Maxim THOMPSON MILLER LEAMAN PDA/ATF-MAX User manual

Page 1
Table of Contents
I. Safety Consideraons..…………………………………….. 1
II. Descripon………………...…...………………...…………… 1
III. System Overview……………………………………………. 2
IV. Operaon……………………………………………...………. 3
V. Menu Screens……………..…..……………………………… 4
VI. Layout & I/O Conguraon….………….…………….. 8
VII. Electrical Connecons…………………………………… 9
VIII. Electrical Schemac……………………………………… 10
IX. Limited Warranty & Contact Info…………………… 11
I. SAFETY CONSIDERATIONS
GENERAL WARNING
Ensure all appropriate personnel read owner’s manual prior to installaon and/or operaon of controller. Failure to
Comply with instrucons and safety precauons could lead to personal injury or product damage. Please call
and ask to speak with one of our customer service representaves if there are any quesons.
CAUTION
Disconnect controller from power source before servicing or removing cover.
II. DESCRIPTION
The PDA/ATF-MAX is a dual purpose controller for both monitoring the pressure dierenal with alarm indicator and automacally controlling
the ush valve of a Thompson strainer.
OWNER’S MANUAL

Page 2
III. SYSTEM OVERVIEW
The PDA/ATF-MAX system consists of the following primary components:
The controller interface contains the controller screen and keypad interface as shown. The clear cover provides protecon for the
controller and can be opened with the two latches on the side of the controller housing to access the keypad.
A) PDA/ATF-MAX controller
B) Power supply
C) Transducer / Wiring assembly
D) Mounng bracket
E) Flush valve assembly
A) Controller Screen
B) Keypad

Page 3
Startup
1) Plug in the power plug into a standard 115VAC wall outlet
2) Upon power-up, the company informaon screen will be shown for 15 seconds.
3) Aer 15 seconds, the screen will change to the manifold pressure screen and will begin monitoring dierenal pressure across
the strainer.
Automac Flushing
Under normal operaon, a med ush will be iniated on a periodic schedule dened by the PDA/ATF-MAX programmed seng.
(every 24 hours per factory seng).
In addion, a med ush will be iniated when the dierenal pressure reaches the setpoint dened by the PDA/ATF-MAX
sengs.
See the MENU SCREENS secon for informaon on changing factory sengs.
Consecuve Flush Alarm
If three consecuve ushing operaons are detected by the PDA/ATF-MAX, a consecuve ush alarm will be triggered and no addi-
onal ush cycles will be iniated unl the alarm is cleared.
To reset the Consecuve Flush Alarm, rst, correct the cause of the alarm, then push the red ESC buon on the controller while a
Status screen is displayed. The oponal Customer’s Remote Reset input, Input iB, allows for a remote reset of the Consecuve
Flush Alarm.
Scrolling through Menu Screens
The PDA/ATF-MAX allows the operator to scroll through a selecon of menu screens by pressing the A or B buons. Press A
to scroll backward to the previous menu or press B to scroll forward to the next menu. The LCD backlight will automacally
turn on for 5 minutes when a buon is pressed, thus allowing the operator to easily view the menus in low light situaons.
Changing Parameter Values
To change an adjustable value, rst scroll to the appropriate menu screen using the A or B buon. Follow the direcons below to
modify the value.
1) The current selected value will show ashing blocks. Use the + or - keys to select another value if desired.
2) Press OK on the selected value. The value will change from ashing blocks to ashing numbers. Flashing blocks indicate the
value is locked into memory. Flashing numbers indicates the value is unlocked and can be changed.
3) Press the + or - buons to change the value. Holding the + or - buon will allow the value to increase at a faster rate aer the
rst 10 increments have passed.
4) When nished, press OK to save the change to memory. The value will return to ashing blocks.
REFER TO THE MENU SCREENS SECTION FOR DETAILED INFORMATION ON EACH SCREEN AND/OR PARAMETER.
IV. OPERATION

Page 4
V. MENU SCREENS
Miller-Leaman Inc.
800-881-0320
Power Up Screen
The Power Up screen displays the company informaon for Miller
Leaman. Each me the PDA/ATF-MAX is plugged in, or when power is
returned aer a loss, this screen will be displayed for 15 seconds. The
Power Up screen can be viewed by unplugging the PDA/ATF-MAX’s
power, then plugging it back on again.
Manifold Pressure Screen:
Aer 15 seconds, the Power Up screen will be changed to the Manifold
Pressure screen. The Manifold Pressure Screen displays the pressure in
PSI for inlet manifold, outlet manifold, and the calculated dierenal
pressure between the inlet and outlet manifolds.
Manifold Pressure
Inlet : 0034.0
Outlet : 0032.0
PSID : 0002.0
Status: OFF MAX
PSID : 00.0
Inlet Pressure Low
PSID : 00.0
Status: OFF MAX
>> High PSID <<
Status: OFF MAX
The Inlet Pressure transducer is monitored to sense sucient Inlet
Pressure and allow Timed Flushes, and Dierenal Pressure Flushing.
When the inlet pressure is sensed as lower than the Setpoint, the
Flush Interval mer will be paused, and a med Flush will not occur.
Dierenal Pressure Flushing will also be inhibited. DP sensing will
connue, and the Status Screen will display >> High PSID << on the
second line. When the Inlet Pressure is sensed as low, the top line of
the Status Screen will display Status: OFF MAX alternang with Inlet
Pressure Low.
The Status Screens
The status screens provide system feedback, allowing the operator to monitor when and how the Flush cycle is occurring. A Flush
cycle can be started manually, automacally via the Flush Interval Timer or the Pressure Dierenal Transducers (PSID), or remote-
ly by oponal Customer Input Signal.
The current status of the controller is displayed as follows:

Page 5
V. MENU SCREENS (CONT.)
Status: AUTO MAX
PSID : 0003.0
Press OK to Start
A Flush Cycle
Status: AUTO MAX
>> High PSID <<
Press OK to Start
A Flush Cycle
Status: ON MAX
Flush Cycle
Press ESC to Stop
Status: AUTO MAX
PSID : 0003.2
Press OK to Start
A Flush Cycle
Status: ON MAX
>> System Alarm <<
Press ESC to Stop
Status: AUTO MAX
Indicates that the Inlet Pressure is not Low, and the controller is waing
for a Flush cycle to begin. The system is assumed to be in normal ltra-
on mode and owing water. The Flush interval mer is running. The
controller displays Status: AUTO MAX when the Inlet Pressure in not
low and a Flush cycle has not begun. A Flush can occur from the Timer,
a high pressure dierenal via the Pressure Transducers, indicated as
>> High PSID << on the display, manually by the operator by pressing
the green OK buon on the controller, or by the Customer Input Signal.
Status: ON MAX
Indicates that the system is in a Flush cycle, iniated either by the Oper-
ator, by the Flush Interval Timer, the Pressure Transducers, or by the
Customer Input Signal. The controller will stop displaying the PSID val-
ue, but will instead indicate Flush Cycle.
The Flush Valve is opened, and the Alarm Light/Sounder output is ash-
ing. This output ashes the Light and Sounder throughout the enre
Flush cycle. The Flush Duraon is nominally set for 8 seconds. The Flush
Duraon me is adjustable - see Setup screen #3 for informaon.
Aer this Flush duraon me, the Flush Cycle is complete. The Open
Flush Valve Output will be turned o, the Alarm Light/Sounder will be
turned o, and the Status Screen will display Status: AUTO MAX.
Status: System Alarm
On any of the status screens, a System Alarm screen can be acvated.
The second line down will be alternately ashing >> System Alarm <<
and whatever was on line 2 before the system alarm occurred.
A system alarm can be any customer specic alarm. The only standard
system alarm is the Consecuve Flush Alarm. This alarm occurs when
the Flush cycle has been iniated three mes in a row by the Pressure
Transducers (PSID). Output #4 will be turned ON, which will then ener-
gize Relay 1 (R-1). Relay 1 provides a Dry Contact signal for the Custom-
er’s Consecuve Flush Alarm monitoring.
The Consecuve Flush Alarm will also cause the Alarm Light/Sounder to
change from ashing to steady ON. The Consecuve Flush Alarm will
also disable any addional Flush Cycles from occurring.

Page 6
Flush Interval & PSID Setpoint Screen
The user-dened interval at which the system will iniate an automac
Flush cycle. The Flush Interval mer resets aer any Flush cycle occurs
(by mer, PD Transducers, operator, or Customer Input Signal). This
value is adjustable from 1 minute to 1000 hrs. Seng both values to
zero will turn o the Flush mer. It is recommended that the operator
adjust the Flush interval mer so that the system Flushes by me be-
fore the pressure dierenal set-point is reached. Factory Preset value
is 24 Hours. This setpoint is located on Screen 2.
The Pressure Dierenal seng in PSI, which when compared to the
calculated Dierenal Pressure from the Inlet and Outlet pressure
transducers, will cause a Flush cycle to begin when exceeded. The rec-
ommended PD setpoint is 1-2 PSID above the “clean” PSID reading at
the systems MAXIMUM ow rate. Seng this PSID Setpoint at low ow
may result in connuous Flushing at higher ow rates, since the Pres-
sure Dierenal increases with ow rate. This value is adjustable from 1
to 30 PSID. Factory preset is 7 PSID. This set-point is located on Screen
2.
Flush Duraon Screen
The me alloed for the Flush Valve to be open. This me should be set
according to the type of lter and the nature of the material being l-
tered. This value is adjustable from 5 to 300 seconds. Factory Preset
value is 8 seconds. This setpoint is located on Screen 3. Please Note -
Flush Valve is not completely open unl 3 seconds into this me val-
ue.
V. MENU SCREENS (CONT.)
Inlet Low Pressure Setpoint Screen
The Inlet Pressure transducer is monitored to sense sucient Inlet Pres-
sure and allow Timed Flushes, and Dierenal Pressure Flushing. On
these systems, when the inlet pressure is sensed as lower than the Set-
point, the Flush Interval mer will be paused, and a med Flush will not
occur. Dierenal Pressure Flushing will also be inhibited. DP sensing
will connue, and the Status Screen will display >> High PSID << on the
second line. When the Inlet Pressure is sensed as low, the top line of
the Status Screen will display Inlet Pressure Low.
Setpoint Adjustment - The Inlet Low Pressure Setpoint is adjustable
from 5 (PSI) to 20 (PSI). Factory Preset value is 15 (PSI). This setpoint is
located on Screen 4
Inlet Low Pressure
Setpoint: 00015
Flush Duration
Seconds: 00008
Flush Interval
HOURS:MM 00024:00
Enter
PSID Setpoint 07

Page 7
Flush Counters Screen
Trip: The number of Flush cycles that have occurred since the counter
was last reset. This includes cycles iniated both manually and auto-
macally. This counter can be reset by pressing the red ESC buon from
the Flush Counters screen.
Life: The number of Flush cycles that have occurred in the controller’s
lifeme. This includes cycles iniated both manually and automacally.
This counter cannot be reset.
Time Since Last Flush & Triggered By Screen
This screen is READ ONLY for informaon and is not adjustable. The
screen shows the amount of me that has elapsed since the system last
Flushed (example: 00011:30 is 11 hours and 30 minutes) and how the
last Flush was triggered. There are four trigger possibilies:
1) Local Operator - Flush triggered manually by an operator
2) Timer - the backush was triggered by me as set on the Backush
Interval screen.
3) PD Transducer - the Flush was triggered by a high pressure dieren-
al, as set on the PSID setpoint.
4) Customer Input - Oponal Customer’s Input signal at input I1 iniat-
ed the Flush Cycle.
V. MENU SCREENS (CONT.)
Flush Counters
Trip: 00010
Life: 000000010
Press ESC to Reset
Time Since Last
Flush 00000:04
Triggered By:
PD Transducers
Controller ID Screen
This screen is READ ONLY and is used to idenfy the controller version
and ID.
Maxim4 PDA/ATF-MAX
Controller v.3.5
Copyright(c)2021
ML31155

Page 8
VI. LAYOUT & I/O CONFIGURATION
Outputs
(Note - each output’s le terminal has been connected to the 24VDC power. The output’s right terminal provides the output sig-
nal)
Output #1 controls the Flush valve.
Output #2 is not assigned.
Output #3 is a relay output for the Alarm Light/Sounder - DP Alarm is ashing and Consecuve Flush Alarm is steady.
Output #4 Consecuve Flush Alarm signal - relay output turned on when the Consecuve Flush count reaches the setpoint. This
output is wired to the coil of Relay 1 (see above) to provide a Dry Contact output.
Inputs
I1 - The oponal Customer Iniate Flush input will signal the PDA/ATF-MAX to start a Flush cycle.
IB - The oponal Customer Remote Alarm Reset input will signal the PDA/ATF-MAX to remotely reset the Consecuve Flush Alarm.
The Analog/Digital Input locaons allow Miller-Leaman Inc. to design customer specic programs. These programs are then able to
receive and process both digital and analog signals from devices such as Pressure Transducers, Flow-meters, Level Switches, etc.
Inputs IC & ID are the Inlet and Outlet Pressure Transducer connecons. These provide a 0-10Vdc signal into the controller. These
signals are converted into pressure level values and compared to each other for the pressure dierenal value. When the PD value
exceeds the PD setpoint, the PDA/ATF-MAX is signaled to start a Flush cycle. The Inlet Pressure Transducer also is used to disable
the Flush Timer and Flush Signal from Dierenal Pressure, should the Inlet Pressure be less than the Inlet Low Pressure Set-point.
Menu
Screen
Keypad
Audible / Visual
Alarm

Page 9
VII. ELECTRICAL CONNECTIONS
NOTE: When using an external power source, the input power to the Controller must be the same as indicated on the
upper le side of the PDA/ATF-MAX. Typically the controller is 24 volts DC. Plug the provided 24VDC Power Supply into
a standard 120VAC Outlet, observing all state and local codes.
Flush Valve
The Flush Valve is connected to Output#1 terminal(+ signal, white wire), Common (-) power termi-nal (Power Common, black
wire), and 24VDC (+) power terminal (Power +, red wire). Please Note - with power on and no signal, the Flush Valve will
move to its closed posion, unl it is closed.
Pressure Transducers
The Pressure Transducers have a three wire connecon, white assigned to the input (IC or ID), blue to the Common (-) terminal,
and the brown to the 24VDC Power (+) terminal .
Customer Iniated Flush Signal (Oponal)
The oponal Customer Iniate Flush Signal input is connected to Input I1. Please Note - this signal must be a discrete 24VDC
signal, that references the Common (-) terminals.
Customer Remote Alarm Reset Signal (Oponal)
The oponal Customer Remote Alarm Reset Signal input is connected to Input IB. Please Note - this signal must be a discrete
24VDC signal, that references the Common (-) terminals.
Consecuve Flush Alarm Output Signal (Dry Contact, Oponal)
Output #4 is the discrete Consecuve Flush Alarm 24VDC output signal, that is connected to the coil of Relay 1 (R-1). This relay
provides a Dry Contact connecon for Customer Consecuve Flush Alarm signal.
Review the Electrical Schemac secon prior to making any connecons to the controller.

Page 10
VIII. ELECTRICAL SCHEMATIC

Page 11
IX. WARRANTY
This warranty is given by Miller-Leaman, Inc. (MLI) and is governed by the Laws of the State of Florida. Venue and jurisdicon of any case or con-
troversy related to the use of this product or this warranty shall lie exclusively in the State Courts of Volusia County, Florida. MLI warrants its
Products against defects in material and workmanship, as per the product warranty schedule listed below, if properly installed, maintained and
operated in accordance with MLI instrucons and good industry pracce, excluding ordinary wear, corrosion, erosion, chemical or abrasive ac-
on. This warranty shall not apply to any Products or parts of Products that (a) used or operated in any applicaon outside the stated specica-
ons or design limitaons of said Products; or (b) have been damaged or in any way altered due to misuse, negligence or accidents; or (c) have
been repaired or altered in any manner outside of MLI factory, unless by express authorizaon of MLI; or (d) have been used in a manner contrary
to MLI instrucons or recommendaons, including without limitaon with respect to site preparaon, maintenance or environmental condions.
MLI MAKES NO OTHER REPRESENTATIONS OR WARRANTIES, EXPRESS OR IMPLIED, INCLUDING, BUT NOT LIMITED TO, ANY IMPLIED WARRAN-
TY OF MERCHANTABILITY OR FITNESS FOR A PARTICULAR PURPOSE. IN NO EVENT SHALL MLI BE LIABLE FOR ANY DELAY, INCONVENIENCE,
WORK STOPPAGE, CARTAGE, SHIPPING, LOSS OF USE OF EQUIPMENT, LOSS OF TIME, INJURY OR DAMAGE TO ANY PERSON, DEATH OF ANY
PERSON, LOSS OF PROFITS OR ANY DIRECT OR INDIRECT INCIDENTAL OR CONSEQUENTIAL LOSS OR DAMAGES RESULTING FROM OR AT-
TRIBUTABLE TO THE USE OF THE PRODUCT. The sole obligaon of MLI under this warranty is to repair or replace, at MLI opon, any Product or
any part or parts thereof found to be defecve. MLI makes no warranes, express or implied, for any goods not manufactured or developed by
MLI and shall assign to Buyer any warranty for such goods extended to MLI by the Manufacturer and Buyer shall look solely to such warranty in
the event of a claim or acon relang to such goods. Warranty period: 12 months from factory ship date.
ML40190—PDA/ATF-MAX Owner’s Manual—Rev A
Office Hours: 8 AM – 5 PM Eastern Time
Web: www.millerleaman.com
Email: support@millerleaman.com
800 Orange Avenue, Daytona Beach, FL 32114
Phone: (386) 248-0500 / Fax: (386) 248-3033
The PDA/ATF-MAX is a product of Miller-Leaman, Inc.
Table of contents
Other Maxim Controllers manuals
Popular Controllers manuals by other brands
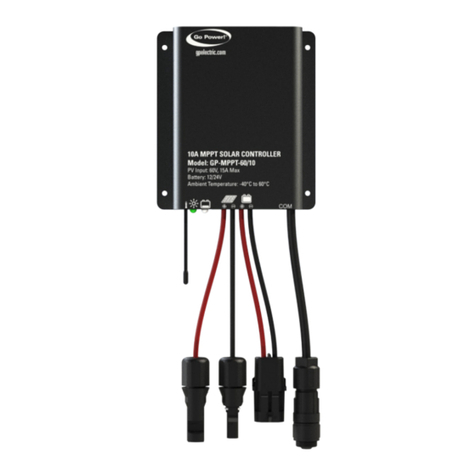
Dometic
Dometic GP-MPPT-60/10 user manual
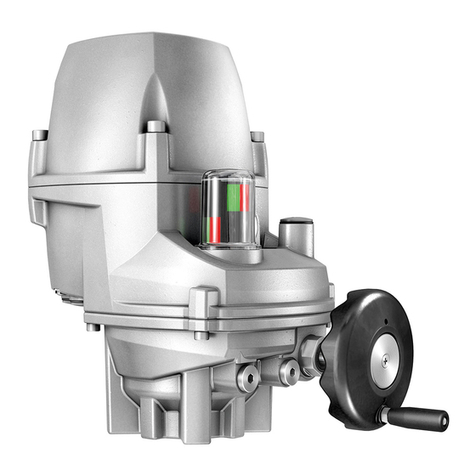
AUMA
AUMA PROFOX PF-Q80 manual
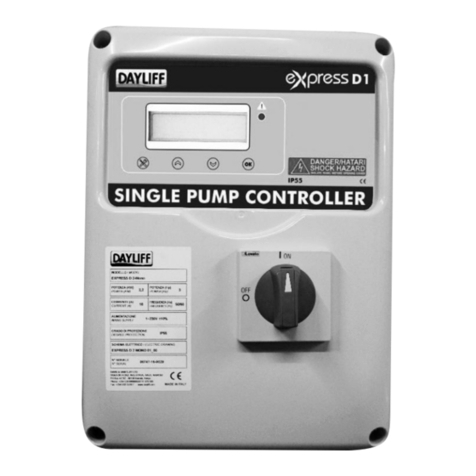
DAYLIFF
DAYLIFF EXPRESS D1-1ph Installation & operating manual
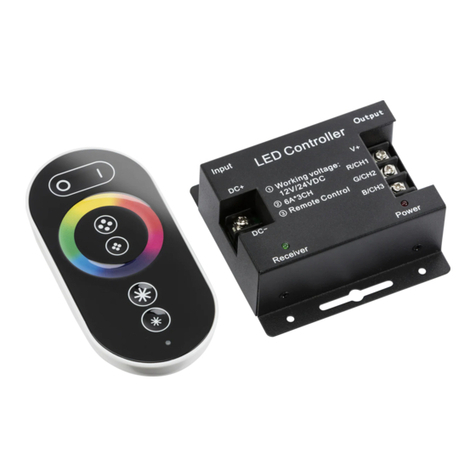
Knightsbridge
Knightsbridge LEDFRA9 Installation & maintenance manual
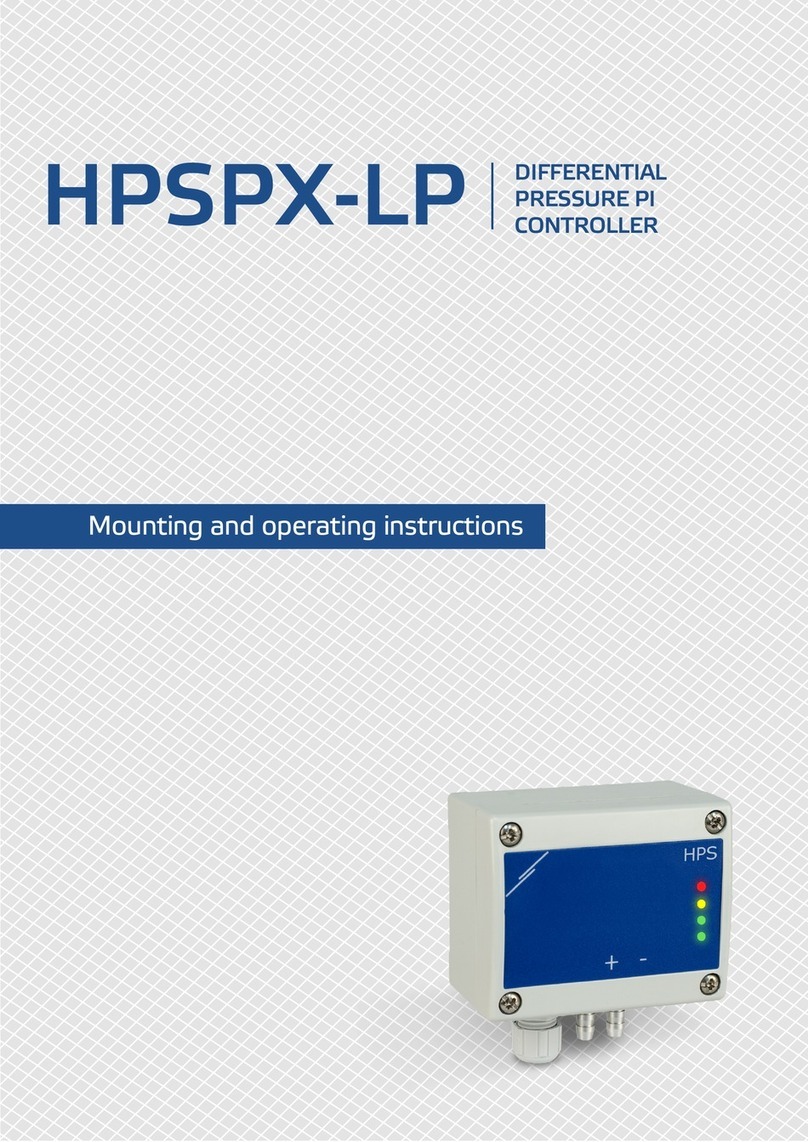
Sentera Controls
Sentera Controls HPSPX-LP Mounting and operating instructions
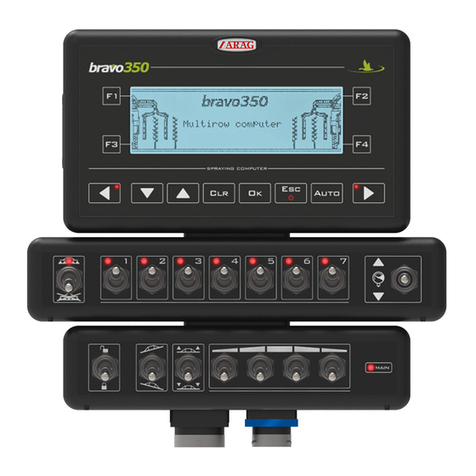
ARAG
ARAG Bravo 3 Series ADDITION TO INSTRUCTION BOOKLET