Koso D52B Operating and maintenance manual

IMO-D52/R52 1
9/21 Rev. 0
DIAPHRAGM
-OPERATED
ACTUATORS
STANDARD SPECIFICATIONS
Installation, Maintenance & Operating Instructions
Model
Diaphragm
(Effective area in
square inches)
Standard
Strokes
(in inches)
D52B / R52B 85 ¾, 1
D52C / R52C 145 1⅛, 1½
D52D / R52D 325 2¼, 3½
Read these instructions carefully before installation or servicing.
WARNING!
FOR YOUR SAFETY AND PROTECTION, IT IS IMPORTANT THAT THE FOLLOWING PRECAUTIONS BE
TAKEN PRIOR TO REMOVING THE VALVE FROM SERVICE OR BEFORE ANY DISASSEMBLY OF THE VALVE:
1. At all times during this procedure, keep hands out of the valve. A remotely actuated valve could close at any
time and result in serious injury.
2. Know what media is in the line. If there is any doubt, check with the proper authority.
3. Wear any protective clothing or equipment normally required when working with the media involved.
4. Depressurize the line and valves as follows:
a.
Open the valve and drain the line.
b.
Close and open the valve to relieve any residual pressure that may be in the valve prior to removing the valve
from service.
c.
After removal and prior to any disassembly, drain any remaining media by placing the valve in a vertical
position and carefully opening and closing the valve several times.
5. The practical and safe use of this product is determined by both the trim and body ratings. Read the name tags
and check both ratings. This product is available with a variety of trim materials. Some of the trim materials have
pressure ratings that are less than the body ratings. All the body and trim ratings are dependent on valve type
and
size, trim material, bolting material, and temperature. Do not exceed these ratings.
KOSO HAMMEL DAHL
CONTROL VALVES
KOSO
HAMMEL DAHL
253
Pleasant Street
West Bridgewater, MA 02379
tel: 774.517.5300
fax:
774.517.5230
www.hammeldahl.com

IMO-D52/R52 2
9/21 Rev. 0
Table of Contents
Installation, Maintenance & Operating Instructions ........................................................................................1
Description ....................................................................................................................................................3
Direct Acting Actuator ................................................................................................................................3
Reverse Acting Actuator ............................................................................................................................3
Receiving and transportation......................................................................................................................3
Storage ......................................................................................................................................................3
Unpacking ..................................................................................................................................................4
Installation.....................................................................................................................................................5
Installation temperature at site....................................................................................................................5
Maintenance space....................................................................................................................................6
Installation position ....................................................................................................................................6
Piping and Wiring work ..............................................................................................................................7
Preparation for Operation and Operation ..................................................................................................8
Preparation for operation ...........................................................................................................................8
Operation ...................................................................................................................................................9
Structure......................................................................................................................................................10
Actuator without manual operation unit ...................................................................................................10
Manual override .......................................................................................................................................11
Principle of Operation ................................................................................................................................12
Direct operation........................................................................................................................................12
Reverse operation....................................................................................................................................12
Daily Inspection and Periodic Inspection ................................................................................................13
Daily inspection........................................................................................................................................13
Periodic inspection...................................................................................................................................13
Troubleshooting and Remedies ................................................................................................................14
Disassembly................................................................................................................................................15
Separating the valve and actuator ...........................................................................................................15
Disassembling the actuator......................................................................................................................16
Assembly.....................................................................................................................................................18
Assembling the actuator ..........................................................................................................................18
Assembling the actuator and the valve ....................................................................................................18
Adjustment after Assembly ......................................................................................................................18
Disposal of Product or Parts .....................................................................................................................19
Maintenance Parts......................................................................................................................................19
These instructions provide information about safe handling and operation of the valve and are subject to
change without notice.

IMO-D52/R52 3
9/21 Rev. 0
Description
Direct Acting Actuator
Model D52 actuators are linear-motion
spring-return pneumatic diaphragm actuators, primarily intended for
use with rising stem type valves. In the “normal” position (no air pressure on the diaphragm), the direct
actuator holds the stem in its retracted position by means of a mechanical spring. Increasing air
pressure
in the upper diaphragm chamber thrusts the actuator stem downward and compresses the spring.
Mounted on pull-stem-to-open valve body assemblies, the direct actuator closes the valve when increasing
air
pressure is applied to the upper diaphragm chamber. Mounted on push-stem-to-open valve body
assemblies, the direct actuator opens the valve when increasing air pressure is applied to the upper
diaphragm chamber. An external spring adjustment permits the spring compression to be changed within
predetermined limits. These actuators are manufactured for
and applied to meet the requirements of the
valve and the service conditions as specified in the sales order and are ordinarily shipped mounted on the
valve body
subassembly and with all accessory equipment mounted, piped, and adjusted.
Reverse Acting Actuator
Model R52 actuators are linear-motion
spring-return pneumatic diaphragm actuators, primarily intended for
use with rising stem type valves. In the “normal” position (no air pressure on the diaphragm), the reverse
actuator holds the stem in its extended position by means of a mechanical spring. Increasing
air pressure
in the lower diaphragm chamber thrusts
the actuator stem upward and compresses the spring.
Mounted on pull-stem-to-open valve body assemblies, the reverse actuator opens the valve when increasing
air pressure is applied to the lower diaphragm chamber. Mounted on push-stem-to-open valve body
assemblies, the reverse actuator closes the valve
when increasing air pressure is applied to the lower
diaphragm chamber. An external spring adjustment permits the spring compression to be changed within
predetermined limits. These actuators are manufactured for and applied to meet the requirements of the
valve and the service conditions as specified in the sales order and are ordinarily shipped mounted on the
valve body subassembly and with all accessory equipment mounted, piped, and adjusted.
Receiving and transportation
This actuator is heavy and therefore needs to be handled carefully and properly, following the
instructions given below. Failure to observe these instructions may cause
serious injuries.
•For hoisting up and down the package containing this actuator, use a suitable
hoisting machine
conforming to the Occupational Health and Safety Law. Do not
allow any person to be beneath
the package being hoisted up, nor operate the
hoisting machine beneath the package being
hoisted up.
•
Storage
(1) It is recommended that the actuator is stored in an as-received packed state before
installation.
(2) Do not store it in a place:
a.
Exposed to rainwater.
b.
Where ambient temperature is higher than 140°F (60°C)
c.
In a dusty environment
d.
In a humid atmosphere
(3) Even when the received actuator has been unpacked for acceptance inspection, it is
recommended that the actuator is repacked as received and stored.
(4) Do not remove the plugs or covers of the wiring port until wiring work is started.
(5) To store the actuator after use, treat it as follows.
a.
Apply rust preventive treatment to the parts that are liable to rust.
b.
Insert plugs or other waterproof treatment to the air-pipe connecting ports and the wiring ports.

IMO-D52/R52 4
9/21 Rev. 0
Unpacking
•When hoisting up the actuator from its packing, use a standard belt suited to lift the actuator. Use
two pairs of lifting rings in a way that the load is applied to them equally. See Fig. 1. However,
if the control valve is hoisted up with the actuator, do not use lifting rings, but hoist the control valve
as illustrated in Fig. 2. Failure to observe these instructions may allow the hoisted control valve to
drop and injure or may cause damage to the actuator.
After unpacking, observe the following precaution to maintain performance of the
actuator.
•If accessories such as positioner, booster relay, solenoid valve and manual operation unit are
attached to the actuator, take care not to apply the load from the lifting belts to them. When you
put the actuator on a floor, do not allow the accessories and the
manual operation unit to
contact the floor directly to avoid them from bearing the load of the actuator.
Fig. 1. Fig. 2.

IMO-D52/R52 5
9/21 Rev. 0
Installation
This actuator is heavy and therefore needs to be handled carefully and properly, following the
instructions given below. Failure to observe these instructions may cause
serious injuries.
•For installing it in your process piping, hoist it using a hoisting machine conforming to the
Occupational Health and Safety Law. Do not allow any person to be beneath the package being
hoisted up, nor operate the hoisting machine beneath the package
being hoisted up.
.
Observe the following items to maintain the performance of this actuator.
•When hoisting up the actuator from its packing, use a standard belt suited to lift its weight. Observe
the warning and cautions given in “Unpacking” Section.
•Do not remove the plugs from air-pipe connecting ports and wiring ports until the
installation
of it to the process piping is completed and the piping or wiring work is started.
•Be careful not to apply a strong impact to it by dropping or hitting while connecting to the process
piping. Otherwise, it might cause failure or require readjustment.
•Secure a sufficient space for maintenance.
•Do not install the actuator in a place subject to strong vibration or where heavy load is applied to it.
Installation temperature at site
In the control valve specification sheet, which is submitted to you after your placement of the order, it
is indicated in which temperature range specifications this actuator was produced. Based upon the
indication, install the actuator in a
place where the ambient temperature is within the following range.
If the ambient temperature does not fall within the permissible range because of radiant
heat or direct
sunlight, provide an appropriate shield or protect the actuator with heat
insulator.
•Standard specification -10 to +70°C 14 to 158°F
•Low-temperature specification -40 to +40°C -40 to 104°F
•High-temperature specification 0 to +100°C 32 to 212°F

IMO-D52/R52 6
9/21 Rev. 0
Maintenance space
Above the control valve, secure a sufficient
space
for replacement of actuator as well as
for inspection of the inside of the control valve.
The dimension “H” does not include
space required for lifting equipment such
as a chain block and hook..
Fig. 3
Installation position
•As a rule, the position of the installed
control
valve should be vertical as
illustrated in Fig. 3.
•If your control valve is equipped with a
manual
override, the control valve
should be installed in a position to
ensure safe and easy operation.
Fig. 4
Actuator size /
model
H
D52B / R52B
24 inches, or more
D52C / R52C
30 inches, or more
D52D / R52D
30 inches, or more

IMO-D52/R52 7
9/21 Rev. 0
Piping and Wiring work
•Use dry and clean instrument air for the operation source of the actuator.
•An appropriate pipe diameter shall be used for instrument air supply piping to such instruments as
positioner, booster relay, etc. so that air pressure will not decrease in piping.
•If order was placed with requirement for mounting of such accessories as positioner, booster relay,
solenoid valve, the air supply piping from these accessories to the
actuator has been completed
prior to shipment. So be careful not to damage the
piping.
•If the actuator is equipped with an accessory, follow the instructions in the operation manual of each
device in instrument air supply piping and instrument wiring.
•Do not use a seal tape for the instrument air supply piping port to an accessory because tape
chips may clog in the piping, causing malfunction of accessory.
•Do not install wiring on a rainy day or in an environment subject to splash of water to avoid electric
leak or damage of the devices.
•Use wires, which have sufficient capacity for keeping the good function of the
accessories.
•Perform reliable wiring work to prevent entry of water or rainwater from external
cable inlets.
(1) For direct connection of signals 3 ~ 14 psig (0.2 ~ 1.0kg/cm2G) from controller to the actuator
Connect an air piping to the instrument air inlet shown in the structural drawing in the “Structure”
section.
(2) For actuator fitted with accessories
Connect pipes and wires to the instruments, referring to the manuals for the
accessories to the actuator.

IMO-D52/R52 8
9/21 Rev. 0
Preparation for Operation and Operation
Preparation for operation
All the adjustments based on the order specification we received have been completed prior
to the delivery from our factory. However, the adjustments might be out of alignment due to
transportation or installation, check the operation of it in combined state
with the on-off
control circuit or the controller after completing the installation.
•If the actuator is equipped with accessories, do not prepare for operation on a rainy day
or in an environment subject to splash of water to avoid electric leak or deterioration of
performance.
•For the accessories which require power supply, before turning on the power, check that
the power supply voltage is equivalent to the voltage displayed on the name
plate of
devices. If not, adjust the voltage to the value on it.
•Use dry and clean instrument air for the operation source of the actuator, and check that
its air-pressure does not exceed the setting air-pressure indicated in the
specifications.
When you change it, please contact Koso America.
•Check that no air leaks from the joint portion of the instrument air piping and the
diaphragm clamping section (the actuator circumference). If any leakage is found,
follow the instructions in the “Disassembling the actuator” section to stop it.
(1) Adjustment of accessories:
When an adjustment is required for accessory, follow the instructions in the operation
manual for each device for adjustment. Use a dial gauge or a stroke detector equivalent
to it to detect a stroke for adjustment of the positioner.
(2) Adjustment of actuator off-balance (See Fig.12 for the encircled parts numbers)
This off-balance does not get out of order during transportation, storage, or
installation. However, when the actuator is separated from the valve body for the
convenience of installation work, follow the procedures shown below to adjust.
•Prepare an air-pressure reducing valve and a pressure gauge equivalent to ASME
B40.100 class.
•Check the spring range and supply air pressure shown on the nameplate attached
to the control valve.
•Keep the hex socket head screw 131, the connector 112 and the indicator 137 in
the same disassembled state as they are when the actuator is separated from
the valve body.
•Close the valve body stem 5.
•Apply the specified air-pressure through the instrument air connection port of the
actuator with using the air-pressure reducing valve and the pressure gauge
equivalent to ASME B40.100 class.
(a) Direct action actuator (the valve closes when the instrument air-pressure is
increased.)
Apply the air-pressure, which is the maximum value of the spring range.
Lower the valve body stem so that the plug contacts the valve seat.
Engage the connector with the threaded portion of the actuator rod 106
and that of the valve stem and fix them firmly with the hex socket set
screws. If they do not engage well with each other, slightly decrease the
air-pressure
from the maximum value of the spring range and engage them
again.

IMO-D52/R52 9
9/21 Rev. 0
Changing air-pressure by the spring range, check that the rod moves as
specified. When a positioner is attached, follow the instructions in the
previous section (1) for adjustment and checking.
(b) Reverse action actuator (the valve opens when the instrument air-
pressure is increased.)
Apply the air-pressure, which is the minimum value of the spring range.
Lower the valve body stem so that the plug contacts the valve seat.
Engage the connector with the threaded portion of the actuator rod 106
and that of the valve stem and fix them firmly with the hex socket set
screws. If they do not engage well with each other, slightly increase the
air-pressure
from the minimum value of the spring range and engage them
again.
Changing air-pressure by the spring range, check that the rod moves as
specified. When a positioner is attached, follow the instructions in the
previous section (1) for adjustment and checking.
Operation
Manual operation: This unit is an optional accessory used to open/close the valve unit
when the air-pressure for operation is not available.
When manual operation is finished, be sure to return the handle shaft to its specified position
(within the distance between a point about 1 mm away from the edge of the
elongate hole on
the MO cover and the edge as shown in Fig. 5 and 6). If it is not returned to the specified
position, rod stroke will be insufficient during automatic operation.
If excessive force is applied when the handle is moved past the specified position, the manual
override may be damaged.
•When the crank handle 205 is turned clockwise, the valve stem 5 moves toward the
valve-closed position. When it is turned counter-clockwise, the valve stem moves toward
the valve-open position.
•For operating the valve in the automatic operation mode, be sure to return the handle to the
specified position as shown in Fig. 5 and 6.
Fig. 5. Direct action (DA) type Fig.6. Reverse action (RA) type Fig.7. Stem adapter

IMO-D52/R52 10
9/21 Rev. 0
Structure
Actuator without manual operation unit
In this actuator, the air-pressure signal from the controller or the air-pressure output from
the positioner
is received by the diaphragm and the intended output and positioning are
achieved in force balance
with the spring. This actuator consists mainly of the steel
diaphragm case, diaphragm, multi-spring
(4 to 8 pieces) and the output shaft.
For each size of the actuator, two types are available. One is the direct action (the valve
closes when
the air-pressure to the diaphragm chamber is increased), and the other is the
reverse action (it opens
when the air-pressure to the diaphragm chamber is increased).
Fig. 8. D52B and D52C
Structure of direct-action type and part names
Fig. 9. R52B and R52C
Structure of reverse action type and part names
No.
Name
101
Yoke
102
Diaphragm upper case
103
Diaphragm lower case
104
Diaphragm plate
105
Stopper
106
Actuator rod
107
Guide holder
108
Diaphragm
109
Spring
110
Spring seat
111
Center plate
112
Connector
113
Scale plate
115
Hanging ring
120
Dry bearing
121
Hexagon bolt
122
Hexagon nut
123
Hexagon bolt
124
Hexagon nut
125
Hexagon bolt
126
Spring washer
127
Seal washer
129
O-ring
130
O-ring
131
Hexagon socket head bolt
132
Hexagon socket set screw
133
Small cap screw
134
Speed nut
137
Indicator
138
Exhaust plug
140
Hexagon bolt

IMO-D52/R52 11
9/21 Rev. 0
Manual override
The manual operation unit is an optional accessory used to open and close this control
valve when
operational air supply is not available. The structure is shown in Fig. 10 and 11.
(1) Model: D52B/R52B, D52C/R52C
Fig. 10. Direct action type Fig. 11. Reverse action type
No.
Name
No.
Name
No.
Name
201
MO cover
209
Thrust ring
221
Conical washer for hex socket head
202
Worm and handle shaft
210
Guide shaft
222
U-nut with cap
203
Worm wheel
215
DU bushing
223
Spring washer
204
Screw rod
216
DU bushing
224
DU bushing
205
Crank handle
217
C-ring
225
Grip
206
Slide nut
218
C-ring
226
C-ring
207
Worm wheel guide
219
Key
227
C-ring
208
Worm guide holder
220
Hex socket head bolt
228
Key

IMO-D52/R52 12
9/21 Rev. 0
Principle of Operation
See Fig.8, 9 and 12 for the encircled part numbers.
Direct operation
In the direct action (DA) type, the valve closes when the air-pressure to the diaphragm chamber
increases. When air-pressure is supplied from the instrument air connecting portion the diaphragm upper
case 102 to the diaphragm chamber, which consists of the diaphragm upper case, the diaphragm 108
and the diaphragm plate 104, both of which are closely set together, are activated to press down the
spring 109 and move downward. At the same time, the actuator rod 106 fixed with the diaphragm and
the diaphragm plate moves down.
Subsequently the movement of the actuator rod is transferred to the valve stem 5 via the connector
112 to move it to the valve-close position. Then when the air-pressure to the diaphragm chamber is
decreased, the diaphragm, the diaphragm plate and the actuator rod move upward by means of the
reaction force of the spring and the stem also moves toward the valve-open position.
Reverse operation
In the reverse action (RA) type, the valve opens when the air-pressure to the diaphragm chamber
increases. When air-pressure is supplied from the instrument air connecting port on the diaphragm lower
case 103 to the diaphragm chamber, which consists of the diaphragm lower case, the diaphragm 108
and the diaphragm plate 104, both of which are closely set together, are activated to press up the spring
109 and move upward. At the same time, the actuator rod 106 fixed with the diaphragm and the
diaphragm plate moves upward.
Subsequently the movement of the actuator rod is transferred to the valve stem 5 via the connector 112
to move it to the valve-open position. Then when the air-pressure to the diaphragm chamber is
decreased, the diaphragm, the diaphragm plate and the actuator rod move downward by means of the
reaction force of the spring and the stem also moves toward the valve-closed position.

IMO-D52/R52 13
9/21 Rev. 0
Daily Inspection and Periodic Inspection
Daily inspection
Perform daily inspection for the control valve are important for process operation.
•Check that air is not leaking from the instrument air pipe connecting port to prevent malfunction.
•If a positioner is provided, check that hunting is not occurring, and the movement of the stem is
smooth.
•Check that abnormal noise and vibration is not occurring in the control valve and the
piping.
If abnormality is found in daily inspection and yet countermeasures cannot be taken immediately,
perform maintenance by disassembly when the plant can be suspended or ask KOSO’s service
representative in charge for repair.
Periodic inspection
Monthly or bimonthly inspection
Perform the following inspections for all the control valves.
•To prevent malfunction, check that air is not leaking from the instrument air pipe
connecting
port.
•If a positioner is provided, check that hunting is not occurring, and the movement of the stem is
smooth.
•While making adjustment, check that abnormal noise and that vibration is not
occurring in the
control valve and the piping.
If abnormality is found in the inspection, and yet countermeasures cannot be taken immediately,
perform maintenance by disassembly when the plant can be suspended, or ask KOSO’s service
representative in charge for repair.
Yearly or biennial inspection and maintenance
Perform inspection, check, lubrication, replacement, etc. for the following items.
•Lubricate the frictional section of the actuator rod and manual operation unit. Use plant approved
lubricants. The factory used lithium grease.Consult factory for additional help.
•Check the O-rings, seal washer and dust seal (optional) for wear.
•Check that there is no flaws such as cracks on the diaphragm.
•Check the bolts and nuts for material loss from wear and corrosion.
•If any defective part is found, replace it with new one.

IMO-D52/R52 14
9/21 Rev. 0
Troubleshooting and Remedies
Symptom
Cause
Remedy
No or slow operation
•Decrease of supply air-pressure
•Supply the specified air-pressure.
•Clogging or leakage from the air
piping
•Clean the piping, retighten the
connecting portion or re-arrange the
piping.
•Air leakage from the clamping parts of
diaphragm
•Retightening, disassemble and repair
(replacement)
•Air leakage from the actuator rod unit
•Disassemble it to replace the O-ring.
•Issue with the accessories such as
positioner, booster relay, solenoid
valve and lock valve
•Apply the specified air-pressure
directly to the instrument air
connecting port of the actuator, not
through the accessories. If no
anomaly is found with it, re-adjust the
booster relay and positioner or check
the accessories and replace them.
•Issue with the actuator
•Disassemble and repair the actuator.
•The manual operation handle is set in
the manual operation position.
•Set the handle to the position shown
in Fig. 5 or 6 in “Operation” section.
•Sensitivity of the positioner is
insufficient.
•Follow the instructions in the operation
manual for the positioner and replace
the capacitor spring.
Instable operation
(hunting)
•Load change by the control fluid
(Insufficient output of the actuator)
•Enlarge the size of the actuator.
•Signal perturbation of the controller
•Change the respective setting of the
controller.
•Fluctuation of supply air pressure
•Re-check the diameter of supply air
piping. Replace it.
•Malfunction of the pressure reducing
valve
•Repair the pressure reducing valve or
replace it.

IMO-D52/R52 15
9/21 Rev. 0
Disassembly
Please follow below instructions when disassembling this actuator.
Separating the valve and actuator
Follow the procedure indicated below.
•Follow the instructions given below for separating, ensure not to damage the valve seat
surface.
•For the direct-action type, reduce the air-pressure within the diaphragm
chamber to zero
(valve-open state).
•For the reverse action type, apply air-pressure to the diaphragm chamber and keep the
valve 10 to40% open.
•Loosen the hex socket head bolt 131, which fastens the connector 112 shown in Fig. 12, to
remove the indicator 137. The state is to be as shown in Fig. 13.
•Apply a rectangle-tipped chisel to the
concave section of the yoke nut17
and hit it
with a hammer to loosen the
nut as shown
inFig. 14.
•When the hex socket set screw 132 in
Fig. 14 is loosened, the
actuator can be
separated from the
valve unit.
When installed on a Hammel Dahl control valve,
the stem 5 will include a stem adapter as shown
in Fig. 12A. When valve maintenance is
required, remove the stem adapter 5A and hex
jam nut 5B.
•Lower the hex jam nut, separating it from
the stem adapter.
Unthread the stem adapter and then the jam
nut, removing both from the valve stem 5.
Fig. 12.
Fig. 12A. Fig. 13. Fig. 14.

IMO-D52/R52 16
9/21 Rev. 0
Disassembling the actuator
See Fig. 8 and 9 for circled part numbers.
Take care not to damage the diaphragm front/rear surfaces and the actuator rod surface during
disassembly work.
Do not disassemble the assembly of the diaphragm and actuator rod unless any anomaly is found in
a visual inspection of the following parts.
Parts to be inspected: The diaphragm front/rear surfaces and the actuator rod surface.
(1) Removing the accessories
When the accessories are mounted on the actuator, remove the air piping and electric
wiring
carefully and then the device itself.
(2) Disassembly of the direct-action type
•Do not loosen the hex nuts 122 to which the hanging ring 115 is attached. Loosen the other
hex nuts 122 and remove the hex bolts 121.
•Loosen the hex nuts, which fasten the two long hex bolts 140, equally and remove these two
bolts. These two pieces each of long hex bolts and nuts set the initial load of the spring.
When these hex bolts are removed, the
spring is at free length.
•Remove the diaphragm upper case 102.
•In this state, pull out the diaphragm/actuator rod assembly (the diaphragm 108, the
diaphragm 104, the actuator rod 106, the center plate 111 and the hex bolt 123) from the guide
holder 107.
•Remove the springs 109, the stopper 105 and the spring sheet 110.
When disassembling the diaphragm/actuator rod assembly, follow the instructions shown below.
•The joint between the hex bolt 123 and the actuator rod is coated with screw lock to prevent
from loosening. For loosening the hex bolt, tighten the double hex nut on the threaded portion of
the actuator rod for mounting the connector and loosen the hex bolt while fixing that nut with a
spanner wrench. And then the diaphragm/actuator rod assembly can be disassembled.
•When the hex bolts 125 are loosened and removed, the diaphragm lower case 103, the
spring washers 126 and the guide holder can be separated from the yoke 101.
Disassembly is completed with the above procedures. Check all the parts and replace
them with new
parts when any damage is found with them.
(3) Disassembly of the reserve action type
•Do not loosen the hex nuts 122 to which the hanging ring 115 is attached. The hex bolts 140
with the handing rings 115 are longer than the other hex bolts 121. Loosen the other hex nuts
122 and remove the hex bolts 121.
•Loosen the hex nuts, which fasten the two long hex bolts 140, equally and remove these two
bolts. These two pieces each of long hex bolts and nuts set the initial load of the spring. When
these hex bolts are removed, the spring is at its free length.
•Remove the diaphragm upper case 102.Remove the spring and the spring seat 110.
•In this state, pull out the diaphragm/actuator rod assembly (the diaphragm 108, the diaphragm
plate 104, the actuator rod 106, the center plate 111, the stopper 105, the hex bolt 123 and the
spring washer or the hex nut 124) from the guide holder 107.
•Follow the instructions shown below for disassembling the diaphragm/actuator rod
assembly.
•Threaded joint of the Diaphragm plate 104 and the actuator rod 106. Loosen the hex nut
124 and remove the hex bolt 123. Using a vise to hold the diaphragm plate, remove the hex

IMO-D52/R52 17
9/21 Rev. 0
nut 124. Tighten the double hex nut on the threaded portion of the actuator rod for mounting
the connector. And then loosen and remove the actuator rod 106 from the diaphragm plate
104 by utilizing the double hex nuts and fitting with a
spanner wrench.
•When the hex bolts 125 are loosened and removed, the seal washers 127, the diaphragm
lower case 103 and the guide holder 107 can be separated. The O-ring 130 attached to the
guide holder can also be removed.
Disassembly is completed with the above procedures. Check all the parts and replace
them with new
ones if any damage is found.
(4) Disassembly of the manual operation unit
•When the hex socket head bolt 220 is removed, the manual operation unit can be removed
from the yoke 101. The parts within it can be checked in this state. If no damage is found, it is
not required to disassemble it. If any damage is found, contact our service department to
repair it or replace it with a new one.
•When the U-nut with a cap 222 is removed, the crank handle 205 and the grip 225 can be
removed.
•The C ring is removed and the guide axis 210 is removed from the MO cover 201.
•Slide nut assembly (the screw rod 204 and the key 228) can detach by removing C ring 226
from the MO cover 201.
•When the C-ring 217 of the slide nut assembly is removed, the worm guide holder 208 and
the worm and handle shaft 202 can be disassembled.
•When the C-ring 218 of the slide nut assembly is removed, the worm guide holder 207 and
the worm wheel 208 can be disassembled.
Disassembling is completed with the above procedures. Check all the parts and replace them with new
ones if any damage is found.

IMO-D52/R52 18
9/21 Rev. 0
Assembly
Assembling the actuator
When assembling the actuator, reverse the disassembling procedure found in “Disassembling the actuator”
section. Replace the worn or damaged parts, if found, with new ones. Supply the lubricant, shown in the
“Periodic Inspection” section, to the sliding surfaces of actuator rod, torque lever, roller unit and manual
operation unit.
When assembling the diaphragm, be sure that the rubber side (KOSO mark side) is the side, to which air
pressure is applied.
Be sure to use new parts for the o-ring 130.
Replace the diaphragm 108 and the packing 117 about every 5 years.
Assembling the actuator and the valve
Assemble the actuator and the valve unit as follows.
•Set the yoke in the same position as before disassembling it and fix it with the hex socket set screw
132. Then completely tighten the yoke nut to reverse direction as shown in Fig. 13. Use the same tools
and procedure, which were used for separating them.
•Lower the stem 5 and check that the plug contacts the valve seat surface.
•When installed on a Hammel Dahl control valve, the stem 5 will require a stem adapter as shown
in Fig. 12A. Prior to installing the stem connector, install the stem adapter and locking nut.
•Thread the locking jam nut to the bottom of the valve stem thread, allowing the nut to remain
loosely fitted.
•Thread the stem adapter onto the valve stem completely. No additional torque is required.
•Thread the locking jam nut toward the stem adapter, contacting the stem adapter and with
sufficient force to lock the adapter in place.
•Follow the instructions given in the “Operation” section-(2) “Adjustment of actuator off-balance”.
Adjustment after Assembly
On completion of the assembly, check the following. If there are any trouble, disassemble the unit, find and
remove the cause, and then reassemble it again.
•Apply the specified air-pressure to the actuator and check that it operates smoothly.
•Check that the leakage quantity of the valve seat is within the specified value.
•Check the hysteresis and linearity are within the specified values.
Follow the instructions in “Installation” for mounting the assembly on the piping after adjustment of it.

KOSO HAMMEL DAHL
253 Pleasant Street
W. Bridgewater MA 02379
Telephone: 774.517.5300
Fax: 774.517.5230
www.hammeldahl.com
Disposal of Product or Parts
Dispose of the product or its parts, consigning it to an industrial waste treatment services authorized by the
governor of prefectural governments, or to a local municipal entity undertaking the disposal, according to the
“Waste Disposal and Public Cleansing Law.”
Maintenance Parts
Maintenance parts or expendables for replacing worn or damaged parts are available by ordering to any local
distributors of our representatives listed below.
This manual suits for next models
5
Table of contents
Other Koso Controllers manuals
Popular Controllers manuals by other brands
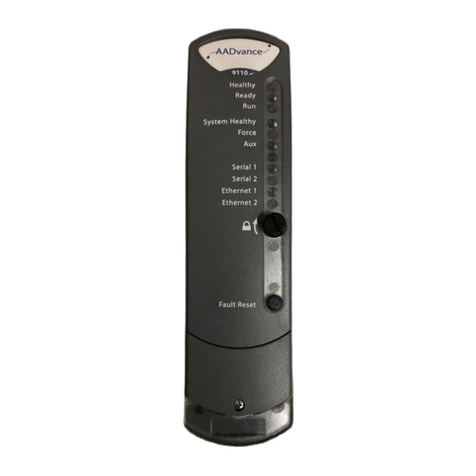
Rockwell Automation
Rockwell Automation Allen-Bradley AADvance T9110 Troubleshooting and Maintenance Manual
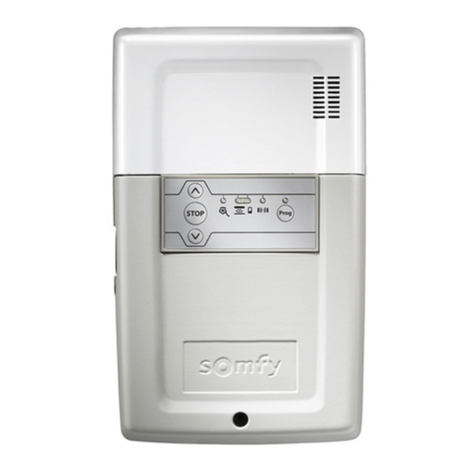
SOMFY
SOMFY ROLLIXO user manual
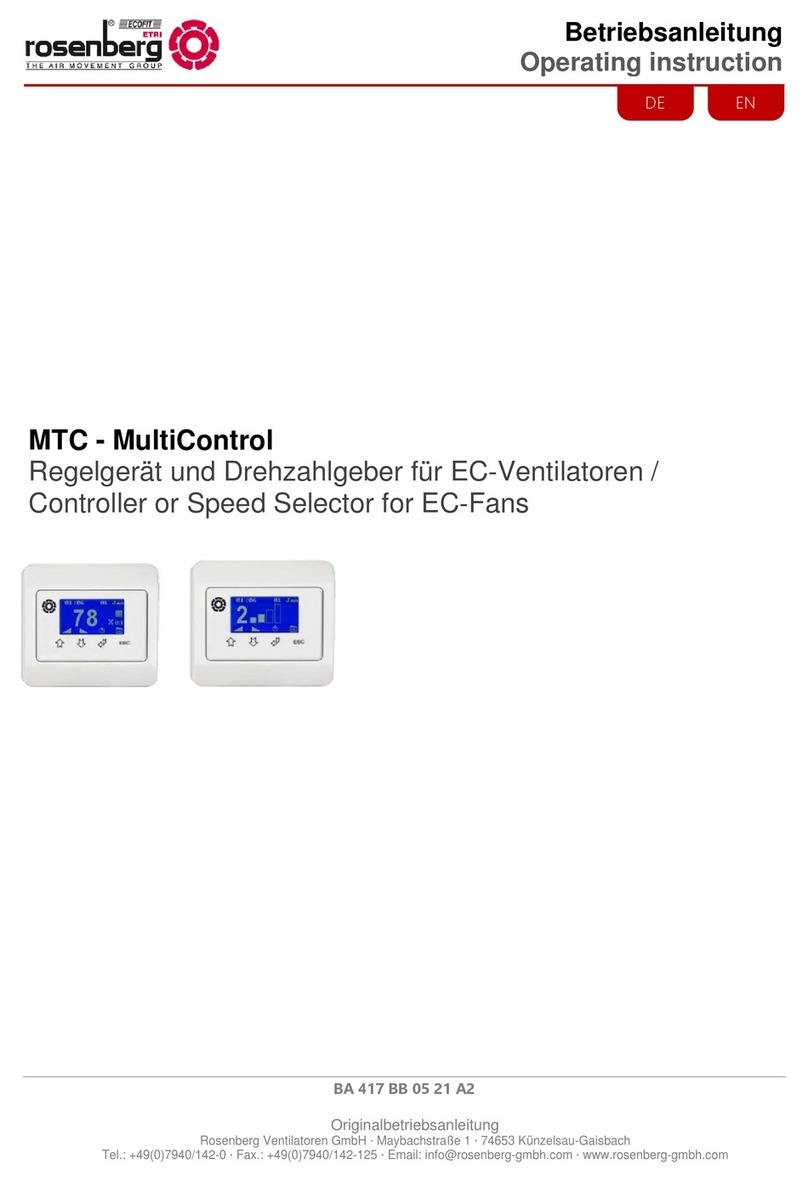
Rosenberg
Rosenberg MTC H55-00077 Operating instruction
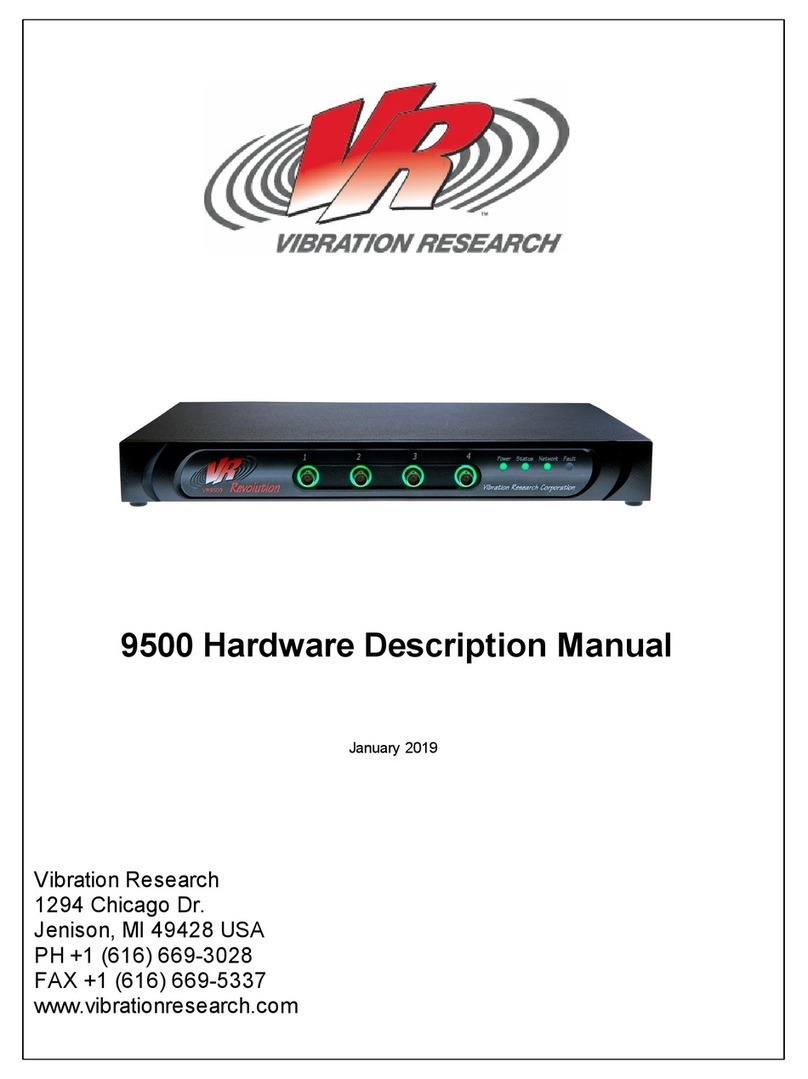
Vibration Research
Vibration Research VR9500 Hardware Description Manual
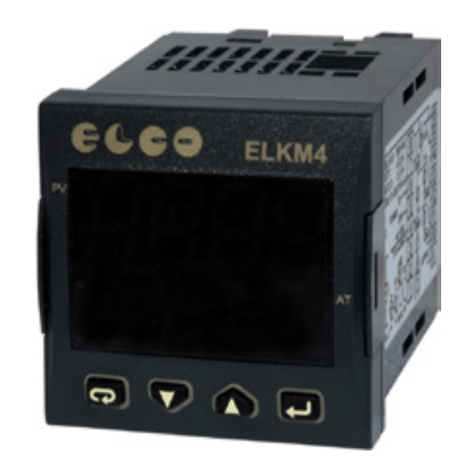
elco
elco ELKM43 quick guide
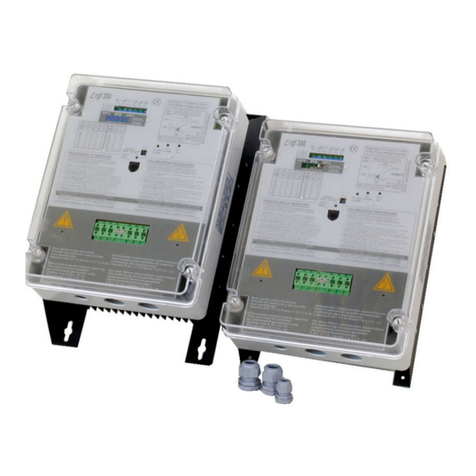
Eliwell
Eliwell RGF 312 manual