Kerotest WELDBALL User manual

KEROTEST WELDBALL BALL VALVE
INSTALLATION, OPERATION, AND
MAINTENANCE MANUAL
NO.:
K-1484
REV.:
A
DATE:
03MAR2022
PAGE:
1 OF 17
KEROTEST WELDBALL®BALL VALVE
INSTALLATION, OPERATION, AND MAINTENANCE MANUAL
Table of Contents
1INTRODUCTION .......................................................................................................................................................................................................3
1.1 SCOPE...................................................................................................................................................................................................................3
1.2 REFERENCES .........................................................................................................................................................................................................3
2ENVIRONMENTAL, HEALTH, AND SAFETY...........................................................................................................................................................3
2.1 WARNINGS AND SYMBOLS.......................................................................................................................................................................................3
2.2 RISKS....................................................................................................................................................................................................................3
3PRODUCT DESCRIPTION AND FEATURES............................................................................................................................................................3
4IDENTIFICATION AND MARKINGS..........................................................................................................................................................................4
4.1 CAUTION TAG.........................................................................................................................................................................................................4
4.2 VALVE I.D. TAG (SAMPLE).......................................................................................................................................................................................4
5FACTORY AND FIELD APPLIED COATINGS..........................................................................................................................................................5
6UNLOADING AND STORAGE..................................................................................................................................................................................5
7VALVE INSTALLATION............................................................................................................................................................................................6
7.1 GENERAL CONSIDERATIONS FOR VALVE INSTALLATION..............................................................................................................................................6
7.2 INSTALLATION OF VALVE WITH WELDED CONNECTIONS .............................................................................................................................................6
7.3 INSTALLATION OF VALVE WITH FLANGES...................................................................................................................................................................7
7.4 INSTALLATION OF VALVE WITH SCREWED ENDS ........................................................................................................................................................8
7.5 INSTALLATION AT THE END OF PIPELINE....................................................................................................................................................................8
7.6 PRESSURE TESTING ...............................................................................................................................................................................................9
8OPERATION..............................................................................................................................................................................................................9
8.1 GENERAL VALVE OPERATION ..................................................................................................................................................................................9
8.2 OPERATING TORQUE AND CRITICAL TORQUE............................................................................................................................................................9
9TROUBLESHOOTING.............................................................................................................................................................................................10
9.1 VALVE SHUT-OFF.................................................................................................................................................................................................10
9.2 VALVE PACKING LEAKAGE.....................................................................................................................................................................................10
10 MAINTENANCE ......................................................................................................................................................................................................10
10.1 RECOMMENDED PERIODIC PREVENTATIVE MAINTENANCE........................................................................................................................................10
10.2 GEAR OPERATOR REMOVAL..................................................................................................................................................................................10
10.3 GEAR OPERATOR REINSTALLATION........................................................................................................................................................................11
10.4 GEAR OPERATOR ADJUSTMENT.............................................................................................................................................................................11

KEROTEST WELDBALL BALL VALVE
INSTALLATION, OPERATION, AND
MAINTENANCE MANUAL
NO.:
K-1484
REV.:
A
DATE:
03MAR2022
PAGE:
2 OF 17
10.5 STEM SEAL O-RING REPLACEMENT ......................................................................................................................................................................12
10.6 REPLACING OPERATING SQUARE WITH GEAR OPERATOR ON NPS 6FP /8RP VALVES ............................................................................................13
11 COMPONENTS .......................................................................................................................................................................................................14
12 PHYSICAL SPECIFICATIONS................................................................................................................................................................................15
13 FACTORY TESTING...............................................................................................................................................................................................16
14 DOCUMENT REVISION HISTORY:.........................................................................................................................................................................17
Table of Tables
Table 1 Operating and Critical Torque by Valve Size.......................................................................................................................................................9
Table 2 Stem Seal Repair Kits..........................................................................................................................................................................................12
Table 3 Valve Dimensions, Weight, and Cv.....................................................................................................................................................................15
Table 4 Minimum Test Pressure and Durations..............................................................................................................................................................16
Table of Figures
Figure 1 P-T Chart ..............................................................................................................................................................................................................4
Figure 2 Caution Tag..........................................................................................................................................................................................................4
Figure 3 Valve I.D. Tag .......................................................................................................................................................................................................4
Figure 4 Lifting the Valve...................................................................................................................................................................................................5
Figure 5 Horizontal Installation..........................................................................................................................................................................................6
Figure 6 Vertical Installation..............................................................................................................................................................................................6
Figure 7 Welding in Vertical Position................................................................................................................................................................................7
Figure 8 Welding in Vertical Position................................................................................................................................................................................7
Figure 9 Welding in Horizontal Position............................................................................................................................................................................7
Figure 10 Bolt Torquing Pattern Examples.......................................................................................................................................................................8
Figure 11 Do Not Use at the End of a Pipeline..................................................................................................................................................................8
Figure 12 End of Pipeline Pup and Cap.............................................................................................................................................................................8
Figure 13 Manual Gear Adjustment.................................................................................................................................................................................11
Figure 14 Stem Seal..........................................................................................................................................................................................................12
Figure 15 Operating Square Components ......................................................................................................................................................................13
Figure 16 Weldball Components .....................................................................................................................................................................................14

KEROTEST WELDBALL BALL VALVE
INSTALLATION, OPERATION, AND
MAINTENANCE MANUAL
NO.:
K-1484
REV.:
A
DATE:
03MAR2022
PAGE:
3 OF 17
1 INTRODUCTION
1.1 Scope
This manual defines for gas utility customers the procedures for handling, storage, operation, and common
repairs on the Weldball®line of steel ball valves used in gas distribution or pipeline applications manufactured by
Vexve.
1.2 References
•API Std 1104 Welding of Pipelines and Related Facilities
•ASME Boiler and Pressure Vessel Code
•ASME B1.20.1 Pipe Threads, General Purpose, Inch
•ASME B16.5 Pipe Flanges and Flanged Fittings: NPS ½ through NPS 24, Metric/Inch Standard
•ASME B16.10 Face-to-Face and End-to-End Dimensions of Valves
•ASME B16.34 Valves Flanged, Threaded, and Welding End
•ASME PCC-1 Guidelines for Pressure Boundary Bolted Flange Joint Assembly
2 ENVIRONMENTAL, HEALTH, AND SAFETY
2.1 Warnings and Symbols
Within this document, you will see the following symbols:
General Advisory Marking - for information or operational procedures, order of operation, etc.
Caution Marking –note designates an action or step that may result in personal injury or
death or equipment/property damage. Personnel performing activities should be fully aware of
the hazards and take necessary steps to prevent any injuries, damage, or unsafe operating/repair
condition.
2.2 Risks
NOTE: Failure to follow the instructions in this manual when installing, operating, and/or
performing maintenance on the valve could lead to loss of life and/or damage to the environment.
3 PRODUCT DESCRIPTION AND FEATURES
Weldball ball valves are welded steel valves used in natural/fuel gas distribution pipelines and are available in
NPS 3/4 through NPS 12, Full Port (FP) / Reduced Port (RP), and in ASME/ANSI Pressure Classes 150 and
300, and 500 CWP.
The valve end connections are welded, flanged (raised and flat face), weld-by-flange, and some threaded
configurations. Other configurations or options are available upon request.
The intent of this manual is to acquaint our customers with installation, operation, and maintenance/service
repair techniques for Weldball ball valves.

KEROTEST WELDBALL BALL VALVE
INSTALLATION, OPERATION, AND
MAINTENANCE MANUAL
NO.:
K-1484
REV.:
A
DATE:
03MAR2022
PAGE:
4 OF 17
Below are some of the features of the Kerotest Weldball steel ball valves:
•Low maintenance
•No gland tightening
•No lubrication required
•Polished 304 stainless steel ball
•Sealed-for-life welded steel construction
•Double O-ring stem seal
•Weather sealed operating square
•Lightweight
•Low operating torque
•Bidirectional installation and operation
•Ultra-Stop* feature for excessive limit torques
•Locking mechanism available on NPS 6 RP and smaller
•Gear Operator option for NPS 6 FP and larger
*The Kerotest Ultra-Stop feature is a heavy duty operating square limit stop designed to accommodate applied
excessive torque during field operation. It can be identified by a notched plate welded to the valve neck and a
pin on the operating square within the notch or as an integral collar and pin. This feature is available on sizes
NPS 3/4 through NPS 8 RP.
4 IDENTIFICATION AND MARKINGS
4.1 Caution Tag
Caution tags are attached to valves with a butt weld end.
4.2 Valve I.D. Tag (Sample)
I.D. tags are attached to valve body. Each valve will have an
identification label attached with the following information:
•Manufacturing company
•Valve Size (NPS)
•ASME/ANSI Pressure Class
•Pressure/Temperature Ratings
•Body and Stem Materials
•Valve Length
•Serial Number
•Date of Manufacture
Figure 1 P-T Chart
Figure 2 Caution Tag
Figure 3 Valve I.D. Tag

KEROTEST WELDBALL BALL VALVE
INSTALLATION, OPERATION, AND
MAINTENANCE MANUAL
NO.:
K-1484
REV.:
A
DATE:
03MAR2022
PAGE:
5 OF 17
5 FACTORY AND FIELD APPLIED COATINGS
The standard factory coating supplied on Weldball is a gray epoxy powder coat not suitable for outdoor or buried
service. It is recommended the customer apply an appropriate coating to the entire valve exterior.
Additionally, the valve may be ordered from the factory with a two-component, high solids epoxy coating rated
for outdoor or buried service.
If a valve appears corroded prior to installation, particularly on the internal components, contact Kerotest to
determine if the valve can be installed.
Fusion Bonded Epoxy (FBE) and/or coatings that require applied heat should not be used. These restrictions
also apply to supplied gear operators. Coatings should be applied per the coating manufacturer's requirements
and specifications for preparation and environmental conditions.
6 UNLOADING AND STORAGE
General Considerations for Unloading and Storage
•Check that the contents of the delivery are as ordered. Check that the valve and related equipment have not
been damaged during transportation.
•Store the valve carefully before installation, preferably in a well-ventilated, dry place, on a shelf or a wooden
grid to protect it from moisture.
•The valve must be transported to the installation site in a sturdy package. Do not remove the flow port or
flange protectors before installation. Protect the valve from sand, dust, and other impurities.
•Use lifting ropes when lifting the large size valves. Do not lift the valve by its operating square or stem (see
Figure 4). Valves are top-heavy and can shift or rotate in the sling.
•The valve is shipped in the open position and should remain open while in storage
•When stored in the original packaging in a well ventilated, clean, dry environment the shelf life is unlimited.
NOTE: Take the weight of the valve into account when handling it.
Figure 4 Lifting the Valve

KEROTEST WELDBALL BALL VALVE
INSTALLATION, OPERATION, AND
MAINTENANCE MANUAL
NO.:
K-1484
REV.:
A
DATE:
03MAR2022
PAGE:
6 OF 17
7 VALVE INSTALLATION
7.1 General Considerations for Valve Installation
CAUTION: Incorrect installation may result in serious personal injury and damage equipment or
facilities. These instructions must be followed carefully when installing the valve.
These general instructions do not cover all possible operating scenarios. For more specific guidance on
the use of the valve or its suitability for an intended use, please contact Kerotest.
•Do not remove the flow port protectors before installation. Keep the valve protected from sand, dust, and
other impurities.
•If the valve was delivered with a gear operator installed, avoid removing it during installation.
•Incorrect re-installation or adjustment of the gear operator can result in leakage.
•Exercise extreme caution when testing the valve before installation in the pipeline.
•The valve or valve assembly must not be lifted with the operating square or the gear operator input shaft
(See Figure 4). Dropping or incorrect lifting of the valve can result in personal injury or equipment damage.
•Use one of the allowed lifting methods shown in Figure 4.
•Prior to installation remove the flow port protectors and check that the inside of the valve is clean.
•Recommended installation position for the valve is with the input shaft facing up or in the horizontal position.
See Figure 5 and Figure 6.
CAUTION: The pipeline and valve shall be cleaned prior to installation as any welding debris or
other impurities can damage the valve.
Figure 5 Horizontal Installation
Figure 6 Vertical Installation
7.2 Installation of Valve with Welded Connections
During welding the ground must be connected to the pipe of the valve body or the pipeline.
Ground cable should be connected to the pipe on the same side as the welding seam. As current may
damage the valve seal, never connect the ground to the valve neck, operating square flange, or
operating square.

KEROTEST WELDBALL BALL VALVE
INSTALLATION, OPERATION, AND
MAINTENANCE MANUAL
NO.:
K-1484
REV.:
A
DATE:
03MAR2022
PAGE:
7 OF 17
•The welder must be qualified in accordance with relevant sections of API 1104, section IX of the ASME
Boiler and Pressure Vessel Code (ASME BPVC), or company approved and qualified welding standard.
•Recommended welding method is manual metal arc welding. Valve pipe end material is carbon steel with a
34ksi tensile strength.
•Do not overheat the valve. Use cooling during the welding such as a wet fabric to protect the valve seat from
excessive heat. Cool down the valve after welding before normal operation. After welding, the valve may not
be opened and/or closed before it has cooled down.
•The valve can first be bridged to the pipeline using spot welding, with 4–8 seams alternately on opposite
sides of the valve.
•The valve must remain open during installation and welding to ensure the seal surfaces are not damaged.
•The ends of the pipes must be parallel to the valve and correctly aligned.
•The length of the valve must be the same as the distance between the pipe ends, taking into consideration
the welding gaps.
•Diameter and wall thickness of the pipes must be compatible with welding ends of valve.
When installed in a horizontal position:
When welding the valve, it must be in the open position to protect the surface of the ball from welding
contamination (See Figure 9).
When installed in a vertical position:
When making the upper seam welding, the valve must be open to protect the surface of the ball from welding
contamination (See Figure 7). When making the lower welding seam the valve must be closed to avoid the
overheating of the valve (See Figure 8).
Figure 7 Welding in Vertical
Position
Figure 8 Welding in Vertical
Position
Figure 9 Welding in Horizontal
Position
When welding the upper seam the
valve must be in open position.
When welding the lower seam the
valve must be in closed position.
The valve must be in open position.
7.3 Installation of Valve with Flanges
•Valve may be installed only by a qualified operator.
•The valve must remain open during installation to ensure that any residue or dirt does not damage the
sealing faces.
•The sealing faces of the pipe flanges must be parallel to the valve sealing faces and correctly aligned.
•The length of the valve must be the same as the distance between the flanges in the pipeline, taking into
consideration the gasket.
•The valve flanges conform to standard ASME B16.5.

KEROTEST WELDBALL BALL VALVE
INSTALLATION, OPERATION, AND
MAINTENANCE MANUAL
NO.:
K-1484
REV.:
A
DATE:
03MAR2022
PAGE:
8 OF 17
•Bolting and gasketing practice conforming to ASME B16.5 is suggested. Bolts and gaskets used on
installation (not included with the valve) must be selected to match operating conditions, temperature,
pressure and medium. Gasket dimensions must be compatible with sealing faces of the flanges.
•Standard end flange facing is 1/16" raised face with phonographic finish. Some valves may be ordered with
a flat face finish. Contact Kerotest or your distributor for further information and availability of flat face
finished valves. Flat face finished valves are slightly shorter than standard faced valves, as allowed per
ASME B16.10.
•End flange bolts should not be fastened in consecutive order. Bolts should be tightened in a cross pattern
similar to Figure 10. Two passes should be made, one pass for half tightness and a final pass for full
tightness. ASME PCC-1 can provide guidelines for assembly of bolted flanges.
Figure 10 Bolt Torquing Pattern Examples
7.4 Installation of Valve with Screwed Ends
•Screwed End Valves are only available on valves ≤ NPS 2 with class 300 ratings.
•Valve ends have NPT pipe threads machined per ASME B1.20.1
•Apply (sparingly) a suitable threading compound to the threads on the pipe.
•Start threading by hand, use wrench to tighten. Do not cross-thread.
7.5 Installation at the End of Pipeline
NOTE: For valves located at the end of a pipeline, it is recommended to install a short pipe pup with a
pressure rated cap to the valve outlet to reduce potential corrosion issues and gas leaks caused by unintended
operation. Following installation, the pup and cap section should be pressurized to match the main pipeline.
(See Figure 11 and Figure 12)
Figure 11 Do Not Use at the End of a Pipeline
Figure 12 End of Pipeline Pup and Cap

KEROTEST WELDBALL BALL VALVE
INSTALLATION, OPERATION, AND
MAINTENANCE MANUAL
NO.:
K-1484
REV.:
A
DATE:
03MAR2022
PAGE:
9 OF 17
7.6 Pressure Testing
During installed valve testing, maximum allowable test pressure is 1.1x the marked rating when the valve is
closed and 1.5x the marked rating when the valve is open.
8 OPERATION
During closing, the valve ball is rotated against the elastomeric seat seals until the solid portion of the valve ball
contacts the seat seals. Positive contact pressure is maintained between the ball and the seat seals by Belleville
springs behind each seat seal. On valves without gear operators, a stop on the operating square provides a
positive stop against the locking plate in the full open and full closed position.
8.1 General Valve Operation
Do not use excessive torque to operate the valve which may damage the valve or the gear
operator!
•Standard valves are equipped with a 2” operating square and can be operated with an adaptor tool or
wrench.
•Standard valves operate clockwise to close, and counterclockwise to open.
•Valve should not be operated as a throttling valve between full open and full close.
•Valves with gear operators will take multiple turns to open or close.
8.2 Operating Torque and Critical Torque
Excessive or unlimited operating torque will ultimately cause failure of the stop pin or Ultra-Stop. The chart
below indicates the minimum torque value where a failure will occur.
Table 1 Operating and Critical Torque by Valve Size
Nominal Valve
Size
(NPS)
Maximum Operating
Torque
(ft-lbs)
Minimum Shear Pin
Failure Torque
(Valves without Ultra-Stop)
(ft-lbs)
Nominal Ultra-Stop
Failure Torque
(ft-lbs)
3/4
5
25
75
1
8
60
75
1-1/4
12
70
75
2
50
150
800
3
80
150
800
4
100
150
1000
6
200 (Class 150)
300 (Class 300)
500
1500
8
350 Without Gear
Operator
The stop failure mechanism is
designed into the gear operator
N/A
10
Only supplied with gear
operator
The stop failure mechanism is
designed into the gear operator
N/A
12
Only supplied with gear
operator
The stop failure mechanism is
designed into the gear operator
N/A

KEROTEST WELDBALL BALL VALVE
INSTALLATION, OPERATION, AND
MAINTENANCE MANUAL
NO.:
K-1484
REV.:
A
DATE:
03MAR2022
PAGE:
10 OF 17
9 TROUBLESHOOTING
9.1 Valve Shut-Off
If seat shut-off is unattainable, there may be some debris trapped between the valve ball and the seat seals.
Reopen the valve full and cycle until desired shut-off has been obtained. If positive shutoff is still not obtained,
please contact Kerotest.
9.2 Valve Packing Leakage
Valve stem leakage may occur if the stem or stem seal O-rings are worn, damaged, or operated outside the
valve temperature limitations. See section 10.5 for replacement of the stem seal O-ring.
10 MAINTENANCE
10.1 Recommended Periodic Preventative Maintenance
The following is recommended periodically:
•Check that the valve is free from surface damage and shaft leaks and repair any damage.
•Fully cycle the valve annually to clear any buildup of debris on the ball and seat surfaces.
•To ensure long-term operational reliability, even when seldom used (around ten times a year or less), the
following is recommended:
Approximately six months after installation and then once a year, inspect the valve for shaft leaks, check
the gear operator / operating square, and ensure the tightness of the screws between valves.
10.2 Gear Operator Removal
The gear operator can be removed when the valve is under pressure.
NOTE: Avoid removing the gear operator from the valve. The gear operator has been adjusted at the
factory to ensure that the valve is leak-free. If the gear operator is removed, it may have to be re-adjusted.
Kerotest does not accept responsibility for adjustments of customer installed gear operators. Refer to section
10.4 for adjustment instructions.
CAUTION: Incorrect disassembly may cause serious personal injuries as well as malfunctions and
damage to the equipment. Extreme caution must be exercised during the disassembly!
Part numbers mentioned in this section refer to Figure 13.
1. Turn the valve to the open position before removing the gear. Valve opens when you turn the operating
square of the gear counterclockwise.
2. Turn the operating square towards the close position (clockwise) to release forces between the valve and
the gear to make it easier to remove the gear. To do this, turn the operating square only until it rotates easily.
3. Remove the bolts (2) of the position indicator plate and remove the position indicator plate (3). Mark the
position of the valve stem to the gear to make it easier to reinstall the gear back into the right position.
4. Remove the attachment bolts of the gear and then remove the gear.

KEROTEST WELDBALL BALL VALVE
INSTALLATION, OPERATION, AND
MAINTENANCE MANUAL
NO.:
K-1484
REV.:
A
DATE:
03MAR2022
PAGE:
11 OF 17
10.3 Gear Operator Reinstallation
Part numbers mentioned in this section refer to Figure 13.
1. When reinstalling the gear operator onto the valve, check that the gear is in the correct position using the
marks made in during removing in section 10.2.
a. If the gear operator is installed back to its original position, there is no need for adjustment.
b. If the gear is turned 180 degrees from its original position, you must carefully check that the valve
closes and opens correctly.
2. Install the gear to the valve and tighten the attachment bolts to 45 ft-lbs.
3. Check that the valve opens and closes correctly. If the limit stops (set with parts 4-7) are not correct, adjust
the gear as described in section 10.4.
10.4 Gear Operator Adjustment
Part numbers mentioned in this section refer to Figure 13.
1. Remove the plastic dust caps (4) from the top
of the mechanical limits. Loosen the locking
nuts (5) and adjusting screws (6 & 7).
2. Turn the valve to the open position.
3. Tighten the OPEN position adjusting screw (7)
until it stops turning. Fix it with the locking nut
(5) and put the dust cup in its place (4).
4. Turn the valve 90 degrees to the closed
position.
5. Tighten the CLOSE position adjusting screw
(6) until it stops turning. Fix it with the locking
nut (5) and put the dust cup in its place (4).
6. Check that the valve opens and closes
correctly.
Figure 13 Manual Gear Adjustment

KEROTEST WELDBALL BALL VALVE
INSTALLATION, OPERATION, AND
MAINTENANCE MANUAL
NO.:
K-1484
REV.:
A
DATE:
03MAR2022
PAGE:
12 OF 17
10.5 Stem Seal O-Ring Replacement
Valve must be in closed position if valve will be under
pressure during this procedure.
Assembly and components may vary by valve size and date
of manufacture.
1. Remove all components until upper O-ring (9) is exposed.
Note that O-ring spacer (10) and lower O-ring (9) are not
normally removed because of difficulty in doing so.
2. Carefully remove upper O-ring.
3. Lubricate new O-ring (9) with Aero Lubriplate or other suitable
lubricant and install over stem and into valve neck. Place stem
seal washer (8A) over stem and into valve neck.
4. Reinstall components.
Valve is ready for service.
Table 2 Stem Seal Repair Kits
Size (NPS & Port)
Kit Part Number
¾
72660306
1 to 1 ¼
72660307
2 RP to 3 RP
72660308
3 FP to 4 RP
72660309
4 FP to 6 RP
72660310
6 FP to 8 RP
72660311
8 FP to 10 RP
72660312
10 FP to 12 FP
72660313
Figure 14 Stem Seal
O-Ring Replacement

KEROTEST WELDBALL BALL VALVE
INSTALLATION, OPERATION, AND
MAINTENANCE MANUAL
NO.:
K-1484
REV.:
A
DATE:
03MAR2022
PAGE:
13 OF 17
10.6 Replacing Operating Square with Gear Operator on NPS 6 FP / 8 RP Valves
Removing Operating Square
1. Cycle valve to full open position.
2. Remove items in this order: operating
square cap screw (1), washer (2), rubber
gasket (3), operating square (4), weather
seal cap screws (5) and nuts (7), (6)
weather seal plate, and stop plate (8).
3. Using a pair of pliers, remove stop pin (9).
Installing Gear Operator
1. Rotate the actuator to orient the gear
operator to the same open/closed position
as that of the valve.
2. Place gear operator on valve stem aligning
key slot of operator with the key on the
stem. Note: the gear operator actuator
shaft should be perpendicular to the flow of
the valve.
3. Align the four threaded holes in the bottom
of the gear operator with the holes in the
body neck flange. Rotate the actuator in
either direction as necessary. If the holes
do not fully align, loosen the internal stops.
These are located under the cap nuts
located on the left side of the gear operator
when facing the actuator. Remove the cap
nuts and loosen the setscrews. This will
allow the actuator to be rotated further.
4. Attach the gear operator to the body neck
flange using the four Ml2 cap screws
(supplied). Torque bolts to 45 ft-lbs.
5. Cycle the valve to full open and full closed
positions. If the valve does not fully open or
close, or over travels past the full open or
closed position, adjust the internal stops on
the gear operator as described in section
10.4.
Figure 15 Operating Square Components
(NPS 6 FP and 8 RP)

KEROTEST WELDBALL BALL VALVE
INSTALLATION, OPERATION, AND
MAINTENANCE MANUAL
NO.:
K-1484
REV.:
A
DATE:
03MAR2022
PAGE:
14 OF 17
11 GENERAL COMPONENTS
Figure 16 General Weldball Components
1. Body - Carbon steel, all welded, high strength, lightweight design
2. Stem - Stainless steel, blow-out proof design
3. Stem Seals - Buna-N, 2 O-rings provide an effective seal within a temperature range of -20°F to 200°F
4. Retainer - Stainless steel, provides stem support and O-ring retention
5. Stem Bearing - Steel/Bronze/PTFE, prevents the development of static charges and provides stem support
6. Ball - Stainless steel, highly polished
7. Ball Seal - PTFE and carbon, preloaded to provide bubble-tight shut-off and continuous wiping of the ball
8. Seat O-Ring - Buna-N, ensures bubble-tight shut-off in low temperature applications
9. Belleville Spring - Spring steel, preloads seats to provide low pressure, bubble-tight sealing
10. Seat Support Ring - Stainless steel, provides seat ring containment and rigidity
11. Travel Stop Pin/Collar - Carbon steel, permits 1/4 turn operation, protects stem from excessive torque damage
12. 2" Operating Square - Ductile iron, provides position indication and locking capabilities (non-gear only)
13. Locking Plate - Carbon steel, enables the valve to be secured in the full open or full closed position
14. Weather Seal Gasket - Buna-N, protects stem area from moisture and debris
15. Operating Square O-Ring - Buna-N, protects stem area from moisture and debris

KEROTEST WELDBALL BALL VALVE
INSTALLATION, OPERATION, AND
MAINTENANCE MANUAL
NO.:
K-1484
REV.:
A
DATE:
03MAR2022
PAGE:
15 OF 17
12 PHYSICAL SPECIFICATIONS
Table 3 Valve Dimensions, Weight, and Cv

KEROTEST WELDBALL BALL VALVE
INSTALLATION, OPERATION, AND
MAINTENANCE MANUAL
NO.:
K-1484
REV.:
A
DATE:
03MAR2022
PAGE:
16 OF 17
13 FACTORY TESTING
To be certain that all valves shipped from the factory are bubble tight, they are subjected to the following tests in
accordance with ASME B16.34
Table 4 Minimum Test Pressure and Durations
Size
(NPS)
Class
CWP1
High Pressure
Air Seat Test
Low Pressure
Air Seat Test
Shell Test
Test
Media
Pressure
(PSIG)
Duration
(Minutes)2
Pressure
(PSIG)
Duration
(Seconds)2
Pressure
(PSIG)
Duration
(Minutes)
¾ - 4
150
285
315
2
80-100
30
450
2
Air
6
150
285
315
5
80-100
30
450
5
Air
8
150
285
315
5
80-100
30
450
5
Water
10
150
285
315
5
80-100
60
450
5
Water
12
150
285
315
5
80-100
60
450
15
Water
¾ - 4
-
500
550
2
80-100
30
875
2
Air
6
-
500
550
5
80-100
30
875
5
Air
¾ - 4
300
740
815
2
80-100
30
1125
2
Air
6
300
740
815
5
80-100
30
1125
5
Air
8
300
740
815
5
80-100
30
1125
5
Water
Footnotes:
1 - Cold Working Pressure
2 - Duration Each Side

KEROTEST WELDBALL BALL VALVE
INSTALLATION, OPERATION, AND
MAINTENANCE MANUAL
NO.:
K-1484
REV.:
A
DATE:
03MAR2022
PAGE:
17 OF 17
14 DOCUMENT REVISION HISTORY:
Rev
Description
Written By
Approval
Approval
Date
A
Update procedure.
Initial Release EAN S-1567
B Snyder &
D Frederick
03MAR2022
Kerotest Manufacturing Corp.
5500 Second Avenue
Pittsburgh, PA 15207
Telephone: (412) 521-4200
www.kerotest.com
sales@kerotest.com
Prior Document Releases:
This procedure was previously distributed as “Kerotest Weldball Valve Operations Manual WB-001”.
Rev
Description
Written By
Approval
Approval
Date
1
Added 6" and 8" short end to end flange end
dimensions; added Welding Recommendations
---
---
---
09-09-1989
2
Added information on 8", 10" and 12" and Class
300 Valves. Also added information on 3/4"
through 1-1/4" valves.
RT Adams
DJ Zolkos
JF Berarducci
01-23-1998
3
Added information on Ultra-Stop Failure
Torques to Critical Torque Table, Page 9.
RT Adams
DJ Zolkos
JF Berarducci
09-09-1998
4
Added stem seal a-ring replacement for stop
collar design on Page 8. Added ref. to stop
collar design on bill of materials, Page 10.
Added full port Weldball data on Page 12.
RT Adams
DJ Zolkos
JF Berarducci
03-15-1999
5
Revised welding precautions on Page 4.
RT Adams
DJ Zolkos
JF Berarducci
06-17-1999
David T Frederick
2022.03.10 14:23:31 -05'00'
Doug Alcock
2022.03.10 15:33:00 -06'00'
Table of contents
Other Kerotest Control Unit manuals
Popular Control Unit manuals by other brands
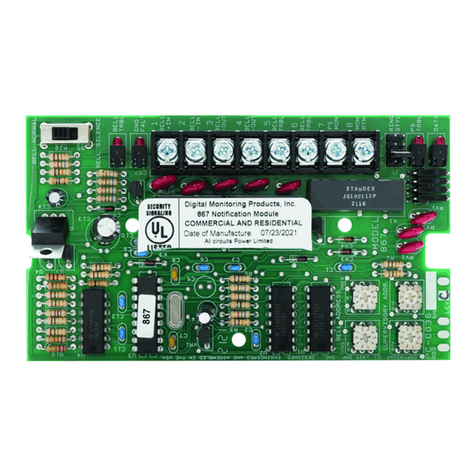
DMP Electronics
DMP Electronics 867 W LX-BUS installation guide
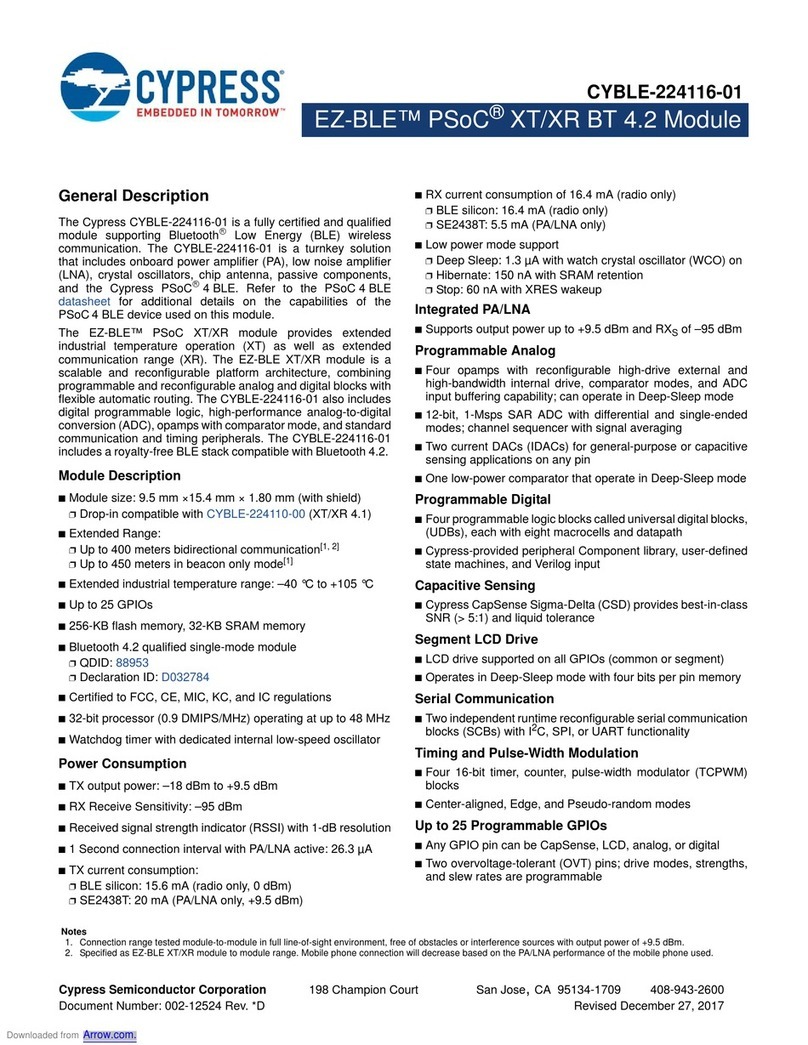
Cypress
Cypress EZ-BLE PSoC CYBLE-224116-01 manual
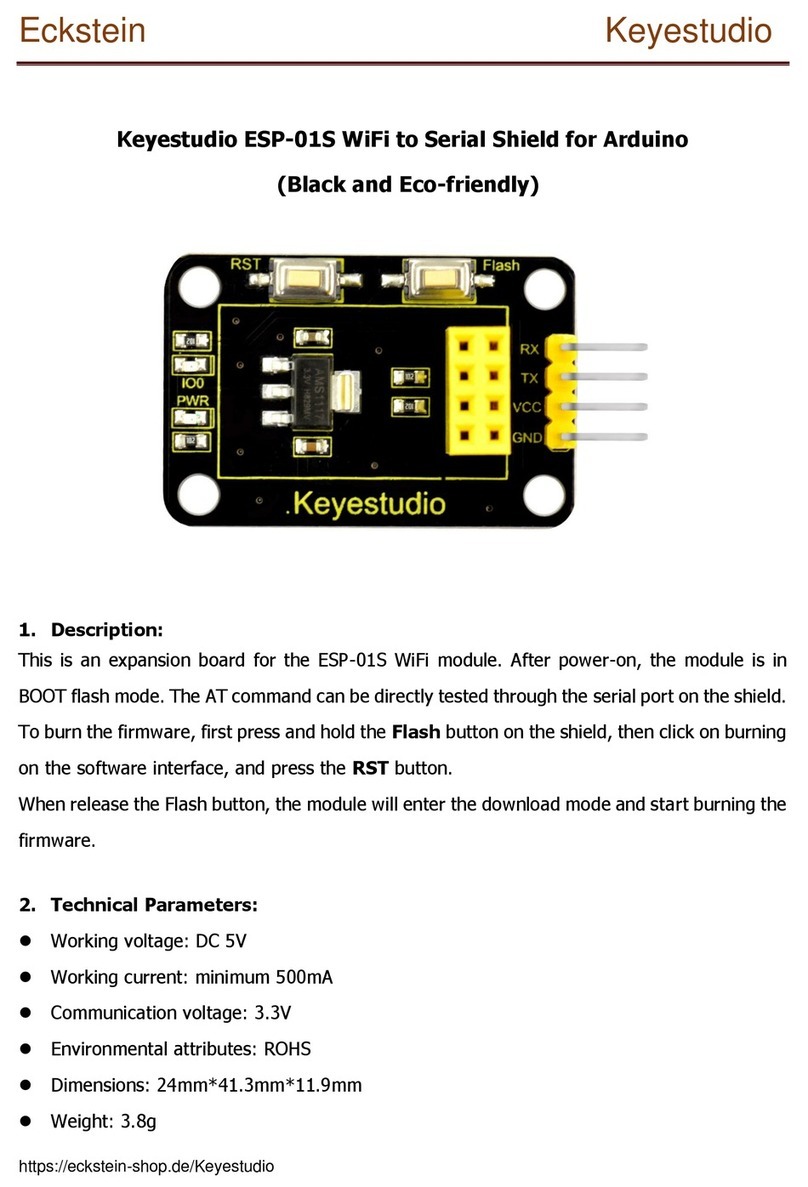
eckstein
eckstein Keyestudio ESP-01S manual
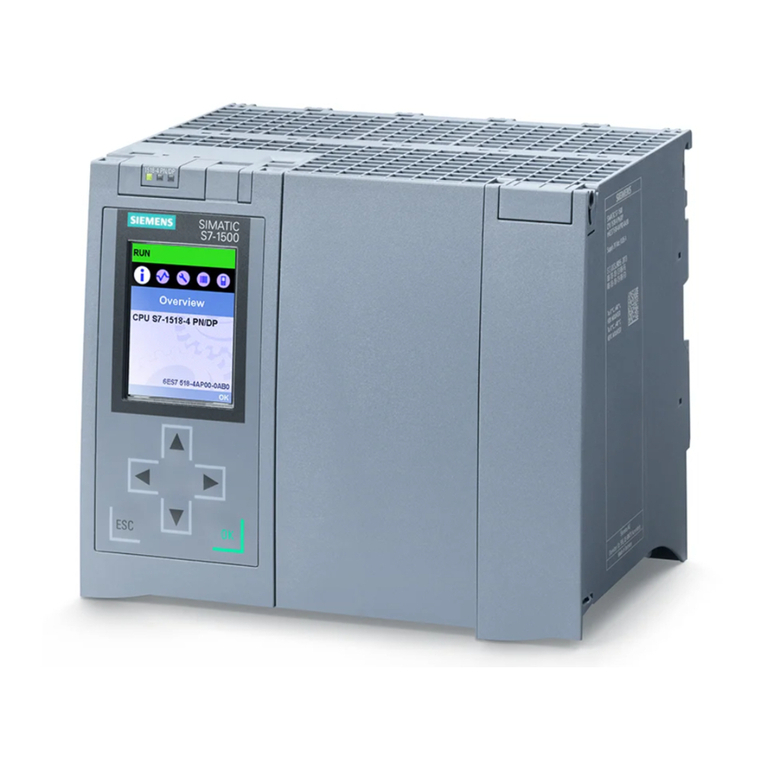
Siemens
Siemens Simatic S7-1500 manual
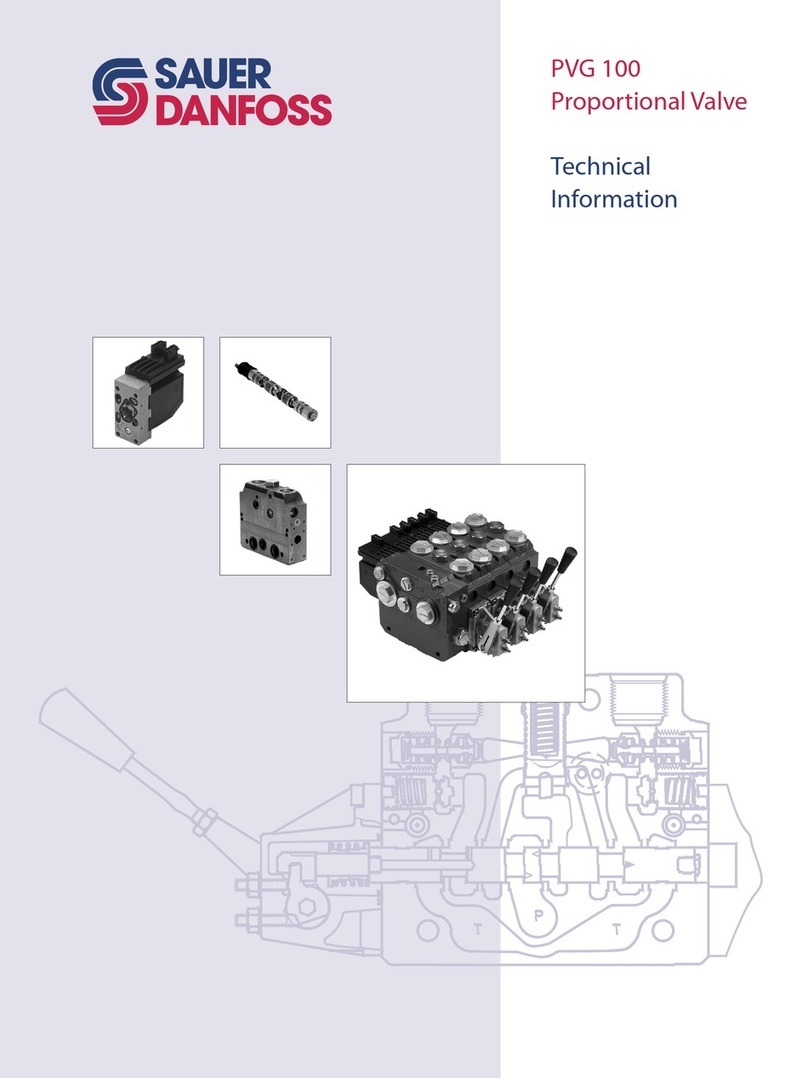
Sauer Danfoss
Sauer Danfoss PVG 100 technical information
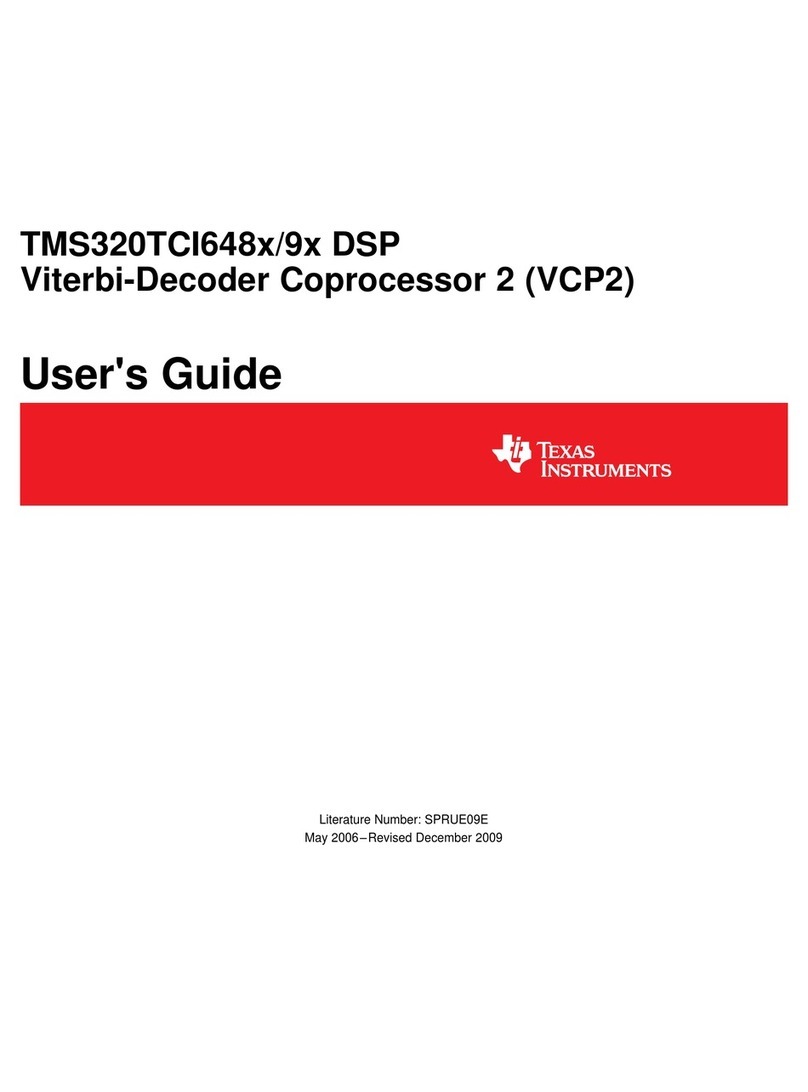
Texas Instruments
Texas Instruments TMS320TCI648 Series user guide