LEYBOLD COMBIVAC CM 51 User manual

Catalog No.
230110
230111
Vacuum Gauge Controller
CM 51COMBIVAC CM 51COMBIVAC
Instruction Manual GA130001441_002_C0


GA130001441_002_C0 –09/2016
3
0. Table of Contents
0. Table of Contents 3
0.1 Table of Figures 7
0.2 Table of Tables 7
1. Description 8
1.1 Validity 8
1.1.1 Part Number 8
1.1.2 Nameplate 8
1.2 Conforming Utilisation 8
1.3 Responsibility and Warranty 9
1.4 Shipping Damage 9
2. Safety 10
2.1 General Information 10
2.2 Key to the Symbols 10
2.3 Basic Safety Information 10
3. General Equipment Description 11
3.1 COMBIVAC CM 51 11
3.2 THERMOVAC (Pirani) Method of Measurement 11
3.3 PENNINGVAC (cold cathode) Method of Measurement 11
3.4 Connectable Gauge Heads 11
4. Technical Data 12
4.1 General Data 12
4.1.1 Mechanical Data 12
4.1.2 Standard Parameters (factory defaults) 13
4.1.2.1 Sensor-dependent Parameters 13
4.1.2.2 General Parameters 13
4.1.3 Environment 13
4.1.4 Standards 14
4.2 Mains Connection 14
4.3 Measurement Channels 14
4.3.1TM Measurement Channels 14
4.3.2 PM Measurement Channel 14
4.3.3 Measurement 14
4.4 Switching Functions / Relay Outputs 15
4.4.1 Switching Function Relay 15
4.4.2 Ready Signal Relay 15

4
GA130001441_002_C0 –09/2016
4.5 Outputs and Inputs 15
4.5.1 Analog Output 15
4.5.2 External Control 16
4.5.3 Serial Interfaces 16
4.5.3.1 RS232 16
4.5.3.2 RS485 16
4.5.4 Profibus-DP 16
5. Installation 17
5.1 Supplied Equipment 17
5.2 Mechanical Installation 17
5.2.1 Rack Installation 18
5.2.2 Front Panel Installation 18
5.2.3 Benchtop Instrument 19
5.3 Connections 20
5.3.1 Rear Side of the Instrument 20
5.3.2 Mains Connection 20
5.3.3 Earthing 21
5.3.4 THERMOVAC Measurement Channels (TM 1 and TM 2) 21
5.3.5 PENNINGVAC Measurement Channel (PM) 21
5.3.6 Analog Output and External Control (Analog Output / Extern Control) 22
5.3.7 RS232 / RS485 Interface (Interface RS232 / RS485) 23
5.3.8 Profibus-DP Interface (Interface Profibus-DP) 23
5.3.9 Relay Output (Relay Output) 24
6. Operation 25
6.1 Front Panel 25
6.1.1 Display 25
6.1.2 Control Pushbuttons 26
6.2 Switching on and off 26
6.2.1 Switching on 26
6.2.2 Switching off 26
6.3 Operating Modes 27
6.4 Measurement Mode 27
6.4.1 Selection 27
6.4.2 Description 27
6.4.3 Pushbutton Functions 28
6.4.3.1 Measurement Channel Selection 28
6.4.3.2 Parameter Mode Selection 28
6.4.3.3 Switching the PENNINGVAC on 29
6.4.3.4 Switching the PENNINGVAC off 29
6.4.4 THERMOVAC Alignment 30
6.5 Parameter Mode 31
6.5.1 Selection 31
6.5.2 Parameter Groups 31
6.5.3 Operating Concept 32
7. Parameters 33
7.1 Switching Function Parameters (PArA SP) 33
7.1.1 Basic Terms 33
7.1.2 Configuring the Switching Functions 34
7.1.3 Adjustment Range 34

GA130001441_002_C0 –09/2016
5
7.2 Sensor Parameters (PArA SEn) 35
7.2.1 Filament Material THERMOVAC (FIL) 35
7.2.2 Type of Gas Correction THERMOVAC (GASTM) 35
7.2.3 Type of Gas Correction PENNINGVAC (GASPM) 36
7.2.4 Sensor Switch-on Type (S-on) 36
7.2.5 Sensor Switch-on Value ( t-on) 36
7.2.6 Sensor Switch-off Type (S-oFF) 37
7.2.7 Sensor Switch-off Value (t-off) 37
7.3 General Parameters (PArA GEn) 37
7.3.1 Unit of Measurement (unit) 38
7.3.2 Analog Output (AnALoG) 38
7.3.3 Display Format (diGit) 38
7.3.4 Display Brightness (bri) 38
7.3.5 Profibus (Pb) 39
7.3.6 Baud Rate (bAud) 39
7.3.7 Interface (rS) 39
8. Computer Interface 40
8.1 Basics 40
8.1.1 Connection 40
8.1.2 Nomenclature 40
8.2 Communication 41
8.2.1 Protocol 41
8.2.2 General String Structure 41
8.3 Command Set (Mnemonics) 42
8.3.1 Command Overview 42
8.3.2 RPV (Read Pressure Value) 43
8.3.3 RVN (Read Version Number) 43
8.3.4 RSS (Read Set Point Status) 44
8.3.5 SHV (Set HV on/off) 44
8.3.6 SKL (Set Key Lock on/off) 44
8.3.7 SAC (Save Actual Configuration) 45
8.3.8 RSA (Read Serial Adress) 45
8.3.9 SSA (Set Serial Adress) 45
8.3.10 RGP (Read General Parameter) 45
8.3.11 SGP (Set General Parameter) 46
8.3.12 RGC (Read Gas Correction) 47
8.3.13 SGC (Set Gas Correction) 47
8.3.14 RSC (Read Sensor Control) 47
8.3.15 SSC (Set Sensor Control 48
8.3.16 RSP (Read Set Point) 48
8.3.17 SSP (Set Set Point) 49
9. Maintenance and Service 50
9.1 Maintenance 50
9.1.1 General Maintenance Information 50
9.2 Troubleshooting 50
9.2.1 Fault Indication 50
9.2.2 Error Messages 50
9.2.3 Help the Case of Faults 51
9.2.4 Fuse Replacement 51
9.2.5 Repair 51

GA130001441_002_C0 –09/2016
7
0.1 Table of Figures
Figure 1 –Nameplate (Examble) 8
Figure 2 –COMBIVAC CM 51 dimensions (in mm) 12
Figure 3 –Rack installation 18
Figure 4 –Front panel cutout dimensions (in mm) 18
Figure 5 –Preparing the top side of the instrument for utilisation as a benchtop unit 19
Figure 6 –Preparing the bottom side of the 19
Figure 7 –Rear panel of the instrument 20
Figure 8 –Connection plug for analog output and external control (SUB-D, 15-way) 22
Figure 9 –Interface connection socket (SUB-D, 9-way) 23
Figure 10 –Connection socket for Profibus DP interface (SUB-D, 9-way) 23
Figure 11 –Connection plug for relay output (SUB-D, 25-way) 24
Figure 12 –Front panel 25
Figure 13 –Operating the pushbutton CHANNEL 28
Figure 14 –Operating the pushbutton PARA 28
Figure 15 –Operating the pushbutton UP 29
Figure 16 –Operating the pushbutton DOWN 29
Figure 17 –Full-scale alignment for the THERMOVAC gauge head 30
Figure 18 –Zero alignment for the THERMOVAC gauge head 30
Figure 19 –Behaviour of a switching function in response to pressure changes 34
0.2 Table of Tables
Table 1 –Part Numbers 8
Table 2 –Connectable gauge heads 11
Table 3 –Switching parameters, factory defaults 13
Table 4 –Sensor parameters, factory defaults 13
Table 5 –General parameters, factory defaults 13
Table 6 –Supplied equipment 17
Table 7 –Display components 25
Table 8 –Display in the measurement mode 27
Table 9 –Parameter groups and corresponding parameters 31
Table 10 –Available sensor parameters 35
Table 11 –Values for the parameter FIL 35
Table 12 –Values for the parameter unit 38
Table 13 –Values for the parameter AnALoG 38
Table 14 –Values for the parameter diGit 38
Table 15 –Values for the parameter bri 38
Table 16 –Values for the parameter Pb 39
Table 17 –Values for the parameter bAud 39
Table 18 –Values for the parameter rS 39
Table 19 –Terms Computer Interface 40
Table 20 –Control Characters Computer Interface 40
Table 21 –Mnemonics for read commands 42
Table 22 –Mnemonics for write commands 42
Table 23 –Mnemonics for read and write commands 42
Table 24 –Error messages 50

8
GA130001441_002_C0 –09/2016
1. Description
1.1 Validity
1.1.1 Part Number
This document applies to the following products:
Part Number
Product
Version
Serial
Number
230110
COMBIVAC CM 51
Three-channel measuring instrument for passive vacuum sensors
1.0
et seq.
1000
et seq.
230111
COMBIVAC CM 51
Three-channel measuring instrument for passive vacuum sensors
with Profibus DP
1.0
et seq.
1000
et seq.
Table 1 –Part Numbers
1.1.2 Nameplate
A nameplate is located on the bottom side of the instrument. When communicating with
Leybold Vacuum GmbH, stating the information on the nameplate is necessary. For this
reason please enter the following information:
Figure 1 –Nameplate (Examble)
1.2 Conforming Utilisation
The COMBIVAC CM 51 is a universal vacuum gauge which owing to the combination of two
principles of measurement - Pirani (Thermovac) and Penning (cold cathode) - permits
measurements and checks within the entire vacuum pressure range between1·10-9 mbar
and atmospheric pressure.
One PENNINGVAC sensor and at most two THERMOVAC sensors can be connected.
The built-in RS232/RS485 as well as Profibus-DP interfaces permit computer-controlled
operation as well as the exchange of the measurement data between the COMBIVAC CM
51 and a computer.
Operate all connected sensors in agreement with the information given in the corresponding
Operating Instructions.
NOTICE:
Based on the technical data please check first whether your measuring
instrument is suited to your kind of application.

GA130001441_002_C0 –09/2016
9
1.3 Responsibility and Warranty
The Leybold Vacuum GmbH will not assume any responsibility or warranty in case the
operator or third persons
do not observe the information given in this document.
do not use the product as intended.
modify the product in any way (conversions, repair work etc).
operate the product with accessories not listed in the corresponding product
documentation.
Subject to technical alterations without prior notice. The figures are not binding.
1.4 Shipping Damage
Examine the shipping package as to any external damage.
In case any damage is determined, file a damage report to the forwarding agent and
the insurer.
Retain the packaging material since damages can only be claimed when returning the
instrument in the original packaging of the manufacturer.
Examine the delivery to ensure that it is complete.
Examine the instrument as to any visually apparent damage.
DANGER: Damaged product.
Commissioning or operating a damaged product is dangerous to life.

10
GA130001441_002_C0 –09/2016
2. Safety
2.1 General Information
The COMBIVAC CM 51 is delivered ready for operation. Even so, we recommend that you
carefully read these Operating Instructions so as to ensure optimum operating conditions
right from the start.
This manual contains important information for understanding, installing, commissioning,
operating and troubleshooting the COMBIVAC CM 51.
2.2 Key to the Symbols
Important instructions relating to technical safety and safe operation are emphasised by
symbols.
DANGER or WARNING:
Information designed to prevent any kind of injury to persons.
DANGER:
Information designed to prevent injury to persons and damage to equipment
in connection with electricity.
NOTICE:
General information pointing to further information, respectively reference
sections.
2.3 Basic Safety Information
During all work like installation, maintenance and repair activities, comply with the
pertinent safety regulations.
DANGER: Mains Voltage
Coming into contact with components at mains voltage level within the
instrument can be dangerous to life when inserting objects or allowing liquids
to enter the instrument.
WARNING: Improper usage.
Improper usage can damage the instrument. Use the instrument only in
agreement with the specifications issued by the manufacturer.
WARNING: Wrong Connection and Operating Data.
Wrong connection and operating data can damage the instrument. Comply
with all specified connection and operating data.

GA130001441_002_C0 –09/2016
11
3. General Equipment Description
3.1 COMBIVAC CM 51
This combination instrument offers three measurement channels, two THERMOVAC and
one PENNINGVAC. Thus measurements and checking of vacuum pressures over 12 full
decades from 1·10-9 to atmospheric pressure is possible. Six switching thresholds permit the
integration of the COMBIVAC CM 51 within complex vacuum control facilities. The two
THERMOVAC channels are immediately active upon powering up. The PENNINGVAC
channel may be switched on and off by one of the two THERMOVAC channels or externally
or manually. The operating status of the switching thresholds and the measurement systems
is displayed and signalled correspondingly through the outputs.
3.2 THERMOVAC (Pirani) Method of Measurement
This method of measurement covering the range of 5·10-4 to 1·103mbar utilises the heat
conductance of the gas for the purpose of measuring its pressure. In order to attain a
response time which is as short as possible, all THERMOVAC instruments rely exclusively
the principle of the controlled Pirani where the measurement filament is part of a Wheatstone
Bridge. When the temperature of the filament changes due to pressure changes, then the
bridge is unbalanced. The quickly responding control circuitry adapts the heating power for
the filament so that the filament temperature again reaches its nominal level thereby
balancing the measurement bridge again. The displayed pressure is dependent on the type
of gas. By default the display of the instruments has been calibrated for nitrogen,
respectively air.
3.3 PENNINGVAC (cold cathode) Method of Measurement
For the purpose of measuring the pressure, a high tension is applied to the sensor thereby
igniting a gas discharge. The thus produced ion current is output by way of a signal which
is proportional to the pressure. This sensor arrangement allows assured and reliable
measurement operation of the cold cathode in the range from 1·10-9 mbar to 1·10-2 mbar.
Two each versions with KF and CF flange are available.
3.4 Connectable Gauge Heads
The following gauge heads can be operated by the COMBIVAC CM 51:
Gauge heads
Type
THERMOVAC
TR 211, TR 212, TR 216
PENNINGVAC
PR 25, PR 26, PR 27, PR 28
Table 2 –Connectable gauge heads

12
GA130001441_002_C0 –09/2016
4. Technical Data
4.1 General Data
4.1.1 Mechanical Data
Dimensions: Breite: 106.4 mm (1/4 19“)
Höhe: 128.4 mm (3 HE)
Tiefe: 174.5 mm
Wight: ≤1.4 kg
Installation depth: ≤230 mm approx. (including connected plugs)
Usage: Rack installation
Front panel installation
Benchtop instrument
Figure 2 –COMBIVAC CM 51 dimensions (in mm)

GA130001441_002_C0 –09/2016
13
4.1.2 Standard Parameters (factory defaults)
4.1.2.1 Sensor-dependent Parameters
Parameter
Parameter description
THERMOVAC
setting
PENNINGVAC
setting
Switching thresold 1 –lower threshold
.
.
Switching thresold 1 –upper threshold
.
.
Switching thresold 2 –lower threshold
.
.
Switching thresold 2 –upper threshold
.
.
Table 3 –Switching parameters, factory defaults
Parameter
Parameter description
THERMOVAC
setting
PENNINGVAC
setting
THERMOVAC filament material
(tungsten)
-
THERMOVAC gas type correction characteristic
(nitrogen)
-
PENNINGVAC gas type correction factor
-
.
Switch-on type for sensor
-
Switch-off type for sensor
-
Table 4 –Sensor parameters, factory defaults
4.1.2.2 General Parameters
Parameter
Parameter description
Setting
Displayed unit of measurement
Analog output
(CM 51)
Number of displayed digits
Display brightness
Profibus address
Baud rate
.
Serial interface
Table 5 –General parameters, factory defaults
4.1.3 Environment
Temperature: Storage: -20 –+60 °C
Operating: +5 –+50 °C (sea level)
+5 –+30 °C (2000 m above sea level)
Relative atmospheric humidity: 80 % max. (up to 30 °C)
decreasing to 50 % max. (over 40 °C)
Use: indoors (altitude 2000 m max. above sea level)
Ingress protection type: IP40

14
GA130001441_002_C0 –09/2016
4.1.4 Standards
Conformity with respect to Low Voltage Directive 2014/35/EU
Conformity with respect to EMC Directive 2014/30/EU
Conformity with respect to RoHS Directive 2011/65/EU
International/national standards as well as specifications:
DIN EN 61010-1 (2011)
(Safety requirements for electrical equipment for measurement, control and
laboratory use).
DIN EN 61326-1 (2013)
(Electrical equipment for measurement, control and laboratory use –EMC
requirements. Industrial interference immunity; electromagnetic emissions household
sector Class B).
4.2 Mains Connection
Voltage: 100 –240 VAC
Frequency: 50/60 Hz
Fuses: 2 x T1.6A H
Power consumption: < 10 W
Current consumption: 0.2 –0.1 A approx.
Overvoltage category: II
Protection category: 1
Connection: Cold-device plug IEC 320 C14
4.3 Measurement Channels
Number: Two THERMOVAC measurement channels
One PENNINGVAC measurement channels
Connection: 6-way DIN socket for THERMOVAC
1-way HV socket (shielded) for PENNINGVAC
4.3.1 TM Measurement Channels
Measurement range: 5·10-4 –1000 mbar
Measurement inaccuracy: ± 20 % of measured value (10-3 –10-2 mbar)
± 15 % of measured value (10-2 –102mbar)
Cable length: up to 100 m
Cable length alignment: automatic
4.3.2 PM Measurement Channel
Measurement range: 1·10-9 –1·10-2 mbar
Measurement inaccuracy: ± 30 % of measured value (10-8 –10-4 mbar)
Cable length: up to 100 m for the pressure range 1·10-8 –1·10-2 mbar
4.3.3 Measurement
Display rate: 4 s-1
Unit of measurement: mbar, Pa, Torr

GA130001441_002_C0 –09/2016
15
4.4 Switching Functions / Relay Outputs
4.4.1 Switching Function Relay
Number: 6
Assignment: 2 per channel
Response time: < 50 ms
Adjustment range: PENNINGVAC 1·10-8 –1·10-2 mbar
THERMOVAC 5·10-3 –5·102mbar
Hysteresis: adjustable > 10 % of measured value
Contact type: changeover contact, floating
Load (resistive): switched current: 1 A max.
switched voltage: max. 30 VAC/30 VDC
Service life: mechanical: 5·106switching cycles
Electrical: 105switching cycles at maximum load
Connection: SUB-D, 25-way, plug
4.4.2 Ready Signal Relay
Number : 3
Assignment: 1 per channel
Response time: < 50 ms
Contact type: normally open contact, floating
Load (resistive): switched current: 1 A max.
switched voltage: max. 30 VAC/30 VDC
Service life: mechanical: 5·106switching cycles
Electrical: 105switching cycles at maximum load
Connection: SUB-D, 25-way, plug
4.5 Outputs and Inputs
4.5.1 Analog Output
Number: 1 per measurement channel
Voltage range: 0 –10 VDC (limit values 0 –10.5 VDC)
Output voltage for fault: 10.2 –10.5 VDC
Deviation of display value: ± 0.2 %
Internal resistance: 100 Ohm
Characteristic: logarithmic
Measurement
Channel
(CM31)
(CM 51)
PENNINGVAC
1.43 VDC/Dekade (0 V ≙1·10-9 mbar)
p = 10-9 mbar · 10(U[V]/1.43V)
p = 10-7 Pa · 10(U[V]/1.43V)
p = 0.75·10-9 Torr · 10(U[V]/1.43V)
1.333 VDC/Dekade (0.667 V ≙1·10-9 mbar)
p = 10-9 mbar · 10((U[V]-0.677V)/1.333V)
p = 10-7 Pa · 10((U[V]-0.677V)/1.333V)
p = 0.75·10-9 Torr · 10((U[V]-0.677V)/1.333V)
THERMOVAC
1.67 VDC/Dekade (0 V ≙ 1·10-3 mbar)
p = 10-3 mbar · 10(U[V]/1.67V)
p = 10-1 Pa · 10(U[V]/1.67V)
p = 0.75·10-3 Torr · 10(U[V]/1.67V)
1.286 VDC/Dekade (1.9 V ≙ 5·10-4 mbar)
p = 5·10-4 mbar · 10((U[V]-1.9V)/1.286V)
p = 5·10-2 Pa · 10((U[V]-1.9V)/1.286V)
p = 3.75·10-4 Torr · 10((U[V]-1.9V)/1.286V)
Response time: 100 ms approx.
Resolution: 10 Bit
Connection: SUB-D, 15-way, plug (jointly used together with the
connection for external control)

16
GA130001441_002_C0 –09/2016
4.5.2 External Control
PLC compatible logic level: (Low) < 7 VDC; 0 A
(High) > 13 VDC; 7 mA (at 24 VDC)
Contact via relay: 24 VDC approx., is provided by the instrument via
a self-resetting fuse (100 mA)
Connection: SUB-D, 15-way, plug (jointly used with the analog output
connection)
4.5.3 Serial Interfaces
4.5.3.1 RS232
Standard: RS232
Parameters: 8 data bits, 1 stop bit, no parity, no protocol
Signals: RXD and TXD
Baud rate: 9600, 19200, 38400 baud
Connection: SUB-D, 9-way, socket (jointly used with RS485)
4.5.3.2 RS485
Standard: RS485 (half-duplex)
Parameters: 8 data bits, 1 stop bit, no parity, no protocol
Signals: A and B
Baud rate: 9600, 19200, 38400 baud
Connection: SUB-D, 9-way, socket (jointly used with RS232)
4.5.4 Profibus-DP
Standard: Profibus-DP
Connection: SUB-D, 9-way, socket

GA130001441_002_C0 –09/2016
17
5. Installation
5.1 Supplied Equipment
Designation
Quantity
COMBIVAC CM 51
1
Mains cord with shockproof plug (EU)
1
Mains cord with shockproof plug (US)
1
Operating Instructions (each GER and ENG)
1
Spare fuses
2
Neck collar screws
4
Plastic sleeves
4
Edge protection
2
Adhesive feet
2
Table 6 –Supplied equipment
5.2 Mechanical Installation
The COMBIVAC CM 51 gauge can be used as follows:
Rack installation
Front panel installation
Benchtop instrument
WARNING: Powering down
Install the instrument or place it so that you are in a position to operate the
mains power switch at any time or ensure that the instrument can be
deenergised at any time.

18
GA130001441_002_C0 –09/2016
5.2.1 Rack Installation
The COMBIVAC CM 51 has been designed for installation within a sub-rack (19", 3 U) in
accordance with DIN EN 60297 (IEC 60297) ( Figure 3, page 18). For this purpose the
supplied equipment includes four neck collar screws and four plastic sleeves.
Figure 3 –Rack installation
Attach the sub-rack within the rack.
Push the COMBIVAC CM 51 into the sub-rack.
Affix the instrument to the sub-rack with the neck collar screws and the plastic sleeves
included in the delivery.
5.2.2 Front Panel Installation
For panel mounting of the instrument, the following cutout ( Figure 4, Page 18) is
required:
Figure 4 –Front panel cutout dimensions (in mm)
Guide the COMBIVAC CM 51 into the cut-out.
Affix the instrument with the neck collar screws and the plastic sleeves included in the
delivery.

GA130001441_002_C0 –09/2016
19
5.2.3 Benchtop Instrument
When intending to use the COMBIVAC CM 51 as a benchtop instrument, then proceed as
follows:
Push one of the two edge protection rubber pieces included in the delivery over the top
edge of the front panel ( Figure 5, page 19)
Place the COMBIVAC CM 51 on its back ( Figure 6, page 19)
Push the second edge protection rubber piece included in the delivery onto the bottom
edge of the front panel
WARNING: Risk of suffering injury.
When using the COMBIVAC CM 51 as a benchtop instrument fit the two edge
protection rubber pieces onto the top and bottom edge of the front panel so
as to avoid injury by sharp edges.
Stick the two rubber feet included in the delivery onto the bottom of the housing.
Figure 5 –Preparing the top side of the instrument
for utilisation as a benchtop unit
Figure 6 –Preparing the bottom side of the
instrument for utilisation as a benchtop
unit
Turn the COMBIVAC CM 51 over again and move it to the desired place.

20
GA130001441_002_C0 –09/2016
5.3 Connections
5.3.1 Rear Side of the Instrument
The Figure 7, page 20 shows the rear panel of the COMBIVAC CM 51. The way in which
the individual connections have been wired is described in the following sections.
Figure 7 –Rear panel of the instrument
A Mains connection with mains switch and fuses
B Ground connection and shield of the TM
measurement cables
C Connection for the PENNINGVAC gauge head
(PM)
D Connections for the THERMOVAC gauge
heads (TM1, TM2)
E Connection for the RS232 or RS485 interface
F Connection for the Profibus-DP interface with
error indicator (red LED)
G Connection for analog output and external
control
H Connection for relay output
5.3.2 Mains Connection
The mains connection on the rear panel ( Figure 7, A, page 20)is intended only for a
mains cord which on the instrument side is provided with a inlet connector for non-heating
apparatus.
NOTICE: Mains cord
Included in the delivery of the instrument is a mains cord. If the plug on the
mains power side is not compatible with your mains power outlets, you will
need a mains cord which meets the following specifications:
Three-wire cable with protective earthing.
Conductor cross-section: 3 x 0.75 mm² or greater.
Cable length 2.5 m maximum.
DANGER: Mains voltage
Appliances, which have not been professionally connected to Earth, can be
life-threatening in the event of a malfunction. For this reason use three-wire
mains cords, respectively extension cords with protective earthing only. Insert
the mains plug into a mains power socket, which provides an Earth contact.
Insert the plug of the mains cord into the mains socket provided on the instrument.
Insert the mains plug of the mains cord into the mains outlet.
This manual suits for next models
3
Table of contents
Other LEYBOLD Controllers manuals
Popular Controllers manuals by other brands
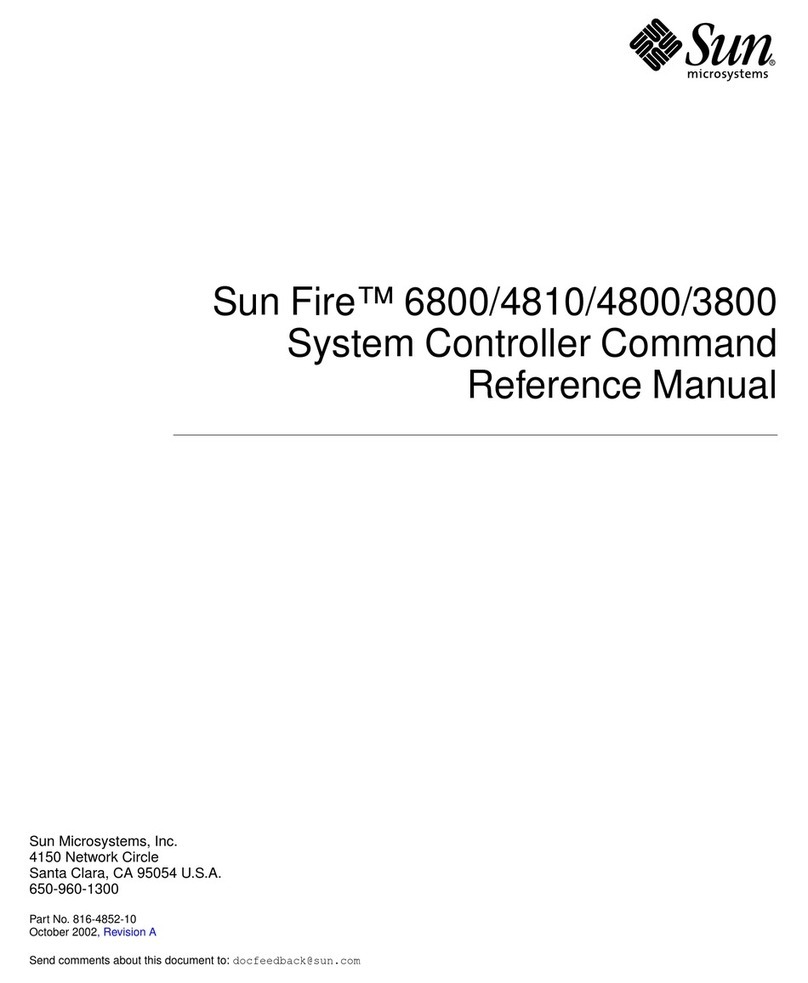
Sun Microsystems
Sun Microsystems Fire 6800 Reference manual
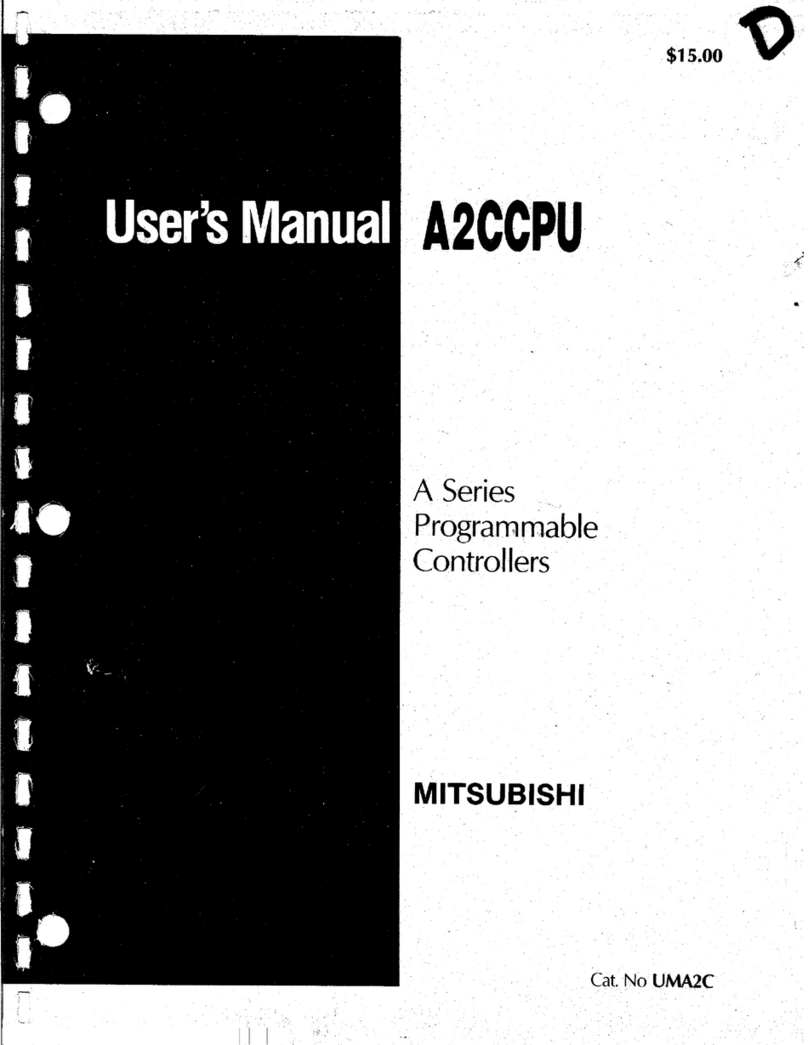
Mitsubishi
Mitsubishi A2CCPU user manual
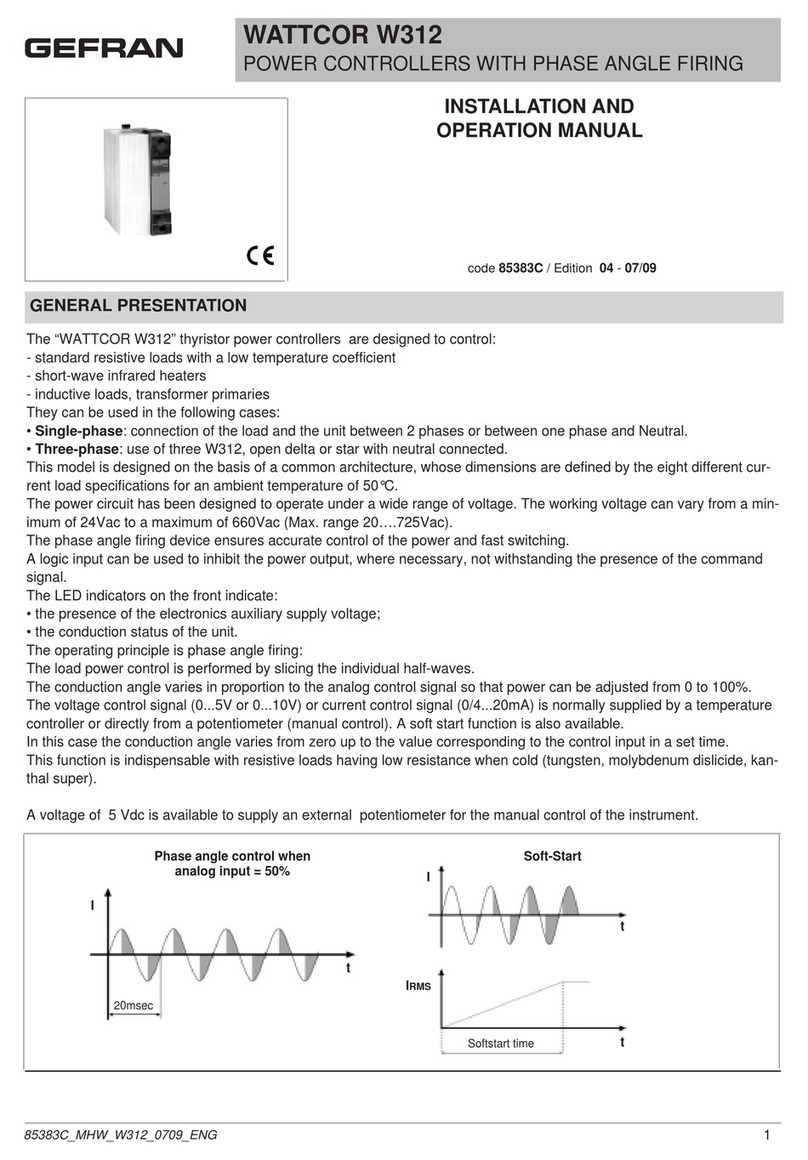
gefran
gefran WATTCOR W312 Installation and operation manual
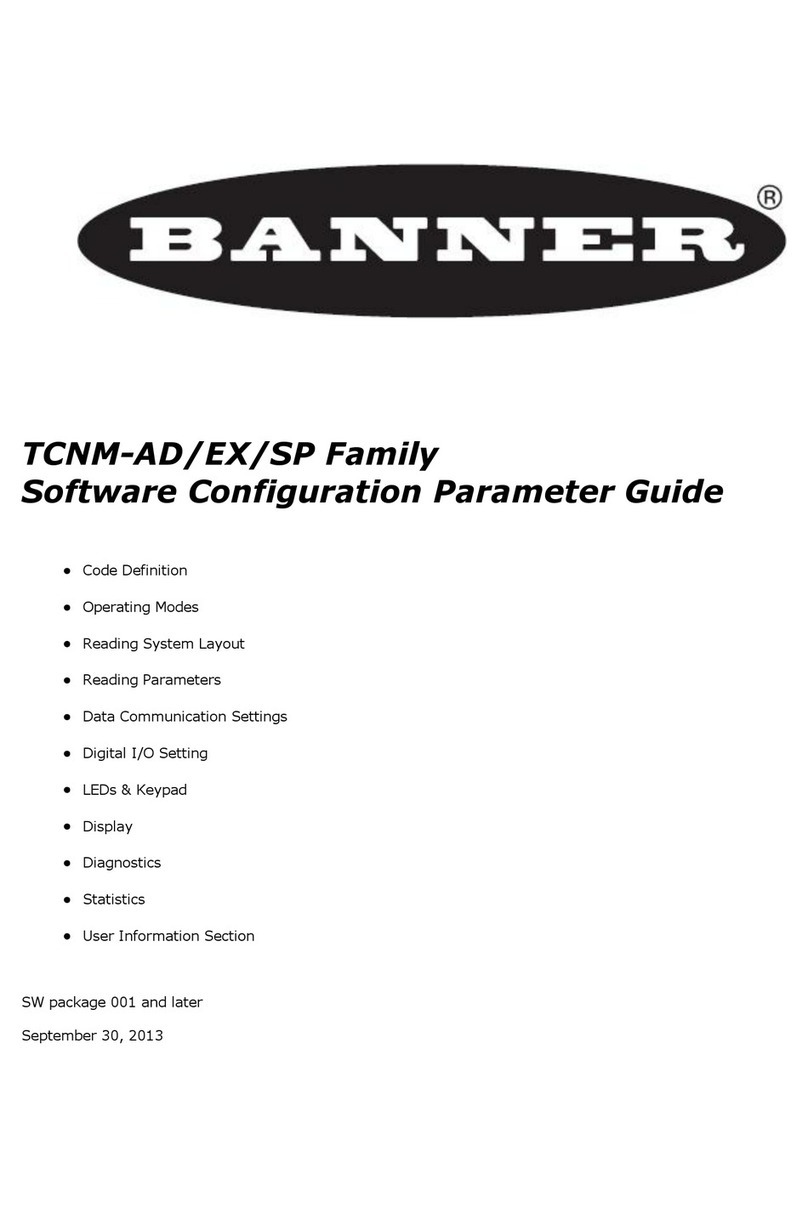
Banner
Banner TCNM-AD Series Parameter guide

Hamworthy
Hamworthy Merley Installation, commissioning and operating instructions

Viking
Viking C-1000B Technical practice