MaxJax M6K User manual

1
MaxJax™
5240 Willis Road
Theodore, AL 36582
844-629-5291
PLEASE READ THE ENTIRE CONTENTS OF THIS MANUAL PRIOR TO INSTALLATION AND OPERATION.BY PROCEEDING WITH LIFT
INSTALLATION AND OPERATION YOU AGREE THAT YOU FULLY UNDERSTAND AND COMPREHEND THE FULL CONTENTS OF THIS
MANUAL. FORWARD THIS MANUAL TO ALL OPERATORS. FAILURE TO OPERATE THIS EQUIPMENT AS DIRECTED MAY CAUSE
INJURY OR DEATH.
August 2020
P/N# 5900228
M6K USER MANUAL
Reference ANSI/ALI ALIOM safety
requirments for installation and service of
automotive lifts before installing lift.
MODEL: M6K
PORTABLE MID-RISE LIFT
6,000 POUND CAPACITY
Patent No. US 8.256.577 B2
Patent No. US 9.150.395.B2

2
IMPORTANT NOTICE
1. Read this manual thoroughly before installing, operating, or maintaining this lift.
2. This lift is designed for indoor use only, and should not be installed in a pit or depression.
3. The oor on which the lift is to be installed must be 4"(101mm) minimum thickness concrete, with a minimum
compressive strength of 3000 psi (20 MPa) and reinforced with steel bar.
4. The lifts have specic electrical requirements as described in the Installation Instructions section of this manual.
5. This lift has a minimum ceiling height requirement as described in the Installation Instructions section of this manual.
6. Failure by the owner to provide the recommended shelter, mounting surface, electrical supply, and ceiling height could
result in unsatisfactory lift performance, property damage, or personal injury.
7. Do not attempt to install this lift if you have never been trained on basic automotive lift installation procedures. Reference
ANSI/ALI ALIOM requirements for installation and service of automotive lifts.
8. Never attempt to lift components without proper lifting tools such as forklift or cranes. Stay clear of any moving parts
that can fall and cause injury. These instructions must be followed to insure proper installation and operation of your lift.
9. Dannmar Equipment will assume no liability for loss or damage of any kind, expressed or implied resulting from improper
installation or use of this product.
10. This lift is rated to 6,000-lbs lifting capacity. NEVER EXCEED rated lifting capacity of lift.
11. Qualied person must be consulted for seismic loads and other local or state requirements.
DEFINITIONS OF HAZARD LEVELS
Identify the hazard levels used in this manual with the following denitions and signal words.
Hazards or unsafe practices which could result in severe personal injury or death.
Hazards or unsafe practices which may result in minor personal injury, product or property damage.
Hazards or unsafe practices which may result in minor personal injury, product or property damage.
Lubricate all plastic guide blocks, bearings, and shafts with grease prior to operating the lift. Lubricate all on a weekly basis.
Motors and all electrical components are not sealed against the weather and moisture. Install this lift in a protected indoor
location. Failure by the owner to provide the recommended shelter could result in unsatisfactory lift performance, property
damage, personal injury, and may void the warranty.
BE SAFE: YOUR NEW LIFT WAS DESIGNED AND BUILT WITH SAFETY IN MIND. HOWEVER, YOUR OVERALL
SAFETYCANBEINCREASEDWITHPROPERTRAININGANDTHOUGHTFULOPERATIONONTHEPARTOFTHE
OPERATOR. DO NOT OPERATE OR REPAIR THIS EQUIPMENT WITHOUT READING THIS MANUALAND THE
IMPORTANTSAFETYINSTRUCTIONSSHOWNINSIDE.KEEPTHISOPERATIONMANUALNEARTHELIFTATALL
TIMES. MAKE SURE THAT ALL USERS READ AND UNDERSTAND THIS MANUAL.

3
IMPORTANT SAFETY INSTRUCTIONS
READ THESE SAFETY INSTRUCTIONS ENTIRELY
Do not attempt to install this lift if you have never been trained on basic automotive lift installation procedures. Never
attempt to lift components without proper lifting tools such as a forklift or crane. Stay clear of any moving parts that can fall
and cause injury.
1. READ ALL INSTRUCTIONS.
2. READ AND UNDERSTAND all safety warning procedures before operating lift.
3. KEEP AREA WELL LIGHTED.
4. WARNING! RISK OF EXPLOSION. This equipment has internal arcing or sparking parts which should not be exposed
to ammable vapors. This machine should not be located in a recessed area or below oor level.
5. KEEP CONTROL HANDLES AND / OR BUTTONS dry, clean and free from grease and oil.
6. CARE MUST BE TAKEN as burns can occur from touching hot parts on the hydraulic unit’s electric motor.
7. DO NOT operate equipment with a damaged power cord or if the equipment has been dropped or damaged until it has
been examined by a qualied service person.
8. DO NOT let the power cord come in contact with hot manifolds or moving fan blades.
9. IF AN EXTENSION CORD IS NECESSARY, a cord with a current rating equal to or more than that of the equipment
should be used. Cords rated for less current than the equipment may overheat. Care should be taken to arrange the
cord so that it will not be tripped over or pulled.
10. ALWAYS UNPLUG EQUIPMENT FROM ELECTRICAL OUTLET WHEN NOT IN USE. Never use the power cord to
pull the power plug from the outlet. Grasp the plug and pull to disconnect.
11. LET EQUIPMENT COOL COMPLETELY BEFORE PUTTING AWAY. Loop power cord loosely around equipment
when storing.
12. TO REDUCE THE RISK OF FIRE, do not operate equipment in the vicinity of open containers of ammable liquids
(i.e., gasoline).
13. ADEQUATE VENTILATION SHOULD BE PROVIDED when working on operating internal combustion engines.
14. KEEP HAIR, LOOSE CLOTHING, FINGERS, AND ALL PARTS OF THE BODY AWAY FROM MOVING PARTS.
15. TO REDUCE THE RISK OF ELECTRIC SHOCK, do not use on wet surfaces or expose to rain.
16. USE ONLY AS DESCRIBED IN THIS MANUAL. Use only manufacturer’s recommended attachments.
17. DO NOT raise vehicle on the lift until installation is completed as instructed in this manual.
18. KEEP HANDS AND FEET CLEAR. Remove hands and feet from any moving parts. Keep feet clear of lift when
lowering. Avoid pinch points.
19. KEEP WORK AREA CLEAN. Cluttered work areas invite injuries.
20. CONSIDER WORK AREA ENVIRONMENT. Do not expose equipment to rain. DO NOT use in damp or wet locations.
Keep area well lighted.

4
21. ONLY TRAINED OPERATORS should operate this lift. All non trained personnel should be kept away from work
area. Never let non trained personnel come in contact with, or operate lift.
22. USE LIFT CORRECTLY. Use lift in the proper manner. Never use lifting adapters other than what is approved by the
manufacturer.
23. DO NOT override self closing lift controls.
24. REMAIN CLEAR of lift when raising or lowering vehicle.
25. CLEAR AREA if vehicle is in danger of falling.
26. ALWAYS ENSURE that the safety locks are engaged before any attempt is made to work on or near vehicle.
27. DRESS PROPERLY. Non skid steel toe footwear is recommended when operating lift.
28. GUARD AGAINST ELECTRIC SHOCK. This lift must be grounded while in use to protect the operator from electric
shock. Never connect the green power cord wire to a live terminal. This is for ground only.
29. DANGER! The power unit used on this lift contains high voltage. Disconnect power at the receptacle before
performing any electrical repairs. Secure plug so that it cannot be accidentally plugged in during service.
30. ALWAYS WEAR SAFETY GLASSES. Everyday eyeglasses only have impact resistant lenses. They are not safey
glasses.
31. MAINTAIN WITH CARE. Keep lift clean for better and safe performance. Follow manual for proper lubrication and
maintenance instructions. Keep control handles and / or buttons dry, clean and free from grease and oil.
32. STAY ALERT. Watch what you are doing. Use common sense. Be aware!
33. CHECK FOR DAMAGED PARTS. Check for alignment of moving parts, breakage of parts or any condition that may
aect its operation. Do not use lift if any component is broken or damaged.
34. NEVER remove safety related components from the lift. Do not use lift if safety related components are damaged or
missing.
NOTE: If attachments, accessories, or conguration modifying components that are located in the load path, aect
operation of the lift, aect the lift electrical listing or aect intended vehicle accommodation are used on this lift
and, if they are not certied for use on this lift, then the certication of this lift shall become null and void. Contact
Dannmar Equipment for information pertaining to certied attachments, accessories, or conguration modifying
components.
SHIPPING DAMAGE CLAIMS:WHEN THIS EQUIPMENT IS SHIPPED,TITLE PASSES TOTHE PURCHASER UPON RECEIPT FROMTHE CARRIER.
CONSEQUENTLY, CLAIMS FOR THE MATERIAL DAMAGED IN SHIPMENT MUSTBE MADE BY THE PURCHASERAGAINSTTHE TRANSPORTATION
COMPANY AT THE TIME SHIPMENT IS RECEIVED.
When removing the lift from the shipping angles pay close attention as the posts can slide and can cause injury. Prior to
removing the bolts make sure the posts are held securely by a fork lift or some other heavy lifting device.

5
SAVE THESE INSTRUCTIONS
OWNER / EMPLOYER RESPONSIBILITIES
• Shall ensure that lift operators are qualied and that they are trained in the safe use and operation of the lift using the
manufacturer’s operating instructions and regional requirements.
• Shall establish procedures to periodically inspect the lift in accordance with the lift manufacturer’s instructions and
regional requirements. The Employer Shall ensure that lift inspectors are qualied and that they are adequately
trained in the inspection of the lift.
• Shall establish procedures to periodically maintain the lift in accordance with the lift manufacturer’s instructions and
regional requirements, Inspection and Maintenance and The Employer Shall ensure that lift maintenance personnel
are qualied and that they are adequately trained in the maintenance of the lift.
• Shall maintain the periodic inspection and maintenance records recommended by the manufacturer and regional
requirements.
• Shall display the lift manufacturer’s operating instructions; ALI/SM 93-1, ALI Lifting it Right safety manual; ALI/ST-10
ALI Safety Tips card; in a conspicuous location in the lift area convenient to the operator.
• Shall not modify the lift in any manner without the prior written consent of the manufacturer or regional requirements.
• Shall provide necessary lockout/ tagout means for energy sources per ANSI Z244.1-1982 (R1993), safety require-
ments for the lockout / tagout of energy sources, before beginning any lift repairs.
INSTALLER /OPERATOR: PLEASE READ THE ENTIRE CONTENTS OF THIS MANUAL PRIOR TO INSTALLATION
AND OPERATION. BY PROCEEDING WITH LIFT INSTALLATION AND OPERATION YOU AGREE THAT YOU FULLY
UNDERSTAND AND COMPREHEND THE FULL CONTENTS OF THIS MANUAL. FORWARD THIS MANUAL TO ALL
OPERATORS. FAILURE TO OPERATE THIS EQUIPMENT AS DIRECTED MAY CAUSE INJURY OR DEATH.
• I have visually inspected the site where the lift is to be installed and veried the concrete to be in good condition and
free of cracks or other defects. I understand that installing a lift on cracked or defective concrete could cause lift failure
resulting in personal injury or death.
• I understand that a level oor is required for proper installation and level lifting.
• I understand that I am responsible if my oor is of questionable slope and that I will be responsible for all charges
related to pouring a new level concrete slab if required and any charges.
• I understand that Dannmar lifts are supplied with concrete fasteners meeting the criteria of the American National
Standard “Automotive Lifts Safety Requirements for Construction, Testing, and Validation” ANSI/ALI ALCTV-2008, and
that I will be responsible for all charges related to any special regional structural and/or seismic anchoring require-
ments specied by any other agencies and / or codes such as the Uniform Building Code (UBC) and / or International
Building Code (IBC).
• I will assume full responsibility for the concrete oor and condition thereof, now or later, where the above equipment
model(s) are to be installed. Failure to follow danger, warning, and caution instructions may lead to serious personal
injury or death to operator or bystander or damage to property.
• I understand that Dannmar lifts are designed to be installed in indoor locations only. Failure to follow installation in-
structions may lead to serious personal injury or death to operator or bystander or damage to property or lift.

6
Failure to follow danger, warning, and caution instructions may lead to serious personal injury or death to operator or
bystander or damage to property.
Please read entire manual prior to installation. Do not operate this machine until you read and understand all the dangers,
warnings and cautions in this manual. For additional copies or further information, contact:
MaxJax™
5240 Willis Road
Theodore, AL 36582
844-629-5291
INSTALLER / OPERATOR
PROTECTIVE EQUIPMENT
Personal protective equipment helps makes installation and operation safer, however, it does not take the place of safe
operating practices. Always wear durable work clothing during any installation and/or service activity. Shop aprons or shop
coats may also be worn, however loose fitting clothing should be avoided. Tight fitting leather gloves are recommended
to protect technician hands when handling parts. Sturdy leather work shoes with steel toes and oil resistant soles should
be used by all service personnel to help prevent injury during typical installation and operation activities.
Eye protection is essential during installation and operation activities. Safety glasses with side shields, goggles, or face
shields are acceptable. Back belts provide support during lifting activities and are also helpful in providing worker protec-
tion. Consideration should also be given to the use of hearing protection if service activity is performed in an enclosed
area or if noise levels are high.

7
M6K PRODUCTION
ITEM No. PART NUMBER DESCRIPTION QTY
1 5215935 M6K POST ASSEMBLY 2
2 5215936 MAXJAX POWER UNIT STAND ASSEMBLY 1
3 5250293 PARTS BOX 1
4 5215938 MAXJAX ARM ASSEMBLY 4
5 5906033 MAXJAX BRANDING LABEL 4
6 5906034 MAXJAX SAFETY LABEL 1
7 5906035 MAXJAX SAFETY LOCKS WARNING LABEL 2
8 5906005 MAX CAPACITY NTRL 6K LABEL, ENLISH-FRENCH 1
9 5906036 SERIAL TAG F, MAXJAX 1
10 5905377 NOTICE LABEL, ALI/WLSIA01 1
11 5905109 WARNING ALI/WL 101 1
12 5905654 LABEL; ALI/ALCTV-2017 GOLD LABEL, CAN-US; MET LABS 1
MAXJAX POWER UNIT STAND ASSEMBLY
ITEM No. PART NUMBER DESCRIPTION QTY
1 5601535 MAXJAX BOTTOM PLATE WELDMENT, STAND 1
2 5601474 M6K HOSE STORAGE BOX WELDMENT 1
3 5755171 MAXJAX STAND HANDLE 2
4 5737162 MAXJAX STAND SUPPORT PLATE 1
5 5215970 MAXJAX HAND CART WHEEL ASSEMBLY 2
6 5715041 MAXJAX Ø25 VINYL GRIP 2
7 5716056 MAXJAX VINYL CAP, Ø22 I.D 2
8 5540113 E RING Ø1/2” OD TRAURC 5133-50 2
9 5545141 WASHER M12 X 24 FLAT CL 10.9 4
10 5530378 PHPS M6 X 1.0. X 40 MM 12
11 5535357 NUT M6 X 1.0 NL 12

8
MAXJAX PARTS BAG
ITEM No. PART NUMBER DESCRIPTION QTY
1 5505071 M6K SAFETY PIN ASSEMBLY 4
2 5746491 MAXJAX LIFT HEAD RELEASE PIN 4
3 5505001 SAFETY CLEVIS PIN 2
4 5530738 HHB M10 X 1.5 X 25 4
5 5545200 WASHER M10 X Ø18 SL 4
6 5530377 HHB M8 X 1.25 X 55 4
7 5550077 FTG -06 NPTF X -06 NPTF, HEX NIPPLE 2
8 5550076 FTG 45° ELB -06 NPTF X -06 NPTF 2
9 5535001 NUT M8 X 1.25 ML 12
10 5550014 FTG NPL -06 NPT F X 3/8 QUICK CONNECTOR COUPLER MALE; NON SPILL
DESIGN
2
11 5550209 FTG -04 NPTF X -06 NPTF, STRAIGHT EXPANDER 2
12 5505350 MODEL #211 HAIR PIN/LARGE 2
13 5540075 R.H. 2.5 WIRE DIA. , Ø20.5 X 75 LG 4
14 5545535 C WASHER SHIM FOR LIFTS 21
15 5530261 PHPS M6 X 1 X 10 4
16 5530304 HHB M8 X 1.25 X 20 8
17 5550074 FTG 90° ELB 3/8” JIC MALE X 3/8” ORB MALE, LONG 1
18 5550170 FTG 90° ELB 3/8” JIC MALE X 3/8” NPTF MALE, LONG 1
MAXJAX PARTS BOX
ITEM No. PART NUMBER DESCRIPTION QTY
1 5174046 PARTS BAG 1
2 5715003 POWER UNIT VIBRATION DAMPENER 1
3 5601488 M6K LIFT HEAD PIN WELDMENT 4
4 5575061 M6K POST WHEEL 4
5 5601487 M6K POST STRAP ASSEMBLY 2
6 5736604 TWO POST LIGHT DUTY BOLT ON ARM RESTRAINT GEAR 4
7 5210236 MAXJAX SAFETY WELDMENT 2
8 5716057 MAXJAX SAFETY COVER 2
9 5570241 HYDRAULIC HOSE ASS. Ø10 X 4520 MM 2
10 5570242 HYDRAULIC HOSE ASS Ø10 X 317 MM DS 1
11 5590103 HYDRAULIC FLOW DIVIDER; MTE 1
12 5746390 MEDIUM LIFT PAD EXTENSION Ø35 X 113 MM 4
13 5215507 ROUND LIFT PAD ADAPTER ASSEMBLY 4
14 5530376 7/8” x 3-13/16” DROP IN SLEEVE ANCHOR 10
14 5580012 LIQUID PTFE THREAD SEALANT 50 ML 1

9
MAXJAX PARTS BAG
MAXJAX PARTS BOX

10
INSTALLATION INSTRUCTIONS
TOOLS REQUIRED
IMPORTANT NOTICE
These instructions must be followed to ensure proper installation and operation of your lift. Failure to comply with these
instructions can result in serious bodily harm and void product warranty. Manufacturer will assume no liability for loss or
damage of any kind, expressed or implied resulting from improper installation or use of this product.
STEP 1
SELECTING SITE
BEFORE INSTALLING YOUR NEW LIFT, CHECK THE FOLLOWING:
1. LIFT LOCATION: Always use architects plans when available. Check layout dimension against oor plan
requirements making sure that adequate space is available.
2. OVERHEAD OBSTRUCTIONS: The area where the lift will be located should be free of overhead obstructions such
as heaters, building supports, electrical lines etc.
3. DEFECTIVE FLOOR: Visually inspect the site where the lift is to be installed and check for cracked or defective
concrete.
4. OPERATING TEMPERATURE. Operate lift only between temperatures of 41° - 104° F (5º - 40 º C).
5. Lift is designed for INDOOR INSTALLATION ONLY.
STEP 2
FLOOR REQUIREMENTS
This lift must be installed on a solid level concrete oor minimum 4"(101mm) thick, compressive strength 3000 psi
(20 MPa) with no more than 3 degrees of slope. FAILURE TO DO SO COULD CAUSE PERSONAL INJURY OR
DEATH.
DO NOT install this lift on any asphalt surface or any surface other than concrete.
DO NOT install this lift on expansion seams or on cracked or defective concrete.
DO NOT install this lift on a second / elevated oor without rst consulting building architect.
DO NOT install this lift outdoors.
• Rotary Hammer Drill or Similar
• 7/8"(22mm) Masonry Bit
• Hammer
• 4 Foot Level (1.5 M)
• Open End Wrench Set: Metric
• Socket and Ratchet Set: Metric
• Hex Key / Metric Allen Wrench Set
• Large Crescent Wrench
• Large Phillips Screwdriver
• Chalk Line
• Medium Phillips Screwdriver
• Tape Measure: 25 Foot (7.5 M) Minimum

11
Remove the 6mm allen bolt and install the
Cylinder Fittings. Asssemble all ttings
together, including quick disconnect,
preferably in a vice. Install tting assembly
into cylinder.
(See gure 2)
STEP 3
INSTALLING HYDRAULIC CYLINDERS
Fig. 1
Fig. 4
Install the column wheels (P/N 5575061) using M8x55 hex head bolts (P/N 5530377) and M8 nylon lock nut
(P/N 5535001) onto each column. Turn the columns over and lay them down with the open side up. Slide the lift head
to the top of the post. Remove the cylinder from the post. (See gure 1)
Slide the tting assembly through the
access hole located on the backside of the
columns. (See gure 3)
Slide the Lift Head until it rests rmly on the Baseplate. Stand the column up.
1.
2.
4.
3.
Fig. 2
Install the Column Handles (P/N 5505071) with M10 x 25 Hex Head Bolts (P/N 5530738) with M10 Washers
(P/N 5545200) and Post Straps Assemblies (P/N 5601487 ) with M10 x 40mm hex bolts and M10 nylon lock nuts.
(See gure 5)
6.
Slide the cylinders through the lift head tube. (See gure 4)
P/N 5505071
4
P/N 5530738
4
P/N 5535013
4
P/N 5530302
4
P/N 5550209
1
P/N 5550076
1
P/N 5550077
1
P/N 5550014
1
Cylinder
Lift Head
5.
Fig. 5
Fig. 3Fig. 3
Fitting Assembly

12
NOTE:
*(Flow Divider)
Pay close attention to
which side the bolts
are on. When facing
the ow divider, the
bolt heads should be
on the left side.
The lift will not work
properly if the ow
divider is installed
upside down.
Assemble cart as shown in the gures below:
1. After installing the cart wheels, attach the
power unit and rubber Power Unit Dampener
pad to the power unit cart using the (4)
M8x20 mm Hex Bolts and Nylon lock nuts.
(See gure 6)
2. Attach the Hydraulic Flow ivider to the power
unit cart using the (4) M8x 20 mm hex bolts
and nylon lock nuts supplied. (See gure 7)
NOTE:
Install ow divider so that when facing it from
the front, the (2) plastic plugs are on the left
and the (1) plastic plug is on the right.*
3. Remove the plastic plug from the
lower left port stamped "IN" on the
ow divider. Install the long 90° Elbow
Fitting (P/N 5550170). When tightening
the Fitting, tighten by hand rst and
then using a wrench turn approx.
3 turns past tight. (See gure 8)
4. Remove the plastic plug from the
power unit and attach the Long 90°
Elbow Fitting (P/N 5550074).
5 Attach the short power unit hose as
shown. DO NOT use teon tape on the
JIC ttings. (See gure 9)

13
STEP 5
SITE LAYOUT
1. Determine the location of where the lift will be installed based on the size of vehicles servicing. The dimensions shown below
are rough guidelines. "Dry-t" the vehicles intended to be serviced in the bay by referring to the ALI Lifting Point Guide for
appropriate lift points before nalizing the column spacing.
2. Once a location is determined, use a carpenters chalk line to layout a grid for the post locations. Keep all dimensions and
squareness within 1/8"or malfunctioning of the lift can occur.
3. After the post locations are properly marked, use a chalk or crayon to make an outline of the columns on the oor at each
location using the post base plates as a template.
4. Double check all dimensions and make sure that the layout is perfectly square.
NOTE:
Wide or narrow installation is possible. The lift can be installed at a width that suits the vehicles you will be raising.
You may even choose to install additional anchors at varied column positions for adaptability to multiple vehicle congurations.
5. Recommended bay dimensions 20'deep and 14' wide.
6. Clearance around lift should be 5”. Clearance above lift must exceed height of top of raised vehicle.
Sport compacts
105"(2667mm) - 115"(2921mm) Typical
Mid size
110"(2794mm) - 120"(3048mm) Typical
Light duty / sport trucks
115"(2921mm) - 120"(3048mm) Typical
Full size trucks
120"(3048mm) - 135"(3429mm) Typical
Use the edge of the base plate to line up the posts along the chalk line.
Chalk line

14
STEP 6
INSTALLATION OF POWER DROP ANCHORS
D
BAC
E
1. Before proceeding, double check location and measurements, make
certain that the base plates of each column are aligned with the chalk/
crayon lines. The concrete must be minimum of 4" (101mm) thick with a
minimum compressive strength of 3000 psi (20 MPa). FOLLOW
PROCEEDURE EXACTLY FOR PROPER FITTING AND ALIGNMENT
OF ANCHORS. (See gure 10)
2. Use the squared-up base plate on the column as a guide. Using a
rotary hammer drill with a 7/8" concrete bit, drill out each hole in the
column to the minimum depth of 5". Do not ream the hole or allow the
drill to wobble. When removing the bit be careful not to move the
columns. Having someone secure or stand on the columns can be helpful.
Repeat for all holes on both columns and move the columns out of the way.
After drilling, thoroughly clean hole using a vacuum cleaner or compressed
air and a nylon brush. (See gure 11)
3. Set the anchor embedment depth: Fully thread the 5/8"
Setting Tool (sacricial hex bolt) with assembled nut and
washer into the anchor. Set the distance between the top of
the anchor and the bottom of the nut/washer to 5/8".
(See gure 12)
4. After setting the nut/spacer, place the anchor into the hole
and hammer downward on the setting tool until the nut and
washer makes contact with the surface of the concrete.
(See gure 13)
5. To set the anchor tighten the nut while holding the bolt
head (to assure the anchor does not spin in place) Do not
use an impact wrench for this step. Tighten 3 full turns to
reach an installation torque of 90 ft-lbs.
(See gure 14)
NOTE: Always wear safety glasses.
Follow drill manufacturer’s instructions.
Use only solid carbide-tipped drill bits
meeting ANSI B212.15 diameter
standards.
Fig. 11
Fig. 12 Fig. 13 Fig. 14
Fig. 10
Set Tool
Hex Bolt
Spacer
5/8”
(16mm)
—
—
▶
—
Drill hole
a minimum of
5" (127mm) deep.
—
—
▶
▶
—
▶
▶
▶
Anchor ▶
—
6. Once the anchor is set remove the cap screw and clear the
anchor with compressed air to remove any concrete dust from
the threads.

15
Before operating your lift, check to make sure both “A” and “B” measurements are equal. The lift arms must be level
before operation. If your lift arms are not level, shim the columns as required.
IMPORTANT LEVELING INSTRUCTIONS
7. Install both columns with bolts and washers to anchors, check plumb and measurements as shown below.
8. If shimming is required, insert the shims as necessary under the
base plate so that when the provided 5/8 x 2"anchor bolts are
tightened, the columns will be plumb both side to side and front to
rear. (See gure 15)
9. With the shims and anchor bolts in place, tighten all 5/8 x 2"anchor
bolts tight to the base plate. DO NOT USE AN IMPACT WRENCH or
the anchors could become compromised.
NOTE:
It will be helpful to mark on or otherwise note the location of shims
used at each drop anchor to assist at time of re-installation.
Inspect all drop-in anchors for proper setting and or damage each time the lift is re-installed. Inspect the concrete for
cracks defects and/or damage. Do not re-install the lift if any of the drop-in anchors are defective or the concrete is
cracked or defective.
It may be necessary to shim the columns to ensure that the columns are plumb. The columns must be plumb and
square or damage or injury may occur when using the lift. Do not exceed 1/8" total shim thickness.
Fig. 15

16
STEP 8
HYDRAULIC POWER UNIT SET UP
STEP 7
CONNECTING HYDRAULIC LINES
Female Quick
Disconnect
Fitting
Install the Female Quick Disconnect ttings to the opposite end of
each hose. (See gure 17)
Recheck all tting connections to make sure they are properly
tightened before proceeding.
Position the power unit stand at the front or rear of the vehicle.
Connect the Female Quck Disconnect tting to the Male Quick
Disconnect located at the bottom of each column. (See gure 18)
Fig. 16 3/8 NPTF Hose
Fittings
Fig. 18
1. Fill the power unit reservoir with 7 quarts (6.6 L) of AW-32 hydraulic oil or Dexron III or VI automatic transmission
uid. Make sure the funnel used to ll the power unit is clean. After bleeding the cylinders, check the oil level to see if
additional oil is needed to ensure the reservoir is full.
2. The lift should be plugged into a dedicated circuit with a 20 amp circuit breaker. The standard power unit for this lift
is:
US: 110V, 60Hz, single phase
CE: 230V, 50Hz, single phase
ALL WIRING MUST BE PERFORMED BY A CERTIFIED ELECTRICIAN ONLY.
RISK OF EXPLOSION
This equipment has internal arcing or parts that may spark and should not be exposed to ammable vapors. The motor
should not be located in a recessed area or below oor level.
• DO NOT run power unit without oil. Damage to pump can occur.
• The power unit must be kept dry. Damage to power unit caused by water or other liquids such as detergents, acid
etc., is not covered under warranty.
• Improper electrical hookup can damage the motor and will not be covered under warranty.
• Motor can not run on 50hz without a physical change in the motor. (US - only)
• Use a separate breaker for each power unit.
• Protect each circuit with a time delay fuse or circuit breaker. (US-only)
1. Thread one end of the 3/8 NPT hose ttings into one of the top ports of the Flow Divider. Do this with both hoses.
(See gure 16)
Fig. 17

17
STEP 9
INSTALLING THE LIFT ARMS
Fig. 20 Quick Release Pin
1. Place the lift arm assembly on the lift heads. Install the lift head pins into the lift head and through
the holes in the arm assembly. Install the quick release pin into place on the arm pin. (See gure 20 and 21)
Fig. 21
2. Loosen the arm restraint gear ring bolts and adjust the arm restraint gears so that the teeth on the gear ring mesh
smoothly with the teeth on the gears of the arm gear stop. (See gure 22)
1. Raise the lift high enough so that the arm gear stops. Attempt to automatically engage the restraint gears on the
arms.
3. Tighten the gear ring bolts
4. Verify the operation of the arm gear stops by pulling up on the
key ring of the arm gear stops. Pivot the arms back and forth
and test the operation of the arm gear stops in various positions.
When releasing the arm gear stop, the pin should drop and the
gears should engage. (See gure 23)
6. Adjust the gear ring on the arm as necessary to ensure smooth
operation and solid engagement of all four arm restraint pins.
Each arm restraint assembly must be inspected and adjusted
as needed before each and every time the lift is operated. Do
not operate the lift if any of the four arm restraint systems are
not functioning properly. Replace any broken components or
components with broken teeth only with authorized or approved
replacement parts.
5. Ensure that the arms do not move when a force of at least
100 pounds is applied laterally to the fully extended arms. If
they move, readjust the arm restraint gear ring and/or tighten
the arm restraint gear ring bolts.
Fig. 22
Arm Restraint Gear
Fig. 23

18
STEP 12
LIFT START UP / FINAL ADJUSTMENTS
DURING THE START-UP PROCEDURE, OBSERVE ALL OPERATING COMPONENTS AND CHECK FOR PROPER
INSTALLATION AND ADJUSTMENT. DO NOT ATTEMPT TO RAISE VEHICLE UNTIL A THOROUGH OPERATIONAL
CHECK HAS BEEN COMPLETED.
1. Apply white lithium grease or equivalent to the inside of the columns where the slide blocks glide.
2. Test the power unit by pressing the push-button switch. Raise the lift a few inches and check all hose connections for
leaks. If the motor gets hot or sounds peculiar, stop and check all electrical connections.
3. Raise the lift to it’s maximum height o the oor until the lift head stops.
4. Lower the lift down below the rst safety stop.
1. With the lift in an elevated position, the hoses connected and the oil reservoir full, loosen the bleeder screws
located at the top of each hydraulic cylinder using an allen wrench. Do not completely remove the bleeder screws.
Watch and listen for trapped air escape the cylinders and uid begins to weep from the screw area. Once steady
uid appears, re-tighten the bleeder screw and cleanup excess oil.
(See gure 19)
STEP 11
BLEEDING THE CYLINDERS
Bleed Screw
Fig. 19
The lift will move down when bleeding, make sure all equipment, personnel,
hands and feet are clear before starting bleeding procedure.
2. Repeat Bleeding proceedure on opposite cylinder.
3. Press the lowering handle on the power unit until the lift lowers
completely to the oor.
DO NOT use lift if an unlevel lifting condition occurs at the arm pad locations that is greater than 3.5"(89mm). If an
unbalanced condition occurs, follow the bleeding instructions shown on this page or consult Technical Support. The lift
must be re-leveled, shimmed and bled each time the lift is reinstalled. Failure to follow these instructions can result in
serious injury or death.
STEP 10
INSTALLING THE SAFETY RELEASE LATCH
SEE PAGE 30

19
LIFT OPERATION SAFETY
• NEVER exceed rated capacity of 6,000-lbs.
• Tighten all anchor bolts prior to operation. If anchor
bolts are loose, or any component of the lift is
defective, do not use lift.
• DO NOT remove or disable arm restraints.
• DO NOT block, open or override self-closing lift
controls; they are designed to return to the “O” or
Neutral position when released.
• ALWAYS inspect all quick connect/disconnect hose
ends before any attempt is made to raise vehicle.
• ALWAYS be sure to have proper overhead
clearance.
• ALWAYS load vehicle on lift carefully. Position
the contact pads according to the vehicle
manufacturer’s recommended lift points. Raise lift
until lift pads contact vehicle. Check pads for secure
contact with the vehicle.
NOTE:
Refer to ALI Quick Reference Guide for all point
recommendations, dangers and safety data.
• ALWAYS remain clear of lift when raising or
lowering vehicles.
• Do NOT use lift if an unlevel lifting condition occurs
that is greater 3.5"(89 mm).
• DO NOT rock the vehicle or remove heavy
components while on the lift that may alter weight
distribution
• ALWAYS ensure Safety Locks are engaged before
any attempt is made to work on or near vehicle.
• NEVER go under raised vehicle if Safety Locks are
not engaged.
WHEN LOWERING THE LIFT PAY CAREFUL
ATTENTION THAT ALL PERSONNEL AND OBJECTS
ARE KEPT CLEAR. ALWAYS KEEP A VISUAL LINE
OF SITE ON THE LIFT AT ALL TIMES. ALWAYS
MAKE SURE THAT ALL LOCKS ARE DISENGAGED.
IF ONE OF THE LOCKS INADVERTENTLY LOCKS
UPON DESCENT THE VEHICLE MAY DISMOUNT
CAUSING PERSONAL INJURY OR DEATH.
• ALWAYS remove tool trays, stands, etc. before
lowering lift.
• ALWAYS release safety locks before attempting to
lower lift.
• ALWAYS move the lift arms to provide an
unobstructed exit before removing vehicle from lift
area.
• NEVER drive over the lift arms.
VISUALLY CONFIRM THAT ALL SAFETY LOCKS
ARE ENGAGED BEFORE ENTERING WORK
AREA. SUSPENSION COMPONENTS USED ON
THIS LIFT ARE INTENDED TO RAISE AND LOWER
LIFT ONLY AND ARE NOT MEANT TO BE LOAD
HOLDING DEVICES. REMAIN CLEAR OF
ELEVATED LIFT UNLESS VISUAL CONFIRMATION
IS MADE THAT SAFETY LOCKS ARE FULLY
ENGAGED AND THE LIFT IS LOWERED ONTO
THE SAFETY LOCKS, REFER TO OPERATION
MANUAL FOR PROPER SAFETY LOCK
PROCEDURES AND/OR FURTHER INSTRUTIONS.
POST INSTALLATION CHECK OFF
Columns are properly leveled
Anchor bolts are tightened
Electric power supply conrmed
Check for hydraulic leaks
Check oil level
Lubrication of critical components
Check for overhead obstructions
Lift arms are level
Arm restraints properly adjusted
All screws, bolts, and pins are secured
Surrounding area is clear
Operation, maintenance and safety manuals on site

20
STEP 13
LIFT OPERATION
TO RAISE VEHICLE:
1. Center the vehicle between columns. Adjust vehicle front-to-back so the center
of gravity falls in the middle of the columns.
2. Position lift contact pads at manufacturers recommended lifting points.
3. Before raising vehicle, be sure all personnel are clear of the lift and surrounding
area. Pay careful attention to overhead clearances.
4. Raise lift by pressing raise button on power unit until contact pads make contact
with the underside of vehicle. *
5. Verifty vehicle is secure and arm restraint locks are engaged on all 4 arms.
6. After the vehicle is raised to the desired height, press the lowering handle until
the lift stops evenly on the safety locks. (See gure 25)
7. When raising the lift, always keep a visual line of site on the lift.
TO LOWER VEHICLE:
1. Before lowering vehicle, be sure all personnel are clear of the lift and sur-
rounding area. Insure all tools and equipment have been cleared from under
the lift.
2. Raise the lift o of the safety lock by pressing the raise button on the power
unit. Make sure you raise the lift by at least one inch from the lock to allow
adequate clearance.
3. Disengage the safety lock on each column by pulling up the release handle.
(See gure 26)
4. Push the lowering handle on the power unit until the lift has descended
completely and all 4 arm restraint gears are completely released.
5. When lowering the lift pay careful attention that all personnel and objects are
kept clear. Always keep a visual line of site on the lift at all times.
BE SURE TO READ ALL SAFETY TIPS PRIOR TO OPERATING LIFT. FAILURE TO DO SO MAY RESULT IN
SERIOUS INJURY OR DEATH.
WEEKLY MAINTENANCE
• Lubricate all moving parts with a white lithium grease.
• Check all connections, bolts and pins to insure proper mounting.
MONTHLY MAINTENANCE
• Make a visual inspection of all moving parts and check for excessive signs of wear.
• Check condition of lift pads and adapters.
• Check condition of arm restraints. Adjust as necessary.
• Inspect all bolts, pins and anchor bolts.
• Replace all faulty parts before lift is put back into operation.
*NOTE: Refer to ALI Reference Guide for all lift point recommendations and
safety data.
Other manuals for M6K
1
Table of contents
Other MaxJax Lifting System manuals
Popular Lifting System manuals by other brands
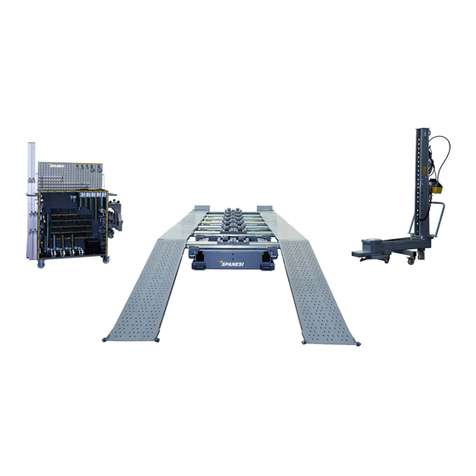
spanesi
spanesi 100 - H 100/6m Series Operation, service and parts manual
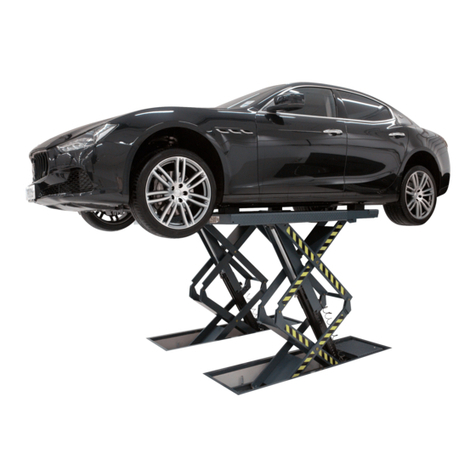
Ravaglioli
Ravaglioli RAV505 IF manual
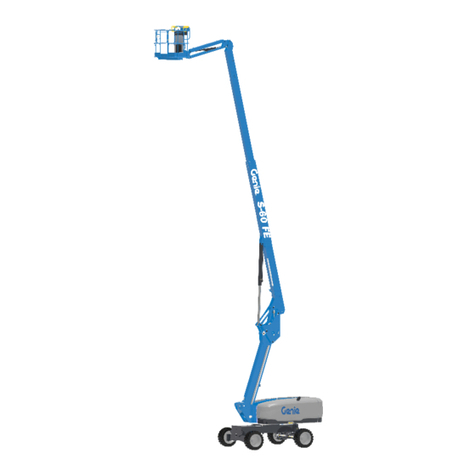
Terex
Terex Genie S-60 FE Service and repair manual

progressive automations
progressive automations flt-02 Assembly instructions

Stockman
Stockman HMS05/1000 user guide
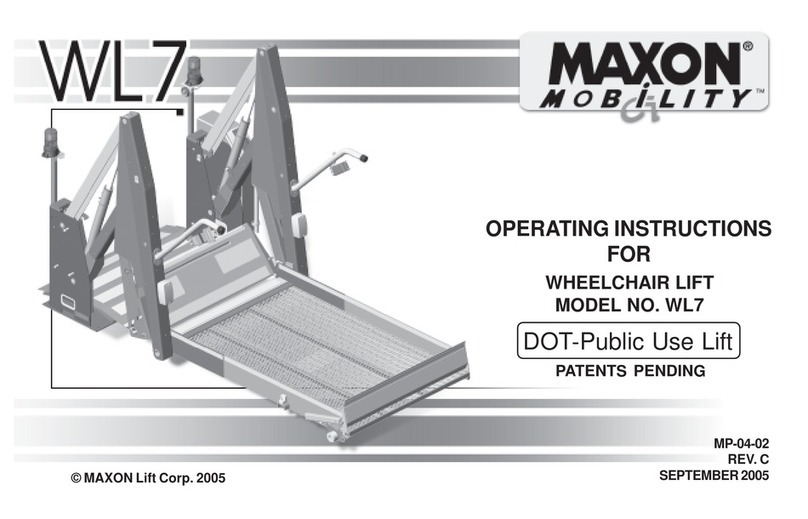
Maxon
Maxon WL7 operating instructions