Maple Systems HMI5040BN User manual

1010-1051 Rev 00 www.maplesystems.com
Introduction
Thank you for purchasing a Maple Systems HMI5000B Series graphic
industrial operator interface terminal. This booklet describes the steps
necessary for installing the following models:
HMI5040B
HMI5070B
HMI5100BN
HMI5040BN
HMI5070BN
The HMI5000B Series touchscreens are configured using the
EZwarePlus software (purchased separately).
For information on programming and configuring the HMI, please refer to
the EZwarePlus Programming Manual (P/N 1010-1015) available on
the EZware software DVD and the Maple Systems website.
For additional information, please refer to the Support Center section of
the Maple Systems website, www.maplesystems.com.
The Support Center provides links to information such as Manuals,
FAQs, Technical Notes, Training Videos, Sample Projects, Controller
Information Sheets, and Controller Cables.
HMI5000B Series
Installation Guide

2 HMI5000B Installation Guide
1010-1051 Rev 00 www.maplesystems.com
Static Awareness
Do NOT remove the rear cover of the HMI5000B Series product –doing
so will void the warranty. When the rear cover is removed the circuitry
inside is exposed to possible damage by electrostatic discharge during
handling.
Minimize the possibility of any electrostatic discharge by:
Handling the HMI at a static-free, grounded workstation.
Discharging personal static by grounding yourself prior to
handling the HMI.
Connecting the chassis ground (FG or ⏚) connector of the HMI
to a clean earth ground.
Placing the HMI in an antistatic bag during transport.
Unpacking the Unit
Carefully unpack the HMI. Check all material in the container against the
packing list. Maple Systems will not accept responsibility for shortages
against the packing list unless notified within 30 days. The equipment
and accessories were inspected and tested by Maple Systems before
shipment. Examine the equipment carefully; if any shipping damage is
evident, notify the carrier immediately. Maple Systems is not responsible
for claim negotiations with the carrier. Save the shipping container and
packing material in case the equipment needs to be stored, returned to
Maple Systems, or transported for any reason.
Packing List
HMI5000B Series Touchscreen
Power Connector
Mounting Clamp Kit
HMI5000B Series Installation Guide
Warranty
A copy of the Warranty and Limitation of Liability is contained in the
product box. It can also be found on the Maple Systems website.

HMI5000B Installation Guide 3
1010-1051 Rev 00 www.maplesystems.com
Technical Support
This manual is designed to provide the necessary information for trouble-
free installation and operation of the HMI. For assistance, please contact
Maple Systems as follows:
Phone: 425-745-3229
Email: support@maplesystems.com
Web: www.maplesystems.com
Installation of HMIs
Information furnished by Maple Systems is believed to be accurate and
reliable. However, no responsibility is assumed by Maple Systems for the
use of this information, or for any infringements of patents or other rights
of third parties which may result from its use. No license is granted by
implication, or otherwise, under any patent or patent rights of Maple
Systems. Maple Systems retains the right to revise or change its
products and documentation at any time without notice.
CE Compliance
The HMIs have been tested to conform to European CE requirements,
which meet or exceed the noise emissions and immunity requirements
as set forth in the EN55022 (Emissions) and EN55024 (Immunity)
standards. The products are designed to withstand electrical noise in
harsh industrial environments. They also conform to requirements that
limit electrical emissions. However, this does not guarantee that the
products will be totally immune from possible malfunction in cases where
severe electrical noise occurs. Therefore, follow these guidelines for
proper wire routing and grounding to ensure the proper operation of the
HMI.
NEMA Rating
The HMI is rated for NEMA 4 (indoor) or IP65/IP66 installations. This
means that when the HMI is properly mounted to a NEMA 4 panel or
other NEMA 4 rated enclosure, the front enclosure of the HMI will
provide protection to the inside of the panel from splashing water, wind-
blown dust, rain, or hose-directed water. The HMI must be installed
according to the instructions in this manual to be properly sealed.

4 HMI5000B Installation Guide
1010-1051 Rev 00 www.maplesystems.com
Environmental Considerations
The HMI is designed to operate in temperatures from 0° to
50°C (32° to 122°F). It is intended for indoor installations and may not be
suitable for use in certain outdoor applications. Avoid installing the HMI
in environments with severe mechanical vibration or shocks. Do not
install the HMI in enclosures with rapid temperature variations or high
humidity. Either case will cause condensation of water inside the device
and eventual damage to the HMI.
Warning: Do not operate the HMI in areas subject to explosion
due to flammable gases, vapors, or dusts.
Warning: If wiring can potentially be exposed to lightning or
power surges, use appropriate surge suppression devices.
Safety Precautions
Please observe the following precautions and ensure compliance with all
local and national electrical standards when installing the HMI. Failure to
comply with these restrictions could result in loss of life, serious personal
injury, or equipment damage.
Warning: Do not connect the HMI to an AC power source. This
will cause permanent damage to the HMI.
Warning: A Hard-wired EMERGENCY STOP should be fitted in
any system using an HMI to comply with ICS Safety
Recommendations.
Warning: Do not attempt to use a DC power supply that does
not meet the HMI’s power requirements. This may cause
malfunction or permanent damage to the HMI.
Warning: Do not power the HMI with a DC power supply used
for inductive loads or for input circuitry to the programmable logic
controller. Severe voltage spikes caused by these devices may
damage the HMI.

HMI5000B Installation Guide 5
1010-1051 Rev 00 www.maplesystems.com
Control Panel Design Guidelines
Pay careful attention to the placement of system components and
associated cable routing. This can significantly enhance the performance
and integrity of the control application.
Cable Routing and Noise Immunity
Follow these guidelines when routing cables to the HMI:
Always route the HMI communication cable and the power cable
away from any AC voltage or rapidly switching DC control lines.
Never bundle the HMI cables together with 120VAC power wires
or with relay wiring.
Try to keep at least 8 inches (20 cm) of separation between the
HMI cables and other power wiring. If voltages greater than
120VAC are used in the system, greater separation is required.
If the HMI cables must come near AC wiring, make sure they
cross at 90 degrees.
Run AC power wires in a separate grounded conduit to reduce
electrical noise interference.
Keep the cable lengths for the HMI as short as possible. Do not
coil excess cable and place it next to AC powered equipment.
Cover any equipment used in the enclosure that operates at high
frequency or high current levels with a grounded metal shield.
Power Supply Selection
The power supply used to power the HMI should provide an output of
+24 VDC ±20% measured at the HMI power connector. A 24VDC
regulated power supply dedicated to the HMI is recommended. Use a
power supply with adequate current rating. A power line filter installed at
the AC input to the HMI power supply is highly recommended as a
safeguard against conducted RF noise, which is often present on factory
power lines. The wires connecting the output of the power line filter to the
power supply should be kept as short as possible to minimize any
additional noise pickup. The case of the power line filter should be
connected to a quiet earth ground. The power line filter should have a
current rating of at least 3 Amps with common mode and differential
mode attenuation. In applications that may have high frequency noise
present, a resistor (~1 MΩ) and capacitor (~4700 pF) should be used in
parallel to clean earth ground on the DC output of the power supply.
Do not use the power supply used to provide power to the HMI to power
switching relays, solenoids, or other active devices.

6 HMI5000B Installation Guide
1010-1051 Rev 00 www.maplesystems.com
Figure 1: Typical Panel Layout
PLC/Host
Ground wires
HMI is
grounded to
control panel
Ground strap
Quiet ground
(isolated)
AC
Power
Line
Filter
HMI
Power
Supply
Shielded
power cable
Control panel is
tied to a reliable
earth ground
1
3
4
5
(rear side)
HMI5040B1
(rear side)
HMI5100BN
2
1. Also HMI5040BN, HMI5070B, and HMI5070BN
2
3

HMI5000B Installation Guide 7
1010-1051 Rev 00 www.maplesystems.com
Control Panel Grounding
The control panel must be connected to a good, high-integrity earth
ground both for safety considerations and shielding purposes. Maple
Systems cannot overemphasize the importance of good grounding.
Failure to use good grounding procedures during installation may cause
sporadic malfunction of the HMI.
Connect the HMI chassis ground terminal to a reliable earth ground with
a low-resistance path. Refer to Figure 1:
Route all earth ground wires that lead from the HMI, the PLC, the
power supply, and the line filter to a central earth ground point such as a
barrier strip. This will ensure that no ground current from one device
influences the operation of the other devices.
Connect the HMI chassis ground terminal to the control panel using a
heavy-gauge short braided cable (#14 AWG) or ground wire to minimize
resistance. Then, make sure the panel is properly grounded to a clean
earth ground.
Note:If the control panel is made of a non-conductive material, it is
essential that the chassis ground terminal of the HMI is connected to
a clean earth ground point located close to the panel.
Connect the power cable’s shield wire to the HMI’s chassis ground
terminal.
Connect the control panel to earth ground using a copper grounding
rod close to the HMI and control panel.
Hinged doors on control panels do not provide a long-term electrical
connection to the rest of the enclosure. Corrosion develops over time
and prevents good electrical contact. For this reason, a separate wire
braid should be installed from the hinged control panel to the rest of the
enclosure.
For a more in-depth overview of ground wiring techniques, refer to
Technical Note #1027, “Ground Wiring and Electrical Noise Reduction”in
the Technical Notes section of the Maple Systems website.
Installation
It is necessary to follow all installation procedures described in this
chapter for electrical noise immunity and CE compliance. The Maple
Systems HMI is designed to connect easily to a PLC. External rear
connectors provide quick connections for power, communications and
programming wiring.

8 HMI5000B Installation Guide
1010-1051 Rev 00 www.maplesystems.com
Connect the HMI to Power
Use the 3-position connector supplied with the HMI to provide power to
the HMI. The power cable for the HMI should be 18AWG, 2-conductor
wire with a shield drain wire and protective shield (foil/braid). Cable (P/N
6030-0009) may be purchased by the foot from Maple Systems for
constructing power cables.
Always run the DC ground wire directly back to the signal return of the
power supply. Do not use the chassis ground wire as the signal return.
Caution: To prevent possible damage to the HMI, wait ten
seconds after removing power from the HMI before applying
power again.
To connect the HMI to power:
1. Route the power cable from the HMI to the power supply. The power
cable should not be any longer than necessary.
2. Install the cable wires, referencing the chart below (with colors
shown for Maple Systems Cable 6030-0009):
a. Strip the power cable shield to expose 2” of the black and red
wires.
b. Strip about ¼” of insulation from the black and red wires.
c. Connect the red wire to the positive (+) input of the HMI power
connector and the 24V DC positive (+) output of the power
supply.
d. Connect the black wire to the negative (–) input of the HMI power
connector and the 24V DC negative (–) output of the power
supply.
e. Connect the power cable shield wire to the HMI power connector
FG or ⏚input. Connect the other side to chassis ground.
Wire Color
Power Supply Output
HMI Input
Red
+
+
Black
–
–
Shield
Chassis ground
FG or ⏚
Note: The power connector on the HMI uses a 3-position terminal
block with screw-down clamps. Lugs are not required.

HMI5000B Installation Guide 9
1010-1051 Rev 00 www.maplesystems.com
Panel Preparation
To provide a NEMA 4 seal, a metal panel or mounting surface that does
not flex more than 0.010” is required. Thin panels or surfaces may bow
between the mounting clamps and not form a seal with the gasket.
Allow sufficient clearance around the unit for the mounting hardware and
cable connections. Cutout dimensions for each particular HMI model are
available for print and download from the Support Center-Dimensional
Drawings section of the Maple Systems website.
The area of the panel or mounting surface where the gasket comes into
contact must be flat and free of scratches, pits, and other features that
prevent the gasket from sealing properly. If the panel or mounting
surface is not uniform, thick, flat, stiff, or smooth enough, then a sealant
such as silicone may be required.
Note: Clean and deburr the panel cutout before the HMI is installed.
Mount the HMI to the Panel
Note: The clamps for some models may be slightly different than
shown here, but operate essentially the same way.
Steps:
1. Prepare the clamps for the HMI by inserting the screws into the
clamp as shown above. Position the screws so that the ends don’t
protrude past the clamp edge.
2. Set the HMI in the panel cutout and hold it in place until all clamps
are in position.
3. Tighten the screw clamps in an even pattern until the unit is secure.
Recommended torque: 3.5 in/lbs.
Caution: Do not over-tighten the screws; the overlay may warp
or the housing may get damaged.

10 HMI5000B Installation Guide
1010-1051 Rev 00 www.maplesystems.com
Configuration Wiring
To configure the HMI using the EZwarePlus software, use the Ethernet
Configuration Cable (P/N 7431-0104) or USB Configuration Cable (P/N
7431-0119).
HMI Model
Configuration Cable
P/N 7431-0104
Ethernet
(Crossover)
P/N 7431-0119
Micro USB
HMI5040B, HMI5070B
X
HMI5040BN, HMI5070BN,
HMI5100BN
X
Ethernet
If using a switch or router between the PC and the HMI, use a straight-
through or crossover cable as required by the switch or router.
In order to download a project to the HMI over Ethernet, the HMI must be
assigned a unique IP address that is on the same subnet as the
development PC.
Follow these steps to enter the System Settings menu and assign the
HMI an IP address:
1. Apply power to the HMI.
2. Click the arrow icon located in the lower-right corner of the screen.
3. Click the gear icon to enter the system settings menu
4. When prompted, enter the system password (default: 111111).
5. Navigate to the Network tab.
6. Enter the desired IP address, or select Obtain an IP Address
Automatically to enable DHCP.
7. Click Apply to save the changes, and OK to exit the system settings
menu.
8. The updated IP address will appear in the system information
window, also accessed via the arrow icon. For more information on
Ethernet configuration options, please refer to the EZwarePlus
Programming Manual.

HMI5000B Installation Guide 11
1010-1051 Rev 00 www.maplesystems.com
USB
A USB driver (included with the EZwarePlus software) must be installed
when downloading from the PC to the HMI via USB connection.
Caution: When connecting two powered devices via USB, a
difference in potential can exist between the ground reference on
each device. If there is a difference in ground potential (voltage),
making a connection via a USB cable can complete a ground
loop that may damage the HMI and PC. The Maple Systems
Micro USB Configuration Cable (P/N 7431-0119) is
recommended for connecting the HMI to the PC. The shield is
not connected between the two ends of the cable, which will
prevent a potentially damaging ground loop from occurring
between the devices. Please refer to Page 6 for proper wiring
instructions.
Note: The USB Host port is designed for data storage only. If
connecting a USB hard drive, power the drive with its own power
supply. Do not charge any device from the USB port.
Maintenance
Fusing Requirements
If the display does not come on within two seconds of power up, remove
power. An internal fuse will prevent damage if the polarity of the DC
power is incorrect. Check wiring to ensure proper connections and try to
power up again
Serial Port Connections
The following diagrams indicate the proper pin connections for the serial
ports of the HMI.

12 HMI5000B Installation Guide
1010-1051 Rev 00 www.maplesystems.com
Serial Port Pinouts
DE9P
HMI5040B
Pin# COM1
[RS-485 2 wire] COM1
[RS-485 4 wire] COM1
[RS-232] COM3
[RS-485 2 wire]
1 Data- RX-
2 Data+ RX+
3 TX-
4 TX+
5GND
6 TXD
7 Data-
8 Data+
9RXD
HMI5040BN
Serial Port Pinouts (cont.)
DE9P
HMI5070B
Pin# COM1
[RS-232] COM2
[RS-485 4 wire] COM2
[RS-485 2 wire]
1 RX- Data-
2 RX+ Data+
3 TX-
4 TX+
5GND
6 TXD
7RTS
8CTS
9 RXD
HMI5070BN

HMI5000B Installation Guide 13
1010-1051 Rev 00 www.maplesystems.com
DE9S DE9P
HMI5100BN
Pin# COM2
[RS-485 2 wire]
COM2
[RS-485 4 wire]
COM3
[RS-485 2 wire]
1 Data- RX-
2 Data+ RX+
3 TX-
4 TX+
5 GND
6 Data-
7
8
9 Data+
Pin# COM1
[RS-232] COM3
[RS-232]
1
2 RXD
3 TXD
4
5 GND
6
7RTS TXD
8CTS RXD
9GND
Note: COM2 [RS-485 2W] and COM3 [RS-485 2W] support the
Siemens MPI 187.5K multi-point interface. However, only one COM
port can be used with the Siemens MPI interface at a time.
Note: COM1 RS232 RTS/CTS and COM3 RS232 cannot be used
simultaneously.

14 HMI5000B Installation Guide
1010-1051 Rev 00 www.maplesystems.com

HMI5000B Installation Guide 15
1010-1051 Rev 00 www.maplesystems.com

16 HMI5000B Installation Guide
1010-1051 Rev 00 www.maplesystems.com
© 2017 Maple Systems Inc. All rights reserved.
Maple Systems Inc.
808 134th Street SW, Suite 120
Everett, WA 98204-7333
Phone: (425) 745-3229
Web: www.maplesystems.com
This manual suits for next models
5
Table of contents
Other Maple Systems Touch Terminal manuals
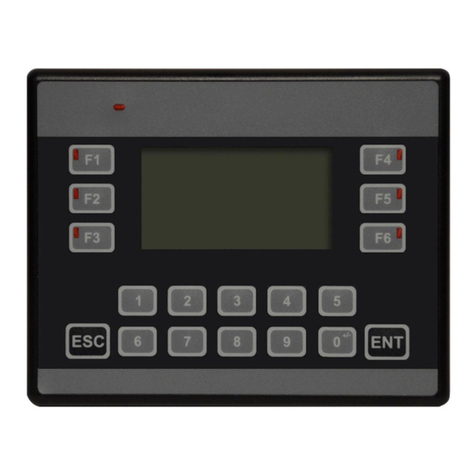
Maple Systems
Maple Systems HMC7030A-M User manual
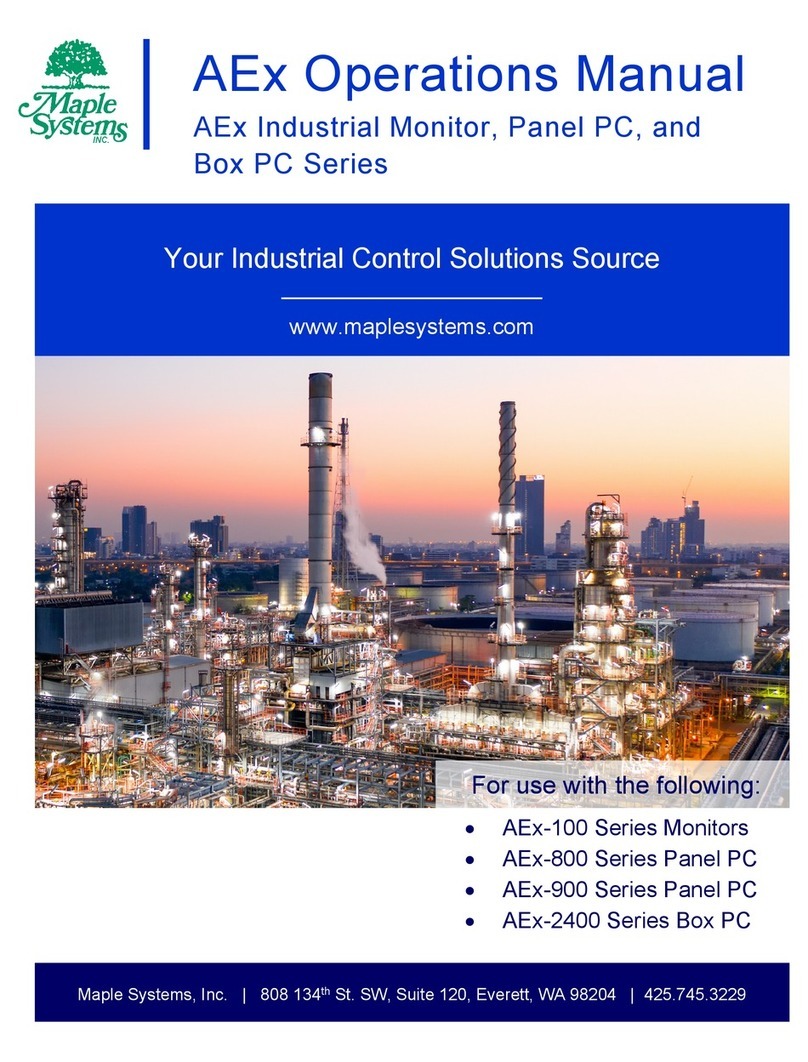
Maple Systems
Maple Systems AEx-100 Series User manual
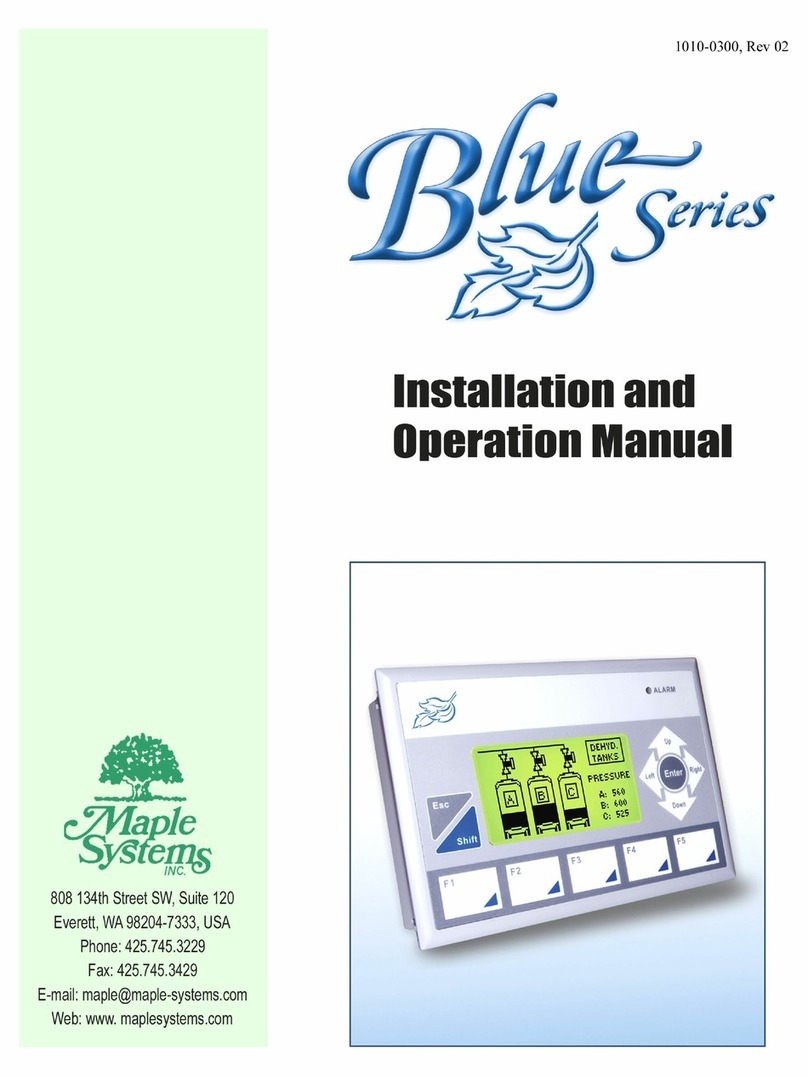
Maple Systems
Maple Systems Blue Series User manual
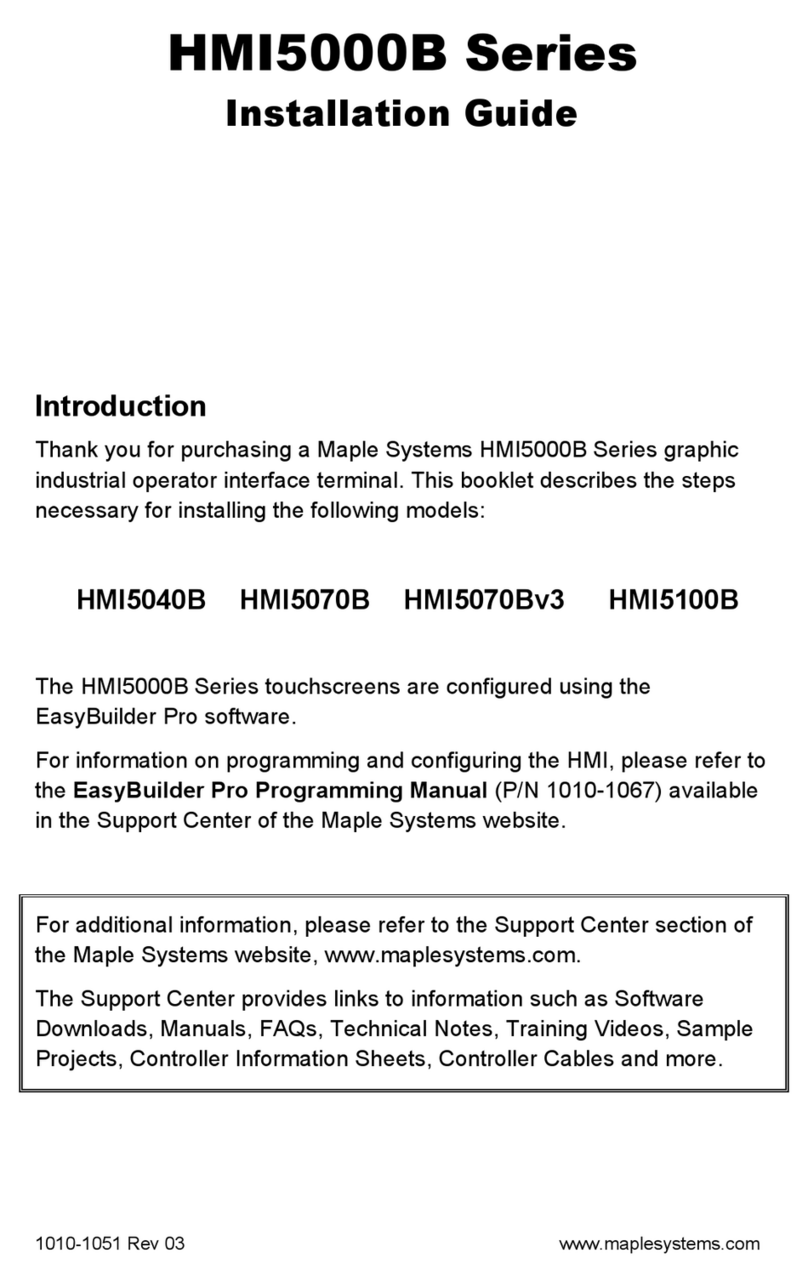
Maple Systems
Maple Systems HMI5070Bv3 User manual
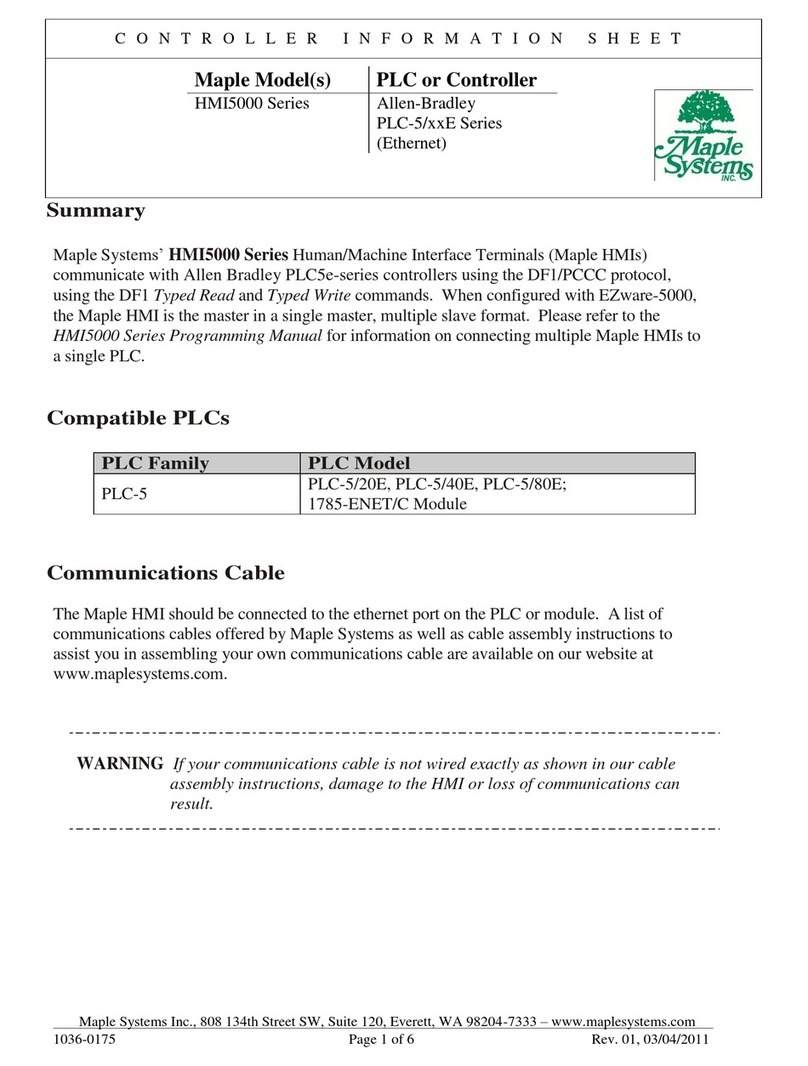
Maple Systems
Maple Systems HMI5000 Series User manual
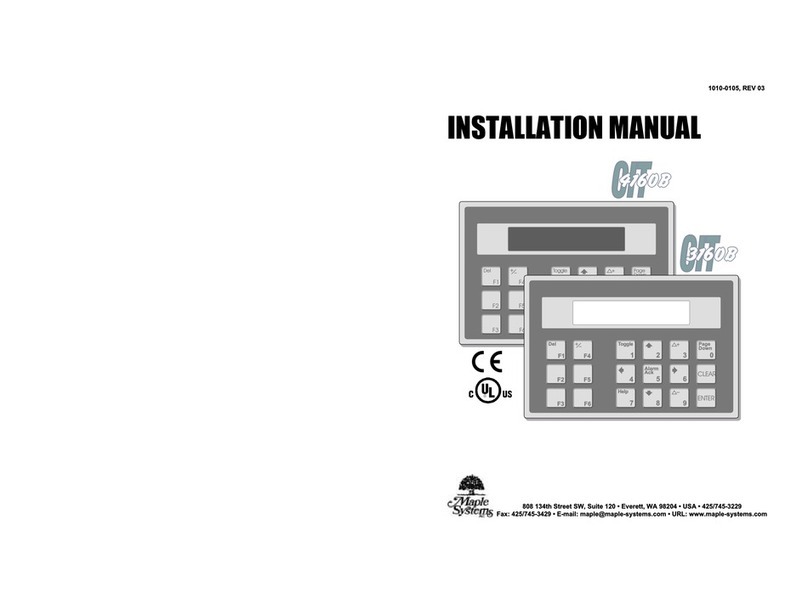
Maple Systems
Maple Systems OIT 3160B User manual

Maple Systems
Maple Systems Silver Series User manual
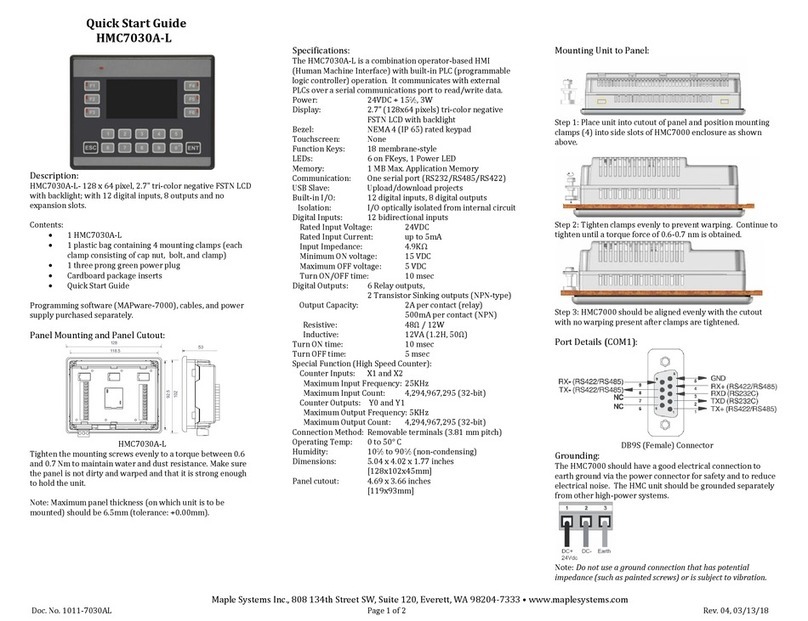
Maple Systems
Maple Systems HMC7030A-L User manual
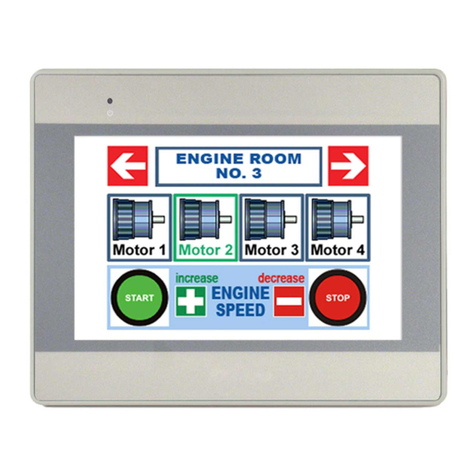
Maple Systems
Maple Systems HMI5000L Series User manual