Mankenberg DM User manual

Operating manual
springloaded Pressure Control Valves
Sheet no. DR/4.1.201.1.1 issue 13.07.2020
© 2020 MANKENBERG GmbH

© 2020 MANKENBERG GmbH
Contents
Chapter Heading Page
0 Introduction ....................................…..................................... 1
1 Intended use ……………………………………........................ 1 - 2
2 Marking of the fitting ......................…..................................... 2
3 Safety instructions ...........................…..….............................. 3 - 4
4 Transport and storage .......................…......…........................ 4 - 5
5 Installation ...........................................…................................ 5 - 7
6 Pressure testing the pipeline section ..…................................ 8 - 9
7 Initial start-up ………………………….……….......................... 9 - 10
8 Normal operation ...........................….................................... 10
9 Maintenance .........................................…............................... 11
10 Troubleshooting help .....................…..….............................. 12 - 13
11 Further information …………………….…..…......................... 13

© 2020 MANKENBERG GmbH
- 1 -
0 Introduction
This manual is intended to assist users of a MANKENBERG pressure-reducing, backpressure regulator, vacu-
um control valve, differential pressure control valve or flow control valve during installation, operation and main-
tenance. Read the manual thoroughly before installing or putting this valve into service.
Failure to follow the following instructions – particularly the cautionary and warning notes
– may lead to hazards and may invalidate the manufacturer's warranty.
MANKENBERG is at your servíce for any assistance and queries.
See Section 11 <Further information> for the addresses.
Technical information is also available at www.mankenberg.de
1 Intended use
A MANKENBERG DM pressure-reducing valve is a device that is intended exclusively for automatically regu-
lating the outlet pressure of the medium (without any additional electrical/pneumatic energy) after it has been
installed in a pipeline system.
The force of the outlet pressure acts on a control mechanism (diaphragm, piston or bellows) and is in balance
with the preload of a spring that has to be adjusted by the user to the required value within the setting range of
the valve.
A MANKENBERG UV backpressure regulator is a device that is intended exclusively for automatically regula-
ting the inlet pressure of the medium (without any additional electrical/pneumatic energy) after it has been in-
stalled in a pipeline system.
The force of the inlet pressure acts on a control mechanism (diaphragm, piston or bellows) and is in balance
with the preload of a spring that has to be adjusted by the user to the required value within the setting range of
the valve.
A MANKENBERG VV vacuum control valve is a modification of the pressure-reducing or backpressure regu-
lator, built to regulate pressures in vacuo. It only regulates the differential pressure to the atmosphere.
A MANKENBERG DV differential pressure control valve is a modification of the pressure reducing or back-
pressure regulator, built to regulate differential pressures.
A MANKENBERG MR flow control valve is a modification of the pressure – reducing or backpressure regula-
tor, built to regulate flow rates.
A pressure-reducing valve / backpressure regulator / differential pressure control valve / flow con-
trol valve / vacuum control valve is not a safety valve. A suitable valve must be present in the sys-
tem to limit any excess pressure.
Pressure-regulating valves are generally supplied with a slackened spring and have to be adjus-
ted to the required pressure after being installed. The required pressure measuring devices must
be installed in an adequate distance in front of and behind the fitting. They are not included in
the supply schedule of MANKENBERG.
MANKENBERG planning documents are available to give users precise assistance in selecting and designing
the appropriate fitting, e.g.:
In the section <DM: Regulating valves for pressure>
<Design of pressure-regulating valves>
<Know-how on pressure-reducing valves / backpressure regulators >
<Type sheet DM... / UV... / VV... / DV... / MR...> with technical data and tables of the setting ranges and the
dimensions.
In the following sections the valve types DM, UV, VV, DV and MR are combined under the heading of “Fitting” or
“Pressure-regulating valves” apart from a few sections that only apply to the valve types mentioned.
caution
danger
note

© 2020 MANKENBERG GmbH
- 2 -
These valves are no shut-off elements ensuring a tight closing of the valve. In accordance
with DIN EN 60534-4 and/or ANSI FCI 70-2 they may feature a leakage rate in closed posi-
tion in compliance with the leakage classes II – V:
Leakage class II (metal sealing double seat cone) = 0.5% Kvs value
Leakage class III (metal sealing cone) = 0.1 % Kvs value
Leakage class IV (PTFE seal cone) = 0.01 % Kvs value
Leakage class V (soft seal cone) = 1.8 x 10-5 x Δp x D* [l/h]
*D=seat diameter
Consequently, according to DIN EN ISO 2503 and DIN EN ISO 7291, a safety valve has to
be installed on the control side, which is dimensioned and adjusted in such a way that the
lower one of both pressure indications as mentioned below is relevant as response pressure:
- 1.5 times the maximum set pressure and/or (P out) of the valve (see nameplate),
whichever is the lowest
- PS out (see nameplate)
The response pressure of the safety valve should be abt. 40 % above the max. set pressu-
re of the pressure control valve.
Contrarily to the Pressure Equipment Directive, Annex 1, Paragraph 7.3, the short-term ma-
ximum excess pressure is limited to 5 % of the max. allowable pressure (see above).
Failure to observe this regulation means danger to life and limb and may cause da-
mage to the pressure-regulating valve.
Pressure-regulating valves are generally supplied with an open spring cap to facilitate
maintenance.
Valves with a sealed spring cap and leakage line connection can be supplied for toxic or
hazardous media. In this case the user must make sure that a suitable leakage line is installed.
MANKENBERG valves are supplied as standard for screw-mounted or flange-mounted pipeline/tank
connections – also for special connections if required.
The upper limit of the permitted operating data for pressure and temperature is permanently
marked on each fitting supplied.
2 Marking of the fitting
Each fitting bears the following markings as a minimum:
The markings (in the case of fittings made of deep-drawn stainless steel, they are etched into the body)
should neither be covered nor painted over, so that the fitting remains identifiable.
,
For
Marking
Remark
Manufacturer
Fitting design
MANKENBERG
Pressure-reducing valve+ type or
backpressure regulator + type or
differential pressure control +type
or flow control valve + type or
vacuum control valve + type
See Section 11 <Further information> for the address
Design name as per accompanying MANKENBERG data
sheet.
Nominal diameter
Nominal pressure
Pressure range
Max. permitted
temp.
e.g. DN or G and numerical value
PN or Class and numerical value
Numerical value for DN in [mm], for G in [inches]
Numerical value for PN in [bar], for Class in [lbs/square
inch]
Unless otherwise indicated, all data give the overpressure
above atmospheric. If 2 numerical values are given, these
apply to the inlet and outlet pressure.
Pressure range and numerical
values
Temperature and numerical
value
Temperatures above 50 °C entail a reduced pressure resis-
tance. This must be considered for the corresponding ma-
terial in accordance with the DIN EN 1092 standard
Body material
Flow direction
ATEX protection
class
e.g. CrNiMo steel
Indicated by an arrow
CrNiMo steel = high-alloy austenitic steel
e.g.
Ex II 2G IIB TX -10°C<Ta<+80°C
only for devices with conformity certification according to
ATEX
danger of
fatalities
caution

© 2020 MANKENBERG GmbH
- 3 -
3 Safety instructions
3.1 General precaution
The same safety regulations apply to a fitting as to the system into which it is installed. These instructi-
ons only give those safety recommendations that have to be additionally observed for the fitting.
3.2 Special safety instructions for the plant operator
The following requirements for the intended use of a fitting are not the responsibility of the
manufacturer but have to be guaranteed by the user:
•
The fitting may only be employed for the purpose described in Section 1 <Intended use>.
•
•
Only competent specialist personnel may install, operate and service the fitting. Competent as defi-
ned in these instructions refers to persons who, because of their training, specialist knowledge and
professional experience, are capable of correctly assessing and properly executing the work with
which they are entrusted and of recognizing and rectifying hazards.
The pipeline system must be properly designed and installed so that the fitting can be mounted and
operated without any tension.
•
•
The fitting must be properly installed in the correct mounting position.
The recommended installation, as described in the relevant MANKENBERG data sheet, must be
used for the pipeline section into which the pressure-regulating valve is installed. All control and/or
leakage lines that are required on the pressure-regulating valve must be laid properly, in accordance
with the accompanying MANKENBERG data sheet.
•
•
A pressure-regulating valve with an open spring must be installed in such a way that it presents no
risk of crushing to the operating personnel.
The usual flow rates should not be exceeded in the pipeline section during continuous operation, and
abnormal operating conditions such as vibrations, unusually high flow rates, etc. should be avoided
or – if unavoidable – clarified with the manufacturer in advance.
•
•
The prevailing operating conditions must comply with the limits of the design data stated in the MAN-
KENBERG order confirmation.
The corrosion protection for the fitting must be adapted to the local environmental conditions.
•
Detailed notes are provided on some of these prerequisites in the following sections.
The fitting must not be coated with thermal insulation.
3.3 Special hazards
Before a fitting is removed from the system or before a fitting is dismantled but partially re-
mains in place, the pressure in the system on both the inlet and outlet side must be
completely reduced so that there is no uncontrolled flow of the medium out of the system.
In the case of toxic or hazardous media, the system must be completely drained before the
fitting is removed.
Caution is required with residues that might continue flowing.
Only valves with open spring:
It is necessary to ensure on site, by an appropriate installation or by providing safety devi-
ces and/or positioning a clearly visible warning sign in accordance with the regulations of
EN 292 (formerly accident prevention regulations), that effective protection is afforded
against objects catching on an exposed spring in the pressure-regulating valve.
If required, MANKENBERG will assist in selecting a suitable type with closed spring cap.
danger
of being
crushed
danger of
fatalities

© 2020 MANKENBERG GmbH
- 4 -
If a pressure-regulating valve has to be dismantled:
The following must be observed at all costs:
First release the tension fully on the spring by turning the setting screw on the spring modu-
le anticlockwise.
When doing so, be sure to follow the notes in Section 7 <Initial start-up>!
Then either seal off the two shut-off valves installed before and after the fitting in accordance
with the MANKENBERG installation recommendation and vent the pressure-regulating val-
ve or remove the pressure from the section of the system and then remove the fitting from
the pipeline.
In case of pressure control valves with hydraulic brake the brake fluid (normally mineral oil)
should be discharged from the brake and disposed of properly prior to removing the valve
from the plant.
If a fitting is removed from a system with a toxic medium and is taken out of the plant:
it must be properly decontaminated before repair.
4 Transport and storage
A fitting must be handled, transported and stored with care:
•
The fitting must be transported and stored in its protective packaging until it is installed.
The fitting has moving internal parts.
Even packaged fittings should be transported smoothly without any shocks.
In the case of a fitting that can no longer be transported by hand, the lifting gear must be at-
tached to a suitable position on the housing (branches).
Under no circumstances may the lifting gear be affixed to any attachments (adjus-
ting screw, handwheel or accessories).
Pressure control valves in a sandwich design with slotted discs (i.e. DM 307/308 and UV
6.7/6.8), in particular, are especially sensitive to transport damage and dirt.
The protective packaging on the body must not be damaged during transport and storage.
•
•
When the fitting is stored prior to installation, it should be kept in closed rooms and protected against
harmful influences such as dirt, moisture and frost.
In special cases, the fitting is supplied free of oil, grease or silicone and is marked accordingly. A fit-
ting such as this must not come into contact with oil/grease/silicone during storage and handling
(particularly when subsequently unpacked).
•
A MANKENBERG fitting generally has functional and/or sealing parts made of elastomer materials.
These cannot be stored for an unlimited period.
ISO 2230 describes the storage conditions for elastomers in detail and specifies the per-
missible storage period.
Functional and sealing parts must be replaced well before the storage period
expires. They are available from MANKENBERG as a “service set”. See also Section 10
<Troubleshooting help>.
MANKENBERG fittings of small and medium nominal diameters are largely made of stain-
less steel (high-alloy CrNiMo steel).
If, under exceptional circumstances, fittings are stored in a unpacked state, they must be
protected against ferritic dust to avoid corrosion.
danger of
fatalities
caution
caution
caution
caution
caution
note
note

© 2020 MANKENBERG GmbH
- 5 -
The fitting is generally not capable of standing alone:
The spring module may have a greater weight/volume than the basic body with its pipe
connections.
Handle with care so that the fitting does not tip over during transport/storage.
•
Pressure-regulating valves are generally supplied with a slackened spring. The spring must not be
pretensioned by means of the adjusting screw until after it has been installed, during initial start-up.
5 Installation
5.1 General notes
The same installation regulations apply to a fitting as to the system into which it is installed.
The following additional notes apply:
•
Section 4 <Transport and storage> should also be observed during transport to the installation site.
•
•
The installation site to allow perfect functioning of a fitting should be a section of pipe without any
flow disruptions, without any angles and without any restrictors or shut-off devices close to the fitting,
either upstream or downstream (optimum distance = 10 x DN). If this does not apply, the installation
situation should be checked with the plant operator and/or MANKENBERG.
The statics of the pipeline must be designed so as to take account of the weight of the fitting – parti-
cularly those with an eccentric mass. If required, the pipeline may have to be properly supported on
both sides next to the fitting (or at the fitting itself) – particularly in the case of fittings with a substan-
tial mass and especially if vibrations are to be expected in the system.
When the fitting is supported, it is important to check that all functioning parts (adjusting screws,
springs) remain capable of moving freely and are not blocked.
•
The fitting must not be coated with thermal insulation.
A fitting that is operated at a medium temperature above 130°C needs undisrupted removal of
heat if it is to function perfectly.
Failure to observe this instruction may cause damage to the fitting and hence in the
pipeline system as well.
•
To protect internal functional parts (e.g. the seat) against damage and/or blockages, it may be necessary
to install a strainer and/or filter upstream of the fitting.
The mesh size of the sieve/filter for protecting against aggregates in the pipe section should be
selected by the plant operator according to the operating conditions.
Failure to observe this instruction may impair the function of the fitting and lead to da-
mage.
5.2 Installation preparations
•
It is necessary to ensure that a fitting is not installed unless its matches the operating conditions in
terms of function, pressure and temperature, range, body material as well as connection type and di-
mensions.
•
No fitting may be operated that does not have a sufficient pressure and temperature range
for the operating conditions – see Section 1 <Intended use> and markings on the fitting.
The manufacturer MANKENBERG should be consulted in the case of any applications out-
side of this range.
Failure to observe this regulation may mean danger to life and limb and may cause
damage to the pressure-regulating valve.
Newly installed tanks and pipeline sections must be thoroughly rinsed and cleaned before commis-
sioning.
•
The corrosion protection for the fitting must be adapted to the local conditions.
note
caution
note
danger of
fatalities

© 2020 MANKENBERG GmbH
- 6 -
,
A pressure-regulating valve with an exposed spring must be installed in such a way that it presents
no risk of crushing to the operating personnel.
Only valves with open spring:
It is necessary to ensure on site, by an appropriate installation (e.g. not freely accessible)
or providing safety devices and/or positioning a clearly visible warning sign in accor-
dance with the regulations of EN 292 (formerly accident prevention regulations), that effec-
tive protection is afforded against objects catching on an exposed spring in the pressure-re-
gulating valve.
If required, MANKENBERG will assist in selecting a suitable type with closed spring cap.
Failure to observe this instruction: danger of crushing for the operating personnel
•
•
Before installing a pressure-regulating valve, it is necessary to make sure that the pipeline section
complies with the recommended installation, as described in the relevant MANKENBERG data
sheet. In particular, a safety valve and a suitable strainer should be installed upstream of the fitting.
Pressure-regulating valves are supplied with a slackened spring:
- in this state of delivery, a pressure reducing valve DM is fully opened and immediately shuts at
minimum outlet pressure.
- in this state of delivery, an backpressure regulator UV is fully closed and immediately opens at
minimum inlet pressure.
- in this state of delivery, a differential pressure control valve, a flow control valve or a vacuum
control valve responds as a pressure reducing valve or backpressure regulator, according to design.
In some model series, a control line has to be laid between the pressure-regulating valve
and the pipeline by the customer – this is described in the above-mentioned recommended
installation. Please note: Only use control lines made of metal, not of plastic!
- distance of valve/connection of control line to the pipeline ≥10x pipe-ø
- when the medium is steam, lay the control line at an angle, with the gradient falling
towards the valve, see (catalogue) section <Know How Pressure-reducing valves>.
The control line should match the connection on the fitting.
- if required, install a throttle to avoid vibration.
In the case of toxic or hazardous media, a leakage line must be installed, that discharges
leaking medium safely and pressureless in case of a damaged control device, thus
avoiding dangerous situations.
The diameter should match the connection of the leakage line at the spring cap.
•
The pressure-regulating valve should first be adjusted during the initial start-up by setting the adju-
sting screw on the spring module to the operating conditions – see Section 7 <Initial start-up>.
However, it is necessary to ensure before installation that there is sufficient room for the appropriate
socket or open-jawed spanner above/below the adjusting screw.
As a general rule, pressure-regulating valves should be installed in horizontal lines so that
the spring module (with open spring or with spring cap) points vertically down.
Only for gaseous media installation with the spring pointing vertically up is permissible.
In case the valve must be emptied completely during operation (angle valves), it must be
installed with the spring cap pointing upwards.
If the valve must be installed in a vertical or diagonal line, increased friction of the func-
tional parts leading to increased abrasion and impaired regulation are to be expected.
danger
of being
crushed
note
important
note
danger of
fatalities

© 2020 MANKENBERG GmbH
- 7 -
5.3 Installation steps
•
Fittings should only be finally unpacked at the installation site and inspected for damage prior to
assembly. Damaged fittings must not be installed.
•
•
It is necessary to ensure that the covers have been removed from all the connection branches
before installation.
The fitting should be inspected to ensure that it is clean. Interior parts must be free of liquid (e.g.
condensate): if necessary, connecting branches should be cleaned before installation with clean
compressed air.
•
•
The type and dimensions of the line or tank connections must match the fitting to be installed and be
flush with the connecting surfaces of the fitting as well as in a parallel plane to the fitting itself.
If the fitting is marked with an arrow on the housing, the flow in the pipe section must match the
marked direction of flow.
•
If installed in the opposite direction to the arrow, the fitting will not perform its intended
function.
The fitting must be installed without any tension. In the case of an already installed system, the
geometry of the pipeline must match the face-to-face length of the fitting.
It is necessary to ensure that even under operating conditions no tension from the
pipeline is transferred to the fitting.
A MANKENBERG fitting made of "high grade" or "high grade pure" stainless steel (austeni-
te, e.g. 1.4404 or 1.4435) does not need any surface protection for normal environmental
atmosphere and for normal weather conditions.
External parts of the fitting made of low-alloy or non-alloy materials that are supplied
ex-works with a primer have to be provided with a suitable coating by the customer.
Caution:
Never paint over the marking(s) of the fitting (either etched into the body or on nameplate).
In addition, the following applies to the pipeline connection:
with flanges:
•
The sealing surfaces on the body of the fitting are formed in accordance with the MANKEN-
BERG order confirmation. The accompanying flange seals are generally not included in
the MANKENBERG supply schedule.
During installation, centre the fitting by means of the flange screws on the mating flange before the
screws are tightened.
with screw-mountings:
The connecting surfaces on the body of the fitting are formed in accordance with the
MANKENBERG order confirmation. The required seals are generally not included in the
MANKENBERG supply schedule.
with welding ends:
•
Properly performed welding must ensure that no significant tension is transferred to either the
section of pipeline or the body of the fitting.
•
Under no circumstances may the body of the fitting exceed the temperature marked on it; otherwise
the sealing and functional parts will be damaged and the whole fitting will become unserviceable.
caution
note
note
note
note

© 2020 MANKENBERG GmbH
- 8 -
When a fitting with a body made of "high grade" or "high grade pure" deep-drawn parts (vi-
sible on the body connection with clamp rings) is welded, the welding joint must be carried
out with special care; it is recommended that the body should be kept cool with a damp
cloth.
Failure to observe this instruction may cause distortion of the fitting body:
even 0.1 mm of permanent distortion in the seat region may render the fitting unservice-
able.
If available, connect control and/or leakage line.
6 Pressure testing the pipeline section
The fitting has already been pressure-tested by the manufacturer. The following points should be obser-
ved when conducting a pressure test on a pipeline section with a pressure-regulating valve installed:
•
•
Pressure-reducing valve:
the test pressure must not exceed 1.5 times the max. adjustable outlet pressure, e.g. a setting range
of 4 to 8 bar gives a max. permitted test pressure of 8 bar x 1.5 = 12 bar.
The test pressure on the inlet pressure side is determined by the pressure marked on the body, in
addition, the permitted reducing rate has to be observed (see order confirmation).
Backpressure regulator:
the test pressure must not exceed 1.5 times the max. adjustable inlet pressure, e.g. a setting range
of 4 to 8 bar gives a max. permitted test pressure of 8 bar x 1.5 = 12 bar.
•
•
Vacuum control valve:
the test pressure must not exceed 1.5 times the max. adjustable pressure. The information described
above should be observed according to whether a pressure-reducing or backpressure regulator
forms the basis for the vacuum control valve.
Differential pressure control valve:
the test pressure must not exceed 1.5 times the max. adjustable pressure. The information described
above should be observed according to whether a pressure-reducing or backpressure regulator
forms the basis for the differential pressure control valve.
•
Under no circumstances may the test pressure exceed 1.5 times the value indicated on the body
with “PN” or “Class”.
Flow control valve:
the test pressure must not exceed 1.5 times the max. adjustable pressure. The information described
above should be observed according to whether a pressure-reducing or backpressure regulator
forms the basis for the flow control valve.
If any leakage occurs on the fitting, Section 10 <Troubleshooting help> should be observed.
If the pipe section is flushed and/or dried after assembly or pressure testing, it isnecessary
to make sure that the fitting has not been damaged by corrosion or excessively high tempe-
rature.
caution
note

© 2020 MANKENBERG GmbH
- 9 -
7 Initial start-up
No fitting may be operated that does not have a sufficient pressure and temperature range
for the operating conditions – see Section 1 <Intended use> and markings on the fitting.
The manufacturer MANKENBERG should be consulted in the case of any applications out-
side of this range.
Failure to observe this regulation may mean danger to life and limb and may cause
damage to the pressure-regulating valve.
The fitting is supplied with no tension on the spring – hence no defined operating pressure has been set
in the factory. During initial start-up, the valve must be adjusted to the system parameters.
The adjusting screw on the spring module should be tensioned for this purpose: Clockwise rotation
(when looking onto the adjusting screw) has the following effect:
•
•
on the pressure-reducing valve: the outlet pressure increases.
on the backpressure regulator: the inlet pressure increases.
•
•
•
on the vacuum control valve: the set pressure increases
on the differential pressure control valve: the operating pressure increases
on the flow control valve: the flow increases
Annotation to the differential pressure control valve:
a differential pressure control valve based on a pressure-reducing valve closes at increasing differential pressure
a differential pressure control valve based on an backpressure regulator opens at increasing differential pressure
Annotation to the flow control valve:
a flow control valve based on a pressure-reducing valve closes at increasing flow rate
a flow control valve based on an backpressure regulator opens at increasing flow rate
Annotation to the vacuum control valve:
a vacuum control valve based on a pressure-reducing valve closes at increasing vacuum
(differential pressure to the atmosphere)
a vacuum control valve based on a backpressure regulator opens at increasing vacuum
(differential pressure to the atmosphere)
The target value to be set by means of the adjusting screw shall be defined by the operator of the sys-
tem and must be calibrated with the aid of a pressure gauge on the plant side (or some other pressure
monitoring device).
When looking onto the adjusting screw:
Never fully remove the adjusting screw (by rotating it anticlockwise).
Do not block the adjusting screw in the position of maximum tension (when rotating it
clockwise).
At the beginning of or shortly after the initial start-up, the sieve or the filter insert of any in-
stalled strainer/filter should be cleaned in order to avoid blocking the strainer/filter.
After the initial start-up:
Check the seals on screw-mounted parts of the body and reseal if necessary.
Ask MANKENBERG for tightening torque, if necessary.
Observe the relevant notes in Section 10 <Troubleshooting help>.
After the initial start-up:
Control the leakage line for leaking medium.
Observe the relevant notes in Section 10 <Troubleshooting help>.
danger of
fatalities
caution
danger
caution
caution

© 2014 MANKENBERG GmbH
- 10 -
© 2020 MANKENBERG GmbH
- 10 -
8 Normal operation
A properly designed and correctly adjusted pressure control valve works automatically within its pressu-
re control range and does not need any form of auxiliary energy.
To obtain optimum regulating accuracy, the desired operating pressure should be in the upper
part of the setting range of the pressure-regulating valve. This is described in detail in the “DM”
Section of the MANKENBERG catalogue under “Calculation of Pressure
Regulators”.
In case of doubt, contact MANKENBERG Service
– see Section 11 <Further information> for addresses.
It is necessary to ensure that the materials selected for the parts of the fitting in contact with
media are suitable for the media in use. The manufacturer accepts no liability for any dama-
ge due to corrosion by aggressive media on parts made of unsuitable materials.
Failure to observe this regulation may mean danger to life and limb and may cause
damage to the pipeline system and to the fitting.
The fitting has functional parts that have to remain capable of moving easily. Make sure
that both the external springs and inner parts in contact with the medium cannot freeze nor
become blocked by dirt. Observe the maintenance intervals.
Failure to observe this instruction may cause damage to the pipeline system and to
the fitting.
It is recommended that the fitting should be inspected to ensure that it is functioning correctly after each
new start-up.
In some series a control line is laid between the pressure-regulating valve and the pipeline
– see Section 5.1 <Installation / General notes>.
Damage to this control line may result in danger to life and limb and may impair the
function of the pressure-regulating valve or even lead to complete failure.
Pressure-regulating valves are designed for the operating point in accordance with the order.
This operating point may occasionally be changed by the customer by means of the adjusting
screw. However, the setting of the adjusting screw must not be permanently altered (e.g. by
adding a motorized actuator).
Failure to observe this instruction may cause damage to the pressure-regulating valve.
note
danger of
fatalities
caution
danger
note

© 2020 MANKENBERG GmbH
- 11 -
9 Maintenance
The automatic function of the fitting requires maintenance to ensure that it continues to operate
perfectly. It is important for maintenance work to take place in a planned manner at periodic
intervals. The maintenance plan in Table 1 is a recommendation by the manufacturer MANKENBERG,
which should be supplemented by practical experience gained by the user under the prevailing opera-
ting conditions. MANKENBERG shall assume no liability resulting from improper maintenance and/
or repairs.
Table 1: Sample plan for maintenance work
During maintenance work (apart from visual inspections) the relevant recommendations and
warning notes in Section 10 <Troubleshooting help> should be observed.
Failure to observe this warning may mean danger to life and limb and may cause
damage to the pipeline system and to the fitting.
When a fitting that has previously been dismantled is being put back into service, the fitting should be
checked for proper sealing capacity and function as well as correct adjustment of the adjusting and
functional components!
Type of maintenance
Work to be performed
Period 1)
Check function
Function / check free
movement of the
spindle
Check whether function is fulfilled as per Section
1 <Intended use>
With a non-rising adjusting screw (without counternut),
cone movement in the valve seat can be detected by
checking the movement of the adjusting screw.
at least 1x per week
at least 2x per year
Check seal on the
body, the pipe connec-
tion and the control
lines
Grease sliding points
Monitor exposed spring
If installed upstream of
the fitting:
clean strainer
Visual inspection
Grease external sliding points with a corrosion-protection
lubricant
at least 1x per
month
at least 4x per year
Visual inspection:
if necessary, remove any dirt/corrosion 2)
According to the manufacturer's instructions
at least 2x per year
Depends on the
contamination of the
medium
Preventive
maintenance
Check safety valve
1) See comment at the beginning of this section: The time intervals are guides which should be adapted
to match the prevailing operating conditions, the properties of the medium in the system and the user's
experience.
2) Caution danger of crushing: shut down the valve for cleaning purposes!
3) Request maintenance set and replacement instructions from MANKENBERG.
Dismantle fitting, see Section 10 <Troubleshooting help>.
Visual inspection diaphragm and functional parts Re-
place all parts of the maintenance set 3)
According to the manufacturer's instructions
at least 1x per year
at least 1x per year
danger

© 2020 MANKENBERG GmbH
- 12 -
10 Troubleshooting help
Be sure to observe Section 3 <Safety instructions> when rectifying faults.
Spare parts must be ordered with all the details on the nameplate
Only original parts from the manufacturer MANKENBERG may be installed.
MANKENBERG experts are available to help in rectifying faults as quickly as possible.
See Section 11 <Further information> for the addresses.
If functional or corrosion damage is detected during maintenance or after a fault:
consult MANKENBERG to find out whether a more suitable fitting is available or whether
the damaged part can be supplied in a better-suited material.
special tools required:
To dismantle the following pressure control valves, a special tool is required (can be
requested at MANKENBERG if required):
- pressure reducing valve DM 662
- backpressure regulator UV 5.1 up to and including DN25 / G1“
- and vacuum control valve deducted from these, e.g. VV 5.1
note
note
Type of fault
Action
Leakage at a connection
body parts
(flange or clamp ring):
reseal connection
Leakage on the spring cap:
the valve must be
repaired
Tighten the screws clockwise (tighten flange screws crosswise).
If the screws of the body connection have to be loosened or removed
(= unscrewing in the anticlockwise direction):
Danger of fatalities
To prevent any risk for operating personnel, make sure that this repair
measure is only carried out on a section of pipe that is not under pressure.
Take note of Section 3.3 <Special hazards> and then Section 5
<Installation in the pipeline>.
The control mechanism (diaphragm, piston or bellows) is defective and
has to be replaced:
Repair necessary, as described further below.
Danger of fatalities
The pretensioned spring must be fully relaxed before a fitting is dis-
mantled!
To prevent any risk for operating personnel, make sure that this repair
measure is only carried out when the fitting is not under pressure.
Take note of Section 3.3 <Special hazards>.

© 2020 MANKENBERG GmbH
- 13 -
11 Further information
You can obtain these instructions, the MANKENBERG data sheets quoted as well as further information
– including English language versions – from the following addresses:
Functional fault
Leakage at the seat means
the set inlet or outlet pressure
is not correctly regulated:
clean the functional parts
Aforeign object may be jammed in the seat and be preventing proper sealing:
- Pressure reducing valve DM:
fully tighten spring
- backpressure regulator UV:
fully release the tension of the spring
- Differential pressure control valve:
according to design, the abovementioned has to be observed.
- Flow control valve:
according to design, the abovementioned has to be observed.
- Vacuum control valve:
according to design, the abovementioned has to be observed so that the
valves open and foreign objects can be flushed out.
If the functional fault cannot be rectified in this way:
Cleaning is necessary: the pressure-reducing valve must be dismantled
Danger of fatalities
The pretensioned spring must be fully relaxed before a fitting is dismant-
led!
To prevent any risk for operating personnel, make sure that this repair measure
is only carried out when the fitting is not under pressure. Take note of Section
3.3 <Special hazards>.
When the valve is not under pressure, take off the spring module by releasing
the clamp rings (or the screw connection) and dismantle the diaphragm (or
piston/bellows) and functional parts for cleaning.
Here all parts of the maintenance set should be renewed.
Afterwards, assemble the fitting and readjust it, as described under
Section 7 <Initial start-up>.
Functional fault
Cleaning alone – see above –
cannot rectify the fault:
the fitting must be repaired
If during cleaning it is found that the control mechanism (diaphragm, piston or
bellows), the cone or other functional parts are damaged:
Repair necessary: damaged parts have to be replaced.
If the repair is to be carried out in the customer's workshop:
make a note of all data according to the markings on the fitting and order the
spare parts and necessary instructions from MANKENBERG. See Section 11
<Further information> for addresses.
or:
Send the fitting to the manufacturer for repair.
See Section 11 <Further information> for the addresses.
Mankenberg GmbH
Spenglerstrasse 99
D-23556 Lübeck

© 2020 MANKENBERG GmbH

Know How Backpressure Regulators
Backpressure regulators control an adjustable constant pressure upstream of the valve. A spring keeps the valve close. As the
inlet pressure rises the valve opens.
Page No. UV/13.1.152.1 - Standing MANKENBERG GmbH | Spenglerstraße 99 | D-23556 Lübeck www.mankenberg.de | Tel. +49 (0) 451 - 8 79 75 0
Selecting valve type and nominal diameter
Using your maximum operating data and the smallest differential
pressure Δp, you should calculate the characteristic performance figure
Kv (see leaflet Calculation of Pressure Regulators). Select a valve whose K
vs value is 30 % greater than the calculated Kv figure. Additional
allowances must be made for high-viscosity liquids or liquids which
vaporise when depressurised.
Backpressure regulators should not be overdimensioned. Their optimum
working range is within 10 % to 70 % of their Kvs value.
Selecting rated pressure and valve material
The rated pressure must exceed the maximum system pressure,
irrespective of safety allowances. Please note also the effect of the
temperature (see DIN 2401).
Selecting the setting range
For good control accuracy you should select a setting range which
places the required inlet pressure near its upper limit. If, for example, the
controlled inlet pressure is to be 2.3 bar, you should select the 0.8 to 2.5
bar setting range, not 2 to 5 bar. If the available setting range is not
wide enough you may go below the bottom limit of the setting range
provided that the valve loading is kept low and a high control accuracy
not required.
Selecting elastomer materials
You should select eleastomers according to the operating temperature
and the requirements of the medium. High-pressure gases, for example,
can diffuse into the elastomer and cause damage when being
depressurised.
Flow velocity
Depending on pressure drop and permitted maximum noise level, we
recommend the following flow velocities:
Liquids 1 - 5 m/s
Saturated steam 10 - 40 m/s
Superheated steam 15 - 60 m/s
Gases up to 2 bar 2 - 10 m/s
Gases above 2 bar 5 - 40 m/s
Sense line (control line)
You should install a sense line if the selected backpressure regulator is
designed for sense line operation. The sense line should be connected at
a distance of not less than 10 times nominal diameter upstream of the
valve. No isolating valves should be installed in the sense line to avoid an
excessive pressure differential between valve body and diaphragm.
To attenuate any oscillations occurring in the pipeline system, the sense
line may be fitted with a restrictor which must never be fully closed
during operation.
In the case of steam and liquids the sense line must be installed so as to
fall towards the valve. Under special operating conditions, for example
intermittent operation with dry steam, an compensation vessel must be
installed. The sense line must be rigid as elastic hoses can induce
oscillations.
Protecting your system
To protect your system you should install a safety valve upstream of the
backpressure regulator to prevent the maximum permitted operating
pressure (normally 1.5 x maximum set pressure) being exceeded. The
safety valve operating pressure should be set approximately 40 % above
the maximum set pressure of the backpressure regulator to avoid
blow-off during slight pressure fluctuations. For example: if the setting
range of the backpressure regulator is 2 - 5 bar the safety valve operating
pressure must be 1.4 x 5 bar = 7 bar.
Protecting the backpressure regulator
To protect the backpressure regulator against damage from solid particles
carried in the pipeline, a strainer or filter should be fitted and serviced at
regular intervals.
Valve seat leakage
These valves are no shut-off elements ensuring a tight closing of the
valve. In accordance with DIN EN 60534-4 and/or ANSI FCI 70-2 they may
feature a leakage rate in closed position in compliance with the leakage
classes II – V:
Leakage class II (metal sealing double seat cone) = 0.5% Kvs value
Leakage class III (metal sealing cone) = 0.1 % Kvs value
Leakage class IV (PTFE seal cone) = 0.01 % Kvs value
Leakage class V (soft seal cone) = 1.8 x 10-5 x Δp x D* [l/h]
*D=seat diameter
Any low leakage requirement must be expressly specified when ordering.
Valve leakage can be considerably reduced by special measures such as
lapping the valve seat, using special cone seals and increasing the control
(diaphragm) surfaces.
Cut-off
For the purpose of installation, servicing and isolation of the valve,
shut-off valves should be installed upstream and downstream of the
backpressure regulator. When closing the shut-off valves the upstream
valve must always be closed first. A bypass line may be necessary to
maintain emergency operation.
Stellited seat and cone
In the case of abrasive media or liquids with pressure drops (inlet
pressure minus outlet pressure) of more than 25 bar the valve cone must
be stellited; for pressure drops above 150 bar the seat must be stellited
as well.
Leakage line
If toxic or hazardous media are used the valve must feature a sealed
spring cap (including setting spindle seal) fitted with a leakage line
connection. When the backpressure regulator is installed on site a
leakage line must be fitted capable of safely and pressureless draining
the escaping medium in case the control valve should become defective.
Mounting position
For gases a backpressure regulator can normally be fitted in horizontal
pipelines with the spring cap at the bottom or at the top. Installation in
vertical pipe runs is possible but can result in increased wear and loss of
control accuracy owing to increased friction.
In the case of liquids a backpressure regulator should be installed with
the spring cover at the bottom. Thus gas traps upstream of the valve are
avoided which would cause the valve to oscillate.
For steam a backpressure regulator should likewise be installed with its
spring cover at the bottom to protect the diaphragm against overheating
by means of a layer of condensate. In case the valve must be emptied
completely during operation (angle valves), it must be installed with the
spring cap pointing upwards.
Start-up
backpressure regulators should be started up and operated without
pressure surges, if possible. A sudden operation of upstream or
downstream valves should be avoided.
Steam operation
If a backpressure regulator is installed in a steam plant the diaphragm
water reservoir must be filled before the plant is started up. There must
be no danger of overheating at the installation site caused by excessive
ambient temperatures or insufficient heat dissipation. backpressure
regulators must not be insolated. In some cases an insulating of the
body is permitted, but only with cast bodies. Never insulate diaphragm
housing, mid section and spring cap (or open springs). Overheating
caused by insulating destroys the elastomere of the control unit.
Setting the pressure
Backpressure regulators are normally supplied by us with a relaxed
spring. This means that a valve is set at the factory to the minimum inlet
pressure. The required pressure should be set under operating
conditions.
Maintenance
Backpressure regulators must be cleaned and serviced regularly.
Valves free of oil and grease or silicone
Please pay attention to order an fit only spares free of oil and grease
resp. free of silicone.
Please consult our engineer if extreme operating conditions apply
or whenever you are in doubt.
Notes on Safety, operating instruction etc. MUST be followed.
1 / 1

Notes on Safety
Sheet no. A/5.1.0.141.1 - Issue 01.06.2014 MANKENBERG GmbH | Spenglerstraße 99 | D-23556 Lübeck www.mankenberg.de Tel. +49 (0) 451 -8 79 75 0
relating to the installation, operation, maintenance and repair of
Mankenberg products
Basic requirements
The equipment must be installed, repaired and operated only by skilled personnel familiar with the installation, commissioning and operation of the
products. “Skilled personnel” in the meaning of these Installation and Operating Instructions are such persons who, thanks to their professional
training, knowledge and experience and their knowledge of the applicable standards, are capable of assessing the work they are asked to carry out
and recognising the possible dangers. Suitable precautions must be taken to avoid any risks which may be associated with the medium contained in
the pipelines and equipment, with the set pressure or the moving parts.
Preparatory work
First you should make sure that your worksite is safe. Organise the required tools and equipment such as working platform, lifting tackle etc. and
make sure that the lighting of the site is adequate. Find out whether protective clothing, ear protectors etc. are needed or mandatory. Check
whether you have suitable tools and any replacement parts you may need. Use only original MANKENBERG parts. Read the operating instructions
carefully and note all the instructions and points.
Medium contained in pipelines and valves
Check which medium is or was in the pipline and find out what safety precautions you have to take. Be especially careful if the medium is toxic,
flammable, hot or a health hazard.
Connecting a leak line
In the case of toxic or hazardous media the valve must be equipped with a sealed spring cover (incl. sealed setting screw) with leak line connection.
In such cases a leak line must be installed which can drain the medium safely in case the valve becomes defective.
Hazards at the installation site
Please note any areas designated as explosion hazard sites. Make sure that there is sufficient ventilation where a shortage of oxygen may occur e.g.
in tanks, vessels or shafts. Allow hot surfaces to cool. Use welding gear only if the worksite is sufficiently ventilated and there is absolutely no danger
of fire or explosion or a release of agents dangerous to health.
Effects on the entire plant or machine
Check the possible effects which your work may have: How will your work affect the total system? Is there a possibility of danger if, for example,
you close isolating valves, switch off the power supply or switch off/ remove/disable safety equipment and ventilation systems or monitoring and
alarm equipment?
Pipeline and valve operating pressure
Make sure that the pipeline section on which you will be working has been completely depressurised and is under atmospheric pressure. Do not
believe that the system is depressurised only because your pressure gauge reads Zero. Make safe and label any valves you have closed.
Electrical connections
Work on electrical systems must be carried out only by suitably qualified experts. Make sure that the electrical power supply has been switched off
and that the system cannot be repowered.
Dismantling
The equipment may contain a preloaded spring which must be relaxed before the equipment can be dismantled. Please follow the operating and
servicing instructions.
Completing the work
Make sure that the plant or system or machine is fully operational again. Test all monitoring, safety and alarm equipment.
Testing the plant/system
When pressure-testing the plant the equipment or valve may be pressurised only up to its maximum rated pressure.
Commissioning
Check the equipment/valve for leaks before commissioning. Do not tighten the pressure setting screw to such an extent that it limits the valve lift or
jams the valve in open position. Do not slacken the pressure setting screw too far. The valve is no longer operational when the spring is completely
relaxed.
Only with valves free of oil and grease or silicone.
Please pay attention to order an fit only spares free of oil and grease resp. free of silicone.
Always follow the operating instructions.
Please consult our engineering department in case of severe operating conditions or if you have any doubt.

Betriebsanleitung
federbelastete Druckregelventile
Blatt Nr. DR/4.0.201.1.1 Stand 13.07.2020
© 2020 MANKENBERG GmbH

© 2020 MANKENBERG GmbH
Inhalt
Kapitel Bezeichnung Seite
0 Einleitung ................................................................. 1
1 Bestimmungsgemäße Verwendung......................... 1 - 2
2 Kennzeichnung der Armatur .................................... 2
3 Sicherheitshinweise ................................................ 3 - 4
4 Transport und Lagerung .......................................... 4
5 Einbau ..................................................................... 5 - 7
6 Druckprüfung des Rohrleitungsabschnitts .............. 8
7 Erste Inbetriebnahme .............................................. 9
8 Normalbetrieb .......................................................... 10
9 Wartung ................................................................... 11
10 Hilfe bei Störungen .................................................. 12 - 13
11 Weitere Informationen ............................................. 13
This manual suits for next models
4
Table of contents
Languages:
Other Mankenberg Control Unit manuals
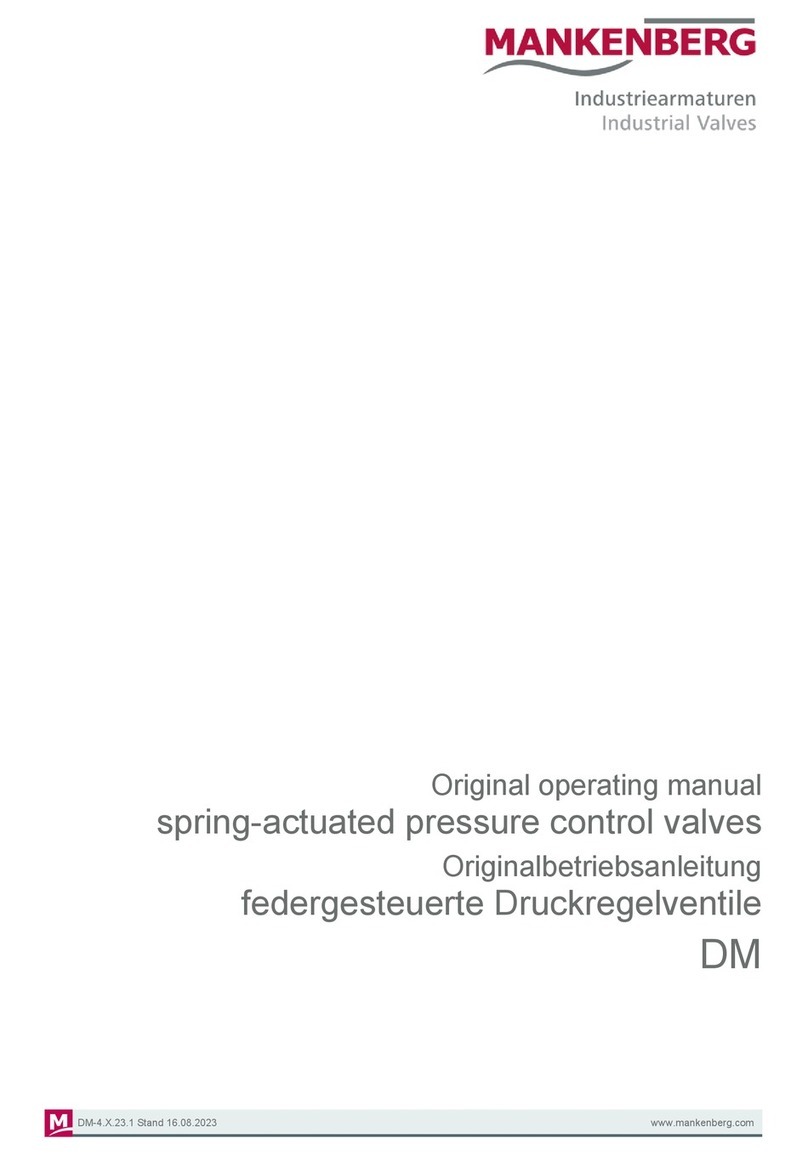
Mankenberg
Mankenberg DM 618Z Installation instructions
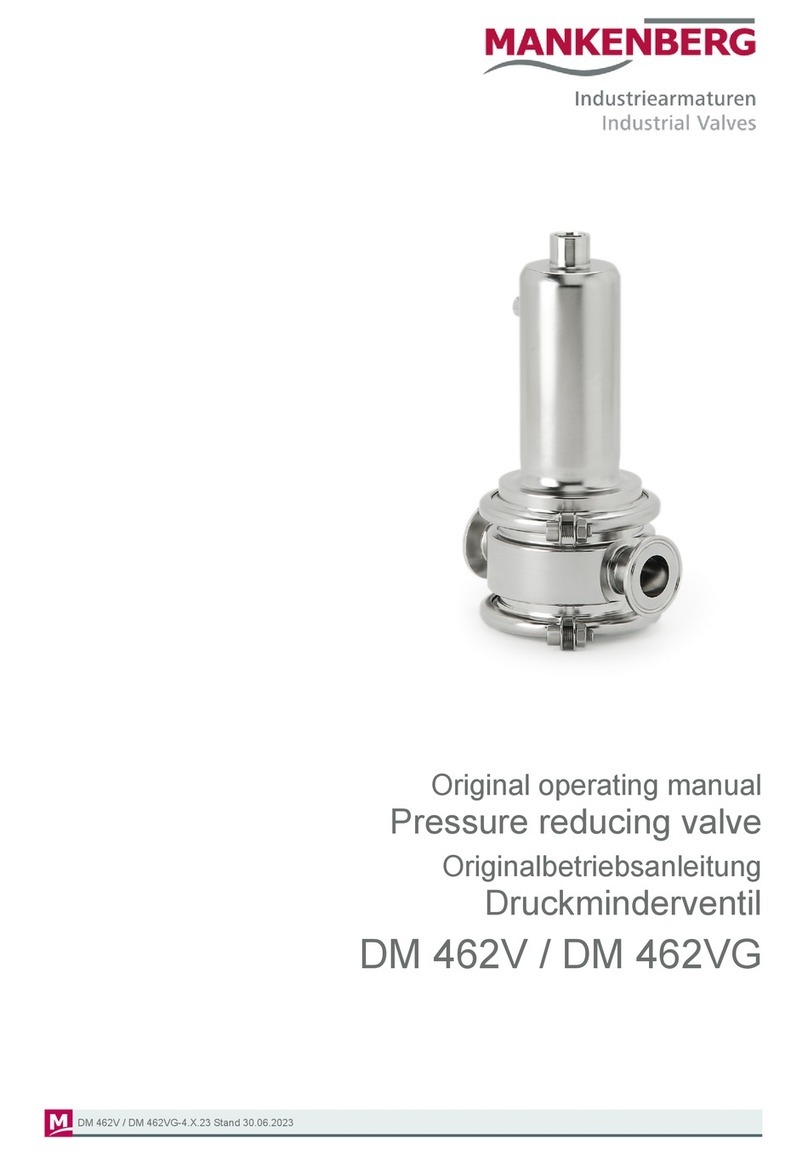
Mankenberg
Mankenberg DM 462V Installation instructions

Mankenberg
Mankenberg EB 1.12 Installation instructions
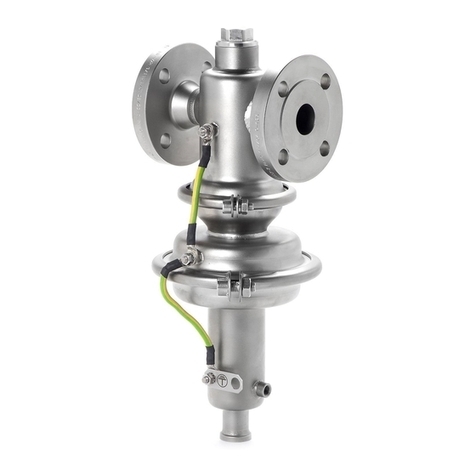
Mankenberg
Mankenberg DM 652 ATEX H2 User manual
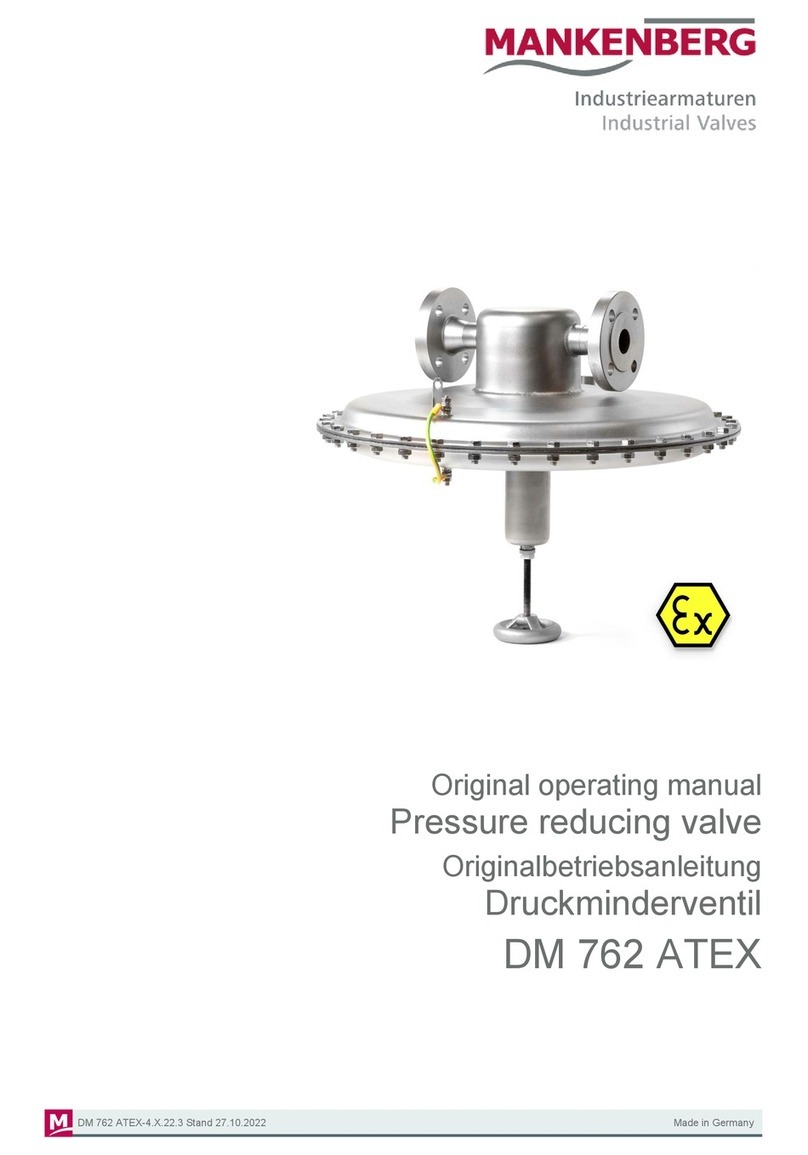
Mankenberg
Mankenberg DM 762 ATEX Installation instructions
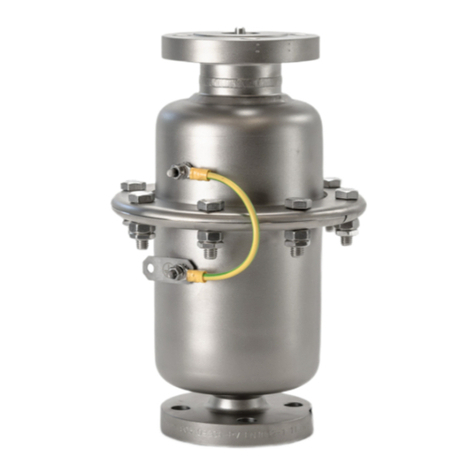
Mankenberg
Mankenberg EB 3.52 ATEX H2 User manual
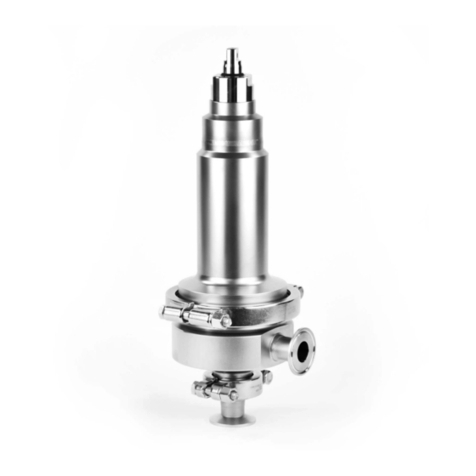
Mankenberg
Mankenberg DM 152V Installation instructions
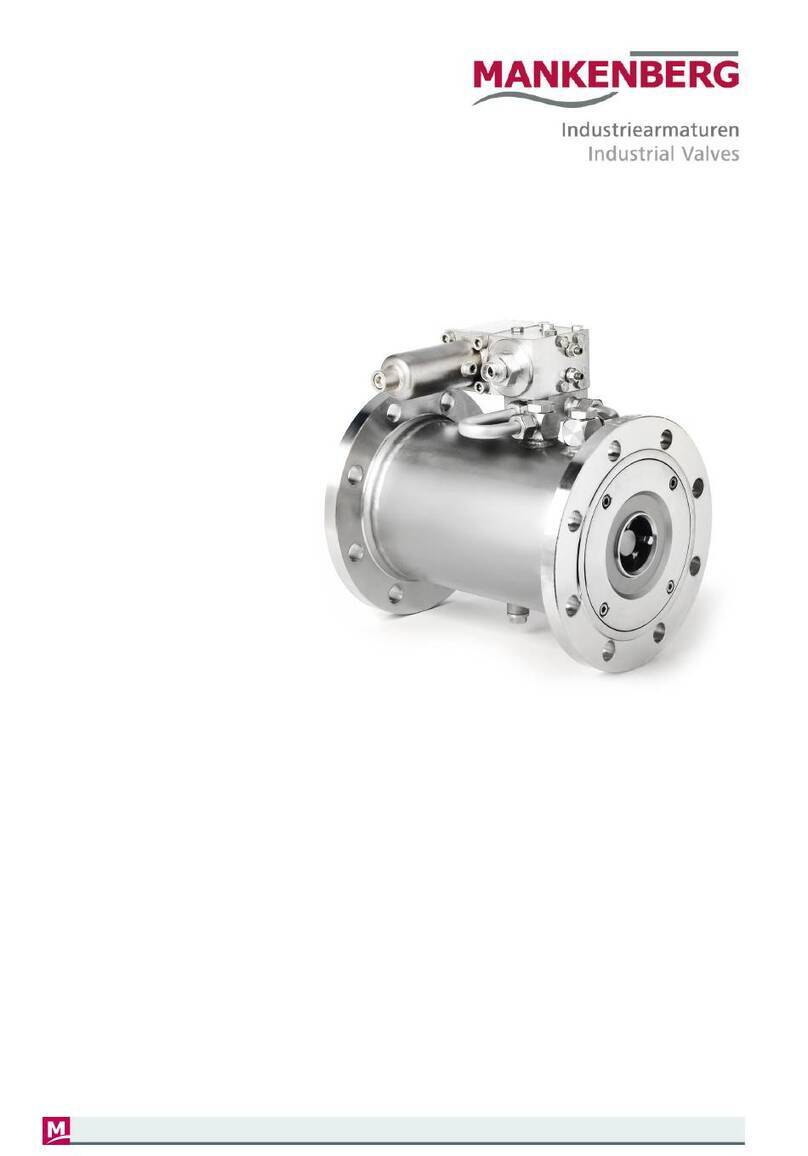
Mankenberg
Mankenberg M-XTRA RP 824 Installation instructions