
6-3.
SMS
Printed
Wiring
Cards
. .
6-3
6-4
Wire-Contact
Relay
Machine
Relay
Gate
-
—
Card
Side
View
.
6-4
6-5
Locations
—
Front
View
.
6-5
6-6
Locations
—
Rear
View
(Reed-
Relay
Machine)
.
6-5
6-7
Locations
—
Rear
View
(Wire-Contact
Relay
Machine)
6-6
6-8
Locations
—
Rear
6-6
6-9
Locations
—
Front
6-7
Abbreviations
IBC
interposer
bail
contact
intlk
interlock
LZ
left
zero
max
maximum
ms
millisecond
MULT
PCH
multipunch
NC
normally
closed
NO
normally
open
No.
number
num
numeric
PCC
program
cam
contact
PM
preventive
maintenance
prem
program
sec
second
SMS
Standard
Modular
System
Vv
volt

Safety
Procedures
Safety
cannot
be
overemphasized.
To
ensure
personal
safety
and
the
safety
of
co-workers,
each
CE
should
make
it
an
everyday
practice
to
observe
safety
precautions
at
all
times.
All
CEs
should
be
familiar
with
the
general
safety
parctices
and
procedures
for
performing
artificial
respira-
tion
that
are
outlined
in
CE
Safety
Practices,
Form
229-1264.
For
convenience,
the
-1
printing
of
this
form
has
been
reproduced.
Always
use
a
reliable
voltmeter
to
verify
that
power
is
actually
off
after
using
power-off
switches.
Although
all
power
supplies
are
provided
with
bleeder
resistors
to
drain
off
capacitor
charges
when
power
is
dropped,
it
is
wise
to
check
all
capacitors
with
a
meter
before
attempting
maintenance.
A
defective
bleeder
resistor
could
create
an
unexpected
hazard.
Anyone
working
near
electrical
circuits
may
accidentally
come
in
contact
with
live
voltage.
Round
off
sharp
edges
on
plastic
guides;
replace
broken
guides.
Check
that
all
applicable
safety
devices
are
on
the
machine.
Check
all
safety
devices
for
proper
operation.
Do
not
permit
machines
to
be run
unattended
with
covers
open
or
removed.
Leave
the
escapement
gearing
cover
in
place
at
all
times
when
the
machine
is
running.
Turn
off
power
when
tilting
the
base.
Use
only
IBM
approved
products.
Read
the
labels.
As
a
general
rule,
cleaning
fluids
should
be
used
only
in
an
open
area.
Breathing
the
concentrated
vapors,
even
for
a
short
time,
may
cause
immediate
reactions.
Review
Customer
Engineering
Memorandums
(CEMs)
for
current
safety
practices.
b.
Rings,
wrist
watches,
chains,
bracelets,
metal
cuff
links,
shall
not
be
worn.
CE
SAFETY
PRACTICES
2
All
Customer
Engineers
are
expected
to
take
every
safety
pre-
caution
possible
and
observe
the
following
safety
practices
13
while
maintaining
IBM
equipment:
1.
You
should
not
work
alone
under
hazardous
conditions
or
14,
around
equipment
with
dangerous
voltage.
Always
advise
your
manager
if
you
MUST
work
alone.
15.
2.
Remove
all
power
AC
and
DC
when
removing
or
assem-
bling
major
components,
working
in
immediate
area
of
16.
power
supplies,
performing mechanical
inspection
of
power
supplies
and
installing
changes
in
machine
circuitry.
17
3.
Wall
box
power
switch
when
turned
off
should
be
locked
or
tagged
in
off
position.
‘Do
not
Operate”
tags,
form
18.
229-1266,
affixed
when
applicable.
Pull
power
supply
cord
whenever
possible.
4.
When
it
is
absolutely
necessary
to
work
on
equipment
hav-
19.
ing
exposed
operating
mechanical
parts
or
exposed
live
electrical
circuitry
anywhere
in
the
machine,
the
following
precautions
must
be
followed:
20.
a.
Another
person
familiar
with
power
off
controls
must
be
in
immediate
vicinity.
21.
-
Each
Customer
Engineer
is
responsible
to
be
certain
that
no
action
on
his
part
renders
product
unsafe
or
exposes
hazards
to
customer
personnel.
.
Place
removed
machine
covers
in
a
safe
out-of-the-way
place
where
no
one
can
trip
over
them.
All
machine
covers
must
be
in
place
before
machine
is
re-
turned
to
customer.
Always
place
CE
tool
kit
away
from
walk
areas
where
no
One
can
trip over
it
(i.e.,
under
desk
or
table).
Avoid
touching
mechanical
moving
parts
(i.e.,
when
lubri-
cating,
checking
for
play,
etc.).
.
When
using
stroboscope
—do
not
touch
ANYTHING
—
it
may
be
moving.
Avoid
wearing
loose
clothing
that
may
be
caught
in
machin-
ery.
Shirt
sleeves
must
be
left
buttoned
or
rolled
above
the
elbow.
Ties
must
be
tucked
in
shirt
or
have
a
tie
clasp
(preferably
nonconductive)
approximately
3
inches
from
end.
Tie
chains
are
not
recommended.
Before
starting
equipment,
make
certain
fellow
CE’s
and
customer
personnel
are
not
in
a
hazardous
position.
Maintain
good
housekeeping
in
area
of
machines
while
per-
forming
and
after
completing
maintenance.
c.
Only
insulated
pliers
and
screwdrivers
shall
be
used.
d.
Keep
one
hand
in
pocket.
e.
When
using
test
instruments
be
certain
controls
are
set
correctly
and
proper
capacity,
insulated
probes
are
used.
f.
Avoid
contacting
ground
potential
(metal
floor
strips,
machine
frames,
etc.
—
use
suitable
rubber
mats
pur-
chased
locally
if
necessary).
5.
Safety
Glasses
must
be
worn
when:
a.
Using
a
hammer
to
drive
pins,
riveting,
staking,
ete.
b.
Power
hand
drilling,
reaming,
grinding,
ete.
c.
Using
spring
hooks,
attaching
springs.
d.
Soldering,
wire
cutting,
removing
steel
bands.
e.
Parts
cleaning,
using
solvents,
sprays,
cleaners,
chemicals,
etc.
f.
All
other
conditions
that
may
be
hazardous
to
your
eyes.
REMEMBER,
THEY
ARE
YOUR
EYES.
Rescue
Breathing
for
Adults
ro
+
ke
~
a
5 c
Do
c
22.
==>
$3
2
>
<£
=:
ees
2o
#240
.
o-
BD
*
c
EO
CO
5
=
” 2
-
S >
=
of
=
£
oa
o
G
Zc
>
-
@ 9
>
_
2
_2
OS
5
D =
o
~
-—
OD)
=
x
c
i.
Es
°5
5
8°
tte
=
—E-
c
2
>
££
G
f€35,35.¢t
~
>
¢F
aoe
gf
E238
o
>
“
£
oe
o:8~
et
Fe
F°QEevE
ss
=
-
a
Me
2X
2S
wd
Oe
G25
3~
x
SB
s
¢*=
>
~
3D
“23.4836
Cf
Sone
=
9
£00
he
”
c
~e
£
275
°C
eR
ma
S
FS
c
ol
7G
5
©
®&
&
>
O
EE
ow
o
“cg
Su
CL
595+
He
32
=
E
noe
ood
3
>
°
s
cc
ar
=
Sie
Hat
2
2
&
Sin
ol
=F
oO
v
ov
Yo
Ee
2c
g%
£
oa
a
Scottzread
GH
YMA
OF
a.
ULF
Boa
om
ere
SF
SBA
eK
OD
h
ED
.
. .
. .
.
. .
Cc
-
ano
F
WO
KR
me
6.
Special
safety
instructions
such
as
handling
Cathode
Ray
Tubes
and
extreme
high
voltages,
must
be
followed
as
outlined
in
CEM’s
and
Safety
Section
of
the
Maintenance
Manuals.
7.
Do
not use
solvents,
chemicals,
greases
or
oils
that
have
a
not
been
approved
by
IBM.
z
8.
Avoid
using
tools
or
test
equipment
that
have
not
been
5
°
approved
by
IBM.
=
&
9.
Replace
worn
or
broken
tools
and
test
equipment.
co
10.
Lift
by
standing
or
pushing
up
with
stronger
leg
muscles
—
2
2
this
takes
strain
off
back
muscles.
Do
not
lift
any
equip-
v
2
ment
or
parts
weighing
over
60
pounds.
aw
O
11.
All
safety
devices
such
as
guards,
shields,
signs,
ground
S
Vv
wires,
etc.
shall
be
restored
after
maintenance.
S
<
KNOWING
SAFETY
RULES
1S
NOT
ENOUGH
=
2
AN
UNSAFE
ACT
WILL
INEVITABLY
LEAD
TO
AN
ACCIDENT
gz
O
USE
GOOD
JUDGMENT
—
ELIMINATE
UNSAFE
ACTS
229-1264-1
1.
Start
Immediately,
Seconds
Count
»y
ER
p-
=
the
oO
—
7
wo
Sok
22
>
0
-
5
=o
®
oO.
£E
a.
>
~ =
£
£
ot
ue
oe
te
~F
TC
>
2
G
a
w
|
E
Oo
Cos
o o
=
no
80
2
~-
2
nn
$<
4
n>
VD
ov
SSE
ow
=
oo
=
—
5
=
@
-
2.
eesck
2
Foe
gt
§
83
<
So°SsG
RP
oF
5»
Be
8
22
>
=o
a5
gor
ve
E
os
2
Endo
22.2
act
£
-
3
‘3
eH3s7°
OG
o
©
Gc
>
£
”
G
O€
c
le
m5
§
20
°
~
2?
.
og
>
es
-
=
5
as
ms
>'S
an
©
2--
TU
£5
oF
fgB
“PFET
EOE
SS
©
o2Ea
=
>
ww
o>
Eos
te
ore
‘a6
2
5%
5%
~
oo
0
=
Sue
FSP
a
Be
“
a
=
LO
Tf@yjes
+
eo
>
cf}
Cc
.
we
=
»
SB
oY
—
Oa
=
2,
©
5
°
o
?
>
oc
Uut
£
>
o
O27
5
6
Cr>om,
EFEvte272%
or
csi.
ES
fj
2
Et
Y
o:r#
ED
o o o a
—
+
o
c
2
@
Ox
E®X®
omtmowee
ze
oc
c
nw
c
os
5
sHVGo0dEL
ot
Gcstvoov’
=
Ofte
Fle
fares
sed
Pour
sauss
g
a
oi
~
«ww
os
vi

Section
1.
Reference
Data
Figure
1-1
shows
machine
characteristics
for
the
IBM
29
Card
Punch.
1.1
OPERATIONS
The
29
Card
Punch
operations
may
be
divided,
as
shown
in
Figure
1-2,
for
troubleshooting.
These
operations
are:
1.
Start
and
Run:
Establishment
of
power
(electrical
and
mechanical)
necessary
for
machine
operations.
This
includes
the
operation
of
the
card
feed
and
the
pick-and-hold
of
the
card
lever
relay.
2.
Interposer
Selection:
Engagement
of an
interposer
or
interposers
with
the
punch
bail
in
preparation
for
punching.
3.
Escapement:
Advancement
of
the
program
drum
and
of
the
escapement-driven
feed
wheels.
Characteristics
Description
Speed:
Without
Print
With
Print
Manual
punching
20
col/sec
18
col/sec
Manual
duplication
10
col/sec
9
col/sec
Automatic
duplication
20
col/sec
18
col/sec
Skipping
80
col/sec
Releasing
80
col/sec
Feed
from
pre-register
to
detail
0.250
sec
station
Hopper
500
cards
Stacker
500
cards
Figure
1-1.
Characteristics
A
Start
and
Run
Card
Lever
Relay
a]
EI
5
Interposer
Escapement
Punch
Drive
Selection
Unit
Cycles
4]
Card
Transport
Figure
1-2.
Operations
Chapter
1.
Reference
Data
and
Service
Aids
4.
Card
Transport:
Mechanical
control
of
the
movement
of
the
card
through
the
machine.
5.
Punch
Drive
Cycle:
Controlled
rotation
of
the
punch
drive
unit
index
shaft.
According
to
the
function,
this
is
required
to
punch
a
hole
in
the
card
at
the
punch
station
or
to
read
a
hole
in
the
card
at
the
pin-sense
station.
1.2
SEQUENCE
OF
OPERATIONS
It
is
essential
that
the
customer
engineer
be
aware
of
the
correct
sequence
of
operations
as
they
are
used
in
any
machine
function.
1.2.1
Functions
When
the
function
is
to
punch
a
character
from
the
keyboard,
the
sequence
of
operations
is:
Start
and
run
Interposer
selection
Escapement
Card
transport
Punch
drive
cycle
Using
the
numbers
only,
the
sequence
is:
1
2
3-4
5
Showing
escapement
and
card
transport
(3-4)
side
by
side
indicates
that
while
3
causes
4,
they
occur
at
the
same
time.
Using
this
notation,
the
sequence
of
these
operations
for
all
of
the
functions
of
the
29
Card
Punch
is
shown
in
Figure
1-3.
The
functions
shown
in
Figure
1-3
are
the
responses
of
the
machine
to
the
inputs
shown
here:
wPWN
SD
Key
Punch
Press
any
character.
Multiple
Punch
Press
the
multiple
punch
key
and
any
numeric
key.
Key
Skip
Press
the
skip
key
in
numeric
or
alpha-
betic
shift.
Press
the duplicate
key
for
one
or
more
columns
with
no
programming.
Manual
Duplicate
Blank
Column
Manual
Duplicate
Press
the
duplicate
key
for
one
or
more
blank
columns
with
no
programming
and
with
the
machine
in
alphabetic
shift.
Pressing
the
duplicate
key
or
the
reading
of
a “0”
in
the
program
card
in
a
column
followed
by
“12’s”
in
the
program
card.
Auto
Duplicate
Blank
Column
Auto
Duplicate
Same
as
“Auto
Duplicate”
but
for
blank
columns
with
the
machine
in
alpha-
betic
shift.
Skip:
Release,
Auto,
Press
release
key
if
starwheels
are
up
or
Drum
if
they
are
down
in
a
column
pro-
grammed
“12”.
An
“11”
in
a
program
card.
Card-to-card
skip.
Release,
Auto
Space
Press
release
key
in
a
nonprogrammed
field
but
with
the
starwheels
down.
29FEMM
(4/69)
1-1

Blank Blank
|Skip:
Column
ColumnjRelease,|
Release
Key
Mult
Skip
|Manual|/Manual]
Auto
|Auto
|Auto,
|Auto
Function|
Punch
Punch
Key
Dup
Dup Dup
|Dup
{Drum
|Space
First
Col
1
3
15
4
4-5
3
1 1
1
1
1
1
-2|
5
5-2
5
3=4
3-4
3-4
3
-4
3-4
3-4
3-4
5
5
5
5
5
nob
ND wm
QtnNn-=
Second
Repeat
|
2-5
3-4
Repeat
Repeat}
3-4
3-4
Repeat
|
Repeat
and
for
All
Repeat
Repeat}
forAll
forAIl
5-2
5-2
for
All
for
All
Other
Cols
for
All|
for
Cols
{Cols
Repeat
|Repeat|
Cols
Cols
Cols
Cycles
Field
for
for
Def
Field
Field
Def Def
3-4
5
Last
Col
Figure
1-3.
Sequence
of
Operations
Section
2.
Diagnostic
Techniques
1.3
INITIAL
APPROACH
The
first
step
in
troubleshooting
is
to
reduce
the
possible
trouble
sources
to
one
of
the
five
operations.
Locate
the
operation
that
breaks
the
correct
sequence
for
the
failing
function.
The
second
step
is
to
vary
the
machine
function
to
one
in
which
the
failing
operation
occurs
in
another
sequence.
This
tests
the
same
operation
with
a
different
input.
For
example,
interposer
selection
is
faulty
during
keypunching
(2,
34,
5).
Varying
the
function
to
manual
duplication
(5-2,
3-4,
5)
allows
interposer
selection
from
the
pin-sense
input
instead
of
the
key
input.
The
cause
of
the
failure,
if
in
a
particular
input
path,can
be
discovered
in
this
way.
If
the
same
operation
fails,
regardless
of
the
input
path
used,
the
failure
is
common
to
all
paths.
Enough
information
may
be
gained
in this
way
to
find
the
cause
of
the
failure
by
using
the
wiring
diagram
and
the
test
probe.
For
those
troubles
that
cannot
be
found
by
using
this
approach,
refer
to
the
appropriate
section
in
Chapter
4.
Diagnosis
of
the
complete
failure
of
all
machine
opera-
tions
should
be
preceded
by
a
continuity
check
of
the
fuses.
If
attempted
punching
fails
to
occur
after
a
card
has
been
registered
at
the
punch
station,
the
card
lever
relay
should
be
checked
first.
Consistent
blowing
of
fuses
indicates
a
short
or
a
ground
on
the
machine.
Line
terminals
and/or
cam
contacts
can
be
checked,
one
at
a
time,
to
locate
this
type
of
failure.
Some
common
possible
sources
of
grounds
are
the
starwheel
contact
and
the
latch
magnet
contact.
1.4
DIAGNOSTIC
FLOWCHARTS
Figure
1-4
defines
the
symbols
used
in
the
diagnostic
flowcharts
(Figures
1-5
through
1-10).
These
flowcharts
aid
in
locating
the
trouble
area
when
diagnosing
fairly
consist-
ent
failures.
1-2
(4/69)
Trouble
approach
action
Error
indication
decision
Direction
comment)
Figure
1-4.
Diagnostic
Flowchart
Symbols
1.4.1
Start
and
Run
Failures
To
locate
start
and
run
failures
(Figure
1-5),
the
starwheels
must
be
raised
and
blank
cards
must
be
used.
1.4.2
Card
Transport
Failures
Diagnosis
of
the
failure
causing
incorrect
card
movement
should
include
an
initial
visual
check
to
confirm
that
the
components
of
the
card
transport
mechanisms
are
oper-
ating.
When
card
transport
failure
occurs,
any
mark
or
nick
on
the
card
will
help
to
indicate
the
source
of
trouble
(Figure
1-6).
A
change
in
registration
during
the
duplication
of
one
punched
card
can be
a
false
indication
of
card
transport
failure.
If
the
escapement
moves
while
the
sensing
pins
are
still
up
through
the
holes
in
the
card,
the
card
will
be
retarded.
The
sensing
pins
usually
leave
marks
on
the
card.
(See
1.4.4.)
Improperly
inserting
cards
into
the
pin-sense
station
can
cause
trouble.
The
card
to
be
duplicated
should
not
be
forced
into
the
pin-sense
station
before
registering
the
card.
1.4.3
Interposer
Selection
Failures
Interposer
selection
may
be
incorrect
from
either
the
keyboard
or
pin-sense
units,
or
both.
If
either
unit
operates
correctly,
the
circuits
and
components
of
the
other
unit
must
be
considered
as
a
source
of
the
trouble.
If
both
units
fail,
the
trouble
is
assumed
to
be
in
the
interposer
magnets
and
associated
circuitry
or
in
the
interposer
mechanism
(Figure
1-7).
Note
that
when
the
interposers
have
been
tripped
for
any
reason,
they
must
be
restored
by
a
drive-unit
cycle.
To
avoid
confusion
in
diagnosis,
the
starwheels
must
be
raised
to
locate
interposer
selection
failures.
1.4.4
Escapement
Failures
Faulty
escapement
is
defined
as:
escaping
too
far,
not
far
enough,
not
at
all,
or
at
the
wrong
time.
Program
control
is
used
with
Figure
1-8
to
locate
escapement
failures.
The
program
card
should
be
punched
for
alternate
three-column
duplications
and
two-column

Slowly
or
overheats
Set
mainline
and
motor
switches
to
ON
Motor
|
Check
motor
start
relay
Check
motor
Card
is
not
fed
to
pre-register
station
Check
card
L_
clack
|
—
par
eerannAO
Check
CF
clutch
cao
Check
CF
magnet
circuit
|
[cheek
card
feed
=
[chest
card
lever
cow)
No
trouble
found,
go
to
card
transport
flowchart
(Figure
1-6)
Check
CF
latch
mechanism
|
Check
CF
4
magnet
circuit
Check
card
feed
mechanism
No
trouble
found,
go
to
card
transport
flowchart
(Figure
1-6)
Does
not
register
Figure
1-5.
Start
and
Run
Failures
No
Yes
Release
and
feed
card
es
a
and
program
drum
ro-
Yes
Register
the
card
and
space
out
Drum
does
not
go
to
column
1
ike
No
spacing
or
punch
drive
cycles
Check
mainline
voltage
Check
mainline
fuses
|
|
Check
motor
start
relay
|
Check
motor
|
Check
punch
clutch
|
operation
Check
de
voltages
|
Check
release
relay
|
Check
skip
relay
|
Check
skip
or
escape
|
circuits
|
|
Check
program
cam
|
contact
|
|
severed
No
trouble
found,
go
to
escapement
flow-
chart
(Figure
1-8)
|
Check
card
lever
relay
contacts
Check
card
lever
contoct
Check
card
lever
relay
pick-and-hold
circuits
No
trouble
found,
go
to
escapement
flowchart
(Figure
1-8)
if
no
spacing,
or
go
to
punch
drive
cycles
flowchart
(Figure
1-9)
if
no
punch
drive
cycles
29
FEMM
(4/69)
1-3

Does
not
leave
hopper
Check
hopper
pressure
plate
|Check
hopper
adjustments
Check
feed
knives
|
|
Check
cards
Check
card
pusher
mechanism
Check
punch
pressure
roll
opening
Check
for
obstruction
in
punch
throat
Hesitates
or
buckles
Check
punch
pressure
roll
for
alignment
Check
upper
rail
card
L
guide
alignment
I<
heck
pin-sense
pressure
r
oll
en
Check
pin-sense
card
<=
for
et
Check
1
roll
or
arm
tension
|
ese
pin-sense
throat
|
Feed
card
from
rereer
Card
movement
satisfactory
Crooked
at
pre-register
station
[Check
hopper
cdjsrment|
Check
feed
knives
Hesitates
or
buckles
Check
pin-sense
pressure
roll
Check
1
card
guide
Check
cards
Check
eject
guide
an
feed
pressure
lls
|
Register
card
|
Check
card
L
Crooked
Registers
Check
operation
of
aligner
fingers
card
|
Check
condition
of
card
Check
traveling
card
(bent,
curled,
etc.)
guide
|
|
|
Check
card
pusher
|
mechanism
L
Check
punch
pressure
Check
eject
roll
or
roll
opening
Offset
Check
eject
guide
arm
tension
J
Does
not
slide
along
upper
rail
Check
punch
pressure
roll
for
alignment
Check
punch
pressure
rails
Releases
Intermittent
Dup
cards,
Measure
distance
between
cards
at
various
columns
Register
card
at
pin-sense
station
Distance
varies
Registers
at
pin~sense
station
Goes
beyond
Check
pin-sense
pressure
rol]
=
Check
—
stop
plate
and
—
Check
—_
arm
tension
Repeat
test
Figure
1-6.
Card
Transport
Failures
1-4
(4/69)
|
Release
card
Releases
|
Stack
card
Stacks
Stacks
correctly
No
Manually
operate
card
feed
and
observe
stacking
mechanism
Does
not
slide
along
upper
rail
Check
pin-sense
pressure
roll
Check
pressure
rail
alignment
Check
traveling
card
guide
No
or
crooked
Check
traveling
card
guide
Check
eject
guide
|
Check
a
roll
or
arm
tension
Check
stacker
cams
|
4

Operate
numeric
and
alphabetic
character
keys
Check
interposer
relatch
Check
keyboard
restore
Check
keyboard
contacts
for
short
circuit
Extra
interposers
or
repeat
punch
cycles
Interposers
No
selected
Yes
Duplicate
space,9...12
Extra
interposers
on
dup
Interposers
No
ONES
Check
interposer
relatch
E
heck
pin-sense
contact
|
Check
common
bar
Check
throat plates
and
card
registration
Key
Check
interposer
magnet
mechanism
Check
interposer
Check
keyboard
shift
ckt
Check
for
magnet
impulse.
If
no
pulse,
proceed
to
key
or
dup
branch
Dup
|
Check
keyboard
contacts
|
Check
restore
circuit
|
Figure
1-7.
Interposer
Selection
Failures
[check
pin-sense
contacts
|
|
Check
sensing pin
|
Check
card
registration
29FEMM
(4/69)
1-5

A.
Alphabetic
Duplicate
With
auto
skip/dup
switch
off,
key
dup
alphabetic
and
blank
columns
Completes
duplicate
field
Yes
C
Perform
B
and
C
+
Extra
column
or
at
wrong
time
Escapement
Check
dup key
contact
Check
12
program
contact
and
circuit
|
t
|
Check
escapemen
|
Check
dup
relay
sep
|
interlock
relay
|
Check
escape
circuit
|
Check
P1
cam
contact
No
trouble
found,
go
to B
No
trouble
found,
go
to
interposer
selection
flowchart
(Figure
1-7)
B.
Numeric
Duplicate
and
Skip
Operate
numeric
keys,
auto
dup
all
12
digits,
and
alternate
skip
|
Check
12
program
co
prsnanaceretieseiray
1
Check
dup
relays
ve
ntact
cemeenenrenrentnel
Check
4
circuits
No
—-
found,
to B
*)
Too
far
Card
goes
Escapement
off
registration
Yes
(nicked
or
torn
holes)
Check
escapement
interlock
relay
L
7
Check
0
program
el
duration
|
Check
PI
timing
and
|
Check
P1
cam
contoct
|
|
—
Check
auto
Le
|
switch
Check
-
clutch
Check
that
punch
interposer
is
Check
r
relay
—
aa
escape
interlock
relay
|
|
engaging
bail
Check
setup
of
IBC
|
Check
escape
circuit
|
No
trouble
found,
go
to
interposer
selection
flowchart
(Figure
1-7)
No
trouble
found,
go
to
interposer
selection
flowchart
(Figure
1-7)
Completes
dup
field
rT.
diel
Check
12
program
contact
r
Check
dup
relays
|
Check
dup
circuit
p=
ait.
a
“~<
Perform
A
and
C
Figure
1-8.
Escapement
Failures
(Part
1
of
2)
1-6
(4/69)

C.
Key
Punch
Operate
any
alphabetic
key
or
skip
key
Too
far
No
|
Escapement
Check
FC
torque
So
C
Perform
A
and
B
+
Check
armature
adjustment
Check
drive
gear
train
|
No
trouble
found,
analyze
original
failing
condition
Figure
1-8.
Escapement
(Part
2
of
2)
skips
through
column
38.
This
is
followed
by
a
25-column
skip
(ending
in
column
63),
an
11-column
alphabetic
duplication, a
5-column
skip,
and
duplication
of
column
80.
1.4.5
Punch
Drive
Cycle
Failures
Locate
punch
drive
cycle
failures
with
the
starwheels
raised
(Figure
1-9).
Diagnosis
of
clutch
failures
should
include
an
initial
manual
cycle
of
the
punch
drive
unit.
Incorrect
clutch
overthrow
or
a
defective
detent
can
be
found
while
performing
this
operation.
1.4.6
Printing
Control
Failures
The
program
card
used
for
locating
escapement
failures
can
be
used
for
locating
programmed
printing
failures.
Diagnos-
tic
flowchart
is
Figure
1-10.
1.5
MACHINE
SERVICE
FEATURES
The
29
Card
Punch
has
two
diagnostic
features
that
have
been
incorporated
to
aid
the
customer
engineer.
These
are:
Motor
switch
Test
probe
1.5.1
Motor
Switch
The
motor
switch
turns
the
motor
off
and
allows
other
areas
of
the
machine
to
remain
energized.
It
is
useful
when
manually
cycling
the
machine.
Some
adjustments
are
made
with
the
motor
stopped.
1.5.2
Test
Probe
The
test
probe
(Figure
1-11)
contains
a
neon
indicator
in
series
with
a
resistor.
One
lead
of
the
indicator
is
connected
Check
FC
torque
or
escape
magnet
Check
escape
mechanism
|
Check
Pl
cam
contact
|
to
the
power
supply.
The
other
lead
is
used
to
trace
circuits
leading
to
coils
or
magnets.
A
jack
is
provided
on
the
power
supply
chassis.
CAUTION
Care
must
be
used
when
probing
relay
points
because
the
point
of
the
probe
might
spread
the
pin
connectors
and
cause
the
reed
switch
to
make
poor
contact
or
break
the
pin.
Be
careful
in
the
use
of
the
test
probe;
an
accidental
short
could
tack
several
relay
points.
The
probe
should
not be
used
to
estimate
circuit
voltages.
Use
the
meter
for
voltage
measurements.
Reed
relays
should
be
probed
through
the
top
of
the
bobbin
because
the
vertical
rows
of
holes
on
the
land
pattern
for
a
particular relay
position
do
not,
in
all
cases,
connect
to
the
relay
connector.
Note:
When
probing
P3,
a
false
indication
may
occur;
P3
appears
not
to
make.
This
is
due
to
the
timing
relationship
between
the
short
duration
of
P3
(7
ms)
and
the
60-Hz
negative
line
pulse
used
to
bias
the
probe.
1.6
SERVICING
TECHNIQUES
1.6.1
Forcing
Extra
pressure
can
be
applied
to
various
components
to
simulate
malfunction.
For
example,
the
friction
drive
can
be
forced
or
retarded
manually
at
the
top
of
the
program
drum,
or
finger
pressure
can
be
applied
to
the
escape
magnet
armature
to
help
or
hinder
its
operation.
Magnetism
of
the
escape
magnet
can
be
detected,
and
its
strength
estimated
with
any
lightweight
steel
blade
(screwdriver
or
burnishing
tool).
|
29FEMM
(4/69)
1-7

multipunch
fail
Perform
escape-punch
first
cycle dup,
and
All
operations
1
Check
clutch
mechanism
|
t
Proceed
to
appropriate
routine
to
diagnose
fault
Check
clutch
circuits
Escape
Punch]
___[Meltipunch
Press
character
key,
Watch
punch
bail
]
First
Cycle
Dup
punch
bail
Manually
duplicate
a
punched
column,
Watch
Hold
down
mutlipunch
key.
Press
combination
key and
watch
punch
bail
More
than
one
Cycles
None
More
than
two
More
than
one
per
key
|
Check
escapement
Check
clutch
mechanism
Check
clutch
circuits
(After
escape
cycle)
None
(After
escape
cycle)
Check
multipunch
relay
|
Check
interposer
bail
|
contact
Check
escape
intlk
Check
clutch
nechonten
|
L
|
Check
multipunch
circuit
Check
clutch
mechanism
|
Check
escape
intlk
relay
|
—
Check
dup
relay
setting
Check
clutch
circuits
|
check
clutch
mechanism
|
Check
clutch
circuits
|
I
I
1
Check
clutch
circuit
L
!
Check
clutch
circuit
|
PO
Lay
Lg
Le
Check
escape
==
No
trouble
found,
go
to
interposer
selection
flowchart
(Figure
1-7)
Figure
1-9.
Punch
Drive
Cycle
1.6.2
Interrupting
Machine
Operation
The
sequence
of
machine
operation
can
be
interrupted
and
controlled
by
removing
a
lead
from
the
controlling
mag-
nets.
For
example,
a
lead
can
be
removed
from
the
escape
magnet
or
from
the
punch
clutch
magnet.
Operation
can
then
be
controlled
by
retouching
the
lead
long
enough
for
one
operation
to
occur.
CAUTION
The
machine
should
not
be
left
static
in
the
middle
of
an
operating
sequence
for
a
long
period
of
time.
The
source
of
undesired
operations
can
often
be
located
by
removing
leads
along
the
undesired
circuit
until
the
source
is
found.
This
should
not
be
done
in
reed-relay
circuits
with
power
on.
1-8
(4/69)
1.6.3
Jumpering
Portions
of
circuitry
suspected
of
being
open
can
be
jumpered
to
determine
whether
they
are
open.
It
is
also
useful
to
jumper
the
desired
voltage
into
a
circuit,
to
determine
how
much
of
the
circuit
operates
correctly.
Circuit
Card
Tab
Connections:
Individual
wires
are
easily
removed
from
the
connectors
to
facilitate
circuit
diagnosis
or
component
isolation.
To
remove
wires
from
Amphenol
connectors,
use
AMP*
disconnect
tool
(part
452815).
1.6.4
Measuring
A
voltmeter
can
be
used
while
the
machine
is
static
to
measure
the
magnitude
of
a
voltage.
Manual
operation
may
*Trademark
of
Amp,
Incorporated

With
print
switch
off,
keypunch
and
dup
all
characters
|
Check
print
suppress
circuit
|
|
Check
print
switch
Check
print
suppress
mechanism
|
Check
print
drive
|
No
troubles
found,
see
4.1]
Yes
Prints
With
print
switch
on
and
starwheels
up,
keypunch
and
print
all
characters
Wrong,
smudgy,
or
too
light
Prints
No
|
Check
ribbon
Yes
|
Check
platen
Print
and
duplicate
all
Check
punch
throat
characters
under
program
for
obstruction
control
Prints
Ne
Yes
Prints
when
suppressed
Check
print
suppress
mechanism
Prints
No
Yes
——
according
to
|
Check
print
relay
|
contacts
Check
print
relay
pick
circuit
Check
print
suppress
mechanism
Check
12
program
contact!
(print
relay
hold
circuit)
Nee
Extraneous
zeros
Left
zeros
Check
print
relay
|
Check
—t
suppress
—
Check
—
suppress
circuit
Check
12
—
contact
)
Check
LZ
switch
|
Check
print
suppress
mechanism
|
!
Check
print
switch
|
Check
print
suppress
|
magnet
circuits
|
!
Check
LZ
print
switch
No
last
character
wrong
Insufficient
zeros
Figure
1-10.
Print
Control
Failures
Check
card
lever
relay
|
Check
print
suppress
mechanism
|
|
Check
LZ
print
switch
es
OL Ld
|
Check
escape
interlock
|
Check
P2
cam
contact
|
and
timing
|
Check
print
relay
29
FEMM
(4/69)
1-9

Figure
1-11.
Test
Probe
be
performed
to
determine
the
timing
of
circuit
breakers.
The
voltmeter
can
also
be
used
while
the
machine
is
operating,
to
detect the
presence
and
relative
magnitude
of
the
voltage.
1.6.5
Cycling
Manually
Turn
the
motor
switch
off.
Observe
machine
functions
while
manually
operating
the
escapement
gear
train
and
the
punch
clutch.
This
allows
voltages
to
be
checked
at
any
time
during
the
machine
cycle.
1.6.6
Interchanging
Units
Keyboards,
relay
boards,
or
relay
gates
may
be
inter-
changed
with
other
machines
of
the
same
type
and
feature
configuration.
This
can
help
isolate
suspected
units
when
diagnosing
intermittent
troubles.
1.6.6.1
Relay
Gate
The
relay
gate
in
either
type
of
machine
is
easily
remove-
able.
In
the
reed-relay
machine,
drop
the
relay
gate
out
of
the
guide
tracks
through
the
slots
provided.
In
the
wire-contact
relay
machine,
first
slide
one
tab
out
of
the
slot,
then
slide
the
other
tab
out.
1.6.6.2
Arc
Suppression
Arc
suppression
is
necessary
for
the
proper
operation
and
longevity
of
the
reed-relay
switches.
If
trouble
is
suspected
in
an
arc
suppression
network,
it
must
be
substituted
with
another.
CAUTION
Removal
of
arc
suppression
for
diagnosis
can
cause
considerable
damage
as
well
as
faulty
operation.
1-10
(4/69)
1.6.6.3
Reed
Relays
When
inserting
reed
relays
on
the
circuit
board,
care
must
be
exercised
not
to
exert
pressure
on
the
coil
portion
of
the
relay.
Pressure
exerted
on
the
coil
can
cause
the
relay
to
flex,
and
breakage
of
the
glass
reed
switch
may
occur.
To
prevent
this
breakage,
the
relay
must
be
positioned
and
pressed
on
the
card
with
equal
pressure
exerted
on
each
of
the
plastic
ends
of
the
relay
(Figure
1-12).
A
short
caused
by
a
defective
part
or
a
slip
of
the
hand
while
troubleshooting
could
damage
several
relays.
All
relays
in
the
circuit
between
the
short
and
the
line
should
be
checked
because
the
sudden
surge
of
current
could
cause
the
interceding
relay
points
to
weld
or
develop
a
tacking
condition.
Do
not
remove
or
replace
relays
during
a
machine
cycle.
If
tacking
is
suspected,
do
not
jar
the
machine
because
the
tacking
problem
may
disappear
temporarily.
Do
not
interchange
relays
or
relay
types.
If
the
relay
used does
not
have
a
hold
coil,
do
not put
one
that
has
a
hold
coil
in
its
place.
Do
not
interchange
relay
reeds,
The
individual
relay
reeds
are
matched
and
should
not
be
interchanged
by
disassembly
or
use
of
ones
from
other
relays.
Repeated
relay
insertions
and
removals
can
cause
the
glass
envelope
to
break;
Berg
connectors
may
lose
tension
and
cause
intermittent
failures.
Check
connector
alignment
with
a
0.010-inch
feeler
gage,
aligning
it
with
adjacent
con-
nector.
Figure
1-12.
Reed
Relay
Insertion
1.7
DIFFICULT-TO-ANALYZE
AND
INTERMITTENT
FAILURES
There
are
some
sources
of
trouble
in
the
29
Card
Punch
that
cause
varying
results
and
are
difficult
to
diagnose.
Among
these
are:
1.
Friction
drive
torque
(too
much,
too
little,
or
jumpy)

No
.
Punch
clutch
spring
(broken,
dry
or
gummy,
or
loss
of
tension)
.
Punch
clutch
armature
(broken
or
worn)
.
Punch
clutch
detent
pivot
stud
(worn
or
loose)
.
Punch
clutch
overthrow
(too
much
or
too
little)
.
Relays
(high
resistance
shorts
or
hold
points
burned
or
welded)
7.
High-speed
cam
contacts
(binding
roller,
strap
tension,
or
loose
contact
pile-up)
8.
Interposer
bail
contacts
(strap
tension,
air
gap,
or
contact
condition).
An
intermittently
failing
machine
should
not
be
returned
to
the
customer
without
investigating
every
suspected
cause
of
the
failure.
NON
&
W
1.7.1
Left-Zero
Feature
1.7.1.1
Left-Zero
Overflow/Iincorrect
Punchout
Incorrect
punchout
of
left-zero
information
occurs
if
the
operator
keys-in
more
digits
than
the
field
can
contain.
Reed-relay
machines
continue
shifting
the
bits
in
the
registers;
the
first
digits
keyed-in
are
lost.
Wire-contact
relay
machines
accumulate
the
overflow
of
bits
in
the
first
register.
|
Examples:
In
a
reed-relay
machine
with
a
five-position
field
programmed,
the
operator
keys-in
1,
2,
3,
4,
5, 6.
The
machine
punches
out
2,
3, 4,
5,
6
when
the
left-zero
key
is
pressed.
In
a
wire-contact
relay
machine
with
a
five-position
field
programmed,
the
operator
keys-in
1,
2,3,
4,5,
6.
The
machine
punches
3,
3,
4,
5,
6
when
the
left-zero
Key
is
pressed.
1.7.1.2
Intermittent
Loss
of
Bits
Common
causes
for
loss
of
information
during
read-in
or
read-out
operations
are:
1.
Keyboard
latch
or
bail
contact
adjustments
2.
Keyboard
restore
bail
contact
adjustment
3.
Error
reset
contact
or
backspace
switch
intermittently
breaking
contact
4.
Loose
slip-on
connectors
to
punch
interposer
magnet
unit
5.
Loose
connectors
in
0-volt
or
48-volt
net
to
LZ
relays
6.
Punch
CBs
out
of
adjustment.
1.7.2
Diagnosis
of
“Heavy”
or
Stiff
Keyboards
To
isolate
the
source
of
trouble
when
a
keyboard
feels
“heavy”
or
stiff,
make
the
following
checks.
1.7.2.1
Key
Pressure
Key
pressure
can
be
affected
by
lubrication,
by
interference
between
the
keystem
and
the
cover,
or
by
sluggish
interlock
disks.
Lubrication:
Check
to
be
sure
that
the
proper
lubricant
is
used
in
the
correct
places.
Refer
to
“Chapter
3.”
Interference:
Check
to
be
sure
that
the
keybuttons
are
centered
within
the
holes
in
the
cover
face.
Interlock
Disks:
Check
for
dirty,
magnetized,
or
oily
interlock
disks.
1.
With
the
machine
on,
press
the
P-key.
2.
Using
a
gram
gage,
operate
the
P-key;
55
to
65
grams
should
be
read.
Note
the
actual
pressure
required
to
operate
the
key.
.
Press
the
Q-key.
4.
Using
the
gram
gage,
operate
the
P-key
again.
The
pressure
required
should
not
exceed
10
grams
more
than
the
reading
noted
in
step
2.
5.
If
step
4
failed
to
meet
the
requirements
specified,
remove
the
interlock
disks.
a.
Wash
the
disks
and
the
race
in
IBM
cleaning
fluid
to
remove
all
traces
of
oil
or
dirt.
b.
Test
for
magnetism
by
sliding
the
disks
down
an
inclined
steel
surface;
replace
all
sticking
disks.
Oo
1.7.2.2
Keyboard
Cycle
Time
To
check
for
slow
keyboard
restore:
1.
Open
keyboard
base
and
place
machine
in
numeric
shift
by
inserting
a
card
between
the
numeric
keystem
contacts.
2.
Feed
a
card
to
column
1.
3.
Short
latch
contact
6
and
time
the
punching
of
80
columns.
Timing
should
be
approximately
4.5
seconds.
4.
If
the
time
exceeds
7
seconds,
repeat
the
punching
operation
with
one
thickness
of
card
inserted
between
the
keyboard
restore
magnet
armature
and
the
core.
5.
If
an
increase
in
speed
of
the
punching
operation
occurs,
adjust
the
armature-to-core
clearance
to
0.005
inch.
(No
increase
in
speed
indicates
a
slow
machine
cycle.)
Note:
Keyboard
restore
magnet
coils
are
connected
in
parallel.
A
short
or
open
in
either
coil
upsets
the
balance
of
the
circuit.
Symptoms
include
slow
keyboard
cycles,
double
punching,
or
extra
spaces.
1.7.2.3
Machine
Cycle
Time
To
check
machine
cycle
timing:
1.
Install
an
80-column
auto-dup
program
card
on
the
program
drum.
2.
With
the
machine
in
alphabetic
shift,
time
the
automatic
duplication
of
80
columns
(using
blank
cards).
Timing
should
be
4
to
4.5
seconds.
3.
If
timing
exceeds
the
limit,
slow
action
is
due
to
the
punch
clutch,
the
friction
clutch,
or
the
escapement
mechanisms.
29
FEMM
(4/69)
1-11

4.
Place
the
machine
in
numeric
shift
and
time
the
automatic
duplication
of
80
columns
(using
punched
cards).
Timing
should
be
4
to
4.5
seconds.
5.
If
timing
exceeds
the
limit,
slow
action
is
due
to
the
interposer
magnet
assembly:
a.
Excessive
magnet-to-armature
air
gap.
©
b.
Interposer
bail
contacts.
1.7.3
Stacker
The
base
should
not
be
raised
or
lowered
by
using
the
stacker
plate
as
a
handle;
relative
position
of
the
stacker
plate
to
the
stacker
assembly
may
be
changed
and
may
require
readjustment.
Improper
adjustment
of
the
traveling
card
guide
can
cause
difficulties
in
reading
the
end
portion
of
a
card.
1.7.4
Starwheel
Adjustment
The
29
Card
Punch
is
designed
so
that
the
starwheel
duration
is
about
9
ms.
One
tooth
on
the
escapement
wheel
equals
12
ms.
This
timing
is
critical
because
too
much
or
too
little
duration
could
cause
relay
points
to
arc.
This
could
be
compounded
if
the
relays
develop
a
tacking
condition.
1-12
(4/69)

Section
1.
Basic
Unit
2.1
INSTALLATION
PROCEDURES
2.1.1
Shipping
Material
1.
Visually
check
for
any
machine
damage
before
signing
the
bill
of
lading.
If
machine
is
severely
damaged,
notify
your
branch
office
before
continuing
the
installation
procedure.
2.
Using
packing/unpacking
instructions
(part
7331107),
locate
and
remove
spacers,
washers,
and
screws
on
base
rubber
mounts.
Also,
remove
the
two
screws
in
the
base
pivot
brackets
to
allow
tilting
of
the
base
for
servicing.
.
Check
for
loose
cables,
connectors,
and
components.
.
Adjust
line
cord
to
keep
excess
cord
off
the
floor.
.
For
Model
C
machines,
refer
to
Field
Engineering
Theory—Maintenance,
IBM
29
Card
Punch
Features/29
Interpreting
Card
Punch,
Model
C,
Form
223-2926.
nb
W
2.1.2
Power
1.
Compare
voltage
requirements
with
those
supplied.
Chapter
5
shows
power
and
receptacle
requirements.
2.
Turn
power
on
and
observe
the
punch
drive
for
smooth
operation.
2.1.3
Keyboard
Operations
1.
Set the
following
switches:
Starwheels
raised.
Punch/interpret
—
PUNCH
(Model
C).
Auto
skip/dup
—
OFF.
Auto
feed
—
OFF.
Print
—
OFF.
.
Left-zero
print
—
OFF.
2.
Put
cards
in
the
hopper.
3.
Press
release
key:
a.
Column
indicator
revolves
80
columns
and
returns
to
column
1.
b.
No
cards
feed
from
the
hopper.
4.
Press
register
key.
Card
feed
cycle
occurs,
but
no
cards
feed
from
the
hopper.
5.
Press
and
hold
feed
key.
Two
cards
feed
from
the
hopper.
6.
Press
A
through
Z
and
0
through
9
keys.
a.
Press
each
key
twice
to
detect
binding
keystems.
b.
Hold
numeric
key
while
keying
numbers.
7.
Release
and
register
second
card.
8.
Set
print
switch
to
on
position
and
press
all
special
character
keys.
9.
Operate
the
clear
switch.
Both
cards
should
feed
to
the
stacker.
No
cards
feed
from
the
hopper.
monooe
Chapter
2.
Console
and
Maintenance
Facilities
10.
Compare
holes
in
the
cards:
a.
Holes
in
the
cards
should
compare
with
the
keys
pressed
in
steps
6
through
8.
b.
Machine
with
print
feature
prints
special
char-
acters
in
corresponding
columns.
11.
Check
registration
by
using
a
card
gage.
2.1.4
Program
and
Function
(Model
A)
1.
Set
the
following
switches:
a.
Auto
skip/dup
—
OFF.
b.
Program
select
—
ONE.
c.
Auto
feed
—
ON.
d.
Print
—
ON.
e.
Left-zero
print
—
ON.
2.
Install
Model
A
program
card
(Figure
2-1)
on
drum,
install
drum
in
machine,
and
lower
the
starwheels.
3.
Feed
two
cards
from
the
hopper.
1.4.1
First
Card
2
1.
Press
O
through
9
keys.
2.
Press
skip
key.
The
cards
move
to
column
34.
3.
Backspace
to
column
14
to
check
that
registration
is
maintained
for
20
columns
of
backspacing.
4.
Press
dash
key.
If
machine
has
X-skip
feature,
program
drum
skips
to
column
34;
if
not,
press
skip
key
and
program
skips
to
column
34.
.
Press
all
alphabetic
character
keys
(A
through
Z).
.
Press
skip
key.
Program
drum
should
be
at
column
80.
7.
Multipunch
0
through
9
in
column
80.
Multipunch
key
must
be
pressed
and
held
while
keying-in
0
through
9.
NN
No
.1.4.2
Second
through
Fifth
Cards
poo’
.
Set
auto
skip/dup
switch
to
on
position.
2.
Set
left-zero
print
switch
to
off
position.
A
“0”
should
be
punched
but
not
printed
in
column
1.
3.
Press
dup
key.
Machine
duplicates
card
and
program
drum
skips
to
column
80.
4.
Press
space
key.
1.4.3
Sixth
Card
2
1.
Set
auto
skip/dup
switch
to
off
position.
2.
Set
program
select
switch
to
TWO.
3.
Press
program
two
key.
4,
Press
dup
key
(duplicate
to
column
11).
5.
Press
skip
key
(skip
to
column
34).
6.
Press
dup
key
(duplicate
to
column
60).
7.
Press
skip
key
(skip
to
column
78).
8.
Press
and
hold
alpha
key;
press
Z,
A,
and
Q
keys.
29FEMM
(4/69)
2-1
Other manuals for 29 CARD PUNCH -
1
Table of contents
Other IBM Computer Accessories manuals
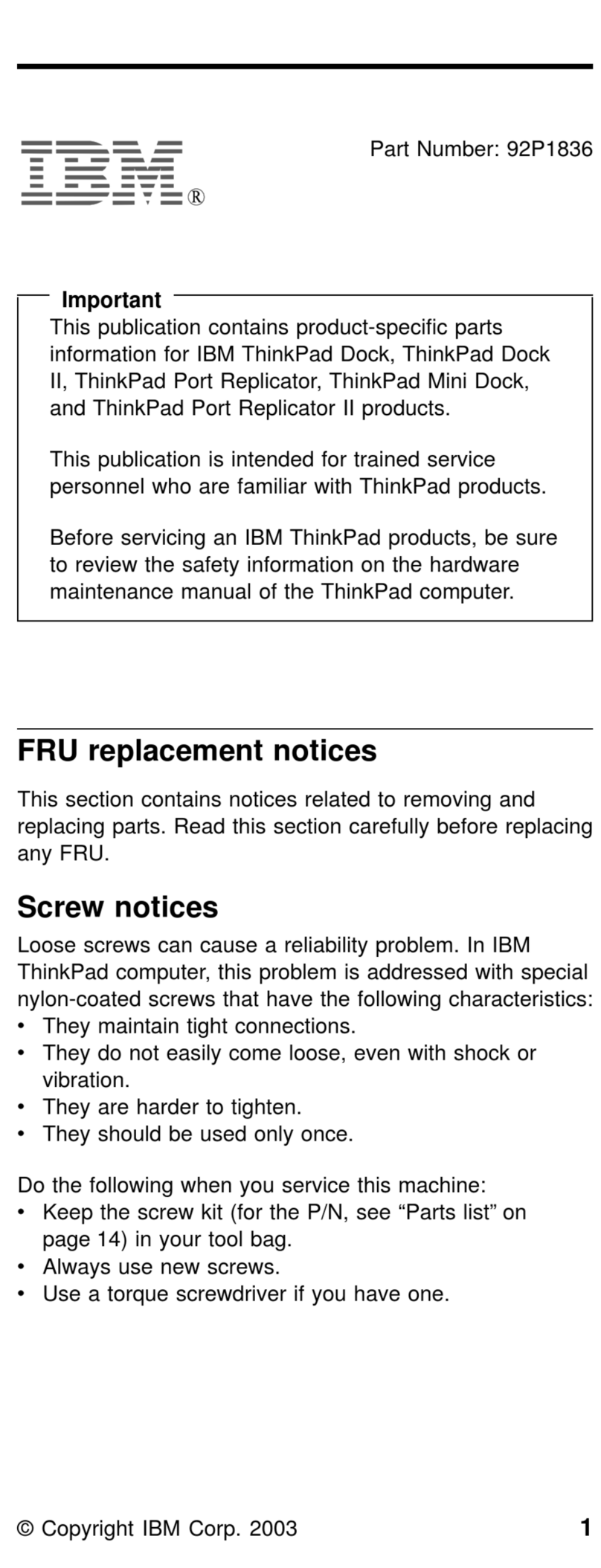
IBM
IBM THINKPAD 92P1836 User manual
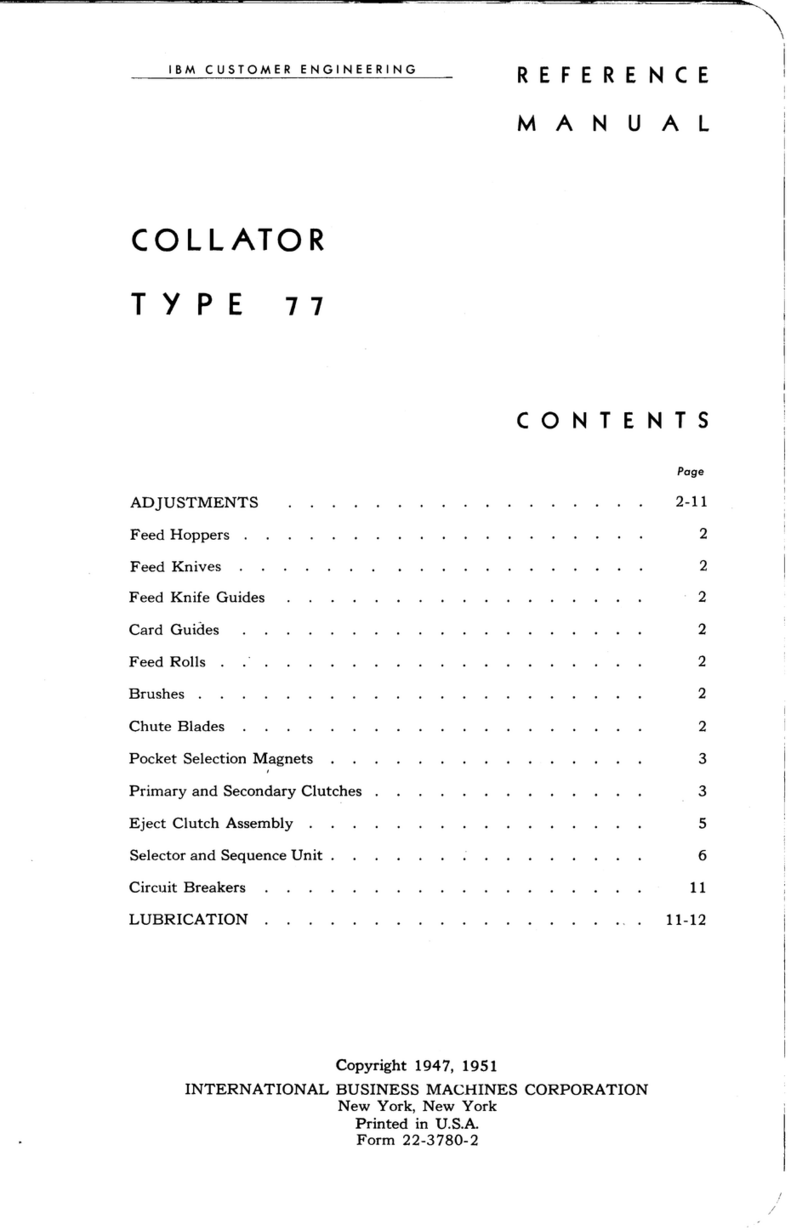
IBM
IBM 77 User manual

IBM
IBM WAVV 2004 User manual

IBM
IBM 29 CARD PUNCH - User manual
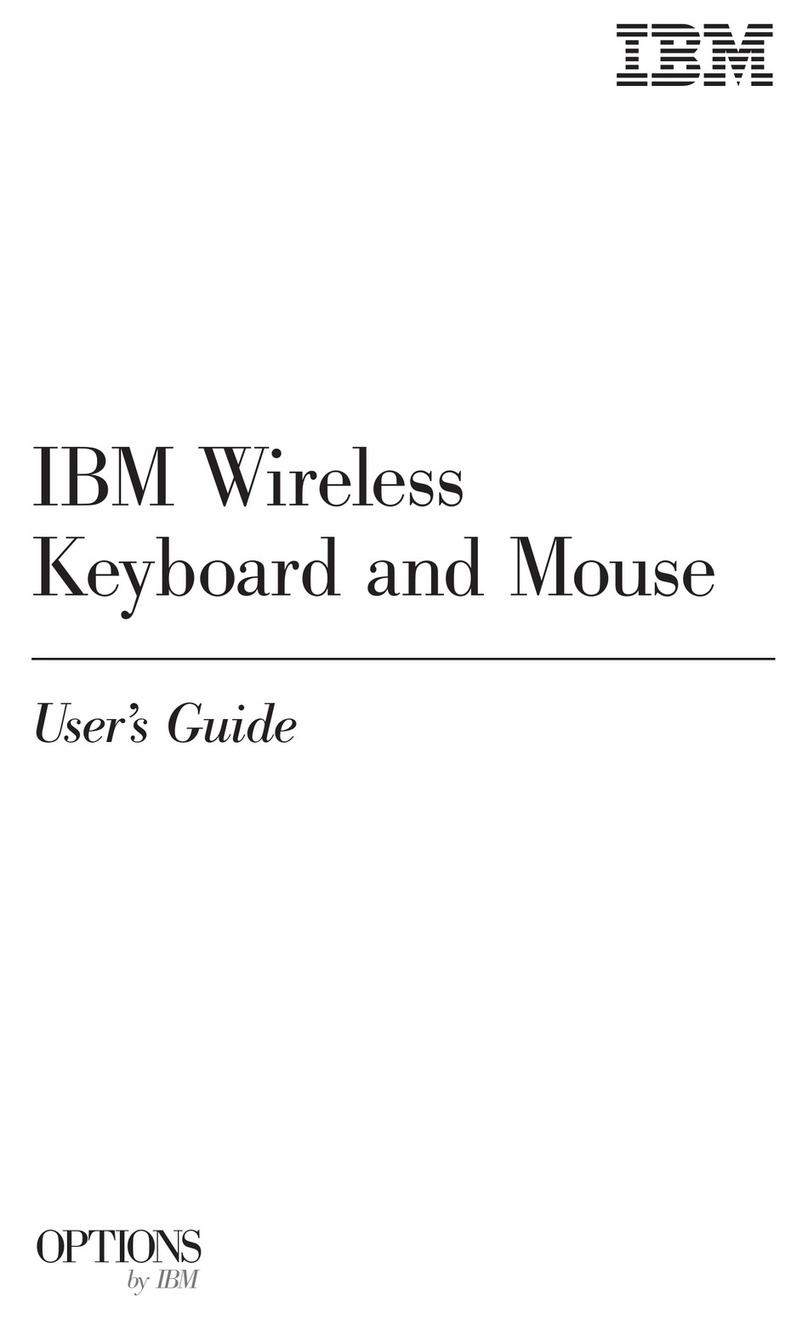
IBM
IBM Wireless Keyboard and Mouse User manual
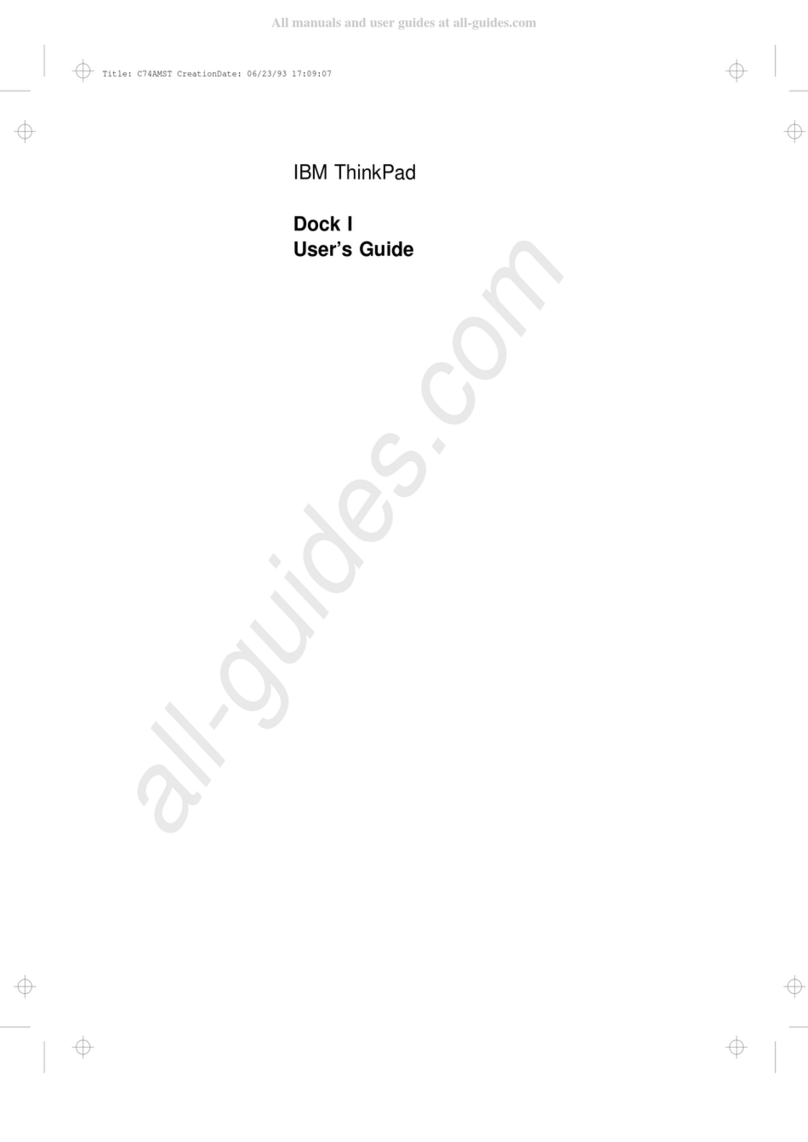
IBM
IBM ThinkPad Dock I User manual

IBM
IBM Multimedia Kit for RS/6000 Manual
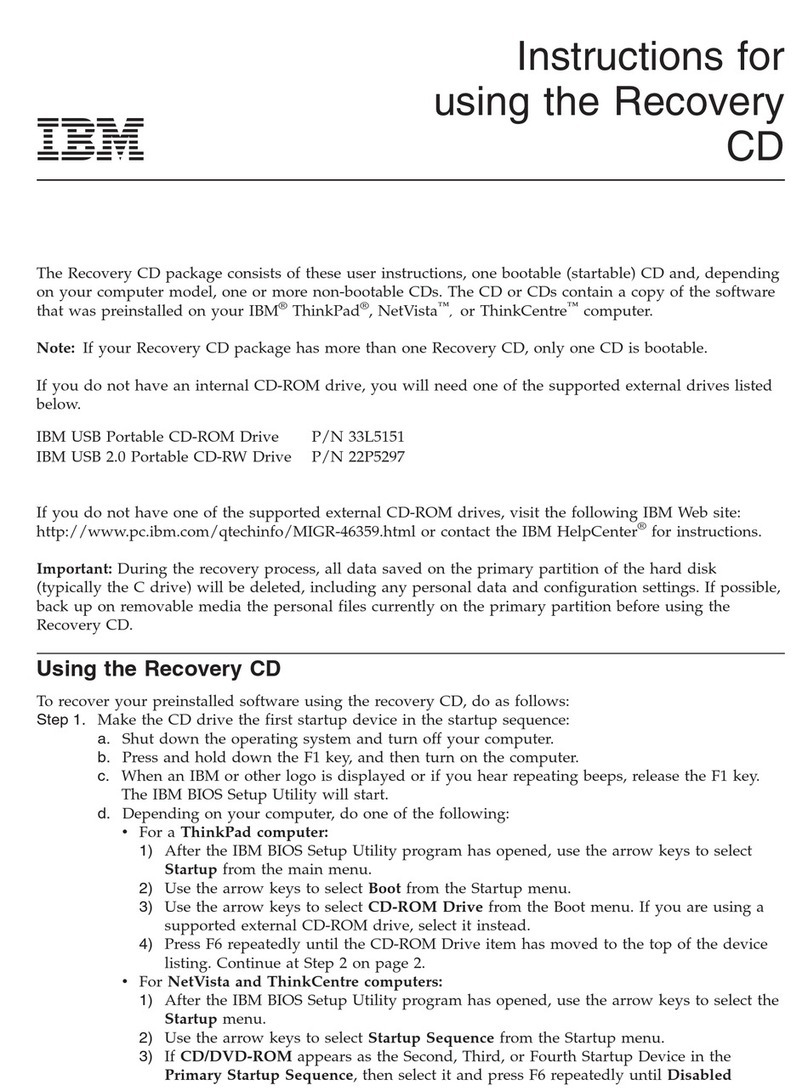
IBM
IBM THINKPAD A30 Installation and operation manual
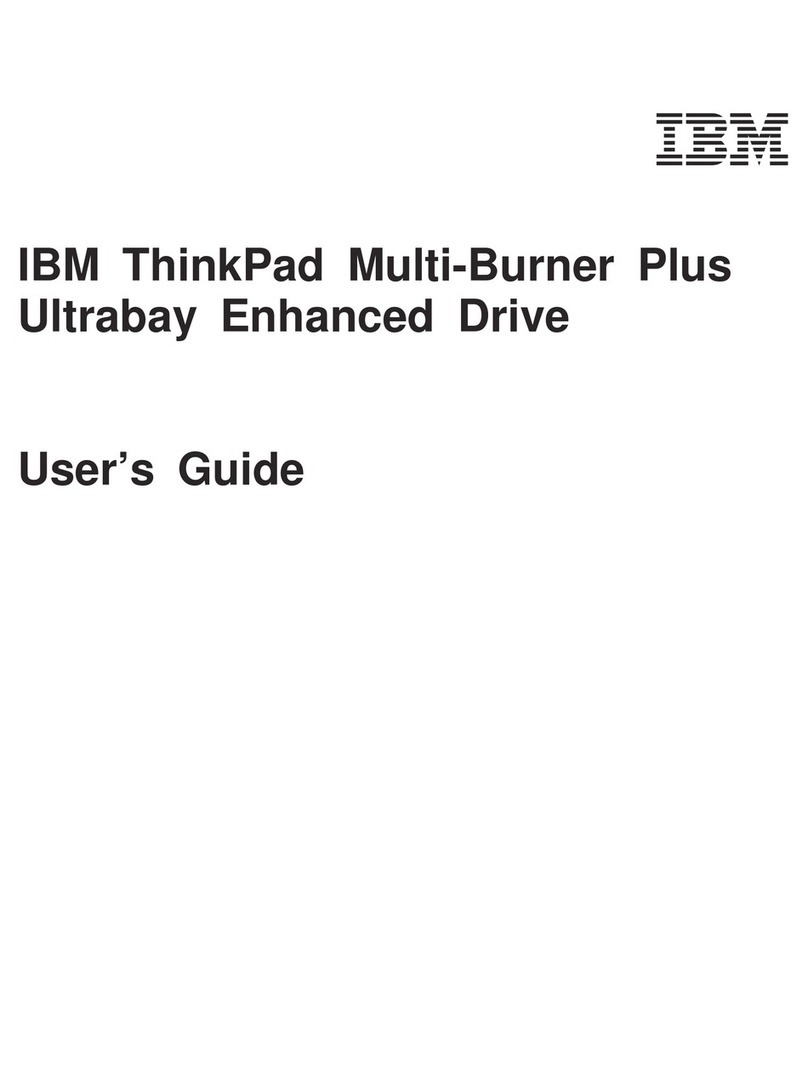
IBM
IBM IBM ThinkPad Multi-Burner PlusUltrabay Enhanced... User manual