Marshall Amplification RDS PRO Series Use and care manual

RDS PRO-SERIES APOLLO 8000
SPREADER CONTROLLER
CALIBRATION MANUAL
SOFTWARE ISSUE : PS401000

ELECTROMAGNETIC COMPATIBILTY (EMC)
This product compiles with Council Directive 89/336/EEC when
installed and used in accordance with the relevant instructions.
IMPORTANT, READ THIS BEFORE USING THE APOLLO
The Apollo installation is part of the Precision Farming System
(“the System”). It is very important that you follow the described
calibration procedures before operating the Apollo instrument.
Calibration and operation of the Apollo must be in accordance
with these instructions. Use of the System is subject to the
following disclaimer;
1. So far as is legally permissable RDS Technology (“RDS”), or
its distributors, shall not be liable, whatever the cause, for any
increased costs, loss of prots, business contracts, income or
anticipated savings or for any special, indirect or inconsequential
damage whatsoever (death or personal injury excluded)
2. The capabilites and functions of the precision farming system
(“the system”) are limited as set out in the specication of the
System, details of which are contained in the Help les and
product literature and which must be read before using the
System.
3. Without prejudice to the generality of the above it is hereby
acknowledged that the System is not designed nor intended to
a) originate variable treatment plans or b) achieve or avoid any
application rate outside application parameters, which in both
cases shall be the responsibility of the operator.
4. The standard terms and conditions of RDS (except clause 7),
a copy of which is available on request, apply to the supply and
operation of the System.
SERVICE AND TECHNICAL SUPPORT
PLEASE CONTACT
Roesner Pty Ltd (Marshall Multispread)
Harvey Western Australia
Freecall 1800 651 288 +61 8 97 291 501
www.roesner.com.au
RDS Technology
United Kingdom
Ph + 44 1453 733300
www.rdstec.com
pg 2

CONTENTS
Section Overview
1.1 The Factory Setup Screen 5
1.2 Control Channels 6
1.3 Data Entry 6
1.4 Calibration Menu Tree 7
Motor Valve Conguration
2.1 Machine options 9
2.2 PWM Valve/Motor Setup 9
2.2.1 Feedback 9
2.2.2 Response 9
2.2.3 Deadband 10
2.2.4 Startup/Control Delay 10
2.2.5 Power-On PWM 10
2.2.6 Valve Setup 10
2.3 Valve Calibration 11
Factory Conguration
3.1 Spreader Conguration Menu 12
3.2 Pro-Series Conguration Menu 13
3.3 Loadcell Interfaces 13
3.3.1 Loadcell Calibration Procedure 14
3.3.2 Angle Sensor Calibration 15
3.3.3 Factors Store 15
3.4 PIN Number Change 16
User Options
4.1 User Options Menu 16
4.2 Set Date and Time 16
4.3 Contrast/Brightness 16
4.4 Customise 17
4.4.1 Units 17
4.4.2 Edit Product Names 17
4.4.3 Step Size 17
Technical Cong Menu
5.1 Display Options 18
5.1.1 Speed Smoothing 18
5.1.2 Rate Lock On 18
5.1.3 Rate Smoothing 18
5.1.4 Off Target 18
5.2 Loadcell Correction 19
5.2.1 Correction Span 19
5.2.2 Min.Stat.Weight 19
5.2.3 Dynamic Time 19
5.2.4 Dynamic Weight 19
pg 3

CONTENTS
5.2.5 Start Delay 19
5.2.6 Steady Weight 19
5.3 Overload Log 20
5.4 Print Cal Data 20
5.5 Pin # Change 20
General Calibration
6.1 Product Select Screen 21
6.2 Spreader Setup Screen 22
6.2.1 Calibration Routine 22
6.2.2 Nudge Factor 23
6.2.3 Working Width 23
6.2.4 Speed Sensor Factor 24
6.2.5 GPS On/Off 25
6.2.6 Simulated Forward Speed 25
General PF Setup
7.1 Logging Interval 26
7.2 Tag Names 26
7.3 Edit Function names and Values 27
7.4 GPS Antenna Offsets 27
7.5 GPS Home Location 28
7.6 Ports Setup 28
7.6.1 Top Port Setup 29
7.6.2 Bottom Port Setup 29
Diagnostics
8.1 Pro Series Diagnostics 30
8.2 Channel Diagnostics 30
8.3 Loadcell Interfaces 30
8.4 Angle Sensor 30
8.5 Dynamic Calibration 30
pg 4

1. OVERVIEW
This manual covers the calibration of the RDS Pro-Series Apollo 8000 for Marshall Multispread
Fertiliser Spreaders.
The Instrument must be calibrated before commencing normal operation. Many settings are made
only on initial calibration eg from the FACTORY SETUP screen. Other calibration settings will need
to be altered on a regular basis, depending upon the product to be spread.
1.1 THE FACTORY SETUP SCREEN
Press the key to select the menu screen. (g 1)
Choose Option 3. Factory Setup (g 2)
Channel Options
Gate Width
Max Gate Height
Drive roller Diameter
Max Weight
Shaft PPR
Cutout Switch Setup
Valve Setup
Loadcell Setup
Store Factors
PIN Number Change
Calibration on Installation
Work through the FACTORY SETUP menu rst. The settings specic to the Multispread; Gate
Width and Height, Drive Roller diameter, Max Weight can be obtained from Roesner Pty Ltd.
pg 5
g 1 : Menu Screen
g 2 : Factory Setup Screen

1.2 CONTROL CHANNELS
The RDS Pro-Series Apollo 8000 is an extremely versatile control system, with the ability to
control up to 4 separate control channels. When tted to the Marshall Multispread only one control
channel is required, the Danfoss proportional valve which drives the Multispread feedbelt. In order
to prevent operator confusion, the remaining 3 control channels have been disabled within the
PS401 version software.
1.3 DATA ENTRY
Alpha-numeric values are entered via the right-hand key pad. Letters are entered by pressing
the key 2 to 5 times and scrolling through the letter options, as per writing an SMS message on a
mobile telephone. (Some Keys have additional special characters not shown on the key legend).
The key will either toggle between lower and upper case characters or when proceding a
numerial entry, will set a minus value.
The key will toggle between 0 and a SPACE.
The key will BACKSPACE the screen cursor if you need to re-enter a character.
The key is the RETURN key and is normally pressed to conrm the data entry into memory.
pg 6

1.4 MENU TREE
Product Select
Rate (kg/ha)
‘D’ FACTOR (kg/m3)
Speed Range (km/h)
Gate Height (mm)
Calibration Routine
Nudge Factor
Working Width (m)
Speed Sensor Factor
Hi Spinner (RPM)
Lo Spinner (RPM)
Lo Weight (kg)
Simulated Forward
Speed (km/h)
1. USER OPTIONS 1. TIME/DATE
2. CONTRAST/BRIGHTNESS
3. CUSTOMISE
4. LANGUAGE
5. HELPLINE
6. INSTRUMENT SELECT APOLLO BELT PS401000R03
1. DISPLAY OPTIONS SPEED SMOOTHING
RATE LOCK ON %
RATE SMOOTHING
OFF TARGET
2. LOADCELL CORRECTION CORRECTION SPAN
MIN.STAT.WEIGHT
DYNAMIC TIME
DYNAMIC WEIGHT
START DELAY
STEADY WEIGHT
3. OVERLOAD LOG MAX LOAD RECORD STORE
4. PRINT CAL DATA
5. PIN NUMBER CHANGE ENTER NEW PIN
1. MACHINE OPTIONS CHANNEL :1
BELT SPEED CONTROL
IN USE : YES/NO
TYPE : PWM VALVE/MOTOR
2. SPREADER CONFIG GATE WIDTH (mm)
MAX GATE HEIGHT (mm)
DRIVE ROLLER DIA (mm)
MAX WEIGHT (kg)
SHAFT 1 (RPM)
SHAFT 2 (RPM)
3. PRO-SERIES CONFIG AREA CUTOUT INPUT
4. CHANNELS CHANNEL
FEEDBACK
RESPONSE
DEADBAND
STARTUP DELAY
VALVE SETUP
5. LOADCELL INTERFACES FUNCTION
LOAD ZERO
LOAD GAIN
CALIBRATION
ROUTINE
6. FACTORS STORE SAVE TO STORE A
RESTORE FROM A
7. PIN NUMBER CHANGE ENTER NEW PIN
CONTINUED OVERLEAF NOTE DEFAULT SETTINGS IN BRACKETS [ ]
2. TECHNICAN CONFIG 0.00 - 19.00 [2.0]
0.00 - 50.00 [2.0]
0.00 - 19.00 [2.0]
0.00 - 50.00 [20.0]
[5.0%]
[200.00 KG]
[30 SEC]
[200.00 KG]
[10 SEC]
[0.75%]
CONFIRM NEW PIN
3. FACTORY CONFIG
[730mm]
[230mm]
[231mm]
DEPENDENT ON MODEL
1.000
NOT USED
IP 0V = [OUT OF WORK]
IN WORK
[BELT SPEED]
[360 PPR]
0.00-9999 [5.0]
0.00-99.9 [2.0]
0.00-99.5 [2.0]
VALVE SETUP PROCEDURE
[NOT USED] 1 MODULE
0.0000
0.0000
LOADCELLS / ANGLE SENSOR
CONFIRM NEW PIN
pg 7

1.4 MENU TREE continued
from menu
4. GENERAL PF SETUP
5. DIAGNOSTICS
1. LOGGING INTERVAL 0.00-99 SEC [5 SEC]
2. TAG NAMES
3. FUNCTION NAME/VALVE
4. GPS ANTENNA OFFSETS
5. GPS HOME LOCATION
6. PORTS SETUP TOP PORT RDS PRINTER ICP100
BTM PORT GPS INPUT
CONTACT ROESNER PTY LTD FOR LIST OF COMPATIBLE GPS CONTROLLERS
1. PRO-SERIES BELT FEEDBACK (HZ)
FORWARD SPEED (KM/H)
VOLTAGE (V)
C/O I/P = HIGH/LOW
LCI’s ON BUS : DEPENDANT ON LOADCELL SETUP
2. CHANNELS BELT CHANNEL
BELT FEEDBACK (HZ)
FORWARD SPEED (KM/H)
ACTUAL RPM
TARGET RPM
PWM SIGNAL - %
SPINNER CHANNEL - NOT USED
GATE CHANNEL - NOT USED
3. LOADCELL INTERFACES CAN MESSAGE - RELATIVE LOAD - VOLTAGE
FILTER STATUS - INACTIVE
ONLY ACTIVE WHEN FORWARD SPEED > O KM/H
CAN SOFTWARE VERSION
4. ANGLE SENSOR PITCH - VOLTAGE AND ANGLE
ROLL - VOLTAGE AND ANGLE
5. DYNAMIC CALIBRATION
pg 8

2. MOTOR VALVE CONFIGURATION
This section applies to the conguration of the Danfoss Proportional Valve and Hydraulic motor
used to drive the Multispread feedbelt.
2.1 MACHINE OPTIONS
Go to the “MACHINE OPTIONS” screen to check the Valve/Motor Setup. (g 3)
MENU
3. FACTORY CONFIG
1. MACHINE OPTIONS
By default the instrument is congured to Channel 1 - PWM VALVE/MOTOR. The IN USE setting
should show YES, if not move the cursor to the line IN USE and select YES, then press enter.
2.2 PWM VALVE/ MOTOR SETUP (g 4)
MENU
3. FACTORY CONFIG
4. CHANNELS
2.2.1 FEEDBACK
The Feedback function displays the Pulse Per Revolution (ppr) returned from the rotary encoder
mounted on the nal drive shaft. The default value is 360 ppr. The rotary encoder returns 360
pulses per revolution of the nal drive shaft.
2.2.2 RESPONSE
The System Response function sets the frequency at which the system adjusts the motor/
proportional valve when reacting to changes in forward speed. A lower setting results in a slower
response, and increases the time taken for the application rate to match the target rate. A higher
setting results in a faster response. If the application rate is unstable and varies around the target
rate, then the response setting may be too high.
Default : 5.0 Range : 0.1 - 9999
ENTER PIN - DEFAULT -1234
ENTER PIN - DEFAULT -1234
pg 9
g 3 : Machine
Options Screen
g 4: Channel
Setup Screen

2.2.3 DEADBAND
The Deadband function sets the range over which the application rate will vary about the target
rate before the valve/motor will respond. A lower value will make the motor adjust more frequently
and vise versa.
Default : 1 Range : 0.01 - 9999
2.2.4 STARTUP/CONTROL DELAY
The Startup/Control Delay function governs the time taken for the belt to begin moving when the
master switch is turned ON.
Default : 2 secs.
In most situations a 2 sec startup delay is acceptable.
2.2.5 POWER-ON PWM
2.2.6 VALVE SETUP (g 5)
The Danfoss Proportional Valve tted to Multispread works on Normal PWM at a PWM frequency
of 100Hz.
The Minimum and Maximum Duty of the Danfoss Proportional Valve needs to be setup on rst
installation. Proportional Valves dont respond over the full PWM range from 1-100%. Typically they
operate from 20% to 70%. To set the Minimum and Maximum PWM % the Valve Calibration
Procedure should be carried out. Before starting the Valve Calibration ensure that the Instrument
is in manual control mode (see page of Operation manual)
VALVE SETUP
VALVE CALIBRATION
The minimum duty is effectively the minimum feedbelt RPM that can be achieved at operating
oil pressure and ow. The maximum duty is effectively the maximum feedbelt RPM that can be
achieved at operating oil and pressure. In normal spreading conditions the feedbelt RPM will be
between 3 and 30 RPM, ensuring an application rate from between 15 to 8000 kg/ha.
pg 10
g 5: Valve Setup Screen

2.3 VALVE CALIBRATION (g 6)
** Important ** The Multispread should be connected to the
oil supply (tractor hydraulics or truck pump), and the oil
must be at operating pressure and ow rate.
To set the Minimum Duty.
Turn the spreader on using the toggle switch. Slowly increase
the PWM % using the PWM UP KEY until the feedbelt just
begins to move.
When the belt is just moving press enter to store the minimum duty and minimum feedbelt RPM.
Then move the cursor down to MAX DUTY
To set the Maximum Duty.
Increase the PWM % using the PWM UP KEY until the maximum speed is reached. eg the point at
which pressing the PWM UP KEY has no effect on the feedbelt speed.
Then press enter to store the maximum duty and maximum feedbelt RPM.
pg 11
g 6 : Valve Calibration Screen

3. SPREADER CONFIGURATION MENU (g 7)
The Spreader Conguration menu contains functions that are unique to each Multispread model,
including gate width and height, drive roller diameter and shaft ppr. These settings are normally
programmed at installation.
MENU
3. FACTORY CONFIG
2. SPREADER CONFIG
Use the cursor to enter the setting below for each function.
GATE WIDTH : The door width in (mm). Multispread 800-900 Series machines - 730mm
MAX GATE HEIGHT : The maximum door height in (mm). The maximum door opening depends
upon the Multispread model. Open the door to its maximum height and then use a tape to
measure the distance from the bottom of the door to the feedbelt.
DRIVE ROLLER DIAMETER : The diameter of the nal drive roller in (mm). The following table
indicates drive roller diamter by Model.
Model Number Drive Roller Diameter
800 Series - 825T-810TM 185mm
945T 178mm
960-912TM 231mm
9160 280mm
MAX. WEIGHT : The maximum machine weight in (kg). See Marshall Multispread Operators
Manual for machine loading gures.
SHAFT 1 : The ppr factor for the spinner shaft, used for measuring spinner RPM. This value
should be set to 1 ppr as only only magnet is tted to the spinner shaft.
SHAFT 2 : Not Used
ENTER PIN - DEFAULT -1234
pg 12
g 7 : Spreader Conguration Menu

3.2 PRO-SERIES CONFIGURATION MENU (g 8)
MENU
3. FACTORY CONFIG
3. PRO SERIES CONFIG
This menu species the conguration of the master cut-out switch. They are two options :
IP 0V = Out of work : In this case the input goes to 0V when the spreader is switch off/out of work
IP 0V = In Work : In this case the input goes to 0V when the spreader is switched on/in work.
Use the cursor to change the setting and press enter to conrm.
In most cases the IP 0V = Out of Work setting is used.
3.3 LOADCELL INTERFACES
This section applies only to machines with a loadcell weighing system tted. The Loadcell
Interfaces menu is used to calibrate loadcell zero point and span and also to zero the angle
sensor. The angle sensor is tted to the loadcell interface to ensure accurate weighing when the
spreader is parked on uneven terrain. The loadcells and angle sensor must be congured before
use. (g 9)
MENU
3. FACTORY CONFIG
5. LOADCELL INTERFACES
FUNCTION : The function setting species the number of CAN interface boards that are used.
If loadcells are not used on the spreader this setting should always be set to NOT USED. In most
cases one CAN interface is used and 1 MODULE should be used in the function setting.
LOAD ZERO : This function displays the amplied voltage when the loadcells are at zero. The load
zero will be stored after the calibration procedure is completed.
LOAD GAIN : This function displays the instantaneous amplied voltage returned from the CAN
interface to the instrument.
ENTER PIN - DEFAULT -1234
ENTER PIN - DEFAULT -1234
pg13
g 8 : Pro-Series Conguration Screen
g 9 : Loadcell Interface Screen

3.3.1 LOADCELL CALIBRATION PROCEDURE
The loadcell calibration should be carried out on level ground. to complete the span calibration you
will be required to put a known weight into the spreader or alternatively load the machine and use
a weighbridge and deduct the self weight of the spreader.
Move the cursor to LOADCELL CALIBRATION ROUTINE and press enter. (g 10)
Ensure the spreader is on level ground and that there is no
material in the hopper.
Then press enter to Zero the loadcells.
The Spreader must then be loaded with a known weight or
loaded and then driven over a weighbridge deducting the
self weight of the spreader. (g 11)
With the spreader loaded, enter the weight in kg and press
enter.
The loadcell calibration is then complete. (g 12)
pg 14
g 10 : Loadcell Calibration Screen 1
g 11 : Loadcell Calibration Screen 2
g 12 : Loadcell Calibration Screen 3

3.3.2 ANGLE SENSOR CALIBRATION
From the LOADCELL INTERFACES menu move the cursor to ANGLE SENSOR and press enter.
Important: Before calibrating the angle sensor ensure the machine is level.
Use the key to select the orientation of the loadcell
interface relative to the direction of travel, and then press
enter. (g 13)
The interface icon on the screen indicates the orientation
of the interface when looking from the top down, as
compared to the direction of travel
To set the angle sensor Zero Point (TARE) press the TARE
key. (g 14)
Ensure the spreader is level, and press enter.
The Angle Sensor calibration is then complete. (g 15)
3.3.3 FACTORS STORE
For extra security calibration data can be manually saved to a separate memory area called
“STORE A”. This data will NOT be over written each time the instrument is turned off, but it WILL
be cleared after a Total Software Reset. (RESET FACTORS)
From the FACTORY CONFIG menu select FACTORS STORE. (g 16)
On the FACTORS STORE MENU move the cursor to SAVE
to store A, press enter to save all factors.
To RESTORE factors move the cursor to Restore from A,
and press enter.
It is a good idea to regularly store calibration factors to
STORE A to prevent unwanted data loss.
pg 15
g 13 : Angle Calibration Screen 1
g 14 : Angle Calibration Screen 2
g 15 : Angle Calibration Screen 3
g 16 : Factors Store Screen

3.4 PIN # CHANGE
The PIN number for the FACTORY CONFIG menu can be set to prevent unauthorised users from
accessing the FACTORY CONFIG menu and potentailly interfering with the instruments calibration
settings.
FACTORY CONFIG
7. PIN # CHANGE
Follow the on screen instructions to change the PIN #.
If you forgot your personalised Pin number you will need to contact Roesner Pty Ltd or RDS for
instructions on reseting the PIN.
4.1 USER OPTIONS MENU
The user options menu enables the operator to customise the Pro-Series display, date/time and
the product names.
4.2 SET DATE AND TIME
MENU
1. USER OPTIONS
1. DATE AND TIME
If you need to change the time or date setting, position the cursor against the relevant line, key in
the new value and press enter.
4.3 CONTRAST/BRIGHTNESS
The contrast and brightness of the screen can be adjusted on the CONTRAST/BRIGHTNESS
menu. (g 17)
1. USER OPTIONS
2. CONTRAST/
BRIGHTNESS
pg 16
g 17 : Display Adjustment Screen

The screen may go darker at very high or very low temperatures. For example, on a very cold
morning it may take a short period of time for the display to gain normal contrast as the instrument
warms up. This is a normal characteristic of this type of display and does not mean the display is
faulty.
If by accident the contrast setting is adjusted so that the screen graphics can no longer be
viewed (ie completely light or dark) - dont panic! Press the for at least 20 seconds. The instru-
ment will bleep at 0.5 second intervals as long as the key is depressed.
You can then adjust the display using the arrow keys.
4.4 CUSTOMISE
The customise menu allows the operator to switch to units (either metric/imperial), edit product
names and adjust the standard step set size.
4.4.1 UNITS
USER OPTIONS
3. CUSTOMISE
1. UNITS
Select appropriate units and then press enter.
4.4.2 EDIT PRODUCT NAMES
Up to 8 different product names can be stored within memory. The product names can be
customised and edited according to the operators applications.
USER OPTIONS
3. CUSTOMISE
2. EDIT PRODUCT NAMES
To edit each product name move the cursor to desired line and use the numbers/letters on the
keypad to edit the product names. When the correct text is enter press enter to store.
4.4.3 STEP SIZE
The step size function changes the percentage of application rate increase/decrease displayed on
the MAIN screen when in AUTO spreading mode. Pressing the Up step key will increase the target
rate by the STEP SIZE. The STEP SIZE % is also shown on the MAIN screen in AUTO mode. In
most cases a 5% STEP SIZE is acceptable. Use the cursor to set the desired step size and then
press enter.
USER OPTIONS
3. CUSTOMISE
3. STEP SIZE
pg 17

5.0 TECHNICAL CONFIG MENU
It is unlikely that the operator will need to access the technical conguration menu in normal use.
the settings within the Technical Cong menu deal with how the instrument handles speed
smoothing, uctuations in application rate, loadcell correction and the printer port setup.
5.1 DISPLAY OPTIONS
MENU
2. TECHNICAL CONFIG
1. DISPLAY OPTIONS
5.1.1 SPEED SMOOTHING
The forward speed display is electronically dampened. If the forward speed is constantly changing
by small increments, you can increase the dampening time to give a steadier readout. The forward
speed will then be calculated over a longer time period, giving a steadier reading.
Adjustable from 0 to 19 seconds. Default : 2 seconds
5.1.2 RATE LOCK-ON
“Rate Lock-On” sets the % by which the application rate uctuates either side of the nominal
application rate before the instrument display changes.
For example, if your actual application rate uctuates in normal operation from 97 kg/ha to
103 kg/ha for a target application of 100 kg/ha, you may decide that it is acceptable for the
instrument to display a steady readout of 100 kg/ha between those limits. ie +/- 3%. In this case
the Rate Lock-On should be set to 3.
Adjustable from 0 to 50% Default : 2%
5.1.3 RATE SMOOTHING
The Application rate display is electronically dampened. If the readouts are constantly chaning by
small increments, you increase the dampening time to give a steadier readout.
Adjustable from 0 to 19 % Default : 2%
5.1.4 OFF TARGET
The Off Target function sets the threshold at which the instrument will alarm “UNDER
APPLICATION” or “OVER APPLICATION” when operating in automatic control mode. It is set as a
percentage either side of the target rate.
Adjustable from 0 to 50% Default : 20%
pg 18

5.2 LOADCELL CORRECTION
The Loadcell Correction menu deals with the setup of the dynamic and static calibration procedure
when loadcells are tted to the spreader.
TECHNICAL CONFIG
2. LOADCELL CORRECTION
5.2.1 CORRECTION SPAN
When in dynamic calibration mode, the instrument will not correct the calibration factor by more
than this percentage.
Default : 5.0%
5.2.2 MIN.STAT WEIGHT
When in static mode, the calibration test cannot be ended until at least this weight has been
spread - both in measured and calibrated weight.
Default : 200.0 kg
5.2.3 DYNAMIC TIME
This is the time period for each dynamic test. The calibration will be updated at this interval.
Default : 30 secs
5.2.4 DYNAMIC WEIGHT
The dynamic test will not end until at least this weight has been spread or until the time period is
elapsed.
Default : 200.0kg
5.2.5 START DELAY
This is the time delay between starting a new bout and the dynamic test starting. This allows time
for the machine to reach normal smooth operating speed.
Default : 10 secs
5.2.6 STEADY WEIGHT
If the a weight uctuation is seen above this level, the weight reading is seen as unstable and a
dynamic test will be aborted.
Default : 0.75%
pg 19

5.3 OVERLOAD LOG
TECHNICAL CONFIG
3. OVERLOAD LOG
In situations when the machine is loaded more than the maximum weight stored in the Spreader
Cong menu a recording will be made in the overload log.
5.4 PRINT CAL DATA
TECHNICAL CONFIG
4. PRINT CAL DATA
It is always a good idea to keep a record of calibration data either in the back of the manual. or as
a print out. Connect the print to the upper serial point. Ensure rst the the port has been
congured for a printer (see ports setup page 29)
Selecting the “PRINT CAL DATA” menu function immediately sends the data to the serial port. The
message “PRINTER BUSY” will be displayed while the data transfer is taking place.
If the bar on the screen stops lling up part way, the instrument cannot communicate with the
printer. Check the connections.
5.5 PIN # CHANGE
The PIN number for the TECHNICAL CONFIG menu can be set to prevent unauthorised users
from accessing the TECHNICAL CONFIG menu and potentailly interfering with the instruments
calibration settings.
TECHNICAL CONFIG
5. PIN # CHANGE
Follow the on screen instructions to change the PIN #.
If you forgot your personalised PIn number you will need to contact Roesner Pty Ltd or RDS for
instructions on reseting the PIN.
pg 20
This manual suits for next models
1
Table of contents
Popular Control System manuals by other brands
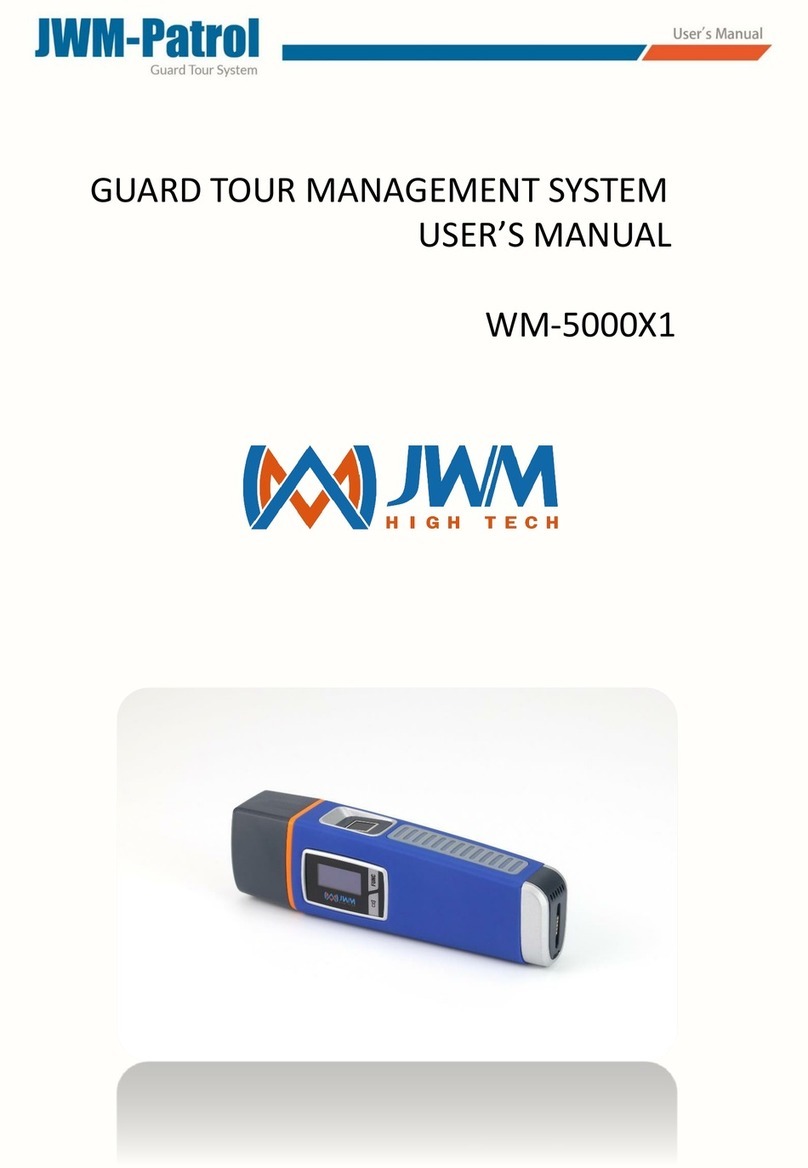
JWM
JWM Patrol WM-5000X1 user manual
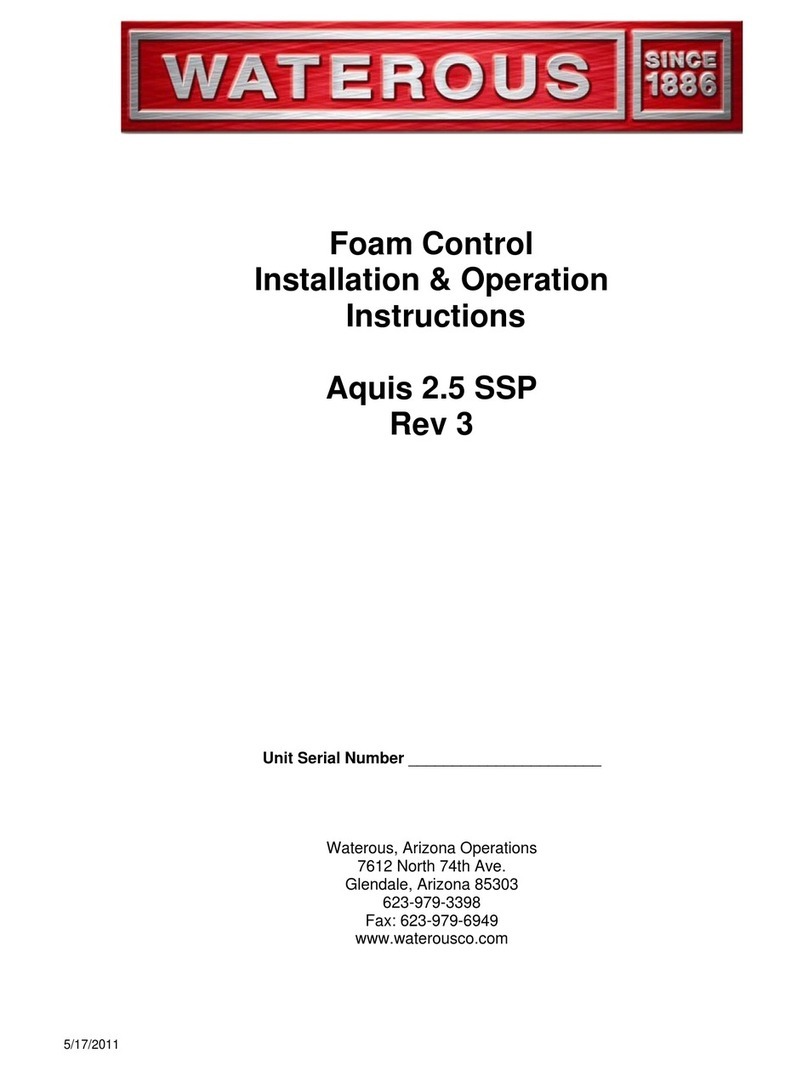
Waterous
Waterous Aquis 2.5 SSP Installation & operation instructions
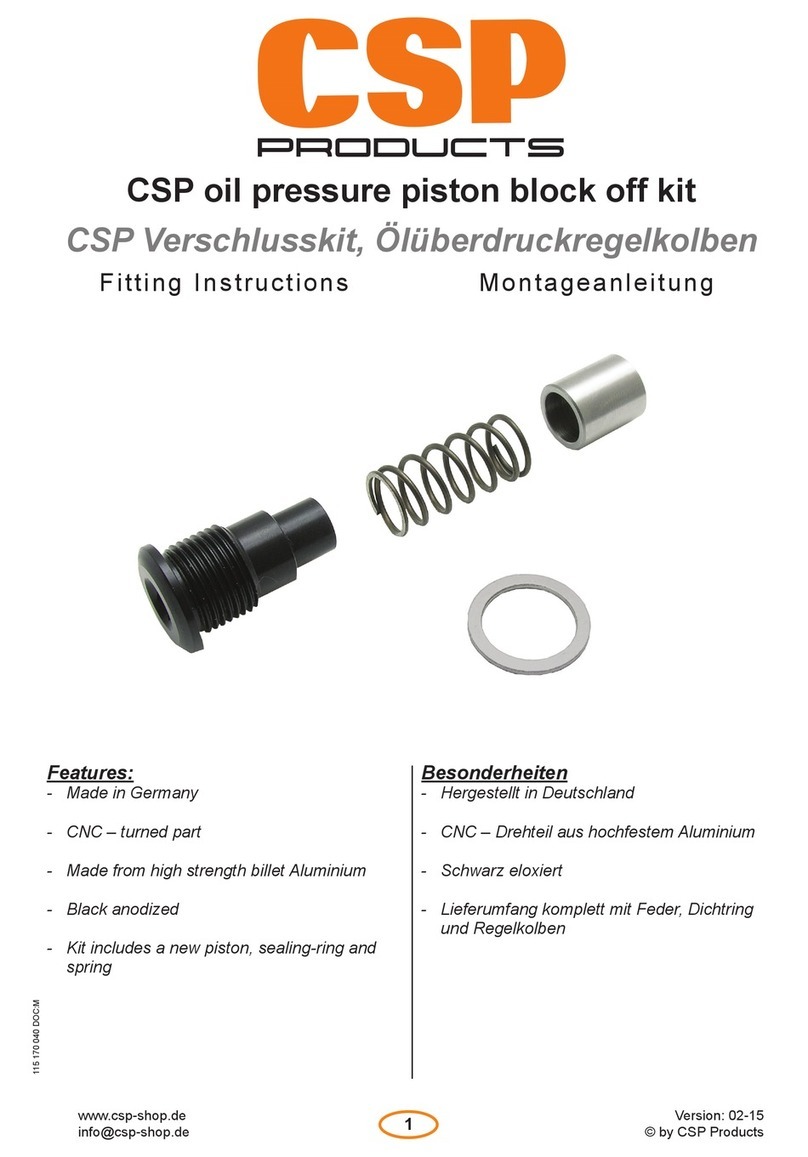
CSP Products
CSP Products 115 170 040 Fitting instructions

iOptron
iOptron iEQ45/8406 manual

Force America
Force America SSC6100 CAN ULTRA Calibration manual
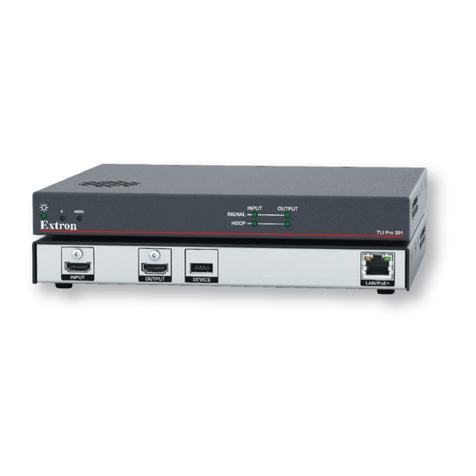
Extron electronics
Extron electronics TLI Pro 201 user guide