ITEM LRE 8 D25 ZU 80 R50 Operating instructions

Linear Unit LRE 8 D25 ZU 80 R25
Notes on Use and Installation

2
Symbols, safety
Meaning:
Important, safety information, recommendation
Maintenance
General safety information
Contents
Symbols, safety 2
General safety information 2
Correct use 3
Improper use 3
Operating parameters 4
Preparation 5
Installation 6
Guide carriage/Bearing Units 6
Potentialapplications 7
Timing-Belt Reverse Unit 8 80 R25 with Bore 8
Potential applications 8
Installing the Timing Belt 8
Fastening options 9
Securing and tensioning Timing Belt R25 T10 9
Positioning Proximity Switches 11
Positioning Proximity-Switch Cams 11
Connecting Drive Set 8 80 D80/D34 – 0.0.668.04 12
ConnectingDriveSetZU880D80/D34AP/WP80–0.0.672.76 13
Synchronising LRE 8 D25 ZU 80 R25 14
Lubrication 15
Maintenance 15
The details and information in the installation guide are provided solely for
the purposes of describing the product and the assembly and disassembly of
variants of Linear Unit LRE 8 D25 ZU 80 R25. The text below usually refers
to these as the Linear Unit or LRE. This information does not discharge the
user from the obligation to carry out his own assessments and checks. It is
important to bear in mind that our products are subject to a natural process of
wear and ageing. These notes contain important information that will enable
you to use the product safely and appropriately. When sold, rented out or
otherwise passed on to another party, this product must be handed over with
the installation guide.
When installing, disassembling, operating and maintaining the Linear Unit, it is
important to ensure that all moving elements are secured so that they cannot
be switched on and moved unintentionally. Rotating and moving parts can
cause serious injury! You must therefore read and follow the safety instructions
set out below.
▪All work on and with the Linear Unit must be performed with “safety first” in
mind.
▪Always switch off the drive unit before you start working on the Linear Unit.
▪Ensure the drive unit is not switched on unintentionally, e.g. by affixing war-
ning notices at the activation point or by removing the fuse from the power
supply.
▪Do not place your hand within the operating range of the Linear Unit’s
moving parts when the unit is still switched on.
▪Fit guards and covers to the moving parts of the Linear Unit to ensure they
are not touched unintentionally.
▪Observe the regulations pertaining to accident prevention and environmental
protection that apply in the country and place of work where the product is
being used.
▪Use only products that are in perfect working order.
▪Failure to use original spare parts will invalidate the product warranty!
▪Check the product for obvious defects.
▪Use the product only within the performance range described in the techni-
cal data.
▪Ensure that all the safety equipment associated with the product is present,
properly installed and in full working order.
▪Do not alter or circumvent safety equipment, or render it ineffective.
The Linear Unit described here corresponds to the state of the art and takes
into account the general principles of safety applicable at the time this installa-
tion guide was published. Nevertheless, failure to observe the safety instruc-
tions and warning notices in this installation guide may result in personal injury
and damage to property.
We will assume no liability for any resulting damage or injury. We reserve the
right to make technical changes that represent technical advances. Keep these
installation notes in a place where they can be easily accessed by all users.
Observe the directions contained in the main user guide for the completed
machine.
The general safety information applies to the entire lifecycle of the partly
completed machine.

3
Correct use
Improper use is defined as any use of the product for purposes other than those
authorised in the installation guide and under the definition of correct use. We
will assume no liability for any resulting damage or injury.
Improper use
Linear Unit LRE 8 D25 ZU 80 R25 with Controller and Motor is a partly com-
pleted machine as defined in the Machinery Directive (2006/42/EC). It must
only be used in accordance with the technical data and safety requirements
set out in this document. Internal company requirements and the regulations
that apply in the country where the product is being used must be observed.
You must not make any design modifications to the aforementioned Linear Unit
yourself. We will assume no liability for any resulting damage or injury. You may
only install, operate and maintain the Linear Unit if:
▪The Linear Unit has been integrated properly and safely into the completed
machine,
▪You have carefully read and understood the installation guide,
▪You are appropriately qualified,
▪You are authorised to do so by your company,
▪You are using only original equipment from the manufacturer.
Unsafe or inappropriate use of the Linear Unit runs a risk of serious injury
through crushing and cuts.
1. During transportation
Observe the handling instructions on the packaging. Until it is installed, the
product must be stored in its original packaging, protected from moisture and
damage. Ensure that moving parts are secured when in transit and cannot
cause any damage.
2. During installation
Always deactivate the power to the relevant system part and ensure it is not live
before installing the product and/or plugging it in or unplugging it. Ensure the
system cannot be switched back on. Lay cables and lines in such a way that
they cannot be damaged and do not represent a trip hazard. Avoid areas that
pose slip, trip and fall hazards.
3. During commissioning
Allow the product to acclimatise for a few hours before starting to use it. Ensure
that the partly completed machine is securely and safely integrated into the
completed machine. Only start up a product that has been installed in full.
4. During operation
Ensure that only persons who have been authorised by the operator have
access to the immediate operating area of the system. This also applies when
the system is not in operation. It must not be possible to actuate moving parts
unintentionally. In the event of an emergency, malfunction or other irregularity,
deactivate the system and ensure it cannot be switched back on. Prevent the
possibility of persons becoming trapped in the system’s accessible hazard
zone.
5. During cleaning
Close all openings with suitable protective equipment to ensure that cleaning
agents cannot penetrate the system. Do not use aggressive cleaning substanc-
es. Do not use a high-pressure cleaner when cleaning the system.
6. During maintenance and servicing work
Carry out the prescribed maintenance work at the intervals stipulated in the
user guide. Ensure that no line links, connections or components are removed
while the system is live and under pressure. Ensure the system cannot be
switched back on.
7.Duringdisposal
Dispose of the product in accordance with the national and international regula-
tions that apply in your country.

4
L
x
y
z
Fz
Mz Fx
Mx
Fy
My
Similar to the picture
Operating parameters
Linear Unit LRE 8 D25 ZU 80 R25 is generally constructed from Line 8 profiles
that have been cut to size and various assemblies. Before starting installation
work, it is important to check that all parts are present.
Support width
Lmax when Fz
max [mm]
Support width
Lmax when
Fy max [mm]
Fy max [N] Fz max [N] Mx max [Nm] My max [Nm] Mz max [Nm] Operating
load
Fx max [N]
Linear Unit LRE 8 D25
120x80 ZU 80 R25
1900 1000 7600 5200 301 520 760 1200
Linear Unit LRE 8 D25
200x80 ZU 80 R25
3600 1300 7600 5200 301 520 760 1200
320
160
40
120
S
H
S
160
L=2xS+H+640
Linear Unit LRE 8 D25 120x80 ZU 80 R25
Maximum stroke Hmax 5620 mm
Safety clearance S 30 mm
Basic mass (when stroke length = 0 mm) m131.1 kg
Mass per mm of stroke m220.7 g/mm
Total mass m = m1+ H * m2
Repeatability 0 .15 mm
Maximum acceleration 10 m/s2
Maximum travelling speed 10 m/s
Feed constant 280 mm/r
1 pce.
0.0.663.36
L=2xS+H+640
320
160
40
120
S
H
S
160
Linear Unit LRE 8 D25 200x80 ZU 80 R25
Maximum stroke Hmax 5620 mm
Safety clearance S 30 mm
Basic mass (when stroke length = 0 mm) m132.8 kg
Mass per mm of stroke m225.0 g/mm
Total mass m = m1+ H * m2
Repeatability 0 .15 mm
Maximum acceleration 10 m/s2
Maximum travelling speed 10 m/s
Feed constant 280 mm/r
1 pce.
0.0.666.53
The maximum possible drive torque is: TD= 52 Nm
The frictional torque or starting torque without load for the Linear Unit, depend-
ing on the Timing-Belt Reverse Units and Timing Belt tension, is: TF= 2.3 Nm

5
320
160
40
120
S
H
S
160
L=2xS+H+640
Environmental considerations:
Storagetemperature: –20°Cto+70°C
Relative humidity: 5% to 85%
Linear Unit LRE is intended as a permanent fixture to be used in an area that is
protected from the weather.
The area should be free from mould and fungus and show no traces of rodents
or other pests.
Do not install or use in close proximity to industrial plants that produce chemi-
cal emissions.
Do not install or use near sources of sand or dust.
Do not install or use in an area that is regularly exposed to high-energy surges
such as those caused by presses or heavy machinery, for example.
In case of doubt regarding resistance to certain chemicals such as test oil,
alloyed oils, aggressive cleaning substances, solvents or brake fluid, we advise
that you consult your specialist representative.
Consult the manufacturer if using in very salty air. Deflection in the linear axis of
the LRE should not exceed 1 mm over an axis of 1000 mm. In scenarios where
high demands are placed on the system dynamics, supports should be added
every 300 mm to 600 mm. These supports must not affect the Reverse Units.
The safety distance S is a reserve distance to accommodate tolerances
and carriage overtravel under high loads and accelerations at the reversal
point. It must be factored into the equation depending on the capabilities of the
drive and Controller, but in any event should not be smaller than shown!
Fundamentally, a Linear Unit converts a rotary motion into a translational
motion.
A Linear Unit is made up of:
▪Guide
▪Drive
▪Support profile
These components are picked for assembly and assembled in part or in full,
depending on customer wishes.
Preparation
Drive,
e.g.: Timing Belt R25 T10 and Timing-Belt Reverse Unit 8 80 R25 with Bore
Support profile,
e.g.: Profile 8 120x80
Guide,
e.g.: Roller guide 8 D25

6
On longer stretches, when the support profiles have already been installed
or are being held in a vice and the Shaft-Clamp Profile has been pressed into
place, you can press the shaft into the Shaft-Clamp Profile section by section
using the Mounting Aid (0.0.265.38) and a lever in the form of a suitable
round steel bar.
d=⌀10mm
b = DIN 6325-10x40 dowel pin
When higher loads are involved, it is advisable to secure the Shaft. Ideally, a
Combination Drilling Jig (c) should be used to machine the Shaft, Shaft-Clamp
Profile and Support Profile as detailed in the following steps:
▪Using a carbide drill, cut a blind hole in the Shaft, 40 mm from the end face
(as shown in the drawing)
▪At the same distance from the end face, cut a through hole (d) through the
Shaft-Clamp Profile and Support Profile together, up to the centre bore of
the Support Profile
▪Press dowel pin (b) DIN 6325 into the Shaft
▪Install the Shaft into the Shaft-Clamp Profile as described above
Installation
Shaft-Clamp Profile and Shaft:
There are various methods for assembling support profile, Shaft-Clamp Profile
and Shaft.
To make installation easier, apply a film of oil or grease to the outer surfaces of
the Shaft-Clamp Profile that come into contact with the support profile before
pressing it into the groove. Do the same to the contact points between the
Shaft and Shaft-Clamp Profile and to the guiding Shaft itself. When working
with short support profiles that have not yet been connected to a fixture, it is
advantageous to undertake installation in the following steps:
▪Press the Shaft-Clamp Profile into the relevant groove of the support profile
▪Use a vice (fitted with protective jaw plates) to press in the Shaft
▪Follow the same sequence for the other side
Bearing Units can be mounted onto any MB system profile element. There
are two different methods that can be used to secure Bearing Units to the
standard Line 8 groove:
a) The heads of the Button-Head Screws and Washers are located within
one of the grooves on the Bearing Unit, which means through holes need to
be provided so that an Allen key can reach the screws. Holes for the most
common fixing arrangement have been pre-drilled into the Bearing Units. For
other fixing arrangements, such as turned through 90° and using the second
groove, holes will need to be drilled.
b) The T-Slot Nuts are located within one of the grooves on the Bearing Unit
and the fastening screws are inserted into the guide carriage.
Guide carriage/Bearing Units
c=Art.No.0.0.373.15forShaftD25

7
180
140
60
120
80
Ø25
320 141
□320
You must prepare the eccentric orientation of the eccentric Bearing Units
before using the guide carriage.
Use an Allen key to turn the eccentric bolt of the rollers:
▪Drive the bolt as far as it will go
▪Turn back ½ a turn
▪Continue turning back until the rearmost eccentric position is reached
If there are undefined loads on the guide unit such as impact loads that
could cause movement in the Bearing Units, the Bearing Units will need to be
reinforced. You can do this by drilling and pinning (a) the Units in the positions
indicated or the areas shown in dark grey.
Application options
When Bearing Units have been prepared and installed in this way, the maximum
play between the rollers and Shafts can be used to adjust preload.
Once the support profile has been machined, prepared and connected with the
Shafts and Shaft-Clamp Profiles, the guide carriage can be slotted into place
on it. Slot the carriage on before fitting the End Cap and Lubricating System (or
remove the latter first).
Slot the guide carriage in its preassembled state onto the support profile that
you fitted the guiding Shafts to earlier.
When adjusting the Bearing Units to eliminate play, ensure that no excess
strain is generated!
After making this adjustment, fix the position of the eccentric bolt by securing
the lock nut with a Pin Spanner (T). While doing so, use an Allen key to hold
the bolt in its selected position.
T = 100 Nm
Finally, install the End Cap and Lubricating Systems and Caps.
In combination with Profile 8 120x80 as a support profile, guide carriages from Line 8 and Double-Bearing Unit 8 D25:

8
141
□320
260
220
200
140
80
Ø25
320
∅60/2.5
120
∅34
160
103.5
14 Ø34
160
103.5
120
Ø60/2.5
14
Installing the Timing Belt
Application options
In combination with Profile 8 80x40 as a support profile:
In combination with Profile 8 80x80 as a support profile:
In combination with Profile 8 120x80 as a support profile:
Timing-Belt Reverse Unit 8 80 R25 with BoreTiming-Belt Reverse Unit 8 80 R25 with Bore
It may be necessary to open Timing Belt Reverse Unit 8 80 R25 in order to
insert or replace the Timing Belt in it. To do this, remove all the screws. Never
use a screwdriver or similar tool to prise open the casing of Timing-Belt Reverse
Unit 8 80 R25 at its joins, as you may unintentionally break off the belt cover.
Separate the two halves of the casing by gently tapping the hub of the timing
pulley (use plastic punches). Once the casing is open, thread the Timing Belt
through (180° reversal with emergence dimension of 40 mm or 80 mm) and
then close Timing Belt Reverse Unit 8 80 R25 again.
Recommended tightening torques for closing the Reverse Unit:
Button-Head Screw M8 = 16 Nm
Hexagon Socket Head Cap Screw M6 = 10 Nm
Caution: If the Timing Belt is to be fed out of the Reverse Unit with an emer-
gence dimension of 40, insert both ball bearings into the two halves of the
Reverse Unit casing so that the back (smooth side) of the Timing Belt is routed
over the ball bearing outer ring.
In combination with Profile 8 200x80 as a support profile, guide carriages from Line 8 and Double-Bearing Unit 8 D25:
Once the carriage has been fitted to the support profile and adjusted to elimi-
nate play, the Timing-Belt Reverse Units can be prepared.
Timing-Belt Reverse Units 8 80 R25 with Bore for an expanding hub coupling
are used to drive or reverse Timing Belt R25 T10 to build Linear Units com-
bined with guides, Gearboxes and Drive Units.

9
21
21
R3
R3
Connecting Timing Belt Reverse Unit 8 80 R25 to Line 8 profiles (con-
struction height 80 mm and over).
Separating the special T-Slot Nut at the pre-determined breaking point.
Fastening arrangement of Timing Belt Reverse Unit 8 40 R25 on different
profiles depending on the position of the Timing Belt when fed back through.
Attachment options
Next, fasten the Timing-Belt Reverse Units to the support profile and align the
Timing Belt with the profile.
Securing and tensioning Timing Belt R25 T10
To secure and tension the Timing Belt on a guide carriage, you will need to fit a
Timing-Belt Tensioner Block in the correct width at each end of the Timing Belt.

10
180
140
60
120
80
Ø25
320
19
⌀5.5
40
20
⌀10.5/5
40
19
44
ΔL =
LFV
_______
1000K
Similar to the picture
The corresponding holes, grooves and fastening materials are provided on
Slide LRF for the purpose of fixing the tensioning elements in place. When
working with high loads, the Fixing Block needs to be pinned (Dowel Pin ISO
2338,⌀6mm)Theprepared⌀5.5mmholesdeterminethepositionofthe
Dowel Pins.
Insert both ends of the Timing Belt into the Tensioning Blocks so that the cavity
inside each Tensioning Block is filled then screw securely into place. Fix one
Tensioning Block in place under the carriage plate and use the other to tension
the Timing Belt with the aid of the long Hexagon Socket Head Cap Screws of
the centrally located Fixing Block. When doing so, adjust the two tensioning
screws alternately to ensure the tension on the Belt is evenly distributed.
The necessary Timing-Belt tension must be determined and set in line with the
anticipated loads.
Tensioning screws
Timing-Belt Tensioner, Tensioning Block 8 R25, 0.0.426.29 [b] Timing-Belt Tensioner, Fixing Block 8 R25, 0.0.426.30 [a]
If the LRE 8 D25 ZU 80 R25 has been supplied fully preassembled, you
will need to check the pre-tensioning against the order specifications. After a
running-in time of 24 hrs, check the operating tension of the Timing Belt again
and adjust it if necessary. When tensioning the Timing Belt, first identify the
zero point at which the untightened Belt has no sag at all and pre-tensioning
begins. To do that, draw the moving part of the Tensioning Block towards its
fixed counterpart by alternately tightening the tensioning screws. Calculate the
necessary tensioning adjustment or elongation of the Timing Belt according to
the operating load of the Linear Unit.
Conventional calculation:
Following applies: FP+ Fx< FBperm
and: FP> Fx
Where: Fx= m x a+ m x g +FB
Where: ΔL= Tensioningadjustment[mm]
L= TotalTimingBeltlength[mm]
FP= Pre-tensioningforceforTimingBelt[N]
FBperm= PermissibleforceforTimingBelt[N]=2400N
Fx= Operatingload[N]
TF= Frictional torque, loss of friction when running light
[Nm]=2.3Nm
rE= Effectiveradius[mm]=44.56mm
C= Constantofexpansion[N]=500N
The calculated tensioning adjustment can be checked by various means.
Typical tools include frequency analysis tools, strain gauges and simple length
measuring devices.
Tip:
The necessary elongation calculated for the Timing Belt is constant along
its full length. The actual elongation of the Timing Belt as calculated for this
segment can be checked and thus adjusted by marking a specific length on
the Timing Belt (e.g. 1 m) and using a steel ruler.

11
Positioning Proximity-Switch Cams
The Proximity-Switch Cams run through Timing-Belt Reverse Unit 8 80 R25.
When used on the drive-side Timing-Belt Reverse Unit 8 80 R25, they are
particularly useful for simplifying the wiring between Drive Unit, limit switch
and motor control unit.
Positioning Proximity Switches
The Proximity-Switch Fastening Set can be used to position and secure induc-
tive Proximity Switches for homing positions and electric terminal position
limits in the system groove of Timing-Belt Reverse Unit 8 80 R25.
The Proximity Switch fixings must be shortened as appropriate to the applica-
tion scenario.
Similar to the picture
The Proximity-Switch Cams are used to mark the electric terminal position
limit and the reference point of the moving unit and Timing Belt. Push them
into the Timing belt from the smooth side, locating them at the desired point
along the length of the belt and centrally in the width of the belt.
The Proximity-Switch Cams can run through Timing Belt Reverse Units 8 40
R25 because the timing pulleys in these units feature a corresponding cut-out.

12
ØD
kmin
kmax
a
b
M
□120
94
12
□120
∅34
Drive Set
[mm] 8 80 D80/D34
⌀D 12-45
a12
b106
kmin 48.5
k max 63.7
Coupling half that accommodates the drive shaft
Coupling Housing with hole (that can be sealed) to allow an Allen key through
to generate the necessary clamping force on the drive shaft.
Connecting Drive Set 8 80 D80/D34 – 0.0.668.04
Drive Set 8 80 D80/D34 is used to connect any drive to Linear Unit LRE 8
D25 ZU 80 R25.
The prepared coupling fits the drive shaft and transmits drive torque without
backlash.
Hexagon Socket Head Cap Screws DIN 912 M8x100 are supplied with the
Drive Set for this purpose and are screwed through the housing of the Drive
Unit and into the Coupling Housing of the Drive Set.
Tightening torque: T = 25 Nm
Machine the drive casing or Adapter Plate according to the requirements of
the motor or gearbox you are using and then screw it to the motor or gearbox.
Take the coupling half that is to be connected to the drive shaft and drill a hole
in it to match the drive shaft then connect the coupling half and the shaft.
The torques transferred by the clamp connection factor in the maximum
matingplayforshaftfits:Shaftk6/holeH7.
Force is transferred from the coupling to the drive shaft by means of frictional
resistance. The Shaft and the hole in the coupling hub must be degreased and
cleaned to ensure the frictional resistance is effective. Hexagon Socket Head
Cap Screws must be secured against working loose.
Adapter plate

13
□120
94
Ø34
12
□120
e
dc
b
a
Similar to the picture
Connecting Drive Set ZU 8 80 D80/D34 AP/WP 80 – 0.0.672.76
DriveSetZU880D80/D34AP/WP80(0.0.672.76)isusedsolelytoconnect
item drives. The Drive Set is fully prepared for installation on the corresponding
Linear Unit. The drive shaft transfers drive torque without backlash.
The torques transferred by the clamp connection factor in the maximum
matingplayfortheshaftfits:Shaftk6/holeH7.Forceistransferredfromthe
coupling to the drive shaft by means of frictional resistance. The shaft and the
hole in the hub must be degreased and cleaned to ensure a frictional connec-
tion for the drive. Fasten the first coupling half to the Reverse Unit, ensuring
that the Hexagon Socket Head Cap Screws used are secured against working
loose. Clamping screw: T = 49 Nm.
Use Hexagon Socket Head Cap Screws DIN 912 M8x100 (included with the
Drive Set, T = 25 Nm) to screw the Coupling Housing of the Drive Set over the
entire Coupling through the casing of the Drive Unit.
Next, use the prepared Centring Piece to fasten the Gearbox flush on the Adapt-
er Plate of the Drive Set. Use Hexagon Socket Head Cap Screw DIN 912 M6x15
(T = 13 Nm) for this purpose.
Hexagon Socket Head Cap Screws DIN 912 M5x20 (T = 10 Nm) are included in
the Drive Set for the purpose of fastening the Motor to the Gearbox.
Working through the Coupling Housing, create a friction-based connection
between the Hexagon Socket Head Cap Screw DIN 912 M8x30 (T = 23 Nm) of
the clamp coupling half and the drive shaft.
a: Hexagon Socket Head Cap Screw DIN 912 M8x100
for connecting a Timing-Belt Reverse Unit
b: Hexagon Socket Head Cap Screw DIN 912 M6x15
c: Hexagon Socket Head Cap Screw DIN 912 M8x20
d: Hexagon Socket Head Cap Screw DIN 912 M5x20
e: Expanding hub coupling D80/D34

14
a
b
⌀34
⌀55
⌀25
Linear Unit Art. No. Synchronising Set Art. No.
Linear Unit LRE 8 D25 120x80 ZU 80 R25 0.0.663.36
Synchronising Set D55/D34 0.0.666.60
Linear Unit LRE 8 D25 200x80 ZU 80 R25 0.0.666.53
Tube D25x3 St
Synchronising Set b
a
D55/D34
a - 82 mm Distance between
Linear Units
A suitable Tube St (sawn to length) turns the Synchronising Set into a com-
plete Synchroniser Shaft.
Synchronising Sets are used when two Linear Units are to be run in parallel.
item Synchronising Sets comprise couplings that are fitted between two Linear
Units and are connected by a Synchroniser Shaft that has been manufactured
in the appropriate length. This ensures that the end result is a highly custom-
ised and flexible design.
Synchronising Sets from item can be used to operate two Linear Units in paral-
lel with just one motor. They comprise shaft Couplings that are tailored to the
relevant Linear Unit and designed to compensate for slight misalignments and
withstand the stated torque over long-term use. The Couplings are pre-prepared
to accommodate a Synchroniser Shaft. Besides featuring a compact design,
expanding hub couplings are also easy to use. The friction-based connection is
created by tightening the central screw with the specified tightening torque. An
integrated pull-off thread makes them easy to dismantle. First, the central screw
is removed, then a longer screw is driven into the same position to effortlessly
relieve tension in the Coupling. How long a Synchroniser Shaft can be depends
on its operating speed. To determine the maximum length for a given speed
or the maximum speed for a given length, please consult the information
contained in the diagrams.
Synchronising LRE 8 D25 ZU 80 R25

15
Tube D25x3 St
Synchronising Set b
a
D55/D34
a - 82 mm Distance between
Linear Units
Maintenance
End Cap and Lubricating Systems are essential in order to protect and lubricate
the Bearing Units. These should be fitted back in place only when the guide
carriage has been mounted on the Shafts. Otherwise, it is important to ensure
the movable wipers are pressed back when sliding the guide carriage onto the
Shaft, to ensure they are not bent.
Wipers located in the internal recesses of the end-face End Cap and Lubricating
Systems are also designed to take up the lubricant. They are pressed against
the guiding Shaft by a spring. These wipers are supplied pre-charged with lubri-
cant and can be topped up with lubricant as required via the hole in the cap.
In the event of considerable soiling, you may need to replace the wipers.
Lubrication
Suitable for use in dry conditions and over the temperature range -20°C to
+70°C.
If operating conditions are unusual - e.g. special type of installation, dust, short
stroke, influence of solvents etc. the lubrication intervals must be adapted
accordingly.
This information does not discharge the user from the obligation to carry out his
own assessments and checks.
It is important to bear in mind that our products are subject to a natural process
of wear and ageing.
The rollers of the guide are maintenance-free. The spring-loaded end cap and
lubricating felts can be topped up with lubricant as required via a hole.
Recommended re-oiling period: Every 6 months or every 2500 km. The felt
pieces are supplied in ready-oiled condition.
Synthetic lubrication oil ISO VG 460, e.g. item Track Oil for Linear Guides
(0.0.612.75).
Add the following quantity to each maintenance hole at the end of each mainte-
nance interval: 1 ml
Greases containing solid particles (e.g. graphite and MoS2 additives) must not
be used!
Oil Can for Linear Guides (one actuation delivers approx. 1 ml of oil).
To ensure adequate lubrication, the carriage must cover a minimum travel
distance.Minimumstrokelength[mm]:160mm
The Timing Belt is a maintenance-free drive element.
Check the tension on the Timing Belt after a running-in phase.
We recommend regular checks for damage and wear. These checks should be
carried out weekly at first and then adjusted to account for environmental and
operational conditions.
The Timing Belt may need to be replaced.
Ideal operating conditions:
Ambient temperature: 10°C ... 40°C
Load: < 5%

You can find the Notes on Use and Instal-
lation online, in the download section for
this product.
10/2017
© item Industrietechnik GmbH Made in Germany
item Industrietechnik GmbH
Friedenstrasse107-109
42699 Solingen
Germany
Phone +49 212 6580 0
Fax +49 212 6580 310
info@item24.com
item24.com
Other manuals for LRE 8 D25 ZU 80 R50
1
Table of contents
Other ITEM DC Drive manuals
Popular DC Drive manuals by other brands
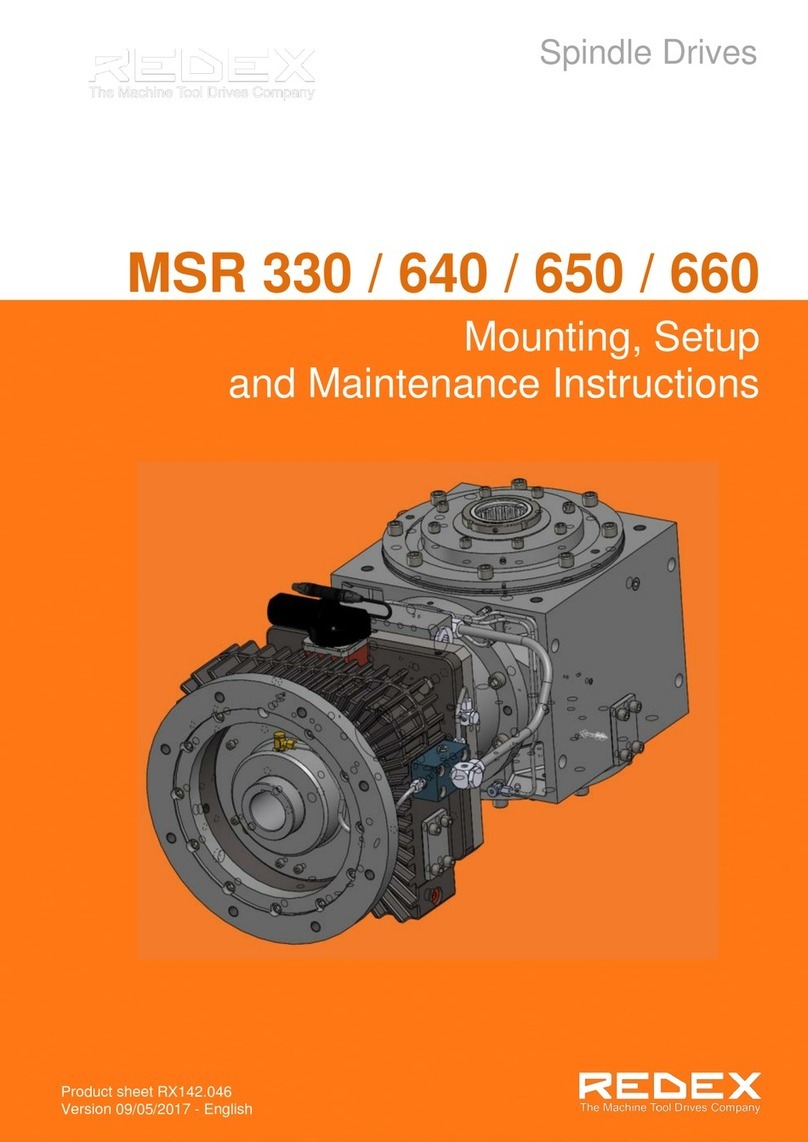
REDEX
REDEX MSR 330 manual
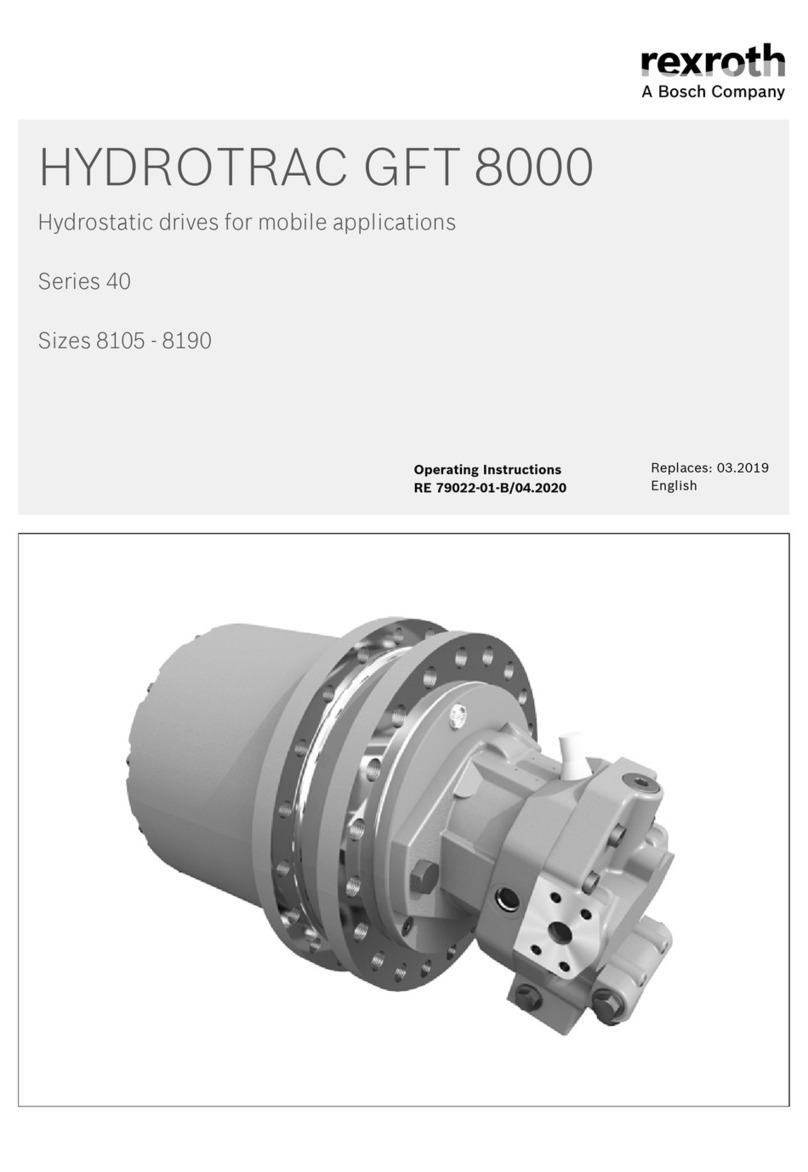
Bosch
Bosch REXROTH HYDROTRAC GFT 8000 operating instructions
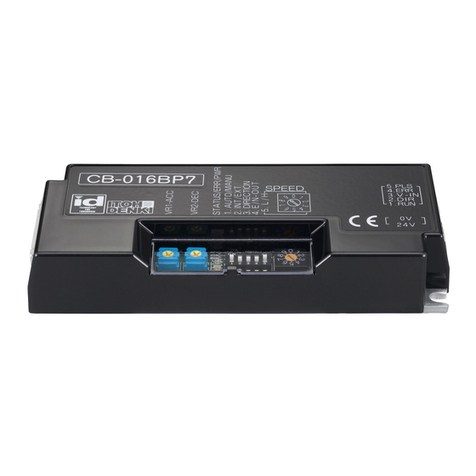
ITOH DENKI
ITOH DENKI CB-016BP7 manual
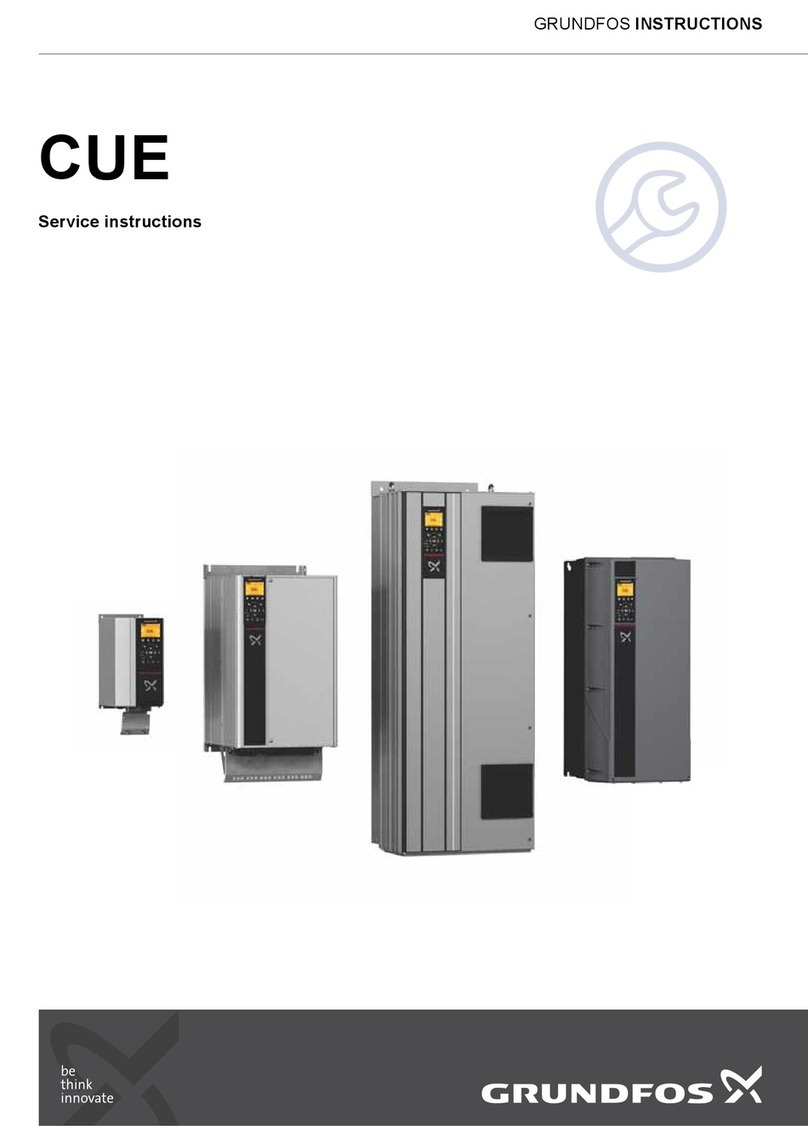
Grundfos
Grundfos CUE Series Service instructions
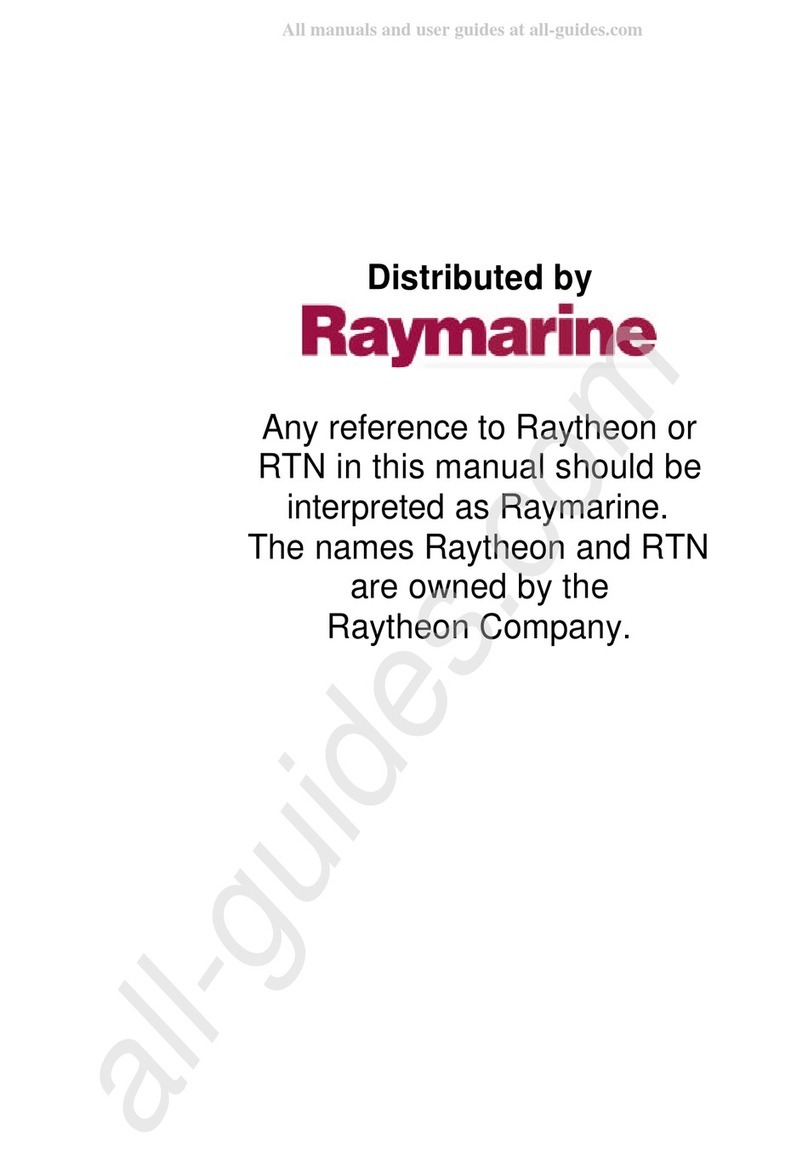
Raymarine
Raymarine E12026 installation guide
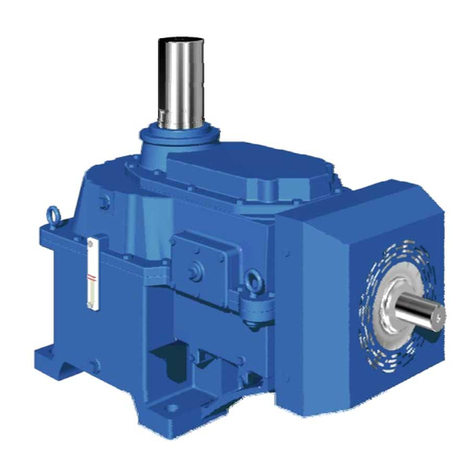
Sumitomo Drive Technologies
Sumitomo Drive Technologies PARAMAX SFC Series Operating and maintenance manual