Meteoclima Ultrasonic Anemometer 2D User manual

THE WORLD OF WEATHER DATA - THE WORLD OF WEATHER DATA - THE WORLD OF WEATHER DATA
Instruction for Use
021537/06/10
Ultrasonic Anemometer 2D
451301
from software version V3.09 Status: 05/2009
Feingerätebau K. Fischer GmbH
Venusberger Str.24 09430 Drebach Germany
Phone +49 37341 487 0 Fax +49 37341 487 30
www.meteoclima.de info@meteoclima.de

2-2021537/06/10
Contents
1Application....................................................................................................................6
1.1 Mode of operation .............................................................................................................7
2Measuring principle.......................................................................................................8
2.1 Wind velocity and direction................................................................................................8
2.2 Acoustic virtual temperature..............................................................................................8
2.2.1 Correction of the acoustic-virtual temperature from Influence of air humidity..............9
3Preparation for operation............................................................................................12
3.1 Selection of installation site.............................................................................................12
3.2 Installation of anemometer..............................................................................................13
3.2.1 Device to Refuse Birds (optionally)...........................................................................13
3.3 Alignment to north...........................................................................................................14
3.4 Electrical Installation for Ultrasonic Anemometer with Connector....................................15
3.4.1 Cables, Cable preparation, Coupling socket Installation ...........................................15
3.4.2 Connector Pin Assignment (Examples of Function)..................................................16
3.5 Electrical Installation for Ultrasonic Anemometer with Screwed Cable Gland..................17
3.5.1 Cable Pin Assignment (Examples of function) ..........................................................17
4Maintenance...............................................................................................................18
5Calibration ..................................................................................................................18
6Warranty.....................................................................................................................18
7Functional description.................................................................................................19
7.1 Serial communication......................................................................................................19
7.1.1 Duplex mode.............................................................................................................19
7.1.2 Response Delay........................................................................................................20
7.1.3 General telegram structure.......................................................................................20
7.1.4 Return values of ULTRASONIC................................................................................21
7.1.5 Access Mode ............................................................................................................21
7.1.6 Baud rate..................................................................................................................23
7.1.7 Instrument ID............................................................................................................23
7.1.8 Bus mode..................................................................................................................24
7.2 Analogue and digital I/O..................................................................................................24
7.2.1 Analog inputs............................................................................................................24
7.2.2 Analogue outputs......................................................................................................25
7.2.3 Scaling of analog wind velocity .................................................................................26
7.2.4 Scaling of analog wind direction................................................................................26
7.2.5 Correction to north....................................................................................................26
7.3 Data acquisition...............................................................................................................27
7.3.1 Instantaneous values and output of raw measured values........................................28
7.3.2 Averaging..................................................................................................................28
7.3.3 Standard deviation....................................................................................................29
7.3.4 Measurement in Burst Mode.....................................................................................30

3-3021537/06/10
7.3.5 Gust Acquisition........................................................................................................33
7.4 Serial data output ............................................................................................................34
7.4.1 Data enquiry..............................................................................................................34
7.4.2 Independent telegram output ....................................................................................34
7.4.3 Fixed telegram formats .............................................................................................35
7.4.4 Generation of check sum..........................................................................................35
7.4.4.1 Type 1 ................................................................................................................36
7.4.4.2 Type 2 ................................................................................................................36
7.4.5 User-specific telegram ..............................................................................................36
7.4.5.1 Generation of a new, user-specific telegram.......................................................36
7.4.5.2 Attachment of definitions ....................................................................................37
7.4.5.3 Deletion of definitions .........................................................................................37
7.4.5.4 Storage of definitions..........................................................................................38
7.4.5.5 Available measured values and data formats .....................................................38
7.4.5.6 Data formats.......................................................................................................40
7.4.6 Status information.....................................................................................................43
7.4.6.1 Extended status information ...............................................................................44
7.4.6.2 THIES status ......................................................................................................45
7.4.6.3 Status Information in the Bayern Hessen Format ..............................................45
7.4.6.4 Status information in telegram 9.........................................................................46
7.5 Behavior of Instrument under extreme Conditions of Measurement Value Acquisition....46
7.5.1 In the event of error:..................................................................................................47
7.5.2 Behaviour of analog outputs......................................................................................47
7.5.3 Behaviour of telegram output....................................................................................47
7.6 Heating control................................................................................................................47
7.7 Instruments with Housing Heating (4.382x.4x.xxx) ..........................................................48
7.8 Output of all system parameters......................................................................................48
7.9 Enquiry about software version........................................................................................49
7.10 Operating Hours Counter.................................................................................................49
7.11 Storing of System Events ................................................................................................49
7.12 Bayern Hessen mode......................................................................................................50
7.13 Forcing a restart..............................................................................................................51
7.14 Energy-saving mode........................................................................................................51
7.15 Bootloader.......................................................................................................................51
7.15.1 X-Modem Boot loader ...............................................................................................52
7.16 Fast boot .........................................................................................................................53
7.17 Plausibility........................................................................................................................53
7.18 Online help......................................................................................................................53
8Configuration of ultrasonic anemometer by customer................................................54
8.1 Storing of Parameter Data Set.........................................................................................54
8.2 Establishing of Delivery Condition....................................................................................54
8.3 Administration of User Information ..................................................................................55
9List of Commands.......................................................................................................56

4-4021537/06/10
10 Command and description.......................................................................................58
11 Appendix 1 Predefined data telegrams....................................................................87
11.1 Telegram 1 VD...............................................................................................................87
11.2 Telegram 2 VDT.............................................................................................................87
11.3 Teleg ram 3 V4DT..........................................................................................................88
11.4 Telegram 4 NMEA..........................................................................................................88
11.5 Telegram 5 VDT, Standard deviation .............................................................................89
11.6 Telegram 7 Vx, Vy, VT...................................................................................................90
11.7 Telegram 8 VD Variant 1................................................................................................90
11.8 Telegram 9 VDT Variant 1..............................................................................................91
11.9 Telegram 11 VDT Variant 2.............................................................................................91
11.10 Telegram 12 Scientific Telegram....................................................................................92
11.11 Telegram 13 VDT Variant 3.............................................................................................92
12 Technical data .........................................................................................................94
13 Dimension Drawing..................................................................................................96
14 Accessories (available as optional features)............................................................98
15 EC-Declaration of Conformity..................................................................................99
Fig.
Figure 1: Device to refuse birds ...................................................................................................13
Figure 2: Coupling socket installation...........................................................................................15
Table
Table 1: Restrictions in full and half duplex mode ........................................................................20
Table 2: Return values with incorrect interpretation of command.................................................21
Table 3: Access key for different command levels .......................................................................22
Table 4: Config. of analog outputs WV/RXD-and WD/RXD+ with parameters AN and SC..........25
Table 5: Assignment of wind direction with 0-540°angle range (as per VDI 3786 sheet 2)..........27
Table 6: List of predefined data telegrams...................................................................................35
Table 7: Measured values and data types for user-specific telegram...........................................39
Table 8: Adjustment of averaging periods with parameter AV......................................................63
Table 9: Measuring instrument addresses in Bayern Hessen command interpreter.....................64
Table 10: List of baud rates with telegram BR..............................................................................65
Table 11: List of baud rates with telegram BX..............................................................................66
Table 12: Pulse control factor with switch-on of heating...............................................................73
Table 13: Conditions for software-controlled switching of heating................................................73
Table 14: Conversion factors between different wind velocities....................................................77
Table 15: Configuration of analog outputs WV/RXD-and WD/RXD+ with parameters AN and SC79

5-5021537/06/10
Patent
European Patent Specification Patent No.: EP 1 448 966 B1
United States Patent Patent No.: US 7,149,151 B2
Operating Instructions
These operating instructions describe all possible applications and settings of the instrument. The
Ultrasonic Anemometer 2D is factory-set.Identification for the factory setting derives from the
order No. and the respective "Factory Setting"
Order number and Setting
see supplementary sheet
"Factory Setting"
With these detailed operating instructions and via the serial interface of the Ultrasonic Anemometer
2 D it is possible for the user to adapt the factory-settings to his own requirements.

6-6021537/06/10
1Application
The Ultrasonic Anemometer 2D is used to detect the horizontal components of wind velocity
and wind direction as well as the virtual temperature in 2 dimensions.
More than 35 different measurement values are available, such as:
•Orthogonal wind velocity vectors (X-and Y-path)
•Scalar wind velocity
•Wind direction
•Acoustic-virtual temperature [°C]
•Acoustic-virtual temperature of the orthogonal measurement path (X-and Y-path) [°C]
•Standard deviation of the vectorial wind velocity (X and-path)
•Standard deviation of the scalar wind velocity
•Standard deviation of the wind direction
•Standard deviation of the acoustic-virtual temperature
•Wind velocity of the gust acc. to WMO
•Wind direction of the gust acc. to WMO
•Measurement in Burst mode with trigger via plug PIN and recording of an analogue input
value.
•More measuring values please refer to chapter 7.4.5.5 (measurement values and data
formats available)
The instrument is especially suited for application in the fields of
•Meteorology
•Climatology
•Regenerative energy, wind power plants
•Traffic engineering, aviation and navigation
•Reconstruction of pollutant dispersal
•Wind alarm devices, building construction and building safety
•Indoor flow measurement
•and in alpine field of application
•as acoustic thermometer

7-7021537/06/10
Due to the measuring principle the instrument is ideal for inertia-free measurement of gusts and
peak values.
The level of accuracy achieved when measuring the air temperature (virtual temperature)
surpasses that of classical methods, in which the temperature sensors are used with weather and
radiation protection, following correction of the influence of damp occurring with certain weather
situations.
Output of the measured values can be either digital and / or analogue.
Digital output: An RS485/422 is available for serial communication. It can be operated in full or half-
mode. For the output of measured values there are a number of predefined telegrams or a user-
defined telegram (e.g. WV, WD, virtual temp., standard deviation, status information, NMEA etc.).
Analogue outputs: Wind velocity and direction as well as acoustic-virtual temperature are output
either as a current or voltage signal. Individual measuring range scaling of the analogue outputs for
WV and WD are selectable.
The analogue outputs can be switched alternatively and individually as analogue voltage inputs
(max. 3). These measuring values are output via the serial interface within a user-defined telegram.
The serial or analogue output of the data is either as an instantaneous value or as a gliding mean.
The sensor arms are automatically heated if necessary with critical ambient temperatures. This
also ensures functionality with snowfall and sleet and minimises the risk of malfunctions due to
icing-up
Thanks to additional ultrasonic transformer heating systems the model No.4.382x.3x.xxx
particularly suitable for difficult conditions in high mountain areas or other critical measuring
locations where icing is to be expected.
Thanks to additional ultrasonic transformer heating systems and additionally integrated housing
heater the model No.4.382x.4x.xxx particularly suitable for extreme conditions in high mountain
areas or other critical measuring locations where icing is to be expected.
1.1 Mode of operation
The Ultrasonic Anemometer 2D consists of 4 ultrasonic transformers, in pairs of two facing each
other at a distance of 200 mm. The two resulting measurement paths are vertical to each other.
The transformers function both as acoustic transmitters and receivers.
The electronic control system is used to select the respective measurement path and its measuring
direction. When a measurement starts, a sequence of 4 individual measurements is performed in
all 4 directions of the measurement paths at maximum speed.
The measuring directions (sound propagation directions) rotate clockwise, first from south to north,
then from west to east, from north to south and finally from east to west.
The mean values are worked out from the 4 individual measurements of the path directions and
used to make further calculations.
The time required for a measuring sequence is approx. 2.5 msec at +20°C at the maximum
measuring speed.

8-8021537/06/10
2Measuring principle
2.1 Wind velocity and direction
The speed of propagation of the sound in calm air is superposed by the velocity components of an
air flow in the direction of the wind.
A wind velocity component in the propagation direction of the sound supports the speed of
propagation; i.e. it increases it while a wind velocity component against the propagation direction
reduces the speed of propagation.
The propagation speed resulting from superposition leads to different propagation times of the
sound at different wind velocities and directions over a fixed measurement path.
As the speed of sound greatly depends on the temperature of the air, the propagation time of the
sound is measured on each of the two measurement paths in both directions. This rules out the
influence of temperature on the measurement result.
By combining the two measuring paths which are at right angles to each other, the measurement
results of the sum and the angle of the wind velocity vector are obtained in the form of rectangular
components.
After the rectangular velocity components have been measured, they are then converted to polar
coordinates by the digital-signal-processor of the anemometer and output as a sum and angle of
wind velocity.
2.2 Acoustic virtual temperature
The thermodynamic interrelationship between the propagation velocity of sound and the absolute
temperature of the air is defined by a root function. The sound velocity is also more or less
independent of the air pressure and only depends on the absolute air humidity to a minor extent.
This physical interrelationship between sound velocity and temperature is ideal when measuring
the air temperature as long as the chemical composition is known and constant.
The levels of gases in the atmosphere are constant and with the exception of water vapour content
vary at most by a few 100ppm (CO2) even over lengthy periods.
Determination of gas temperature via its sound velocity is performed directly from measurement of
Wind from NNE
Y -component
X -component
E
W

9-9021537/06/10
its physical properties without the step of thermal coupling of this gas to a sensor which would
otherwise be necessary.
The advantages of this measuring method are firstly its inertia-free reaction to the actual gas
temperature, and secondly, the avoidance of measuring errors such as those that occur for
example when a solid-state temperature sensor is heated by radiation or cooled through the
evaporation of water on the sensor.
Many comparative tests between different weather and thermal radiation shield housings show the
indirect effect of the above-mentioned sources of measurement errors on the temperature sensor.
[1]
At sites with a high likelihood of icing-up ultrasonic anemometers are also used already as acoustic
thermometers, as classical temperature sensors are no longer vented with weather and thermal
radiation shield housings after icing-up. Due to the deteriorated thermal coupling to the outer world
they response only extremely time-delayed, or due to the missing discharge of the own power
dissipation the measured temperature is too high. [2]
2.2.1 Correction of the acoustic-virtual temperature from Influence of air humidity
Given the dependence, albeit low, of the sound propagation velocity on the air humidity level, the
"acoustic virtual temperature" relates to dry air without any water vapour content.
The deviation of the measured "acoustic temperature" from the real air temperature shows linear
dependence on the absolute humidity level of the air.
The amount of water vapour in the air proportionately increases the velocity of sound as H2O
molecules only have around half the mass of the other air molecules (O2and N2).
The velocity of sound however only increases with the molar mass fraction of water vapour in the
air to a disproportionately low degree.
The reason for this is the lower mean translatory velocity of the water vapour molecules in
comparison with the other air molecules. With the more complex H2O molecules greater degrees of
freedom of motion are possible than with the more simple O2and N2 molecules so that the total
energy content (temperature) is divided between the possible degrees of freedom of translation
and rotation as kinetic energy.
O2and N2 molecules have 3 degrees of freedom of translation and 2 degrees of freedom of
rotation, and H2O molecules 3 degrees of freedom of translation and 3 degrees of freedom of
rotation.
The adiabatic exponent
γ
of each gas is determined by the total number of degrees of freedom
according to the following interrelationship:
n
2
1+=
γ
The adiabatic exponents measured for dry air d
γ
and water vapour v
γ
are:
399463.1=
d
γ
and 331.1=
v
γ
The dependence of the acoustic virtual temperature
Tv
on the water vapour content of the air can
be calculated using the following relationship:
•
−−
•
−+•= e
M
M
p
e
M
M
TtTv
d
v
d
v
d
v
1
1
γ
γ
[1]

10 -10 021537/06/10
where
Tt
is the acoustic virtual temperature of dry air and v
Mthe molar mass of water vapour,
and d
Mdescribes the molar mass of dry air. The ratios d
v
M
Mwith the value 0.621978 and d
v
γ
γ
with
the value 0.95108 can be included in the equation as fixed constants. [3]
The ratio p
edescribes the water vapour pressure divided by the air pressure. , corrected by the
effect of the water vapour pressure on the air pressure..
The vapour pressure
e
can be calculated according to the relationship s
e
RH
e•=
100
where
RH
stands for relative humidity and s
efor saturation vapour pressure.
The saturation vapour pressure is a function of temperature and can be calculated according to the
Magnus formula with coefficient according to Sonntag
( )
TKT
sehPaTe +
•
•= 12.243 62.17
112.6 [4]
with the temperature of interest where T must be specified in °C.
The following simplified expression with T as the temperature in Kelvin results for calculation of the
acoustic virtual temperature measured with humid air:
[ ]
•−
•+•= ep e
TtTv 378022,0
329102,01
The correcting effect of the water vapour pressure on the air pressure is relatively low, and is, for
ex., approx. 2,8 % with + 40 °C and 100 % relative humidity.
The water vapour pressures to be expected in the nature are clearly below. The error with the
simplification of the formalism can consequently almost be neglected.
Simplified formula:
•+•= p
e
TtTv 329,01
Example:
With an air temperature of +20°C, relative humidity of 100% and an air pressure of 1000hPa an
acoustic virtual temperature of 22.25°C is calculated fro m the sound velocity.
The acoustic virtual temperature is therefore 2.25°C above the actual air temperature and can be
corrected accordingly using the above equation if the humidity level of the air is known, e.g. relative
humidity and the air pressure.
Calibrated measurements performed in the climatic exposure test cabinet with different
temperatures as parameters and relative humidity levels between 10% and 90% have shown that
the factor in the above equation should be nearer 0.30.
•+•= p
e
TtTv 30.01
If required to improve accuracy of the calculated real air temperature, one or more iteration steps
could be performed to determine the accurate saturation vapour pressure when using the
measured relative humidity and the measured acoustic temperature as corrective variables as the
real air temperature (corrected acoustic virtual-temperature) is necessary for the calculation of the
saturation vapour pressure.

11 -11 021537/06/10
References:
[1] Lanzinger, Eckhard (Deutscher Wetterdienst), Langmack, Hans (Universität Hamburg):
Measuring air temperature by using an ultrasonic anemometer
[2] Musa, Mark (Meteo Swiss), Tammelin, Bengt (Finnish Meteorological Institute) et al.:
Measurement of temperature with wind sensors during severe winter conditions
[3] Aspiration-Psychrometer tables, Deutscher Wetterdienst, 7. edition
[4] Coefficient of the Magnus formula acc. to Prof. Dr. Sonntag

12 -12 021537/06/10
3Preparation for operation
Attention:
The working position of the anemometer is vertical (sensor
arms "above".
During installation, de-installation, transport or maintenance of
the anemometer it must be ensured that no water gets into the
shaft and connector or cable gland of the anemometer.
When using a lightning rod take care that it be installed in a
angle of 45°to a measuring arm; otherwise there wil l be
deviations in the measured values.
3.1 Selection of installation site
As described above, the ultrasonic anemometer transmits sound packages required to measure
the propagation speed. If these sound packages meet surfaces that reflect sound well, they are
thrown back as an echo and can may result in incorrect measurements under unfavourable
conditions.
It is therefore advisable to install the ultrasonic anemometer at a minimum distance of 1 metre to
objects in the measuring level.
In general, wind meters should register wind conditions over a wide area. To obtain comparable
values when measuring the ground wind, measurement should be performed at a height of 10
metres above even and undisrupted terrain. Undisrupted terrain means that the distance between
the wind transmitter and the obstruction should be at least ten times the height of the obstruction
(s. VDI 3786). If it is not possible to comply with this provision, the wind meter should be installed at
a height at which measured values are influenced by obstructions located in the vicinity to the least
possible extent (approx. 6-10 m above the interference level). On flat roofs the anemometer should
be installed in the middle of the roof and not at the edge to thus avoid any preferential directions.
The ultrasonic-anemometer has an electro-magnetic compatibility which is far in excess of the
required standard threshold value.
Within the complete frequency range, required by standard, electro-magnetic fields with 20 V/m
(capacity of the test transmitter) could not affect the measuring value acquisition of the instrument.
In case you intend to install the instrument at transmitter masts or other sources of strong electro-
magnetic radiation, where the local field strength is far above the standard threshold value, please
contact the manufacturer.

13 -13 021537/06/10
3.2 Installation of anemometer
Proper installation of the ultrasonic anemometer is carried out using a tube socket R1½" (Ø 48.3
mm) and 50 mm in length. The inside diameter of the pipe socket must be at least 40 mm as the
ultrasonic anemometer is electrically connected from below. After electrical connection (see
chapter 3.4) the ultrasonic anemometer is fitted on the tube or mast socket. Now the mechanical
north adjustment of the Anemometer takes place, see chapter 3.3.
The instrument is fixed to the shaft with the four Allen screws (SW 4 mm).
3.2.1 Device to Refuse Birds (optionally)
A protective pin prevents bigger birds from sitting on the instrument. The device consists of a pin
(V4A) and a protective cap, and is screwed into the available thread on the arm carrier of the
Ultrasonic Anemometer, if necessary.
Mounting:
Protective cap of the thread on the arm carrier of the Ultrasonic Anemometer is removed, for ex. by
means of a screw driver. Pin is screwed tightly in to the thread acc. to figure 1 for ex. by means of
a pincer. The protective cap serves as mounting protection and is removed after installation of
instrument.
Figure 1: Device to refuse birds

14 -14 021537/06/10
3.3 Alignment to north
For exact determination of the wind direction the anemometer has
to be installed aligned to the north (true north).
To align the anemometer, the arm of the sonic transformer
marked red must point to north (true north). To do so, select a
conspicuous feature of the landscape to the north or south with a
compass and turn the mast or anemometer until the opposing
arms are aligned in this direction.
It is recommended using a telescope for this process.
When aligning the instrument to north using a compass, the
magnetic variation (= deviation in direction of compass needle
from true north) and local interfering magnetic fields (e.g. iron
parts, electric cables).
Attention:
If an additional north marking “N” is attached on the sensor head
(see figure), it is overriding for the north alignment
In the bottom of the anemometer stand there is a north-drilling.
The north-drilling serves for the use of a so-called north-ring with
bolt. The north-ring is not included in delivery.
Remark: For Model 4.3820.36.390 only
In the bottom of the anemometer stand there is a north notch in
the form of an isosceles triangle. The upper notch vertex indicates
towards the red-marked arm. The north notch serves for the use of
a so-called north-alignment-ring. The north-alignment-ring is not
included in delivery.
Remark: For Model 4.3822.40.340 only
In the anemometer stand there is a south driling with cylnder pin.
The pin is opposite to the red-marked north arm.

15 -15 021537/06/10
3.4 Electrical Installation for Ultrasonic Anemometer with Connector
The ultrasonic anemometer is equipped with a plug for electrical connection. A coupling socket
(mating) is included in delivery. It is located in the lower part of the transport packing. A plastic fit-
up aid for holding the bush insert while screwing it together with the coupling sleeve, is included in
delivery.
3.4.1 Cables, Cable preparation, Coupling socket Installation
For pin assignment please refer to supplement „factory settings“. Examples see
chapter 3.4.2.
The cable must have the following properties:
8 cores; 0,5 to 0,75 mm² core cross-section for supply ; min. 0,14 mm² core cross-section for data
communications ; 7-8 mm cable diameter, resistant to ultraviolet rays, overall shielding.
Remark:
Optionally, a completely converted connecting cable can be included in delivery
for the ultrasonic-anemometer (see accessories).
Coupling socket 507550 (Binder, Serial 423), EMC with cable clamp
View X
Cable- pull- relief
Cable mounting 1
Viev X
wire
Cable clamp
shield
Cable shield
1. Stringing parts on cable acc. to plan given
above.
2. Stripping cable sheath 20 mm
Cutting uncovered shield 15 mm
Stripping wire 5mm.
Cable mounting 1
Putting shrink hose or insolating tape between
wire and shield.
Cable mounting 2
If cable diameter permits, put the shield
backward on the cable sheath.
3. Soldering wire to the insert, positioning shield
in cable clamp.
4. Screwing-on cable clamp.
5. Assembling remaining parts acc. to upper plan.
6. Tightening pull-relief of cable by screw-wrench
(SW16 und 17).
Cable mounting 2
Viev X
Figure 2: Coupling socket installation

16 -16 021537/06/10
3.4.2 Connector Pin Assignment (Examples of Function)
Remark:
-For exact allocation of function please refer to supplement “Factory Settings”
-The pins 1 –6 (incl.) are galvanically isolated from the supply voltage and from
housing.
•Serial Interface, Full-duplex
Pin
Allocation Function View of solder terminal
of coupling socket
1RXD-Serial interface
2TXD-Serial interface
3ADIO Function not preset
4RXD+ Serial interface
5TXD+ Serial interface
6AGND Analogue ground
7AC/DC Supply, reverse-polarity protected
8AC/DC Supply reverse-polarity protected
Shield
•Serial Interface, halve-duplex and
analogue outputs
Pin
allocation Function
View of solder terminal
of coupling socket
1WG Analogue output wind speed
2TXD-/ RXD-Serial interface
3ADIO Function not preset
4WR Analogue output wind direction
5TXD+ / RXD+ Serial interface
6AGND Analogue ground
7AC/DC Supply, reverse-polarity protected
8AC/DC Supply, reverse-polarity protected
Shield
1
2
34
5
678
•Serial Interface, halve-duplex and
analogue inputs
Pin
Allocation Function
View of solder terminal
of coupling socket
10-9,96V Analogue input
2TXD-/ RXD-Serial interface
30-9,96V Analogue input
40-9,96V Analogue input
5TXD+ / RXD+ Serial interface
6AGND Analogue ground
7AC/DC Supply, reverse-polarity protected
8AC/DC Supply, reverse-polarity protected
Shield
1
2
34
5
678
1
2
34
5
678

17 -17 021537/06/10
3.5 Electrical Installation for Ultrasonic Anemometer with Screwed Cable Gland
The ultrasonic anemometer is equipped with a fix-connected cable by means of a screwed cable
gland. The cable end is open. The core ends are marked by means of pin numbers on cable
marking rings.
3.5.1 Cable Pin Assignment (Examples of function)
Remark:
-For exact allocation of function please refer to supplement “Factory Settings”
-The pins 1 –6 (incl.) are galvanically isolated from the supply voltage and from
housing.
•Cable assignment:
Analogue outputs, serial interface halve-duplex
Pin Colour Code Assignment Function
1white WG Analogue output wind speed
2green TXD-/ RXD-Serial interface
3black 1 ADIO Heating control
4brown WR Analogue output wind direction
5yellow TXD+ / RXD+ Serial interface
6black 2 AGND Ground for analogue output
and serial interface
7black 3 AC/DC Supply, reverse-polarity protected
8black 4 AC/DC Supply, reverse-polarity protected
green / yellow shield

18 -18 021537/06/10
4Maintenance
As the instrument does not have moving parts, i.e. is not subject to wear during operation, only
minimal servicing is required. Given that the sensor surfaces are normally kept clean by rain, it will
only be necessary to occasionally remove residues from the sensor surfaces in regions with very
little rain. Cleaning can be carried out as required using non-aggressive cleaning agents in water
and a soft cloth during routine checks.
Attention:
During storage, installation, de-installation, transport or
maintenance of the anemometer it must be ensured that no
water gets into the shaft and connector or cable gland of the
anemometer.
5Calibration
The ultrasonic anemometer does not contain any adjustable components such as electrical or
mechanical trimming elements. All components and materials used show invariant behaviour in
terms of time. This means that no regular calibration is required due to ageing. Errors in measured
values are only caused by mechanical deformation of the transformer arms and associated
changes in measurement path lengths.
The acoustic-virtual temperature can be used to check the effective-acoustic measurement path
length. A change of 0.17% in the measurement path length and thus a measuring error of 0.17%
for the wind velocity corresponds to a deviation in the virtual temperature of 1 K at 20°C; there is a
measuring error of approx. 1% for the wind velocity with a 6 K deviation of acoustic-virtual
temperature.
In the event of any change in the measurement paths of the anemometer the manufacturer should
be consulted regarding recalibration.
Important:
Mechanical deformation of the measuring arms results in
errors in the measured values, which involve the output of
error telegrams / error signals to the analog interfaces.
6Warranty
Damage caused by improper handling or external influences, e.g. lightning, do not fall under the
warranty provisions. The warranty entitlement expires if the instrument is opened.
Important:
The ultrasonic anemometer must be returned in the original
packaging as the warranty entitlement otherwise expires with
mechanical damage, e.g. deformation of measuring arms.

19 -19 021537/06/10
7Functional description
The functioning of the ULTRASONIC instrument is described below. Due to the limited number of
plug connections some functions exclude the simultaneous operation with other functions. Such
dependency is described in each case. For example, in half duplex mode independent telegram
output is not permissible. There are also restrictions regarding the functional definition of the cable
connector. This is due to the double assignment of individual PINs.
7.1 Serial communication
The ULTRASONIC provides an RS485 / RS422 interface for serial communication. It can be
operated either in full or half duplex mode and at different baud rates.
A standard terminal program, for ex., can be used for communication with the ULTRASONIC. With
a Windows-based operating system Hyper Terminal is included in the scope of supply. It has to be
installed subsequently if required.
The manufacturer, generally, is not aware of a possible use of the Ultrasonic Anemometer in a bus
formation. Therefore, the instrument has a wave terminating resistor, which can be connected by
the software, for half-duplex-operation. See command: BT (bus termination).
When starting the ULTRASONIC, the communications parameters are output to the serial
interface. Output takes place at 9600.8N1. The baud rate, the duplex modus and the ID are output:
Example:
THIES ULTRASONIC
!00BR00005
!00DM00001
The ULTRASONIC starts with ID 0, with a baud rate of 9600.8N1 and full duplex mode.
7.1.1 Duplex mode
Duplex mode decides the type of physical connection of the serial interface. In full duplex mode the
send and receive signals are each transmitted via separate pairs of cables. This means it is
possible to send and receive signals at the same time.
In half duplex mode transmission of the send and receive signals is via the same pair of cables in
the time division (successively) (: see Command DM.
For a bus operation in the half-duplex-mode (RS485), where the ULTRASONIC, in general, is
operated as “slave”, it is necessary to switch the line-transmitter into the “high–impedance-state”
during the intermission, so that the replies of the other bus parties are not suppressed.
It might be important with point-to-point-connections in the full-duplex-mode (RS422), depending
on the disturb-ratio on the communication lines, that the line-transmitter remains active during the
intermissions. So, a maximum differential input level leads to a maximum signal/noise ratio.
A half-duplex-mode can be selected via the command DM (duplex mode). With this mode, on
principle, the line-transmitter is switched on only when sending. For the full-duplex-operation there
are two modes: one for bus operation (RS485), where the line-transmitter is controlled as in half-
duplex mode, and another one (RS422), where the line-transmitter remains active even in case of
reception. See command DM.
For the ULTRASONIC there are restrictions on the parameter combination or function of the
terminals depending on the transmission type selected. Due to the limited number of plug
connector contacts multiple assignment of the connections are necessary. The following table
shows the functional options for the modes full and half duplex.

20 -20 021537/06/10
Full duplex mode Half duplex mode
Independent telegram output possible
(see Command TT)Independent telegram output not possible
Bus mode not possible (RS485, DM=1),
No bus mode possible (RS422, DM=2) Bus mode possible (RS485, DM=0)
No output of analogue values to PIN RXD-and
RXD+ Output of analogue values possible
No readin of ID from external PINs
(see Command XI)Readin of ID from external PINs possible
(see Command XI)
Analogue inputs to PINs RXD-and RXD+ not
possible.
(see Command AA, Command AB)
Analogue inputs to PINs RXD-and RXD+ possible
(see Command AA, Command AB)
Heating control via PIN ADIO possible Heating control via PIN ADIO possible
Table 1: Restrictions in full and half duplex mode
7.1.2 Response Delay
With the serial communication please take into consideration that the ULTRASONIC responds
immediately to arriving telegrams. The response time of the instrument is in the lower range of
milliseconds. Possibly, the delay between receiving signal and sending signal might be too short for
some interface converters. It is possible that, within this time period, the interface converter has
not yet switched over from the mode ‘sending’ to the mode ‘receiving’. This might lead to absurd
telegrams.
In order to avoid this effect, the ULTRASONIC has the parameter RD (response delay). With this
parameter the response is additionally delayed, on receipt of a query or command, by the selected
value in milliseconds.
The parameter depends on the order-number of the instruments.
7.1.3 General telegram structure
For serial communication the ULTRASONIC has a fixed telegram format which also permits
communication in bus mode. It has the following form:
NNBB<cr> <cr> stands for Carriage return (Enter key)
for a data enquiry or
NNBBPPPPP<cr> <cr> stands for Carriage return (Enter key)
for a parameter change.
The individual letters have the following meaning:
NN: Two-position ID of the ULTRASONIC. It can be selected in the range from 00 to 99.
The presetting is the ID '00': see also Command ID and Command XI
BB: Two-position command. A complete list can be found in section Command list.
PPPPP: If a new parameter is to be set, the parameter is changed with a 5-position value. The
parameter is always right-justified; i.e. it thus has to be padded from the left with zeros.
Example:
Telegram No. 4 is to be interrogated. The relevant command is:
00TR4<cr> <cr> stands for Carriage return (Enter key)
The prerequisite is that the ULTRASONIC ID has the value '0'.
Table of contents
Popular Measuring Instrument manuals by other brands
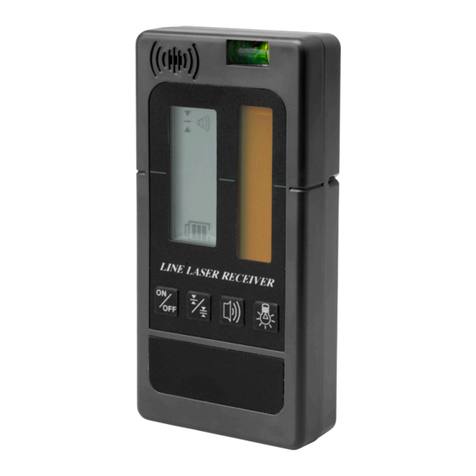
Meec tools
Meec tools 010976 operating instructions
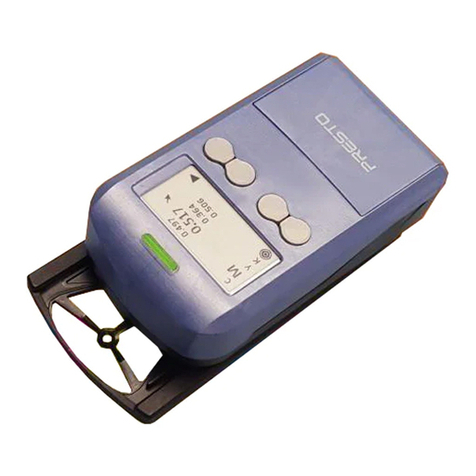
Beta
Beta Presto Spectro instruction manual
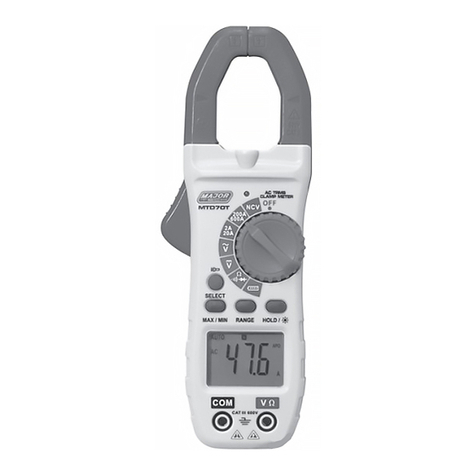
Major tech
Major tech MTD70T instruction manual
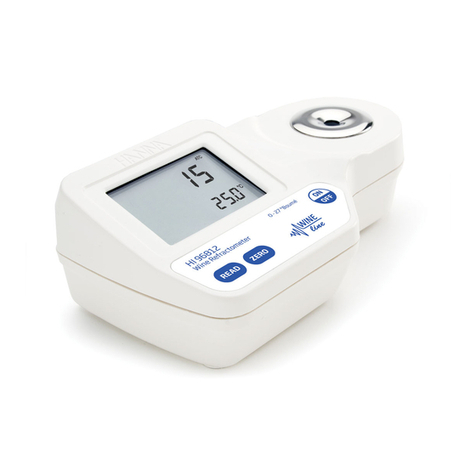
Hanna Instruments
Hanna Instruments HI 96812 instruction manual
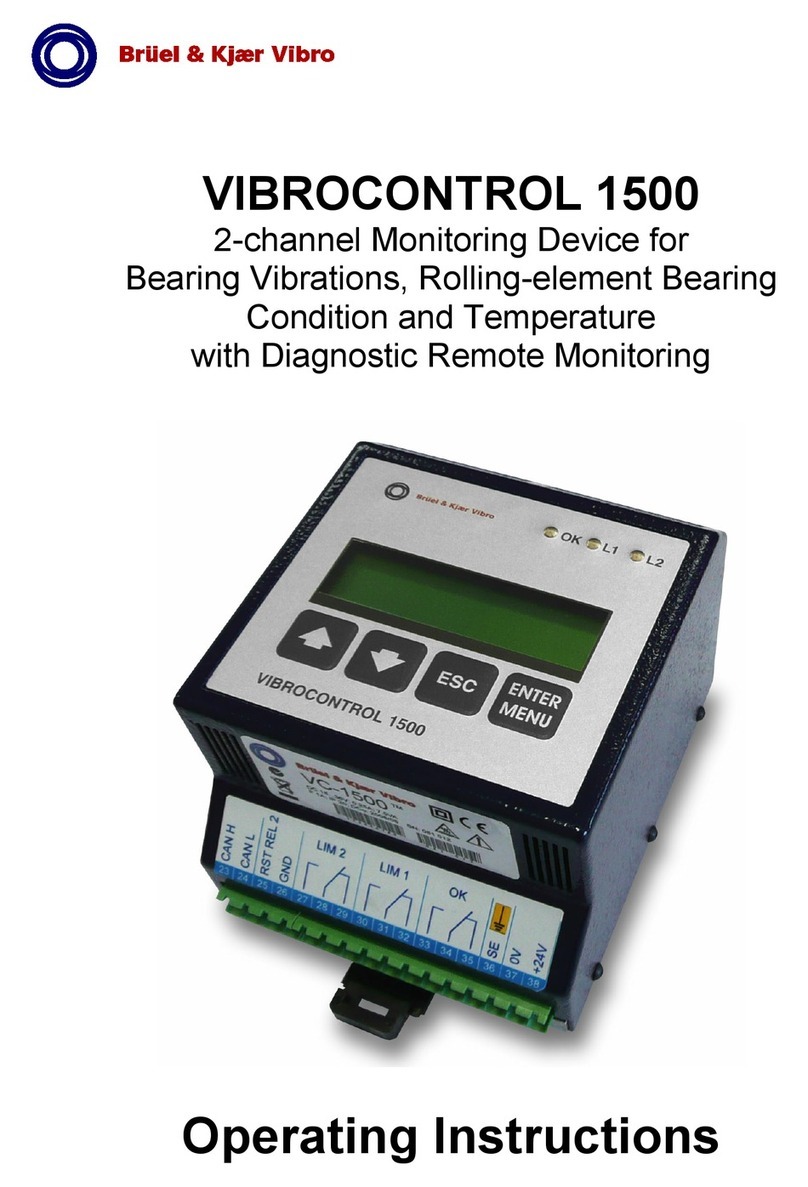
Brüel & Kjær Vibro
Brüel & Kjær Vibro VIBROCONTROL 1500 operating instructions
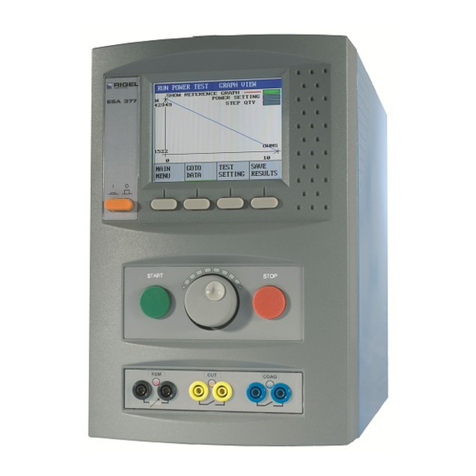
Rigel
Rigel 377 instruction manual