SOR 1600 Series User manual

Form 1636 (03.19) ©SOR Inc.
1/16
Installation
Before beginning installation, inspect the level controller for damage that may have
occurred during shipment and remove all cardboard packing material.
The 1600 Series Level Controllers normally ship unassembled as 3 separate parts:
– The level controller body assembly.
– The displacer with swivel.
– The displacer arm.
Thoroughly clean the vessel connection surface to remove any accumulated debris.
Threaded and gasketed surfaces on the controller’s process connection should also be
cleaned before installing the level controller.
When installing the level controller, apply PTFE tape or pipe thread sealant for units
with NPT connections. For units with flanged connections, install with a suitable gasket
between the flange faces.
The SOR
®
1600 Series Level Controllers
are designed for use in liquid level
and interface level applications with
pneumatic instrumentation. For
assistance with the calibration and
maintenance procedures found in these
General Instructions, please visit the
SOR Inc. Youtube channel for video
walkthroughs.
1600 Series
Liquid Level Controllers
General Instructions
Registered Quality System to ISO 9001
Design and
specifications are
subject to change
without notice.
For latest revision, go to
SORInc.com
Table of Contents
Installation...................................... 1
Reference Diagram............................ 4
Maintenance.................................... 4
Parts List ........................................ 8
Repair Kits ..................................... 12
Mounting Reference Drawings .............12
Dimensions ....................................13
Troubleshooting ............................... 15
hl l ll f d h h
NOTE: If you suspect that a product is defective, contact the factory or the SOR
Representative in your area for a Return Material Authorization number (RMA). This
product should only be installed by trained and authorized personnel.

2/16
Form 1636 (03.19) ©SOR Inc.
Refer to Page 12 for mounting reference drawings
START UP
Pneumatic Pilot
Connect supply pressure to the connection point labeled “SUPPLY” on the backside of the
controller case. On the model 1600 sealed controller it is the top connection, while on the
model 1601 non-sealed controller it is the right connection when facing the backside of
the controller case. Connect the device the pneumatic signal is being output to with the
connection point labelled “OUTPUT”.
Electric Pilot
If the 1600 Series level controller was supplied with an electronic switch rather than a
pneumatic pilot, the switch will carry the following ratings:
The SPDT electric pilot uses an explosion proof electric switch to eliminate the need
for a pneumatic gas supply. This is beneficial when redusing fugitive emissions by
no longer using natural gas to power on site pneumatic devices. The electric pilot is
typically used to send an electric signal on high or low level to an electric actuator on a
valve or to a pump for pump control.
Connect the displacer arm with the level controller body by inserting the displacer
arm into the body opening, located on the backside of the controller case. Ensure the
displacer arm is aligned within the body before screwing the arm in.
– If the level controller will utilize a vertically-oriented displacer: screw the displacer
swivel onto the displacer arm then connect the swivel and displacer.
–
If the level controller will utilize a horizontally-oriented displacer: if necessary, first unscrew
the swivel from the displacer before connecting the displacer to the displacer arm.
Electrical power must be disconnected before cover is removed.
Failure to do so could result in severe personal injury or substantial
plant damage.
Contact Rating 15A @ 125, 250 & 480VAC
Agency Approval Rating DIV 1&2, Class I, Groups B, C. & D , DIV 1&2, Class II, Groups
E, F & G, II2G ExdIIB + H2 T6 Gb
Agency UL, CSA, ATEX, IECEx, INMETRO
Wiring Diagram
Blue (C)
Black (NO)
Red (NC)
Green (GND)

Form 1636 (03.19) ©SOR Inc.
3/16
Open the controller case and move the torque bar back and forth by hand and verify the
displacer arm moves freely and is not resting against anything. The displacer arm must
be oriented approximately parallel with the ground – if needed, rotate the adjusting
knob under the balance spring to adjust the displacer arm resting position.
LEVEL ADJUSTMENT
After completing Start Up procedure and with the displacer arm oriented parallel with
the ground, the level set point is ready to be adjusted.
a. To Lower the Level Set Point: Rotate the adjusting knob clockwise to increase
spring tension of the balance spring.
b. To Raise the Level Set Point: Rotate the adjusting knob counterclockwise to
decrease spring tension of the balance spring.
After the level set point is satisfactorily set, the proportional band (dump cycle) is ready
to be adjusted. A larger dump cycle corresponds to a larger span between the controller
on and off points, while conversely a smaller dump cycle results in less time passing
between dumping due to the shortened span between the on and off points.
a. Loosen the thumb screw, located on the sensitivity fulcrum.
b. To Decrease the Dump Cycle: Move the sensitivity fulcrum along the flapper bar in
the direction of the pilot, i.e. towards the smaller numbers.
c. To Increase the Dump Cycle: Move the sensitivity fulcrum along the flapper bar
opposite the direction of the pilot, i.e. towards the larger numbers.
d. A larger dump cycle corresponds to a larger span between the controller on and
off points, while conversely a smaller dump cycle results in less time passing
between dumping due to the shortened span between on and off.
e. Once the dump cycle is appropriately set, tighten the thumb screw on the sensitivity
fulcrum.
LIQUID LEVEL INTERFACE
Loosen the thumb screw, located on the sensitivity fulcrum, and position the
sensitivity fulcrum 1/4” away from the snap ring (see reference diagram Page 4).
a. Begin by slowly rotating the adjusting knob counterclockwise to reduce tension
on the spring, and then allow the upper liquid level to rise until the displacer is fully
submerged.
b. Once the displacer is submerged in only the upper liquid, this adjustment can be
fine-tuned by slowly rotating the adjusting knob clockwise to increase
spring tension until the level controller emits an output pressure signal.
c. Slowly rotate the adjusting knob counterclockwise to reduce spring tension until
the level controller stops sending an output pressure signal.

4/16
Form 1636 (03.19) ©SOR Inc.
Reference Diagram
Cap Screw
Pivot Pin
Torque Bar
Sensitivity Fulcrum
Thumb Screw
Displacer
Arm
Lock Nut
Upper Spring Retainer
Balance Spring
Adjusting Knob
Shaft
Pilot Snap Ring Flapper Bar
Output Connection
Supply Connection
1601 Non-Sealed
Displacer
Arm
Output
Connection
Supply
Connection
1600 Sealed
Displacer
Arm
Torque Arm
Torque Arm
Adjusting Screw
m
m
m
m
m
m
m
m
m
m
m
m
m
m
m
m
m
m
m
m
w
Body
Case
Body
Case
The torque arm calibration is pre-set at the factory and should not be
adjusted. If the torque arm calibration has been tampered with, adjust it such
that the torque bar is parallel with the case bottom while the displacer arm is
positioned in the middle of the body. See reference diagram on Page 4.
Allow the lower liquid level to rise until it reaches the appropriate interface level set point.
a. The interface level set point can be fine-tuned by slowly rotating the adjusting knob
clockwise to increase spring tension until the level controller emits an output
pressure signal.
b. Slowly rotate the adjusting knob counterclockwise to reduce spring tension until the
level controller stops sending an output pressure signal.
If a longer dump cycle is required, loosen the thumb screw and slide the sensitivity
fulcrum away from the snap ring (towards the larger numbers). Re-tighten the thumb
screw and then repeat steps 1) and 2) of the above procedure.

Form 1636 (03.19) ©SOR Inc.
5/16
Maintenance
The following procedure is only for the level controller and does
not apply to the pilot. See Page 6 for pilot removal/replacement
instructions.
LEVEL CONTROLLER FIELD DISASSEMBLY
Slowly rotate the adjusting knob counterclockwise until there is no tension on the
balance spring.
Remove the balance spring and upper spring retainer from the controller case.
Unscrew the lock nut from the flapper bar. Separate the flapper bar from the pivot pin.
Do not remove either of the pivot pins from the controller case.
Do not remove the sensitivity fulcrum or the thumb screw from the
apper bar.
Unscrew the lock nut from the torque bar. Separate the torque bar from the shaft.
Hold the torque arm in place and then loosen the two cap screws until the torque
arm moves freely about the shaft.
Separate the torque arm and the spacer from the shaft.
There are two hex bolts located behind the torque arm that attach the controller
case to the body. Unscrew these bolts and separate the controller case and body.
LEVEL CONTROLLER FIELD REASSEMBLY
Reattach the controller case to the body with two hex bolts, tightening the bolts to
6 ft-lbs.
Slide the washer then the spacer onto the shaft.
If the torque arm adjusting screw has been removed or adjusted, situate the
adjusting screw such that there is an equal amount of thread above and below the
torque arm.
Slide the torque arm back onto the shaft and position the torque arm adjusting
screw perpendicular to the controller body. Loosely attach the two cap screws that
hold the torque arm on the shaft. The torque arm should still move freely about the
shaft.
Slide the torque bar back onto the shaft. With the round tip of the torque arm
adjusting screw touching the torque bar, adjust the torque arm until the torque bar
is parallel with the displacer arm.
Unless the case mounting orientation is being converted, the torque
arm adjusting screw position does not need to change.

6/16
Form 1636 (03.19) ©SOR Inc.
Do not overtighten the lock nut to the torque bar. The lock nut should
be loose enough for the torque bar to rotate with ease.
Slide the torque bar back off of the shaft. Beginning with the cap screw closest to
the slotted end of the torque arm, secure the torque arm to the shaft by tightening
the cap screws to 100 in-lbs.
Slide the torque bar back onto the shaft, making sure the hole for the spring re-
tainer is facing downward. Screw the lock nut back onto the shaft while still leaving
1/16” of space between the lock nut and torque bar.
Slide the flapper bar back onto the pivot pin and re-attach the lock nut – if
converting the case mounting orientation:
a. Unscrew the thumb screw from the sensitivity fulcrum and screw it back into
the opposite side of the sensitivity fulcrum. The sensitivity fulcrum should be
secured in approximately the same position on the flapper bar.
b. For Left Hand Direct Acting / Right Hand Reverse Acting, slide the flapper bar
onto the left pivot pin.
c. For Right Hand Direct Acting / Left Hand Reverse Acting, slide the flapper bar
back onto the right pivot pin.
Position the upper spring retainer so it is seated in the hole on the underside of the
torque bar, and then re-install the balance spring between the adjusting knob and
upper spring retainer.
LEVEL CONTROLLER CASE MOUNTING CONVERSION
Completely disassemble the level controller following the procedure on Page 4.
Reassemble the level controller with the following modifications:
a. The torque arm adjusting screw should be rotated 90° from its original position.
b. The thumb screw should be removed from the sensitivity fulcrum and re-
installed on the opposite side.
c. The torque arm, torque arm adjusting screw, sensitivity fulcrum, torque bar,
flapper bar, balance spring and stud bolt should all be re-assembled into the
opposite side of the controller case.
Do not overtighten the lock nut to the apper bar. The apper bar must
rotate freely around the pivot pin.
Do not overtighten the cap screws.

Form 1636 (03.19) ©SOR Inc.
7/16
Pneumatic Pilot Removal/Replacement
Disconnect the supply and output lines from the backside of the controller case.
For the 1600 sealed controller, the pilot is attached to the case by four bolts
mounted through the pilot clamp. Undo these bolts and remove the pilot from the
controller case.
For the 1601 non-sealed controller, the pilot is attached to the case by two cap
screws mounted through the top of the case. Undo the cap screws and remove the
pilot from the controller case.
Either replace the pilot completely or rebuild it using a pilot repair kit. See Page 12
for part numbers of replacement pilots and pilot repair kits.
Re-install the pilot by reversing the steps followed above. For the 1600 sealed
controller, it is recommended that the pilot gasket be replaced even if it does not
appear to be damaged.
Level Controller Pilot Action Conversion
Slowly rotate the adjusting knob counterclockwise until there is no tension on the
balance spring.
Unscrew the lock nut from the flapper bar. Separate the flapper bar from the pivot pin.
Unscrew the thumb screw from the sensitivity fulcrum and screw it back into the
opposite side of the sensitivity fulcrum.
Slide the flapper bar onto the opposite pivot pin it was removed from. The thumb
screw on the sensitivity fulcrum should be facing outwards.
Screw the lock nut back on to secure the flapper bar to the pivot pin.
The pilot action conversion is now complete and the level controller is ready for
recalibration. See Page 2 for Level Adjustment procedure.
For best performance with your 1600 series Liquid Level Controller,
only genuine SOR replacement parts and repair kits should be used.
See Page 12 for part numbers.
Do not overtighten the lock nut to the apper bar. The apper bar must
rotate freely around the pivot pin.
For electric switch pilot, consult factory for repair-replacement.

8/16
Form 1636 (03.19) ©SOR Inc.
Parts List
1600 SEALED LEVEL CONTROLLER
,7(0 47< '(6&5,37,21
;+(;+($'%2/7
+(;-$0187667
;+(;+($'%2/7
;+(;62&+6&5
;+(;+'6&5(:
+(;/2&.1871</21,16(57667
;5281'+($'0(7$//,&'5,9(6&5(:
+(;187
;+(;+'6&5667
;+(;+'6&5667
)8//7+5($'
;+(;+'6&5(:
$'3751370;137)667
%$&.835,1*7)(2537)(63/,7
%$5$'-867,1*/(9(5$/80,180
%$5)/$33(5
%$572548(
%($5,1*%$//2';,'667
%/2&.%($5,1*
%/2&.%($5,1*&$3
%2'<+(;&$5%2167((/
137
&$6(&21752//(50$&+,1('
&$67,1*&/$03
&$67,1*&/(9,66:,9(/
'(&$/6(16,7,9,7</+
'(&$/6(16,7,9,7<5+
',63/$&(5',$;/21*
'2250$&+,1('
),/7(56&5((136
)2$07$3($'+(6,9(%27+6,'(6
:,'(;7+,&.
)8/&5806(16,7,9,7<1</21:81)
*$6.(72'&25'
'8520(7(56+25($
*$6.(7/(16
*$8*(35(6685(
+($9<'87<635,1*
,16(57'225.12%
.12%'225667
/$%(/6(5,(6/,48,'/(9(/&21752//(5
/(16'225
/(16+2/'(5
/2:(5635,1*5(7$,1(5
0$1,)2/'0$&+,1('
0$1,)2/'&$6(*$6.(7
1$0(3/$7(&21752//(5
1$0(3/$7(625/2*27$//6,=(%/$1.
25,1*%81$1'
25,1*%81$1'
25,1*%81$1'
3,/270$1,)2/'*$6.(7%81$1
3,1*5229(''2:(/',$;/*
5(7$,1(5635,1*833(5
5(7$,1,1*5,1*(;7(51$/(67</(
5(7$,1,1*5,1*(;7(67</(
5,9(7',$;/*667
29$/+'6(0,78%(
6&5(:$'-867,1*81)$
6&5(:7+80%;/*667
6+$)7&21752//(5
6+$)7)/2$7137
61$33,/27$66(0%/<6($/('
63$&(5
635,1*'225/$7&+
678')/$33(5%$5
6:,9(/)(0$/($'$37(5
6:,9(/0$/($'$37(5
72/(5$1&(5,1*
:$6+(52';,';7+.66

Form 1636 (03.19) ©SOR Inc.
9/16
1600 SEALED
LEVEL CONTROLLER
6(&7,21%%
6&$/(
6((6(&7,21%%
,7(0 47< '(6&5,37,21
%$&.835,1*7)(2537)(63/,7
%($5,1*%$//2';,'667
%/2&.%($5,1*
%/2&.%($5,1*&$3
%2'<+(;&$5%2167((/
137
25,1*%81$1'
25,1*%81$1'
25,1*%81$1'
6+$)7&21752//(5
63$&(5
72/(5$1&(5,1*
:$6+(52';,';7+.66
Linear = mm/inches
Drawing 5678301

10/16
Form 1636 (03.19) ©SOR Inc.
1601 NON-SEALED LEVEL CONTROLLER
5()(5(1&($66(0%/<
,7(0 47< '(6&5,37,21
+(;-$0187667
;+(;+($'%2/7
;+(;+'6&5(:
+(;/2&.1871</21,16(57667
;+(;+($'6&5(:667
;5281'+($'0(7$//,&'5,9(6&5(:
+(;187
;+(;+'6&5667
;+(;+'6&5667
)8//7+5($'
;+(;+'6&5(:
$'$37(51370;137)
$'3751370;137)667
%$&.835,1*7)(2537)(63/,7
%$5$'-867,1*/(9(5$/80,180
%$5)/$33(5
%$572548(
%($5,1*%$//2';,'667
%/2&.%($5,1*
%/2&.%($5,1*&$3
%2'<+(;&$5%2167((/
137
&$6(&21752//(50$&+,1('
&$67,1*&/(9,66:,9(/
'(&$/6(16,7,9,7</+
'(&$/6(16,7,9,7<5+
',63/$&(5',$;/21*
'2250$&+,1('
)2$07$3($'+(6,9(%27+6,'(6
:,'(;7+,&.
)8/&5806(16,7,9,7<1</21:81)
*$6.(72'&25'
'8520(7(56+25($
*$6.(7/(16
*$8*(35(6685(/+
*$8*(35(6685(5+
+($9<'87<635,1*
,16(57'225.12%
.12%'225667
/$%(/6(5,(6/,48,'/(9(/&21752//(5
/(16'225
/(16+2/'(5
/2:(5635,1*5(7$,1(5
1$0(3/$7(&21752//(5
1$0(3/$7(625/2*27$//6,=(%/$1.
25,1*%81$1'
25,1*%81$1'
25,1*%81$1'
3,1*5229(''2:(/',$;/*
5(7$,1(5635,1*833(5
5(7$,1,1*5,1*(;7(51$/(67</(
5(7$,1,1*5,1*(;7(67</(
5,9(7',$;/*667
29$/+'6(0,78%(
6&5(:$'-867,1*81)$
6&5(:7+80%;/*667
6+$)7&21752//(5
6+$)7)/2$7137
61$33,/27$66(0%/<
63$&(5
635,1*'225/$7&+
678')/$33(5%$5
6:,9(/)(0$/($'$37(5
6:,9(/0$/($'$37(5
72/(5$1&(5,1*
:$6+(52';,';7+.66

Form 1636 (03.19) ©SOR Inc.
11/16
6(&7,21((
6&$/(
1601 NON-SEALED
LEVEL CONTROLLER
6((6(&7,21((
,7(0 47< '(6&5,37,21
%$&.835,1*7)(2537)(63/,7
%($5,1*%$//2';,'667
%/2&.%($5,1*
%/2&.%($5,1*&$3
%2'<+(;&$5%2167((/
137
25,1*%81$1'
25,1*%81$1'
25,1*%81$1'
6+$)7&21752//(5
63$&(5
72/(5$1&(5,1*
:$6+(52';,';7+.66
Linear = mm/inches
Drawing 5678300

12/16
Form 1636 (03.19) ©SOR Inc.
Repair Kits
Pneumatic Pilot Replacement Kits Throttling Quick Opening
Sealed (1600) With Plugs 5678390P 5678292P
Non-Sealed (1601) Brass 5678388P 5678393P
Vibration Resistant Brass 5678386P 5678395P
316SS 5678389P 5678394P
Vibration Resistant 316SS 5678387P 5678396P
Without Plugs 5678392P 5678123P
Sealed Door Assembly 5678484P
Standard Door Assembly 5678483P
Displacer Assembly Kits Displacer Kit 12” 316SST 5678481P
Displacer Kit 12” PVC 5678480P
Displacer Kit 24” 316SST 5678482P
Pilot Repair Kits Quick Opening 5678476P
Throttling 5678477P
Swivel Assembly Kit 5678485P
Process Seal Repair Kit BUNA-N 5678478P
Process Seal Repair Kit VITON 5678479P
Mounting Reference Drawings
LEFT HAND MOUNT RIGHT HAND MOUNT

Form 1636 (03.19) ©SOR Inc.
13/16
101.6
4
101.6
4
73.0
2-7/8
A
124.
6
4-29
/
1/4" NPTF
1
Dimensions
20.2
51/64
B
A
124.6
4-29/32
131.5
5-11/64
43.3
1-45/64
/4" NPTF
1
Linear = mm/inches
Drawing 5678451
222.3
8-3/4
205.8
8-7/64
53.2
2-3/32
97.6
3-27/32
C
2" NPTM
1
NOTES:
1. DIMENSION APPROXIMATE AND BASED ON A FIVE THREAD ENGAGEMENT.
1
1600 SEALED
LEVEL CONTROLLER
Dimensions are for
reference only. Contact
the factory for certified
drawings for a particular
model number.
DISPLACER DIM A DIM B
1.88 X 12 PVC 340.8
13-27/64
47.6
1-7/8
1.66 X 12 316SST 340.8
13-27/64
42.2
1-21/32
1.66 X 24 316SST 645.6
25-27/64
42.2
1-21/32
ARM LENGTH DIM C
10 INCH 130.4
5-1/8
15 INCH 257.4
10-1/8

14/16
Form 1636 (03.19) ©SOR Inc.
25.4
1
69.1
2-23/32
152.5
6
124.6
4-29/
3
A
1/4" NPTF
1
16.4
41/64
42.9
1-11/16
109.4
4-5/16
124.6
4-29/32
A
B
1/4" NPTF
1
C53.3
2-3/32
205.6
8-3/32
222.3
8-3/4
97.6
3-27/
3
2" NPTM
1
NOTES:
1. DIMENSION APPROXIMATE AND BASED ON A FIVE THREAD ENGAGEMENT.
1
Linear = mm/inches
Drawing 5678450
1601 NON-SEALED
LEVEL CONTROLLER
Dimensions are for
reference only. Contact
the factory for certified
drawings for a particular
model number.
ARM LENGTH DIM C
10 INCH 130.4
5-1/8
15 INCH 257.4
10-1/8
DISPLACER DIM A DIM B
1.88 X 12 PVC 340.8
13-27/64
47.6
1-7/8
1.66 X 12 316SST 340.8
13-27/64
42.2
1-21/32
1.66 X 24 316SST 645.6
25-27/64
42.2
1-21/32

Form 1636 (03.19) ©SOR Inc.
15/16
Troubleshooting
Symptom Probable Cause(s) Corrective Action(s)
The output pressure
gauge is indicating an
output signal when:
Fluid level is
below the displacer
on a direct action
controller.
Fluid level is
above the displacer
on a reverse action
controller.
There is too much
tension on the balance
spring, resulting in too
much force on the torque
bar.
The displacer arm
is set too high or the
displacer is contacting an
object inside the vessel.
Slowly rotate the adjusting knob
counterclockwise to reduce spring
tension until the level controller stops
sending an output pressure signal.
Check the output pressure gauge again
when the liquid level rises (direct action)
or falls (reverse action).
Move the torque arm up and down to
check the displacer arm position.
—If the torque arm moves only in one
direction, this indicates the displacer
arm is riding at the top/bottom of the
vessel connection.
—If the torque arm moves too easily,
this indicates the displacer is no longer
connected to the displacer arm.
—Adjust the displacer arm so it’s
centered in the vessel connection.
The output pressure
gauge is indicating no
output signal when:
Fluid level is above
the displacer on a
direct action controller
Fluid level is
below the displacer
on a reverse action
controller.
There is not enough
tension on the balance
spring, resulting in not
enough force on the
torque bar.
The displacer arm
is set too low or the
displacer is contacting an
object inside the vessel.
Slowly rotate the adjusting knob
clockwise to increase spring tension
until the level controller begins sending
an output pressure signal. Check the
output pressure gauge again when the
liquid level falls (direct action) or rises
(reverse action).
Move the torque arm up and down to
check the displacer arm position.
—If the torque arm moves only in one
direction, this indicates the displacer
arm is riding at the top/bottom of the
vessel connection.
—If the torque arm moves too easily,
this indicates the displacer is no longer
connected to the displacer arm.
—Adjust the displacer arm so it’s
centered in the vessel connection.
Before beginning maintenance or troubleshooting, isolate the level
controller from the process and ensure that all pressure has been vented
from the controller body. Disconnect and vent the supply and output lines
connected to the back of the controller case.

16/16
Form 1636 (03.19) ©SOR Inc.
Symptom Probable Cause(s) Corrective Action(s)
The controller fails
to repeat at the same
liquid level after each
dump cycle, and
occasionally fails to
dump or shut off at all.
The torque bar
appears difficult to
move, and when
depressed the torque
bar does not return
to original position
quickly.
Foreign material has
accumulated inside the
level controller body.
Disconnect the level controller from the
process and flush the debris out of the
body using a suitable solvent solution.
The pilot bleeds
supply pressure
continuously.
For a snap pilot,
foreign debris has
become trapped under
the ball inside the pilot.
For a throttling pilot,
foreign debris has
become trapped under
the pin inside the pilot.
Remove the pilot from the controller
case using the procedure on Page
5. Unscrew the cap screws from the
bottom of the pilot which allows it to
come apart. Carefully clean all of the
pilot components and then reassemble
the pilot and install it back into the
controller case.
In an interface level
application:
Sometimes the
vessel overfills or
drains completely
(especially with
changing process
temperature).
Additionally, the
displacer arm is not
riding at the top/
bottom of the vessel
connection nor is the
displacer contacting
an object inside the
vessel.
The specific gravities
of the upper and lower
liquid are close and a
temperature change is
causing them to vary and
become too close for
interface level detection.
The displacer is not large
enough to detect the
difference in the specific
gravities.
Contact SOR customer service and
provide the exact specific gravities
or API gravities for both the upper
and lower liquid of the interface. SOR
engineering will determine appropriate
displacer sizing per the provided
application parameters.
14685 West 105th Street, Lenexa, KS 66215
913-888-2630
800-676-6794 USA
Fax 913-888-0767
SORInc.com
This manual suits for next models
2
Table of contents
Other SOR Control System manuals
Popular Control System manuals by other brands
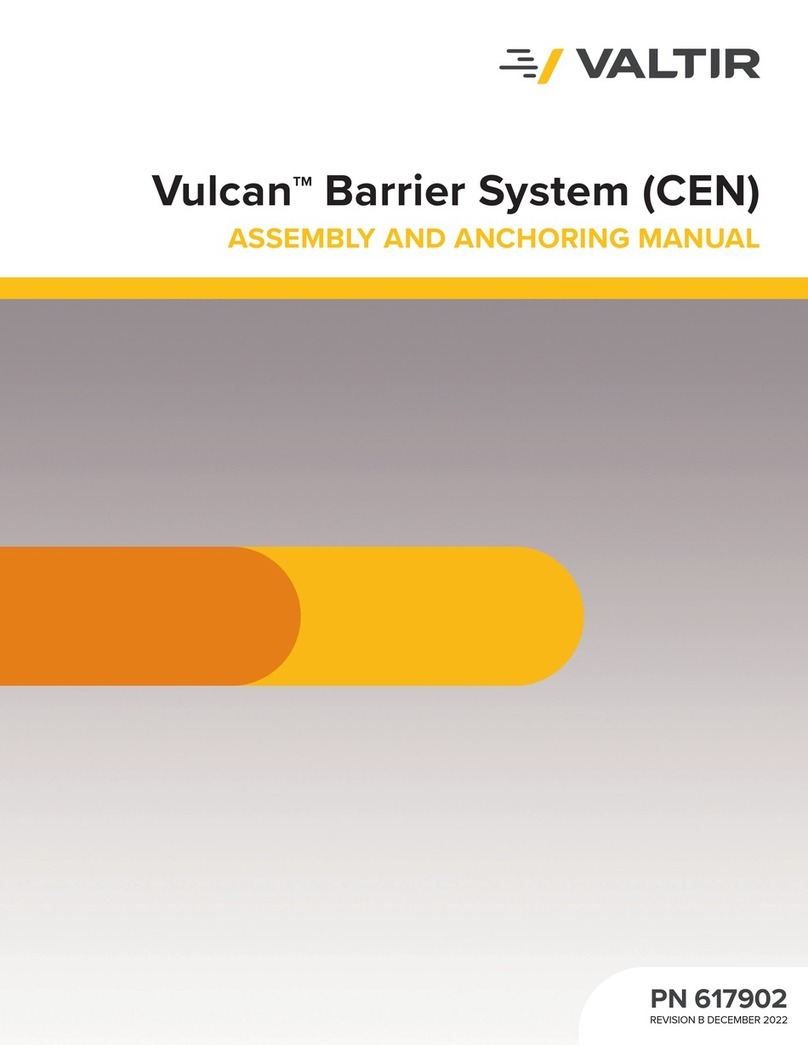
VALTIR
VALTIR Vulcan Barrier System CEN Assembly manual
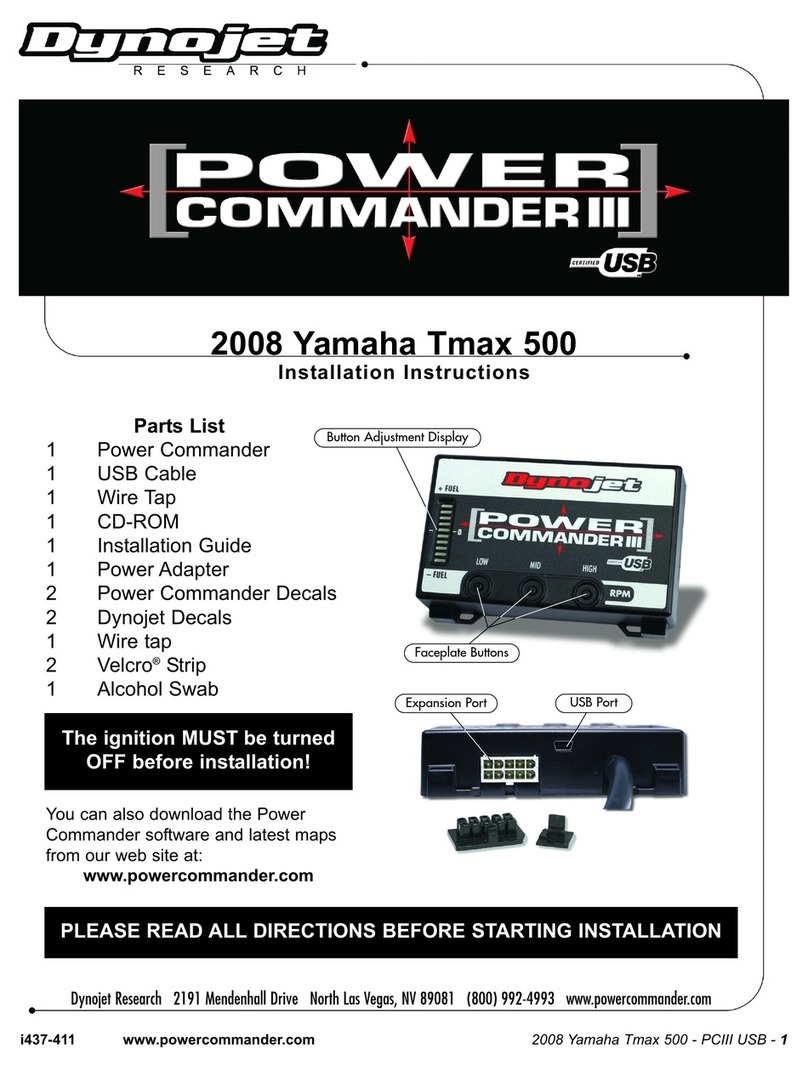
Dynojet
Dynojet POWER COMMANDER 3 Installation Instructions and Technical Information

Siemens
Siemens SIPLUS HCS4300 PROFINET Compact operating instructions
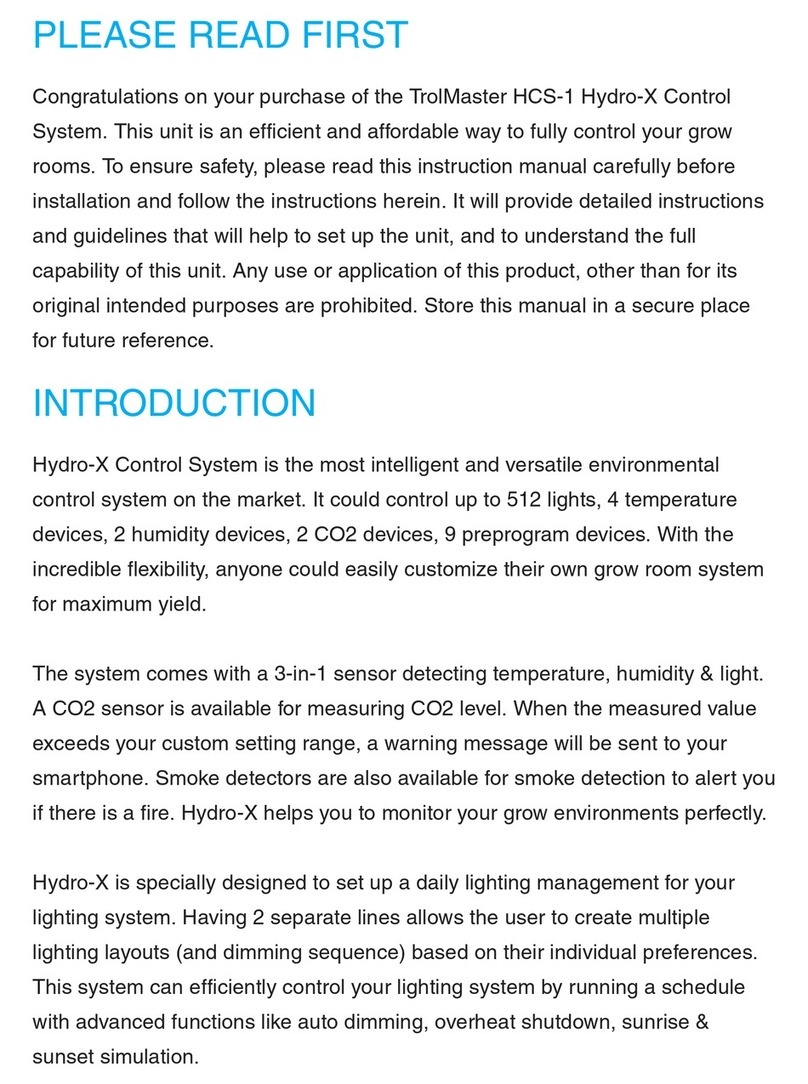
TrolMaster
TrolMaster HCS-1 manual
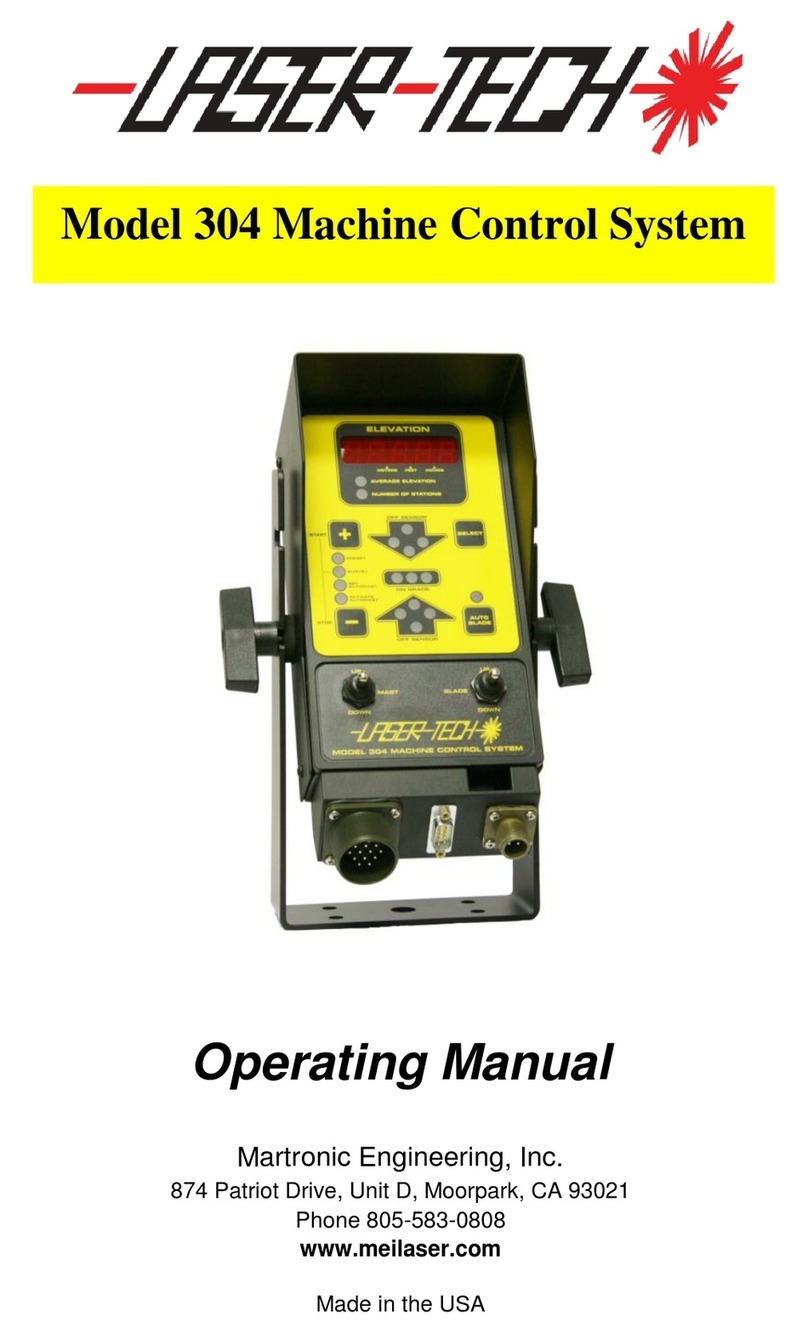
Martronic Engineering
Martronic Engineering Laser Tech 304 operating manual
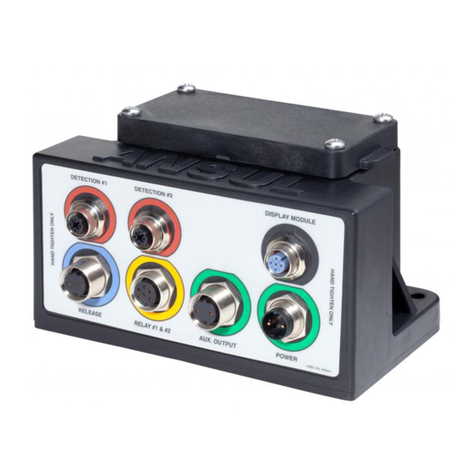
Ansul
Ansul CHECKFIRE 210 owner's guide