Johnson Controls RLBC Series User manual

RLBC SERIES ULTRASONIC HEAT METER
USER MANUAL
(DN50-DN150)

2RLBC SERIES ULTRASONIC HEAT METER
TECHNICAL PARAMETERS
CHARACTERISTICS
• Low battery alarming.
• Automatic data correction technology.
• Alarms when the temperature sensor is disconnected or has
a short cut.
• High definition and wide temperature LCD display.
• 8 levels of flow rate and separately adjusted, with high
precision.
• Ultra-low power consumption (static power consumption is
less than 7μA).
• The tube adopts forging technology and with straight-
through integrated body.
• Measuring mechanism has no moving parts and no wear and
tear forever. The measuring accuracy will not be influenced
by using period.
• Easy deployment, horizontal or vertical installation.
• M-BUS, RS485 communication interface, long distance
communication.
• Can be used as integrated or remote type
OVERVIEW
RLBC Smart Ultrasonic Heat Meter is a high performance, low power electronic heat meter developed with reference to related
standards. It is used to measure and display the heat released (absorbed) by the heat (cold) liquid flowing through the heat-cooled
exchange system. It consists of flow sensor, microprocessor and pairing temperature sensor. The microprocessor gets the flow
signal through flow sensor and the signal of water temperature at the entrance and exit from the temperature measuring circuit,
and then calculates exchanged heat by the heat-carrying liquid according to the standard heat calculation formula.
RLBC heat meter have the option of M-BUS, RS485 interface for user choose, with related devices can complete remote energy
management system, which can achieve real-time data reading and control the user's power consumption conveniently.
Flow sensor
Size (mm) Permanent flow rate
(m3/h)
Minimum flow rate
(m3/h)
Maximum flow rate
(m3/h)
DN50 15 0.6 30
DN65 25 1 50
DN80 40 1.6 80
DN100 60 2.4 120
DN125 100 4 200
DN150 150 6 300
Temperature Sensor
Temperature range 4℃~ 95℃
Temperature difference range 3K~ 90K
Minimum display temperature 0.1℃
Minimum display of flow rate 0.1 m3
Minimum display of heat power 0.01MW·h
Minimum display temperature 0.1℃
Static working current ≤7μA
Battery lifetime >6 years
Digit number of display screen 8 digits
Maximum accumulated heat
power
4.2×106MW·h (Only final 8 numbers can be displayed when accumulated heat power is more than
999999.99 MW·h)
Maximum accumulated flow
rate
4.2×109m3(Only final 8 numbers can be displayed when accumulated flow rate is more than
9999999.9m3)
Working status indicator Always display in cycle
Accuracy Class 2
Pressure resisting 1.6MPa
Loss of pressure ≤0.025MPa
Power supply DC3.6V lithium battery, DC12V±0.6VDC (Modbus)
IP Protection IP54
Connection Flange (ISO7005-2)
Valve body material Ductile Cast Iron (QT450—10)
Communication M-Bus(CJ/T188 protocol); RS485(Modbus protocol)
Ambient operating temperature 5℃~55℃
Ambient storage conditions temperature -25℃~55℃, relative humidity <93%RH

3
RLBC SERIES ULTRASONIC HEAT METER
DIMENSION
INSTALLATION
1. Whole meter installation
• It is suggested that install a filter in front of the heat meter.
• It is suggested that install valve in front of the filter, convenient for repairing and cleaning the filter.
• Clean the pipe before installation to avoid threads, tones or other sundries in the pipeline from causing malfunction of the meter.
• During the installation, please don't wrench, move or knock the component inside of the pipe, to avoid knock against the meter body.
• The heat meter head and its base meter is separate structure and connected by wired connection. So the meter head can be
installed at the position where it is easy to read meter data (the terminal extension line between the meter head and the base
meter is 3m, please refer to the real meter).
• The whole meter installation illustration:
Note: during the installation, please install the joint for inlet temperature sensor into the base meter of ultrasonic heat meter.
Integrated Type Remote Type
Size L(mm)W(mm)H(mm)H1(mm)Connection
DN50 200 165 332 232 Flange¢125-4×¢ 18
DN65 200 185 354 254 Flange¢145-4×¢ 18
DN80 225 200 367 267 Flange¢160-8×¢ 18
DN100 250 220 390 290 Flange¢180-8×¢ 18
DN125 250 250 406 306 Flange¢210-8×¢ 18
DN150 300 285 433 333 Flange¢240-8×¢ 22
Note:Ship out with integrated type as default, if need remote type, please refer to user manual

4RLBC SERIES ULTRASONIC HEAT METER
2. Installation of temperature sensor
A. Installation of temperature sensor for DN50~DN65
• Dimension of probe protecting tube is shown as above.
• Punching a hole vertically at suitable place on the outlet pipe (Diameter of the hole is 15mm).
• Place the probe protecting tube into the punched hole, soldering at the soldering point.
• After cooling the soldering junction, twist the outlet probe into the bottom of the probe protecting tube.
• Seal the probe and probe protecting tube.
B. Installation of temperature sensor for DN80~DN150
(1) Choose the suitable probe and protection tube and welding base according to the pipe diameter, please refer to the following
picture. Unit: mm
Size Probe Length L1
(mm)
Protection Tube L2
(mm)
Welding base
Length L3
(mm)
Inner Diameter D1
(mm)
External Diameter D2
(mm)
DN80 ~DN150 120 85 20 18 28
(2) Punching an installation hole vertically at suitable place on the outlet pipe.(about 18mm)
(3) Welding a base around the installation hole.
(4) After cooling the welding junction, cover the sealed copper gasket on outlet probe protecting tube and shelter sealing adhesive
tape on external thread of the tube, then screw the protecting tube into outlet pipe base, be sure to screw it down.
(5) Insert the probe into the bottom of protecting tube and fixed it with screws.
(6) Seal the probe and the protecting tube.
NOTE:
(1) The inlet probe protecting tube is installed on the meter body before leave factory, only need to install outlet probe.
(2) When welding the base of meter, please upward the internal threaded end, and weld the non-threaded end.

5
RLBC SERIES ULTRASONIC HEAT METER
3. Remote installation
Default as integrated product when ship out from factory. The length between meter head and base meter is 3m.
1. Remove the anti-tamper caps from the screw hole and unscrew the M4 Hex bolts to separate the upper case body and pipeline
body apart. Remove the protective cover from joint part of the three-core cord, then loose and separate the three-core cord
apart.
2. Pull out the connector of six-core cord from the upper case body and then install the bottom cover for the upper case body.
Make sure to press the anti-tamper caps firmly after screwed the bolts.
3. Pull out the connector of six-core cord from the pipeline body and connect with the corresponding connector from the upper
case body. Make sure to align the connectors before tighten up the cover (Note: DO NOT CONNECT THE CONNCETORS
WITHOUT ALIGNMENT). Install the upper cover for the pipeline body by M4 Hex bolts and press the anti-tamper caps firmly to
the screw holes.
4.Install the protective cover to the joint parts of the three-core and six-core cords. Seal the joint part by using the lead seal on
the protective cover.
Upper case body
Pipeline
Upper case body
Six-core cord
Three-core cord
Upper case body
Connector
Upper case Pipeline
Upper case body
Protective cover
Pipeline
Extension cord
Six-core cord
Protective cover
Pipeline
Three-core cord
①②
③④

6RLBC SERIES ULTRASONIC HEAT METER
USAGE
1. Display
Note: If the cumulative heat and cumulative flow beyond the maximum display range of one LCD screen, the LCD only
displays the last 8 digits of data.
2. Data communication
2.1 Remote communication
The ultrasonic heat meter can be supported by collector, concentrator and software to realize remote meter-reading. Before using,
have to create address file in the software, for the same collector, the heat meter ID cannot be repeated. The management office
staff can get the information, such as total consumption of heat power, working status, battery status and etc.
Ultrasonic heat meter remote communication interface: M-bus and RS485 interface
Heat meter will display the following information on LCD in turn :
Total heat power: Total XX.XX MW·h
Total flow rate: Total XX X.X m3
Instantaneous flow rate: Present XXX.XXX m3/h
Inlet temperature: In XX.X ℃
Outlet temperature: Out XX.X ℃
Temperature difference: XX.X K
Instantaneous power: XXX.XX kW
Total working time: Total XXX h
Note:
a. Adopt CJ/T188-2004 Household Measurement Metering Data Transmission Technical Conditions for communication
Each heat meter has an ID on the meter (12 digits ID), such as “ID: 201511293058”, then the heat meter ID will be
“00201511293058”.
b. Adopt GB/T 26831 Community Energy Measurement and Data Collection System Specification
Primary address: factory default is 0, with the range of 1-250, during the debugging of the data collection system, the
primary address is reconfigured through the second address to facilitate meter reading.
Second address: the last 8 digits of meter ID number. For example: the meter printing is "ID: 201511293058", then the
second address is 11293058.

7
RLBC SERIES ULTRASONIC HEAT METER
It will come back to normal working status after display the 24 months info.
Note:
a. For M-bus communication, no need to distinguish the negative and positive pole, just connect the M-bus trunk to the
collector.
b. RS-485 communication line is a 4-core wire, red and blue are 12V AC (or DC) power lines, no need to distinguish
the positive or negative pole when connect the lines. Yellow and green are 485 communication lines, yellow should
connect with A, and green should connect with B. The RS-485 communication line connection between devices must
be connected by hand in hand mode as below picture:
3. Data Inquiry
Heat meter stores data for latest 24 months, such as monthly consumption for heat power and flow. To swipe a magnet on the
position where print ID XXXXXXXX, the heat meter will display below information:
Version number: No. XXXX
Meter size: dnXXX (will display caliber if the stored caliber is
not 0, otherwise it will display the next info)
Primary address: XXX
Meter ID (first 4 digits): XXXX
Second address (last 8 digits): XXXXXXXX
Year, month, date: XX-XX-XX
Hour, minute, second: XX.XX.XX
Current time (year and month): XX-XX
The current month used heat power: Total XXX kW·h
The current month used flow rate: Total XXX.XX m3
Time of last month (year and month): XX-XX
The used heat power of last month: Total XXX kW·h
The used flow rate of last month: Total XXX.XX m3
...... ......
Year and month of the last 23 months: XX-XX
The used heat power of the last 23 months: Total XXX kW·h
The used flow rate of the last 23 months: Total XXX.XX m3

8RLBC SERIES ULTRASONIC HEAT METER
WORKING STATUS
Item Normal working status
Minimum display unit of heat power 0.01MW•h
Minimum display unit of accumulated flow rate 0.1m3
Minimum display unit of inlet and outlet temperature 0.1℃
Minimum display unit of temperature difference 0.1K
Err5 Err6 Err7 Err8 Err9 PT1000 disconnection, open circuit etc Check the hardware
Err-H Infrared communication error Infrared communication again
Unstable flow rate
Ultrasonic probes are not in the same horizontal
plane when horizontally install, and may have air
inside the pipe
Install the meter again and clear
the air inside of the pipe
“o”shows on the upper left ( air warning) Air in the pipe Clear air inside the pipe
1. DN50 ~65 Ultrasonic heat meter
2. DN80 ~150 Ultrasonic heat meter
Ultrasonic Heat
Meter
Temperature
Sensor
Protecting tube
of temperature
sensor
6 cores terminal
extension cord
Joint
protection Tamper cap Manual
Temperature
sensor welding
base
1 Piece
1 Pair
(Inside ultrasonic
heat meter)
1 Piece 1 Piece 2 Pieces 4 Pieces 1 /
Ultrasonic Heat
Meter
Temperature
Sensor
Protecting tube
of temperature
sensor
6 cores terminal
extension cord
Joint
protection Tamper cap Manual
Temperature
sensor welding
base
1 Piece
1 Pair
(Inside ultrasonic
heat meter)
1 Pair 1 Piece 2 Pieces 4 Pieces 1 1 Piece
ERROR SOLUTION
ACCESSORIES
QUALITY GUARANTEE
Standards:
GB/T 32224-2015 Heat meter
GB/T 26831 Community energy measurement and collection data system specification

9
RLBC SERIES ULTRASONIC HEAT METER
Note: The manual is for reference only and is subject to change without notice.
NOTES
During transportation for heat meters, please handle with care, no
bumping, and should avoid to store them in strong electromagnetic
field.
Ultrasonic heat meter can be installed horizontally or vertically on the
water inlet.
When installed horizontally, the display should be on a level surface.
When installed vertically, it must be installed on the straight pipe with
the water flow direction from down to up.
The installation place should avoid flooding, frozen and pollution, and
should leave enough space for repair and maintenance, The direction of
water flow should be consistent with the direction of the flow indicator
on the pipe.
Do not exert too much force when connecting the meter to the pipe,
so as to avoid crushing the sealing gasket and causing water leakage.
During the usage, the smart heat meter should be protected from
strong impact and severe vibration.
Please install two straight pipes with the same diameter (D) as the heat
meter and with a length of 10D and 5D respectively in the upstream
and downstream of the heat meter, otherwise it will cause serious
errors.
ABOUT BATTERY
When the battery power is low, please replace it in time, please change them in time, otherwise, it may cause the big error
of measurement data or cannot control the prepaid function. When replace battery, please pay attention to the positive and
negative polarity of the battery.
It must be replaced battery and sealed by professional agency.
When replacing the battery, please pay attention to the positive and negative polarity of the battery. Use the same type of
battery as the original one, and do not replace it with other models.
The old battery should be handled by environmental manipulation.
The removed batteries should not be disposed at random or contact with other metal objects or batteries, in case causing
fire or explosion. The removed batteries should be disposed properly to protect the environment.
Do not charge or modify the battery. Do not short circuit the battery, and keep it away from fire and water
Do not short circuit batteries. Do not put the battery close to flame or water..
Do not overheat or solder the batteries. Do not subject the batteries to severe physical shocks.

FAN-4535EN(0821) ©2021 江森自控版权所有
Table of contents
Other Johnson Controls Measuring Instrument manuals

Johnson Controls
Johnson Controls EM-1000 Series User manual
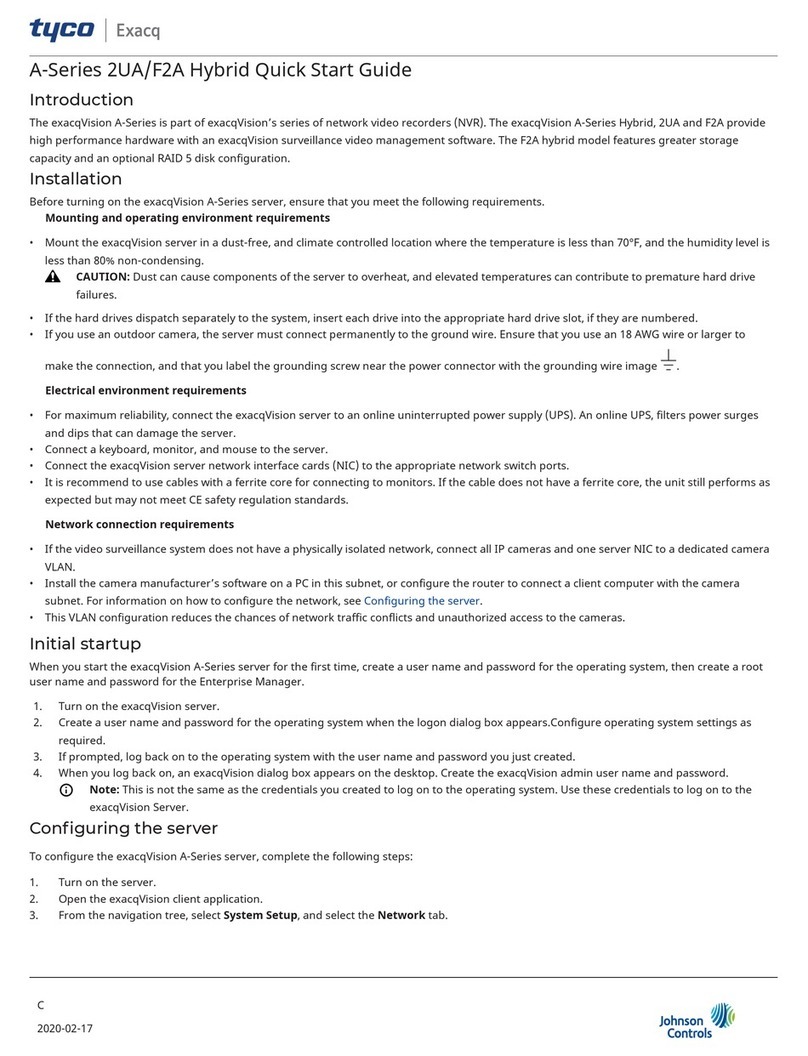
Johnson Controls
Johnson Controls Tyco exacqVision F2A User manual
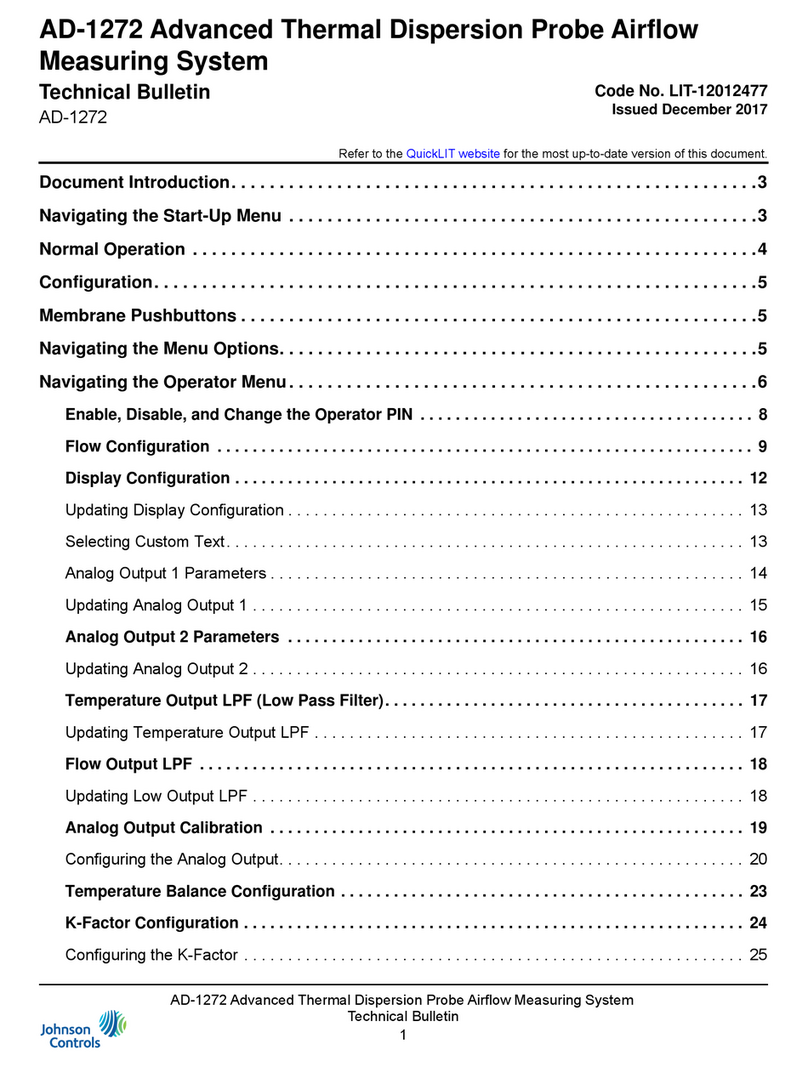
Johnson Controls
Johnson Controls AD-1272 Service manual
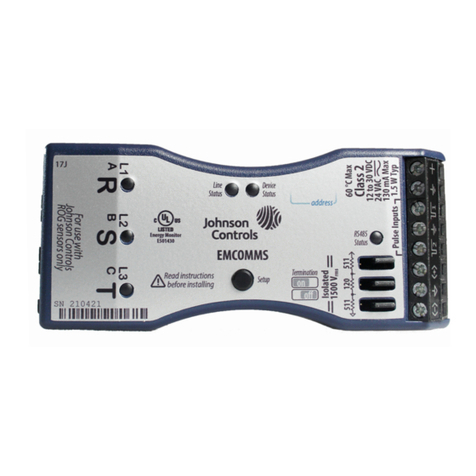
Johnson Controls
Johnson Controls EMCOMMS Series User manual

Johnson Controls
Johnson Controls PENN W43A14 User manual
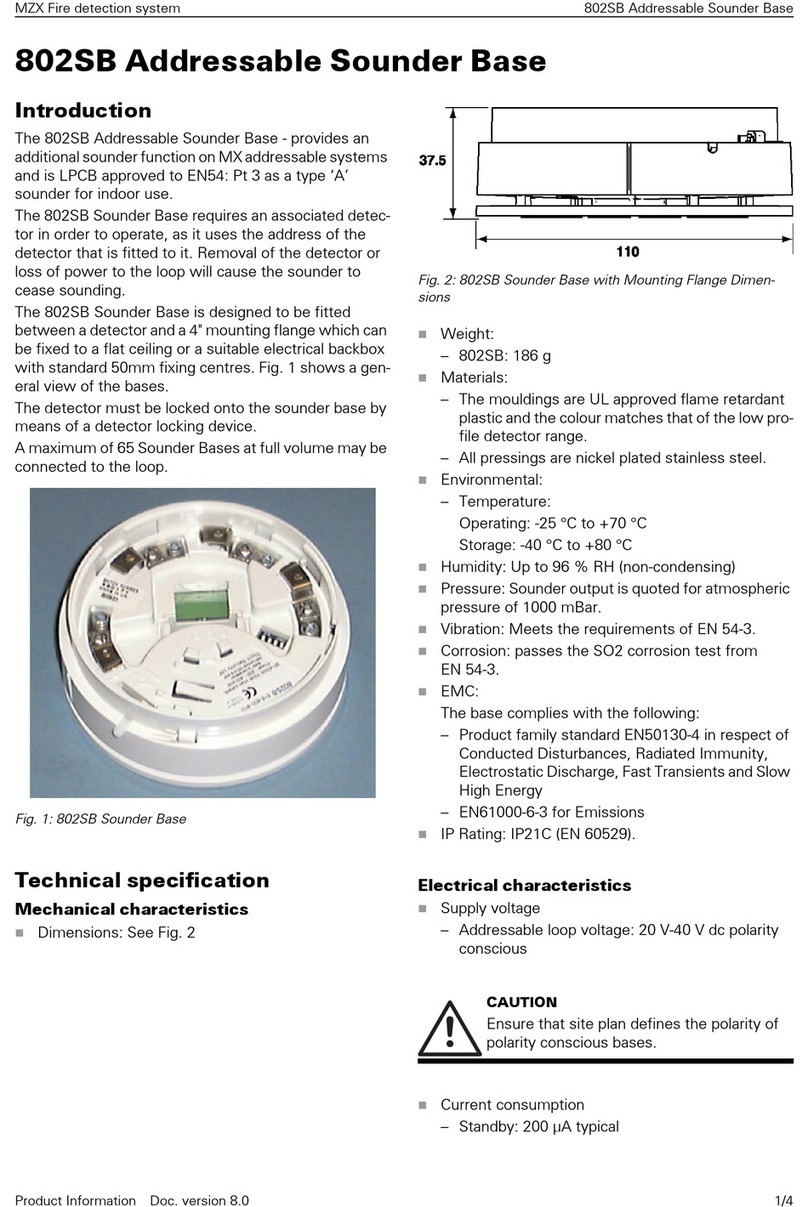
Johnson Controls
Johnson Controls 802SB User manual
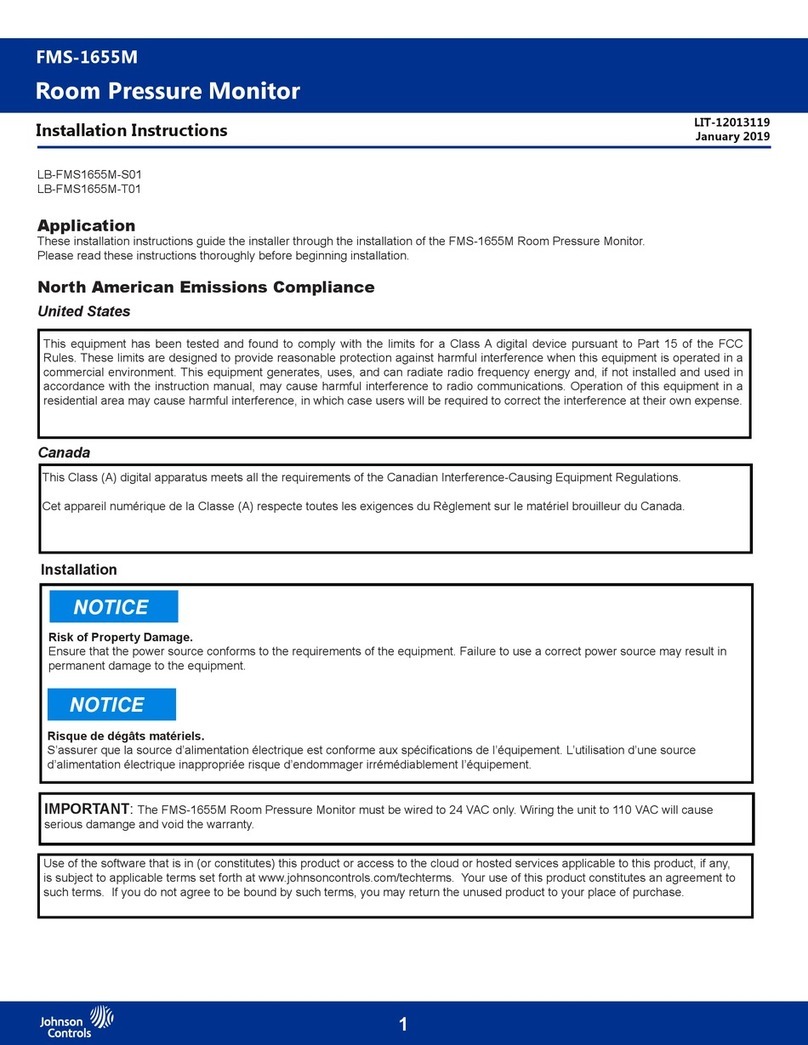
Johnson Controls
Johnson Controls FMS-1655M User manual
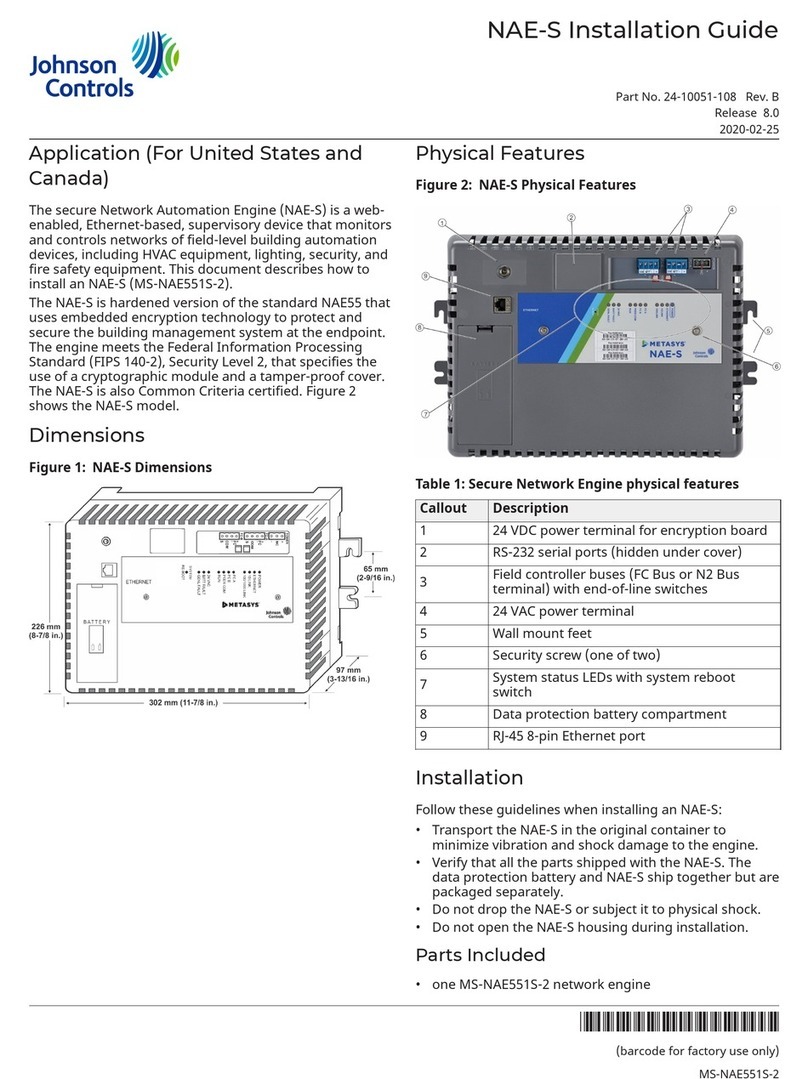
Johnson Controls
Johnson Controls NAE-S User manual
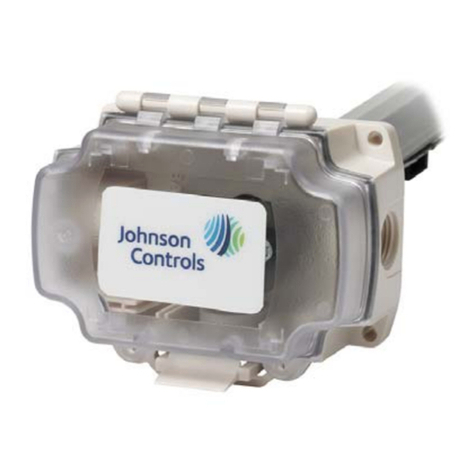
Johnson Controls
Johnson Controls AD-1252 User manual
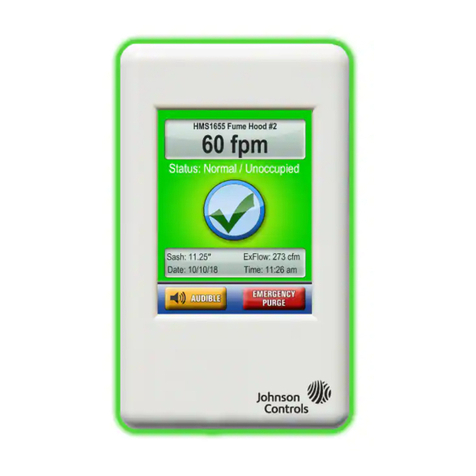
Johnson Controls
Johnson Controls CMS-1655 Assembly instructions