Knorr-Bremse SKP User manual

Doc. No. Y276710 (EN - Rev. 001)
May 2020
ELECTRICAL SCREW COMPRESSOR
SERVICE MANUAL

2
» Y276710 – (EN - REV. 001) | May 2020
Disclaimer
The information contained in this document is intended for the exclusive use of trained persons within the commercial vehicle industry, and must not be passed on
to any third party. All recommendations regarding products and their servicing or usage are with reference to Knorr-Bremse products and should not be considered
applicable to products from other manufacturers.
This information does not purport to be all-inclusive and no responsibility is assumed as a result of its use. We cannot accept any liability nor oer any guarantee
regarding data accuracy, completeness or timeliness. The information does not represent any guarantee or ensured characteristics of the Products or Systems
described. No liability can be accepted based on the information, its use, recommendations or advice provided. In no event may we be held liable for any damage
or loss except in the case of wilful intent or gross negligence on our part, or if any mandatory legal provisions apply.
Any legal disputes arising from the use of this information shall be subject to German law.
Note: If service work is carried out on the vehicle, it is the responsibility of the workshop to ensure the vehicle is fully tested and in full functional order before the
vehicle is returned into service. Knorr-Bremse accepts no liability for problems caused as a result of appropriate tests not being carried out.
This disclaimer is an English translation of a German text, which should be referred to for all legal purposes.
Revision Details
Rev. 000 June 2017 New document
Rev. 001 May 2020 Layout change

3
» Service Manual - Electrical Screw Compressor
CONTENTS
CONTENTS . . . . . . . . . . . . . . . . . . . . . . . . . . . . . . . . . . . . . . . . . . . . . . . . . . . . . . . . . . . . . . 3
SAFETY AND ENVIRONMENT GUIDELINES . . . . . . . . . . . . . . . . . . . . . . . . . . . . . . . . . . . . . . . . . . 4
1 GENERAL INFORMATION . . . . . . . . . . . . . . . . . . . . . . . . . . . . . . . . . . . . . . . . . . . . . . . . . . . 6
1.1 Technical changes . . . . . . . . . . . . . . . . . . . . . . . . . . . . . . . . . . . . . . . . . . . . . . . . . . . . . . . . . . . . . . .6
1.2 Target group for this document . . . . . . . . . . . . . . . . . . . . . . . . . . . . . . . . . . . . . . . . . . . . . . . . . . . . . .6
1.3 Notes and warning messages . . . . . . . . . . . . . . . . . . . . . . . . . . . . . . . . . . . . . . . . . . . . . . . . . . . . . . .7
2 BASIC SAFETY INFORMATION. . . . . . . . . . . . . . . . . . . . . . . . . . . . . . . . . . . . . . . . . . . . . . . . 8
2.1 Validity . . . . . . . . . . . . . . . . . . . . . . . . . . . . . . . . . . . . . . . . . . . . . . . . . . . . . . . . . . . . . . . . . . . . . .8
2.2 Operator’s commitment to due care . . . . . . . . . . . . . . . . . . . . . . . . . . . . . . . . . . . . . . . . . . . . . . . . . . .9
2.2.1 Assignment of personnel . . . . . . . . . . . . . . . . . . . . . . . . . . . . . . . . . . . . . . . . . . . . . . . . . . . . . . . . . . . . . . . . . . .9
2.2.2 Availability of the document . . . . . . . . . . . . . . . . . . . . . . . . . . . . . . . . . . . . . . . . . . . . . . . . . . . . . . . . . . . . . . . . . 9
2.2.3 Amendments to the document . . . . . . . . . . . . . . . . . . . . . . . . . . . . . . . . . . . . . . . . . . . . . . . . . . . . . . . . . . . . . . .9
2.2.4 Spares and wearing parts . . . . . . . . . . . . . . . . . . . . . . . . . . . . . . . . . . . . . . . . . . . . . . . . . . . . . . . . . . . . . . . . . . .9
3 TECHNICAL DESCRIPTION . . . . . . . . . . . . . . . . . . . . . . . . . . . . . . . . . . . . . . . . . . . . . . . . . 10
4 INSTALLATION AND REMOVAL . . . . . . . . . . . . . . . . . . . . . . . . . . . . . . . . . . . . . . . . . . . . . . 11
4.1 Installation . . . . . . . . . . . . . . . . . . . . . . . . . . . . . . . . . . . . . . . . . . . . . . . . . . . . . . . . . . . . . . . . . . . .11
4.1.1 Handling . . . . . . . . . . . . . . . . . . . . . . . . . . . . . . . . . . . . . . . . . . . . . . . . . . . . . . . . . . . . . . . . . . . . . . . . . . . .12
4.1.2 Disconnect the compressor. . . . . . . . . . . . . . . . . . . . . . . . . . . . . . . . . . . . . . . . . . . . . . . . . . . . . . . . . . . . . . . . . 13
4.1.3 Mechanical installation. . . . . . . . . . . . . . . . . . . . . . . . . . . . . . . . . . . . . . . . . . . . . . . . . . . . . . . . . . . . . . . . . . . . 13
4.1.4 Air connection . . . . . . . . . . . . . . . . . . . . . . . . . . . . . . . . . . . . . . . . . . . . . . . . . . . . . . . . . . . . . . . . . . . . . . . . . 14
4.1.5 Coolant connection . . . . . . . . . . . . . . . . . . . . . . . . . . . . . . . . . . . . . . . . . . . . . . . . . . . . . . . . . . . . . . . . . . . . .15
4.1.6 Electrical connection . . . . . . . . . . . . . . . . . . . . . . . . . . . . . . . . . . . . . . . . . . . . . . . . . . . . . . . . . . . . . . . . . . . . . 16
4.1.7 Storage conditions . . . . . . . . . . . . . . . . . . . . . . . . . . . . . . . . . . . . . . . . . . . . . . . . . . . . . . . . . . . . . . . . . . . . . . 16
4.2 Removal . . . . . . . . . . . . . . . . . . . . . . . . . . . . . . . . . . . . . . . . . . . . . . . . . . . . . . . . . . . . . . . . . . . . 17
5 MAINTENANCE . . . . . . . . . . . . . . . . . . . . . . . . . . . . . . . . . . . . . . . . . . . . . . . . . . . . . . . . 18
5.1 Compressor design . . . . . . . . . . . . . . . . . . . . . . . . . . . . . . . . . . . . . . . . . . . . . . . . . . . . . . . . . . . . . 19
5.2 Inspection . . . . . . . . . . . . . . . . . . . . . . . . . . . . . . . . . . . . . . . . . . . . . . . . . . . . . . . . . . . . . . . . . . . 20
5.2.1 Oil level check . . . . . . . . . . . . . . . . . . . . . . . . . . . . . . . . . . . . . . . . . . . . . . . . . . . . . . . . . . . . . . . . . . . . . . . . . 21
5.2.2 Oil temperature switch check . . . . . . . . . . . . . . . . . . . . . . . . . . . . . . . . . . . . . . . . . . . . . . . . . . . . . . . . . . . . . . .21
5.2.2 Oil top-up . . . . . . . . . . . . . . . . . . . . . . . . . . . . . . . . . . . . . . . . . . . . . . . . . . . . . . . . . . . . . . . . . . . . . . . . . . . . 21
5.3 Servicing. . . . . . . . . . . . . . . . . . . . . . . . . . . . . . . . . . . . . . . . . . . . . . . . . . . . . . . . . . . . . . . . . . . . 22
5.3.1 Oil drainage. . . . . . . . . . . . . . . . . . . . . . . . . . . . . . . . . . . . . . . . . . . . . . . . . . . . . . . . . . . . . . . . . . . . . . . . . . . 23
5.3.2 Exchanging the coalescing lter. . . . . . . . . . . . . . . . . . . . . . . . . . . . . . . . . . . . . . . . . . . . . . . . . . . . . . . . . . . . . . 24
5.4 Repair. . . . . . . . . . . . . . . . . . . . . . . . . . . . . . . . . . . . . . . . . . . . . . . . . . . . . . . . . . . . . . . . . . . . . . 25
6 TROUBLESHOOTING. . . . . . . . . . . . . . . . . . . . . . . . . . . . . . . . . . . . . . . . . . . . . . . . . . . . . 26
7 DISPOSAL . . . . . . . . . . . . . . . . . . . . . . . . . . . . . . . . . . . . . . . . . . . . . . . . . . . . . . . . . . . 29

4
» Y276710 – (EN - REV. 001) | May 2020
Note: The safety advice listed below is applicable to general service and diagnostic work on braking systems. Also observe any recommendations from the axle or
vehicle manufacturer concerning towing, jacking-up and securing the vehicle.
CAUTION: KNORR-BREMSE IS NOT LIABLE FOR ANY INJURIES OR DAMAGES CAUSED BY IMPROPER USE OF SPECIFIED SERVICE KITS AND/OR
SERVICE TOOLS. FURTHERMORE, MISUSE OF TOOLS OR INCORRECT INSTALLATION OR APPLICATION OF SERVICE KITS MAY RESULT IN DAMAGE OR
POTENTIALLY UNSAFE VEHICLE OPERATIONS. IN THIS CASE, KNORR-BREMSE DOES NOT HAVE ANY WARRANTY OBLIGATIONS.
Before and whilst working on or around compressed air systems and devices, the following precautions should be observed, along with the many
hazard notes contained throughout the document:
1 Always wear safety glasses when working with air pressure.
2 Never exceed the vehicle manufacturer’s recommended air pressures.
3 Never look into air jets or direct them at anyone.
4 Never connect or disconnect a hose or line containing pressure; it may whip as air escapes.
5 When removing or servicing a product, ensure all pressure related to the specic system it is contained in has been depleted to 0 bar. Be aware that if the vehicle
is equipped with an air dryer system, it can also contain air pressure along with its purge reservoir, if tted, even after pressure has been drained from the other
reservoirs.
6 If it is necessary to drain the air pressure from reservoirs, etc., keep away from brake actuator push rods and levers since they may move as system pressure
drops. On vehicles tted with air suspension, it is advised when undertaking such work, to support the chassis from sudden lowering and therefore prevent any
possibility of being trapped between the chassis and axle or ground.
7 Park the vehicle on a level surface, apply the parking brakes, and always chock the wheels as depleting vehicle air system pressure may cause the vehicle to roll.
8 When working under or around the vehicle, and particularly when working in the engine compartment, the engine should be shut o and the battery
disconnected. Where circumstances require that the engine be running, EXTREME CAUTION should be taken to prevent personal injury resulting from contact
with moving, rotating, leaking, heated or electrically charged components. Additionally, it is advisable to place a clear sign on or near the steering wheel
advising that there is work in progress on the vehicle.
9 When working on vehicles equipped with air suspension, to guard against injury due to unexpected downward movement of the chassis caused by sudden
pressure loss in the suspension system, ensure that the vehicle chassis is mechanically supported with a ‘prop’between the chassis and the axle or between the
chassis and the ground.
10 Examine all pipework for signs of kinks, dents, abrasion, drying out or overheating. Be aware that kinks in pipework may result in air pressure being trapped in the
pipework and associated equipment. Replacement hardware, tubing, hose, ttings, etc. must be of equivalent size, type and strength as original equipment and
be designed specically for such applications and systems. Check the attachment of all pipework; it should be installed so that it cannot abrade or be subjected
to excessive heat.
11 Components with stripped threads or damaged/corroded parts must be replaced completely. Do not attempt repairs requiring machining or welding unless
specically stated and approved by the vehicle or component manufacturer.
12 Never attempt to install, remove, disassemble or assemble a device until you have read and thoroughly understood the recommended procedures. Some units
contain powerful springs and injury can result if not properly dismantled and reassembled. Use only the correct tools and observe all precautions pertaining to
use of those tools.
13 Before removing any device note its position and the connections of all pipework so that the replacement/serviced device can be properly installed. Ensure that
adequate support or assistance is provided for the removal/installation of heavy items.
14 Use only genuine replacement parts, components and kits as supplied by Knorr-Bremse or the vehicle manufacturer. Only use the recommended tools as
specied in related Knorr-Bremse instructions.
15 The serviced or replaced product must be checked for correct function and eectiveness.
16 If products have been dismantled, serviced or replaced, whose performance could aect braking performance or system behaviour, this should be checked on
a roller dynamometer. Bear in mind that a lower performance may be experienced during the bedding-in phase if new brake pads/linings and/or brake discs/
drums have been tted.
17 The use of impact screwdrivers or impact wrenches in conjunction with Knorr-Bremse service tools for air disc brakes is not permitted. The service tools are not
designed for such use. It is likely that the tools or the vehicle will be damaged and there is a serious risk of injury – see Caution above.
18 Do not use compressed air to clean the disc brake. Avoid air contamination of brake dust.
19 Prior to returning the vehicle to service, make certain that all components and the complete brake systems are leak free and restored to their proper operating
condition.
SAFETY AND ENVIRONMENT GUIDELINES

5
» Service Manual - Electrical Screw Compressor
Welding
To avoid damage to electronic components when carrying out electrical welding, the following precautions should be observed:
1 In all cases, before starting any electrical welding, remove all connections from any electronic control units or modules, noting their position and the order in
which they are removed.
2 When re-inserting the electrical connectors (in reverse order) it is essential that they are tted to their correct assigned position - if necessary this must be
checked by PC Diagnostics.
Disposal of Waste Equipment by Business Users in the European Union
This symbol on the product, packaging or in user instructions, indicates that this product must not be disposed of with other general waste. Instead,
it is your responsibility to dispose of the waste electrical and electronic parts of this product by handing them over to a company or organisation
authorised for the recycling of waste electrical and electronic equipment. For more information about arrangements for waste equipment
disposal please contact your Knorr-Bremse distributor or local Knorr-Bremse representative.

6
1
» Y276710 – (EN - REV. 001) | May 2020
1 GENERAL INFORMATION
1.1 Technical changes
1.2 Target group for this document
DANGER
Please read this entire document carefully to ensure safety of operation and to avoid personal
injuries and damage to equipment.
NOTE
This document will be useful to other target groups as well, e. g. project engineers.
However, it does not claim to provide complete information for such target groups.
KNORR-BREMSE reserves the right to change the unit or this document at any time without giving special notice.
This document is intended for use by trained service technicians who:
- have the skill, experience, safety awareness and professional ability
- to remove and install the unit,
- to inspect, service and debug the unit,
- have read and understood this document from start to nish and are familiar with the safety codes and
accident prevention regulations for these activities.

7
1
» Service Manual - Electrical Screw Compressor
GENERAL INFORMATION
1.3 Notes and warning messages
DANGER
Failure to comply with these instructions will lead to irreversible personal injuries which may have
fatal consequences.
WARNING
Failure to comply with these instructions may lead to irreversible physical injuries which may have
fatal consequences.
CAUTION
Failure to comply with these instructions may lead to personal injuries and/or to damage to the unit
or the environment.
DANGER (= word of alert)
Source of the danger
Consequence of the danger
Remedial measures
NOTE
Notes contain useful hints and additional information about the unit.
Safety notes have a specic structure which is explained here for DANGER:
Notes do not contain any messages relevant to safety and are intended merely to complete the reader’s information.
Warning messages in other parts of this document draw the reader‘s attention to the individual risks concerning use of
the product. Warning messages and notes generally precede the descriptions of the relevant applications.

8
2
» Y276710 – (EN - REV. 001) | May 2020
2 BASIC SAFETY INFORMATION
2.1 Validity
WARNING
Validity note (item number or type designation) ignored!
The consequences may be personal injuries and damage to the unit.
The validity notes in the document must always be taken into account. The item number or type
designation is stated on the name plate and must agree with the validity note stated in this
document.
This document is valid for units with type designations: SKP.
NOTE
If the unit cannot be uniquely identied, e. g. because the name plate is illegible or missing, please
contact KNORR-BREMSE.

9
2
» Service Manual - Electrical Screw Compressor
BASIC SAFETY INFORMATION
2.2 Operator’s commitment to due care
2.2.1 Assignment of personnel
2.2.2 Availability of the document
2.2.3 Amendments to the document
2.2.4 Spares and wearing parts
The operator shall ensure that the personnel assigned to the specied activities possesses the qualications dened
for the given target group.
The operator shall ensure that the present document is always available to the relevant personnel in a complete,
up-to-date and readable form.
The operator shall ensure that, at the place of use, the present document is regularly amended by, or replaced with,
instructions based on:
- statutory accident prevention regulations
- statutory accident protection regulations
- trade association regulations
The operator shall ensure that none other than genuine KNORR-BREMSE parts or KNORR-BREMSE approved spares or
wearing parts are used.
The installation of spares other than approved may impair the safety and reliability of the given unit and overall
system and invalidates any warranty on the part of KNORR-BREMSE.
NOTE
Please use only recomanded spare kits shown on our website www.knorr-bremseCVS.com.

10
3
» Y276710 – (EN - REV. 001) | May 2020
3 TECHNICAL DESCRIPTION
The model SKP compressor is used to generate and supply compressed air in commercial vehicles.
Packaging:
- Nominal dimensions in mm (L x W x H) : 364 x 280 x 321
- Weight: Screw compressor with oil, without coolant approx 29 Kg
Fig. 1 Screw compressor unit

11
4
» Service Manual - Electrical Screw Compressor
4.1 Installation
CAUTION
Beware of contaminating the pneumatic system!
Device and/or system functions will fail.
Keep out dirt during installation. If necessary, blow out the pipes of the pneumatic system.
CAUTION
Beware of disregarding the installation instructions!
Safety will be diminished and functions restricted.
Installation instructions and installation drawings must be taken into account.
CAUTION
Beware of installing untested units!
Safety will be reduced and functions restricted.
Make sure that units are always tested before they are installed.
The system must have been tested and found to be in order before the vehicle is cleared for service.
NOTE
It is vital to observe the maker’s safety instructions and directions for the use of cleaning substances,
sealants, adhesives, auxiliary products, working substances, etc.
4 INSTALLATION AND REMOVAL

12
4
» Y276710 – (EN - REV. 001) | May 2020
INSTALLATION AND REMOVAL
4.1.1 Handling
The device is tted with a lifting eye.
This lifting eye is not intended to lift the complete assembly with e-motor.
Fig. 2 Lifting Eye

13
4
» Service Manual - Electrical Screw Compressor
INSTALLATION AND REMOVAL
4.1.2 Disconnect the compressor
4.1.3 Mechanical installation
WARNING
Beware of electric shock!
Danger of physical injuries that may have fatal consequences.
Before starting work, switch o the power supply to the electrical connection and prevent it from
being restored without due authorization.
Disconnect the wiring harness.
Remove air inlet pipe from vehicle; plug the compressor inlet pipe ø28 to avoid any contamination.
Disconnect the delivery pipe; plug it (M22x1.5) to avoid any contamination.
Disconnect the 2 coolant pipes; collect the coolant liquid; then plug the tube ø16 to avoid any contamination.
Purge internal pressure: see section 5.1.1.
Unscrew the 4 screws M12 on the e-motor connection ange.
Unscrew the 2 screws M8 at the bottom of the compressor.
Move the compressor a minimum of 20 mm back from the e-motor to disengage the coupling.
Make sure that the plastic coupling star remains with the compressor.
The screw compressor unit is delivered:
- With oil, coupling, and compressor wiring harness.
- Without air lter, xing bolts or dampers.
Compressor fastening interface is made by:
- 2 threaded holes for M8 screws at the bottom of the compressor for chassis attachment.
- 4 holes ø14 in the ange for e-motor attachment (M12 screws).
- Alignment with e-motor: ø100 H7 in compressor ange.
Tightening torques
- M8 screws 25 ± 2 Nm (oiled)
- M12 screws 65 ± 5 Nm (oiled)
Fig. 3 Fastening
4 holes ø14
ø100H7
2 threaded holes M8

14
4
» Y276710 – (EN - REV. 001) | May 2020
INSTALLATION AND REMOVAL
4.1.4 Air connection
Once mechanically installed, the unit must be connected to the air, water and electrical systems. See below the
location of these dierent connections.
Air out
Air in
Air inlet Air outlet
42 Nm max
Fig. 4 Air connection locations
Fig. 5 – Air connection dimensions

15
4
» Service Manual - Electrical Screw Compressor
INSTALLATION AND REMOVAL
4.1.5 Coolant connection
Liquid coolant according vehicle manufacturer specication (mixture of glycol + water).
Water in / Out
Fig. 6 Coolant connection dimensions Fig. 7 Coolant connection locations

16
4
» Y276710 – (EN - REV. 001) | May 2020
INSTALLATION AND REMOVAL
4.1.6 Electrical connection
The wiring harness must be connected for compressor operation.
The compressor is equipped with 2 electrical switches: max temperature & minimum oil level.
The max temperature switch:
- Is required by EN1012-1 to prevent compressor operation in case of overheating.
- Is closed under normal operating conditions, and will open the circuit at 120°C max.
The minimum oil level switch is 24V power supplied and will be activated when maintenance oil level is reached:
- If the level is OK, no signal is supplied.
- If the level is NOT OK, 24V signal is supplied.
The compressor has to be stored in a protected and dry place, at a constant ambient temperature, and shall be
protected against any exposure to ozone and UV rays. The compressor can be safely stored under these conditions
for a period of 2 years.
Storage temperature range: -30°C to +50°C.
TE Connectivity 1170373-1
1 Temperature control
2 Temperature control
3 + 24V
4 Ground
5 Oil level signal
6 Not used
4.1.7 Storage conditions
6 5 4
3 2 1
Fig. 8 Electrical connection location

17
4
» Service Manual - Electrical Screw Compressor
INSTALLATION AND REMOVAL
4.2 Removal
WARNING
Pneumatic system is under high pressure.
Particles ejected, for instance, will cause severe eye injuries.
Observe the safety regulations for pneumatic systems.
Prior to removal, exhaust the pressure from the (sub)system.
CAUTION
Beware of contaminating the pneumatic system!
Device and/or system functions will fail.
Keep out dirt after removal, such as by masking the ports.

18
5
» Y276710 – (EN - REV. 001) | May 2020
Maintenance is basically subdivided into:
- Inspection
- Servicing
- Repair
Maintenance must be performed every 1500 operating hours or at least once a year:
- Changing oil
- Replacing the coalescing lter
- Compressor visual check to track any potential issue (leakages, shocks…)
- Replacing the vehicle air lter, according manufacturer requirements
Operating hours are dened as when the compressor is running.
To estimate the operating hours, use the following calculation:
- Vehicle mileage (d)
- Vehicle average speed (v)
- Bus operating time (t) = d/v
- Estimated duty cycle (tc)
- Compressor operation hours (coh) = t x tc
5 MAINTENANCE

19
5
5
» Service Manual - Electrical Screw Compressor
MAINTENANCE
5.1 Compressor design A: Filling plug
B: Drainage plug (gravity)
C: Drainage plug (vacuum)
D: Coalescing lter
E: Air lter (option)
F: Temperature switch
G: Oil level switch
H: Electrical connector
K: Max pressure valve
L: Min pressure valve
M: Oil Cooler
P: Electrical heater (option)
G
P
A E
H
F C K
B
D
L
M

20
5
» Y276710 – (EN - REV. 001) | May 2020
MAINTENANCE
5.2 Inspection
WARNING
Beware of electric shock!
Danger of physical injuries that may have fatal consequences.
Before starting work, switch o the power supply to the electrical connection and prevent it from
being restored without due authorization.
WARNING
Beware of bolting joints incorrectly!
Damage to the screwed members and the area around them. The following consequences are
imaginable in given mounting scenarios: loss of functionality, damage to motor/compressor set,
derailment due to loss of motor/compressor set mounted under-oor.
The use of impact screwdrivers is prohibited.
WARNING
Pneumatic system is under high pressure.
Personal injury.
Prior to removal, exhaust the pressure from the (sub)system while observing the safety regulations
for electrical and pneumatic systems.
CAUTION
Use of unacceptable working substances!
Damage to equipment, total failure possible.
The oil grade must agree with the installation drawing and/or oil label. Never mix dierent types of
oil.
CAUTION
Hot surfaces!
Danger of burns close to the motor/compressor set.
Allow the surfaces to cool down, and wear gloves for protection.
CAUTION
Incorrect disposal of substances harmful to the environment!
This would mean unnecessary and legally punishable harm to the environment.
Observe the ocially applicable waste disposal regulations.
The external condition of the unit and the system functionality for which the unit is used must be checked at regular
intervals as specied by the vehicle operator.
Table of contents
Popular Compressor manuals by other brands

UK Sound
UK Sound 176 user manual
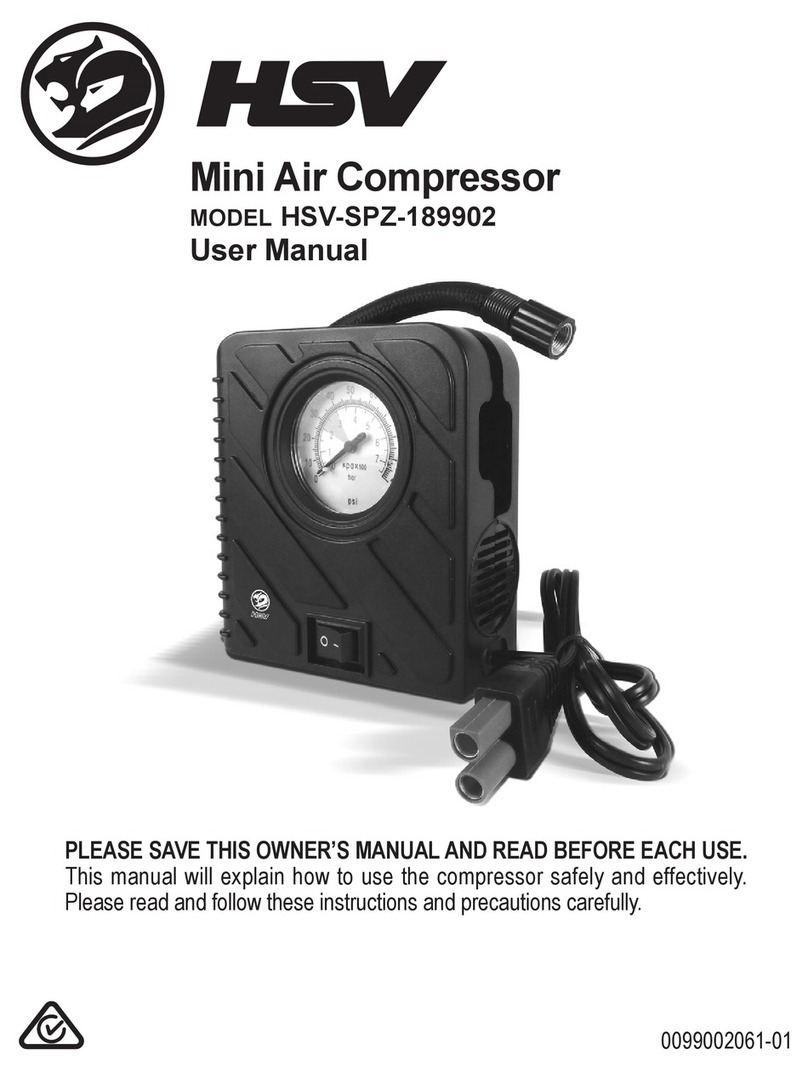
HSV
HSV HSV-SPZ-189902 user manual
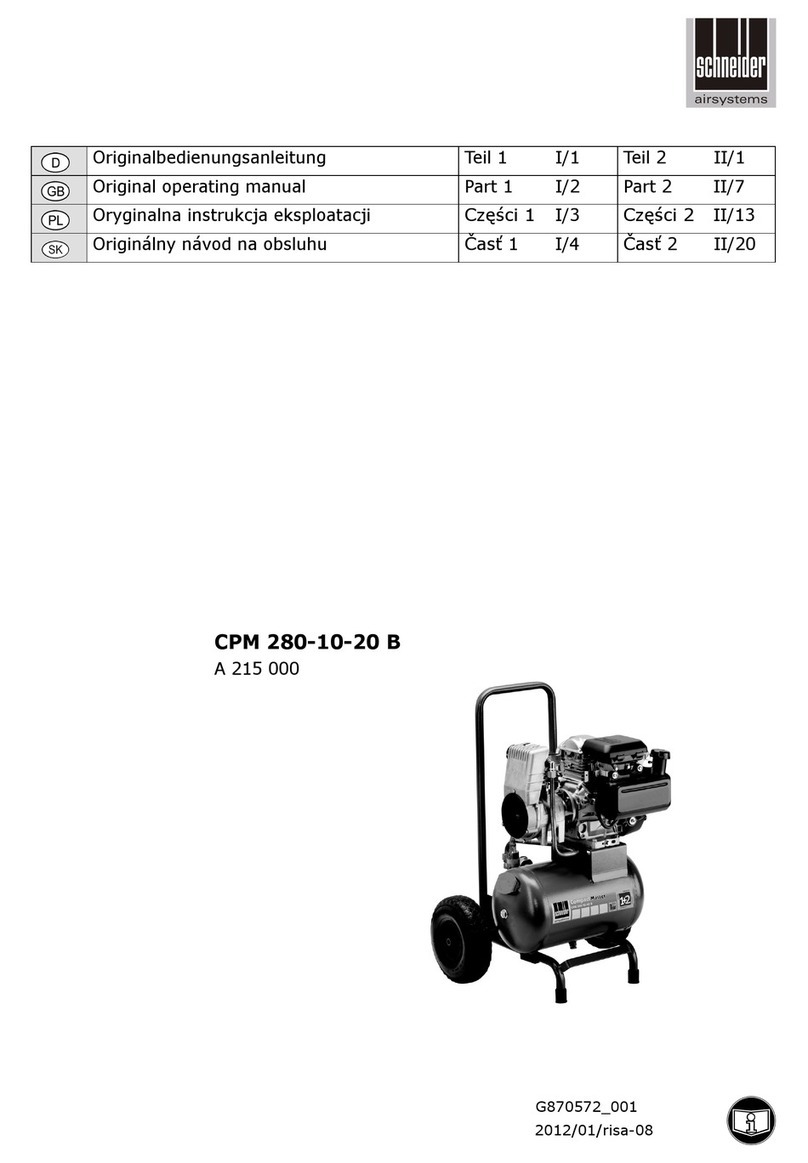
Schneider Airsystems
Schneider Airsystems CPM 280-10-20 B Translation of the original operating manual

Koci Elektromaschinen
Koci Elektromaschinen KC 100 Operating instruction

RAWLINK
RAWLINK 68675 instruction manual
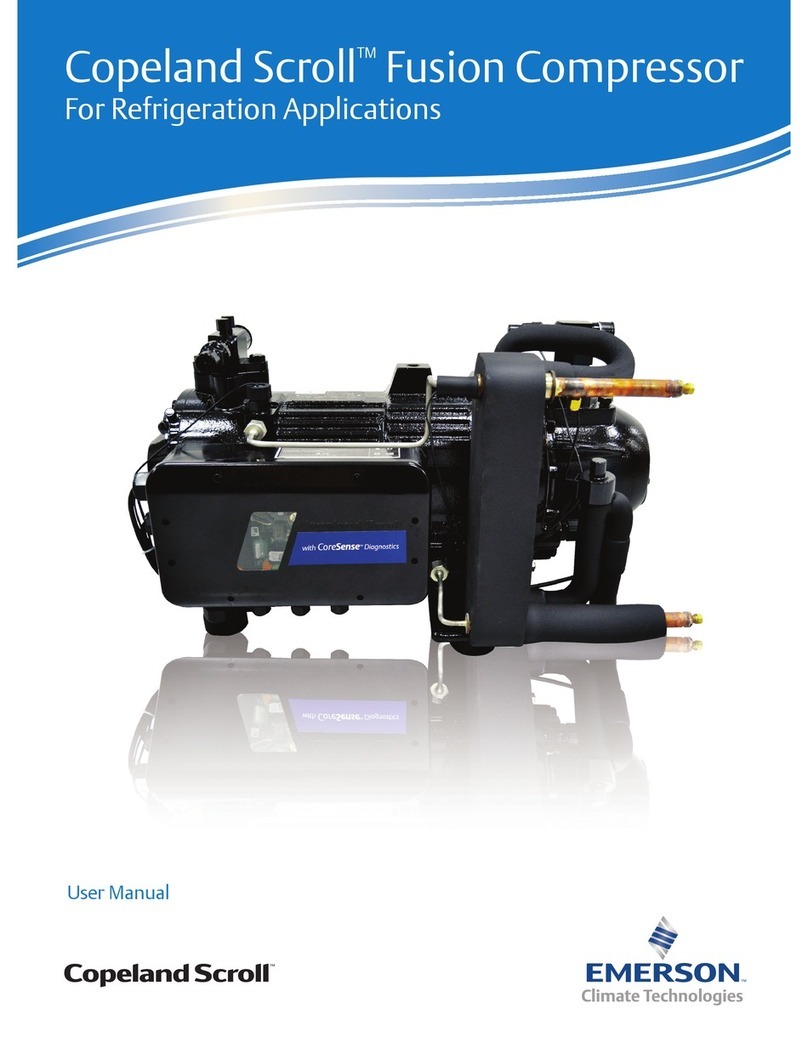
Emerson
Emerson Copeland Scroll QF115L user manual