Lutz-Jesco TOPAX MC User manual

Multi-channel controller TOPAX®MC
Dosing
Conveying
Control
Liquids
Gases
System
s
Operating instructions
Read the operating manual!
The user responsible for installation and operation related mistakes!
BA-46020-02-V01


Table of Contents 3
© Lutz-Jesco GmbH 2019
Subject to technical changes.
190729
BA-46020-02-V01
Multi-Channel Controller TOPAX®MC Operating instructions
Table of Contents
1 Notes for the Reader ..........................................................4
1.1 General non-discrimination......................................................4
1.2 Explanation of the signal words ................................................4
1.3 Explanation of the warning signs ..............................................4
1.4 Identification of warnings.........................................................4
1.5 Identification of action instructions ...........................................4
2 Safety .................................................................................5
2.1 General warnings.....................................................................5
2.2 Working in a safety-conscious manner .....................................5
2.3 Personnel qualification.............................................................5
3 Intended use ......................................................................7
3.1 Notes on product warranty .......................................................7
3.2 Intended purpose.....................................................................7
4 Product description ...........................................................8
4.1 Scope of delivery .....................................................................8
4.2 Design and function .................................................................8
4.3 Rating plate .............................................................................9
5 Technical data.................................................................. 10
5.1 TOPAX®MC...........................................................................10
5.2 Input modules........................................................................10
5.3 Output modules .....................................................................11
6 Dimensions ......................................................................11
6.1 Outside dimensions ...............................................................11
6.2 Drillhole dimensions ..............................................................11
7 Installation .......................................................................12
7.1 Principles ..............................................................................12
7.2 Installation on the wall ...........................................................12
7.3 Electrical installation..............................................................12
7.4 Terminal connection...............................................................13
7.5 Connecting sensors ...............................................................14
7.6 Connecting actors..................................................................15
7.7 Digital inputs .........................................................................16
7.8 RC protection for relay............................................................16
7.9 Connecting Ethernet ..............................................................17
7.10 RS485-interface ..................................................................17
8 Commissioning ................................................................18
8.1 First steps..............................................................................18
8.2 Configuration.........................................................................19
8.3 Password protection ..............................................................24
8.4 Network settings....................................................................25
9 Operation..........................................................................26
9.1 Confirming a message ...........................................................26
9.2 Logbook ................................................................................26
9.3 Viewing the trend display .......................................................27
9.4 Manual mode.........................................................................27
9.5 Adjustment ............................................................................27
9.6 Setpoints and Setpoint sets....................................................31
9.7 Access via network ................................................................32
10 Maintenance ....................................................................33
10.1 Maintenance intervals..........................................................33
10.2 Keeping logfiles ...................................................................33
10.3 Updating software................................................................33
10.4 Battery change ....................................................................33
10.5 Replacing the fuse ...............................................................34
10.6 Resetting the settings ..........................................................34
10.7 Finishing maintenance.........................................................34
11 Troubleshooting ...............................................................35
12 Modbus addresses...........................................................36
13 EU Declaration of Conformity...........................................42
14 Warranty claim.................................................................43
15 Glossary ...........................................................................44
16 Index.................................................................................45

Notes for the Reader
Identification of action instructions
4© Lutz-Jesco GmbH 2019
BA-46020-02-V01
Multi-Channel Controller TOPAX®MC Operating instructions
1 Notes for the Reader
This operating manual contains information and behaviour rules for the
safe and designated operation of the device.
Observe the following principles:
nRead the entire operating manual prior to starting-up the device.
nEnsure that everyone who works with or on the device has read the
operating manual and follows it.
nMaintain the operating manual throughout the service life of the de-
vice.
nPass the operating manual on to any subsequent owner of the device.
1.1 General non-discrimination
In this operating manual, only the male gender is used where grammar
allows gender allocation. The purpose of this is to make the text easy to
read. Men and women are always referred to equally. We would like to
ask female readers for understanding of this text simplification.
1.2 Explanation of the signal words
Different signal words in combination with warning signs are used in this
operating manual. Signal words illustrate the gravity of possible injuries if
the risk is ignored:
Signal word Meaning
DANGER Refers to imminent danger. Ignoring this sign may
lead to death or the most serious injuries.
WARNING!
Refers to a potentially hazardous situation.
Failure to follow this instruction may lead to death
or severe injuries.
CAUTION
Refers to a potentially hazardous situation.
Failure to follow this instruction may lead to
minor injury or damage to property.
NOTE Refers to a danger which, if ignored, may lead to
risk to the machine and its function.
Table 1: Explanation of the signal words
1.3 Explanation of the warning signs
Warning signs represent the type and source of a danger:
Warning sign Type of danger
General danger
Danger from electrical voltage
Danger from poisonous substances
Danger of damage to machine or functional
influences
Table 2: Explanation of the warning signs
1.4 Identification of warnings
Warnings are intended to help you recognise risks and avoid negative
consequences.
This is how warnings are identified:
Warning sign SIGNAL WORD
Description of danger.
Consequences if ignored.
ð
The arrow signals a safety precaution to be taken to eliminate the
danger.
1.5 Identification of action instructions
This is how pre-conditions for action are identified:
ü
Pre-condition for action which must be met before taking action.
@A resource such as a tool or auxiliary materials required to perform
the operating instructions.
This is how instructions for action are identified:
èSeparate step with no follow-up action.
1. First step in a series of steps.
2. Second step in a series of steps.
4Result of the above action.
ü
Action completed, aim achieved.

Safety
Personnel qualification 5
© Lutz-Jesco GmbH 2019
Subject to technical changes.
190729
BA-46020-02-V01
Multi-Channel Controller TOPAX®MC Operating instructions
2 Safety
2.1 General warnings
The following warnings are intended to help you eliminate the dangers
that can arise while handling the device. Risk prevention measures al-
ways apply regardless of any specific action.
Safety instructions warning against risks arising from specific activities
or situations can be found in the respective sub-chapters.
DANGER
Mortal danger from electric shock!
Incorrectly connected, incorrectly placed and damaged cables can
cause injury.
ð
Replace damaged cables immediately.
ð
Do not use extension cables.
ð
Do not bury cables.
ð
Secure cables to avoid being damaged by other equipment.
CAUTION
Increased risk of accidents due to insufficient qualifica-
tion of personnel!
The device may only be installed, operated and maintained by person-
nel with sufficient qualifications. Insufficient qualification will increase
the risk of accidents.
ð
Ensure that all action is taken only by personnel with sufficient and
corresponding qualifications.
ð
Prevent access to the system for unauthorised persons.
NOTE
Do not dispose of the device in the domestic waste!
Do not dispose of electric devices via the domestic waste.
ð
The device and its packaging must be disposed of in accordance
with locally-valid laws and regulations.
ð
Dispose of different materials separately and ensure that they are
recycled.
Hazards due to non-compliance with the safety instructions
Failure to follow the safety instructions may endanger not only persons,
but also the environment and the device.
The specific consequences can be:
nFailure of major unit und system functions.
nFailure of required maintenance and repair methods.
nDanger for individuals through dangerous dosing media.
nDanger to the environment from overdosing.
2.2 Working in a safety-conscious manner
Besides the safety instructions specified in this operating manual, further
safety rules apply and must be followed:
nAccident prevention regulations.
nSafety and operating provisions.
nSafety regulations on handling hazardous substances.
nEnvironmental protection provisions.
nApplicable standards and legislation.
2.3 Personnel qualification
Any personnel who work on the device must have appropriate special
knowledge and skills.
Anybody who works on the device must meet the conditions below:
nAttendance at all the training courses offered by the owner.
nPersonal suitability for the respective activity.
nSufficient qualification for the respective activity.
nTraining in how to handle the device.
nKnowledge of safety equipment and the way this equipment functions.
nKnowledge of this operating manual, particularly of safety instructions
and sections relevant for the activity.
nKnowledge of fundamental regulations regarding health and safety
and accident prevention.
All persons must generally have the following minimum qualification:
nTraining as specialists to carry out work on the device unsupervised.
nSufficient training that they can work on the device under the supervi-
sion and guidance of a trained specialist.

Safety
Personnel qualification
6© Lutz-Jesco GmbH 2019
BA-46020-02-V01
Multi-Channel Controller TOPAX®MC Operating instructions
These operating instructions differentiate between these user groups:
2.3.1 Specialist staff
Thanks to their professional training, knowledge, experience and knowl-
edge of the relevant specifications, specialist staff are able to perform the
job allocated to them and recognise and/or eliminate any possible dan-
gers by themselves.
2.3.2 Trained electricians
Due to their professional training, knowledge and experience as well as
knowledge of specific standards and provisions, trained electricians are
able to do the electrical work assigned to them and to recognise and
avoid any potential dangers by themselves.
They are specially trained for their specific working environment and are
familiar with relevant standards and provisions.
They must comply with the legally binding regulations on accident pre-
vention.
2.3.3 Trained persons
Trained persons have received training from the operator about the tasks
they are to perform and about the dangers stemming from improper be-
haviour.
Trained persons have attended all trainings offered by the operator.
2.3.4 Personnel tasks
In the table below you can check what qualifications are the pre-condi-
tion for the respective tasks. Only people with appropriate qualifications
are allowed to perform these tasks!
Qualification Activities
Specialist staff
nTransportation
nMechanical installation
nCommissioning
nTaking out of operation
nFault rectification
nMaintenance
nRepairs
nDisposal
Trained electricians nElectrical installation
Trained persons nControl
Table 3: Personnel qualification

Intended use
Intended purpose 7
© Lutz-Jesco GmbH 2019
Subject to technical changes.
190729
BA-46020-02-V01
Multi-Channel Controller TOPAX®MC Operating instructions
3 Intended use
3.1 Notes on product warranty
Any non-designated use of the device can impair its function and the pro-
tection provided. This leads to invalidation of any warranty claims!
Please note that liability is on the side of the user in the following cases:
nThe device is operated in a manner which is not consistent with these
operating instructions, particularly safety instructions, handling in-
structions and the section "Intended Use".
nInformation on usage and environment (section 5 “Technical data” on
page10) is not adhered to.
nIf people operate the device who are not adequately qualified to carry
out their respective activities.
nUnauthorised changes are made to the device.
3.2 Intended purpose
The controller monitors the current measured values during water treat-
ment and controls the dosing systems connected for water treatment. In
this way, the controller ensures constant water values in various applica-
tions and can be deployed universally. One of the main applications is the
maintenance of water quality in industry and public swimming pools by
measuring and evaluating the water parameters chlorine value, pH value,
redox value, total chlorine as well as conductivity and the control of chlo-
rine gas dosing systems.
Foreseeable misuse
The following section provides information regarding the device applica-
tions which are classified as non-intended use.This section is intended to
allow you to detect possible misuse in advance and to avoid it.
Foreseeable misuse is assigned to the individual stages of the product
lifetime:
3.2.1 Incorrect assembly
nConnecting the mains voltage without a protective earth.
nNon-fused or non-standard mains voltage.
nNot possible to immediately or easily disconnect the power supply.
nWrong connecting cables for mains voltage.
nSensors and actors connected to the incorrect terminals or incorrectly
configured.
nProtective earth removed.
3.2.2 Incorrect start-up
nCommissioning with damaged or obsolete sensors.
nCommissioning without the establishment of all protective measures,
fastenings etc.
3.2.3 Incorrect operation
nProtective equipment not functioning correctly or dismantled.
nUnauthorised modification of the controller.
nIgnoring of alarm or error messages.
nThe elimination of alarm or error messages by insufficiently-qualified
personnel.
nBridging the external fuse.
nDifficult operation due to insufficient lighting or poor access to the de-
vice.
nOperation not possible due to dirty or illegible display.
3.2.4 Incorrect maintenance
nCarrying out maintenance during ongoing operation.
nNo adequate or regular inspection of correct functioning.
nNo replacement of damaged parts or cables.
nNo securing against reactivation during maintenance work.
nUse of the wrong spare parts.

Product description
Design and function
8© Lutz-Jesco GmbH 2019
BA-46020-02-V01
Multi-Channel Controller TOPAX®MC Operating instructions
4 Product description
4.1 Scope of delivery
Please compare the delivery note with the scope of delivery. The follow-
ing items are part of the scope of delivery:
nController
nOperating instructions
nMounting set
nSensors (optional)
nCable connection from the device to the sensors (optional)
4.2 Design and function
4.2.1 Functional diagram
Fig. 1: Functional diagram of a two-channel controller
Gap Field Description
Sensors
1. Free chlorine
2. Disturbance variable
3. pH
1. Measuring the free chlorine
2. The disturbance variable is a variable flow volume which can be taken into account
3. Measuring the pH value
Input modules
1. Current module
2. Digital 1
3. Virtual 1
4. pH/Redox module
1. Module for 4 − 20 mA signals and sensors with 24 V voltage supply
2. Digital input for the external control of a function (here: external stop)
3. Parameter calculated (here effective chlorine)
4. Module for pH and Redox sensors
Control system 1. Controller 1
2. Controller 2
1. Controlling the free chlorine inc. pH/temperature compensation and disturbance variable
2. Controlling the pH value inc. temperature compensation
Output modules 1. Module 1
2. Module 2
1. Module on slot 1 to connect an actor (here: MAGDOS LD)
2. Module on slot 2 to connect an actor (here: MEMDOS LP)
Table 4: Explanation
Sensors Input
modules
Control
system
Output
modules
Actors
Free
chlorine
Disturbance
variable
On/Off
pH
Current
module
Digital 1
Virtual 1
(Effective chlorine)
pH/Redox
module
Controller 1 Module 1
pH /
Temp Disturbance
variable
Function
(External stop)
Controller 2
Temp Module 2
Compensation
Compensation

Product description
Rating plate 9
© Lutz-Jesco GmbH 2019
Subject to technical changes.
190729
BA-46020-02-V01
Multi-Channel Controller TOPAX®MC Operating instructions
4.2.2 Functions of the device
The stationary device measures the water values using sensors. Con-
trolling actors such as dosing pumps controls the water values to the de-
sired setpoint.
4.2.3 Main view
The main menu view will appear upon the start of the device or 5 minutes
after the last input. The main view shows the current values from up to
four sensors and further information.
Fig. 2: Main view with three sensors
Item Function
1Login/password settings
2 Date/time
3Measured values
4Main menu
5File Browser
6Status row for messages
Table 5: Components
4.3 Rating plate
There is information on the equipment about safety or the product's way
of functioning. The information must stay legible for the duration of the
service life of the product.
Fig. 3: Rating plate TOPAX® MC
Item Description
1Product name
2Technical specifications
3Label showing conformity with applicable European
directives
4WEEE label
5Serial number
6Part number
7Month/year of manufacture
Table 6: Rating plate
6
2
1
45
3
7
6
5
2
1
3
4

Technical data
Input modules
10 © Lutz-Jesco GmbH 2019
BA-46020-02-V01
Multi-Channel Controller TOPAX®MC Operating instructions
5 Technical data
5.1 TOPAX®MC
Information Value
Voltage supply 100 − 240 V AC, 50/60 Hz
Power consumption max. 20 W
Housing dimensions (W x H x D) 302 x 240 x 107 mm
Load capacity of the alarm relay 250 V AC, 8 A (ohmic load)
Analogue outputs for remote transmission 4 x 0/4 − 20 mA, max. 500 Ω
Disturbance variable input 0/4 − 20 mA
Intervention of the disturbance variable, amplification between 0.1 − 10 times
Interfaces
Ethernet Modbus TCP/IP
RS485 Modbus RTU (optional)
Protection class IP65
Ambient temperature -5 to +45 °C
Air humidity max. 95 %, non condensing
Control characteristic P, PI, PID or PD behaviour, control direction selectable with disturbance variable feed
forward, 2-side control selectable
Table 7: Technical data
5.2 Input modules
All input modules consist of an input for temperature measurement via Pt100 and a second input for the measurement of a further water parameter. On
some input modules, this input will measure a number of different parameters.
Sampling system Value
Temperature input -10 to +90 °C
Measurement input pH Redox
module
pH value pH 0 – pH 14
Redox 0 − 1000 mV
Measurement input potentiostat
module
Cl2(Free chlorine)
Measuring range dependant on the slope up to c. 18 mg/l.
ClO2(Chlorine dioxide)
Measurement input current
module
Excess chlorine measuring cell CS120 Measuring range dependant on the slope up to c. 20 mg/l.
Diaphragm-covered measuring cell,
conductivity or another 0/4−20mA
sensor
0/4 − 20 mA, max. 500 Ω
Voltage current module 24 V
Table 8: Technical data

Dimensions
Drillhole dimensions 11
© Lutz-Jesco GmbH 2019
Subject to technical changes.
190729
BA-46020-02-V01
Multi-Channel Controller TOPAX®MC Operating instructions
5.3 Output modules
Output Value
Relay module 2 x 230 V AC, 5 A (ohmic resistive load)
Optocoupler module 2 x 80 V DC, 5 mA
Servomotor relay
Output 230 V AC, 5 A (ohmic resistive load)
Input 1 − 10 kΩ
Servomotor mA
Output 0/4− 20 mA, max. working resistance 500 Ω
Input 0/4 − 20 mA
Table 9: Technical data
6 Dimensions
All dimensions in millimeter (mm).
6.1 Outside dimensions
Fig. 4: Outside dimensions
6.2 Drillhole dimensions
Fig. 5: Dimensions for wall mounting
302
240
267
171

Installation
Electrical installation
12 © Lutz-Jesco GmbH 2019
BA-46020-02-V01
Multi-Channel Controller TOPAX®MC Operating instructions
7 Installation
7.1 Principles
Make sure that the installation location complies with the following re-
quirements:
nThe display is easily accessible and is visible.
nPlan to leave min. 20 cm free space for the installation of the cable
underneath the device. You must be able to install the cable without
kinking or damage.
nVarious lines (e.g. voltage supply, data cable and sensitive lines for
measuring purposes) must be installed separately. The different lines
should only cross at 90° so as to prevent falsifications.
nElectrical, magnetic and electromagnetic fields affect signal transmis-
sion and can destroy electronic components.
nCompliance with the permissible ambient temperatures (section 5
“Technical data” on page10).
7.2 Installation on the wall
Resources required:
@Assembly kit
@Drill
@Slotted screwdriver
Perform the following steps:
1. Drill the four drillholes for wall mounting. The exact dimensions are
stated in section 6 “Dimensions” on page11.
2. Unscrew the screw on the right-hand side of the device and pull out
the rod.
4You can now open the device.
3. Open the device and use the screws for wall mounting. Ensure that
the device is secured to the wall.
4. Close the device again using the rod.
ü
The device is fitted on the wall.
7.3 Electrical installation
The voltage supply to your device can now be performed via a normal
Schuko plug or a control cabinet. Perform the specifications of this sec-
tion for devices without a pre-fitted Schuko plug.
Precondition for action:
ü
The device was installed in accordance with section 7.2 Installation
on the wall.
ü
A voltage supply with 100 − 240 V AC (50/60 Hz) is available.
ü
The voltage supply is deactivated before the start and secured
against reactivation.
ü
The housing is open.
Resources required:
@Grounding-type plug
@Wire end sleeves 0.75 − 2.5 mm²
DANGER
Mortal danger from electric shock!
Improper installation or damaged components of the electrical instal-
lation may result in injury.
ð
Ensure that work on the electrical installation is only carried out by
a qualified electrician.
ð
Make sure that work on the eelectrical installation is only carried out
when it is voltage-free.
ð
Ensure that power supply is protected by a residual current circuit
breaker.
ð
Replace damaged cables or components immediately..
1. Fit wire end sleeve to the cable ends if the supply cable does not
have them.
2. Open the device housing.
3. Lead the supply cable through a cable screw connection to the un-
derside of the device.
4. Turn the cable screw connection union nut until the line is fixed in the
screw connection so that the screws connection performs strain re-
lief. Ensure that the feed cable is installed loosely.
5. Connect the voltage supply to the clamps 44 − 52. Observe the divi-
sion into protective earth (PE), neutral conductor (N) and the phase (L)
on the circuit board.
Fig. 6: Connected voltage supply
ü
Electrically installation
i
Only 3 of 9 clamps are required for connection of the voltage
supply. You can use the free clamps to supply further devices
with voltage.
The contact load rating amounts to max. 4A.

Installation
Terminal connection 13
© Lutz-Jesco GmbH 2019
Subject to technical changes.
190729
BA-46020-02-V01
Multi-Channel Controller TOPAX®MC Operating instructions
7.4 Terminal connection
81 9
2 3 4 5 6 7 10 11121314151617181920
29303132333435 36212223242526272837383940
41 42 43 44 45 46 47 48 49 50 51 52
USB
AB
Fig. 7: Overview of the connection clamps
Terminal Function Description
1LED output 1 (red) +
5 V with 220 Ω series resistance for LEDs of the water
sampling stations
2LED output 1 (green) +
3LED output 2 (red) +
4LED output 2 (green) +
5LED output 3 (red) +
6LED output 3 (green) +
7LED output 4 (red) +
8LED output 4 (green) +
9 − 10 LED output GND -Ground for the LEDs
11 Disturbance variable input +0/4 − 20 mA
12 -
13 Analogue output 1 +
0/4 − 20 mA, max. working resistance 500 Ω
14 -
15 Analogue output 2 +
16 -
17 Analogue output 3 +
18 -
19 Analogue output 4 +
20 -
21 − 36 Digital inputs 1 − 8 Function configurable
37 − 40 Ethernet connection
41 − 43 Alarm relay Clamps 41+42 normal on
Clamps 42+43 normal off
44 − 46
Connection supply voltage
Protective earth (PE)
47 − 49 Neutral line (N)
50 − 52 Phase (L)
Table 10: Terminal connection
LED outputs
Input 1
Input 2
Input 3
Input 4
Output 1
Output 2
Output 3
Output 4
Ethernet Digital inputs
0/4 – 20mA
Alarm relay
Voltage
RS485

Installation
Connecting sensors
14 © Lutz-Jesco GmbH 2019
BA-46020-02-V01
Multi-Channel Controller TOPAX®MC Operating instructions
7.5 Connecting sensors
Up to four input modules can be connected to the device. A water param-
eter and the temperature can be measured with every module.
Precondition for action:
ü
The voltage supply has been disconnected and protected against
re-connection.
ü
The housing is open.
Resources required:
@Sensors
@Connecting cable
Perform the following steps:
1. Lead the cable through one of the cable screw connections on the
underside into the interior of the housing.
2. Connect the wires onto the clamp block of the input modules. Comply
with the terminal plans in the following sections.
ü
Sensor connection completed.
NOTE
Electronic distortion of the measurement results.
Incorrect installation of the electrical cables can distort the measure-
ment results.As a result,the control of connected devices can be faulty.
ð
Do not route the connecting cable parallel to the mains and control
connections, and always with a clearance of at least 15cm. Lay
connection junctions at an angle of 90°.
7.5.1 pH Redox module input circuit board
4
3
2
1
Fig. 8: Module for measuring the pH and Redox
Terminal Function Sensors
1Temperature input Resistance thermometer
TE110/Pt100
2Temperature input
3- (wire with Ø 1.5 mm) pH single-rod measuring
chain PE110/rH-single-rod
measuring chain ME110
4+ (wire with Ø 2 mm)
Table 11: Terminal connection
Ø 2
Ø 1,5
Fig. 9: Connect the cable from the pH or Redox sensors correctly
7.5.2 Potentiostat module input circuit board
4
3
2
1
5
Fig. 10: Module for the potentiostats
Terminal Function Sensors
1Temperature input Resistance thermometer
TE110/Pt100
2Temperature input
3Measuring electrode
3 electrode potentiostat4Counter electrode
5Reference electrode
Table 12: Terminal connection
7.5.3 Current module input circuit board
A number of sensors require an operating voltage for their measurement.
These sensors are connected to the current module and supplied with
24V.
4
3
2
1
5
Fig. 11: Current module
Terminal Function Sensors
1Temperature input Resistance thermometer
TE110/Pt100
2Temperature input
3 - - Excess chlorine measuring
cell CS120/conductivity
measuring cell
4(for 4 − 20 mA or
CS120)
+
-Total chlorine measuring
cell GCM/diaphragm-cov-
ered measuring cell Cl 4.1/
diaphragm-covered
measuring cell CD 4 MA*
524 V DC output +
Table 13: Terminal connection
* Requires 24 V supply module
Centre conductor
Screen

Installation
Connecting actors 15
© Lutz-Jesco GmbH 2019
Subject to technical changes.
190729
BA-46020-02-V01
Multi-Channel Controller TOPAX®MC Operating instructions
7.6 Connecting actors
Depending on the equipment of the device, you have various possibilities
of actuating actors such as dosing pumps or regulation valves.
7.6.1 Alarm relay
The alarm relay on the main board forwards alarms.
41 42 43
Fig. 12: Alarm relay
Terminal Function Description
41 + 42 normal on The relay works on these
clamps as an opener.
42 + 43 normal off The relay works on these
clamps as a closer.
Table 14: Terminal connection
7.6.2 Output circuit board relay
4
3
2
1
Fig. 13: Output circuit board with relay
Terminal Function Description
1
Relay X.2 Second digital output
2
3
Relay X.1 First digital output
4
Table 15: Terminal connection
Actors Configuration
MAGDOS dosing pumps On/Off
MEMDOS dosing pumps On/Off
MEMDOS SMART dosing pumps On/Off
MIDIDOS/MINIDOS dosing pumps On/Off
Peristaltic pumps Pulse length
Table 16: Actors and configuration
7.6.3 Output circuit board optocoupler
4
3
2
1
Fig. 14: Output circuit board with optocoupler
Terminal Function Description
1 +
Optocoupler X.2 Second digital output
2 -
3 +
Optocoupler X.1 First digital output
4 -
Table 17: Terminal connection
Actors Configuration
MAGDOS dosing pumps
Pulse frequencyMEMDOS dosing pumps
MEMDOS SMART dosing pumps
Table 18: Actors and configuration
7.6.4 Servomotor relay output circuit board
This output is suitable for connecting a servomotor with or without feed-
back via a potentiometer from 1 – 10 kΩ.
3
2
1
6
5
4
Fig. 15: Servomotor relay
Terminal Function Description
1 − 2 Opening the regulation
valve Relay output
2 − 3 Closing the regulation valve Relay output
4
Feedback via potentiom-
eter
5
6
Table 19: Terminal connection
Actors Configuration
C7700 chlorine control valve Servomotor with potentiometer/
servomotor without potentiometer
Table 20: Actors and configuration
0 %
100 %

Installation
RC protection for relay
16 © Lutz-Jesco GmbH 2019
BA-46020-02-V01
Multi-Channel Controller TOPAX®MC Operating instructions
7.6.5 Output circuit board servomotor 20 mA
The output connects a servosmotor with or without feedback.
Fig. 16: Output module ATE (20 mA) with feedback
Terminal Function Description
1 - GND
2Input (feedback) 4 − 20 mA
3 Output 4 − 20 mA
Table 21: Terminal connection 20 mA
Actors Configuration
C7700 chlorine control valve Servomotor with 20 mA/
continuous output (20 mA)
EASYZON chlorine dioxide plant
Continuous output (20 mA)
MAGDOS dosing pumps
MEMDOS dosing pumps
MEMDOS SMART dosing pumps
Table 22: Actors and configuration
7.6.6 Testing the outputs
You can use manual mode to test the correct connection of an actor.
Take the alarm chain into account before conducting the test and inform
any connection points or interrupt the alarm chain for the period of the
test.
Test the connected actors
Precondition for action:
ü
The actors have been connected in accordance with section 7.6
“Connecting actors” on page15.
ü
The device housing cover is closed.
ü
The voltage supply has been established and the device has been
switched on.
Instruction:
1. Working in the main menu, navigate to “Manual mode” (section 9.4
“Manual mode” on page27).
4You will now see all the outputs.
2. Select the output to which you have connected the actor and which
you wish to test.
3. Enter a value between 0 and 100 % and check whether the actor re-
acts as desired.
ü
Actor has been tested.
Testing the analogue outputs
You can also test the connection of terminals 13 to 20.
Precondition for action:
ü
The device housing cover is closed.
ü
The voltage supply has been established and the device has been
switched on.
Instruction:
1. Working in the main menu, navigate to System > Outputs > Ana-
logue.
4You will now see all analogue outputs (terminals 13 – 20).
2. Press “Test signal”.
3. Set the mA value.
4. Press "Start”.
ü
Analogue outputs tested.
7.7 Digital inputs
You can use up to 8 digital inputs to evaluate switching statuses and to
detect them as alarm message which are to be documented in the log-
files.
Further information about the settings of the digital inputs can be found in
section 8.2.1.6 “Digital inputs” on page21.
7.8 RC protection for relay
When connecting to the relay, note that inductive loads must be sup-
pressed. If this is not possible, the relay contact on the device terminal
must be protected by an RC protective circuit/interference suppression
element.
If devices with inductive loads from a nominal current of 1 A are connect-
ed to a relay, the contacts in the relay may become bonded. Thus, the de-
vice will operate in an uncontrolled manner. To prevent bonding if the load
circuit suffers a short-circuit, the relays must be protected separately on
the maximum relay switching current.
Precondition for action:
ü
You would like to connect an inductive load to the relay.
Instruction:
1. Switch off the device.
2. Clamp the interference suppression element parallel to the inductive
load.
3. Should it prove impossible to perform point 2, clamp the interference
suppression element parallel to the relay output.
ü
RC element clamped.
79829_1
Bild BA Ausgangsmodul ATE (20 mA) mit Rückmeldung
EASYCON
3
2
1

Installation
RS485-interface 17
© Lutz-Jesco GmbH 2019
Subject to technical changes.
190729
BA-46020-02-V01
Multi-Channel Controller TOPAX®MC Operating instructions
7.9 Connecting Ethernet
You can use the Ethernet connection for the following actions:
nReading / writing via Modbus TCP/IP protocol (PLC or Computer)
nAccess via web browser
nAccess via TFTP server
The device is fitted with a network input in the form or a 4-pole and
D-coded M12x1 socket. Lutz-Jesco GmbH offers different lengths of spe-
cial twisted-pair network cables to make the typical Ethernet RJ-45 plug
connection. If you use third-party cables, choose a Category 3 cable with
an impedance of 100 Ω or above.
Pin Assignment Wire colours
1 TX- yellow
2 TX+ orange
3 RX- white
4 RX+ blue
- Screen -
Table 23: Ethernet connection socket
Fig. 17: Ethernet socket
Installing a wired network
During installation, comply with the following points:
nThe Ethernet is cabled in a star topology. The maximum cable length
is 100 m.
nOnly use screened cables and connectors.
nOnly use CAT5 cables or better.
7.10 RS485-interface
Fig. 18: Jumper position on RS485
i
When using multiple devices on a data line, you must activate
a 120 Ω resistance on the last device.
You can activate the resistance by setting the jumper to “ON”
as shown in Fig. 18.
Your device can have an optional RS485-interface. Using a two-paired
data cable you can connect up to 14 devices with a PC or a PLC. Modbus
RTU protocol serves as a protocol for data transfer. You can use the ad-
dresses 1 to 14. The addresses 0 and 15 are reserved for internal purpos-
es and are not supported.
RS485 Modbus settings:
nBaud rate: 9600
nWord length: 8 Bit
nStop bit: 1 Bit
nParity: None
nYou can read out a maximum of 40 addresses at once.
The list of Modbus commands can be found in section 12 “Modbus ad-
dresses” on page36.
Perform the following steps:
1. Open the device housing.
2. Connect a two-paired data cable to terminals A and B of the RS485
module.
3. Connect the device with your network.
ü
Device connected with network.
ON OFF
A B A B
Ethernet
port

Commissioning
First steps
18 © Lutz-Jesco GmbH 2019
BA-46020-02-V01
Multi-Channel Controller TOPAX®MC Operating instructions
8 Commissioning
Outputs
Controller functions Behaviour
Relays
Optocoupler
Servomotor
relay
Servomotor
20 mA
x On/Off nThe output switches if a value is exceeded.
nHysteresis can be set from 0.1 – 50 %.
x x Pulse frequency or
2 sides pulse frequency
nRelay: 10 – 100 pulses per minute
nOptocoupler: 10 – 350 pulses per minute
nThe pulse frequency is dependant on the control deviation and the set control
parameters.
nWith a control output power of Y = 25 % and a maximum pulse frequency of
100pulses/min., the controller would output 25 pulses/min.
xPulse length or
2 sides pulse length
n0 – 3600 seconds cycle duration
nRelay output (e.g. for solenoid valve)
nDepending on the control deviation and the defined control parameters, the relay
pulls in or drops out for the set cycle duration. If the cycle lasts 30 seconds and the
controller output power is 40% the relay applies for example for 12 seconds,
followed by 18 seconds of non-application.
xServomotor with
potentiometer
nA feedback potentiometer can be connected (1 – 10 kΩ) for servomotors with
position feedback.
nCompensate the feedback potentiometer. During compensation, the servomotor is
first started and then stopped automatically.
xServomotor without
potentiometer
nFor servomotors without feedback.
nMeasure and set the runtime of the servomotor.
xContinuous output nContinuous control output from 0/4 – 20 mA for the actuation of constant actors.
xServomotor with 20 mA
feedback
nServomotors which are controlled via 4 – 20 mA and have a 4 – 20 mA position
feedback.
Table 24: Functions of the individual controllers
8.1 First steps
You need to make a number of basic settings before operating the device.
This section leads you through initial commissioning.
Precondition for action:
ü
The device has been installed in accordance with section 7 “Installa-
tion” on page12.
Configuration assistant
With initial commissioning, a configuration wizard will lead you through
the basic settings: Your preferred language, the measured values, con-
troller assignments and switch outputs. With the exception of the lan-
guage, the values configured here can only be set in the configuration as-
sistant. The finer settings are made in the sub-menus.
Working in the configuration assistant, determine the tasks of the in-
stalled modules, the controller and the output modules.
The finer settings such as the behaviour of these modules are made later,
e.g in the “Outputs” menu item.
Perform the following steps:
1. Set the preferred language and press on the arrow.
2. Measured values: Determine the desired measured value for the in-
stalled input modules. Press the right-hand arrow.
Controller: You can assign inputs for up to four controllers in this tab.
Select a sensor, a virtual input or a timer. Set the centre row of the
control function (Table 24: Functions of the individual controllers) and
press the right-hand arrow. Controllers 1 − 4 must be assigned to the
output modules 1 − 4 in a fixed fashion.
3. Control output: You can assign a function to outsput modules in this
tab. Only the output modules which are still free are displayed. Press
the right-hand arrow.
4. Confirm the security query with “Yes” to save the configuration.
ü
The configuration assistant has been ended.
i
Start the configuration assistant manually in System > Setup
> Configuration > “Configuration assistant”.

Commissioning
Configuration 19
© Lutz-Jesco GmbH 2019
Subject to technical changes.
190729
BA-46020-02-V01
Multi-Channel Controller TOPAX®MC Operating instructions
8.2 Configuration
The device is set up variably and can be individually adapted to meet your
requirements. As such, it is necessary to adjust the configuration of the
inputs and outputs to the sensors and actors used.
The following section leads you through the device configuration.
8.2.1 Inputs
You can connect up to four sensors for various water parameters and the
temperature to the device. You can also use eight digital inputs.
8.2.1.1 Sensors inputs
The sensors in the device must be configured individually to enable pre-
cise and error-free measurement of the water parameters. You can per-
form various settings.
Perform the following steps:
1. In the main menu, navigate from System > Inputs to the “Sensors”
tab.
2. In the “Sensors” tab, configure every connected sensor and state the
following information.
3. Input: Select the input module of the sensor which you wish to con-
figure.
4. Signal: Enter the type of the sensor signal. Depending on the input
module, the signal type has been specified or you can select a signal
type.
5. Value: Here, you can check which water parameters are measured.
This setting can only be changed in the configuration assistant.
6. Unit: Select the appropriate unit.
7. Measuring range: Enter the maximum measuring range of the sensor.
8. Min-alarm: Activate or deactivate the minimum alarm and state a
value under which the alarm will be triggered.
9. Max-alarm: Activate or deactivate the maximum alarm and state that
will trigger the alarm if itis exceeded.
10. Delay: Set a time delay for the minimum and maximum alarm.
ü
Configuration of the sensors completed.
8.2.1.2 Temperature input
You can connect up to four temperature sensors to the device. This ena-
bles you to measure the temperatures at various positions.
Perform the following steps:
1. In the main menu under System > Inputs, navigate to the “Tempera-
ture” tab.
2. In the “Temperature” tab, configure every connected temperature
sensor and state the following information.
3. Measurement: Chose between “On” and “Off”.
4. Min-alarm: Activate or deactivate the “Minimum-alarm” and enter a
temperature under which the alarm will be triggered.
5. Max-alarm: Activate or deactivate the “Maximum-alarm” and enter a
temperature to exceed which the alarm will be triggered.
ü
Configuration of the temperature sensors completed.
8.2.1.3 Compensation
The water parameters which you measure with the device can be falsi-
fied by interference (e.g. with temperature or pH value).
The device can compensate these interferences automatically.
Perform the following steps:
1. Working in the main menu under System > Inputs, navigate to the
“Compensation” tab.
2. Working in the “Compensation” tab, configure every sensor connect-
ed for which the measured value is to be compensated and state the
following information.
3. Temperature: If it is possible to compensate for the influence of the
temperature, you can select a fixed reference value or one of the four
temperature inputs.
4. pH value: If it is possible to compensate for the pH value error, you
can select a fixed reference value or a sensor input.
ü
Configuration of the compensation completed.
8.2.1.4 Disturbance variable
You can connect the measurement of a disturbance variable (e.g. a flow
volume) to an analogue 4 − 20 mA input. The disturbance variable can
then be taken into account with a factor (0.1 to 10) during the calculation
of the control variable Y. The control variable Y will be multiplied with the
disturbance variable during the calculation.
Example: If the factor = 2 and the disturbance variable amounts to 42%,
the controller can be set to a maximum of the control variable Y = 84 %. If
the factor = 0.5 and the disturbance variable amounts to 42%, the con-
troller can be set to a maximum of the control variable Y=21%.
Perform the following steps:
1. Working in the main menu under System > Controller, navigate to the
“Flow input” tab and state the following information.
2. Disturbance variable: Set the disturbance variable to an input signal
of 4–20mA or 0–20mA. You can also deactivate the disturbance
variable.
3. Unit: As a rule, the disturbance variable is the measurement of a flow.
Select the desired unit.
ü
Configuration of the disturbance variable input completed.

Commissioning
Configuration
20 © Lutz-Jesco GmbH 2019
BA-46020-02-V01
Multi-Channel Controller TOPAX®MC Operating instructions
8.2.1.5 Virtual inputs
You can calculate a new value from multiple measurements or reference
values using a virtual input. You can assign the new virtual value to a con-
troller in the configuration assistant.
In this way, you can calculate a difference, the combined chlorine and the
effective chlorine and use them as a basis for controlling your actors.
Difference
You can calculate the difference between two measured values or the dif-
ference between a measured value and a fixed reference value.
Perform the following steps:
1. Working in the main menu under System > Inputs, navigate to the
“Virtual” tab.
2. State the following information.
3. Calculation: Select “difference”.
4. Select a sensor.
5. Select a second sensor or a reference value. The second sensor must
output the same measured value as the first. You will need to enter
the reference value manually.
6. Min-alarm: Activate or deactivate the minimum alarm and state a dif-
ference value which, if it falls below a value, will trigger an alarm.
7. Max-alarm: Activate or deactivate the maximum alarm and state a
difference value which, if exceeded, will trigger an alarm.
8. Delay: Set a time delay for the minimum and maximum alarm.
ü
Configuration of the difference completed.
Combined chlorine
Combined chlorine is calculated from the difference between the total
chlorine and the free chlorine:
Combined chlorine = total chlorine - free chlorine
At least one total chlorine measurement is required to calculate com-
bined chlorine. The chlorine value can be entered manually as a single
reference value or a corresponding sensor input is selected.
Perform the following steps:
1. Working in the main menu under System > Inputs, navigate to the
“Virtual” tab.
2. Working in the “Virtual” tab, configure the desired calculation of the
combined chlorine and state the following information.
3. Calculation: Select “Combined chlorine” to calculate the combined
chlorine.
4. Total chlorine: Select the sensor which measures the total chlorine.
5. Free chlorine: Select the sensor which measures the free chlorine. If
no sensor is present, you can enter a reference value measured once
which can be used for the calculation.
6. Min-alarm: Activate or deactivate the minimum alarm and state a
value under which the alarm will be triggered.
7. Max-alarm: Activate or deactivate the maximum alarm and state a
value over which the alarm will be triggered.
8. Delay: Set a time delay for the minimum and maximum alarm.
ü
Configuration of the combined chlorine completed.
Effective chlorine
The disinfectant effect of the free chlorine is highly dependant on the pH
value of the process water. The pH value influences the reactivity of the
Chlorine ions. This relationship is underscored by the dissociation curve
(Fig. 19 “Dissociation curve of the effective chlorine” on page 20) of
the chlorine.
The actual disinfectant effect of the chlorine is generated by the hy-
pochlorous acid (HClO). The figure shows that the proportion of the HClO
is largest between pH 2 and pH 7.5. The disinfectant effect is very low
outside this pH value.
For photometric measurements the pH value of the sample is buffered to
approx. pH 6.5. As a result the measurement has a higher effective chlo-
rine content than is actually in the process water. For high pH-values sig-
nificant differences will therefore occur between the expected and actual
disinfection if assessed by photometric analysis. The calculation of the ef-
fective chlorine can be used to display the proportion of the hypochlorous
acid (HCIO), i.e. the proportion which contributes to the disinfectant effect.
100 %
50
10
5
1
0,5
0,1
1
0 2 4
�
I
6 8
\
\
\
\
\
\
\
10 12
+ +
+ +
14
(pH)
Fig. 19: Dissociation curve of the effective chlorine
Perform the following steps:
1. Working in the main menu under System > Inputs, navigate to the
“Virtual” tab.
2. Working in the “Virtual” tab, configure the desired calculation of the
effective chlorine and state the following information.
3. Calculation: Select “effective chlorine” to calculate the effective chlo-
rine.
4. Free chlorine: Select the sensor which measures the free chlorine.
5. pH value: Select the sensor which measures the pH value. If no sen-
sor is present, you can enter a reference value measured once which
can be used for the calculation.
Other manuals for TOPAX MC
1
Table of contents
Other Lutz-Jesco Controllers manuals
Popular Controllers manuals by other brands
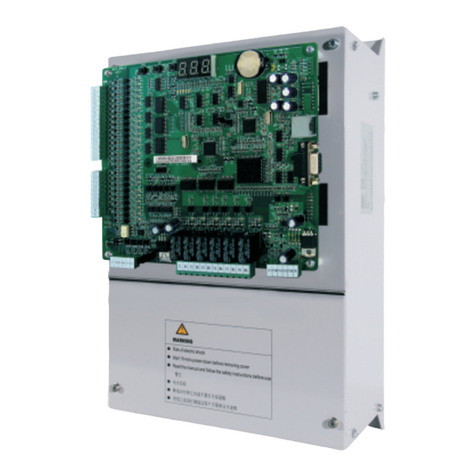
Suzhou MONARCH Control Technology Co., Ltd.
Suzhou MONARCH Control Technology Co., Ltd. NICE3000 New user manual
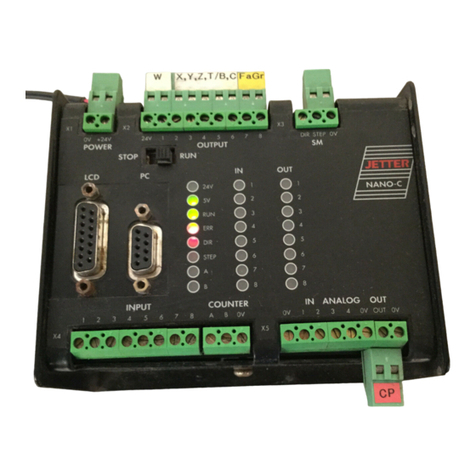
Jetter
Jetter NANO-C Version Update
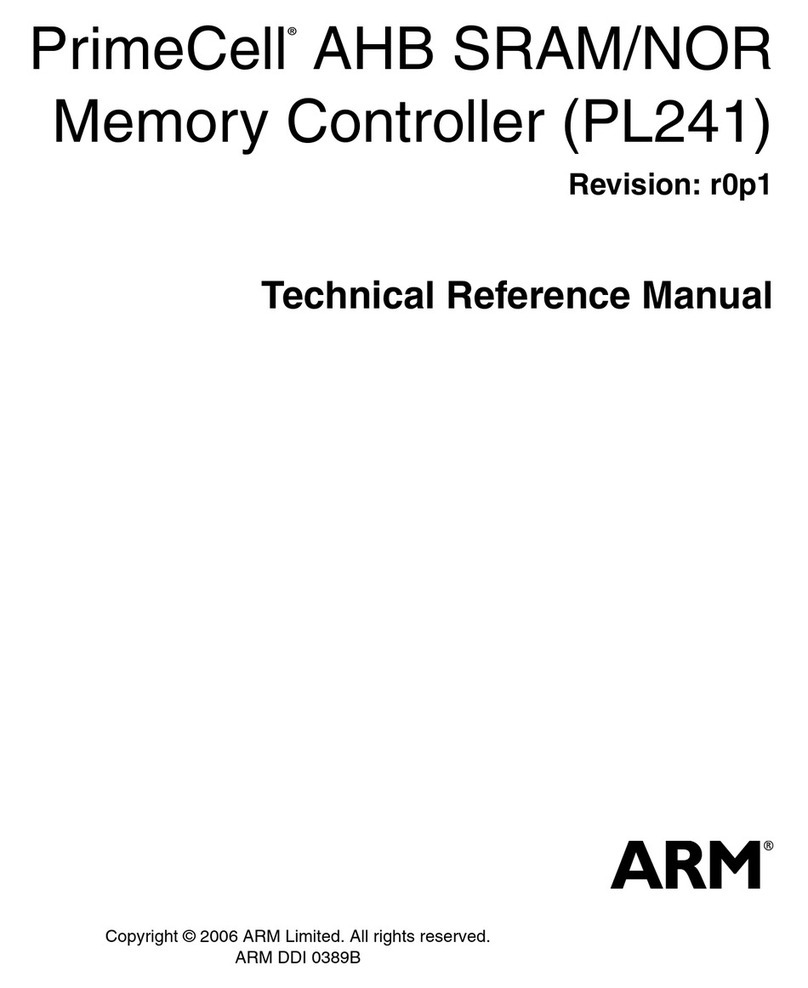
ARM
ARM PrimeCell PL241 Technical reference manual
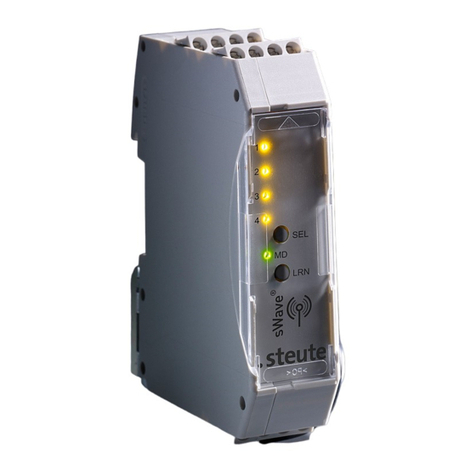
steute
steute RF Rx SW868-NET-4S-A Mounting and wiring instructions
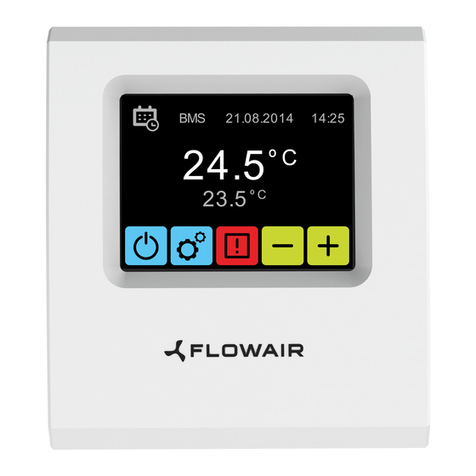
flowair
flowair T-box user manual
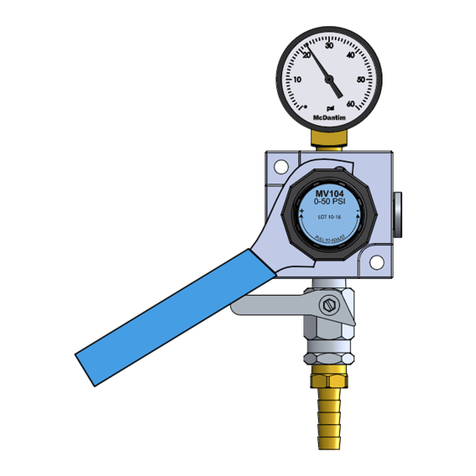
McDantim
McDantim Secondary TruRegs User's installation guide