IME SF 5P User manual

Page0
OPERATING MANUAL
BLAST CHILLER

Page1
Device »Article number
Type »Part number
SF 5P » 07900
SF 5 N » 07901
SF 6P » 07902
SF 6 N » 07903
SF 10P » 07904
SF 10 N » 07905
SF 20P » 07906
SF 20 N » 07907

Page2
Table of contents
Table of contents Page 2
Preface Page 3
Information about gas safety Page 4
Installation Page 5
Control panel Page 7
Engagement of the operations Page 9
Cleaning and maintenance Page 10
Guarantee / assurance Page 12
Notes on safety Page 13

Page3
Preface
The present instruction appertains to thedocuments delivered with the equipment and contains all necessary information for a
correct service and maintenance of the product: protective film do remove (to make of Abb2)and, that the packing material
according to the valid rules of the country, in which the product is used, non-polluting is disposed.
The user shouldread then through the contained information attentively and keep the instruction in a slightlyaccessible place
for all users authorized to that.
Our product is certain for the professional use and may from that only served by specialists for his functional purpose and
exclusivelygraze
For possible damage, that are to be put down to an inappropriate use of the product, onto a transport with
inappropriate means, onto illicit alterations as well as all steps, that were not considered in this instruction , the
manufacturer does not take over any liability.
• Transportation Pic1
Any product shift may
only with means of transport calm for that
to occur as a lifting truck or
Manual truck, that half the one
Having to exceed product length.
• Unpacking
To attract protective gloves and wrapping
loosen (Pic1)equipment with the aid of a lifting truck
remove lift foot remove and
setting up at the destination.
• Safety
Before the electric supply of the machine must be
guaranteed, that the dates V, Kw N hertz of the stages as
well as the service with the information. On the number plate
(Pic 3) toagree on the reverse page of the equipment
Pic2
Pic3
Before any cleaning and maintenance jobs
always pulling the power plug of the equipment.

Page4
Information about the gas safety
Danger signalling:
-Suffocation
-A fast liquid vaporization can lead to
frostbite
Immediate help efforts:
-In case of inhalation:
Bring That one injured immediately onto the
fresh air and, if necessary, to add oxygen or to
carry out the mouth-to-mouth resuscitation.
Giving no adrenaline or similar substances.
-In the case ofeye contact:
Rinse Eyes with plenty water and carefully at
least 15 minutes long. After that visit a Doctor
for look up.
-Withskin contact:
Beats immediately with plenty water wash
and to take off impure lining immediately.
Toxic information:
-Local effect
A narcosis effect can induce a concentration
which is basically above the boundary value.
The inhalation of highly concentrated and
decomposing products canbreath need (Water
lung) for the result have.
-Specific effect:
A fast liquid vaporization can lead to
frostbite.
Fire measures:
-Adequate fire extinguishers x-arbitrary
-Special dangers: Increase of pressure
-Special means: Chilling with water.
Measures with accidental gas escape:
-Individual precautions
Bringing the personnel into safety rooms.
Anticipating an adequate aeration and
employing own protection agents.
-Evaporated environmental precautions
-Evaporated cleaning means
Handling:
-In the working spaces a sufficient change of
air and/ or Gas vacuum procedure-to carry
out . Itself is recommended to use only well
ventilated rooms.
Information of ecological kind:
-Okotoxic effect
Pentafluorine ethane (R125): global heating -
potential of the halo carbides; HGWP;
(R l 1 = 1) = 0.84.
Ozone impoverishment potential;
COP; (R l 1 = 1 ) = 0.
Tetrafluorethane: (R134a): ): global heating -
potential of the halo carbides;
HGWP; (R11 = 1 ) = 0.28.
Ozone impoverishment potential;
COP; (R 11 = 1) = 0.
Trifluorethane: global heating -potential of
the halo carbides; HGWP;(R11 = 1) =1,1.
Ozone impoverishment potential;
COP; (R11 = 1 ) = 0.
Disposal references:
Recycling the product. If this should not be
possible, the elimination in one furnished for
that and to the receptionand neutralization of
gases and other poisonous workmanship
products must authorize plant are carried out.

Page5
Installation
The installation may only be from specialists under
observation of the legal accident protection
definitions of the valid rules of law of the country in
which the device is used l at this has the specialists
the task, to check possible fire prevention rules.
Setting up the machine at the planned place and letting
in this case a sufficient open space (at least 10 cm)
between the device and possible walls or obstacles
which could prevent the correct air circulation(Pic 4)
Pic4
Make that freedom of movement is available
sufficiently for the maintenance operations
The device may not be in rooms with small air
circulation into the full sun with high temperature
levels or into the proximity of heat sources are set up
(Pic 5)
Pic5
Aligning the device with the aid of a spirit level and
through the arrangement of the feet with adjustable
elevation
(Pic 6)
Surrounding temperature must not exceed that
boundary 32°C since the correctoperation can not in
addition be guaranteed to the machine
In case of special placements the plumber must take
into account the possibility to equip the product with a
covering.
(Pic 7)

Page6
• Electric supply
The equipment must connect onto the mains voltage by
means of one error current-safety switch, under
observation of the valid rules of law
the country's, in which it fits and( Pic 8) is connected.
The earth wire must be connected onto anearthing
systemPic 8
Drain
The device is supplied with a receptacle to the
absorption of water of condensation. As an alternative
to that the drain can be connected onto the connector in
this connection at the ground
(Pic 9)
Control checks
If during the transportation the equipment was not in
upright situation, at least four hours must pass by until
the machine can be turned on
Before the engagement the following controls carry
out:
Checking the connection to the water pipe during the
operation through the regulation of the pressure valve.
Checking the correct circulation of the water of
condensation. The standard pressure values check The
Electric Supply The Current Consumption check
Checking possible gas escapes through installation-
conditional questions or punches. A complete cold or
freezing -cycle carry out.
The customer must have received the necessary
information about the correctuseof the product. The
installation and setting-up of the equipment may be
carried out only by the specialists that together with the
customer the assurance certificate will sign.
THE manufacturing firm is not liable for possible
thing or person damage, that were caused through
an unproper installation.
• Protection appliances at the device
Door –Micro switch
Safety pressure switch stops the apparatus operation
near doorway
Turns on at over and lower pressure in the cooling
circuit, thermal relay compressor and engine fan turns
on in •case of overload and incorrectoperation
• Heart sensor
Must be introduced in the middle (the heart) of the
product, consider, that not spiked the needlepoint lace
the product or osculated the receptacle (Pic 10)
Before every use the cleaning of the probe is to be
recommended to avoid impurities flat receptacles, no
lids or insulating sheets employ since in this way
through the direct contact with the cold air the cool
times are reduced. For a fast cooling receptacles with
3,5 kg are to product as well as to a fat property of 8
cm. or at a fast deepfreeze 5, advisable, cm
Storage
In the cold producer the product is homogeneous and
not concentrated distribute. It is indispensable that the
products of the room temperature to be chilled or to be
chilled deeply remain criticized as little as possibly,
around in this way a greater tenderness of the
Food's achieve.
It recommends, not to introduce foods with a
temperature ofunder +70C° into the cold producer the .
The freezing-property conducts during the fast cooling
+70°C -+5°C and +70°C, l8°Cduring the deepfreeze.
After the cooling or deepfreeze the product with a deck
is, a protective foil or to keep under pressure
hermetically.
The chilled products are kept in a refrigerator at +4C,
the deep-frozen products in a deep freezer at-20°C
The cold producer is not a normal refrigerator !

Page7
• Operations
Fig. 11
• Patching panel information
START / STOP press button
Compressor Led
Temperature&timedisplay
display
Cooling press button
Deepfreeze press button
Storage press button
Alarm Led
Time press button
Led exhaust wheels
Pin probe Led
Thawing course Led
Programming Led
ON / OFF press button

Page8
START / STOP
Switch the chosen cycle at switched off machine
COOLING (+70°C -+5°C )
Prepares with plus temperature or anyway 0°C approaches the
machine the cooling in front of. THIS IS TEMPERATURE -WORTH
through a programming parameter variable.
DEEPFREEZE (+70°C --18°C )
Prepare with minus temperature the machine for the cooling. This IS
TEMPERATURE -WORTH through a programming parameter variable
STORAGE
Prepare the machine for the preserving of the foods.
If neither the coolingpress buttonnor deepfreeze were pressed, the
machine works just the same as a normal refrigerator does, the
storage temperature can be prepared with regard to those ones for
that in the planned value (middle or small temperature) through
fitting keystroke (that in this connection Led lights up). If, however,
the cool course is prepared already through this keystroke only to
light up the Ledof the temperature of the coolcourse preset
concerningthat.
Heart sensor
Announce the temperature either in the cell or in the product heart. The lighting
up of the corresponding Led announces the chosen option.
TIME THAWING COURSE LED
Switch off the pin probe. At reached time end; that through
the parameter in this connection was prepared, one goes from
to the cooling to the storage/preserving about. The display gives
the still missing time to at the end of the cool course at Through
Keystroke "pin probe" becomes some seconds
take one of the two announced.
ON/OFF
The reversing gear turns on and from. The EWFC 1000 stands
always turnedly also in the eliminated state under tension
COMPRESSOR LED
Announces that the compressor in operation is. A possible flashing
shows the switch on-wait state at.
FAN ROTOR LED
Announces that the exhaust wheels in operation are. A possible
flashing shows the switch on -wait state at.
PIN LED
If at, the pin is turned on: if from, the pin is switched off since the
time circuit function was chosen. A flashing announces, that the pin
is in the wait state, meant a flashing after a certain space of time after
the start of the cooling course that the pin was not introduced in the
product and the control is Time Switched automatically.
THAWING COURSE LED
This system warning light announces, that the thawing course
became turned on.
PROGRAMMING LED
Flash during the programming onto.
ALARM LED
Led combined with alarm repetition exit. Near alarm probe
turnedon.
• Functional references
During the device engagement becomes through
keystroke thatone
Requested selection of the desired operation. On the display the
information "SEL" appears and that following Led's
light up.
Cooling
Deepfreeze
Storage

Page9
Engagement the following operations through respective keystroke possible:
1. Cooling (+70°C/+3°C)Press button Press button cycle start
2.Deepfreeze (+70°C/-18°C) Press button Press button cycle start
3. Storage (+3°C) Press button Led at Press button cycle start
4. Storage (-18°C) Press button Led at Press button cycle start
5. Cooling (+70°C/+3°C) storage + (+3°C)Press button +Button Press button cycle start
6.Deepfreeze (+70°C/ 18°C) storage + (-18°C)Press button +Button Press button cycle start
Course of events manner
The food into the cell pursue pin probe into the middle of the product
to be chilled insert.
ON/OFF takes about the press button
turning on On the display
theSEL information appears and
the following Led's to light up onto.
Cooling
Deepfreeze
Storage
There are three choices.
Cooling in the product heart
(advisable)
Pressing press button to
cooling
(if after the cooling the foods
) press button are supposed to be lain
down
Pressing storage .
Cycle through START/STOP keystroke
to turn on ON the display appears
the one measured from the probe
Temperature level.
Deepfreeze in the product heart
(advisable)
Pressing press button to deepfreeze
if after the deepfreeze the foods
) storage press button are supposed to be lain down
press.
Cycle through START/STOP keystroke
turn on and on that
Display appears to that of the probe
measured temperature level.
After the cooling and deepfreeze
become in case of turned on storage
thefoods with a temperature level
from +3C(after the cooling) or-18 C
(after the deepfreeze) keeps.
In Any Case appears on the display
the respective temperature level of the cell.

Page10
Cooling with Time controller
Cooling press button
then time press button
and START/STOP
press.
Onthe display appears
the calm cool time.
For the change of the timing
Press button ofPROGafter that of
ON/OFF
as long as press, to the display
ilA announces. For the change the
Timing and throughkeystroke
RED. is
about the ON/OFF press button, that
one becomes
During increases and through keystroke
ON/OFF reduced.
That appearing on the display
Time is in the minute -cycle through
START/STOPkeystroke
toturn on.
• List of the alarm signals
CP Chamber probe does not function
HP Probe in the heart functions not
EP Evaporator probe does not function
LI Temperature outside the min boundary value
HI Temperature outside the boundary value max
Cleaning and maintenance
After every working day the interior of the cool cell is
carefully to be cleaned, around To guarantee a correct
hygiene and quality of the handled foods.
Only with water and neutral detergent clean (Pic 12)
No abrasives. Dredge or diluent employ.
Out the possibility the water of condensation onto the ground
to let tile (Pic 9), our products also with oneare
Receptacle to the water of condensation absorption loads, that regular
must be emptied (fig. 13).
Time controller deepfreeze
Deepfreeze press button then TIME press
button
and START/STOP press. On that
The calm deep-freezing -time appears to display.
For the change of the press button timing
PROG after that of ON/OFF as long as
press,
until the display announces ilC. For the change
the
Timing and through RED keystroke,
ON/OFF is above the press button, becomes
thetime extends and through keyst roke
ON/ OFF reduced.
That appearing on the display,
Time is in minutes cycle through
START / STOP keystroke
turning on.
If the pin probe was not introduced in the product heart,
the device automatically runs for a limited time (the at
last entered time). Lighting that one up Led time and
PROBE onto.
For the retention of the serviceability of the machine the
condenser is, to keep that behind the front grill clean. To that
is for the elimination of the dirt on the bracings ( \Pic. 14) to
carry out a monthly cleaning with a metal brush and a
vacuum cleaner no peaked subjects employ.

Page11
For the retention of the serviceability of the machine the condenser
is, to keep that is behind the front rust clean To that is for the
elimination of the dirt on the bracings ( \Pic. 14) to carry out a
monthly cleaningwith a metal brush and a vacuum cleaner. Do not
employ any peaked subjects.
During the maintenance and cleaning jobs gloves are to use, some
eyeglasses and a protection mask.
After these work flows arethat one before the engagement
Equipment the protectors again attach.
Non standard maintenance
This maintenance may be carried out only by the specialists
that is authorized to jobs and this product typology.
Disposal
The cold producer is equipped with refrigerant or with
lubricating oil. From that the disposal in this connection or
elimination of the severe observation of the valid rules of law of
the country are, in which the installation is carried out.,
subordinate.

Page12
Guarantee / assurance
1.1 Company
IME
A-5020 Salzburg/Austria
Telephone (++43) 0662 880070
Facsimile (++43) 0662 8800708
TRADER
MACHINE TYPE
Blast Chiller Type.........
MACHINE-NO.
-------------------------------------------------
YEAR OF MANUFACTURE
-------------------------------------------------
DELIVERY DATE
-------------------------------------------------
a) Our customer obliges, to check the product immediately upon delivery and inform us of obvious lacks
immediately in writing possible. Claims, that emerge later are also to be announced immediately in
writing, this at the latest within the legal warranty time period. If the customer refrains from the immediate
defect-signalling, the product is regarded so as being approved of. The customer has the immediate
occasion to give to us the check of the state of the device on site.
b) The guarantee occurs fundamentally through improvement. Price reduction claims come only then to the
effect, if we have agreed explicitly in writing.
c) We provide guarantee for all devices supplied by us -except for used merchandise, for which we do not
take over any guarantee -this within 6 months from actual delivery of the product at the Customers.
Within this period of time we render full material replacement. Freight and wrapping costs and/or way time
and ride costs are charged by us in any case.
d) We only guarantee, that within proper connection to the prescribed tension as well as at perfect voltage
ratios, correct service as well as installed in conformity to regulations, from which Operating manual clear
maintenance, expert installation through a licensed electrician the usually presupposed or explicitly
guaranteed services and functions are filled. We point out explicitly, that the measurements indicated in
our brochures or catalogues, services or functions in the same way as the design, at any time also
without previous announcement can be changed and are un-obligatory from that. We do not render any
guarantee in the case of contacts of unauthorized hand and/or non-compliance of the valid terms of
payment. The guarantee does not refer to glass, fireclay or parts which are subject to natural wear. A
warranty claim is fulfilled only with presentation of the corresponding bill and announcement of the serial
number of the device.
e) The guarantee for the expert market includes only the free substitute of defective parts, at which the
repair parts are sent against settlement to the customers and the customer at accrued liability of the
defective part a corresponding credit is exhibited.
f) For damages or mistakes that do not damage the definition of-appropriate use, no liability is taken over
g) Further claims of our customer are turned away, in particular compensation for direct and/or indirect
damages (Faulty consequential damages), unless, there are intention or coarse negligence.

Page13
Notes on safety
1.) Read the device operating manual exactly before initiation and consider
!
2.) All maintenance and cleaning jobs to be carried out only at switched off
device (Main power switch on „0).
3.) Service of the device only of trained personnel.
4.) Putting main power switches on „0" also in case of stoppages.
5.) All repair jobs (in particular with electric troubles) may be carried out
only by specialists at the machine.
6.) Use only accessories and attachments which are indicated in the
operating manual. The use of other accessories can mean a danger for
you.
7.) This device is exclusively to the chilling and freezing of suitable foods.
Case of fault
power-and/or. gas pipe supply to be interrupted through main power switches (or for
example protection, etc power plug.). Do not start device under no circumstances again if
device or incoming lines show damages or the reason for malfunction is unclear. In this
case the device must not be used beforeafter an inspection through a professional service
again. Hot oil (for example near deep fat fryers) not to temper with water.
This manual suits for next models
7
Table of contents
Popular Chiller manuals by other brands
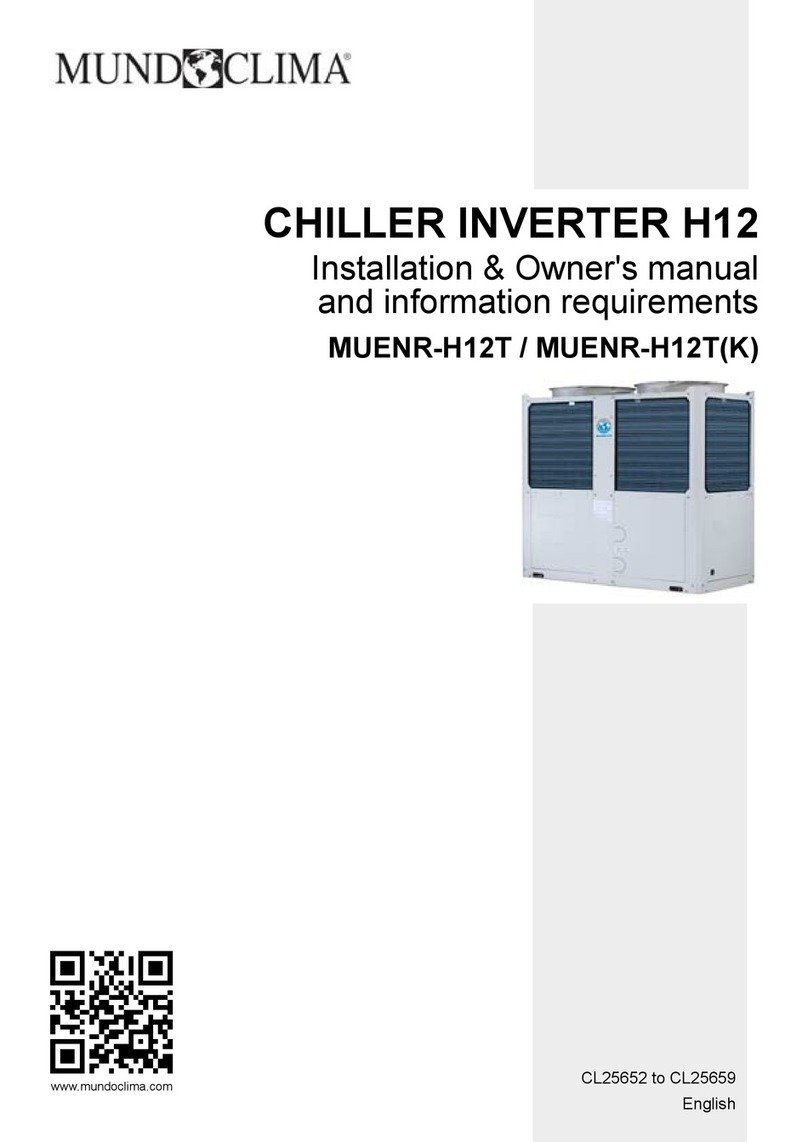
mundoclima
mundoclima H12 Series Installation & owner's manual

Alto-Shaam
Alto-Shaam quickchiller QC-3 Operating procedure guide

innove
innove Glass Chiller user manual
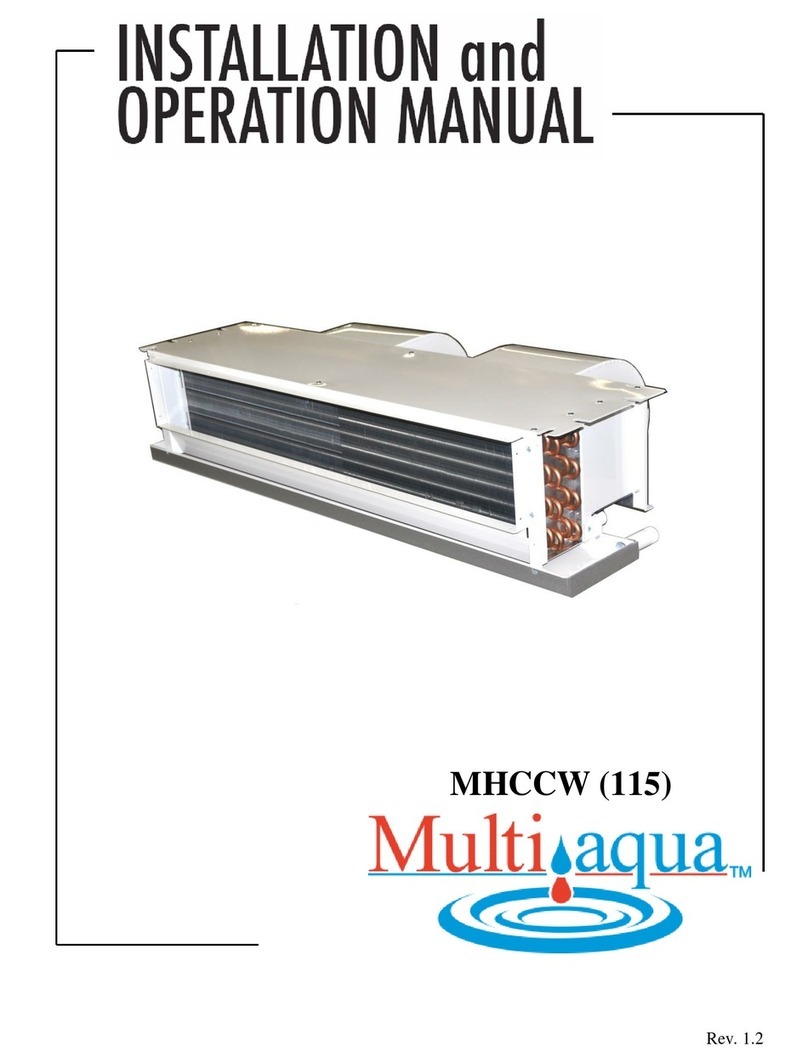
Multiaqua
Multiaqua MHCCW-08 Installation and operation manual
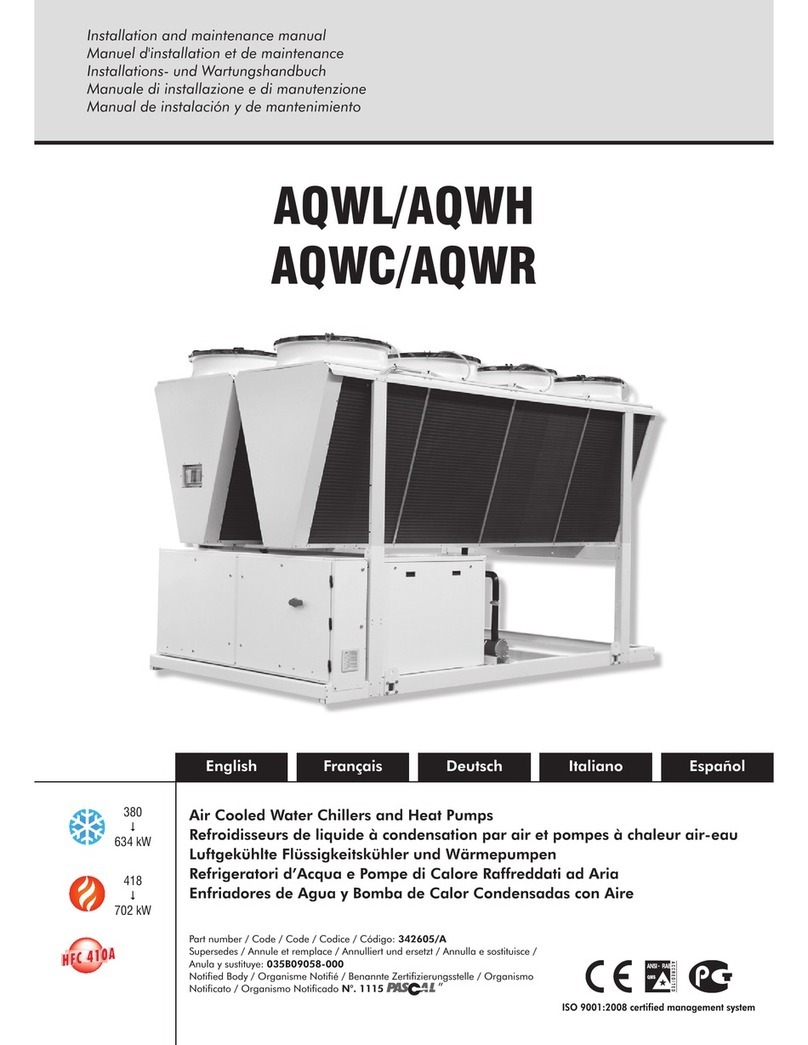
System air
System air AQWL Installation and maintenance manual

Hitachi
Hitachi SAMURAI Series Service manual
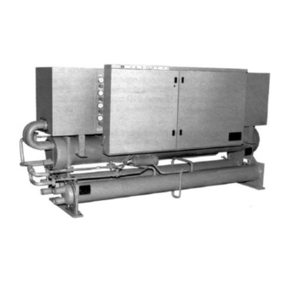
McQuay
McQuay WHR 017EW product manual

CLIMAVENETA
CLIMAVENETA i-LIFE2 manual

York
York MILLENNIUM YCAS Installation operation & maintenance

Colortronic
Colortronic AquaSnap 30RAN010-055 installation instructions
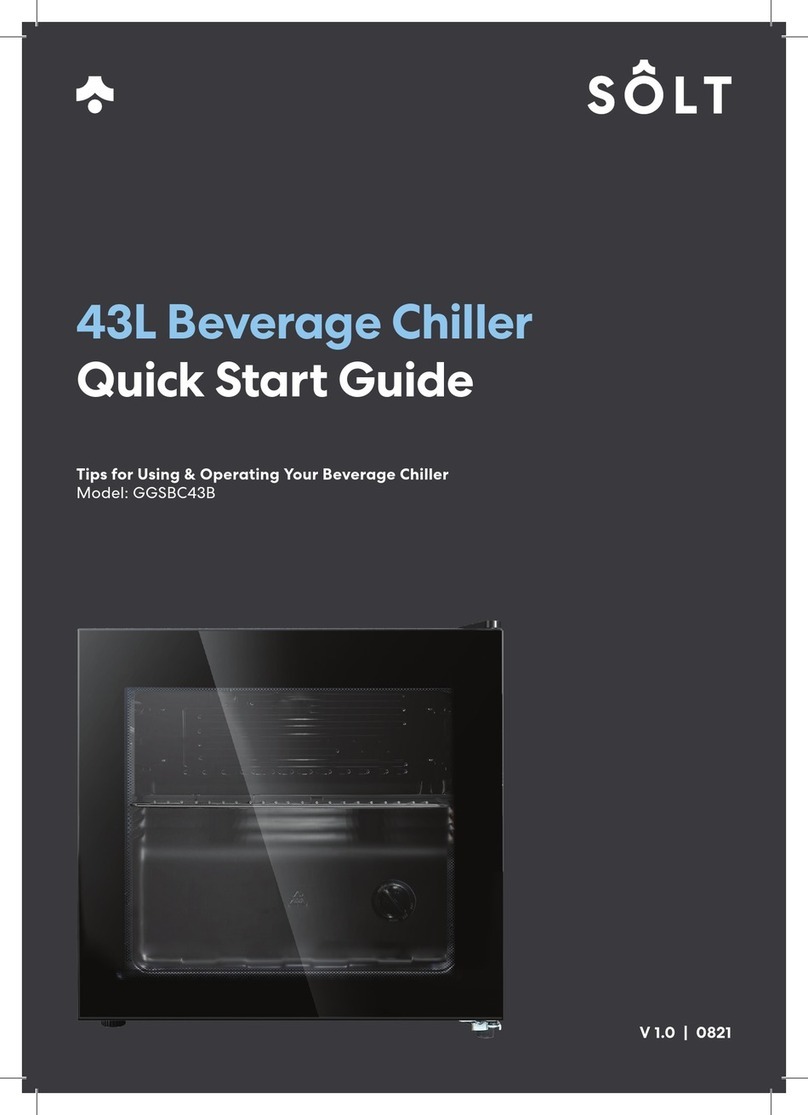
Solt
Solt GGSBC43B quick start guide

Carrier
Carrier 17/19EX Start-up, operation and maintenance instructions