Metaltecnica 0080 Instruction manual

Metaltecnica srl
Via G. Matteotti, 151 – 28077 Prato Sesia (No) – Italy Tel. +39 0163 850497 – Fax +39 0163 851212
e-mail: mz@metaltecnicazanolo.com http: www.metaltecnicazanolo.com
INSTALLATION – OPERATION – MAINTENANCE MANUAL
ITEM 0080 KNIFE GATE VALVE WITH DISCHARGE
ISTR 0080_EN EDITION 1/2013

Metaltecnica srl pag. 2/13
CONTENTS
1. Overview
1.1 Type of products
1.2 Key of symbols
1.3 Marking and certifications
2. Handling
3. Installation
4. Gate valve actuation
5. Size - materials – operating conditions
6. Limits of use
7. Maintenance
7.1 Ordinary maintenance
7.2 Extraordinary maintenance
8. Storage
9. Decommissioning
10. List of components
1. Overview
Flanged gate valve completely made of brass. Its closing element is a stainless steel knife to which the
control stem is connected. Gate valve is opened by the stem moving vertically. The stem is actuated by
means of manual levers or hydraulic or pneumatic cylinders fitted onto the upper head.
1.1 Type of products
ITEM 0080
Knife gate valve with brass body and stainless steel knife - manual model. Available size: 4” – 6” – 8”.
ITEM 0080/0500 – ITEM 0080/0501
Knife gate valve with brass body and stainless steel knife actuated by hydraulic cylinder item 0500 (0501 for
8”), opening with oil, closing with gas spring. Available size: 4” – 6” – 8”.
ITEM 0080/0550
Knife gate valve with brass body and stainless steel knife with double-acting hydraulic cylinder item 0550.
Available size: 4” – 6” – 8”.
ITEM 0080/0570 – ITEM 8F2/0575
Knife gate valve with brass body and stainless steel knife with double-acting pneumatic cylinder item 0570
(0575 for 8”). Available size: 4” – 6” – 8”.
ITEM 0080/0571 – ITEM 0080/0576
Knife gate valve with brass body and stainless steel knife with double-acting magnetic pneumatic cylinder
item 0571 (0576 for 8”). Available size: 4” – 6” – 8”.
1.2 Key of symbols
this symbol draws attention to additional information and/or instructions to be followed in the event
that the gate valve is employed in potentially explosive atmospheres.
this symbol draws attention to important information and/or instructions to prevent serious injuries to
the operator and/or serious damages to the system and the environment.

Metaltecnica srl pag. 3/13
1.3 Marking and certifications
1.3.1 Pressure Equipment Directive (97/23/CE)
Gate valves are considered pressure vessels. Therefore they are subject to the PED (97/23/EC). PED
equates valves to pipes. The applicable compliance assessment scheme is Table No 9, “pipe as per art. 3,
paragraph 1, letter c, point 2, second dash”. It refers to “pipes for liquids having a vapour pressure at the
maximum allowable temperature of not more than 0.5 bars above normal atmospheric pressure (1013
mbars), within the limits below:
group 2 fluids, when PS is more than 10 bars, DN (NPS) is more than 200 and PS × DN (NPS) is more than
5,000 bars.
In particular, these gate valves are subject to Article 3, Section 3, thus they do not require CE marking.
1.3.2 ATEX Directive (94/9/CE)
Gate valves series 0080 meet the requirements of Directive 94/9/EC for protection against explosion. The
reference framework is the following:
EN 13463-1 “Non-electrical equipment for use in potentially explosive atmospheres – basic method and
requirements”
EN 13463-5 “Non-electrical equipment for use in potentially explosive atmospheres – protection by
constructional safety”
Atex gate valves bear the following marking:
II 2 G/D TX
1370 – n.00000000
T.F. 0080
Thus gate valves are:
certified for use on equipment of Group II, category 2
certified for use in the GAS zones 1 and 2 and in the DUST zones 21 and 22 (dust)
Temperature class: TX resulting from the room temperature or the temperature of the operating fluid
because the cylinders are not provided with internal heat sources.
The 1370 number identifies the Notified Body (Bureau Veritas Italia S.p.A.) the T.F. 0080 Metaltecnica
technical file has been filed with; the following number is the registration receipt issued by the Notified Body.
1.3.3 Machinery Directive (2006/42/EC)
Gate valves with hydraulic or pneumatic actuators are considered machinery, thus they are subject to
Directive 2006/42/EC. Gate valves meet the minimum safety requirements required by the directive.

Metaltecnica srl pag. 4/13
2. Handling
The indications below must be followed when handling the products:
Use personal protective equipment (gloves, safety glasses, safety shoes, etc.)
handle gate valves that weigh more than 20 Kg by means of cranes, hoists or forklifts with the proper
slings. If necessary, use the proper eyebolts screwed into the threaded holes on machine body.
Never handle the gate valve using the plastic protection casing
Handle the gate valves with care to prevent impacts and damages. Handle taking care not to cause any
impacts or damages to the gate valve.
3. Installation
The indications below must be followed during installation:
handle the gate valves complying with the instructions under 2 “Handling”
check the valve for overall integrity and internal part cleaning
check that there is the proper space between the connecting flanges of the two pipe sections. Also check
that the flanges are parallel and properly aligned. Otherwise, during assembly gate valve body may
suffer heavy stresses that would negatively affect gate valve proper operation.
During installation, gate valves must feature the proper support. The two pipe sections must be properly
supported, too, in order to prevent gate valve body from suffering system stress.
Check gate valve proper orientation considering the flow direction. Gate valve body is marked with an
arrow indicating flow direction (or the direction of the higher pressure)
Check the position of installation considering that, if possible, it would be better to install the gate valve
vertically on horizontal pipes. However, the gate valve can be installed inclined on horizontal pipes
(please install in this position only if it is strictly necessary) or horizontal on vertical pipes. For this
installation users should better use gate valves with discharge inclined 45° (right or left) with respect to
the vertical axis. The gate valve can be installed horizontally on vertical pipes; In this last case, a
properly sized supporting frame must be provided for the gate valve and/or the hydraulic or pneumatic
actuators. Any other different position of installation may require specific measures to be undertaken and
may cause use restrictions. Therefore, these cases are to be assessed with Metaltecnica Technical
Department.
Tab.1 diagram of the position of installation
Vertical gate valve on horizontal pipes.
The two pipe sections must be properly supported in
order to prevent gate valve body from suffering
system stress.
Inclined gate valve on horizontal pipes
The two pipe sections must be properly supported in
order to prevent gate valve body from suffering
system stress.

Metaltecnica srl pag. 5/13
Horizontal gate valve on vertical pipes
The two pipe sections must be properly supported in
order to prevent gate valve body from suffering
system stress.
Horizontal gate valve on vertical pipes.
Provide the proper supporting frame for the gate
valve and/or the hydraulic or pneumatic actuators.
Place the fixing screws and tighten them alternatively and uniformly as follows: tighten one screw, than
the diametrically opposed one and so on for all the screws.
Once the gate valve has been installed, check that all the accessories -such as hydraulic actuators,
pneumatic actuators, manual control levers- are properly connected.
Before gate valve commissioning, carry out some no-load opening and closing cycles checking proper
operation and seal.
Before disassembling the gate valve from the system for maintenance and/or replacement purposes,
the electrical supply and the hydraulic and pneumatic feed must be disconnected, releasing the pressure
of the lines and of the gate valve itself.
In the event that the gate valve is used in potentially explosive atmospheres, follow the indications below:
Consider whether the gate valve is suitable to the hazard zone in which it will be installed (see
Directive 99/92/EC).
Additional electric, mechanical, magnetic equipment can be applied exclusively when they are
compliant with the Atex Directive and provided with declaration of conformity and a classification suitable
to the area in which they will be installed.
Remember that the maximum surface temperature does not depend on the gate valve; it depends,
instead, on the operating conditions such as the temperature of the process fluid used, temperature of
the environment, external heat sources.
Do not disassemble the gate valve close to heat sources which, through radiation, conduction or
convection, may heat the gate valve and increase its surface temperature above the minimum ignition
temperature of the potential explosive atmosphere.
Carry out the proper gate valve grounding. Gate valves are provided with a screw on the upper head
to which an electric cable shall be connected. It will, thus, act as a conductor and discharge any possible
electrostatic currents in the system.
Before disassembling the gate valve, check that there is electrical continuity between the two pipe
sections.
During installation, maintenance and disassemble, avoid mechanical impacts, which may cause
sparks.

Metaltecnica srl pag. 6/13
4. Gate valve actuation
Supplied gate valves can be actuated as follows:
a. manual control
Gate valve manual model, complete with the fork for lever connection to stem end. The opening lever
shall be provided by the user.
b. single-acting or (items 0500 – 0501) or double-acting hydraulic actuator
Gate valves can be supplied with single- or double-acting hydraulic cylinders. As for the technical details
and conditions for operation of the hydraulic cylinders, please refer to the relevant datasheets.
Information on the installation, use and maintenance is included in manual ISTR 0500_IT. The following
points (4.1 – 4.2) describe the procedure for cylinder assembly onto the gate valve.
c. double-acting pneumatic actuator (items 0570 – 0575) and double-acting magnetic pneumatic
actuator
Gate valves can be supplied with double-acting pneumatic cylinders, both standard and magnetic. As for
the technical details and conditions for operation of the pneumatic cylinders, please refer to the relevant
datasheets. Information on the installation, use and maintenance is included in manual ISTR 0500_IT.
The following points (4.1 – 4.2) describe the procedure for cylinder assembly onto the gate valve.

Metaltecnica srl pag. 7/13
4.1 Cylinder-gate valve assembly procedure items 0500 – 0501
The procedure below shows how to assemble a cylinder item 0500 on a disassembled gate valve (pre-
arranged for cylinder assembly) and with knife provided separately.
a) Unscrew the screws (16) and remove the head (12) from the body (1)
b) Disassemble the stem-fastening clamp (8) from the knife (7) by unscrewing the screws (9) from the nuts
(17)
c) Insert the gasket (13) (only 1 ring) in head top seat (12)
d) Screw the cylinder to the head (12) by 8-10 mm.
e) Insert cylinder stem end into the T-shaped slot of the knife (7) and secure the two elements through a
fastening clamp (8) and the relevant screws (9) and nuts (17).
f) Position the gasket (10) on body upper part (1) and then insert the knife (7) manually inside the body,
pushing as much as possible.
g) Rotate the head by 90° leaving the two knife sides (7) out.
h) By using a mallet, hit the two sides of the knife alternatively until they are almost fully inserted inside the
body.
i) Rotate the head (12) and centre it with the body. Then partially tighten the screws (16) to the body (1) so
as to avoid blocking the head on the body.
j) Tighten the cylinder onto the head and avoid pressing the gasket too much. To obtain a correct sealing,
screw the cylinder manually until it touches the gasket and then rotate again by 90° with a hex wrench.
Pressing the gasket too much may block stem movement.
k) Tighten the screws (16) in several steps screwing them one by one alternatively until they stop, allowing
the components to be correctly fastened.
l) Secure the cylinder onto the head by unscrewing the ring (20) until it stops against the head.
m) Connect the cylinder to the hydraulic line and carry out some opening and closing cycles before installing
the gate valve.

Metaltecnica srl pag. 8/13
4.2 Procedure for the assembly of gate valve-cylinder items 0550 – 0570 – 0571 – 0575 – 0576
This procedure explains how to assemble the cylinders items 0550 - 0570 (and their different models) on a
disassembled gate valve (prearranged for cylinder assembly), and with knife provided separately.
a) Unscrew the screws (16) and remove the head (12) from the body (1)
b) Disassemble the stem-fastening clamp (8) from the knife (7) by unscrewing the screws (9) from the nuts
(17)
c) Insert the gasket (13) (only 1 ring) in head top seat (12)
d) Pull the stem completely out from the cylinder and then screw the cylinder to the head (12) by 8-10 mm.
e) Insert cylinder stem end into the T-shaped slot of the knife (7) and secure the two elements through a
fastening clamp (8) and the relevant screws (9) and nuts (17).
f) Put the gasket (10) on body top surface (1) and then insert the knife (7) into the body.
g) Push the head-cylinder assembly towards the body until the head fully (or almost fully) stops against the
body. During this stage, cylinder stem will return inside the cylinder, thus making this procedure easier.
h) Partially tighten the screws (16) to the body (1) so as to avoid blocking the head (12) on the body.
i) Tighten the cylinder onto the head and avoid pressing the gasket too much. To obtain a correct sealing,
screw the cylinder manually until it touches the gasket and then rotate again by 90° with a hex wrench.
Pressing the gasket too much may block stem movement.
j) Tighten the screws (16) in several steps screwing them one by one alternatively until they stop, allowing
the components to be correctly fastened.
k) Secure the cylinder onto the head by unscrewing the ring (20) until it stops against the head.
l) Connect the cylinder to the hydraulic line (item 55) or to the pneumatic line (item 57) and carry out some
opening and closing cycles before installing the gate valve.

Metaltecnica srl pag. 9/13
5. Size - materials – operating conditions
The technical information on the overall sizes, the material used and the operating conditions are available in
the company catalogue or on our web-site www.metaltecnicazanolo.com. The technical data sheets for each
item can be requested to the Metaltecnica’s technical office.
6. Limits of use
Gate valves cannot be used under pressure and temperature conditions other than those indicated in the
specific datasheets.
Gate valves cannot be used with group 1 fluids (97/23/EC DIR) or with fluids whose chemical
composition is not compatible with gate valve material.
Gate valves cannot be used in explosive atmospheres other than those indicated in paragraph 1.3.2.
7. Maintenance
The gate valve only requires few and simple maintenance procedures, which must be carried out by qualified
operators using proper personal protective equipment.
7.1 Ordinary maintenance
Periodically check that no fluid is leaking between body and head, near the upper stuffing box (manual
model), and that no oil is leaking from hydraulic actuators.
In order to avoid knife blockage, the scheduled maintenance tables shall include, at regular intervals,
some opening and closing cycles of the normally closed gate valves and of the valves actuated manually
by the lever, especially if thick fluids or liquids that tend to encrust are used.
When necessary, clean the external surfaces of gate valve and actuators using a damp cloth, thus
preventing dust from accumulating. Do not clean using compressed air, thus preventing potentially
dangerous dust from being scattered into the surrounding atmosphere.
Check monthly the external condition of the gate valve-cylinder unit and make sure that no part has
been eaten by rug. In this case, replace the eaten parts immediately.
Monthly check the integrity of the connections to the earthing terminals.
7.2 Extraordinary maintenance
Basically, extraordinary maintenance operations are those reported below:

Metaltecnica srl pag. 10/13
7.2.1 Replacement of seat gasket on gate valve body, to be carried out as follows:
a) Open the gate valve completely and remove it from the pipe.
b) Unscrew the screws fixing the head to the body and remove the whole upper unit (including head, knife
and actuator, if any).
c) Unscrew the threaded sleeve from gate valve body
d) Remove the worn out seat gasket from gate valve body.
e) Remove gate valve body with care and place it on a level surface with gasket slot facing upwards.
f) Place seat gasket on the relevant slot making sure that the rounded part faces slot bottom.
g) Press the gasket using a flat tool without sharp edges, starting from the cut side and getting step by step
to the opposite cut side. To make this operation simpler, you can cut the gasket before starting as
shown. It is important that gasket rounded part rests on slot bottom and that the external part is level and
even.
h) When this operation is completed, cut gasket excess part flush to discharge sides.
i) If necessary, slightly punch slot edges to guarantee that gasket is retained better.
j) Check that sleeve gaskets are intact and, if necessary, replace them by following the procedure under
7.2.2.
k) Screw the sleeve to gate valve body
l) Put the upper assembly into place again (it includes head, knife and actuator) and replace the sealing
gasket between body and head, if necessary.
m) Secure the head onto gate valve body
n) Before operating gate valve again, carry out some opening and closing cycles checking proper seal.

Metaltecnica srl pag. 11/13
7.2.2 Replacement of the seat gasket (sealing ring) on the sleeve to be carried out as follows:
a) Open the gate valve completely and remove it from the pipe.
b) Unscrew the screws fixing the head to the body.
c) Remove upper assembly, including head, knife and actuator, if any.
d) Unscrew the threaded sleeve from gate valve body.
e) Remove worn out gaskets.
a) Carefully clean the threaded sleeve and place it on a level surface with gasket slot facing upwards.
b) Insert the o-ring in the deeper inner slot.
c) Place seat gasket on the relevant slot making sure that the rounded part faces slot upper part.
d) Force the seat gasket by slightly pressing it on 4 equally distant points so that it enters the slot by
approximately 0.5 mm, thus ensuring that it remains into place.
e) Then, press the gasket by using a flat tool without sharp edges until it is completely inserted into the slot.
During this stage, make sure not to damage seat gasket rounded part; users should better using a
presser with a large surface, so as to press a larger gasket part.
f) Insert the o-ring in the relevant slot on the sleeve.
g) Screw the threaded sleeve until it stops against gate valve body.
h) Put the upper assembly into place again (it includes head, knife and actuator) and replace the sealing
gasket between body and head, if necessary.
i) Secure the head onto gate valve body
j) Before operating gate valve again, carry out some opening and closing cycles checking the proper seal.

Metaltecnica srl pag. 12/13
7.2.3 Kit gaskets replacement procedure for pneumatic and hydraulic actuators
For hydraulic and pneumatic actuators maintenance, please refer to the installation - use - maintenance
manual ISTR 0500_IT
8. Storage
When storing before installing or in the event of long-term storage, it is recommended to store the gate
valves in a cool (maximum 40°C), well-ventilated place, away from direct sunlight or other heat sources and
keep it dry.
9. Decommissioning
Before being decommissioned, the gate valves must be disassembled from the system following the
procedure below:
open the gate valve and empty the pipes on which it is assembled.
cut off any power supply, pneumatic or hydraulic feed
Disassemble the gate valve by using suitable personal protective equipment (gloves, safety glasses,
safety shoes, etc.)
Clean the gate valve in order to avoid leaks of the treated fluid which may cause damages to persons,
property and environment. For the same reason, the hydraulic oil of the hydraulic cylinder, if any, must
be carefully removed.
After the cleaning, recyclable materials (metal parts, plastic parts) must be separated from special waste
(P.T.F.E. gaskets, rubber parts, etc.) according to the local existing law.
The scrapping of assembled and not cleaned gate valves can cause emissions and damages to
the environment.

Metaltecnica srl pag. 13/13
10. List of components
Below is an example of general part list. It refers to item 0080. The exploded diagrams of the spare parts of
all gate valve types and of the relevant actuators can be requested from Metaltecnica Technical Department.
Pos. Name Pos. Name
1 Body 10 Gasket
2 Seat ring 11 Stem
3 O-ring 12 Head
4 O-ring 13 Gasket
5 Screwed pipe coupling 14 Gland
6 o-ring 7 15 Fork
7 Knife 16 TCEI screw / socket head cap screw
8 Clamp 17 Self-locking nut
9 Screw
This manual suits for next models
3
Table of contents
Popular Control Unit manuals by other brands
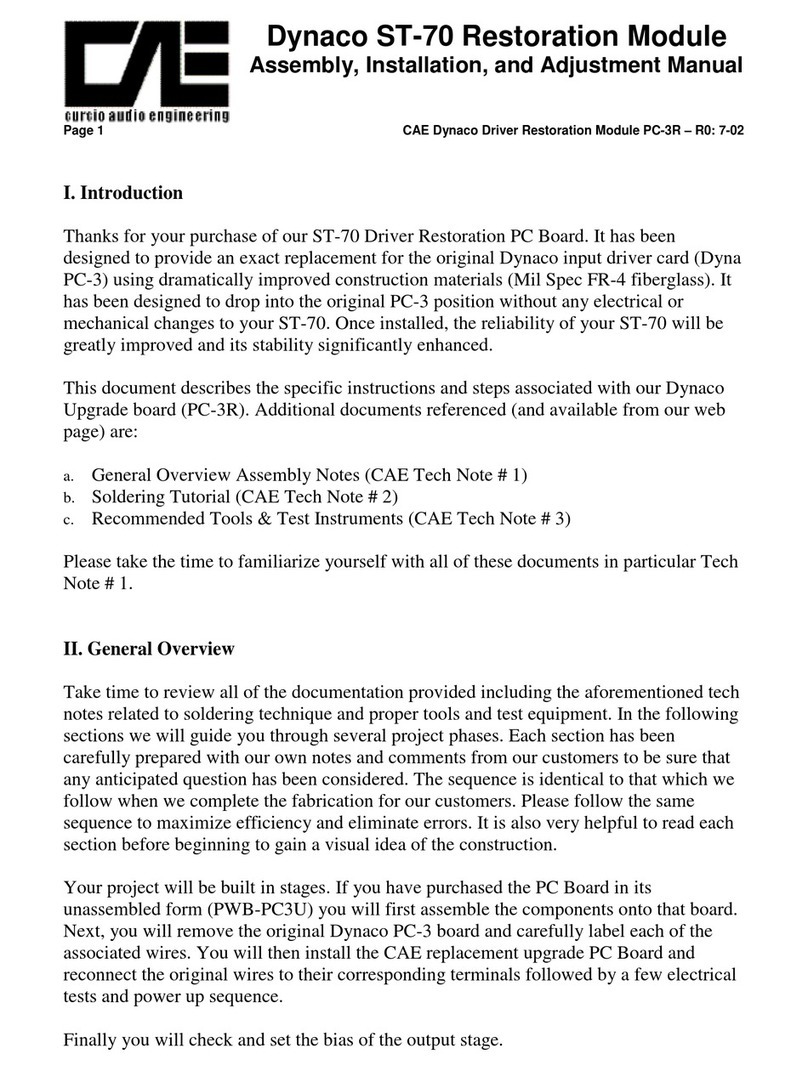
CAE
CAE Dynaco ST-70 Restoration Module Assembly, installation and adjustment Manual
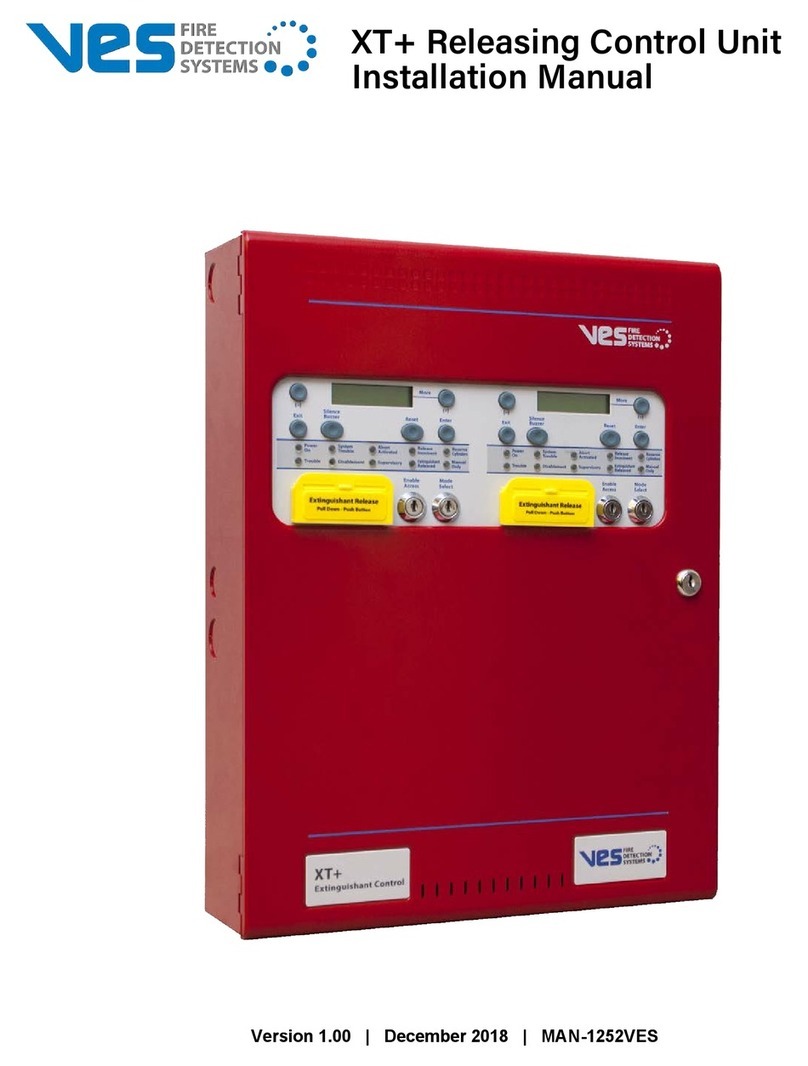
VES
VES XT+ installation manual
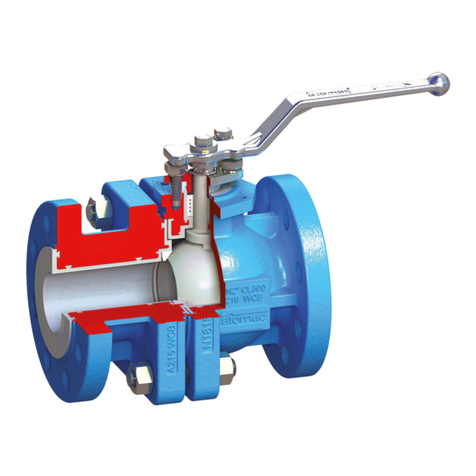
Flowserve
Flowserve AKH2.2 Technical manual

Bray
Bray 740 Series Installation, operation and maintenance manual
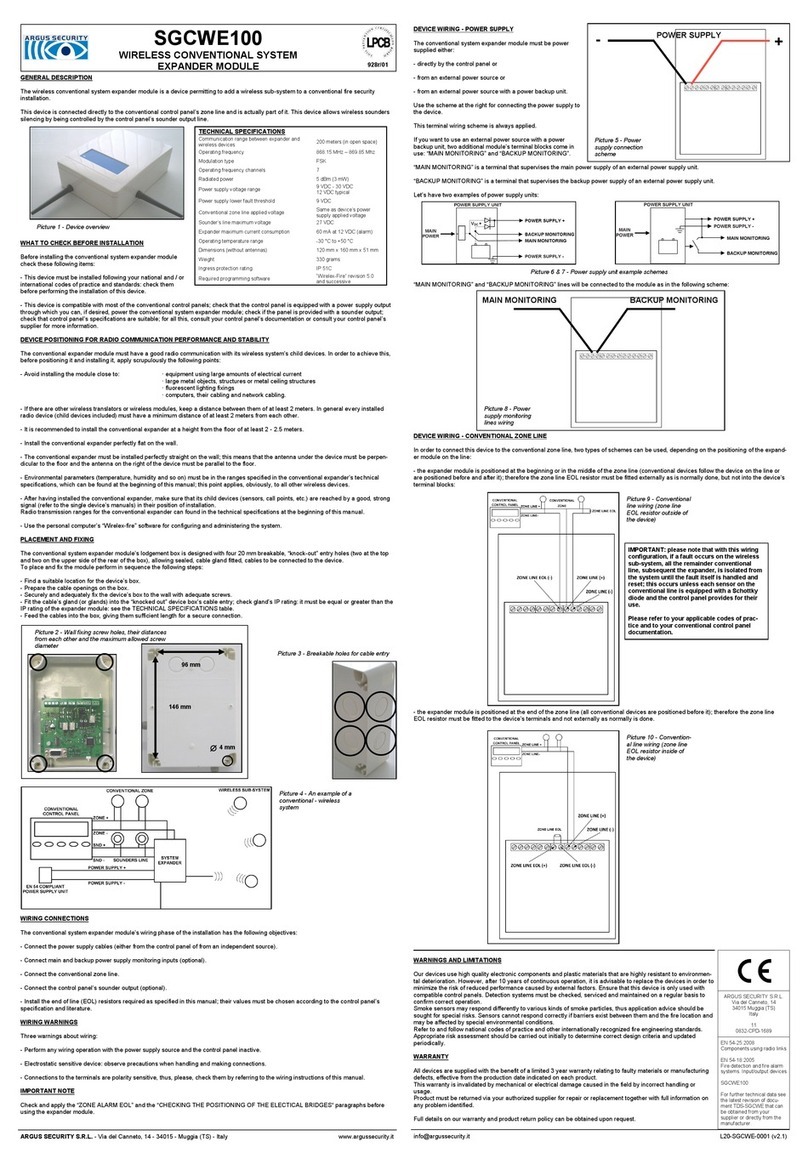
Argus Security
Argus Security SGCWE100 Quick user guide
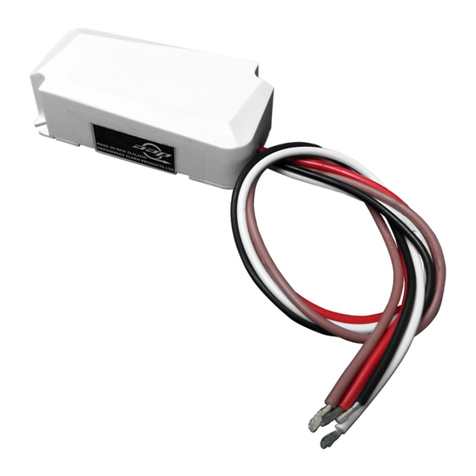
AAP
AAP TRX Mains Connection diagram