JP Fluid Control ST-SA Series User manual

JP FLUID CONTROL
MANUAL-ST-SA English www.jpfluidcontrol.com 1
ST-SA SERIES
SOLENOID VALVES
2/2-WAY
SEMI-DIRECT OPERATED
NORMALLY CLOSED
Solenoid Valve ST-SA-series
The ST-SA is a semi-direct operated 2/2-way solenoid
valve. The valve is normally closed. The valves have an
orifice of 10.5mm and can be used from a zero pressure
difference. The body material can be brass or stainless
steel with a NBR, EPDM or FKM seal. The ST-SA solenoid
valves are compatible with all coils from the CS1-series.
Example of product code
Dimensions
Series
Standard (ST)
Function
2/2 way
Operation
Semi-direct (S)
Position
Normally Closed (A)
Body Material
Brass (B) / SS 316 (S)
Seal &
Media Temperature
NBR (N)
-10..+80°C
EPDM (E)
-30..+130°C
FKM (F)
-10..+120°C
Thread
BSPP / NPT (N)
Ambient Temperature
Max +50°C
Min. Pressure Difference
0 bar
Max. Pressure
16/10 bar (AC/DC)
Coil series
CS1
Voltage
230V AC 50/60Hz (230AC)
24V AC 50/60Hz (024AC)
24V DC (024DC)
12V DC (012DC)
Insulation Class
Class F
Power
15 W
Duty Cycle
100% ED
Connector
EN 175301-803 (formerly DIN 43650A)
Protection Class
IP 65 (with cable plug)
Circuit Diagram
1
2
2
1
Pipe
Body
Orifice
Kv (m3/h)
1/4" (014)
Brass (B)
10.5 mm (105)
1.25
1/4" (014)
Stainless Steel (S)
8 mm (080)
1.02
3/8" (038)
Brass (B)
10.5 mm (105)
1.43
3/8" (038)
Stainless Steel (S)
8 mm (080)
1.02
1/2" (012)
Brass (B)
10.5 mm (105)
1.49
1/2" (012)
Stainless Steel (S)
8 mm (080)
1.02

JP FLUID CONTROL
MANUAL-ST-SA English www.jpfluidcontrol.com 2
ST-SA SERIES
SOLENOID VALVES
1. TECHNICAL SPECIFICATIONS
1.1. Principle of operation
A solenoid valve is a valve for neutral, clean liquids and gases, which is
electrically controlled with the aid of a solenoid. 2/2 way means that the
valve has two ports (input / output) and two positions (closed / open). The
valve is normally closed, this means that the valve is closed when de-
energized.
Semi-direct operated solenoid valves combine the properties of both direct
and indirect operated solenoid valves. The force that is required to open
and close the diaphragm is supplied by both the solenoid plunger as well as
the pressure of the medium. This allows them to work from zero bar
pressure differential. Furthermore, they can control a high flow rate with a
relatively small solenoid core. They can be used in only one flow direction.
This type of solenoid valves is used in systems that require a reasonable flow
rate, but the pressure difference between input and output is low or
unknown.
1.2. Area of application
Body material
The ST-SA series is available with a brass or stainless steel body material.
Body material
Allowed media
Brass (ASTM #37800)
Neutral and non-corrosive media.
Stainless Steel (S316)
Suitable for aggressive media and
corrosive media like seawater.
Diaphragm
The ST-SA series is available with several materials. In the following table a
concise overview is presented of compatible media.
Diaphragm
Temperature
Allowed
media
Not allowed
FKM
-10°C..120°C
Most fuels
and oils,
cold water,
detergents,
compresse
d air.
Glycol-based brake
fluids, ammonia gas,
hot water and steam,
low molecular weight
organic acids (such as
acetic acid.
EPDM
-30°C..130°C
Water and
steam,
alcohol.
Oils, fats, fuels,
solvents.
NBR
-10°C..80°C
Neutral
media, like
air, cold
water,
hydraulic
oil.
Fuels, strong acids,
brake fluid.
1.3. Flow chart
In the flow chart, the flow of water from 20°C is shown as a function of
the positive pressure difference across the valve. The flow rate is
expressed in liters per minute and the pressure in bar. The graph shows
different pipe diameters. The stainless steel valves (SS) of the ST-SA
series have a lower flow rate due to a smaller orifice.
1.4. Duty cycle
The solenoid valve is suitable for continuous use. High switching
frequencies and high pressures can reduce the lifespan.
1.5. Compliance
The coils are CE marked and comply with the LVD Directive (2006/95/EC)
and Directive (2004/108/EC), provided that the cables and connectors
are properly connected.
1.6. Type label
The properties of both the valve and the coil are displayed on a label on
the coil. In the figure below, an example is shown.
JP FLUID CONTROL
ST-SA012B105E
Normally Closed
Pipe: 1/2"
Seal: EPMD
Pressure: 0 –16 bar
Orifice: 10.5 mm
Coil: CS1-230AC
230V~50Hz IP-65
POSITION
PRODUCTCODE
PIPECONNECTION
SEAL MATERIAL
WORKING PRESSURE
ORIFICE
CE-MARK
PRODUCTCODECOIL
PROTECTION GRADE
VOLTAGE
COIL
VALVE
1.7. Exploded view
In the figure below is an exploded drawing of the ST-SA series is
displayed.
10
100
0.5 2.5 4.5 6.5 8.5 10.5 12.5 14.5
Water flow (l/min)
dp (bar)
1/4" 3/8" 1/2" SS

JP FLUID CONTROL
MANUAL-ST-SA English www.jpfluidcontrol.com 3
ST-SA SERIES
SOLENOID VALVES
#
Brass (B)
Stainless Steel
(S)
1
SS 302
SS 302
2
SS 302
SS 302
3
PA
PA
4
Epoxy
Epoxy
5
Top: 430F
Rest: SS 304
Top: 430F
Rest: SS 304
6
NBR/EPDM
/FKM
NBR/EPDM
/FKM
7
SS 302
SS 302
8
430F
430F
9
SS 302
SS 302
10
NBR/EPDM
/FKM
NBR/EPDM
/FKM
11
Brass #37800
SS 316
2. GENERAL SAFETY INSTRUCTIONS
►This product is not a safety device and may not be used as
such.
►The product may not function properly as a result of dirt,
wear, damage (for example, by dropping) or improper use.
Therefore, the product should not be used in applications
where a malfunction can cause danger or damage.
►Check the compatibility of the medium used, temperature
and other operating conditions with the materials and
specifications of the product. It is the responsibility of the
user to select the right product for the application.
►This product is not intended or approved for medical
applications, food and/or application in gas appliances.
►Solenoid valves can only be used with clean liquids or gases.
It is recommended to install a filter before the solenoid valve.
►Never exceed the limits for pressure, temperature or voltage
as indicated on the product and/or in the technical
documentation.
►The temperature of a solenoid valve coil can rise during
operation; this is normal. Overheating will cause smoke and a
burning smell. In this case, the power supply must
immediately be disconnected.
►A solenoid valve opens and closes quickly. Improper use can
cause pressure waves (fluid hammer) in the pipes with
possible damage as a consequence.
►Beware of electric shock when working with electrical
equipment.
3. INSTALLATION AND MAINTENANCE
1.1. Safety instructions before starting
►It is recommended to install the product in a dry
environment. In moist environments, make sure that no
moisture can penetrate the coil, actuator or connector.
Ensure that the solenoid valve is installed in an area with
adequate ventilation to facilitate heat dissipation. Make sure
the solenoid valve is not in contact with or in the vicinity of
flammable materials. Ensure that the product is protected
from frost. Frost may damage the product and/or block the
moving parts, causing the product to malfunction.
►Operations may only be performed when the system is not
pressurized, electrically disconnected and cooled down.
►Turn off the power supply before performing any work on the
solenoid valve to prevent the risk of electrical shock and to
prevent activation of the solenoid valve.
►The product is only safe when properly installed and operated
by qualified persons. Please read the safety instructions and
technical documentation carefully before installation, use or
servicing. Always observe applicable and generally accepted
safety
Measures.
►Ensure a safe startup after installation or maintenance.
►Water hammer is a typical consequence of a high flow rate
and pressure in pipes with small diameters. There are several
solutions to this problem:
►Reduce the pressure with a pressure reducing
valve before the solenoid valve.
►Increase the pipe diameter if possible.
►Dampen the water hammer by using a flexible
hose or buffer before the solenoid valve.
1.2. Installation
Clean fluids and gases
The solenoid valve can be used in combination with clean liquids or
gases. Make sure that the pipe may contain dirt before installing the
valve. It is recommended to install a filter (500 µm) before the solenoid
valve.
Mounting the valve
Be aware of the direction of flow of the medium when installing the
valve. Solenoid valves with an arrow on the housing must be connected
in the indicated direction. The pipes on both sides of the valve must be
securely fastened. Use a wrench for both valve and pipe while tightening,
to prevent unnecessary stresses in the system. The solenoid valve must
be fixed via the provided connection points. Only exert force at the
designated areas on the body such as the hexagon; never to the coil or
armature. Avoid vibration in the pipes. Use a suitable sealant for
threaded connections of the solenoid valve. Avoid the entry of sealing
material in the valve, this can lead to malfunctioning of the valve.
Position
It is recommended to install the solenoid in vertical position with the coil
facing upwards. This reduces the probability of the collection of debris in
the solenoid valve. When the solenoid valve is mounted at an angle, it is
recommended to deviate maximally 90° from the vertical position.

JP FLUID CONTROL
MANUAL-ST-SA English www.jpfluidcontrol.com 4
ST-SA SERIES
SOLENOID VALVES
Maximum angle 90°.
IN
OUT
Check the flow direction with the help of the indications on the
valve body.
Only exert force at the designated faces, never at the coil or
armature.
Installation of the coil
►Make sure the coil is labeled with the valve characteristics.The
device can be damaged by the use of unsuitable tools.
►The temperature of the coil increases during use, this is normal.
Overheating will cause smoke and a burning smell. In this case, the
power supply must be shut down immediately.
►The coils can be rotated if the coil nut is loosened. After the
determination of the correct position, the nut should be fastened
with a torque of 5Nm.
Installation of the cable plug
►Always connect the earth (3), which is provided with a ground
fault at voltages above 50V. Never use liquid or gas for
grounding electrical equipment. The power supply is
connected to terminals (1) and (2). The polarity does not
matter.
►Verify the voltage and frequency before connecting the coil.
►When mounting the connector, make sure that no moisture
can ingress between the coil and connector. The connector
screws should be fastened with a torque of 0.5Nm.
12
31
2
3
Connector: EN 175301-803 (formerly DIN 43650A).
The poles (1) and (2) should be connected to the power supply , polarity
is not important. Pole (3) is the earth. Connect the connector
thoroughly to avoid ingress of moisture. Ensure that drops in cannot
slip along the cable and enter the connector.
Connecting the power supply
►Never connect power to the coil when it is not not attached
to the solenoid valve! The coil may burn out.
►Only connect power if you are sure that there is no pressure
in the system and no hazardous situations can occur.

JP FLUID CONTROL
MANUAL-ST-SA English www.jpfluidcontrol.com 5
ST-SA SERIES
SOLENOID VALVES
4. SPARE PARTS
The coil can be replaced. The product codes of the coil are shown in the
table below.
Product Code
Voltage
CS1-230AC
230V AC 50Hz
CS1-024AC
24VAC 50Hz
CS1-024DC
24V DC
CS1-012DC
12V DC
The diaphragm, springs and plunger of the solenoid valve can be
replaced. The product codes of the diaphragms are shown in the table
below:
Product Code
Housing
Seal
ST-SA-N-REV
Brass
NBR
ST-SA-E-REV
Brass
EPDM
ST-SA-F-REV
Brass
FKM
ST-SA-SN-REV
Stainless Steel
NBR
ST-SA-SE-REV
Stainless Steel
EPDM
ST-SA-SF-REV
Stainless Steel
FKM
Follow the drawing in 1.7 for the correct assembly of the solenoid valve.
5. DISPOSAL
The removal of the product should be performed in accordance with the
applicable laws. Keep in mind the media that are still present in the valve.
This manual can be downloaded from www.jpfluidcontrol.com Modifications reserved © JP Fluid Control
This document has been prepared with great care. JP Fluid control assumes no responsibility for any errors that may appear in this document. No rights can be derived from this document.
This manual suits for next models
14
Table of contents
Other JP Fluid Control Control Unit manuals
Popular Control Unit manuals by other brands
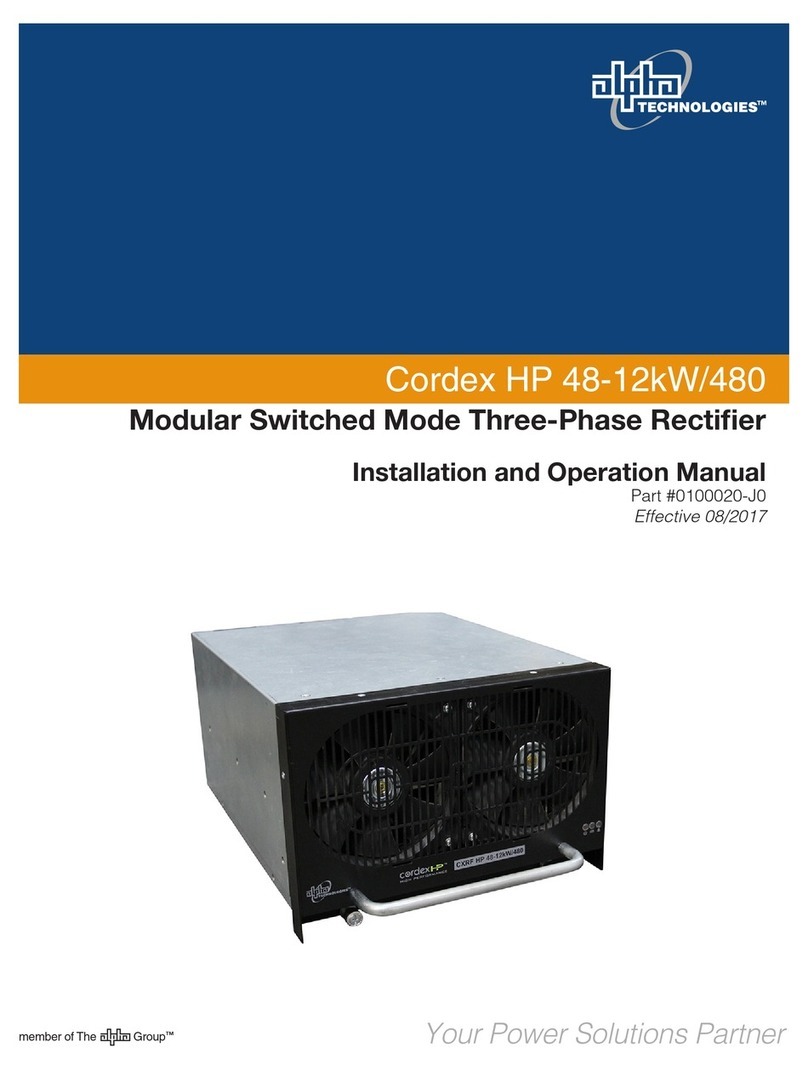
Alpha Technologies
Alpha Technologies Cordex HP Installation and operation manual
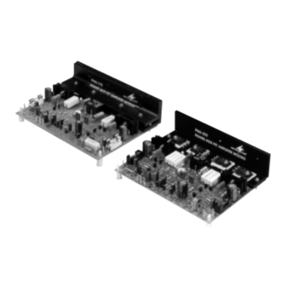
Monacor
Monacor PMA-102 Mounting instructions
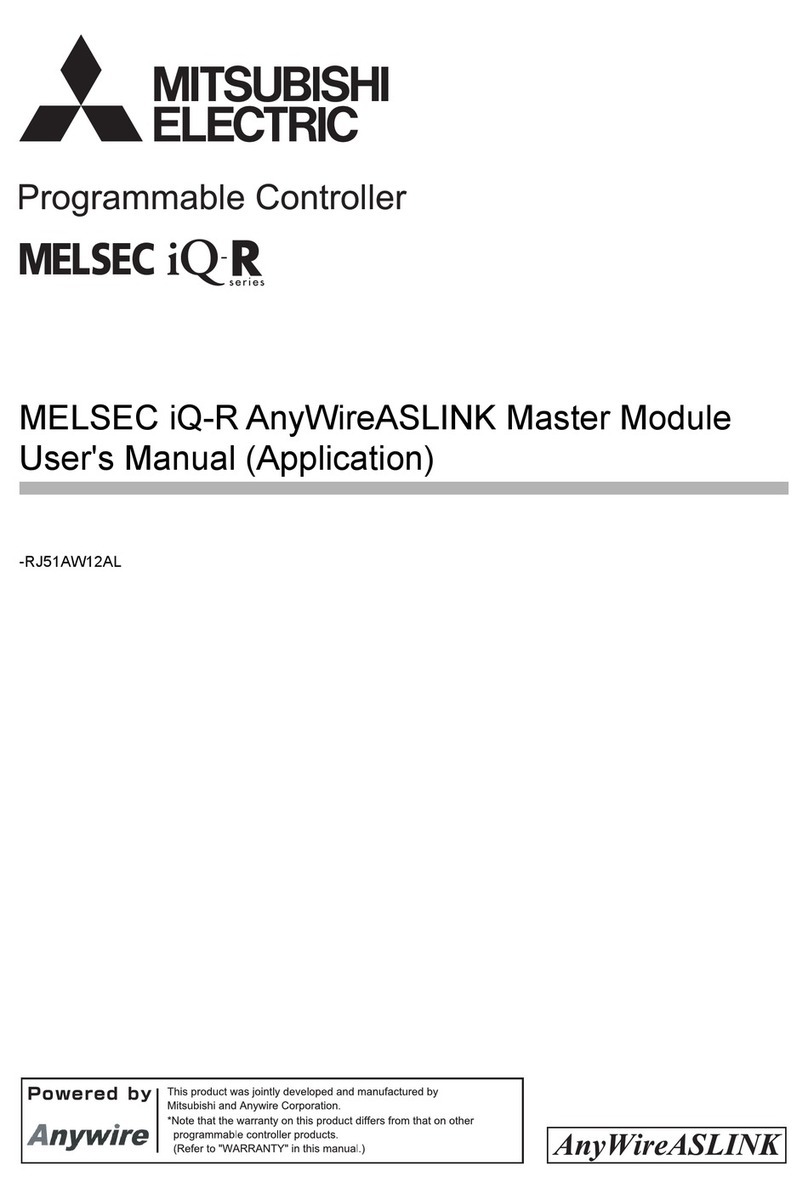
Mitsubishi Electric
Mitsubishi Electric MELSEC iQ-R AnyWireASLINK user manual
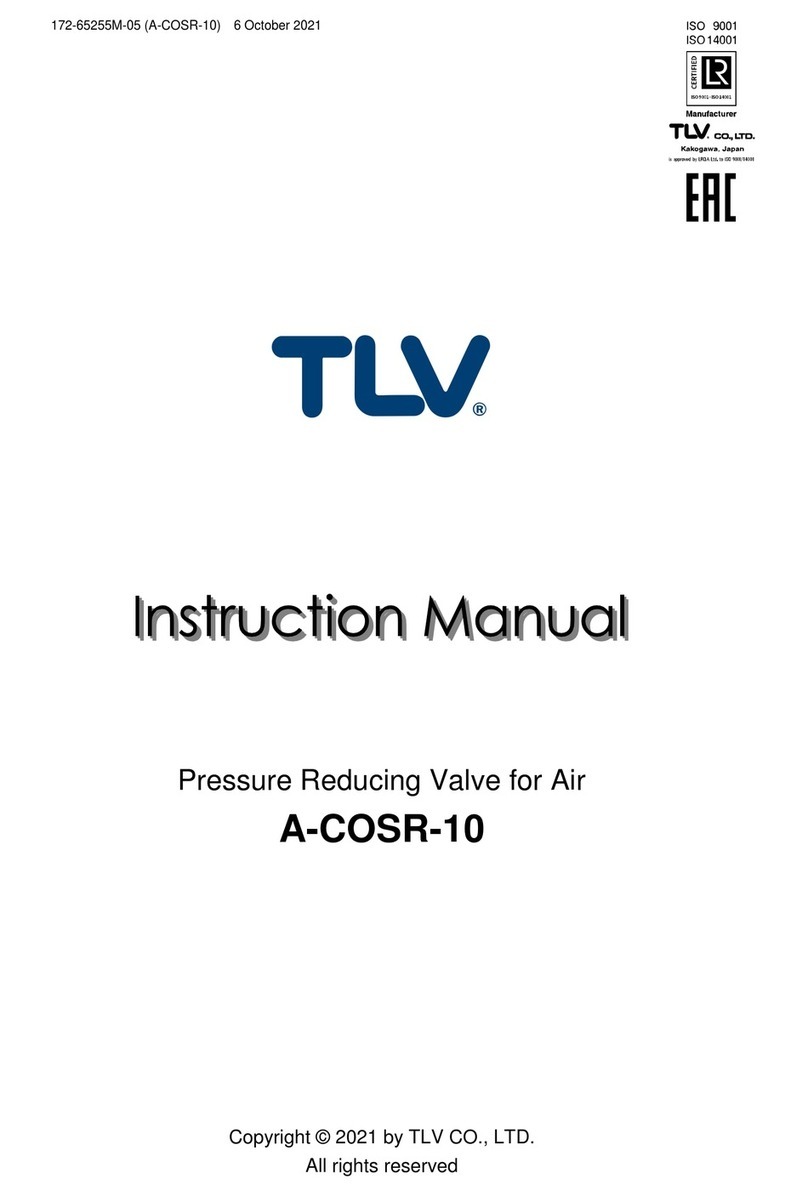
TLV
TLV A-COSR-10 instruction manual

Emerson
Emerson White-Rodgers 36C01 installation instructions
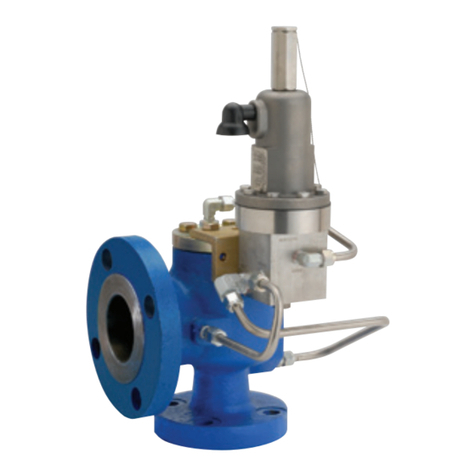
Emerson
Emerson Anderson Greenwood Type 443 Installation and maintenance instructions