Kemppi FLEXLiTE TX Series User manual

Flexlite TX
Operating manual - EN
FLEXLITE TX
© Kemppi 2 1920910 / 2039

Flexlite TX
Operating manual - EN
CONTENTS
1. Flexlite TX 4
2. About equipment 5
3. Installation 7
3.1 Assembling torch 8
3.2 Installing torch remote 10
3.3 Installing start switch extension 12
3.4 Connecting torch 14
4. Operation 17
4.1 Consumable and gas flow selection 18
4.2 Electrode tip 19
5. Maintenance 21
5.1 Troubleshooting 23
5.2 Disposal of machine 25
6. Technical data 26
6.1 Technical data TX 133 27
6.2 Technical data TX 135 28
6.3 Technical data TX 163 29
6.4 Technical data TX 165 30
6.5 Technical data TX 223 and TX 253 31
6.6 Technical data TX 225 and TX 255 32
6.7 Technical data TX 303 and TX 353 33
6.8 Technical data TX 305 and TX 355 34
6.9 Technical data TX E 223, TX E 253 and TX E 353 35
7. Ordering codes 36
© Kemppi 3 1920910 / 2039

Flexlite TX
Operating manual - EN
1. FLEXLITE TX
These instructions describe the use of Kemppi's Flexlite TX TIG welding torches. Flexlite TX torches are designed for
manual welding in demanding industrial use and they are compatible with Kemppi TIG welding equipment with 4-
pin or 7-pin connectors. Flexlite TX range covers both water-cooled and gas-cooled models.
Flexlite TX torches are available in two different levels, K3 and K5, each designed to serve specific welding needs.
K3 level K5 level
TX 133 TX 135
TX 163 TX 165
TX 223 TX 225
TX 253 TX 255
TX 303 TX 305
TX 353 TX 355
Important notes
Read the instructions through carefully. For your own safety, and that of your working environment, pay particular
attention to the safety instructions delivered with the equipment.
Items in the manual that require particular attention in order to minimize damage and harm are indicated with the
below symbols. Read these sections carefully and follow their instructions.
Note: Gives the user a useful piece of information.
Caution: Describes a situation that may result in damage to the equipment or system.
Warning: Describes a potentially dangerous situation. If not avoided, it will result in personal damage or fatal injury.
DISCLAIMER
While every effort has been made to ensure that the information contained in this guide is accurate and com-
plete, no liability can be accepted for any errors or omissions. Kemppi reserves the right to change the spe-
cification of the product described at any time without prior notice. Do not copy, record, reproduce or
transmit the contents of this guide without prior permission from Kemppi.
© Kemppi 4 1920910 / 2039

Flexlite TX
Operating manual - EN
2. ABOUT EQUIPMENT
The Flexlite TX TIG welding torches are packed with features designed to support professional welding. The equip-
ment consists of:
1. Gas nozzle
2. Collet body
3. Collet
4. Insulating ring*
5. Torch body
6. Electrode back cap
7. Control cable connector (start and remote signals)
8. Welding cable connector (shielding gas and welding current)
9. Coolant outlet and inlet hose connectors (water-cooled models only)
K3 level torches differ from K5 level torches in connectors, for example. For information on K3 level torch connectors,
refer to "Connecting torch" on page14.
10. ON/OFF switch
11. Switch cover
12. Torch handle
© Kemppi 5 1920910 / 2039

Flexlite TX
Operating manual - EN
* Some Flexlite TX torch models also include a back cap insulating ring, in addition to the gas nozzle insulating ring.
Separate K3 level torches with a DIX connector and a manual gas valve in the torch body are also available. Use these
torches with MMA power sources for scratch and TouchArc TIG ignition.
Dedicated lens models of the collet body and the gas nozzle exist for laminar flow welding. Bigger lens consumables
require an additional insulating ring.
EQUIPMENT IDENTIFICATION
Serial number
Serial number of the device is marked on the rating plate or in another distinctive location on the device. It is
important to make correct reference to the serial number of the product when ordering spare parts or mak-
ing repairs for example.
Quick Response (QR) code
The serial number and other device-related identification information may also be saved in the form of a QR
code (or a barcode) on the device. Such code can be read by a smartphone camera or with a dedicated code
reader device providing fast access to the device-specific information.
© Kemppi 6 1920910 / 2039

Flexlite TX
Operating manual - EN
3. INSTALLATION
Ensure that the welding equipment is not connected to the mains or that the welding torch is not connected to the
welding machine at this stage.
Protect the equipment from rain and direct sunshine.
"Assembling torch" on the next page
"Installing torch remote" on page10
"Installing start switch extension" on page12
"Connecting torch" on page14
Before installation and use
Ensure compliance with your local and national safety requirements regarding the installation and use of high
voltage units.
Check the contents of the packages and make sure the parts are not damaged.
Do not connect welding equipment to the mains before the installation is complete.
© Kemppi 7 1920910 / 2039

Flexlite TX
Operating manual - EN
3.1 Assembling torch
This chapter describes a typical Flexlite TX welding torch assembly. The details shown may vary depending on the
exact torch setup.
1. Install the insulating ring and collet body.
Some Flexlite TX torch models also include a back cap insulating ring, in addition to the gas nozzle insulating ring.
2. Install the gas nozzle and the collet.
© Kemppi 8 1920910 / 2039

Flexlite TX
Operating manual - EN
3. Prior to installing the tungsten electrode, grind the electrode tip to the appropriate dimensions for your welding
application. For more information, refer to the section "Electrode tip" on page19.
4. Push the electrode into the torch and through the collet and gas nozzle.
5. Install the electrode back cap. Tighten the back cap to lock the electrode in place.
Do not use excessive force. Overtightening may damage the torch components.
By loosening the electrode back cap, the electrode can be installed also by pushing it into the torch from the other side.
© Kemppi 9 1920910 / 2039

Flexlite TX
Operating manual - EN
3.2 Installing torch remote
You can install a torch remote on a K5 level torch only.
Many Flexlite TX welding torches are equipped as standard with ON/OFF start/stop switches. Optional remote control
devices can be fitted to these TX torch models, allowing both start/stop function and welding current adjustment.
Ensure that the welding equipment is not connected to the mains or that the welding torch is not connected to the
welding machine at this stage.
1. Open the switch cover by releasing the screws in the rear section of the cover and remove the cover.
2. Take the existing circuit board out of its slot in the handle and unplug the connector.
© Kemppi 10 1920910 / 2039

Flexlite TX
Operating manual - EN
3. Connect the torch remote control circuit board to the connector and place it in its slot in the handle. (Rocker
switch model shown on the left and roller switch model on the right:)
4. Install the new switch cover by placing the front end of the cover in first and then pushing the rear end of the
cover down. (Rocker switch model shown on the left and roller switch model on the right:)
5. Secure the switch cover in place with the two screws in the rear section of the cover.
© Kemppi 11 1920910 / 2039

Flexlite TX
Operating manual - EN
3.3 Installing start switch extension
The standard ON/OFF switch can be replaced with an extended start switch.
1. Open the switch cover by releasing the screws in the rear section of the cover and remove the cover.
2. Replace the standard start switch button on the cover with the extended start switch button.
© Kemppi 12 1920910 / 2039

Flexlite TX
Operating manual - EN
3. Install the cover with the start switch extension in place.
4. Secure the switch cover in place with the two screws in the rear section of the cover.
The switch extension cannot be used with the S neck TX torch models.
© Kemppi 13 1920910 / 2039

Flexlite TX
Operating manual - EN
3.4 Connecting torch
Hand tighten the torch connectors. Loose connectors may overheat, create contact disturbances, mechanical damage
and water or gas leakage.
For connecting the torch, refer also to your welding equipment’s instructions.
Gas-cooled TIG torch (K5 level)
1. Connect the welding cable and the control cable to the power source. Secure by turning the connectors clock-
wise.
Water-cooled TIG torch (K5 level)
1. Connect the welding cable and the control cable to the power source. Secure by turning the connectors clock-
wise.
© Kemppi 14 1920910 / 2039

Flexlite TX
Operating manual - EN
2. Connect the coolant inlet and outlet hoses to the cooling unit. Note that the connectors are color-coded.
Make sure to connect the coolant hoses to the correct hose connectors. If the connections cross, the torch and torch
body may overheat.
Connectors in TIG torch (K5 level)
1. Welding cable connector
2. Control cable connector
3. Coolant hose connector
4. Coolant hose connector
© Kemppi 15 1920910 / 2039

Flexlite TX
Operating manual - EN
Connectors in TIG torch (K3 level)
1. Control cable connector.
2. Welding cable and coolant connector. In water-cooled torches this is the coolant outlet hose connector. In gas-
cooled torches this is the shielding gas connector.
3. Coolant inlet hose connector (water-cooled torches only).
4. Shielding gas connector (water-cooled torches only).
With K3 series torches that have a DIX connector, use a separate gas hose for gas connection.
Connectors in TIG torch with euro connector (K3 level)
1. Euro connector
2. Coolant hose connector
3. Coolant hose connector
© Kemppi 16 1920910 / 2039

Flexlite TX
Operating manual - EN
4. OPERATION
Before using the equipment, ensure that all the necessary installation actions have been completed according to
your equipment setup and instructions.
Welding is forbidden in places where there is an immediate fire or explosion hazard!
Welding fumes may cause injury. Take care to ensure sufficient ventilation during welding and wear respiratory pro-
tection!
Always check before use that interconnecting cable, shielding gas hose, earth return lead/clamp and mains cable are in
serviceable condition. Ensure that the connectors are correctly fastened. Loose connectors can impair welding per-
formance and damage connectors.
Many Flexlite TX torches are equipped with an ON/OFF switch. The exact operation and function of the switch may
vary depending on your welding machine settings (e.g. 2T, 4T or Minilog).
In K3 level DIX torches with a manually operated shielding gas valve to regulate the shielding gas flow, open and close
the gas valve in the torch body.
1. Ensure that the earth return cable is connected to the welding machine and piece to be welded.
2. To start welding, press the ON/OFF switch (1) on the welding torch handle.
3. With the roller and rocker switch versions: Adjust the welding current by rolling the roller switch (2/3) or by
pulling/pushing the rocker switch (2/3).
Welding current adjustment is available for K5 level torches only.
© Kemppi 17 1920910 / 2039

Flexlite TX
Operating manual - EN
4.1 Consumable and gas flow selection
The tables in this chapter provide some basic guidance only and must not be considered as a definitive source of elec-
trode and gas flow rate information.
The welding current setting defines the electrode size and the shielding gas flow rate. The most typical shielding gas
for TIG welding is argon.
The following tables provide some basic guidance for the electrode size and shielding gas flow rate selection.
Welding current DC- (AC) Electrode Gas nozzle Gas flow rate
A ø mm Number ø mm l/min
5...80 (5...50) 1.0 4/5 6.5/8.0 5...6
70...150 (30...100) 1.6 4/5/6 6.5/8.0/9.5 6...7
130...250 (80...150) 2.4 6/7 9.5/11.0 7...8
220...350 (120...210) 3.2 7/8/10 11.0/12.5/16.0 8...10
330...500 (180...280) 4.0 10/11/12 16.0/17.5/19.0 10...12
Electrode Welding current Base material
Type Symbol color Fe Ss Al Ti
WC20 grey AC, DC- x x x
WZ8 white AC, DC- x
Wgreen AC, DC- x
© Kemppi 18 1920910 / 2039

Flexlite TX
Operating manual - EN
4.2 Electrode tip
DC welding
For DC TIG welding, grind the tip of the tungsten electrode lengthways, into cone shape. The sharpened electrode
tip provides a steady and concentrated arc into the weld piece. The sharpening angle and length has an effect on
the arc width and penetration depth.
Sharpening principle:
Where I = 1…5 x d.
The sharpening length best suited for your purposes depends on the most used welding current level:
a. Low currents
b. Mid currents
c. High currents
When sharpening the electrode, always grind along the electrode.
AC welding
In AC TIG welding the electrode tip temperature can exceed the melting point of the electrode. Therefore the elec-
trode diameter selected and its suitability for welding current applied, can be evaluated based on the formation of
the electrode tip.
a. Too low welding current or too big electrode size. The arc is not steady and directed on the weld piece.
b. Suitable current.
c. The welding current is too high for the electrode diameter selected.
© Kemppi 19 1920910 / 2039

Flexlite TX
Operating manual - EN
When using Kemppi AC TIG equipment for specific applications, it is also possible to prepare and maintain a small
point on the electrode tip (d). This improves the directional control of the welding arc and weld pool size.
Tip: You can also prepare the basic tip formation for AC welding with the following technique:
1. Adjust the welding current a little higher than required.
2. Burn the arc over a waste piece of material, keeping the torch electrode in a vertical position.
3. Extinguish the arc immediately when the electrode tip has formed rounded spherical surface, no larger
than the diameter of the electrode, holding the same torch position as the electrode cools during the
post gas cycle.
4. Reduce the current setting to a level suitable for the work target and start welding.
Electrode tip length
The optimal protrusion (l) of the electrode tip measured from the gas nozzle tip depends on the electrode diameter,
welding current level and weld joint type.
Tip: Cleaning the electrode with steel wool can improve ignition and overall welding properties, by removing
surface oxides.
© Kemppi 20 1920910 / 2039

Flexlite TX
Operating manual - EN
5. MAINTENANCE
When planning routine maintenance, consider the operating frequency of the welding equipment and the working
environment.
Correct operation of the welding equipment and regular maintenance helps you avoid unnecessary downtime and
equipment failure. Mainly due to the high temperatures, the TIG torch head and parts require regular checks and
maintenance. Periodically, check the cables set for damage and ensure connections are tightened correctly.
Daily maintenance
Disconnect the power source from the mains power supply before handling electrical cables.
Torch head maintenance
•All insulations are undamaged and intact.
•Gas nozzle is intact and suitable for work.
•Shielding gas flows freely and steadily.
•Electrode is intact and suitable for work.
•Fastening parts of the electrode are intact and the electrode is fastened tightly in place.
•Check all the cables and connectors. Do not use them if they are damaged.
Maintenance of torch cable
•Torch cable insulations and connectors are intact.
•There are no sharp bends in the torch cable.
•Components are tightly fastened.
•Check that the current transfer surface on the torch current connector is clean and undamaged.
•Check the protective hose on the cable for damage.
For repairs, contact your Kemppi dealer.
Periodic maintenance
Only qualified service personnel are allowed to carry out periodic maintenance.
Check the electric connectors of the unit at least every six months. Clean oxidized parts and tighten loose con-
nectors.
Use the correct tension torque when fastening loose parts.
Do not use pressure washing devices.
Service workshops
Kemppi Service Workshops complete the welding system maintenance according to the Kemppi service agreement.
The main aspects in the service workshop maintenance procedure are:
•Cleanup of the machine
•Maintenance of the welding tools
•Checkup of the connectors and switches
© Kemppi 21 1920910 / 2039
Other manuals for FLEXLiTE TX Series
3
This manual suits for next models
12
Table of contents
Languages:
Other Kemppi Flashlight manuals
Popular Flashlight manuals by other brands
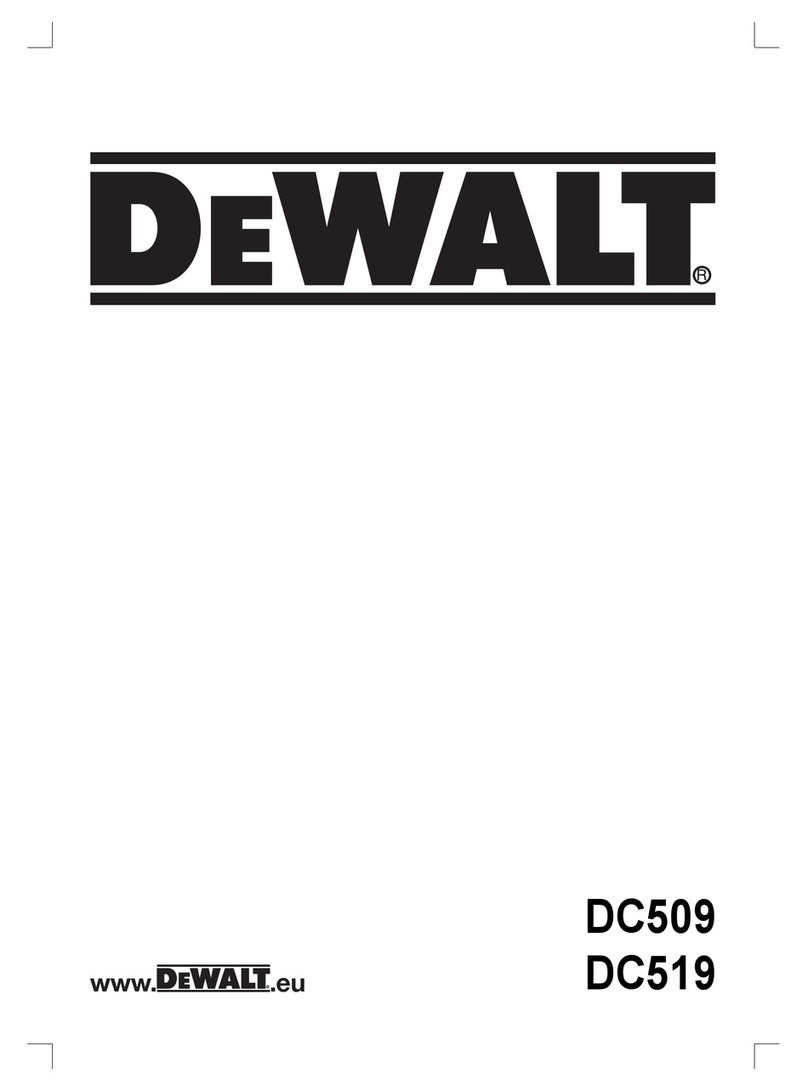
DeWalt
DeWalt DC509 user manual
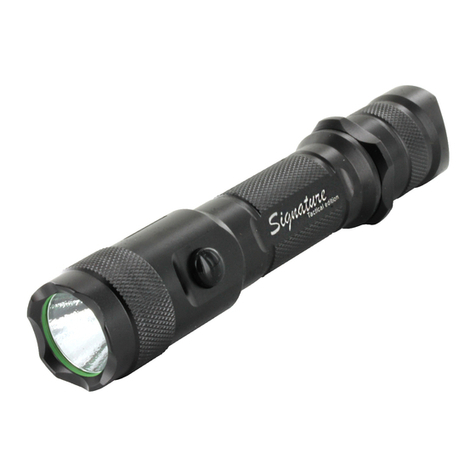
Lumapower
Lumapower Signature Tactical LX user manual
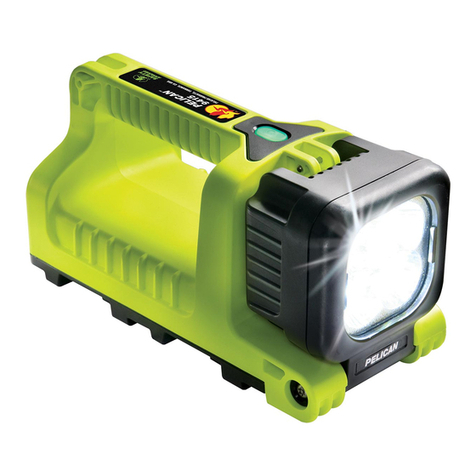
Pelican
Pelican 9415 quick start guide
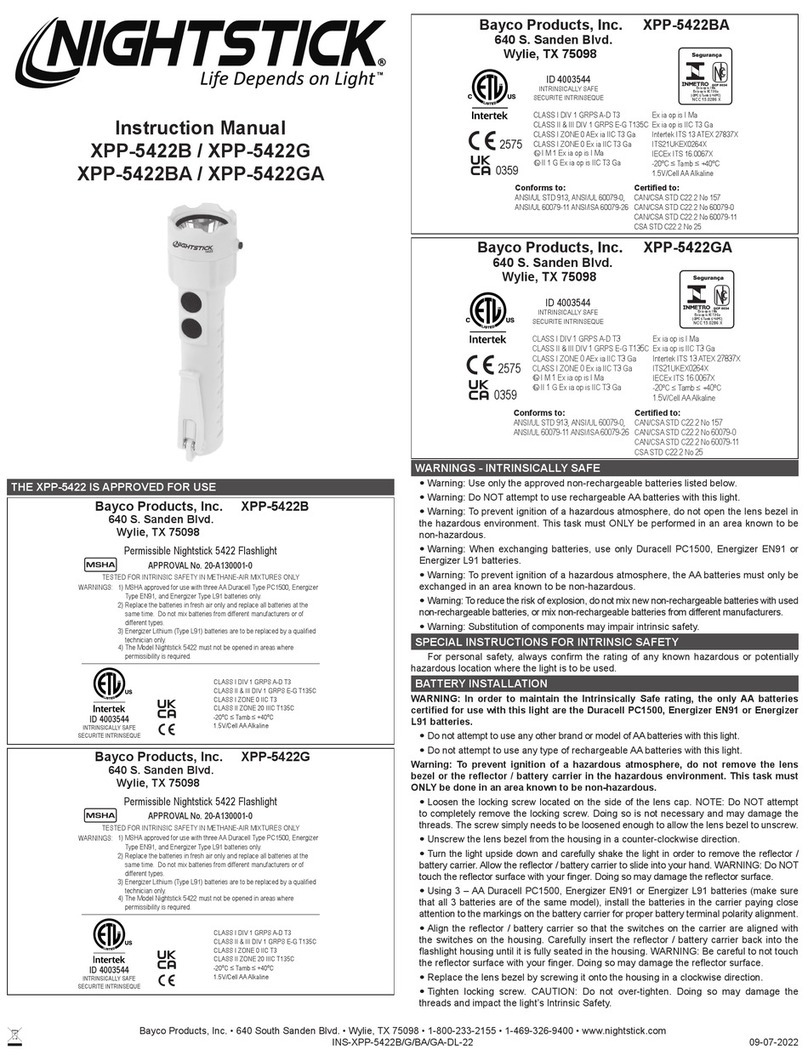
Bayco Products
Bayco Products NIGHTSTICK XPP-5422BA instruction manual
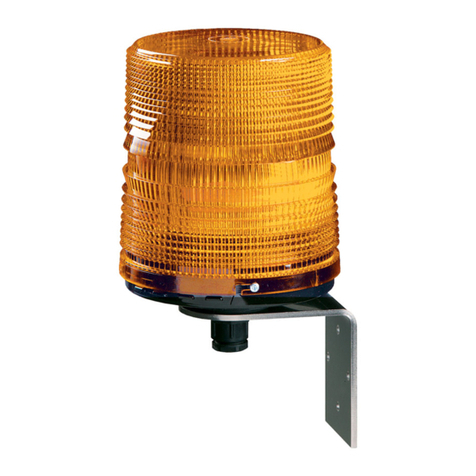
Pfannenberg
Pfannenberg PMF 2020 Operating and assembly instructions
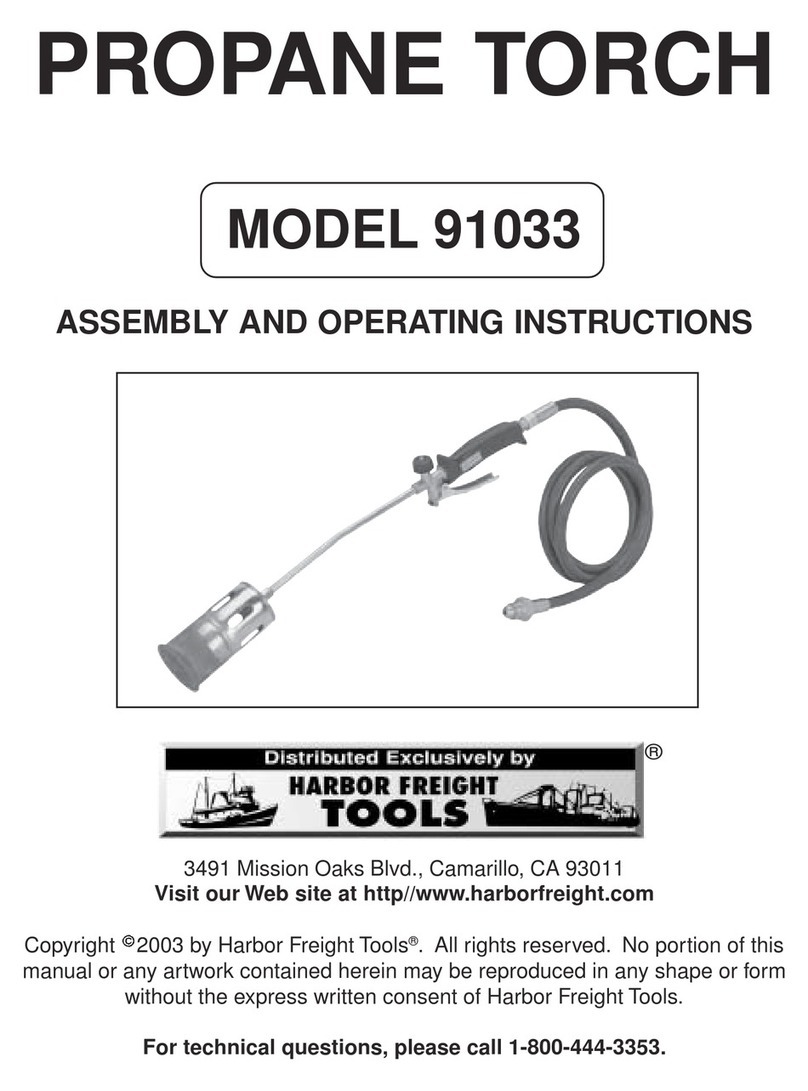
Harbor Freight Tools
Harbor Freight Tools 91033 Assembly and operating instructions