JUKI PS-800 User manual

PS-800 Panel operation
INSTRUCTION MANUAL

Contents
CHAPTER I INTRODUCTION TO CONTROL SYSTEM .........................................................................1
1.1 OVERVIEW ......................................................................................................................................................... 1
1.2 FUNCTIONAL DESCRIPTION................................................................................................................................ 1
1.3 NOTES................................................................................................................................................................ 2
1.3.1 Safety Instruction....................................................................................................................................... 2
1.3.2 Work Environment..................................................................................................................................... 3
1.3.3 Power Supply Requirement ....................................................................................................................... 3
1.3.4 Grounding Requirement ............................................................................................................................ 3
CHAPTER II DESCRIPTION OF MAIN INTERFACE .............................................................................5
2.1 SYSTEM POWER-UP............................................................................................................................................ 5
2.2 MAIN INTERFACE OF PROCESSING ..................................................................................................................... 5
2.2.1 Display Instruction for Main Interface of Processing................................................................................. 5
2.2.2 Test Interface Display Description.............................................................................................................. 8
2.2.3 Display Instruction for Manual Frame Movement Interface ................................................................... 10
2.2.4 Display Instruction for Reference Setup Interface................................................................................... 12
2.2.5 Process Statistics Interface Display Instruction ....................................................................................... 14
2.3 MAIN MENU INTERFACE .................................................................................................................................. 15
CHAPTER III FILE MANAGEMENT ................................................................................................17
3.1 MEMORY FILE MANAGEMENT ......................................................................................................................... 17
3.2 MANAGEMENT OF FILES IN USB FLASH DISK ................................................................................................. 18
CHAPTER IV FILE EDITING ...........................................................................................................20
4.1 MAIN INTERFACE OF FILE EDITING.................................................................................................................. 20
4.2 CAPTURING GRAPHS........................................................................................................................................ 20
4.3 IDLE CAPTURE ................................................................................................................................................. 23
4.4 SINGLE NEEDLE ACQUISITION .......................................................................................................................... 24
4.5 STRAIGHT LINE CAPTURE ................................................................................................................................ 24
4.6 RECTANGLE CAPTURE ..................................................................................................................................... 25
4.7 POLYLINE SEGMENT CAPTURE......................................................................................................................... 25
4.8 ARC CAPTURE.................................................................................................................................................. 26
4.9 CIRCLE CAPTURE............................................................................................................................................. 27
4.10 CURVE CAPTURE............................................................................................................................................ 28
4.11 MULTIPLE CURVES ......................................................................................................................................... 28
4.12 REINFORCEMENT PRESET .............................................................................................................................. 30
4.13 FUNCTION CODE ............................................................................................................................................ 32
4.14 GRAPH EDITING ............................................................................................................................................. 35
CHAPTER V PARAMETER FILE......................................................................................................45
CHAPTER VI USER PARAMETERS .................................................................................................47

6.1 USER PARAMETERS INTERFACE ....................................................................................................................... 47
6.2 INTRODUCTION TO USER SETTING PARAMETERS ............................................................................................ 49
CHAPTER VII MACHINE PARAM ..................................................................................................61
7.1 MACHINE PARAM INTERFACE .......................................................................................................................... 61
7.2 INTRODUCTION TO SETTING UP MECHANICAL PARAMETERS......................................................................................... 63
CHAPTER VIII ASSIST SETTING.....................................................................................................72
8.1 ASSIST SETTING INTERFACE ............................................................................................................................ 72
8.2 INPUT TEST ...................................................................................................................................................... 73
8.3 OUTPUT TEST................................................................................................................................................... 73
8.4 NETWORK SETTINGS........................................................................................................................................ 75
8.5 DATE SETTINGS................................................................................................................................................ 76
8.6 LOCK SETTINGS ............................................................................................................................................... 77
8.7 SYSTEM LANGUAGE ........................................................................................................................................ 78
8.8 SYSTEM UPGRADE ........................................................................................................................................... 79
8.9 DRIVER PREVIEW............................................................................................................................................. 81
8.10 TEST TRANSFER ............................................................................................................................................. 81
CHAPTER IX MACHINE STATE ......................................................................................................83
APPENDIX I: INFORMATION PROMPT AND SOLUTIONS ...............................................................84
APPENDIX II: QUICK START GUIDE ..............................................................................................89

1
Chapter I Introduction to Control System
1.1 Overview
Thank you very much for using the automatic template sewing machine control system of our
company!
This system can match with the various types of template machine, satisfying different sewing
requirements with satisfactory sewing effect for all sorts of cloth!
Before using, please read the Instruction carefully to ensure the correct use of this system. Please
keep the instruction appropriately in order to check at any time.
In case of discrepancies between actual machine and this Instruction due to different machine
configurations and software update, the operating functions shall prevail.
1.2 Functional Description
(1) One machine with multi-purpose, simple operation
Full automatic template sewing machine can replace many kinds of special machinery such as
traditional flat sewing machine, long arm sewing machine, bartack sewing machine, embroidery
machine, etc. in certain circumstances to achieve multi-usage
After placing the template well, the operating personnel only needs to press the start key, automatic
processing can be completed, the operation is quite simple
With standardized operation; the machine can work out amazing effects for a variety of stitches
and a variety of fabric!
(2) The man-machine interface is friendly and easy to use
7 inches color LCD touch screen, with clear display, easy to touch
Support display in Chinese,Vietnamese,Korean,Japanese and English
Up to 256M (or 128M) file storage space, to store and process many files
Convenient file Collection (template making), modification, management functions
(3) Precise motion control technology with efficient sewing
Using international advanced DSP chip, fast system run speed, high hardware integration, stable
performance

2
Support step-by-step, closed loop step-by-step, brushless DC, servo drive, using smooth curve for
speed governing, smooth operation
Compact mechanical structure, good rigidity, high sewing position precision, low noise
(4) The upper computer graphics editing software is easy to use
Such files in dxf, dst, dsb, ai, plt, edi, tzf format that are generated by software such as Autocad,
Coredraw are easily converted into processing files
The software has comprehensive graphics editing functions, supports layer editing and adding
various kinds of special sewing stitch lines
With common control instruction set, customizable control instruction (functional code), high
dexterity of action
For each layer, each graphic, each stitch point, a variety of mechanical control commands can be
inserted into, to meet the diversified and precise automatic sewing requirement
(5) Rich user parameter settings, comprehensive auxiliary functions
Detail settings can be carried out for various mechanical actions
Point position, painting line, automatic mold slot opening function of some equipment can be
extended
Support automatic identification of template, U Disk system updates, broken threads detection,
continue sewing in power down, processing statistics, forecast for lack of bobbin thread, system
self-test, parameter backup and recovery, encryption lock machine...
1.3 Notes
1.3.1 Safety Instruction
In order to avoid the possible risk and prevent damage to the device, please observe the following
safety matters:
Note:
Please don't carry out maintenance and debugging to electric system by non-specialists, this
will reduce the safety performance of equipment, enlarge the fault, and even cause harm to
the personnel and property losses.

3
Some parts inside the case have high pressure; after the system is powered on, please do not
open the case cover, in order to avoid accidental injury.
Please do not pile up sundry around the control box, and in the process of using; remove dust
on the surface of control box and the filter regularly, so as to keep good ventilation for the
system, which is good for heat dissipation.
Without authorization of the company, please do not make any change to the product
arbitrarily, and the company shall not hold any responsibility for the consequences!
Warning:
If it really needs to open the case cover, it must be carried out5 minutes after cutting
off power and guided by professionals to contact components inside the electrical cabinet!
Danger:
When the machine is at work, it is forbidden to contact with any moving part or open
the control equipment, plug or pull out motor interface, otherwise it may cause personal
injury or the machine not to work!
It is forbidden for electrical equipment to work in places with humidity, dust,
corrosive gas, flammable and explosive gas, otherwise it may cause electric shock or fire!
1.3.2 Work Environment
Solid, level ground installation
Good ventilation, healthy environment, less dust
Temperature in work space: 5 to 40 ℃
Relative humidity in work space: 30% to 90% without condensation
1.3.3 Power Supply Requirement
Single-phase AC220V/50 to 60 HZ
It needs to be equipped with the voltage regulation equipment when the power grid voltage
fluctuation is more than 10%
Equipment power is between 1.0 to 2.0KW according to different machine configuration
1.3.4 Grounding Requirement
In order to prevent electric shock or fire accident of electrical equipment due to causes such

4
as electric leakage, over voltage, insulation, etc., please make sure the electronic control with
reliable grounding
The grounding resistance should be less than 100 ohms, conductor length within 20 meters,
conductor cross-sectional area greater than 1.0 square millimeters

5
Chapter II Description of Main Interface
2.1 System Power-up
Upon system power-up, the HMI displays the boot screen, when the spindle will automatically
rotate for testing and reset other parts. The reset action is related to power-up reset parameters setup.
2.2 Main Interface of Processing
2.2.1 Display Instruction for Main Interface of Processing
The main interface of processing is automatically activated after the display of boot logo. The
main interface of processing is shown below:
Fig. 2-1 Main interface of processing
Key functions in the main interface of processing are described as follows:
Processing file preview area: Show the currently selected file graph; click to switch between “full
graph” (scale for optimal display) and “at ratio” (actual ratio to the processing range). When the
processing graph is greater than 8,000 stitches, only “full graph” display mode is available.
List of memory files: Show the list of memory files; click to choose different processing files.
:lock file" key: Lock the currently processed file to prevent misoperation. Once a file is
Prompt message area
Whether current time
is in sync with the
network
Total stitch count of
processing file and the
current processing
stitch count
Touch key
USB flash disk
Indicator lamp
Processed quantity
Current
processing file
name and the
length & width
Length of bottom
thread used
Lock file icon
Working speed of
spindle
Processing file
preview area
List of memory files

6
locked up, other processing files can't be chosen, when icon will appear in the preview area.
Click once to lock, and click again to unlock.
Note: Automatic template recognition will work only in the locked state of "lock file". The
recognized template is displayed in the "prompt message area", and the corresponding numbered file
will be automatically selected. If the "template recognition mode" is set to "by file name", electronic
tag (identifier) will be used to match the file name; if it is set to "by serial number of file", the serial
number of file will be matched using a code scanner.
:The needle-threading function. After entering the threading state, the pressing foot is
automatically lowered and the starting operation is automatically locked to prevent accidental
start-up.
: "Acceleration" key. The rotating speed of spindle increases by 100 rpm. If this key is
pressed and held (long-pressed), the speed will increase continuously until the set max speed is
reached. Arbitrary change to rotating speed can be prohibited by setting a password.
: "Deceleration" key. The rotating speed of spindle decreases by 100 rpm. If this key is
pressed and held, the rotating speed will decrease continuously until the set min. speed is reached.
Arbitrary change to rotating speed can be prohibited by setting a password.
: Display the current spindle speed. Click to pop up the “File Speed” setting interface to
set the independent speed of the current file. If set to 0, it means no independent processing speed.
: "Bottom thread statistics" key. Show the used length of bottom thread. Press the key to
enter the processing statistics interface.
: "Processing statistics" key. Show the finished quantity. Press the key to enter the
processing statistics interface.
: "Main menu" key, Press the key to get into main menu interface.
: "Try" key, It is used to simulate the processing process based on graphical trajectory.
When this key is depressed, XY axes rotate while the spindle is stationary.
: "Segment fast reverse" key, Manually move back without load to the starting point of

7
the previous continuous curve. Return without load means the spindle remains stationary while
XY axes move. This key is used to preview the designated needle location or start the processing
from the designated needle location.
:"Segment fast forward" key,Manually move forward to the starting point of next
continuous curve, when the spindle remains stationary.
:"Single needle return without load" key: Press the key, and one stitch will retract at single
step without load; continuous backward movement is activated when this key is pressed and held.
:"Single needle forward without load" key: Press the key, and one stitch will go forward
at single step without load; continuous forward movement is activated when this key is pressed
and held.
:"Total stitch count setup” key: The number in the upper line indicates the stitch count of
processing file, while the number in the lower line indicates the current stitch count. Press the key,
when the “Jump stitch” setup window pops up.
Note: “Jump Stitch” window description: …: Number input for set value; : The set
value returns to 0; : The set value plus 1; : The set value minus 1; : Delete a
digit from right to left : Cancel current modification; : Confirm current
modification;
: Connection with wireless network has been established; : Connection with cloud
server has been established
:"Page left" key, Turn the page to the left to view memory files.
:"Page right" key, Turn the page to the right to view memory files.
:"File" key, View all memory files.
:"Reset" key, Press the key, when the shafts start to rotate, while the machine is reset.
:"Reference" key, Press the key to get into XY axes reference point setup page.

8
:"Manual press frame up/down" key, Press the key to switch between lifting and pressing
of press frame.
:"Manual press foot up/down" key, Press the key to switch between lifting and pressing
of press foot.
:"Press foot thread clamp” setup key, Set press foot height or thread clamp strength. Note:
This function is not available unless the press foot type is set to motorized press foot in parameter
software.
:"Next interface” key, Press the key to get into test interface.
2.2.2 Test Interface Display Description
Bottom thread winding and other manual operations can be performed in the processing assist
interface.
Key functions in the assist interface are described as follows:
: Auto hook change. If the machine is designed with “auto hook change” feature, signal
will be output for rotating hook change when the key is depressed.
:"Bottom thread winding on/off" key: Press the key to switch between “allow” and
“prohibit”. Activate “Allow” and press the "Start" switch to start the winding operation, when the
spindle will wind the thread at the speed set in this page. The winding will stop if the start switch or
is depressed again or the set winding time elapses. “Prohibit” means thread winding is

9
prohibited.
: Show current rotational speed of spindle.
: Show current angle of spindle (0-999).
: Set the winding speed of spindle.
: “Spindle REV” key: Press the key, when the spindle starts to reverse and move slowly.
: “Spindle FWD” key: Press the key, when the spindle starts to rotate forward slowly.
: “Needle rod up/down” key: Press the key to switch between upper position (the highest point
of needle) and lower position (the lowest point of need).
: “Trim” key: Press the key, when the machine sews one stitch to realize a complete trim
operation.
, , , , : Press the key, when the corresponding output is
turned on; lift the key, when the output is turned off.
, … : Press the key, when the corresponding IO output function is always
ON; press again to turn off the output. For some electric control, the LED lamp will be always ON.
Note: Please don't press and hold the electromagnet control output for long (e.g.
); otherwise, the electromagnet connected with this output may get damaged due to overheating!
: Zoom, increase, decrease, and set the stitch length for each line segment of the current
drawing. The interface is as follows:

10
:To reduce or enlarge the current graphics as a whole, the width and length are the
actual width and length of the reduced or enlarged graphics.
: For the beginning or end of each line segment of the current figure, the change
depends on the stitch length of needles increases or decreases.It meanis to increase if the value is
greater than 0, and vice versa.
: Modify the length of the stitching needle of the current figure. Reserved
Commands means that retain some functional code instructions inserted by users after modifying the
length of needle spacing
: Press the key to get into the suspension position interface that is used to set the
positions (up to 6) of suspension during sewing operation.
: “Previous interface” key,Press the key to go back to the main interface of processing.
: “Manual frame movement” key,Press the key to get into the manual frame movement
operation interface.
Thread winding: Press touch key “Start” at the bottom of the screen in this interface, and
confirm, when the spindle motor will rotate for thread winding at the set speed, while key
appears at original position of ; click this key to stop winding operation. The winding
operation can also be stopped by pressing “Start” and “Emergency stop” buttons. The speed can be
regulated through during winding operation.
2.2.3 Display Instruction for Manual Frame Movement Interface
Click on and successively in the main interface of processing to get into the
manual frame movement interface. In the manual frame movement interface, it’s possible to move
the frame manually and control the rotation of each shaft.

11
Key functions in the manual frame movement interface are described as follows:
, , : “Frame movement speed switching” key,Click to switch among low,
medium and high speeds. Correspond to patterning speeds 1, 2 and 3 in “user parameters”.
: 8 direction keys,Move in X and Y directions.
“Z+”, “Z-”, “shaft 1+”, ... “shaft 3-”: Rotate corresponding shafts manually; some of the shafts
have no effect on certain machines.
:The default is “No”
, indicating that the manual frame-shift operation cannot be performed
before resetting. You can select “Yes ”to perform a temporary manual frame-shift operation before
reset. If it has been reset, this function is invalid.
: The current X and Y coordinates are set to the stop coordinates of X and Y axes after
resetting.
: Enter the head offset interface for setting the offset position of heads 2 and 3 in relation
to head 1. Head 1 is a sewing head. Desired functions such as laser cutting head and brush head can
be assigned to heads 2 and 3.
Display of the angular
position of spindle
Shafts 1, 2 and 3
coordinates display
X/Y/Z coordinates
display
Key depression
speed switchover; 3
speeds are available
Direction key: The
frame can be moved
in 8 directions

12
Click , when the coordinates of head 1 become the coordinates employed in
. Set the values of heads 2 and 3 in relation to head 1 below, and
will change correspondingly; click OK to save the settings.
: “Needle rod up/down” key,Press the key to switch between upper position (the highest
point of needle) and lower position (the lowest point of need).
:"Return" key,Press the key to return to the previous operation interface.
2.2.4 Display Instruction for Reference Setup Interface
Click in the main interface of processing to get into the reference point setup interface.
The template reference point can be set in this interface.
: Lifting function is mainly used for "rotary head" type machine, outputting IO
corresponding to the set parameters (P249). High and low level switch each other.
: As mentioned earlier (all foot pressing functions on the interface are the same)

13
Reason for reference point setup:When the processing file generated through the software in upper
computer is imported into the memory and previewed for the first time, the system puts the file at the
center of the processing range (click the “Processing file preview area” to switch the display mode),
and writes this position information into processing file. As shown in the figure below:
The fabricated template is placed on workbench in the position that may be as shown in the figure
below:
Hence, it's necessary to align reference point 1 with A, and reference point 2 with B. Adjust the
position of processing pattern in the system so that it corresponds to the template slotting position.
Detailed steps are as follows:
1) Select the file for which the reference point should be set up in the main interface of
processing, and place the corresponding template. Click to enter the reference point
setup interface, and the system will automatically move the frame to reference point 1.
If dual reference points are set up in upper computer software, the upper left corner of the
interface will indicate "set up reference point 1". See whether the reference point 1 is located
at template slot A; in the case of offset, click the arrow keys to move the point until they
coincide with each other.
2) Click to finish the setup of reference point 1. The system automatically moves frame

14
to reference point 2, when the upper left corner of interface indicates "set up the second
reference point". Click direction keys to move the frame so that reference point 2 coincides
with the position of template B. To return to re-set reference point 1, click key to
switch to reference point 1 for setup.
3) Click to finish the setup of reference point 2, when the system automatically returns
to the main interface of processing. The system will write this position into processing file,
while the processing preview area pattern will be adjusted to correspond to the position of
template. Upon the completion of reference point alignment, additional alignment is not
needed as long as you don't modify this file and template. If the upper computer does not set
up dual reference points, the sewing start point will be taken as reference point 1 by default,
in which case the system will return to main interface of processing after the alignment of
reference 1. By setting up system parameters, it is possible that reference alignment is not
needed at the first use. Please consult the manufacturer for detailed settings.
2.2.5 Process Statistics Interface Display Instruction
Click or in the main interface of processing to enter the processing
statistics interface. In this interface, you can view the processing quantity, time, bottom thread length
and other information.
The interface is described as follows:
Total number of files completed by history: The number on the left represents the total
number of processing times accumulated; The number on the right represents the total number of
processing times in 7 days of the current figure. Click "Clear" to clear the total number of both
processing times and 7 days of the current graphics.

15
Total number of files completed by today: The number on the left indicates the total
number of processing times accumulated on that day. The number on the right indicate the cumulative
number of processing times on the day of the current figure. Click "Clear" to clear the total number of
processing times of the current graphics and the number of file processing times.
Use length of bobbin thread(mm): Refers to the length of the baseline that has been used up. After
setting it to the,it will accumulate baseline length of the current file when processing begins.
Total length of bobbin thread(mm): Refers to the total length of the initial bottom line in the
spindle. When winding, it can be estimated that the total length is equal to the average circumference
of the spindle multiplied by the speed multiplied by the winding time
Current value of Counter: Refers to the total number of processed documents. Each time the
processing is completed, it will automatically add 1, which cannot be closed.
Total number of Counter: Refers to the target number of times a processing document has been
completed.
Working time: Show the total processing time. Just count "working..." state time.
Today's work time: Show the processing time of the day. Click Clear to clear 0.
Work time yesterday: It shows the processing time yesterday. Click Clear to clear 0.
: Refers to the error margin of the remaining length of the baseline. (Baseline length
detection device for special purpose).
: The blue character in the lower left corner indicates the last processing time.
: The white words in the lower left corner indicate the total time of starting this time.
2.3 Main Menu Interface
Press key in main interface of processing to enter the main menu interface, as shown in
the figure:

16
File management: Manage, import and export the files in memory and USB flash disk.
File edition: Create new sewing graphs or edit & modify original graphs.
Parameter file: Write parameters into the system, and export system parameters in the form of
file; the transfer of files between memory and USB flash disk, etc.
User parameters: The parameters frequently used by user; parameters are adjusted based on
processing requirements to realize convenient processing and improve processing efficiency.
Machine parameters: Only accessible to machine assemblers.
Assist settings: Used for processing assist settings and testing, etc.
Network file: (Temporarily unavailable)
Machine state: For remote administration device to report various status of machine for solutions.

17
Chapter III File Management
File management is performed to import, export and delete files in USB flash disk and memory.
The system only recognizes the processing files with extensions .SLW. Processing files are created
with PC graph edition software delivered with machine or through file capture.
3.1 Memory File Management
Press key in main menu interface to enter file management interface as shown in the
figure below:
The system memory can store up to 999 processing files, of which the total size shall not exceed
128M. Support file names in Chinese and English (case sensitive); each file name can consist of up to
15 Chinese characters or 30 characters (the displayed number of characters may vary depending on the
interface). In the case of wrong format of processing file or file corruption, no preview is displayed
here.
Click to select a file, when the selected file turns red; the selected file shall be handled as needed.
Key description:
: Copying file, Copy the currently selected file. File copy can be created by clicking
“Copy” and entering the new file name.
: Deleting selected file, Delete the currently selected one or more files.
: Sorting file, Insert the currently selected one or more files into designated location. For
example, select “002:TEST2”, click , enter “1” into the pop-up dialog box, and click "OK". The
file ranks first and turns into “001:TEST2”.
: “Electronic tag and barcode write” key, The function is determined by “User parameters” -
“Other settings” - “Template recognition mode: By file name/file number”.
Other manuals for PS-800
1
Table of contents
Popular Control Panel manuals by other brands

Bentel Security
Bentel Security Omnia user manual
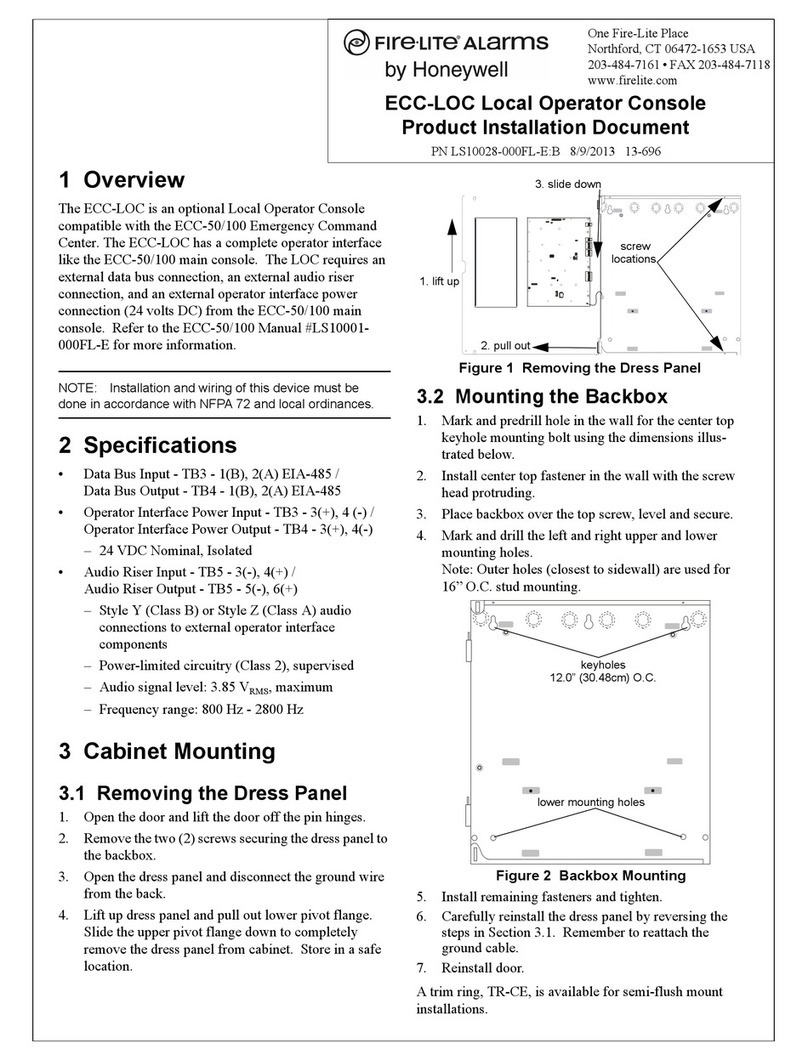
Honeywell
Honeywell Fire-lite ECC-LOC Product Installation

SILENT KNIGHT
SILENT KNIGHT 5207 Installation, programming, and operation manual
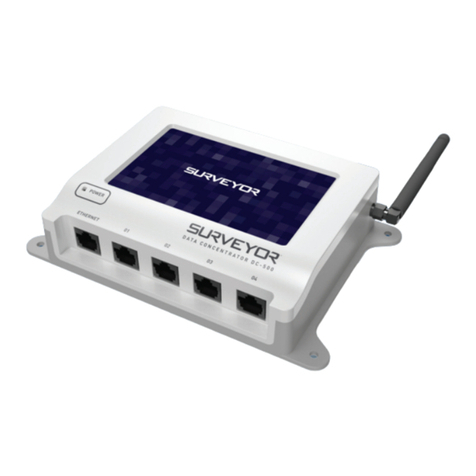
Venstar
Venstar SURVEYOR DC500 installation instructions
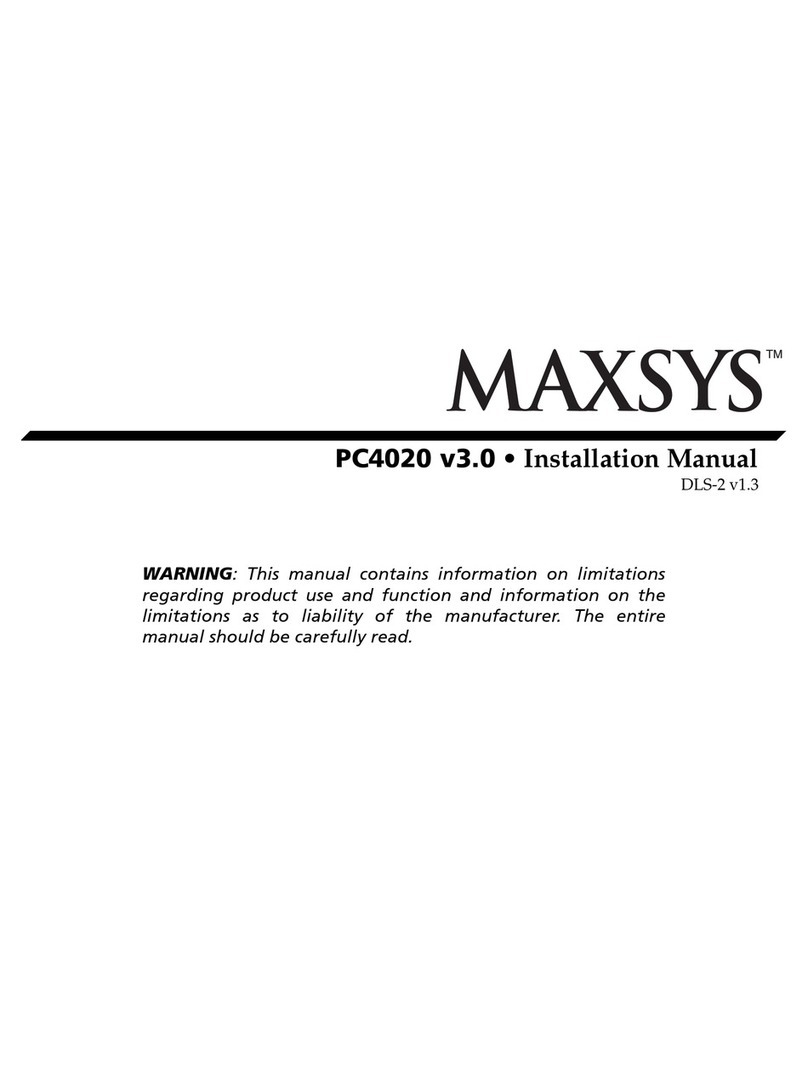
Maxsys
Maxsys PC4020 installation manual

Eaton
Eaton DALI installation guide