Marathon TSC 900 Service manual

9087A –198th Street, Langley, BC Canada V1M 3B1 Telephone (604) 888-0110
TSC 900
TRANSFER SWITCH CONTROLLER
INSTALLATION, OPERATING &
SERVICE MANUAL
Part ID 013190 PM0151 REV 1 15/10/08

9087A –198th Street, Langley, BC Canada V1M 3B1 Telephone (604) 888-0110

TSC 900 TRANSFER SWITCH CONTROLLER
PM 151 REV 1 15/10/08 Thomson Power Systems
TABLE OF CONTENTS
1. INTRODUCTION 1
1.1. PRODUCT REVISION HISTORY 1
1.2. GENERAL DESCRIPTION 1
2. INSTALLATION 2
2.1. GENERAL INFORMATION 2
2.2. NOTES TO INSTALLER 3
2.3. AC VOLTAGE SENSING INPUT 4
2.4. AC CURRENT SENSING INPUT 4
2.5. AC CONTROL POWER INPUT 5
2.6. AUXILIARY DC CONTROL POWER INPUT 5
2.7. PROGRAMMABLE INPUTS 5
2.8. OUTPUTS 5
2.9. EXTERNAL ATS CONTROL WIRING 5
2.10. REMOTE START CONTACT FIELD WIRING 6
2.11. COMMUNICATION CABLE INSTALLATION 6
2.12. DIELECTRIC TESTING 7
3. DESCRIPTION 8
3.1. GRAPHICAL HMI CONTROLLER (GHC) DISPLAY HARDWARE 9
3.2. SWITCH CONTROL UNIT (SCU) HARDWARE 10
3.3. ATS OPERATION MODE DESCRIPTIONS 12
3.4. AUTOMATIC SEQUENCE OF OPERATION 14
3.4.1. OPEN TRANSITION TRANSFER 14
3.4.2. CLOSED TRANSITION TRANSFER 15
3.4.3. AUTOMATIC LOAD SHED OPERATION 17
3.4.4. TEST MODE 18
3.4.5. ABNORMAL SEQUENCE OF OPERATION 19
3.5. GHC DISPLAY MAIN MENU PAGE DESCRIPTIONS 20
3.5.1. HOME PAGE 21
3.5.2. UTILITY METERING PAGE 22
3.5.3. GENERATOR METERING PAGE 22

TSC 900 TRANSFER SWITCH CONTROLLER
PM 151 REV 1 15/10/08 Thomson Power Systems
3.5.4. LOAD METERING PAGE 23
3.5.5. ALARMS PAGE 24
3.5.6. ALARMS LOG PAGE 25
3.5.7. EVENTS LOG PAGE 25
3.5.8. SYNC PAGE 26
3.5.9. SCHEDULER PAGE 27
3.5.10. SETTINGS PAGE 27
3.5.11. SYSTEM PAGE 28
3.6. GHC DISPLAY SYSTEM SUBMENU PAGE DESCRIPTIONS 29
3.6.1. IMPORT/EXPORT DATABASE 29
3.6.2. TIME/DATE SETUP 29
3.6.3. MANAGE USERS 30
3.6.4. SYSTEM INFORMATION 30
3.6.5. INPUT MAPPING 31
3.6.6. OUTPUT MAPPING 31
3.6.7. LOGS 32
3.6.8. COM STATUS 32
4. OPERATING INSTRUCTIONS 33
4.1. GHC SCREEN PAGE NAVIGATION 33
4.2. ON LOAD TEST INSTRUCTIONS (UTILITY POWER FAIL SIMULATION) 34
4.3. OFF LOAD TEST INSTRUCTIONS (GENERATOR NO LOAD TEST) 35
4.4. TIMED TEST INSTRUCTION 36
4.5. OPEN/CLOSED TRANSITION TRANSFER OPERATION 37
4.5.1. OPEN TRANSITION IN-SYNC TRANSFER OPERATION (MODEL X) 38
4.5.2. CLOSED TRANSITION OPERATION (MODEL 3 & 4) 38
4.6. TRANSFER FAIL ALARM RESET 39
4.7. TIMER BYPASS 40
4.8. MANUAL UTILITY RETRANSFER CONTROL 41
4.9. SERVICE DISCONNECT MODE 41
4.10. PHASE UNBALANCE PROTECTION ALARM RESET 42
4.11. TRANSFER HALTED ALARM RESET 43
5. PROGRAMMING INSTRUCTIONS 44
5.1. PASSWORD SECURITY DESCRIPTION (USERS ADMIN) 44
5.2. USER LOGIN PROCEDURE 45

TSC 900 TRANSFER SWITCH CONTROLLER
PM 151 REV 1 15/10/08 Thomson Power Systems
5.3. ADMINISTRATOR PASSWORD MANAGEMENT PROCEDURE 46
5.4. SYSTEM TIME/DATE ADJUSTMENT 47
5.5. VOLTAGE CHANGE PROCEDURE 48
5.6. EXERCISE TIMER SETUP 49
5.6.1. ADDING NEW EXERCISE SCHEDULE EVENT 50
5.6.2. EDITING EXISTING EXERCISE SCHEDULE EVENT 50
5.7. PROGRAMMABLE INPUT MAPPING 51
5.8. PROGRAMMABLE OUTPUT MAPPING 54
5.9. SYSTEM SETTINGS 58
5.9.1. SYSTEM PHASES 58
5.9.2. SYSTEM VOLTAGE 58
5.9.3. SYSTEM FREQUENCY 58
5.9.4. PHASE ROTATION REVERSED 58
5.9.5. RATED GENERATOR POWER 59
5.9.6. CT RATIO (CURRENT TRANSFORMER) 59
5.9.7. PT RATIO (POTENTIAL TRANSFORMER) 59
5.9.8. LOAD NAME 59
5.9.9. SOURCE 1 (UTILITY) NAME 59
5.9.10. SOURCE 2 (GEN) NAME 59
5.9.11. APPLICATION MODEL 59
5.9.12. SWITCH OPERATION 59
5.9.13. SWITCH MODEL 60
5.9.14. TRANSFER SWITCH MECHANISM OPERATION TIME 60
5.10. OPTION SETTINGS 60
5.10.1. CURRENT METERING 60
5.10.2. GEN (SOURCE 2) COMMIT TO TRANSFER 60
5.10.3. ENABLE LOAD SHED ON UNDER FREQUENCY 60
5.10.4. ENABLE LOAD SHED ON OVER POWER 61
5.10.5. HALT OPERATION ON REVERSED SOURCE 61
5.10.6. ENABLE FAIL TO UNLOAD ALARM (CTTS MODEL 4) 61
5.10.7. TRIP UTILITY (SRC 1) WHEN CLOSED TRANSITION INHIBIT ACTIVATED 61
5.10.8. HALT TRANSFER ON FAIL TO EXTERNAL SYNC CHECK 61
5.10.9. MANUAL UTILITY RETRANSFER CONTROL 62
5.10.10. FORCE TRANSFER 62
5.10.11. GHC SLEEP MODE TIMEOUT 63
5.10.12. LOAD POWER METERING 63
5.10.13. MODBUS RTU 63
5.10.14. MODBUS TCP/IP 63
5.10.15. ENABLE SECURITY BYPASS 63

TSC 900 TRANSFER SWITCH CONTROLLER
PM 151 REV 1 15/10/08 Thomson Power Systems
5.10.16. FAIL TO AUTO SYNC ALARM 63
5.10.17. OPEN TRANSITION IN-SYNC TRANSFER (ATS MODEL X) 64
5.10.18. CLOSED TRANSITION TRANSFER (CTTS MODEL 3 & 4) 64
5.10.19. NEUTRAL DELAY BYPASS 64
5.10.20. REVERT TO OPEN TRANSITION 65
5.10.21. ENABLE TRANSFERS TO UTILITY 65
5.10.22. ENABLE TRANSFERS TO GENERATOR 65
5.10.23. EXTENDED PARALLEL TRANSFER (CTTS MODEL 4) 66
5.11. DELAY SETTINGS 67
5.11.1. UTILITY RETURN DELAY 67
5.11.2. GEN COOL DOWN DELAY 67
5.11.3. GEN START DELAY 67
5.11.4. GEN WARM UP DELAY 67
5.11.5. GEN COMMIT TO TRANSFER DELAY 67
5.11.6. DEPART DELAY 67
5.11.7. TRANSFER FAIL DELAY 68
5.11.8. TRANSFER MAX ERROR CONDITION DELAY 68
5.11.9. TIMER GUARD DELAY 68
5.11.10. TRANSFER FIND NEUTRAL DELAY 68
5.11.11. TRANSFER NEUTRAL DELAY 68
5.11.12. TRANSFER PRE DELAY (LDC) 68
5.11.13. TRANSFER POST DELAY (LDC) 69
5.11.14. DISCONNECTION RESUME TIME 69
5.11.15. LOAD SHED INITIATE DELAY 69
5.11.16. LOAD SHED UNSHED DELAY 69
5.11.17. TRIP RETRY ON/OFF PULSE TIME (SRC1&2) 69
5.11.18. TRIP RETRY DURATION TIMER (SRC1&2) 70
5.11.19. CLOSE RETRY ON/OFF PULSE TIME (SRC1&2) 70
5.11.20. CLOSE RETRY DURATION TIMER (SRC1&2) 70
5.12. UTILITY/GEN SET POINTS (VOLTAGE/FREQUENCY) 71
5.12.1. UNDER VOLTAGE DELAY (DROPOUT) 71
5.12.2. UNDER VOLTAGE DROPOUT 71
5.12.3. UNDER VOLTAGE PICKUP 71
5.12.4. OVER VOLTAGE DELAY (PICKUP) 71
5.12.5. OVER VOLTAGE DROPOUT 71
5.12.6. OVER VOLTAGE PICKUP 72
5.12.7. UNBALANCED VOLTAGE LATCH 72
5.12.8. PHASE UNBALANCE DELAY (PICKUP) 72
5.12.9. PHASE UNBALANCE DROP OUT 72
5.12.10. PHASE UNBALANCE PICK UP 72
5.12.11. UNDER FREQUENCY DELAY (DROPOUT) 72

TSC 900 TRANSFER SWITCH CONTROLLER
PM 151 REV 1 15/10/08 Thomson Power Systems
5.12.12. UNDER FREQUENCY DROPOUT 73
5.12.13. UNDER FREQUENCY PICKUP 73
5.12.14. OVER FREQUENCY DELAY (PICKUP) 73
5.12.15. OVER FREQUENCY DROPOUT 73
5.12.16. OVER FREQUENCY PICKUP 73
5.12.17. SOURCE VOLTAGE BLACKOUT DELAY (DROPOUT) 73
5.12.18. SOURCE VOLTAGE BLACKOUT DROPOUT 73
5.12.19. SOURCE VOLTAGE BLACKOUT PICKUP 74
5.12.20. PHASE REVERSAL DELAY (PICKUP) 74
5.12.21. PHASE REVERSAL DROP OUT 74
5.12.22. PHASE REVERSAL PICK UP 74
5.12.23. GEN MUST START DELAY 74
5.13. LOAD VOLTAGE SET POINTS 74
5.13.1. LOAD VOLTAGE BLACKOUT DELAY (DROPOUT) 75
5.13.2. LOAD VOLTAGE BLACKOUT DROPOUT 75
5.13.3. LOAD VOLTAGE BLACKOUT PICKUP 75
5.14. LOAD SHED SET FREQUENCY & POWER POINTS 75
5.14.1. LOAD SHED POWER (kW) DELAY (PICKUP) 76
5.14.2. LOAD SHED POWER (kW) DROP OUT 76
5.14.3. LOAD SHED POWER (kW) PICK UP 76
5.14.4. LOAD SHED FREQUENCY PICK UP 76
5.14.5. LOAD SHED FREQUENCY DROP OUT 76
5.15. IN-SYNC TRANSFER SET POINTS 76
5.15.1. CLOSED TRANSITION MAX OVERLAP TIMER 76
5.15.2. IN-SYNC WAIT DELAY 77
5.15.3. EXTERNAL SYNC CHECK WAIT DELAY 77
5.15.4. SOURCE FREQUENCY DIFFERENTIAL HIGHER THRESHOLD 77
5.15.5. SOURCE FREQUENCY DIFFERENTIAL LOWER THRESHOLD 77
5.15.6. SOURCE VOLTAGE DIFFERENTIAL HIGHER THRESHOLD 77
5.15.7. SOURCE VOLTAGE DIFFERENTIAL LOWER THRESHOLD 77
5.15.8. FAIL TO UNLOAD TIMER (CTTS MODEL 4) 78
6. FACTORY DEFAULT PROGRAMMING 79
7. TSC 900 TYPICAL CONNECTION DIAGRAM 80
8. TSC 900 WIRING PIN CONNECTIONS 81
9. TROUBLESHOOTING 82
10. REPLACEMENT PARTS 85

TSC 900 TRANSFER SWITCH CONTROLLER
PM 151 REV 1 15/10/08 Thomson Power Systems
11. PRODUCT RETURN POLICY 86
12. NOTES 87

TSC 900 TRANSFER SWITCH CONTROLLER
PM 151 REV 1 15/10/08 Thomson Power Systems
1
1. INTRODUCTION
1.1. PRODUCT REVISION HISTORY
The following information provides an historical summary of changes made to this product
since the original release.
SCU Firmware Version
621, 15/04/07
Original Release
867, 15/10/03
Add Closed Transition Transfer Capability, Misc
Feature Enhancements & Bug Fixes
GHC Firmware Version
1.0.0.0 15/04/07
Original Release
1.1.0.xxxxx 15/10/03
Add Closed Transition Transfer Capability, Misc
Feature Enhancements & Bug Fixes
Operating & Service Manual Version
Rev 0 15/04/07
Original release
Rev 1 15/10/08
Add Closed Transition Transfer Capability, Misc
Feature Enhancements & Bug Fixes
Related Product Instruction Manuals
TSC 900 ModbusTM Communication, PM152
TS 870 Instruction Manual, PM062
TS 870 Quick Start Manual, PM150
TS 880 Instruction Manual, PM064
Contact Thomson Power Systems, to obtain these instruction manuals. A soft-copy of the
most current versions of these manuals are available at www.thomsonps.com.
1.2. GENERAL DESCRIPTION
The TSC 900 controller utilizes multiple 32 bit microprocessor-based design technology, which
provides high accuracy for all voltage sensing and timing functions. Digital Signal Processing
(DSP) technology is utilized for all voltage, frequency and current sensing. The TSC 900 is
factory configured to control all the operational functions and display features of the automatic
transfer switch. All features of the TSC 900 are fully programmable from the front panel color
graphical touchscreen display and are security password protected. The graphical
touchscreen display screen provides a user-friendly operator interface with many display
options available. The microprocessor design provides many integrated standard features,
which were previously only available as add-on optional features.

TSC 900 TRANSFER SWITCH CONTROLLER
PM 151 REV 1 15/10/08 Thomson Power Systems
2
2. INSTALLATION
CAUTION!!!
This equipment contains static-sensitive parts. Please observe the following
anti-static precautions at all times when handling this equipment. Failure to
observe these precautions may cause equipment failure and/or damage.
The following precautions must be observed:
Discharge body static charge before handling the equipment (maintain exposed body contact
with a properly grounded surface while handling the equipment, a grounding wrist strap
can/should also be utilized).
Do not touch any components on the printed circuit board with your hands or any other
conductive equipment.
Do not place the equipment on or near materials such as Styrofoam, plastic and vinyl. Place
the equipment on properly grounded surfaces and only use an anti-static bag for transporting
the equipment.
2.1. GENERAL INFORMATION
NOTE:
Installations should be done in accordance
with all applicable electrical regulation
codes as required.
The following installation guidelines are provided for general information only pertaining to
typical site installations. For specific site installation information, consult Thomson Power
Systems as required. NOTE: Factory installations of THOMSON POWER SYSTEMS

TSC 900 TRANSFER SWITCH CONTROLLER
PM 151 REV 1 15/10/08 Thomson Power Systems
3
supplied transfer switches that have been tested and proven may deviate from these
recommendations.
2.2. NOTES TO INSTALLER
If the transfer switch has programmable/multi-tap system voltage capability (refer to electrical
schematic), confirm the transfer switch has been configured for the system voltage.
WARNING
Failure to confirm and match transfer
switch voltage with the system voltage
could cause serious equipment damage.
If the transfer switch requires reconfiguring, the TSC 900 controller will also require
reprogramming.
CAUTION!!!
Qualified personnel must complete all installation and/or service work performed
only. Failure to do so may cause personal injury or death.

TSC 900 TRANSFER SWITCH CONTROLLER
PM 151 REV 1 15/10/08 Thomson Power Systems
4
2.3. AC VOLTAGE SENSING INPUT
The TSC 900 can accept direct AC voltage sensing inputs on the generator, utility and load
from 120-600VAC (nominal). Sources up to 600VAC (phase to phase) and can connected wye
or delta with grounded or ungrounded neutral without the need for additional sensing
transformers. The TSC 900 voltage sensing can support the following types of electrical
systems:
2.4. AC CURRENT SENSING INPUT
The TSC 900 can accept 4 x 0-5Aac current inputs from the secondary windings of current
transformers (CT’s). CT’s are to be connected on the load side of the ATS (Phase A,B,C & N).
Wiring of CT primary and secondary windings must be done in strict accordance with
schematic diagram to ensure the correct phasing on 3 phase systems.
WARNING
Do not unplug any current transformer inputs while
energized as severe high voltages can develop which may
cause personal injury or death.

TSC 900 TRANSFER SWITCH CONTROLLER
PM 151 REV 1 15/10/08 Thomson Power Systems
5
2.5. AC CONTROL POWER INPUT
The TSC 900 requires 120VAC (nominal) control power input voltage. Independent AC control
power is required from both utility and generator supplies via potential transformers. AC
control power is utilized for internal TSC 900 control circuits and external control device loads.
The TSC 900 requires approximately 12VA AC power for internal control circuits. The
maximum external load is limited by output contact ratings (i.e. 10A resistive, 120/250VAC).
Total AC control power requirements for each supply must be determined by adding both
internal and external load requirements.
2.6. AUXILIARY DC CONTROL POWER INPUT
The TSC 900 can be optionally supplied with 24Vdc auxiliary control power input voltage for
applications requiring continuously energized control and display features. The maximum input
power draw is 20Watts. The 24Vdc power must be from a regulated/filtered DC supply with
maximum +-10% voltage range.
2.7. PROGRAMMABLE INPUTS
The TSC 900 provides Qty 16 Programmable Inputs. Each input is activated by external
contact closure to common (i.e. DC Negative ground). Each programmable input can be
independently programmed to different functions. Refer to Programming section for available
features.
2.8. OUTPUTS
The TSC 900 provides the following types of output circuits:
Engine Start Contacts
Qty 2
Isolated Form B contacts (10A, 250VAC Resistive)
Programmable Output Contacts
Qty 8
Isolated Form C contacts (2A, 250VAC Resistive)
Close to Utility Supply
Qty 1
120VAC1, 10A (Resistive) powered output contact
Close to Generator Supply
Qty 1
120VAC1, 10A (Resistive) powered output contact
Trip Utility Supply
Qty 1
120VAC1, 10A (Resistive) powered output contact
Trip Generator Supply
Qty 1
120VAC1, 10A (Resistive) powered output contact
1 NOTE: Output voltage is dependent upon AC control power input voltage.
Interposing relays are required between the TSC 900 outputs and the end device if loads
exceed the output current rating.
2.9. EXTERNAL ATS CONTROL WIRING
As a minimum, all external control wiring to/from the ATS must conform to the local regulatory
authority having jurisdiction on electrical installations. Specific wire sizes listed below are for
typical circuits of distances up to 500ft (150m)1, are as follows:
Utility or Generator Voltage Sensing #14 AWG (2.5mm2)

TSC 900 TRANSFER SWITCH CONTROLLER
PM 151 REV 1 15/10/08 Thomson Power Systems
6
Transfer output signals #14 AWG (2.5mm2)
Remote Start Contact for Engine Controls #14 AWG (2.5mm2)
NOTE: For long control wire runs or noisy electrical environments the control wires
should be twisted & shielded with a suitable drain wire. The shielded cable drain wire
must be grounded at one end only. The drain wire grounding location may vary as
micro-processor controllers generally exist at both ends (engine generator set &
transfer switch) and one may be more susceptible depending on the level of induced
noise. The most susceptible controller will require the shield ground point as close as
possible to the controller. Wire runs from 500ft to 1000ft should be twisted and
shielded and increased to #12 AWG where total loop resistance is greater than 5
ohms.
1For distances exceeding 1000ft. (300m) consult Thomson Power Systems
2.10. REMOTE START CONTACT FIELD WIRING
Field wiring of a remote start contact from a transfer switch to a control panel should conform
to the following guidelines to avoid possible controller malfunction and/or damage.
2.8.1. Remote start contact wires (2 #14 AWG (2.5mm2)) should be run in a separate
conduit (ferromagnetic type) and in all cases separated from any AC wiring.
2.8.2. Avoid wiring near AC power cables to prevent pick-up of induced voltages.
2.8.3. An interposing relay may be required if field-wiring distance is excessively long
(i.e. greater than 1000 feet (300m)) and/or if a remote contact has a resistance
of greater than 5.0 ohms. In extremely noisy environments, the wire run
lengths indicated may not provide reliable operation and can only be corrected
by the use of an interposing relay. The interposing relay is generally installed at
the engine controls and utilizes DC power. It is strongly suggested that the
ground return wire of the interposing relay be used for the interface to the TSC
900 remote start contact, this will ensure integrity of the DC power supply to the
engine generator set controls in the event of a shorted or grounded wire remote
start interface wire.
2.8.4. The remote start contact provided is voltage free (i.e. dry contact). Exposing
the remote start contact to voltage or current levels in excess of its rating will
damage the transfer controller.
2.11. COMMUNICATION CABLE INSTALLATION
Communication cable wiring from the controller’s communication port must be suitably routed
to protect it from sources of electrical interference. Guidelines for protection against possible
electrical interference are as follows:

TSC 900 TRANSFER SWITCH CONTROLLER
PM 151 REV 1 15/10/08 Thomson Power Systems
7
Use high quality, shielded cable only with drain wire grounded at the controller end
only.
Route the communication cable at least 3 M (10’) away from sources of electrical
noise such as variable speed motor drives, high voltage power conductors, UPS
systems, transformers, rectifiers etc.
Use separate, dedicated conduit runs for all communication cables. Do not tightly
bundle communication cables together in the conduit. Conduit should be
ferromagnetic type near sources of possible electrical interference. The entire
length of conduit should be grounded to building earth ground.
When communication cables must cross over low or high voltage AC power
conductors, the communication cables must cross at right angles and not in parallel
with the conductors.
For additional information on protection against electrical interference, contact
THOMSON POWER SYSTEMS factory.
2.12. DIELECTRIC TESTING
Do not perform any high voltage dielectric testing on the transfer switch with the TSC 900
controller connected into the circuit, as serious damage will occur to the controller. All AC
control fuses or control/sensing circuit isolation plugs connected to the TSC 900 must be
removed/disconnected if high voltage dielectric testing is performed on the transfer switch.

TSC 900 TRANSFER SWITCH CONTROLLER
PM 151 REV 1 15/10/08 Thomson Power Systems
8
3. DESCRIPTION
The TSC 900 controller consists of two parts; a front door mounted graphical touch screen display
(GHC), and a switch control unit (SCU) which is mounted inside the transfer switch door. The two
parts are interconnected via a USB 2.0 high speed communication cable which includes DC power.
USB 2.0 Cable
GHC
SCU

TSC 900 TRANSFER SWITCH CONTROLLER
PM 151 REV 1 15/10/08 Thomson Power Systems
9
3.1. GRAPHICAL HMI CONTROLLER (GHC) DISPLAY HARDWARE
The GHC Display is shown as in FIGURE 7. The GHC is interconnected to the SCU via plug-in
USB cable. The main features of the GHC Display are described as follows with reference to
FIGURE 7.
FIGURE# 7
1. RS232 Communication Port #1: This port is utilized for Modbus RTU Serial communication
2. RS232 Communication Port #2: This port is utilized RS232 Serial communication
3. USB Communication Port #1: This port is utilized for communication from GHC to TSC 900
SCU module.
4. Ethernet Communication Port: This port is utilized for Modbus TCP Ethernet communication
5. USB Communication Port #2: This port is utilized for customer use.
6. USB Communication Port #3: This port is utilized for customer use.
7. SD Memory Card Slot: This is used for program operation and memory storage
1
2
3
4
5
6
7

TSC 900 TRANSFER SWITCH CONTROLLER
PM 151 REV 1 15/10/08 Thomson Power Systems
10
3.2. SWITCH CONTROL UNIT (SCU) HARDWARE
The Switch Control Unit internal PCB is shown in the following diagram:
2
1
4
3
5
8
7
9
11
12
13
14
15
16
6
10
17
18

TSC 900 TRANSFER SWITCH CONTROLLER
PM 151 REV 1 15/10/08 Thomson Power Systems
11
The Switch Control Unit (SCU) with case and main I/O connections are detailed in the
following diagram:
1. J9 –24Vdc Auxiliary Control Power
2. J2 –Utility Voltage Sensing (PH A,B,C,N)
3. J3 –Generator Voltage Sensing (PH A,B,C,N)
4. J4 –Load Voltage Sensing (PH A,B,C,N)
5. J5,6,7,8 –Load Current Sensing (PH A,B,C,N)
6. J21 –SCU SD Memory Card (Card Located inside case-not shown)
7. J11a Programmable Output Contacts #1-4
8. J11b Programmable Output Contacts #5-8
9. J12a Programmable Inputs #1-8
10. J12b Programmable Inputs #9-16
11. J10a Engine Start 2 Contact (Single Gen SRC 2)
12. J10b Engine Start 1 Contact (Dual Gen SRC 1)
13. J13 –GHC Aux 5Vdc Power
14. J14- GHC USB Port
15. J15 –RS232 Programming Port
16. J1 –ATS Control
17. SCU Healthy Diagnostic LED
18. Engine Start Outputs On Diagnostic LED
12
10
9
7
11
8
6
18
1
2
3
4
5
16
15
14
13
17

TSC 900 TRANSFER SWITCH CONTROLLER
PM 151 REV 1 15/10/08 Thomson Power Systems
12
3.3. ATS OPERATION MODE DESCRIPTIONS
The TSC 900 has the following main operating modes as described per the table below:
Mode
Description
ATS Mechanism
Control Outputs
Engine Start Output
AUTO
ATS automatically transfers to generator
(source 2) during a utility (source 1) failure and
automatically returns power to utility once
restored
Outputs automatically
operate ATS
mechanism per
automatic sequence of
operation
Output contact closes to start
engine during a utility (source 1)
failure and opens to stop engine
once utility power has transferred
back on load.
OFF
ATS is Out of Service - will not automatically
operate during a utility power failure
Outputs remain in their
last state to keep ATS
in its current position
Output is disabled - engine will not
start during a utility power failure1
MANUAL
ATS is Out of Service -will not automatically
operate during a utility power failure. ATS can
be operated manually for testing or emergency
operation
Outputs de-energize to
allow ATS to be
operated manually
Output is disabled - engine will not
start during a utility power failure1
.Engine will stop if was previously
running
SERVICE
DISCONNECT
ATS transfers to neutral position to disconnect
power to the load. ATS will not automatically
operate during a utility power failure.
Outputs momentarily
energize to move ATS
mechanism to the
neutral position
Output is disabled - engine will not
start during a utility power
failure1.Engine will stop if was
previously running
ON LOAD
TEST
When ONLOAD TEST mode is initiated, a utility
power failure condition will be simulated which
will cause engine to start and ATS will transfer
to generator supply. When TEST mode is
terminated, ATS will transfer back to utility
supply and engine will stop
Outputs automatically
operate ATS
mechanism per
automatic sequence of
operation
Output contact closes to start
engine during the ONLOAD TEST
mode. Output automatically opens
when test mode is terminated and
ATS is back on utility power
OFF LOAD
TEST
When OFF LOAD TEST mode is initiated,
engine will start and run off load. When OFF
LOAD TEST mode is terminated, engine will
stop
Outputs do not change
state unless utility or
generator supply fails
in Off Load test mode
Output automatically closes to start
engine during the OFF LOAD test
mode. Output automatically opens
when test mode is terminated
TIMED TEST
When a TIMED TEST is initiated, the ATS will
perform test per the selected type (i.e. on load
or off load) and time period. The Generator, will
continue to run for the TIMED TEST duration,
then will automatically stop.
Outputs operate ATS
mechanism per
automatic sequence of
operation if
programmed for ON
LOAD TEST operation.
Output contact closes to start
engine during the TIMED TEST
mode. Output automatically opens
when exercise mode is terminated
EXERCISE
SCHEDULE
When an EXERCISE SCHEDULE occurs, the
ATS will perform exercise test on the pre-
selected calendar date and time. The
Generator will operate on load or off load as
selected, and will continue to run for the
Exercise duration period as selected. If a re-
occurring Exercise mode is selected, ATS will
repeat an exercise test based on the calendar
dates and times as selected.
Outputs operate ATS
mechanism per
automatic sequence of
operation if
programmed for ON
LOAD TEST operation.
Output contact closes to start
engine during the EXERCISE test
mode. Output automatically opens
when exercise mode is terminated
1The TSC 900 requires continuous control power (i.e. utility/gen power on, or 24Vdc aux power on) to keep the automatic engine
start output disabled. If control power is de-energized, the engine start output will energize in approximately 3 minutes, once its
internal control power reservoir de-energizes. This in turn will cause a repeating engine start/stop event every 3-4 minutes. To
prevent engine start/stop cycling condition upon loss of control power, the local engine control panel should be selected for the OFF
operating mode.
Table of contents
Other Marathon Controllers manuals
Popular Controllers manuals by other brands
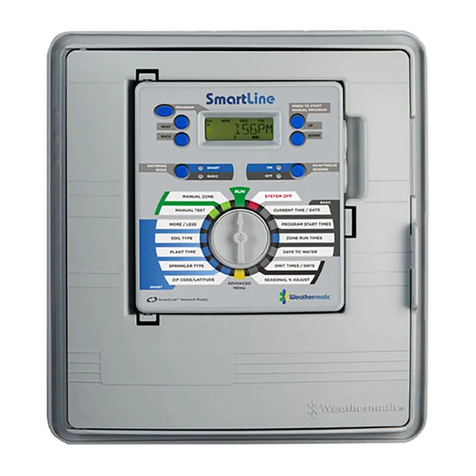
Weathermatic
Weathermatic smartline SL800 owner's manual
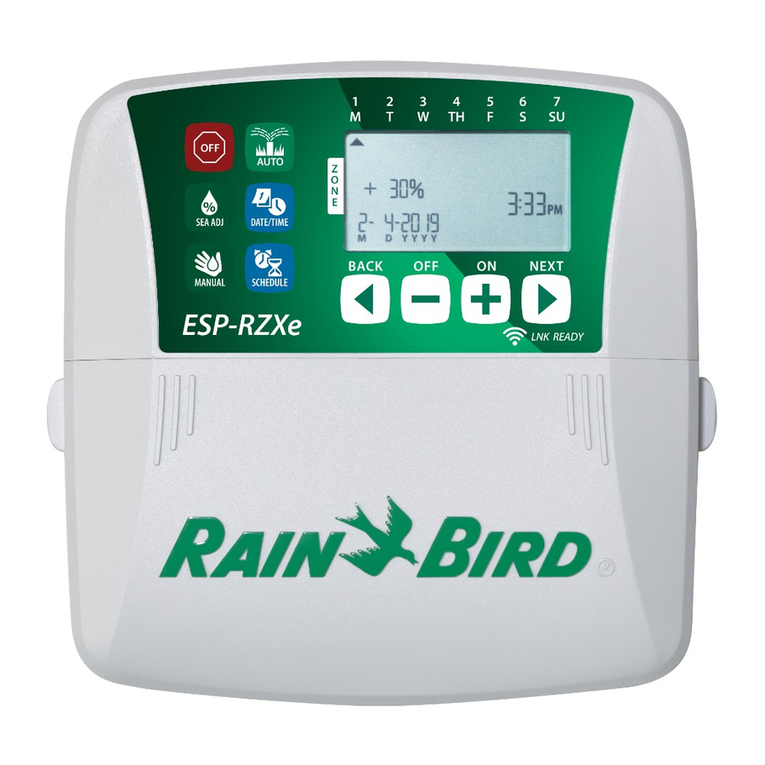
Rain Bird
Rain Bird ESP-RZXe quick start guide
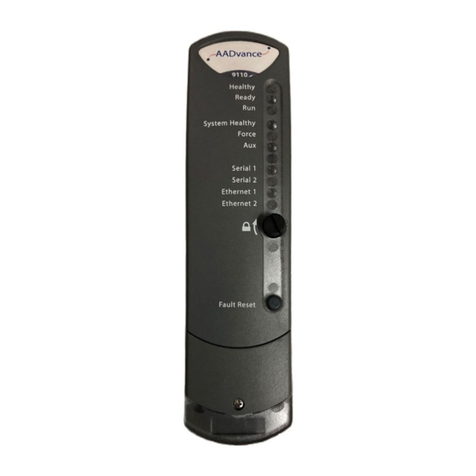
Rockwell Automation
Rockwell Automation Allen-Bradley AADvance T9110 Solutions handbook
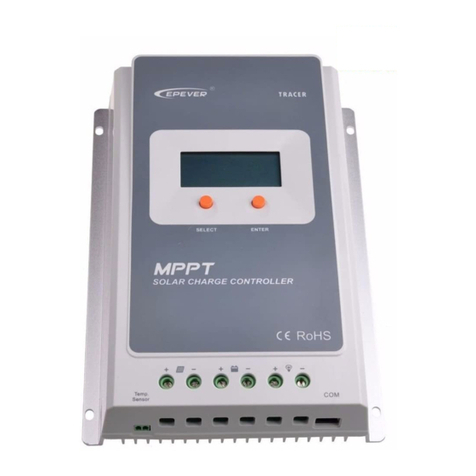
Epever
Epever Tracer1206A user manual
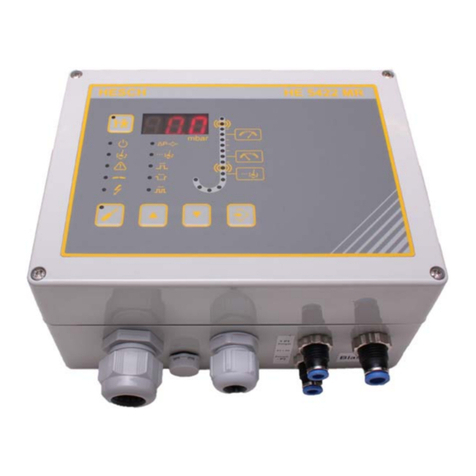
HESCH
HESCH HE 5422 MR operating manual

thomann
thomann Stairville LED Pixel Rail Drive640 MKII user manual