IBM 353 User manual




















This manual suits for next models
1
Other IBM Storage manuals
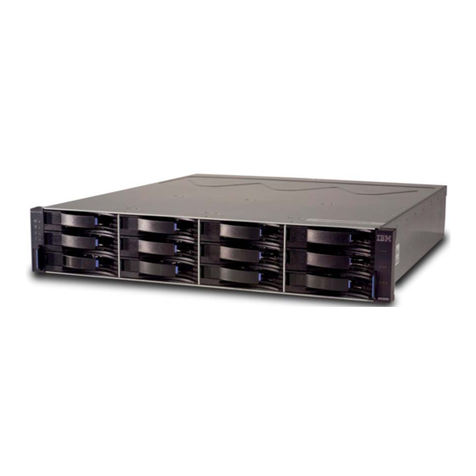
IBM
IBM System Storage DS3300 Operating instructions
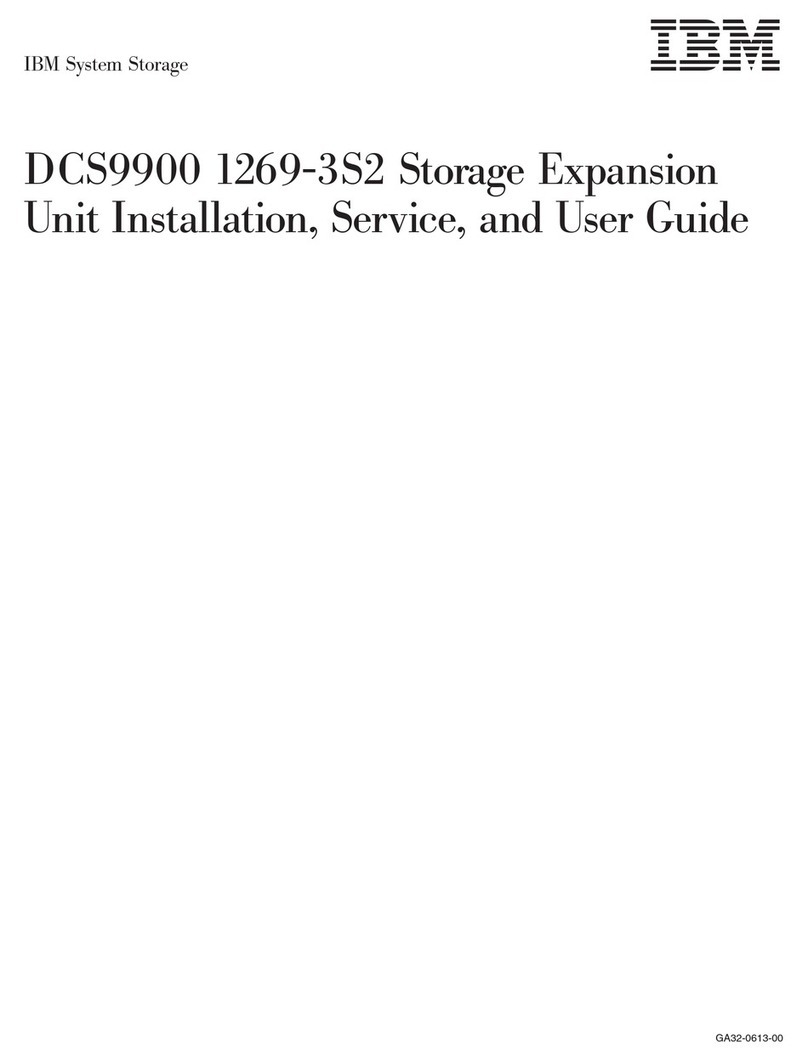
IBM
IBM 1269-3S2 Manual
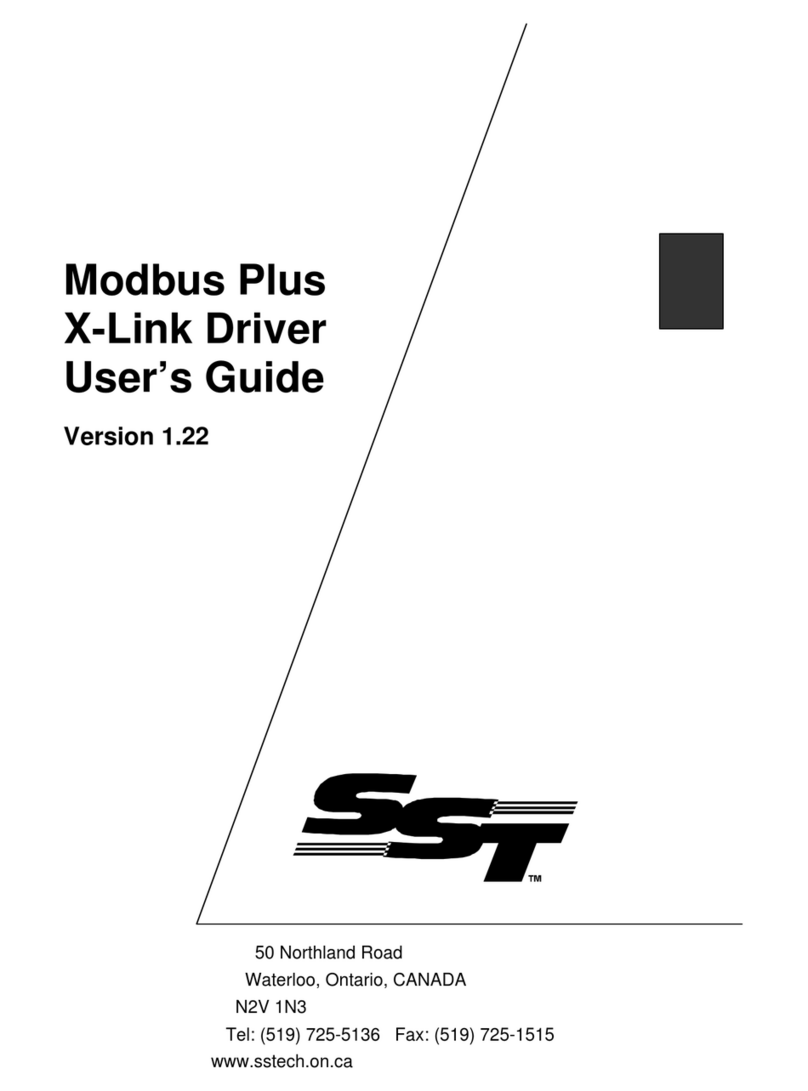
IBM
IBM Modbus Plus User manual
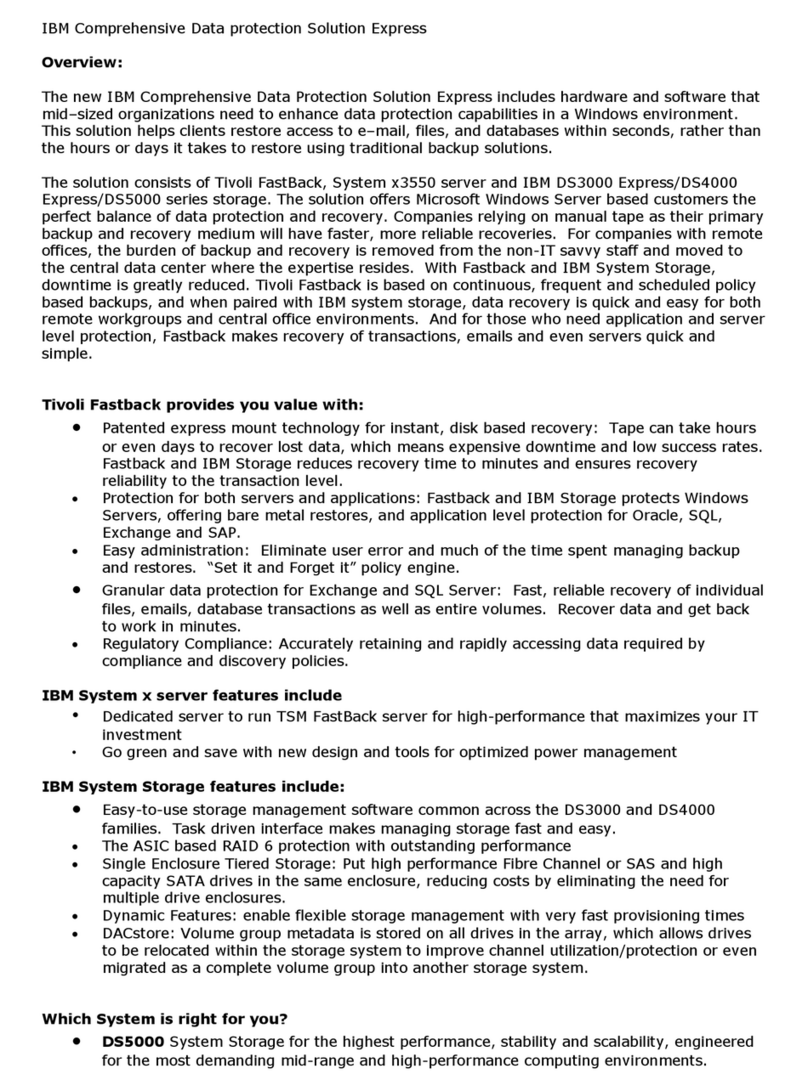
IBM
IBM System Storage DS5000 series Installation guide
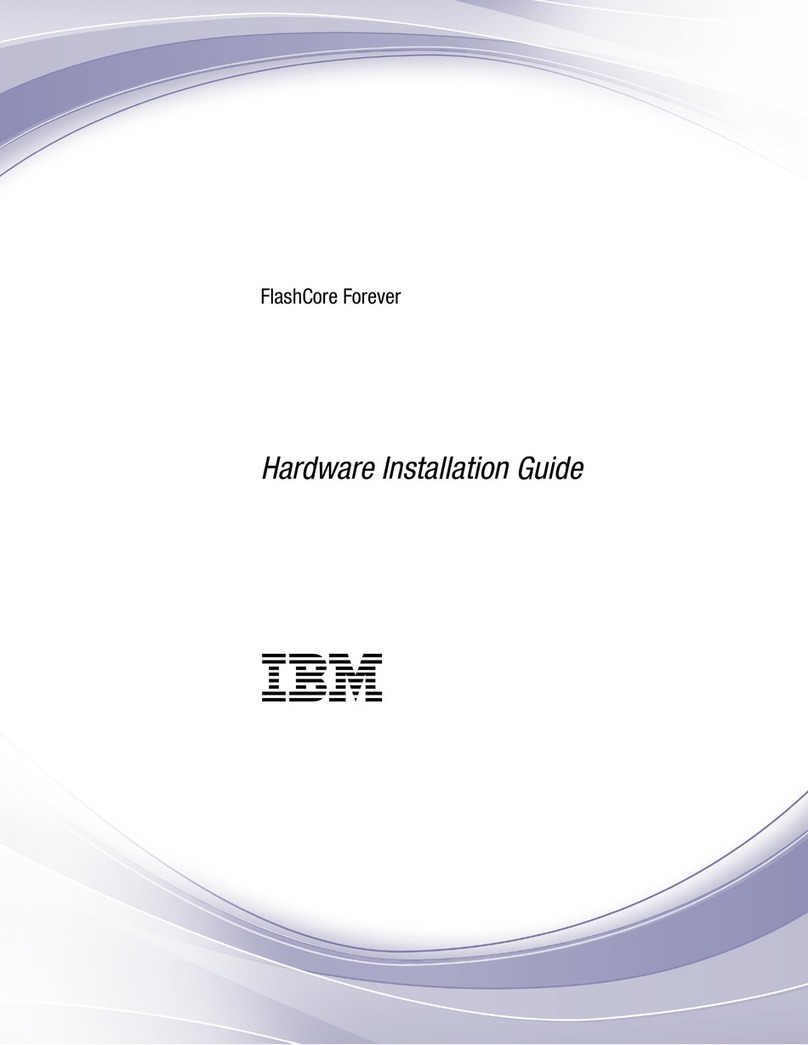
IBM
IBM FlashSystem 9150 Manual
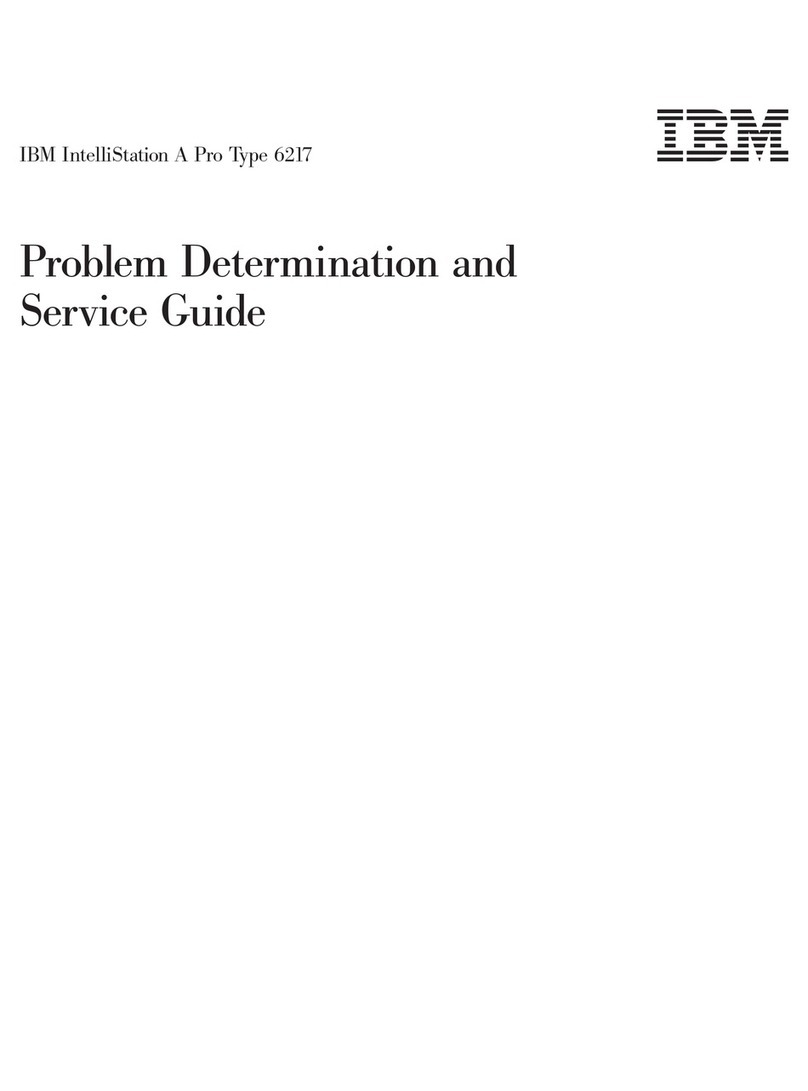
IBM
IBM IntelliStation A Pro 6217 User manual
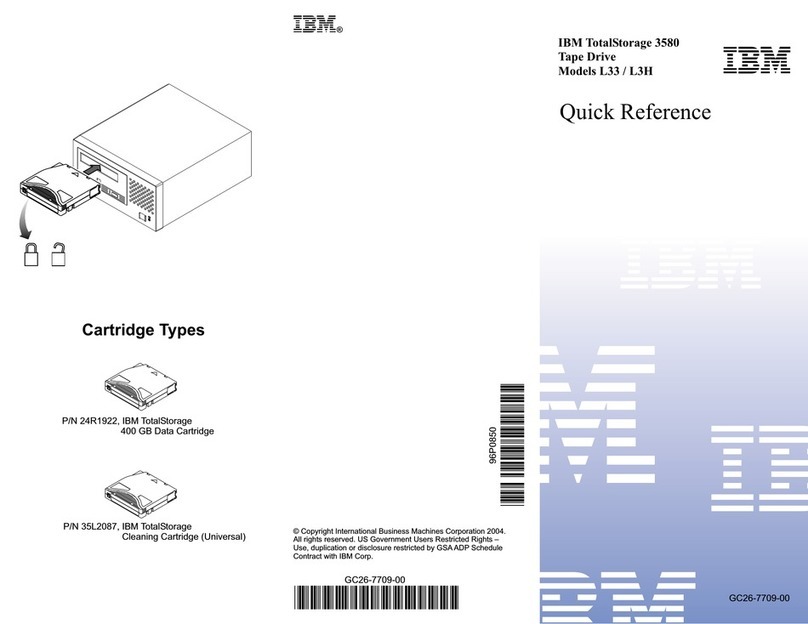
IBM
IBM TotalStorage 3580 L33 User manual
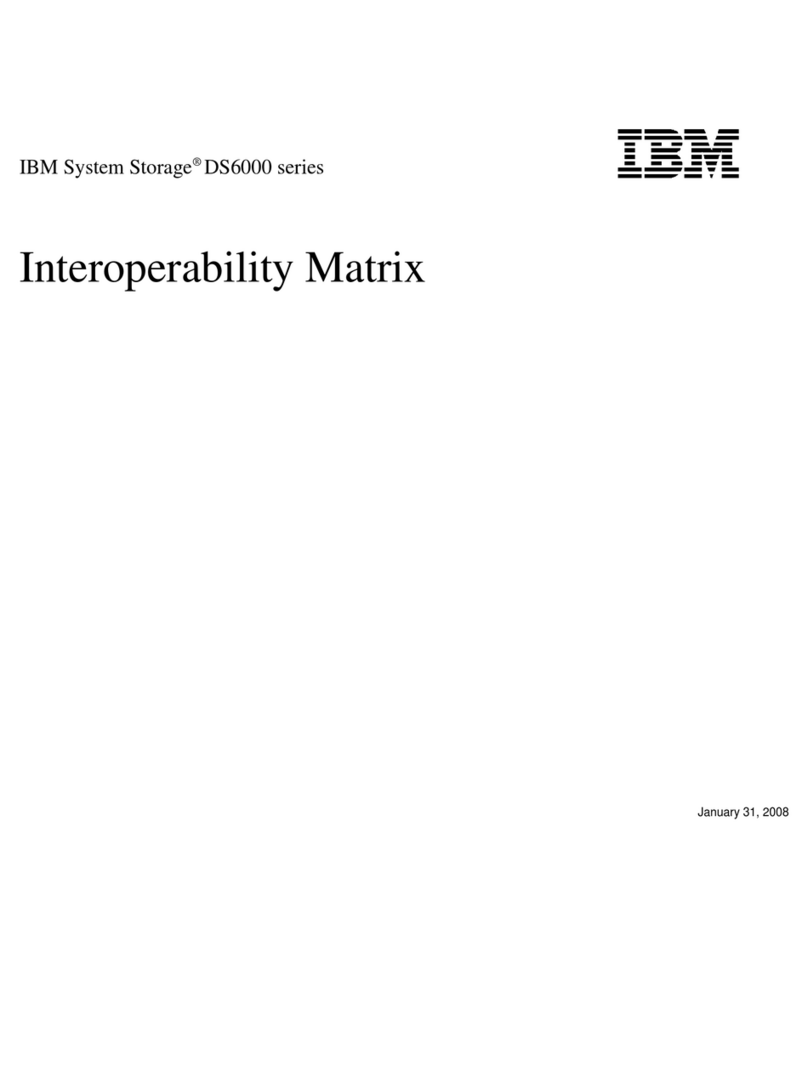
IBM
IBM System storage DS6000 Series Installation guide
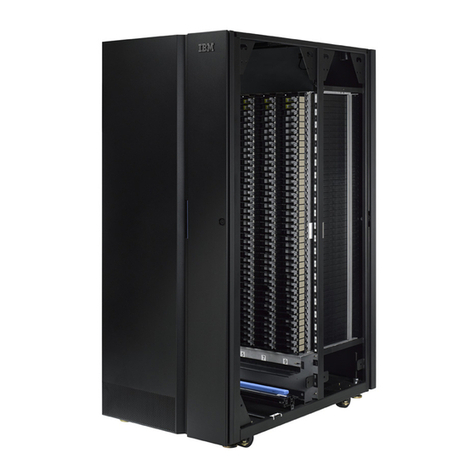
IBM
IBM System Storage TS3500 Technical manual
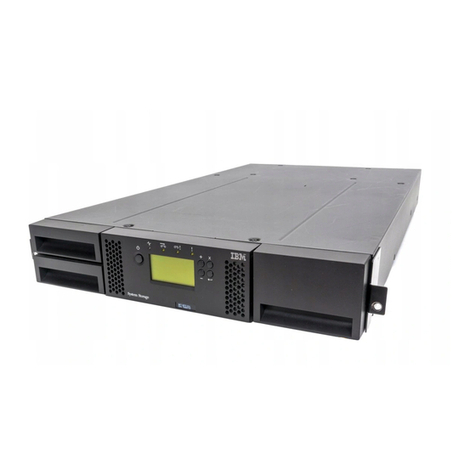
IBM
IBM System Storage TS3100 User manual
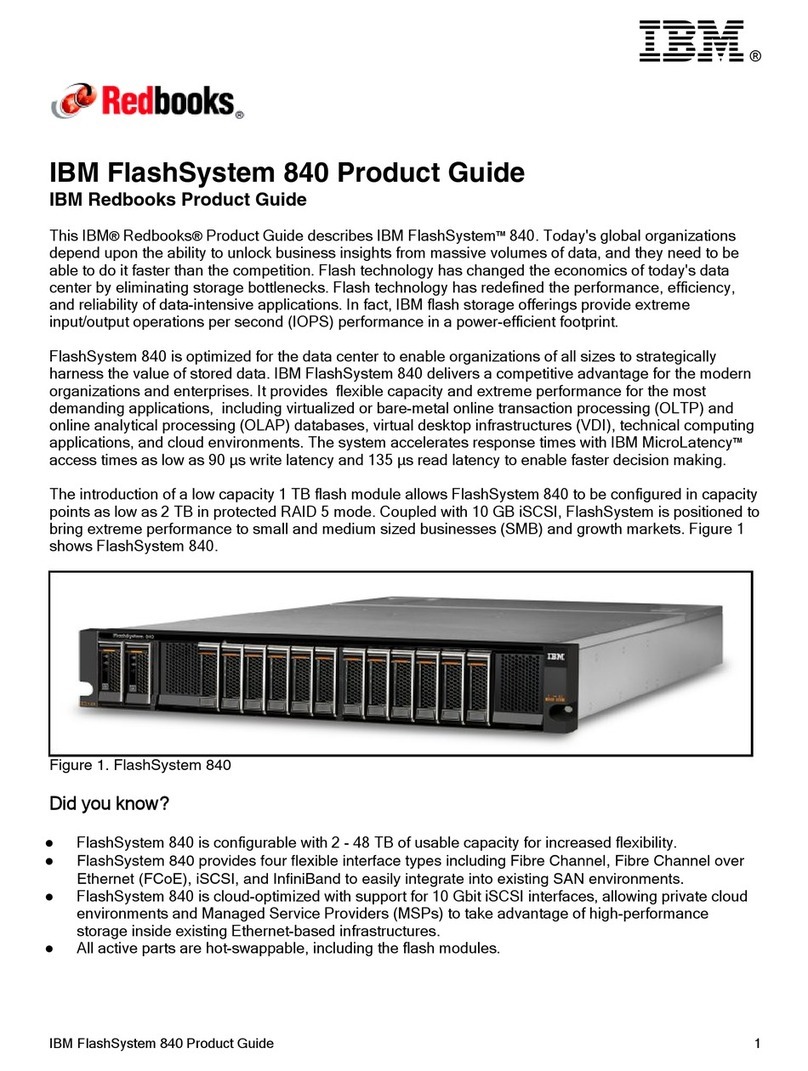
IBM
IBM FlashSystem 840 User manual
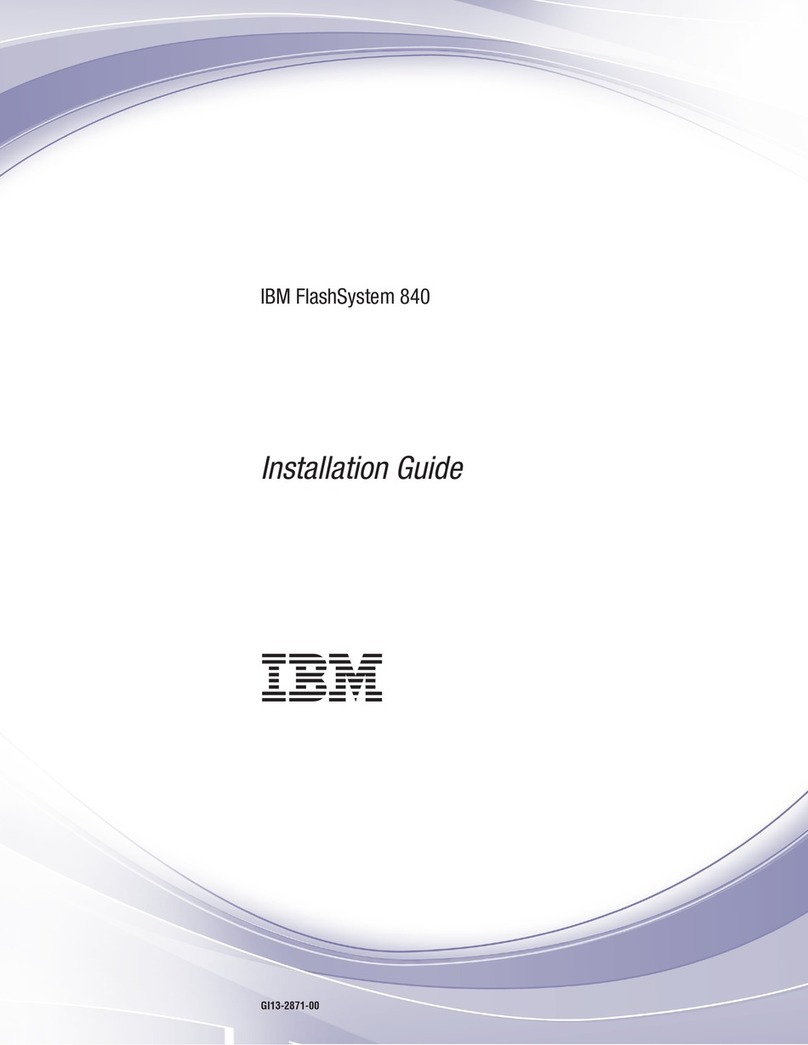
IBM
IBM FlashSystem 840 User manual
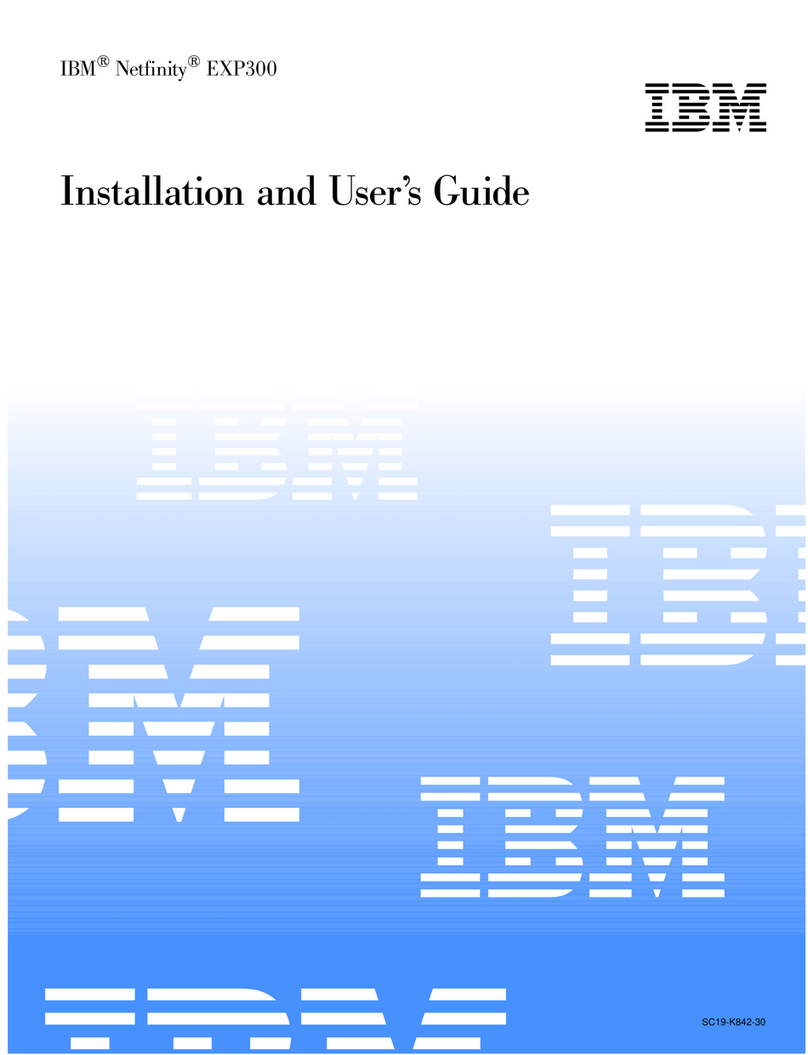
IBM
IBM Netfinity EXP300 User manual
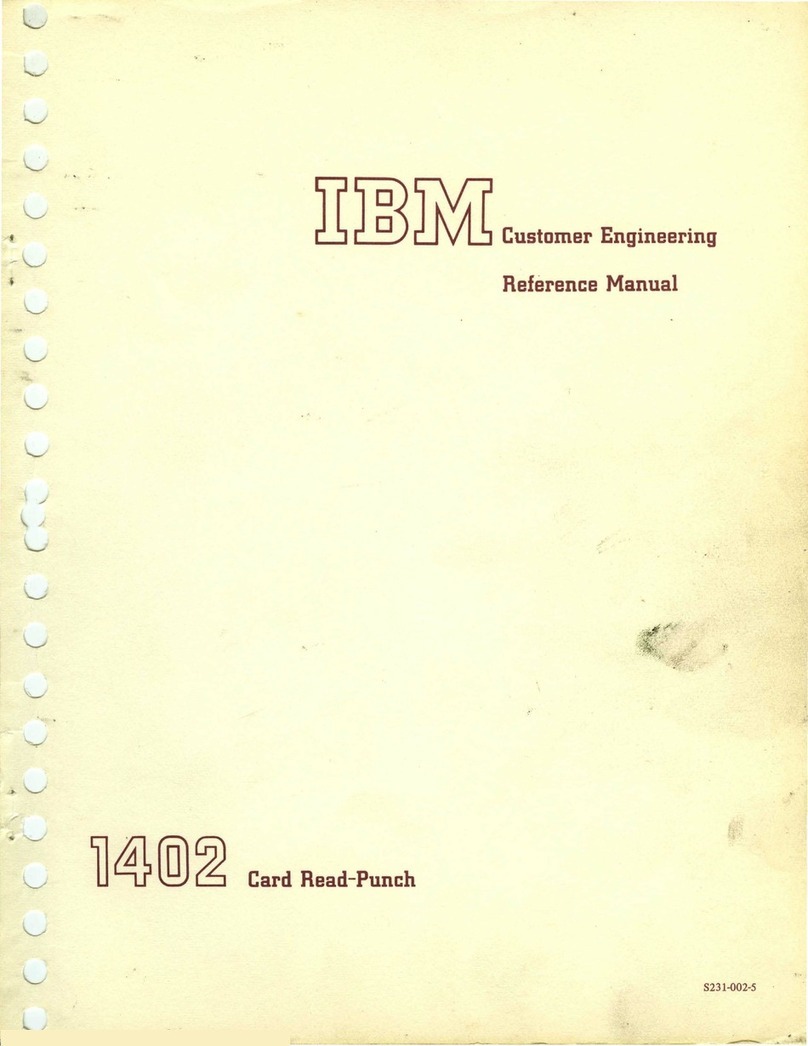
IBM
IBM 1402 User manual
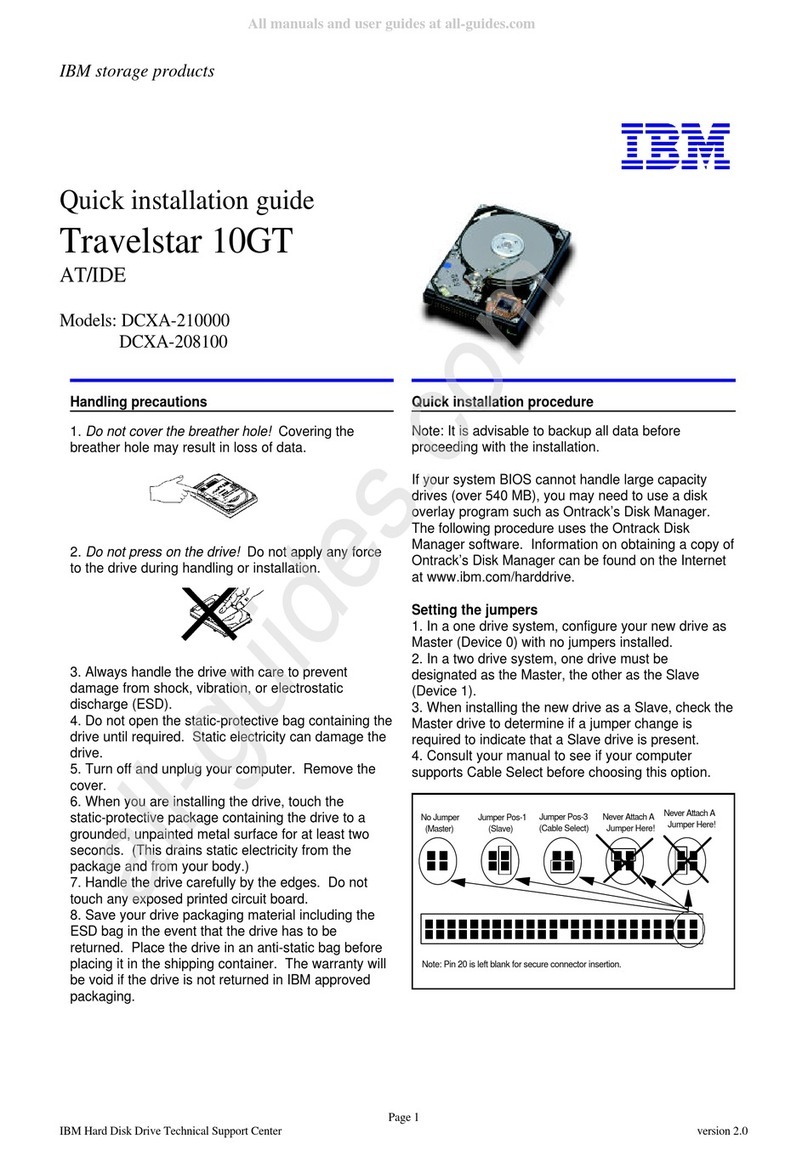
IBM
IBM DCXA-210000 User manual
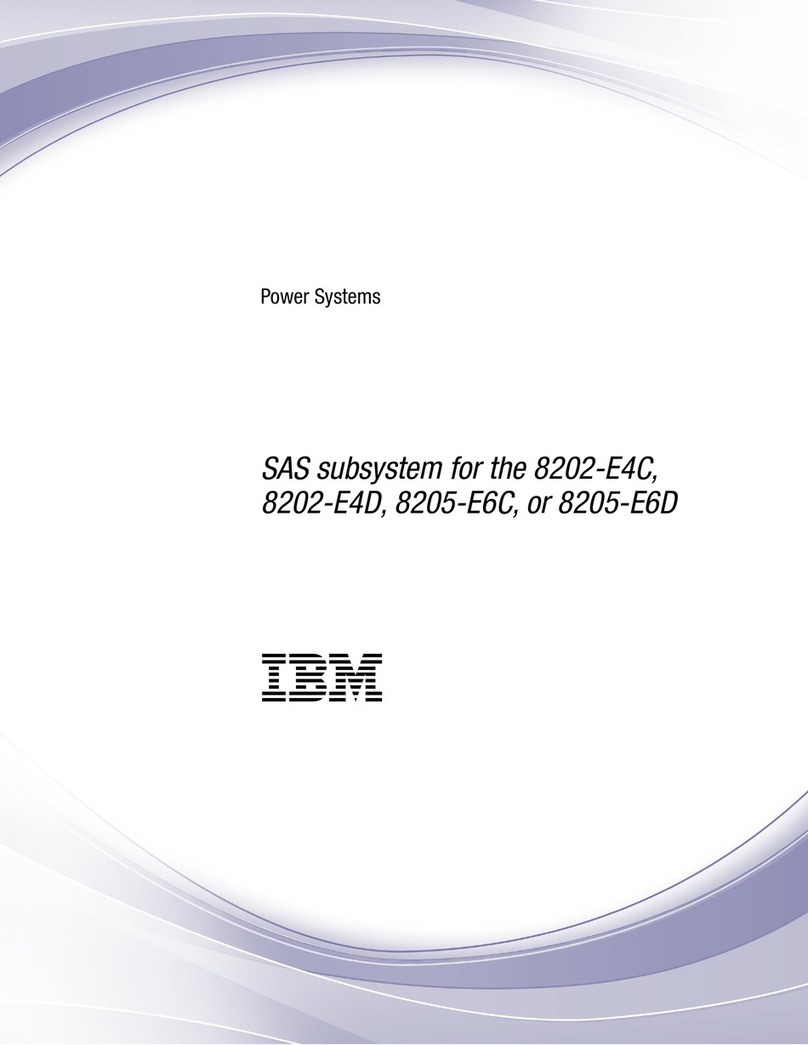
IBM
IBM Power Systems Series User manual
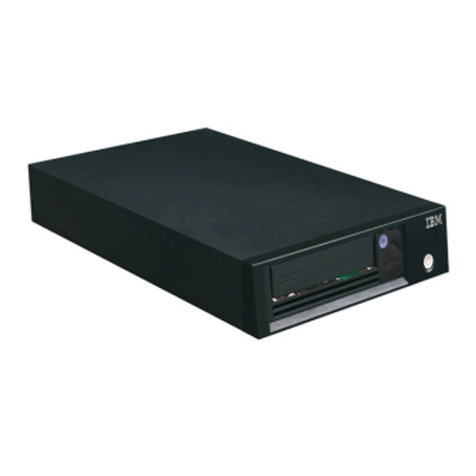
IBM
IBM System Storage TS2230 User manual
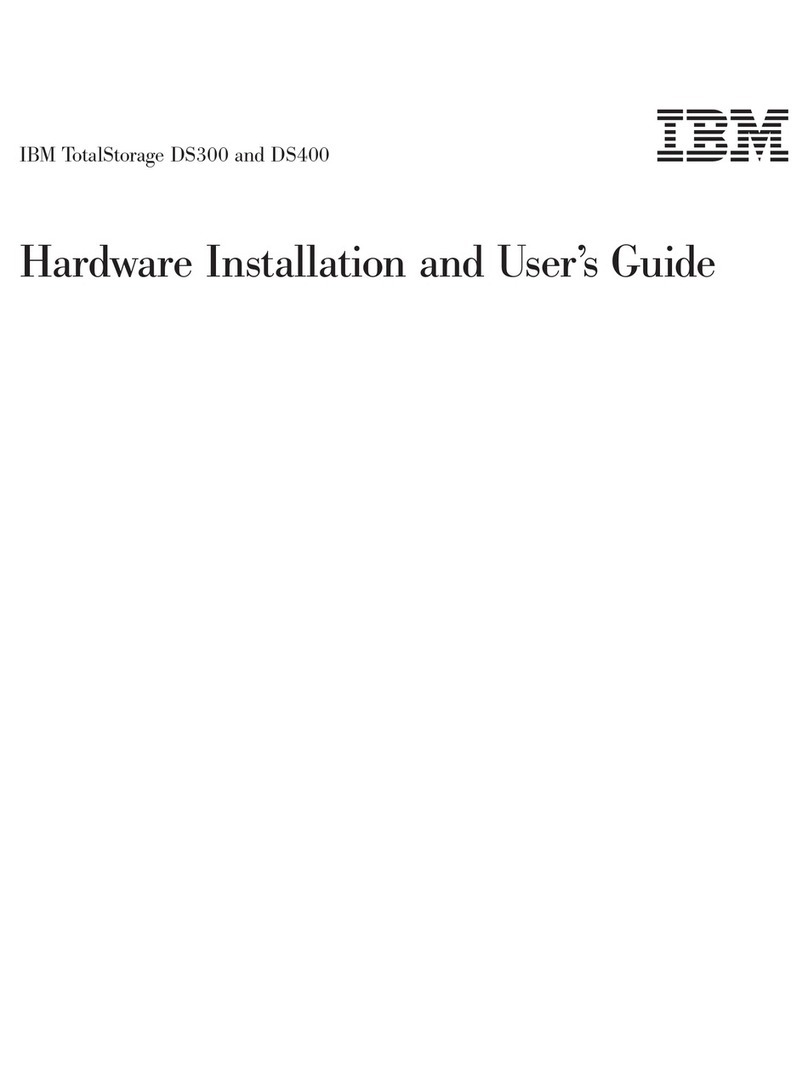
IBM
IBM TotalStorage DS300 User manual
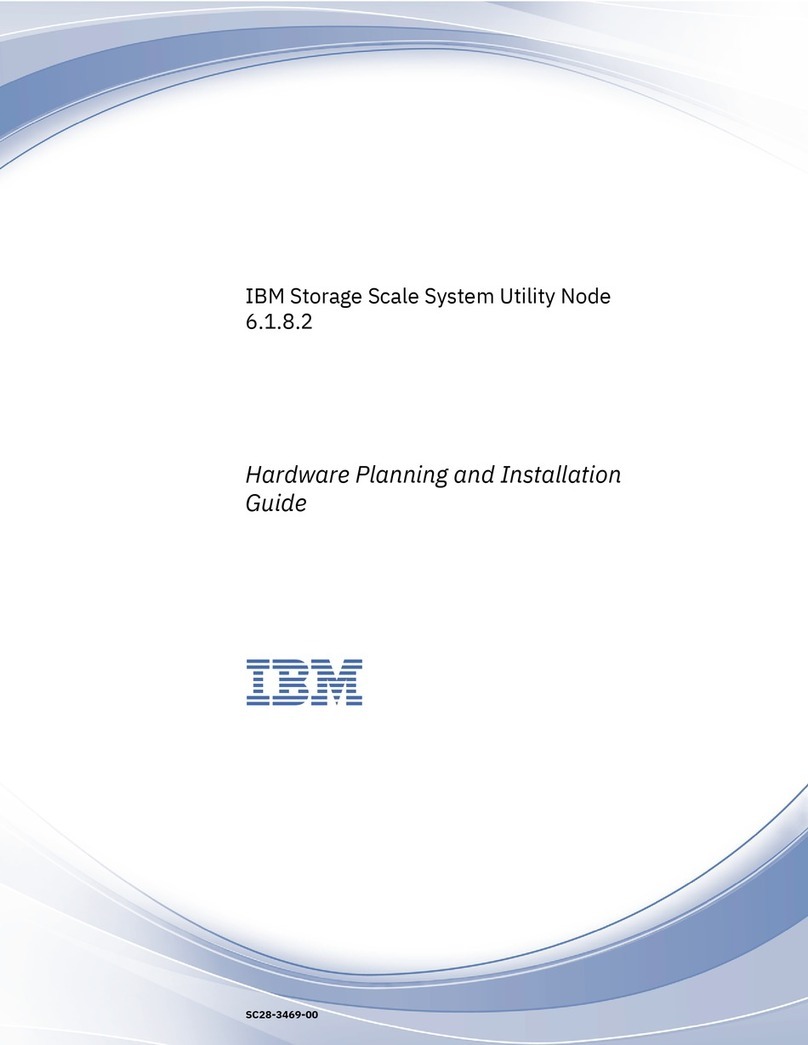
IBM
IBM 6.1.8.2 Technical manual
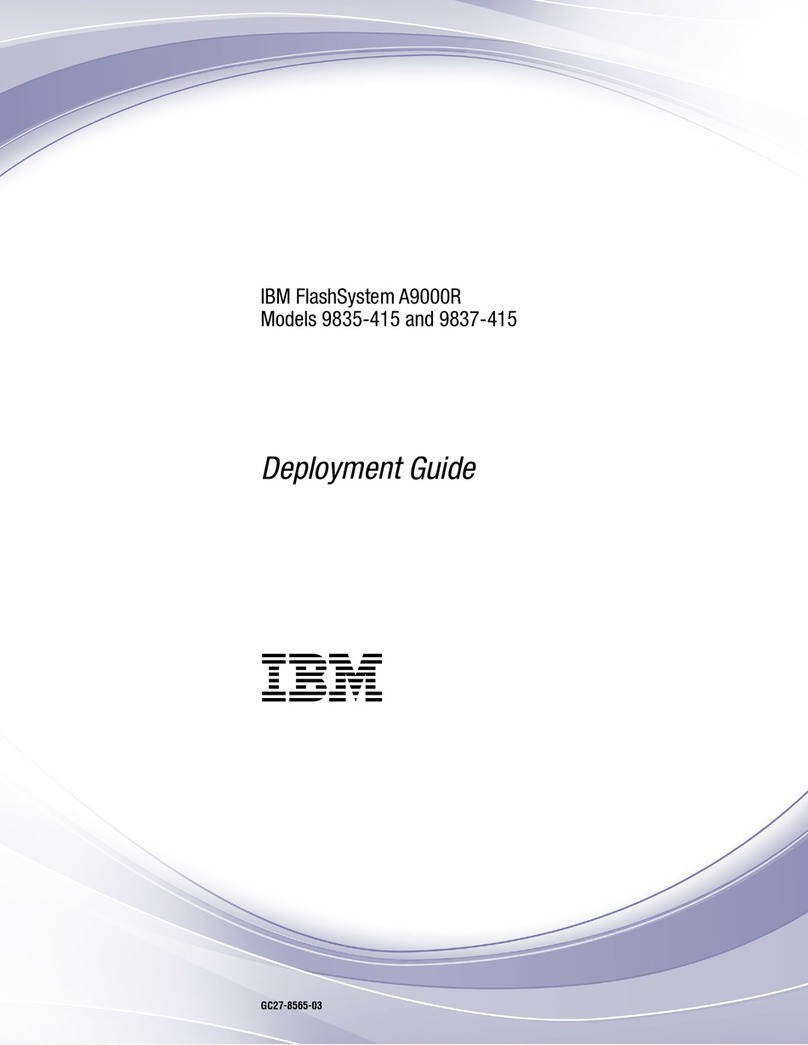
IBM
IBM FlashSystem A9000R Quick reference guide
Popular Storage manuals by other brands

Acer
Acer Veriton M661 user guide
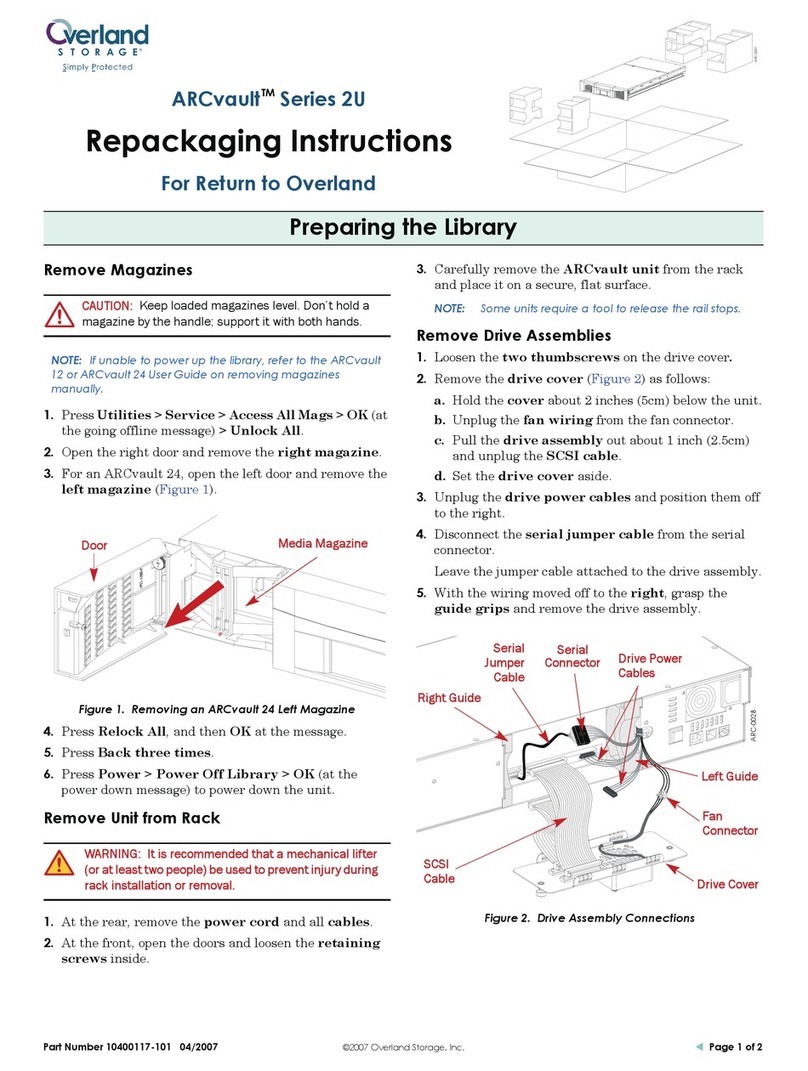
Overland Storage
Overland Storage ARCvault 2U Series quick start guide
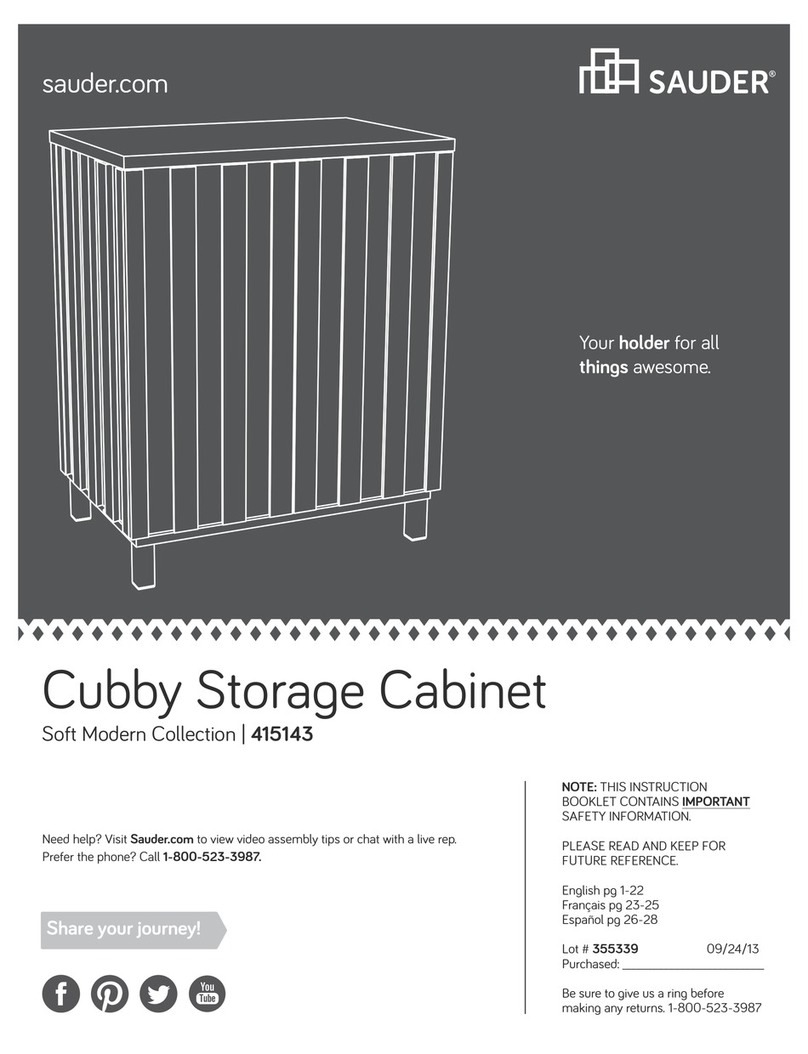
Sauder
Sauder Soft Modern 415143 manual
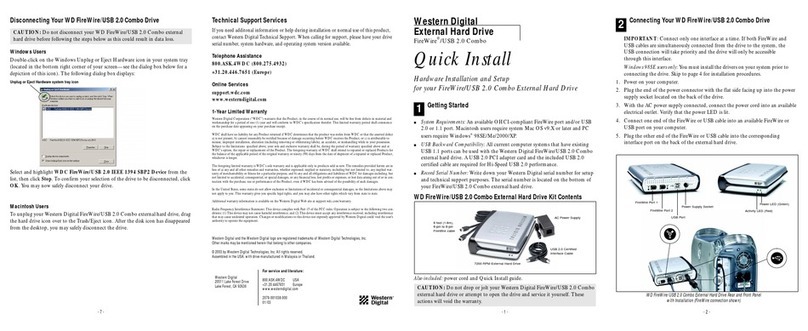
Western Digital
Western Digital WD800B002-RNN - FireWire Hard Drive 80 GB... Quick install guide
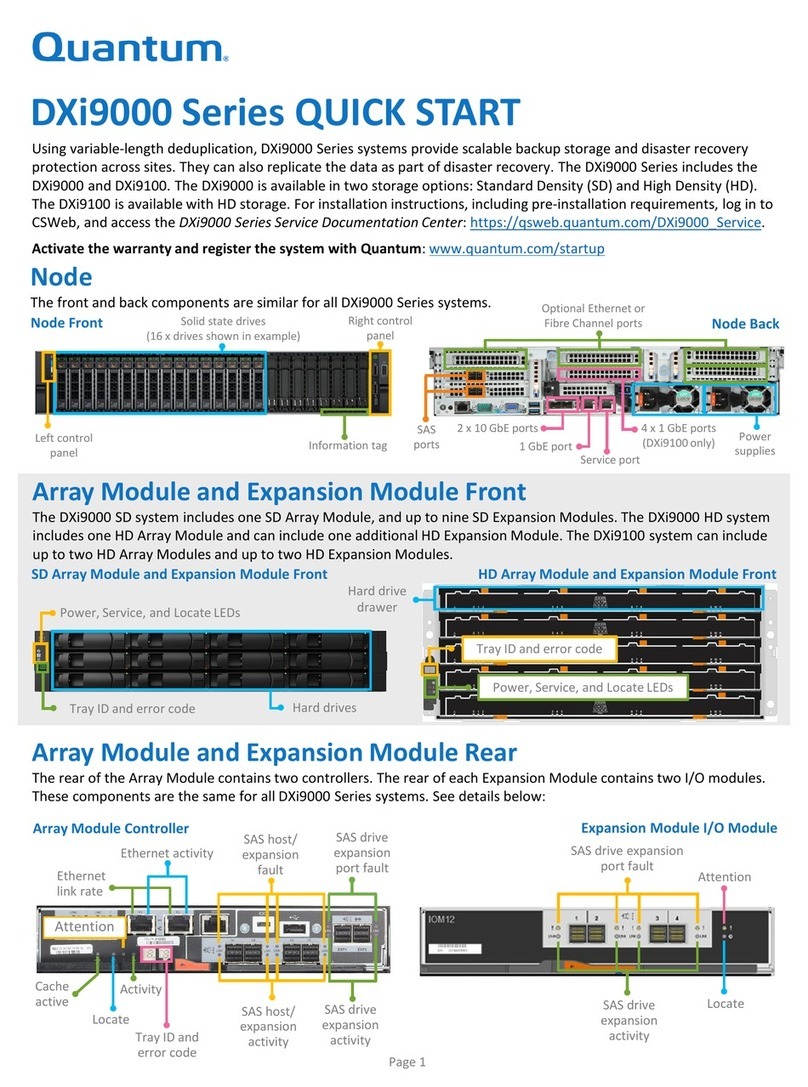
Quantum
Quantum DXi9000 Series quick start guide
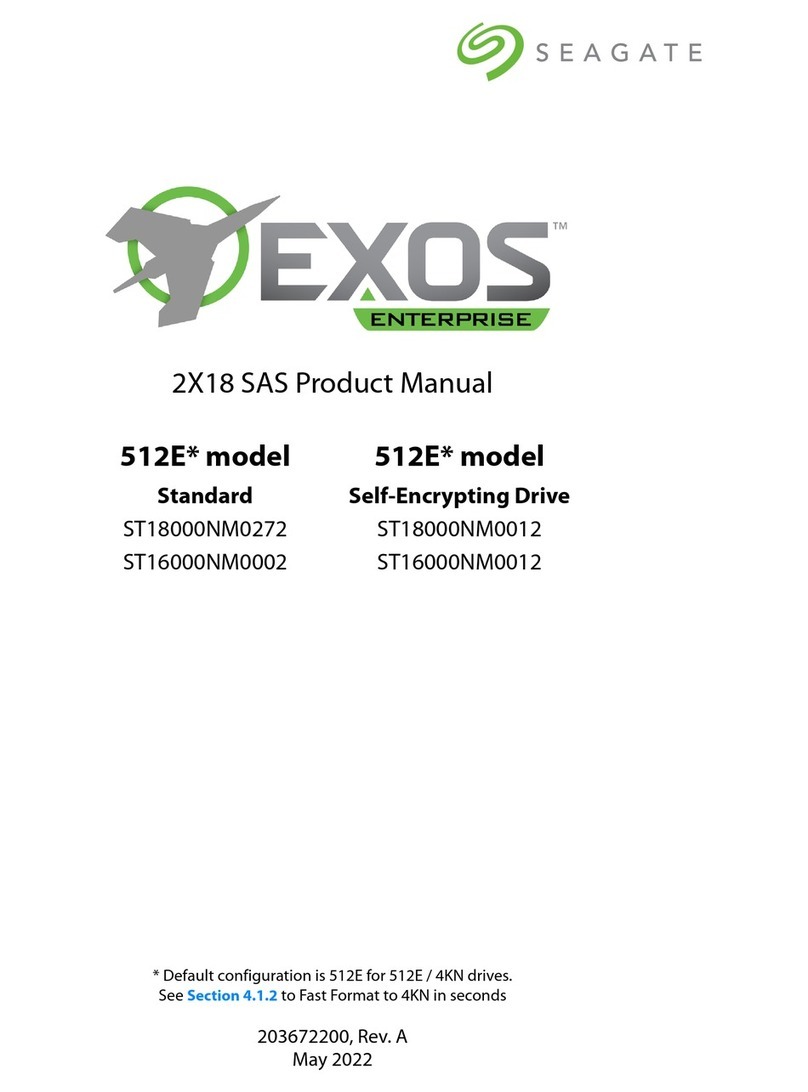
Seagate
Seagate EXOS ENTERPRISE 2X18 SAS 512E Standard product manual