Milltronics HydroRanger I User manual

HYDRORANGER I
PROCESS MEASUREMENTS
PROGRAMMABLE LEVEL SYSTEM
Instruction Manual
PL-399
May 1993
33453990

Table of Contents
I GENERAL INFORMATION
Important 1 – 1
HydroRanger I 1 – 1
II SPECIFICATIONS
HydroRanger I 2 – 1
Programmer 2 – 2
Transducer 2 – 2
Alternate Temperature Sensor 2 – 3
Current Output Isolator 2 – 3
Cabling 2 – 3
III INSTALLATION
HydroRanger I 3 – 1
Transducer 3 – 1
Programmer 3 – 1
Current Output Isolator 3 – 2
Interconnection 3 – 2
Synchronization 3 – 2
Internal Checks 3 – 3
IV START-UP
General 4 – 1
Programmer Keypad Summary 4 – 2
Parameter Entry 4 – 3
Display Messages 4 – 6
V FUNCTIONAL
Transceiver 5 – 1
Transducer 5 – 1
Damping and Process Rate 5 – 1
Temperature Compensation 5 – 2
Sound Velocity 5 – 3
Blanking 5 – 3
Agitator Discrimination 5 – 4
Relays 5 – 5
Analog Output 5 – 10
VI APPLICATIONS
Simple Level Application 6 – 3
Example 1
Pump Control Application 6 – 7
Example 2
i

Pump Run-on 6 – 10
Pump Totalizer Application 6 – 13
Example 3
Volume Application 6 – 17
Example 4
Differential Level Application 6 – 25
Example 5
OCM Application 6 – 29
Example 6a
Other 6 – 41
Example 6b
Applications with Standpipes 6 – 44
Example 7
VII PARAMETER DESCRIPTION
Parameters 7 – 1
VIII TROUBLESHOOTING
Oscilloscope 8 – 1
Troubleshooting guide 8 – 4
IX MAINTENANCE AND SPARE PARTS
Maintenance 9 – 1
X APPENDICES
Sound Velocities 10 – 1
Glossary 10 – 2
Alphabetical Parameter Listing 10 – 4
Illustrations
Fig. 1 HydroRanger I Outline and Mounting Diagram
Fig. 2 Circuit Board Layout
ii

SECTION I
GENERAL INFORMATION
IMPORTANT
First and foremost, it is essential that this manual be read and understood before
installation and start-up of the HydroRanger I.
Section VI, Applications, provides a general description of the common applications
found in industry and illustrates them with examples. It is suggested that you refer to
the sub-section which most suits your application. The calibration may be further
optimized by referring to Section VII, Parameter Description or Appendix III,
Parameter Listing.
The HydroRanger I
The Milltronics HydroRanger I is a multi-purpose level monitoring system consisting of a
HydroRanger I in a watertight enclosure, a programmer and a transducer.
The HydroRanger I emits an ultrasonic pulse via the transducer. The echo is reflected
from the material and received by the transducer. The echo is processed by the
HydroRanger I and the time at which the ultrasonic pulse hits the level or target is
extracted and compared to the time at which it was sent. This time differential is then
converted into distance, material level, volume flow or differential level as a basis for
display, relay control, analog output and totalizing.
As well as simple level measurement, the HydroRanger I was designed to handle
specific applications such as: pump control, pumped volume totaling, differential level
and open channel flow measurement.
■
PL-399 1 – 1

SECTION II
SPECIFICATIONS
HydroRanger I
Power » 100/115/200/230 V ±15%, stab selectable
» 50/60 Hz, 15 VA
» optional : » 12 V DC model, 10 to 18 V DC
» 24 V DC model, 18 to 36 V DC
Fuse » 1/4 amp MDL Slo-Blo or equivalent
Range » 0.3 to 10 m (1 to 33 ft.)
Accuracy » 0.25% of range or 6 mm (0.24"),
whichever is greater
Resolution » 0.1% of range or 2 mm (0.08"),
whichever is greater
Memory » EEPROM (non-volatile) no back-up
battery required
Display » Liquid Crystal Display
4 digits - 18 mm (0.7") high
Operating Temp. » -20 to 60 °C
(range in which electronics will (-5 to 140 °F)
operate within specs, includes
temperature rise above ambient
due to operation in enclosure.)
Ambient Temp. » -20 to 50 °C
(range outside of (-5 to 122 °F)
HydroRanger I enclosure)
OUTPUTS:
transducer drive » 41 KHz, 400 V peak pulses of 1 mSec. max.
duration at a max. repetition rate of 300 mSec.
analog » 0 - 20 or 4 - 20 mA
» max. loading: 350 ohms, return to ground
750 ohms, return to -12 V
» resolution: 0.1% of range
» optional mA isolator
PL-399 2 – 1

relays » 5 multi-purpose relays (for alarms, pump control, ...)
» 1 Form ’C’ SPDT contact per relay, rated
5 A at 220 V AC non-inductive
» adjustable deadband
NOTE:
All relays are certified for use in equipment where the short circuit
capacity of the circuits in which they are connected is limited by fuses
having ratings not exceeding the rating of the relays.
Enclosure » CSA type 4 (NEMA 4/ IP 65 style)
» 160 mm W x 240 mm H x 82 mm D
(6.3" W x 9.5" H x 3.2" D)
» polycarbonate
Weight » 1.8 Kg (4 lb)
Programmer
Enclosure » general purpose
» 67 mm W x 100 mm H x 25 mm D
(2.6" W x 4" H x 1" D)
» ABS plastic
Operating Temp. » -20 to 50 °C
(-5 to 122 °F)
Battery » 9 V (ANSI/NEDA 1604, PP3 or equivalent)
Transducer
Model » ST-H with integral temperature sensor
Construction » 1" NPT conduit thread with standard 10 m (33 ft)
of neoprene jacketed cable.
» 2" NPT, 2" BSP or PF2 mounting thread
» Tefzel®encapsulated
Operating Temperature » -40 to 73 °C (-40 to 165 °F)
Pressure (vessel) » 200 kPa (2 bar or 30 psi) max.
Beam Angle » 12°
PL-399 2 – 2

Options » Flange Adapter Kit. Refer to PL-397.
» Submergence Coupling. Refer to PL-403
Temperature Sensor (Optional)
Model: » TS-3
Refer to associated Temperature Sensor Manual, PL-401.
Current Output Isolator (Optional)
Model: » LIs-1 loop isolator
Refer to associated Current Output Isolator manual, PL-293.
Cabling (Optional)
Transducer » RG-62U coax
» max. distance to electronics: 336 m (1200 ft.)
» must be run in grounded metal conduit
Temp. Sensor » Belden 8760, 2 wire shielded
» max. distance to electronics: 336 m (1200 ft.)
» can be run with transducer cable.
TEFZEL
Tefzelis a fluoropolymer inert to most chemicals. For exposure to specific
environments, check with chemical compatibility charts before installing and operating
the HydroRanger I in your application.
Tefzelis a registered trade mark of Dupont.
■
PL-399 2 – 3

SECTION III
INSTALLATION
HydroRanger I
The HydroRanger I should be mounted in an area that is within the unit’s ambient
temperature range and is suitable for the specified enclosure. The front cover should be
accessible for calibrating and viewing.
It is advisable to keep the HydroRanger I away from high voltage or current runs,
contactors and SCR control drives.
DO NOT MOUNT THE HydroRanger I
IN DIRECT SUNLIGHT
WITHOUT THE USE OF A SUN SHIELD
Refer to Figure 1 for outline and mounting dimensions.
Transducer
NOTE: Wiring of transducer cable must be done in conjunction with approved
conduit, boxes and fittings and to procedures in accordance with all
governing regulations. All transducer cabling must be run in grounded
metal conduit for optimum noise rejection. Refer to Figure 4 for outline
and wiring.
1. Mount the transducer above the highest anticipated material level by at least
30 cm (1 ft).
2. Install the transducer so that it can have a clear sound path perpendicular to
the liquid surface.
3. To avoid false echoes, install the transducer such that the sound path will
not intersect vessel fill spouts, rough vessel walls, ladders ... etc. Where
possible, the transducer should be mounted 0.3 m (1 ft) from the closest
vessel wall for every 3 m (10 ft) of depth.
Example: if the vessel is 10 m deep, the transducer should be mounted
at least 0.3 m/3 m x 10 m = 1.0 m from the closest vessel wall.
Programmer
In order to calibrate the HydroRanger I, a programmer must be set into the recess on
the HydroRanger I front cover. It can be removed when operating in the RUN mode.
(Note: since a programmer need not be ordered with each unit, check your order if you
think that the programmer is missing).
PL-399 3 – 1

Current Output Isolator
The isolator is mounted onto the upper left hand corner of the motherboard using the
two long machine screws provided. It is then interconnected from its input terminals to
the motherboard output terminals, TB-1, using twisted pair maximum 16 ga. wire. Refer
to Figure 2 and 3.
Proper shielding and grounding are required in order to minimize noise levels that could
otherwise affect weak receiver signals by introducing false echoes.
The isolator enclosure is grounded by the mounting bolts to the motherboard. This can
be checked with an ohmmeter if a poor connection is suspected.
THE ISOLATOR OUTPUT WIRING MUST BE A SHIELDED TWISTED PAIR. THE SHIELD MUST BE
INTACT UP TO THE ISOLATOR AND THE SHIELD GROUNDED AT THE ISOLATOR MOUNTING
SCREW ONLY. DO NOT GROUND SHIELD AT ANY OTHER POINT AS THIS WILL VOID ISOLATION.
Interconnection
NOTE: All wiring must be done in conjunction with approved conduit, boxes and
fittings and to procedures in accordance with all governing regulations.
Refer to Figure 2 for wiring of power, analog output, transducer and temperature sensor
to the main electronics.
Synchronization
In applications where more than one HydroRanger I, up to a maximum of 8, are going
to be used or where their transducers will be sharing a common conduit,
synchronization is required. When synchronized no HydroRanger I(s) will transmit
within 180 mSec. of the prior one(s).
To synchronize HydroRanger I’s, interconnect the SYNC terminals TB1-4 of all
motherboards and ensure that there is a common hydro ground interconnecting
all units.
To synchronize HydroRanger Is and MultiRanger Plus’s interconnect the SYNC
terminals TB1-4 of all motherboards and ensure that there is a common ground
interconnecting all units.
To synchronize HydroRanger I’s and MultiRangers, interconnect the SYNC terminal
TB1-4 of the HydroRanger I to the SYNC terminal TB1-9 of the MultiRanger.
To synchronize more than 8 MultiRangers or MultiRangers with other Milltronics
ultrasonic level detection models (e.g. MicroRanger, AiRanger, etc. ...), consult
Milltronics or your distributor.
Refer to Figure 3 for details on synchronization wiring.
PL-399 3 – 2

Internal Checks
•If the integral ST-H temperature sensor is not used, jumper ‘J2’ must be
set to ‘TS/P65’.
•Make sure that voltage stab connector, ‘J9’, is properly set for either 100,
115, 200 or 230 V AC operation.
•One fuse, 1/4 Amp, must be installed.
•Make power connection. Be sure that wires are securely fastened and to
proper terminals,
do not operate with grounding (earthing) wire disconnected.
■
PL-399 3 –3

SECTION IV
START-UP
General
The HydroRanger I has two modes of operation: RUN and CALIBRATE. When the unit
is powered up, after installation procedures have been completed, it is factory set to
start-up in the run mode, to detect the distance from the transducer face to the target in
meters. This is the normal mode of operation, which can be programmed to display
level, volume, totals or flow readings and yield corresponding mA output and relay
closures for alarms, pump controls, etc.
The CALIBRATE mode is selected by pressing the RUN/CAL keypad switch. This
mode will enable the user to calibrate the HydroRanger I to suit his preferences and to
the particular application to which the HydroRanger I is being be applied.
NOTE
The first step when calibrating is to reset all parameters to their
factory setting by using the master reset P-99.
After having entered all the required parameters, the HydroRanger I can be made to
simulate its operation within the particular application giving display, relay operation and
analog output. Refer to parameters P-76 through P-78.
When calibration has been completed, the HydroRanger I can be put into normal
operation by pressing the RUN/CAL keypad switch.
Unsatisfactory response in the run mode, after calibrating, may indicate that the
transducer aiming requires adjustment.
PL-399 4 – 1

Programmer Keypad Summary
—
Calibrate mode: numeric entries
Run mode: 1 = H.TOT; press to view high total, P-2 = 4 or 5 (P-55)
press to view level at DLD transducer #1, P-2 =3
2 = L.TOT; press to view low total, P-2 = 4 or 5 (P-54)
press to view level at DLD transducter #2, P-2 =3
3 = HEAD; press to view head reading, P-2 = 5
4 = FLOW; press to view flow rate, P-2 = 5
5 = mA; press to view mA output
6 = TEMP; press to view temperature (P-65)
7 = RATE; press to view rate of level change (P-70)
8 = CONF; press to view echo confidence (P-80)
9 = HRS 1; press to view pump 1 running time (P-24)
0 = HRS 2; press to view pump 2 running time (P-25)
Calibrate mode: decimal point entry
Run mode: HRS 3; press to view pump 3 running time (P-26)
Calibrate mode: negative entry
Run mode: HRS 4; press to view pump 4 running time (P-27)
Calibrate mode: clears display
Run mode: HRS 5; press to view pump 5 running time (P-28)
Calibrate mode: used to initiate parameter display after having entered
the calibrate mode or used to calibrate for percent reading
Run mode: READ; press to view reading (P-76)
Alternates operating modes
Calibrate mode: press to take a measurement
Run mode: press to view distance (P-78)
advance to next parameter
go back to previous parameter
1 9
.
—
CLR
*
RUN
CAL
MEAS
↑
↓
PL-399 4 – 2

alternates display to show either the parameter number or parameter
contents
enters display as contents of selected parameter
Parameter Entry
Initial Start-Up
NOTE All entries are made via the calibrator keypad. All calibrators are
interchangeable, thus any calibrator can be used in conjunction with any
HydroRanger I. The term “key” refers to any keypad switch of the
calibrator.
1)Apply power to the HydroRanger I and place the calibrator in its front cover
recess
run will be momentarily displayed and then a distance reading corresponding to
the parameter factory settings will appear. This is a space or distance
reading of up to approximately 12 m.
If ’CAbL’/’LOE’ is alternately displayed, an open, short circuited or reversed
polarity transducer connection is being indicated.
If LOE is displayed rather than a continuous numeric reading the actual
material distance may be beyond 12 m. Proceed with the calibration and if
LOE persists, consult the troubleshooting guide, Section VIII.
2)press
CAL will be displayed
3)press
P-1 will appear
NOTE: the CAL display will revert to the run mode if is not pressed within a
minute and a half of initially pressing the CAL switch.
The user may now program the HydroRanger I.
ALT
DSP
ENTER
RUN
CAL
*
*
PL-399 4 – 3

Parameters are entered as follows:
With ’P-#’ displayed, the user may increment or decrement the displayed parameter
until the desired parameter is obtained or access the desired parameter directly by
pressing the appropriate numbers on the keypad.
e.g.’P-1’ is displayed, P-27 is desired.
Press and then .
P-27 will be displayed.
If the wrong switch is depressed, press to clear the parameter display and the
desired numbers again selected.
Setting Parameters:
Once the desired parameter has been obtained on the display,
Press
this will cause the display to show the contents of the selected parameter.
The contents may be changed to a new value or code by pressing the de-
sired numbers and then .
NOTE: after a minute and a half, the contents display will revert to the parameter
number if the keypad is not further used. Press again if desired to
return to display of contents.
e.g. P-1, units, is displaying a value of ’2’ (cm); 1-% (% meters) is desired
press
and then
1P will be displayed
press
1P will momentarily flash off to indicate that it has been entered.
2 7
CLR
ALT
DSP
ENTER
ALT
DSP
1 *
ENTER
PL-399 4 – 4

To set the next parameter:
press
the next parameter will be displayed momentarily, followed by a display of
its contents. The contents may be changed as previously described.
To directly access a parameter:
press
P-#
will be displayed
enter desired parameter number
press
the contents of this parameter are now displayed and may be changed as
previously described.
To reset a parameter to its factory value:
select the desired parameter
press
present contents will be displayed
press
display will go blank
press
factory setting of selected parameter is displayed and automatically
entered.
↑
ALT
DSP
ALT
DSP
ALT
DSP
CLR
ENTER
PL-399 4 – 5

Display Messages
Display Message
Comment
cable loss of echo » messages CAbL and LOE
will alternately flash, indicating
open, short circuited or
reversed transducer connection
have entered calibrate
mode
» appears after pressing
“RUN/CAL” switch
clear all parameters -
return factory setting
»P-99
overflow » reading is larger than display
capabilities
loss of echo » displayed in run mode to
indicate loss of echo
percent » appears when calibrating units
of measurement in percent
parameter number » indicates which parameter is
being displayed
have entered run mode » appears after pressing
“RUN/CAL” switch
no value » contents of parameter empty
or no reading display
invalid request » application does not yield
requested reading option or
spare parameter
CAbL LOE
CAL
C.ALL
EEEE
LOE
#P
P-#
run
- - - - -
PL-399 4 – 6

SECTION V
FUNCTIONAL
Transceiver
The HydroRanger I transceiver will transmit a set of long and/or short pulses per
measurement. The number and duration of the pulses is dependent upon P-88.
A short pulse has a maximum measurement range of 2 m (6.6 ft) from the transducer
face and the CABLE LOE message does not work.
A long pulse has a measurement range of 2 m (6.6 ft) from the transducer face out to its
maximum setting (P-3, empty distance to transducer plus P-87, range extension).
Submergence detection (P-23) does not work with a long pulse.
Transducer
The HydroRanger I is designed to work in conjunction with the ST-H series of
transducers with integral temperature sensor.
The transducer converts the electrical energy of the transmit pulse from the transceiver
into acoustical energy and converts the acoustical energy of the echo back into
electrical energy for the transceiver receive period.
The effective acoustical energy is generated from the face of the transducer and is
radiated outward, decreasing in amplitude at a rate inversely proportional to the square
of the distance. Maximum power is radiated axially (perpendicular) from the transducer
face in a line referred to as the axis of transmission. Where power is reduced by half
(-3 dB), a conical boundary defining the sound beam, centered about the axis of
transmission is established. The diametric measurement of the cone in degrees
defines the beam angle and varies according to the transducer type.
Impedance matching is used to optimize the transfer of power from the transducer into
air and from the air back into the transducer.
Damping and Process Rate
The HydroRanger I provides damping to control the maximum rate of change of the
displayed material level, volume or flowrate and of the mA output signal. As most relay
functions respond to the dampened level reading, they indirectly fall under the control of
the damping function. Damping may be set within the range of 0.001 to 9999 in units
selected per minute (e.g. if P-1 = 3 and P-68 = 15, then the fill damping rate is 15
ft/min). P-68 is set to provide damping specifically for filling conditions while P-69 is set
to provide damping specifically for emptying conditions.
The required damping may be estimated by filling and emptying the vessel at its normal
rate. The rate of material level change can be viewed via process rate display
PL-399 5 – 1

parameter, P-70 or by pressing the “7" calibrator key while in the RUN mode. The
amount of P-68 and P-69 damping should be equal to or greater than the rates of level
change encountered in P-70. The process rate averaging parameter P-71 selects the
method of averaging used to determine the process rate display, however it has no
bearing on the damping function.
Damping is often used to slow down the rate of response of the display especially
where liquid surfaces are in agitation or material falls into the sound path during filling.
When in the calibrate mode, the damping is automatically overridden to give fast
response when “MEAS” is pressed. In the RUN mode, the response can be further
increased by turning the fuzz filter (P-72) and agitator discriminator (P-73) OFF - ONLY
if they are not required.
If the transducer aiming is being adjusted while in the run mode, it is suggested that
damping be at its factory setting of 10 to start. The damping can later be changed to
suit prevailing conditions.
Upon a loss of echo condition and after the fail-safe timer (P-75) expires, the display will
go to fail-safe high at the fill damping rate if P-74 = 1 or to fail-safe low at the empty
damping rate if P-74 = 2.
Temperature Compensation
In order to provide compensation for uniform temperature variances of the sound
medium, temperature compensation is provided. Temperature compensation consists
of on board circuitry in the HydroRanger I and the integral ST-H temperature sensor.
The integral temperature sensor uses the transducer’s wiring and input terminals (TB1 -
8/9) to interface with the on board circuitry. Note: jumper ‘J2’ must be set to ‘TRANS’.
Optionally, the alternate TS-3 Temperature Sensor can be used to provide a
temperature input, rather than by using the integral temperature sensor.
In order to do this:
» set jumper ‘J2’ to ‘TS/P65’
» optional TS-3 Temperature Sensor must be connected to TB1 - 5/6/7
If the temperature of the sound medium is to remain constant, compensation may be
programmed into the HydroRanger I instead of using the remote sensor input by one of
the following methods:
1. » set jumper ‘J2’ to ‘TS/P65’
» insure that the temperature sensor input TB1 - 5/6 is left open/unconnected
» select P - 65
» enter temperature in °C
2. » set jumper ‘J2’ to ‘TS/P65’
» insure that the temperature sensor input TB1 - 5/6 is left open/unconnected
PL-399 5 – 2

» select P - 61
» perform an empty calibration
The following temperature functions (in °C) can be viewed:
P-65 air temperature: » present temperature at sensor
or
» preset temperature, if sensor not used
P-66 max. air temperature: » highest temperature encountered
during operation
P-67 min. air temperature: » lowest temperature encountered
during operation
Sound Velocity
The HydroRanger I can be calibrated to compensate for transducer operation in
homogenous vapours with sound velocities other than that of air.
The basis is to physically measure the level (measuring tape or sight glass) and enter
this value via P-61. The HydroRanger I then calculates the sound velocity by
comparing the entered physical measurement to its own ultrasonic measurement
(empty calibration, P-61).
P-63, velocity at 20°C, can be used to enter the known velocity at 20°C of sound in a
particular gas or vapour or to view the resultant velocity of a sound velocity
compensation, normalized to 20°C.
P-64, velocity at P-65, can be used to enter the known velocity at the temperature of
P-65 of sound in a particular gas or vapour or to view the resultant velocity of a sound
velocity compensation, at the temperature of P-65.
Refer to Appendix I, for typical sound velocities in various gases and vapours.
Blanking
Near blanking (P-5) is used to ignore the zone in front of the transducer where ringing
or other false echo is at a level that interferes with the processing of the true echo.
Ringing is the inherent nature of the transducer mass to continue vibrating after the
transmit pulse has ceased. The amount of ringing varies with the type of transducer
used and decays to acceptable levels in the order of milliseconds. Excessive cold and
overtightening of the transducer mounting (refer to Figure 6) will increase the ring time
such that it may appear as an echo during the receive cycle. This is usually indicated
by an incorrect high level reading. This condition may be verified with the use of
an oscilloscope (refer to Section VIII) and may be overcome by increasing the
near blanking.
PL-399 5 – 3

Far end blanking is a design function that ignores the zone below the zero or empty
level where false echoes may appear at levels that interfere with the processing of the
true echo.
In applications where the zero level is above the bottom of the vessel and it is desired
to monitor the zone below the normal zero, range extension (P-87) may be used to
extend the range into the far end blanking. Range extension is entered as a percent of
P-3. As range extension reduces the protection afforded by the far end blanking,
it should be used judiciously. Avoid excessive range extension as this may
reduce the measurement’s reliability and accuracy. As range extension is factory
set for 20% of P-3, if it is found that false echoes are appearing ahead of the blanking
zone, P-87 should be reduced accordingly.
Blanking is automatically corrected for sound velocity change where temperature
and/or velocity compensation are used, keeping the blanking at the distance at which
it was entered.
Agitator Discrimination
In applications where there is an agitator operating in the vessel, the blades may
interfere with level readings when the material level is lower than the blades. In such a
case, the agitator discriminator (P-73) can be turned on (factory setting).
With the agitator turned on, the reading will not change unless the echo is closer for at
least 5 consecutive measurements nor will it change unless the echo is farther for at
least 2 consecutive measurements.
This feature allows the HydroRanger I to remain locked on the true echo, even if there
are occasional false echoes due to the agitator blades, electrical noise or crosstalk from
other ultrasonic units.
ringing true echo
(level)
false echo
typical receiver signal
P-5
near blanking
far end
blanking
typical processed signal
0
level
end of
transmit
range extension (P-87)
as % P-3
empty distance to transducer
P -3
range
PL-399 5 – 4
Table of contents
Other Milltronics Measuring Instrument manuals
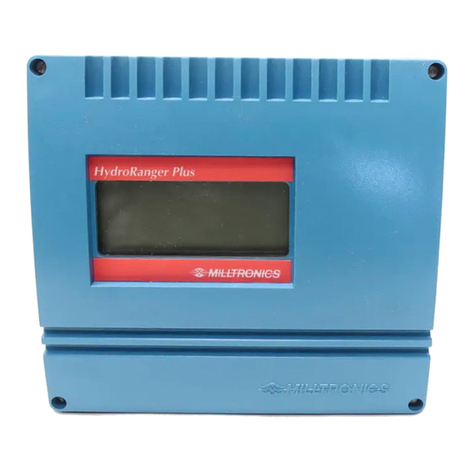
Milltronics
Milltronics HydroRanger Plus User manual

Milltronics
Milltronics ILE-37 User manual
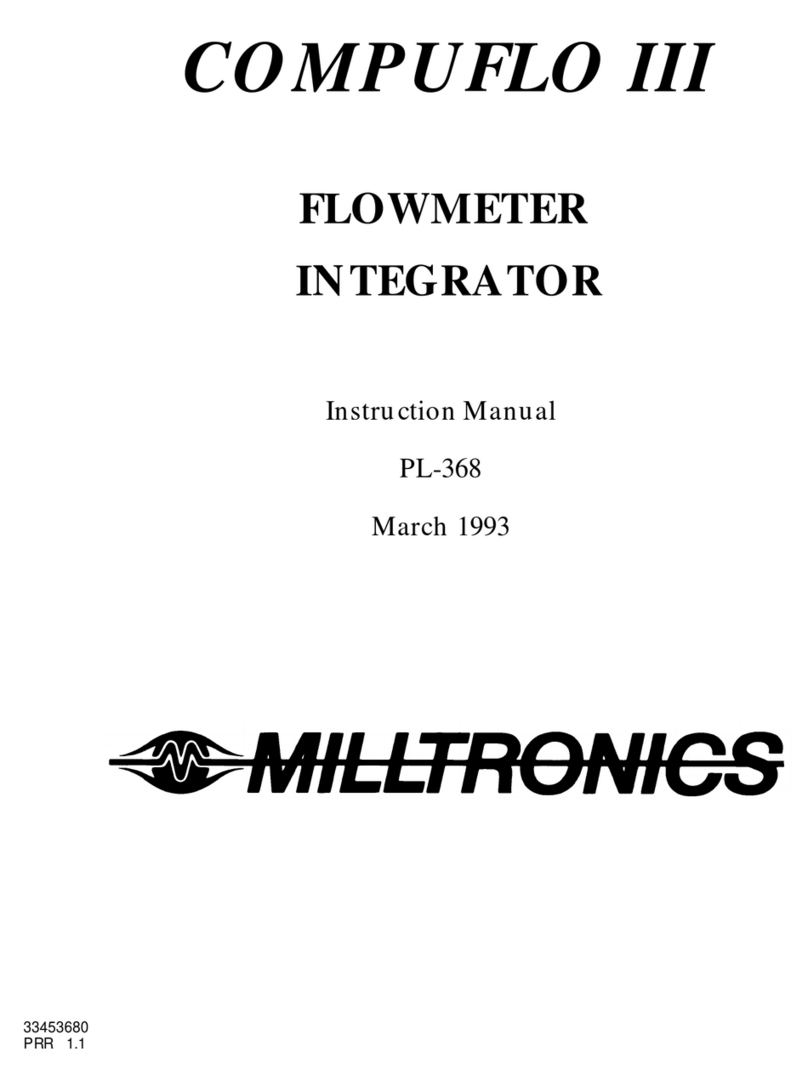
Milltronics
Milltronics COMPUFLO III User manual
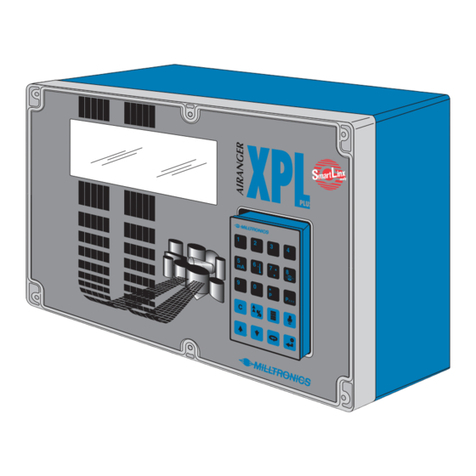
Milltronics
Milltronics airanger XPL plus User manual
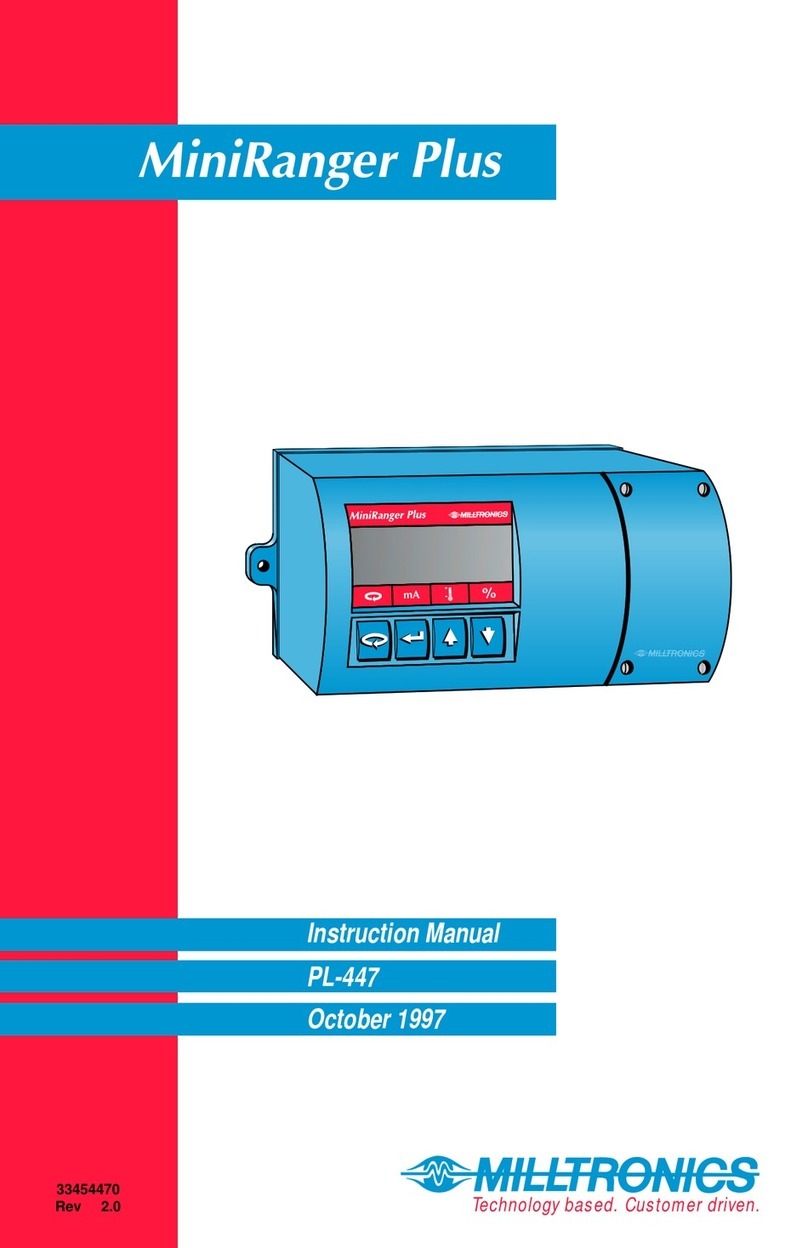
Milltronics
Milltronics miniranger plus User manual
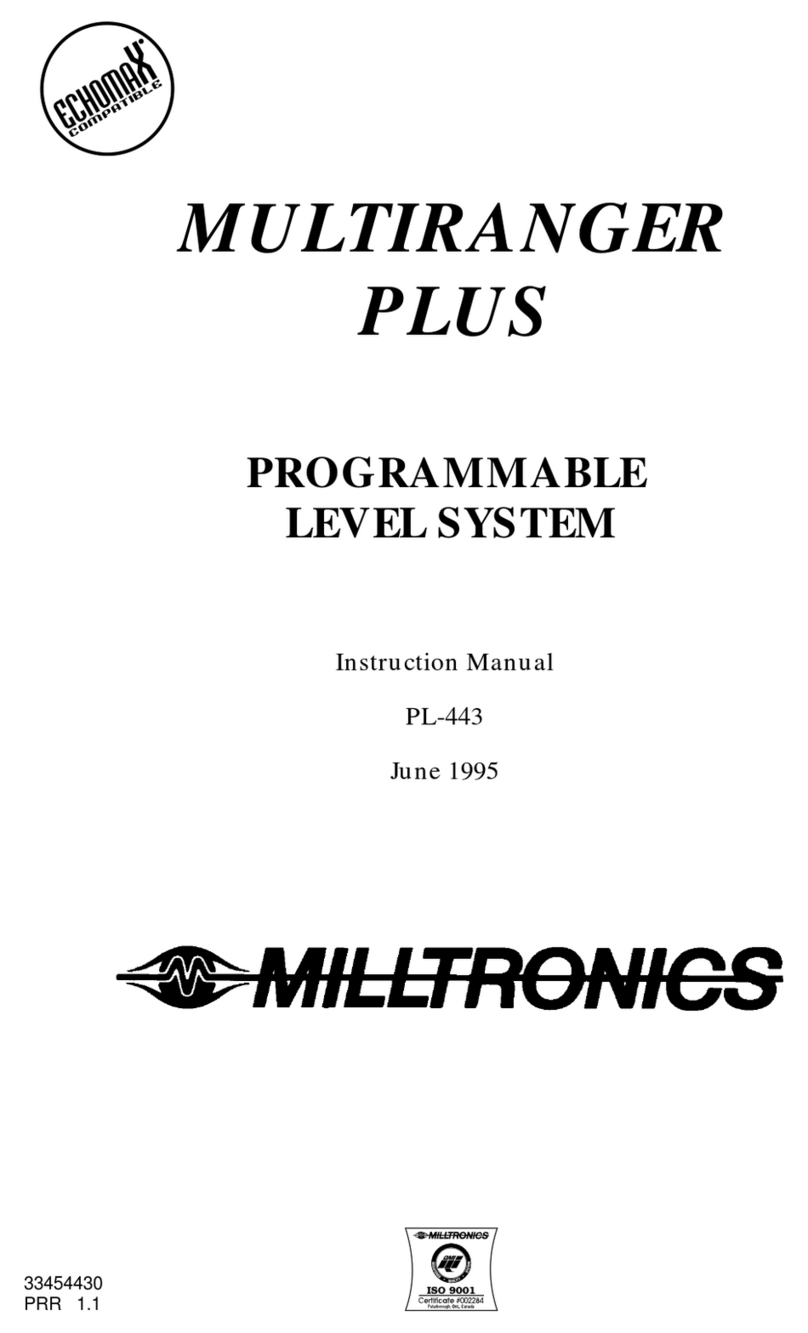
Milltronics
Milltronics MultiRanger Plus User manual
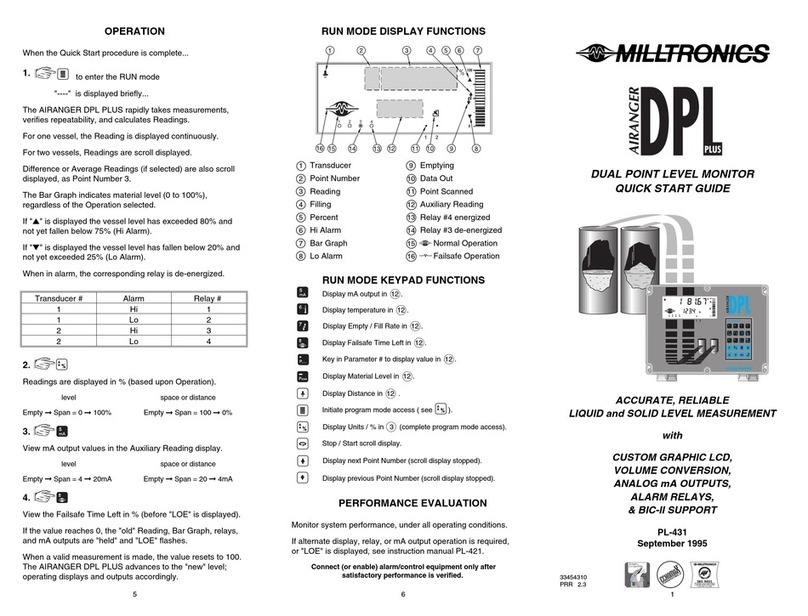
Milltronics
Milltronics AIRANGER DPL PLUS User manual
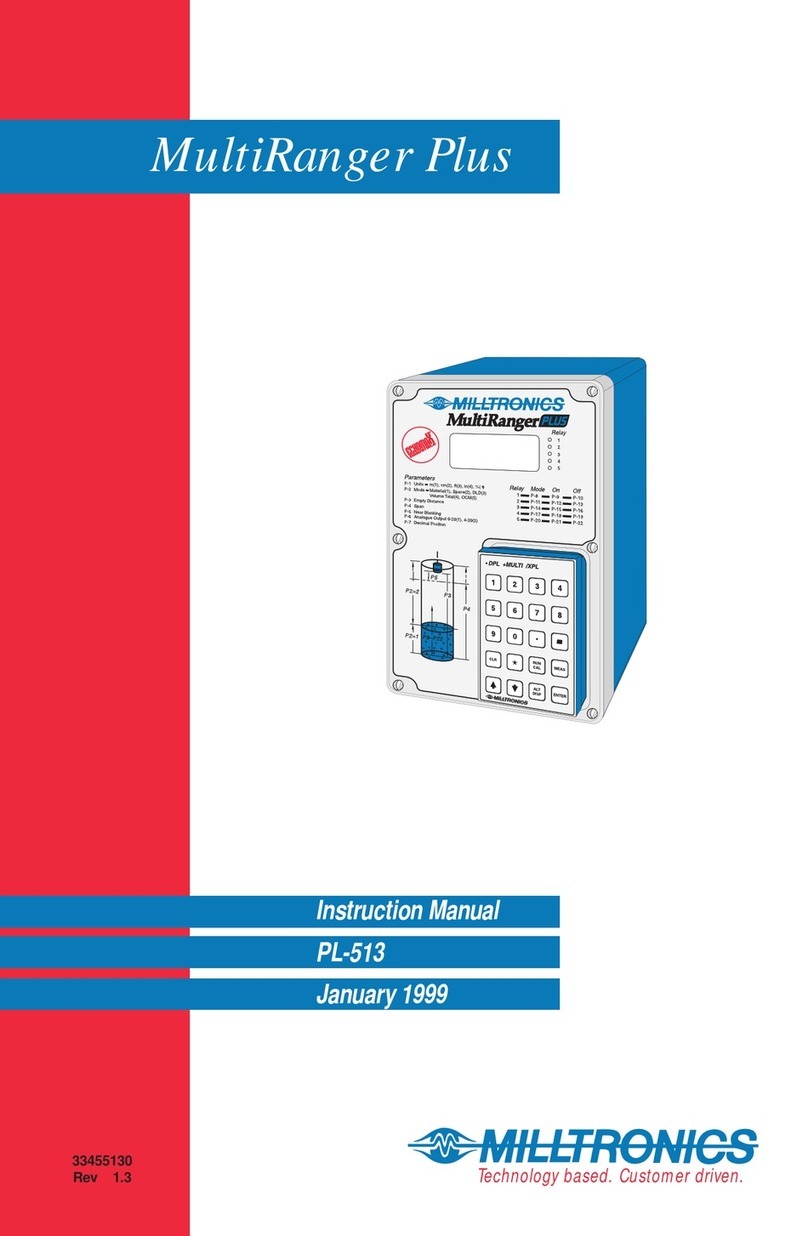
Milltronics
Milltronics MultiRanger Plus PL-513 User manual

Milltronics
Milltronics IQ Radar 160 User manual
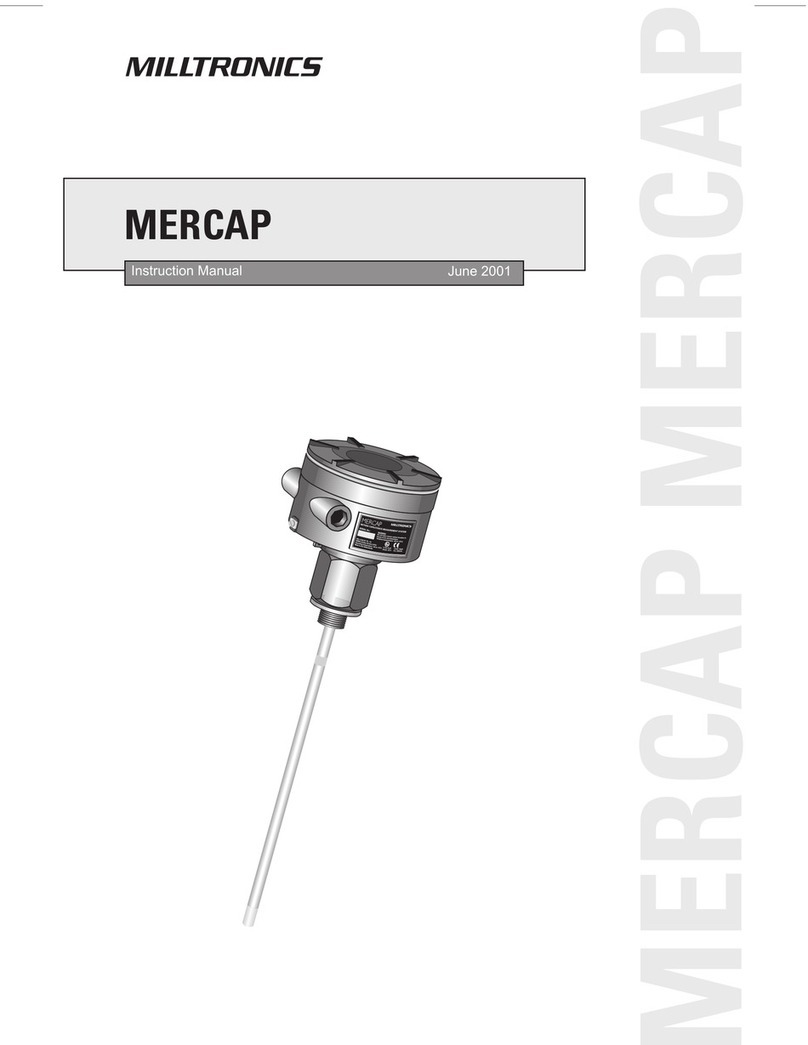
Milltronics
Milltronics Mercap MCP01 S series User manual