Metro DataVac MB-IP User manual

+33 (0) 450 39 08 49
Metro Fax +33 (0) 450 39 08 33
Rue de la Jonchère web www.metro-fr.com
F-74420 Boëge E-mail info@metro-fr.com
MB-IP
Master module for M-Bus network
User’s manual

Version 1.0
1. TABLE OF CONTENTS
1.TABLE OF CONTENTS ___________________________________________ 2
2.FOREWORDS __________________________________________________ 3
3.INTRODUCTION ________________________________________________ 5
3.1.PRODUCT PRESENTATION ........................................................................ 5
3.2.CARACTERISTICS ........................................................................................ 5
3.2.1.MAIN TECHNICAL CHARACTERISTICS ............................................... 5
3.2.2.DIMENSIONS AND INSTALLATION ...................................................... 6
3.2.1.CONTAINS OF THE PACKAGING ......................................................... 7
4.CONNECTORS _________________________________________________ 8
4.1.THE USB FULL-SPEED CONNECTOR ........................................................ 9
5.COMMUNICATION - ASCII PROTOCOL ____________________________ 10
5.1.NETWORK SETTING : IP ADDRESS, MASK AND GATEWAY SETUP ..... 10
5.2.IDENTIFICATION OF THE M-BUS MODULES ........................................... 10
5.3.COMMANDS FOR READING THE PROBES .............................................. 14
5.4.COMMANDS FOR READING MULTIPLE PROBES (FROM FIRMWARE
VERSION 2.1) ....................................................................................................... 15
5.5.COMMAND TO GET INFORMATION ABOUT PROBES (METRO PROBES
ONLY ON THE MB-8I MODULES) (FROM FIRMWARE VERSION 2.1) .............. 16
5.6.MB-IP VERSION .......................................................................................... 17
5.7.INPUTS/ OUTPUTS (MB-IO MODULES) .................................................... 17
5.8.RESOLUTION OF A MODULE FOR TTL PROBES (MODULE MB-2T) ...... 20
5.9.RESET THE COUNTER OF THE MODULES FOR TTL, 1VPP OR 11µA
PROBES (MODULE MB-2S) ................................................................................. 20
5.10.STEP AND INTERPOLATION OF AN INCREMENTAL PROBES 11µA OR
1VSS 20
5.11.CALIBRATION OF THE AIR GAGE MODULE MB-AG (FROM FIRMWARE
VERSION 2.1) ....................................................................................................... 20
5.12.DEFINITION OF THE TEMPERATURE INPUT ON THE MB-TP MODULES
(FROM FIRMWARE VERSION 2.1) ...................................................................... 21
6.MODBUS TCP COMMUNICATION PROTOCOL ______________________ 22

2. FOREWORDS
ONE YEAR LIMITED GUARANTEE FOR THE MB-IP
MANUFACTURER'S RESPONSIBILITY
SPARE PARTS AND LABOUR.
The manufacturer commits himself to pay for repair or replacement costs (labour
costs included) during a period of one year as from the date the guarantee came into
force. The spare parts can be new or renovated and are guaranteed until the end of
the initial guarantee period.
FIRST END-USER COVERAGE.
This guarantee applies only to the first end-user of the product and is not assignable
to any other subsequent purchaser or user.
RESTRICTIONS.
Any accessory or expansion item not included in the original factory packaging is not
guaranteed.
The present guarantee does not cover: installation or repair costs, damages resulting
from circumstances beyond the manufacturer's control like damages following acts of
God, misuse, or careless mistake from the user, damages during the transport or due
to a wrong installation, use or application, such as any material damage caused by
the use of non supplied products, components or accessories. It also does not cover
products modified without any written approval from the manufacturer, including
electrical or mechanical modification, removal of serial numbers or of the
manufacturer's trademarks or of any other identification.
THE SOLE RECOURSE UNDER THIS GUARANTEE SHALL BE THE REPAIR OR
THE REPLACEMENT OF DEFECTIVE PARTS AS INDICATED ABOVE. UNDER
NO CIRCUMSTANCES THE MANUFACTURER CAN BE HELD LIABLE FOR
INDIRECT OR SPECIAL DAMAGES OR FOR DAMAGES RESULTING FROM THE
USE OF THE PRODUCT, INCLUDING ANY LOSS OF DATA, BUSINESS OR
PROFIT, AND WHETHER THESE DAMAGES CAN BE FORESEEN OR NOT AND
WHETER THEY ARE BASED ON A GUARANTEE VIOLATION OR NOT.
THE PRESENT GUARANTEE REPLACES ANY OTHER EXPRESSED OR IMPLIED
GUARANTEE INCLUDING BUT NOT LIMITED TO ANY GUARANTEE OF
MARKETING OR ADEQUACY FOR A PARTICULAR USE; AND ALL THESE
GUARANTEES ARE EXPRESSLY EXCLUDED AND CANCELLED.
WARNING
The information contained in this booklet can be changed without notice.
The manufacturer makes no warranty whatsoever with respect to the warranties of
commercial quality of this product or its suitability to a particular use.

Version 1.0
The manufacturer is not responsible for mistakes that could be found in this handbook
and also for direct or indirect damage resulting from the equipment, its performances
and the use of this product.
CLEANING
Use a soft cotton cloth slightly soaked with an ethyl alcohol based product.
DO NOT USE the following products: acetone, benzene, toluene and halogens
hydrocarbons.

3. INTRODUCTION
3.1. PRODUCT PRESENTATION
The MB-IP module allows to connect the entire range of M-Bus modules (except the
MB-BT – Bluetooth) on a PC or a PLC with USB or Ethernet through and ASCII
protocol or with MODBUS-TCP.
Up to 254 inputs can be connected.
A footswitch ref 18020 can be also connected on the MB-IP.
The power supply is done through an external power transformer
3.2. CARACTERISTICS
3.2.1. Main technical characteristics
Up to 254 inputs
Ethernet port for computer or PLC communication
M-Bus port for connecting the M-Bus multiplexers (except the MB-BT – Bluetooth
module)
USB full speed port with ASCII protocol
Reset button
Data transfert through footswitch pulse or through a command on the Ethernet or
USB port
Operating Temperature : +15°C à +30°C
Relative humidity : maximum 80%
Dimensions : width 83 mm, height 39 mm, depth 74 mm
Weight : 165 grammes
Standard 7.5*35 DIN Rail mounting

Version 1.0
3.2.2. Dimensions and installation
The M-Bus modules are made on a robust aluminium profile.
All the M-Bus modules are designed and must be installed on a standard DIN rail
(7.5*35) in order to ensure a correct fixation.

3.2.1. Contains of the packaging
The MB-IP package contains :
- 1 MB-IP module
- 1 USB cable
- 1 transformer + 1 power supply cable
- 1 Mini-CD including USB driver and this user manual

Version 1.0
4. CONNECTORS
USB Full-Speed with
ASCII protocol
(Creates a virtual
COM PORT)
Ethernet with ASCII or
modbus TCP.
RJ45 connector.
Footswitch input
Power supply
connector
12-30 VDC
Reset button

4.1. THE USB FULL-Speed CONNECTOR
This section is useful to setup the IP address of the module, or if you intend to use the MB-IP
with the USB connection.
Connecting the MB-IP on the computer with USB will create a virtual COM Port.
Follow the following instructions before using the MB-IP :
1- Launch the file « driver USB.exe » located in the directory « Driver USB » on the mini-
cd.
2- Connect the MB-IP to your computer through the USB cable, a with the power supply.
The following message appears few seconds after:
3- A COM PORT (USB SERIAL PORT) appears in the device manager menu.
(Configuration panel Device manager Ports (COM & LPT)
You can then note the COM port number. It can be useful later for the configuration of
your acquisition software.

Version 1.0
5. COMMUNICATION - ASCII PROTOCOL
The ASCII protocol allows to identify the modules on the bus, to read individually the
probes, to read the inputs status of an I/O module, to write on a output of an I/O
module etc…
All the commands ends by <CR> (Ascii $0D)
5.1. Network setting : IP address, mask and gateway setup
To enable the Ethernet communication, The IP address of the computer has to be
specified to the module. The USB link is firstly used to set the correct IP address.
The following commands allows to set the IP address and networks parameters :
IP address:
o Command : @IP=XXX.XXX.XXX.XXX<$0D> with XXX.XXX.XXX.XXX
= IP address of the MB-IP like 192.168.001.001
Subnet mask:
o Command : @MK=XXX.XXX.XXX.XXX<$0D> with XXX.XXX.XXX.XXX
= subnet mask address of the MB-IP like 255.255.255.000
Gateway:
o Command : @GW=XXX.XXX.XXX.XXX<$0D> with
XXX.XXX.XXX.XXX = Gateway address of the MB-IP like
192.168.000.001
From this moment, the Ethernet communication is available.
5.2. Identification of the M-Bus modules
Before reading the probes, it is necessary to identify the connected modules on the
MB-IP. This has to be done only the first time.
Up to 254 input can be connected. The address of the input will thus be from 00 to
FE.
Identify a module:
o Command : @NY=XX<$0D> with XX = address of the first channel in
hexadecimal
o Move the first probe of the module or press the ID button depending on
the module you use.

o Answer : XXXXXXXXXX<$0D> when the module has been correctly
identified (example : 9#I816102422<CR>). The value corresponds to
the unique identification number of the module.
Example : identify a MB-8I (8 inductive probes), a MB-4C module (4 Sylvac capacitive
probes), and a MB-IO module (8 inputs/outputs) :
00 to 07 08 to 0B 0C
STEP 1 – Identify the MB-8I module
Command : @NY=00<$0D>
Move the first probe of the module or press the ID button depending on the module
you use.
Answer (example) : 9#I816102422<$0D>
The channels from 00 to 07 will be attributed to the MB-8I
STEP 2 – Identify the MB-4C module
Command : @NY=08<$0D>
Answer (example) : 9#C416102465<$0D>
The channels from 08 to 0B will be attributed to the MB-4C
STEP 3 – Identify the MB-IO module
Command : @NY=0C<$0D>
Answer (example) : 9#E816133461<$0D>
The MB-IO is now identifed at the address 0C
Note : the MB-IO takes only 1 address in the BUS.

Version 1.0
List of identified modules :
o Command : @ID? <$0D>
o Answer : @NN=XXXXXXXXXX<$0D>
@NN=XXXXXXXXXX<$0D>
@NN=XXXXXXXXXX<$0D><$0A>
Where NN=address of the first channel of the module
Where XXXXXXXXXX = ID number of the module
If no module is identified, the answer will be : <$0D><$0A>
Example : make the list of the modules identified on the last example :
00 to 07 08 to 0B 0C
o Command : @ID? <$0D>
o Answer : @00=9#I816102422<$0D>
@08=9#C416102465<$0D>
@0C=9#E816133461<$0D><$0A>

Erase 1 module :
o Command : @CL=XX<$D>
Where XX = address of the first channel of the module to be removed.
Example : erase the MB-4C module identified on the last example :
00 to 07 08 to 0B 0C
o Command : @CL=08<$D>
Erase all the modules :
o Command : @RAZ<$0D>
o Answer :
RAZ IDs… DONE <$0D>
RAZ Config… DONE<$0D>

Version 1.0
5.3. Commands for reading the probes
For asking the value of a probe, the computer or PLC must send a 3 characters
string : o Command : NN<$0D> with NN = address of the probe
o Answer : +/-000.0000 <$0D> (position in mm)
The first character is the ASCII code of the Hexadecimal value for the bits 4 to 7
(Example : 0 30h ; F 46h)
The 2nd character is the ASCII code of the Hexadecimal value for the bits 0 to
3
The 3rd character is the « carriage return » (ASCII 0Dh)
0000 0000 = probe 1
1111 1110 = probe 255
Example : read the probes n°3 connected on the MB-8I (8 inductive probes)
and the probe n°1 on the module MB-4C (4 Sylvac capacitive probes),
previously identified on the last example :
The probe°3 of the first module is at the address 02
Command : 02<$0D>
Answer (example) : 001.4554<$0D >
The probe n°3 of the first module (address 02) indicates 1.4554mm
The probe°1 of the second module is at the address 08
Command : 08<$0D>
Answer (example) : 023.9874<$0D >
The probe n°1 of the second module (address 08) indicates 23.9874mm
If no probe is connected, the value –999.9999<$0D> is sent.
7 6 5 4 3 2 1 0
1st character
2
nd
character

5.4. Commands for reading multiple probes (from firmware version 2.1)
For asking the value of several probes, the computer or PLC must send a 6
characters string :
o Command : SS :EE<$0D> with SS = address of the first probe and EE
the address of the last probe
o Answer : +/-000.0000;+/-000.0000;… ;+/-000.0000<$0D> (position in
mm)
Like for reading 1 probe, the first character is the ASCII code of the Hexadecimal
value for the bits 4 to 7 (Example : 0 30h ; F 46h) of the first probe
The 2nd character is the ASCII code of the Hexadecimal value for the bits 0 to
3 of the first probe
The 3rd character is a separator « : » between the first and the last probe
(ASCII 3A)
The 4th character is the ASCII code of the Hexadecimal value for the bits 4 to 7
(Example : 0 30h ; F 46h) of the last probe
The 5th character is the ASCII code of the Hexadecimal value for the bits 0 to
3 of the last probe
The 6th character is the « carriage return » (ASCII 0Dh)
0000 0000 = probe 1
1111 1110 = probe 255
7 6 5 4 3 2 1 0
1st character
2
nd
character
3rd character
7 6 5 4 3 2 1 0
4th character
5th character
:

Version 1.0
Example : read the probes n°1 to 5 connected on the MB-8I (8 inductive
probes previously identified on the last example :
The probe°1 of the first module is at the address 00
The probe°5 of the first module is at the address 04
Command : 00:04<$0D>
Answer (example) : 001.4554;000.1234;001.4567;002.9874;010.5414;<$0D >
The probe n°1 of the first module (address 00) indicates 1.4554mm
The probe n°2 of the first module (address 01) indicates 0.1234mm
The probe n°3 of the first module (address 02) indicates 1.4567mm
The probe n°4 of the first module (address 03) indicates 2.9874mm
The probe n°5 of the first module (address 04) indicates 10.5414mm
If no probe is connected, the value –999.9999<$0D> is sent.
5.5. Command to get information about probes (Metro probes only on the
MB-8I modules) (from firmware version 2.1)
The Metro inductive probes have special feature that allows among other things to
know the stroke of the probe :
o Command : @GI=xx<$0D> with xx= address of the channel from 00
to FE
o Answer : NO PROBE<$0D> if no probe is connected
or
o Answer : STROKE=4<$0D> with 4=4mm (when a M804S probe is
connected)

5.6. MB-IP version
It could be asked by the technical support.
It could be useful to send this command first to see if the communication works
correctly.
o Command : @SN?<$0D>
o Answer : XXX<$0D> (XXX is the version number)
5.7. Inputs/ Outputs (MB-IO modules)
It is possible to connect MB-IO modules on the MB-IP.
MB-IO modules are fitted with 8 optocoupled inputs/outputs.
The 8 outputs are similar to the « open collector PNP » type. They can be used with
an external power supply 12 to 30 VDC maximum. The maximal output current
drained by each output is 50mA
The 8 inputs represent a 2.2kOhms load connected to the 0 volt.
The inputs and outputs are isolated by optocoupler.

Version 1.0
Examples of connection between a PLC and a MB-IP
Output to PLC
0V of the PLC
I1
0 V
MB-IO module PLC
+ 24V
Output
+ 24 V from the PLC
0 V
MB-IO module PLC
0 V 0 V
0V of the PLC
PLC output
+ 24V
E1
Input
+ 24 V from the PLC
+ 24V
+ 24V

Outputs
Activate 1 or several outputs :
o Command : OXX=YY<$0D>
Where XX = address of the MB-IO module and YY the status of the
outputs in Hexadecimal
Example : Activate the output 8, 7 and 2 of the MB-IO module, previsouly
identified at the adress 0C
Pin
number
8 7 6 5 4 3 2 1
BIN 1 1 0 0 0 0 1 0
HEX C 2
Command : O0C=C2<$0D>
Inputs
Read the inputs status of a MB-IO module :
o Command : IXX<$0D>
Where XX = address of the MB-IO module
o Answer : YY<$0D>
Where YY = status of the inputs in Hexadecimal
Example : Read the input of the MB-IO module, previsouly identified at the
adress 0C. (For the example we define that the inputs 4 and 2 have been
activated by the external system).
HEX 0 A
BIN 0 0 0 0 1 0 1 0
Pin
number
8 7 6 5 4 3 2 1
Command : I0C<$0D>
Answer : 0A<$0D>

Version 1.0
5.7.1. Resolution of a module for TTL probes (module MB-2T)
If you use the MB-2T module for TTL probes, you will need to send a command for
setting the resolution of each input of the module, depending on the probe you have
connected.
o Command @RESxx=YY<$OD>
Where xx = address of the channel to configure
Where YY = resolution in 0.1µm 05 for 0.5µm or 10 for 1µm
5.7.2. Reset the counter of the modules for TTL, 1Vpp or 11µA probes
(module MB-2S)
o Command Cxx<$0D>
Where xx = address of the channel to configure
5.7.3. Step and Interpolation of an incremental probes 11µA or 1Vss
o Command @STPxx=II,PP<$0D>
Where xx = address of the channel to configure
Where II = interpolation from 20 to 200 with II=real step/10
example 02 for 20 and 20 for 200
Where PP = STEP en µm (example 0.2 for the Heidenhain MT12XX,
MT25XX, 10 for Heidenhain MT101, 20 for Heidenhain ST12xx or ST30XX)
5.7.4. Calibration of the Air Gage module MB-AG (from firmware version
2.1)
The MB-AG (for 1 air gage) needs to be calibrated in 2 points with a MIN and a MAX
master corresponding to the tolerance limits of the part.
Calibration with the MIN master
o Command @AGLnn=99850<$0D> (example for a MIN master of
9.9850mm) , where nn=address of the module
o Answer : SET<$0D>
Calibration with the MAX master
o Command @AGHnn=100150<$0D> (example for a MAX master of
10.0150mm), where nn=address of the module
o Answer : SET<$0D>
Table of contents
Other Metro DataVac Control Unit manuals
Popular Control Unit manuals by other brands

PMA
PMA KS 98 Operating instruction
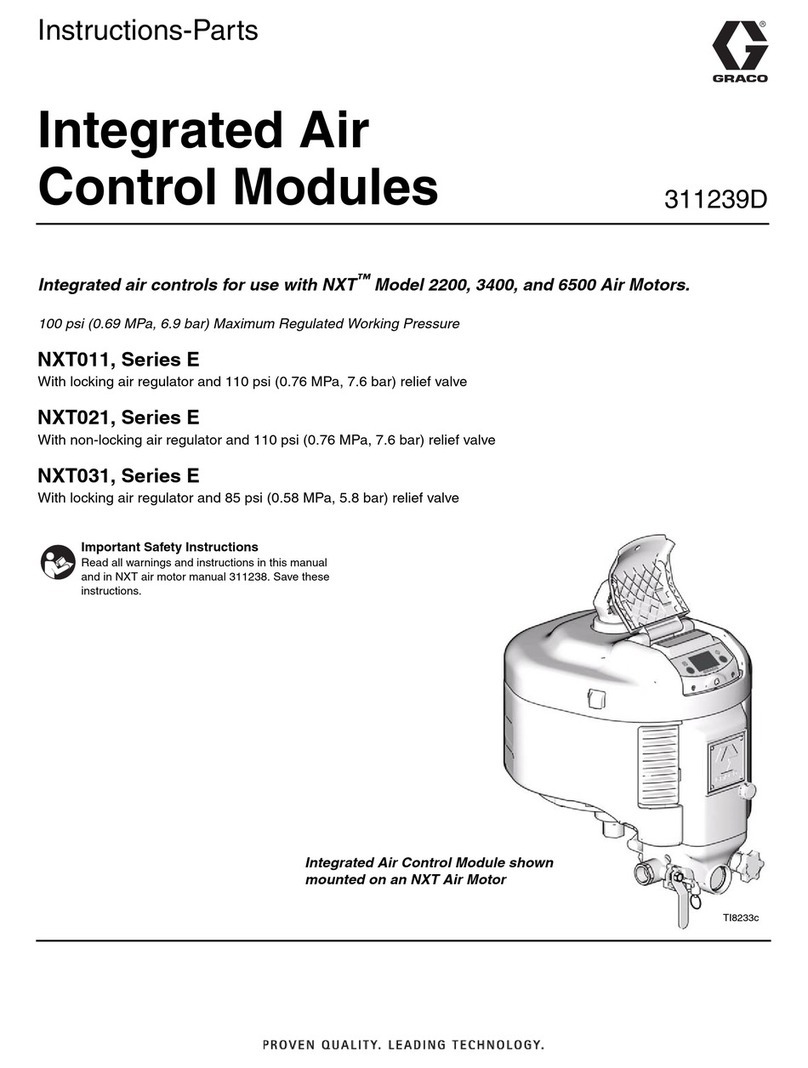
Graco
Graco NXT011 Instructions-parts list

SYR
SYR BA 6600 Instructions for use and installation
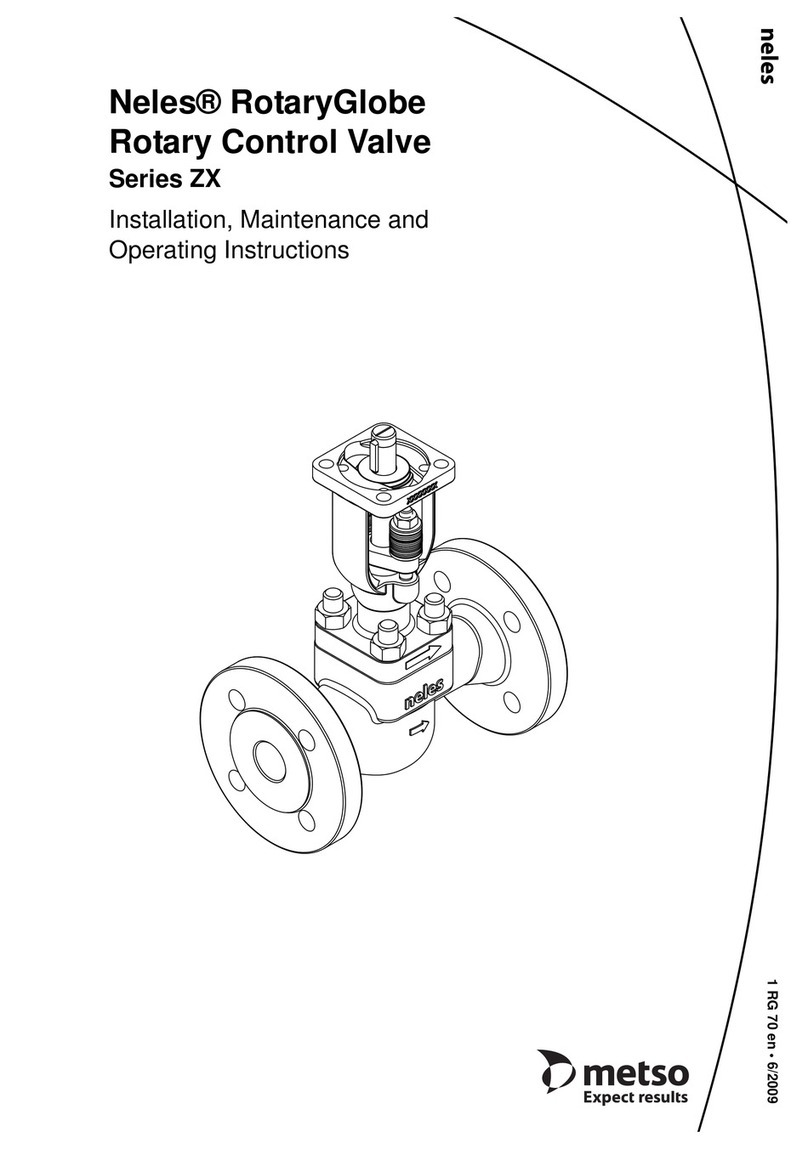
Metso
Metso Neles RotaryGlobe ZX Series Installation maintenance and operating instructions
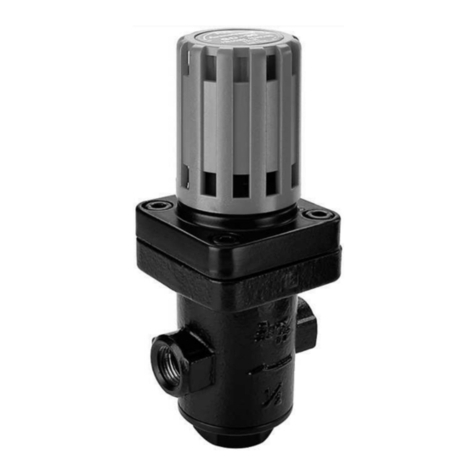
Armstrong
Armstrong GD-30 instructions
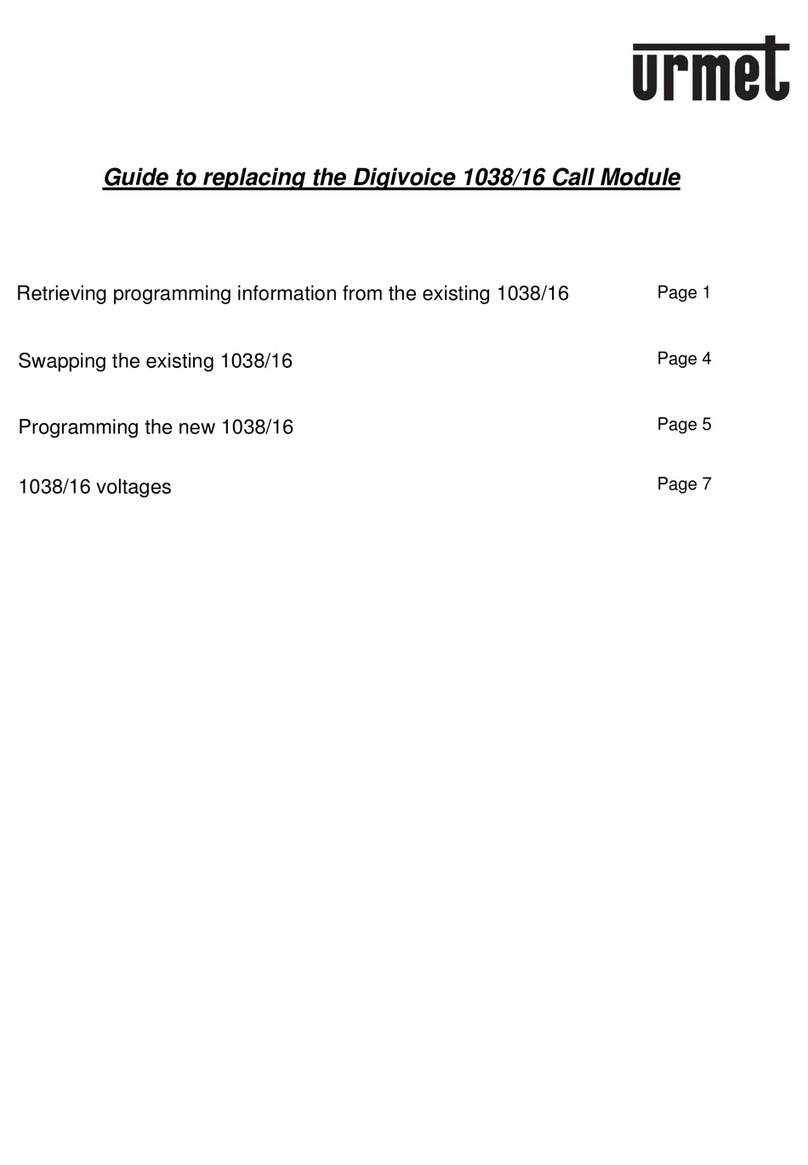
urmet domus
urmet domus DIGIVOICE K-Steel 1038/16 Guide