ircon Modline 4 User manual

INSTALLATION and OPERATION MANUAL
Revision S 5
04/2019
Americas
Everett, WA USA
Tel: +1 800 227 8074 (USA and Canada, only)
+1 425 446 6300
solutions@flukeprocessinstruments.com
EMEA
Berlin, Germany
Tel: +49 30 4 78 00 80
info@flukeprocessinstruments.de
China
Beijing, China
Tel: +8610 6438 4691
info@flukeprocessinstruments.cn
Worldwide Service
Fluke Process Instruments offers services, including repair and
calibration. For more information, contact your local office.
www.flukeprocessinstruments.com
© 2019 Fluke Process Instruments
Specifications subject to change without notice.
Fluke Process Instruments

Interchanging non-CE-approved
components such as older sensing heads,
indicators, PC boards, and cables will not
maintain compliance to the CE Directive.
!!
CAUTION
For installing, operating, and servicing this instrument, please observe all cautions and
warnings that are located throughout this manual.
CE Compliance Information
Cautions and Warnings
Example of a Caution.
!!
CAUTION
Example of a Warning.
!!
WARNING
ii


iv
WARRANTY
IRCON, Inc. warrants equipment manufactured by it to be free from defects in materials and workmanship
for a period of one year from the date of shipment by IRCON. Customer-paid repairs are warranted for 90
days from date of shipment. If within such period any such equipment shall be proved to IRCON’S satis-
faction to be so defective, such equipment shall be repaired or replaced at Ircon’s option, provided the
defective equipment is returned to Ircon, transportation charges prepaid by purchaser. This warranty shall
not apply (a) to equipment not manufactured by Ircon, (b) to equipment which shall have been repaired or
altered by others than Ircon so as, in its judgement, to affect the same adversely, or (c) to equipment
which shall have been subject to negligence, accident, or damage by circumstances beyond Ircon’s control
or to improper operation, maintenance or storage, or to other than normal use or service. With respect to
equipment purchased by IRCON but not manufactured by Ircon, the warranty obligations of Ircon shall in
all respects conform and be limited to the warranty actually extended to Ircon by its supplier (the manufac-
turer). The foregoing warranties do not cover reimbursement for transportation, removal, installation, or
other expenses which may be incurred in connection with repair or replacement.
Except as may be expressly provided in an authorized writing by IRCON, IRCON shall not be subject
to any other obligations or liabilities whatsoever with respect to equipment manufactured by IRCON or
services rendered by IRCON. THE FOREGOING WARRANTIES ARE EXCLUSIVE AND IN LIEU OF
ALL OTHER EXPRESS AND IMPLIED WARRANTIES EXCEPT WARRANTIES OF TITLE, INCLUDING
BUT NOT LIMITED TO IMPLIED WARRANTIES OF MERCHANTABILITY AND FITNESS FOR A
PARTICULAR PURPOSE.
LIMITATION OF LIABILITY
Anything to the contrary herein contained notwithstanding, IRCON, IT’S CONTRACTORS AND
SUPPLIERS OF ANY TIER, SHALL NOT BE LIABLE IN CONTRACT, IN TORT (INCLUDING
NEGLIGENCE OR STRICT LIABILITY) OR OTHERWISE FOR ANY SPECIAL, INDIRECT, INCIDENTAL,
OR CONSEQUENTIAL DAMAGES WHATSOEVER. The remedies of the purchaser set forth herein are
exclusive where so stated and the total cumulative liability of Ircon, it’s contractors and suppliers of any
tier, with respect to this contract or anything done in connection therewith such as the use of any product
covered by or furnished under the contract, whether in contract, in tort (including negligence or strict liabili-
ty) or otherwise, shall not exceed the price of the product or part on which such liability is based.
Risk of Personal Injury
When this instrument is used on a critical process where failure of this
instrument could cause personal injury or property damage, the user
must provide a redundant device or system that will initiate a safe
process shutdown . The user should also follow NEMA safety guide-
lines in the Appendix of this manual.
CAUTION



Section 1 – INTRODUCTION
1.1 GENERAL DESCRIPTION
MODLINE 4 is an infrared thermometer with a built-in two
wire transmitter. Power it up with a 16 to 40 volt direct
current source and you get a 4 to 20 mA current (maximum)
that varies linearly with temperature. You can use this
current to operate a 4 to 20 mA indicator, recorder, con-
troller or datalogger – or a combination of devices in
the series. Figure 1.1 shows the basic electrical circuit.
This instrument is built for long, trouble-free service in even
the harshest environments. Everything is packaged in
sealed aluminum casting rated NEMA 4. The instrument
can be ordered with a water-cooled casting for operation
in high ambient temperatures.
The lens is recessed and sealed in the front of the casting.
A screw-on back cover with torquing slots gives access to
the adjustments and connections (see figure 1.2). A 1/2
inch NPT conduit hub is provided for wiring. NOTE: The
back cover of the water-cooled enclosure has a pair of
torquing studs.
The MODLINE 4 is easy to install, operate and maintain.
The lens is pre-adjusted and sealed so you don’t have to
make optical adjustments. Just choose a clear sight path
with no obstructions, aim the sensor at the object you want
to measure and read the temperature on your indicator.
The controls on the back panel allow you to adjust for
emissivity of the material you are measuring and for the
most suitable response time for your process. If the instru-
ment includes a peak picker (block D of model number
= 1), an additional control is provided for peak picker
decay time. As long as your process stays the same, you
will make these adjustments only once when you set
up the instrument.
The high-level current signal (20 mA maximum) minimizes
noise problems often associated with long cable runs.
Twisted pair cable with an overall shield is all you need
for most applications.
Seven different MODLINE 4 series that differ in spectral
responses, cover a wide variety of processes. Temperature
ranges covering 0 to 2500°F and 0 to 1300°C are available.
Note: General illustrations in this manual that show the
standard MODLINE 4 casting also apply to instruments
with water-cooled castings.
1-1
Fig. 1.1 - BASIC MODLINE 4 ELECTRIC CIRCUIT
Fig. 1.2 - MODLINE 4 REAR VIEW (WITH
COVER REMOVED) and FRONT VIEW
Note: standard enclosure shown.

Section 1 – INTRODUCTION
1.2 HOW IT WORKS
The MODLINE 4 works on a simple principle. A heated
object radiates infrared energy, and the intensity of
radiation depends on the temperature of the object. By
measuring the radiation intensity, it is possible to measure
the temperature without contacting the object.
Fig. 1.3 shows a MODLINE 4 series with a digital meter
across a DC power supply. The current in this circuit is
determined by the MODLINE 4.
Infrared radiation enters the lens of the MODLINE 4
and is focused on an infrared detector. The detector
converts infrared energy to an electrical signal that
varies with the intensity of infrared radiation. This
signal is amplified, linearized, and scaled to the desired
temperature range by the MODLINE 4 electronic circuits.
The resulting output current causes the pointer to deflect
on the meter. If the meter scale is matched to the MOD-
LINE 4 range, it’s a simple matter to read temperature
values directly from the scale.
Fig. 1.3 shows how the MODLINE 4 measures a change
in temperature. Assume the MODLINE 4 is scaled for
the 500 to 1500°F range. The circuit current is 4 mA
when the MODLINE 4 is viewing a 500°F target and
20 mA when viewing a 1500°F target. The current
varies linearly between 4 and 20 mA for temperatures
between 500 and 1500°.
In Fig. 1.3a, the target temperature is 500°F. The target
will radiate a certain intensity of infrared energy at
this temperature. When the MODLINE 4 senses this
radiation, it causes 4 mA current in the meter. The
pointer rests at the lowest scale limit (500°).
Figures 1.3b and 1.3c shows what happens when
target temperatures increases. The MODLINE 4 detects
more infrared radiation, and the meter current increases
to display higher temperature readings.
Summarizing the action, the MODLINE 4 provides a DC
current proportional to the infrared energy it senses.
This current can be fed through a variety of current-
sensitive devices to indicate temperature or provide a
desired control action.
1-2
FIG. 1. 3 - BASIC OPERATING PRINCIPLE OF
MODLINE 4 INSTRUMENT

TABLE 1.1 – SUMMARY OF MODLINE 4 SERIES
1–3
Section 1 — INTRODUCTION
1.3 OPERATING WAVELENGTHS
It takes a whole family of instruments to cover a
wide range of measurement applications. MOD-
LINE 4 features such a family-seven series operat-
ing at distinct infrared wavelengths. Each series
includes the temperature spans that are common
for the applications involved.
The wavelength regions selected for the various
MODLINE 4 series are listed in Table 1.1. This
table also summarizes some of the primary appli-
cations for these ranges.
120 to 400°F
150 to 500°F
200 to 600°F
300 to 1000°F
50 to 200°C
100 to 400°C
150 to 500°C
43 Measures thin, clear films of C-H
Type plastics such as polyethylene,
polypropylene, polystyrene, vinyls,
and nylon. Also ideal for paints and
organics such as waxes and oils.
3.43 ± 0.07 microns
0 to 200°F
0 to 500°F
0 to 1000°F
0 to 100°C
0 to 250°C
0 to 600°C
500 to 1000°F
500 to 2500°F
300 to 800°C
300 to 1300°C
500 to 1000°F
600 to 1400°F
250 to 600°C
350 to 800°C
44
22
45
46
Ideally suited to all types of very low
temperature applications such as
print drying, food, wood, paper and
textile processing, vacuum forming,
and infrared heating.
Measures subsurface glass tem-
perature. Good unit to see though
hot gasses and flame.
All types of medium temperature
applications involving metals.
8 to 14 microns
200 to 1000°F
500 to 1500°F
500 to 2500°F
100 to 600°C
300 to 850°C
300 to 1300°C
47 Measures glass surface tempera-
ture in such operations as forming,
bending, tempering annealing, and
sealing. Also suitable for infrared
heating.
4.8 to 5.2 microns
0 to 600°F
500 to 1500°F
500 to 2500°F
0 to 300°C
300 to 800°C
300 to 1300°C
48 Measures refractory brick, painted
surfaces, plastics glass and infrared
heating of these products.
Especially good for thin films of
plastics, oils, paper, wood, and
other organic material.
7.5 to 8.5 microns
3.7 to 4.0 microns
2.0 to 2.6 microns
Series Standard Ranges Wavelength Primary Applications

Section 1 – INTRODUCTION
1.4 OPTICAL RESOLUTION
The MODLINE 4 detector “sees” a certain area
(spot on a target surface. The diameter of the
spot is determined by the design on the
optical system and by the distance to the
ttarget.
Fig. 1.4 is a plot of spot sizes at every incre-
ment of distance from the front flange of the
MODLINE 4. The three dimensional “Cone of
Vision” defines the viewing area of the
MODLINE 4 at any given distance. Anything
inside the cone is in the field of view and
anything outside of the field of view is not.
If unobstructed, the cone of vision would expand
to infinity. But in practice, you aim it so it falls
on a target at some finite distance. In Fig. 1.4
below, the cone of vision falls on the target at
the separation distance (D). At this distance,
the diameter of the cone or viewing area on
the target surface will have a spot size (d).
1-4
®
Note that if you move the MODLINE 4 a little
closer the target will intersect a smaller cross
section of the cone and give you a smaller spot.
Moving it further away will give you a larger spot.
Spot size/separation distance relationships for
the MODLINE 4 are give in the Model Indentifi-
cation table (see section 1.5). This relationship
defines the optical resolution or the smallest
target the instrument can measure at any given
distance. If the spot is larger than the target, the
output current will be influenced partly by the
target temperature and partly by the background
temperature, and the instrument will give a false
temperature reading.
The importance of resolving the target will be
emphasized in the installation procedures.
FIG. 1.4 SPOT SIZE vs. SEPARATION DISTANCE RELATIONSHIP

Section 1 — INTRODUCTION
Seven standard series are identi-
fied by this two-digit block. See
Table 1.1 for characteristics of
each series.
2 2 = 22 Series (8 to 14 µm)
4 3 = 43 Series (3.43 ±0.07 µm)
4 4 = 44 Series (8 to 14 µm)
4 5 = 45 Series (3.7 to 4.0 µm)
4 6 = 46 Series (2.0 to 2.6 µm)
4 7 = 47 Series (4.8 to 5.2 µm)
4 8 = 48 Series (7.5 to 8.5 µm)
22 or 44 SERIES
02F=000 to 0200°F
05F=000 to 0500°F
10F=000 to 1000°F
01C=000 to 0100°C
02C=000 to 0250°C
06C=000 to 0600°C
45 SERIES
1 5 F = 500 to 1500°F
2 5 F = 500 to 2500°F
0 8 C = 300 to 0800°C
1 3 C = 300 to 1300°C
46 SERIES
1 0 F = 500 to 1000°F
1 4 F = 600 to 1400°F
0 6 C = 250 to 0600°C
0 8 C = 350 to 0800°C
47 SERIES
1 0 F = 200 to 1000°F
1 5 F = 500 to 1500°F
2 5 F = 500 to 2500°F
0 6 C = 100 to 0600°C
0 8 C = 300 to 0800°C
1 3 C = 300 to 1300°C
43 SERIES
0 4 F = 120 to 0400°F*
0 6 F = 200 to 0600°F
1 0 F = 300 to 1000°F
02C=050 to 0200°C*
0 4 C = 100 to 0400°C
0 5 C = 150 to 0500°C
*Restrictions:
Case operating temperature range
50 to 113°F (10 to 45°C);
Sudden ambient temperature change
(up or down) of 10°C (18°F) will
cause noticeable errors until the
instrument temperature stabilizes.
Minimum response time setting
10 seconds for target temperatures
from 120 to 300°F (50 to 150°C);
Minimum emissivity setting 0.5. 48 SERIES
06F=000 to 0600°F**
1 5 F = 500 to 1500°F
2 5 F = 500 to 2500°F
03C=000 to 0300°C**
0 8 C = 300 to 0800°C
1 3 C = 300 to 1300°C
**High Resolution versions may require
higher response time settings.
Standard temperature ranges
available in each MODLINE 4
Series are listed below:
BLOCK A Series Designation BLOCK C Optical Resolution
Optical Resolution relates to the
circular area viewed (Spot Size) at
any given distance from the front
of the MODLINE 4. See diagram
and data below.
0 = Standard Resolution
1 = High Resolution
2 = Very High Resolution
BLOCK B Temperature Range
BLOCK B
Temperature Range
(continued)
MODEL NUMBER
A
Series Temp. Range Opt. Res. Output Enclosure
B C D E
1–5
BLOCK D Output
Standard Modline 4 output is
4-20mA, linear, corresponding
to the temperature range. Peak
Picker is optional (standard with
Series 22).
0 = 4 to 20 mA
1 = 4 to 20 mA with
Peak Picker
BLOCK E Enclosure
Standard Enclosure is an
aluminum casting with NEMA 4
rating (Series 43 through 48).
Water-cooled Enclosure has a
built-in air purge.
0 = Standard Enclosure
1 = Water-cooled Enclosure
Please note: A “9” in any
block means the instrument
has been specially modified.
Refer to Section 1.7 for
details of the modification.

Section 1 – INTRODUCTION
1.5 MODEL IDENTIFICATION
Note the model and serial numbers on the side
plate of the sensor. Unscrew the back cover
to make sure the model and serial numbers on
the identification plate match those on the
packing slip and on the side plate. The model
number digit is explained below.
Example: Model 44-01C-1-1-0
This model number designates a series
44 instrument with a temperature range
of 0 to 100°C and high optical resolution.
Output is 4 to 20 mA (peak picker included)
and the instrument has a standard
enclosure.
1-6
®

1–7
Section 1 — INTRODUCTION
1.6 SPECIFICATIONS
The following specifications are common to all Series of MODLINE 4:
Operating Wavelength Region: Varies by Series (see Table 1.1)
Emissivity Range: Adjustable from 0.10 to 0.99 in 0.01 increments
Power Supply and Load Requirements: Input voltage: 24V direct current (dc) nominal16V direct
current (dc) minimum to 40V direct current (dc) 20mA
maximum. In order for the MODLINE 4 to meet
European Electromagnetic Compatibility Directive,
a CE version power supply is required.
Load resistance: ≤1 ohm at 16 to 24V direct current;
1200 ohms at 40 V direct current (see Section 2.4 for
additional information)
Fuse Rating: For customer supplied power supplies, the power supply
must be fused such that at 40V direct current the current
(I) level must be less than 4 amps. At 16V direct current
the current (I) cannot exceed 8 amps and the power
supply total output must not exceed 150 VA.
Output Current: 4 to 20 mA direct current
Response Time: Continuously adjustable from approximately
(to 95% of any change in input) 0.15 sec to 10 sec
Peak Picker Decay Range: Continuously adjustable from approximately
(for models with Peak Picker) 15 sec to 30 min for full-scale decay
Humidity Limits: 0 to 90% non-condensing
Enclosure Material: Aluminum
Weight: Standard Enclosure: 2.6 lbs (1.2 kg)
Water-cooled Enclosure: 20 lbs (9.25 kg)

1–8
Section 1 — INTRODUCTION
The following specifications differ for Series 22 as compared to Series 43 through 48:
Series 43 through 48 Series 22
Calibration Accuracy: Within 0.75% of full-scale Within 1.0% of full-scale
temperature or 3 °F (1.7 °C), temperature or 5 °F (2.8 °C),
whichever is greater
For the 43-02C and 43-04F:
within 0.75% of full-scale
temperature or 4°F (2.3°C)
whichever is greater
whichever is greater
Repeatability: 0.3% of full-scale temperature 0.5% of full-scale temperature
Temperature Coecient: ≤0.015%* of span per °F change ≤0.020% of span per °F change
from nominal value of 77 °F from nominal value of 77 °F
over range of 32 to 150 °F over range of 32 to 130 °F
≤0.027%* of span per °C change ≤0.035% of span per °C change
from nominal value of 25 °C from nominal value of 25 °C
over range of 0 to 66 °C over range of 0 to 54 °C
Case Operating Standard enclosure: Standard enclosure:
Temperature Range: 32 to 150 °F (0 to 66 °C) 32 to 130 °F (0 to 54 °C)
(see previous page for exceptions)
Water-cooled enclosure: Water-cooled enclosure:
32 to 400 °F (0 to 204 °C) 32 to 400 °F (0 to 204 °C)
Environmental Rating: NEMA 4 NEMA 4
Optical Centering: Optical axis within 1 °of Optical axis within 2 °of
mechanical center axis (within mechanical center axis (within
0.2 in. per foot or 17 mm per 0.4 in. per foot or 33 mm per
meter separation distance) meter separation distance)
*For Series 43-04F: ≤0.05% per °F
*For Series 43-02C: ≤0.09% per °C

1–9
Section 1 — INTRODUCTION
1.7 PRODUCT MODIFICATIONS
There are no special modifications in this instrument. It is standard in all respects.

Section 2– INSTALLATION
2.1 INTRODUCTION
MODLINE 4 gives you the capability of building a
custom-made temperature monitoring system for
your process, If you follow the simple guidelines
described in this section, you system will give
accurate, trouble free service.
The MODLINE 4 is compatible with most 4 to 20
mA devices used in industry today. You can select
a variety of indicators, recorders and other devices
to complete your system. Combine these devices
in series if you like or combine groups of MODLINE
4’s and switch them manually or automatically to
monitor key checkpoints in the process. As long
as your system stays within the MODLINE 4 speci-
fications, you will get good results. Most of the
descriptions are based on the use of optional
IRCON components. However, the descriptions
also apply to any other devices that are compatible
with the MODLINE 4 system.
- Model PS4-24 Power Supply
- TV-VIEW-VAAC Digital Indicator
Power Supply
2. 2 BASIC SYSTEM
Fig. 2.1 illustrates a simple system consisting of the
MODLINE 4, a Digital Meter and a Power Supply.
These components form a continuous current loop.
System power is provided by the Power Supply which
provides a DC output typically between 16 and 40 V
direct current. AC line voltage is used to operate
to operate the supply.
Loop current is determined by the MODLINE 4 which
is calibrated to provide a 4 to 20 mA output. this
current flows through all series loop components.
It varies with target temperature over the full
temperature span of the instrument. For example,
an instrument with a temperature span of 500 to
1500°F will have a 4 mA output when viewing a
500°F target. The output increases to 20 mA when
viewing a 1500°F target. The output is a linear
16 mA span, from 4 to 20 mA, over the instrument
temperature range as illustrated in the Fig. 2.1 curve.
2-1
®

Section 2 – INSTALLATION
2.3 SUPPLY AND LOAD REQUIREMENTS
Table 2.1 shows how load voltage increases with
load resistance. As load resistance increases, you
need more DC supply voltage to cover the load
voltage and still leave enough to operate the
load voltage and still leave enough to operate the
MODLINE 4.
Use Table 2.1(see following page)asa guide in
selecting your power supply. Be sure to total up all
load resistance in your lood and add cable
resistance if it will have a noticeable effect on loop
resistance. If you plan to operate several indicators
or other devices in the series, be sure to use toe
TOTAL series resistance in your calculations (see
figure 2.2 for an example).
NOTE: Connecting cable wires contribute a certain
amount of resistance which adds to the load
resistance. However, cable resistance per foot is
usually small, and a cable run of 1500 feet will add
no more than a few ohms to the circuit.
The MODLINE 4 operates at any supply voltage
between 16 and 40 volts direct current. If you
exceed the 40-volt upper i mit, you stand a chance
of damaging the MODLINE 4 sensor. If you go
below the 16-volt lower limit, the MODLINE 4
simply will not work.
If you furnish you own components, make sure
they meet MODLINE 4 requirements. For a
power supply, important specifications to look
for are supply voltage and current capacity. For
indicators, recorders, and other load elements,
pay strict attention to the load resistance and,
of course, the zero scale and full scale currents.
Part of the power supply voltage is dropped
across the load and is not available for the
MODLINE 4. In figure 2.1, for example, suppose
the analog indicator has a resistance of 7 ohms.
At the full scale current of 0.02A, the voltage
drop across the indicator will be:
E = IE = 0.02 x 7 = 0.14 V
If the power supply voltage is 24 V, the MOD-
LINE 4 operating voltage at maximum current
will be 24 – 0.14 = 23.86 V, well above the
required minimum of 16 V.
2-2
®

Section 2 - INSTALLATION
FIG. 2.2 MODLINE 4 MULTIPLE LOAD ELECTRICAL CIRCUIT
2.4 MULTIPLE LOAD SYSTEM
In Fig. 2.2, a recorder, analog indicator and controller are
connected in a series in the loop. The 4 to 20 mA current
determined by the MODLINE 4 flows through all of these
load elements, producing voltage drops proportional to the
resistance of each load element. The total load voltage is
the sum of these voltage drops plus the drop across the
connecting wires.
Assume the resistances are as indicated in Fig. 2.2:
TABLE 2.1
MINIMUM DC SUPPLY REQUIREMENTS
FOR MULTIPLE LOADS
Total Load Total Load Minimum DC
Resistance Load Supply
(ohms) (volts) (volts)
≥50 1 17
100 2 18
200 4 20
300 6 22
400 8 24
500 10 26
600 12 28
700 14 30
800 16 32
900 18 34
1000 20 36
1100 22 38
1200 24 40
With 8 V dropped across the load elements and cables,
a supply voltage of at least 24 V is needed to ensure the
required 16 V minimum for the MODLINE 4 (see table 2.1 –
Minimum DC Supply Requirements).
IMPORTANT: DC supply voltage must never
exceed 40 volts!
2-3
®

Section 2 - INSTALLATION
2.5 MULTIPLE LOOP SYSTEMS
Fig. 2.3 is an example of a multiple loop system. Two
MODLINE 4 loops are operated from a single power
supply. An arrangement of this type is suitable for measuring
temperatures at two or more stations with an independent
readout for each station. The advantage is the economy of a
single power supply for all loops.
An important consideration in this system is the current capacity
of the power supply. For example, if loops A and B in Fig. 2.3
are both measuring full scale temperature, currents 1Aand 1B
will be 20 mA for a total supply current of 40 mA.
The IRCON model PS4-24 power supply has a current
capacity of 200 mA giving it the capability of powering up to
ten MODLINE 4 loops.
2. 6 SWITCHED MODLINE 4 SYSTEM
FIG. 2.3 MULTIPLE LOOPS OPERATED
FROM SINGLE SUPPLY
Sometimes you can gain economy or efficiency by switching
between circuit components. Fig 2.4 shows how this idea might
be used to switch a single indicator and power supply to either of
two MODLINE 4 units. This time-sharing system permits
measuring the temperature at either of two stations on a single
indicator.
The switching system shows consists of a double pole, double
throw switch which allows simultaneous switching of both
MODLINE 4 output leads. The switch can be a manual or
an automatically controlled switch or a set of appropriate
relay contacts.
NOTE: These illustrations give you an idea of how
versatile MODLINE 4 can be in system design. Our systems
give you just about any results you’re looking for. If you need
qualified help in choosing components or planning your
system, contact IRCON Applications Engineering.
.
FIG. 2.4 SWITCHED MODLINE 4 UNITS
2-4
®

2–5
Section 2 — INSTALLATION
2.7PRE-INSTALLATION NOTES
2.7a. General
The MODLINE 4 is a fixed focus instrument. The
optical components are factory aligned to provide
a fixed optical pattern which determines the size of
measuring area, or what is called the "spot size" at
any given distance from the front flange of the unit.
This is the area the detector in the MODLINE 4 will
"see" on the target surface.
Every step has been taken to ensure accurate
measurements with excellent repeatability. the
optical and electronic systems are factory calibrat-
ed against precision laboratory standards to ini-
tially set their accuracy specification.
If the MODLINE 4 is installed with reasonable
care, it will provide accurate temperature measure-
ments and a long, trouble-free operating life.
Modline 4 instruments are available in standard of
water-cooled castings as shown in Fig. 2.5. The
optical and electrical systems are essentially the
same in both versions. Any differences that affect
installation or operation will be pointed out in the
following instructions.
WATER
FITTINGS
MOUNTING
FLANGE
MOUNTING
FLANGE
CONDUIT
HUB
CONDUIT
HUB
AIR FITTING LENS
LENS
FIG. 2.5 – MODLINE 4 STANDARD AND WATER-COOLED CASTINGS
Risk of Personal Injury
When this instrument is being used in a critical
process that could cause property damage and
personal injury, The user should provide a
redundant device or system that will initiate a
safe process shutdown in the event that this
instrument should fail. The user should follow
NEMA safety guidelines in the appendix.
!!
CAUTION
Table of contents
Other ircon Measuring Instrument manuals
Popular Measuring Instrument manuals by other brands

Felix Storch
Felix Storch Check it! F-920 Operation manual
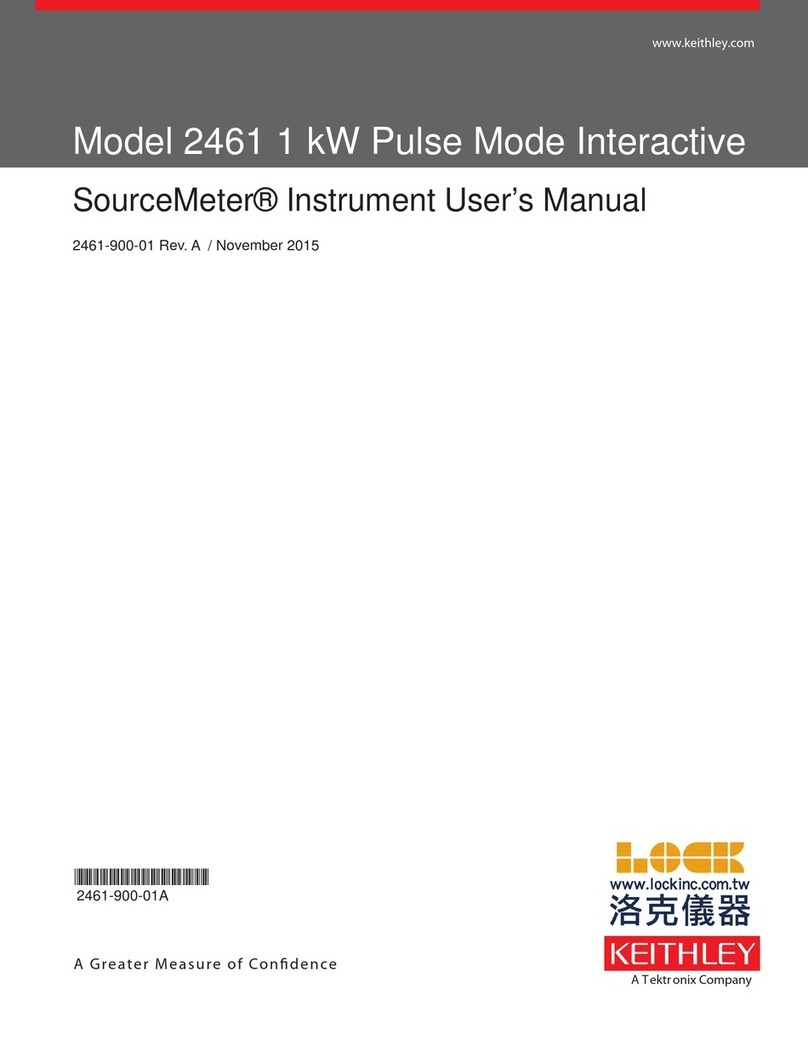
Tektronix
Tektronix Keithley SourceMeter 2461 user manual
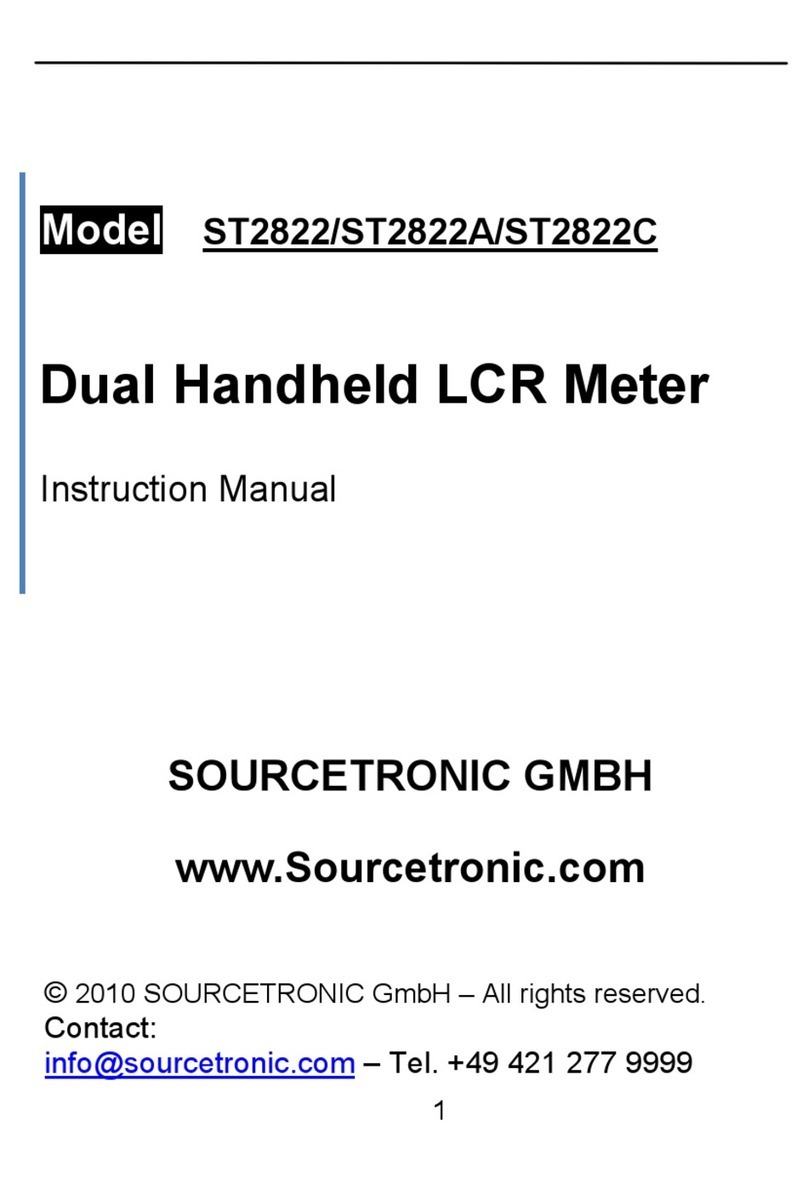
Sourcetronic
Sourcetronic ST2822 instruction manual
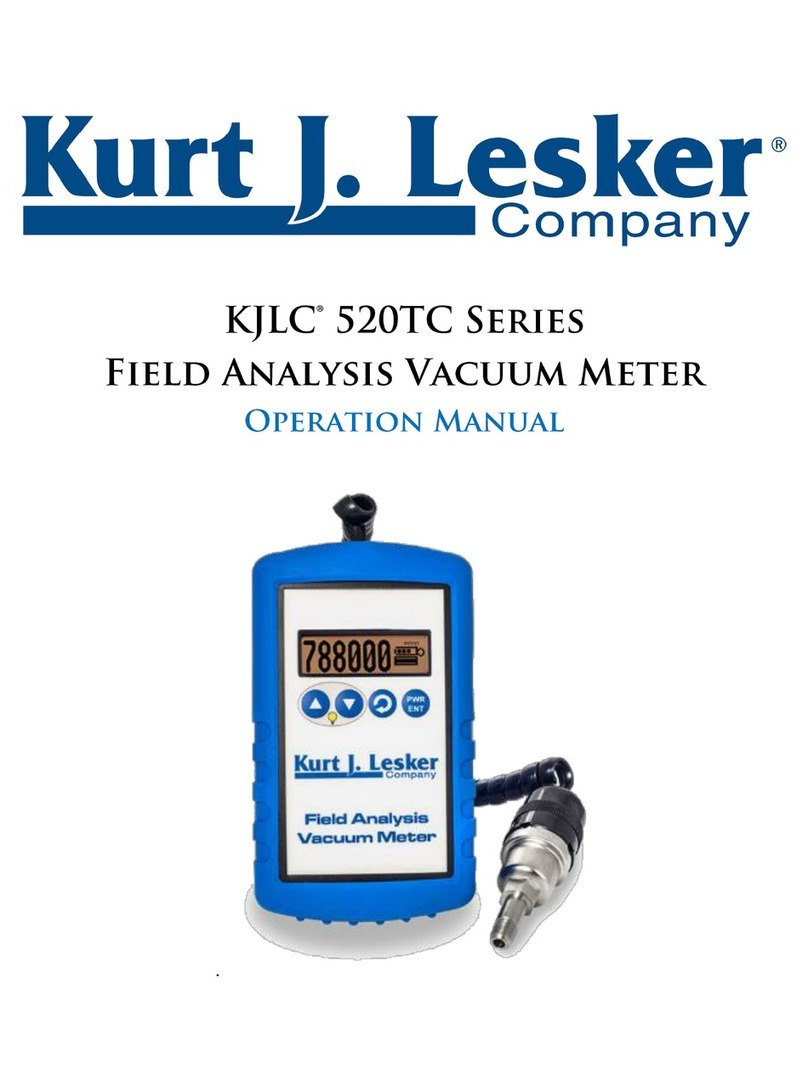
Kurt J. Lesker
Kurt J. Lesker 520TC Series Operation manual
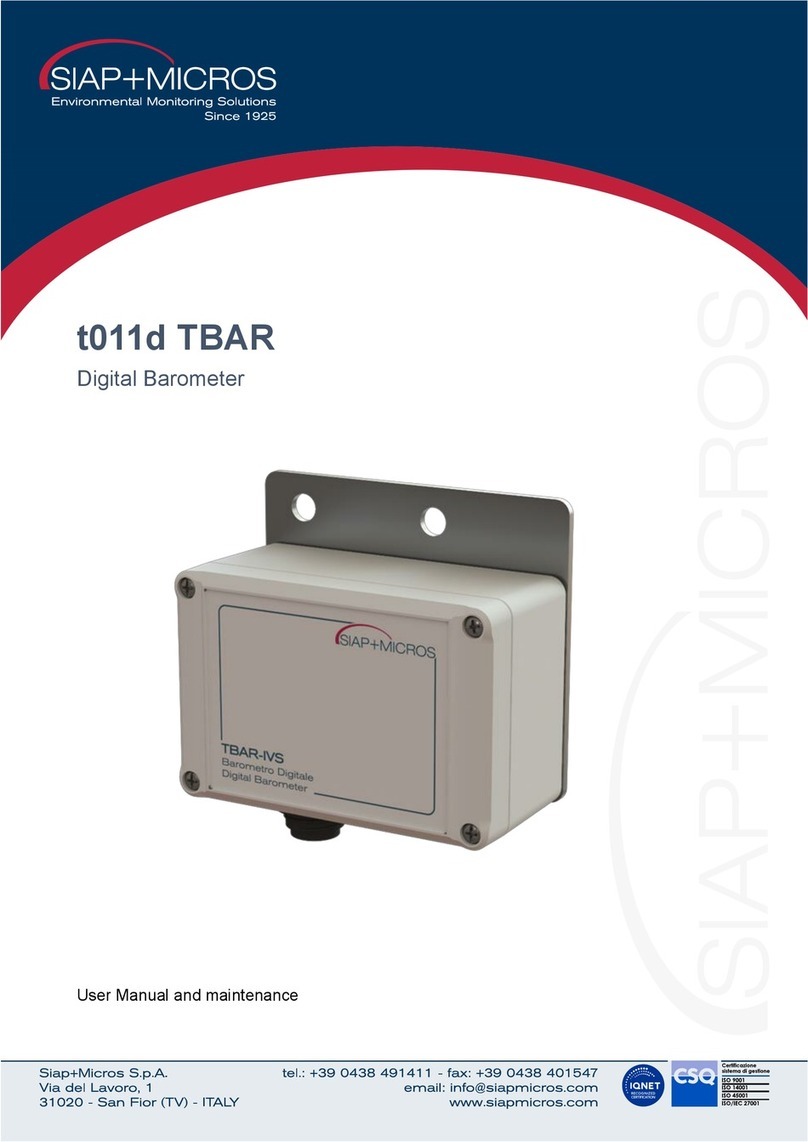
SIAP+MICROS
SIAP+MICROS t011d TBAR User manual and maintenance
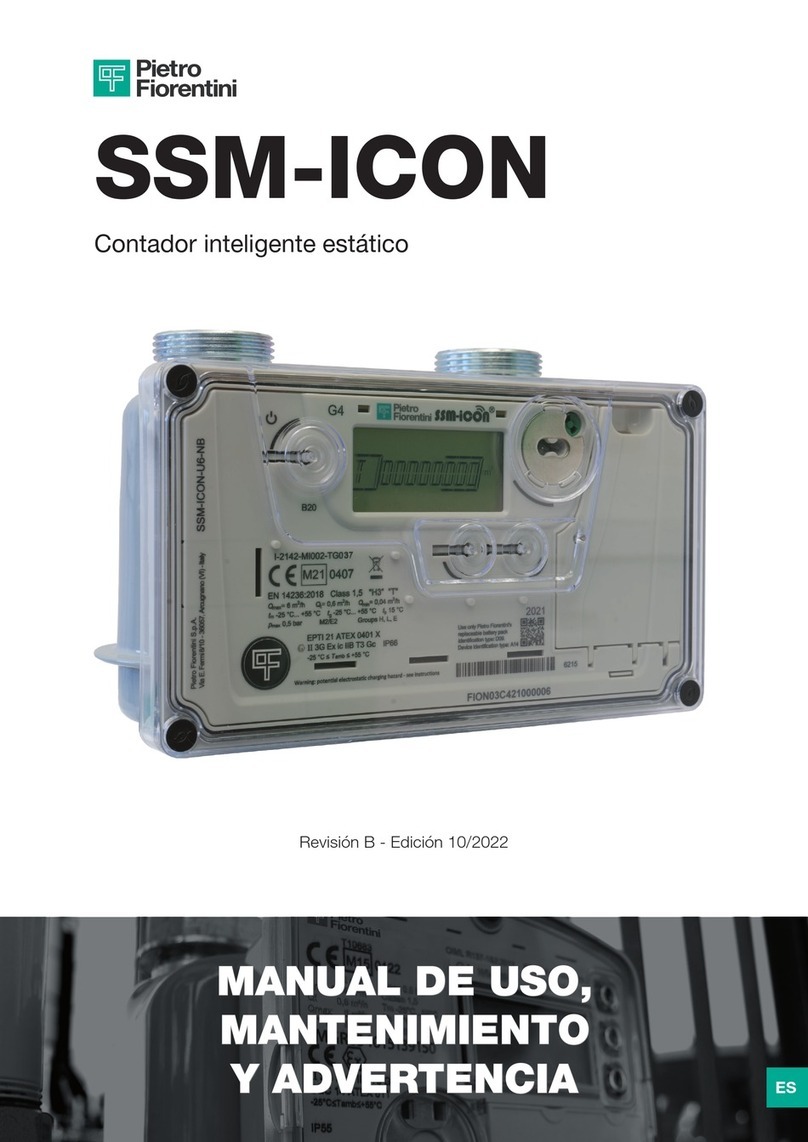
PIETRO FIORENTINI
PIETRO FIORENTINI SSM-ICON Use and maintenance manual