SEMIKRON SKYPER User manual

© by SEMIKRON / 2020-05-25 / Technical Explanation / SKYPER®12 PV
PROMGT.1026/ Rev.7/ Template Technical Explanation
Page 1/37
1. Introduction...............................................................................................................................2
2. Block Diagram and Application Example ........................................................................................3
2.1 Block diagram.......................................................................................................................3
2.2 Application example ..............................................................................................................4
2.2.1 Primary side ...................................................................................................................4
2.2.2 Secondary side ...............................................................................................................5
3. Dimensions and mechanical precautions........................................................................................8
3.1 Dimensions ..........................................................................................................................8
3.2 Plug-in connection .................................................................................................................8
3.3 Support post.........................................................................................................................9
3.4 Solder connection..................................................................................................................9
3.5 Handling instructions ........................................................................................................... 10
4. Interface Description................................................................................................................. 11
4.1 Footprint ............................................................................................................................ 11
4.2 Pin assignment ...................................................................................................................11
4.2.1 Pin assignment of pin header X10 | Primary side............................................................... 11
4.2.2 Pin assignment of pin header X100 | Secondary side | TOP ................................................ 12
4.2.3 Pin assignment of pin header X200 | Secondary side | BOT ................................................12
4.3 Power supply | Primary side ................................................................................................. 13
4.4 Gate drive signals | Primary side ........................................................................................... 14
4.5 Filter selection, jitter and propagation delay time | Primary side ............................................... 15
4.6 Error output | Primary side ................................................................................................... 15
4.7 Error input | Primary side ..................................................................................................... 16
4.8 Error mode selection | Primary side ....................................................................................... 17
4.9 External error input | Secondary side.....................................................................................17
4.10 Gate resistors | Secondary side.............................................................................................19
4.11 External boost capacitors | Secondary side ............................................................................. 20
5. Protection features ................................................................................................................... 21
5.1 Failure management............................................................................................................21
5.2 Dead time and Interlock.......................................................................................................24
5.3 Short pulse suppression (SPS) .............................................................................................. 25
5.4 Undervoltage lockout (UVLO)................................................................................................ 25
5.5 Dynamic short circuit protection by VCEsat-monitoring (DSCP)....................................................26
5.5.1 DSCP | Functional description ......................................................................................... 27
5.5.2 DSCP | Calculation hints ................................................................................................ 28
5.6Active clamping................................................................................................................... 29
5.7 Soft Off..............................................................................................................................30
5.8 Safe short circuit turn-off in multilevel topology ......................................................................31
6. Electrical characteristic.............................................................................................................. 31
7. Product Qualification ................................................................................................................. 32
8. Environmental conditions .......................................................................................................... 33
9. Marking...................................................................................................................................35
Technical Explanation
SKYPER®
12 PV
Revision:
03
Issue date:
2020-05-25
Prepared by:
Niklas Hofstötter
Reviewed by:
Daniel Obernöder
Approved by:
Marco Honsberg
Keyword: IGBT driver core, L5070901

© by SEMIKRON / 2020-05-25 / Technical Explanation / SKYPER®12 PV
PROMGT.1026/ Rev.7/ Template Technical Explanation
Page 2/37
1. Introduction
The SKYPER®12 PV is the most compact driver core within the SKYPER®family and demonstrates its real
advantages in low and medium power photovoltaic and ESS applications. In spite of its unrivalled
compactness of only 36mm x 45mm the SKYPER®12 PV provides reinforced insulation for operating
voltages of up to 1500 VDC in accordance with EN62109-1 & EN61800-5-1. The powerful output stages of
20A peak current per channel drives semiconductor module with gate charges of up to 20µC reliably.
SEMIKRON's highly integrated ASIC technology allows using 30% fewer components than standard
solutions which achieve a MTBF rate of 12 million hours at full load for the dual-channel driver core in
accordance with the industry standard SN29500.
Figure 1: SKYPER®12 PV
KEY FEATURES
Two output channels
1.25W output power and 20A peak output current per channel
Up to 1500V DC-Link voltage
±3 ns jitter per channel
Fully isolated secondary side power supply
Selectable filter settings
Soft turn-off in case of any secondary side error event
Short pulse suppression (SPS)
Under voltage lockout (UVLO)
Dynamic short circuit protection (DSCP)
Selectable error management modes for standard and multilevel applications
MTBF rate > 12 Million hours at full load

© by SEMIKRON / 2020-05-25 / Technical Explanation / SKYPER®12 PV
PROMGT.1026/ Rev.7/ Template Technical Explanation
Page 3/37
2. Block Diagram and Application Example
2.1 Block diagram
Figure 2: SKYPER®12 PV | Block diagram
Power Supply
Management
Power Supply
Management
Short Pulse
Suppression
Interlock
Signal
Processing
Dead Time
Generation
Filter
Management
UVLO
Error
Management
Gate Drive
Management
Power Supply
Management
Error
Management
Error
Management
Gate Drive
Management
UVLO
DSCP
DSCP
UVLO
nERR_IN_TOP
nERR_IN_BOT
PWR_VS_P_BOT
PWR_GND_BOT
PWR_VS_N_BOT
PWR_VS_P_TOP
PWR_GND_TOP
PWR_VS_N_TOP
BOT_ON
BOT_OFF
BOT_SOFTOFF
CLMP_IN_BOT
VCE_IN_BOT
CFG_VCE_BOT
TOP_ON
TOP_OFF
TOP_SOFTOFF
CLMP_IN_TOP
VCE_IN_TOP
CFG_VCE_TOP
PWR_VS
PWR_GND
TOP_IN
BOT_IN
CFG_FLT
CFG_IDT
nERR_IN
nERR_OUT
CFG_ERR

© by SEMIKRON / 2020-05-25 / Technical Explanation / SKYPER®12 PV
PROMGT.1026/ Rev.7/ Template Technical Explanation
Page 4/37
2.2 Application example
Figure 3 and Figure 4 show a typical SKYPER®12 PV core setup to control a multilevel semiconductor
module. The SKYPER®12 PV employs SEMIKRON’s highly-integrated ASIC chipset allowing easy
configuration with only a few simple external circuits and in turn reducing the project and development
time as well as the cost.
2.2.1 Primary side
Figure 3: SKYPER®12 PV | Application example | Primary side
Table 1: SKYPER®12 PV | Application example | Primary side | Recommended values
Component
Value
Remark
CTOP_IN / CBOT_IN
1nF
Optional filter capacitors suppressing high-frequency signals.
For further information please refer to [3].
CBST
-
Optional boost capacitor, dimensioning according to chapter
4.11.
RTOP_IN / RBOT_IN
10kΩ
Optional pull-down resistors, for steady off state of the
corresponding output, if no input signal is applied.
RnERR_OUT
4.75kΩ
Optional pull-up resistor, mandatory if error output is used.
Dimensioning according to chapter 4.6
PWR_GNDX10:01
CBST
SKYPER®12 PV
PWR_VSX10:09
CFG_ERRX10:05
PWR_VSX10:10
nERR_OUTX10:03
nERR_INX10:04
PWR_VS
TOP_INX10:07
PWR_GNDX10:01
nERR_OUT
TOP_IN
RnERR_OUT
CTOP_IN
RTOP_IN
BOT_INX10:08
PWR_GNDX10:01
BOT_IN
CBOT_IN
RBOT_IN
CFG_IDTX10:02
CFG_FLTX10:06
PWR_GNDX10:01PWR_GND

© by SEMIKRON / 2020-05-25 / Technical Explanation / SKYPER®12 PV
PROMGT.1026/ Rev.7/ Template Technical Explanation
Page 5/37
2.2.2 Secondary side
Figure 4: SKYPER®12 PV | Application example | Secondary side
DC+
RG(on)_TOP
RG(softoff)_TOP
RVCE_TOP DVCE_TOP
DGE_TOP
T1
SKYPER®12 PV
VCE_IN_TOP X100:02
TOP_ON X100:05
TOP_OFF X100:06
TOP_SOFTOFF X100:09
PWR_GND_TOP X100:08
RG(off)_TOP
RGE_TOP
CGE_TOP
VCE_IN_BOT X200:02
BOT_ON X200:05
BOT_OFF X200:06
BOT_SOFTOFF X200:09
PWR_GND_BOT X200:08
RG(on)_BOT
RG(softoff)_BOT
RVCE_BOT DVCE_BOT
DGE_BOT
T2
RG(off)_BOT
RGE_BOT
CGE_BOT
N
PWR_VS_P_TOP X100:03
nERR_IN_TOP X100:04
CFG_VCE_TOP X100:01
CLMP_IN_TOP X100:07
PWR_GND_TOP X100:08
PWR_VS_N_TOP X100:10
CBST(N)_TOP
R2_CFG_TOP
R1_CFG_TOP
CCFG_TOP
CBST(P)_TOP
PWR_VS_P_BOT X200:03
nERR_IN_BOT X200:04
CFG_VCE_BOT X200:01
CLMP_IN_BOT X200:07
PWR_GND_BOT X200:08
PWR_VS_N_BOT X200:10
CBST(N)_BOT
R2_CFG_BOT
CCFG_BOT
CBST(P)_BOT
R1_CFG_BOT

© by SEMIKRON / 2020-05-25 / Technical Explanation / SKYPER®12 PV
PROMGT.1026/ Rev.7/ Template Technical Explanation
Page 6/37
Table 2: SKYPER®12 PV | Application example | Secondary side | Recommended values
Component
Value
Remark
CBST(P)_TOP / CBST(N)_TOP
CBST(P)_BOT / CBST(N)_BOT
-
Optional boost capacitors, dimensioning according to chapter
4.11.
CCFG_TOP / CCFG_BOT
-
Optional capacitor to adjust the blanking time tbl(VCE) of the
dynamic short circuit protection function. Necessary, if DSCP
is used. Dimensioning according to chapter 5.5.
CGE_TOP / CGE_BOT
-
Optional capacitor to prevent gate oscillation in case of short
circuit events or in case of parallel operation of semiconductor
power modules. For further information please refer to [3].
DGE_TOP / DGE_BOT
Optional suppressor diode to prevent gate voltage
overshoots. For further information please refer to [3].
DVCE_TOP / DVCE_BOT
-
Optional high voltage diode for VCE-monitoring, mandatory if
DSCP is used. Dimensioning according to chapter 5.5.
R1_CFG_TOP / R1_CFG_BOT
≥ 10kΩ
Optional resistors to adjust the trip level VCE(ref) of the
dynamic short circuit protection, necessary if DCSP is used.
Dimensioning according to chapter 5.5.
R2_CFG_TOP / R2_CFG_BOT
-
Optional resistors to adjust the trip level VCE(ref) of the
dynamic short circuit protection, necessary if DCSP is used.
Dimensioning according to chapter 5.5.
RGE_TOP / RGE_BOT
10kΩ
Optional resistor to avoid an open gate of the semiconductor,
if the driver is not supplied. For further information refer to
[3].
RG(off)_TOP / RG(off)_BOT
RG(on)_TOP / RG(on)_BOT
≥ 1.25Ω
Necessary resistors to adjust the semiconductors’ turn-on
and turn-off behavior. Dimensioning according to chapter
4.10.
RG(softoff)_TOP
RG(softoff)_BOT
≥ 1Ω
Mandatory resistor to adjust the semiconductors’ turn-off
behavior in case of soft turn-off. Dimensioning according to
chapter 4.10.
RVCE_TOP / RVCE_BOT
511Ω
Optional series resistor for VCE-monitoring, mandatory if
DSCP is used.

© by SEMIKRON / 2020-05-25 / Technical Explanation / SKYPER®12 PV
PROMGT.1026/ Rev.7/ Template Technical Explanation
Page 7/37
Referring to the application example shown in Figure 3 and Figure 4, Table 3 describes the settings made.
Table 3: SKYPER®12 PV | Application example | Settings
Function
Configuration
Remark
Chapter
Active clamping
Disabled
Disabled by connecting the pins
CLMP_IN_TOP and CLMP_IN_BOT to
the corresponding PWR_GND pins.
5.6
Bidirectional error
(=HALT)
Disabled
Disabled by connecting the pin
nERR_IN to pin PWR_VS.
4.7
Dynamic short circuit
protection (DSCP)
Enabled at both output
channels
Enabled by connecting the pins
VCE_IN_TOP and VCE_IN_BOT to the
corresponding collectors of the
semiconductors through RVCE_TOP,
DVCE_TOP and RVCE_BOT, DVCE_BOT.
DSCP configuration via pins
CFG_VCE_TOP and CFG_VCE_BOT.
5.5
Dead time generation
Disabled
Disabled by connecting pin CFG_IDT to
pin PWR_VS.
5.2
Error mode
In case of any secondary
side error condition the
event will be reported at
the pin nERR_OUT. The
driver turns-off the
affected output
immediately and the
second output with the
next turn-off signal at
the corresponding input.
Both outputs remain
blocked until the error
state is reset .
Selected by connecting pin CFG_ERR to
pin PWR_VS.
5.1
Error propagation
delay time
700ns (typical value)
Fixed value.
5.1
External error
Disabled at both
secondary sides.
Disabled by connecting the pins
nERR_IN_TOP and nERR_IN_BOT to
the corresponding PWR_VS pins.
5.1
Filter
Analogue
Selected by connecting pin CFG_FLT to
pin PWR_GND.
5.3
Interlock
Disabled
Disabled by connecting pin CFG_IDT to
pin PWR_VS.
5.2
Jitter
±3ns (typical value)
Selected by connecting the pin
CFG_FLT to pin PWR_GND.
4.5
Short pulse
suppression (SPS)
200 ns (typical value)
Selected by connecting pin CFG_FLT to
pin PWR_GND.
5.3
Undervoltage lockout
(UVLO)
Always active on primary
and secondary side
-
5.4

© by SEMIKRON / 2020-05-25 / Technical Explanation / SKYPER®12 PV
PROMGT.1026/ Rev.7/ Template Technical Explanation
Page 8/37
3. Dimensions and mechanical precautions
3.1 Dimensions
Figure 5: SKYPER®12 PV | Dimension drawing
All dimensions in mm. Please consider higher tolerances of connector position according to IPC A 610.
STEP file on request.
3.2 Plug-in connection
The SKYPER®12 PV provides simple electrical and mechanical connection to adapter or control boards by
its standard pin headers. The primary side and the two secondary side plug-in connectors are 10 pin dual
row 2.54mm pin headers. For a secure mechanical connection of the SKYPER 12 PV IGBT driver it is
essential that the pin headers can be fully supported by the female mating connectors.
Example for a suitable female mating connector:
Description
Shape
Manufacturer
Art. no.
(female) RM2.54 10p
SMD 2ROW
Suyin
254100FA
Using SMD type mating connectors allows optimized board layout especially for SEMIKRON’s spring contact
modules like SEMiX.
8,13
8.13
18,79
max. 20.00
5,092.54
5,212.54
3,42
44,70
3,42 36,08
35,80
3.42
33.75
45.00
3.42
36.00
36.4
Ø3,2
AA 2:1
41,17
4,13 4,15
4,40
13,68
4.13
13.77
3.42
4.52
41.27
4.23
3.2

© by SEMIKRON / 2020-05-25 / Technical Explanation / SKYPER®12 PV
PROMGT.1026/ Rev.7/ Template Technical Explanation
Page 9/37
3.3 Support post
To increase the robustness of the mechanical connection between the SKYPER®12 PV driver and the
corresponding board a support post could be assembled. If a support post is used, make sure it has the
correct length. A too short support post would bend both, the driver and the corresponding board that it is
mounted on, thus increasing mechanical stress. If the support post is too long, the mating connectors may
not fully support the pin header and insufficient or instable electrical and mechanical contact might occur.
The mounting hole is located in the insulation area between the secondary sides of the driver. To avoid
reduction of creepage and clearance distances when utilizing a support post, the support post’s material
must have a CTI 600 classification at least.
Example of a support post:
Description
Shape
Manufacturer
Art. no.
Nylon support post
Dual lock
Essentra
DLMSPM-8-01 (>12mm)
Figure 6: SKYPER®12 PV | Support post
mounting hole for support post principle of a supported driver on an adapter
board
3.4 Solder connection
The SKYPER®12 PV driver core can be soldered directly onto an adapter or control board. It should be
noted that if the driver is placed too close to the adapter or control board, the clearance distances from the
driver’s primary to secondary side as well as the clearance distances between the secondary sides may be
reduced.
Soldering hints
•The solder’s temperature must not exceed 260°C and the solder time must not exceed 10 seconds.
•The ambient temperature must not exceed the specified maximum storage temperature of the driver.
•The solder joints should be in accordance to IPC A 610 Revision D (or later) - Class 3 (Acceptability of
Electronic Assemblies) to ensure an optimum connection between driver core and printed circuit
board.
•The driver is not suited for hot air, reflow or infrared reflow processes.

© by SEMIKRON / 2020-05-25 / Technical Explanation / SKYPER®12 PV
PROMGT.1026/ Rev.7/ Template Technical Explanation
Page 10/37
3.5 Handling instructions
Please ensure electric static discharge protection during handling. The driver should only be removed from
its original packaging just before mounting. When mounting the driver it has to be ensured that the work is
done in an ESD-protected workplace environment. Persons working with the driver have to wear ESD
wristbands, overalls and shoes. If tools are used for mounting, those must comply with ESD standards.
When handling the driver, do not pick up the driver at the transformers. The driver MUST be handled at the
PCB sides.
Figure 7: SKYPER®12 PV | Handling instruction

© by SEMIKRON / 2020-05-25 / Technical Explanation / SKYPER®12 PV
PROMGT.1026/ Rev.7/ Template Technical Explanation
Page 11/37
4. Interface Description
4.1 Footprint
The footprint of the SKYPER®12 PV with its primary side pin header X10 and the secondary side pin
headers X100 and X200 are shown in Figure 8.
Figure 8: SKYPER®12 PV | Footprint | Bottom view
4.2 Pin assignment
4.2.1 Pin assignment of pin header X10 | Primary side
Table 4: SKYPER®12 PV | Pin assignment –Primary side | X10
Pin
Signal
Function
Specification
X10:01
PWR_GND
Ground potential of power
supply and digital signals
To be connected to ground
X10:02
CFG_IDT
Interlock dead time
configuration
15V logic; 150kΩ (pull-up)
LOW = 2µs interlock dead time
HIGH = No interlock dead time
X10:03
nERR_OUT
Error output
Open collector output; max. 18V/15mA
(external pull-up resistor needed)
LOW = Error
HIGH = No error
X10:04
nERR_IN
Error input
15V logic inverted; 150kΩ/10nF (pull-up)
LOW = External error
HIGH = No external error
X10:05
CFG_ERR
Error behaviour
configuration in case of any
error condition
15V logic; 150kΩ (pull-down)
LOW = Both outputs switch off
HIGH = Affected output switches off
X10:06
CFG_FLT
Filter configuration for
switching signals
15V logic; 150kΩ (pull-down)
LOW = Analogue filter (tSPS(ana))
HIGH = Digital filter (tSPS(dig))
X10:07
TOP_IN
Switching signal input (TOP)
15V logic; 33kΩ/0.01nF (pull-down)
LOW = TOP switch off
HIGH = TOP switch on
X10:08
BOT_IN
Switching signal input (BOT)
15V logic; 33kΩ/0.01nF (pull-down)
LOW = BOT switch off
HIGH = BOT switch on
X200
X100
X10
1
10
1
10 1
10

© by SEMIKRON / 2020-05-25 / Technical Explanation / SKYPER®12 PV
PROMGT.1026/ Rev.7/ Template Technical Explanation
Page 12/37
X10:09
PWR_VS
Driver power supply
Stabilised +15V ±3%
X10:10
PWR_VS
Driver power supply
Stabilised +15V ±3%
4.2.2 Pin assignment of pin header X100 | Secondary side | TOP
Table 5: SKYPER®12 PV | Pin assignment –Secondary side | TOP | X100
Pin
Signal
Function
Specification
X100:01
CFG_VCE_TOP
VCE-monitoring reference
voltage
External voltage divider needed
X100:02
VCE_IN_TOP
VCE-monitoring input
External blocking diode needed
X100:03
PWR_VS_P_TOP
Power supply output,
positive voltage
Equal to VG(on)
(external buffer capacitors can be
optionally connected)
X100:04
nERR_IN_TOP
External error input
15V logic inverted; 150kΩ/0.01nF (pull-up)
LOW = External error
HIGH = No external error
X100:05
TOP_ON
On signal terminal for TOP
semiconductor
External gate resistor needed
(under consideration of Iout(avg), Iout(peak),
VG(on))
X100:06
TOP_OFF
Off signal terminal for TOP
semiconductor
External gate resistor needed
(under consideration of -Iout(avg), -Iout(peak),
VG(off))
X100:07
CLMP_IN_TOP
VCE-clamping input
150kΩ/0.01nF (pull-down)
In case of activated TOP_OFF:
LOW = TOP_OFF equal to VG(off)
HIGH = TOP_OFF floating
X100:08
PWR_GND_TOP
Ground potential of power
supply and digital signals
Reference potential of gate voltages
(emitter/source of power semiconductor)
X100:09
TOP_SOFTOFF
SoftOff signal terminal for
TOP semiconductor
External gate resistor needed
X100:10
PWR_VS_N_TOP
Power supply output,
negative voltage
Equal to VG(off)
(external buffer capacitors can be
optionally connected)
4.2.3 Pin assignment of pin header X200 | Secondary side | BOT
Table 6: SKYPER®12 PV | Pin assignment –Secondary side |BOT | X200
Pin
Signal
Function
Specification
X200:01
CFG_VCE_BOT
VCE-monitoring reference
voltage
External voltage divider needed
X200:02
VCE_IN_BOT
VCE-monitoring input
External blocking diode needed
X200:03
PWR_VS_P_BOT
Power supply output,
positive voltage
Equal to VG(on)
(external buffer capacitors can be
optionally connected)
X200:04
nERR_IN_BOT
External error input
15V logic inverted; 150kΩ/0.01nF (pull-up)
LOW = External error
HIGH = No external error
X200:05
BOT_ON
On signal terminal for BOT
semiconductor
External gate resistor needed
(limits under consideration of Iout(avg),

© by SEMIKRON / 2020-05-25 / Technical Explanation / SKYPER®12 PV
PROMGT.1026/ Rev.7/ Template Technical Explanation
Page 13/37
Iout(peak), VG(on))
X200:06
BOT_OFF
Off signal terminal for BOT
semiconductor
External gate resistor needed
(limits under consideration of -Iout(avg), -
Iout(peak), VG(off))
X200:07
CLMP_IN_BOT
VCE-clamping input
150kΩ/0.01nF (pull-down)
In case of activated BOT_OFF:
LOW = BOT_OFF equal to VG(off)
HIGH = BOT_OFF floating
X200:08
PWR_GND_BOT
Ground potential of power
supply and digital signals
Reference potential of gate voltages
(emitter/source of power semiconductor)
X200:09
BOT_SOFTOFF
SoftOff signal terminal for
BOT semiconductor
External gate resistor needed
X200:10
PWR_VS_N_BOT
Power supply output,
negative voltage
Equal to VG(off)
(external buffer capacitors can be
optionally connected)
4.3 Power supply | Primary side
For a proper operation of the SKYPER®12 PV driver core, a power supply of at least 15W/1A shall be
connected to the driver’s power supply pins. During power-up of the driver turn-on signals should not be
applied to the driver’s inputs TOP_IN/BOT_IN, otherwise the driver will not leave the error state.
Please note, when controlling power semiconductor modules with a gate charge ≥ 2.5 µC external boost
capacitors (CBST) are recommended to support the supply voltage on the primary side. Dimensioning of
such boost capacitors shall be done according to chapter 4.11.
Figure 9: SKYPER®12 PV | Primary side | Power supply
SKYPER®12 PV
CBST
PWR_VS
PWR_GND PWR_GNDX10:01
PWR_VSX10:10
PWR_VSX10:09

© by SEMIKRON / 2020-05-25 / Technical Explanation / SKYPER®12 PV
PROMGT.1026/ Rev.7/ Template Technical Explanation
Page 14/37
4.4 Gate drive signals | Primary side
The signal inputs TOP_IN/BOT_IN of the SKYPER®12 PV driver core have a +15V schmitt trigger logic. A
HIGH signal at the input of the driver turns on the corresponding output of the driver. A LOW signal at the
input leads to a switch-off command at the corresponding output. Pulses below 1µs are not allowed.
Short pulses as well as voltage peaks, e.g. caused by interference, are suppressed by the driver and will
not be transmitted to the outputs. Further information to the short pulse suppression are referred in
chapter 5.3.
Figure 10: SKYPER®12 PV | Primary side | Gate drive signals
When using the driver in environments with high levels of electromagnetic noise, it is recommended to
connect a filter capacitor (CTOP_IN/CBOT_IN) of several hundred pico Farads as close as possible to the signal
inputs. Please note that these capacitors affect the propagation delay time of the driver. The RTOP_IN/RBOT_IN
resistors pull the inputs to low-level when no control signals are applied. The recommended value of the
pull-down resistors is approximately 10kΩ.
Parameter
Min
Typ
Max
Threshold high
-
-
10V
Threshold low
5V
-
-
SKYPER®12 PV
CTOP_IN
TOP_IN
PWR_GND
RTOP_IN
PWR_GNDX10:01
TOP_INX10:07
CBOT_IN
BOT_IN
PWR_GND
RBOT_IN
PWR_GNDX10:01
BOT_INX10:08

© by SEMIKRON / 2020-05-25 / Technical Explanation / SKYPER®12 PV
PROMGT.1026/ Rev.7/ Template Technical Explanation
Page 15/37
4.5 Filter selection, jitter and propagation delay time | Primary side
SEMIKRON’s highly-integrated mixed signal ASICs the SKYPER®12 PV permit the selection of filter type,
jitter and propagation delay time to meet specific requirements of applications.
The filter time can be set via the configuration pin CFG_FLT. Connecting the CFG_FLT pin to the PWR_VS
pin enables the digital filter employing very low tolerances over the full temperature range.
Depending on the settings made the SKYPER®12 PV driver provides a very low jitter of typically ±3ns. For
this mode, the analogue filter has to be enabled and the driver’s internal dead time generator has to be set
inactive. The dead time generator is inactive, if either the interlock feature is disabled via the CFG_IDT pin
or the dead time of the applied pulse pattern is longer than the dead time of internal generator of the
driver of typically 2µs. A detailed description of the interlock function and the dead time generation is
referred in chapter 5.2.
CFG_FLT
CFG_IDT
Setting
Filter time
Delay time
Jitter
HIGH
HIGH/LOW
Digital filter
390ns
830ns
±12.5ns
LOW
LOW
Analogue filter
200ns
500ns
±3ns /±12.5ns
LOW
HIGH
Analogue filter
200ns
500ns
±3ns
4.6 Error output | Primary side
The SKYPER®12 PV reports any detected error event at the nERR_OUT pin by pulling it to low-level. The
error output is an open collector output and requires an external pull-up resistor (RnERR_OUT). The
recommended value of the pull-up resistor is in the range of
.
As long as the driver has not been reset the error output will be at low-level.
A detailed description, how to reset the driver to exit the error state and resume to operation is described
in chapter 5.1.
Figure 11: SKYPER®12 PV | Primary side | Error output
Please note, if the nERR_OUT terminal of SKYPER®12 PV is directly connected to a nERR_OUT terminal of
another SKYPER®12 PV driver, only one pull-up resistor must to be applied.
SKYPER®12 PV
PWR_VS
nERR_OUT nERR_OUTX10:03
PWR_VSX10:09
PWR_GND PWR_GNDX10:01
RnERR_OUT

© by SEMIKRON / 2020-05-25 / Technical Explanation / SKYPER®12 PV
PROMGT.1026/ Rev.7/ Template Technical Explanation
Page 16/37
4.7 Error input | Primary side
The nERR_IN input is optionally used to report a system related external error event to the
SKYPER®12 PV. If the nERR_IN input is pulled down to low-level the driver enters into error state.
Depending on the error mode configuration, described in chapter 4.8, the driver sets its outputs either
immediately or with the next turn-off command at its corresponding input to low-level and locks them.
After reset, as described in chapter 5.1, the driver will be ready to transfer the signals to the output stage
again. If no reporting to the external error input is required, the nERR_IN input can be connected to the
PWR_VS pin or to the nERR_OUT pin.
In multiphase or parallel operation the nERR_IN input offers the possibility to force the outputs of each
driver in the system to off-state and locks them, simultaneously, without the need of an external control
unit. Therefore all nERR_OUT outputs and all nERR_IN inputs have to be connected together forming a
common bi-directional HALT line. Additionally, all CFG_ERR configuration pins have to be connected to
ground potential, as shown in Figure 12. In this configuration, any driver connected to the HALT line can
force the outputs of all connected drivers to off-state and locks them, when the driver pulls its nERR_OUT
output to low-level.
If a specific turn-off sequence is required –as it is common practice in NPC multilevel applications –the
configuration pins CFG_ERR have to be connected to the PWR_VS pins. A low-level of the HALT line locks
the outputs of the connected drivers, but does not immediately force them to low-level. Outputs which are
in on-state can be forced to off-state by the controller sending a turn-off command to the corresponding
signal inputs TOP_IN/BOT_IN.
If the driver is used in environments with high levels of EMI noise, it is recommended to connect an
additional filter capacitor as close as possible to the nERR_IN pin and the PWR_GND pin.
Figure 12: SKYPER®12 PV | Primary side | Error input
Parameter
Min
Typ
Max
Threshold high
-
-
11 V
Threshold low
7.5 V
-
-
SKYPER®12 PV | 1
PWR_VS
nERR_OUT nERR_OUTX10:03
PWR_VSX10:09
PWR_GNDX10:01
RnERR_OUT
SKYPER®12 PV | 2
nERR_OUTX10:03
nERR_INX10:04
PWR_GND PWR_GNDX10:01
nERR_INX10:04
X10:05 CFG_ERR
X10:05 CFG_ERR

© by SEMIKRON / 2020-05-25 / Technical Explanation / SKYPER®12 PV
PROMGT.1026/ Rev.7/ Template Technical Explanation
Page 17/37
4.8 Error mode selection | Primary side
The configuration pin CFG_ERR selects the behavior of the SKYPER®12 PV driver core on error events.
Connecting the CFG_ERR pin to the PWR_GND pin forces the driver to set its outputs to off-state
immediately when an error is detected. As long as the driver has not been reset the error event is reported
at the corresponding output and the driver’s outputs are locked. Whereby, depending on whether an error
is detected on the primary or on the secondary side the driver switches off the connected semiconductors
via the standard turn-off or the soft-off path. If an error occurs on the primary side the driver will activate
the standard turn-off paths of both channels. If an error occurs on the secondary side, the driver will
activate the soft-off path of the affected secondary side. The semiconductor connected to the other
secondary side will be switched off via the standard turn-off path.
If the CFG_ERR pin is connected to the PWR_VS pin, the driver locks its outputs in case of any error event’s
occurrence and, hence, reports the error event at the terminal nERR_OUT. The affected output at which the
error occurred will be set to off-state, immediately. The second output will be set to off state when the
driver has received a turn-off command at the corresponding signal input TOP_OFF/BOT_OFF. Depending
on whether an error is detected on the primary or secondary side the driver activates the standard turn-off
or the soft-off path, as described above.
Further information related to the primary and secondary side error events, as well as on the error reset
conditions is referred in chapter 5.1.
4.9 External error input | Secondary side
Each secondary side of the driver provides an error input (nERR_IN_TOP/nERR_IN_BOT) to handle external
error events. These inputs are low active. Pulling one input to low-level forces the driver into error state.
The behaviour of the driver in case of an external error event depends on the configuration at the
configuration pin CFG_ERR, as described in chapter 4.8.
The external error input is typically used to monitor temperature, current or voltage of modules, phase legs
or systems. The error input of the secondary TOP/BOT side can be disabled by connecting it to the
PWR_VS_P_TOP/PWR_VS_P_BOT pin.
Figure 13 shows a recommended comparator circuitry to process the NTC’s signal and derive the required
logic signal for the input of the SKYPER®12 PV. When the voltage at the comparator’s positive input falls
below the voltage level of the negative input the nERR_IN input will be pulled to low-level and generates an
external error event. Assuming that resistors R3and R4have the same value the comparator’s trip level is
reached when the value of the NTC falls below the value of RCGF(temp). Please note that the negative supply
pin of the comparator is connected to PWR_VS_N which has to be taken into account, in case the NTC
thermistor is monitored by an external application circuit in addition.
Figure 13: SKYPER®12 PV | Secondary side | Example of an external error input circuitry
R1
SKYPER®12 PV
PWR_VS_P_TOP X100:03
nERR_IN_TOP X100:04
PWR_GND_TOP X100:08
PWR_VS_N_TOP X100:10
ϑ
R2
C1
C2
RCFG(temp)
C3
R3
R4

© by SEMIKRON / 2020-05-25 / Technical Explanation / SKYPER®12 PV
PROMGT.1026/ Rev.7/ Template Technical Explanation
Page 18/37
Recommended values
Component
Value
Remark
C1
1nF
C2
100nF
C3
1µF
R1
30.1kΩ
R2
15kΩ
R3
30.1kΩ
R4
30.1kΩ
RCFG(temp)
-
The value of the resistor RCFG(temp) has to be determined
considering the resistance characteristic of the connected
thermistor and the desired trip level.
Parameter
Min
Typ
Max
Threshold high
-
-
13 V
Threshold low
2 V
-
-

© by SEMIKRON / 2020-05-25 / Technical Explanation / SKYPER®12 PV
PROMGT.1026/ Rev.7/ Template Technical Explanation
Page 19/37
4.10 Gate resistors | Secondary side
Equipped with three output channels at each secondary side (TOP_ON/TOP_OFF/TOP_SOFTOFF and
BOT_ON/BOT_OFF/BOT_SOFTOFF) the SKYPER®12 PV driver offers the possibility to optimize turn-on and
turn-off behavior of the IGBT separately. By default, the driver uses the TOP_ON/TOP_OFF and
BOT_ON/BOT_OFF output to turn-on or turn-off the connected semiconductor. The SOFTOFF output will be
activated by the driver if a secondary side error event has been detected to turn-off of the connected
semiconductor slowly, which in turn shall prevent from excessive voltage overshoots to protect the
semiconductor against destruction by over voltage. It is mandatory to populate a suitable soft-off gate
resistor, otherwise the semiconductor will not be turned-off in case of a secondary side error. A detailed
explanation of when the driver is activating the soft-off path is referred in chapter 4.8.
The gate resistor influences the IGBT switching time, switching losses, reverse bias safe operating area
(RBSOA), short-circuit safe operating area (SCSOA), EMI, dV/dt, di/dt and reverse recovery current of the
freewheeling diode. The gate resistor essentially optimizes the safe operation of the power semiconductor
in accordance with the individual application parameters, e.g. IGBT technology, diode, switching frequency,
losses, application layout, inductivity / stray inductance, DC-link voltage and driver capability. The
complete design of an application must be viewed as a whole, with due considering of the above-mentioned
parameters at least. Interacting and interfering effects within the whole application must be considered,
evaluated and addressed. [4]
The minimum value of the gate resistors RG(on) and RG(off) could be calculated by the following equation:
The minimum allowed value of the RG(softoff) is 1Ω. Additional hints how to determine the values of the gate
resistors are referred in [4].
Figure 14: SKYPER®12 PV | Secondary side | Gate resistors
Please note that some of SEMIKRON’s driver cores using an ASIC internal N-channel MOSFET for Soft Off.
To protect this MOSFET against stress when turning-off the TOP_ON/BOT_ON channel it is recommended to
place the RG(softoff) resistor in series with the RG(off) resistor.
Since each turn-on and turn-off of a semiconductor means charging or discharging the input capacitance of
the connected power semiconductor, the gate resistor has to be suitable for such pulse load. For this
reason, SEMIKRON recommends the use of pulse current suitable resistors. The following table provides
examples.
DC+
RG(on)_TOP
RG(softoff)_TOP
T1
SKYPER®12 PV
TOP_ON X100:05
TOP_OFF X100:06
TOP_SOFTOFF X100:09
PWR_GND_TOP X100:08
RG(off)_TOP
AC
RG(int)_TOP
RE_TOP
IGBT

© by SEMIKRON / 2020-05-25 / Technical Explanation / SKYPER®12 PV
PROMGT.1026/ Rev.7/ Template Technical Explanation
Page 20/37
Description
Shape
Manufacturer
Art. no.
MELF resistors
MELF / MiniMELF SMD
Vishay Beyschlag,
Vishay Draloric,
Vitrohm
PRO MELF resistors,
SMM0207, SMM 0204,
ZCM series
4.11 External boost capacitors | Secondary side
The SKYPER®12 PV allows driving of semiconductor power modules with a gate charge (QG) of up to 20µC
per output. To stabilize the gate voltages VG(on) and VG(off) during the semiconductor switching, the use of
boost capacitors for each output channel is recommended, if the connected gate charge is larger than
2.5µC. For maximum effectiveness, these capacitors have to be placed as close as possible to the
corresponding terminal as shown in Figure 15.
Figure 15: SKYPER®12 PV | Secondary side | Boost capacitors
The required capacitance of the optional external boost capacitors can be estimated by the following
equation:
Please note, when assembling boost capacitors at the secondary sides, also boost capacitors have to be
assembled at the primary side, as shown in Figure 9.
SKYPER®12 PV
CBST(N)_TOP
CBST(P)_TOP
PWR_VS_P_TOP X100:03
PWR_GND_TOP X100:08
PWR_VS_N_TOP X100:10
Table of contents
Other SEMIKRON DC Drive manuals
Popular DC Drive manuals by other brands
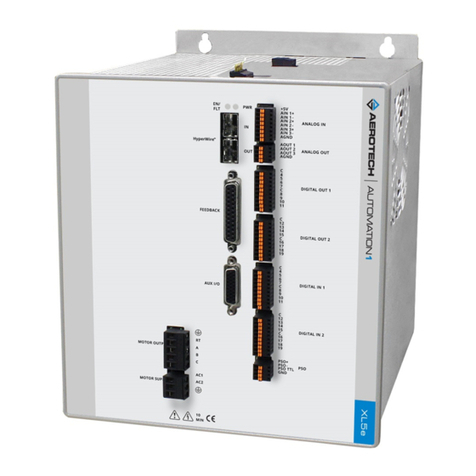
Aerotech
Aerotech Automation1 XL5e Hardware manual
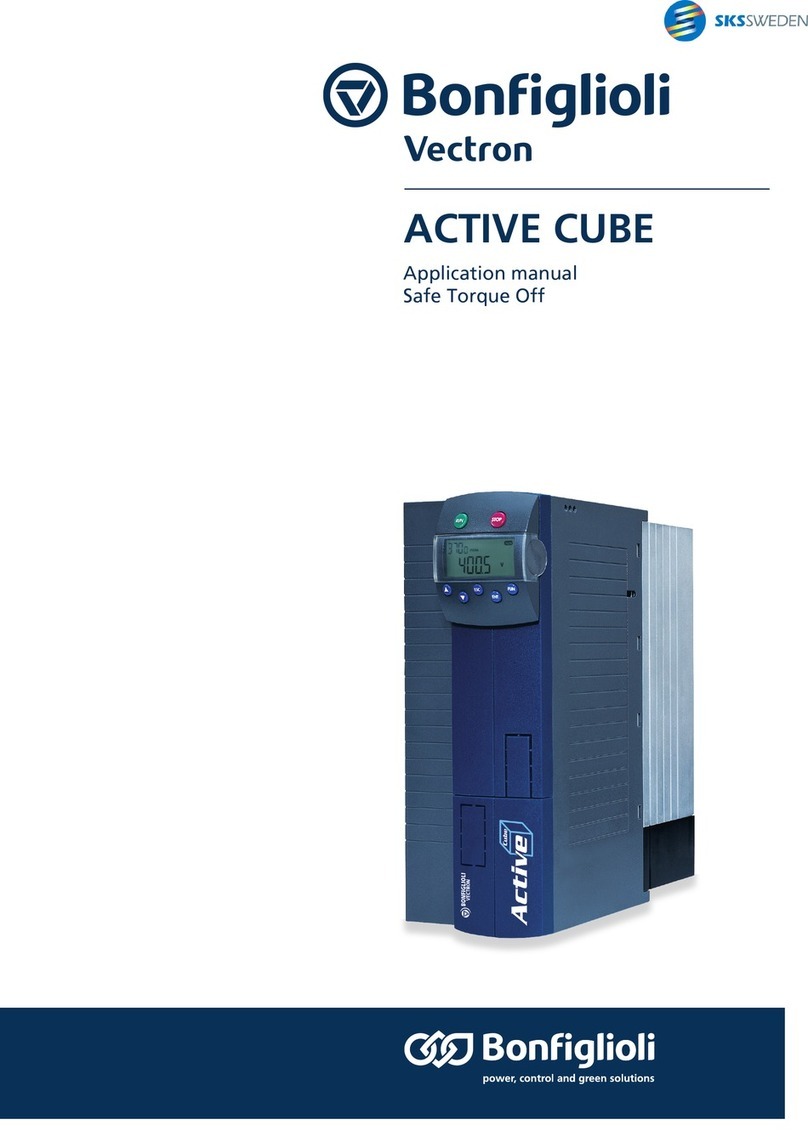
BONFIGLIOLI Vectron
BONFIGLIOLI Vectron ACTIVE CUBE Applications manual
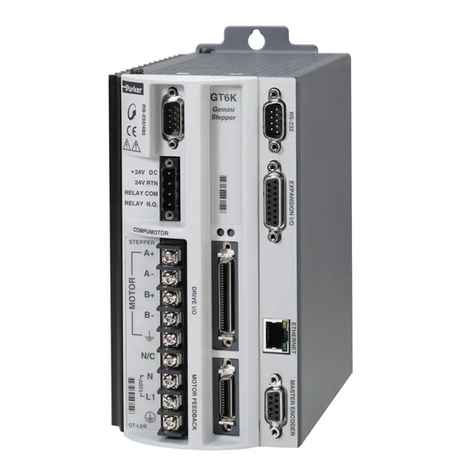
Parker
Parker GT6-L8-NK Hardware installation guide
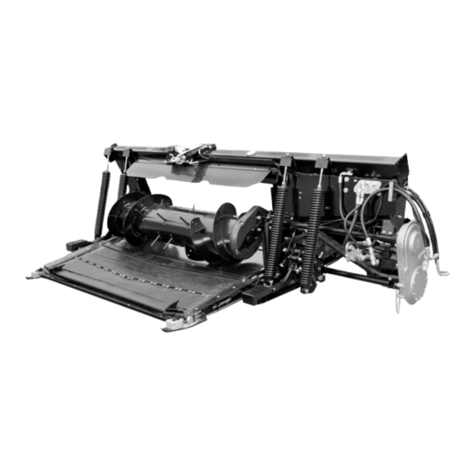
MacDon
MacDon 279708 installation instructions
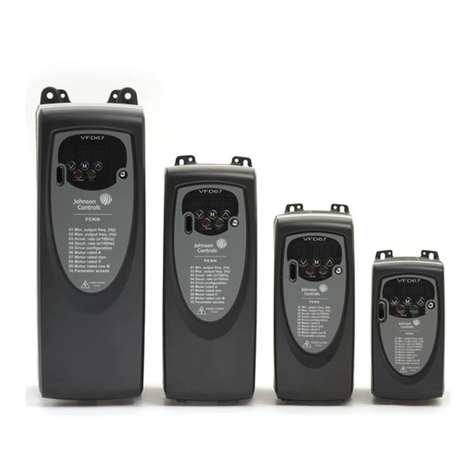
Johnson Controls
Johnson Controls VFD67 Series Quick start commissioning guide
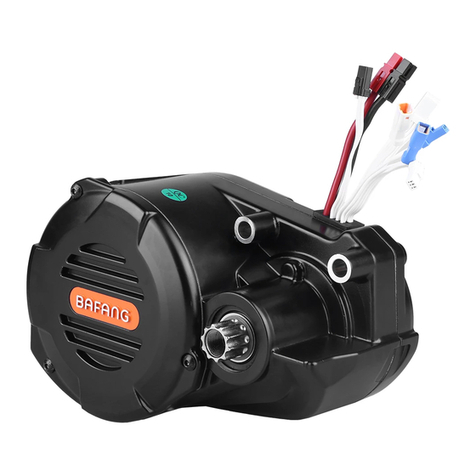
BAFANG
BAFANG MM G510.500 18 027 manual
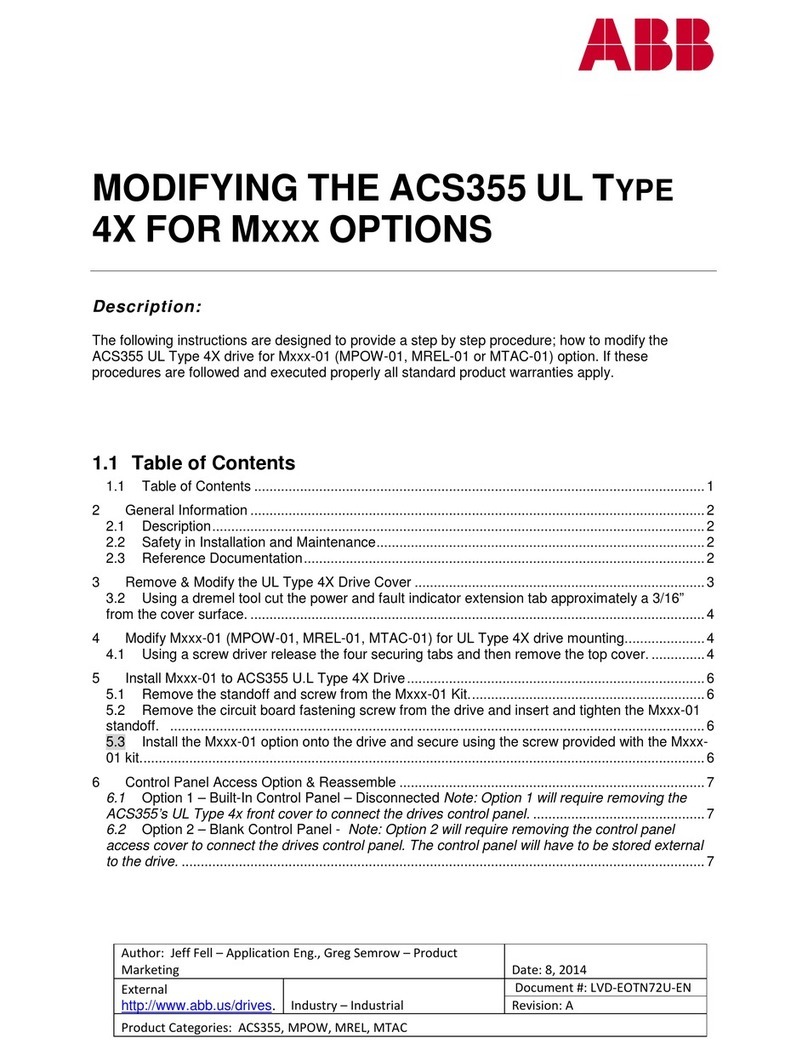
ABB
ABB ACS355 UL 4X quick start guide
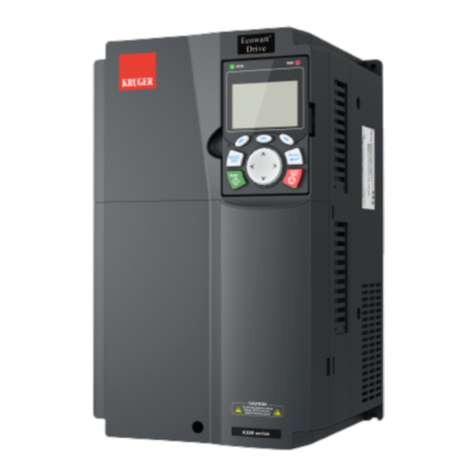
Kruger
Kruger Ecowatt K320 Series Operation manual

Becker
Becker U30 Assembly and operating instructions

ARNOLD
ARNOLD UA 500 operating instructions
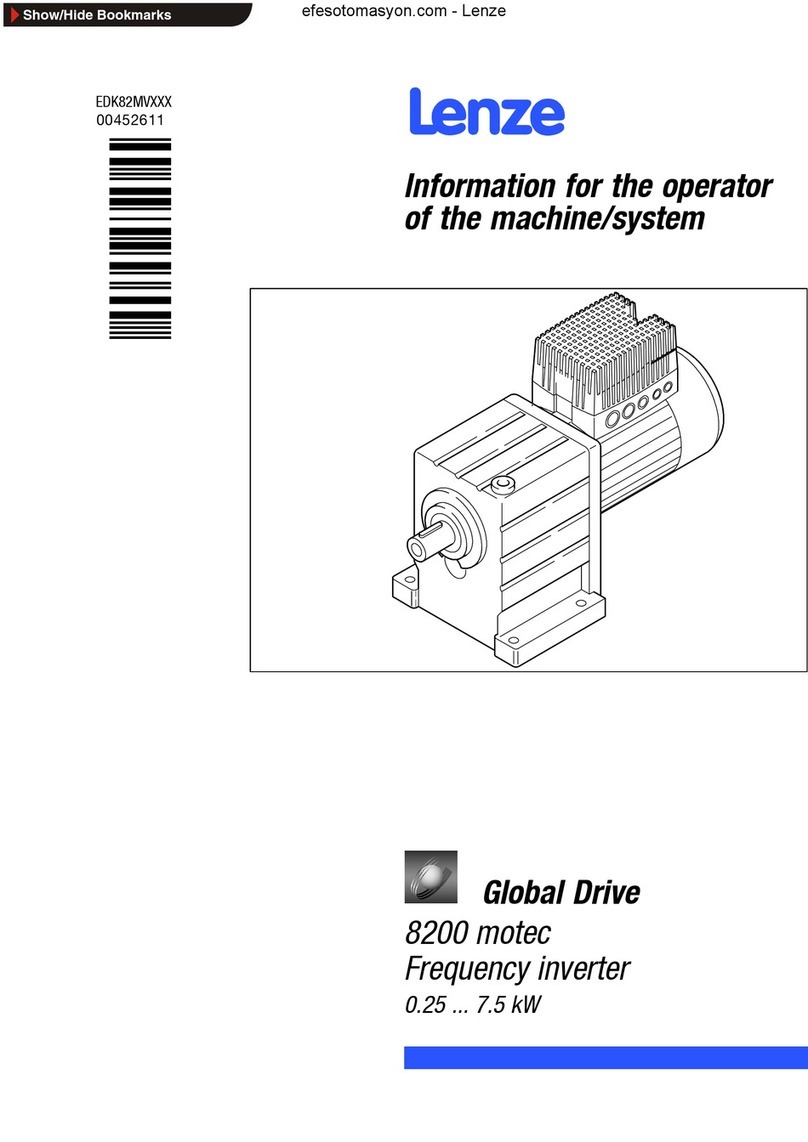
Lenze
Lenze Global Drive 8200 motec Series Information for the operator of the machine
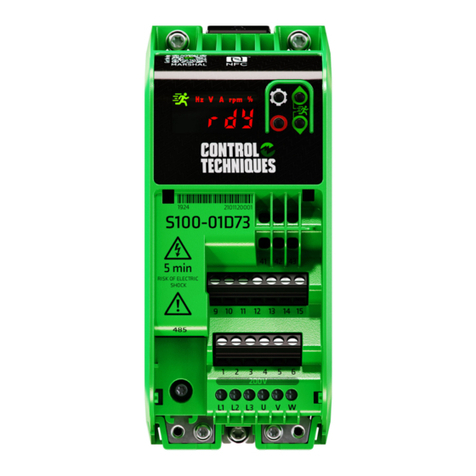
Nidec
Nidec COMMANDER S100 user guide