Lutz MD1xL User manual

0698-401 MD1xL / MD2xL - 08/2020
Translation of the original instructions
COMPRESSED AIR MOTORS
Type
MD1xL
MD2xL
en
Read this operating instructions before start up!
To be retained for future reference.

2
0698-401 MD1xL / MD2xL - 08/2020
en
Table of Contents
1. Concerning this manual.................................................................................................................... 3
1.1 Terms.......................................................................................................................................... 3
1.2 Target groups ............................................................................................................................. 3
1.3 Associated applicable documents .............................................................................................. 3
1.4 Warnings and symbols............................................................................................................... 4
1.5 Latest state ................................................................................................................................. 4
1.6 Copyright .................................................................................................................................. 4
2. Safety ................................................................................................................................................ 5
2.1 General safety information......................................................................................................... 5
2.2 Proper use .................................................................................................................................. 7
2.3 Specicdanger........................................................................................................................... 8
2.4 Identication.............................................................................................................................. 9
3. Transport and storage....................................................................................................................... 9
3.1 Transport .................................................................................................................................. 9
3.2 Storage ....................................................................................................................................... 9
4. Starting up ...................................................................................................................................... 10
4.1 Compressed air connection...................................................................................................... 10
4.2 Assembly of pump tube to the motor....................................................................................... 11
5. Operation........................................................................................................................................ 12
5.1 Controlling compressed air motor MD1xL ............................................................................... 12
5.2 Controlling compressed air MD2xL .......................................................................................... 12
6. Maintenance and servicing............................................................................................................. 13
7. Repairs .......................................................................................................................................... 13
8. Disposal .......................................................................................................................................... 13
9. Instructions for the explosion protection........................................................................................ 14
9.1 ATEX-Identication ................................................................................................................... 14
9.2 Explosion protection regulations.............................................................................................. 14
9.3 Identiedignitionhazardsandtheimplementedprotectivemeasures .................................. 14
9.4 Equipotential bonding and earthing........................................................................................ 15
9.5 Classicationofzonesforexplosionhazardareas ................................................................... 16
9.6 Traceability ............................................................................................................................... 16
Annex .................................................................................................................................................. 17
Declaration of conformity..................................................................................................................... 19

3
0698-401 MD1xL / MD2xL - 08/2020
en
1. Concerning this manual
This manual
• is part of this product
• is valid for all mentioned series
• describes the safe and proper use in all operating stages
1.1 Terms
User: Single person or organisation who is using the products e.g. customer, user, assistant
Children:Young persons up to and including the age of 14 years.
1.2 Target groups
Target group Task
User ►Retain these operating instructions at the product’s place of use for
future reference.
►Demandthestatoreadandobservetheseinstructionsandthe
additional valid documents, in particular the safety information and
warnings.
►Observe additional regulations and instructions concerning the
plant.
Qualiedpersonnel,installer ►Read, observe and follow these instructions and the additional valid
documents, in particular the safety information and warnings.
Tab. 1: Target groups and their tasks
1.3 Associated applicable documents
Document Purpose
Operating instructions pump tube Safe and proper use of the pump tube
Supplementary operating instructions for additional delivered components
Tab. 2: Associated applicable documents and purpose

4
0698-401 MD1xL / MD2xL - 08/2020
en
1.4 Warnings and symbols
Warning Level of risk Consequences in case of
non-compliance
DANGER direct danger death or serious injury
WARNING possible direct danger death or serious injury
CAUTION possible dangerous situation light injury
NOTICE possible dangerous situation damage of property
Tab. 3: Warnings and consequences in case of non-compliance
Symbol Meaning
Safety information
►Comply with all measures that are marked with a safety sign to prevent injuries or
death.
iInformation / Recommendation
►What to do
→Cross reference
3Requirement
Tab. 4: Symbols and meaning
1.5 Latest state
Pleasendthelateststateofthisoperatinginstructionunderwww.lutz-pumpen.de.
1.6 Copyright
The content of this operating instruction and the images contained in them are subject to the copyright
protectionofLutzPumpenGmbH.

5
0698-401 MD1xL / MD2xL - 08/2020
en
2. Safety
The manufacturer will not be held responsible for any damages resulting from non-compliance of the
overall documentation, in particular for damages in case of non-compliance of the operating instructions.
2.1 General safety information
Observe following regulations before accomplishing all activities.
Product safety
The motor is constructed in conformity with the state of the art and approved safety-related standards.
Danger however can occur during use for life and health of the user or third parties or damage of the
motor and other material assets. Therefore:
• Operate the motor only in a technically sound state, for its proper use, and conscious of safety and
hazardstakingintoaccounttheseinstructions.
• Ensure that these instructions and all associated applicable documents are complete, legible, and stored
in a place that personnel can access at all times.
• Refrain from any manner of working that endangers personnel or uninvolved third parties.
• In the case of a safety-relevant malfunction, stop the motor immediately and enlist a responsible person
to rectify the malfunction.
• In addition to the overall documentation, observe the statutory or other safety and accident prevention
regulations, as well as the valid standards and guidelines of the respective operating country.
Modications
Unless the manufacturer has provided its consent in writing, the manufacturer is not liable for interventions
performedbytheuser(modications)ontheproduct,suchasconversion,alteration,newdesign,etc.
Modicationsnotagreedwiththemanufacturermayhavethefollowingeects,amongothers:
• Functional impairments on the appliance or plant
• Damage to the appliance and other property damage
• Environmental damage
• Personal injuries right through to death
Duties of the operator
Safety-conscious working
• Operate the motor only in a technically sound state, for its proper use, and conscious of safety and
hazardstakingintoaccounttheseinstructions.
• Ensure observance and monitoring of:
- Proper use
- Statutory or other safety and accident prevention regulations
- Safetyprovisionsinhandlinghazardoussubstances
- Valid standards and guidelines in the respective country of operation
• Provide protective equipment.

6
0698-401 MD1xL / MD2xL - 08/2020
en
Personnel qualication
• This device must not be used by children. It may be used by persons of reduced physical, sensory or
mental capacity or by persons lacking in experience or knowledge provided that they are supervised
orhavebeeninstructedinthesafeuseofthedeviceandunderstandtheassociatedhazards.Cleaning
or user maintenance must not be performed by children.
• Ensure that personnel tasked with work on the motor have read and understood these instructions and
all associated applicable documents, particularly safety, maintenance and servicing information, before
they start work.
• Clarify responsibilities, competencies and monitoring of the personnel.
• Ensurethatallworkiscarriedoutbytechnicalqualiedpersonnelonly:
- Assembly, servicing, maintenance work
- Work on the electrics
• Personnel to be trained must only work on the motor under the supervision of technical personnel.
• Personnel holding the motor in their hands during operation will be subjected to vibrations. The upper
limbs are exposed to an acceleration of less than 2.5 m/s².
Statutory warranty
• Duringtheguaranteeperiod,obtainthemanufacturer'spermissionformodications,maintenance
work or alteration.
• Use only original parts.
Duties of the personnel
• Observe the notices on the motor and maintain them in a legible state.
• Use protective equipment where necessary.
• Only perform work on the motor during downtime.
• Disconnect the motor from the compressed air during all assembly and maintenance work.
• Aftercompletingalltheworkonthemotor,remountthesafetydevicesinaccordancewithspecications.

7
0698-401 MD1xL / MD2xL - 08/2020
en
2.2 Proper use
A compressed air driven drum and container pump comprises motor and pump tube to suit the particular
application.ApplicationofthecompressedairmotorsMD1xLandMD2xLinexplosivehazardareasorfor
pumpingammableliquidsisonlyallowedincombinationwithapumptubeapprovedforcategory1/2G.
• Motor may only be operated with pump tube.
• The motor must not be immersed in the liquid being pumped.
• The motor can be used in the following environment:
- temporarilyoutdoorswithoutprotectionfromweathereects
- on roofed surfaces
- in open and closed rooms
- inexplosivehazardareas
• Observe following technical data:
Type MD1xL MD2xL
Power output 1000 W 1000 W
Max. operating pressure 6 bar 4) 6 bar 4)
Air consumption1) 1.5 Nm³/min 1.5 Nm³/min
Ambient temperature -20°C up to +60°C -20°C up to +60°C
ATEX-identication2) II 2G Ex h IIB T6 Gb II 2G Ex h IIB T6 Gb
II 2D Ex h IIIC T80°C Db II 2D Ex h IIIC T80°C Db
Sound pressure level3) <85dB(A) <85dB(A)
Sound power level <96dB(A) <96dB(A)
Weight 1.0 kg 1.4 kg
Order No. 0004-725 0004-735
1) In standard condition
2) Drum pumps are approved for explosion groups IIA and IIB and temperature class T4. Thus a result hereof, the
combinationmotor/pumptubeisalsoapprovedonlyformatters(liquidtobepumpedand/orenvironment)of
thisclassication.
3) Measured at 6 bar operating pressure with fully throttled pump tube
4) 5barforoperationinhazardousareasorwhenpumpingammableliquids.
If the product and supplied accessories are used for other purposes than the intended purpose, it is the
responsibilityoftheusertocheckthesuitabilityandadmissibility.Productusenotconrmedinwriting
by the manufacturer absolves the manufacturer of any liability.
The manufacturer is not liable for consequences of incorrect treatment, use, maintenance, servicing and
operation of the appliance, as well as normal wear and tear. The same applies if faults arise from inter-
ventionorcongurationsonthepartoftheusernotconrmedbythemanufacturer.

8
0698-401 MD1xL / MD2xL - 08/2020
en
Prevention of obvious misapplication (examples)
• Motor may only be operated with correctly mounted pump tube.
• Motormayonlybeusedinpermissibleexplosionhazardarea
• Use suitable compressed air supply
• Do not connect the compressed air supply while the engine is switched on
• Do not immerse the motor in the liquid being pumped
• Do not drive inadmissible devices with the motor
• Do not allow the motor to be operated by children or people in need of protection
• Do not use improper accessories
• Do not use improper or inadmissible spare parts
• Observe maintenance intervals
2.3 Specic danger
Explosion hazard area
!DANGER
Danger of explosion from use in an explosion hazard area!
Theclassicationofammableliquidsismadeaccordingtoregulation(EC)1272/2008(CLP).Whenpum-
pingammableliquids,theoperationalsafetyregulationandthefollowingpointshavetobeobserved:
Compressedairmotorsarenon-electricaloperatingappliancesnotrequiringocialapprovalwhenused
inzone1.
• ThecompressedairmotorscorrespondtotheATEX-directive(groupeII,category2forgasesanddust).
• ThemotorsarethereforesuitablefordrivingLutzdrum-andcontainerpumpsofcategory1/2.
• Application restrictions are depending on the respective pump tube (→operating instructions pump
tube).
• Onlyauthorizedformobileuse.
• Connect equipotential bonding (→chapter9).
• Use conductive pressure hoses only (→operatinginstructionspumptube).
• The pump motor must remain outside the drum or container.
• Operating pressure must not exceed 5 bar.
• The temperature of the compressed air supplied must not exceed the max. permissible ambient tem-
perature.
• Motor and pump tube operation must be controlled.
• Donotoperatethemotorwithammablegases.
• Prescribed inspection periods: Grooved ball bearing and vane, both have to be exchanged at latest after
1.000 operating hours.
• The presence of strong charge-generating processes, in particular the arrangement within transported
dust and within a distance of 1 m from high-voltage electrodes, must be excluded.
→Chapter 9: Instructions for the explosion protection

9
0698-401 MD1xL / MD2xL - 08/2020
en
2.4 Identication
Rating plate
1Type
2Serial number of the motor
3 ATEX-Identication
4 Yearofconstructionofthemotor(lasttwodigitsoftheserialnumbere.g.-18for2018)
5 CE-Identication
3. Transport and storage
3.1 Transport
Unpacking and checking condition of delivery
►Unpack the motor on receipt and check for transport damages.
►Report transport damages to the manufacturer immediately.
►Check that the consignment is complete as ordered.
3.2 Storage
►Storemotordry,protectedagainstweathereectsandUV-rays.

10
en
0698-401 MD1xL / MD2xL - 08/2020
4. Starting up
4.1 Compressed air connection
!WARNING
Danger of injury due to uncontrolled restarting of the motor!
►Switchingothemotorbeforeconnectingthecompressedair.
Fig. 1
Function and service life largely depend on the condition and pressure of the compressed air supplied.
Excessive moisture or dirt particles in the compressed air will destroy the motor. A high percentage of
condensateinthecompressedairwillcauseaslightrustdepositinthemotorandtheairoutletmuer
will get covered by ice during air expansion.
Therefore, when starting the compressed air motor, observe the following items (→Fig.1):
• Before connecting the motor to the compressed air supply, clean the compressed air line and the hose
by blowing out with low pressure to remove any dirt particles from the line. Wear safety goggles, hold
thelinetightanddonotstandintheareaoftheairow.
• Mainairlines(6)requireaslightinclinationofatleast1%inthedirectionofowsothatcondensation
watermaybedrainedthroughavalve(7)atthelowestpoint(manuallyorautomatically).
• Branchpipesshouldbeconnectedpointingupwards(5)inthecaseofahorizontalmainline(6)-and
inthecaseofaverticalmainline(4)notatthelowestpoint.Thus,anycondensationwatercollectedin
themainlinewillbepreventedfromowingintothebranch.
• Usemaintenanceunits(3)consistingofairlterandoiler.TheoilerisnotnecessaryformotorsMD1xL
andMD2xL,butisrecommendedforlongerservicelife.Themotorpoweris10-20%lowerwithnon
lubricated air than with lubricated air.

11
en
0698-401 MD1xL / MD2xL - 08/2020
• Install the maintenance unit with an air connection of at least G 1/4 in the immediate vicinity of the
compressedairmotor(1).Usearesin-freeandacid-freemineraloilwithaviscosityof20to30mm²/s
intheoiler(3).Theoilconsumptionshouldbe1dropperminuteasaminimum.
• Theairlter(3)requiresregularmaintenanceduringwhichthetrappedcondensationwaterisdrained
andthelteriscleaned.
• Thecompressedairmotorwillachievemaximumperformanceat6bar(87psi).Thepressureinthe
pneumaticsystemexceeding6bar,apressureregulator(3)mustbeinstalled.Adjustmentofthepressure
regulator(3)mustbeeectedwiththemotorrunning.
• Installanairhose(2)of13mminsidediameterbetweenmaintenanceunitandcompressedairmotor
tominimizethepressurelosses.
• Use a stop valve in the pressure line in order to connect and disconnect the motor without pressure.
• Note the resulting pressure loss when using quick-action couplings.
Recommendation for compressed air supply
• TheclassicationofthecompressedairqualitycanbetakenfromISO8573-1:2010.
• Standard values of compressed air quality are e.g. to be found in VDMA 15390-1: 2014-12.
• For lubricated air, a minimum compressed air quality by ISO 8573-1: 2010 [-: 4: 4] is recommended.
• For non lubricated air, a minimum compressed air quality by ISO 8573-1: 2010 [6 3: 3] is recommended.
• Excessivewatercontentinthecompressedaircancausefreezingofthewaterparticles.Thismaybethe
causefordamagingthevanesorcloggingthemuer,whichmayaecttheperformanceofthemotor.
4.2 Assembly of pump tube to the motor
3Motorisswitchedo
►Connect the motor with the pump tube.
►Turn the motor slightly to ensure that the driver (→Fig.2,Item1)
engages in the coupling (→Fig.2,Item2).
►Firmly connect the motor and pump tube by means of the
handwheel(right-handthread)(→Fig.2).
Fig. 2

12
en
0698-401 MD1xL / MD2xL - 08/2020
5. Operation
!WARNING
Danger of rolling-up and pulling-in of objects!
►Do not put any objects in the opening for the coupling control
(→Fig.4).
►Donotworkonthemotorwiththinandloose-ttinggloves.
!WARNING
Danger of injury due to uncontrolled restarting of the motor!
►The pump must not be left unattended while in operation.
►Ifthepowersupplyfails,themotormustbeswitchedo.
5.1 Controlling compressed air motor MD1xL
►Forswitching-on/othemotor,insertacheckvalveinthecom-
pressedairline(e.g.ballvalvefromLutzaccessories).
5.2 Controlling compressed air MD2xL
►On: Moveswitchfromtheo-position(→Fig.5,item1)tothe
required speed (→Fig.5,item2).
O: TurnbacktheswitchtoO-position.
Fig. 4
Fig. 5

13
en
0698-401 MD1xL / MD2xL - 08/2020
6. Maintenance and servicing
If the compressed air motor is missing the required power, check the following points:
Fault Cause Remedy
Airpressurenotsucient
(6bar/87psi)
• Compressed air line is leaky
• Pressure losses
• Seal or replace the compressed
air line
• Enlarge the cross-section of the
compressed air line
Airpressureuctuating • Compressed air line is leaky
•Compressedairline,mueror
airlterblocked
• Error during generation of
compressed air
• Seal or replace the compressed
air line
• Clean compressed air line,
muerorairlter
• Check air compressor
Airlteronmaintenanceunit
is dirty or blocked
• Impurities in compressed air •Cleaningtheairlter
Lack of oil in the compressed
air system
• Oiler impure or damaged • Clean, repair or replace oiler
Muerblocked • Impurities in compressed air
• Dust in the environment
•Cleanmuer
If none of the above defects is detected, the compressed air motor must be repaired.
7. Repairs
►RepairsshouldonlybemadebythemanufacturerorauthorizedLutzdealers.
►OnlyuseoriginalLutzPumpenspareparts.Ifothersparepartsareused,liabilityonthepartofLutz
Pumpen is obsolete.
8. Disposal
Dispose of the motor according to the locally applicable regulations.

14
en
0698-401 MD1xL / MD2xL - 08/2020
9. Instructions for the explosion protection
9.1 ATEX-Identication
II 2G Ex h IIB T6 Gb
II 2D Ex h IIIC T80°C Db
9.2 Explosion protection regulations
►Following standards were used for the compressed air motors:
- EN 1127-1:2011 Explosive atmospheres — Explosion prevention and protection — Part 1: Basic
concepts and methodology
- EN ISO 80079-36:2016 Explosive atmospheres — Part 36: Non-electrical equipment for explosive
atmospheres — Basic method and requirements
- EN ISO 80079-37:2016 Explosive atmospheres — Part 37: Non-electrical equipment for explosive
atmospheres — Non- electrical type of protection constructional safety ‘'c’', control of ignition sources
‘'b’', liquid immersion ‘'k’'
►FollowingregulationshavetobeobservedfortheuseofequipmentinhazardousareaswithintheEU:
- DIRECTIVE 1999/92/EC on minimum requirements for improving the safety and health protection of
workers potentially at risk from explosive atmospheres
- Regulation(EC)1272/2008(CLP)
►National rules and regulations have to be observed.
9.3 Identied ignition hazards and the implemented protective measu-
res
Identied ignition hazard Implemented protective measures
Hotsurface Cooling by adiabatic expansion of the compressed air
Heatdissipationmateriallygiven
Preventingheatingofthebearingsduetospeciedreplacement
interval
Mechanically generated sparks Use of suitable materials
Discharge of static electricity Connecting the conductive housing parts to the equipotential
bonding
Constructive limitation of the electrostatic charge in plastic parts

15
en
0698-401 MD1xL / MD2xL - 08/2020
9.4 Equipotential bonding and earthing
►Before starting up, an equipotential bonding must be established between the pump, the container
tobeemptiedandthecontainertobelled(→Fig.6).
►Clamptheequipotentialbondingcable(orderno.0204-994)tocreateanequipotentialbondingbetween
the pump and the container to be emptied. For better conductivity, remove the paint and dirt from the
clamping points.
►Equipotentialbondbetweenthecontainerstobeemptiedandtobelledviaaconductivesubstrate
(e.g.aconductivegrating).
►Ensure that a conductive transition between container and earthing potential is available.
Fig. 6
Legend:
(1)Equipotentialbondingcable,(3)conductivehose,(4)conductiveconnectionfromhosetohose
connector,(5)pumptubeforzone0,(6)explosion-proofcompressedairmotorforzone1,(7)nozzle,
(8)maintenanceunit,(9)earthpotential

16
en
0698-401 MD1xL / MD2xL - 08/2020
9.5 Classication of zones for explosion hazard areas
Explosionhazardareasaredenedasareasinwhichexplosiveatmospheresmayoccurinpotentially
dangerous volumes on account of local and operational conditions.
Areasinwhichexplosionsmayoccuronaccountofammablegases,vapoursormists,followingclassi-
cationofzonesisapplied:
Zone 0 Dangerous explosive atmosphere persists constantly or for a long time.
Zone 1 Dangerous explosive atmosphere persists occasionally.
Zone2Dangerousexplosiveatmospherepersistsrarelyandbriey.
Explanation of the zone classication when using drum pumps for ammable liquids
• Inside the drum or container. Zone 0
• Bungholeofthedrumortheupperedgeofthecontainer:Boundarybetweenzone0andzone1
• Rooms in which media are transferred from one drum or container to another: Zone 1
The result for drum and container pumps is:
►OnlypumptubesofunitgroupII,category1/2Gmaybeusedtopumpammableliquids.
►Regardlessoftheirtypeofprotection,motorsmaynotbeusedinzone0.
►MotorsofunitgroupII,category2Gmaybeusedinzone1.
9.6 Traceability
Productsforpotentiallyexplosiveatmospheresareidentiedbyanindividualserialnumber.
LutzPumpenensuresthetraceabilityofthisdeviceuptotheinitialpointofdeliveryaccordingtoATEX
Directive.
All persons who redeliver the device are obliged to guarantee its traceability to enable subsequent recall
actions.

17
en
0698-401 MD1xL / MD2xL - 08/2020
Annex
Purity classes of the compressed air according to ISO 8573-1:2010
Class Particles per m² Moisture content and
water Complete oil [10]
0.1..–0,5μm
[1.6, 9]
0.5..–1μm
[1.6, 9]
1..–5μm
[1.6, 9]
0Accordingtodenition
and better than class 1
Accordingtodenition
and better than class 1
Accordingtodeni-
tion and better than
class 1
1≤20.000 ≤400 ≤10 ≤-70°C
[2,5]
≤0,01 mg/m³ [1,3]
2≤400.000 ≤6.000 ≤100 ≤-40°C ≤0,1 mg/m³
3 --- ≤90.000 ≤1.000 ≤-20°C ≤1 mg/m³ [1,4]
4 --- --- ≤10.000 ≤+3°C ≤5 mg/m³
5 --- --- ≤100.000 ≤+7°C
6≤5 mg/m³ [1,7] ≤+10°C
75 – 10 mg/
m³
[1,7] ≤0,5 g/m³
[1,8]
80.5.. – 5 g/
m³
95.. – 10 g/m³
X > 10 mg/m³ [1,7] > 10 g/m³ > 5 mg/m³ [1,4]
[1] –referenceconditions1bar(a)and20°Cat0%relativehumidity
[2] –unless otherwise agreed or stated, reference conditions 7 bar and 20°C
[3] –measured according to ISO 8573-2 and ISO 8573-5
[4] –measured according to ISO 8573-2 ; measurement according to ISO 8573-5 optional
[5] –measured according to ISO 8573-3 and, if required, ISO 8573-9
[6] –measured according to ISO 8573-4
[7] –measured according to ISO 8573-8
[8] –measured according to ISO 8573-9
[9] –if particles greater than 5 µm have been measured, class 0-5 cannot be applied
[10] –liquid, aerosol and vapour oil content

18
en
0698-401 MD1xL / MD2xL - 08/2020

Translation of the original declaration of conformity
We herewith declare under the sole responsibility that the following product complies with
the EU Directives listed.
Manufacturer: Lutz Pumpen GmbH
Erlenstraße 5-7
D-97877 Wertheim
Product: Compressed air motor
Types: MD1xL
MD2xL
Relevant European Directives: ATEX 2014/34/EU
Machinery Directive 2006/42/EC
Applicable harmonised standards: EN ISO 12100:2010
EN ISO 80079-36:2016
EN ISO 80079-37:2016
The notied body Physikalisch-Technische Bundesanstalt 0102, Bundesallee 100,
38116 Braunschweig, is keeping the technical documentation referred to in ATEX-Directive
annex VIII, point 2 under the registration number PTB 03 ATEX D039.
Marking: II 2G Ex h IIB T6 Gb / II 2D Ex h IIIC T80°C Db
Person authorised to compile the technical le:
Lutz Pumpen GmbH
Erlenstraße 5-7
D-97877 Wertheim
Wertheim, 27.06.2018
Heinz Lutz, CEO

Lutz Pumpen GmbH
Erlenstraße 5-7
D-97877 Wertheim
Tel. (+499342)879-0
Fax (+499342)879404
e-mail:[email protected]
http://www.lutz-pumpen.de
Subject to technical changes. 08/2020 Order No. 0698-401 Printed in Germany / Dru.
This manual suits for next models
3
Table of contents
Other Lutz Engine manuals
Popular Engine manuals by other brands

DentalEZ
DentalEZ StarDental Titan-E instruction manual
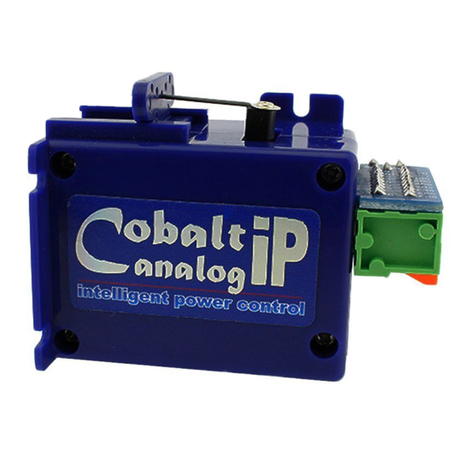
DCCconcepts
DCCconcepts Cobalt IP Analog owner's manual
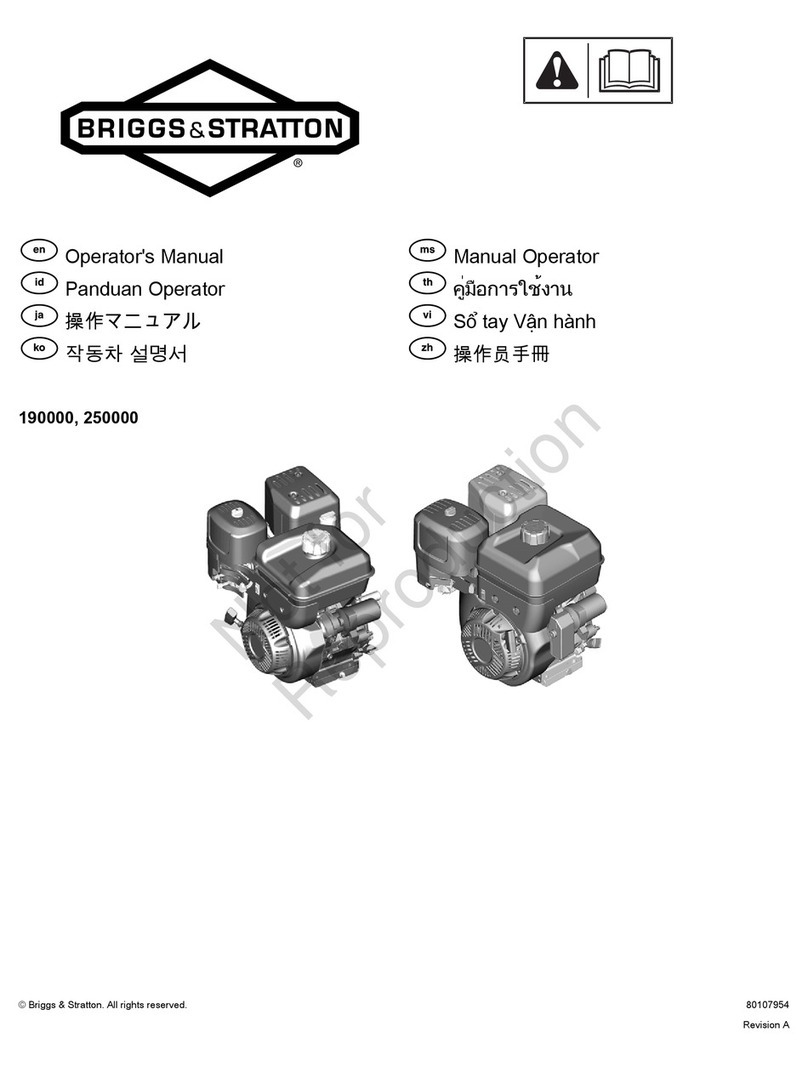
Briggs & Stratton
Briggs & Stratton 250000 Series Operator's manual

Universal Motors
Universal Motors M-12 owner's manual
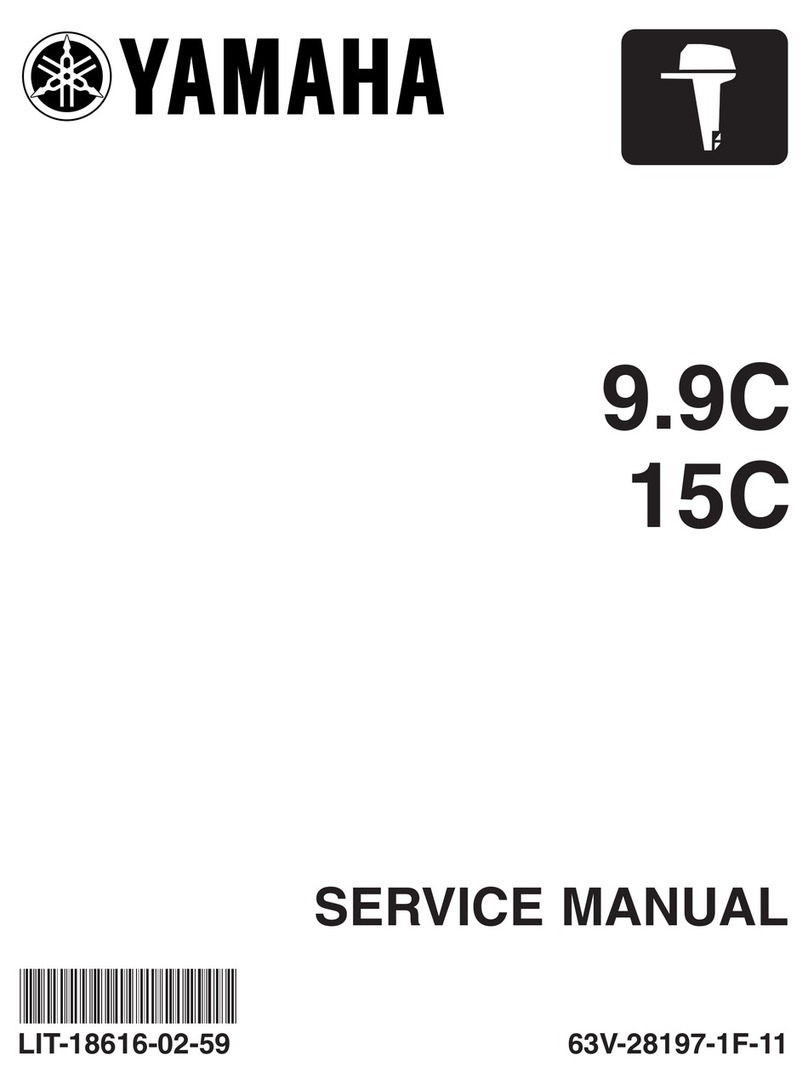
Yamaha
Yamaha 9.9C Service manual
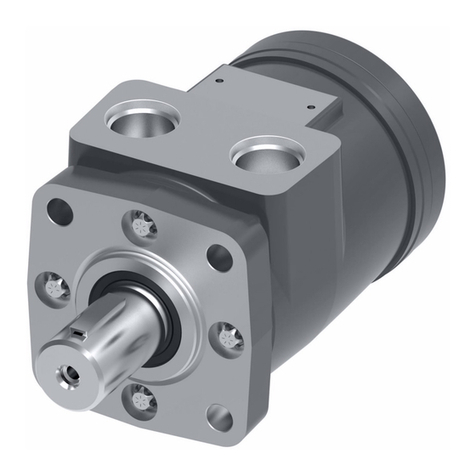
Eaton
Eaton Char-Lynn Parts and repair manual