Label Vista SMP User manual

AUTOMATIC
UNDERFLOOR
SWING DOOR
DRIVE
Vista SMP- Drive
Unit
Operator for
automatic swing
doors
English
Translation of the ORIGINAL INSTRUCTIONS
VISTA-SMP-16005_GB_Rel.2.2_09/2016 - CD0420GB

INDEX:
GENERAL SAFETY WARNINGS
page 4
GENERAL SAFETY OBLIGATIONS
4
1)
MODEL DESCRIPTION
5
2)
TECHNICAL SPECIFICATIONS
5
MECHANICAL SECTION
3) COMPONENTS OF THE VISTA SMP OPERATOR
6
4)
PRELIMINARY CHECKS
7
5)
TECHNICAL DRAWINGS
8
5.1) POSITION OF THE OPERATOR USING 76MM GLASS RAIL WITH DOUBLE ACTION ACCESSORIES
8
6) SITE PREPARATION
9
6.1) Main Control box –installation 10
6.2) Floor unit –drive housing/cradle installation
10
6.3)
Cut out prep/mounting cradle install
steps
11
7) POWER SUPPLY
12
8) CONTAIMENT
12
8.1) Example containment double door
12
8.2) Example containment single door
13
8.3) Control panel to floor operator wiring
13

ELECTRONIC SECTION
9) ELECTRICAL CONNECTIONS
14
10) NOTES
15
11) PWN-T POWER SUPPLY MODULE AND ELECTRIC WIRING
16
12) L-NEP LOGIC BOARD
18
13) N-DSEL DIGITAL PROGRAMMER –SCOPE AND CONNECTIONS
18
14) COMMISSIONING OF AUTOMATED DEVICE (INITIAL SET-UP)
19
14.1) FIRST START OF N-DSEL DIGITAL PROGRAMMER
19
14.2) USE OF N-DSEL DIGITAL PROGRAMMER
19
14.3) SERIAL COMMUNICATION SET-UP
19
14.4) INITIAL SET-UP
20
14.5) FUNCTIONAL TESTING
22
14.6) INPUTS DIAGNOSTICS
22
15) PROGRAM SELECTORS
23
15.1) MANUAL PROGRAM SELECTOR
23
15.2) EV-MSEL MECHANICAL KEY SELECTOR
23
15.3) N-DSEL DIGITAL PROGRAMMER USED LIKE PROGRAM SELECTOR
24
16) GENERAL PROGRAMMING MENU
26
17) FUNCTIONS AND REGULATIONS
27
17.1) FUNCTIONS SETTING
27
17.2) PARAMETERS SETTING
31
18) LANGUAGE
35
19) PASSWORD MANAGEMENT
35
19.1) HOW TO CHANGE THE TECHNICAL PASSWORD
36
19.2) HOW TO CHANGE THE PRIMARY PASSWORD
36
19.3) HOW TO CHANGE THE SERVICE PASSWORD
37
19.4) ENABLING USER (primary and service) PASSWORD USAGE
38
19.5) DEACTIVAING THE USER PASSWORD USAGE
38
20) INFORMATION AND EVENTS MEMORY
39
21) MAINTENANCE
42
22) ELECTRIC LOCK APPLICATION
42
22.1) ELECTRIC LOCK / ELECTRIC STRIKE
42
22.2) MAGNETIC LOCK
43
23) SAFETY SENSOR DEVICES
43
23.1) SENSOR OA-EDGE T
43
23.2) SENSOR 4SAFE ON SW
44
23.3) SENSOR TOPSCAN-S
44
24) EN/RF1 RADIO RECEIVER
45
25) DISABLED PEOPLE COURTESY FUNCTION
46
26) DOUBLE LEAF DOOR SET
47
26.1) ELECTRICAL WIRING FOR A DOUBLE LEAF DOOR SET
47
26.2) DOOR SET-UP
47
26.3) FUNCTIONAL TESTING
50
26.4) PEDESTRIAN OPENING
50
26.5) CONSIDERATION ON THE USE OF N-DSEL PROGRAMMER IN A DOUBLE DOOR SYSTEM
51
27) INTERLOCK SYSTEM
52
27.1) INTERLOCK ELECTRIC CONNECTION
52
27.2) INTERLOCK APPLICATION WITH INDEPENDENT INTERNAL RADAR
52
27.3) INTERLOCK APPLICATION WITH ONLY ONE INTERNAL RADAR
53
28) MEANING OF THE ACOUSTIC SIGNAL
54
DECLARATION OF INCORPORATION OF PARTLY ASSEMBLED MACHINERY
55

GENERAL SAFETY WARNINGS
Carefully read this instruction manual for the safe installation and operation of the automatic
door. Improper installation and incorrect use of the product could cause serious injury.
Keep the instruction manual for future reference.
The installer must provide all the information about operation and provide the system user with the user manual delivered
with the product.
MEANING OF THE SYMBOLS USED IN THESE INSTRUCTIONS
DANGER: Indication of dangerous situations that could cause material damage and personal injury.
WARNING: Identifies the procedures that must be understood and followed to prevent product damage or malfunctions.
NOTE: To point out and place attention on important information.
GENERAL SAFETY OBLIGATIONS
The mechanical and electric installation must be performed by specialised personnel in accordance with current directives
and regulations.
The installer must make sure that the structure to be automated is stable and robust and if necessary, make it this way by
making structural modifications.
Keep product and packaging materials out of children's reach, as they might be a source of
danger. Do not let the children stay or play within the range of the door.
This product was designed and built exclusively for the purpose described in this documentation. Any other use that is not
specifically indicated could adversely impact the condition of the product and the safety of people.
iSee Access Solutions accepts no responsibility for incorrect product installation and usage, as well as for any damages
caused by changes made without its prior consent.
iSee Access Solutions is not responsible for the construction of the fixtures to be motorised.
The IP67 degree of protection requires that the operator is installed exactly as per the installation instructions.
This product cannot be installed in explosive environments or atmospheres, or in the presence of flammable gases or
fumes.
Make sure that the characteristics of the electric distribution network are compatible with the technical data indicated in this
manual and that upstream of the system there is a double pole isolation switch with an opening distance of the contacts of
at least 3mm and a 30mA residual current device.
Ensure the electric circuit is fully earthed.
The automatic door must be checked, started up and tested by an iSee Access Solutions trained engineer and
commissioned to EN16005.
A risk assessment must be conducted for every automation as required by the Machine
Directive. Disconnect the power supply before working on the automation and before
opening the cover of the control panel.
Maintenance is of fundamental importance for the proper operation and safety of the automation. Check the efficiency of all
parts every six months.
Use only original spare parts for maintenance and when replacing product components.
Cleaning operations must be performed with the power supply disconnected, using a damp cloth. Do not deposit or let
water or other liquids penetrate into the floor operator or the accessories that are part of the system.
It is recommended to take out a maintenance contract.
Risk assessment
The automatic swinging doors must be designed and installed in a way to protect users against the risk and danger of
crushing, impact and shearing between the door and adjacent parts near the door.
The person responsible for starting-up the automation must perform a risk assessment based on the place of installation
and the type of users that could use the automatic door.
The Vista SMP underfloor operator, as required by EN16005 standard, must be equipped by protection devices (sensors) in
accordance with EN12978
A = Main closing edge
B = Secondary closing edge
C = Opposite closing edge
The dangers of crushing and shearing related to the secondary closing edge must be prevented
either structurally or by supplementary protective measures (25mm rubber profile, rollerblind FG).
Any residual risks must be properly signalled.
4

1) MODEL DESCRIPTION
The Vista SMP underfloor operator has an electro-mechanical motor for opening the pedestrian swing doors.
The electronic control equipment is located inside the control panel.
The Vista SMP underfloor operator can be used with a single or double action straps and top centres
All models are reversible, therefore in the case of a power failure the door can be opened manually.
Before starting with assembly check the technical drawings and specification chart that provides the weight limits based on the
height and width of the door leaf.
The technical data provided in the charts refers to a typical installation, but the data can be influenced by variables present in every
system, such as friction, environmental conditions, alignment of the leaf hinge, etc....
2) TECHNICAL SPECIFICATIONS
POWER SUPPLY
115/230Vac +/-10%, 50-60Hz
POWER
120W
POWER SUPPLY OF EXTERNAL ACCESSORIES
24Vdc, 1A
ELECTRIC MOTOR
24Vdc
FLOOR UNIT
525 x 135 x 130 mm
WEIGHT
15 Kg. (floor box & control panel)
PROTECTION DEGREE
IP67
AMBIENT TEMPERATURE
-15°C +50°C
FREQUENCY OF USE
continuous
LIMIT SWITCH AND ANTICRUSHING SAFETY
encoder controlled
REACTION TO OBSTACLES
reversal of direction
OPENING TIME for 95°
4 - 12 seconds adjustable
CLOSING TIME for 95°
5 - 15 seconds adjustable
PAUSE TIME
0 - 20 seconds adjustable
REFERENCE VALUES FORCE
Vista
SMP
Motor
Min
Max
AUTOMATIC CLOSING TORQUE (Nm)
60
85
AUTOMATIC OPENING TORQUE (Nm)
60
85
5

MECHANICAL SECTION
3) COMPONENTS OF THE VISTA SMP OPERATOR
Floor unit & Cradle –525mm long x 135mm wide x 135mm high
Control panel –Single - 430mm long x 110mm wide x 120mm deep
Double –550mm long x 110mm x 120mm deep
6

4) PRELIMINARY CHECKS
Before assembling the automation, make sure the following requirements have been met:
•The door frame structure must be solid and must not show any significant deformations.
•The leaf structure must be rigid and robust.
•The leaf pivots must be suitable and in a good condition.
•The dimensions and weight of the leaf must lie within the operating limits of the operator (max. recommended 2.45m2
–150KG).
•The leaf must move in a regular manner without friction along its entire stroke.
•The door requires mechanical end stops consisting of a mechanical retainer in the opening position and a final
stopper when closed.
The door stop for the open position is not supplied with the operator.
7

5) TECHNICAL DRAWINGS
5.1 Double action door strap
FFL
100
65
525
135
Standard Dorma bottom rail insert to
recieve bottom pivot
Vista Underfloor Operator
75
24
33 42
32
12
Elevation
Section
Vista Underfloor Operator
12
FFL
Standard Dorma bottom rail insert to
recieve bottom pivot
Standard Dorma 100mm bottom rail
2
10
130
135
100
8

6 Site Preparation
This part is intended to help in the setting out and installation of the drive into the floor.
Your Vista SMP underfloor door system may not necessarily have all the possible operating elements described
within. Refer to the project specification for clarification of the operating elements supplied.
Please read through the following sections carefully, paying particular attention to dimension and accuracy of
setting out. Mistakes made during the early stages of installation can be costly in terms of time and money. IF IN
DOUBT ASK.
Caution: To prevent damage to the drive:
It is essential to fit door stops for the door in both open and closed
positions. These can be fitted just prior to hanging door leaves but
provision in terms of location and suitable choice should be considered in
advance (barrier with built in stop in open areas). The drive may not be
commissioned without correctly fitted door stops.
NOTE: Example layout diagrams and specifications in this document are for example/guidance purposes only and
reference should be made to your project specification for full details of equipment sup-plied.
9

6.1 Main control box installation
The control box houses all the electrical control boards for the drive unit(s). It is located remotely from the drive
up to a maximum of 10m.
The location should be chosen with consideration to accessibility for adjustment and maintenance, where
possible it should be located in sight of the drive.
The box is surface mounted using suitable fixings. For a single and double drive installation the control box
measures 430mm high x 110mm width x 120mm depth for a single operator and 550mm x 110mm x 120mm for
a double operator system.
6.2 Floor unit - Drive housing installation
The cut out/excavation required for the floor box at a minimum is: 150mm(W) x 560mm(L) x 140mm(D). The
position of the drive depends on the variation of pivot used for hanging the door leaves (single/double action straps
or roller guide).
The floor unit is provided with a ‘mounting cradle’that must be correctly installed and positioned before the motor
unit is applied.
Mounting cradle
Dimensions –525mm long x 135mm wide x 120mm high
The mounting cradle has been designed to offer the floor unit a secure fixing before concrete is applied to maintain
the IP rating of the operator.
The cradle is U-shaped with two positioning slots, four fixed fixing holes and a pivot point hole on the base, and
four slots to ensure exact location of the motor casing (two on each side).
10

6.3 Cut out mounting cradle –installation steps
Step 1: Place cradle in cut out in floor with the pivot point hole nearest the hinge side of the door.
Step 2: Plumb down from the top pivot and ensure the pivot point hole of the cradle is aligned.
Step 3: Fix the cradle into place via the two positioning slotted holes using countersunk screws (screw length to be
determined by installer). This will allow a slight movement and offer a final adjustment to align the floor unit with the centre
line of the door and also align the pivot point with the top centre.
Step 4: Fix the cradle via the four fixing holes using countersunk screws (screw length to be determined by installer to offer
secure fixing). Remove the screw from the slotted holes.
Step 5: Place the motor unit into the cradle locating the threads into the slots on the side of the cradle.
Step 6: Secure motor unit into place by tightening nuts on threads.
Step 7: Make good, by filling in void around floor units with concrete/cement
Cement box end
view
Floor cut out
Cut out mounting
cradle
Motor box
Caution: For correct installation it is essential:
The top of the steel primary cover is mounted exactly flush with FFL.
The box is aligned exactly parallel to the door opening.
The box is positioned to match that of the door pivot.
The box is firmly secured in position.
The box is protected from damage
Debris prevented from entering the conduit ends.
Door stops at 0 degree & fully open position are fitted to prevent
damage to drive
11

7) Power supply
A single-phase 230V, 5A fused supply is required to the control box. The supply must be protected with a 30
mA residual current circuit breaker device conforming to BS 4293:1983. In accordance with BS EN 60204-
1:1993 a means of electrically isolating the mains supply adjacent to the door should also be provided.
8) Containment
Containment 1 No. 20mm conduit is required from the drive housing to the control box (ensure the flexible
conduit is compatible with the Type A –Adaptalok ATS conduit gland). The drive is supplied with an
Adaptalok ATS IP68 Rated 20mm flexible conduit connector gland loose in the floor unit.
Recommended Adaptalok conduit types to suit the Adaptalok gland supplied with floor unit –Type PA, PL,
CP, PR & PADL
www.adaptaflex.com
Depending on the application some or all of the following 20mm conduit containment will be required from
the control box to:
•Program switch
•Activation devices
•Fire Alarm interface
•Door mounted safety sensors
Where an interface to the fire alarm is required, the signal cabling from the fire alarm system must be brought
to the control box location. The fire alarm contact should be a normally open volt free contact.
8.1 Example of containment –pair of doors
Isee
underfloor
operator
Control
panel
Safety sensor/transfer loop -
cable 8 x 0.75mm
3 position switch to turn
automatic doors off when
manually locked
Floor box
Safety sensor and
transfer loop
Double pole
switched
fused spur
230V AC -
5A
Floor box
Safety sensor and
transfer loop
Push pad -
internal
activation
Push pad -
external
activation
Safety
sensor/transfer loop
- cable 8 x 0.75mm
WARNING –The Adaptalok ATS conduit gland on the end of the motor box is IP68 rated,
therefore you must ensure you install the correct conduit to the gland and sufficient care must be
taken when terminating the conduit end and taking cables into the unit. Any water ingress may damage
the unit, appropriate materials and measures must be considered and taken. For any uncertainty
regarding recommended conduits, contact www.adaptaflex.com
12

8.2 Example of containment –single door
Isee
underfloor
operator
Control
panel
3 position switch to turn
automatic doors off when
manually locked
Double pole
switched
fused spur
230V AC -
5A
Floor box
Safety sensor and
transfer loop
Push pad -
internal
activation
Push pad -
external
activation
Safety
sensor/transfer loop
- cable 8 x 0.75mm
WARNING –The Adaptalok ATS conduit gland on the end of the motor box is IP rated, therefore
you must ensure you install the correct conduit to the gland and sufficient care must be taken when
terminating the conduit end and taking cables into the unit. Any water ingress may damage the unit,
appropriate materials and measures must be considered and taken. For any uncertainty regarding
recommended conduits contact www.adaptaflex.com
8.3 Control panel to floor operator wiring
As standard there are two cables that are required as standard that must be run inside the 20mm conduit from
the control panel to each floor drive.
1. Motor cable –2 core x 1.00mm2 –*IMPORTANT* see section 12)
2. Encoder cable –4 core x 0.5mm2 –*IMPORTANT* see section 12)
These two cables are terminated in both the control box and floor unit.
Floor unit:
Motor cables –Black & Red
Encoder cables –Red, Black, Blue & Yellow
Control box from L-NEP LOGIC BOARD
Motor cables –Motor plug –Red & Black
Encoder cables –Encoder plug - Red, Black, Blue & Yellow
13

9) ELECTRIC CONNECTIONS –(see 12. L-NEP Logic Board for connections between floor box and control board)
PWN-T
MAINS POWER SUPPLY
DISCONNECTOR
230Vac
M1
MANUAL
GND
PROGRAM
NEUTRAL
SELECTOR
PHASE
SAFETY SENSOR FOR CLOSING
+24V-
TEST
M2
AUX1
1
SAFETY SENSOR FOR OPENING
SEN./CL. 2
TEST
COMMON 3
+24V-
M6
AUX2
4
SEN./OP. 5
25 TEST
OPEN
6
26 GND
COMMON 7
27 AUX3
RAD.EX
8
28
24V
RAD.IN
9
29
O.C.
START
10
M3
COMMON 11
OPEN
- GND
M7
M8
12
A
13
B
14
- 24V +
C
N.O.
N.C.
+EL.
+13V
EXTERNAL RADAR
INTERNAL RADAR
15
16
17
18
19
20
21
M4
+24V-
+24V-
START
ELECTRIC LOCK
BUTTON
24V
DIGITAL
PROGRAMMER N-DSEL
14

Installation Checklist
1. Excavate area to receive the floor unit, ensure the hole is at least 550mm long x 150mm wide
and 140mm deep.
2. Excavate the floor for the conduit run or have a conduit route planned between the control
panel and the floor drive.
3. Mount the control panel internally within 10m of the floor operator location, with provision of a
5A switch fused spur located within 1500mm of the control panel location.
4. Install the floor operator into the floor cut out, following the instructions in this manual. Firstly
fix the cradle, then place and fix the drive unit into the cradle.
5. Plumb down from the top centre to ensure the pivot point of the floor operator is in the correct
position.
6. Install the Adaptaflex conduit between the control panel and floor operator ensuring there is a
draw cable already pulled into the conduit. Having as few bends as possible with large radius
in the bends will assist when pulling in the motor and encoder cables, (motor and encoder
cables can be prewired in place of the draw cable).
7. Pull in the motor and encoder cables leaving approx. 1m of cables at both the control panel
and floor operator locations for connection.
8. To connect the motor and encoder cable in the floor operator box, remove the stainless steel
cover, remove the primary steel cover, lift back the black neopreme seal and you will find both
cables ready for connection.
9. Once connected, carefully replace neopreme seal, fix primary steel cover into place, fix
stainless steel cover plate into place.
10.Mount door onto floor operator and top pivot and ensure the door is free swinging from 0
degrees to 130 degrees open. It is critical there are isn’t anything inhibiting the door through its
opening and closing stroke.
11.Fix physical stops in the door closed position and the fully open position.
12.Run the cables for any auxillary products to be incorporated into the system (activation, safety
sensors, key switches etc)
13.Fix auxillary products
14.Connect and commission to EN16005
15.Attach ‘Automatic door’ and ‘Keep Clear’ stickers in relevant areas of door
Please be aware it is not advised to fix handles on automatic doors. It is strongly recommended
should pull handles be fitted to the door, they do not exceed 1/3 of the height of the door and
centrally located to ensure they do not interfere with safety sensor operation.
Care must be taken when connecting the conduit to the gland on the floor operator, this is the only
area where water may penetrate and all warrantees will be null and void if water ingress is found
from this location.
15

11) PWN-T POWER SUPPLY MODULE AND ELECTRIC WIRING
VOLTAGE CHANGE
115V 230V
GROUND
115/230V
OPEN
! In case of 230Vac mains voltage, put the 4-pole connector of the transformer primary in the J3 connector (230V) of PWN-T board
(factory setting).
! In case of 115Vac mains power supply, put the 4-pole connector of the transformer primary in the J2 (115V) connector of PWN-T board.
TERMINAL BOARD M1
230 Vac power supply: phase to terminal F, neutral to terminal N, ground connection with terminal ground symbol.
! Ground the operator by connecting the ground cable from the line to the Fasten connector on the plate the PWN-T board is
fastened to. A cable, connected with ground terminal of PWN-T board, is connected with the second fasten.
! The electric line is protected by 2A fuse F1.
TERMINAL BOARD M2
Terminals 1-3-4
MANUAL PROGRAM SELECTOR, located on operator side panel (factory
wiring): closed contact on position I to terminal 1 (AUX1);
Central contact to terminal 3 (common);
Closed contact on position II to terminal 4 (AUX2);
For more information on the operating modes of manual program selector, refer to "Program selectors" paragraph.
Terminals 2-3
Input of SAFETY SENSOR FOR CLOSING, N.C. contact.
The operation of safety sensor for closing must be enabled by N-DSEL digital programmer (function F18
ON). The activation during closing provokes the door reopening.
Terminals 5-7
Input of SAFETY SENSOR FOR OPENING, N.C. contact.
The operation of safety sensor for opening must be enabled by N-DSEL digital programmer (function F19 ON).
The activation during opening stops the door leaf movement; when the sensor deactivates, the opening restarts at low speed.
Terminals 6-7
OPEN input.
Input contact logic state can be selected as N.O. (default condition) or N.C. by N-DSEL digital programmer (function
30). The activation allows opening the door of all operating programs.
16

TERMINAL BOARD M3
Terminals 8-11
EXTERNAL RADAR input, N.O. contact.
It controls the door opening.
It is not active when the program selector is on “Exit only” and “Night lock”.
Terminals 9-11
INTERNAL RADAR input, N.O. contact.
It controls the door opening.
It is not active when the program selector is on “Entrance only” and “Night lock”.
Terminals 10-11
START input, N.O. contact.
It controls the door opening.
It is not active when the program selector is on “Night lock”.
TERMINAL BOARD M4
Connection of N-DSEL digital programmer.
Terminal 12 = - GND (power supply negative);
Terminal 13 = signal line A;
Terminal 14 = signal line B;
Terminal 15 = + 13V (power supply positive).
TERMINAL BOARD M6
Terminal 25
TEST output for safety sensors set for monitoring.
! For more information, refer to "Safety sensors" paragraph.
Terminals 26-27
AUX 3 input, N.O. contact.
Unlocking the electric lock. A pulse on the AUX3 input of the control unit unlocks the electric lock for 10 seconds to allow the opening of
the door by hand. As long as AUX3 input is activated the electric lock remains unlocked.
Terminals 28-29
Open Collector output of door status, it activates with open door and deactivates with closed door.
Connect a max. 100mA charge between 29 (O.C.) and 28 (positive + 24V) terminals.
! In Interlock function (F26=ON), terminal 29 is used for connection of interlock operation; for more information, refer to “Interlock
system” paragraph.
TERMINAL BOARD M7
Terminals 16 (negative) - 17 (positive)
24Vdc output, max. 20W, for the power supply of control and safety sensors.
Led 2 ON indicates the proper operation of output.
TERMINAL BOARD M8
Terminals 18-19-20
Free contact of relay RL1 for electric lock connection; (18 = Common, 19 = N.O., 20 = N.C.).
Terminals 16 (negative) - 21 (positive)
24Vdc output for electric magnet or electric lock power supply.
! For more information, refer to "Applications with electric lock" paragraph.
CONNECTORS
Connector J1 = transformer secondary (factory wiring).
Connector J2 = transformer primary (for 115V mains voltages).
Connector J3 = transformer primary (for 230V mains voltages, factory wiring).
Connector J4 = wiring of electric signals to connector J10 of L-NEP logic board.
Connector J5 = wiring of motor power supply to connector J11 of L-NEP logic board.
Led 1 ON indicates the presence of output voltage.
Connector J6 = connection with N-BAT battery module (see “N-BAT battery module”)
17

12) L-NEP LOGIC BOARD –*IMPORTANT CONNECTION*
PART DESCRIPTION
Connector J7 = WR5MS wiring for Master Slave communication in two-leaf swing door.
For more information, refer to "DOUBLE LEAF DOOR SET" paragraph.
Connector J8 = Encoder wiring –connect to 4 core cable from floor drive box. *IMPORTANT*
Connector J10 = wiring of electric signals from connector J4 of PWN-T module.
Connector J11 = wiring of motor power supply from connector J5 of PWN-T module.
Connector J12 = insertion for EN/RF1 radio receiver.
For more information, refer to "EN/RF1 radio receiver" paragraph.
Jumper J13 = it selects the logic status of safety sensor monitoring signal.
For more information, refer to "Safety sensors" paragraph.
Connector J14= Motor wiring –connect to 2 core cable from floor drive box. *IMPORTANT*
Jumper J15 = it selects two speed levels for door closing without power supply.
For models with LET and SLT closing spring only.
Jumper J15 activated = low speed.
Jumper J15 deactivated = high speed.
Led 3 –Led 4 = display of encoder signals.
Led 5 = display of MP1 microcontroller operation (micro A):
led on = correct operation;
led off or slowly flashing = fault on logic board.
Buzzer = warning buzzer.
MP1 = microcontroller “A”
Mp2 = microcontroller “B”
SW1 = dip-switch for operator type selection:
1 OFF / 2 OFF = single leaf operator or Master operator in double leaf
1 ON / 2 OFF = Slave operator in double leaf
13) N-DSEL DIGITAL PROGRAMMER –SCOPE AND CONNECTIONS
N-DSEL digital programmer is a tool necessary to the installer to configure the
operation of the automatic door and perform the set-up of operations, functions
and parameters, to perform system diagnostics and have access to events
memory containing information on automated device and its operation.
Access to the programming menu is protected by safety technical password so that
specialized and authorized personnel only can operate on the automated device.
N-DSEL digital programmer can also be used by the final user, but only for
choosing the operating mode of automatic door; the user can also select the
preferred language and set up a user password to prevent the use of digital
programmer by unauthorized persons.
Connect N-DSEL digital programmer to PWN-T module of Neptis SMP operator by
0.5mm 4-conductor cable.
Terminal +13V
= connect to terminal 15 of PWN-T board (+13V);
Terminal
-
= connect to terminal 12 of PWN-T board (- GND);
Terminal
A
= connect to terminal 13 of PWN-T board (A);
Terminal
B
= connect to terminal 14 of PWN-T board (B);
B A CN2 +13 -
For each subject-matter described in the following paragraphs the use of
digital programmer (hereinafter N-DSEL) is explained in the specific case.
18

14) COMMISSIONING OF AUTOMATED DEVICE (INITIAL SET-UP)
After completing the mechanical installation and performing electric connections, manually shift the door leaf for its entire stroke, to
ensure that no friction appears on the movement.
SET-UP operation is compulsory to allow the operator electronic control unit to acquire stroke points.
When the set-up begins, the door must be closed and during the stroke learning cycle, no obstacle shall appear in the leaf movement area.
The VISTA SMP operator is equipped with a function allowing it to learn the position of the side wall during the initial set-up.
This function is useful as it allows to store the wall position at the end of the opening stroke, and as a consequence to precisely set the
point at which the tripping of the opening safety sensor causes the leaf to decelerate in the last few degrees of the opening stage.
It is important that you adjust the safety sensor detection field before starting the operator set-up cycle.
If Neptis SMP operator controls a single-leaf automatic door, dip 1 and 2 on SW1 dip-switch of L-NEP logic board must be set
on OFF. If two Neptis SMP operators must control a double-leaf automatic door, refer to “Double-leaf door set” paragraph..
Follow chapter 14.1 only if N-DSEL digital programmer is new and powered for the first time.
Follow chapter 14.2 if digital programmer has already been used before.
14.1 FIRST START OF N-DSEL DIGITAL PROGRAMMER
Power the VISTA SMP operator by mains voltage, the control unit buzzer emits some
quick, short beeps.
! Language selection is shown on the display of N-DSEL digital programmer;
! use F2 and buttons to move the arrow in correspondence with the language desired.
!Press EXIT button to exit “Language” section and enter “Serial
communication set-up” section, see paragraph14.3.
14.2 USE OF N-DSEL DIGITAL PROGRAMMER
Power the VISTA SMP operator by mains voltage, the control unit buzzer emits some
quick, short beeps.
The display signals the lack of communication between N-DSEL and operator control
units since the serial code of L-NEP logic board is not stored on N-DSEL.
Press button for about 5 seconds to enter the general programming menu.
! F1 button allows moving forward among menu symbols.
! Select RS485 symbol.
!Give a quick pulse to ENTER button to enter the “Serial communication setup”
section, see paragraph14.3.
14.3 SERIAL COMMUNICATION SET-UP
N-DSEL programmer automatically detects the presence of operator electronic control unit (fig. A) and stores the serial code of L-NEP
logic board (fig. B).
When acquisition of serial code is completed, the display must show the closed padlock symbol on letter M and open padlock on letter
S, for a single leaf door (fig. C).
fig.A fig.B fig.C
For a double-leaf swing door, refer to “Double-leaf door set” paragraph.
Press EXIT button to exit “Serial communication set-up” section and enter the general programming menu.
19

14.4 INITIAL SET-UP
From general programming menu, F1 button allows moving forward among menu
symbols. Select INITIAL SET-UP symbol.
Give a quick pulse to ENTER button to enter the “Initial setup” section.
Type the 10-character technical password for access to set-up configuration.
The default technical password supplied by Label to N-DSEL digital
programmer is “A-A-A-A-A-A-A-A-A-A”
Press the button in correspondence with letter A, asterisk appears on the first letter case
on the display; repeat this operation for all the other characters required.
If the password typed is correct, you enter the section dedicated to set-up configuration; if
the password typed is wrong, you return to general programming menu.
It is recommended to change the default technical password.
Refer to “Password management” paragraph.
In this section, F1 / F3 buttons allows selecting the function ON / OFF status, while
button allows moving to the following function.
Press F2 button to return to previous function.
Select the door type: single leaf OFF, or double leaf ON (in this last case, refer to
“Double-leaf door set” paragraph).
In the settings of the setup, the function S02 should not be considered for the operator SMP
Select ON if an electric lock is present only.
Only if S03 function has been set to ON
If an electronic lock exists, select type:
pulse OFF (electronic lock or electric strike) or permanent ON (electric magnet).
Select ON only if a safety sensor has been installed on closing.
20
Table of contents
Popular DC Drive manuals by other brands
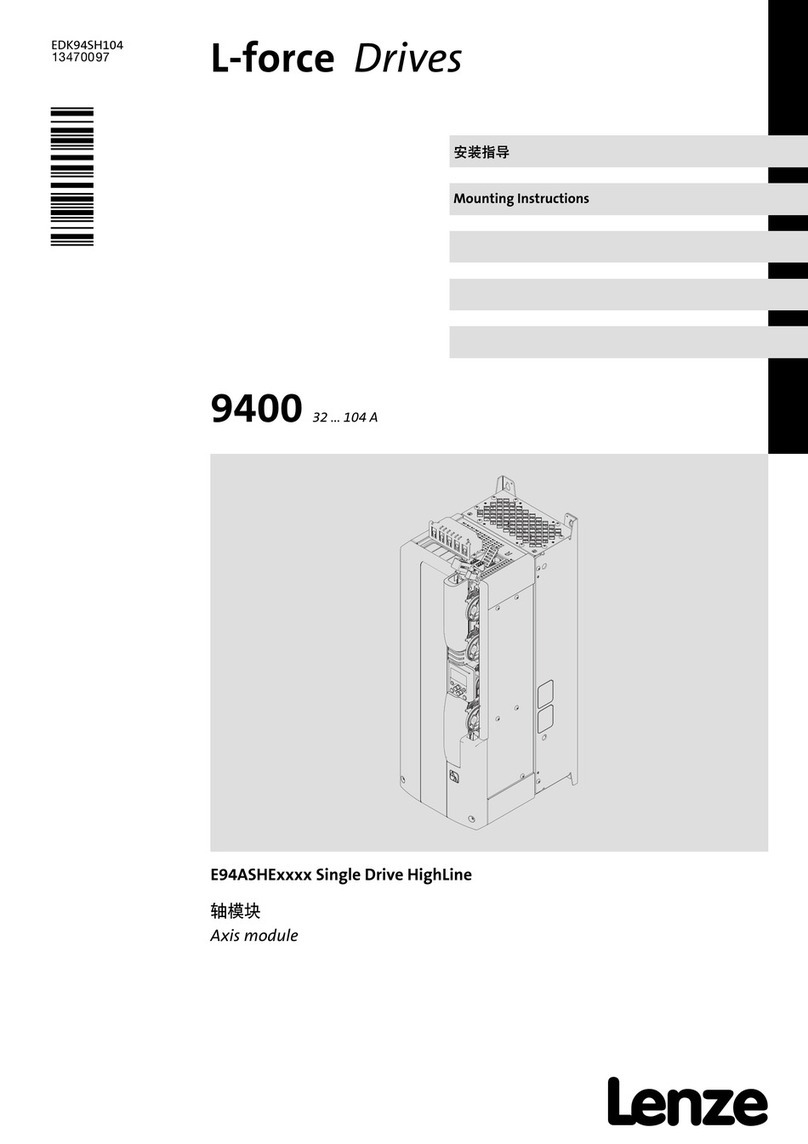
Lenze
Lenze L-force Drives E94ASHE Series Mounting instructions
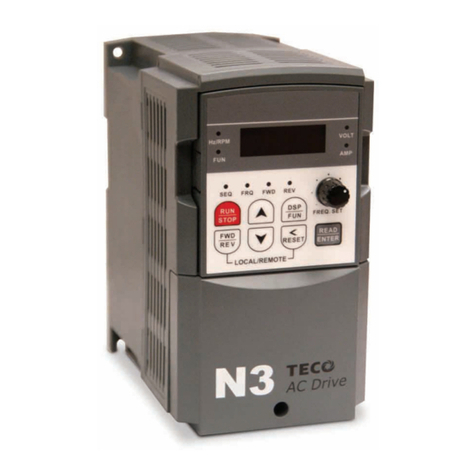
TECO-Westinghouse
TECO-Westinghouse N3 quick start guide

Trane
Trane Liquid-Cooled Adaptive Frequency AFDE Installation, operation and maintenance
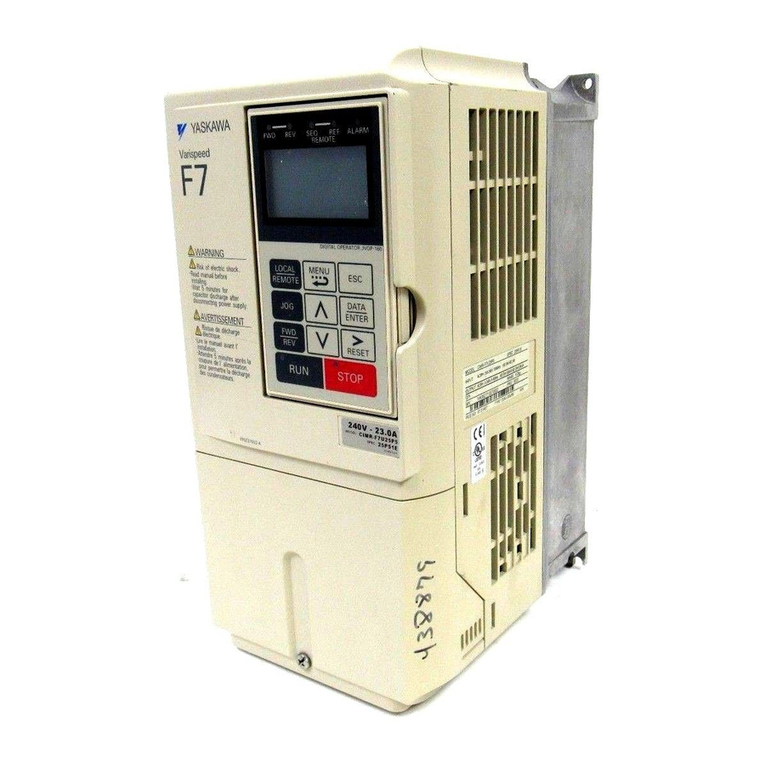
YASKAWA
YASKAWA Varispeed f7 Programming manual
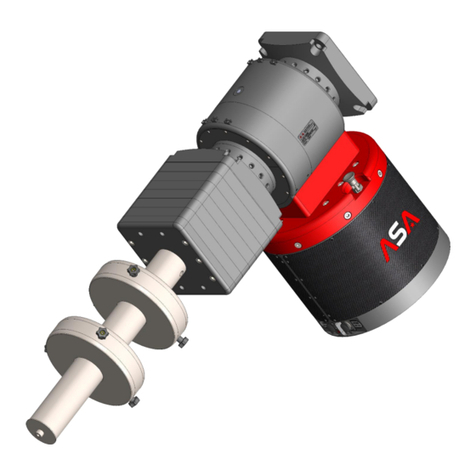
ASA Electronics
ASA Electronics DDM200 Original user manual

Mitsubishi Electric
Mitsubishi Electric FR-E800-SCEPA quick start guide