Jflow controls 5500 Series User manual

INSTRUCTION MANUAL
5500 SERIES PLUG VALVES
Scope of Manual
This instruction manual includes installation, maintenance and parts information for the J Flow 5500 Series
Plug Valve.
Do not install, operate or maintain a 5500 Series valve without being fully trained and qualied in valve in-
stallation, operation and maintenance. To avoid personal injury or property damage, it is important to carefully
read, understand and follow all the contents of this manual including all safety cautions and warning. If you
have any questions about these instructions, contact J Flow Controls before proceeding.
Installation Instructions
1. Before installing, inspect the valve and any associated equipment for damage and any foreign material.
Make certain the valve interior is clean and the pipelines are free of foreign material.
2. Use accepted piping and welding practices when installing the valve in the line.
FLANGED PLUG VALVES
1. Remove ange protectors
2. Insert valve into process line
3. Use appropriate gasket and bolts, and bolt the valve into your process line
SOCKET WELD AND BUTT WELD VALVES
1. Socket weld and butt weld plug valves must be welded into line prior to operation. Use only ASME qualied
procedures and personnel for weld instruction.
2. Remove the plastic protection cap.
3. Inspect the valve and any associated equipment for damage and any foreign material. Make certain the
valve interior is clean and the pipelines are free of foreign material.
4. The area to be welded should be cleaned of grease and oil and moisture free.
5. The valve should be shipped in the open position.
6. Carefully examine the maximum temperatures of the body sleeve area. You should not exceed the respec-
tive maximum temperatures. Contact the factory for additional help if needed.
7. Th welder can wrap a damp, reproof cloth around the body at core area to reduce the temperature at the
body sleeve area. Cold water can also be poured as needed to reduce the temperature.
8. For valves with socket welding end - insert the tube in the socket to maximum and retract is 0.08”. Make
two welding tacks to dene welding position then continue welding.
9. For valves with butt weld ends, leave a 0.08” gap between pipe and valve end and ll gap with weld for full
penetration.
10. Weld using low heat input and gradual welding technique. Discontinue welding after each pass or as often
as needed. When ordered, the valve conguration and construction materials were selected to meet partic-
ular pressure, temperature, and controlled uid conditions. Some body/trim material combinations are limit-
ed in their pressure drop and temperature ranges. Do need exceed maximum temperatures of materials.
Allow the metal to cool below 175 degrees F prior to continuing the weld.
J Flow Controls® • 4665 Interstate Drive • Cincinnati, OH 45246 • 513-330-6354 • www.jowcontrols.com

INSTRUCTION MANUAL
5500 SERIES PLUG VALVES
Operating Instructions
1. Lever: Align lever with valve body to open valve, move lever to 90° of valve body to close.
2. Gear Operator: turn ear operator wheel clockwise to open valve, counterclockwise to close valve.
Maintenance Instructions
Plug valves and installed gear operators on Sleeved plug valves do not require maintenance - periodic lubrica-
tion. However, in the case of any maintenance, follow the below instructions.
1. Always wear protective glove, clothing and eyewear when performing any maintenance operation to avoid
personal injury.
2. Disconnect any operating lines providing air pressure, electric power, etc. Be sure any actuator cannot
suddenly open or close the valve.
3. Use lock-out procedures to be sure that the above measures stay in effect while you work on the
equipment.
4. Check with your process or safety engineer for any additional measures that must be taken to protect
against process media.
5. Certain adjustments may be performed as needed.
Seal Adjustments
1. All J Flow Control Valves are factory adjusted and pressure tested for bubble tight seal. Normally further
adjustment is not required. Should seepage occur at the plug stem or downstream, the following
adjustment procedure should be followed.
Locate the three adjusting bolts spaced at 120° from each other around the plug stem. Each of these bolts
should be tightened in 1/4 turn increments until seepage stops. Care should be taken to prevent over
adjusting as this will result in excessive operating torque. The valve should be operated a full cycle after
each adjustment.
Should seepage still occur after adjustment, seals may require replacement.
Top Seal Replacement
1. Caution: Before attempting to disassemble the valve, care should be taken to ush out any hazardous u-
ids and release entrapped pressures. Failure to do so could result in serious personal injury.
Top Seal Replacement - Disassembly Procedure
1. Back off the three adjusting bolts until they are several turns clear of contact with the thrust collar.
2. Rotate the plug oneor two times which will allow the plug to pop up from the sleeve relieving any pressure
that may be trapped below the plug.
J Flow Controls® • 4665 Interstate Drive • Cincinnati, OH 45246 • 513-330-6354 • www.jowcontrols.com

INSTRUCTION MANUAL
5500 SERIES PLUG VALVES
J Flow Controls® • 4665 Interstate Drive • Cincinnati, OH 45246 • 513-330-6354 • www.jowcontrols.com
3. The cover bolts should then be loosened four complete turns only and the plug rotated one or two cycles,
or until it is evident the plug is loose not allowing trapped pressure.
4. All the cover bolts and cover should be removed.
5. With a twisting motion, lift the plug from the body.
6. Discard all of the stem seal components and metal diaphragm from the plug stem, but retain the metal thrust
collar for reuse.
7. The plug and sleeve should be ushed and wiped clean of any residue and visually inspected for any
damage before reassembly. (Note: If damaged, the Peek Sleeve is not field replaceable. Consult factory for
replacement valve.
Top Seal Replacement - Reassembly
8. Refer to Exploded View.
9. Place the plug in the body with the ports in the open position. New top seal components should be placed
on the plug stem in the following order:
- Combine diaphragm and stem seal collar
- Delta ring
- Combination formed metal diaphragm and static eliminator
- The used thrust washer should be placed on top of the metal diaphragm
- The adjustment bolts should be backed off ush with bottom of cover bore
- Place the cover over the plug stem
- Press the plug into the body using a press until the plug port opening is approximately 1/16 inch above
the bottom of the body port opening
10. Make sure the diaphragm is sitting in the inner counter bore of the body and the metal diaphragm
and seating shoulder of the cover are sitting in the outer body bore.
11. The cover bolts should be tightened uniformly to the following torque valve
Bolt Size Ft. lb
5/16" 12
3/8" 20
7/16" 35
1/2" 45
5/8" 95
3/4" 130
12. Tighten the adjusting bolts uniformly 1/4 turn at a time until contact is made with the thrust collar, plus 1/4
turn each to seat the plug.
13. Replace the wrench or gear operator assembly and rotate the plug one full cycle.
14. Leave the plug in the open position until installation.

INSTRUCTION MANUAL
5500 SERIES PLUG VALVES
J Flow Controls® • 4665 Interstate Drive • Cincinnati, OH 45246 • 513-330-6354 • www.jowcontrols.com
35
No Part Name Materials No Part Name Materials
1Nameplate A276 304 19 Single Way Fitting
2Rivet T3 20 Connector A182-F6A
3Lower Cap A216 WCB 21 Sealant 7605
4Nut 1025+CR 22 Stem 4140-FNP
5Adjustable Screw 1045+Zn 23 Gasket RPTFE
6Plate 1045 24 Stem Sealant 7602
7Gasket Plate A36 25 Emergency Stem Injector Flexible Graphite
8Settel Gasket A276 304 26 Fire Safe Graphite Packing
9Graphite Gasket Flexible Graphite/304 27 Screw A193-B7
10 Bolt B 28 Connector Plate A105
11 Seat Ring NBR 29 Nut A194-2H
12 Plug A216 WCB+PTFE 30 Bolt A193-B7
13 Body A216 WCB 31 Stem Seal Ring NBR
14 Spring 17-7PH 32 Flexible Parallel Pin 1065
15 SS Ball A276 304 33 Single Flat Pin 1035
16 Spring A276 304 34 Flexible parallel pin 1037
17 Bolt Cap 1025+Zn 35 Gear actuator
18 Injector Injector
3433
32
31
30
29
28
27
26
25
24
23
22
21
20
19
18
17
16
15
14
13
12 11 10 9 8765 4 321
Exploded View
Note:
Exploded view and parts list below
are representative of the various
plug valve configurations available.
Consult project Code 1 Drawings for
specific details of valves and
materials of construction provided.
Table of contents
Other Jflow controls Control Unit manuals
Popular Control Unit manuals by other brands
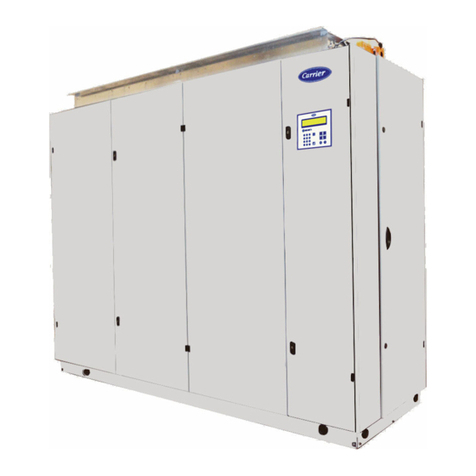
Carrier
Carrier 50CO Series Installation, operation and maintenance instructions

Honeywell
Honeywell S4567A 1001 instruction sheet
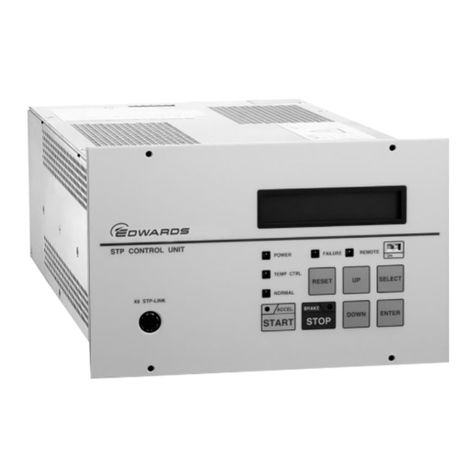
Edwards
Edwards SCU-800 instruction manual
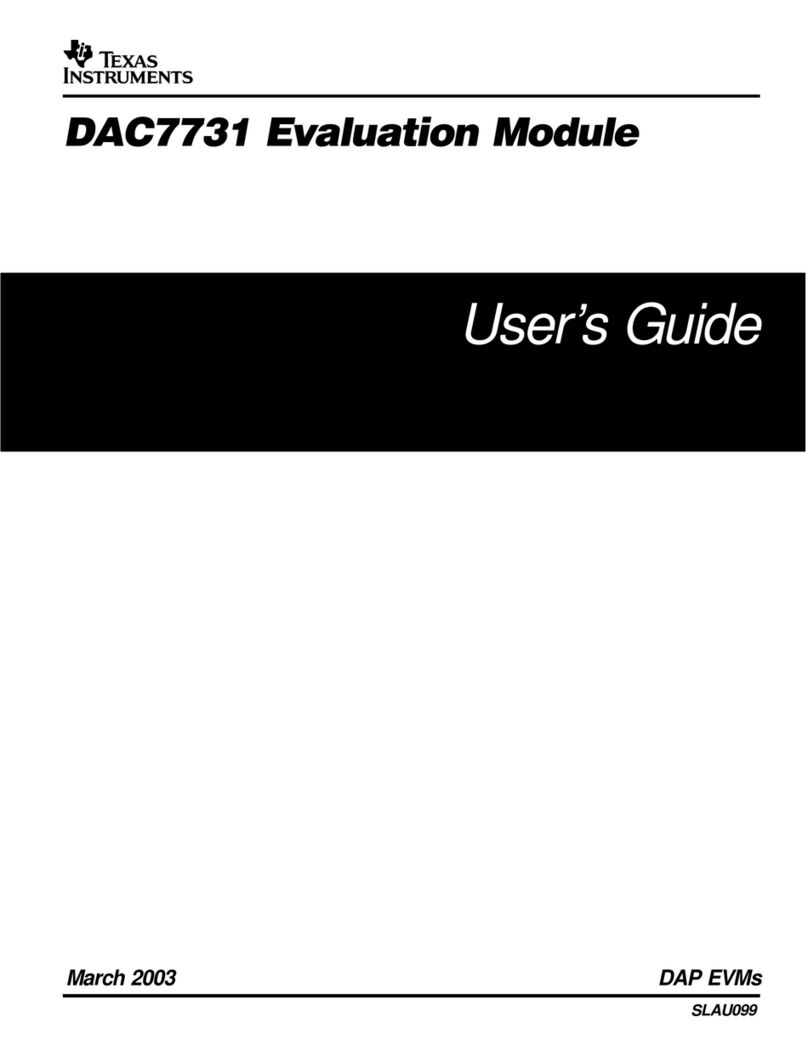
Texas Instruments
Texas Instruments DAC7731 user guide
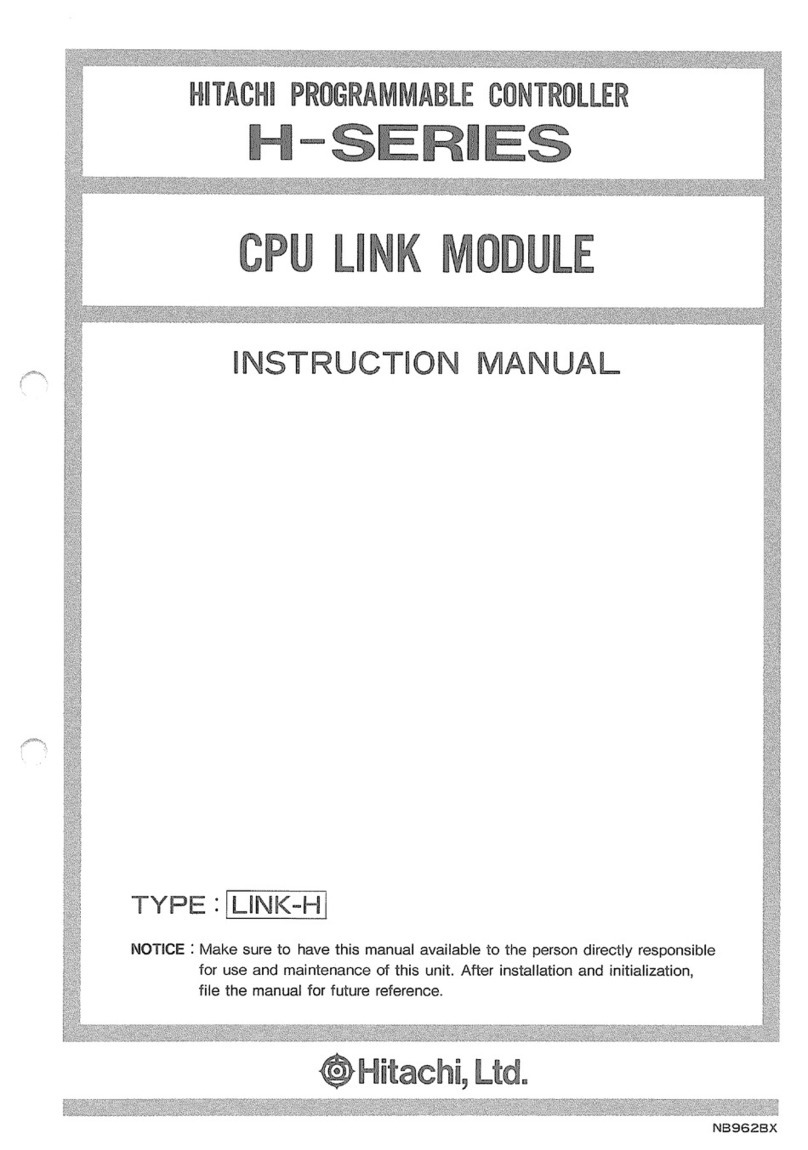
Hitachi
Hitachi H Series instruction manual
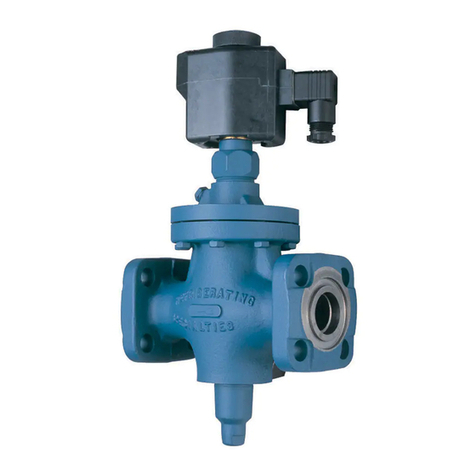
Parker
Parker S5A Installation, Service and Parts Information