MECOS IMC15 User manual

Magnetic Bearing and Motor
Controller
IMC15 BG10837-XXN
Operating Instructions Rev_E 02/2021

(c) 2021
MECOS AG
Hardstrasse 319
CH-8005 Zürich
SWITZERLAND
Tel. +41 52 355 52 11
Fax +41 52 355 52 24
mecos@mecos.com
www.mecos.com
Specifications are subject to change without notification.

Table of Contents
i
TABLE OF CONTENTS
1SYSTEM OVERVIEW ............................................... 1
2REMARKS ON SAFETY ............................................. 2
2.1 UL Markings ...............................................................2
3INTENDED USE .................................................... 4
4INSTALLATION ..................................................... 5
4.1 Overview ...................................................................5
4.2 Mounting ...................................................................6
4.3 Electrical Connectors ...................................................7
4.3.1 Introduction ................................................................7
4.3.2 Magnetic Bearing Connectors ........................................7
4.3.3 Motor Terminal Block ...................................................8
4.3.4 Line Terminal Block ......................................................9
4.3.5 Connectors of the Customer Specific Interfaces .............10
4.3.6 EMC Issues ...............................................................11
5OPERATION ....................................................... 13
5.1 Display and Keypad ...................................................13
5.2 Navigation using the Keypad ......................................16
5.3 Menus .....................................................................18
5.3.1 Menu Tree ................................................................18
5.3.2 Mode 1: Main Menu ....................................................19
5.3.3 Mode 2: AMB ............................................................21
5.3.4 Mode 3: Drive ...........................................................21
5.3.5 Mode 4: Current Faults (Fault and Warning Monitor) .......22
5.4 Fault and Warning Monitor .........................................23
5.4.1 Introduction ..............................................................23
5.4.2 Using the Fault and Warning Monitor ............................25
5.5 Fault History ............................................................27
5.5.1 Introduction ..............................................................27
5.5.2 Using the Fault History ...............................................28
5.6 Updating the Firmware .............................................30

5.6.1 Introduction ............................................................. 30
5.6.2 Flash Card and Handling ............................................ 30
5.6.3 Complete Update ...................................................... 32
5.6.4 Inifile Update ............................................................ 34
5.6.5 Display Update ......................................................... 36
6TROUBLESHOOTING ..............................................38
6.1 Fault Categories ........................................................38
6.2 Error Messages by Categories .....................................39
6.3 Troubleshooting Procedures ........................................40
7MAINTENANCE ....................................................53
8TECHNICAL DATA .................................................54
9DECLARATION OF CONFORMITY ................................57
10WARRANTY ........................................................58
11APPENDIX .........................................................59
12GLOSSARY ........................................................61

1 System Overview
1
1 SYSTEM OVERVIEW
The IMC15 (Integrated Magnetic Bearing and Motor Controller,
15 kW) integrates electronics (MBE) for operating a five axes
active magnetic bearing system (AMB) as well as a frequency
converter (FC) for driving permanent magnet synchronous
motors with power ratings of up to 15 kW.
The magnetic bearing electronics is a proven MECOS desgin
which, as a new feature, supports cables longer than 23
meters in which case a sensor amplifier, type SMX6B (Sensor
Matching Box), has to be mounted on the blower. The motor
drive features constant voltage DC bus, IGBT power stage,
output harmonics filter and vector control, thus providing
excellent dynamic performance. Output filter and dynamic
breaking resistor are integrated into the housing of the IMC15,
thus,no additional installation work is required.
The drive as well as the MBE are fed from the same DC bus
and are controlled by the same processor. This architecture
not only allows to control the entire system over one single
interface but also to safely shut down the system in case of a
mains failure by using the kinetic energy of the rotor fed back
into the DC bus (generator operation).
Acting as interfaces to the IMC15 are a display with a keypad,
a CAN bus interface and a digital interface (Dig I/O) that can
be configured to meet specific requirements. Display and key-
pad give the user or operator access to all basic functions
whereas the field bus together with the corresponding soft-
ware package allows to freely configure the entire system. The
Dig I/O interface is designed for use with a PLC and offers 8
digital channels that can be configured as either inputs or out-
puts. Additionally an insulated 24V supply is available on the
same connector.
A glossary explaining the most frequent acronyms and abbre-
viations used throughout this manual can be consulted in the
appendix.

IMC15
2
2 REMARKS ON SAFETY
During operation, the IMC15 and the electric drive system as a
whole may, according to its degree of protection, have moving
or rotating parts as well as hot surfaces. Electric drive systems
with frequency converters are therefore potentially hazardous.
In order to prevent injuries and damage to property only qua-
lified persons being familiar with MECOS AMB and electrical
drive systems may install and operate the IMC15.
Qualified persons are familiar with mounting, commissioning
and operation of MECOS AMB as well as MECOS frequency
converters and have received proper training corresponding to
their function. These persons have to read this manual and
pay attention to all safety remarks before commissioning of
the IMC15 starts.
The IMC15 is exclusively repaired by MECOS AG. Any unautho-
rized opening and modification of the device may lead to inju-
ries and damage to property.
2.1 UL Markings
57.1 Branch Circuit Short Circuit Protection
Suitable for use on a circuit capable of delivering not more
than 30kA rms symmetrical Amperes, 480 Vac. When protec-
ted by a circuit breaker having an interrupting rating not less
than 35 kA rms symmetrical Amperes, 480 Volts maximum.
Adapté pour utilisation sur un circuit ne pouvant pas fournir
plus de 30kA rms, 480 Vac, lorsque protégé par un disjoncteur
n'étant pas inférieur à 35kA rms, 480V maximum.
Das Gerät ist für den Einsatz in Stromkreisen bis 30kA rms,
480 Vac, wenn geschützt durch einen Motorschutzschalter
nicht kleiner als 35kA rms, 480V maximum.

2 Remarks on Safety
3
56.2 Overload, Over-Current, and Over-Speed Protec-
tion
The motor must have an integral thermal protection PTC
according to DIN 44082. The PTC must be connected to the
terminal block J2.
Max. Motor rating: 29.5Arms AC, 15kW.
Le moteur doit avoir une protection intégrée contre surtempé-
rature PTC selon DIN 44802. Le PTC doit être connecté au bloc
de jonction J2.
Puissance moteur max: 29.5Arms AC, 15kW.
Der Motor muss einen integrierten Übertemperaturschutz PTC
nach DIN 44082 haben. Der PTC muss an die Klemme J2
angeschlossen werden.
Max. Motor Leistung: 29.5Arms AC, 15kW.

IMC15
4
3 INTENDED USE
The IMC15 is intended for use in electrical plants or machines.
If used in machines, the commissioning of the IMC15 (start of
the intended use) has to be delayed until it has been verified
that the machine complies with the regulations of EU directive
98/37/EG (directive for machines). EN60204 has to be consi-
dered.
The technical data as well as the indications concerning instal-
lation have to be taken from the device label as well as from
this document. As a general rule, only motors and AMBs
approved by MECOS AG may be operated by an IMC15 having
the appropriate set of parameters.
The device has to be protected from any improper handling.
Please note that, during handling and transportation, no com-
ponents, hardware modules or parts of the housing are bent or
deformed such that insulating spacings may be altered.
Since electronic devices may fail, it is the user‘s responsability
(the customer‘s responsability in case of an OEM agreement)
that during a shutdown or a fault in the plant (machine) the
IMC15 is brought to a safe state.
The electrical installation has to be carried out according to
appropriate regulations, all information going beyond this
point have to be taken form this documentation.
Installation hint:
This equipment is intended for use in clean and dry environ-
ments in accordance to UL 61800-5-1, Pollution degree 2 and
Over Voltage Category III.

4 Installation
5
4 INSTALLATION
4.1 Overview
1. Display (LCD)
2. Keypad
3. Mounting rail for magnetic bearing cabling
4. Slot for flash memory card
5. Dowel pin for electrical shield connection
6. Terminal block for stator winding temperature monitoring by PTC
(cage clamp: AWG 26-14, 0.14-1.5 mm2)
7. Terminal block for motor and mains connections
(screw terminal block:AWG 18-6, 0.82-13.3 mm2)
8. Digital I/O interface
9. Connector for the sensors (cable lenghts up to 23 m)
10. Connector for the sensors using SMX6B for variable cable lengths
from 2 to 31 m as well as CAN bus
11. Connector for the bearing magnets

IMC15
6
4.2 Mounting
All installation work has to be carried out by qualified person-
nel.
Before installing the device check it thoroughly on transporta-
tion damage and mind the following points:
•Never install a device having transportation damages!
•Report any case of transportation damage immediately to
the manufacturer!
•Always send back the device using the original packaging!
For the installation please refer to the dimensions given in the
appendix. When placing the device in the plant (e.g. a cabinet)
please check, that air flow for cooling the device is not blocked
and that the climatic requirements are respected at all times.
Due to the heating of the device under operation, the following
spacings have to be respected for the installation:
The IMC15 is listed as an „open type device“ and must be
installed into a machine or a plant. Installations that allow
open access to the device are prohibited.

4 Installation
7
4.3 Electrical Connectors
4.3.1 Introduction
All installation work has to be carried out by qualified person-
nel and according to appropriate regulations.
The electrical connections have to be carried out using the
connection diagram in the appendix. Since this is an applica-
tion-specific document, it has to be ensured, that the correct
document (correct version of this manual) ist being used.
The device may only be energized when the installation has
been successfully completed. Always connect the mains last.
4.3.2 Magnetic Bearing Connectors
In order to operate the magnetic bearings, both bearing mag-
nets and sensors must be connected to the device. For the
sensors there are two options: For cable lengths up to 23
meters without additional SMX6B-amplifier, for variable cable
lengths from 2 to 31 meters with SMX6B-amplifier mounted on
the blower.
Always be sure to properly connect the shielding and to fasten
the cables tightly on to the mounting rail.
Designation Function Connector
X4 Sensors Sensors using
cables <23 m
D-Sub 15 pin, female
X1 TSA/
SMX6B/CAN
(Combination
Interface)
Sensors using
cables > 23 m
and additional
SMX6B-amplifier D-Sub 21 pin, female, mixed
X3 Bearings Bearing magnets
D-Sub 25 pin, female

IMC15
8
4.3.3 Motor Terminal Block
To ensure proper sense of rotation, always respect the motor
phase succession given by the supplier.
The device has been designed to be used with permanent
magnet synchronous motors and has to be set anew if the
motor changes. Never operate any motor without prior con-
sent of MECOS AG.
If the motor is equipped with a PTC for stator winding tempe-
rature limit monitoring, it can be connected to the terminal
block J2 intended for that use (no polarity to be respected)

4 Installation
9
4.3.4 Line Terminal Block
The succession of phases can be chosen freely for the mains
connection. Conventions of the respective switching cabinet
wiring have to be respected.
Special attention has to be paid to the following points:
•Always use the line filter specified by MECOS AG (mfr
Schaffner EMC, Type FN3258-30-33 or FN3258-30-47, or
mfr. FUSS, type 3F460-030.270).
•Do not use any type of series choke for adaptation of
input voltage or enhancing quality of input current.
•The mains connection has to be fused at 32 A using a
device approved „for use with UL 61800-5-1“ and as „self
protected combination motor controller“ (see also chapter
2.1).

IMC15
10
4.3.5 Connectors of the Customer Specific Interfaces
Dependig on the model of IMC15 one or more of the following
connectors may be provided:
For the pin assignment and electrical specification of the
DigI/O connector please refer to the appendix.
Designation Function Connector
X5 Multipur-
pose Measurement
signals D-Sub 9 pin, male
X6 CAN Field bus
D-Sub 9 pin, female
X7 Profibus Field bus
D-Sub 9 pin, female
X2 Dig I/O Digital inputs,
outputs and insu-
lated supply Mini-Combicon 12 pin, male

4 Installation
11
4.3.6 EMC Issues
The IMC15 has been designed to fulfill the low voltage direc-
tive as well as the EMC directives provided the installation has
been carried out correctly. EMC- certification has been obtai-
ned in an accredited laboratory. The results may not be uncon-
ditionally applied to any type of installation containing an
IMC15.
In order to fulfill the EMC-directives attention has to be paid to
the following points:
1Ensure good electrical connection between mounting base
and device (use tooth locked washers)
2Ground the shielding of the motor cable onto the mount-
ing plate as close as possible to the device
3Use shielded motor cable
4Ensure good grounding of load
5Use line filter (mfr Schaffner EMC, Type FN3258-30-33 or
FN3258-30-47, or mfr. FUSS, type 3F460-030.270)
6Be sure to have good connections to the central grounding
point of the plant
7Use shielded cable for the control lines, be sure to ground
the shielding properly
8Use mounting rail as shielding point for AMB cables
Hint: Be sure to connect mounting base well to the central
grounding point of the plant.

IMC15
12

5 Operation
13
5 OPERATION
5.1 Display and Keypad
The alphanumeric display has 4 rows of 20 characters each.
The text-based menus are supported by 5 addtional symbols.
The keypad consists of 6 push buttons whose respective func-
tions are explained by a symbol or a piece of text. 3 push but-
tons are equipped with light emitting diodes (LED) for an
additional indication of the device state.

IMC15
14
No Name Function
1Menu title Title of menu page
2Context depen-
dent symbol Navigating through and choosing from
menus
3Menu number Number of the displayed menu
4Navigation aid Inidicates, if there are further menus
available by pushing „up“ or „down“
5Lift up /
Lift down Levitating/delevitating of the rotor
LED flashes green: rotor ist being levi-
tated/delevitated
LED constantly green: rotor levitating
6Drive on /
Drive off Starting / stopping of the motor
LED flashes orange: drive is braking.
LED constantly orange: drive is running
Function only implemented up to SW
Version 4.09
7Mode
(abbreviated
by „M“)
Change between modes
LED flashes red: warning
LED constantly red: fault
8Up Navigation button
No LED
9Enter Navigation button
No LED
10 Down Navigation button
No LED

5 Operation
15
Symbols:
Symbol Function Indicates
Navigation aid See further options by pressing „up“
Navigation aid See further options by pressing „up“
or „down“
Navigation aid See further options by pressing
„down“
Context depen-
dent symbol Choose from a menu
Context depen-
dent symbol View contents of fault history or cur-
rent fault monitor

IMC15
16
5.2 Navigation using the Keypad
The navigation is based on screens, which are organised in 4
modes to form a menu structure. By using the keypad,
screens can be displayed and their contents be either chosen
(activated) and/or displayed.
Table of contents
Popular Controllers manuals by other brands
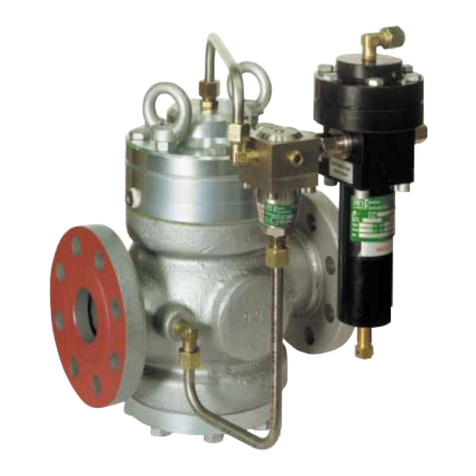
PIETRO FIORENTINI
PIETRO FIORENTINI APERFLUX 851 Technical manual
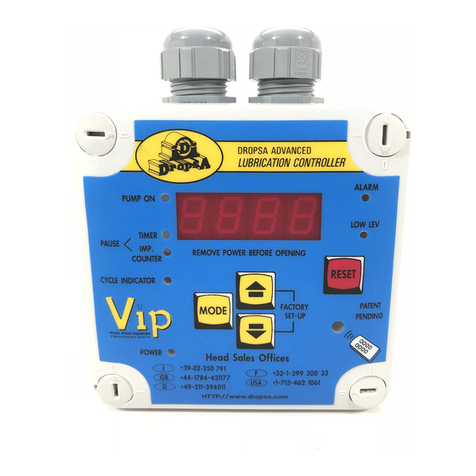
DROPSA
DROPSA ADVANCED LUBRICATION CONTROLLER INSTRUCTION AND PRODUCT DATA SHEET
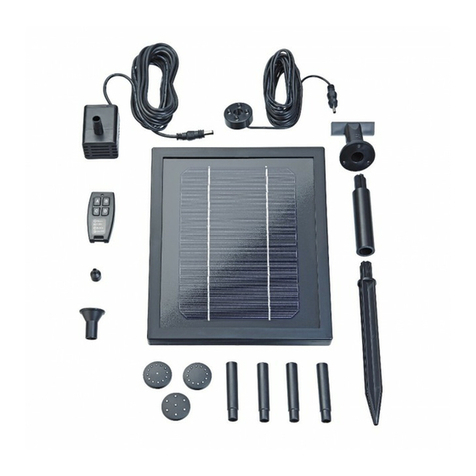
Pontec
Pontec PondoSolar 250 Control operating instructions
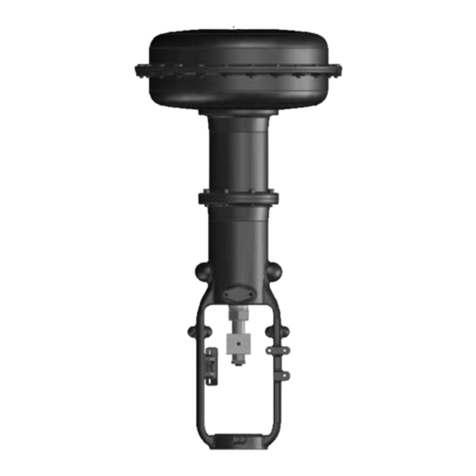
Emerson
Emerson Fisher 657C instruction manual
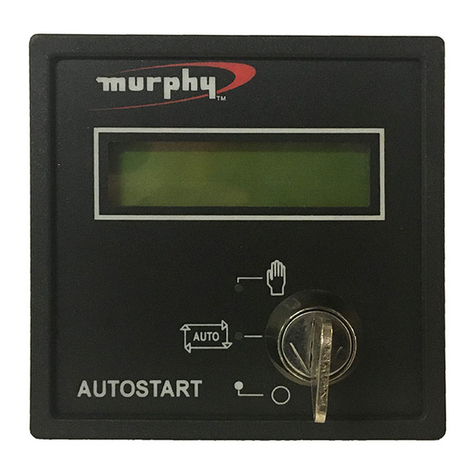
Murphy
Murphy Autostart 710 AS710S owner's manual
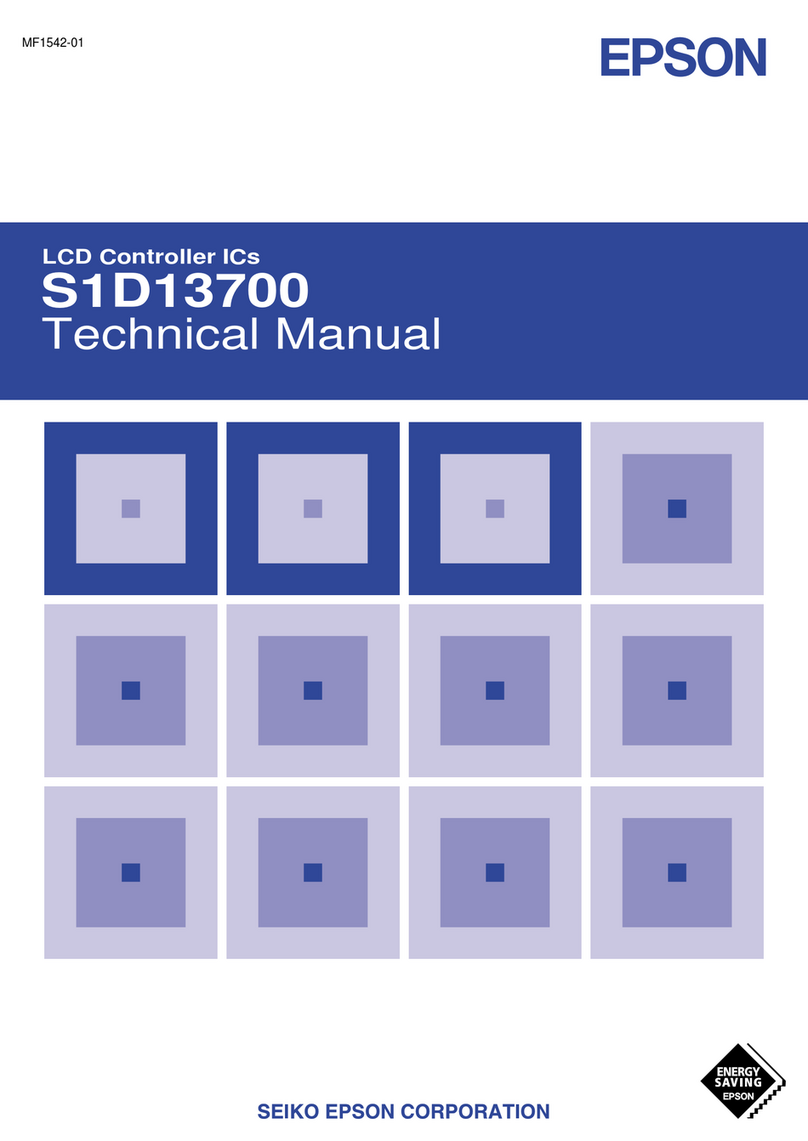
Epson
Epson S1D13700 User's & technical manual