Lutz-Jesco C 7523 User manual

Dosing
Conveying
Control
Liquids
Gases
Systems
Original operating instructions
© Lutz-Jesco GmbH 2018
BA-24721-02-V02
Chlorine gas changeover unit
C 7523
Operating instructions
Read the operating manual!
The user is responsible for installation and operation related mistakes!


Table of Contents 3
© Lutz-Jesco GmbH 2018
Subject to technical changes
180321
BA-24721-02-V02
Chlorine gas changeover unit C 7523 Operating instructions
Table of Contents
1 Notes for the Reader ..........................................................4
1.1 General non-discrimination......................................................4
1.2 Explanation of the signal words ................................................4
1.3 Explanation of the warning signs ..............................................4
1.4 Identification of warnings.........................................................4
1.5 Instruction for action identification ...........................................4
2 Safety .................................................................................5
2.1 General warnings.....................................................................5
2.2 Information about chlorine .......................................................5
2.3 Hazards due to non-compliance with the safety instructions .....5
2.4 Working in a safety-conscious manner .....................................6
2.5 Personal protective equipment.................................................6
2.6 Personnel qualification.............................................................6
2.7 Personnel tasks .......................................................................6
3 Intended use ......................................................................7
3.1 Notes on product warranty .......................................................7
3.2 Intended purpose.....................................................................7
3.3 Prohibited dosing media...........................................................7
4 Product description ...........................................................8
4.1 Scope of delivery .....................................................................8
4.2 Design and function .................................................................8
4.3 Rating plate .............................................................................8
5 Technical data.................................................................... 9
6 Dimensions ......................................................................10
7 Installation .......................................................................11
7.1 Installation location................................................................11
7.2 Installing the device ...............................................................11
7.3 Hydraulic installations............................................................11
7.4 Electrical installation..............................................................12
7.5 Installation examples .............................................................14
7.6 Installation with bypass..........................................................14
7.7 Installation with a vacuum manifold........................................15
7.8 Installation with a positive pressure manifold..........................16
7.9 Completing the installation.....................................................16
8 Commissioning ................................................................17
8.1 Checking the vacuum system.................................................17
8.2 Turning on the device .............................................................17
8.3 Adjusting the switch point ......................................................17
9 Operation..........................................................................18
9.1 Controls.................................................................................18
9.2 Operating modes ...................................................................18
9.3 Disposal ................................................................................19
10 Shutdown.........................................................................20
10.1 Short-term shutdown...........................................................20
10.2 Long-term shutdown ...........................................................20
11 Maintenance ....................................................................21
11.1 Maintenance intervals..........................................................21
11.2 Maintenance accessories.....................................................21
11.3 Preparing the system for maintenance .................................21
11.4 Minor maintenance..............................................................21
11.5 Cleaning the contact gauge..................................................22
11.6 Maintenance on the ball valve ..............................................22
11.7 Functional control ................................................................23
11.8 Finishing maintenance.........................................................23
12 Troubleshooting ...............................................................24
13 Spare parts.......................................................................26
13.1 Spare parts..........................................................................26
13.2 Maintenance sets ................................................................27
14 EU Declaration of Conformity...........................................28
15 Declaration of no objection..............................................29
16 Warranty claim.................................................................30

Notes for the Reader
Instruction for action identification
4© Lutz-Jesco GmbH 2018
BA-24721-02-V02
Chlorine gas changeover unit C 7523 Operating instructions
1 Notes for the Reader
This operating manual contains information and behaviour rules for the
safe and designated operation of the device.
Observe the following principles:
nRead the entire operating manual prior to starting-up the device.
nEnsure that everyone who works with or on the device has read the
operating manual and follows it.
nMaintain the operating manual throughout the service life of the
device.
nPass the operating manual on to any subsequent owner of the device.
1.1 General non-discrimination
In this operating manual, only the male gender is used where grammar
allows gender allocation. The purpose of this is to make the text easy to
read. Men and women are always referred to equally. We would like to
ask female readers for understanding of this text simplification.
1.2 Explanation of the signal words
Different signal words in combination with warning signs are used in this
operating manual. Signal words illustrate the gravity of possible injuries if
the risk is ignored:
Signal word Meaning
DANGER Refers to imminent danger. Ignoring this sign may
lead to death or the most serious injuries.
WARNING
Refers to a potentially hazardous situation.
Failure to follow this instruction may lead to death
or severe injuries.
CAUTION
Refers to a potentially hazardous situation.
Failure to follow this instruction may lead to
minor injury or damage to property.
NOTE Refers to a danger which, if ignored, may lead to
risk to the machine and its function.
Table 1: Explanation of the signal words
1.3 Explanation of the warning signs
Warning signs represent the type and source of a danger:
Warning sign Type of danger
General danger
Danger from poisonous substances
Danger from electrical voltage
Danger of damage to machine or functional
influences
Table 2: Explanation of the warning signs
1.4 Identification of warnings
Warnings are intended to help you recognise risks and avoid negative
consequences.
This is how warnings are identified:
Warning sign SIGNAL WORD
Description of danger.
Consequences if ignored.
ðThe arrow signals a safety precaution to be taken to eliminate the
danger.
1.5 Instruction for action identification
This is how pre-conditions for action are identified:
üPre-condition for action which must be met before taking action.
@A resource such as a tool or auxiliary materials required to perform
the operating instructions.
This is how instructions for action are identified:
èSeparate step with no follow-up action.
1. First step in a series of steps.
2. Second step in a series of steps.
4Result of the above action.
üAction completed, aim achieved.

Safety
Hazards due to non-compliance with the safety instructions 5
© Lutz-Jesco GmbH 2018
Subject to technical changes
180321
BA-24721-02-V02
Chlorine gas changeover unit C 7523 Operating instructions
2 Safety
2.1 General warnings
The following warnings are intended to help you eliminate the dangers
that can arise while handling the device. Risk prevention measures al-
ways apply regardless of any specific action.
Safety instructions warning against risks arising from specific activities
or situations can be found in the respective sub-chapters.
DANGER
Danger to life from chlorine poisoning!
Chlorine is poisonous. In severe cases, breathing in chlorine may lead
to death. It irritates the eyes, the respiratory system and the skin.
ðUse sufficient personal protective equipment.
ðUse a respirator mask with gas filter type B that complies with EN
14387 during any work on the system.
ðAlways comply with the accident prevention regulations that apply
at the place of use.
ðGet rid of leaks without delay. You must get rid of even very minor
leaks without delay. Together with the humidity, chlorine forms
hydrochloric acid and corrosion results in rapidly increasing
leakage.
ðUse only chlorine-resistant seals.
ðOnly use seals once. Reusing them leads to leaks.
DANGER
Danger to life from missing safety device!
Chlorinators without gas warning devices are an increased safety risk,
since it is not possible to detect escaping chlorine gas in good time or
at all.
ðInstall a gas warning device.
WARNING
Increased risk of accidents due to insufficient qualifica-
tion of personnel!
Chlorinators and their accessories must only be installed, operated and
maintained by personnel with sufficient qualifications. Insufficient qual-
ification will increase the risk of accidents.
ðEnsure that all action is taken only by personnel with sufficient and
corresponding qualifications.
ðPrevent access to the system for unauthorised persons.
NOTE
Damage to the plant due to the formation of hydrochloric
acid
Chlorine gas is highly hygroscopic.This means that humidity enters the
system at any open connection on devices or pipes, which results in the
formation of hydrochloric acid and contamination. thus inevitably caus-
ing damage to the units.
ðKeep all connections (including in the vacuum system and on all
devices not currently in use) closed at all times.
2.2 Information about chlorine
Chlorine is a hazardous substance. The chemical element chlorine is a
greenish-yellow, toxic gas with a pungent odour, which can be detected
in the air at concentrations below 1 ppm (= 1 ml/m³).
Chlorine is 2.5 times heavier than air and accumulates at ground level.
Chlorine is extremely toxic for water organisms. The reason for the toxici-
ty of chlorine is its extraordinary reactivity. It reacts with animal and veg-
etable tissue and thus destroys it.
Air with a chlorine gas content of 0.5 -1% leads to a quick death in mam-
mals and humans, as it attacks the respiratory tract and the pulmonary
alveolus (formation of hydrogen chloride or hydrochloride acid).
NOTE
Faults due to insufficient chlorine quality
Impurities in the chlorine gas form deposits in devices and valves and
can attack the components chemically. This can lead to malfunctions.
ðOnly use technically pure chlorine that meets the following
requirements:
- Mass content of chlorine at least 99.5%
- Water content max. 20 mg/kg
Chlorine that complies with EN 937 meets these requirements.
2.3 Hazards due to non-compliance with the safety
instructions
Failure to follow the safety instructions may endanger not only persons,
but also the environment and the device.
The specific consequences can be:
nfailure of important functions of the device and of the corresponding
system,
nfailure of required maintenance and repair methods,
ndanger to persons,
ndanger to the environment caused by substances leaking from the
system.

Safety
Personnel tasks
6© Lutz-Jesco GmbH 2018
BA-24721-02-V02
Chlorine gas changeover unit C 7523 Operating instructions
2.4 Working in a safety-conscious manner
Besides the safety instructions specified in this operating manual, further
safety rules apply and must be followed:
naccident prevention regulations,
nsafety and operating provisions,
nsafety regulations on handling hazardous substances,
nenvironmental protection provisions,
napplicable standards and legislation.
2.5 Personal protective equipment
Based on the degree of risk posed by the dosing medium and the type of
work you are carrying out, you must use corresponding protective equip-
ment. Read the Accident Prevention Regulations and the Safety Data
Sheets to the dosing media find out what protective equipment you need.
You will require the minimum of the following personal protective equip-
ment:
Personal protective equipment required
Respirator mask
Protective clothing
Safety shoes
Protective gloves
Table 3: Personal protective equipment required
Wear the following personal protective equipment when performing the
following tasks:
nCommissioning,
nAll work on gas-bearing sections of the plant,
nChanging the chlorine tank,
nShut-down,
nMaintenance work,
nDisposal.
2.6 Personnel qualification
Any personnel who work on the device must have appropriate special
knowledge and skills.
Anybody who works on the device must meet the conditions below:
nattendance at all the training courses offered by the owner,
nsufficient qualification for the respective activity,
ntraining in how to handle the device,
nknowledge of safety equipment and the way this equipment functions,
nfamiliar with this operating manual,
nknowledge of fundamental regulations regarding health and safety
and accident prevention.
All persons must generally have the following minimum qualification:
ntraining as specialists to carry out work on the device unsupervised,
nsufficient training that they can work on the device under the
supervision and guidance of a trained specialist.
These operating instructions differentiate between these user groups:
2.6.1 Specialist staff
Thanks to their professional training, knowledge, experience and knowl-
edge of the relevant specifications, specialist staff are able to perform the
job allocated to them and recognise and/or eliminate any possible dan-
gers by themselves.
2.6.2 Trained persons
Trained persons have received training from the operator about the tasks
they are to perform and about the dangers stemming from improper be-
haviour.
Trained persons have attended all trainings offered by the operator.
2.7 Personnel tasks
In the table below, you can check what personnel qualifications are re-
quired for the respective tasks. Only people with appropriate qualifica-
tions are allowed to perform these tasks!
Qualification Activities
Specialist staff nTransportation
nAssembly
nHydraulic installations
nCommissioning
nTaking out of operation
nFault rectification
nMaintenance
nRepairs
nDisposal
Trained persons nStorage
nControl
Table 4: Personnel qualification

Intended use
Prohibited dosing media 7
© Lutz-Jesco GmbH 2018
Subject to technical changes
180321
BA-24721-02-V02
Chlorine gas changeover unit C 7523 Operating instructions
3 Intended use
3.1 Notes on product warranty
Any non-designated use of the device can impair its function and the pro-
tection provided. This leads to invalidation of any warranty claims!
Please note that liability is on the side of the user in the following cases:
nThe device is operated in a manner which is not consistent with these
operating instructions, particularly safety instructions, handling
instructions and the section "Intended Use".
nInformation on usage and environment (see section 5 “Technical
data” on page9) is not adhered to.
nIf people operate the device who are not adequately qualified to carry
out their respective activities.
nNo original spare parts or accessories of Lutz-Jesco GmbH are used.
nUnauthorised changes are made to the device.
nMaintenance and inspection intervals are not adhered to as required
or not adhered to at all.
nThe device is commissioned before it or the corresponding system
has been correctly and completely installed.
nSafety equipment has been bridged, removed or made inoperative in
any other way.
3.2 Intended purpose
Changeover unit C 7523 is intended exclusively for chlorinators using the
vacuum process. It serves to switch between two vacuum supply batter-
ies.
3.3 Prohibited dosing media
The device must not be used for the following media and substances:
nall media apart from gaseous chlorine
nnot technically pure chlorine with a mass content of less than 99.5%

Product description
Rating plate
8© Lutz-Jesco GmbH 2018
BA-24721-02-V02
Chlorine gas changeover unit C 7523 Operating instructions
4 Product description
4.1 Scope of delivery
Please compare the delivery note with the scope of delivery. The follow-
ing items are part of the scope of delivery:
nMotor ball valve
nContact gauge
nVarious hydraulic connections (optional)
nWall holder
nControl with power plug
nPlastic wall panel (optional)
nInstallation material for wall fixing
nOperating instructions
4.2 Design and function
Chlorine gas dosing systems in a water treatment system must be per-
manently ready for operation so that the water can be sufficiently disin-
fected at any point. This explains the fitting of the systems with two sup-
ply batteries - one side in operation, the other on stand-by. The vacuum
chlorine changeover valve effects automatic switching between the two
cylinders or drum batteries.
Fig. 1: Structure of the device
If the power supply from the operation battery ebbs, the vacuum generat-
ed by the injector will become stronger. The control (1) detects lack of
chlorine through the contact vacuum gauge (2) and actuates the motor
(3) on the 3-way ball valve (4).
The control signals the operating state with coloured LEDs in the flow
chart. The most important operating signals are available for remote indi-
cation as relay contacts.
The "residue discharge" function enables the consumption of residue
from incompletely-emptied tanks of a total vacuum battery. Working in
set intervals, the changeover unit then switches to the battery registered
as empty and removes the residue.
Manual changeover can be triggered by the push of a button. If there is a
power failure, the changeover can be made mechanically by hand.
4.3 Rating plate
There is information on the equipment about safety or the product's way
of functioning. The information must stay legible for the duration of the
service life of the product.
Material: PVC/FPM
230 V, 50/60 Hz, IP65
max. 4 kg/h
XX/XXXX
S/N: XXXXXXXXXX
P/N:
Made in
Germany
*102A12345678*
*12345678012345*
C 7523-
Lutz-Jesco GmbH 30900 Wedemark
Am Bostelberge 19 Germany
Fig. 2: Rating plate
No. Description
1Product name
2 Material
3Voltage supply
4Max. flow rate
5Label showing conformity with applicable European directives
6WEEE label
7Serial number
8Part number
9Month / year of manufacture
Table 5: Rating plate
3
2
1
4
1
2
3
5
9
4
6
8
7

Technical data 9
© Lutz-Jesco GmbH 2018
Subject to technical changes
180321
BA-24721-02-V02
Chlorine gas changeover unit C 7523 Operating instructions
5 Technical data
Description Value
Throughput up to 80 kg/h Cl2
Operating pressure -1…0 bar
Contact gauge Ø63 mm, -1…0 bar
Setting range of the switching point on the contact gauge -0.9…-0.1 bar
Changeover time approx. 22 s
Material in contact with the media PVC / FPM / Silver / coated brass
Further materials Coated steel, PP, ABS
Voltage supply 115/230 V, 50/60 Hz
Power consumption Normal mode max. 0.3 A
Switch-on current max. 17.5 A (peak)
Load capacity of the relay max. 3 A / 250 V AC
Weight Without mounting plate approx. 5 kg
With mounting plate approx. 7 kg
Protection class IP 65
Ambient temperature 0 – 55 °C, avoid direct sunlight
Air humidity max. 95%, non condensing
Table 6: Technical data
Product Hydraulic connections Max. flow rate
C7523-4K Hose 8/12 mm 4 kg/h Cl2
C7523-10K Hose 12/16 mm 10 kg/h Cl2
C7523-40K Pipe DN25/Ø32 40 kg/h Cl2
C7523-80K Pipe DN32/Ø40 80 kg/h Cl2
Table 7: Maximum flow

Dimensions
10 © Lutz-Jesco GmbH 2018
BA-24721-02-V02
Chlorine gas changeover unit C 7523 Operating instructions
6 Dimensions
All dimensions in millimetres (mm).
Fig. 3: Dimensioned drawing C 7523 on mounting plate
Fig. 4: Dimensioned drawing C 7523 as assembly kit
490
200
152.5
440
Ø 9
10
74
~150
152.5
440
490
273
152.5
125
130
85
130
64
~140
125 231
Ø6.5
Patch cable,
Length 2 m

Installation
Hydraulic installations 11
© Lutz-Jesco GmbH 2018
Subject to technical changes
180321
BA-24721-02-V02
Chlorine gas changeover unit C 7523 Operating instructions
7 Installation
NOTE
Damage to the system due to incorrect installation
The failure to observe installation instructions (e.g. use of unsuitable
tools, incorrect torque) can damage the system parts.
ðUse suitable tools.
ðNote the specified torque.
7.1 Installation location
The changeover unit is fitted in the room of the chlorine supply.
The room must fulfil the following requirements:
nsecured against access by unauthorised persons,
nprotected against weather conditions,
nfrost-free,
npermitted ambient temperature maintained (see Section 5 "Technical
data" on page 9),
nroom of sufficient size to allow trouble-free assembly as well as
inspection and maintenance of the device at all times,
nan electrical connection is given,
nthe room must comply with the locally valid prescriptions.
7.2 Installing the device
Install the device on a vertical even wall. The control should be mounted
at approx. eye-level.
Fig. 5: Attaching the wall plate
Precondition for action:
üA flat wall.
üThe mounting material is suitable for the wall.
Resources required:
@Water level
@Drill
@2 open-end spanners SW13
Perform the following working steps:
1. Hold the device against the wall and align it horizontally. The mount-
ing position is shown in section 7.5 “Installation examples” on
page14.
2. Mark the mounting point on the wall.
3. Drill in the marked holes and insert the rawlplug.
4. Screw in the stair bolts (1) a into the rawlplug until the wooden
thread seals with the wall surface.
5. Place a nut (2) and washer (3) on every screw.
6. Push the wall plate (4) onto the hanger bolts.
7. Place a washer (5) and a cap nut (6) on every screw.
8. Adjust the nuts (2 + 6) so that the wall plate is held evenly and with-
out tension.
9. Tighten the nuts.
üThe device is fitted on the wall.
7.3 Hydraulic installations
PVC-U pipes or PE hoses are used as conduits. If the line is to supply mul-
tiple consumers, the line should be calculated for the total of the con-
sumption volume.
The following nominal widths are recommended for the vacuum line
(pressure loss max. 25 bar, calculated at 0.9 bar (a) with 4x90° angles):
Chlorine
Line between the vacuum regulator and dosing
device
5 m 10 m 20 m 30 m 50 m 100 m
1 kg/hr DN 8 DN 8 DN 8 DN 8 DN 8 DN 12
2 kg/hr DN 8 DN 8 DN 8 DN 12 DN 12 DN 12
4 kg/hr DN 8 DN 12 DN 12 DN 12 DN 12 DN 15
10 kg/hr DN 12 DN 12 DN 15 DN 15 DN 20 DN 20
15 kg/hr DN 12 DN 15 DN 20 DN 20 DN 20 DN 25
25 kg/hr DN15 DN 20 DN 20 DN 25 DN 25 DN 32
40 kg/hr DN 20 DN 25 DN 25 DN 25 DN 32 DN 32
60 kg/hr DN 25 DN 25 DN 32 DN 32 DN 32 DN 40
80 kg/hr DN 32 DN 32 DN 32 DN 32 DN 40 DN 50
Table 8: Max. flow rate
Where necessary, a large distance can be installed in a large nominal
width and a connection in the nominal width of the device can be select-
ed for shorter sections shortly before and after the device.
M
M
L
A
L
1
L
B
L
C
L
2
L
D
Item Meaning
1Vacuum regulator
2Vacuum changeover unit
3Dosing device
LA...LD
Lines connected to the device
each with approx. 0.5m in the connection nominal width
L1+ L2
Large distances in a larger nominal width
The total of L1and L2should not exceed the max. length
indicated in Tab. 8
Table 9: Long vacuum line
1 2 3 4 56
1 2 3

Installation
Electrical installation
12 © Lutz-Jesco GmbH 2018
BA-24721-02-V02
Chlorine gas changeover unit C 7523 Operating instructions
7.3.1 Establish the hose connection
Precondition for action:
üThe device is fitted on the wall.
üThe transport protection on the connection has been removed.
Resources required:
@Sharp knife
Fig. 6: Establish the hose connection
Perform the following working steps:
1. Cut the hose (1) a at right angles.
2. Slide the union nut (2) onto the hose.
3. Slide the hose end onto the cone of the hose connection (3).
4. Tighten the union nut by hand.
5. Fix the hose to the wall.
üHose connected fitted.
7.3.2 Make the PVC adhesive bond.
Precondition for action:
üThe device is fitted on the wall.
üThe vacuum line is fixed with sufficient pipe clamps and meets the
connection in an un-tensioned state.
üAll parts are clean and dry.
üThe transport protection on the connection has been removed.
Resources required:
@Pipe cutter
@File or chamfer tool
@PVC adhesive and cleaning agent
@Non-fuzzing paper towels
Perform the following working steps:
1. Cut the PVC pipe at right angles. Make a chamfer on the pipe exterior
(approx. 3 mm x 20°).
2. Clean the pipe and the bushing with the cleaning agent recommend-
ed by the manufacturer of the adhesive.
3. Glue the pipe in the connection. Follow the instructions on the PVC
adhesive.
Fig. 7: Make the PVC adhesive bond.
4. Mount the connection on the device. Ensure that the O-ring is fitted.
5. Tighten the union nut by hand.
6. Allow the bond to harden for at least 3 hours prior to the leak test.
üPVC seal connection made.
7.4 Electrical installation
DANGER
Mortal danger from electric shock!
Improperly installed or damaged components in the electronics instal-
lation can cause injury.
ðEnsure that all work on the electrical installation is performed by a
qualified electrician.
ðEnsure that all work on the electrical installation is performed in a
de-energised state.
ðEnsure that the power supply is secured with a fault current
protective circuit.
ðReplace damaged cables or components without delay.
Open the control housing
Resources required:
@Flat-bladed screwdriver, size 3
Perform the following working steps:
1. Hold the screwdriver in the right-hand clearance on the front of the
housing.
2. Move the screwdriver grip towards the lid of the housing until the
hinge part disconnects from the adjustment lock.
3. Pivot the housing lid to the left.
üHousing opened.
Close the control housing
Perform the following working steps:
1. Pivot the housing lid towards the housing floor.
2. Pivot the hinge part towards the lid until it snaps in audibly.
3. Press against the hinge part with your hand until it locks audibly in
place.
üHousing closed.
32
1

Installation
Electrical installation 13
© Lutz-Jesco GmbH 2018
Subject to technical changes
180321
BA-24721-02-V02
Chlorine gas changeover unit C 7523 Operating instructions
Terminal plan
Fig. 8: Control circuit board
Position Description
AConnector for the ribbon cable
BSwitch SW1/SW2
CMicrofuse 3.15 A (T)
DReserve fuse
Table 10: Elements of the circuit board
Switch Function Switch
downwards
Switch
upwards
SW1 Residue
discharge
OFF
(delivery state)
ON
SW2 Service switch Normal mode
(delivery state)
Diagnosis
(only for the
factory customer
services dept.)
Table 11: Functions of the switch SW1/SW2
A B C D
Terminal Function
1 L Left-hand
rotation phase
Voltage output to the motor
ball valve
2 L Right-hand
rotation phase
3 PE Protective
conductor
4 N Neutral
conductor
Table 12: Terminal connection
Terminal Function
5 Left
Position feedback from the motor ball valve6 com
7 Right
8 +
Input for the contact gauge
9 -
10 Relay operating output on left
(NO, max. 3 A/250 V AC)
11
12 Relay operating output on right
(NO, max. 3 A / 250 V AC)
13
14 Relay output on left battery empty
(NO, max. 3 A / 250 V AC)
15
16 Relay output on right battery empty
(NO, max. 3 A / 250 V AC)
17
18 NO
Relay output fault (max. 3 A / 250 V AC)
active if both side are empty or fault on the motor
19 com
20 NC
21 N Neutral
conductor
Mains input
115 - 230 V AC
22 PE Protective
conductor
23 L Phase
Table 12: Terminal connection

Installation
Installation with bypass
14 © Lutz-Jesco GmbH 2018
BA-24721-02-V02
Chlorine gas changeover unit C 7523 Operating instructions
Motor connection
In its delivery state, the motor of the ball valve is connected in accordance
with the following plan.
1 2
3
2
3
1
BK
BN
GY
GNYE
BK GY
BN
Fig. 9: Motor connection
Position Description
AControl circuit board
BLarge plug on the motor
CSmall plug on the motor
Table 13: Motor connection
7.5 Installation examples
Fig. 10: Installation example
Item Description
1Dosing device
2Reaction section (L = DN x 10)
3Injector non-return valve C 3101
4Angle piece
5 Injector
6Reaction section (L = DN x 5)
Table 14: Components
7.6 Installation with bypass
The volume to be removed from a supply battery is limited by the number
of pressure tanks connected. To prevent the unnecessary connection of
too many pressure tanks, in the majority of cases, the supply battery is
designed for normal operation. Such installations are fitted with a bypass
valve for higher volumes required at short notice (e.g. a shock chlorina-
tion). It is thus possible to extract from both supply batteries simultane-
ously.
Fig. 11: Installation with bypass valves
If the dosing system is also to be operated whilst maintenance is per-
formed on the changeover unit, 5 manual valves are required in the pipe
line.
Fig. 12:
A
AA
B
B
Installation with 5 service valves
Check
valve In normal operation During service
A Open Closed
B Closed Manual switching
Table 15: Function of the service valves
A
C
B

Installation
Installation with a vacuum manifold 15
© Lutz-Jesco GmbH 2018
Subject to technical changes
180321
BA-24721-02-V02
Chlorine gas changeover unit C 7523 Operating instructions
7.7 Installation with a vacuum manifold
Fig. 13: Installation with a vacuum manifold
Position Description Position Description
1Chlorine cylinder 11 Motive water set
2Vacuum regulator 12 Injector with non-return valve
3Vacuum manifold 13 Vacuum breaker
4Safety blowoff valve 14 Chlorine solution injection nozzle
5Activated carbon cartridge 15 Gas warning device
6Vacuum changeover unit with 2 bypass valves 16 Horn
7Safety shutoff valve 17 Strobe
8Flow meter 18 Gas sensor
9Control valve 19 Sprinkler system
10 Motive water pump
Table 16: Designation of components
1
15
17 16
8
9
1211
4
6
5
10
14
7
2
3
18
19
13

Installation
Completing the installation
16 © Lutz-Jesco GmbH 2018
BA-24721-02-V02
Chlorine gas changeover unit C 7523 Operating instructions
7.8 Installation with a positive pressure manifold
M
Fig. 14: Installation with a positive pressure manifold
Position Description Position Description
ARoom for the chlorine gas supply 8Changeover unit with 5 service valves
BDosing device room 9Dosing device
1Chlorine barrel 10 Injector with non-return valve
2Chlorine barrel scale 11 Motive water pump
3Pressurised manifold 12 Gas warning device
4Chlorine gas filter 13 Horn
5Moisture eliminator with heating collar 14 Gas sensor
6Vacuum regulator 15 Entrance port of the chlorine eliminator
7Activated carbon cartridge
Table 17: Designation of components
7.9 Completing the installation
The cable screw connections must be tightened after assembly in order
to ensure the IP protection class of the installation. All union nuts on the
screw connections of the piping are tightened by hand.
A B
12
12
3
6
8
7
9
10
13
5
11
15
4
14

Commissioning
Adjusting the switch point 17
© Lutz-Jesco GmbH 2018
Subject to technical changes
180321
BA-24721-02-V02
Chlorine gas changeover unit C 7523 Operating instructions
8 Commissioning
8.1 Checking the vacuum system
NOTE
Operating faults through leakages in the vacuum system
Small leaks in the vacuum system will not be recognised in normal
operation, since no chlorine escapes. Air will enter the system with
moisture.The moisture can combine with the chlorine to create depos-
its and operating malfunctions.
With the injector switched off, there may be a slight chlorine smell.
ðCheck the vacuum system.
ðEnsure that all action is taken only by personnel with sufficient and
corresponding qualifications.
Precondition for action:
üThe vacuum system is fully assembled.
üAll the open connections of the vacuum system were closed.
üThe injector is ready for operation.
Perform the following working steps:
1. Interrupt the voltage supply of the changeover unit.
i
The position of the ball valve is adjusted manually during the
check. Error messages are generated if the voltage supply is
activated.
2. Switch the selection lever on the motor of the changeover unit to
MAN (=manual operation)
3. Turn the grip on the motor in such a way that the left supply battery is
connected.
4. Interrupt the chlorine supply from the connected supply battery. To
do so, either connect the tank valve of a valve in the supply line to the
vacuum regulator.
5. Open the valve on the dosing device to adjust the dosing quantity.
6. Switch on the injector and wait until the vacuum pressure gauge dis-
plays at least -0.5 bar.
i
A number of dosing devices contain a valve which protects the
injector against too strong a vacuum. If this valve is set e.g. to
0.4 underpressure, a negative pressure of 0.5 bar cannot be
reached during the leak test.
7. Switch off the injector.
4The vacuum must stay unchanged for at least five minutes.
8. If the vacuum collapses quickly, eliminate the leak and repeat the
check on the vacuum system.
9. Turn the grip on the motor in such a way that the right supply battery
is connected. Repeat steps 4-8.
üVacuum system checked.
NOTE
Damage of the gauge
The search for leaks in the vacuum system often uses compressed air
or nitrogen with a slight positive pressure as the leak point can then be
recognised using a soapy solution. This test damages the contact
gauge.
ðDismantle the contact gauge before checking the vacuum system
with positive pressure.
8.2 Turning on the device
Precondition for action:
üThe device is fully assembled.
üThe leak test was performed.
Perform the following working steps:
1. Switch on the voltage supply.
2. Ensure that the selection lever on the motor is set to AUTO.
èThe motor moves automatically to the operating position last set.
üDevice switched on.
8.3 Adjusting the switch point
It is rare that the switch point of the contact gauge needs to be adjusted.
Possible reasons for this could include:
nVery weak performance of the injector.
nDosing device with restrictor valve for the vacuum.
Fig. 15: Adjusting the switch point
Perform the following working steps:
1. Remove the transparent cover (2) from the contact vacuum gauge. To
do so, unscrew the outside ring (1) from the device. Observe the
seal(3).
2. Move the red marking (4) on the desired switch point.
3. Refit the transparent lid and tighten the ring nut by hand. Ensure the
correct position of the seal.
üSwitch point of the contact gauge adjusted.
43 2 1

Operation
Operating modes
18 © Lutz-Jesco GmbH 2018
BA-24721-02-V02
Chlorine gas changeover unit C 7523 Operating instructions
9 Operation
9.1 Controls
9.1.1 Operator controls of the control unit
All operating states are displayed on the control.
M
Fig. 16: Control elements
Position Description Meaning
1LED red Left battery empty
2 Key Acknowledge the cylinder change left
and switch left manually
3LED green Left battery full
4LED green Operation left battery
5LED yellow Motor works
6LED green Operation right battery
7LED green Right battery full
8 Key Acknowledge the cylinder change
right and switch right manually
9LED red Right battery empty
Table 18: Control elements
9.1.2 Motor operating elements
Fig. 17: Motor operating elements
Position Description Meaning
1Selector lever
MAN Manual operation
AUTO Automatic operation
2Plug small Position switch
3Plug large Voltage supply
4Hand lever Manual operation, if the selector
lever(1) is set to MAN
Table 19: Motor operating elements
9.2 Operating modes
9.2.1 Automatic operation
Control element Position
Switch SW2 on the circuit board OFF
Selector lever on the motor AUTO
Table 20: Set automatic operation
When in automatic operation, the changeover unit reacts to the switching
status of the contact gauge. When receiving notification that the current
supply battery is empty, the changeover unit changes to the standby bat-
tery.
7
9
8
3
1
2
4 5 6
1
2
3
4

Operation
Disposal 19
© Lutz-Jesco GmbH 2018
Subject to technical changes
180321
BA-24721-02-V02
Chlorine gas changeover unit C 7523 Operating instructions
9.2.2 All empty
If both batteries are empty, the valve on the battery last used remains
stationary.
Signal Empty battery Used battery
LED battery empty (red) Flashes Flashes
Relays empty ON ON
LED battery full (green) OFF OFF
Operation LED (green) OFF ON
Relays operation OFF ON
Relays malfunction ON
Table 21: State of the control during "Everything empty"
The notification of 2 empty batteries is issued with two minutes delay; in-
stallations with very long vacuum lines can experience a delay in the is-
sue of the OK notification from the contact gauge. The green LED flashes
in the newly-connected cylinder during the waiting time.
9.2.3 Residue discharge
Residue discharge is an optional function in automatic operation.
Control element Position
Switch SW1 on the circuit board ON
Table 22: Setting residue discharge
Total vacuum batteries can experience changeover even when not all of
the chlorine tanks of the battery are empty. This is due to the strong cool-
ing of the tanks following the extraction of too large a quantity of chlorine.
With active residue discharge, the changeover unit switches to the supply
battery notified as empty from which the residual quantity is removed.
This is performed in a 15 minute rhythm. Changing the cylinder and
pressing the "OK" button ends the residue discharge.
Signal Empty battery Used battery
LED battery empty (red) ON OFF
Relays empty ON OFF
LED battery full (green) Flashes ON
Operation LED (green) ON OFF
Relays operation ON OFF
Relays malfunction OFF
Table 23: State of the control during "Residue discharge"
9.2.4 Manual operation
Control element Position
Selector lever on the motor MAN
Table 24: Setting residue discharge
The ball valve on the hand grip of the motor is activated in manual opera-
tion. The motor no longer follows the signals of the control. This can lead
to fault messages during manual operation.
Signal Condition
LED valve Flashes
Relays malfunction ON
Table 25: Malfunction state of the control with MAN
9.3 Disposal
NOTE
Do not dispose of the device in household waste!
Do not dispose of electrical appliances with household waste.
ðDispose of the unit and its packaging material in accordance with
local laws and regulations.
ðDispose of different materials separately and recycle them.
ðBefore disposing of the old equipment, you must clean off the
remaining chlorine by rinsing it with nitrogen or air.
ðDevices returned to the manufacturer must be sent risk-free and
with a declaration of no objection (see page 29).

Shutdown
Long-term shutdown
20 © Lutz-Jesco GmbH 2018
BA-24721-02-V02
Chlorine gas changeover unit C 7523 Operating instructions
10 Shutdown
10.1 Short-term shutdown
Perform the following working steps:
1. Close the chlorine tank valves.
2. Use the injector to suck off the remaining chlorine.
3. Switch off the injector.
üChlorinator shut down for the short term.
10.2 Long-term shutdown
Perform the following working steps:
1. Close the chlorine tank valves.
2. Use the injector to suck off the remaining chlorine.
3. Run the chlorinator for approximately five minutes with nitrogen or
dry compressed air.
4. Switch off the injector.
5. Close all the open connections to protect the lines and devices from
humidity and dirt.
üChlorinator shut down for the long term.
The device remains in the installation location during the operating
pause. All connections remain closed. The voltage supply should remain
active so that condensate is unable to gather in the control.
Ensure ideal storage conditions where possible:
nthe storage place must be cold, dry, dust-free and generously
ventilated,
ntemperatures between +2 °C and +40 °C.
nRelative air humidity must not exceed 90 %.
i
If it has been out of use for a long period, we recommend
performing a little maintenance before starting up (see
"maintenance intervals" on page 21).
This manual suits for next models
4
Table of contents
Other Lutz-Jesco Control Unit manuals
Popular Control Unit manuals by other brands
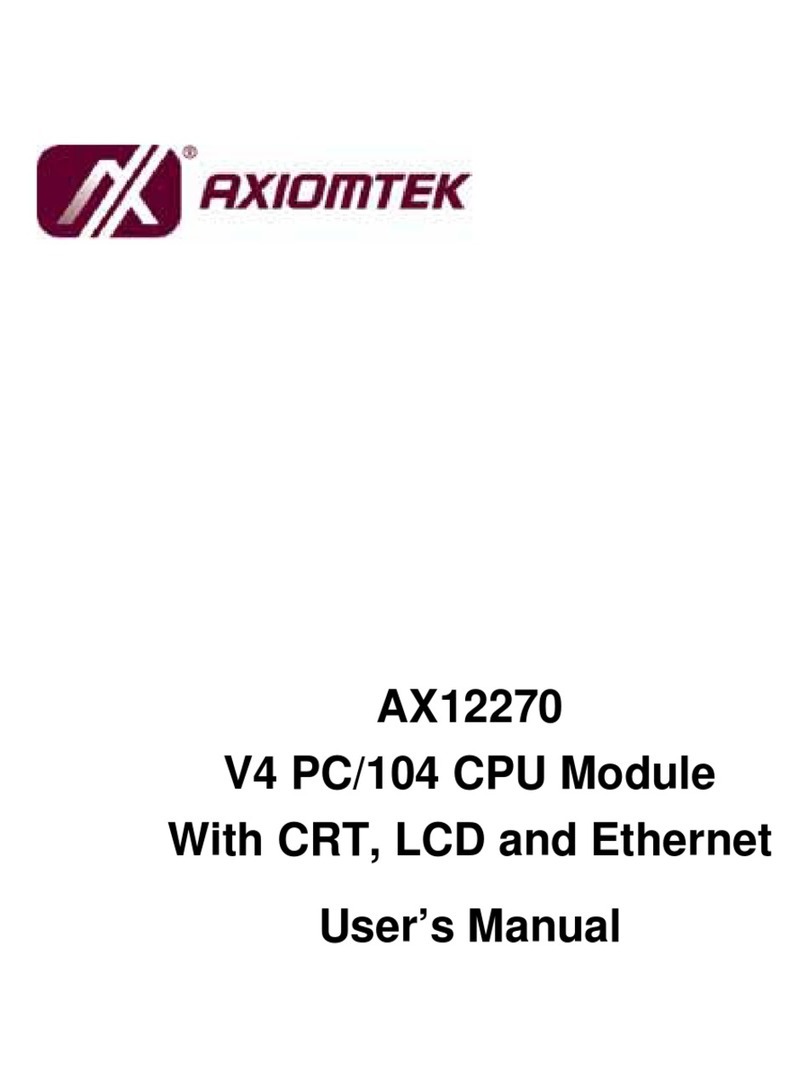
AXIOMTEK
AXIOMTEK AX12270 user manual
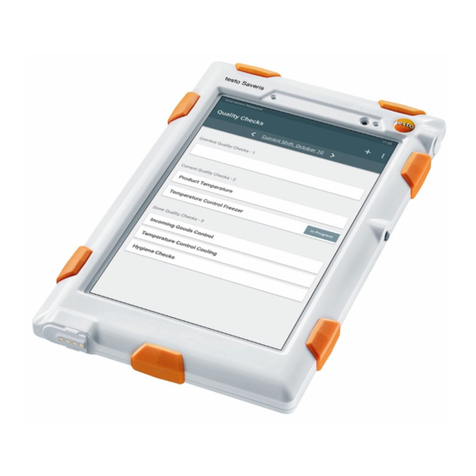
TESTO
TESTO Saveris 0573 2600 01 instruction manual
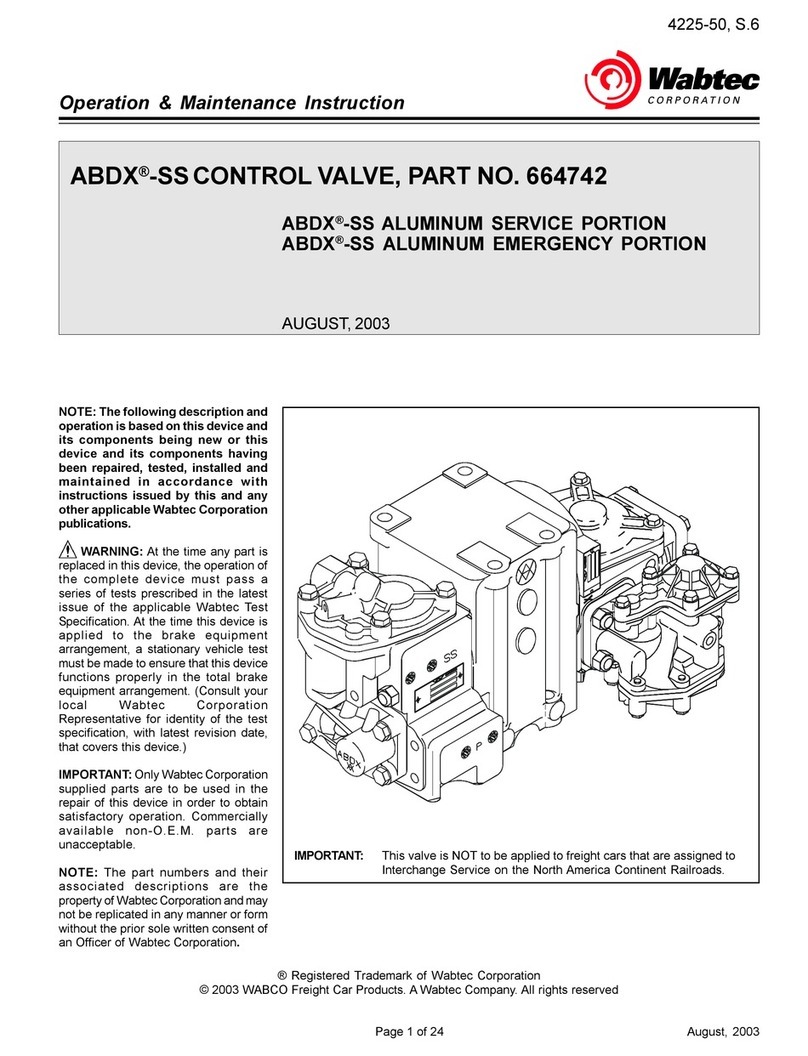
Wabtec
Wabtec ABDX-SS 664742 Operation and maintenance instruction
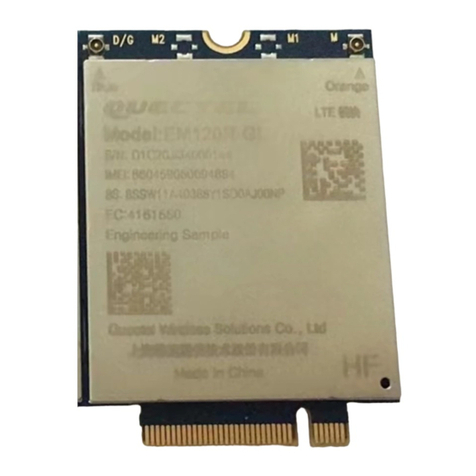
ThinkPad
ThinkPad EM120R-GL Regulatory notice
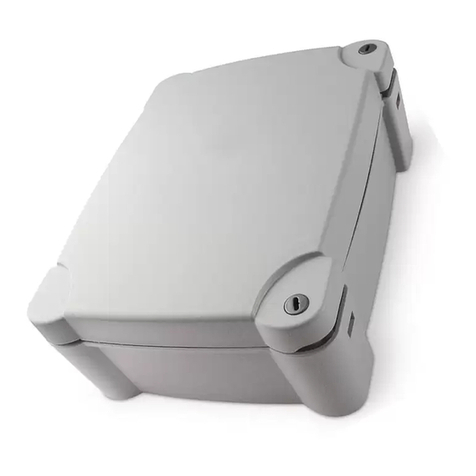
Nice
Nice MINDY A60A Instructions and warnings for installation and use
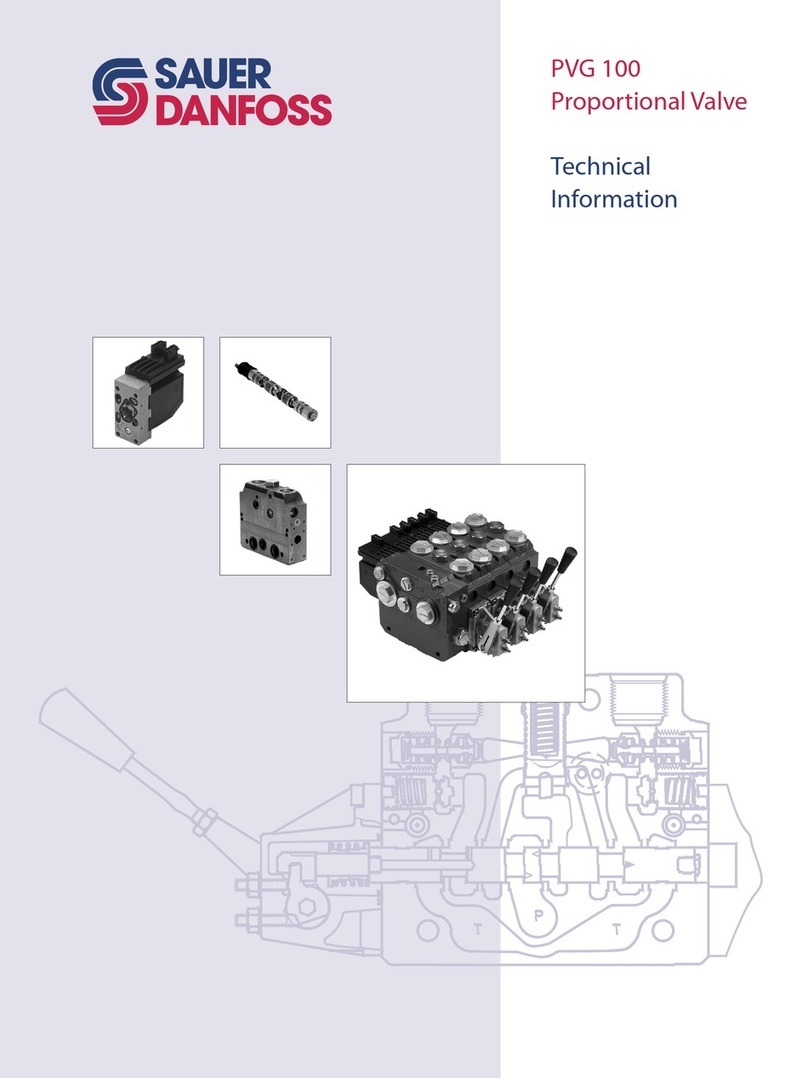
Sauer Danfoss
Sauer Danfoss PVG 100 technical information