M2 MT-3000A User manual

SPECIFICATIONS
MODEL NUMBER.....................................................MT-3000A (Elevation Positioner)
ROTATING TORQUE...............................................4500 Inch lbs. (at slowest speed)
GEAR RATIO............................................................19200:1
ROTATION SPEED / 0-90 DEGREES.....................35 Seconds (Speed Controlled)
ROTATION RANGE..................................................0-180 Degrees
READOUT RESOLUTION........................................0.1 Degrees
TRAVEL ACCURACY...............................................+/- .5 Degrees
INPUT VOLTAGE.....................................................28-42 VDC
DIMENSIONS...........................................................W=30” / H=12” / D=30”
FINISH ......................................................................Gold Zinc
CABLE REQUIREMENTS........................................(2) #16AWG, (2) #22AWG Shilded
WEIGHT ...................................................................97 lbs.
M2 Antenna Systems, Inc. 4402 N. Selland Ave. Fresno, CA 93722
Tel: (559) 432-8873 Fax: (559) 432-3059 Web: www.m2inc.com
©2015 M2 Antenna Systems Incoporated 11/17/11
Rev.02
M2 Antenna Systems, Inc.
Model No: MT-3000A

2
MT-3000A PRE ASSEMBLY NOTES
LENGTH OF CABLE TERMINAL 1 & 2 MINIMUM AWG TERMINAL 5 & 6 MINIMUM AWG
125 FEET #18 AWG #22-24 AWG
125-200 FEET #16 AWG #22-24 AWG
200-300 FEET #14 AWG #22-24 AWG
300-450 FEET #12 AWG #22-24 AWG
FOR A SUCCESSFUL INSTALLATION THERE ARE SIX POINTS THAT MUST BE
CONSIDERED BEFORE ASSEMBLING THE MT-3000AEL.
1.The MT-3000AEL can accommodate main boom diameters of 3” to 5”. If your crossboom is
smaller or larger, the mounting plates may need hole pattern modification. If you plan to use a
tower section as a crossboom, M2 has tower adapter plates available. Call us at 559 432 8873 to
discuss your special needs.
2. Multi conductor cable is needed to supply motor voltage / current and provide position feed-
back information. M2 can supply the required cable or you can purchase the ideal cable from The
Wireman. The ideal cable contains two #12 AWG wires ti power the 28 volt DC motor and two
#22 AWG shielded wires to return the square wave position information to the controller.
3. Tower and mast requirements vary with the size of the array and the environment. Generally,
towers like Rohn 25 or larger are adequate using mast sizes of 2 inch minimum.
4. Mast quality is crucial for large arrays. Do not use 1-1/2” water pipe (1-7/8” O.D.) as it is too
soft. For small 4 Yagi arrays 2: x .180 wall steel tubing is recommended. Tube steel should
meet ASTM 512, 513, or 519 specifications or equivalent. Simply stated steell with a psi rating
over 50,000 PSI ( Pounds per square inch) is required. M2 can supply your mast if no local steel
supply exists in your area.
5. Unless you need a tall mast for other antenna in your system, we recommend that the
MT3000AEL is mounted with no more than 1/2” of mast protruding above the mounting plate. This
will allow the system to rotate the full 180 degrees which aids during assembly and maintenance.
We recommend that no more than 2 feet of mast extend beyond the top of the tower. 3 to 5 feet
of mast inside the tower is adequate. We also recommend a top bearing and a secondary bear-
ing inside the tower above the rotator.
6. The azimuth rotator is also very important in a good installation. Our OR2800PXEL azimuth
rotator is totally compatible with the MT-3000AEL elevation rotator control box and the two control
units link together so only one RS232 cable is required if you use computer control for tracking.
Prop Pitch motors are also good for azimuth rotation and can be controlled using an M2 controller
that is similar to the OR2800 controller but with higher current transformer and motor control cir-
cuitry. Again this PP controller is compatible with the MT-3000AEL controller.
Other possible rotators that could be adequate for you array are:
HDR-300
Tailtwister (T2X)
Ham IV

3
MT-3000A PRE-INSTALLATION ASSEMBLY
All installations are unique in some way, which means it's OK to preassemble certain hardware, or rear-
range the assembly process to meet specific site requirements. A quick review of the assembly notes
and drawings should help firm up the appropriate strategy. Please remember to double-check all hard-
ware for tightness BEFORE it becomes inaccessible.
PRE-INSTALLATION TIPS AND CONSIDERATIONS:
The MT-3000AEL gear box is shipped dry without oil, see the gear box motor detail for filling instructions. The For
best results, test and calibrate the MT-3000AEL (positioner, cable, and control unit) on a work bench or tem-
porary foundation. This will familiarize you with the components and controls, their proper function, and allow test-
ing of the terminal wiring and connection. Upon completion, the positioner can be run to a known compass or land-

4
MT-3000A & AXIS ASSEMBLY DETAIL
NOTE:
IF YOU PURCHASED & ARE INSTALLING THE OPTIONAL LIMIT SWITCH KIT.
LIMIT SWICTH PARTS MUST BE INSTALLED DURING THIS PROCEDURE.
REFER TO LIMIT SWITCH KIT PAGES BEFORE ASSEMBLING PARTS & HARDWARES
SHOWN BELOW.

5
DRIVE SPROCKET & AXIS BEARING DETAIL

6
LEVELING BAR ASSEMBLY
The leveling bar is mainly an installation tool to help keep mounting pads parallel during main
cross boom installation.
Depending on your installation, topography & H-Frame type, your leveling bar can be installed in
many configurations. The leveling bar can be removed after installation or left in place as long
as it does not limit your system travel.
SHOWN AT 0.0° ON
THE HORIZON
FRONT OF
ARRAY

7
MT-3000A CHAIN INSTALLATION
4
1 1. Install Master Link to chain and Chain
Anchor.
Note: For installation ease keep bolts on
chain achors loose. Untill chain as been
routed thru sprokets and secured on
other end of D-Ring.
2
2. Route chain thru sprokets as shown on
picture #2.
4. Make sure and tighten bolts on Chain
Anchors. See next page for chain & idler
adjustment details.
CHAIN
ANCHOR
MASTER LINK #40
3
3. Use Master Link to secure chain to Chain
Anchor on other end of D-Ring.
CHAIN
ANCHOR
MASTER
LINK
#40

8
CHAIN & IDLER SPROCKET ADJUSTMENT
Excessive chain slop or play may develop after using system for some time. We have incorporated
in a chain adjustment to keep chain slop or play at a minimum.
Please review drawings shown for more detailed information.
To adjust system:
1. Remove the chain cover (Cover not shown on picture above). Position your array where it might
be slightly out of balance so to allow the chain slop to gather between the adjustment idler sprocket
and the large drive sprocket. Loosen the 1/2-13 x Locking nut on the adjustment sprocket slightly.
2. Use a 9/16” socket wrench to turn adjustment bolt.
3. Clockwise rotation of the adjustment bolt will tighten the chain. Adjust the chain to 1/8” of slop or
play. Over tighting the chain can put excessive tension on the idlers and gear box drive shaft.
4. Counter clockwise rotation of the adjustment bolt will loosen the chain.
Note: Over tighting the chain can put excessive tension on the idlers and gear box drive
shaft. A loose chain can allow elevation axis system movement
5.Tighten locking bolts and nuts testsystem. Look for consistent chain tension throughout your sys-
tem movement.
6. After test tighten all hardware and replace cover.
DRIVE
SPROCKET
ADJUSTMENT
IDLER SPROCKET
ADJUSTMENT
BOLT

9
GEAR BOX MOTOR DETAIL
The New MT-3000AEL has been outfitted with a high performance high efficiency gear box
using all roller bearings and gear oil. The gear box has been assembled with a light coat of lubricat-
ing oil. No load testing can be performed during ground set up and test before gear box is filled with
oil. Gear oil should be installed before final installation. SAE 80/90 WT oil has been provided. In nor-
mal operation the motor shaft is only subject to oil splash, a splash seal has been installed for nor-
mal operation. Some oil seepage can occur if the motor is stored incorrectly. See drawing below
for storage position. Be sure to drain oil before storage or shipping.
Filling instructions
Remove oil fill level screw with washer and oil fill plug. Use SAE 80/90 WT oil & fill gear box to oil
level line using the open oil fill level screw hole as a visual guide. Immediately re-insert oil fill level
washer & screw & oil fill plug. Wipe any excess oil.

10
LSK-3000 LIMIT SWITCH KIT
NOTE:
LIMIT PLATE MUST BE INSTALLED TO BEARING ADJUSTMENT BODY PLATE WITH; BOLT, 1/4-20
X 1/2” (QTY. 2) BEFORE IT BECOMES UN-ACCSESIBLE. WHEN INSTALLING
BEARING / ADJUSTMENT BODY PLATE TO AXIS ASSEMBLY.
(SEE PHOTOS FOR MORE INFORMATION)
LIMIT STOP BLOCK
BOLT, 1/4-20 X 1-3/4”,SS
LOCKNUT, 1/4-20,SS
D-RING SPROCKET

11
LSK-3000 LIMIT SWITCH KIT
NOTE:
INSTALL LIMIT SWITCH BOX TO MOTOR. ROUTE CABLES AS SHOWN BELOW & REFER
TO LIMIT SWITCH BOX PICTURE FOR WIRING DETAILS. INSTALL LIMIT SWITCH BOX
COVER WITH SCREWS SUPPLIED WITH COVER.
LIMIT SWITCH BOX WIRING DETAIL
BLACK or MTR CCW/DWN
WHITE or MTR CW/UP
ORANGE or Reed Switch DC+
BLUE or Reed Switch Return
DWN LIMIT UP LIMIT
DWN Limit - Black Wire
DWN Limit - White Wire
UP Limit - White Wire
UP Limit - Black Wire

12
MT-3000A PARTS & HARDWARE
DESCRIPTION QTY
Axis Assembly (welded)............................................................................... 1
Mast Mount Plate......................................................................................... 1
“T” Plate, Coast Side (welded)..................................................................... 1
“T” Plate, Drive Side .................................................................................... 1
D-Ring Sprocket .......................................................................................... 1
Leveling Bar Assembly................................................................................ 1
MT-3000AEL, Elevation 1200:1 Gear Box & Motor ..................................... 1
Axis Bearing Housing .................................................................................. 2
Axis Bearing, 1.0 x 2.0 (bcg1641dctntg18).................................................. 2
Bearing / Adjustment Body.......................................................................... 1
Drive Shaft Bearing (bcgr122rs) .................................................................. 1
Adjustment Screw assembly........................................................................ 1
Sprocket Guide Block.................................................................................. 1
Sprocket Guide Pad (delrin) ........................................................................ 2
Idler Sprocket, #40 15 tooth (bcgm41e15)................................................... 2
Idler Spacer................................................................................................. 1
Drive Gear #40 10 tooth (bcgm40b1034) .................................................... 1
Key Stock 3/16 x 1.0 ss............................................................................... 1
Roller Chain, #40 x 56.750 END TO END................................................... 1
Chain Anchor............................................................................................... 2
Master Link #40........................................................................................... 2
HARDWARE
Bolt, 1/2-13 x 5 1/2”, Hex Hd, ss.................................................................. 3
Bolt, 1/2-13 x 4” (Tap Bolt) ss...................................................................... 2
Bolt, 1/2-13 x 3/4”, Hex Hd, ss..................................................................... 2
Washer, Flat 1/2 x 2” OD ss (HWS05000305)............................................. 2
Washer, Flat 1/2”, ss.................................................................................... 6
Washer, Locking 1/2”, ss............................................................................. 4
Nut, 1/2-13 ss.............................................................................................. 2
Nut, Locking 1/2-13...................................................................................... 5
Bolt, 3/8-16 x 1”, Hex Hd, ss........................................................................ 4
Nut, Locking 3/8-16 ss................................................................................. 4
Bolt, Flat Head 5/16-18 x 1-3/4” ss.............................................................. 4
Bolt, Flat Head 5/16-18 x 1-1/2” ss.............................................................. 4
Nut, Locking 5/16-18, ss.............................................................................. 8
Bolt, 1/4-20 x 1-3/4”, ss................................................................................ 2
Bolt, 1/4-20 x 1-1/2”, ss................................................................................ 1

13
DESCRIPTION QTY
Bolt, 1/4-20 x 1”, Hex Hd, ss........................................................................ 4
Nut, Locking 1/4-20, ss................................................................................ 5
Screw, Allen Head cap 10-32 x 1-1/8”, ss.................................................... 4
U-Bolt and Cradle 4”.................................................................................... 4
U-Bolt and Cradle 3”.................................................................................... 4
U-Bolt and Cradle 2” HD..............................................................................4
Nut, 3/8-16,ss .............................................................................................. 16
Washer, locking 3/8”, ss .............................................................................. 16
Allen Wrench, 3/16 ...................................................................................... 1
Allen Wrench, 5/32 ...................................................................................... 1
Allen Wrench,1/8 ......................................................................................... 1
OPTIONAL LIMIT SWITCH KIT (LSK-3000)
Limit Switch Junction Box / Mounting Hardware.......................................... 1
Limit Switch Plate ........................................................................................ 1
Limit Switch Spacer ..................................................................................... 1
Limit Switch w/ 36” wire (eswe1117x2)........................................................ 2
Limit Stop..................................................................................................... 2
Bolt, 1/4-20 x 1 3/4”, Hex Hd, ss.................................................................. 2
Bolt, 1/4-20 x 1/2”, Hex Hd, ss..................................................................... 2
Screw, 8-32 x 5/8”, Hex Hd, ss.................................................................... 2
Screw, 10-32 x 1-1/4”, Ph Phl, ss ................................................................ 2
Screw, 10-32 x 3/8”, Ph Phl, ss.................................................................... 2
Flat Washer, #10 ss..................................................................................... 4
Locking Washer, #10 ss .............................................................................. 4
Carefully manufactured by:
M2ANTENNA SYSTEMS, INC.
4402 N. Selland Ave.
Fresno, CA 93722
(559) 432-8873 Fax: 432-3059
www.m2inc.com Email: [email protected]
MT-3000A PARTS & HARDWARE

14
12 MONTH LIMITED WARRANTY
This warranty gives you specific legal rights. You may also have other rights which will vary from state to state
or province to province.
M2 warrants the MT-3000AEL Positioner unit against defects in material and workmanship for a period
of 12 months from date of purchase. During the warranty period, M2 will, at its option, either repair or
replace products or components which prove to be defective. The warranty shall not apply to defects or dam-
age resulting from:
Improper or inadequate maintenance by user
Improperly prepared installation site
Unauthorized modifications or misuse
Accident, abuse, or misapplication
Normal wear
M2 specifically does not warrant this product for any direct, indirect, consequential, or inci-
dental damages arising form the use or inability to use the product. Some states or provinces do not allow the
exclusion or limitation of liability for consequential or incidental damages so the above limitation may not apply.
In the event repair or replacement are necessary, purchaser shall contact M2 for return authoriza-
tion. In many cases this contact can simplify and expedite the repair / replacement process and help reduce
costs and downtime.
The purchaser shall be responsible for packing the product properly for return and for charges to ship
the product to M2. Always include with the shipment, a statement detailing the problem / failure and any other
pertinent observations. Insuring the product for shipment is recommended. Use the original packing materials
whenever possible. M2 is responsible for charges (in the United States) to return the repaired / replacement
product only where warranty service is involved.
M2 Antenna Systems, Inc. 4402 N. Selland Ave. Fresno, CA 93722
(559) 432-8873 Fax (559) 432-3059 Web: www.m2inc.com
Table of contents
Popular Controllers manuals by other brands
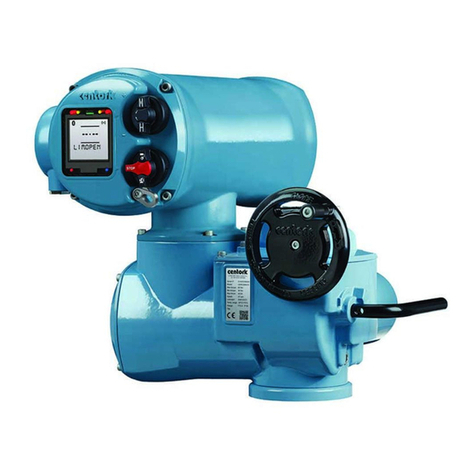
rotork
rotork centork CK Series Startup guide
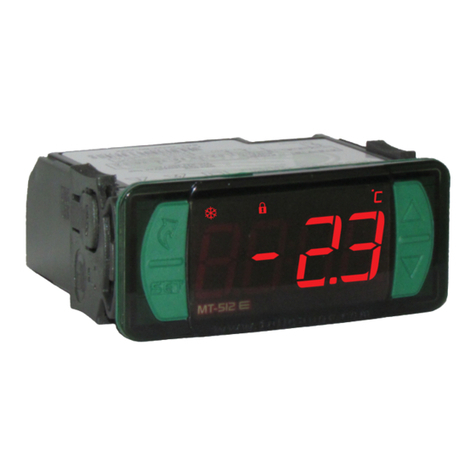
Full Gauge Controls
Full Gauge Controls MT-512 E 2HP quick start guide
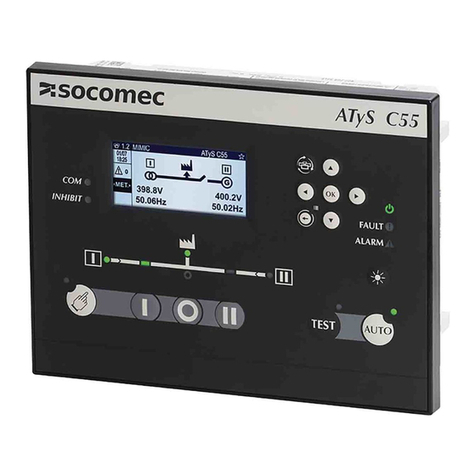
socomec
socomec ATyS C55 Installation and operating manual
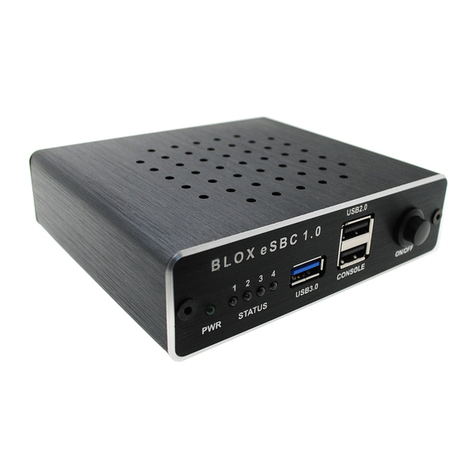
ALLO
ALLO BLOX ESBC Quick installation guide
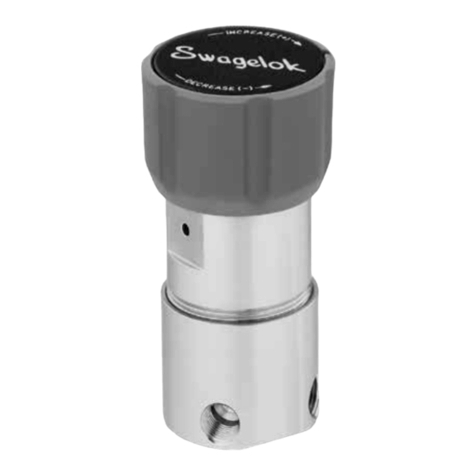
Swagelok
Swagelok KCP Series Maintenance instructions
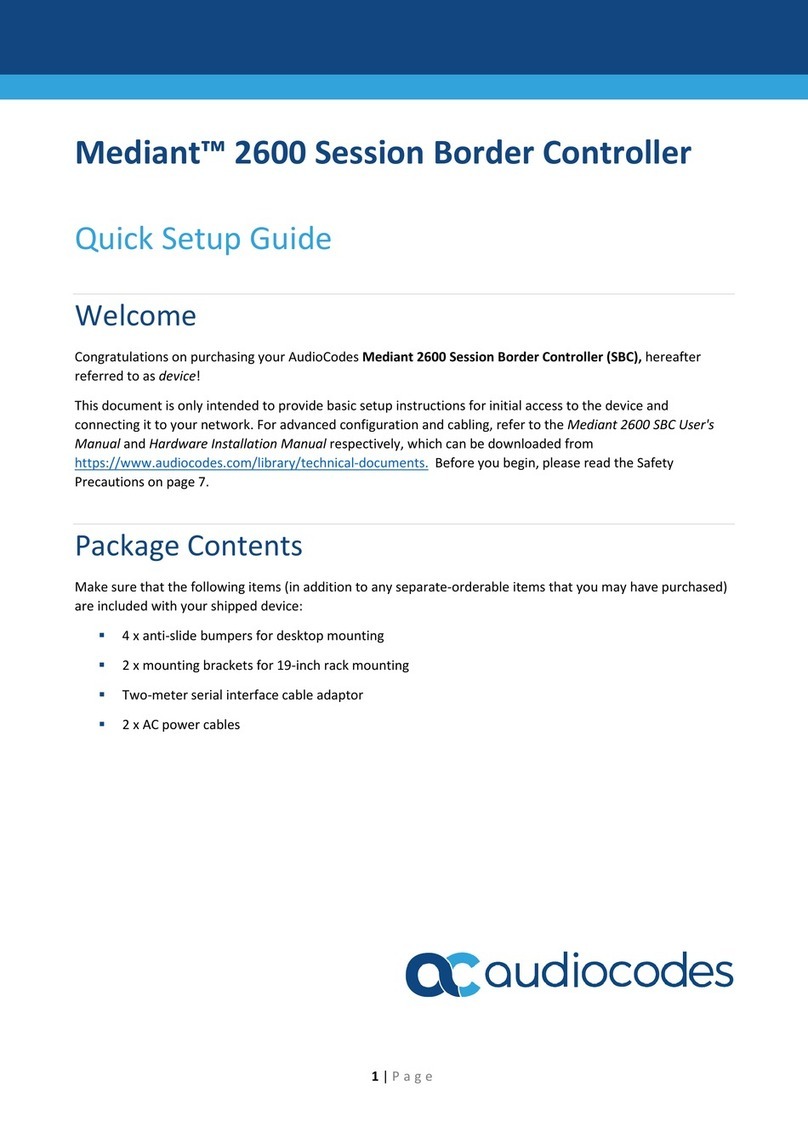
AudioCodes
AudioCodes Mediant 2600 Quick setup guide
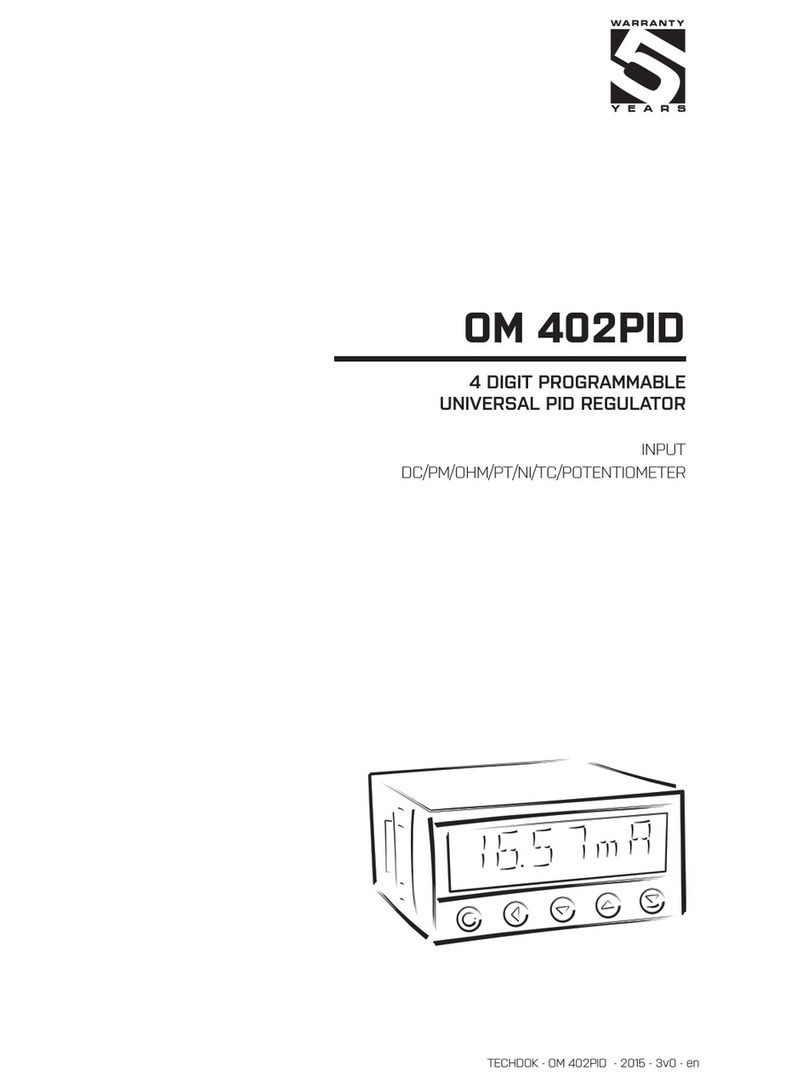
Orbit Merret
Orbit Merret OM 402PID manual
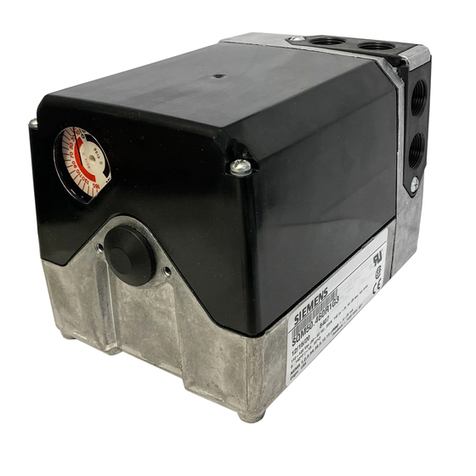
Siemens
Siemens SQM50 series installation instructions
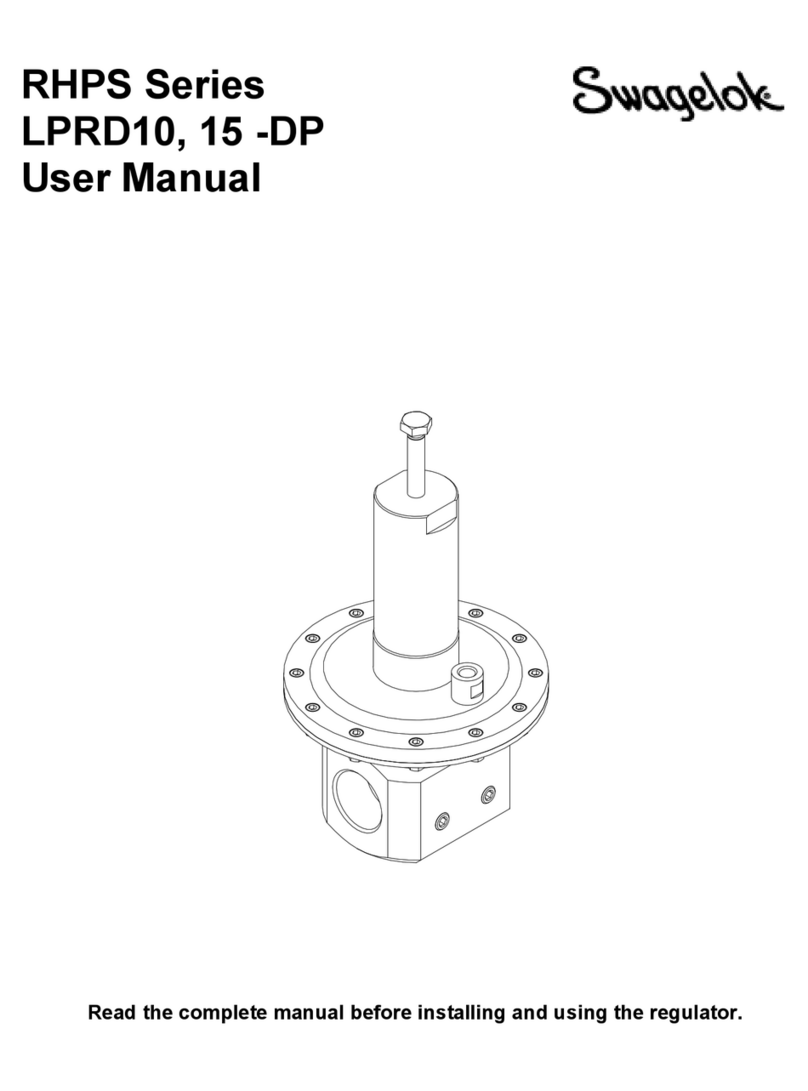
Swagelok
Swagelok RHPS Series user manual
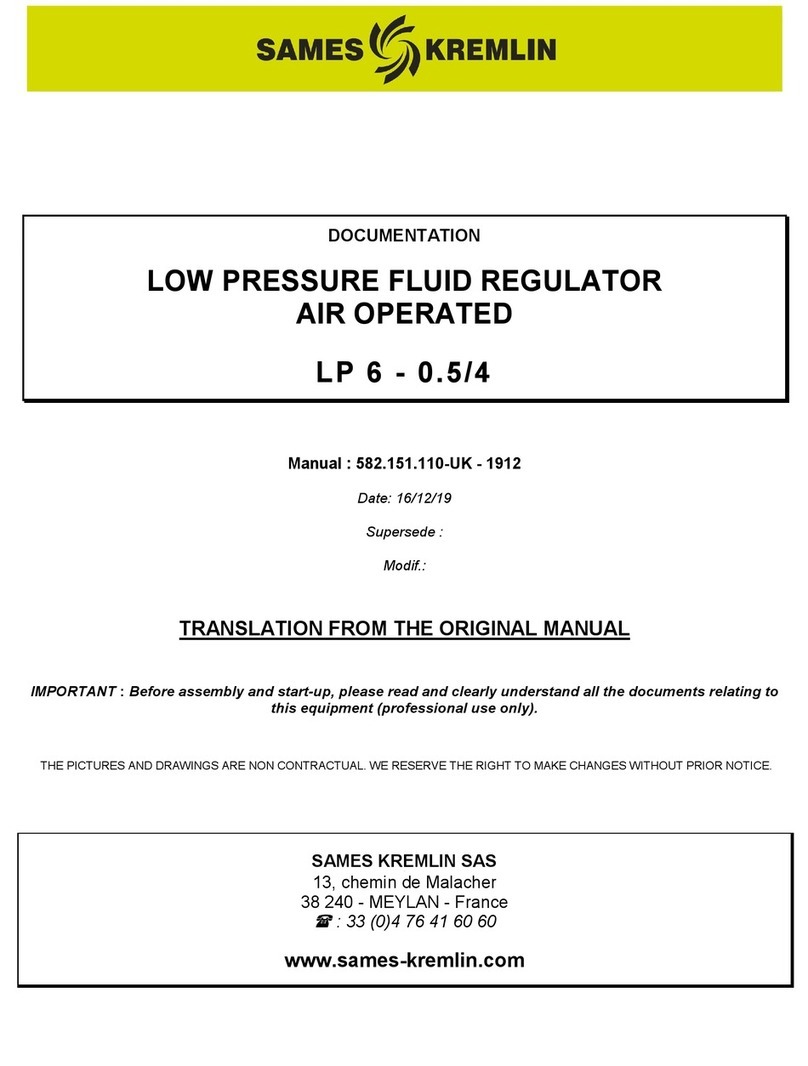
SAMES KREMLIN
SAMES KREMLIN LP 6 - 0.5/4 Translation from the original manual
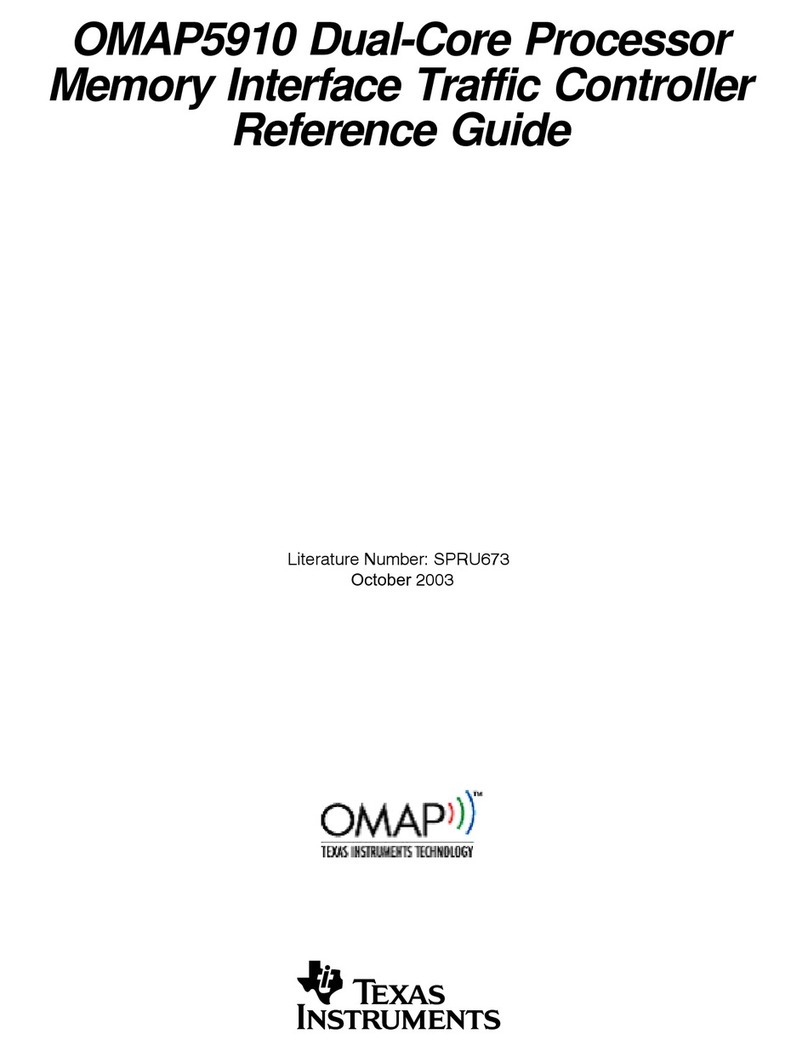
Texas Instruments
Texas Instruments OMAP5910 reference guide
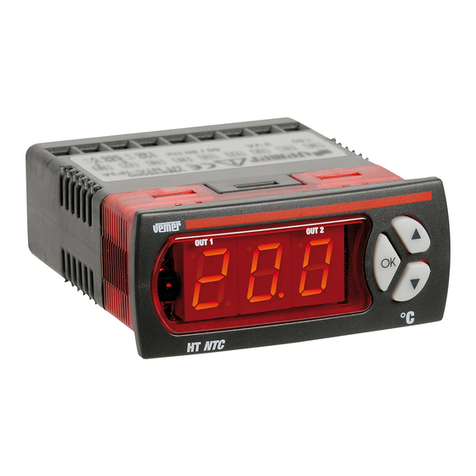
Vemer
Vemer HT NiPt Series user manual