Medisoft 800 Series User manual

Series 800 Treadmills
Service Manual
and
troubleshooting guide
870 A/S/C Model
REV. 1/01.07-2019

Service Manual 800 series Rev. 1/01.07.2019
Medisoft RAM Italia S.r.l. - All rights reserved
The information contained in this manual is strictly
private and property of Medisoft Ram Italia srl.
This document can not be copied, photocopied,
reproduced entirely or in part without previous
written consents from Medisoft Ram Italia srl
Valid as of 27 July, 2017

Service Manual 800 series Rev. 1/01.07.2019
Medisoft RAM Italia S.r.l. - All rights reserved
CONTENTS
Service Manual and troubleshooting guide
1 - Introduction............................................................................................................................1
2 - System breakdowns and diagnostic procedures ....................................................................2
3 - Diagnosis of the inclination subsystem .................................................................................2
3.1 - Flow chart for the diagnosis of inclination subsystem ..........................................................3
3.2 - Transmission check ...............................................................................................................4
3.3 - Connection check...................................................................................................................4
3.4 - RS232 cable check.................................................................................................................4
3.5 - Substitution of RS232 cable ..................................................................................................4
3.6 - Inclination check....................................................................................................................5
3.7 - Treadmill check .....................................................................................................................5
3.8 - Removal of hood....................................................................................................................6
3.9 - Control board input check .....................................................................................................6
3.10 - Filter board and control board fuses check............................................................................7
3.11 - Test control boardand elevation motor..................................................................................8
3.12 - Test limit switch ....................................................................................................................9
3.13 - Test of 0% limit switch........................................................................................................10
3.14 - Substitution of control board...............................................................................................10
3.15 - Inclination actuator screw lubrication .................................................................................11
3.16 - Substitution of elevation motor ...........................................................................................12
4 - Diagnosis of velocity subsystem .........................................................................................13
4.1 - Flow chart for the diagnosis of velocity subsystem.............................................................14
4.2 - Velocity check.....................................................................................................................15
4.3 - Inverter check ......................................................................................................................15
4.4 - Control board fuse check.....................................................................................................16
4.5 - Test signal control inverter..................................................................................................17
4.6 - Substitution of Control Board..............................................................................................17
4.7 - Test alimentation inverter....................................................................................................18
4.8 - Substitution of inverter........................................................................................................18
4.9 - Substitution of velocity motor.............................................................................................19
5 - Diagnosis of power subsystem ............................................................................................20
5.1 - Flow chart for power subsystem diagnosis..........................................................................21
5.2 - Warning light check.............................................................................................................22
5.3 - Plug check............................................................................................................................22
5.4 - Check imput main switch ....................................................................................................22
5.5 - Power cord substitution .......................................................................................................23
5.6 - Check output main switch ...................................................................................................23
5.7 - Replacement main switch....................................................................................................24
5.8 - Replacement warning light..................................................................................................24
5.9 - Lock safety switch...............................................................................................................24
5.10 - Check emergency buttons....................................................................................................25
5.11 - Test switch on......................................................................................................................25
5.12 - Check filter board................................................................................................................26
5.13 –Contactor test ......................................................................................................................26
5.14 - Test alimentation coil contactor...........................................................................................27

Service Manual 800 series Rev. 1/01.07.2019
Medisoft RAM Italia S.r.l. - All rights reserved
5.15 - Replacement contactor.......................................................................................................287
5.16 - Test alimentation control board.........................................................................................287
5.17 - Trasformer replacement.......................................................................................................28
5.18 - Check fuses control board ...................................................................................................28
5.19 - Test output J9 connector......................................................................................................29
5.20 - Check cable and emergency buttons....................................................................................29
5.21 - Security switch test..............................................................................................................30
6 - Diagnosis of gliding subsystem...........................................................................................31
6.1 - Flow chart for gliding subsystem diagnosis ........................................................................32
6.2 - Tautness check of drive belt ................................................................................................34
6.3 - Tautening of drive belt.........................................................................................................35
6.4 - Lubrication and gliding system check.................................................................................35
6.5 - Tautness check of running belt............................................................................................36
6.6 - Tautening of running belt ....................................................................................................36
6.7 - Replacement of gliding system............................................................................................37
6.8 - Disassembling the gliding subsystem..................................................................................40
6.9 - Replacing of running belt ....................................................................................................41
6.10 - Disposal of running belt.......................................................................................................41
6.11 - Deck Cleaning .....................................................................................................................41
6.12 - Lubrication of deck..............................................................................................................42
6.13 - Clean of rollers and control of bearings ..............................................................................43
6.14 - Cleaning of running belt......................................................................................................43
6.15 - Wear test drive belt ……………………………………………………………………….43
6.16 –Replacement of drive belt...................................................................................................43
6.17 - Restoring the gliding subsystem..........................................................................................44
7 - Maintenance planning –Critical Parts…………………………………………………….46
Annex A Transmission protocol technical specifications .............................................................47
7 - Maintenance planning –Critical parts…………………………………………………….46
8 - Setting RS232 command execution in MPH or Km / h.......................................................55
9 - List of the most important replacement parts......................................................................56
10 - Electric wiring diagram .......................................................................................................61

Service Manual 800 series Rev. 1/01.07.2019
1
Medisoft RAM Italia S.r.l. - All rights reserved
1 - Introduction
This manual identifies some of the most frequent system breakdowns of the series 800 treadmills
and describes the diagnostic procedures in order to eliminate breakdowns and return the system to
its correct functioning.
It refers principally to the troubleshooting of the 800 series.
WARNING:
Before resolving any treadmill breakdowns one must check that the connector located at the base
of the right handle has been correctly screwed in during the installation phase.
The incorrect closure of the connector’s ring nut could cause contact with some pins and not with
others. This could create breakdown symptoms as described below.

Service Manual 800 series Rev. 1/01.07.2019
2
Medisoft RAM Italia S.r.l. - All rights reserved
2 - System breakdowns and diagnostic procedures
WARNING:
Before undertaking any maintenance procedure, the service technicians must take the following
precautions:
1) Use tools with insulated handles
2) Wear personal protective clothing and equipment, such as insulated gloves and shoes,
3) Switch off the equipment (ON/OFF switch to "0") and remove the plug from the outlet.
The following table lists the most frequent system breakdowns and associates the symptoms with
various diagnostic procedures.
Symptom
Diagnostic Procedure
Par
The treadmill does not raise or fall
Diagnosis of the inclination subsystem
3
The treadmill does not rotate (does not move)
Diagnosis of the velocity subsystem
4
The treadmill does not turn on
(the belt does not elevate and it does not rotate)
Diagnosis of the power subsystem
5
The treadmill is not regularly sliding
Diagnosis of the sliding subsystem
6
3 - Diagnosis of inclination subsystem
This procedure, whose flow chart is described in the next paragraph, takes into consideration the
possible causes of the inclination subsystem’s breakdown starting from the most probable and
listing descending order those with least probability.
Possible breakdown factors:
1. Transmission of the command from the PC to the treadmill
2. Fuse on filter board and control board
3. End run micro-switches
4. Power board
5. Elevation motor

Service Manual 800 series Rev. 1/01.07.2019
3
Medisoft RAM Italia S.r.l. - All rights reserved
not OK
Not OK
not OK
not OK
OK
not OK
OK
not OK
OK
not OK
OK
OK
OK
not OK
OK
Not OK
OK
not OK
OK
OK
OK
not OK
OK
not OK
3.1 - Flow chart for the diagnosis of inclination subsystem
3.5 Substitution RS 232
cable
Stop
Start
3.2 Transmission
check
3.3 Connection check
Stop
3.4 RS 232 cable check
3.6 Inclination check
3.9 Control board
imput check
3.10 Filter board and
control board fuse check
3.12 Test of the limit
switch
Send the treadmill to
the manufacturer
3.8 Removal of the hood
3.7 Treadmill check
Stop
3.11 Test control board
and elevation motor
elevaz.
3.13 Test of 0% limit
switch
3.14 Substitution of the
control board
3.15 Substitution of the
elevation motor

Service Manual 800 series Rev. 1/01.07.2019
4
Medisoft RAM Italia S.r.l. - All rights reserved
3.2 - Transmission check
The trial consists in verifying whether the command (of elevation or of rotation) correctly reaches
the treadmill. It requires the use of software installed on a personal computer in order to send the
command to the treadmill.
If the transmission of the command does not work, the software should show an error message.
Consequently, if the error message shows on the PC, it means that the transmission check is not
OK. Should this not occur, the transmission check should be considered OK.
Note: Unfortunately not all software on all PC’s have the possibility of determining whether the
command reached the treadmill in the correct manner, and therefore in these cases, one should
consider the check not OK, even in the absence of error messages.
3.3 - Connection check
With this check one must verify whether the connectors of the RS232 cable are properly inserted in
the ports of the PC and of the treadmill. It requires the manual verification of the positioning of the
connectors and possible reinsertion of them.
After this verification, one must send a new command (of elevation or of rotation) to the treadmill
and verify if the treadmill responds accordingly or not. If the treadmill correctly executes the
command it means that the connection check is OK, otherwise not OK.
3.4 - RS232 cable check
This check consists of the verification that the connection cable RS232 between the PC and the
treadmill is intact. It requires a visual trial, checking that the cable has not undergone damage and
that it is immune from cuts, tears, or crushing.
If the cable appears in a good state the check of the cable RS232 is OK, otherwise not OK.
3.5 - Substitution of RS232 cable
Essential tools:
•Screwdriver
Essential replacement parts:
•RS232 serial cable
This very simple procedure requires removal of the RS232 cable disconnecting the cable from the
ports and then substituting it with a new cable.

Service Manual 800 series Rev. 1/01.07.2019
5
Medisoft RAM Italia S.r.l. - All rights reserved
3.6 - Inclination check
In order to execute the elevation check it is obviously necessary that the treadmill is under tension
and should the hood be open, it is necessary to act very carefully. To apply tension, with the cover
open, the following operations must be executed, in order:
1) block the security contact in the closet position(Fig.1)
2) connect the power plug
3) main switch to the ON position
WARNING:
At this moment, the machine is under tension and you are advised to act very carefully in order to
avoid accidental contact with the parts under tension.
The elevation check can be performed utilizing the software from the PC in order to send an
elevation command to the treadmill. If the treadmill elevates itself in the proper way after the
command is given, the elevation check is considered OK; otherwise not OK.
After the execution of the check and given that one must still work on the treadmill with the cover
open, it is recommended to remove the tension following these steps:
1) Switch OFF the treadmill
2) Unplug the power plug
3.7 - Treadmill check
Essential tools:
•RAM Serial Tester
This check is executed utilizing an instrument called a “RAM Serial Tester” (CERST), which is
able to send elevation and rotation commands to the treadmill.
The objective of this check is to verify the behaviour of the treadmill in reaction to commands
received from the “Serial Tester”.
If the treadmill exhibits the correct behaviour, one must hypothesize that the cause of the
malfunctioning is external and must be researched on the PC software that prepares the structure of
the commands, or on the system which transmits commands.
When the serial tester receives power, the display shows the velocity and inclination information.
The instrument has four buttons with the following functions:
START/STOP: activates and deactivates the treadmill
VEL/INC : moves the cursor on the display and allows the selection of velocity or inclination
UP () : increases by 0.5 the velocity or inclination
DOWN () : decreases by 0.5 the velocity or inclination
The “Serial tester” device is also provided with an RS232 plug for the connection to the treadmill.
When one presses the Start/Stop, Up or Down buttons, the serial tester sends the corresponding
command to the treadmill.

Service Manual 800 series Rev. 1/01.07.2019
6
Medisoft RAM Italia S.r.l. - All rights reserved
The reception of the command by the treadmill is signalled by a change in the symbol on the lower
right hand part of the display, that goes from > (greater) to < (lesser) or vice versa.
The check is executed by disconnecting the PC connector from the RS232 port and connecting the
serial tester. Once the serial tester and the treadmill are turned on, it is possible to utilize the various
buttons of the serial tester to send commands to the treadmill, thereby observing its behaviour.
If the treadmill acts correctly based on the commands received, the check is considered OK;
otherwise not OK.
3.8 - Removal of hood
Necessary tools:
•Philips screwdriver
•Screwdriver
In order to remove the motor hood cover, the following steps must be taken, in the order indicated:
1) Switch OFF the treadmill by main switch
2) unplug the power plug
3) unscrew the screws of the RS232 connector on the hood and remove the connector
4) remove the hood by unscrewing the four screws found at its base
5) re-insert the connector in the serial port RS232 on the motor box
Should the hood come off prior to having executed operations 1) and 2), a security switch will
interrupt the power to the treadmill. The main switch will remain under tension and the warning
light will remain on to signal the operator that it’s necessary to follow the operations listed above in
1) and 2).
3.9 –Control board input check
Tools needed:
•5,5 mm wrench
•hook or elastic restraint safety switch
Remove the protective cover of the control board placed under the engine of elevation with 5,5mm
wrench.
Attach the hook to the safety restraint (Fig.1-4), switch ON the treadmill by main switch and verify
visually that the light-emitting diodes DL1, DL2 and DL3 on the control board are lit (Fig.2-3).
If these diodes are lit, the test is OK, otherwise it is not OK.

Service Manual 800 series Rev. 1/01.07.2019
7
Medisoft RAM Italia S.r.l. - All rights reserved
Fig. 1 Fig. 2 Fig. 3
3.10 - Filter board and control board fuses check
Tools needed :
•5,5 mm wrench
•Multi meter
Remove the protective cover of main switch with 5,5mm wrench (Fig. 4).
Remove the fuse F1 (1A) from filter board (Fig. 5) and with the multi meter check if it’s good.
Remove the protective cover of the control board (Fig. 6).
Remove the fuses one at a time F1 (1A) and F2 (6.3 A) of the control board (Fig. 7) and with the
multi meter check if it's good
If the fuses are good, the test is OK, otherwise it is not OK.
Fig. 4 Fig. 5

Service Manual 800 series Rev. 1/01.07.2019
8
Medisoft RAM Italia S.r.l. - All rights reserved
Fig. 6 Fig. 7
3.11 - Test control board and elevation motor
Tools needed :
•5,5 mm wrench
•Small Screwdriver
•2 pieces of electrical cable
Remove the cover of the control board placed under the engine of elevation with 5,5mm wrench.
With the screwdriver disconnect the 2 wires on the right side of the connector J8, then make a
bridge between these terminals (Fig. 8).
Now reverse the polarity of the wires of the connector J7 (red or brown wire in the left side, black
or blue wire on the right) (Fig. 9).
Switch on the treadmill and if everything is ok, must start immediately to go up (let him go up to at
least 15/20 seconds before stopping the run by turning off the switch, because this will allow us to
comfortably make the next test).
If the treadmill upon activation of the main switch does not start, the test is not OK.
If the treadmill start immediately the test is OK.
If the test is OK, restore connections J8 (remove the bridge and reconnect the wires) and J7 (reverse
wires to restore the correct polarity), leaving the carpet about halfway elevation.

Service Manual 800 series Rev. 1/01.07.2019
9
Medisoft RAM Italia S.r.l. - All rights reserved
Fig.8 Fig.9
3.12 - Test limit switch
Tools needed :
•Small screwdriver.
•Multi meter
With the help of the multi meter, check the operation of the switches, verifiable on the J8 connector
screws (with clamp screws face view, the two on right are keyed to the switch mounted on the
beam, the two on the left correspond to the switch mounted on aluminium bracket).
These switches should be "normally closed".
If pushing the switch they open the contact the test is OK, otherwise it is not OK.
NOTE: The operation of the switches will be highlighted during the normal operation of the
treadmill by LEDs DL3 and DL4 (Fig. 10), who not lit after their activation (LED DL4 will go off
when the treadmill is at 0% elevation) (Fig. 11).
Fig.10 Fig.11

Service Manual 800 series Rev. 1/01.07.2019
10
Medisoft RAM Italia S.r.l. - All rights reserved
3.13 - Test of 0% limit switch
Tools needed :
•Line graph or meter
Measure the distance between the base plate and the tongue of the switch mounted on the beam, at
the precise moment in which the same, gradually crushing it with a finger snaps . The measure at
the point of tripping must always be 36-37 mm (Fig. 12).
If this measure were to be different from that shown, bend the metal rod in order to restore the
correct measure.
Fig.12
3.14 –Substitution of Control Board
Tools needed :
•5,5 mm wrench
•5,0 mm wrench
Remove the cover of the control board situated below the elevation motor, with 5,5mm wrench.
Disconnect all the connectors, pulling them upward.
With the 5 mm wrench, unscrew the small fixing columns and substitute the board.

Service Manual 800 series Rev. 1/01.07.2019
11
Medisoft RAM Italia S.r.l. - All rights reserved
3.15 - Inclination actuator screw lubrication
Tools needed:
•10mm Allen key
•19mm wrench
•Grease
Get the treadmill up to 23,5 of inclination and folds the treadmill on his hip (fig.13).
With the 19mm wrench and the 10mm Allen key unscrew the stem fixing the actuator (fig.14).
Unscrew and remove the actuator’s stem and use the grease for lubricate it. (fig.15-16).
Cleaning the actuator screw, insert and fasten the stem on the screw.
Grease the screw and finally proceed with mounting and fixing the actuator at the cart. (Fig.17).
During this operation pay attention at the correct position of the limit switch 25%.
Fig.13 Fig.14
Fig.15 Fig.16
Fig.17

Service Manual 800 series Rev. 1/01.07.2019
12
Medisoft RAM Italia S.r.l. - All rights reserved
3.16 –Substitution of Elevation motor
Tools needed :
•5,5 mm wrench
•8 - 10mm Allen key
•17 - 19mm wrench
To do this you must pick up the treadmill and stand on a table, leaving free the part where are the
fixing screws.
Remove the protective cover of the control board placed under the engine of elevation, with 5,5mm
wrench and unplug the connectors J3 and J7.
WARNING: At a time when it is removed the screw that fixing the elevation motor to
the cart, the gas spring mounted in parallel to the engine, push the cart to the maximum excursion
with great force.
Ensure that there is enough space in this movement and especially keep your hands away until the
system is stopped.
At a time when it is removed the screw that fixing the elevation motor to the cart, the gas spring
mounted in parallel to the engine, push the cart to the maximum excursion with great force.
Ensure that there is enough space in this movement and especially keep your hands away until the
system is stopped.
With the Allen wrench 8-10 and 17-19 wrench, loosen the screw that fixing the elevation motor to
the cart and then, bearing in mind the earlier warning, remove the screw(Fig.18).
After this operation, we can remove the screw fixing in the upper support to replace the
actuator(Fig.19).
Fig.18 Fig.19

Service Manual 800 series Rev. 1/01.07.2019
13
Medisoft RAM Italia S.r.l. - All rights reserved
4 - Diagnosis of velocity subsystem
CAUTION:
Each time the machine is switch off (by pressing the emergency stop button, or switch OFF the
main switch) an electrical safety system prevents the immediate reboot, so you must leave the
machine off for at least 30 seconds to restore full functionality.
This procedure, whose flow chart is described in the next paragraph, considers the possible causes
of malfunctioning of the velocity subsystem, beginning with the most probable and listing in
descending order the least probable causes.
Possible factors of malfunction:
1. Transmission of the command from the PC to the treadmill
2. Inverter
3. Control board fuse
4. Control board
5. Velocity motor

Service Manual 800 series Rev. 1/01.07.2019
14
Medisoft RAM Italia S.r.l. - All rights reserved
not OK
not OK
OK
not OK
OK
not OK
not OK
OK
OK
OK
Not OK
not OK
not OK
OK
not OK
OK
OK
OK
OK
not OK
OK
not OK
4.1 - Flow chart for diagnosis of velocity subsystem
3.5 Substitution of RS
232 cable
Start
3.2 Transmission test
3.3 Connection check
Stop
3.4 RS 232 cable check
4.2 Velocity test
4.3 Inverter check
3.8 Removal of the
hood
Stop
3.7 Treadmill check
Stop
4.4 Control board fuse
check
4.9 Substitution of the
velocity motor
4.2 Velocity test
Stop
Send the treadmill
to the manufacturer
4.5 Test signal control
inverter
4.6 Substitution of the
control board
4.7 Test alimentation
inverterr
4.8 Substitution of the
inverter
Stop
4.2 Velocity check

Service Manual 800 series Rev. 1/01.07.2019
15
Medisoft RAM Italia S.r.l. - All rights reserved
4.2 - Velocity check
In order to execute the velocity check the treadmill must obviously be under tension, and should the
hood be open, one must be extremely careful. To apply tension with the hood open, the following
steps should be followed in the following order:
1) block the security switch in the closed position
2) connect the power plug
3) switch ON the main switch
WARNING:
From this moment on, the machine is under tension, and you are advised to be extremely careful
in order to avoid accidental contact with the parts under tension
The velocity check is performed using the PC’s software to send a movement command to the
treadmill. If the belt moves in the correct way after having received the command, the velocity
check is OK; otherwise it is NOT OK.
After executing the check, since one has to continue working on the treadmill with the cover open,
you are advised to remove the tension from the treadmill, using the following steps:
1) Switch OFF the main switch
2) unplug the power plug
4.3 - Inverter check
To execute the inverter check, you must work with the hood open and the machine under tension.
To apply tension, following the steps in the order given:
1) block the security switch in the closed position
2) connect the power plug
3) switch ON the main switch
WARNING:
From this moment on, the machine is under tension, and you are advised to be extremely careful
in order to avoid accidental contact with the parts under tension
The test is simply to control if the inverter display is lit and that the light of the "STOP" button
flashes (Fig. 20).
If the display is lit, but not flashes, switch OFF the main switch, wait 30 seconds and restart.
If the display is illuminated and the light of the "STOP" button flashes the test is OK, otherwise it
is not OK.

Service Manual 800 series Rev. 1/01.07.2019
16
Medisoft RAM Italia S.r.l. - All rights reserved
Fig.20
4.4 - Control board fuse check
Tools needed :
•5,5 mm wrench
•Multi meter
Remove the protective cover of the control board (Fig. 21).
Remove the fuse F1 (1A) from the control board (Fig. 22) and check if it's good.
If the fuse is good, the test is OK, otherwise it is not OK.
Fig.21 Fig.22
Other manuals for 800 Series
1
This manual suits for next models
3
Table of contents
Other Medisoft Treadmill manuals
Popular Treadmill manuals by other brands
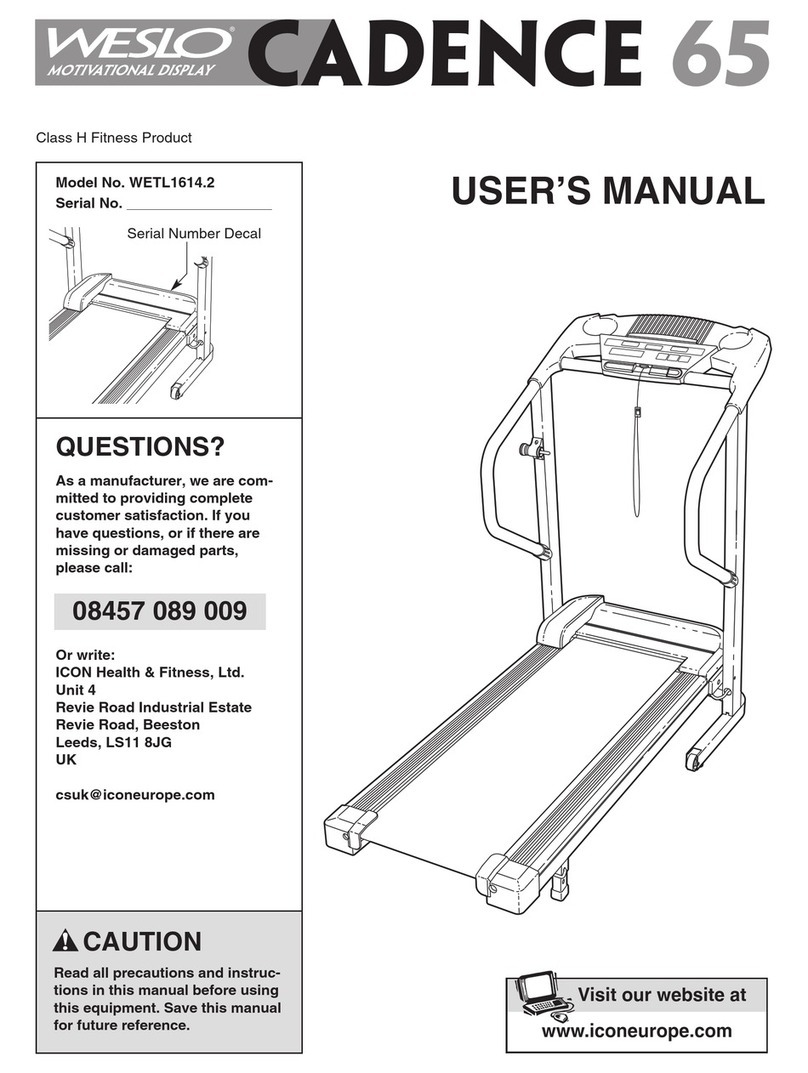
Weslo
Weslo Cadence 65 user manual
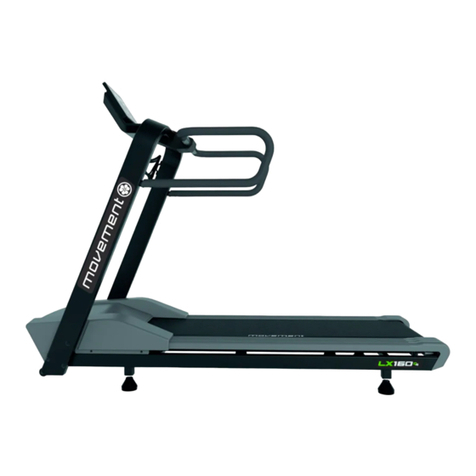
Movement
Movement LX150 instruction manual
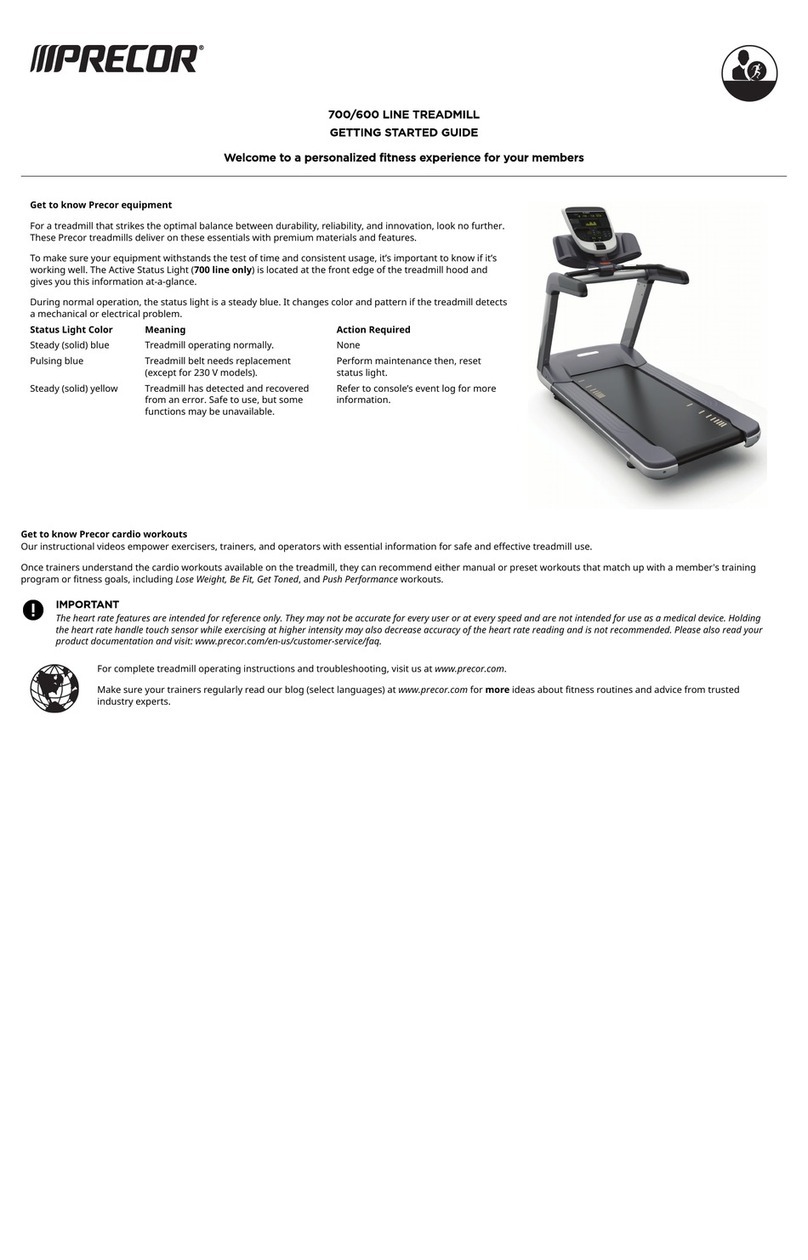
Precor
Precor Experience Series 700 Line Getting started guide

ICON Health & Fitness
ICON Health & Fitness Pro-Form City L6 user manual

h/p/cosmos
h/p/cosmos 190/65 3p Operating instructions and service manual
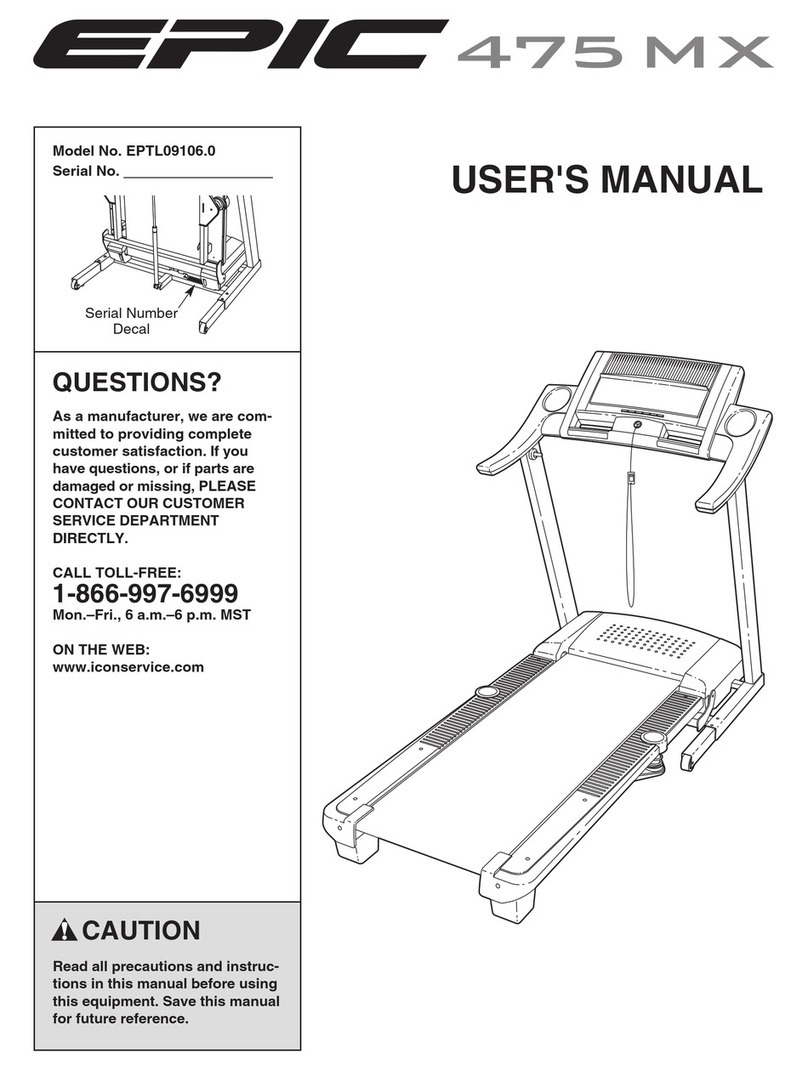
Epic
Epic EPTL09106.0 user manual