microguard 414 Programming manual

MICROGUARD414 / 424
TROUBLE SHOOTING MANUAL
HYDRAULIC CRANES
INFORMATION
TEST
W
MAX
W
100%
MicroGuard 414
CRANE
SETUP STOWED
DEDUCT
WORKING
AREADEDUCT
ERECTED STOWED
SELECT
VIEW SET CLEAR DOWN UP
CONTRASTOPERATOR ALARMS

MicroGuard 414 Trouble Shooting Manual Hydraulic Cranes
MicroGuard 414 Trouble Shooting Manual Page 2 of 26 March 2, 2006
CONTENTS
SUBJECT
System Description Page 3
Fault Diagnosis Procedures Page 4
Voltage Checks Page 7
Accessing Computer Boards Page 8
System Faults Pressure Transducers Page 9
BoomExtension Sensor Page 12
BoomAngle Sensor Page 13
Swing Sensor Page 14
No DutyFound Page 15
Executive ROM Page 15
PersonalityROM Page 15
Scratchpad RAM Page 15
DutyROM Page 15
Current DutyBad Page 15
Configuration Uncalibrated Page 15
Digital and Analog I/O Page 15
Display Page 15
Anti Two-Block System Page 16
Sensor Replacement Pressure Transducers Page 18
Extension Sensor Reel Page 18
BoomAngle Page 19
Chip Replacement Chip Replacement Guide Page 19
Executive ROM Replacement Page 19
PersonalityROM Replacement Page 19
DutyROM Replacement Page 19
Computer Board Replacement Page 19
Terminal Board Replacement Page 20
Glossary Page 21
Computer Layout Page 24
Termination Board Layout Page 25
Reeling Drum Layout Page 26

MicroGuard 414 Trouble Shooting Manual Hydraulic Cranes
MicroGuard 414 Trouble Shooting Manual Page 3 of 26 March 2, 2006
SYSTEMDESCRIPTION
The systemis intended to aid the crane operator in the
efficient operation ofhis crane bycontinuously
monitoring the load and warn ofan approach to an
overload or two-blockcondition. The systemmonitors
crane functions bymeans ofhigh accuracysensors and
continuouslycompares the load suspended belowthe
boomhead with acopyofthe crane capacitychart which
is stored in the computer memory.Ifan overload is
approached, the systemwarns bymeans ofaudible and
visual alarmsand can be configured to cause function
kick-out.
The MicroGuard 414 indicator provides the operator with
a continuous displayof:
•Rated Capacity
•Actual Load
•Percentage ofRated Capacity
•Radius ofthe Load
•Angle ofthe Main Boom
•Working Area
•Crane Configuration
and bymeans ofalternate displaypush-buttons it
provides the operator with:
•Length ofthe Main Boom
•Height ofthe BoomHead
On screen messages provide the operator with visual
indications ofthe various alarmswhich mayoccur during
normal operation ofthe system.These values are
displayed on the leftand upper right display.The lower
right displaygives information about the currently
selected crane configuration.
TEST
MicroGuard 414
INFORMATION
100%
OPERATOR ALARMS CONTRAST
VIEW SET CLEAR DOWN UP
CRANE
SET UP STOWED
DEDUCT WORKING
AREA
DEDUCT
ERECTED STOWED
SELECT
W
W
MAX

MicroGuard 414 Trouble Shooting Manual Hydraulic Cranes
MicroGuard 414 Trouble Shooting Manual Page 4 of 26 March 2, 2006
FAULTDIAGNOSIS PROCEDURES
Faults in the systemare detected automatically.Each
timethe systemis switched on it goes through a start up
selftest which lasts about 2-3seconds. During normal
operation aself-test can be initiated bypressing the
TESTbutton on the display.
Fault conditions in external sensors are detected without
the need for a systemself-test.
Iffaults are detected in the system during aself-test they
are indicated on the displayin the following way:
•The word FAULTwill appear in the information area
ofthe left display.
•The RED LAMP will illuminate and the AUDIBLE
ALARM will sound.
When faults occur in the systemtheycan be diagnosed
byuse ofthe display.
Details ofthe fault locations are obtained bypressing
and holding the test button. Holding the test button will
cause the systemto go through aselftest during which
faults will be detected. On completion ofthe self-test, if
the test button continues to be pressed, the fault screen
will appear. The fault screen will remain visible for as
long as the test button is pressed. Information will be
displayed on the screen in four groups.
•Group A Sensor faults
•Group B I/O faults
•Group C Memoryfaults
•Group D General faults
FAULTCODES
GROUP A”ANALOG SENSORS
CODE
AAA
000 NO FAULTS
001 AIN0 PISTON PRESSURE
TRANSDUCER
002 AIN1 ROD PRESSURE TRANSDUCER
004 AIN2 EXTENSION SENSOR
008 AIN3 BOOM ANGLE SENSOR
016 AIN4 S STRUCTURE ANGLE SENSOR
032 AIN5 SWING POTENTIOMETER “A”
064 AIN6 SWING POTENTIOMETER “B”
GROUP B”INPUTS AND OUTPUTS
CODE
BB FAULT
00 NO FAULTS
01 1 DIGITAL INPUTAND OUTPUT
02 2 ANALOG INPUTAND OUTPUT
04 4 DISPLAYUNIT
GROUP C”MEMORY
CODE
CC
00 NO FAULTS
01 1 EXECUTIVE ROM
02 2 DUTYROM
04 4 SCRATCHPAD RAM
08 8 PERSONALITYROM
GROUP D”GENERAL
CODE
DD
00 NO FAULTS
01 1 NO DUTYFOUND
02 2 CURRENTDUTYBAD
04 4 CONFIGURATION UNCALIBRATED
08 8 2 HZ OSCILLATOR

MicroGuard 414 Trouble Shooting Manual Hydraulic Cranes
MicroGuard 414 Trouble Shooting Manual Page 5 of 26 March 2, 2006
GROUP A’FAULTCODES
Ifafault is detected bythe systemanumber will appear
under one or more ofthe four group headings Athrough
D. This number will correspond to one or more fault
diagnosis numbers. The meaning ofthese numbers can
be determined bylooking at the appropriate code in the
fault interpretation table.
Group Afault codes relate to analog sensors. Each
sensor is allocated anumber and this number is also the
number ofthe channel to which it is connected in the
system.
•Sensor 0 Piston Pressure
•Sensor 1 Rod Pressure
•Sensor 2 Extension Sensor
•Sensor 3 BoomAngle
•Sensor 4 Superstructure Angle
•Sensor 5 Swing Potentiometer “A”
•Sensor 6 Swing Potentiometer “B”
Each sensor is allocated aFAULTCODE and this is the
number which appears under the group heading in the
fault code display.
001Sensor 0 Piston Pressure
002 Sensor 1 Rod Pressure
004 Sensor 2 Extension Sensor
008 Sensor 3 BoomAngle
016 Sensor 4 S structure Angle
032 Sensor 5 Swing Potr “A”
064 Sensor 6 Swing Potr “B”
When there are no faults detected in the system ‘000 will
appear under all group headings indicating that there are
no detected faults in the system. When there are faults in
onlyone sensor then the code will be one ofthe codes
listed above. When there are faults in more than one
sensor then the codes indicated will be the sumofthe
fault codes.
EXAMPLES OF FAULTCODES:
Fault 0 AAA B CC DD
000 0 00 00
No faults detected.
Fault 1 AAA B CC DD
001 0 00 00
Piston pressure transducer.
Fault 2 AAA B CC DD
002 0 00 00
Rod pressure transducer
TEST
MicroGuard 414
INFORMATION
100%
OPERATOR ALARMS CONTRAST
VIEW SET CLEAR DOWN UP
CRANE
SET UP STOWED
DEDUCT WORKING
AREA
DEDUCT
ERECTED STOWED
SELECT
W
W
MAX
AAA B CC DD
000 0
0000
PRESS AND HOLD
FAULT CODES

MicroGuard 414 Trouble Shooting Manual Hydraulic Cranes
MicroGuard 414 Trouble Shooting Manual Page 6 of 26 March 2, 2006
Fault 3 AAA B CC DD
003 0 00 00
Piston pressure transducer
Rod pressure transducer
Fault 4 AAA B CC DD
004 0 00 00
Extension Sensor
Fault 5 AAA B CC DD
005 0 00 00
Piston pressure transducer
Extension sensor
Fault 6 AAA B CC DD
006 0 00 00
Rod pressure transducer
Extension sensor
Rod pressure transducer
Fault 7 AAA B CC DD
007 0 00 00
Piston pressure transducer
Rod pressure transducer
Extension sensor
Fault 8 AAA B CC DD
008 0 00 00
Boomangle sensor
Fault 9 AAA B CC DD
009 0 00 00
Piston pressure transducer
Boomangle sensor
Fault 10
AAA B CC DD
010 0 00 00
Boomangle sensor
Rod pressure transducer
Fault 11
AAA B CC DD
009 0 00 00
Boomangle sensor
Piston pressure transducer
Rod pressure transducer
Fault 32
AAA B CC DD
032 0 00 00
Swing potentiometer “A”
Fault 64
AAA B CC DD
064 0 00 00
Swing potentiometer “B”
Fault 96
AAA B CC DD
096 0 00 00
Swing potentiometer “A”
Swing potentiometer “B”
This sequence continues up to the maximumfault code
of 127 which is the sumofall group “A”fault codes.
Fault 127
AAA B CC DD
127 0 00 00
All analog sensors.
This fault condition is seldomcaused bythe
simultaneous failure ofall sensors. It is more usuallythe
result ofthe failure ofthe analog drive voltage which is
the supplyvoltage for all sensors. This power supply
fault maybe due to the failure ofthe power supplyor
maybe due to damage to the cable which connects the
sensor to the computer.
When this fault occurs carryout Power SupplyVoltage
checks before checking individual sensors.

MicroGuard 414 Trouble Shooting Manual Hydraulic Cranes
MicroGuard 414 Trouble Shooting Manual Page 7 of 26 March 2, 2006
POWER SUPPLY VOLTAGES
The computer unit contains 2 major boards, the Terminal
Connection Board and the Computer Board. Both of
these assemblies are located in an aluminumbox which
is usuallylocated on the rear wall ofthe cab and can be
inside or outside the cab depending on crane model. All
ofthe cables fromthe various sensors and the display
are connected to the Terminal Connection Board. To
gain access to the Terminal Connection Board refer to
Page 9 ofthis manual.
INPUTPOWER
The computer operates froman input voltage in the
range 11 to 36 volts DC. This input voltage is measured
across the B+ and B- terminals on the Terminal
Connection Board and corresponds to the batteryvoltage
ofthe crane. At voltages below10.5 and above 38 volts
the systemwill power down until correct voltage is
restored.
If the INPUTPOWER is not within these limits checkthe
batteryand/or alternator before servicing the computer.
INTERNAL POWER SUPPLIES
The computer generates its own internal power fromthe
incoming batteryvoltage.
This power can be monitored at the test points inside the
computer adjacent to the fuses and BatteryInput
Terminals.
To monitor the Internal Power Supplies use a Digital
Voltmeter set to the appropriate DC voltage range
Connect the black(-ve) lead to GND
Connect the red (+ve) lead in turn to
+15V +/- 0.1
-15V +/- 0.1
+5V +/- 0.1
Ifthe voltages are out ofrange it maybe necessaryto
replace the computer.
Before replacing the computer, refer to
Crane Warning Systems Inc
Product Support Department
863-619-5585
Ground
+15volts
+5volts
-15volts
InternalPower
Terminals
Battery+
Battery-
Internal Power
Terminals

MicroGuard 414 Trouble Shooting Manual Hydraulic Cranes
MicroGuard 414 Trouble Shooting Manual Page 8 of 26 March 2, 2006
ACCESSING MAIN COMPUTER BOARD
AND TERMINATION BOARD
1. Remove the four screws(1) securing the
computer lid to the computer box. This lid is NOT hinged
so care should be taken not to allowthe lid to fall from
the box. Set the lid aside.
2. Under the lid you will see the Main Computer
Board. This board contains the Micro Processor and its
related components. This unit is held in place bytwo
screws(2) located at the leftand right ofthe Main
Computer Board backing plate and is connected to the
Terminal Connection Board via 2ribbon cables These
cables carrythe signals to and fromthe Termination
Board. These will be to the top ofthe Main Computer
Board.
3. Ifyou are going to checkvoltages on the
Termination Board, remove the two screws located at the
leftand right ofthe Main Computer Backing Plate and
swing the assemblyup. Takecare not to damage the
ribbon cables. These ribbon cables must remain
connected to the Main Computer Board for voltage
checks.
CHECKING ANALOG DRIVE VOLTAGE
Tocheckthe Analog Sensor Drive Voltage use the
following procedure:
1. Access the Termination Board.
2. With the systempower on and adigital volt
meter set to read DC voltage, place the negative lead on
any -DR (- Drive) terminal (1) ofthe Analog Input Group.
3. Place the positive lead ofthe meter on any+DR
(+ Drive) terminal (2).
4. The voltage should be 5.25+/-0.1volts.
5. Ifthe Analog Drive Voltage is not within this
range disconnect all ofthe external sensor cables,
including pressure transducers, cables 1 through 5.
6. Recheckthe Analog Drive Voltage. Ifthe voltage
is still out ofrange, the Computer Board will need to be
replaced. Ifthe voltage is within range, reconnect each
cable, one at atime, checking the Analog Drive Voltage
after each cable is connected.
7. Ifafter reconnecting anyone ofthe sensors the
Analog Drive Voltage goes out ofrange, it is probable
that the wiring to the sensor is grounded. or the sensor
itselfis faulty.
Checkall wires and the sensor itselfand repair or
replace as required .
+DR
0V
-DR
+DR
0V
+DR
-DR
-DR
0V
AIN0
0V
0V
AIN2
AIN1
-DR
AIN5
AIN6
AIN3
0V
0V
+VP
+VP
+VP
+VP
0V
+DR
+DR
0V
TX0-
TX0+AIN4
TX1+
TX1-
-DR
DRIVE
VOLTAGE
5.25 +/-0.1
Theanalog drivevoltage can be
measured betweenanyDR+terminal
andanyDR-terminal.Itis5.25volts
DC+/-0.1 volts.

MicroGuard 414 Trouble Shooting Manual Hydraulic Cranes
MicroGuard 414 Trouble Shooting Manual Page 9 of 26 March 2, 2006
PRESSURE CHANNEL FAULT GUIDE
FUNCTIONAL TESTS
A fault in a pressure transducer is such that a fault on
one channel can cause an apparent fault in the other
channel. It is necessaryto test both channels and both
transducers together in order to determine which
transducer is at fault.
1. Access the calibration routine bysimultaneously
pressing and holding
SELECT(1) and TEST(2) keys
The displaywill request entryofthe calibration
securitycode.
2. The securitycode is entered bythe consecutive
pressing ofthe calibration arrowkeyswhich MUSTbe in
the following sequence:
Up, (3), Down (4),
Left (5), Right (6),
SELECT(1)
Ifthe wrong sequence is used or ifthe entryis not
completed within 5seconds then the calibration entrywill
be aborted and must be re-entered. After accessing the
calibration routine, the systemalarmwill sound as a
reminder that you are in the calibration routine.
3. Use the Up (3) or Down(4) Arrowkeysto scroll
to command 06 Zero. Press Select (1)
5. Press the LeftArrow(5) and then use the Up (3)
or Down(4) Arrowkeysto select TX0(pressure
transducer 0 piston side). Press Select (1).
6. With the boomin the rest or the boomhoist
cylinder fullyretracted relieve all pressure fromboth
transducers. With no pressure the upper displayshould
indicate 0+/-20 bits.
7. Press the LeftArrow(5) and then use the Up (3)
or Down(4) arrowkeysto select TX1 (pressure
transducer rod side). With no pressure in the cylinder the
upper displayshould read 0+/- 20 bits.
8. Ifthe transducers were disconnected in step 5
tighten the fittings. With the boomfullyretracted, boom
up to a 60 degree angle.
9. Access the Zero ofTX0as described in step 5,
the upper displayshould read 200+/-100 bits.
10. Access the Zero ofTX1as described in step 7,
the upper displayshould read 5+/-25 bits.
11. Boomdown. As the boomis moving down, the
displayed bits ofTX 1 should increase.
12. Place the retracted boomat a60 degree angle.
Access the Zero ofTX0as described in step 4, and
extend the boom.As the boomis extended the displayed
bits ofTX0should increase. When the boomis fully
extended the displayshould read 400+/-100 bits for a
three section boomand 600+/-100 bits for afour section
boom.
The values listed are nominal values. The actual values
will differ according to howthe machine is equipped. A
three section boomwill showasmaller value on TX0
under the sameconditions as afour section boom.
Additional equipment on the main boom,such as stowed
fly,auxiliaryhead sheaves and hookblockswill give a
higher value than the main boomalone. Ifanyvalue is
out ofrange, contact your distributor or factoryservice
department before replacing apressure transducer.
Refer to page xx ofthis manual for pressure transducer
replacement.
13. Exit the calibration routine bypressing the TEST
(2) key.
Ifthe foregoing functional tests indicate faults in the
pressure channels then proceed with Power Supply
Tests and the test ofthe resistance ofthe bridge ofthe
pressure transducers.
TEST
MicroGuard 414
INFORMATION
100%
OPERATOR ALARMS CONTRAST
VIEW SET CLEAR DOWN UP
CRANE
SET UP STOWED
DEDUCT WORKING
AREA
DEDUCT
ERECTED STOWED
SELECT
W
W
MAX
1
2
34
5 6

MicroGuard 414 Trouble Shooting Manual Hydraulic Cranes
MicroGuard 414 Trouble Shooting Manual Page 10 of 26 March 2, 2006
PRESSURE CHANNEL FAULT GUIDE
TRANSDUCER RESISTANCE MEASUREMENT
The pressure transducer is abalanced bridge composed
ofstrain gauges bonded to aflexible diaphragm.The
following resistance tests can be carried out to establish
the viabilityofthe pressure transducer.
Piston Pressure Transducer
1 With the power to the computer off,disconnect
the piston pressure transducer fromconnector 1on the
computer.
2 With the DVM set to the Ohmsrange, measure
the resistance between pins “C”an “D”ofconnector
MS3474W14-5PZ.
The resistance should be 350Ω+/- 10Ω
3 With the DVM set to the Ohmsrange, measure
the resistance between pins “B”an “E”ofconnector
MS3474W14-5PZ.
The resistance should be 350Ω±10Ω
4 With the DVM set to the Ohmsrange, measure
the resistance between pins B, C, D, E, and the case of
the transducer. Measure the resistance between B, C, D,
Eand the case ofthe connector. There should be no
connection between the case and any of the pins.
Rod Pressure Transducer
5 With the power to the computer off,disconnect
the rod pressure transducer fromconnector 2on the
computer.
6 With the DVM set to the Ohmsrange, measure
the resistance between pins “C”an “D”ofconnector
MS3474W14-5PZ.
The resistance should be 350Ω±10Ω
3 With the DVM set to the Ohmsrange, measure
the resistance between pins “B”an “E”ofconnector
MS3474W14-5PZ.
The resistance should be 350Ω±10Ω
4 With the DVM set to the Ohmsrange, measure
the resistance between pins B, C, D, E, and the case of
the transducer. Measure the resistance between B, C, D,
Eand the case ofthe connector. There should be no
connection between the case and any of the pins.
BLUE, DRIVE-
PIN “D”RED, DRIVE +
PIN “C”
350Ω+/-10
YELLOW, SIGNAL+
PIN “D”
GREEN, SIGNAL-
PIN”E”
350Ω+/-10
A
B
C
E
D
“B”TO “E”350Ω+/-10Ω
“D”TO “C”350Ω=+/-10Ω
PRESSURETRANSDUCERCONNECTOR
MS3475W-5PZ
PRESSURETRANSDUCER
MS3475W14-5PZ

MicroGuard 414 Trouble Shooting Manual Hydraulic Cranes
MicroGuard 414 Trouble Shooting Manual Page 11 of 26 March 2, 2006
PRESSURE CHANNEL FAULT GUIDE
ANALOG DRIVE VOLTAGE
Analog sensor voltages are measured at the analog
input group terminals.
The drive voltage for all analog sensors is measured
between any+DR and -DR in the analog input group and
is 5.25volts DC ±0.1
Tomeasure this voltage use aDigital Voltmeter set to
the DC voltage range.
1 Connect the black(negative) lead ofthe DVM to
anyDR- terminal in the analog input group.
2 Connect the red (positive) lead ofthe DVM to
anyDR+ terminal in the analog input group.
3 Measure the drive voltage;
5.25 volts DC ±0.1
4 Ifthe voltage is out ofrange disconnect all ofthe
analog sensors bydisconnecting the sensor connectors
fromthe computer in order to determine ifanysensor or
its cabling is causing the drive voltage to be incorrect.
5 Ifthe drive voltage is correct with all ofthe
sensors disconnected then connect each sensor in turn
to determine which sensor is causing the drive voltage to
incorrect.
6 Ifanysensor is causing the drive voltage to be
incorrect carryout the trouble shooting procedure for that
sensor.
Ifthe drive voltage is incorrect with all sensors
disconnected it maybe necessaryto replace the
computer.
Before replacing the computer carryout the Power
SupplyTests detailed on Page xx ofthis manual
NOTE FOR TECHNICIANS FAMILIAR WITH MG3
UNLIKE THE MG3A SERIES, THE MG4 SERIES DOES
NOTHAVE ADUAL CHANNEL PRE-AMPLIFIER.
THERE IS NO POINTIN THE COMPUTER WHERE
ANALOG VOLTAGES RELATIVE TOPRESSURE CAN
BE MEASURED.
AIN0 AND AIN1 HAVE DIFFERENTFUNCTIONS IN
THE MG4 SYSTEM AND ARE NOTTHE POINTAT
WHICH TO MONITOR PRESSURE VOLTAGES.
+DR
0V
-DR
+DR
0V
+DR
-DR
-DR
0V
AIN0
0V
0V
AIN2
AIN1
–DR
AIN5
AIN6
AIN3
0V
0V
+VP
+VP
+VP
+VP
0V
+DR
+DR
0V
TX0-
TX0+ AIN4
TX1+
TX1-
-DR
DRIVE
VOLTAGE
5.25 +/- 0.1
Theanalog drive voltagecan bemeasured
betweenanyDR+ terminal andany DR–
terminal. Itis 5.25volts DC +/–0.1volts.
Faults in anycableorsensorcancause the
analogdrivevoltagetobefaulty.

MicroGuard 414 Trouble Shooting Manual Hydraulic Cranes
MicroGuard 414 Trouble Shooting Manual Page 12 of 26 March 2, 2006
BOOM EXTENSION SENSOR AIN2 2
Tocheckthe BoomExtension Sensor Voltage use the
following procedure.
1 Fullyretract the boom.
2 Access the Relayand Termination Board.
Measure the analog sensor drive voltage(refer to page 8
ofthis manual).
3. With aDigital Volt Meter set to read DC voltage
place the negative lead on any0Volt terminal ofthe
Analog Input Group.
4. Place the positive lead ofthe meter on the AIN2
2terminal ofthe Analog Input Group. The voltage should
be 0.25 volts ±0.1volt.
5. Extend the boom as far as safeto do. The boom
need not be horizontal for this test.
6. The voltage should be less than 5volts. (Usually
around 2.5 volts depending on the boomlength).
7. During extension the voltage should increase
linearlyand during retraction the voltage should
decrease linearly.
8. Ifthe voltage is out ofthe range listed above,
remove the four screwssecuring the cover on the
extension reel located on the leftside ofthe main boom
section and remove the cover.
9. Under the cover on the right side ofthe
extension reel you will see aterminal strip. This terminal
strip has six wires connected to the bottomscrews.
10. With aDigital Volt Meter set to read DC Voltage,
place the negative lead on the terminal with the blue wire
attached to it (- Drive) and the positive lead on the
terminal with the red wire attached to it (+Drive).
11. The voltage should be 5.25 ±0.1 volts. Ifthis
voltage is out ofrange and the Analog Drive Voltage
measured in the computer was OK then it is possible that
the cable is open or grounded between the Computer
and the Extension Reel. Check all connections and plugs
which maybe between these twocomponents. Repair or
replace as required. Refer to the MicroGuard 414 wiring
details in the Installation Manual for the model ofcrane
under test.
12 With the negative lead ofthe voltmeter
connected to blue, drive negative and the positive lead of
the voltmeter connected to white, extension signal, the
voltage should be the sameas the voltage measured at
AIN2 ofthe analog input group in the computer. Ifthis
voltage is not the sameit is possible that the cable
between the reel and the computer is faulty.
+DR
0V
-DR
+DR
0V
+DR
-DR
-DR
0V
AIN0
0V
0V
AIN2
AIN1
-DR
AIN5
AIN6
AIN3
0V
0V
+VP
+VP
+VP
+VP
0V
+DR
+DR
0V
TX0-
TX0+AIN4
TX1+
TX1-
-DR
DRIVE
VOLTAGE AIN2, VOLTAGE
VARIESWITH
BOOMEXTENSION
RED
DR+ WHITE
DR-
BLUE, SIGNALTO
COMPUTER

MicroGuard 414 Trouble Shooting Manual Hydraulic Cranes
MicroGuard 414 Trouble Shooting Manual Page 13 of 26 March 2, 2006
BOOM ANGLE SENSOR AIN 3
1. Place the main boomat a0degree angle. Verify
that it is at a 0 degree angle with an inclinometer.
2. Access the Terminal Connection Board. Check
the Analog Drive Voltage. (refer to page 8 ofthis manual)
3. With adigital voltmeter set for DC Volts, connect
the negative lead ofthe meter to any0Volt terminal of
the Analog Input Group.
4. Connect the positive lead to the AIN 3terminal
ofthe Analog Input Group.
5. With the boomhorizontal the voltage should be
2.6 ±0.25 volts.
6. Raise the main boomto a60 degree angle.
Verifythat it is at a 60 degree angle with an inclinometer.
7. With the boomat a60 degree angle the voltage
should be 3.5 ±0.25 volts.
8. Ifthis is out ofrange, remove the cover fromthe
reeling drumlocated on the left side ofthe main boom.
9. Under the cover on the right side ofthe
extension reel you will see aterminal strip. This terminal
strip has six wires connected to the bottomscrews.
10. With aDigital Volt Meter set to read DC Voltage,
place the negative lead on the terminal with the blue wire
attached to it (- Drive) and the positive lead on the
terminal with the red wire attached to it (+Drive).
11. The voltage should be 5.25 ±0.1 volts. Ifthis
voltage is out ofrange and the Analog Drive Voltage
checked in step 2was OK then it is possible that the
reeling drumcable is open or grounded between the
Computer and the Extension Reel. Checkall connections
and plugs between these twocomponents. Repair or
replace as required. Refer to the MicroGuard 414 wiring
details in the Installation Manual for the model ofcrane
under test.
12 With the negative lead ofthe voltmeter
connected to blue, drive negative and the positive lead of
the voltmeter connected to green, angle signal, the
voltage should be the sameas the voltage measured at
AIN3 ofthe analog input group in the computer. Ifthis
voltage is not the sameit is possible that the cable
between the reel and the computer is faultyor the boom
angle sensor is faulty.
13. Ifthe above voltage checksare within range and
no grounds or opens are found in the wires, replace the
BoomAngle Sensor as described on page xx ofthis
manual.
RED
DR+ WHITE
DR-
GREEN, ANGLE
SIGNAL TO AIN3
+DR
0V
-DR
+DR
0V
+DR
-DR
-DR
0V
AIN0
0V
0V
AIN2
AIN1
-DR
AIN5
AIN6
AIN3
0V
0V
+VP
+VP
+VP
+VP
0V
+DR
+DR
0V
TX0-
TX0+AIN4
TX1+
TX1-
-DR
DRIVE
VOLTAGE. AIN3, Voltage
varieswith
boom angle.
2.6 at0 deg.
3.5 at60 deg.

MicroGuard 414 Trouble Shooting Manual Hydraulic Cranes
MicroGuard 414 Trouble Shooting Manual Page 14 of 26 March 2, 2006
SWING POTENTIOMETER
AIN 5 AND AIN 6
The position ofthe upper structure in relation to the
carrier must be determined. This is accomplished by
means ofswing potentiometer mounted in the collector
ring. Ifthe system does not have an input from the swing
potentiometer it will not be able to find a duty.
Tocheckthe Swing Potentiometer use the following
procedure:
1. Access the Relayand Termination Board.
Checkthe Analog Drive Voltage. (refer to page 8ofthis
manual).
2. With adigital voltmeter set for DC volts check
the voltage at the connections to the potentiometer
located on the Anti Two-Block board. Connection 1has a
red wire attached to it and connection 3has ablackwire
attached to it.
3. Connect the blacklead ofthe DVM to connection
3(blackwire) and the red lead ofthe DVM to connection
1(red wire). The voltage should be 4.125 +/- 0.1 volts. If
this voltage is out ofrange the Termination Board will
need to be replaced.
4. With the blacklead on any0Volt terminal check
the voltage at AIN 5terminal and AIN 6terminal The
voltage should be 4.50 +/- 0.1 maximumand 0.365 +/-
0.1 minimum.Both ofthese voltages should rise and fall
linearlywithin this range as the upper is rotated leftor
right .Ifthe Drive Voltage and the Voltage at the
connection to the potentiometer were correct and the
voltages on AIN 5and AIN 6are out ofrange the swing
potentiometer will need to replaced.
Contact your distributor or your Factory Service
Department for procedures on replacing the swing
potentiometer.
+DR
0V
-DR
+DR
0V
+DR
-DR
-DR
0V
AIN0
0V
0V
AIN2
AIN1
-DR
AIN5
AIN6
AIN3
0V
0V
+VP
+VP
+VP
+VP
0V
+DR
+DR
0V
TX0-
TX0+AIN4
TX1+
TX1-
-DR
DRIVE
VOLTAGE.
AIN5andAIN6,
Voltagevaries
withrotation of
upper.
4.2 maximum.
0.36minimum
whentheupperis
rotating.
1
4
2
3
Voltagemeasuredbetween2and 4 =5.25 volts.
Voltagemeasuredbetween1and 3 =4.125 volts.

MicroGuard 414 Trouble Shooting Manual Hydraulic Cranes
MicroGuard 414 Trouble Shooting Manual Page 15 of 26 March 2, 2006
NO DUTY FOUND
The systemneeds the sameinformation that the
operator would need in order to read aload chart. Iffor
anyreason this information is not available the fault “No
DutyFound “will result. This fault could occur ifeither
the BoomAngle Sensor, or Extension Sensor inputs are
faulty.The systemuses all ofthese inputs to determine
the dutyselection. Upon correction ofthe Sensor fault
the systemwill again be able to find a duty.
OTHER SYSTEM FAULTS
EXECUTIVE ROM
The Executive ROM fault code indicates failure of IC2 on
the main computer board. This chip can be replaced
without the need for re-calibration. The chip is labeled
M414150.
PERSONALITY ROM
The PersonalityROM fault code will be present until the
systemis fullycalibrated . At the completion ofcalibration
acode is automaticallyinserted into the memorywhich
enables the systemto carryout the selftest. Ifthe fault
code occurs in normal service it could indicate either a
failure ofIC7 or the loss ofdata in the device. It will be
necessaryto obtain acopy of the PersonalityROM which
was made at the completion ofthe initial calibration or
carryout acomplete re-calibration ofthe system.
Contact your Distributor or FactoryService Department
for details.
SCRATCHPAD RAM
The Scratchpad Ramfault code indicates the failure of
IC6 on the Main Computer Board. This itemis not user
serviceable and requires the replacement ofthe Main
Computer.
DUTY ROM
This fault is associated with the failure ofthe DutyChip
IC3 on the Main Computer Board. It can be replaced
without the need for re-calibration. It contains the load
chart data for the crane on which it is fitted and must be
the exact type for the load chart on the machine.
CURRENTDUTY BAD
This fault indicates failure ofthe DutyChip IC3 on the
Main Computer Board. It can be replaced without the
need for re-calibration. It contains the load chart data for
the crane on which it is fitted and must be the exact type
for the load chart on the machine.
CONFIGURATION UNCALIBRATED
When amachine is initiallycalibrated its dutychip may
contain more configurations than are to be sold with that
particular machine. Flyor jib options which are not
supplied with the machine will not showup in the Crane
Set Up menu. Refer to the Calibration Procedure,
Command 13 for details ofhiding or showing
attachments.
DIGITAL I/O & ANALOG I/O
Digital and Analog I/O faults are not user serviceable.
When this fault code is detected it will be necessaryto
replace the Main Computer Board.
DISPLAY UNIT
This unit is not user serviceable. When this fault code is
detected it will be necessaryto replace the DisplayUnit.
This can be done byremoving the four screwssecuring
the displayinto the dash and unscrewing the cable from
the backofthe display.Connect the displaycable to the
new display,install it into the dash and secure with the
four mounting screws.

MicroGuard 414 Trouble Shooting Manual Hydraulic Cranes
MicroGuard 414 Trouble Shooting Manual Page 16 of 26 March 2, 2006
ANTI TWO BLOCK SYSTEM
SYSTEMWILL NOTSHOW TWO-BLOCK WHEN
MACHINE IS TWO-BLOCKED:
1. Access the Termination Board (refer to page 8 of
this manual).
2. Makecertain that the Anti Two-Blockweight is
attached to the boomhead switch and that the selector
switch is properlypositioned.
3. Remove the brownwire connected to the ATB IN
terminal ofthe digital input group. (SEE PAGE 17). The
systemshould showa Two-Blockwarning.
4. Connect ajumper wire fromthe 0volt terminal to
the ATBIN terminal. (SEE PAGE 17). The Two-Block
warning should no longer be displayed. Ifthe Two-Block
warning remains the problemis in the Termination
Board.
5. Remove the jumper wire and reconnect the
brownwire to the ATBIN in terminal. Remove the four
cover screwsfromthe extension reel located on the left
side ofthe main boomand remove the cover.
6. Remove the brownwire fromthe terminal strip.
The systemshould showaTwo-Block warning .If it does
not, the brownwire or its connections between the
Terminal Board and the extension reel are grounded. If
the systemdoes showaTwo-Blockwarning there is a
ground in the wiring or connections between the
extension reel and the Switch at the boom head. Check
all wires and connections between these two
components and repair or replace as required.
SYSTEMSHOWS TWO-BLOCK WHEN MACHINE IS
NOTTWO-BLOCKED
1. Checkthat the selection switch ofthe Two-Block
switch located at the main boomhead is correctlyset.
2. Makecertain that the Anti Two-Blockweight is
attached to the boomhead switch.
3. Access the Termination Board.
(refer to page 8 ofthis manual).
4. Remove the brownwire connected to ATBin
terminal ofthe digital input group. The system should
showa Two-Blockwarning.
5. Connect ajumper wire fromthe 0volt terminal to
the ATBIN terminal. The Two-Blockwarning should no
longer be displayed. Ifthe Two-Blockwarning remains
the problem is in the Termination Board assembly.Ifnot,
the problemis in the external wiring or switches.
6. Remove the jumper wire and reconnect the
brownwire to ATBin terminal. Remove the four screws
fromthe extension reel located on the leftside ofthe
main boom.
7. Connect ajumper wire between the black wire
and the brownwire on the terminal strip. The Two-Block
warning should no longer be displayed. Ifit remains, the
brownwire is open between the Termination Board and
the Extension Reel. Ifthe warning is no longer displayed
the problemis somewhere between the extension reel
and the boomhead switch. Checkall wires and
connections between these twocomponents and repair
or replace as required.
BROWN
A2B SIGNAL BLACK
0VOLT
REELINGDRUM TERMINAL
STRIP

MicroGuard 414 Trouble Shooting Manual Hydraulic Cranes
MicroGuard 414 Trouble Shooting Manual Page 17 of 26 March 2, 2006
ANTI TWO-BLOCK LOGIC LEVELS
The signal fromthe ATBswitches at the boomand fly
tips is aswitched ground. The ground signal is sourced
in the computer at the 0volt terminal ofthe digital input
group.
When there is no ATBalarmthe switches at the boom
head are closed allowing the ground to be returned to the
computer at the ATBIN terminal.
When there is atwo-blockcondition the appropriate ATB
switch will go to the open position therebyremoving the
ground fromATBIN and causing ATBAlarmand
Function Disconnect.
The ATBalarmand Function Disconnects are controlled
separatelybythe ATB board in the computer.
The ATB board, located in the computer box;
•Operates the function disconnects bycontrolling
the coil ofRL2, ATB relay, at D OUT1.
•Operates the audible alarmand on screen
message bycontrolling the logic level at DIN13.
The logic levels are as follows:
NO ALARM ATB ALARM
ATB SWITCH CLOSED OPEN
ATB IN LOW
0.2 VOLT HIGH
5 VOLT
D OUT1 LOW
0.2 VOLT HIGH
5 VOLT
D IN 13 HIGH
12 VOLT LOW
0.2 VOLT
The voltage levels are approximations and small
variations are to be expected.
DOUT1
ATBIN
ATBBOARD
RL2
A2B
RL1
LOAD
DIN13
DOUT1 CONTROLSTHEA2B
RELAYRL2
NO A2B=LOW, 0.2VOLT
ALARM =HIGH,5VOLT
DIN13 CONTROLSTHE
AUBIBLEALARM AND
ONSCREENMESSAGE.
NOA2B=HIGH12VOLT
ALARM =LOW0.2VOLT
ATBIN
NOA2B=LOW
O.2VOLT
ALARM=HIGH
5VOLT
0V

MicroGuard 414 Trouble Shooting Manual Hydraulic Cranes
MicroGuard 414 Trouble Shooting Manual Page 18 of 26 March 2, 2006
PRESSURE TRANSDUCER REPLACEMENT
1. It is recommended that the replacement
transducer is closelymatched to the sensitivityofthe old
transducer. The sensitivityvalue is recorded on the serial
number plate.
2. Remove the connector connecting the
transducer to be replaced fromthe computer box.
3. With the boomcylinder completelyretracted, in
the rest, or with the boomsafely supported, remove the
transducer to be replaced.
4. Install the newtransducer on the boomhoist
cylinder.
5. Run the cable to the computer box and connect
it to the appropriate computer box connector.
6. Pick aknownweight to verifythe accuracyof the
system.Ifthe load reading is not within tolerance after
the replacement ofapressure transducer, carryout
Command 6, Pressure, ofthe MG414 Calibration
procedure.
EXTENSION REEL REPLACEMENT
Toreplace the extension Reel assemblyuse the
following procedure:
1. Fullyretract the main boom.
2. Disconnect the connector to the Two-Block
switch and remove the cable fromthe main boomhead
anchor .Allowthe cable to retract onto the reel, be
careful not to let the cable retract too rapidly.
3. Remove the Extension Reel Cable connector .
4. Remove the four mounting bolts (5) securing the
Extension Reel to the boomand remove the reel.
5. Mount the newreel to the boom,secure with the
mounting bolts and connect the Extension Reel Cable
Connector.
6. Remove the shipping cable clampfromthe new
cable and allowit to slowlyrewind onto the drumuntil
there is no pre-tension. Continue to re-wind the drumin
the samedirection until the distance between the boom
head and the connector is approximately12 ft. At this
point there will be no pre-tension.
7. Pull the cable out passing it through the cable
guides until the end ofthe cable is 3ft. beyond the boom
head.
8. Wrap the cable around the boomhead anchor a
minimumoffive times and secure with a wire tie or the
shipping cable clamp.
9. Connect the cable to the connector coming from
the Two-Blockswitch .
10. Manuallyturn the large gear connected to the
potentiometer fullycounter-clockwise.
11. Observe the length displayand turn the large
gear at least 3clicksclockwise until the length display
reads the retracted boomlength.
12. Replace the Extension Reel Cover, securing it
with the four screws.
13. Extend and retract the main boomand see that
the boomlength reading on the displayis correct.
BOOM ANGLE SENSOR REPLACEMENT
Toreplace the BoomAngle Sensor which is fitted inside
the reeling drum, use the following procedure:
1. With the power off,remove the 4bolts holding
the cover ofthe reeling drumand remove the cover.
2. Disconnect the 3wires connecting the angle
sensor to the terminal strip. Remove the twobolts
securing the sensor to the reeling drumand remove the
old angle sensor.
3. Install the newsensor in the reeling drumin the
original location, secure it with the mounting bolts and
connect the cable.
4. Raise the boomto a60 degree angle and verify
the angle with an inclinometer. While viewing the display
adjust the sensor until the displayreads 60 degrees and
tighten the mounting bolts.
6. Place the boomhorizontal, verifythat it is at 0
degrees with an inclinometer.
7. Verifythat the displayed boom angle is reading 0
degrees +/- 0.5 degrees.

MicroGuard 414 Trouble Shooting Manual Hydraulic Cranes
MicroGuard 414 Trouble Shooting Manual Page 19 of 26 March 2, 2006
EXTERNAL BOOM ANGLE SENSOR
REPLACEMENT ONLY
Toreplace the External BoomAngle Sensor use the
following procedure:
1. With the power off,disconnect the BoomAngle
Sensor cable fromthe sensor located on the leftside of
the boomnear the boomextension reel.
2. Remove the twobolts securing the sensor to the
boomand remove the old sensor.
3. Install the newsensor on the boom,secure it
looselywith the mounting bolts and connect the cable.
4. Raise the boomto a60 degree angle and verify
the angle with an inclinometer. While viewing the display
adjust the sensor until the displayreads 60 degrees and
tighten the mounting bolts.
5. Place the boomhorizontal, verifythat it is at 0
degrees with an inclinometer.
6. Verifythat the displayed boom angle is reading 0
degrees +/- 0.5 degrees.
EXECUTIVE ROM CHIP REPLACEMENT
The Executive ROM Chip contains the main program
data which the computer uses to function and must be
specific to the system.
1. Access the Main Computer Board. (Refer to
page 8 ofthis manual)
2. With the power off remove IC2, the Executive
ROM Chip fromits socket. (Refer to General Chip
Removal and Installation this manual).
3. Install the newExecutive ROM Chip into the
socket. Makecertain the notch in the chip is lined up with
the notch in the socket and all pins are properlyinserted .
PERSONALITY ROM CHIP REPLACEMENT
The PersonalityROM Chip must be the proper chip for
the particular machine serial number. This chip contains
calibration data which is unique to each machine.
1. Access the Main Computer Board. (refer to page
8 ofthis manual).
2. With the power off remove IC7, the Personality
ROM Chip fromits socket. (Refer to General Chip
Removal and Installation this manual).
3. Install the newPersonalityROM Chip into the
socket. Makecertain the notch in the chip is lined up with
the notch in the socket and all pins are properlyinserted.
DUTY ROM CHIP REPLACEMENT
The DutyROM Chip must be specific to the load chart
used in the machine. This chip contains acopyofthe
load chart and must match the load chart in the machine.
1. Access the Main Computer Board. (refer to page
8 ofthis manual).
2. With the power off remove IC3, the DutyROM
Chip fromits socket .(Refer to General Chip Removal
and Installation this manual).
3. Install the newDutyROM Chip into the socket.
Makecertain the notch in the chip is lined up with the
notch in the socket and all pins are properlyinserted.
NOTE: Replacement of the Executiveor DutyROM
Chip does NOT necessitate the re-calibration of the
system.
NOTE: Replacement of the PersonalityROMChip
does NOTnecessitate re-calibration of the system
if the newPersonalityROMChip is an exact
duplicate of the original. If a copyof the Personality
Chip is not available the system will need to be
completelyre-calibrated.

MicroGuard 414 Trouble Shooting Manual Hydraulic Cranes
MicroGuard 414 Trouble Shooting Manual Page 20 of 26 March 2, 2006
COMPUTER BOARD REPLACEMENT
1. With the power off,access the Computer Board.
(refer to page 8 ofthis manual).
2. Locate the tworibbon cables connecting the
Computer Board to the Termination Board.
3. The ribbon cables are held in place bytwo
locking tabs on each cable end .These locking tabs
must be pushed awayfromthe cable to disconnect the
cable. As the locking tabs are pushed the connector will
come loose fromthe Main Computer Board.
4. Loosen the twoscrewsholding the Computer
backing plate to the box.
5. Remove the Computer Board Assembly.
There are three computer chips on the Main Computer
Board which must be ofthe correct type. These three
chips are :
IC2 Executive ROM
IC3 DutyROM
IC7 PersonalityROM
The Executive ROM must be specific to the system.
The DutyROM contains acopyofthe load chart and
must correspond to the Load Chart Number ofthe
particular serial number machine.
The PersonalityROM contains data which is unique to
the particular serial number machine.
6. Install the;
•Executive ROM Chip.
•DutyROM Chip.
•PersonalityROM Chip.
7. Place the Main Computer Assemblyinto the
computer box and tighten the twomounting screws,
make certain to allowaccess to the ribbon cables.
8. Reconnect the twoRibbon Cables being certain
to fullyengage the connector and locking tabs
9. Replace the Computer Box cover and secure
with the four screws.
COMPUTER BOX REPLACEMENT
TERMINAL BOARD AND BOX ONLY, USING THE
COMPUTER BOARD FROM THE ORIGINAL BOX.
1. Remove the Main Computer Board.
2. Disconnect all cable connectors fromthe
Computer Box.
3. Remove the four screwssecuring the Computer
Box.
4. Remove the Computer Box.
5. Install the newcomputer and secure with the
four mounting screws.
6. Reconnect all cable connectors.
NOTETHATCONNECTORS 1AND 2ARE
SIMILAR AND THEYARE COLOR CODED AND
MUSTBE CONNECTED WITHTHE COLOR ON
THE CABLE MATCHING THE COLOR ON THE
SOCKET.
CHIP REMOVAL AND INSTALLATION
When removing and installing chips be certain the power
is switched off.Do not touch the chip pins unless you are
properlygrounded. Static electricitycan damage chips.
1. Make certain the power is off.
2. Remove the chip to be replaced with achip
removal tool.
NOTE: Chip removal and installation tools are available
fromanyelectronics store.
3. Insert the newchip into the installation tool per
the instructions on the package.
4. Insert the newchip into the socket, making
certain that the notch in the chip (1) lines up with the
notch in the socket (2).
5. Double checkthat all pins are properlyinserted
into the chip socket. These pins are veryeasilybent.
Failure to have all pins inserted can cause damage to
the systemand the chip.
Other manuals for 414
1
This manual suits for next models
1
Table of contents
Popular Control Panel manuals by other brands
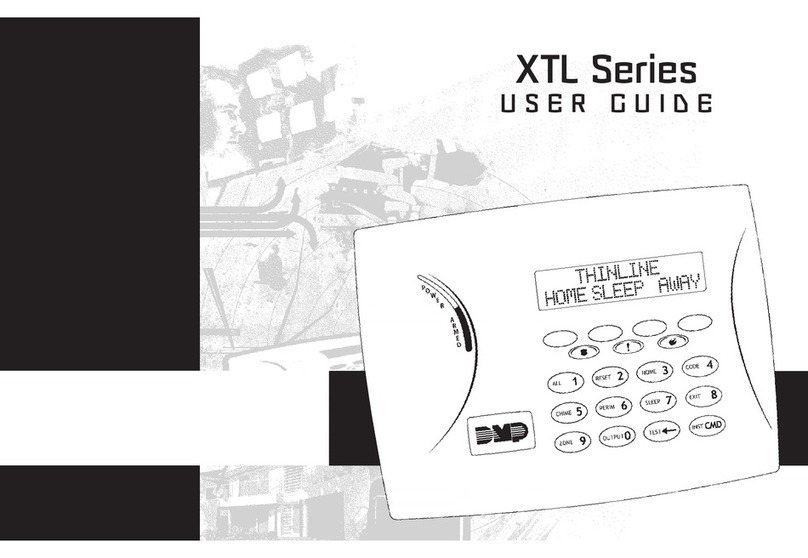
Digital Monitoring Products
Digital Monitoring Products XTL Series user guide
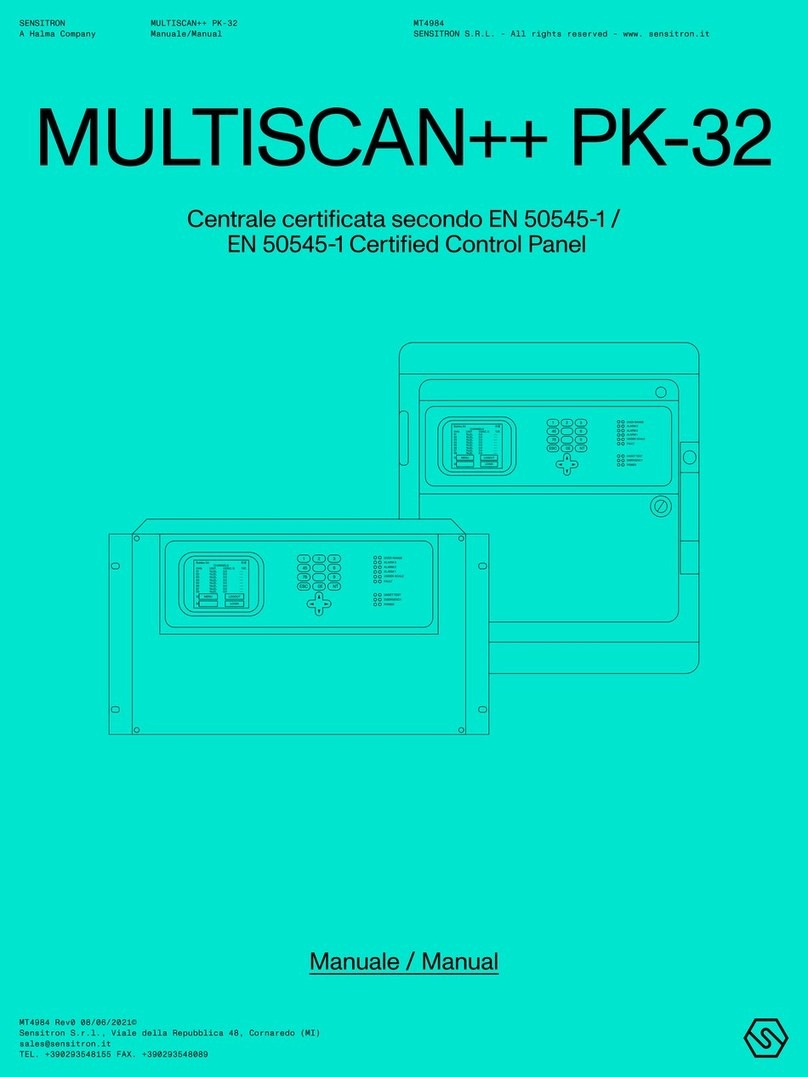
Halma
Halma SENSITRON MULTISCAN++ PK-32 manual
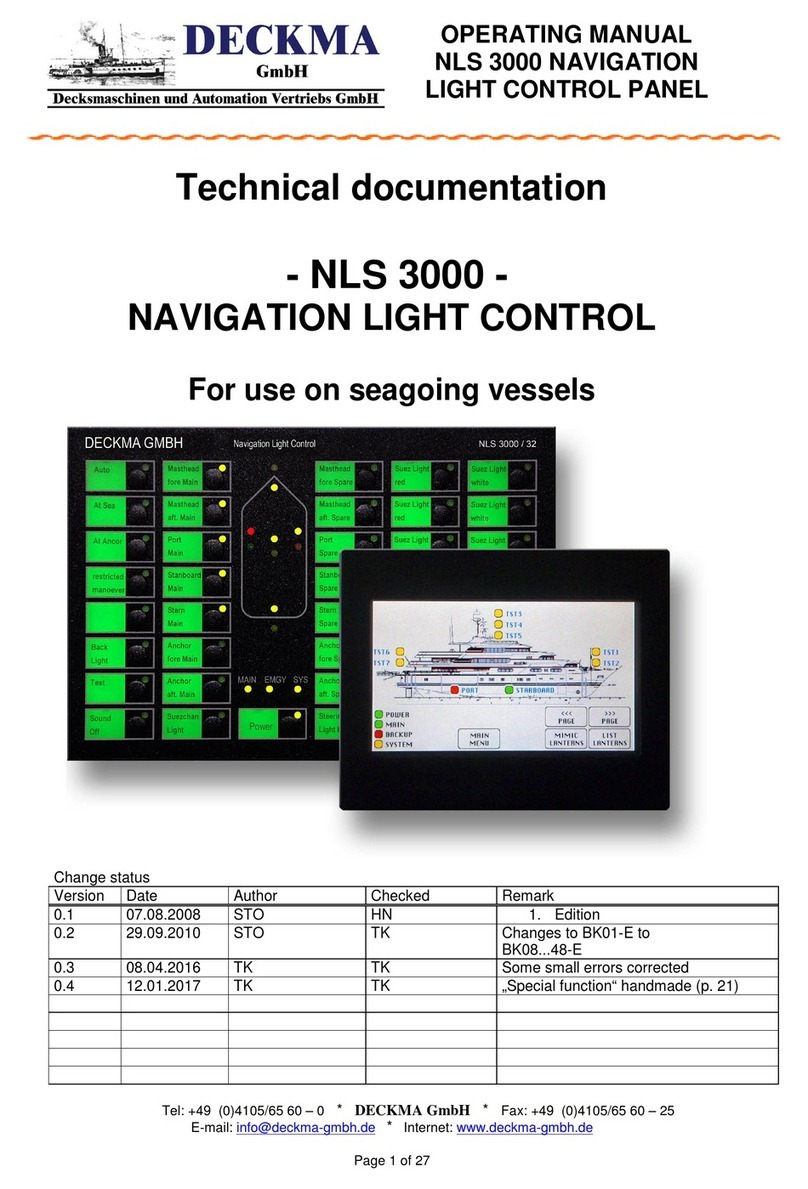
Deckma Hamburg
Deckma Hamburg NLS 3000 Technical documentation
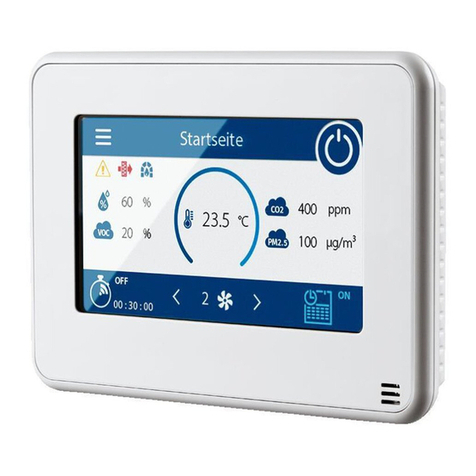
BLAUBERG Ventilatoren
BLAUBERG Ventilatoren S25 user manual

Vertiv
Vertiv Liebert DPM user manual
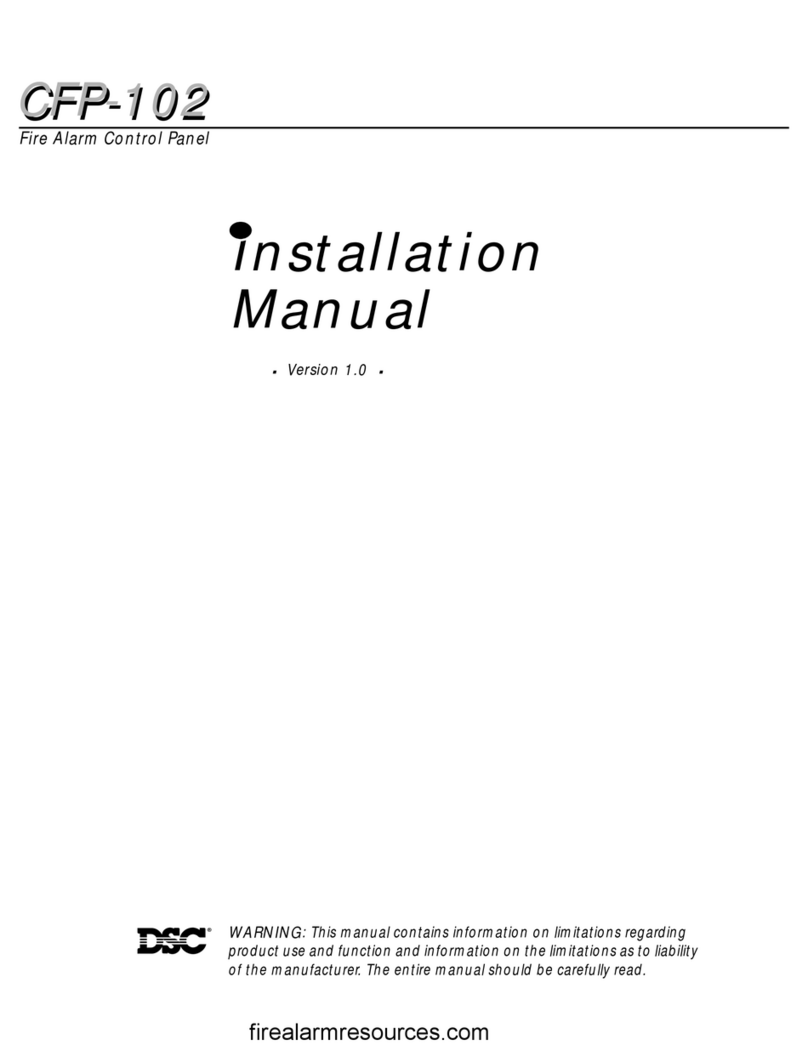
DSC
DSC CFP-102 instruction manual