KEPCO MMI-1 Series User manual

MMI-1XX SERIES
Operating and Installation
Instructions
for use with MMI-10, MMI-40, MMI-100, MMI-110
and MMI-140
Kessler Ellis Products
10 Industrial Way East
Eatontown, NJ 07724
Phone: 732-649-7100
FAX: 732-649-7099
Website: www.kep.com
For use with version 4.XX 99588REV02182021
$10.00


1
PROPRIETARY NOTICE
The information contained in this publication is derived in part from proprietary and patent data. This
information has been prepared for the expressed purpose of assisting operating and maintenance
personnel in the efficient use of the instrument described herein. Publication of this information does
not convey any rights to use or reproduce or to use it for any purpose other than in connection with
the installation, operation and maintenance of the equipment described herein.
Copyright 1999 by Kessler Ellis Products
Contents
About this Manual ..........................................................................................................................2
1.0 Getting Started.........................................................................................................................3
1.1 What is the MMI 1XX Series?..........................................................................................3
1.1.1 The MMI Series and Its Environment ............................................................................3
2.0 Installation Instructions ............................................................................................................4
2.1 Mounting Instructions...........................................................................................................4
2.1.1 Location Considerations................................................................................................4
2.1.2 Making a NEMA-4 Mounting..........................................................................................4
2.1.3 Environmental Considerations.......................................................................................5
2.2 Power Connections ..............................................................................................................6
2.2.1 Power Requirements.....................................................................................................6
2.2.2 Grounding Requirements...............................................................................................8
2.2.3 CE Requirements ..........................................................................................................8
2.2.4 Safety Guidelines...........................................................................................................9
2.3 Communications Connections............................................................................................10
2.3.1 Connection to an External Device ...............................................................................10
2.3.2 Connection to a Personal Computer ...........................................................................11
2.4 CE Requirements...............................................................................................................12
2.4.1 EU directives that apply to the MMI-1XX Series:.........................................................12
2.4.2 General Installation Guide Lines for EU Installations..................................................12
2.4.3 General Safety Guide Lines for EU Installations.........................................................13
3.0 MMI Operations......................................................................................................................14
3.1 The Message Queue..........................................................................................................14
3.1.1 Queue Activation Messages are stored in the Queue when:......................................14
3.1.2 Queue Action...............................................................................................................14
3.1.3 The Interrupt Message.................................................................................................14
3.2 Alarm Messages.................................................................................................................15
3.3 Using the Function Keys ....................................................................................................16
3.3.1 The Function key may have message text assigned to it or may be chained to a message.
..............................................................................................................................................16
3.3.2 No message text is assigned to the Function key and no messages are chained to or from
the Function key....................................................................................................................16
3.4 Entering Numerical Values.................................................................................................17
3.5 Using the Up and Down Arrow keys (MMI-110 &140 Only)...............................................18
3.6 MMI Response ...................................................................................................................18
3.6.1 Response Time to Message Calls...............................................................................18
3.6.2 Response Time to Function Key Presses ...................................................................18
3.6.3 Response Time to Serial Port Transmissions .............................................................18

2
4.0 Trouble Shooting....................................................................................................................19
4.1 Power Problems.................................................................................................................19
4.2 Communications Problems ................................................................................................19
4.3 Commonly Asked Questions..............................................................................................20
4.4 Repair and Return Policies.................................................................................................21
Insert Planning Worksheet .......................................................................................................23
Message Planning Worksheet..................................................................................................24
Alarm Planning Worksheet.......................................................................................................25
About this Manual
This document is based on information available at the time of its publication. While efforts have been
made to be accurate, the information in this document may not cover all details or variations in
hardware or software, nor does it provide for every possibility in connection with installation,
operation, or maintenance. Features may be described herein which are not present in all hardware.
Kessler Ellis Products assumes no obligation of notice to holders of this document with respect to
changes subsequently made. Information in this document is subject to change without notice and
does not represent a commitment on the part of Kessler Ellis Products.
Some common terms used
MTR:This stands for Message Triggering Register. The MTR is the register that holds the
message number for the MMI to display.
PLC: Programmable Logic Controller. Typically, the MMI is connected to one of these devices.
This is a generic term covering a large range of programmable devices used in machine control
applications.
Symbology
Warning! Indicates that the reader should pay special attention to the accompanying text.
Precautionary steps should be taken to insure that the installation is in compliance with warnings.
Warnings include hazardous conditions that could cause personal injury or equipment damage if care
is not taken.

3
1.0 Getting Started
1.1 What is the MMI 1XX Series?
MMI 1XX Series The MMI Series are small interfaces for PLCs. They display messages
that are preloaded into them with a Personal Computer. They have 8
legendable keys, which can be programmed to perform various functions.
Equipment Checklist An MMI system should include:
An MMI-1XX Series base unit
An interface cable to the programmable controller
A personal computer with MMI programming software.
A PC to MMI cable is required.
Designed For Use Provides a convenient way for a machine operator to:
•View machine status and parameters.
•Change machine status or applicable operating parameters of the
machine.
•Maintain the running of the machine.
It also gives enhanced capabilities to the machine through:
•RS232 ASCII output.
•Direct keypad interface
•Visually displayed prompts.
1.1.1 The MMI Series and Its Environment
Where Used The MMI Series is designed for use in a factory environment. They are designed
to operate under the same temperature conditions as PLC's used in an industrial
environment. They may not be suitable for use in certain outdoor applications.
Please consult the factory for advised usage in outdoor applications.
NEMA
Rating The MMI-1XX Series front bezel is Nema 4 rated. When installed properly in a
NEMA 4 panel, the NEMA 4 rating of the panel will not be compromised. This
means that fluids will not enter the panel during wash downs.
Electrical
Environment The MMI Series has been tested to conform to European CE requirements. This
means that the MMI circuitry is designed to resist the effects of electrical noise.
This does not guarantee noise immunity in severe cases. Proper wire routing and
grounding will insure proper operation of the MMI.
Mechanical
Environment Avoid installing MMI units in environments where severe mechanical vibration
or shock are present.
2x20 or 4x20
DISPLAY

4
2.0 Installation Instructions
2.1 Mounting Instructions
2.1.1 Location Considerations.
Care should be taken when locating equipment behind the MMI to ensure
that AC power wiring, PLC output modules, contactors, starters and relays,
and any other source of electrical interference are located away from the
back of the unit.
Particular note should be taken to the position of variable speed drives and
switching power supplies. Their input and load cables should be screened to
a central star earth point.
2.1.2 Making a NEMA-4 Mounting.
Panel
Details The MMI can be mounted into panels with a depth of 6"(152mm). It is
recommended that the MMI be mounted on the front panel of a steel
enclosure, through a 5.43"(138mm) X 2.68"(68mm) opening. Allow a
clearance of 1"(25mm) on each side of the unit for mounting hardware.
Allow clearance for cable connections to the back of the unit. Unit depth
may vary according to cable type used. Typically, plan a depth to
accommodate at least 5"(130mm) behind the panel.

5
Standard
Mounting Put the MMI through the panel cut out. Slide the Clamping frame over the
case until the clips snap into the retaining slots. Tighten the clamping screws
in an even pattern until the MMI is secured in the panel.
NEMA-4
Mounting Slide the Bezel frame over the case. Slide the gasket over the case so that it
rests behind the Bezel Frame. Continue with standard mounting as described
above.
Specifications Note: To seal to NEMA-4 specifications, supplied bezel kit must be used and
panel cannot flex more than 0.010". When optional bezel kit is used, the bezel
must be sealed to the case using an RTV type sealer to maintain NEMA-4
rating. When optional bezel kit with gasket is used, the maximum panel
thickness allowed is 0.375". Without bezel kit, maximum panel thickness is
0.400". Without bezel kit or gasket, maximum panel thickness is 0.500".
Clamping Frame
Panel Gasket
Bezel Frame
2.1.3 Environmental Considerations
•The MMI is to be used indoors as a built in display. Make sure that the
display is installed correctly and that the operating limits are followed (See
Specifications).
•The MMI should not be installed where fast temperature variations and/or
high humidity are present. This will cause condensation of water in the
device.
•Do not operate the MMI in areas subject to explosion hazards due to
flammable gases, vapors or dusts.

6
2.2 Power Connections
Make sure that all local and national electrical standards are met when the installing the MMI.
Contact your local authorities to determine which codes apply.
2.2.1 Power Requirements
Power The MMI can be powered by DC power only. The specified voltage
range is +12 to 27 Volts DC. This insures compatibility with most DC
systems. The power conditioning circuitry inside the unit is accom-
plished by a switching power supply. Due to the nature of switching
power supplies, a wide range of over and under voltages may be used
without adversely affecting the unit.
Fusing
Requirements It is recommended that all input power lines be protected from
incorrect wiring or product failure by a 400 mA fuse or a breaker. If the
display does not come on within 2 seconds of power up, remove
power. An internal diode will prevent damage if the polarity of the DC
power is incorrect. Check wiring to insure proper connections and try
to power up again.
Caution
Strain Relief Adequate strain relief must be provided for the power connector, to
ensure that vibration or the disturbance of cables during maintenance
does not cause the connector to pullout. Retention of the power cables
by a tye-wrap onto the trunking, or an adhesive pad mounted tye-wrap
point is normally suitable.
Caution
High Voltage Connecting high voltages or AC power mains to the DC input will
make the MMI unusable and may create an electrical shock hazard to
personnel. Such a failure or shock could result in serious personal
injury, loss of life and or equipment damage.
DC voltage sources should provide proper isolation from main AC
power and similar hazards.
Caution
Emergency Stop A Hard wired EMERGENCY STOP should be fitted in any system
using the MMI to comply with ICS Safety Recommendations.
Caution Supply
Voltage Condition Do not power the MMI and inductive DC loads, or input circuitry to the
PLC with the same power supply. The 24 VDC output from some
PLC's may not have enough current to power the MMI.

7
Caution Power
Cycling Power supplies with large capacitive outputs may cause problems if
power is cycled within a short time period. The power supply’s
capacitor will supply enough current to keep the microprocessor
running for a few minutes but not enough to keep the display active. If
full power is restored during that time the microprocessor may not
initialize the display module. The result is that the display will remain
blank or show just the cursor in the upper left-hand corner and the rest
of the unit will be fully functional.
To remedy this problem run power to the unit through a “seal in”
circuit or remove the capacitor (the MMI does not mind if power is
unregulated) or wait sufficient time between power cycles.
Caution Wire
Routing Wire lengths should be minimized (Maximum 1600' (500 m)
shielded, 1000' (300 m) unshielded).
Wires should be run in pairs with a neutral or common paired with a
hot or signal line.
If wiring is to be exposed to lightning or surges, use appropriate
surge suppression devices.
Keep AC, high energy, and rapidly switching DC wiring
separate from signal wires.
Equip ungrounded DC supplies with a resistor and capacitor in parallel
to earth ground. This provides a path for static and high frequency
dissipation. Typical values to use are 1MOhm and 4700pF.
Connection
To make a connection, strip about 1/4" of insulation off the end of the wire, turn the connector
screw counterclockwise until the gap is wide open, insert the wire all the way in, and turn the screw
clockwise until it’s tight.
Connect positive DC line to terminal 1 and the DC ground to terminal 2.

8
2.2.2 Grounding Requirements
Chassis ground must be used. DC ground (Terminal 2) is not directly
coupled to Earth ground internally. It is preferable not to ground DC
negative return to chassis ground, pin 3, as poor site earths can
introduce noise into a system, but if necessary an earth connection
should be made, from the power supply return point to the central star
earth point.
Ground conductors should be as short and as large in size as possible.
The conductors must always be large enough to carry the maximum
short circuit current of the path being considered. Ground conductors
should be connected from a tree from a central star earth ground point.
This ensures that no ground conductor carries current from any other
branch.
Typical Label on Rear of MMI-1XX Series unit.
+12 to 27 VDC Wiring Diagram
View from top of connector
3 Earth Ground
2 - DC Ground
1 + 12 to 27 VDC
2.2.3 CE Requirements
To make the MMI comply with EMC directives, and to reduce susceptibility to electrical interference, a
separate #14 AWG ground wire should be taken to terminal 3 of the power connector. This
ground connection should be run directly to the central star earth connection point (as
recommended in most PLC Installation Instructions).

9
2.2.4 Safety Guidelines
This section presents recommended installation practices, and procedures. Since no two applications
are identical, these recommendations should be considered as guidelines.
Hardware
Considerations WARNING!
The system designer should be aware that control devices in
Programmable Controller systems can fail and thereby create an
unsafe condition. Furthermore, electrical interference in an operator
interface, such as the MMI, can lead to equipment start-up, which
could result in property damage and/or physical injury to the
equipment operator.
If you, or your company, use any programmable control systems,
which require an operator or attendant, you should be aware that this
potential safety hazard exists and take appropriate precautions.
Although the specific design steps depend on your particular
application, the following precautions generally apply to installation of
solid-state programmable control devices. In addition, these
precautions conform to the guidelines for installation of Programmable
Controllers as recommended in the NEMA ICS 3-304 Programmable
Control Standards.
Programming
Considerations To conform with ICS Safety Recommendations, checks should be
placed in the PLC program to ensure that all writable registers that
control critical parts of plant or machinery should have upper and
lower limit checks built into the program, with an out-of-limit safe shut
down procedure to ensure safety of personnel.
ICS 3-304.81 Safety Recommendations: Consideration should be given to the use
of an emergency stop function which is independent of the programmable controller.
Where the operator is exposed to the machinery, such as in loading or unloading a machine tool, or where
the machine cycles automatically, consideration should be given to the use of an electromechanical override
or other redundant means, independent of the programmable controller, for starting and interrupting the cycle.
If provision is required for changing programs while the equipment is in operation, consideration should
be given to the use of locks or other means of assuring that such changes can be made only by authorized
personnel.
These recommendations are intended as safeguards against the failure of critical components and the
effects of such failures or the inadvertent errors that might be introduced if programs are changed while the
equipment is in operation.*
* The ICS 3-304.81 Safety Recommendations are reproduced by permission of the National Electrical
Manufacturers Association from NEMA ICS 3-304, Programmable Controller Standard.

10
2.3 Communications Connections
2.3.1 Connection to an External Device
The DB9 port farthest from the power connector, as you look at the back of the case, is the port for
connecting to a PLC or external device (Controller Connector).
Cable
Requirements Different cables are required for various devices. The KEP part numbers
have the SMIC prefix. Refer to a KEP catalog or datasheet for a complete
listing of MMI-1XX compatible devices.
These cables can be obtained from the same distributor where you
purchased the MMI-1XX.
Caution Restrict cable length to less than 500' (150m) for RS485/422 devices and 50'
(15m) for RS232 devices to avoid communications problems.
Communications problems cause the MMI display to hold until
communications can be established.
Shielded cable must be used for long lengths or cables run in
an electrically noisy environment.
Do not run cables next to AC power lines or near sources of
electrical noise.
Be sure that the cable ends have been inserted all of the way
into mating connectors and are secure.
Pin Designations Pin assignment of the 9 pole SUB-D RS232 to external device port
Pin# Symbol Function
1 Shield Earth Ground
2 TxD Transmitted Data
3 RxD Received Data
4 Not used
5 GND Signal Ground
6 Vcc DO NOT GROUND THIS PIN
7 Not used
8 CTRL Flow Control Line for RS485
9 RSV DO NOT USE Reserved for MMI use

11
2.3.2 Connection to a Personal Computer
The 9 Pin Female connector closest to the power connector on the back of the unit is the
programming port (PC Connector).
Connection This port can be attached to a Computer via a DB9 Male to DB9 Female straight
through cable. Make sure 2 and 3 are not reversed.
Port Activation This port is activated by disconnecting the MMI from the SMIC cable.
The Programmer Port and the MMI cannot be on line to the PLC at the same
time. The MMI does not have networking capabilities.
Print Out The MMI has print out capabilities. When a message is assigned to be sent out
the serial port, the transmit line of the computer port becomes active
momentarily.
Note: The receive line is never active when the MMI is connected to a PLC.
Pin Designations The MMI has print out capabilities. When a message is assigned to be sent out
the serial port, the transmit line of the computer port becomes active
momentarily.
Note: The receive line is never active when the MMI is connected to a PLC.
Pin assignment of the 9 pole SUB-D RS232 to Computer port
Pin# Symbol Function
1 Not used
2 TxD Transmitted Data
3 RxD Received Data
4 Not used
5 GND Signal Ground
6 Not used
7 Not used
8 Not used
9 Not used

12
2.4 CE Requirements
2.4.1 EU directives that apply to the MMI-1XX Series:
•EMC Directive (89/336/EEC, 92/31/EEC, 93/68/EEC) electromagnetic emissions and immunity
•Low Voltage Directive (73/23/EEC, 93/68/EEC) electrical safety
•Machinery Directive (89/392/EEC, 91/368/EEC, 93/44/EEC, 93/ 68/EEC) machine safety
MMI products will be CE-marked to indicate compliance with the EMC Directive. Declarations of
Conformity that specify the directive(s) and the catalog numbers of the products covered are available
from Kessler Ellis Products.
The MMI has been designed to operate satisfactorily in electromagnetic noise (immunity) and without
emitting high levels of electrical noise into the environment (emission). The MMI was designed to
meet European Community standards when installed per the wiring instructions in this manual.
Compatibility
Standards The MMI has been designed to meet electromagnetic compatibility for
industrial environments.
•CISPR (EN 55011) Group 1, Class A Radiated Emissions levels
•EN50081-2 Generic emission standard, industrial environment
(Also US FCC Class A)
•EN50082-2 Generic immunity standard, industrial environment
2.4.2 General Installation Guide Lines for EU Installations.
•Be aware that wiring leaving the cabinet where the MMI is installed may be exposed to
interference sources.
•The installation practices in the individual product installation manuals of other components in the
system must also be followed.
•Locally applicable grounding safety regulations and machinery directives should be followed for
providing a protective ground to earth. The EMC ground must be a low impedance, low
inductance path to the machine chassis ground.
•The MMI power supply must be through an IEC-rated isolation transformer.
•The Power supply to the PLC must be controlled to ensure that it does not exceed overvoltage
category II per EN60204-1 (IEC 240).
•Other requirements of the Machinery Directive involving displays, languages, instructions,
Emergency Stop functions, machine operation, protective guards and interlocks are the
responsibility of the machine manufacturer.

13
2.4.3 General Safety Guide Lines for EU Installations.
•Only qualified personnel should be allowed to specify, apply, install, operate, maintain or perform
any other function related to MMI products. Qualified persons are defined as follows: System
application and design engineers who are familiar with the safety concepts of automation
equipment. Installation, start-up, and service personnel who are trained to install and maintain
automation equipment. Operating personnel trained to operate automation equipment and trained
on the specific safety issues and requirements of the particular equipment.
•Before switching on the equipment, make sure that the voltage range for the equipment is correct.
•Emergency tripping devices in accordance with EN60204/IEC204 must be effective in all
operating modes of the automation equipment. Resetting the emergency off device must not
result in any uncontrolled or undefined restart of the equipment.
•Automation equipment and its operating elements must be installed so that unintentional
operation is prevented.
•Make sure that operating sequences interrupted by a voltage dip or power supply failure resume
proper operation when the power supply is restored. If necessary, the equipment must be forced
into the “emergency off” state.
•Install the power supply and signal cables so that inductive and capacitive interference voltages
do not affect automation functions.

14
3.0 MMI Operations
Once the MMI is programmed and connected to the PLC, normal operation begins. The MMI
establishes communications with the PLC. It then requests the number in the Message Triggering
Register (MTR) and displays the corresponding message.
3.1 The Message Queue
Occasionally messages are called up faster than they can be displayed. When this happens
messages are held in a Queue and wait their turn to be displayed. The message Queue holds up to 5
message numbers.
3.1.1 Queue Activation Messages are stored in the Queue when:
1 A series of Chained messages are being displayed.
2 A message with a long minimum display time is displayed.
3 A message with a long scrolling time is displayed.
3.1.2 Queue Action
The Queue is emptied on a first in first out basis. If the Queue is full, additional messages will be lost.
Warning Function keys that have displayable message text assigned to them clear
the Queue.
3.1.3 The Interrupt Message
Message number 255 is the Interrupt message. When message 255 is called the Queue is
immediately cleared. The next message number that appears in the message triggering register is
then displayed.
An example of Queue operations:
Message 62 is being displayed with a minimum time of 10 seconds.
Display Queue
23 —
During that period message numbers 34, 15 and then 211 are called for by the MTR.
Display Queue
23 34
15
211
The MMI will put message 34, 15 and 211 in the Queue. When message 23 has timed out, message
34 will be called up and displayed.

15
Display Queue
34 15
211
When 34 is done, message 15 will be
displayed.
Display Queue
15 211
When 15 is done, message 211 will be
displayed.
Display Queue
211 EMPTY
Message 211 will continue to be displayed until a new message number is put
in the MTR
3.2 Alarm Messages
You can define up to 32 alarms. These can be defined either by 2 Words (16 bits) or 32 distinct bits.
Alarms can take up to 304 bytes of memory. Alarms have a hierarchical structure and are triggered
by bit ON status only.
Note: The host PLC has the entire responsibility for performing all acknowledges and clear functions.
It is suggested that the function keys on the MMI and their existing functions be used for these
purposes in conjunction with the PLC program.
If Alarms are defined wordwise, the unit reads the designated (2) alarm registers. The registers bits
are then parsed from 0 to 15 (Register 1) then 0 to 15 (Register 2). If Alarms are defined bitwise, MMI
reads the bits as a cluster or individually in order as specified by a list of designated bits. The first
logical 1 bit encountered is processed as an alarm. Its associated message is displayed and acted
upon. Further parsing action is inhibited until the alarm is cleared or an alarm of higher priority is
encountered in subsequent reads.
Note: If a bit is not assigned a message number then activating the bit suppresses all alarms after
that bit.
Alarms interrupt MTR operations. MTR operations resume when all alarms are cleared or inhibited.

16
Description of alarm operation
Triggering a message
Bit 1 of alarm register one is assigned message #34, which reads This is a test
message.
Bit 5 of alarm register one is assigned message #35, which reads The phone is
ringing.
Bit 2 of alarm register two is assigned message #36, which reads An alarm
message.
Bit 2 of register two goes to the ON state. The display shows message 36:
AN ALARM MESSAGE.
Then bit 1 of alarm register one goes to the ON state. The display shows message
34:
THIS IS A TEST MESSAGE.
Finally, bit 5 of alarm register one changes to the ON state. The display shows message 34:
THIS IS A TEST MESSAGE.
Note how the first alarm encountered inhibits the message from bits 5 of reg. 1 and 2 of reg. 2 from
being displayed. Actually, they are never processed.
Bit 0 of register one goes to the ON state. Since no message is assigned to that bit the display shows
the message that is in the Message Triggering Register or the default message.
3.3 Using the Function Keys
The MMI-100, 110 and 140 models have programmable function keys. Simply press a Function key
to initiate their programmed action and/or call up their associated messages. One of the following
conditions will apply.
3.3.1 The Function key may have message text assigned to it or may be chained to
a message.
The Function key message will interrupt the active display.
Note: Function keys with message text assigned to them clear the message
Queue and interrupt minimum display times, chained and scrolling messages.
The message assigned to the Function key will be displayed.
At the end of a Function call and after all message chaining is done, the display does one of the 3
options listed in priority below.
1 Chains, if programmed, to the next message.
2 Displays the message whose number is next in the message Queue.
3 Displays the message whose number is in the MTR.
3.3.2 No message text is assigned to the Function key and no messages are
chained to or from the Function key.
Press the Function key. The Queue is not cleared and the display is not be interrupted but the
function is carried out.

17
3.3.3 No message is assigned to the Function key.
When the Function key is pressed, nothing happens.
3.4 Entering Numerical Values
MMI-110
MMI-140 The MMI-110 & 140 may have data or bit status embedded in messages for
the purpose of editing. Such data is usually machine status, setpoints and
other setup parameters that may need to be changed from time to time.
Such values flash when they are displayed. The operator may change
these values by the following procedure:
•Press the CLR DATA key. The function keys will now act as numerical
entry keys.
•Key in the new data value or use the 1 and 0 keys to change status.
•Press the ENT key. Only after the ENT key is pressed will the new
value will be written to the PLC.
•To escape from entering a value, wait ten seconds. The MMI will time
out and display the value that is in the register in the PLC.
MMI-100 The MMI-100 has no direct facility to allow the operator to enter
operational parameters outside of limited function key capabilities.
Numerical entry can still be achieved using some Controller Logic and the
function keys. This technique will use 5 or 6 MMI-100 function keys.
•Designate a register in the PLC as the working register. This register
will be modified by Controller Logic prompted by function key actions.
•Define 4 of the function keys to turn bits on momentarily. Use the
function key’s bits to trigger one shots that add 1, 10, 100 or 1000 to
the working register. You may want to designate another function key to
clear the working register.
•Define a momentary function key to act as the Enter key. When this key
is pressed the Controller Logic should move the working register to its
intended destination.
•Label the function keys appropriately.

18
3.5 Using the Up and Down Arrow keys (MMI-110 &140 Only)
The Up and Down Arrow keys on the MMI-110 & 140 are used to step up
or down through a preprogrammed list of messages. The list may be
called up by the PLC or by pressing a Function key. The message will stay
on the display until a new message is called by the MTR, Function Key
press or one of the arrow keys is pressed. When the top of the list is
reached the up arrow is ignored. When the bottom of the list is reached the
next message called by the down arrow will be the top of the list.
3.6 MMI Response
The MMI is limited in its response to key presses and information update by the serial
communications to the PLC. The MMI has been optimized to provide reasonable response times to
events.
3.6.1 Response Time to Message Calls
A message number must be in the MTR for at least 300 milliseconds to be recognized by the MMI.
3.6.2 Response Time to Function Key Presses
Function keys are handled on an interrupt basis. As soon as a key is pressed a communication is
sent to the PLC. Response to a key press by the PLC depends on the PLC’s scan time and
communications handling. Typically, response times are less than 1 second. We do not recommend
using the function keys for JOGGING applications.
3.6.3 Response Time to Serial Port Transmissions
When a called message has the attribute to be sent to the serial port, the MMI-1XX will send the
message to the port before displaying it. Response time is determined by the number of registers/bits
embedded in the message. The serial port baudrate also determines how long it will be before the
message is displayed. A 200 character scrolling message with several embedded registers and bits
sent out at 300 baud may take up to 10 seconds to appear on the display.
This manual suits for next models
5
Table of contents
Popular Network Hardware manuals by other brands
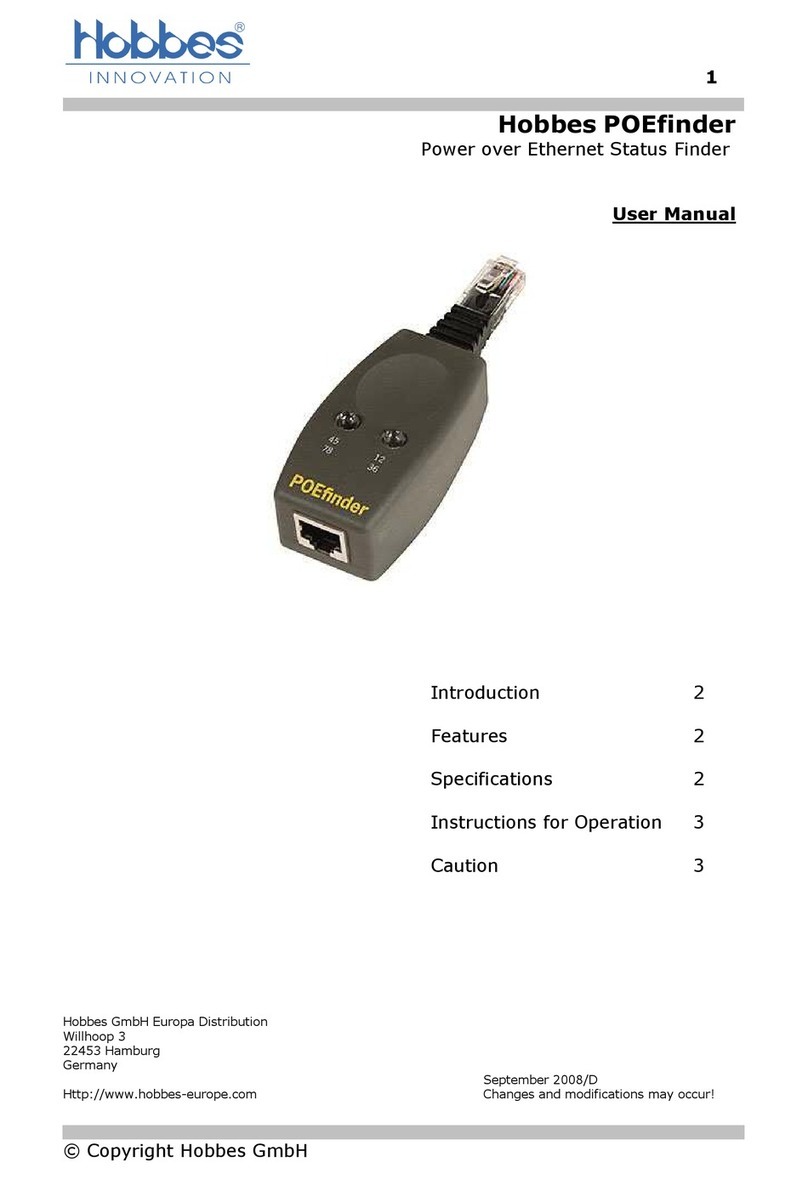
Hobbes
Hobbes POEfinder user manual
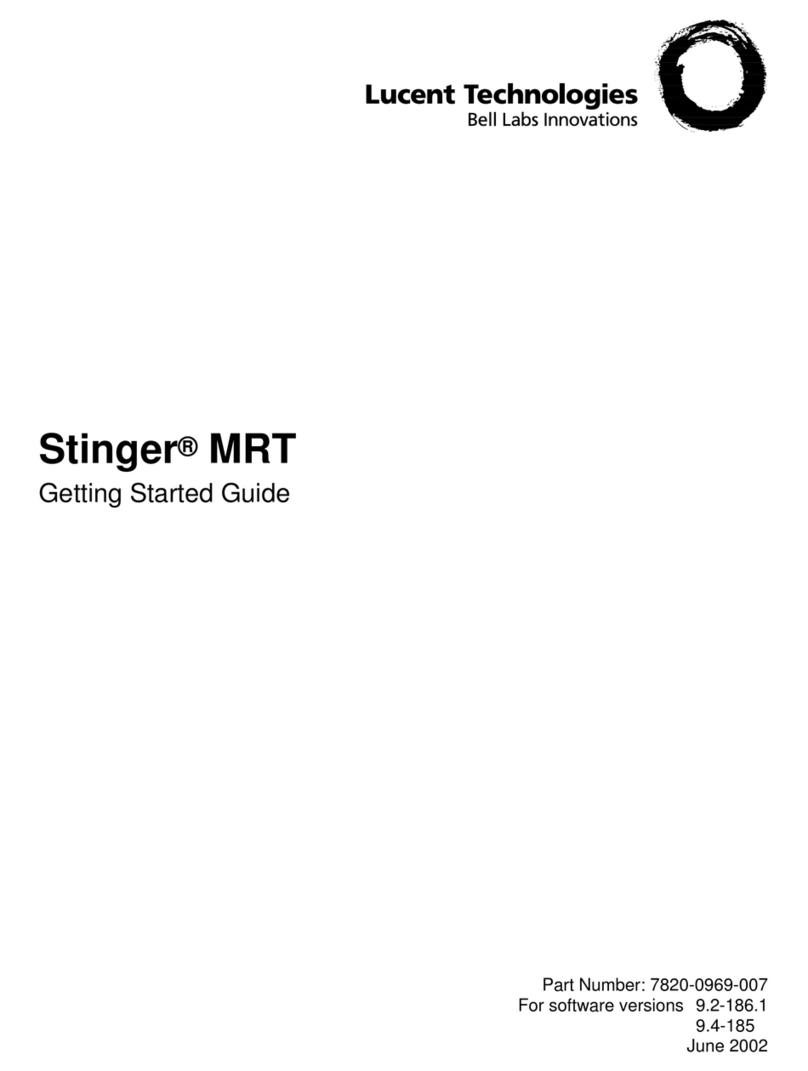
Lucent Technologies
Lucent Technologies Stinger MRT Getting started guide
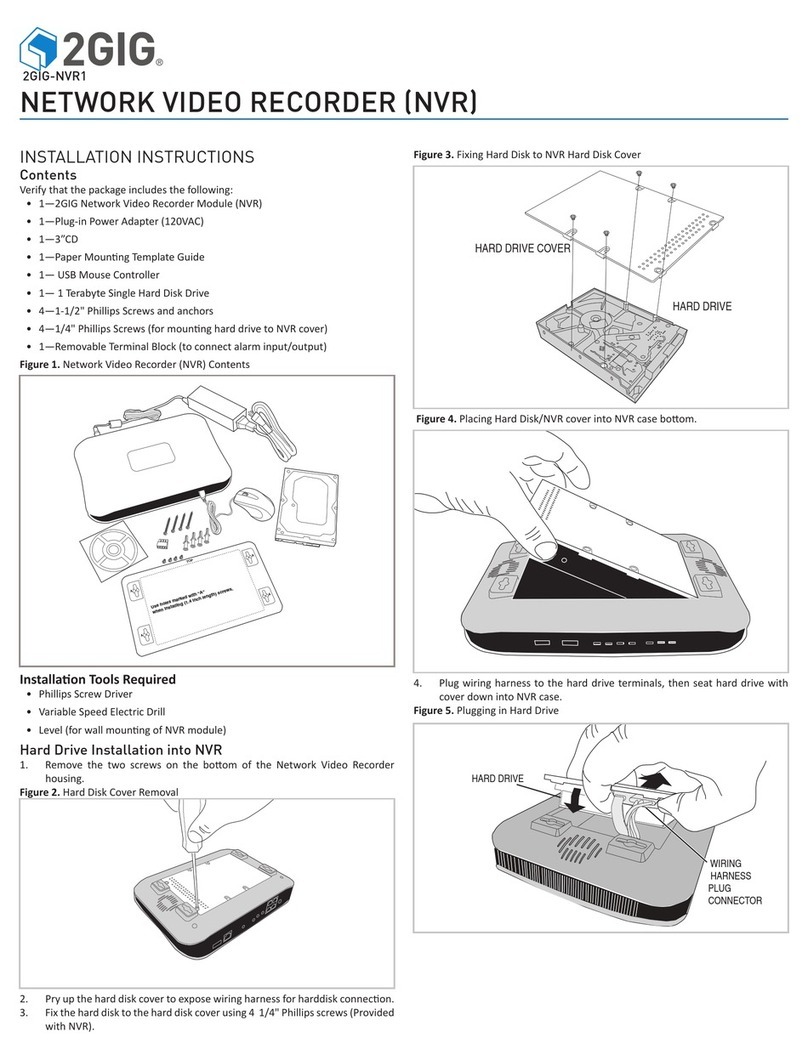
2gig Technologies
2gig Technologies 2GIG-NVR1 installation instructions
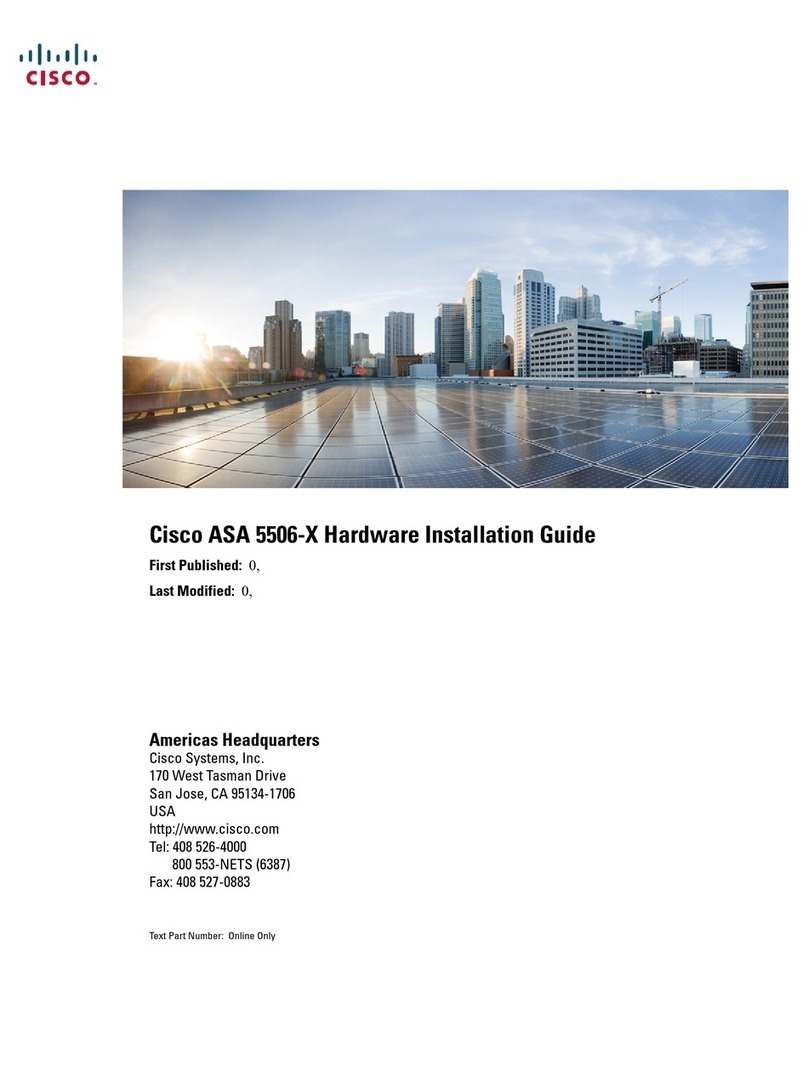
Cisco
Cisco ASA 5506-X Hardware installation guide
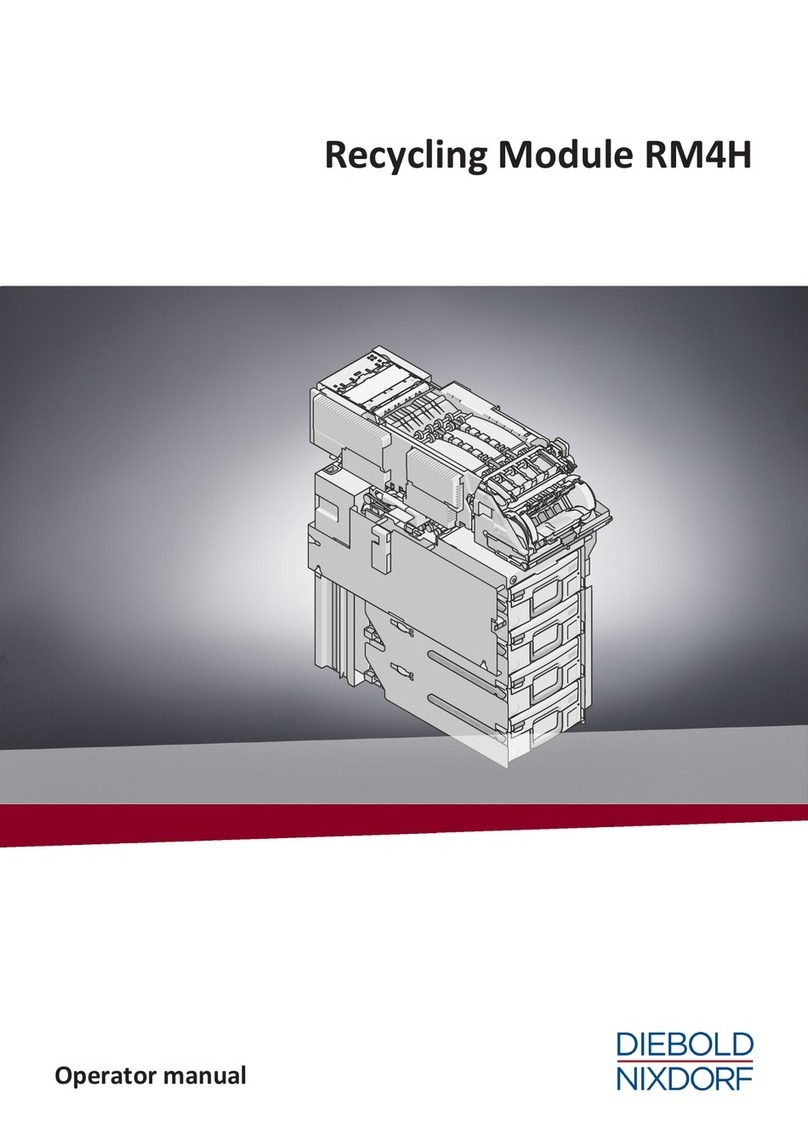
DIEBOLD NIXDORF
DIEBOLD NIXDORF RM4H Operator's manual
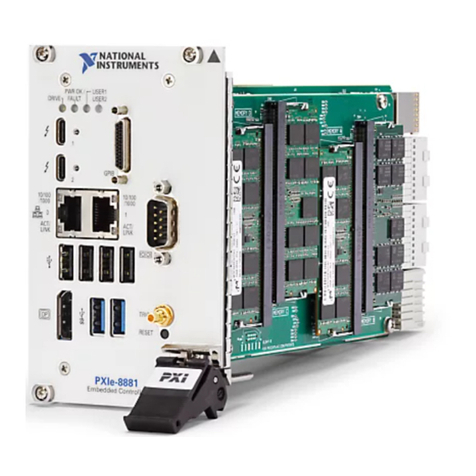
NI
NI PXIe-8881 user manual