LAMBERT FLAPS V6 HBR (3P) Instruction Manual

FLAPS_V6_HBR_datasheet_manual_EN.odt
FLAPS V6 HBR (3P)
(right-hand design with rotary switch and 4 LED indicators)
1/33

FLAPS_V6_HBR_datasheet_manual_EN.odt
Page intentionall left blank
2/33

FLAPS_V6_HBR_datasheet_manual_EN.odt
Table of contents
1 Important notes and warnings.......................................................................5
2 Product description.........................................................................................
2.1 Product use......................................................................................................6
2.2 Main product functionalities...............................................................................6
2.3 Inputs..............................................................................................................6
2.4 Controls............................................................................................................7
2.5 Outputs............................................................................................................7
2.6 Indication.........................................................................................................7
2.7 Protections........................................................................................................7
2.8 Description of the control panel..........................................................................8
2.8.1 Control panel HBR (4 control positions)........................................................8
2.8.2 Control panel HBR 3P (3 control positions)...................................................9
2.8.3 Differences between HBR and HBR 3P variants and how to read this manual
when using the HBR 3P variant............................................................................10
3 Specifications...............................................................................................11
3.1 Electrical characteristics...................................................................................11
3.2 Mechanical specifications.................................................................................11
3.3 Allowed operating conditions............................................................................12
3.4 Lifetime and warrant ......................................................................................12
3.5 Tests according to DO-160G.............................................................................13
4 Installation in an airplane............................................................................14
4.1 Mechanical installation.....................................................................................14
4.2 Position sensor mounting.................................................................................15
4.3 Actuator installation.........................................................................................16
4.4 Electrical connections.......................................................................................17
4.4.1 Electrical connections of actuator with internal position sensor and limit
switches.............................................................................................................18
4.4.2 Electrical connections with simple actuator, external position sensor and limit
switches.............................................................................................................19
4.4.3 Electrical connections for dimming control unit displa elements..................20
5 Description of functions................................................................................21
5.1 Normal mode – automatic................................................................................21
5.2 Errors and faults..............................................................................................22
5.3 Safet mode – manual.....................................................................................23
5.4 Device setup mode..........................................................................................24
5.5 Position programming mode.............................................................................26
5.6 Landing gear control output.............................................................................28
5.7 Dimming of indicator elements.........................................................................28
Errors and faults, troubleshooting................................................................29
6.1 Indicated errors and faults...............................................................................29
6.2 Troubleshooting..............................................................................................32
3/33

FLAPS_V6_HBR_datasheet_manual_EN.odt
Page intentionall left blank
4/33

FLAPS_V6_HBR_datasheet_manual_EN.odt
1 Important notes and arnings
Thank ou for purchasing FLAPS V6 HBR. For a comfortable and safe use of this product,
please pa attention to THE ENTIRE MANUAL, especiall the notes and warnings below.
•Although the FLAPS V6 HBR control unit has been thoroughl tested to ensure
maximum safet in all conceivable situations, THE RIGHT FUNCTIONALITY
DEPENDS ON THE RIGHT INSTALLATION AND SETTINGS.
•Therefore, it is NECESSARY to READ CAREFULLY and UNDERSTAND THIS
MANUAL COMPLETELY.
•Keep this manual printed in an airplane for cases of emergenc or change of
ownership.
•THIS PRODUCT IS NOT APPROVED FOR INSTALLING IN CERTIFIED AIRPLANES.
•The pilot MUST UNDERSTAND the control of this product before the first flight. DO
NOT use the product unless ou are sure how it works!
•Do not allow unauthorized persons to handle the installed product.
•After installing the product, before the first flight, turn on ALL possible sources of
electromagnetic interference on board the aircraft and ensure that the instrument is
functioning properl .
•Use of the device in conflict with this manual, with bad wiring, outside the allowed
operating conditions, etc., ma cause the device to malfunction or damage and
endanger flight safet .
•If the product repeatedl indicates an error, do not use it and turn off the power!
(except for switching to safet manual mode in the event of a position sensor error
where the position of the flaps can be manuall controlled)
•AVOID contact with liquids and chemicals
•Before installation, check the mechanical integrit of the device and its accessories
•DO NOT disassemble the device!
•After installation, carefull check the functionalit of the device and its installation
•The responsibilit for the installation is entirel with the installer.
•Responsibilit for performed control actions is full with the operator (pilot).
•If ou do not agree to the notes and warnings above, do not use this product.
Compan LAMBERT ELECTRONIC s.r.o. reserves the right to change, improve the product
or manual without prior or subsequent notice.
5/33

FLAPS_V6_HBR_datasheet_manual_EN.odt
2 Product description
2.1 Product use
Product FLAPS V6 is designed for electric control of flaps of UL aircraft. It is usuall
supplied as a set: electronic control unit + servo motor (in case of motor without internal
sensor: + position sensor + 2x protective limit switch).
THIS PRODUCT IS NOT APPROVED FOR INSTALLING IN CERTIFIED
AIRPLANES.
2.2 Main product functionalities
Basic list of main product functionalities:
•Automatic movement of the motor (flaps) to predefined positions
•user adjustable positions
•user-adjustable LBUS pin function (one of the following)
◦landing gear control output
◦input for dimming the displa elements of the device
•Possibilit to use Hone well RTY series sensor as a position sensor (automaticall
detected b the device)
•Intelligent fault detection of position sensor, motor, undervoltage, high temperature
and more
•indication of operating and fault states
2.3 Inputs
The flaps control unit has the following inputs:
•power suppl inputs (dashboard electricit from the airplane)
•input for position sensor connection
•2 inputs for optional limit switches
•dimmer signal input (shared with landing gear output control function)
6/33

FLAPS_V6_HBR_datasheet_manual_EN.odt
2.4 Controls
The flaps control unit has the following controls:
•rotar switch with 3 to 4 positions (depending on t pe)
•2 SET buttons
2.5 Outputs
The flaps control unit has the following outputs:
•motor power output
•output to landing gear control unit (shared with dimmer signal input function)
2.6 Indication
The flaps control unit has the following indication elements:
•4x two-color LED (positions correspond to the rotar switch, b combining it is
possible to achieve a total of 3 colors - orange, red, green)
The indication in this manual is represented by pictograms with the following
meaning:
LED emits some color (orange, red, green)
LED is off
LED slowl (1x/s) flashes in some color (orange, red, green)
LED fast (5x/s) flashes in some color (orange, red, green)
LED slowl (1x/s) alternates two colors
LED quickl (5x/s) alternates two colors
2.7 Protections
The flaps control unit has the following protections:
•reverse polarit protection
•protection against overvoltage spikes of both polarities
•protection against interference and short circuit at the potentiometer input
•Undervoltage protection
•High temperature protection
•short circuit protection at motor output
7/33

FLAPS_V6_HBR_datasheet_manual_EN.odt
2.8 Description of the control panel
2.8.1 Control panel HBR (4 control positions)
8/33
rotar switch
lever
(points to the set
position)
position 0 with indication
LED
position 1 with indication
LED
position 2 with indication
LED
position 3 with indication
LED
SET button (UP)
SET button (DOWN)

FLAPS_V6_HBR_datasheet_manual_EN.odt
2.8.2 Control panel HBR 3P (3 control positions)
The panel has 4 indicator LEDs, as well as the basic HBR version, but the rotar switch
lever can onl be rotated between positions 0 to 2. The IND position is onl an indicator
LED.
9/33
rotar switch
lever
(points to the set
position)
position 0 with indication
LED
position 1 with indication
LED
position 2 with indication
LED
position IND with
indication LED
SET button (UP)
SET button (DOWN)

FLAPS_V6_HBR_datasheet_manual_EN.odt
2.8.3 Differences bet een HBR and HBR 3P variants and ho to
read this manual hen using the HBR 3P variant
•The fault indication is the same as for the 4-position HBR variant
◦onl the designation of the LED at position 3 is changed to IND in this variant, ie
wherever the mention of LED 3 appears in this manual, this applies equall to
IND, ie 3 = IND
•in firmware (FW) version 2.01 of the control unit (indicated on the nameplate,
current version as of the date of publication of this manual) the following
exceptions from the functionalities for HBR 3P appl :
◦safet mode allows onl the flaps to be raised to the 0° position due to the
absence of position 3
◦passing be ond edge position 2 is not indicated b flashing LED 2
◦it is not possible to perform mirror adjustment of the positions, ie position 0
must alwa s be with the actuator piston retracted
10/33

FLAPS_V6_HBR_datasheet_manual_EN.odt
3 Specifications
3.1 Electrical characteristics
Parameter Value Unit Notes
Power suppl voltage Vin 11 ÷ 16 V
Power consumption (t p) 0.5 W @12V power suppl , stand-b state without faults,
actuator stopped at the selected position, without
dimming
load(motor) current (max) 9 A Higner current activates overcurrent protection
rated motor current 4.6 A Linak LA12 t pe
the dimming voltage range at the
DIMBOX accessor input
10 ÷ 16 V PWM frequenc 80 ÷ 200 Hz
Position sensor resistance 8 ÷ 12 kΩResistive sensor t pe
NOTE The above specifications appl to the control unit or Linak LA12 actuator
3.2 Mechanical specifications
Parameter Value Unit Notes
weight of control unit FLAPS V6
HBR
144 g
weight of Linak LA12 actuator
with 1m cable
833 g
DIMBOX accessor weight TBD g
dimensions of control unit FLAPS
V6 HBR
60 x 60 x 65 mm
dimensions of actuator Linak
LA12
266 x 85 x 50 mm Včetně upevňovacích ok, zatažená pístnice
Dimensions of DIMBOX
accessor
42 x 12 x 16 mm
11/33

FLAPS_V6_HBR_datasheet_manual_EN.odt
3.3 Allo ed operating conditions
Parameter Value Unit Notes
Operating temperature -30 ÷ +75 °C
Operating humidit 10 ÷ 90 %RH non-condensing
Operating atmospheric pressure 800 ÷ 1100 hPa
IP protection IP20 -
NOTE The above specifications appl to the control unit.
3.4 Lifetime and arranty
The product is designed with regard to its intended use, for a long service life, higher than
the intended service life (see below).
However manufacturer LAMBERT ELECTRONIC s.r.o. HIGHLY RECOMMENDS to
replace the product with a new one when it reaches its planned service life
(any of the parameters below), or at the latest 10 years after purchase.
Parameter Lifetime Notes
Device flight hours 5000 h
Motor engine hours 500 h motor overload reduces service life to 20%
Rotar switch c cles 30000 turns
Position sensor c cles 15000 passing the sensor path in one direction
Note: The above parameters are valid when the prescribed operating parameters (suppl voltage, operating
temperature, etc.) are observed. These parameters are recorded in the device and evaluated in the event of
the warrant complaint.
The manufacturer grants a 24-month warranty from the date of purchase. Exceeding
an of the above durabilit parameters will void the warrant if this occurs before the
warrant period has elapsed since the product was purchased.
The warranty also void in case of using the product in violation of this manual!
12/33

FLAPS_V6_HBR_datasheet_manual_EN.odt
3.5 Tests according to DO-160G
THIS PRODUCT IS NOT APPROVED FOR INSTALLING IN CERTIFIED
AIRPLANES.
The following tests according to DO-160G were performed on the control unit in an
accredited testing laborator , and met the criteria:
Name of the test Chapter Criterion Notes
Temperature and altitude 4 B1
Temperature Variation 5 B1
Shock & Crash safet 7 A
Vibration 8 R-B4
Magnetic effect 15 A
RF Sesceptibilit 20 TT
RF emission 21 B
13/33

FLAPS_V6_HBR_datasheet_manual_EN.odt
4 Installation in an airplane
Please pa special attention to the installation and wiring of all components of the flaps
controller when installed in an airplane. This is important for the proper functioning of the
equipment and the safet of the airplane.
4.1 Mechanical installation
The sketch below shows the dimensions needed to fit the FLAPS V6 HBR control unit to
the airplane dashboard.
Mounting holes are provided with M3 thread and 4 mm thread depth.
14/33

FLAPS_V6_HBR_datasheet_manual_EN.odt
4.2 Position sensor mounting
If an actuator without an integrated position sensor is used in the installation, it is
necessar to use an external position sensor that is rigidl mechanicall attached to the
actuator rod so that the control unit has undistorted actuator position information.
ATTENTION! The position sensor shall be mechanicall coupled so that when the piston
rod is full extended or full retracted, the position sensor is still within its valid travel
range and remains at least 5% to its edge. (For example, the Hone well RTY050 rotar
sensor has a range from -25 ° to + 25 °, so use the range from -22.5 ° to + 22.5 °)
ATTENTION! Make sure that the position sensor is mounted correctl and that it is
reliabl secured against self-releasing.
15/33

FLAPS_V6_HBR_datasheet_manual_EN.odt
4.3 Actuator installation
Observe the following points when installing the actuator:
•use the full mechanical travel range of the actuator piston rod to full retract or
extract the flaps, adjust the design of the flaps control elements so that the
actuator (piston rod) is retracted as much as possible with the zero flaps
(position 0), with full flaps (position 3, or position 2 for HBR 3P) pulled out as far as
possible
•verif the self-locking of the actuator in individual positions 0,1,2,(3) (all positions -
according to the used control unit) with respect to the maximum design loading
pressure on the flaps in flight; if the pressure exceeds the self-locking, use a higher
self-locking actuator
ATTENTION! Failure to observe the above points may result in damage to the
airplane / flaps in extreme situations
ATTENTION! If the actuator is not equipped with internal limit switches, it is
NECESSARY to install these switches externall . More about this in the relevant section
of chapter Electrical connections.
ATTENTION! If external limit switches are used in installation, it is necessar to ensure
that the are reliabl activated before the actuator piston rod hits one of its ends. Choose
the location of the limit switches with sufficient margin.
ATTENTION! If external limit switches are used in installation, make sure that the are
activated at the ends of the track, even if the are loosened slightl , b self-loosening of
the screws, or other defects on switches or aircraft components.
16/33
(POSITION 2 for HBR 3P)

FLAPS_V6_HBR_datasheet_manual_EN.odt
4.4 Electrical connections
On the back of the device there is a 10-pin Molex Mini-Fit JR connector, which is used to
connect the actuator, position sensor, limit switches, LBUS pin, power suppl .
The figure below shows a view of the back and connector with numbered pins:
Pin no. Signal name Description Notes
1 LIMSW_UP Limit switch – against flaps
rising
Opposite for inverse mechanical
coupling
2 LIMSW_DOWN Limit switch – against flaps
lowering
Opposite for inverse mechanical
coupling
3 POT_HI Position sensor suppl (+)
4 POT_MID Position sensor feedback
signal
5 POT_LOW Position sensor suppl (-)
6 VIN (+12V) Power suppl (positive)
7 OUTB Motor power output B (+) for move flaps down
8 LBUS LBUS signal adjustable function
9 OUTA Motor power output A (+) for move flaps up
10 GND Power suppl (negative)
ATTENTION! Use a suitabl rated fuse in the power suppl .
NOTE It is recommended to use shielded cabling, especiall for motor conductors (to
reduce radiated noise from the motor). Connect the shield to GND ONLY on the control
unit side. NEVER at both ends!
17/33
view of the connector in the control unit

FLAPS_V6_HBR_datasheet_manual_EN.odt
4.4.1 Electrical connections of actuator ith internal position
sensor and limit s itches
If the actuator ou are using contains both a position sensor and limit switches, connect
the control unit according to the following diagram.
ATTENTION! Alwa s refer to the documentation for the actuator used to identif the
appropriate signals for the motor and position sensor. Then connect to the corresponding
pins of the control unit connector, which are described in the table in chapter 4.4.
ATTENTION! If pins 1 & 2 are not connected to GND via external wiring, the
control unit will NOT work properly !
ATTENTION! Alwa s check with care that the actuator moves the flaps in the intended
direction and not vice versa. If it moves the other wa around, the motor wires are
probabl swapped. Then this test should be performed WITHOUT a connected position
sensor, when the control unit enters Safet (manual) mode and therefore this test will not
be affected b a potentiall inverted position sensor (which is second option what coud be
wrong).
18/33

FLAPS_V6_HBR_datasheet_manual_EN.odt
4.4.2 Electrical connections ith simple actuator, external position
sensor and limit s itches
If our actuator does NOT include a position sensor or limit switches, it is NECESSARY TO
CONNECT EXTERNAL ONES. Connect the control unit according to the following diagram,
with an example of external limit switches and Hone well RTY050 position sensor.
ATTENTION! Alwa s check with care that the actuator moves the flaps in the intended
direction and not vice versa. If it moves the other wa around, the motor wires are
probabl swapped. This test should be performed WITHOUT a connected position sensor,
when the control unit enters Safet (manual) mode and therefore this test will not be
affected b a potentiall inverted position sensor (which is second option what coud be
wrong).
ATTENTION! Alwa s make sure that it stops the actuator for the direction to be
protected before final mounting each of the limit switches. If it stops in the opposite
direction, then reverse the electrical connection of the switches – i.e. swap pins 1 and 2
on the control unit connector.
ATTENTION! When using a digital electronic position sensor (such as the RTY050), make
sure the polarit of the power suppl is correct. Alwa s read the sensor manual (different
EU and US pinning). Follow the table in chap. 4.4 of this manual describing the pins on the
control unit connector.
19/33

FLAPS_V6_HBR_datasheet_manual_EN.odt
4.4.3 Electrical connections for dimming control unit display
elements
ATTENTION! Never connect the dimmer directly to the control unit (without
DIMBOX accessory) !!! The control unit may be irreversibly damaged!
The figure below shows the wiring diagram for dimming of the indicator elements. It
shows how to connect the dimmer via DIMBOX (accessor to the FLAPS V6 HBR control
unit).
ATTENTION! For simplicit , the diagram does not include other important elements and
connections mentioned in the previous chapters! Onl those that are necessar to explain
the wiring for dimming the indicator elements.
ATTENTION! To use the indicator dimming function, ou must configure the control unit
as described in chapter 5.5 Device Setup Mode.
DIMBOX accessor has fixed wires marked with labels, more info in the table below:
Wire label Signal function desc. Notes
OUT DIMBOX output to LBUS input of control unit FLAPS V6
IN Positive input for dimmer
signal - PWM 10 ÷ 16 V,
80 ÷ 200 Hz
Dimmer with positive output PWM switching
connected to the same potential as the control
unit and DIMBOX
GND Negative power suppl (-) Connected to the same GND potential as the
control unit
20/33
Table of contents
Popular Control Unit manuals by other brands
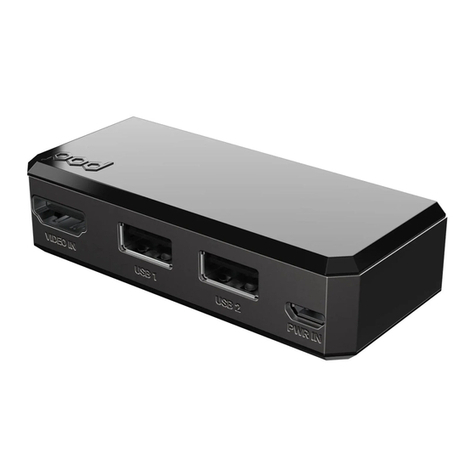
argon audio
argon audio POD manual
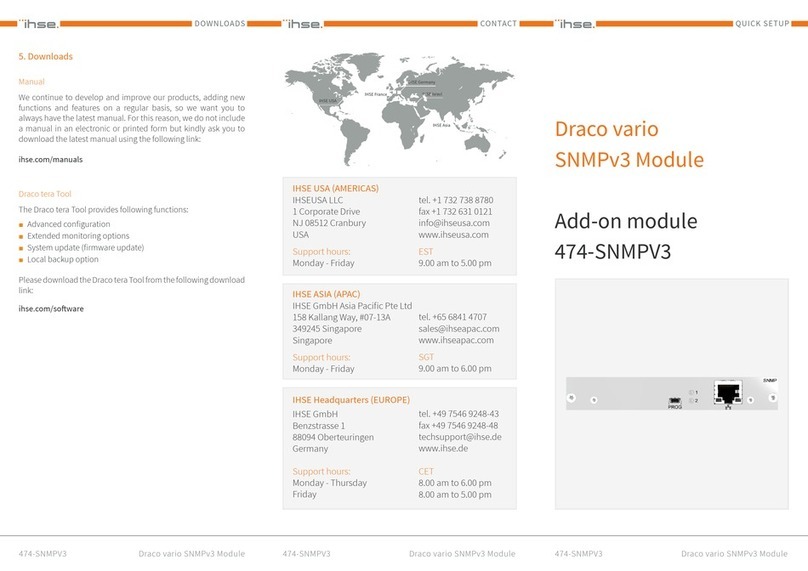
Ihse
Ihse Draco vario 474-SNMPV3 Quick setup
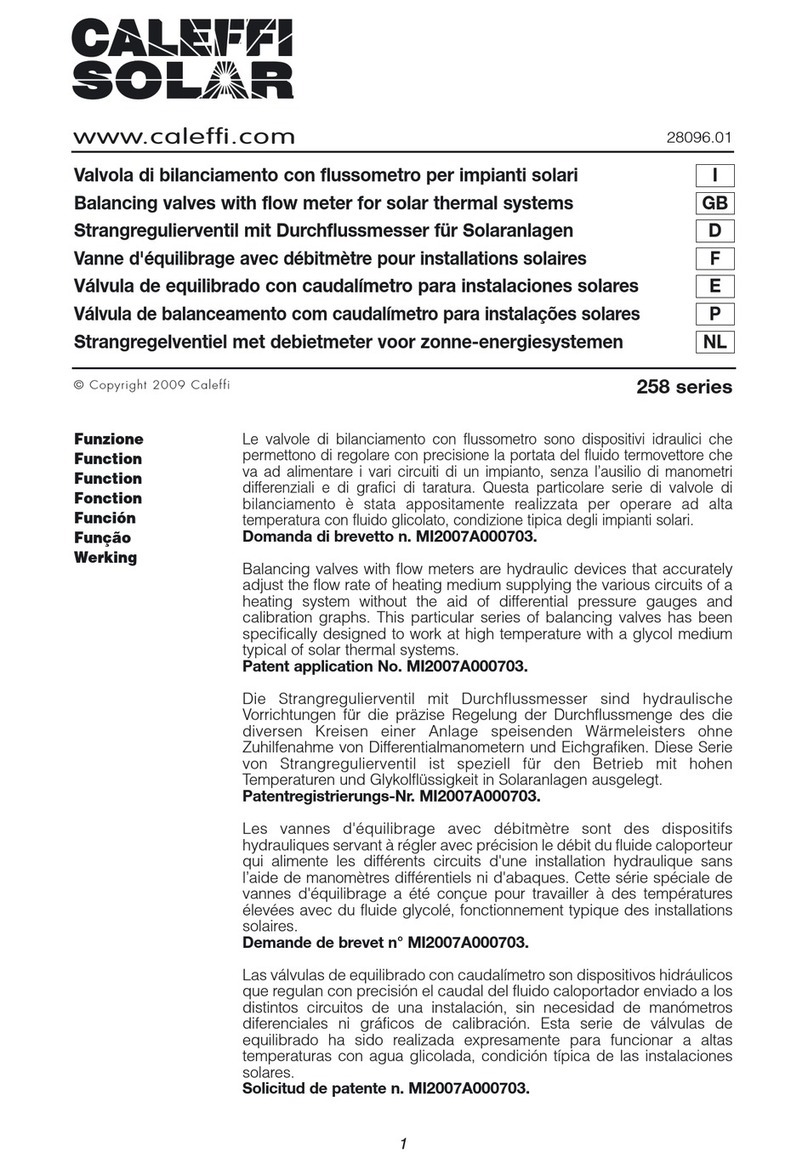
Caleffi solar
Caleffi solar 258 Series manual

GORMAN-RUPP
GORMAN-RUPP GRP33-08A Installation, operation, and maintenance manual with parts list
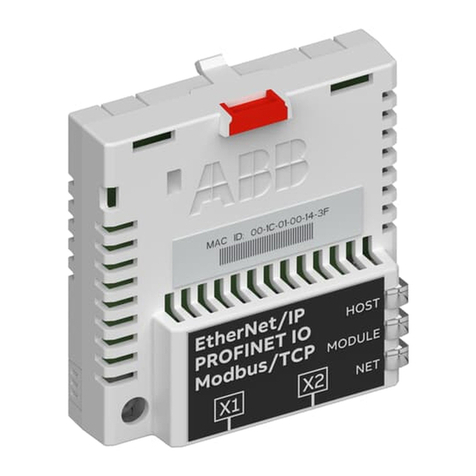
ABB
ABB FENA-21 Quick installation and start-up guide
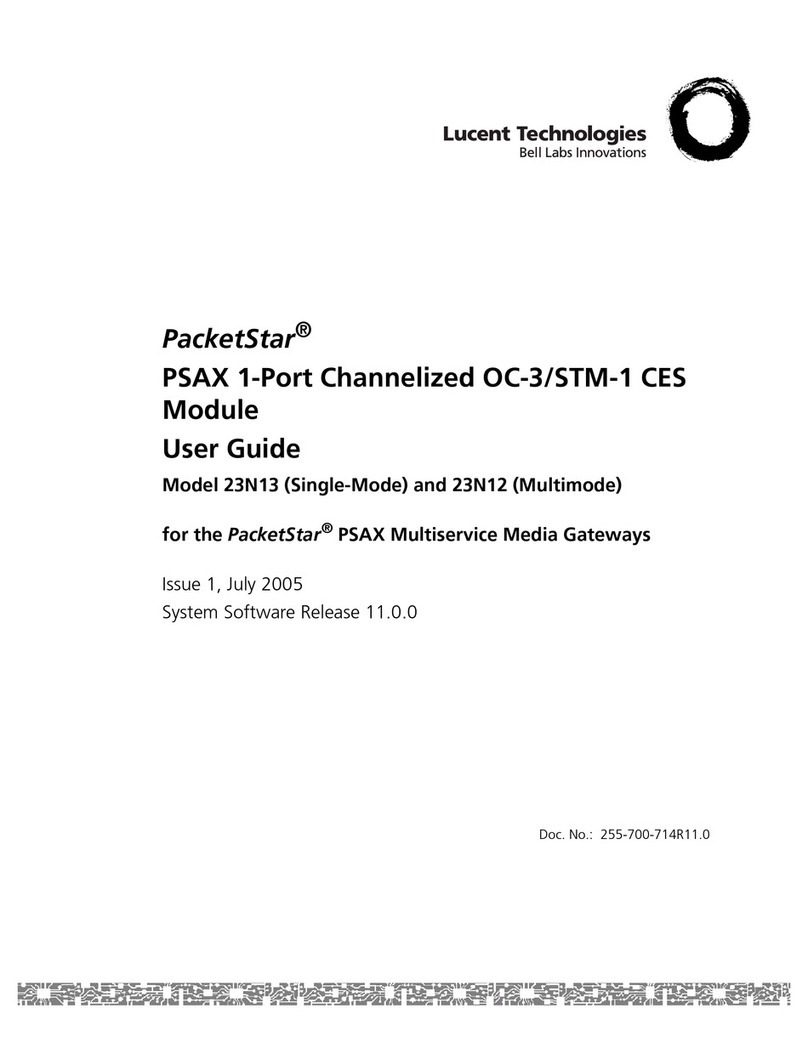
Lucent
Lucent PacketStar PSAX user guide