Kee WALK Step Over Manual

KEE WALK Step Over Operation & Maintenance Manual
SAFETY AT THE HIGHEST LEVEL

CONTENTS PAGE
System Overview 1
Checking the Step Over System’s Components 3
Platforms for the Major Roof Types 6
Assembling the Step Over 8
Finished Step Over 13
Kee Walk Mini Step Over 14
Assembling and xing the Mini Step Over - Fixed Version 15
Assembling and xing the Mini Step Over - Free standingg 16
Kee Walk Step Over System Recertication 17
Contents

System Overview
1
Step Over
KEE WALK®Step Over is a complete range of safety Step
Overs designed specically to provide permanent safe access
for areas on roofs or in warehouses where regular access for
maintenance and inspection is required.
A KEE WALK®Step Over system is designed to provide a
safe means of access up and over obstructions present in a
designated walkway as part of a safe roof access system or
as a standalone item used internally (I.e warehousing) when
access is required. Can be combined with KEE WALK, or as a
stand alone item when access or egress is required over an
obstruction.
The Step Over system provides both a demarcation route for
at roofs which are not accessible to the public, where access
is still required for the purpose of carrying out repairs and
maintenance. They can also be used within a warehousing
environment or internal application where access up and over
plant or equipment is required in order to provide safe passage
from point to point.
APPLICATION
KEE WALK®Step Over has been designed to be fully adjustable
and can accommodate heights from 600mm up to 1400mm.
DURABILITY
KEE WALK®Step Over is available in a range of high quality
nishes. The components are supplied with a galvanised
nish carried out to BS EN ISO 1461 and ASTM A53: Hot Dip
Galvanised Coatings Specication and Testing Methods, giving
an average coating of between 65-85 microns. All cast clamps
have Threadkoat applied to all tapped holes. All grub screws are
carbon steel and have Kee Koat protection applied to ensure
minimal maintenance.
COMPONENT BASED SYSTEMS
All products consist of high quality tubing that seamlesly
complements our existing safety portfolio. KEE WALK®Step
Over mounts easily to all variants of the KEE WALK Walkway &
KEEGUARD systems as well as Safe Access Solutions such as
Mobile Access Platforms & Static Access Platforms.
VERSATILE SYSTEMS
The KEE WALK®Step Over range has been specially designed
with different heights and foot styles to accommodate all levels
and roof types. The exibility of the KEE KLAMP design allows
the systems to be used on plant congested or complex detailed
roofs. The product range has been extended to suit specic
requirements and includes the standard design and bespoke
solutions.

System Overview
2
TESTING & CERTIFICATION
Tested in accordance with the following
(See Specication Section for full details) :-
EN ISO 14122: 2016 Part 3
KEE WALK® Step Over systems do not require physical xing
to the building’s structure. The complete system’s design,
manufacture, testing and installation have been internally
assessed and designed in accordance with EN 14122-3
European Standards.
OFFICIAL DOCUMENTATION
All Systems comply with the following: - Work at Height
Regulations.
- HSG-33, Health & Safety in Roof work
- HSE INDG 284- Working on Flat Roofs
- BS EN 516: 2006
AESTHETICS
The smooth lines of the standard galvanised nish can be
further enhanced by the application of powder coating to EN
13438.
MATERIALS
Steel tubing to EN 10255. 42.4mm diameter tube x 3.2mm wall
thickness. All steel components galvanised to BS EN ISO 1461.
All xings are hot dipped galvanised to BS EN ISO 1461.
All cast clamps have Threadkoat applied to all tapped holes.
All grub screws are carbon steel and have Kee Koat protection
applied to ensure minimal maintenance.
Where tubing is cut on site zinc rich paint is applied to the cut
end of the tube.
Powder Coating to EN 13438.
KEE WALK tread is manufactured in high grade nylon/
aluminium incorporating raised textured sections. Open tread
design ensures water drains away
SYSTEMS DISTRIBUTORS
KEE WALK®Step Over is available as a supply and installation
service or component supply only. Products are available from
Kee Safety directly or one of its licensed distributors.

Checking the Step Over System’s Components
3
10-7
325-7
62-7
440-7
10-76
326-7
63-7
KGTF1
29-7
45-7
69-7
TB3-7
55-7
74-7
77-7
TB150
C50-77
199-6
105-7
TRSTEPASSY
3. Designation and function of the components for standard systems
The Step Over system consists of the following pre-assembled modules & individual components. The exact number of individual components depends upon the length and construction of a specic
system. All ttings are cast from malleable cast iron to BS EN 1562 and galvanised to BS EN ISO 1461 and full part numbers for reference are detailed below. Aluminium toe board is 6062-T6 grade.
Note: A complete list of all parts and details on the total weight of the Step Over system is provided with the delivery. The load-bearing capacity of the roof must be equal to or exceed the capacity specied.

Checking the Step Over System’s Components
4
Weighted foot assembly Front guardrail upright Step module guardrails
Bridge module guardrails Toe board assembly
Bridge module Back upright assembly Stair tread assembly
A B C
D E H
FG

Checking the Step Over System’s Components
5
Exploded view of system layout and location of components and sub-assemblies:
A
B
C
D
E
H
F
G

Platforms for the Major Roof Types
6
Roof Type Obstacle Height (mm) Obstacle Width (mm) Foot Type Part Number
Membrane/Asphalt/PVC 600 1000 440-7 STMB600
Membrane/Asphalt/PVC 800 1000 440-7 STMB800
Membrane/Asphalt/PVC 1000 1000 440-7 STMB1000
Membrane/Asphalt/PVC 1200 1000 440-7 STMB1200
Membrane/Asphalt/PVC 1400 1000 440-7 STMB1400
4. The Kee Safety Step Over modules are available to suit all major roof types
The Step Over range consists of a number of different congurations to suit the major at roof types. Membrane and concrete roof type platforms are standard units, whereas metal prole roofs are
bespoke to the particular application, requiring a survey and semi-bespoke base plate layout design. This will ensure a perfect t and other height/width/length variables can be accommodated as a
bespoke solution - contact Kee Safety for further information.
Step Overs for Membrane/Asphalt/PVC roofs
Step Over shown with 440 base feet for Membrane/Asphalt/
PVC roofs.

Platforms for the Major Roof Types
7
Roof Type Obstacle Height (mm) Obstacle Width (mm) Foot Type Part Number
Concrete 600 1000 62-7/63-7 STCR600
Concrete 800 1000 62-7/63-7 STCR800
Concrete 1000 1000 62-7/63-7 STCR1000
Concrete 1200 1000 62-7/63-7 STCR1200
Concrete 1400 1000 62-7/63-7 STCR1400
The Kee Safety Step Over modules are available to suit all major roof types
The Step Over range consists of a number of different congurations to suit the major at roof types. Membrane and concrete roof type platforms are standard units whereas metal prole roofs are bespoke
to the particular application, requiring a survey and semi-bespoke base plate layout design. This will ensure a perfect t and other height/width/length variables can be accommodated as a bespoke
solution - contact Kee Safety for further information. Where access is limited on a roof, or within a warehouse environment, we can offer the below solution.
Concrete floors/restricted access roofs*
*Concrete slab and elastomeric pad to be used on membrane/asphalt/PVC roofs to spread the imposed load from the platform.

Assembling the Step Over
8
STEP 1
Assembling back leg upright with weights and cross rail
Take both back upright assemblies (Part G) to the position of the obstacle, along with the weighted
foot assemblies (Part A).
Starting with the left-hand side back upright assembly, up end the upright such that it is orientated
with the 10-7 tting at the bottom. Pick up the weight cross rail, and feed through into the lower
tting of the upright, and slide the right-hand side towards the left.
Insert the cross rail at mid-point to connect both uprights together.
Insert the 74-7 ttings into the 440-7 weights and add the weights to either end of the tube, ensuring
the weights are inserted fully. Tighten the 74-7 grub screws to 39Nm.
Manoeuvre the assembled rear upright into position at the point of install.
Tighten all grub screws to the required 39Nm torque setting.
5. Installation should only be carried out once the design has been verified in the Step Over
Configurator and the installer has been fully trained by Kee Safety.
Tool list:
Ratchet
Hex key socket screw sized 5/16”AF
Torque wrench 10-60Nm
Electric/battery drill
Electric/battery impact driver
Selection of drill bits – including 8.5mm diameter bit
Tape measure
Line and level
Full metric socket set
Fell set metric spanners
Full set of metric Allen keys
Full set of imperial Allen keys
Copper/rubber mallet
Rags and cleaning uid
STEP 1
STEP 1

Assembling the Step Over
9
STEP 3 - Assemble bridge module and guardrail onto rear leg uprights
Take the bridge platform subassembly (Part F) framework and insert into the 326 tting present
on one side of the rear uprights, followed by the guardrails (Part B) into the ttings further up the
upright.
Bring the opposite outer leg assembly to meet the platform, and locate tubes from bridge module
subframe into the slope ttings present on the uprights.
Add the Kee Walk bridge tread assembly to the substrate, ensuring it is centred left/right and front/
back and x into place using the 105-7 ttings to the underside and securing in place with self-
drilling screw.
Repeating all sub sets of step 1 to build other side of platform uprights
Inserting bridge subframe tubes into uprights at obstruction
Inserting bridge subframe tubes into uprights at obstruction and securing walkway
STEP 2 - Repeat Step 1 for other side of stair case
Repeating of Step 1 enables the other side of the uprights to be built, which in turn allows the
next phase of the build to commence.
STEP 2
STEP 3
STEP 3

Assembling the Step Over
10
STEP 4 - Staircase assembly
Take the stair tread assembly module (Part H) to the area in which it is to be installed, and collect
the 440 weights, cross tubes and relevant ttings (Part A).
Insert the lower weight cross tube into the lower 10-7 ttings sliding from left to right; space the tube
such that an equal overhang exists both sides and tighten grub screws on 10-7’s to 39Nm.
Locate cross brace tube into C50-77 tting and tighten.
Take the pre-assembled stair module and move towards assembled bridge platform in previous
steps.
STEP 5 - Staircase assembly
Locate upper tube from staircase and brace tube in the correct orientation to meet the corresponding
tube sockets in the lower 29-7 and upper 326-7 tting.
Starting with the upper tube, manoeuvre the lower tube down towards the stair assembly and lower
the staircase so that the upper tube can be inserted Into the 326-7 tting. Before tting fully, locate
the lower tube into 29-7 tting.
Push both tubes on both sides home, ensuring staircase is square. Lightly tighten grub screws to
locate stair assembly into place.
Insert the 74-7 tting into the weights and slide the weights onto the end of the tube ensuring that
they are fully inserted.
Double check for location, once happy tighten all grub screws to 39Nm. Repeat the procedure for
the other staircase.
STEP 4 STEP 5

Assembling the Step Over
11
STEP 6 - Assemble the remaining guardrails and toe board
Take the forward assembled uprights (Part B) and insert into the 29-7 tting present on the stair
assembly and loosely tighten the ttings.
Starting on one side, insert the two inclined hand rails (Part C) into the 326-7 ttings present on the
rear upright, and manoeuvring the front upright forward insert both rails in the 29-7 and the 55-7
ttings, move the upright back to its upright position and loosely tighten.
Using a spirit level, ensure the forward upright is plumb and level in the X and Y plane, once level,
tighten all grub screws to 39Nm.
Repeat for other side of staircase, and then repeat the entire procedure for the other staircase.
STEP 7 – Fitting toe board
Locate toe board (Part E) inboard of bridge platform and pick the TBFP1 xing packs and TB3-7
toe-board xing clamps.
Insert the M12 bolts into the extruded channel, and locate 1 bolt either side of each upright as
shown in the illustration.
Locate the TB3 clip onto the bolts, ts the nuts and washers.
Level the toe board and tighten the xings to 25Nm.
STEP 6 STEP 7

Assembling the Step Over
12
STEP 8 - Levelling and finalising of treads
With the platform now fully assembled, check the tread rise (distance in height between treads),
going (where the tread sits in plan), and angle.
Starting at the bottom tread, measure the rise between the treads ensuring that there is no more
than 5% difference between any two tread heights*.
Looking from above, there should be a minimum of 10mm overlap on the treads*.
Starting at the top tread, and using a spirit level, ensure that all treads are level left/right and
forwards/backwards. If an adjustment needs To be made in the fore/aft level simply slacken the
grub screws on the 45-76 and 10-76 on both sides, adjust tread to correct, level angle and re-
tighten.
If adjustment needs to be made to accommodate the 10mm overlap between treads, simply undo
the 13mm nuts holding the tread extrusion to the 199-6 tting and adjust, ensuring that they
are re-tightened on completion.
(* = The Stair rail and tread assemblies are pre-assembled at Kee Safety so no major adjustments
should be required)
STEP 9 - Check and recheck all grub screws and finalise assembly
Once all treads are level, the platform is fully assembled, and the toe board is present ALL grub
screws are to be torqued to 39Nm
Starting at the lower left staircase, working from the lowest point, systematically tighten all grub
screws with a calibrated torque wrench and indelibly mark the grub screws with a paint marker
once at torque.
This performs two functions, it lets the installer know once a grub screws has been tightened, but
also on annual inspection allows the inspector to see if a grub screw has come lose and needs
attention.
The same principle is applied to all other xings, using 18Nm for all 13mm headed xings, 25Nm
on toe board M12 xings and Tek Screws to be tightened until a compressing of the foam backed
washer is observed.
It is IMPERATIVE that ALL grub screws and fixings are checked on the ENTIRE assembly and
torqued up to the correct torque value and marked!!
STEP 8
STEP 9

Finished Step Over
13
6. Step Over assembled with 440-7 feet for membrane/asphalt/PVC roofs
Step Over assembled with Top Fix baseplates for metal profile roofs
Step Over assembled with 62-7/63-7 feet for concrete roofs
METAL PROFILE ROOF APPLICATION
Whilst we can supply Step Over platforms for membrane/asphalt/PVC and concrete from stock,
owing to the vast variety of roong proles and xing methods it is not possible to carry stocks of
Step Over platforms specic to each roong type and manufacturer.
A bespoke solution is available following a site survey to best advise on the product that is most
suited to the requirement, contact Kee Safety for more information.

Kee Walk Mini Step Over
INSTALLATION
Installation should be carried out by at least 2 competent
persons. Step Over units can be heavy and care should be
taken at all times.
You will need the following in order to install the Mini Step
Over.
Tool list:
1No 13mm socket
1No 13mm spanner
¼” Hex key socket
Torque wrench 10- 60 Nm approx
Small magnetic level
MINI STEP 200MM CLEARANCE - FIXED
Designed to clear obstacles up to 200mm in height, this
Mini Step Over provides safe access over smaller hazards
STMFX2003 - 473mm clearance. Weight 14.05kg
STMFX2004 - 713mm clearance. Weight 15.55kg
STMFX2005 - 963mm clearance. Weight 17.05kg
MINI STEP 400MM CLEARANCE - FIXED
Designed to clear obstacles up to 400mm in height, this
Mini Step Over provides safe access over larger hazards
STMFX4003 - 473mm clearance. Weight 36.24kg
STMFX4004 - 713mm clearance. Weight 37.34kg
STMFX4005 - 963mm clearance. Weight 39.24kg
MINI STEP 200MM CLEARANCE - FREE
STANDINGG
With recycled PVC weighted bases to eliminate the need to x the
unit to the roof, this unit is designed to clear obstacles up to 200mm
in height.
STMFS2003 - 240mm clearance. Weight 65.63kg
STMFS2004 - 490mm clearance. Weight 67.13kg
STMFS2005 - 740mm clearance. Weight 68.63kg
MINI STEP 200MM CLEARANCE - FREE
STANDINGG
With recycled PVC weighted bases to eliminate the need to x
the unit to the roof, this unit is designed to clear obstacles up to
400mm in height.
STMFS2003 - 433mm clearance. Weight 83.93kg
STMFS2004 - 673mm clearance. Weight 85.43kg
GENERAL
Two options are available, free standing, which the unit stands
on two 26kg base weights, or xed, which can be attached to
suitable securing surfaces.
KEE WALK Mini Step Over Fixed systems require physical xing
to the buildings structure.
KEE WALK Mini Step Over free standing systems are safe for
wind speeds in excess of 86mph.
TESTING
All modules meet the requirements of EN 516 : 2006.
Modules STMFS200* and STMFX200* also meet the
requirements of EN 14122:3 - 2016.
MINI STEP MODULE KITS
Low maintenance, KEE WALK Mini Step Over modules are made from Galvanised steel, Aluminium extrusion and reinforced Nylon treads and are tested and
compliant to EN 516 Class 1-C. Available as kits, the Step Overs are supplied at packed, but are quick and easy to assemble.
2 Height clearances options, 200mm and 400mm
3 lengths available, 3, 4 and 5 tread options
Two xing options, free standing and xed
14
DANGER TO LIFE!
Establish that the is installed correctly!! Failure to
do so could result in death or serious injury.
Recycled PVC base weights weight in excess of 26KG
each! Take care when handling.

b) )Peel back rubber end cap and slide 2no. M8 bolts onto the
end of the aluminium extrusion. Replace rubber end cap. Pass
M8 bolts through 62-6 tting and secure using M8 xings and
a 13mm spanner. Using a torque wrench tighten to 15N/m.
Repeat process for 3 other legs.
a) Unpack and check contents. The package should contain
1no. platform, 4no. legs and M8 xings.
c) Turn unit over and place over obstacle. Either x to surface
or sturdy obstacle using appropriate xing method. Ensure all
xings are tight with ttings torqued to 29N/m and M8 nuts are
tightened to 15N/m.
Assembling and fixing the Mini Step Over - Fixed Version
b) Peel back rubber end cap and slide 2no. M8 bolts onto the
end of the aluminium extrusion. Replace rubber end cap. Pass
M8 bolts through 62-6 tting and secure using M8 xings and
a 13mm spanner. Using a torque wrench tighten to 15N/m.
Repeat process for 3 other long legs.
c) Turn unit over and place over obstacle. Either x to surface
or sturdy obstacle using appropriate xing method. Ensure all
xings are tight with ttings torqued to 29N/m and M8 nuts are
tightened to 15N/m.
a) Unpack and check contents. The package should contain 1no.
platform, 4no. long legs, 4no. short legs, 2no. step platforms, and
M8 xings. Add 4no. legs to step tread - 2no. short at the front
and 2no. long at the back. Tighten grub screws.
STMFX400* MODULES
STMFX200* MODULES
15

b) Peel back rubber end cap and slide 2no. M8 bolts onto the
end of the aluminium extrusion. Replace rubber end cap. Pass
M8 bolts through 62-6 tting and secure using M8 xings and
a 13mm spanner. Using a torque wrench tighten to 15N/m.
Repeat process for 3 other legs.
b) Peel back rubber end cap and slide 2no. M8 bolts onto the
end of the aluminium extrusion. Pass M8 bolts through 199-6
tting and secure using M8 xings and a 13mm spanner. Using
a torque wrench tighten to 15N/m. Repeat process for 3 other
legs.
a) Unpack and check contents. The package should contain
1no. platform, 2no. weighted bases and M8 xings. Place
weighted bases in position either side of obstacle. Lower
platform into position ensuring 199-6 tting lines up with the
aluminium extrusion as per diagram.
c) Ensure all xings are tight with ttings torqued to 29N/m and
M8 nuts tightened to 15N/m.
c) Ensure all xings are tight with ttings torqued to 29N/m and
M8 nuts tightened to 15N/m.
Assembling and fixing the Mini Step Over - Free standingg
a) Unpack and check contents. The package should contain
1no. platform, 4no. legs, 2no. weighted bases and M8 xings.
Position weights either side of obstacle. Position legs so that the
62-6 oblong ttings are at the top and 61-6 sit on the oor. Slide
tting to tubes with vertical legs on the inside of the horizontal
tubes as per diagram above. Tighten the grub screws.
STMFS400* MODULES
STMFS200* MODULES
16

Kee Walk Step Over System Recertification
17
Periodic inspections by a competent person are recommended by the manufacturer. In
UK/Europe these are required under Regulation 5 of the Workplace (Health, Safety &
Welfare) Regulations, the Work at Height Regulations and BS EN 365. The frequency will
depend upon the environment, location and usage but should be at least every 12 months.
Walk and visually inspect the complete installed system in relation to the client's general
needs. Establish if any modications and/or additional products are required to reect any
refurbishment requirements or additional plant & equipment which have been installed and
require access.
Check installation conguration is complete as per the original installation drawing/plan.
Ensure the system has not been modied or tampered with by un-authorised persons.
Check all base feet are in contact with the roof.
Check all counter weights (where present on original drawing) are in place as per the
original drawing. This is essential for longevity of the roof.
Check all grub screws are in place and correctly torqued.
Check the general height and level of the system including the leg centres and platform
overall conguration.
(This only tends to be an issue if the system has been tampered with between inspections).
Any galvanised components showing signs of corrosion should be wire brushed thoroughly
and galvanised spray/paint applied as appropriate. If rusted signicantly, take digital
photographs and include these in the inspection report.
Where toe boards are tted check the brackets that support the toe board are in place and
sufciently torqued.
Where applicable check xings to walls/structures including cat ladder clamps are in place
and sufciently torqued.
7. KEE WALK STEP OVER SYSTEM RECERTIFICATION

KEE WALK® Step Over
KEE WALK is a registered trademark of Kee Safety Ltd. Whilst every effort has been made to ensure the accuracy of the information contained within this brochure Kee Safety Ltd cannot be held responsible for any errors or omissions.
Kee Safety Ltd reserves the right to alter or withdraw products without prior notice. Kee Safety Ltd accepts no responsibility for any loss or damage arising from improper use of their products. ©2016 Kee Safety Ltd. All Rights Reserved.
KS/KWSOMM_UK_v2/1018
Kee Safety Ltd.
Cradley Business Park
Overend Road
Cradley Heath
West Midlands
B64 7DW
Tel: +44 (0) 1384 632188
Fax: +44 (0) 1384 632192
Email: sales@keesafety.com
www.keesafety.com
Table of contents
Popular Lifting System manuals by other brands
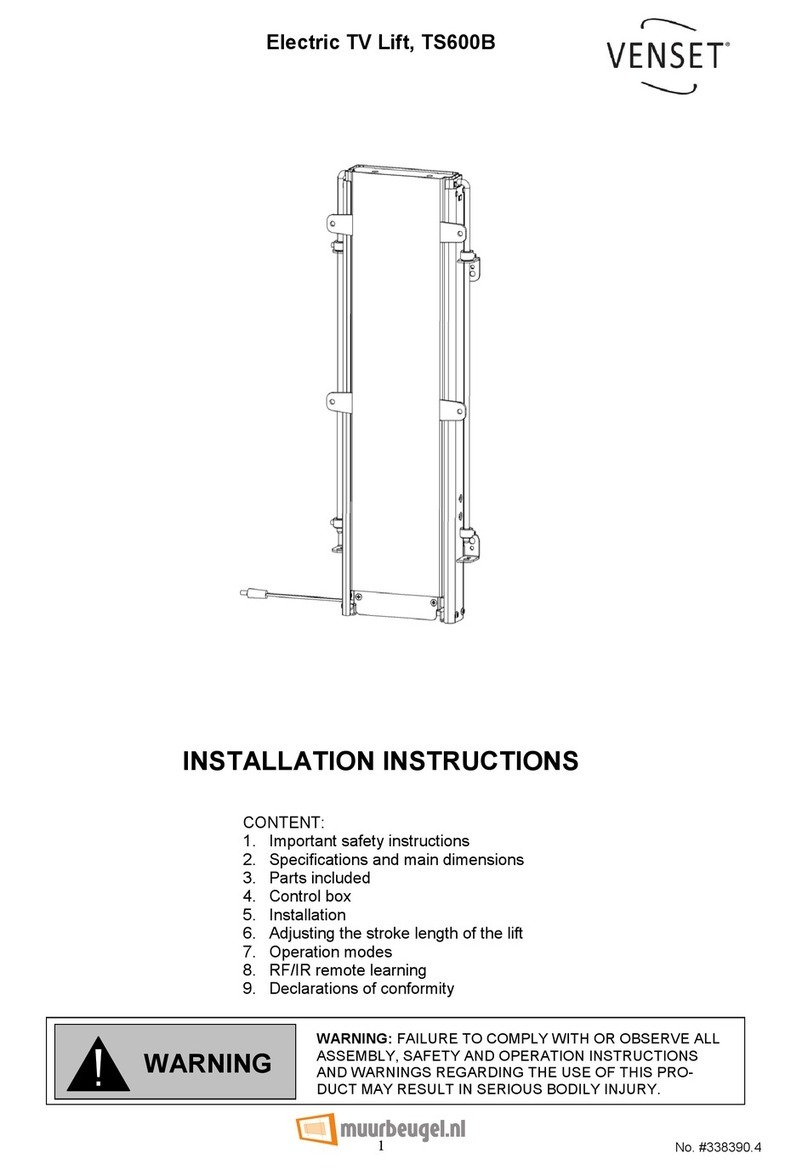
Venset
Venset TS600B installation instructions

AmeriGlide
AmeriGlide Hercules II Hybrid installation guide
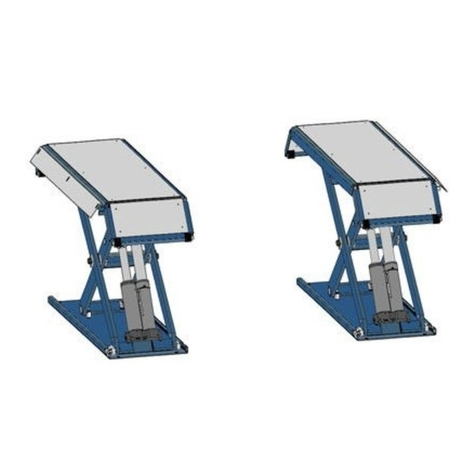
Nussbaum
Nussbaum Sprinter NT Operating Instruction and Documentation
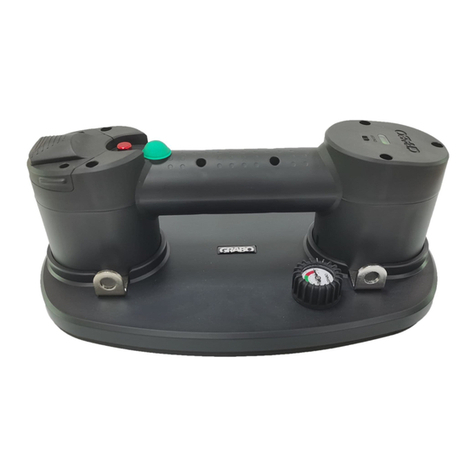
Grabo
Grabo NEMO Operator's manual
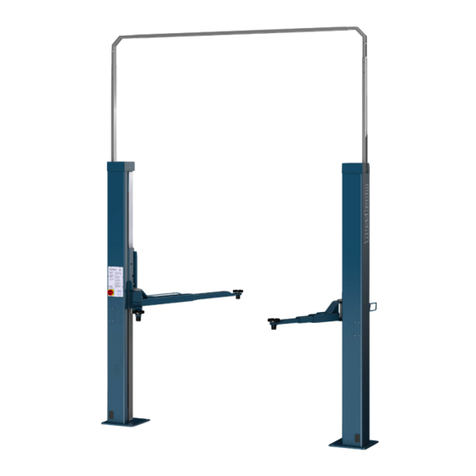
Nussbaum
Nussbaum ATT HYMAX S 3000 Operating manual, Inspection book
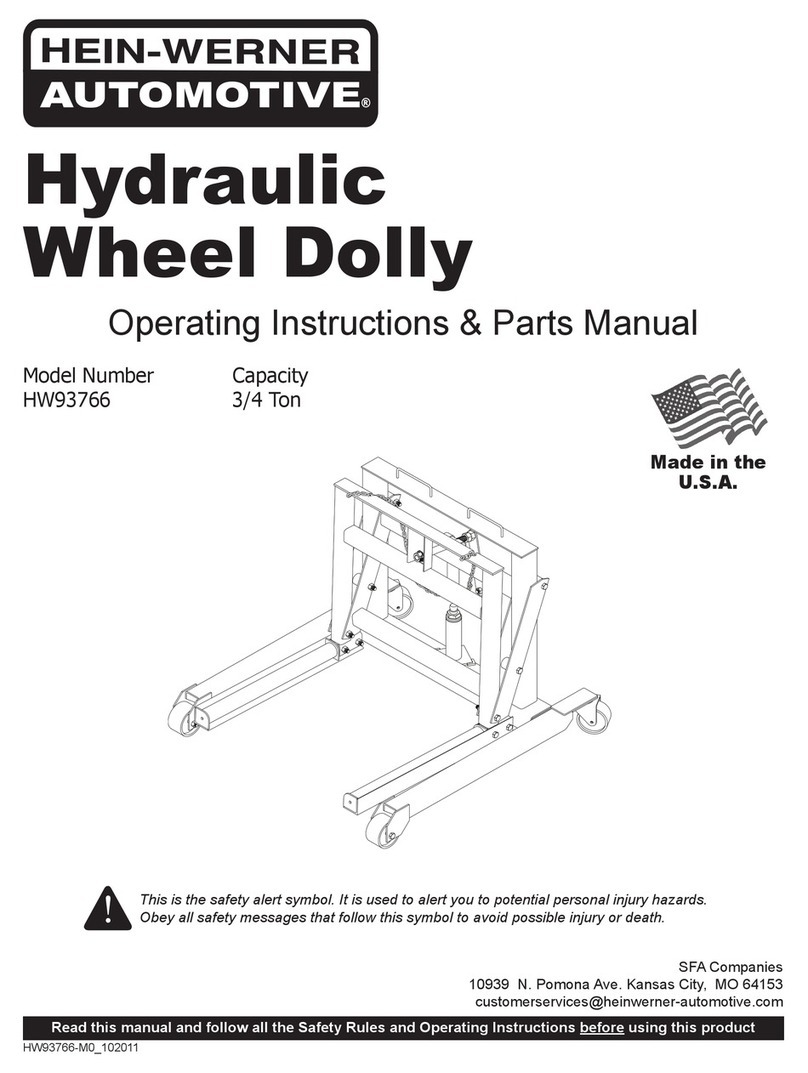
HEIN-WERNER AUTOMOTIVE
HEIN-WERNER AUTOMOTIVE HW93766 Operating instructions & parts manual