Medha MAS 696 User manual

MEDHA SERVO DRIVES PVT. LTD.
Operator’s Manual
IM - 70 rev 3
TM
TYPE MAS 696
AC-AC TRACTION SYSTEM

Information in this document is subject to change without notice.
Copyright © 2010 Medha Servo Drives Pvt. Ltd. All rights reserved.
This document contains confidential, proprietary information of Medha Servo
Drives Pvt. Ltd. Unauthorized copying, reproduction, or disclosure of any portion
of the contents of these materials by any means—including printed or duplicated
materials, on‑screen publication, or Web documentation—is expressly forbidden.
Medha logo is trademark of Medha Servo Drives Pvt. Ltd. Any other trade-
marks are the property of their respective owners.
Document No: IM - 70 rev 3
Released: June. 2011.

Contents
Chapter 1 - System Overview...................................................5
Introduction.....................................................................5
Major Features of MAS 696 System.....................................8
Chapter 2 - General Safety Precautions..................................11
WDG4/WDP4 Locomotive Safety Precautions......................11
Automatic Discharge.......................................................12
Chapter 3 - Starting the Engine..............................................14
Chapter 4 - Stopping Procedure for WDG4/WDP4
Diesel Engine.......................................................18
Engine Stopping System..................................................18
Chapter 5 - Electrical Control Cabinets...................................20
ECC#1..........................................................................20
ECC#2...........................................................................21
ECC#3..........................................................................24
Driver Accessible Panels...................................................26
Circuit Breaker Panel.......................................................26
Test Panel.......................................................................28
Engine Control Panel on ECC#1........................................29
Control and Operating Switch Panel...................................31
Chapter 6 - Speedometer........................................................33
Chapter 7 - Tractive Effort/Dynamic Brake Effort Meter.........34
Chapter 8 - Indicating Lights Panel........................................35
Chapter 9 - Starting Fuse and Battery Switch Box......................39

Contents
Chapter 10 - Operation Section..............................................40
Preparation for Service....................................................40
Starting Lead Locomotive Engine.......................................43
Starting Trailing Locomotive Diesel Engine...........................45
Setting Locomotives on Line.............................................45
Precautions before Moving Locomotive..............................46
Handling Light Locomotive...............................................46
Coupling Locomotive Together..........................................47
Dynamic Braking for Locomotive in Tandem........................47
Engine on Train (Coupling Locomotive to Train)...................47
Pumping Up Air...............................................................48
Double Heading Service...................................................48
Helper Service................................................................48
Changing Operating Ends.................................................49
Stopping Engines............................................................50
Chapter 11 - Display Unit and Navigation Through Menus......51
Locomotive Control Computer Display Panel Details.............52
Menu Screens, Sequential Flow and Key Actions
for Display.....................................................................53
How to Select SELF TESTS................................................54
TM Cutout......................................................................56
Crew Messages List.........................................................60
Chapter 12 - Dos and Dont's, Display Menu Screens
and Parameters.................................................64

Chapter 1
SYSTEM OVERVIEW
1.1 Introduction
WDG4 and WDP4 series Diesel Electric
Locomotive of Indian Railways are driven by
3-phase AC Traction Motors, employing AC-
DC-AC Power Transmission system. Medha
Servo Drives Pvt. Ltd. has designed and
developed indigenously the AC-AC Traction
System type MAS 696 suitable to the above
said series of locomotives delivering up to
4500 HP.
MAS 696 is a comprehensive solution
encompassing complete locomotive control
and fault diagnostic features along with 3 MW
traction converter. MAS 696 AC AC Traction
system comprises of four cabinets:
ŸElectrical Control Cabinet 1 (ECC#1)
ŸElectrical Control Cabinet 2 (ECC#2)
ŸElectrical Control Cabinet 3 (ECC#3)
ŸTraction Control Cabinet (TCC)
The Diesel Electric Locomotive is equipped
with Turbo charger, 16 cylinders, two stroke
Diesel Engine. The Main Generator Assembly
is directly coupled with the Main Crank shaft of
the Diesel Engine. The Main Generator is 3
phase Alternator consisting of two
independent and Interwoven sets of stator
winding and rotor field common to both Fig. 1.1 Cabinets of AC AC
Traction System
ECC #2
ECC #1
ECC #3
TCC

6
Medha Servo Drives Pvt Ltd. MAS 696 Operator’s Manual
windings. Overview block diagram is given in Fig. 1.2.
The Diesel Engine drives the main Generator Assembly. The Main Generator
assembly has two Alternators which are MAIN ALTERNATOR and
COMPANION ALTERNATOR. The Traction Alternator converts the Diesel
Engine mechanical power into 3 phase AC electrical power. The Alternator’s
two windings’ (left bank and right bank) outputs are connected to two air
cooled Rectifier Assemblies consisting of high voltage, high current silicon
Diodes with Fuses in the 3 phase Full Wave Rectifier circuit. The two
Rectifiers output are connected in series across the DC LINK. The AC
3-phase power is converted into DC power by Rectifier Assembly. These are
the internal parts of TA-17-CA-6B Main Generator Assembly.
Rectified DC power supply is applied to DC LINK. When all DCL switch gears
are closed, DC voltage is applied to IGBT based Traction Inverters. Each
Traction Inverter has separate control module in the form of Traction
Computer. The Traction Computer receives Traction Motors’ speed,
temperature, Voltage and Current values for controlling the IGBTs to
maintain required torques according to Notch selection.
The Traction inverters have main role in controlling the 3 phase induction
motors. The Traction Inverters converts the DC power into 3 phase AC power
for variable frequency using IGBT based technology. Six DC LINK switch
gears passes the DC power to the six Traction Inverters through its closing
TM1 TM 3 TM 5 TM2 TM 4 TM 6
C A
Deisel
Engine Alternator
Auxiliary
Generator
Starting
Motors
A.G.
Control
(ZCD/GD)
Excitation
Control
Propulsion
Control
Governor
Engine
Control
Air
Compressor
Locomotive
Battery Unit
TCC
Grid
Resistors
Rectifier
Traction
Computer
Traction
Inverter
Traction
Computer
Traction
Inverter
Traction
Computer
Traction
Inverter
Traction
Computer
Traction
Inverter
Traction
Computer
Traction
Inverter
Traction
Computer
Traction
Inverter
Fig. 1.2 Block Diagram of Locomotive Control System

7
Chapter 1 - System Overview Medha Servo Drives Pvt Ltd.
contacts with the help of DC Motor controlled by Locomotive Control
Computer (LCC) which is housed in Electrical Control Cabinet 1 (ECC#1).
Traction Control Cabinet (TCC) consists of six Traction Computers, 6 DCL
switch gears, 6 IGBT based Inverters, DC link Capacitors and Crow bar
circuit. Based on the Inputs received from Locomotive Computer and
analogue feedbacks from Traction motors, Traction computer converts the
DC power into 3 phase AC power required to the traction motors. LCC
receives the operator request as digital inputs and analog signal from
different sensors and sends request to the traction computer for converting
required amount of Power during Motoring and Dynamic Braking modes. The
term TCC refers to an Electrical System that converts DC power into 3 phase
AC power during motoring and 3 phase AC power into DC power during
dynamic brake. The terms Invert and Convert are interchangeable in this
locomotive during Power Mode and Dynamic Brake Mode.
The Traction Motors are 3 phase AC Induction Motors. The 3 phase AC
power from Inverters are fed to the Traction Motors mounted on the Trucks,
Each Traction Motor is geared with a pair of Wheels with the gear ratio 17:90
(MAC loco) for Goods Service and 17:77 (PAC loco) for Passenger service.
The Traction Motors once again convert the Electrical power into Mechanical
power to provide high starting Torque required for Locomotive service. These
are explained in detail in later chapters.
1.1.1 Auxiliary Generator
The Auxiliary Generator (Aux. Gen.) Is driven by the Engine gear train at
three times of engine speed. Its field is controlled by LCC through AG PWM.
AC power from Aux.Gen. is supplied to an external 3 phase Full wave
rectifier in the Battery Charging Assembly. There it is converted to 74 volts
DC power for Companion Alternator excitation, control system operation and
Locomotive Battery charging. The Aux. Gen. also supplies 74 volts DC power
for Fuel Pump Motor, Turbo lube oil Pump circuits, Locomotive lighting and
other miscellaneous equipments.
1.1.2 Companion Alternator
The Companion Alternator (CA) is coupled directly to the Traction Alternator
within the Main Generator housing. The Companion Alternator is physically
connected to the Main Gen. assembly but electrically independent to the
Traction Alternator. Companion Alternator has 16 field poles on the same
rotor back of Main Gen. field poles. The rotating CA field poles receiving low
voltage current from Aux. Gen. through a pair of slip rings are adjacent to the

8
Medha Servo Drives Pvt Ltd. MAS 696 Operator’s Manual
Main Alternator slip rings. CA produces 3 phase 45-230 V AC supply to
excite Main Alternator field through SCR Assembly and Power fed to the
Radiator Fans 1 & 2, Inertial Blower motor and Traction Inverter Blowers.
1.2 Major Features of MAS 696 System
Major Features of the System in operation point of view are explained
hereafter.
1.2.1 DYNAMIC BRAKE
Dynamic Brake is an electrical braking method used to regulate the speed of
the Locomotive by translating the Kinetic Energy in the Traction Motors into
Electric Energy. This Mechanical rotating energy is converted to Electrical
Power by using Traction Motors as electrical Generators. The power
generated by these Traction Motors are applied to the Grid Resistors, which
dissipate the generated power in the form of heat into the atmosphere, there
by reducing the speed of the train.
Re-generation operation of AC Induction Machine is not so easy to explain.
To examine the entire Braking process, consider first a DC Machine in a
Generating mode. In this case a stationary magnetic field is established in
the stator of the Motor. The momentum of the Train causes the Motor to Turn.
As the motor turns, the Armature cuts through the stationary magnetic field
in the stator. This cutting generates a current flow in the Armature which is
dissipated through Grid resistors.
On the DC Machines four power cables are run to the Motor, two are
connected to the field and two to the Armature. The cabling that runs to the
Grid Resistors makes a connection with the Armature. For Motoring
operation, armature cables and field cables are connected in series and
across the generator. During Dynamic Brake, Filed cables are connected
across the generator and armature cables are connected to the grid resistors
to dissipate the generated energy in the form of heat to the atmosphere.
In the AC Machines only three cables are connected to the Motor. These
cables supply 3 phase AC source needed by Motors both in Power and
Dynamic Brake mode. For more braking effort the Inverters supply more
power to the field. So power must always flow into the Motor to excite the field
(regardless of operation mode).
Power is multiplied by two components, Voltage and Current. The direction
of power flow depends on the relationship between Voltage and Current with

9
Chapter 1 - System Overview Medha Servo Drives Pvt Ltd.
respect to the time or phase relationship. The phase relationship depends on
the speed of the Rotating Field with respect to the Rotating speed of the
Rotor. If Rotor speed lags Field speed, Voltage and Currents are nearly in
phase and Power flows into the Motor most of the time. If Rotor Speed
exceeds Fields speed, Voltage and Current are out of phase by nearly 180
degree and Power flows out of the Motor most of the time.
1.2.2 Alerter/VCD System
The Alerter indicator light is mounted on the control consol, below the
indicator light panel. The Alerter reset push button mounts on the control
consol desktop surface. The Audible Alarm is mounted on the ECC#1 Engine
control panel. ALERTER SYSTEM can be ENABLED through Display Unit
by selecting proper option. When Locomotive Brakes are released, the
Alerter system requests an Acknowledgement from the operator from time to
time, once in 60 seconds. If the Acknowledgement request is not answered
within 60 seconds, the Locomotive control Computer drives a Digital Output
to flash the Alerter light for 17 sec. After 17 sec drive, one more Digital Output
provides an audible sound for 17 sec. If the Alerter request is not
acknowledged, while the Aleter light is flashing or alerter alarm is sounding,
the alarm stops sounding and a penalty Brake is applied for 34 seconds or
until Locomotives speed drops to zero, whichever occurs first. Then the
penalty brake application must be reset before normal operation of train to
continue. One must follow Railway rules and operating practices regarding
use of Alerter Equipment.
Pressing either alerter reset button while the Alerter light is flashing or the
Alerter Alarm is sounding, resets the acknowledgement request timing cycle.
Using the Automatic Brake handle to moderately reduce the brake pipe
pressure also resets the timing cycle. Automatic Brake handle operation also
resets the timing cycle. In addition, movement of the Throttle Handle,
Independent Brake handle or Dy. Brake handle also reset the timing cycle,
as well as pressing the HORN or SAND button.
1.2.3 A E B : Auto Emergency Brake System
While traveling through a terrain with a considerable large Down-Gradient,
speed of the Train needs to be kept under control, so that the AEB system
does not allow to enter in uncontrollable speed zone. Indian Railways has
studied and defined optimum speeds for every section. There is popular
saying that human can do mistakes. There is always chance that a manually
controlled Loco may exceed the section speed limit. Which in turn may cause
major accidents/loss/damage. To avoid this, Indian Railways incorporated a

10
Medha Servo Drives Pvt Ltd. MAS 696 Operator’s Manual
system called "Auto Emergency Brake System", which by default initiates
Braking in the event of Train/Loco crossing the permissible set speed. The
microprocessor based inbuilt AEB system, developed by M/S Medha Servo
Drives Pvt. Ltd., is implemented on WDG4 and WDP4 Locomotives.
1.2.4 Blended Brake System
The MAS 696 system Locomotives are equipped with blended brake system.
It is simultaneously applying Dynamic Brake and Air Brake, when the driver
operates the Automatic Air brake handle in the service zone. The KNORR
CCB Air Brake system controls the Airbrake on the Locomotives and cars
coupled in train, and requests some amount of Dynamic Braking from LCC
for blended brake operation.
1.2.5 Manual TE Limiting
To avoid putting stresses on weak bridges when Locomotive is traversing
them, the Manual TE Limiting option was developed to enable the operator
to limit the Tractive Effort through (lighted) switch mounted on Engine control
panel. The position of the switch indicates the loco pilot that the feature has
been turned ON, indicating that the switch is active. The tractive effort limit
may be imposed by train line Input from another locomotive equipped with
this feature via TEL relay.
1.2.6 Auto Flasher
To switch ON of Flasher Lights automatically during Train parting, RDSO has
suggested modification in the existing Brake and Electrical control circuit of
Locomotives, to link switching ON of Flasher Light switch drop in Brake pipe
pressure on Locomotive. The flasher lights are applied automatically
whenever Emergency/penalty brake application takes place, as indicated by
the 'Loss of PCS'. The flasher can still be turned ON manually so that if the
operator have an Emergency that did not drop PCS, the Flashers can still be
activated.

Chapter 2
GENERAL SAFETY
PRECAUTIONS
This manual provides guidelines and cautions for Locomotive operating
personnel. Though enough care is taken while designing MAS 696 system
developed by M/S MEDHA SERVO DRIVES PVT. LTD, which is
implemented on WDG4/WDP4 Locomotive, the Microprocessor based
system to keep as similar as existing WDG4 and WDP4 Locomotives in
operational point of view, due to advanced features, some modifications
have taken place. This manual includes information compiled for a typical
WDG4/WDP4 Locomotive with basic equipment and its functions explained
in short notes. These instructions do not cover all details or variations in
equipment, nor provide for every contingency. If any further information is
required, or if problems arise which are not covered sufficiently, M/S
MEDHA's representatives can be contacted.
Information about adjustment, testing and maintaining Locomotive
equipment is provided in other Locomotive service manual and various
maintenance instructions.
2.1 WDG4/WDP4 Locomotive Safety Precautions
WDG4/WDP4 Locomotive has an AC Electrical Transmission system and
therefore includes special equipment not found on Locomotive having the
usual DC/DC or AC/DC Transmissions. For safety sake, it is necessary to
fallow certain unique precautions before inspecting the equipment or
operating the Locomotive.
The Locomotive operator shall not access any devices within the ECC#1 due
to residual high voltage. Access within ECC#1 is limited to maintenance
individuals that are knowledgeable of the WDG4/WDP4 DC LINK discharge
procedure. The output of the Main Generator is the DC LINK VOLTAGE.
Large capacitors are located within each of Traction Inverter to filter Main

12
Medha Servo Drives Pvt Ltd. MAS 696 Operator’s Manual
Gen. Voltage. These capacitors operate at the DC LINK Voltage between
600 to 3400 V DC. When the Locomotive shutdowns, these capacitors could
remain high Voltage causing severe injury or death to the operating and
maintenance personnel.
A procedure has been developed to discharge this high voltage into Dynamic
Brake Grids to prevent the possibility of Injury.
1. Before shutdown of the Locomotive, keep RUN/ISOLATE switch in
ISOLATE position and then shutdown the Locomotive. All 'BRAKING
CONTACTORS' picks up and discharge the DC LINK capacitors
through Grid resistors in one second. After 20 seconds all DC LINK
switch geares are driven to shorting position.
2. After shutdown, the Locomotive remains the COMP. CONTROL and
TURBO LUBE PUMP Circuit Breakers in ON position. These two
CB's are required to perform POST LUBRICATION for TURBO
SUPER CHARGER for 35 minutes.
3. If any disturbance for Post lubrication occurs within 35 minutes, while
cranking, Computer does not allow for cranking unless PRE-
LUBRICATION is successfully completed for 15 minutes.
2.2 Automatic Discharge
The DCL Voltage is discharged automatically, when the Locomotive operator
takes manual action to shutdown the Locomotive. There are 3 general ways
to discharge the DC LINK capacitors and other components prior to
servicing, plus a fourth method to maintain the short.
1. Reverser in Centre Position (Through Bleeder Resistors)
Each Traction Inverter has Bleeder Resistors (400 k ohms/200 W)
across the DC LINK. When the Reverser is moved from Forward or
Reverse to Centre, main Generator Excitation stops. If no further
action is taken, the Bleeder Resistors discharges the DC LINK
voltage to less than 50 Volts in approximately 50 minutes.
Although very reliable, the Bleeder Resistors do not guarantee the
discharge since the resistor could be interrupted internally or
externally.
2. Run/Isolation Switch (Through Dynamic Brake Grids)
The normal way to discharge the DC LINK capacitors is through
two Dynamic Brake Grids in parallel. When Locomotive operator
turns Isolation switch from RUN to ISOLATE (or the LCC loses the

Chapter 2 - General Safety Precautions Medha Servo Drives Pvt Ltd.
13
RUN digital Input signal), the parallel Brake Grid path is connected
to the DC LINK by four Braking contactors (B1, B2, B3, B4). This
method discharges the DC LINK capacitors in less than ONE second.
3. Brake Chopper and Hard Crow Bar
Whenever the DCL V >= 2800V Brake Chopper fires to bring the
DCL V to <= 2600 V, if the DCL V >= 3000 V TCC Lockout the
operation of Inverters, and the DCL V >= 3400 V Locomotive
Control Computer fires Hard Crowbar, at DCL V >= 3600 V HW
Fires Hard Crowbar. Automatically recycling of DCL switch gears
when DCL Voltage decoys, if there was no other Crowbar event in
last 10 minutes.
ŸAfter the DC LINK has been discharged by braking grids or the brake
chopper or crow bar, the DC LINK Contactors moves to the open
position. Moving all the DC LINK switch gears to the open position
causing all Traction Inverters to be shorted and grounded with busbar
connected to connectors of the DCL contactors.
a. When the Engine is shutdown (regardless of the Isolation switch
position) the control computer picks up all the Braking contacotrs,
the DC link Voltage dissipate through grid resistors. Once the DC
LINK capacitors are discharged, DCL contactor moves to open
position.
b. Whenever the Battery Knife switch or Local control circuit breaker
is opened, the LCC detects the loss of Local control or Knife
switch and moves all DCL contactors to shorted position. Indian
Railways Electrical Control Cabinet 1 comprises of all electrical
controls of the locomotive along with Locomotive Control
Computer.

Chapter 3
STARTING THE ENGINE
The WDG4/WDP4 Locomotive is equipped with dual STARTOR MOTORS
for cranking the Diesel Engine, at left side near the Engine Ring gear. Diesel
Engine fuel oil must be circulated through fuel system before the Engine
starts. When the FP/ES switch is held in PRIME (left), the Locomotive
computer starts the fuel Pump motor. After ensuring the return fuel sight
glass clear without bubbles (approximately 20 seconds), turn the FP/ES
switch to START (right) position. These STARTOR MOTORS run with
Battery supply available on Locomotive to start the Diesel Engine.
While cranking the Diesel Engine, ensure the following:
1. Ensure that Throttle Handle of both control console is in IDLE,
Reverser handle at center and RUN/ISOLATE Switch is in ISOLATE
position.
2. Ensure there is sufficient oil level of Compressor Oil, Engine Lube Oil
and Governor Oil.
3. Ensure there is sufficient Coolant Water level in the water tank
(Engine dead – Full).
4. Ensure that no one is working on the Engine, Generator Room,
Compressor Room etc. and all doors are closed.
5. Ensure that the MU Engine Stop button is in RUN position (For RUN
press Green portion inside).
6. Ensure that the engine Over Speed Mechanism (OST) is reset.
7. Ensure that the Governor Low Lube Oil Button (LLOB) is reset.
8. Ensure that the Crankcase (oil pan) pressure and Low water
pressure detector reset buttons are reset (pressed inside). If any
button is found ejected, press and hold it for 15 seconds immediately
after Engine starts.

15
Medha Servo Drives Pvt Ltd. MAS 696 Operator’s Manual
Engine should be Pre-Lubricated, if it has been shutdown for more than 48
hours. See Engine Maintenance Manual for Pre-Lubrication procedure.
To Start The Engine, follow the below procedure:
1. Close the Battery knife Switch. Ensure that the Starting Fuse is
installed in good condition and it is at correct rating. (800 Amps for
WDG4/WDP4).
2. Switch ON Control and Local Control circuit Breakers on Breaker
panel.
3. Switch “ON” TURBO lube pump Circuit Breaker to pick up “TLPR”
when Turbo lubrication is required.
4. Switch 'ON' DCL 1 CB, DCL 2 CB, DCL 3 CB, DCL 4 CB, DCL 5 CB
and DCL 6 CB on Circuit Breaker panel to control DCL switch gear
motor for closing and opening the DCL switch gear.
5. Switch ON all Traction Computer circuit breakers TC-1 CB, TC-2 CB,
TC-3 CB, TC-4 CB, TC-5 CB and TC-6 CB. All Traction Computers
Initializes and power ON self check is done.
6. Switch ON COMP. CONTROL Circuit Breaker. The MAS 696 System
Initializes and Power ON self check is done. If any abnormality is
found, the same message is informed through Display Unit for
correction, otherwise the MAIN MENU is displayed.
7. Switch ON all Traction Computer Blower circuit breakers TCC BLWR
1 CB, TCC BLWR 2 CB, TCC BLWR 3 CB, TCC BLWR 4 CB, TCC
BLWR 5 CB and TCC BLWR 6 CB to control and protect TC Blower
motors.
8. Switch ON the CONTROL & FP slide switch on control console No.
2. This allows fuel pump to RUN, when FP/ES switch is in Fuel prime
or Engine Start position.
9. Switch ON the FUEL PUMP Circuit Breaker.
10. Switch ON the AC CONTROL Circuit Beaker.
11. Switch ON the Governor Booster Pump CB, if it is available on
locomotive.
Check Time and Date of Loco shutdown from the Engine
logbook. If the Loco has been shutdown for more than 48 hours,
don't start the Engine and contact home shed for advice.
NOTE

Chapter 3 - Starting the Engine Medha Servo Drives Pvt Ltd.
16
12. Turn the FP/ES switch lever to PRIME and hold it there (normally 10
- 20 sec, then release it) until the fuel flows clear and free from
bubbles in the return fuel sight glass.
13. Turn the FP/ES switch lever to ENGINE START and hold it there until
the Engine Starts and speed increases to Low Idle RPM 200. Do not
crank for more than 20 seconds.
14. After holding the engine RPM above 200 rpm, release the FP/ES
button.
15. Check Low water pressure detector reset button on EPD after Engine
starts. If the detector is not reset, the Engine shuts down after a short
time delay. If the detector trips, press continuously for 15 seconds.
ŸIf the Governor Booster pump is not provided on
Locomotive, Advance the Governor linkage Lay shaft
gently while cranking, till the Engine is running.
ŸVerify that the Ground Relay CUTOUT Switch is closed
(lever up) and sealed properly. It is located on the Circuit
Breaker Panel.
ŸNever discharge Batteries excessively by repeated cranking.
If first two or three attempts are failed, identify the fault
or check and reset safety devices like OSTA/LLOB etc. If
any one is tripped, recheck cranking procedure.
ŸEnsure that MU Engine Stop button is not operated in
the consist Locomotives.
ŸFollow the correct Cranking and Shutdown procedure to
enhance Engine and Turbo life.
NOTE
To prevent over heating of starting Motors, which may damage
them, do not allow Engine cranking for more than 20 seconds.
If Engine fails to start after cranking for 20 seconds, wait for 2
minutes to cool starting Motors before cranking Engine again.
CAUTION

17
Medha Servo Drives Pvt Ltd. MAS 696 Operator’s Manual
16. Follow specified standard Railroad precautions in setting of
LEAD/TRAIL switch for safe operation.
17. Follow correct Air Brake equipment setup procedure to avoid delay
and incorrect operation.
18. To perform Air Brake System normal working, keep LEAD/TRAIL
switch in LEAD position on required control console, in other control
console it must be in TRAIL only.
19. Check the Display for CREW MESSAGES one by one and clear as
per the Computer advice.
20. Keep Auto Brake Handle in Full Service on working control console
and observe the following message after 10 seconds.
Message: To restore normal Air Brake operation, keep Auto
Brake Handle in RUN position.
ŸKeep the Engine at Low Idle for 6 minutes. Don't shift the
ISOLATION switch to RUN position immediately to avoid
automatic shutdown due to low water and low LUBE OIL
Pressure. After six minutes automatically Engine speed
increases for Air compressor operation or Low water
temperature.
ŸEnsure that the Batteries are charging and Battery Ammeter
is showing charging side (Green zone).
ŸDo not apply load before Engine water inlet temperature
has been reached 49º C.
CAUTION

Chapter 4
STOPPING PROCEDURE FOR
WDG4/WDP4 DIESEL ENGINE
4.1 Engine Stopping System
The normal way to shutdown a Diesel Engine is to cause the Engine
Governor to bring the fuel injector to the NO FUEL position. There are
several ways to cause the Governor to bring the fuel injectors to NO FUEL
position including operating the following switches:
1. EFCO/STOP: The Emergency Fuel Cutoff & Engine Stop push
Button switch mounted on the high voltage cabinet Engine control
panel in the cab.
2. EFCO 2: The emergency fuel cutoff push Button switch mounted on
the left side of the locomotive just above the fuel tank filler.
3. EFCO 3: The emergency fuel cutoff push button switch mounted on
the right side of the Locomotive just above the fuel tank filler.
4. MU ENG.STOP: The multiple Engine Stop/Run switch mounted on
the control console#2 pressing the STOP portion of this switch stops
all Engines in the consists. This is the result of the pickup of SDR
relay, when SDR is picked up, Governor DV solenoid energizes and
Fuel Rack comes to No Fuel position.
5. The Governor also brings the fuel injectors to the NO FUEL position,
if any of the following conditions is occurred:
ŸEngine lube oil pressure is too low.
ŸEngine lube oil is too Hot.
ŸEngine coolant water pressure is too low.
ŸEngine crank case pressure is too high.

19
Medha Servo Drives Pvt Ltd. MAS 696 Operator’s Manual
6. After shutdown of the Locomotive let the COMP. CONTROL and
TURBOLUBE PUMP Circuit Breakers remain in ON position. These
two CB's are required to perform POST LUBRICATION for TURBO
SUPER CHARGER for (maximum) 35 minutes.
Fig. 4.1 EFCO Engine Stop
Fig. 4.2 MU Engine Stop

Chapter 5
ELECTRICAL CONTROL
CABINETS
As mentioned in Chapter 1, MAS 696 AC AC Traction System comprises of
four Cabinets, viz. ECC#1, ECC#2, ECC#3 and TCC. The three Electrical
Control Cabinets are explained in detail in the following sections:
5.1 ECC#1
The Electrical Control Cabinet, as shown in Fig. 5.1, is located in the drivers
cab. It houses equipments that controls and supplies power to the
Locomotive.
The various internal equipments (not driver
accessible) included in ECC#1 are:
1. Main Control Panel (Relays, Resistors
etc.)
2. Locomotive Control Computer MLC 691
3. ADB 1, 2, 3, 4 and FDB
4. Four Braking contactors (B1, B2, B3, B4)
5. Silicon Control Rectifier (SCR) Assembly
High voltage and current are present within this cabinet. Do
NOT open a cabinet door except to access the Circuit Breaker
panels.
WARNING
Fig. 5.1 Electrical Control Cabinet#1
Table of contents
Other Medha Control System manuals
Popular Control System manuals by other brands
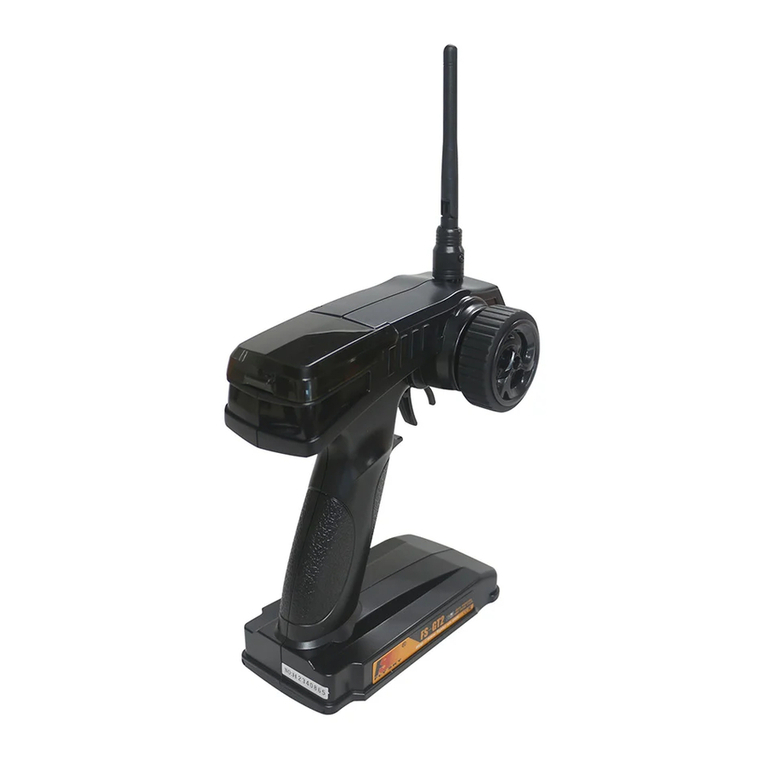
Fly Sky
Fly Sky FS-GT2 instruction manual
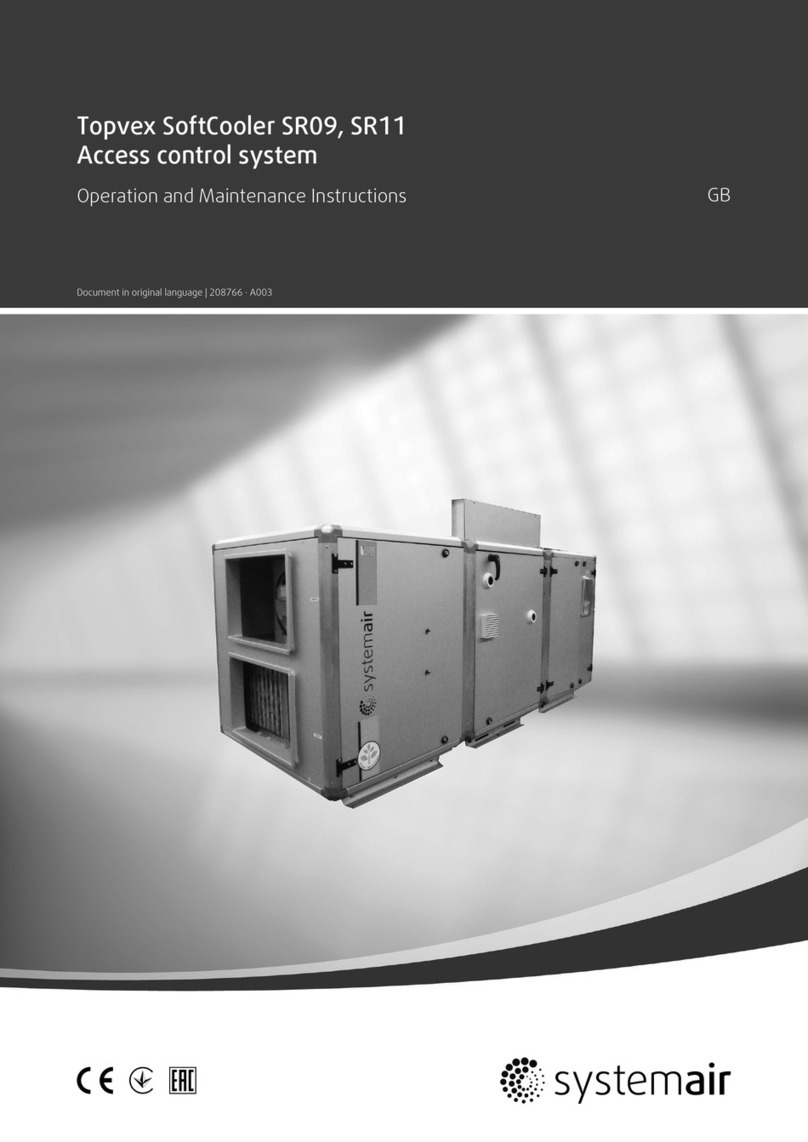
System air
System air Topvex SoftCooler SR11-L manual
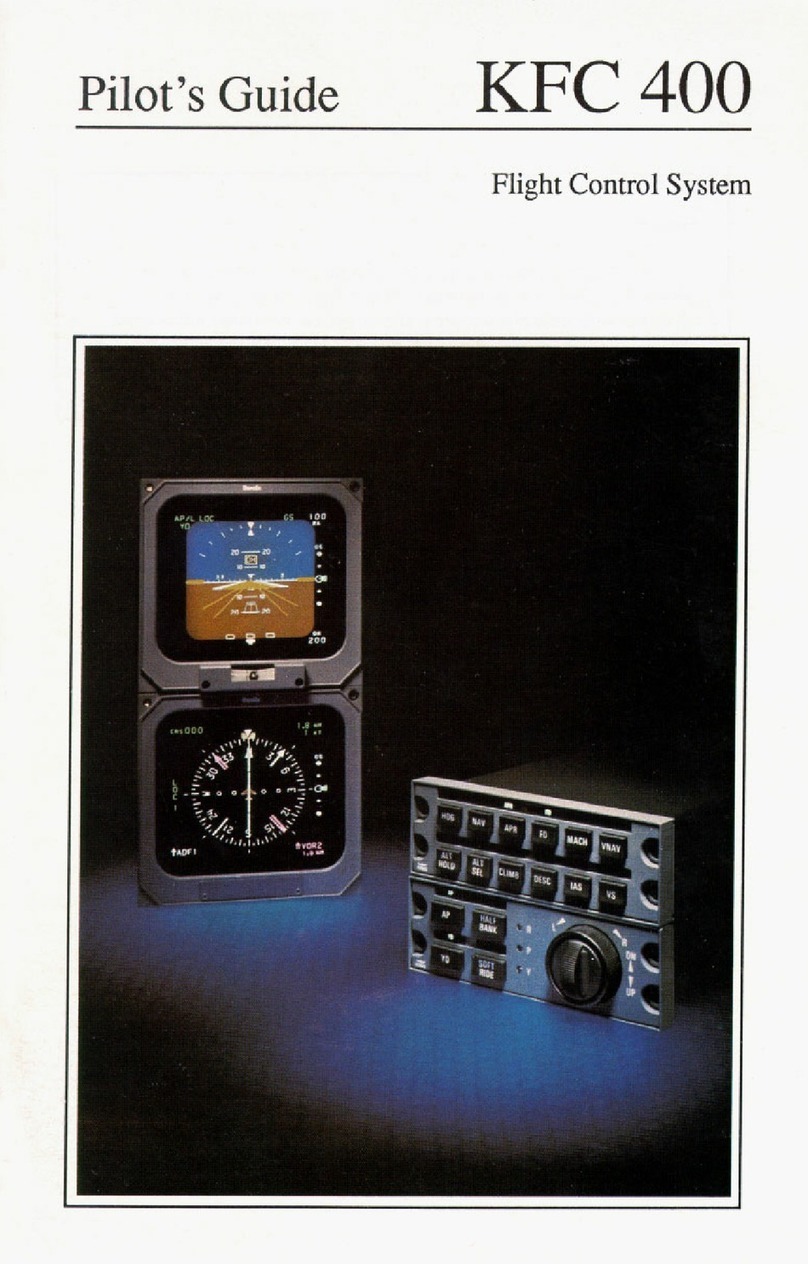
BENDIXKing
BENDIXKing Skymap IIIC pilot's guide
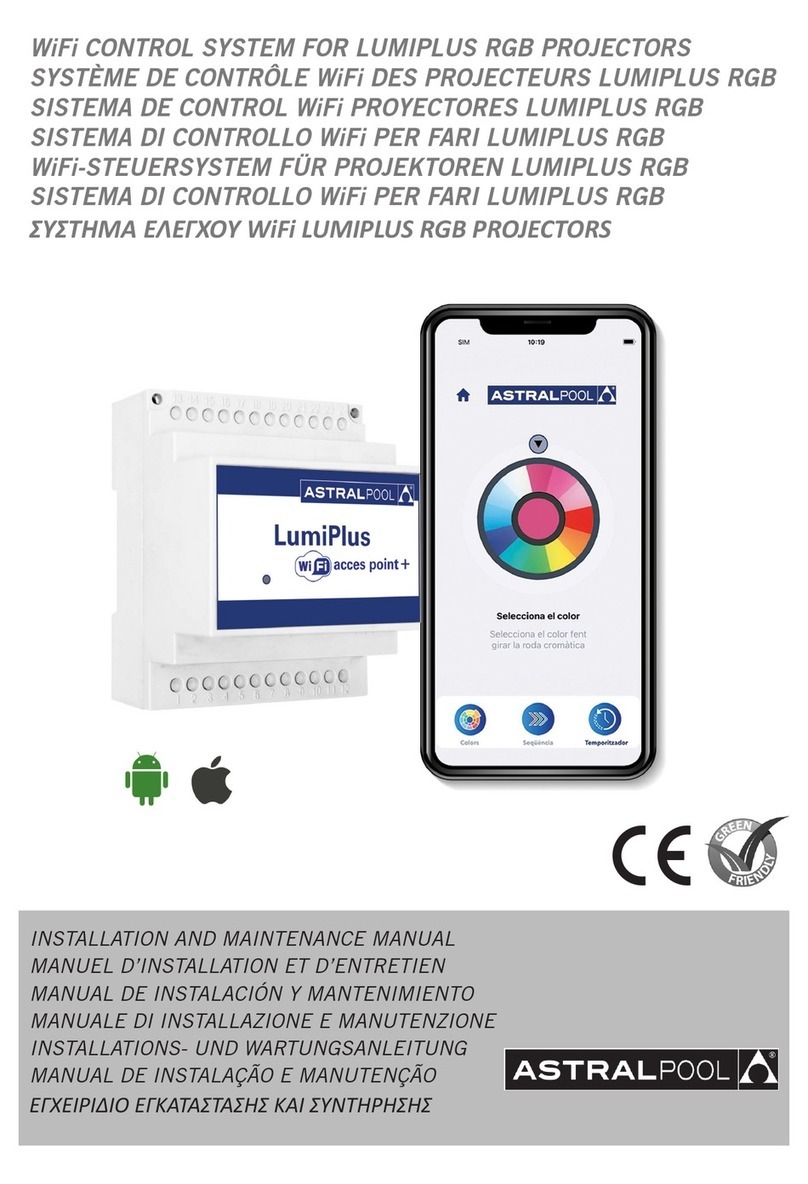
Astral Pool
Astral Pool LumiPlus 75813 Installation and maintenance manual
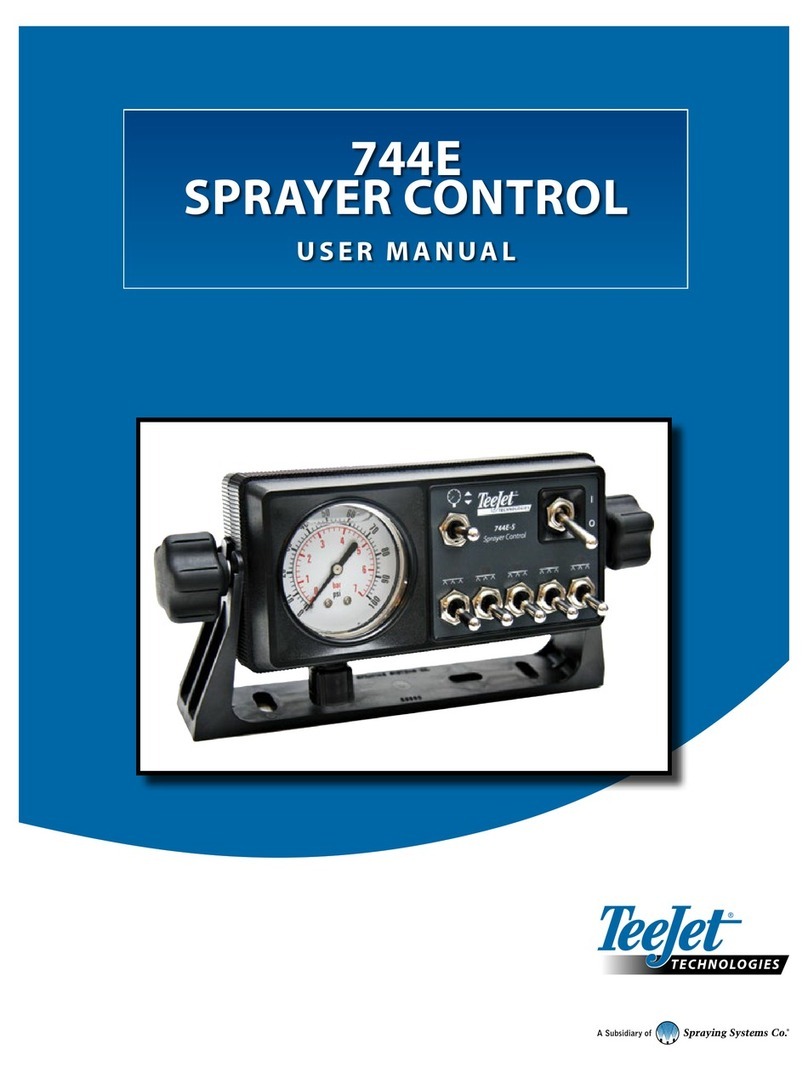
Spraying Systems
Spraying Systems TeeJet Technologies 744E user manual
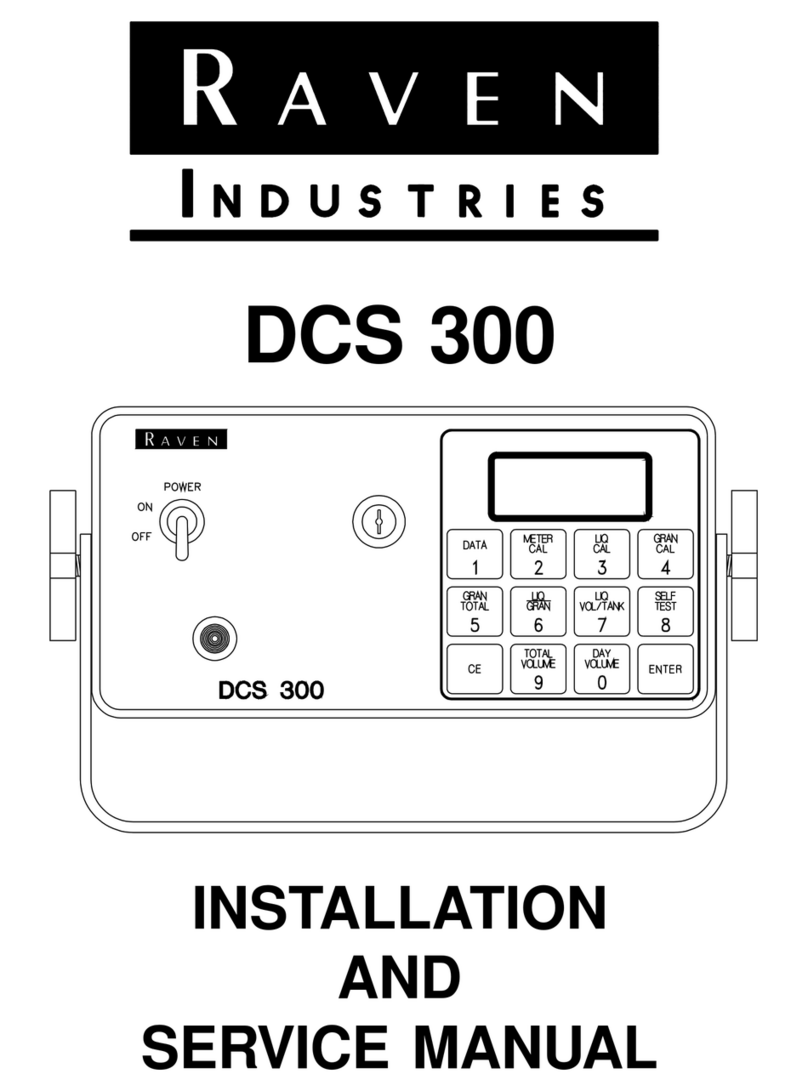
Raven
Raven DCS 300 Installation and service manual