Leslie PMC-1 Manual

PMC-1
Electro-Pneumatic
Controller
26/2.5.1
Rev. 3
INSTALLATION, OPERATING,
AND MAINTENANCE INSTRUCTIONS
DIAGRAMS & PARTS LIST
12501 Telecom Drive, Tampa FL 33637
PMC-1 ELECTRO-PNEUMATIC CONTROLLER
T A B L E O F C O N T E N T S
Specifications . . . . . . . . . . . . . . . . . . . . . . . . . . . . . . . . . . . . . . . . . . .2
Introduction . . . . . . . . . . . . . . . . . . . . . . . . . . . . . . . . . . . . . . . . . . . .4
Operation . . . . . . . . . . . . . . . . . . . . . . . . . . . . . . . . . . . . . . . . . . . . . .4
Installation . . . . . . . . . . . . . . . . . . . . . . . . . . . . . . . . . . . . . . . . . . . . .4
Pneumatic Connections . . . . . . . . . . . . . . . . . . . . . . . . . . . . . . . . . . .4
Field Wiring . . . . . . . . . . . . . . . . . . . . . . . . . . . . . . . . . . . . . . . . . . . . .4
Start-Up . . . . . . . . . . . . . . . . . . . . . . . . . . . . . . . . . . . . . . . . . . . . . . .5
Troubleshooting . . . . . . . . . . . . . . . . . . . . . . . . . . . . . . . . . . . . . . . . .6

2
SPECIFICATIONS
SUPPLY VOLTAGE: 115 VOLTS 50/60 HZ
230 VOLTS 50/60 HZ
24V DC
OPERATING VOLTAGE RANGE: 90 TO 110% OF RATED VOLTAGE
POWER CONSUMPTION: 10 WATTS (MAX.), .7W STEADY STATE
INPUT: 4 - 20 mA (STD), PROTECTED AGAINST ACCIDENTAL 24V
INPUT TO THE CURRENT INPUT TERMINALS
RTD (OPTIONAL)
OUTPUT: 4-20 mA(STD), ACCURACY ±5% SPAN; MAX LOAD = 350 Ω
CONTROL ACTION: DIRECT OR REVERSE (SWITCH SELECTABLE)
LOCAL SET POINT ADJUSTMENT: PUSH BUTTON SWITCHES AND DIGITAL DISPLAY
REMOTE SET POINT ADJUSTMENT: 4 - 20mA STANDARD INPUT, DEFAULTS ON LOSS OF SIGNAL
DISPLAY MODES: CALIBRATION (HIGH/LOW), SET POINT, PROCESS VALUE,
DEVIATION
AIR SUPPLY: 100 PSI MAX., 40 MICRON FILTERED
OUTPUT: 0 TO MAXIMUM SUPPLY PRESSURE
AIR CONSUMPTION: NO AIR CONSUMPTION AT STEADY STATE
DISPLAY: 3-1/2 DIGIT LCD BACKLIT DISPLAY (GREEN BACKGROUND)
ACCURACY: ±0.5% OF FULL SPAN
SETTING ACCURACY: ACTUAL SET VALUE COINCIDES WITH INDICATED SET VALUE
RESPONSE SPEED RANGE: 200:1
AMPLIFIER GAIN (SLOW LOOP): NORMAL= 6(MAX); HIGH = 12(MAX)
DEAD BAND: ADJUSTABLE FROM ±0% TO 5% OF FULL SPAN
INPUT RESISTANCE TO CURRENT
LOOP: 100 OHMS X CURRENT + 0.7 VOLTS
AMBIENT TEMPERATURE: -4°F TO 140°F (-20° TO 60°C)
(HEATERS FOR -40°F OPTIONAL)
WEIGHT: 8 LBS. (3.6KG)
OVERALL DIMENSIONS
(INCLUDING MOUNTING BRACKET): 9.75” WIDE X 13.5” HIGH X 6.3” DEEP (25CM X 34CM X 17CM)
ENCLOSURE APPROVAL NEMA 1-2-3-3S-4-4X-12-13.
ENCLOSURE MATERIALS: ENCLOSURE: NORYL
HINGED COVER: POLYCARBONATE
PNEUMATIC FITTINGS: 1/8 NPT (FEMALE)
AIR DELIVERY: SOLENOID FULLY OPEN: 0.76 SCFM AT 30 PSI
1.23 SCFM AT 60 PSI
1.71 SCFM AT 90 PSI
AUTO/MANUAL: ALLOWS MANUAL OPERATION OF SOLENOID VALVES TO
LOAD OR VENT THE ACTUATOR

3
PMC CONTROLLER MOUNTING DIMENSIONS
INCHES
[MM]
A.C. Power Electrical Signal
(Input/Output)
Pneumatic Input 100 psi Max.
Vent
Pneumatic Output
FIGURE 1

WARNING - Electrical power must be supplied
through an external circuit breaker or fuse protection.
An external switch must be provided to turn off
power. Always turn off power before removing the
internal field wiring panel.
Pneumatic connections:
Connect air supply and output lines to the 1/8” NPT
connections at the bottom of the controller The center
connection is for air exhaust and is supplied with a porous
metal filter/silencer which should not be removed.
Corrosion resistant 3/8 in. O.D. tubing or 1/4 in. pipe is
recommended for the air lines. Connect air supply to the
right hand connection labeled “Input” and output to left
hand connection labeled “Output” to actuator. See Figure 1.
The supply line should be fitted with a pressure gauge and 50
micron filter/regulator to remove any floating particles. If the
supply air is mixed with traces of oil, a filter capable of
removing oil should be used. (CAUTION: Some lubricating
oils permanently damage solenoid valves.)
WARNING - Turn off electrical power before
removing the internal field wiring panel
Field Wiring:
1. After mounting the PMC-1 at the desired location, open
the cover by loosening 5 screws and the thumb screw.
Then remove the field wiring panel by loosening two
captive screws. The terminal block wiring diagram
shown in Figure 2 appears on the back of the panel.
Power and signal lines should be routed through
separate conduits to avoid interference. Transmitter or
RTD signal lines should use shielded cable grounded at
terminal 2 in insure against RF interference.
2. Connect the transmitter wires as shown in Figure 3 . A
two wire transmitter should be powered with the 24v DC
supply from the PMC-1 by connecting the positive wire
to terminal number 1 and the other transmitter wire to
terminal 3 of TB-2. Twisted pair wires can be used for
connecting the transmitter to the PMC-1. If a shielded
pair of wires is used,connect the shield to terminal 2 of
TB-2. Jumper at J5/J6 must be on J5. For 4-wire
transmitters,see Appendix B.
3. For external set point connection (4-20mA) connect two
wires to terminals 5 and 4 of TB-2. Terminal 5 is positive
(current flows into terminal 5) and terminal 4 is
negative. (See Figure 4)
A. Introduction
The Leslie PMC-1 electro-pneumatic controller can be used
to control pressure, temperature. liquid level, and other
process variables. It accepts signals from any standard 4-20
mA transmitter and provides a pneumatic output to operate a
diaphragm control valve, etc. It provides the following
features:
1) The controller supplies 24 volt D C. power for the
transmitter, eliminating the need for a separate D.C.
power supply.
2) It provides high volume air output at pressures up to 100
psig to directly operate a diaphragm control valve. I/P
transducers and valve positioners are not required or
recommended.
3) There are no small air orifices to plug or foul (.060” dia.
solenoid ports)
4) There is no air consumption except when air is being
loaded onto the control valve diaphragm.
B. Operation
The electronic circuit of the controller compares the signal
from the transmitter to the desired set point. If the error is
greater than the dead band, electrical pulses are sent to one
of the two internal air solenoid valves. One valve increases
output air pressure and the other bleeds it. Each time a pulse
is received, the resulting pressure on the diaphragm of the
control valve increases or decreases slightly. If the error is
large, the solenoid valves are held open longer to increase the
speed of output changes. For small errors, the pulse width is
decreased to prevent overshoot. The response speed
adjustment can be used to control how quickly the output
changes for a given error. Adjusting the dead band will allow
the controller to ignore small changes or “noise” in the
system. The overall result is a more accurate and stable
system.
C. Installation
Mount the controller in a location that will allow access to
the internal adjustments. See Figure 1 for mounting
dimensions. It should be mounted in a location where the
temperature will be between -4°F and 140°F. Temperatures
above or below these limits will affect the LCD although the
controller would continue to function. A location within 50
ft. of the control valve is recommended to reduce time lags in
the pneumatic signal. Where the distance to the control valve
is large, an optional external solenoid valve package (PMC-1
local control module model RCS-90) can be used.
FIGURE 2
4

CAUTION - All the pneumatic connections must be
tight enough to be leak proof for proper operation. Air
connections MUST be checked with a soapy water
solution and bubble tight.
WARNING - Keep stop valves closed until all
adjustments and checks in steps 2 -10 are completed.
WARNING - Turn off electrical power before
removing the internal field wiring panel.
2) Take off field wiring panel by loosening screws.
3) Set the direct/reverse switch (SW3) to the proper
position. (See Figure 7). When set on direct, the air
output will increase when the signal from the
transmitter increases and vice versa.
For example, if the system is being used to control
pressure downstream of a normally closed control valve,
reverse action would be required (increasing system
pressure will increase the signal from the transmitter
and this must produce a decrease of output signal air
pressure to close the control valve).
4) Install the set point selector jumper J16-J21. This
jumper allows the PMC-1 to operate in one of two
different set point modes, local or remote.
LOC Local set point
REM/LOC
REM/LPOS
REM/VENT
REM/LOAD
}
REM/ZERO
Installing jumper in ‘LOC” (local) position allows set
point adjustments using the up or down push buttons
located on the front panel, only when the “SP” LED is lit.
By inserting the jumper in any of the remaining five
positions, the controller accepts a (4-20mA) external set
Remote set point
with selection of
defaults.
4. Terminals 8 through 12 have been reserved for adding
future options to the controller.
5.
Terminals 13, 14, 15 are used to connect the optional
local control module model RCS-90. This module can be
used if the PMC-1 is mounted at a remote location from a
control valve.
6. When the PMC-1 is being used as a temperature
controller with an RTD, an optional signal conditioning
card, calibrated for a temperature range suitable for the
process, must be installed in TB 5. Jumper at J5/J6 must
be on J6. (See figure 7) For a 3 wire RTD, connect the
two RTD wires that are internally connected together
(zero resistance between them) to terminals 16 and 17
and the remaining connection to terminal 18 of TB-2.
(See Figure 5). For a 2 wire RTD, jump terminals 16 and
17. (See Figure 6). See Appendix C for guidelines on
practical distance limitations.
7.
Power and signal lines should be routed through separate
conduits to avoid interference. Set the 115/230 voltage
switch (SW1) to match the supply voltage. DO NOT TURN
ON A.C. POWER YET. With AC power circuit breaker
OFF, connect power leads (unpowered) to TB-1 (Figure 7).
Connect the black wire (HI) to terminal 1, the white wire
(LO) to terminal 2 and the green or green/yellow earth
ground wire to terminal 3 of TB-1. If the PMC-1 is power-
ed by 24v DC, connect the positive connection to terminal
6 and the negative connection to terminal 7 of TB-2, and
DO NOT connect any wires to TB-1. (See Figure 8).
8. For 4-20mA output, connect recorder, alarms or other
auxiliary device to TB-7 noting the polarity. NOTE: The
4-20mA output will be within ±0.5% (of span) of the
value indicated on the PMC-1. Re-calibrate the remote
device to agree with the PMC-1, do not re-calibrate the
PMC-1.
D. Start-Up
1) Close stop valves upstream and downstream of the
diaphragm control valve.
WIRING DIAGRAMS FOR TYPICAL INSTALLATIONS
Wiring Connections for 4—20 mA Transmitter (e.g. pressure or level)
4—20 mA transmitter return
Ground
24 VDC power output to transmitter
Wiring Connections for External Set Point
4—20 mA input
4—20 mA return
FIGURE 3
FIGURE 4
5
NOTE:
Jumper J5/J6
must be on J5

point signal with five selectable defaults in case of loss of
external set point signal.
“REM/LOC” Controller will default to Local set point control.
“REM/LPOS”
Default to the last valve position prior to loss of signal.
“REM/VENT” Vent air from actuator on loss of signal.
“REM/LOAD” Load air into the actuator on loss of signal.
“REM/ZERO” Default to “ZERO” set point on loss of signal.
5) If the PMC-1 is being used for controlling slow reacting
processes like temperature and level, select the control for-
mat for slow-acting control loops by moving the process
speed switch to the “SLOW” position. (See figure 7). For
fast processes (like pressure control) switch the process
speed switch to the “FAST’ position. For control loops
other than pressure, temperature, or level, install the
PMC-1 with the control format that will be most suited to
the control system’s reaction to control valve change.
6) For initial adjustment, turn the response knob to mid
position, and dead band to position 0.5.
7) Connect the appropriate jumper, as shown in Figure 7 to
locate the decimal point for maximum resolution of the
display in relation to the input transmitter. (The PMC-1
is shipped with the jumper at J10). The following table
shows the range of the display at each jumper position.
The LCD display reads the value of the selected mode as
indicated by the lit LED.
EXAMPLE: If the PMC-1 controller is being used to
control pressure, and the pressure transmitter is
calibrated for a range of 0-100 psig, then the maximum
resolution will be achieved by placing the decimal point
between the third and fourth digits (J9), so that the
display will read “100.0” at full scale.
8) Replace the field wiring cover and turn on the external
electrical power.
9) Display calibration using mode selection button.
The display can be calibrated in a range from-1000 to
+1999 units. A decimal point can be placed after the
second, third or fourth digit. If a change is required,
turn off the external power, then see step 7, above.
a) Press the mode selection button until the “Calibrate
LO” LED is lit. Using a small screw driver supplied
with the unit adjust the “LO” potentiometer on the
front of the panel so that the display indicates the
bottom range of the transmitter.
b) Press the mode selection button until the “Calibrate
Hl” LED is lit. Adjust the “HI” potentiometer on the
front of the panel so that the display indicates the top
range of the transmitter.
EXAMPLE ONLY: DO NOT CALIBRATE TO THESE
VALUES. If the PMC-1 controller is being used to
control temperature, and the RTD with optional
circuit card is calibrated for -25 deg. C to +175 deg. C,
then the display must be calibrated to read “-25.0”
when the “CALIBRATE LO” LED is lit, and “175.0”
when the “CALIBRATE Hl” LED is lit.
J7 = 0.000 to ±1.999
J8 = 00.00 to ±19.99
J9 = 000.0 to ±199.9
J10 = 0000 to ±1999
10) Using one of the pressure sensitive labels supplied, label
the display to indicate the unit of measurement for your
process, i.e. pressure, temperature, gpm, etc.
11 ) Adjust the air supply pressure to the controller by
adjusting the filter/regulator. The pressure should be set
5 to 10 psig higher than required to operate the
diaphragm control valve. Do not exceed 100 psig or the
rating of the equipment served, whichever is less.
12) Push the mode select button until the “SP” LED lights
up. Using the up/down buttons, adjust LCD display
observing operation of the diaphragm control valve. If it
does not move in the proper direction use the
direct/reverse switch (SW3) to obtain desired operation
of the valve.
13) Adjust the set point to move the control valve to the
closed position.
14) The system can now be started.
WARNING - This instruction can not cover the
safety precautions and procedures required for safe
start-up of every system. Make sure you understand
the system and its safe operation before start-up.
15) For bumpless transfer, move the auto/manual switch to
the manual position. Select the “SP” (set point) mode
and adjust to desired set point. Select the ‘PV’’ (process
value) mode. Using the load or vent buttons, adjust the
system until the display agrees with the set point. Move
the auto/manual switch to the auto position for
continued automatic control.
16) Adjust response speed and dead band to provide stable
control. Maximum speed and minimum dead band will
provide the highest accuracy but the system may cycle.
It’s best to adjust the response speed and dead band at
minimum and maximum system flows.
Initial Tunlng
17) Adjust response speed and dead band as follows:
Temperature or level control Speed of response 3.0
Dead band .5
If temperature or level cycles, reduce speed of response.
If no cycling is occurring, keep increasing speed or
response until cycling begins, then back off half a unit.
Pressure or flow control Speed of response 6.0
Dead band .5
If pressure or flow cycles, reduce speed of response. If no
cycling is occurring, keep increasing speed of response
until cycling occurs, then back off half a unit.
The ideal tuning of the PMC-1 would be the maximum
speed of response and minimum dead band setting you
can use without the system going into constant
oscillation after an upset.
E. Troubleshooting—General
1) System cycles
a) Make sure Pneumatic connections from PMC-1 to the
valve are leak free. (Check with soapy water)
b) Adjust dead band and response speed. (See step 17 of
start-up instructions).
c) Check that the diaphragm control valve is operating
within its rated flow rangeability (usually 10-90%
open) and valve stem doesn’t stick.
6

7
FIGURE 5
CONNECTING AN RTD TO THE PMC
FIGURE 6
PMC-1
16 17 18
Usually black
Black
Red
TB-2
Approximate
resistance = 0 Ω
Approximate
resistance
@ 75°F = 109 Ω
Unused terminal (not connected)
3 Wire RTD Head
Wiring Connections for Two—Wire RTD (temperature)
Jump
Black RTD lead
Red RTD lead
Terminal colored red
or other contrasting color
NOTE:
Jumper J5/J6
must be on J6.

8
2) Control valve operates in the opposite direction required
to satisfy the system .
a) Check position of direct/reverse switch.
3) Controller does not operate at all (LCD display off).
a) Check A.C. power connection.
b) Check fuse (F1 in Figure 2).
c) PMC-1 operates but no display, replace LCD display.
4) Controller does not respond to changes in local set point
adjustment.
a) Check that the set point jumper is in the local
position.
5) Controller does not respond to changes in the controlled
variable.
a) Check connections and signal from transmitter.
b) Re-check LO-HI calibration and set point.
6) The displayed process value does not match the actual
when measured against thermometer or pressure gauge.
a) Check display calibration (step 9 of start-up
instructions).
b) Check calibration of transmitter. (See instructions
supplied with transmitter).
c) Remember, the accuracy of the PMC-1 is ±.5% of span
(much better than most gauges or thermometers).
For example, if calibration was from 32-212°F, the
span is 180° so the indicated temperature of the PMC-
1 would be within (.005 x 180) .9°F of actual.
7) Control valve does not respond to controller output.
a) Check filter/regulator supplying air to controller to
make sure that the output pressure is 5-10 psig higher
than the pressure required to fully stroke the valve.
b) Check actuator operation.
8) Process never quite makes the set point.
a) Check pneumatic connections for leaks.
For Temperature Control Systems
1) RTD connection to PMC-1
a) If an RTD is being used, make sure that the wires are
connected according to the diagram in the PMC-1
Installation and Operation Manual. If in doubt,
measure the resistance across the terminals, as shown
in Figure 5.
2) RTD installation in piping
a) If the process temperature indicated by the PMC-1 (a
function of the RTD signal) lags considerably behind a
thermometer installed in the process line, check to
make sure that the RTD is installed directly into the
flow path of the process fluid. Unless absolutely
necessary, the RTD should not be inside a thermowell.
If the above steps have been taken and the lag is still
too great, thermocouple with transmitter may be
necessary.
3) RF interference
a) For best protection from radio frequency interference.
make sure that the temperature sensing element is
connected to the PMC-1 using shielded cable that the
shielding is connected to the earth ground.
4) Insufficient air pressure to PMC-1
a) Make sure that the air pressure supplied to the PMC-1
is sufficient to fully stroke the control valve or to
provide the maximum outlet pressure required from a
regulator.
5) Leaks in pneumatic lines
a) Small pneumatic line leaks can cause control
instability, particularly when using the PMC-1 with a
regulator. Use a soap solution or “snoop” to locate
possible leaks.
6) Too much air pressure to PMC-1
a) If too much air pressure is supplied to the PMC-1, it
can overload the actuator or regulator diaphragm
causing overshoot and slow response when venting is
required.
7) Inaccurate calibration
a) If the process temperature indicated by the PMC-1 is
significantly different from the temperature indicated
by a thermometer, check to make sure that the PMC-
1 is calibrated according to the range of the signal
conditioning card installed (if using an RTD) or the
range of the temperature transmitter (if using a
thermocouple).
8) Trapping problems
a) A steam trap that is under sized or malfunctioning
can cause the heat exchanger to flood during high
load conditions, giving rise to wide swings in process
temperature. Check for this problem by manually
bypassing the trap under full load conditions, and
observe whether there is an improvement in
temperature control.
9) Incorrect Installation of Regulator
a) A poorly installed regulator can cause cycling. Make
sure that the regulator is installed in the proper
orientation and that the sensing line is installed to
provide proper condensate drainage, as indicated in
the regulator’s Installation and Operation Manual.
10) Poor performance or malfunction of control valve
a) A malfunctioning control valve component, such as a
leaking or broken actuator stem seal, can cause the
system to work poorly or not at all. Also, if an existing
control valve from another manufacturer has been
used in the system, check for hysteresis, ability to
throttle properly, and sizing (over or under).
10 Most Common Problems
1 ) Leaky air connections - must be tested bubble tight with
soapy water solution.
2) Incorrect field wiring. Re-check connections in reverse
order of how they were connected.
3) Loose connections.
4) Incorrect calibration.
5) Speed of response and dead band adjustment.
6) Insufficient air pressure supply.
7) LCD decimal selector in wrong position.
8) Oversized or malfunctioning control valve/regulator.
9) Poor condensate drainage from heat exchangers.
10) Wrong supply voltage.

FIGURE 8
FIGURE 7
Wiring Connections for 24VDC Power
24VDC
External Power Supply
9
Improper installation or maintenance of this equipment
can cause damage or personal injury.
1. When installing new equipment, check that it is suitable
for the fluid, pressures and temperatures in your system.
2. Make sure that all pressure has been vented from the
system before loosening or disassembling any part of the
piping system or valve.
3. Before pressurizing the system, make sure that all bolts
and gasket joints are tight.
4.
When starting up the system, open inlet and outlet stop
valves slowly to prevent fluid hammer and thermal shock.
5. Use genuine Leslie replacement parts. Other parts may
look the same but may have lower strength or
temperature limits.
If you have any questions about the installation, repair or
operation of your Leslie equipment, please call Leslie
Controls or your local representative.
NOTE:
Unit is shipped with jumper wire in position J5 for pressure applications.
For temperature applications, move jumper wire to position J6.
J1 CONNECTS “EXT SET” POINT VOLTAGE (0.4 TO 2 VOLTS) TO TB-2 TERMINAL 8
(MARKED AUX# ON PC BOARD)
J2 CONNECTS “PV” VOLTAGE (0.4 TO 2 VOLTS) TO TB-2 TERMINAL 9 (MARKED AUX
#2 ON PC BOARD)
J3 CONNECTS “DEV” VOLTAGE (0-±4 VOLTS) TO TB-2 TERMINAL 10 (MARKED AUX #3
ON PC BOARD). THIS IS HIGH IMPEDANCE OUTPUT.
J4 CONNECTS 24V INTERNAL POWER TO SOLENOID. IF SOLENOIDS ARE POWERED
EXTERNALLY BY EXTERNAL POWER SUPPLY (WHEN SOLENOIDS ARE DIFFERENT
FROM STANDARD) J4 MUST BE REMOVED AND EXTERNAL POWER CAN BE
BROUGHT TO THE SOLENOIDS AT TB-2 PIN 14.
J5 JUMP WHEN EXTERNAL 4-20MA PROCESS FEEDBACK TRANSMITTER IS USED
-OR-
J6 JUMP WHEN RTD SIGNAL CONDITONAL CARD IS INDSTALLED IN THE PMC-1.
J7 DECIMAL POINT SELECT, REFER TO SECTION D, PARA. 7.
J8 DECIMAL POINT SELECT, REFER TO SECTION D, PARA. 7.
J9 DECIMAL POINT SELECT, REFER TO SECTION D, PARA. 7.
J10 DECIMAL POINT SELECT, REFER TO SECTION D, PARA. 7.
J11
SLOW LOOP GAIN ADJUSTMENT (DERIVATIVE GAIN ADJUSTMENT). J13 IS DEFAULT.
J12
SLOW LOOP GAIN ADJUSTMENT (DERIVATIVE GAIN ADJUSTMENT). J13 IS DEFAULT.
J13
SLOW LOOP GAIN ADJUSTMENT (DERIVATIVE GAIN ADJUSTMENT). J13 IS DEFAULT.
J14
SLOW LOOP GAIN ADJUSTMENT (DERIVATIVE GAIN ADJUSTMENT). J13 IS DEFAULT.
J15
SLOW LOOP GAIN ADJUSTMENT (DERIVATIVE GAIN ADJUSTMENT). J13 IS DEFAULT.
J16 SET POINT DEFAULT CONDITION SELECTOR, REFER TO SECT. D, PARA. 4.
J17 SET POINT DEFAULT CONDITION SELECTOR, REFER TO SECT. D, PARA. 4.
J18 SET POINT DEFAULT CONDITION SELECTOR, REFER TO SECT. D, PARA. 4.
J19 SET POINT DEFAULT CONDITION SELECTOR, REFER TO SECT. D, PARA. 4.
J20 SET POINT DEFAULT CONDITION SELECTOR, REFER TO SECT. D, PARA. 4.
J21 SET POINT DEFAULT CONDITION SELECTOR, REFER TO SECT. D, PARA. 4.
J22 CONNECTS EXTERNAL SIGNAL FROM TB-2 PIN8 (AUX 1) TO STEERING CIRCUIT IF
USED, J1 JUMPER MUST BE REMOVED.
-OR-
J23 CONNECTS INTERNAL PROCESS SPEED CONTROL CIRCUIT, TO STEERING
CIRCUIT
J24 CONNECTS DERIVATIVE CIRCUIT OUTPUT SIGNAL TO TB-2 PIN9 (AUX 2). IF USED,
REMOVE JUMPER J2.
-OR-
J25 DO NOT USE (STRICTLY FOR FACTORY USE).
J26 CONNECTS CIRCUIT COMMON TO TB-2 PIN7.
J27 INACTIVE. CONNECTS TO AN OPTIONAL BOARD, IF INSTALLED.
J28 INACTIVE. CONNECTS TO AN OPTIONAL BOARD, IF INSTALLED.
J29 INACTIVE. CONNECTS TO AN OPTIONAL BOARD, IF INSTALLED.
CAUTION

APPENDIX A
WIRING MULTIPLE DEVICES
IN SERIES WITH THE PMC-1
10
The PMC-1 is provided with a 4-20mA output for recorders,
alarms, etc. It may be possible to overload the 4-20mA
output, and additional devices need to be powered in series.
The purpose of this Appendix is to provide guidelines for
wiring another device, such as a chart recorder, in series
with the PMC-1 and a transmitter.
The acceptability of such a practice is based on the following
rule: The total voltage drop of all devices in the circuit must
be less than the output voltage of the power supply.
The PMC-1’s power supply puts out a total of 24 VDC to the
transmitter circuit. As stated in the specifications, the input
resistance of the PMC’s transmitter circuit is 100Ω. Using
Ohm’s law, the voltage drop at 20mA (.020 Amps) can be
calculated as follows:
Voltage (V) = Resistance (R)
Current (I)
Voltage = Resistance x Current
Voltage = 100 x .020 + 0.7
Voltage = 2.7 Volts
Thus, at 20mA, the voltage drop of the PMC’s transmitter
loop is 2.7 volts.
EXAMPLE:
The PMC-1 is being used in a level control application. The
differential pressure transmitter used to measure the level
has a minimum power requirement of 12 volts. A chart
recorder with an impedance (resistance) of 450Ωis being
considered for use with the level control system. Can the
chart recorder be wired in series with the PMC-1 and dp
transmitter?
Voltage (Chart Recorder) = 450Ωx .020 = 9 V
Total Voltage = 2.7(PMC-1) + 12(dp Transmitter) +
9(Chart Recorder)
Total voltage = 23.7 V
Since the total voltage is less than the 24 volt output of the
power supply, the chart recorder can be wired in series with
the PMC-1 and dp transmitter.
Note: Long lengths of wire can result in additional resistance
in the loop and must be considered when the total voltage
drop from all devices in the loop approaches the voltage of
the power supply output. When in doubt, consult Leslie for
assistance.
PMC-1
Recorder
(4-20mA Input)
Transmitter

APPENDIX B
CONNECTING 2-WIRE AND 4-WIRE
TRANSMITTERS TO THE PMC-1
Electronic transmitters used to measure pressure, level, and
other variables are classified as 2-wire or 4-wire, depending
on how they are powered. The PMC-1 can be used with either
type of transmitter.
The most common transmitter type is the 2-wire transmitter,
which has one power input wire (24VDC nominal) and one
signal output wire (4-20 mA) . In most cases, there is actually a
third wire leading from the transmitter, but it is still referred
to as 2-wire.
The 2-wire transmitter is connected to the PMC-1 as shown
in Figure 8. Terminal 1 supplies 24vDC power to the
transmitter, and terminal 3 receives the 4-20mA signal back.
11
Terminal 2 is an earth ground.
A 4-wire transmitter needs two additional wires, because it
receives its power from a separate power source. This type of
transmitter can also be used with the PMC-1, and it is
connected as shown in Figure 9. Since it receives its power
from a separate source, terminal 1, the PMC-1’s power is not
used. The 4-20mA signal from the transmitter is connected
to terminal 3, as in the case of the 2-wire transmitter, but the
circuit is completed by connecting the other wire from the
transmitter to terminal 4, circuit common. If the transmitter
is equipped with an earth ground, it should be connected to
terminal 2.
PMC-1
24VDC
Earth Ground
4-20mA
2-Wire
Transmitter
Circuit Common
4-Wire
Transmitter
Power
Source
PMC-1
Earth Ground
4-20mA
* 1
* 2
* Terminal connections for Ashcroft transmitters only

APPENDIX C
RTD DISTANCE LIMITATIONS
WITH THE PMC-1 ELECTRO-PNEUMATIC CONTROLLER
When using the PMC-1 electro-pneumatic controller to control
temperature with an RTD and optional built-in signal
conditioning card, consideration must be given to the distance
of the RTD from the PMC-1 controller.
Since the RTD changes resistance in proportion to
temperature change, the signal received by the signal
conditioning card installed in the PMC-1 is a variable voltage
signal. The signal conditioning card converts the voltage signal
into a 4-20mA signal, which can be used by the PMC-1.
The wire connecting the RTD to the PMC-1 provides additional
resistance, which varies according to the gauge and length of
the wire Although the additional resistance of the wire is
insignificant over short distances, it can affect accuracy over
long distances. The following guideline can be used to insure
that any error induced by wire length will be less than 1%.
12
MAX. LENGTH
WIRE GAUGE FOR 3-WIRE RTD
AWG mm2 Feet Meters
20 .50 90 27.4
22 .25 55 16.8
24 .22 30 9.1

APPENDIX D
CONTROL OF AIR SIGNAL ON POWER LOSS
FOR PMC-1 ELECTRO-PNEUMATIC CONTROLLER
The PMC-1 electro-pneumatic controller modulates a control
valve by loading or unloading air to the control valve’s
pneumatic actuator in a series of pulses. These pulses are
controlled inside the PMC-1 by two normally closed solenoid
valves.
If the AC power to the PMC-1 should fail for any reason, both
internal solenoid valves will remain closed, and the control
valve will be locked in its last position. If the avoidance of
sudden process changes on power loss is important, this
lock-up action is a desirable feature.
In certain situations, however, safety considerations may
dictate the use of a normally closed control valve that should
shut down the system on loss of power to the controller. In
such cases, the arrangement shown above is recommended.
A standard three-way solenoid valve is installed in the air line
between the PMC-1 and the control valve. The solenoid is
energized from the same power source used by the PMC-1.
When the solenoid is energized, ports B and C are connected,
and the pneumatic circuit between the PMC-1 and control
valve is complete. On loss of power, the solenoid is no longer
energized, and ports A and B are connected, allowing the
pressure on the actuator diaphragm to vent to atmosphere. If
a normally closed actuator has been selected, the control
valve will close, and the system will shut down.
A simpler solution, however, is the PMC-1/Vent on Power
Failure option which eliminates the need for a separate
three-way solenoid valve. Both the venting solenoid and its
power source are included in the PMC-1 internally mounted.
No extraneous air lines or power sources are needed.
13
PMC-1
Up to 100 psi
Plant air
Airset
Line power
Transmitter
Three-way
solenoid valve

APPENDIX E
TYPICAL TEMPERATURE CONTROL APPLICATION
FOR PMC-1 ELECTRO-PNEUMATIC CONTROLLER
The Leslie PMC-1 electro-pneumatic controller provides an
accurate, economical alternative to conventional pneumatic
or electronic controllers. A standard RTD (resistance
temperature device) is connected to the PMC-1 at the
dedicated RTD input terminals. An optional signal
conditioning card installed in the PMC-1 converts the
resistance signal from the RTD into a 4-20mA signal. The
PMC-1 compares the input from the signal conditioning card
to the set point, and, using a series of short pneumatic
pulses, modulates the control valve as required to maintain
the set point. The PMC-1’s “slow loop” control mode can be
selected for enhanced control in systems that respond slowly
to control valve changes.
During installation, the PMC-1 is calibrated by dialing in the
upper and lower limits of the signal conditioning card. The
set point and process status can then be read directly from
the backlit LCD display. The PMC-1 can be calibrated to
display the temperature in either Fahrenheit or Celsius
degrees.
14
PMC-1
Up to 100 psi
Plant air
Airset
Optional signal conditioning card installed
Drive current
Resistance Signal (Ohms)
Hot out
Trap
Cold in
Steam RTD

APPENDIX F
TYPICAL PRESSURE CONTROL APPLICATION
FOR PMC-1 ELECTRO-PNEUMATIC CONTROLLER
A standard pressure transmitter is connected to the PMC-1 at
the transmitter input terminals. The PMC-1 provides 24VDC
power to the pressure transmitter, compares the 4-20mA
signal returned to the set point and, using a series of short
pneumatic pulses, modulates the control valve as required to
maintain the desired pressure.
The pressure transmitter is connected to the process pipe by
means of a pig tail and isolating valve. The isolating valve
provides the ability to change or calibrate the pressure
transmitter without otherwise disturbing the system. The pig
tail is important in steam applications to avoid overheating
the pressure transmitter. The loop in the pig tail maintains a
condensate buffer between the steam and the sensing
diaphragm of the pressure transmitter.
During installation, the PMC-1 is calibrated by dialing in the
upper and lower limits of the pressure transmitter. The set
point and process status can then be read directly from the
backlit LCD display in the units of measurement preferred by
the user.
15
PMC-1
Up to 100 psi
Plant air
Airset
4-20mA
24VDC
Pressure transmitter
Pigtail

APPENDIX G
TYPICAL LEVEL CONTROL APPLICATION
FOR PMC-1 ELECTRO-PNEUMATIC CONTROLLER
The Leslie PMC-1 electro-pneumatic controller provides an
accurate, economical alternative to conventional pneumatic
or electronic controllers. A standard differential pressure
transmitter is connected to the PMC-1 at the transmitter is
connected to the PMC-1 at the transmitter input terminals.
The PMC-1 provides 24VDC power to the dp transmitter,
compares the 4-20mA signal returned to the set point and,
using a series of short pneumatic pulses, modulates the
control valve as required to maintain the desired level. The
PMC-1’s slow loop control mode can be selected for
enhanced control in systems that respond slowly to control
valve changes.
In a closed system, the differential pressure transmitter is
piped as shown above. The upper sensing line measures the
static pressure in the system and acts as a reference point.
the difference between the upper and lower sensing lines is
the head pressure of the liquid. In an open system, the
reference line is vented to atmosphere. A three-valve
manifold is recommended for use with the dp transmitter to
facilitate isolation of the transmitter for replacement or in-
line calibration.
During installation, the PMC-1 is calibrated by dialing in the
upper and lower limits of the differential pressure
transmitter. The set point and process status can then be
read directly from the backlit LCD display in the units of
measurement preferred by the user.
When ordering a dp transmitter for use in a liquid level
application, it is important to specify the range (high/low
level limits) and the suppression (“WC” in reference line).
PMC-1
Up to 100 psi
Plant air
Airset 4-20mA
24VDC
DP transmitter with
3-valve manifold
26/2.5.1Rev.3-0103
12501 Telecom Drive, Tampa, FL 33637
Ph: (813) 978-1000 • Fax: (813) 978-0984
www.lesliecontrols.com
Table of contents
Other Leslie Controllers manuals
Popular Controllers manuals by other brands

SOMFY
SOMFY TaHomaPad io Installer manual
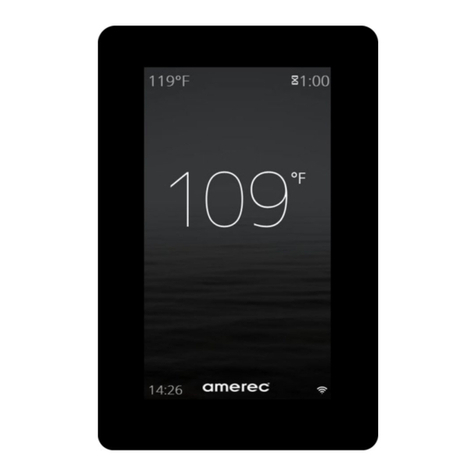
Amerec
Amerec Elite operating instructions
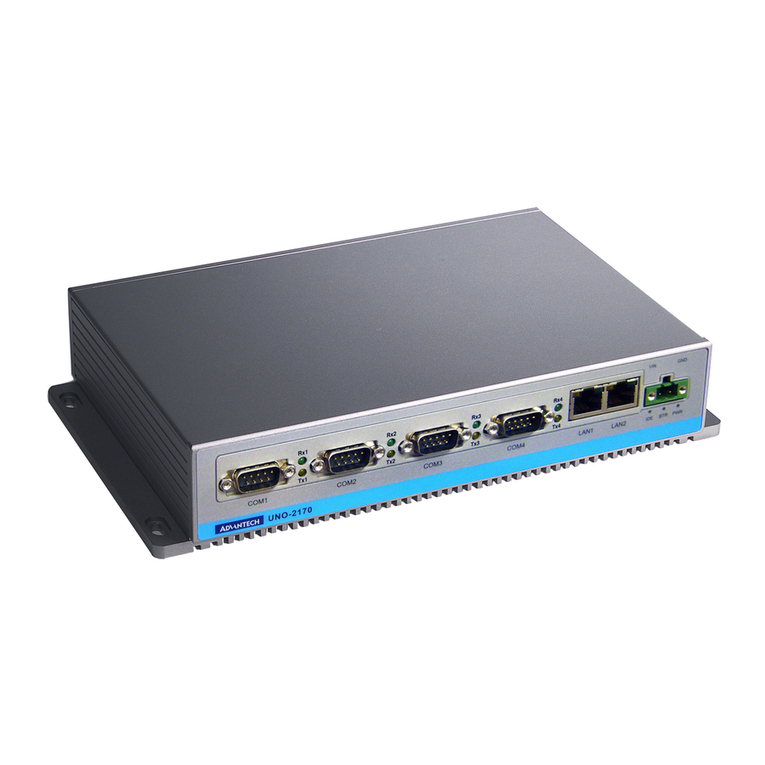
Advantech
Advantech Celeron M Universal Network Controller with PC/104 Extension... user manual
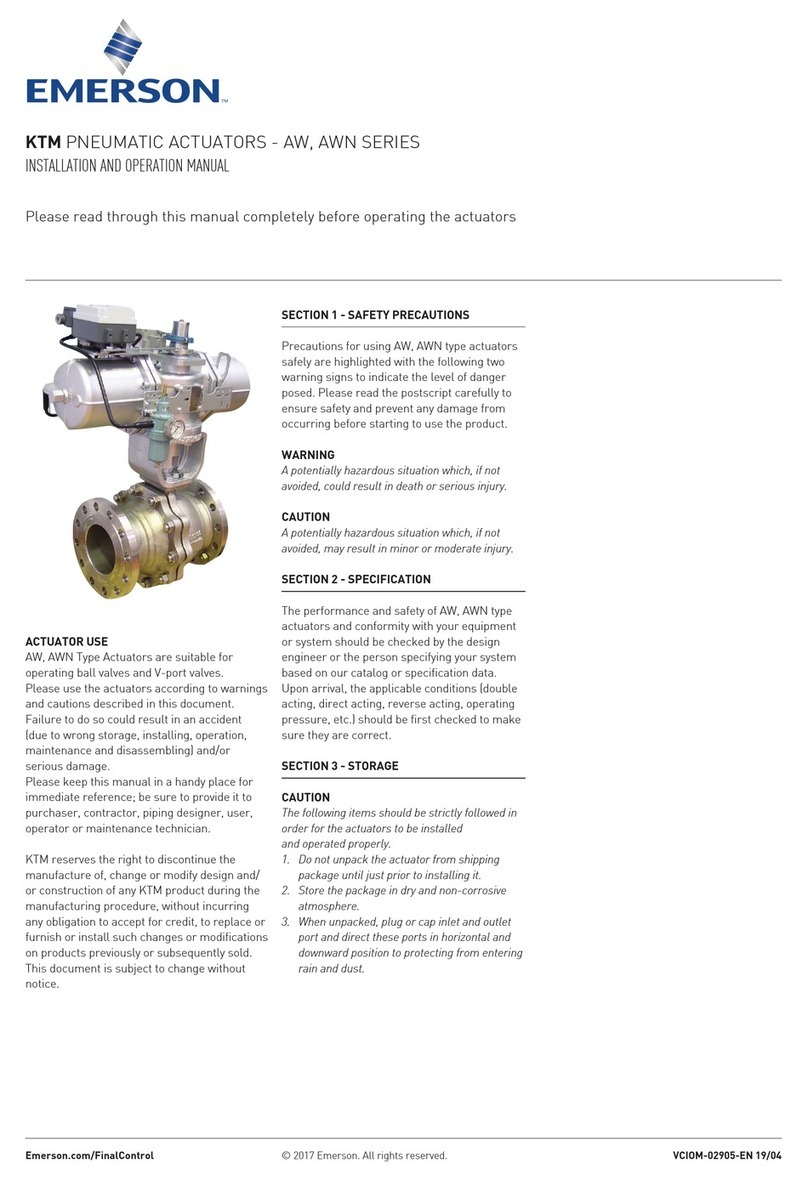
Emerson
Emerson AW Series Installation and operation manual

Contemporary Research
Contemporary Research ICC-ZS2 product manual
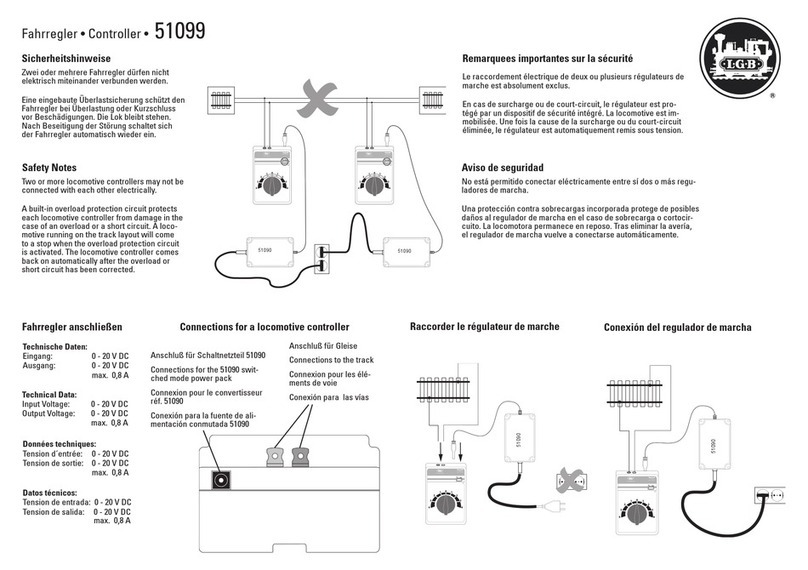
L. G. B.
L. G. B. 51099 instructions
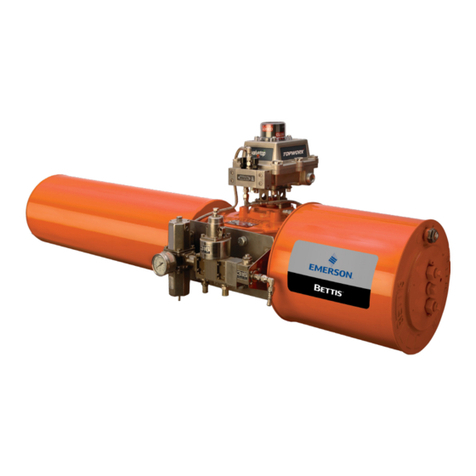
Emerson
Emerson Bettis G Series Installation, operation and maintenance manual
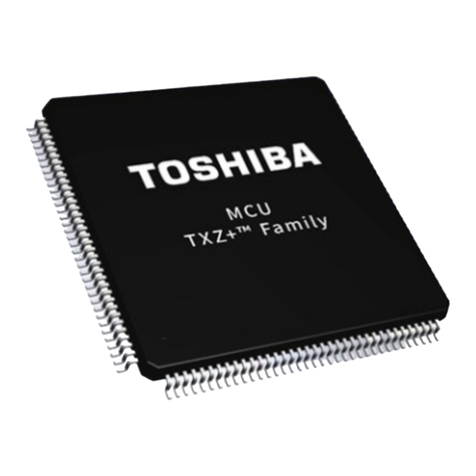
Toshiba
Toshiba TXZ+ Series Reference manual

AudioCodes
AudioCodes Mediant 4000 quick guide

Dakota Digital
Dakota Digital PAC-3500 manual
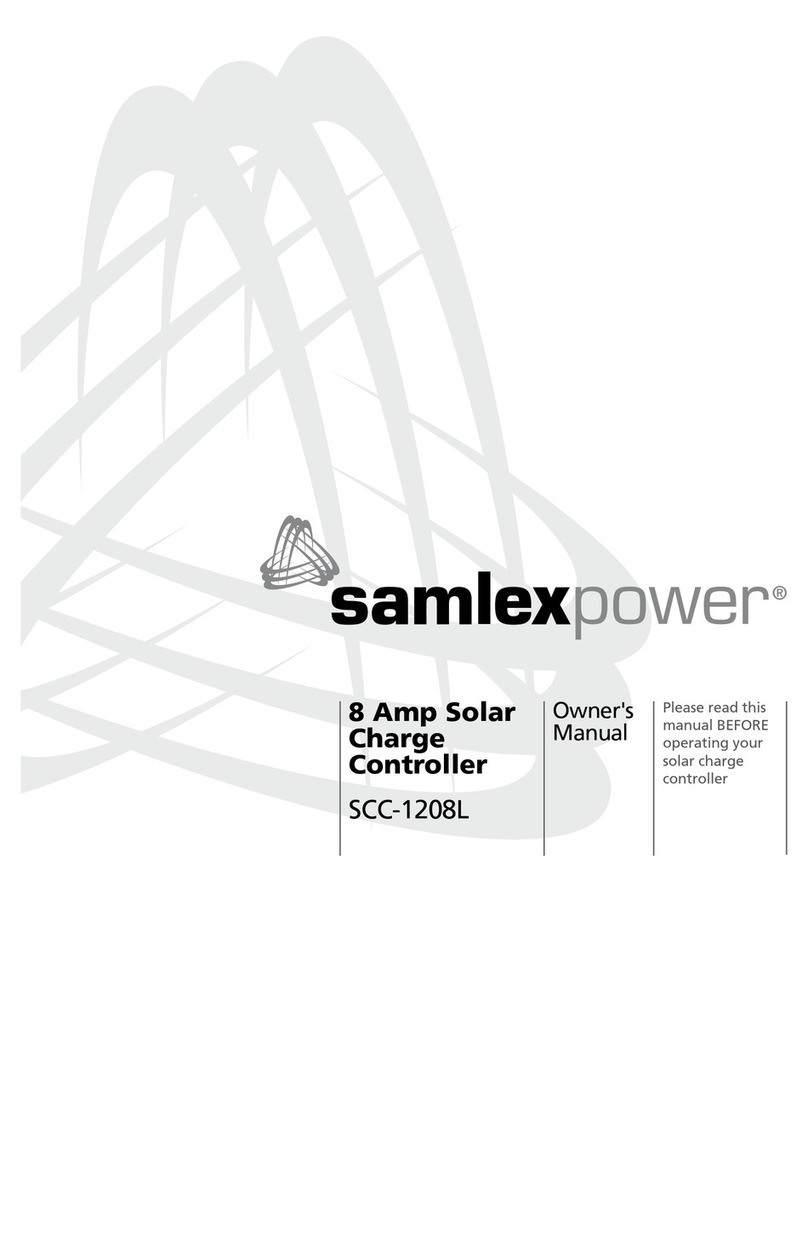
SamplexPower
SamplexPower SCC-1208L owner's manual
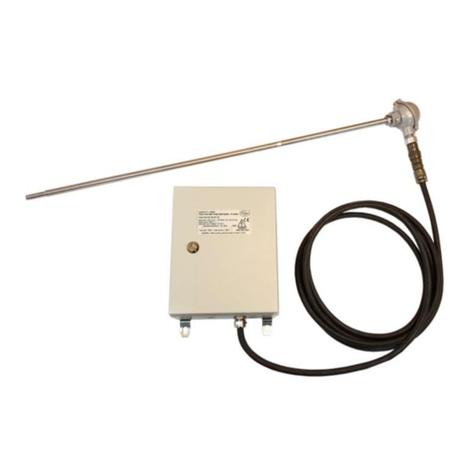
Fireye
Fireye SureFire II instruction manual