Marq 2102 User manual

HPA2102(RH) 3
This information is needed for your
warranty. Please fax to MARQ c/o
Shawna Sanders after initial installa-
tion. If no date is received, then the
company will use the shipping date for
the date the warranty begins.
Machine# ________________________________________________________
Company Name ___________________________________________________
Company Address__________________________________________________
________________________________________________________________
Phone# __________________________________________________________
Fax# ____________________________________________________________
Date Of Installation ________________________________________________
Purchased From ___________________________________________________
Head of Maintenance _______________________________________________
Warranty Information
PO Box 9063
Yakima, WA 98909
Phone: (509) 966-4300
FAX: (509) 452-3307
Email: [email protected]

HPA2102(RH) 5
Company...................................................................................................................7
Introduction ..............................................................................................................8
Safety........................................................................................................................9
Specifications .........................................................................................................10
Installation ..............................................................................................................11
Leveling &Adjusting Height.................................................................................................. 11
Electrical Connections............................................................................................................ 11
Air Connections...................................................................................................................... 11
Adjusting Air Cylinder Speed................................................................................................. 11
Conveyors ............................................................................................................................... 11
High Performance Adjustable Case Sealer ............................................................12
Machine Operation.................................................................................................13
Components............................................................................................................15
Main Electrical Panel.............................................................................................................. 15
Main Air Prep Unit ................................................................................................................. 16
Main Air Valve .................................................................................................................................. 16
Air Pressure Regulator/Filter/Lubricator.......................................................................................... 16
Solenoid Valves....................................................................................................................... 17
Air Cylinders .......................................................................................................................... 18
Air Cylinder ...................................................................................................................................... 18
Cushion Adjustment Screws ............................................................................................................. 18
Main Drive Unit...................................................................................................................... 19
Flight Bar Assembly ......................................................................................................................... 19
Brake / Clutch Module ..................................................................................................................... 19
Gear Box ........................................................................................................................................... 19
SprocketAnd Chain Drive Assemblies.............................................................................................19
Tol-o-matics ...................................................................................................................................... 19
Sensing Devices...................................................................................................................... 20
Controls ..................................................................................................................21
Power, Buttons, and Switches................................................................................................. 21
Operating Procedures ............................................................................................. 22
Start-up ................................................................................................................................... 22
Normal Shutdown................................................................................................................... 22
Emergency Shutdown ............................................................................................................. 22
Clearing Jams ......................................................................................................................... 23
Changeover ............................................................................................................................. 23
Motorized Adjustments...........................................................................................................23
Table of Contents

6HPA2102(RH)
Table of Contents
Machine Adjustments.............................................................................................24
Side Rail ................................................................................................................................. 24
Arch Assembly ....................................................................................................................... 24
Side Compression Rollers ...................................................................................................... 25
Maintenance ...........................................................................................................26
Daily Preventive Maintenance ................................................................................................ 26
Weekly Preventive Maintenance............................................................................................. 27
Monthly Preventive Maintenance ........................................................................................... 28
Semiannual Maintenance........................................................................................................ 28
Troubleshooting......................................................................................................29
Appendix A: Sequence Of Operation.................................................................38
Appendix B: Spare Parts Kit ..............................................................................39
Appendix C: Vendor Documentation .................................................................41
Warranty Information .............................................................................................42

HPA2102(RH) 7
Company
MARQ Packaging Systems, Inc. was founded in 1965 by Ted Marquis to design and manufacture
economical and reliable case erector/bottom sealers. We have expanded our manufacturing producing a
complete line of case packers, partition assembler/inserters, case erector/bottom sealers, case sealers, and
trayforming equipment available with or without the Q.C. (Quick Change) option. MARQ machines seal
cases with either hot melt, cold glue, pressure sensitive tape or any combination thereof. Also available
are uniform sealers, random sealers, and case vibrators. MARQ innovations have helped establish new
standards in many areas of the packaging industry. Each MARQ machine is designed to adjust to case
sizes outside its standard making MARQ's line of basic machines adaptable to hundreds of uses.
MARQ's 65,000 square foot plant, located near theYakima International Air Terminal, is staffed with
design engineers, craftsmen, and a sales force who team up for a one-on-one effort with each of MARQ's
customers. We at MARQ Packaging Systems, Inc. take pride in the fact that our products bear the
MARQ of Quality and Excellence.
Over 30 years of complete customer satisfaction has proven the reliability of the combined forces of the
case sealer and the computer.
If parts are required for your MARQ Case Sealer, they may be obtained from MARQ Packaging, 3801 W.
Washington Ave,Yakima, WA 98903.
THE ONE AND ONLY CAM (COMPUTER ADJUSTABLE MACHINE)
CASE PACKER, PARTITION ASSEMBLY/INSERTING, CASE ERECTING, CASE SEALING
AND TRAYFORMING MANUFACTURER.

8HPA2102(RH)
Introduction
Manual Overview
This manual contains information needed to operate, maintain, and troubleshoot your machine. The
following page describes the general safety precautions you should take when you operate the Case
Sealer.
The main body of the manual contains information on the machine and its operation. The various controls
are described. Operating Procedures are shown in step by step detail. Toward the end of the manual you
will find maintenance and troubleshooting information.
The Appendixes contain a Sequence of Operation based on the electrical and program flow. Also included
in the Appendixes is a list of suggested spare parts.
The final page of this manual contains warranty information.
Throughout this manual:
• The names of all BUTTONS, KEYS and SWITCHES will appear in BOLD CAPITAL LETTERS.
• Left and right references are made when standing at the hopper end of the machine and looking at the
discharge end.
• Optional Features will be marked with an asterisk (*).
If you are viewing the manual on a computer screen:
• Click on most page references to jump to that page.
• Click on the footer on any page to jump to the table of contents.
Satisfactory operation of the MARQ Case Sealer depends on proper application, correct installation, and
proper maintenance. In addition, modifications to the equipment may result in less than satisfactory
performance.
Contact Information:
MARQ Packaging
3801 W WashingtonAve
Yakima, WA 98903
Phone: (509) 966-4300
FAX: (509) 452-3307
MARQ Packaging, Chicago Facility
1901 Raymond Drive, Suite 5
Northbrook, IL 60062
Phone: (847) 753-9490
Email: inf[email protected]
Internet: www.marq.net
PLEASE READ YOUR MANUAL BEFORE OPERATING YOUR MARQ EQUIPMENT

HPA2102(RH) 9
Safety
Precautions:Always maintain operator safety!
Before working on your Case Sealer, disconnect all incoming power.
Turn off all electrical and air connections to this equipment before repairing, cleaning or removing
jammed cases.
Do not put hands or tools into equipment while the Case Sealer is operating.
Do not operate the Case Sealer without all guards and safety mechanisms in place.
Do not where neckties, jewelry, loose clothing, or other items that can become caught in moving parts or
mechanisms in the vicinity of the Case Sealer.
Wear all company-specified personal protective equipment while operating the Case Sealer.
Do not operate, troubleshoot, or maintain the Case Sealer while under the influence of any type of drug or
alcohol.
Always observe all safety warnings and notices on the machine and in this manual.
Do not use flammable or toxic cleaning fluids such as gasoline, benzene, or ether when cleaning and
maintaining the Case Sealer.
Safety Features
The Case Sealer is equipped with an Emergency Stop button. This red pushbutton is located on top of the
main electrical panel on the right hand side of the machine. Press the Emergency Stop button to
immediately stop machine operation. This button must be pulled back up by hand before the machine can
be restarted.
Safety Guarding with interlocks is available for all MARQ machines. Machines equipped with Safety
Guarding cannot be started unless ALL guard doors are closed. If any doors are opened while the
machine is running the system will immediately shut down. The doors must be shut and the machine
must be reset in order to restart.
TURN ELECTRICAL AND AIR OFF BEFORE
CLEANING OR REPAIRING MACHINE DANGERDANGER
123456789012345678901234567890121234567890123456789012345678901212345678901234567890123456789012123456789012345678901234567890121234567890
123456789012345678901234567890121234567890123456789012345678901212345678901234567890123456789012123456789012345678901234567890121234567890
123456789012345678901234567890121234567890123456789012345678901212345678901234567890123456789012123456789012345678901234567890121234567890
123456789012345678901234567890121234567890123456789012345678901212345678901234567890123456789012123456789012345678901234567890121234567890
123456789012345678901234567890121234567890123456789012345678901212345678901234567890123456789012123456789012345678901234567890121234567890
123456789012345678901234567890121234567890123456789012345678901212345678901234567890123456789012123456789012345678901234567890121234567890
123456789012345678901234567890121234567890123456789012345678901212345678901234567890123456789012123456789012345678901234567890121234567890
123456789012345678901234567890121234567890123456789012345678901212345678901234567890123456789012123456789012345678901234567890121234567890
123456789012345678901234567890121234567890123456789012345678901212345678901234567890123456789012123456789012345678901234567890121234567890
123456789012345678901234567890121234567890123456789012345678901212345678901234567890123456789012123456789012345678901234567890121234567890
123456789012345678901234567890121234567890123456789012345678901212345678901234567890123456789012123456789012345678901234567890121234567890
123456789012345678901234567890121234567890123456789012345678901212345678901234567890123456789012123456789012345678901234567890121234567890
123456789012345678901234567890121234567890123456789012345678901212345678901234567890123456789012123456789012345678901234567890121234567890
123456789012345678901234567890121234567890123456789012345678901212345678901234567890123456789012123456789012345678901234567890121234567890
123456789012345678901234567890121234567890123456789012345678901212345678901234567890123456789012123456789012345678901234567890121234567890
123456789012345678901234567890121234567890123456789012345678901212345678901234567890123456789012123456789012345678901234567890121234567890
123456789012345678901234567890121234567890123456789012345678901212345678901234567890123456789012123456789012345678901234567890121234567890
123456789012345678901234567890121234567890123456789012345678901212345678901234567890123456789012123456789012345678901234567890121234567890
123456789012345678901234567890121234567890123456789012345678901212345678901234567890123456789012123456789012345678901234567890121234567890
123456789012345678901234567890121234567890123456789012345678901212345678901234567890123456789012123456789012345678901234567890121234567890
123456789012345678901234567890121234567890123456789012345678901212345678901234567890123456789012123456789012345678901234567890121234567890
! Special Caution !
Do not tamper with any interlock guard switches.

10 HPA2102(RH)
Specifications
Main Drive Unit Motor:..................................................................O.P.D.R. Motor
Voltage: ................................................................................................230V 3 Phase
Transformer: ................................................................................................1.0KVA
Air Required: ................................................................. 3 CFM @ 80PSI per cycle
Controller:........................................................................................................... NA
Sealant: ........................................................................................MARQ Tape Head
Production Rate:..................................................................... 15 Cases Per Minute
Case Type: .................................................................. Regular Slotted Cases (RSC)
Paint:.........................................................................................................Dark Gray
Options
The following is a list of included options for machine #Q01002 HPA2102(RH), built for Life Data Labs.
•Raised Lug Drive 7-8"
•Spare Parts Kit #801-35
•Low Tape, Tape Out with Beacon
•230V 3 Phase Electrical

HPA2102(RH) 11
NOTE: It is very important that once the machine arrives it is checked carefully for any damage that may
have occurred in transit. Since MARQ's terms are F.O.B.Yakima, it is your responsibility to contact the
carrier and file any necessary damage claims with them.
Each MARQ Case Sealer is tested prior to shipping to ensure proper operation. Due to variations in case
sizes, packing conditions, bulge and weight, it may be necessary to make minor changes in the settings
discussed below to obtain optimum performance and operation.
Leveling & Adjusting Height
The Case Sealer should be leveled for proper height using the machine's adjustable legs.
• The standard infeed deck height is set at 25-27"
• The machine should not be resting on casters during operation.
Electrical Connections
The following electrical connections are required:
• Main Drive Shaft - 230v AC 3 ph 3/4 HP
• Control Box - 110v AC 1ph 60 Hz
• Other voltages are available on request.
Air Connections
An air supply capable of delivering the required volume of air at 80 psi should be connected to the
machine using a filter/regulator/lubricator. Air line requirements between the compressor and the machine
should be as follows:
• 1/2” pipe 0–25 ft.
• 3/4” pipe 25–60 ft.
• 1” pipe 50 ft. or over.
Adjusting Air Cylinder Speed
Most of the air valves on the machine have exhaust restrictors to control the speed of the air cylinders
they operate. To increase the speed of an air cylinder, open the exhaust restrictor until the desired speed
is reached. To decrease the speed of an air cylinder, close the exhaust restrictor until the desired speed is
reached. See page 17, Solenoid Valves for more on adjusting the air flow.
Conveyors
For optimal performance powered conveyors should always be used in conjunction with MARQ Sealers.
The infeed conveyor should be powered at .75 feet per second to insure case separation at the gate.
Installation

HPA2102(RH) 13
Machine Operation
The gate drops to allow the case to enter the machine.
Power rollers push the case into the machine, so that the side
lugs can transfer the case through the machine.
The kicker folds the trailing minor flap.
Folding rods fold the leading minor flap.
The major flaps are folded over by major flap folding arms.
When a case reaches the gate, it is detected by the gate photo
eye.
figure 13-1. Gate Photoeye
figure 13-2. Gate and Power Rollers
figure 13-3. Flap Folders

16 HPA2102(RH)
Components: Main Air Prep Unit
figure 16-1. Main Air Prep Unit
MainAir Prep Unit
The main air prep unit has a two-position gate valve that directs or shuts off
high-pressure air to the machine. (See fig. 16-2)
Air Pressure Regulator/Filter/Lubricator
A sight gauge shows the amount of the air pressure in pounds per square
inch (psi). For the machine to operate correctly this must read at a constant
80 psi. (See fig. 16-3)
The regulating hand knob adjusts the air pressure. It is located just below
the sight gauge. Pulling down and turning the knob clockwise increases air
pressure. Pushing the Knob back up locks adjustment in place. (See fig.
16-3 or 16-1B)
The filter assembly removes debris from the air system. (See fig. 16-4)
On the bottom of the filter assembly casing there is a screw-type pet cock
for draining accumulated moisture. (See fig. 16-1A)
A soft start adjustment screw lets you adjust the speed of the airflow being
applied to the machine. (See fig. 16-1C)
An oil reservoir supplies lubricant to the air lines. (See fig. 16-5)
Adjust the amount of oil supplied in the air system by turning the
adjustment knob on top of the oil reservoir. A window allows for counting
of the drops supplied. Adjust lubricant for 1 drop for every 10-15 cases.
Turn either left (positive) to increase, or right (negative) to decrease. (See
fig. 16-6)
The oil reservoir is filled with a non-detergent hydraulic oil.A 10W or
transmission fluid will work in this system as long as it is a non-detergent
oil.
figure 16-2. Air Gate
figure 16-3. Pressure Gauge
figure 16-4. Air Filter
figure 16-5. Oil Reservoir
figure 16-6. Oil Window
A B C

HPA2102(RH) 17
Components: SolenoidValves
Solenoid Valves
A solenoid valve (fig. 17-1) receives an electrical signal from
the controller to shuttle a plunger back and forth. The plunger
directs air from the air lines to the air-driven devices on the
machine.
The manual override is a small blue screw on the top of the
solenoid valve (fig. 17-2). It can be turned, using a screwdriver,
to override the electrical signal, which causes the plunger to
shift and direct air from the "B" port of the valve to the "A"
port, causing the cylinder to actuate.
The exhaust restricters are located on the bottom of each valve
(fig. 17-3). Turn the screws to increase (counter-clockwise)
or decrease (clockwise) the air flow.
Valves
1 SOL Gate
2 SOL Kicker
3 SOL Air Dump
figure 17-1. Parker Hanafin Solenoid Valves
figure 17-2. Manual Override
figure 17-3. Exhaust Restrictors

18 HPA2102(RH)
Air Cylinder
An air cylinder houses a piston that is driven back and forth by
high-pressure air that actuates the air-driven devices on the
machine. (fig 18-1)
CushionAdjustment Screws
The cushion adjustment screws are set screws that are turned
to adjust the travel of the piston into the cushion. Turning the
screw clockwise increases the cushion and allows the piston
rod to ratchet at a higher rate of speed. This adjusts the cylin-
der stroke.
figure 18-1. Rexroth Air Cylinder
Components: Air Cylinders

HPA2102(RH) 19
Components: Main Drive Unit
Side Lug Assembly
• Side Lugs
The side lugs are "L" shaped pieces of metal mounted
on a drive chain which moves the cases through the
machine.
• Side Lug Motor
The side lug motor is a .75 HP motor that powers the
side lug drive chains that transfer cases through the
machine.
• Micro Limit Switch
The micro limit switch is mounted under the side lug
drive chain to signal the position of the side lugs to the
controller. The side lugs trip the switch arm on the limit
switch as they rotate around the drive chain.
Brake/Clutch Module
The brake/clutch module is a 90 volt AC assembly that starts
and stops the side lug drive chain as it transfers cases
through the machine. This allows cases to be stopped at each
station for the performance of various operations.
Gearbox
The gearbox is a set of gears that transfers the power from
the motors horizontally to drive the machine's side lug drive
chain. PLEASE REFER TO THE MAINTENANCE
SECTION OF THIS MANUAL FOR LUBRICATION
INSTRUCTIOINS. FAILURE TO LUBRICATE GEAR
BOX PROPERLY MAY CAUSE MACHINE FAILURE
AND VOIDYOUR WARRANTY.
Sprocket and Chain Drive Assemblies
A set of motor driven idler sprockets and chains drive the
machine's side lugs.
Tol-O-Matics
All Float-A-Shaft gear boxes have been lubricated at the
factory with Anderol®786. However, units require more
lubrication prior to operation. See the Weekly Maintenance
section for further details.
figure 19-1. Zerk Fitting on Tolomatic Gearcase

20 HPA2102(RH)
Components: Sensing Devices
Limit Switches (LS)
1Gate Enable
When made while a case is at the gate photoeye the gate is
dropped allowing the case to enter.
The Gate Enable switch is located beneath the right rail. It
is the second switch from the infeed end of the machine.
2F.B. Disable
If the case is still entering when the FB Disable switch is
made then the motor is stopped until the case has cleared the
gate photoeye.
The F.B. Disable switch is located beneath the right rail. It
is the first switch from the infeed end of the machine.
3Arch Safety *
If this switch is made during arch adjustment the adjustment
motor will be disabled until the direction select switch is set
to the opposite direction.
Top Low Tape *
Top No Tape *
When the Low Tape switch is released the yellow beacon
will come on and the display will indicate a low tape
situation. When the No Tape switch is released the yellow
beacon will flash, the machine will hold, and the display will
indicate a no tape situation.
Photoeyes (PE)
1Gate
When the gate photoeye is made and the Side Lug reaches
the point specified in the GATE_POINT variable, the gate
drops allowing a case to be pulled into the machine by the
power rolls.
2Kicker Off
3Kicker On
When both eyes are blocked by the case the kicker is fired.
When the first eye is unmade by the case the kicker is
retracted.
Both the Kicker photoeyes are mounted above the right rail.
Bottom Low Tape *
Bottom No Tape *
When the Low Tape switch is released the yellow beacon
will come on and the display will indicate a low tape
situation. When the No Tape switch is released the yellow
beacon will flash, the machine will hold, and the display will
indicate a no tape situation.
figure 20-1. Top Tape Supply Sensors
figure 20-2. Bottom Tape Supply Sensors
figure 20-3. Gate Enable and F.B. Disable Switches and
tKicker Photoeyes
Table of contents
Popular DC Drive manuals by other brands
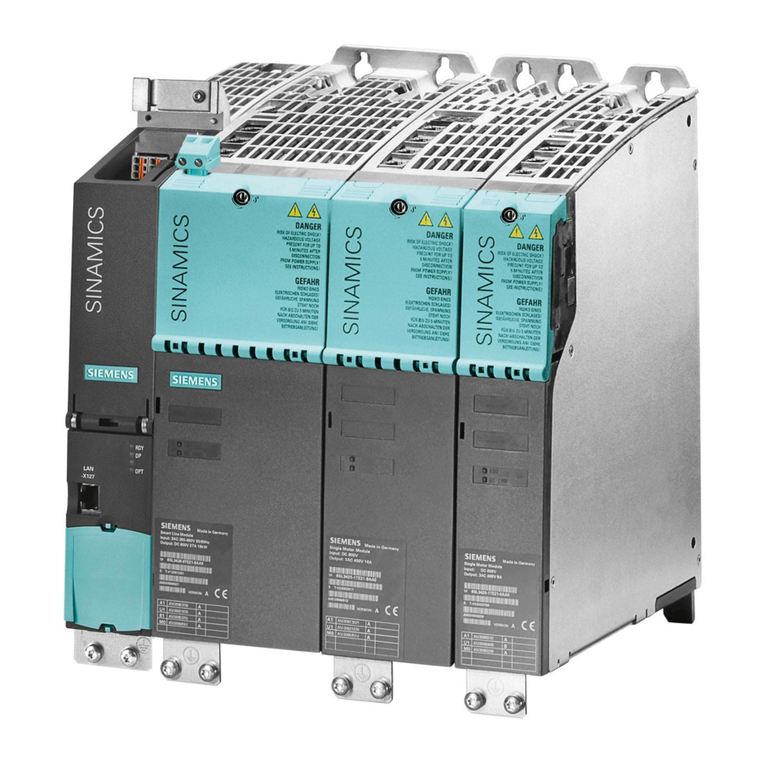
Siemens
Siemens SINAMICS S120 Function manual

LiFud
LiFud LF-GSD040YG manual
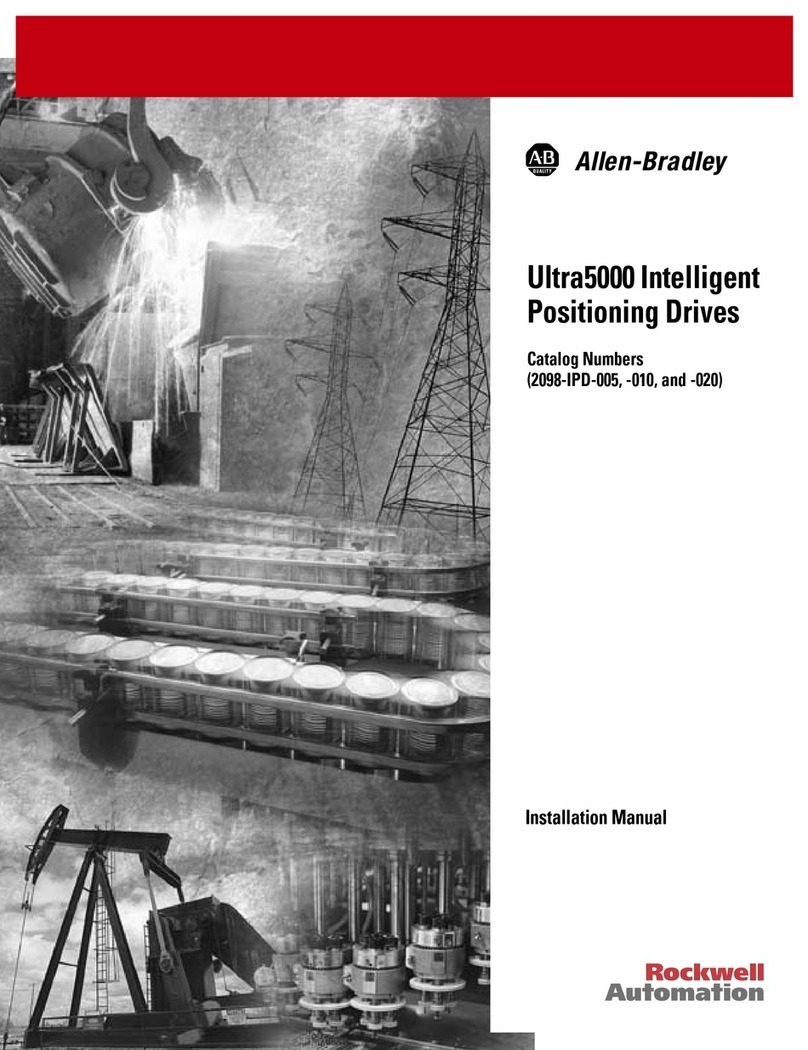
Rockwell Automation
Rockwell Automation Allen-Bradley Ultra5000 installation manual
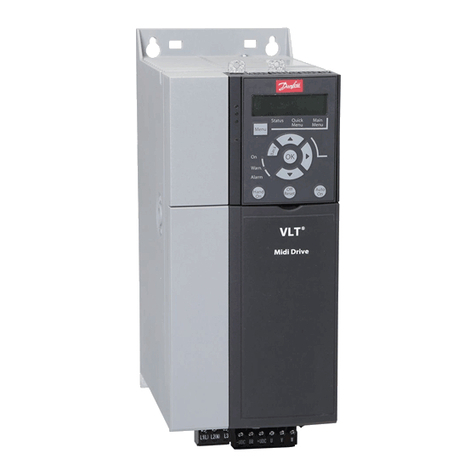
Danfoss
Danfoss VLT Midi Drive FC 280 Programming guide

GFA
GFA ELEKTROMAT SI 60.24-55,00 installation instructions

Pfeiffer Vacuum
Pfeiffer Vacuum TC1200 operating instructions

Küenle
Küenle KFU 210 Series Quick start manual
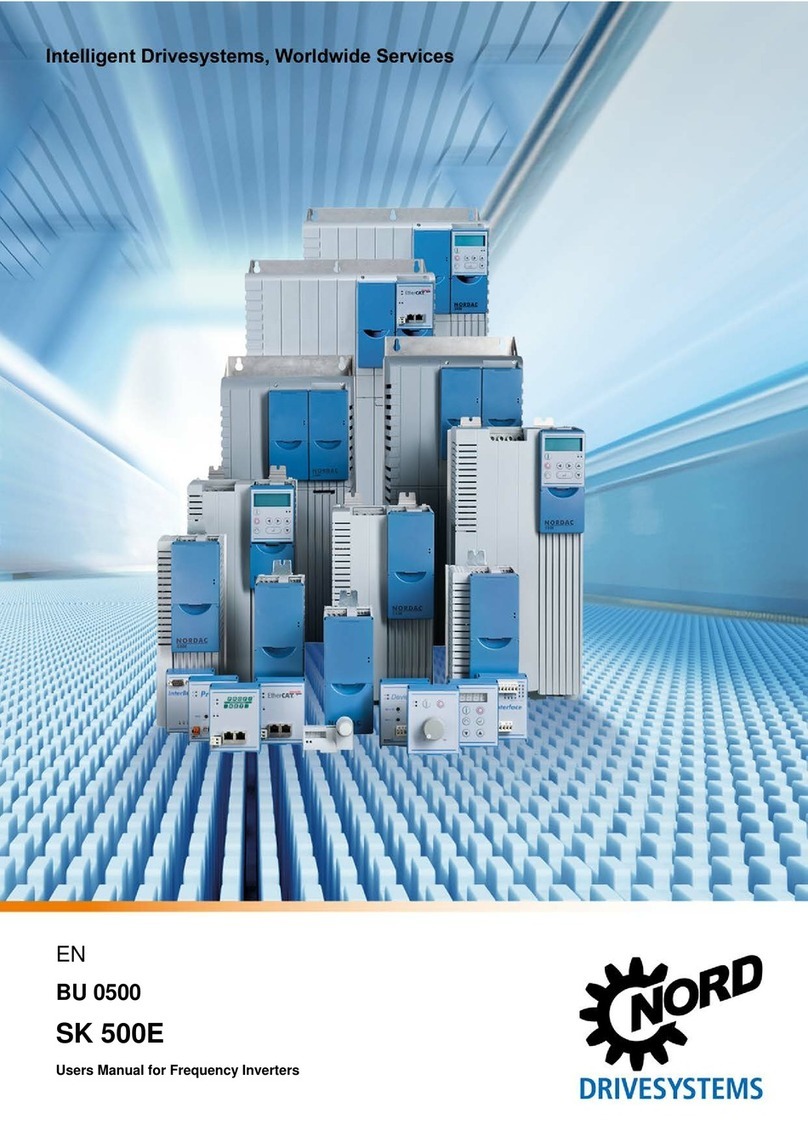
Nord Drivesystems
Nord Drivesystems SK 500E user manual

O&K Antriebstechnik
O&K Antriebstechnik S5 Series Repair manual
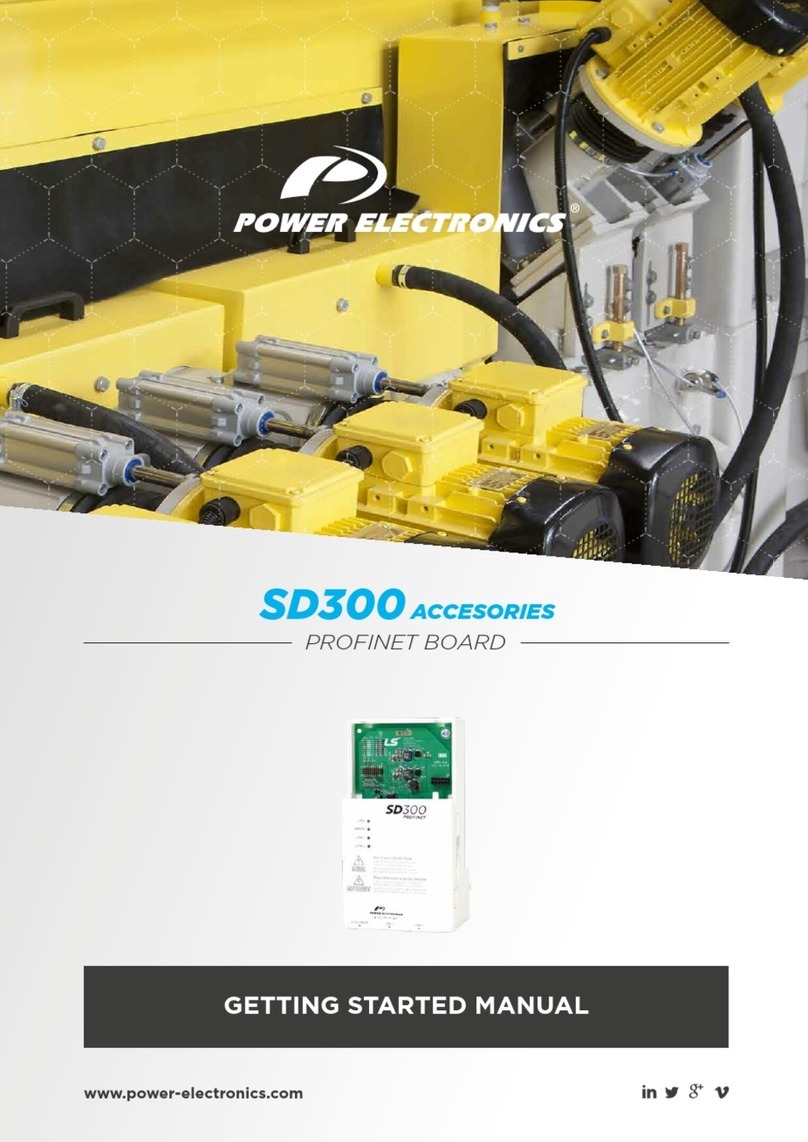
Power Electronics
Power Electronics SD 300 Series Getting started manual
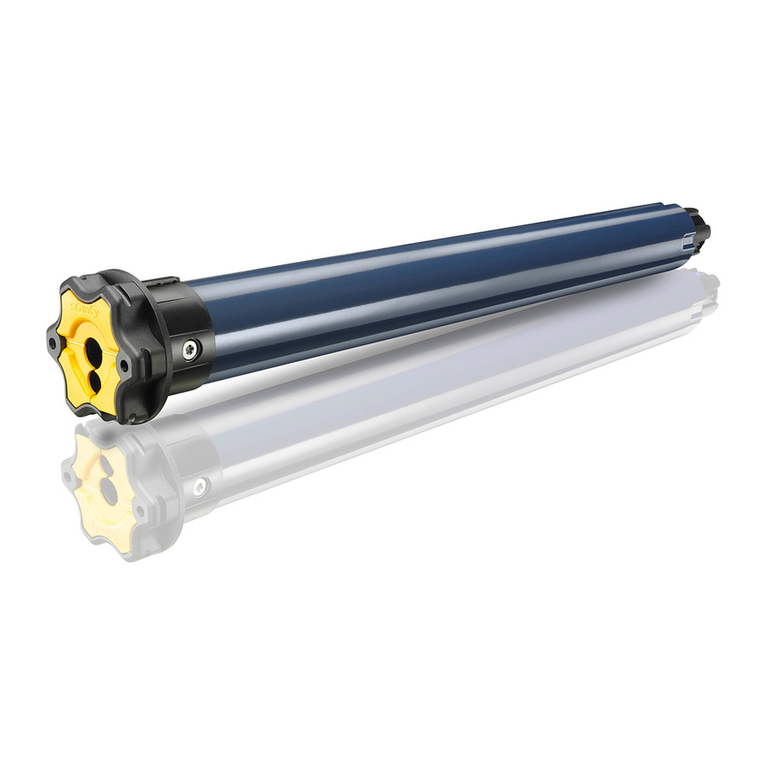
SOMFY
SOMFY S&SO-RS100 io Original instructions
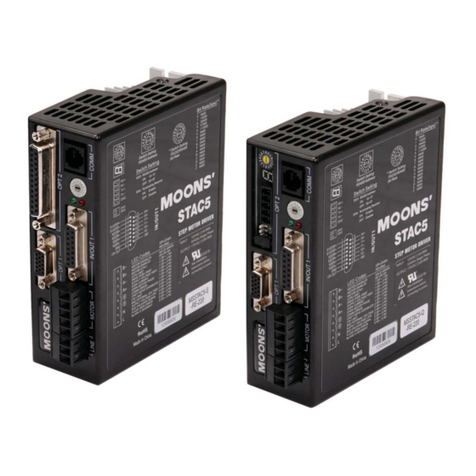
Moons'
Moons' MSSTAC5-2V Quick setup guide