IBM B-1 User manual

IBM
ELECTRI€
TYPEWRITERS
"
CUS
,rOMER
ENGINEERING
.
'\
,
B-1

ELECTRIC
IBM
TYPEWRITERS
CUSTOMER
ENGINEERING
INSTRUCTION
MANUAL
MODEL
B1
Issued
to
__________________
_
Branch
Office
________________
_
Department
___________________
_
Address
__________________
_
If lost
or
mislaid,
finder
will
kindly
return
to
the
above
address
INTERNATIONAL
BUSINESS
MACHINES
CORPORATION
New
York
22,
New
York

CONTENTS
Motor
and
Drive -------------------------
Key
Levers,
Letter
Cams
and
Type
Bars
---------------
Escapement ---------------------------
Margin
Set
- - - - - - - - - - - - - - - - - - - - - - - - - - -
Margin
Release -------------------------
Line Lock ----------------------------
Carriage
and
Rai
Is
- - - - - - - - - - - - - - - - - - - - - - - -
Paper
Feed - - - - - - - - - - - - - - - - - - - - - - - - - - -
Platens
-----------------------------
Functiona
I Cams -----
Space
Bar ------
Shift
- - - - -
Tabulation
--
Carriage
Return
Backspace ---
Ribbon - - - - - - - -
©
1958
by
INTERNATIONAL BUSINESS MACHINES CORPORATION
590
Madison
Avenue,
New
York
22,
New
York
Printed
in
U.S
.A.
May
1958
FORNVPART
NO:
241-5010-1
Page
1
3
7
9
10
11
12
14
17
19
20
21
23
27
31
33

c
•
c

IBM ELECTRIC TYPEWRITER
MODEL··Bl
INSTRUCTION MANUAL
MOTOR AND
DRIVE
Motor.
The
AC
and
the
DC
motor used in the Model
B,
IBM
Electric
Typewriter
is
rated
at
1/40
HP. It
is
equipped with
self-
aligning
bronze bearings which
are
surrounded with saturated
oil wicks and oil return cups.
The
AC
motor operates on the induction principle and runs
at
a speed
of
approximately 1625
R.P.M.
No
governor brushes
or
starting
contacts
are required, thus assuring
quiet
operation
(Fig.
1).
A two mfd
capocitor,
in
the
starting winding
circuit,
provides
the
means to start
the
motor and control
the
direction
of
rotation.
The
capacitor
also remains in the
circuit
whi
Ie
the
motor
is
running and is used to minimize
operating
vibrations
(Fig.
2).
Motor Mounting Shaft
Figure
1.
AC
Motor
And
Mounting
The
capocitor
is
wrapped in insulating material
and
mounted
to
the
rear
frame by the
capacitor
mounting
bracket.
The switch
is
mounted on
the
right side frame. It
is
operated
by a switch lever
and
link.
The switch lever has a white
portion for
the
"ON"
position
to
attract
attention.
It moves
the
key
lever
locking bar .to
the
left
and
to
the
front when
the
switch
is
turnedUOFF"
(Fig.
27).
This locks
all
keylevers
ex-
cept
the
shift
key
lever.
The shift
key
lever is not
affected
because in
the
locked down upper case position,
it
wouldob-
struct
the
action
of
the
key
locking
bar~
The
DC
motor is a shunt
\Hound
brush motor, in which speed
is
dependent
on
stable
line
voltage
(Fig.
3).
This motor
is
characterized
by
a.low
starting torque
and
astable
speed under
load.
Advantages
of
this motor
are
that
it
requires no
gover-
nor
or
governor contacts and requires
only
a simple switch
cir-
cuit
and
a fuse. Changing machine specifications
from
one
1
White
llac:lc
Gray
sJitch
capacitor
Figure
2.
AC
Wiring
Diagram
current
to
another
is
simple and fast, because the same
mount-
ing parts are used for both
AC
and
DC
motors. However, when
changing a machine
from'
AC
to
DC, a nonmagnetic governor
pawl assembly must be
installed.
The standard governor powl
can
become magnetized by a
DC
motor and
magnetically
at-
tach
itself
to
the
friction governor
plate
and cause faulty
tabu-
lation and
escapement.
Black
Figure
3.
DC
Wiring
Diagram
The
AC
and
DC
motor
is
suspended
from
ci
shaft
that
is
sup-
ported by
the
left side frame and a motor mounting bracket
on
the
rear
frame. This shaft
is
held in
place
by
C-clips.
Rub-
ber grommets, held in cup like recesses
of
the
motor end
bells,
insulate
the
motor vibrations
from
the
shaft.
A lower
grom~et
insulates
the
motor
from
the nut
and
screw
that
positions
the
motor on
the
left side frame
(Fig.
1).
The latest rubber motor
mounts
or
.grommets incorporate a "finned" design to reduce
motor noise
(Fig.
4).
To
further reduce vibration and harmonic noise transmitted
through
the
motor mounts, a ring mount
is
now used on 115V
and 230V 60
cycles
AC
motors
(Fig.
5).
The three mounting
holes in
the
frames used for
the
previous motor,
are
also used
by the ring mount.
In
addition,
a ring mount
bracket
support
has been added
to
eliminate
any
left
or
right motion
of
the
right ring mount
bracket.
Every motor mounting includes a
static
eliminator,
which
grounds
the
motor to the frame
of
the.
typewriter.
A small
piece
of
copper wire
is
formed in a
"U"
around
Qneof
thegrom'
mets
or
rings
to
.prevent
the
bui Id-up
ofa
static
charge.

Upper Motor Mount
-*""--I-NIIII
Stotic Eliminator
/litl
Lower Moior Mount
Figure
4.
n
Finned
II
Motor
Mounts
Ring Mounting Bracket
Figure
5.
Ring
Mounted
Motor
Two
bakelite
shields, formerly used, have been eliminated on
all
motors. This allows a
greater
flow
of
air
through the motor
thereby
reducing its operating temperature.
Drive
The positive drive mechanism consists
of
toothed belts and
pul-
leys to transfer the rotation
of
the motor
to
the power roll (Fig.
6).
speed reduction
from
the motor
to
the power roll
is
approxi-
mately6:
1.
This reduction
is
accomplished by using a combi-
nation
of
3 pulleys and 2
belts.
A drive belt transfers the
ro-
tation from the motor pulley
to
the large side
of
the
inter-
mediate
pulley.
A belt
from
the small side
of
the intermediate
pulley,
known as the driven
belt,
transfers the rotation
of
the
intermediate pulley
to
the power roll
pulley.
The power roll
pulley
is
aj'tached
directly
to
the
end
of
the power roll shaft
by two bristo
set
screws.
The intermediate
pulley
~s
mounted
to
the left side frame by
means
of
an intermediate shaft, a retaining
plate
and a
nut.
The retaining
plate
acts
as a locking
device
for
the
nut.
The
shaft and nut have a left-hand thread
so
that
the rotation
of
the pulley prevents loosening
of
the
shaft.
2
Figure
6.
Positive
Drive
Mechanism
The pitch
of
the machine
is
the number
of
typed
characters
or
spaces
to
the
inch.
Machine pitch usually
is
determined
by
the
size
of
the type used. Type style and
size
also indicate
the power. roll speed needed for best impression results. The
speed
of
the
power roll
is
varied by using motor pulleys
of
different diameters. The diameter
of
the
motor
pulley
deter-
mines the number
of
teeth
on
the
pulley,
and
these
numbers
are
molded on the
pulley.
The drive belts vary
in
diameter
to
compensate for
motorpul-
ley
sizes.
This
facilitates
belt
adjustments on shaft mounted
motors. Strips
of
yel)oV(
or green paint on the drive belts
indicate
the small and large belts,
respectively.
The following chart provides recommendations for the proper
motor
pulley,
drive
belt
and power roll speed on
most
ma-
chine.s
of
a given
pitch.
Pitch Power
Roll
Speed
No.
of
Teeth Drive Belt
FPM
RPM
on Mtr. Pulley
12
and 14 95 242
14
Y~llow
6.2/5,
8,
9,
and
10
103 261
15
Green
;-1,1;',
The ring mounted. motor
must
be kept
toward
the
rear
to
pre-
vent interference with the lower
line'lock
bell
crank.
It is,
therefore,
necessary to
use
the longer green belt with
all
ring
mounted motors, regardless
of
the motor
pu
lIey used.
Earlier model positive,belt drives had motor
pulley
combi-
nations
of
13
-
15
teeth
and 14 -16
teeth.
Power roll speeds
.
of
95 and 103 feet per minute
are
the
only
ones currently
speci-
fied,
therefore a
14
-15 tooth motor
pulley
has replaced two
previous pulleys.
The purpose
of
the
power roll
is
to supply motion for
all
cam
operated
mechanisms. It consists
of
a hollow
met,af
cylinder
to
which a rubber tube.
is
glued (Fig.
7).
Two
end plugs,

Power
Roll
Drive Pulley
locknut
@t;D
Power
Roll
~~
Io.!l'--=="-.
Clutch
lever
Retaining Bolt "'/l f
Coiled
Compression Spring
Figure
7.
Power
Roll
Mechanism
containing a solid power roll shaft,
are
pressed into the ends
of
the
cylinder.
This shaft mounts the power roll to
the
ma-
chine by passing through self-aligning porous bronze bearings
that
are
held
in
retainers on both side frames. The left end
of
the
shaft
is
the mounting for the power roll
pulley.
The right
end
of
the shaft
is
rectangular and extends through a
rectangu-
lar hole
in
the
clutch
friction
disc.
KEY
LEVERS,
LETTER
CAMS AND
TYPE
BARS
Letter Key Levers
The
~ear
ends
of
the keylevers
are
mounted
in
slots
in
the
key
lever bearing support and
are
held
by
a fulcrum wire which
passes through a hole
in
each
key
lever (Fig.
8).
This wire
serves as the fulcrum point for all
key
levers. The left to
right motion
of
the front ends
of
the
key
levers
is
limited by
slots in
the
front
key
lever guide cotnb (Fig.
9).
Key lever
Com
lever
Bearing Support
Figure
8.
Key
Lever
and
Cam
Mounting
3
springs hold
the
key
levers
in
the raised,
or
rest position. 'The
springs
are
located between the front ends
of
the
key
levers
and the
~pring
lugs on
the
top
of
the front guide comb
(Fig.
15)
The travel
of
each
key
lever
is
limited
by
strips
of
rubber
mounted across the top and bottom
of
the slots
in
the front
guide comb. The rubber strips prevent metal
to
metal
contact
and
are
a noise reduction
feature.
A sponge rubber keyboard
stabi lizer reduces
key
button vibration during machine
oper-
ation (Fig. 15). It
is
located between the adjusting lugs on
..
the top
of
the
key
levers and
the
key
lever bearing support.
The adjusting lugs make it possible
to
raise or lower individual
key
levers.
Figure
9.
Key
Lever
Guide
Comb
Letter Cams
Cam lever assemblies
are
mounted
in
slots in the cam bearing
support and
are
held by a fulcrum wire which passes through
a hole
in
each
cam lever
(Fig.
8).
A type bar link
is
hooked
through a hole
in
the long
arm
or extension
of
the
cam
lever.
The
other
end
of
this link hooks into
the
bottom
of
the type
bar.
The rest position
of
the type bar, against the type rest,
determines the rest position
of
the cam
lever.
When the type
bar
is
fully
actuated
or
against the
platen,
the
cam lever
is
also rotated
to
its full
actuated
position. Each cam lever
assembly is made
up
of
three main parts; the
c.am
lever,
the

cam,
and the trip lever (Fig. 15).
The cam consists
of
a steel body with nylon molded
at
the
bear-
ing
point,
the
tai
I, and the shoe
that
contacts' the power
roll.
The cam
is
mounted to the cam lever by means
of
a shoulder
rivet.
It
is
free to
rotate
about the
rivet,
but the amount
of
rotation
is
limited
in
one direction by a steel stop which
pro-
jects
from
the
cam.
The stop contacts the side
of
the cam lever
and determines the rest position
of
the cam (Fig. 15). A cam
spring extends between a hook on
the
cam lever and a hook on
the cam and holds the cam
in
its rest position. The heel
of
the
nylon shoe contacts the cam lever when the cam
is
fully rotated
and limits rotation
in
this
direction.
Earlier steel bodied cams
did not have steel stops. The nylon heel
of
the cam was larger
and served as a cam stop
in
both
directions
of cam
rotation.
The st.eel stop was incorporated
to
minimize cam bounce when
the cam returned to its rest position.
The trip lever
is
mounted to the cam lever
by
a shoulder rivet
(Fig. 15).
An
elongated slot
in
the trip lever allows
it
to slide
front
to
rear
to
rotate around the
rivet.
A hook
on
the trip
lever mounts a sprint
that
extends to a hook on the cam
lever.
The tri I lever springs holds the trip lever
up
and to the rear
in
its rest position. The trip lever has two formed lugs. The top
lug
is
positioned
directly
under the lug on the key
lever.
The
boftom lug
is
directly
above the
cam.
Impression Control Indicator
Figure
10.
Cam
Knockout
Bar
Assembly
The cam knockout bor assembly
is
an aluminum casting
to
which
two sets
of
flat knockout spring fingers are secured (Fig. 10).
There
is
one knockout finger for
each
cam lever assembly. The
height of
each
knockout finger, is controlled by individual
impression control screws which are located
in
the knockout bar
below the fingers. The knockout bar assembly pivots between
the left and right side frames on two pins
that
are
secured
by
set screws.
An
impression control
eccentric
shaft
is
positioned
beneath the
rear
of
the knockout bor and pivots in two bronze
bearings which
are
mounted to the left and right side frames
(Fig.
10). A plastic
gear
is
pinned
to
the left end
of
the shaft
and
meshes with the
teeth
on the impression control
indicator.
The impression control indicator pivots
on
a stud on the left
side frame. The rear
of
the
knockout bar
is
held down against
the impression control
eccentric
shaft
by
two springs.
4
Type
Bars
Type bars
are
mounted in a slotted segment
and
are
held by a
curved type bar fulcrum wire (Fig. 11). The lower end
of
the
type bor extends below the segment and has a hole in
it
for
the type bar link. Above the segment
is
the body
of
the
bar,
identified by
the
reinforcing
rib,
and the type head which
includes the type slug and
the
wider section
of
the bar
(Fig.
12). The part referred to as the throat extends
from
the
top
of
the reinforcing rib to the bottom
of
the
head.
A type mark,
used to identify the type
style,
is
located between the upper
and lower case type faces on the type slug.
An
anticlash
I
ug
prevents damage
to
the type face if one type bar
fo
Ilows
another to the
platen
before the first bar has gotten out
of
the
way.
The type face
is
curved
to
the same arc as the platen
so
that
all parts
of
the type face will strike
evenly.
A hole
is
provided
in
the
type head
to
facilitate
forming
of
the
head
during type alignment. A locater lug found on some type
styles
is
used
at
the factory
to
facilitate
soldering
of
the type
slug to the
bar.
Fulcrum
Wire
Ret.aining
Screws
Figure
11.
Type
Bar
Mounting
Changable type bars
are
available
to permit the operator
to
interchange type bars in specified positions, thus providing
a
greater
number
of
special
characters (Fig. 13). This feature
is
available
only
for positions
0,
32,36,
39,
40,
41,
42, 43,
and
the standard numerical type bar positions.
Changeable
type bars ore not porvided for
alphabetic
positions
or
position
#38. A special type bor link incorporating a spring
clip
is
.
used with changable type bars. This link will not drop
off
the
cain lever when
the
operator removes a type bar and drops
the.
link.
Each changable type bar is designated for one type bar
posi-
tion
only
and
is
to
be aligned
to
the
typewriter for which
it

Type
Slug
Figure
12.
Type
Bar
Identification
Figure
13.
Changeable
Type
Bars
is
to
be
used.
The typebar segment
is
a
semi-circular
carbon
steel
casting
with slots
cut
into
it
to mount and guide the type bars
(Fig.
11).
The segment also provides
the
mounting for
the
universal
bar,
and the type
guide.
The rear
of
the segment
is
hollowed out
to
allow dirt and erasures
to
be pushed through
the
slots by the
typebars during
their
travel to the
platen.
Two
screws and
two pins mount
the
segment to
the
segment support.
The type guide
is
a formed part
of
heavy metal and
is
attached
to
the segment by four screws and a dowel pin (Fig.
11).
The
5
four screws pass through oversize holes in
the
type
guide,
so
the guide may be positioned by pivoting it on the dowel
pin.
The type guide has two major parts: The ring and
the
type
guide (Fig.
14)-.
Type
Slug
Type
Bar
Ring -
part
of
type
guide
Type
face
makes contact
Figure
14.
Type
Ring
and
Cylinder
When a type bar
is
fully
actuated,
it contacts the ring when
the
type face
is
approximately
.003"
from
the
platen
or
cylinder.
This relationship
is
known as proper ring and
cylin-
der.
During a typing
operation,
the type bar
must
whip
or
bend above the ring
so
the type face
can
make an impression
on the
paper.
This whipping
action
prevents
the
typ'e face
from
lingering on the paper.and smearing.
(Operation)
Depression
of
the
key
button by the operator causes
the
rear
end
of
the
key
lever
to
pivot about the fulcrum wire
in
the
key
lever bearing support (Fig. 15). The lug on the bottom
of
the keylever contacts
the
top lug
of
the
trip
lever forcing
the trip lever
to
rotate down unti I its lower lug
contacts
the
nylon
cam.
Continued depression forces the cam to
rotate
out
of
its rest position, until the serrations on
the
nylon heel
of
the cam engage the power
roll.
The distance between the
heel
of
the cam and the cam rivet
is
less than
the
distance
between the toe
of
the cam and the
rivet.
This
is
called
the
rise
of
the
cam.
As
the
power roll forces the cam to
rotate,
the
contact
point between
the
power roll and the cam proceeds
from
the heel toward
the
toe.
The weight
of
the type bar and
the tension
of
the cam lever spring hold the cam against the
power
roll.
The rise
of
the cam then forces
the
cam fulcrum
point,
or
rivet,
away
from
the power
roll,
and Causes the
cam lever to rotate about
the
cam lever fulcrum
wire.
The
long
arm
of
the cam lever and
the
type bar link
are
moved
toward the front
of
the
machine.
The link pulls
the
bottom
of
the type
bar
toward
the
front
of
the machine, causing
the
type
bar
to
rotate about its fulcrum
wire.
The type head,leaves
its rest position and begins
to
travel toward the
platen.
Be-
fore the type head reaches
the
platen,
the
tai
I
of
the
cam
contacts the cam knockout finger (Fig. 16). The cam stops
rotating,
but the momentum
of
the type bar causes
the
type
head to continue toward
the
platen.
This forces
the
cam lever

Letter
...
aRI
_____
~_:!'
Steel Stop
~~~,-~
Eccentric
Shaft Screw
Cam
Fulcrum
Figure
15.
Cam
and
Type
Bar
Operation
to continue its motion toward the front
of
the machine.
Con-
tinued motion
of
the cam lever causes the nylon shoe on the
cam
to
leave the power roll and the cam spring restores the
cam to its rest position against the cam
lever.
The moving
type bar
contacts'the
ring,
then whips or bends,
abave
the ring
so
the type head may complete its travel into the type
guide.
The type face strikes the ribbon and makes
its
impression on
the
paper.
The striking force
or
impression
of
each
type bar
is
determined by how long
the
cam
is
allowed
to
rotate against
the power roll before it reaches the knockout finger. The
long-
Cam
Lever Fulcrum
Figure
16.
Cam
Knockoff
Point
6
er
the cam remains engaged with the power
roll,
the longer
the
type
bar
wi
II
be powered and the greater will be its
strik-
ing force.
After the type bar strikes the
platen,
the type bar and cam
lever reverse
their
direction.
If the
key
lever
is
helddowrl,
the rear edge
of
the top lug on the
trip
lever will engage the
front edge
of
the lug on the
key
lever as
the
cam lever
as-
sembly restores. The cam
leverwill
restore
to
its rest position,
but the
trip
lever
wi
II
remain against the
key
lever
lug unti I
the
key
lever
is
allowed to restore. The restoration
of
the
key
lever allows
the
trip
lever spring to restore the trip lever
up
toward the rear
of
the machine. This actioD
of
the
trip,
lever insures a single operation
of
the cam and
allowsthe
type
bar to restore
to
the rest position, regardless
of
how long
the
operator
ho
Ids
the
key
button depressed.
When the type bar
r-.eturns
to
rest,
it
strikes a spring loaded;
rubber type rest
pad,
which is suspended between two frames
on the segment support (Fig. 11). The type rest reduces type
bar rebounding away
from
the rest position and reduces
nois~.
This enables th'e type bar
to
be ready immediately for
another
operation.
The impression
of
the
type bars can be controlled by two
methods.
An
impression control screw isprovided below
each
knockout finger
to
give individual .adjustment for this impres:"
sion
of
each
typebar (Fig. 10).
An
impression control
indi-
cator
is
available to
the
operator,
to
provide a means
of
regu-
latingthe
height
of
the
knockout bar assembly
(Fig.
10). This
adjusts the knockout point
of
the cams as a group. Moving
the impression control indicator rotates the ec,centric shaft
below the cam knockout bar assembly. Raising the bar
de-
creases the impression
of
all
type bars, and lowering the bar
increases the impression
of
all
type bars. A reference
scale,
graduated
from
0 to 10,
is
on the impression control
indicator.

Repeat/Non
Repeat Key Levers
A
repeat/non
repeat
underscore
is
provided as standard equip'"
ment.
A
one
piece
repeat
key
lever,
a plunger and a
spr~ng
ore
used with a standard cam
unit
to
provide
thi-s
feature.
The
keylever
has a two step
key
I.ever
lug.
The front guide comb
has six positions where
repeat/non
repeat
letter
units may be
installed
at
the
factory:
0,
8,
32, 36, 39, and 42 (Fig.
9).
Installation requires the removal
of
the
rubber
from
the
front
.guide comb where
the
repeat
character
is
desired.
Two
dif-
ferent plunger springs
are
available;
the lighter spring
is
to
be
used with
key
levers
in
the upper two rows.
Figure
17.
Repeat/Non
Repeat
Key
Levers
Escapement
Tr:jp
Lever
When
the
repeat/non
repeat
key
lever
is
depressed
to
the
limit
of
its normal
travel,
the
rear
step on
the
key
lever lug will
provide a single operation
ofthe
cam
(Fig.
17). If
the
key
lever
is
held down in this position,
the
rear step on
the
key
lever lug will prevent
the
trip
lever
from
restoring. Further
depression
of
the
key
lever
is
allowed by
the
spring loaded
plunger.
This will cause
the
front step
of
the
key
lever lug
to
depress
the
trip
lever for a
repeat
action
of
the
cam.
If
the
key
lever is he
Id
down in this position,
the
trip
lever
wi
II
be
cammed down by
the
front step on
the
key
lever
lu"g,
each
time
the
cam
lever
assembly restores
from
a former
operation.
A
special
two
piece
key lever
is
used for field installation
of
a
repeat/non
repeat
character
in
any
letter
position desired
(Fig.
17).
This feature may be .crippled when a plunger and spring
is
used
by
installing a plunger bushing in
place
of
the compression
spring. It
is
necessary
to
replace
the
plunger with the space
,bar plunger in order for
the
bushing
to
be
used.
ESCAPEMENT
The escapement mechanism controls movement
of
the
car-
riage.
The mechanism consists
of
the
universal
bar,
escape-
ment
pawl,
and the escapement rack (Fig. 18).
The universal bar and universal bar support
are
fastened to
the
back
of
the
segment with two hex headed screws. Flexible
mounting springs
connect
the
universal bar
to
the
support and
position
the
universal bar against
the
back
of
the segment.
The escapement powl bracket
is
fastened to
the
rear rail with
Yigure
18.
Escapement
Mechanism
7

two screws. A
single
escapement
pawl
is
mounted on
the
escapement pawl
bracket
by a shoulder rivet passing through
an
elongated
hole-in
the
pawl.
An escapement 'pawl spring
pulls
the
escapement pawl
tip
to
the
right and into
the
escape-
ment
rack.
The
escapement
pawl
spacer
cont$lins a larger
elongated
hole and
is
~ounted
,on
the
same sholllder
rivet
as
the
escapement
pawl.
A short pawl spacer spring loads
the
spacer
toward
the
right
and
to
the
rear.
Also mounted to
the
pawl
bracket
with
another
shoulder
rivet
is
the
escapement trip
lever.
The escapement rack
is
secured
ot
the
underside
of
the
car-
riage with dowel pins and screWs. It contains a number
of
teeth
per inch corresponding to
the
pitch
of
the
typewriter.
(Operation)
The escapement
is
asingle pawl
type
operated
each
time a
type
bar moves to
the
platen,
or
whenever
the
space ,bar
mech-
an
ism
is
activated.
As
the
type
bar moves toward
the
platen,
it
contacts
the
uni-
versal bar and pushes it toward
the
rear.
An
adjusting
plate
mounted on the universal bar transfers
the
universal bar motion
to
the
escapement
trip
I
ink.
Motion
of
the
trip
link toward
the
rear rotates
the
escapement
trip
lever,
on its shoulder moLint-
ing
rivet,
so
that
the
top
of
the
trip
lever
moves toward
the
front
of
the
machine.
The top
of
the
trip
lever
contacts
an
upright lug on
the
escapement pawl
sP<;lcer,
part
of
which
is
behind
the
tail
of
the escapement
pawl,
and rotates
the
left
erid
of
the
escapement
pawl
spacertoward
the
front
of
the
type-
writer.
As
the upright lug moves forward, it carries
the
tail
of
the
escapement pawl
forware.
The escapement pawl pivots
abaut
its shoulder mounting
rivet,
and
the
pawl
tip
is
removed
from
the
escapement rack
(Fig.
19).
Elongated
Mounting
Hole
Carriage held
by
escapement
pawl
~:;::
Pawl
spacer
trips
pawl
from
rack
__
J\J\.!\IIJ\I\JV
__
Pawl
spacer
still
forward
Carriage
must
overcome
inertia
before
it
moves.
After
escapement paWl
resh?res
to
next
tooth
of
rack,
corriege
starts
~.
move
Carriage completes
movement
under
mainspring
tension
Figure
19.
Escapement
Pawl
Operation
8
After
clearing
the
rack
tooth,
the
escapement pawl snaps
to
the
right under tension
of
the
pawl spring and immediately
contacts
the
next
rack
tooth.
The type bar continues on toward
the
platen
and prints, causing
the
pawl
spacer
to
continue
its
forward
travel.
A portion
ofthe
escapement
pawl
bracket
serves as
an
overthrow stop and prevents
the
spacer
from
get-
ting
in
front
of
the
pawl
tait.,
As
the
type
bar reverses its
direction,
the
pawl
spacer
spring restQres
the
spacer
to
the
rear,
clear
of
the
escapement pawl
tai
I
(Fig.
19).'
Because
of
its
relatively
heavy
mass
and
inertia,
the
carriage
does not
move until
all
of
these actions have
taken
place.
As
the
car-
riage moves to
the
left under tension
of
the
main spring,
the
escapeme,nt pawl
is
pushed to
the
left unti I
the
edge
of
its
elongated
mounting hole contacts
the
mounting
rivet.
This
stops and holds
the
carriage.
The
tai
I
of
the
escapement
pawl
is
again
in
front
ofthe
escapement pawl
spacer
lug
(Fig.
19).
Thus,
the
escapement mechanism completes
one
operation
and
is
in
position for
the
next.
The motion described
above
occurs under power
operation
only;
if
a
type
bar
is
raised to
the
platen
by
hand,
the
car-
riage and escapement pawl
wi
II
move before
the
escapement
pawl
spacer
restores. The
elongated
slot in
the
escapemen't
pawl
spacer
a I
lows
the spacer to be moved
to
the
left past 0
the
tail
of
the
escapemerit pawl and prevents
either
damage to
parts
or
jamming
of
the
carriage.
As
the
type bar moves
away
from
the
platen
the
spacer
wi"
restore
to
its norma I rest
po-
sition.
Maximum escapement speed
is
obtained
by
keeping
the
escape-
ment pawl
spacer
overthrow to a minimum
after
the
tripping
point has been
reached.
This permits
the
spacer
to restore as
rapidly
as possible.
Each time
the
escapement pawl
is
operated,
main spring tension
is
allowed
to move
the
carriage
one
space
to
the
left~
Mounted
tq
the
power frame casting
is
the
main spring and holder
as-
sembly
containing
the
main spring
(Fig.
20).
The main spring
drum rotates about a mounting stud which passes through
the
center
of
the main sp,ring and into
the
power frame. Tension
is
appl ied to
the
main spring drum by
the
main spring and
transferred
to
the
carriage
by,
the tension
tape.
A loop on
the
end
of
the
tension
tape
is
attached
to
the
carriage
by
one
of
Lug
of
main spring drum
Figure
20.
Main
Spring
and
Holder
Assembly

two methods. Early 12" and 16"
tapes
used a hook fastener
which was secured
in
a hole in
the
carriage
bed with a rubber
plug
(Fig.
21).
Currently
all
tension
tapes
are
screwed to
the
right
end
of
the
escapement
rack.
An
improved main spring and
holder
assembly was introduced
ahead
of
the
present centrifugal· governor mechanism. It was
designed to provide a more constand
carriage
tension by
the
use
of
a cross curve spring. This spring
replaced
the former
style and was designed
to
minimize failures during
repeat
space
bar
operations and also to provide for a less
critacal
tab
friction
governor
adjustment.
Early main spring and holder assembl ies
were mounted to the power frame with two screws which
pre-
vented
the
holder
from
turning
(Fig.
21).
The improved
as-
sembly mounts to
the
power frame by
the
main spring drum
mounting
stud.
An
ear
on
the
holder
contacts
the
power frame
and
prevents rotation
of
the
holder.
By
employing a
special
disc in
the
drum assembly, this type
of
assembly may be used
as a
replacement
for
the
former
style.
The improved main spring and holder assembly has been further
improved for
safety
on machines above Serial number
553017.
The
centrifugal
governor drum
gear
and
main spring
are
now
held
together
by a
retainer
clip
(Fig.
22). This prevents
the
main spring
from
accidentally
jumping out
of
the
holder when
it
is
being installed
or
removed. The power frame has been
countersunk to provide
clearance
for
the
retainer
clip.
Installation and removal
of
all
main springs and drums should
continue
to
be made with extreme
caution.
Figure
21.
Early
Main
Spring
and
Holder
Assembly
Two types
of
trip
links have been used on
the
Model
Bl.
One
is
the
solid link with pin
clevis,
the
other
uses a
clevis
contain-
ing a compression spring. The spring
clevis
was designed
to
improve impression by
equalizing
the
tripping force
at
various
typing
speeds.
This spring
clevis
is
not used presently
and
may
be
replaced
by-the
conventional
link and
clevis
if
desired
(Fig.
18)
•
Two types
of
escapementpawl\:lracket
assemblies
are
used on
the
Model
Bl.
Machines
of
62/5
and 14
pitch,
and
all
deci-
9
mal
tabulation
models use an escapement pawl with .038"
of
left to right motion. This assembly bears no
identification
mark.
Machines
of
8,
9,
10, and
12
pitch
use an
escapement
pawl with .058"
of
motion and
can
be identified by a round
groove
in
the front
edge
of
the
pawl tai I and
spacer.
The
spacer
.used
with this pawl has
the
upright lug positioned
.010"
to
the
right.
This arrangement
is
referred to as
the
"floating
pawl" and permits increased typing speed without
type
piling.
Increasing the length
of
the
elongated
slot in
the
escapement
pawl allows
the
pawl to snap further
to
the
right
after
being
tripped.
Consequently,
the
carriage
begins to move
the
pawl
back to
the
left
sooner.
The pawl
spacer
lug, being further
to
the
right will pick up
the
pawl
tail
earlier
and be
ready
for
the
next
operation.
The floating
type
escapement pawl
is
also used on
the
Model B
lift
platen
typewriter above Serial number 358277. The toll
bi
Iler and decimal
tab
machines use
the
former non floating
style
pawl.
Main
Figure
22.
Main
Spring
Holder
MARG1N
SET
The term "margin" denotes
the
distance
between
the
edge
of
the
paper
and
the
typewritten
material.
Left and right margins
are
determined by the position
of
the
margin stops on
the
mar-
gin
rack.
Carriage
travel
is
limited when
the
stops strike
the
Mar{lin Set Bracket
Figure
23.
Margin
Set
Mechanism

'margin control
levert
which
is.
located just below the margin
rack.
The margin stops
encircle
the margin rack and contain
!eeth
that
mesh
with those on the rack (Fig.
23).
The number
of
teeth
per inch correspond to the pitch
of
the·
machine.
The margin set
is
designed to allow the operator
to
reposition
the
margin stops without moving her hands
from
the
keyboard.
To
change the margin, the operator
must
follow four steps:
position the
carriage
at
the existing margin; then depress the
margin set button; move the carriage to the desired position
with
the
button
held
down; then release the button and check
the position
by
operating the carriage return.
The front end
ofthe
margin set
key
lever has a bottom lug
with
an angular camming surface
that
contacts the carriage return'
key
lock
(Fig~23).
The upright extension on the
rear
of
the
key
lever receives the adjustable clevis on the margin set
link.
The rear
of
the
link
is
attached
to
a lever on the margin set
shaft.
The right end
ofthe
shoft
is
pivoted on the right side
frame and the left end
is
pivoted on the right-hand motor
bracket.
A rocker
arm
is
attached
to
the left side
of
the
shaft
and contacts a stud on the bottom
of
the margin set
lever.
The margin set bracket has countersunk holes where the
chamfered ends
of
the margin set lever hub
contact
the'
bracket.
The bracket
is
held to
the
inside
of
the rear frame by two
screws, one
of
which goes through the motor
bracket.
Earlier
brackets did not extend down as far on the
rear
frame and did
not have countersunk holes for the hub
of
the set
lever.
Prior
to
the use
of
the
screw
and
stop
nut,
a pin and two
C-clips
were used
to
mount the set lever on the
bracket.
The changes
were designed to
eliminate
side play
in
the margin
set
lever.
(Operation)
When
the
margin set
key
lever
is
depressed, its bottom lug
cams the
key
lever locking bar into a position
that
locks
an
operations
except:
backspace,
space bar, shift and margin
release.
This protects
the
margin set mechanism
from
damage
by
carriage
return
or
tabulation while setting margins. The
upright extension on the
key
lever pulls
the
margin
set
link
forward
so
the
lever on the margin set shaft rotates forward.
The rocker arm on
the
margin set shaft moves the bottom
of
the
margin set lever
to
the
rear.
The margin
set
lever rotates about
its fulcrum
point,
and
the
front end
of
the lever
is
lowered.
With the
carriage
at
either
margin, the margin
set
lever will
contact
the
margin stop and lower it
farenough
to
disengage
it
from
the
margin
rack.
With the margin. set keybuttoh
held
down,
the
carriage
may be positioned by using the space
bar,
backspace,
or carriage' release levers. The new position
of
the
carriage
wi
II
also be the new position
of
the margin stop
after
releasing the
margihset
key
button.
Carriages longer than 12" require one
or
more
center
supports
attached
to
the
margin rack to make the rack
rigid.
These
center
supparts obstruct the travel
of
the margin stops. Margin
setting is therefore restricted
to
an
area
bounded by a margin
rack
center
support and
the
extreme left
or
right margin.
MARGIN
RELEASE
Margin
release
provides tlie,operator with a means
of
releasing
the
carriage
from
the restriction
of
either
the left
or
tight
mar-
gin stop without moving the stops. Margin release is used
to
lower
the
margin control lever enough
to
allow
the
margin
10
stops
to
pass. This permits additional
carriage
travel
from
the
position
of
the
set
margin stop to the
carriage
final stop, yet
retains the margin stop setting for further use.
The
margin
release
key
button
is
attached
to
the front end
of
a long
key
lever
that
extends back to the
tab
actuating
lever
on the governor control bracket assembly
(Fig.
24).
The mal'-
gin release
key
lever does not extend into
the
front guide
comb. A shoulder
screw
mounts the
key
lever
to
the
poWer
frame and serves as its fulcrum
point.
The motion
of
the
key
lever
is
restricted by the
key
lever fulcrum wire within
the'
elongated slot
in
the
key
lever (Fig.
24).
Figure
24.
Margin
Release
Key
Lever
When the
key
button
is
depressed, the
key
lever pivots on its
fulcrum screw. The
rear
of
the
key
lever contacts and raises
the margin release
eccentric,
which
is
attached
to
the
tab
actuating
lever.
The
tab
actuating
lever raises by rotating on
its mounting
rivet.
A hook extension on the
top
of
the
actu-
ating
lever
is
positioned
in
a slot
in
the left end
of
the
tab
lever.
The
actuating
lever raises the left end
of
the
tab
lever,
using
the
tab
lever pivot screw as a fulcrum
point.
The margin
con-
trolleveris
lowered by this
operation,
as
it
is
a part
of
the
tab
lever assembly. The margin stops may now pass
over
the
margin control leve.r.
Earlier machines used a different
key
lever arrangement which
required more force on the
key
button 0 Depression
oithe
key-
button raised the rear end
of
the margin release
key
lever qnd
its link. The link rotated
the
margin release bellcrank which
moved a push rod toward the rear (Fi
g.
25).
The push rod
rotated a small bellcrank mounted on
the
governor control

Tab
Figure
25.
Early
Margin
Release
Key
Lever
bracket.
The
tab
actuating
lever was
riveted
to this bellcrank
and
was raised
by
this
action.
The
balance
of
.the motion was
the
same as
the
present style margin
release.
LINE LOCK
The purpose
of
the
Iine lock
is
to
prevent
the
operator
from
typing
one
character
over
another
when
the
carriage
has
reach-
ed
the
right margin control
lever.
The
operator
receives
a
warning
of
the
approaching right margin when
the
bell rings
approximately
10 spaces
from
the
margin.
When
the
letter
key
levers lock
at
the
margin, the
operator
must
then
decide
whether to complete
or
hyphenate
the
word being
typed.
To
unlock
the
key
baard,
the
line lock
is
released by depressing
the
margin
release.
The
operator
can
then
complete
the
word
or
line.
If
the
operator
has just completed a word as
the
ma-
chine
gees into line
lock,
moving
the
carriage
from
the
right
margin will release the machine
from
the
line lock position.
This
can
be done with
either
carriage
return
or
backspace.
Upper Line Lock Bellcrank
Figure
26.
Line
Lock
Mechanism
11

(Operation)
The right margin stop contacts the large flat portion on the
right end
of
the margin control lever
(Fig.
26). The margin
control lever
is
mounted
to
the
tab
lever assembly by means
of
elongated
slots
that
allows-left
to
i'ighf motion
of
the
lever.
The margin stop moves the margin control leyer to the
left.
A
lug on the left end
of
the margin control lever contacts the
up-
per line lock bellcrank which
is
mounted by a shoulder rivet
to
the
tab
horseshoe
bracket.
The upper bellcrank rotates,
pushing down
the
vertical line lock link which lowers the
hori-
zontal
arm
of
the
lower line
lockbellcrank.
The lower
bell-
crank,
whicb
is
mounted
to
the
left side frame, rotates and
moves the push rod toward the front
of
the machine.
The
front
end
of
the push rod contacts the left end
of
the
key
lever
lock-
ing bar and moves it. under the
tab
and letter key levers (Fig.
27)
The carriage return keylock
is
not moved during line lock.
This leaves carriage return unlocked, and
is
done to permit
the
carriage to be returned to the next writing
line.
lock Bar Fulcrum Wire
paper as the typewriter is
operated.
The paper
is
guided
around the
ploten
by
the
deflector,
and held against
the
platen
-by the
feed
rolls. The feed rolls
are
mounted
to
the
inner
carriage,arid will be covered in
detail
under
"pAPER
FEED".
Theinrie;carriagecontrols
th¢ front.
to
rear position
of
the
platen and
is
moye~
by the
multiple
copy control
lever)Fig.
28}. This
leverrotOtesa~haft,
called
the platen guide
shaft.
This shaft includes ecceritrit.'collars
that
work
against parts
mounted
to
the
outer
carriage
"cmd
cams the entire inner car":
riage forward
or
backward.
Th.e
firsf three positions move the
carriage less than the last two, affording a finer initial
adjust-
ment.
The inner carriage
co~sists
of
the following (Fig. 29):
left
and'
right platen guide
plates,
platen- g!Jide shaft,
fel;ld
roll release
camshaft,
paper
bai/pivot
shaft and the paper
table
tie-rod.
Other
parts on the inner c\Jrriage
wi
II
be
c:;overed
under
their
respective mechanisms.
The_
platen_guide
plates
cire
mounte.d to the
outer
carriage
in
a manner thcit allows
them to move front to
rear.
They
are
spring-loaded to the
rear
to
eliminate
any
play.
The left platen guide
plate
has one
extra
bearing point
o,n
the outer carriage
to
obtain additional
stability
for the line space mechan-ism. Earlier machines used
a carriage side frame
eccentric
nut as a third bearing point for
the guide
plates,
and the plates were not spring
loaded.
Paper Release lever
Figure
27.
Une
Locking
Bar Eccentric Collar
The operation
of
margin release lowers the rrorgin control
lever
and
allows it
to
restore to the right, due to the tension
of
the
tab
check lever spring, and assume its rest position.
The spring load on the
key
lever locking bar restores the line
lock mechanism
to
its rest position. Moving the carriage to
the right a
Iso
permits the margin control lever to return
to
its
rest position and
this,
in
;turn, allows the restoration
of
a11
line lock parts.
The
letter
key
levers can
be
locked by the
key
lever
locking'
bar
in
one
of
two positions. When the
kElY
lever
is
in
the rest
position, the locking bar moves underneath a locking lug
on
the
key
lever, and prevents the depression
of
any
key
lever.
Should
the operator have a
key
lever depressed as the line lock
is
actuated,
the locking bar
wi
II
move over the
lop
of
the
lock-
ing lug and
the
key
lever
will
be locked
in
the depressed
po"-
sition.
One
piece
repeat/non
repeat
key
levers
are
made
without a locking lug to prevent
their
being locked
in
the
de-
pressed, or operating position'. This feature prevents possible
damage to the paper
from
continued repeat
action
at
the right
margin.
CARRIAGE
AN D
RAILS
The basic purpose
of
the carriage is to support
aR.d
position the
12
Figure
28.
Multiple
Copy
Control
The vertical motion of the
platen
is
eliminated
by the
platen
latches
that
~otate
over
the
top
of
each
platen
bushing and
hold the bushing down against the end
plates
of
the outer
car-
riage {Fig. 29}., The
outer
carriage consists
of
the carriage
bed,
and the two carriage end
plates.
These parts
are
welded
together
to
-form
a
bax-type
carripge'construction that gives
maximum rigidity
to
the
carriage.
The carriage bed
nas
two rows
of
milled
teeth
running its full
length.
These provide motion for the rotation
of
the
staw
wheels
in
the plastic truck assemblies (Fig.
30).
Each truck
coritains four steel rollers
that
engage
the
carriage
ways and
the
rai
Is
to allow,free motion
of
the
carriage
to
the left and
right.
The truck
rollersfit
into holes
in
the truck housing.
These holes have smalt bosses
that
retain the rollers
and
keep

Platen Retaining Plate
Figure
29.
Carriage
Parts
them
from
falling
out
when
the
truck
is
removed
from
the
ma-
chine.
Early truck rollers used nylon retainers
that
snapped
into recesses in
the
truck.
The ten tooth star wheeI
is
pinned
into
the
truck.
Motion
of
the
teeth
on
the
carriage
bed rotates
the
star
wheel,
which also meshes with similar
teeth
on
the
rail,
and
the
star
wheel moves
the
truck assembly. The
car-
riage moves
at
a
ratio
of
2:1 with respect to the truck assembly.
The bottom
of
each
carriage
end
plate
has an extension
that
strikes
the
carriage
fina I stop, mounted underneath
the
front
rail,
when the
carriage
is
moved beyond
the
left
or
right
mar-
gin stops. The
carriage
final stop may be depressed
against
a spring load when
carriage
removal
is
desired.
Carriage
re-
moval
is
made possible, without disturbing rail adjustments,
as
the
carriage
ways and rails have milled
teeth
their
full
length
(Fig.
31).
The front and rear rails
are
mounted on
the
power frame
casting.
Starwheel meshes with teeth
I_
on top of the carriage
way
~
__
~_.----
...,
""w
(}i--~;
-~~--~-
Starwheel meshes with t8eth
on boHom
of
the ra
iI
Figure
30.
Carriage
Truck
Assembly
13
Carriage
motion
is
involved in many operations
of
the
machine.
Typing,
space
bor and
tabulation
cause
carriage
motion to
the
left.
Carriage
return,and backspace cause
carriage
motion to
the
right.
Hand
carriage
release can
be
used by
the
operator
to
move
the
carriage
in
either
direction.
To
do
this,
the
operator
depresses
the
left
or
right
carriage
release button and
moves
the
carriage
whi
Ie
holding down on
the
button.
The
button rotates
the
carriage
release
lever,
which
is
mounted
on a stud on
the
carriage
end
plate
(Fig.
28).
The
lever
pushes
the
carriage
universal bar toward the
rear
of
the
machine.
The
universal bar runs
the
full length
of
the
carriage
and
is
mount-
ed
to
the
carriage
end
plates.
The universal bar
contacts
an
upright I
ug
of
the
pawl
re
lease lever (Fi
g.
32).
The pawl
release lever
is
mounted to
the
rear
rail by an
eccentric
and
screw.
It has a lug which extends behind
the
rear
rail and
actuates
the
backspace inter
lock.
It has
another
I
ug
under-
neath
the
raiI
that
rests between
the
escapement
pawl and
the
escapement
rack.
This lug pulls
the
pawl
from
the rack when
the
pawl
release
lever
is
rotated.
Release
of
the
carriage
re-
lease button and restoration
of
all
release
parts to rest allows
the
pawl to return
to
the
rack.
The
other
parts on
the
carriage,
such as
paper
feed
parts,
tab,
margin and escapement racks
are
covered under
their
respective
sections.
The
rear
rai I provides the mounting for many parts
that
control
carriage
motion and
position.
These will
alsobe
covered under
their
respective mechanisms.
The number
of
truck assemblies, writing line and
paper
size
vary
with
carriage
length in
accordance
with
the
following
.chart.

Writing Line
Carriage
Length Number
of
Trucks Between Margin Writing Line Paper Size
Stops (Maximum)
12"
4
10.4"
11.25"
11"
16" 6
14.4"
15.25"
15"
20" 8
18.4"
19.25"
19"
24"
10
22.4"
23.25"
23"
30"
12
28.4"
29.25"
29"
lH
Rail
Support
Figure
31.
Carriage
and
Rails
Intermediate
pawl
release
lever
.trikes
this
Escapement
engaged
in
Pawi
release
lever at
rest
Tab lever .trikes,hi.lug
Figure
32.
Pawl
Release
Lever
PAPER
FEED
The paper feed mechanism
is
a part
of
the carriage assembly.
Paper feed and paper release
are
the two bosic functions
of
this mechanism.
The inner carriage provides the mounting for the paper feed
mechanism
so
that
when the inner carriage
is
cammed front
or
rear by
the
multiple copy control mechanism, the paper feed
14
and release parts will move with the
platen.
The paper feed mechanism
i"s
made
up
of
many parts;
all
of
which
aid
in the proper feed
or
release
of
the
paper.
Paper Feed
To
begin the
operation,
the typist places the paper against
the
rear
paper
table
(Fig. 33). This
table
is
a part
of
the
car-
riage and
is
to the
rear
and above the
platen.
It
is
supported
Rear
Pressure
Lever
Figure
33.
Paper
Feed
Mechanism

Rear
Pressure
Lever Feed
Rof.(
Tension Springs Carriage Release Universal
Bar
j,
...
..".,-~
...
Front
Pressure
Lever Platen
Guide
Shaft
Center Support
Shaft Eccentric
Figure
34.
Feed
Roll
Mechanism
on
the
paper
bai I pivot shaft and
the
paper
table
tie
rod.
Arms
from
the
front paper
table
serve as latches to hold
the
rear
paper
table
to
the
tie
rod
shaft.
As
the
paper
is
inserted into
the
machine,
an
adjustable
guide mounted on
the
rear
paper
table
serves to position
the
paper for its left margin
position.
Next
the
paper
contacts
the
rear
rolled edge
of
the
deflector
(Fig.
33).
This
edge
guides
the
paper into
the
"V" formed by
the
rear
feed rolls and
the
platen.
The bottom
of
the
deflector
contains lugs
that
stradle
the
feed roll release cam shaft and
serve to position
the
deflector.
Support lugs on
the
rear
pres-
sure levers control the distance between
the
deflector
and the
pl~ten.
Sixteen inch and longer deflectors
are
connected
by
a rod which
is
spot-welded
within
the
rolled
edge.
A single
piece
deflector,
designed to faci Ii
tate
manufacture
is
in
all
16" machines above serial number
613547.
Horizontal
and
rotational
movement
of
the
single
piece
deflector
is
pre-
vented
by two formed I
ugs
on
the
rear
of
the
deflector.
These
lugs seat in undercuts on
the
feed roll
release
cam
shaft.
The
former
spot-welded
lug-type
deflector
wi
II
remain
avai
lable
for
replacement
on machines prior
to
this
change.
If
it
is
de-
sirable
to
con'vert to
the
new single
piece
deflector
on machines
prior to this
change,
it
will be necessary to
replace
the
feed
roll
release
cam
shaft.
The new shaft
is
interchangable
with
the
former
shaft.
Rotation
of
the
platen
causes
the
paper
to be fed between
the
re~r
feed rolls and
the
platen.
Feed rolls
are
spring loaded
against
the
platen
and are rotated by
their
friction on
the
paper
or
platen
(F
ig.
33).
As
the
front
edge
of
the
paper leaves
the
rear
feed rolls, it
is
guided by
the
deflector
unfil
it
moves in
between
the
front feed rolls and
tbe
platen.
Both
front and
rear
feed rolls now hold
the
paper
firmly agairist
the
platen
and
insure its rotation wifh the
platen.
Feed
ro
II
pressure
is
supplied by
applying
a twist to flat torsion
springs
(Fig.
34).
The ends
of
these springs
are
mounted in
15
slots
in
plastic
bushings which
are
molded
to
the
pressure
levers.
Feed
ro
lis mount on shafts whose ends mount in these
pressure levers. Feed roll pressure
is
determined by
the
amount
of
twist put into
the
spring by
their
adjusting screws.
The ends
of
the
springs
attempt
to
rotate
the
plastic
bushings
and pressure levers, and in this manner supply a constant
up-
ward pressure to
the
feed
rolls.
The pressure
lever
bushings
are
mounted in holes in
the
feed roll
cradles
and
the
cradles
are
mounted to
the
feed roll
release
cam shaft and
the
platen
guide
shaft.
Left
to
right motion
of
the
cradles
is
restricted
by a feed roll
center
support on
one
side,
and a spring
clip
on
the
platen
guide shaft on
the
other
side.
Left
to
right
motion
of
the pressure levers
is
restricted by
the
cradle~
which
are
held on
the
plastic
bushings by spring
clips.
Each feed roll
is
molded
to
a hub and two hubs
are
mounted
on
each
feed roll
shaft.
This arrangement gives maximum
bearing surface for
the
rotation
of
each
feed
roll.
The feed
roll shaft
is
mounted
in
"D" shaped holes
in
the
pressure levers.
These holes
keep
the
shaft
from
rotating.
The shaft has a spring
loaded plunger
at
one
end
for
ease
of
removal and
replacement.
Feed roll hubs and rear feed roll shafts have been redesigned
to
reduce
the
length
of
the
feed roll hub by
approximately
1/4
inch.
This
change
appears
on machines above serial
num-
ber
519557.
Feed rolls have been
placed
in
the
center
of
the
hub
(Fig.
34) and
the
hub assemblies
are
retained
on
the
shaft
by two
adjustable
clips which permit adjustment to
reduce
end
play
of
the
feed rolls to a minimum. The clips
are
also used
to ho
Id
the
shaft in
place
in
the
rear
pressure
levers.
The
front feed rolls
are
sti
II
mounted on
the
shaft with
the
spring
plunger.
It
is
necessary
to
use this shaft
in
order
to
hold
the
front pressure levers in
place.
The feed roll
center
support
is
mounted on
the
carriage
bed
and helps
to
position
the
feed roll
cradle
assemblies
(Fig.
35).
In
addition,
the
center
support provides rigid support for
the
feed roll release cam shaft and
the
center
platen
guide
shaft

eccentric.
Sixteen inch and longer machines use the
center
support as a mounting for the margin rack
center
support.
As
the paper rotates further, it
is
guided upward by
th~
front
extensions on the
deflector
and the front paper
scale
(Fig.
33).
Margin Rack Cen/er.
Support
Feed
Roll
Release Shaft
Figure
35.
Feed
Roll
Center
Support
The front paper
scale
is mounted on the platen guide shaft.and
is
spring loaded toward the platen by a coi I spring mounted
around this
shaft.
The
scale
contains calibrations which
cor-
respond
to
the
pitch
of
the machine.
Dust
Cover Adiusting Screw
Figure
36.
Line
Gage
Card
Holders
Above the front
scale
and immediately below the writing line
•
are
the line gage card holders (Fig.
36).
These assist
in
hold-
ing the
paper,
and more "specifically, cards
to
the platen
in
the
writing
area.
The line gage card holders
are
mounted
to
the front rail dust
cover,
which
in
turn
is
mounted
to
the front
'rail.
The card holders also have a
scale
calibrated
to
the
.
'pitch
of
the
machine.
Later machines
uSe
an offset line gage
6ard holder for the purpose
of
reducing the possibility
of
under-
printi
ng
on the
paper.
The two screws
that
mount the card holders also mount the
16
'indicator
pointer
(Fig.
36)
• This pointer
is
used .to
indicate
the position
of
the
carriage
in
relation to
the
type
guide.
The
operator
reads the front scale ,calibration
indicated
by the
pointer
to
check
the
carriage
position.
'
Above
the
writing line the paper
is
engElged by two
or
more
rubber rollers which
are
m<:>lmted
on
the
paper boil (Fig.
37).
,These rollers hold the paper to the
platen
above
the
writing
nn~so
as to reduce the possibility
of
over
printing on the
paper.
The rollers
also·feedthe
pop-er
away
from
the operator
so
the writing line is plain
Iy
visible.
Bail
Shaft
Figure
37.
Paper
Bail
The 'paper boil has three positions which
are;
above tbe
plate
in
the
raised position,
in
front
of
the platen
in
the forward
position, and against the pla'ten
in
the
operating
position.
These positions
are
made
possible by the use
of
paper baiI cam
levers
to
which
the
coiled bai I springs supply pressure • The
bail arms
are
mounted to the paper bail pivot
shaft,
and
are
free to 'rotate about this mounting. The pivot shaft
is
als9
free to
rotate.
A steeI
ro
Iler
is
mounted on the bottom
of
each
bai I arm and receives pressure
from
the cam
lever.
This
pres-
sure forces the rear end
of
the bai I arm up and the
frc;mt
end,
'including
the
bail rolls, down. The bail rolls
are
free to
rotate
about the baiJ
shaft,
but contain a spring
clip
that
re-
stricts
their
laterial motion, unless
they
are pushed with enough
force
to
over
come the resistance
of
these spring
clips.
When
the bai I
is
moved
from
the forward
to
the
operating
position,
a plastic roller mounted on
each
bai I arm rides
over
chrome
plated
strips
of
metal,
called
bumpers, which
are
mounted on
each
carriage end
cover.
These insure easy operation and
help the bail rolls pull the paper against
the
platen in the
area
of
the writing
line.
.
Next
the paper passes in front
ofthe
front paper
table
(Fig.
33).
Its purpose
is
to
prevent refeeding
of
the copy paper and
can be used as an erasing platform.
The front paper
table
contains two scales;
the
top
is
cal
ibrated
in
inches, the bottom corresponds
to
the pitch
of
the
machine.
(
Thrs
table
provides an
easy
method
of
checking machine
pitch.
Simply count
the
number
of
calibrations on
the
bottom
scale
in
one inch on
the
top
scale.
The
sum
equals the pitch
of
the
machine.
Other manuals for B-1
1
Table of contents
Other IBM Typewriter manuals
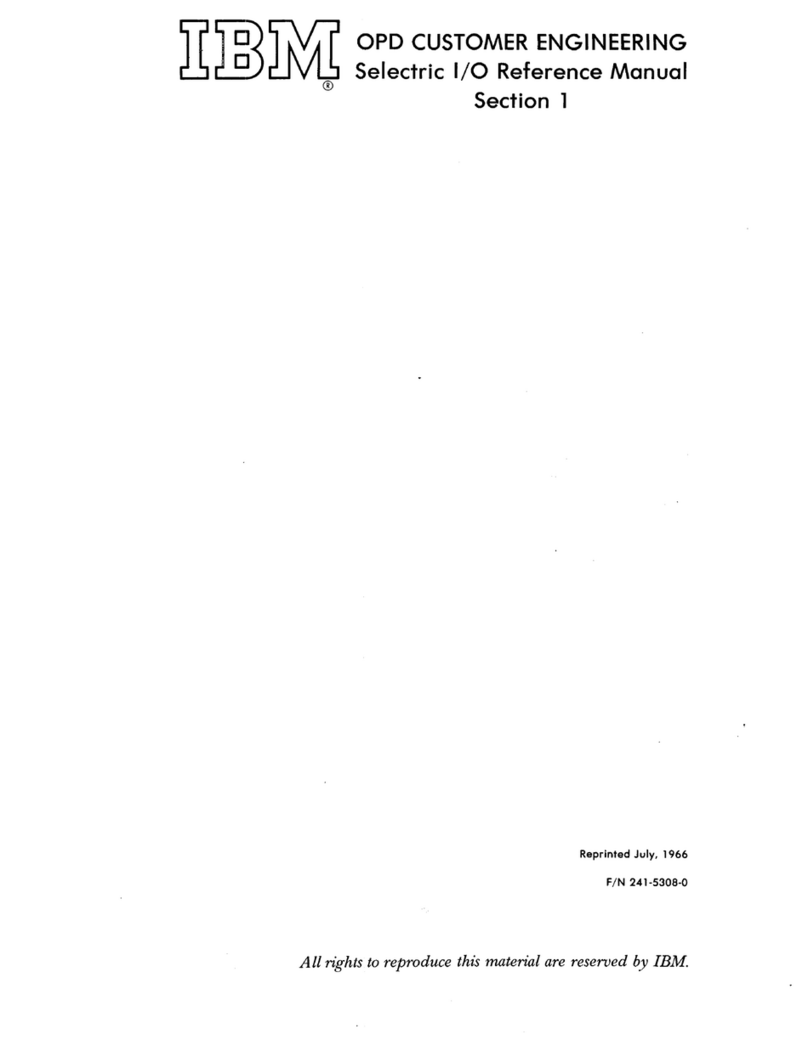
IBM
IBM Selectric User manual
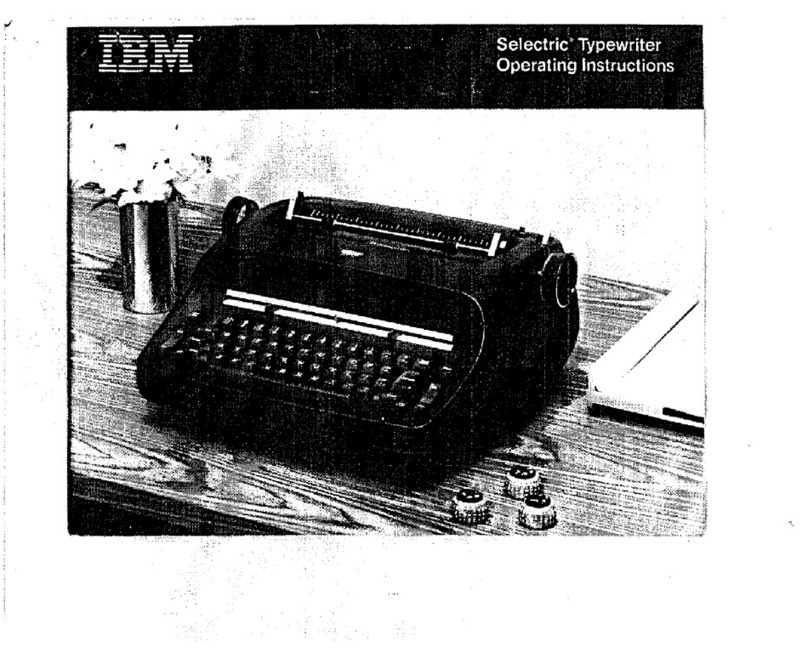
IBM
IBM Selectric User manual
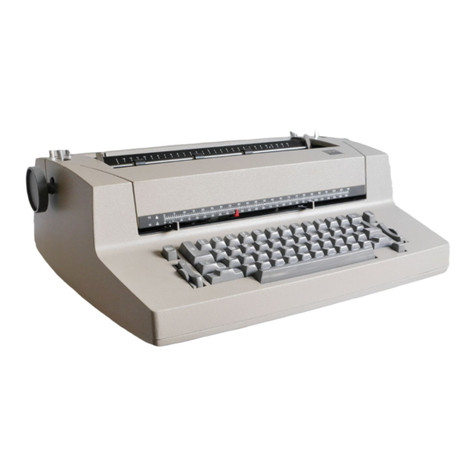
IBM
IBM Selectric II User manual
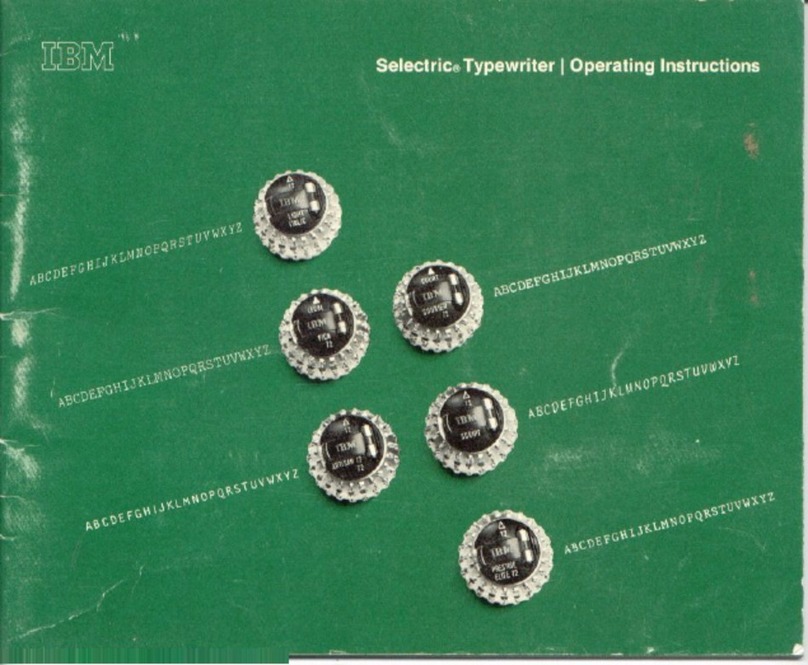
IBM
IBM Selectric User manual
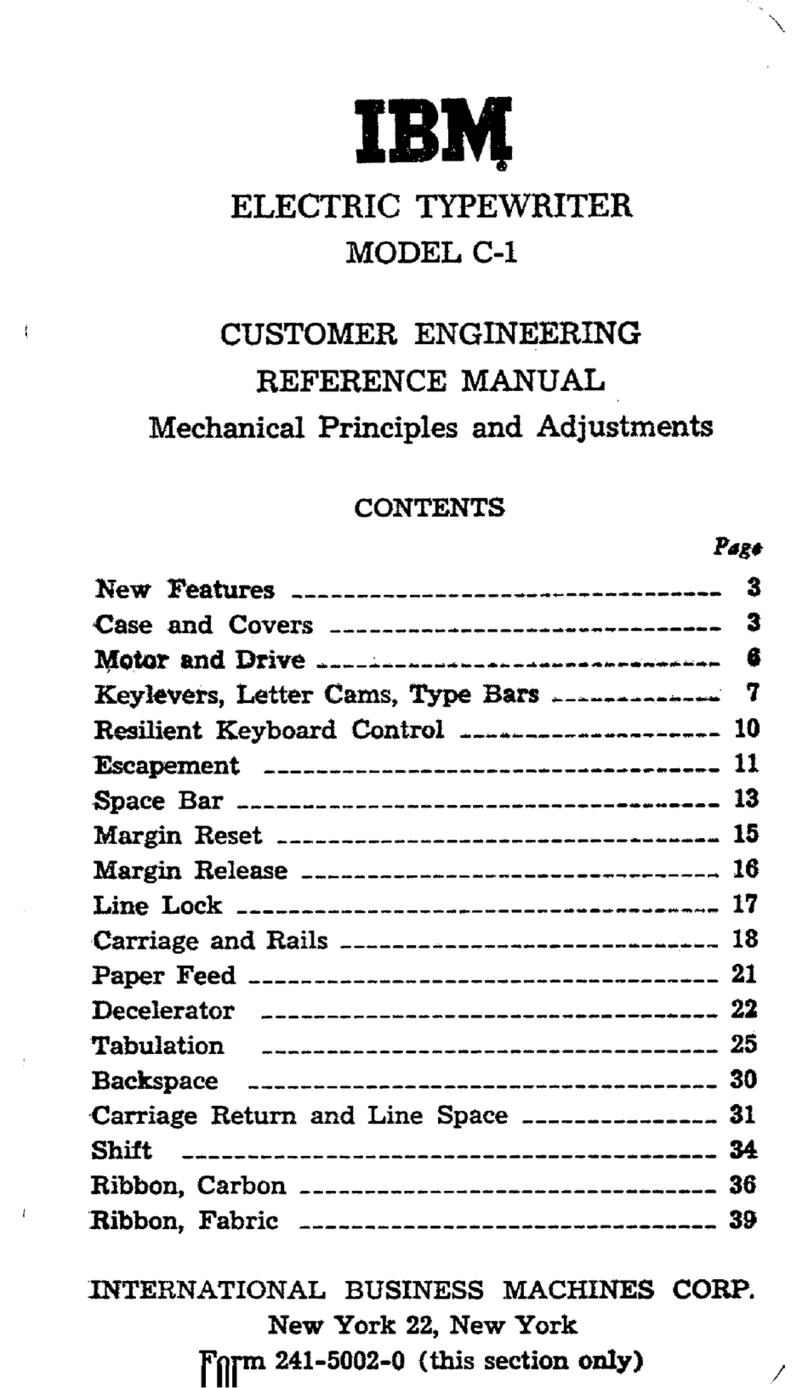
IBM
IBM C-1 User manual
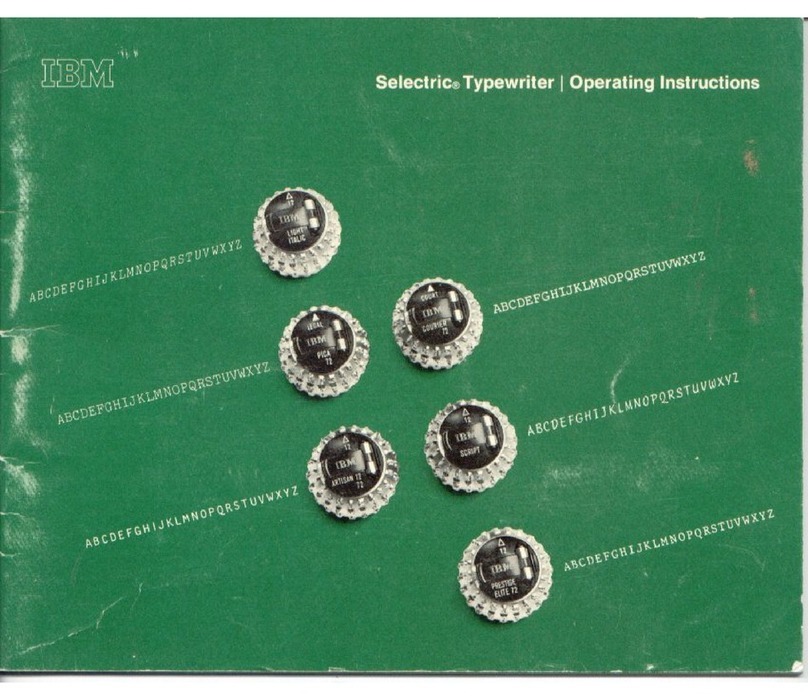
IBM
IBM Selectric User manual
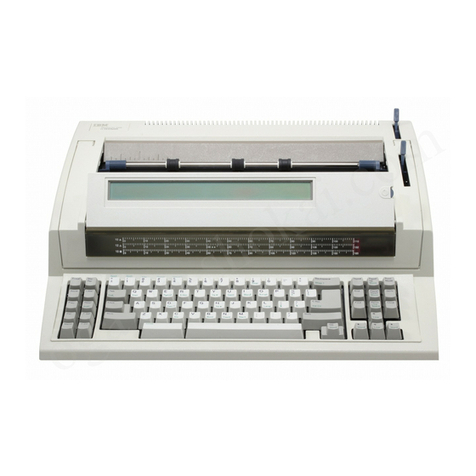
IBM
IBM Wheelwriter 2500 User manual
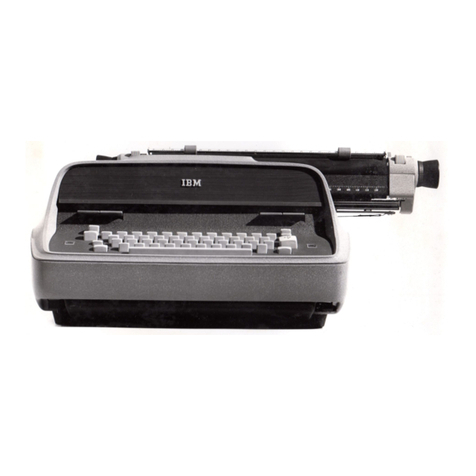
IBM
IBM Executive User manual

IBM
IBM Selectric III - Correcting Selectric III User manual
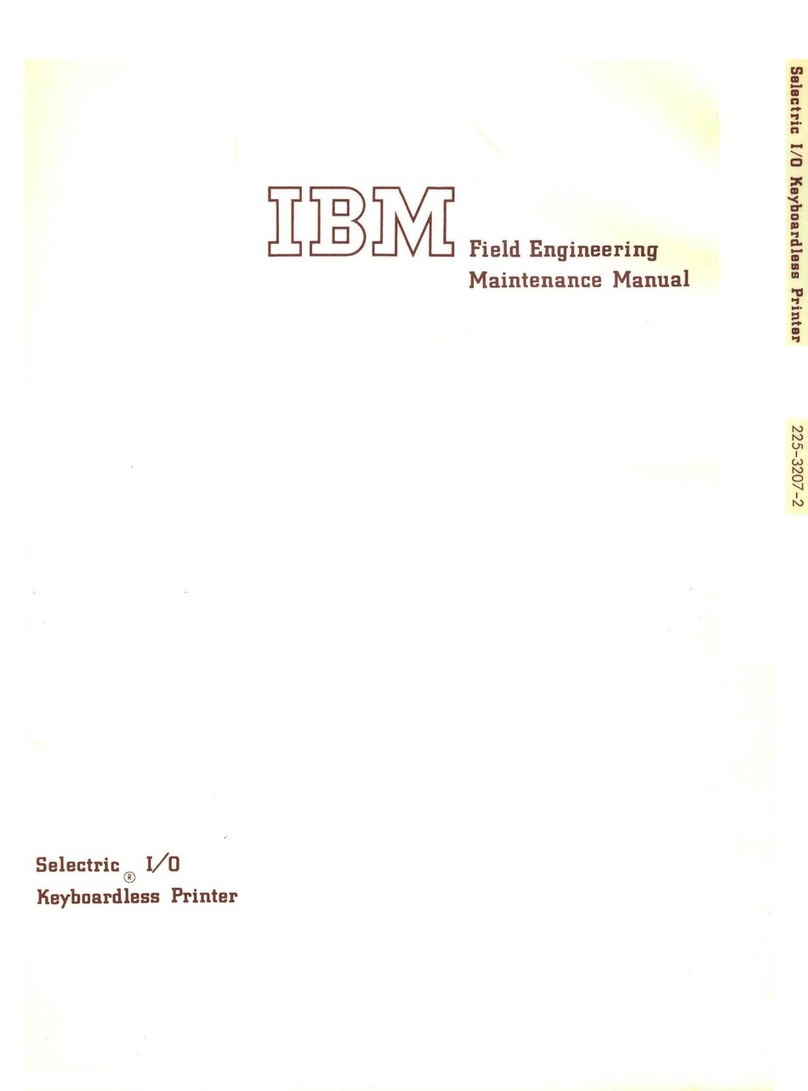
IBM
IBM Selectric User manual
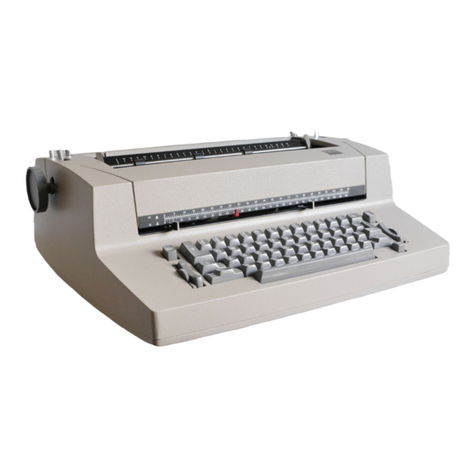
IBM
IBM Selectric II User manual
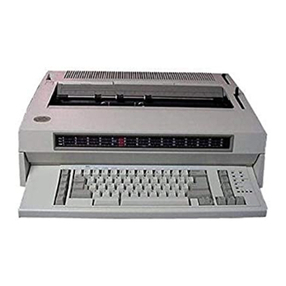
IBM
IBM Wheelwriter 10 - IBM Wheelwriter 10 Professional... Manual
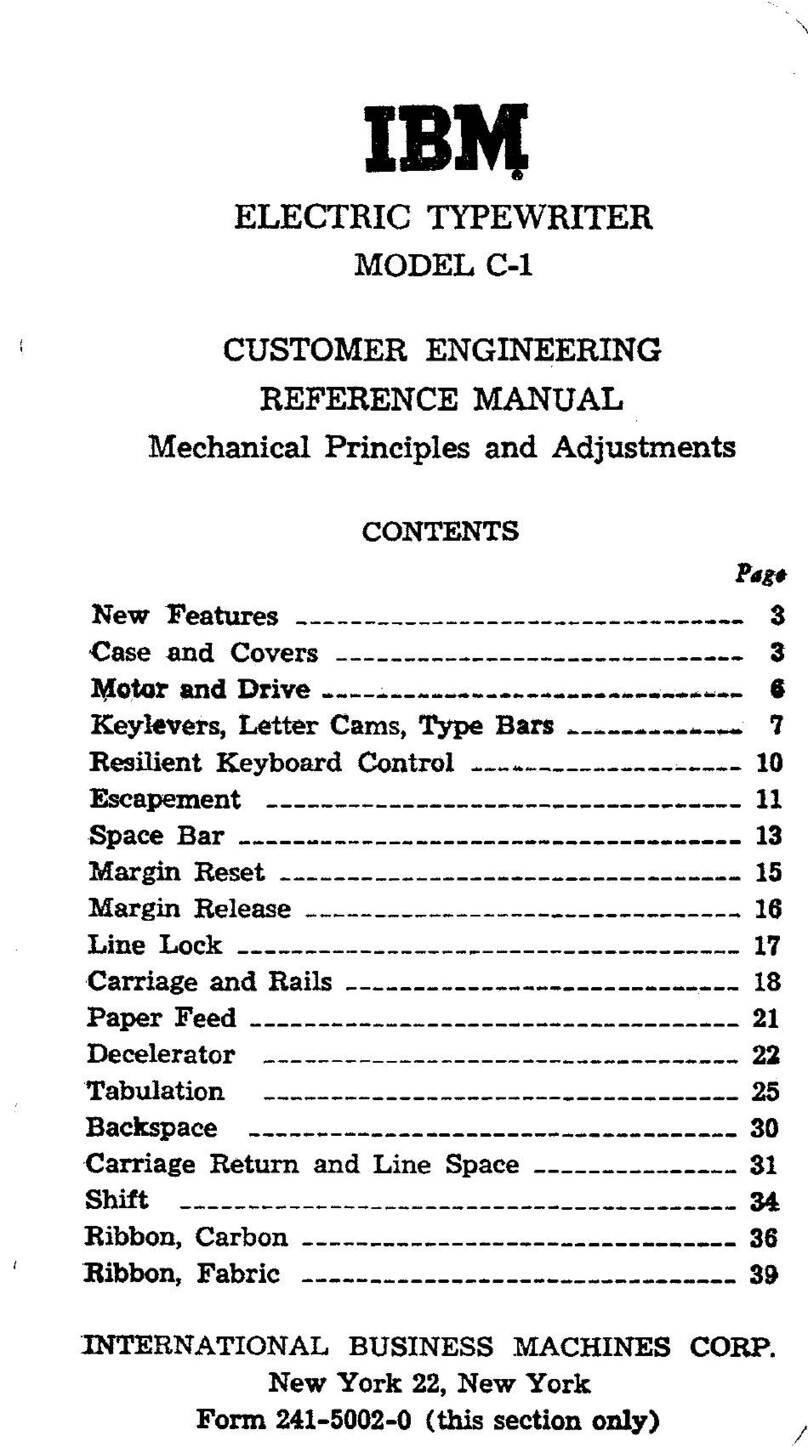
IBM
IBM C-1 User manual
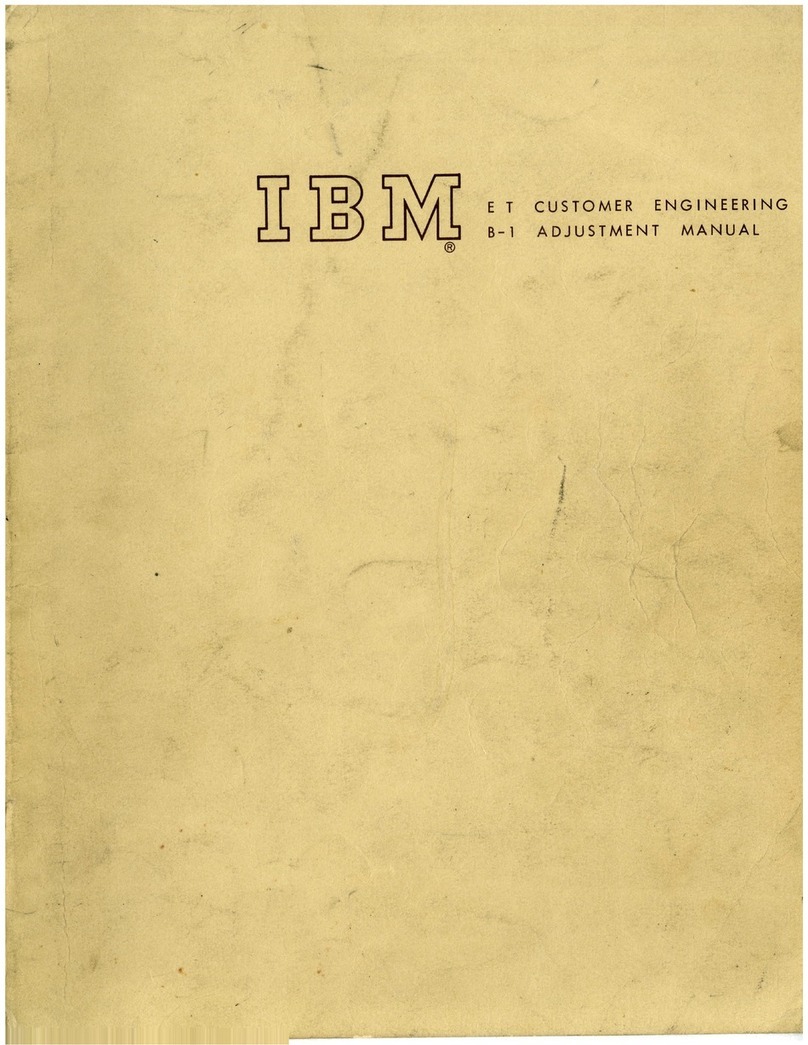
IBM
IBM B-1 Guide
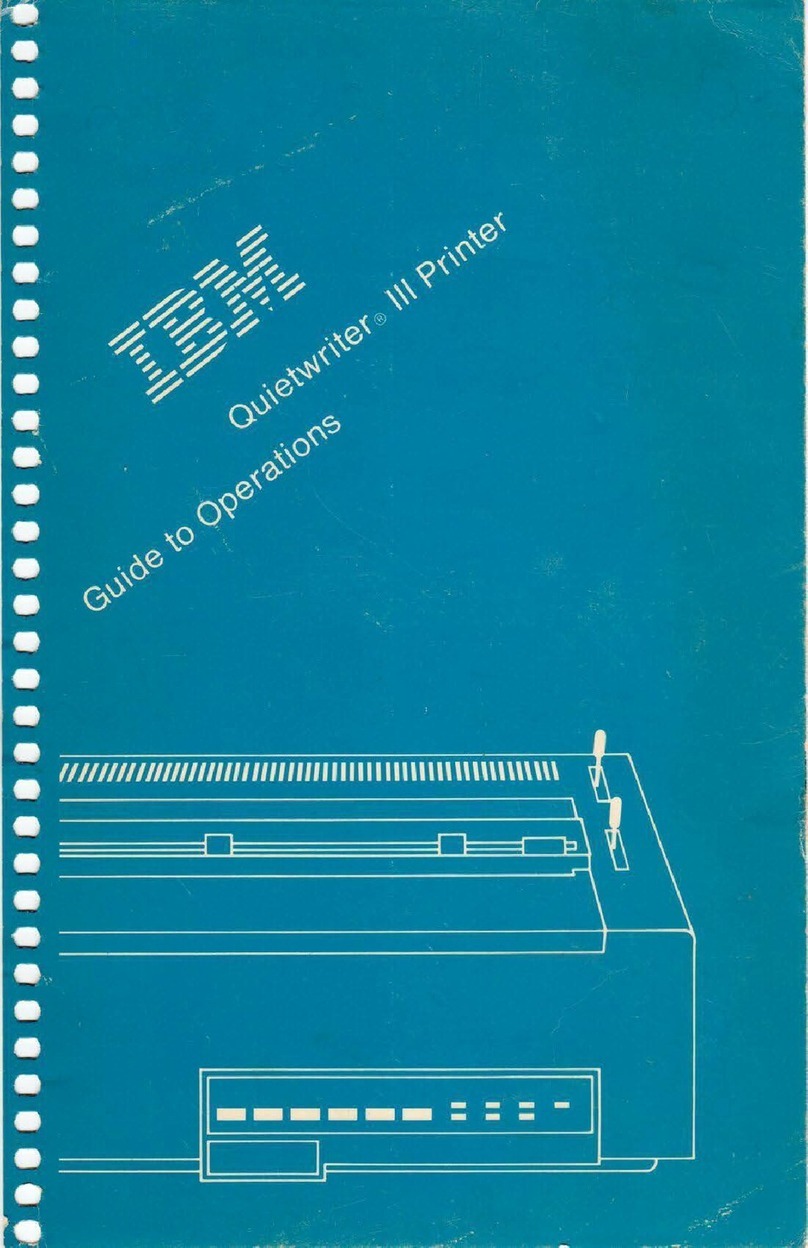
IBM
IBM Quietwriter III 5202 User manual
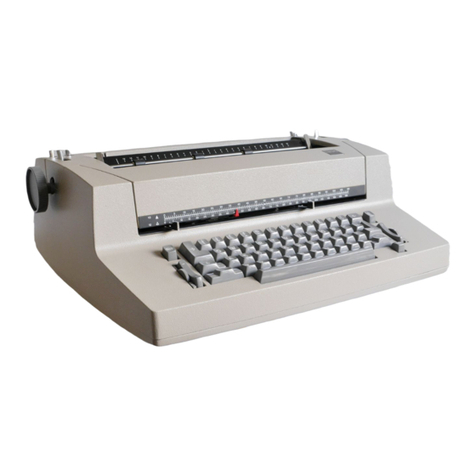
IBM
IBM Selectric II User manual
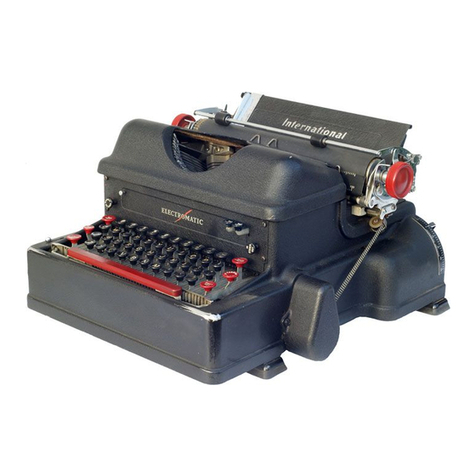
IBM
IBM 01 Operating manual
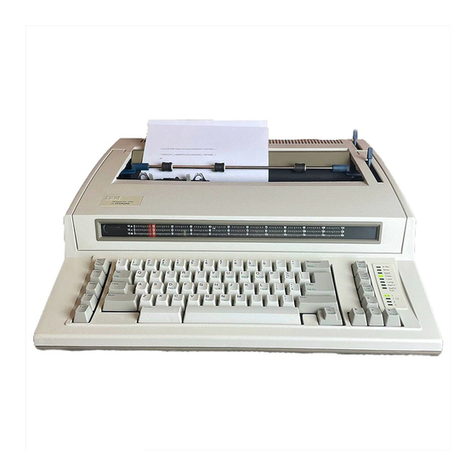
IBM
IBM Personal Wheelwriter 6781 Manual
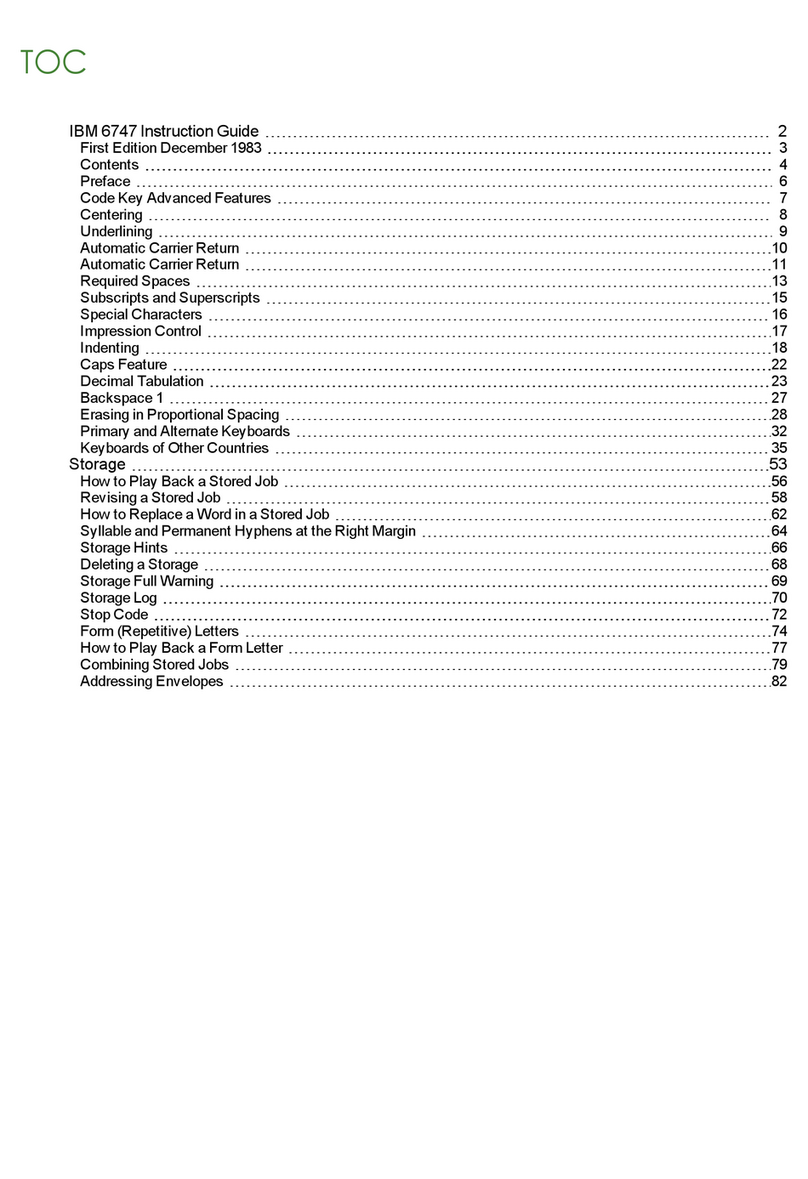
IBM
IBM 6747 Manual
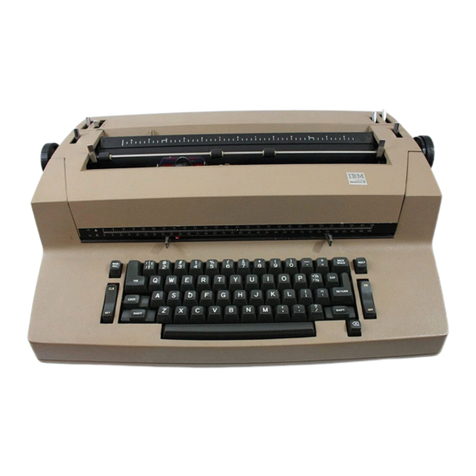
IBM
IBM Selectric Personal Typewriter User manual