Kerotest MODEL-1 User manual

KEROTEST CUSTOMER
MODEL-1 GATE VALVE
INSTALLATION, OPERATION, AND
MAINTENANCE MANUAL
NO.:
K-1464
REV.:
11
DATE:
06/26/2018
PAGE:
1 OF 30
KEROTEST CUSTOMER MODEL-1 GATE VALVE
INSTALLATION, OPERATION, AND MAINTENANCE MANUAL
Table of Contents
1SCOPE .........................................................................................................................................................................................3
2PRODUCT DESCRIPTION AND FEATURES .....................................................................................................................................3
3CAUTIONS AND WARNINGS ........................................................................................................................................................4
4VALVE IDENTIFICATION...............................................................................................................................................................4
5VALVE COMPONENTS .................................................................................................................................................................4
6ACCESSORIES ..............................................................................................................................................................................6
6.1 HANDWHEEL ......................................................................................................................................................................................6
6.2 LOCKING DEVICE .................................................................................................................................................................................6
6.3 COATING ...........................................................................................................................................................................................7
7FACTORY TESTING.......................................................................................................................................................................8
8STORAGE, HANDLING, AND INSTALLATION.................................................................................................................................9
8.1 STORAGE ...........................................................................................................................................................................................9
8.2 HANDLING .........................................................................................................................................................................................9
8.3 INSTALLATION.....................................................................................................................................................................................9
8.3.1 General Notes on Installation ............................................................................................................................................... 9
8.3.2 Screwed End Valves...............................................................................................................................................................9
8.3.3 Socket Weld End Valves ...................................................................................................................................................... 10
8.3.4 Flanged End Valves ............................................................................................................................................................. 10
8.3.5 Butt Weld End Valves..........................................................................................................................................................11
8.3.6 Butt Weld End X Flange End Valves ....................................................................................................................................11
9OPERATION...............................................................................................................................................................................12
9.1 GENERAL VALVE OPERATION ...............................................................................................................................................................12
9.2 OPERATING TORQUE..........................................................................................................................................................................12
9.3 CRITICAL TORQUE..............................................................................................................................................................................12
9.4 PRESSURE DROP................................................................................................................................................................................13
10 REPAIR SERVICE ........................................................................................................................................................................13
10.1 SHUT-OFF OR SEAT LEAK ....................................................................................................................................................................13
10.1.1 Clearing Internal Debris..................................................................................................................................................13
10.1.2 Body and Wedge Seating ...............................................................................................................................................13
10.2 EXTERNAL STEM PACKING LEAK............................................................................................................................................................14
10.2.1 Packing Shim Installation Under Pressure......................................................................................................................14
10.2.2 Repacking a Valve with Zero Pressure............................................................................................................................15
10.3 EXTERNAL BONNET SEAL LEAK .............................................................................................................................................................18
10.3.1 Sealing a Bonnet Leak with Zero Pressure......................................................................................................................18
10.3.2 Sealing a Bonnet Leak Under Pressure ...........................................................................................................................18
10.4 BROKEN STEMS.................................................................................................................................................................................22
10.4.1 Valve Operation with Broken Stem ................................................................................................................................22
10.4.2 Stem Repair .................................................................................................................................................................... 22
10.5 SERVICE PARTS ORDERING PROCEDURE .................................................................................................................................................23
APPENDIX A: BROKEN BOLT REMOVAL ..............................................................................................................................................24
INFORMATION AND BACKGROUND .................................................................................................................................................................24
MODEL-1 BOLT REMOVAL PROCEDURE ..........................................................................................................................................................24
APPENDIX B: BONNET SCREW TIGHTENING PROCEDURE ...................................................................................................................26
INCREMENTAL TIGHTENING PROCEDURE:.........................................................................................................................................................26
CROSS-PATTERN TIGHTENING SEQUENCES:......................................................................................................................................................26
APPENDIX C: MODEL-1 –NPS 1 AND 1 ¼ BOLT REPLACEMENT FIXTURE FOR FIELD SERVICE REPAIR ..................................................28

KEROTEST CUSTOMER
MODEL-1 GATE VALVE
INSTALLATION, OPERATION, AND
MAINTENANCE MANUAL
NO.:
K-1464
REV.:
11
DATE:
06/26/2018
PAGE:
2 OF 30
Table of Tables
Table 1: Valve Specifications ................................................................................................................................................................5
Table 2: Handwheel Options ................................................................................................................................................................6
Table 3: Minimum Test Parameters .....................................................................................................................................................8
Table 4: Valve Torque Values .............................................................................................................................................................12
Table 5: Pressure Drop and Cv............................................................................................................................................................13
Table 6: Gland Cap Screw Torque Values............................................................................................................................................16
Table 7: Packing Repair Part Numbers................................................................................................................................................16
Table 8: Packing Repair All-Thread Studs ...........................................................................................................................................17
Table 9: Bolt Replacement Support Clamps........................................................................................................................................19
Table 10: Bonnet Cap Screw Torque Values .......................................................................................................................................19
Table 11: Bonnet Gaskets...................................................................................................................................................................21
Table 12: Bonnet Cap Screws .............................................................................................................................................................21
Table 13: Broken Stem Repair Kit Part Numbers ................................................................................................................................23
Table 14: Bonnet Bolt Removal Chart.................................................................................................................................................25
Table 15: 72631146 Repair Kit Components.......................................................................................................................................25
Table 16: Cross-Pattern Tightening Sequences...................................................................................................................................26
Table of Figures
Figure 1: Model 1 Pressure-Temperature Chart....................................................................................................................................3
Figure 2: Valve Components.................................................................................................................................................................5
Figure 3: Design Changes......................................................................................................................................................................5
Figure 4: Locking Device .......................................................................................................................................................................7
Figure 5: Bolt Torquing Pattern Examples ..........................................................................................................................................11
Figure 6: Valve Packing Components..................................................................................................................................................17
Figure 7: Support Clamp Installations.................................................................................................................................................19
Figure 8: Teflon Rope Installation Diagram ........................................................................................................................................20
Figure 9: All-Thread Installation Diagram ...........................................................................................................................................20
Figure 10: Broken Stem Repair...........................................................................................................................................................23
Figure 11: Bonnet Broken Bolt Diagram .............................................................................................................................................24
Figure 12: Example Pattern for 12-Bolt Tightening Sequence.............................................................................................................27
Figure 13: Bolt Replacement Instructions (1 of 2)...............................................................................................................................28
Figure 14: Bolt Replacement Instructions (2 of 2)...............................................................................................................................29

KEROTEST CUSTOMER
MODEL-1 GATE VALVE
INSTALLATION, OPERATION, AND
MAINTENANCE MANUAL
NO.:
K-1464
REV.:
11
DATE:
06/26/2018
PAGE:
3 OF 30
1 SCOPE
This operations manual defines for gas utility customers the procedures for proper use and
common repairs on the Model 1 line of metal seat gate valves.
2 PRODUCT DESCRIPTION AND FEATURES
Below are some of the features of the Kerotest Model-1 steel gate valves:
Maintenance free
No gland tightening
No lubrication required
Low operating torque
Field repairable
Dual integral angled seats and wedge
Bidirectional installation and operation
The intent of this manual is to acquaint our customers with installation, operation, and
maintenance/service repair techniques for Model-1 Gate Valves. Model-1 Gate Valves are cast
steel valves used in natural/fuel gas distribution pipelines and are available in NPS 1 through NPS
16, in ASME/ANSI Pressure Classes 150 and 300 and intermediate pressure rating of 500 WOG
Maximum Operating Pressure (MOP, psi). The valve end connections are welded, flanged, weld-
by-flange, and some threaded and socket ended. Temperature limits of the valves are -20°F to
250°F with allowable pressures as shown in Figure 1.
Figure 1: Model 1 Pressure-Temperature Chart
Class 300
500 WOG
Class 150
0
100
200
300
400
500
600
700
800
-20
0
20
40
60
80
100
120
140
160
180
200
220
240
Maximum Operating Pressure (psig)
Operating Temperature (°F)
Model 1 - Pressure Temperature Chart
Class 300
500 WOG
Class 150

KEROTEST CUSTOMER
MODEL-1 GATE VALVE
INSTALLATION, OPERATION, AND
MAINTENANCE MANUAL
NO.:
K-1464
REV.:
11
DATE:
06/26/2018
PAGE:
4 OF 30
3 CAUTIONS AND WARNINGS
Within this document, you will see the following symbols;
General Advisory Marking - for information or operational procedures, order of
operation, etc.
Caution Marking –note designates an action or step that may result in personal injury
or death or equipment/property damage. Personnel performing activities should be
fully aware of the hazards and take necessary steps to prevent any injuries, damage,
or unsafe operating/repair conditions.
4 VALVE IDENTIFICATION
Each valve will have an identification nameplate attached with the following information:
Manufacturing company
ASME/ANSI pressure class, or intermediate pressure rating (such as 500 WOG)
Temperature and pressure ratings
Body and stem materials
Serial number
1
Date of manufacture
Name of the product line
5 VALVE COMPONENTS
Model-1 Valves are divided into 2 basic designs: (1) Prior to 1988 production date and (2) after
1988 production date. Valves produced after 1988 contain a weather seal O-ring. Figure 3 shows
the part differences between the two versions.
1
Serialization marking on tags began September 2014. As of February 2018, the serial number is also
stamped directly on the body of the valve

KEROTEST CUSTOMER
MODEL-1 GATE VALVE
INSTALLATION, OPERATION, AND
MAINTENANCE MANUAL
NO.:
K-1464
REV.:
11
DATE:
06/26/2018
PAGE:
5 OF 30
Figure 2: Valve Components
Figure 3: Design Changes
Table 1: Valve Specifications
Valve
Size
NPS
C/L to
Top
(in)
Number of
Turns to
Open/Close
1
7.25
5.5
1-1/4
7.25
5.5
2
8.75
7.3
3
10.43
10.3
4
12.68
13.3
6
16.43
19.8
8
20.25
26.3
10
27.00
21.8
12
30.75
25.8
16
41.37
69.0

KEROTEST CUSTOMER
MODEL-1 GATE VALVE
INSTALLATION, OPERATION, AND
MAINTENANCE MANUAL
NO.:
K-1464
REV.:
11
DATE:
06/26/2018
PAGE:
6 OF 30
6 ACCESSORIES
6.1 Handwheel
If required, the 2” operating square may be removed and replaced with a handwheel.
Table 2: Handwheel Options
Valve
Size NPS
Handwheel Diameters (inches)
9
12
14
16
18
24
1
1-1/4
2
72530140
3
72530165
4
72530165
6
72530173
8
72530181
10
72530199
12
72530199
16
72537699
6.2 Locking Device
Model-1 valves can be ordered with a locking device installed or it may be installed by
customers. This locking device prevents unauthorized users from changing the valve
state (open or close) with a customer supplied lock. When installed, the lock and/or the
cap may turn, but no torque is applied to the stem. To install this device, perform the
following (see Figure 4);
1. Remove nut which holds operating square in place and replace with swivel assembly
(1). Keep the lock washer (2) on the assembly.
2. Place cap (3) on swivel assembly (1).
3. Attach a padlock (not furnished) to swivel assembly to complete locking device

KEROTEST CUSTOMER
MODEL-1 GATE VALVE
INSTALLATION, OPERATION, AND
MAINTENANCE MANUAL
NO.:
K-1464
REV.:
11
DATE:
06/26/2018
PAGE:
7 OF 30
Figure 4: Locking Device
6.3 Coating
The Model-1 valve is ordered with either a zinc chromate gray primer coating or a two-
component, high solids green epoxy coating. The gray primer will provide a limited indoor
non-exposed protection against corrosion. It is the responsibility of the customer to
provide long duration corrosion protection coverings or systems once installed per CFR
192 Subpart I.
The two component, high solids epoxy coating is generally applied 4 to 8 mils dry film
thickness (DFT) unless specified by the customer.
If a valve appears corroded prior to installation, particularly on the internal components,
contact Kerotest to determine if the valve can be installed.

KEROTEST CUSTOMER
MODEL-1 GATE VALVE
INSTALLATION, OPERATION, AND
MAINTENANCE MANUAL
NO.:
K-1464
REV.:
11
DATE:
06/26/2018
PAGE:
8 OF 30
7 FACTORY TESTING
To be certain that all valves shipped from the factory are bubble tight, they are subjected to the
following tests.
Table 3: Minimum Test Parameters
Table 3a: Hydrostatic Shell Test
Valve Size
NPS
Class 150 (285 MOP)
500 WOG
Class 300 (740 MOP)
Time
(minutes)
Pressure
(psig)
Time
(minutes)
Pressure
(psig)
Time
(minutes)
Pressure
(psig)
1 –4
2
450
2
875
2
1125
6 –8
5
450
5
875
5
1125
10
5
450
NA
NA
5
1125
12 –16
15
450
NA
NA
15
1125
Table 3b: Hydrostatic Seat Test
Valve Size
NPS
Class 150 (285 MOP)
500 WOG
Class 300 (740 MOP)
Time
(minutes)
Pressure
(psig)
Time
(minutes)
Pressure
(psig)
Time
(minutes)
Pressure
(psig)
2 –4
2
315
2
550
2
815
6 –10
5
315
5**
550
5
815
12 –16
10
315
NA
NA
10
815
* Time Listed Per Each Side
** 10” Not Applicable
Table 3c: Air Shell Test
Valve Size
NPS
Class 150 (285 MOP)
500 WOG
Class 300 (740 MOP)
Time
(minutes)
Pressure
(psig)
Time
(minutes)
Pressure
(psig)
Time
(minutes)
Pressure
(psig)
1 –4
2
150
2
150
2
150
6 –10
5
150
5
150
5
150
12 –16
15
150
10
150
15
150
Table 3d: Air Seat Test
Valve Size
NPS
Class 150 (285 MOP)
500 WOG
Class 300 (740 MOP)
Time
(seconds)
Pressure
(psig)
Time
(seconds)
Pressure
(psig)
Time
(seconds)
Pressure
(psig)
1 –8
30
80 –100
30
80 –100
30
80 –100
10 –16
60
80 –100
60
80 –100
60
80 –100
* Time Listed Per Each Side
The above tests equal or exceed those valve tests required by API 6D.
Note: valves built before changes to US CFR in July 2006 were rated as follows:
Class 150 –275 MOP
Class 300 –720 MOP

KEROTEST CUSTOMER
MODEL-1 GATE VALVE
INSTALLATION, OPERATION, AND
MAINTENANCE MANUAL
NO.:
K-1464
REV.:
11
DATE:
06/26/2018
PAGE:
9 OF 30
8 STORAGE, HANDLING, AND INSTALLATION
8.1 Storage
Store the valve carefully before installation, preferably in a well-ventilated, dry place, on a
shelf or a wooden grid/pallet, preferably in the original packaging, to protect it from
ground water and moisture. Leave flange and port protectors in place to provide limited
internal corrosion and contamination protection.
Protect the valve from sand, dust, and water when storing or transporting.
When properly stored, the Model-1 has a shelf life greater than 10 years.
8.2 Handling
CAUTION: For heavy large valves, use rated lifting slings or straps. The valve or valve
assembly must not be lifted by the operating square or handwheel. Most Model-1 valves
with the operating square facing up are top-heavy and can shift or rotate in the sling.
Dropping or incorrect lifting of the valve can result in personal injury or damage to nearby
equipment or property.
If pressure testing is performed prior to pipeline installation, exercise extreme caution
with methods, tools, and procedures for capping and securing the valve.
8.3 Installation
8.3.1 General Notes on Installation
CAUTION: Incorrect installation may result in serious personal injury or damage to
nearby equipment or property. These instructions must therefore be followed
carefully when installing the valve.
NOTE: The valve must only be installed in intended applications. Valves should be
installed with the wedge in the closed position
Prior to installation, remove port and flange protectors and check that the inside of
the valve is clean and free of corrosion.
For valves located at the end of a pipeline, it is recommended to install a short
pipe pup with pressure rated cap to the valve outlet to reduce potential corrosion
issues. Following installation, the pup and cap section should be pressurized to
match the main pipeline.
8.3.2 Screwed End Valves
Screwed End Valves are only available on 2” valves, 500 WOG or Class 300.
Valve ends have NPT pipe threads machined per ASME B1.20.1
Apply a suitable threading compound to the threads on the pipe. The threading
compound should be applied sparingly.
By hand, thread the fitting onto the mating component until hand-tight, being
careful not to cross thread.

KEROTEST CUSTOMER
MODEL-1 GATE VALVE
INSTALLATION, OPERATION, AND
MAINTENANCE MANUAL
NO.:
K-1464
REV.:
11
DATE:
06/26/2018
PAGE:
10 OF 30
The wrench used for installing these valves should be applied to the end of the
valve next to the pipe to which it is being connected
Tighten fitting about 4-5 turns past hand-tight.
8.3.3 Socket Weld End Valves
NOTE: in order that the valve seats are not affected during the welding operation,
the wedge should be in the closed position
Socket Weld End Valves are only available on 1” valves, Class 300
Valve ends are machined per ASME B16.11
Valves should be installed using either the electric arc or oxy-acetylene welding
methods by welders and welding procedures qualified under Section IX of the
ASME Boiler and Pressure Vessel Code or an equivalent requirement
Valve bodies are carbon steel (ASTM A216, GR WCB). Type 7018 Welding
Rod is suggested for welding these valves in the pipeline.
8.3.4 Flanged End Valves
End flanged dimensions conform to ASME B16.5
2
The length of the valve must be the same as the distance between the flanges
in the pipe line, taking into consideration the gasket.
Standard end flange facing is 1/16" raised face with phonographic finish. Some
valves may be ordered with a flat face finish. Contact Kerotest or your
distributor for further information and availability of flat face finished valves. Flat
face finished valves are slightly shorter than standard faced valves, as allowed
per ASME B16.10.
Bolting and gasketing practice conforming to ASME B16.5 is suggested. The
bolts and gaskets used on installation must be selected to match operating
conditions, temperature, pressure and medium. Gasket dimensions must be
compatible with sealing faces of the flanges.
End flange bolts should not be fastened in consecutive order. Each one
tightened should be 180° opposite the previous one (see Figure 5). Two
passes should be made. Once pass for half tightness and final pass for full
tightness. ASME PCC-1 can provide guidelines for assembly of bolted flanges.
2
NPS sizes 10, 12, and 16 Class 150 valves conform to Class 300 flange thickness and flange outside
diameter requiring longer bolts.

KEROTEST CUSTOMER
MODEL-1 GATE VALVE
INSTALLATION, OPERATION, AND
MAINTENANCE MANUAL
NO.:
K-1464
REV.:
11
DATE:
06/26/2018
PAGE:
11 OF 30
Figure 5: Bolt Torquing Pattern Examples
8.3.5 Butt Weld End Valves
NOTE: in order that the valve seats are not affected during the welding operation,
the wedge should be in the closed position.
Valve ends are machined per ANSI B16.25
Valves should be installed using either the electric arc or oxy-acetylene welding
methods by welders and welding procedures qualified under Section IX of the
ASME Boiler and Pressure Vessel Code or an equivalent requirement
Valve bodies are carbon steel (ASTM A216, GR WCB). Type 7018 Welding
Rod is suggested for welding these valves in the pipeline.
8.3.6 Butt Weld End X Flange End Valves
Refer to Butt Weld End Valves and Flanged End Valves for installation

KEROTEST CUSTOMER
MODEL-1 GATE VALVE
INSTALLATION, OPERATION, AND
MAINTENANCE MANUAL
NO.:
K-1464
REV.:
11
DATE:
06/26/2018
PAGE:
12 OF 30
9 OPERATION
9.1 General Valve Operation
Standard valves are equipped with a 2” operating square and can be operated with an
adaptor tool or wrench.
Standard valves operate clockwise to close, and counterclockwise to open. See Table
1 for the number of turns required to fully open/fully close a valve based on NPS. See
Table 4 for torque required to fully close the valve.
If valves are in the open position in a pipeline for a period of time, there is a chance
that sediment or dirt may collect inside the valve. When these valves are to be closed,
it should be done slowly. The valve should not be closed completely but "throttled" for
a short time in order that the turbulence created will flush away any sediment or dirt
that might have settled in the valve.
Note: In the event of an emergency, the above method need not be followed, as the
valve should be closed as quickly as possible.
9.2 Operating Torque
Valves are designed to operate at the prescribed torque values below in Table 4.
9.3 Critical Torque
Excessive or unlimited torque will ultimately cause a structural failure of the valve.
Table 4 indicates the torque value where stem failure is designed to occur. This
failure location is below the operating square and does not create a leak.
Table 4: Valve Torque Values
Valve Size
NPS
Operating Torque
(ft-lbs)
Min Stem Failure Torque
(ft-lbs)
Min Safety
Factor**
1
50
130
2.6
1-1/4
50
130
2.6
2
60
309
5.2
3
70
309
4.4
4
75
350
4.7
6
125
735
5.8
8
150
735
4.9
10
210
1170
5.6
12
280
1170
4.2
16
450
3700
8.2
** Minimum Safety Factor = Minimum Stem Failure Torque / Operating Torque

KEROTEST CUSTOMER
MODEL-1 GATE VALVE
INSTALLATION, OPERATION, AND
MAINTENANCE MANUAL
NO.:
K-1464
REV.:
11
DATE:
06/26/2018
PAGE:
13 OF 30
9.4 Pressure Drop
Valve pressure drop (equivalent length in feet of pipe) and Cv (Flow Coefficient) are
indicated in Table 5.
Table 5: Pressure Drop and Cv
Valve Size
NPS
Equivalent Length
in Feet of Pipe
Cv
1
1.1
60
1-1/4
1.5
105
2
2.3
255
3
3.4
610
4
4.5
1370
6
6.8
2447
8
8.9
4408
10
10.2
7000
12
13.0
10473
16
16.5
16750
10 REPAIR SERVICE
Note: If the service methods described below do not solve the problem, call your
Customer Service Representative at Kerotest Manufacturing at (412) 521-4200, email
10.1 Shut-Off or Seat Leak
If valve shutoff does not occur using normal operation, fully open the valve, then, using
Table 1 count the number of turns to close until it stops. If the turn count is less than the
table, then there may be an obstruction. Follow the instructions in 10.1.1, otherwise,
follow 10.1.2. If these steps do not correct the problem, contact Kerotest.
10.1.1 Clearing Internal Debris
If valves are in the open position in a pipeline for a period of time, there is a
chance that sediment or dirt may collect inside the valve. When these valves are
to be closed, it should be done slowly. The valve should not be closed completely
until "throttled" for a short time in order that the turbulence created will flush away
any sediment or dirt that might have settled in the valve.
10.1.2 Body and Wedge Seating
When complete shut-off is not obtained, the valve can be reseated in the following
manner. Drive wedge into seats with moderate effort, turn back 1 or 2 complete
turns and again drive into seats with moderate effort. Continue this procedure until
shut-off is obtained. Do not exceed the maximum operating torque specified in
Table 4

KEROTEST CUSTOMER
MODEL-1 GATE VALVE
INSTALLATION, OPERATION, AND
MAINTENANCE MANUAL
NO.:
K-1464
REV.:
11
DATE:
06/26/2018
PAGE:
14 OF 30
10.2 External Stem Packing Leak
Valve leaks are generally caused by the failure of the packing seal, typically from worn
packing or utilizing a valve outside of packing temperature limitations.
CAUTION: These procedures may remove the Gland Plate from the valve while under
operating pressure, exposing the operator to potential personal injury or damage to
nearby property if the steps are not followed explicitly.
Note: Repairs should only be made using Kerotest repair parts as listed in Table 7, Table
11, or Table 12. A diagram of valve parts is shown in Figure 6. All-thread information by
valve size is shown in Table 8.
10.2.1 Packing Shim Installation Under Pressure
For a stem leak perform this repair first. Refer to Figure 6 for a diagram of the area
of the valve affected by this repair and the corresponding components. Shims are
required for this repair and can be obtained by contacting Kerotest. See Table 7
for corresponding part numbers and recommended quantities.
1. Open valve fully. Apply an additional opening torque equal to the Operating
Torque in Table 4 to stop gas flow between the lower thrust washer (13) and the
stem shoulder (12).
2. Remove nut (1), and operating square (2).
3. Remove two of the cap screws (3) that are opposite each other. Replace with two
all-thread studs (size and length recommended in Table 8). Thread all-thread
studs into bonnet until they bottom. Install a nut on each stud and tighten. Remove
all remaining cap screws (3).
4. Slowly and evenly loosen the two nuts on the all-thread studs, watching that the
studs do not unthread from bonnet as the nuts are turned. If gland (4) rises as the
nuts are loosened, the flow was not stopped in Step 1. Retighten the nuts, replace
and retighten the missing cap screws (3), and repeat Step 1 applying a higher
torque in the opening direction.
Repeat this process until you are able to loosen the nuts without the gland rising.
Continue to loosen the nuts until the top of the nuts are flush with the top of the
safety studs.
5. Remove nuts and gland (4). The upper thrust washer (7) may remain on the gland
(4) or on the stem (11). If the upper thrust washer (7) was removed with the gland
(4), replace it on the stem (11).
Note: If the valve was manufactured prior to 1988, there will not be a weather seal
O-ring (5).
6. Place 2-3 additional shims on the top packing adapter (8).
7. Position gasket (6) and gland (4), with weather seal lead-in chamfer side down, on
bonnet being careful not to cut the O-ring (5). Insert cap screws (3) in open holes
and hand tighten. Remove the all-thread studs and insert remaining cap screws
(3). Tighten all cap screws (3) to torque shown in Table 6. Place operating square
(2) on stem (11) and then secure with nut (1).

KEROTEST CUSTOMER
MODEL-1 GATE VALVE
INSTALLATION, OPERATION, AND
MAINTENANCE MANUAL
NO.:
K-1464
REV.:
11
DATE:
06/26/2018
PAGE:
15 OF 30
8. Slowly close the valve to allow pressure on the packing and check for leaks. If
repair is unsuccessful, section 10.2.1 may be repeated a few times and more
shims added.
9. If the leak remains, contact Kerotest for support in servicing the valve as described
at the beginning of this section.
10.2.2 Repacking a Valve with Zero Pressure
This procedure requires a repair kit available from Kerotest. Each repair kit will
contain two upper packing adapters. Use the new packing adapter that visually
matches the one removed. Reference Table 7.
1. Close valve tightly with wrench.
2. Remove nut (1) and operating square (2).
3. Remove all cap screws (3) and gland (4). Remove weather seal O-ring (5). Upper
thrust washer (7) may remain in gland (4) or on stem (11).
Note: If the valve was manufactured prior to 1988, there will not be a weather seal
O-ring (5).
4. Rotate stem (11) in same direction as closing the valve until it is free from the
wedge. Withdraw stem from valve. Lower thrust washer (13) may remain in the
bonnet or on the stem (11).
5. Remove packing shims (14), top packing adapter (8), v-rings (9), and lower
packing adapter (10).
6. Replace lower thrust washer (13) in bonnet if removed.
7. Lubricate new parts with light oil and insert in packing chamber as follows: Lower
packing adapter (10), v-rings (9), top packing adapter (8), and packing shims (14).
8. Insert stem (11) in bonnet and rotate slowly by hand in the opening direction of the
valve. Continue rotation until stem shoulder (12) contacts lower thrust washer (13).
9. Place upper thrust washer (7) on stem (11) if removed. If the valve has the
weather seal O-ring (5), install it in the stem groove. Position gasket (6) and gland
(4), with weather seal lead-in chamfer side down, on bonnet, being careful not to
cut the O-ring. Insert cap screws (3) fully and tighten to torque shown in Table 6.
Place operating square (2) on stem (11) and then secure with nut (1).

KEROTEST CUSTOMER
MODEL-1 GATE VALVE
INSTALLATION, OPERATION, AND
MAINTENANCE MANUAL
NO.:
K-1464
REV.:
11
DATE:
06/26/2018
PAGE:
16 OF 30
Table 6: Gland Cap Screw Torque Values
Valve Size
NPS
Torque
(ft-lbs)
1
15 –20
1-1/4
15 –20
2
20 –30
3
20 –30
4
20 –30
6
20 –30
8
20 –30
10
45 –60
12
45 –60
16
125 –175
Table 7: Packing Repair Part Numbers
NPS 1 Model 1
NPS 1¼ Model 1
NPS 2 Model 1
NPS 3 Model 1
NPS 4 Model 1
NPS 6 Model 1
NPS 8 Model 1
NPS 10 Model 1
NPS 12 Model 1
NPS 16 Model 1
Part Number
Description
QTY
72552508
PACKING KIT
1
X
X
72552516
PACKING KIT
1
X
X
72552524
PACKING KIT
1
X
72552532
PACKING KIT
1
X
X
72552540
PACKING KIT
1
X
X
72552557
PACKING KIT
1
X
72546068
PACKING SHIM
10
X
X
88366968
PACKING SHIM
10
X
X
88366976
PACKING SHIM
10
X
88366984
PACKING SHIM
10
X
X
88366992
PACKING SHIM
10
X
X

KEROTEST CUSTOMER
MODEL-1 GATE VALVE
INSTALLATION, OPERATION, AND
MAINTENANCE MANUAL
NO.:
K-1464
REV.:
11
DATE:
06/26/2018
PAGE:
17 OF 30
Figure 6: Valve Packing Components
Table 8: Packing Repair All-Thread Studs
Valve Size
NPS
All-Thread
Stud and Nut Size
All-Thread
Stud Length
(inches minimum)
1-1/4
5/16 –18 UNC
2.00
2 and 3
3/8 –16 UNC
2.50
4, 6 and 8
3/8 –16 UNC
3.00
10 and 12
1/2 –13 UNC
4.25
16
3/4 –10 UNC
6.25

KEROTEST CUSTOMER
MODEL-1 GATE VALVE
INSTALLATION, OPERATION, AND
MAINTENANCE MANUAL
NO.:
K-1464
REV.:
11
DATE:
06/26/2018
PAGE:
18 OF 30
10.3 External Bonnet Seal Leak
Another possible cause for an external leak could be a failure at the seal between the
valve bonnet and body.
Caution: When a bonnet leak is detected, do not attempt to re-tighten the existing bonnet
bolts and, do not attempt to operate the valve since loads applied could cause damaged
bolts to break.
10.3.1 Sealing a Bonnet Leak with Zero Pressure
1. Depressurize then fully open the valve.
2. Remove all bonnet bolts.
Note: Refer to APPENDIX A: BROKEN BOLT REMOVAL for instructions on
removing broken bolts.
3. Remove the bonnet assembly. This will include the stem and gate.
Note: When removing the bonnet, lift straight up so that no side load or impact can
occur to the stem during removal. Mark the orientation of the bonnet and the
wedge to the body during removal. During reassembly, match the original
orientation.
4. Replace the gasket with only factory authorized replacement. Coat the gasket on
both sides with Slic-Tite®PTFE paste prior to installation.
5. Lower the bonnet back on to the body. Ensure that the gate is in line with the
internal seats of the body and the gasket remains in position and does not shift
when the bonnet makes contact.
6. Install new factory authorized bolts into the bonnet. Tighten them in the sequence
and to the torques specified in APPENDIX B: BONNET SCREW TIGHTENING
PROCEDURE.
Note: Kerotest part numbers for bonnet gaskets and bonnet bolts (cap screws) are
listed in Table 11 and Table 12 respectively.
10.3.2 Sealing a Bonnet Leak Under Pressure
1. Remove and replace bolts one at a time (see Table 12). Torque each new bolt to
the recommended value specified in Table 10 as it is replaced. If using support
clamps to replace the bolts, follow Step 2.
Note: For valve sizes NPS 2 to 6 it is strongly recommended that support clamps
be used during bolt replacement. For valve sizes NPS 8 to 12, there is a support
clamp available but it is not required. These clamps are available from Kerotest,
see Table 9 for associated part numbers.
Note: When replacing bonnet bolts on NPS 1 or NPS 1-1/4 size valves, a special
Kerotest bolt replacement fixture and procedure must be used. This is shown in
APPENDIX C: MODEL-1 –NPS 1 AND 1 ¼ BOLT REPLACEMENT FIXTURE
FOR FIELD SERVICE REPAIR.

KEROTEST CUSTOMER
MODEL-1 GATE VALVE
INSTALLATION, OPERATION, AND
MAINTENANCE MANUAL
NO.:
K-1464
REV.:
11
DATE:
06/26/2018
PAGE:
19 OF 30
Table 9: Bolt Replacement Support Clamps
Clamp Part Number
Compatible Valve Sizes
72544794
2” and 3”
72544802
4” and 6”
72546093
8”, 10”, and 12” 1
1This support clamp is not required for bolt replacement.
Table 10: Bonnet Cap Screw Torque Values
Valve Size NPS
Torque (ft-lbs)
1
38-42
1 ¼
38-42
2
71-79
3
109-121
4
109-121
6
109-121
8
213-237
10
351-389
12
351-389
16
1140-1260
Figure 7: Support Clamp Installations

KEROTEST CUSTOMER
MODEL-1 GATE VALVE
INSTALLATION, OPERATION, AND
MAINTENANCE MANUAL
NO.:
K-1464
REV.:
11
DATE:
06/26/2018
PAGE:
20 OF 30
2. If using these clamps, initially place one in between the two bolts that are closest
to the leak location. Another clamp should be placed on a diametrically opposite
location on the bonnet. See Figure 7.
3. Replace the bolts on either side of both clamps, tightening the new bolts to the
torques listed in Table 10. Then move both clamps in between the next two bolts
to be replaced. Remember to always keep both clamps diametrically opposite of
each other.
4. After replacing all of the existing bonnet bolts if the leakage has stopped the repair
is complete and the valve is ready for service.
If the leakage continues, contact Kerotest for support in servicing the valve.
Figure 9: All-Thread Installation Diagram
Figure 8: Teflon Rope Installation Diagram
Other manuals for MODEL-1
1
Table of contents
Other Kerotest Control Unit manuals
Popular Control Unit manuals by other brands
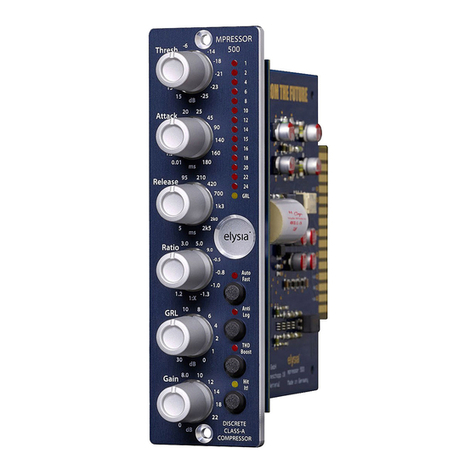
elysia
elysia Mpressor 500 manual
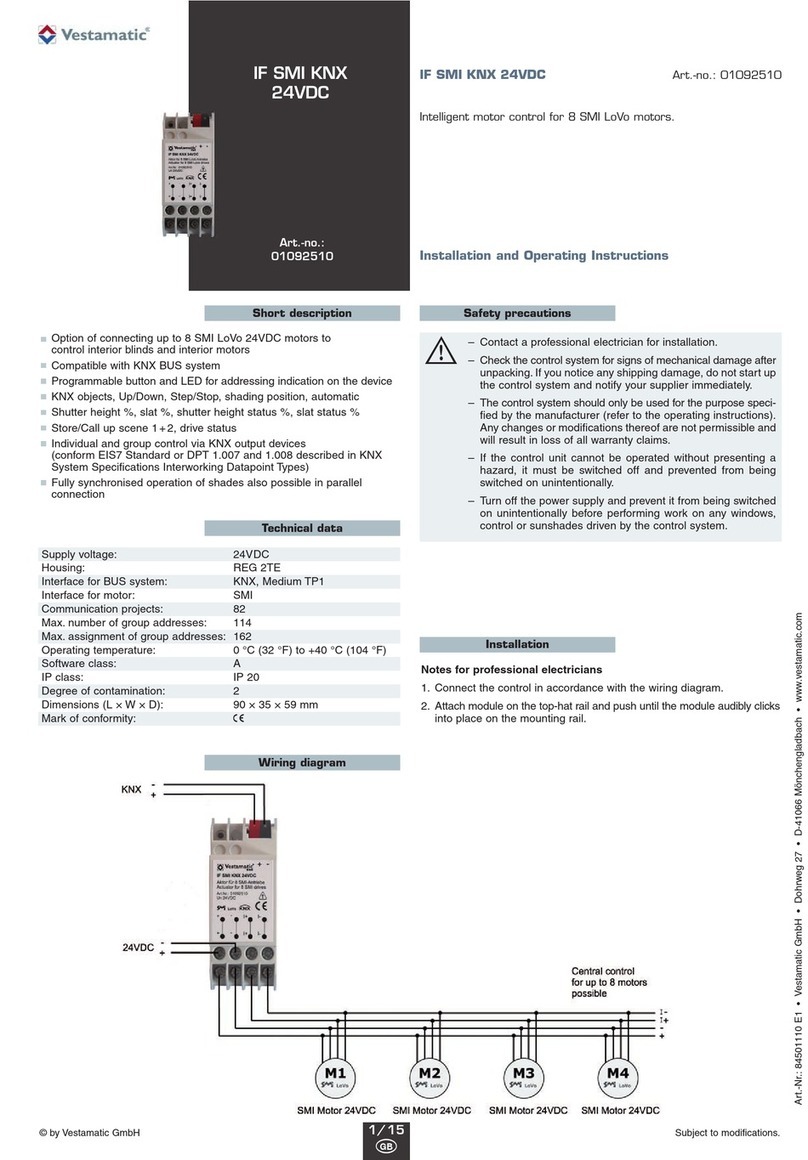
Vestamatic
Vestamatic IF SMI KNX 24VDC Installation and operating instructions
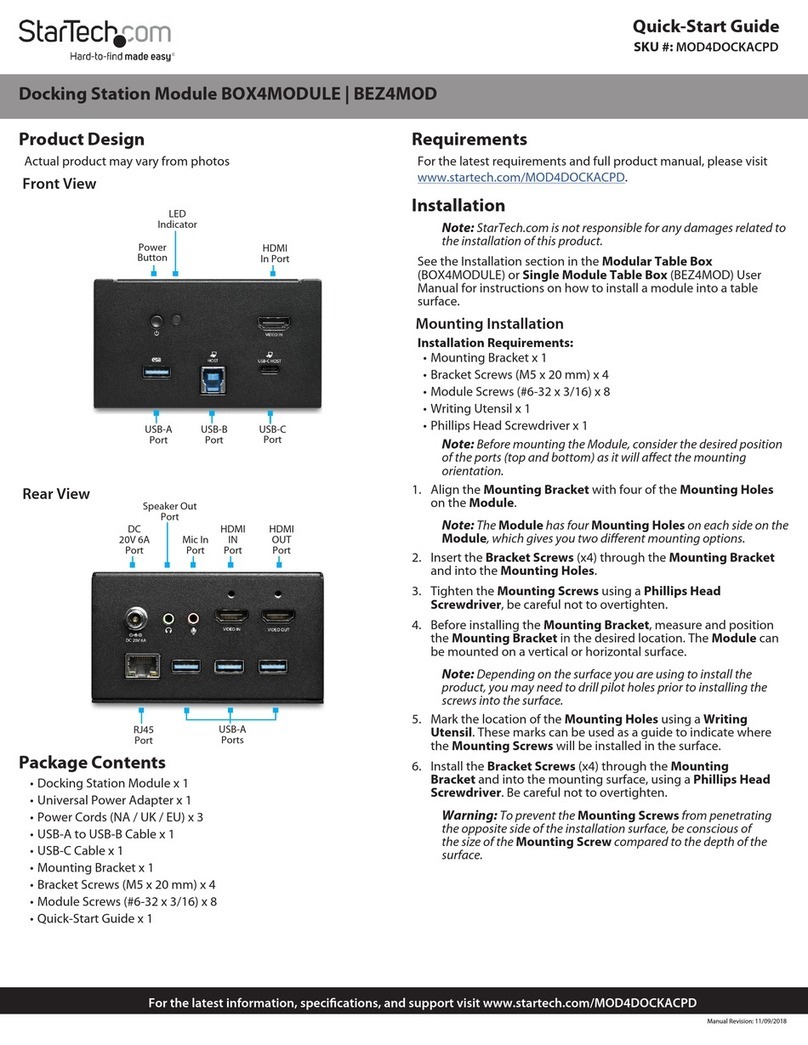
StarTech.com
StarTech.com BOX4MODULE quick start guide
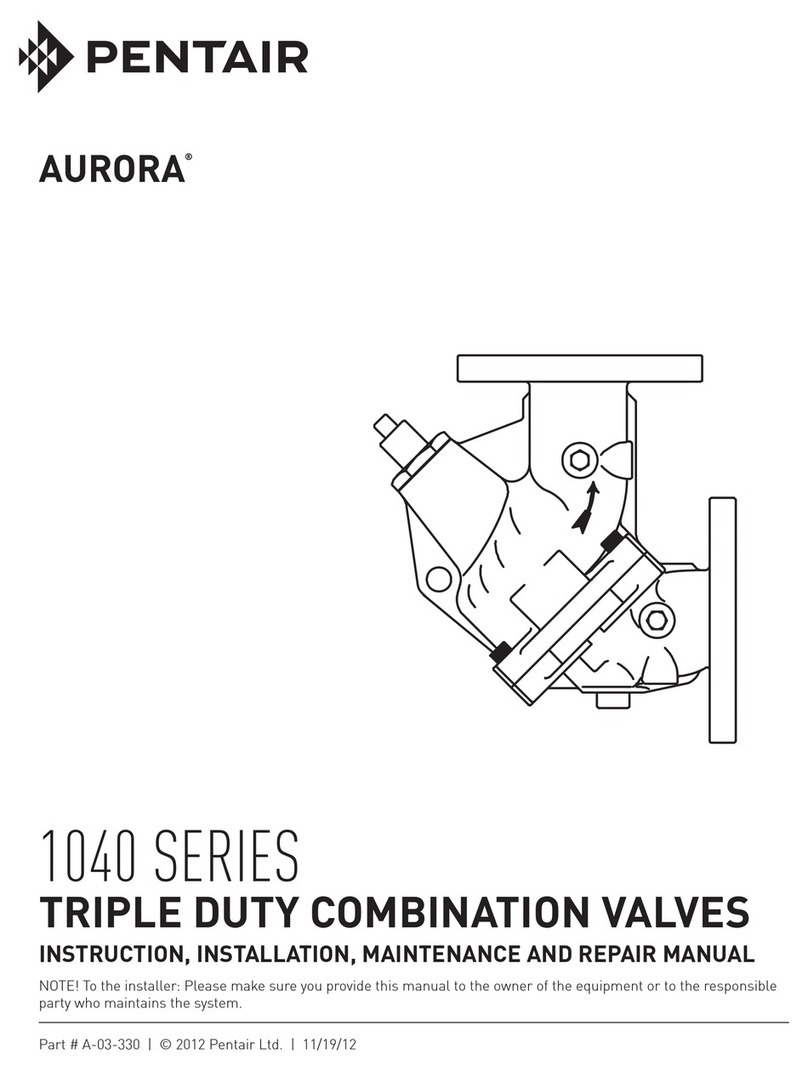
Pentair
Pentair AURORA 1040 Series INSTRUCTION, INSTALLATION, MAINTENANCE AND REPAIR MANUAL
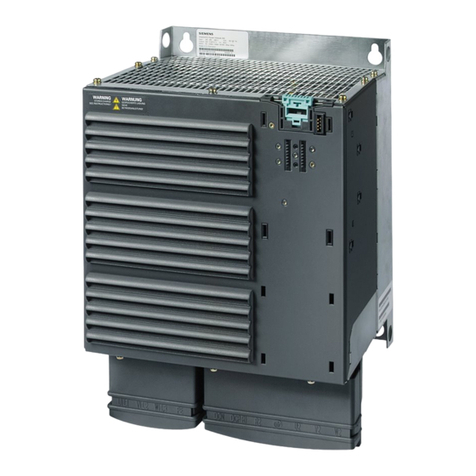
Siemens
Siemens PM250 Hardware installation manual

Meganex
Meganex MEG35007 Installation and operation manual