Mintech MC-1250 User manual

1
/
36
Mintech
MC-1250
Operating manual

2
/
36
Please read Chapter Three carefully and all requirements
should be strictly observed.
It is strongly recommended that the users read this manual and
in particular Chapter One, safety instructions and precautions,
before operating the machine.
Do not use the machine in condition of opening the door of
the control cabinet.
Every effort has been made to ensure that the data given in this
document is accurate. The information, figures, tables,
specifications and schematics contained herein are subject to
change without notice. Should you experience any difficulties
with your machine or need any technical information, please
contact with our company.
Notice

3
/
36
Chapter One: Safety Instructions and Precautions
Chapter Two: general description
Chapter Three: Installation and Utility Requirements
Chapter Four: Operation
Chapter Five: Maintenance and Troubleshooting

4
/
36
Chapter One
1.1 General Information
1.2 Laser Safety
1.3 Safety
Instructions
in Operation
1.4 Safety
Instructions
in Maintenance

5
/
36
1 Safety Instructions and Precautions
It is strongly recommended that any personnel who are
involved with the operation or maintenance of this
equipment should first read the contents of this manual.
Only authorized personnel who have been instructed in
and fully understand the necessary safety procedures
must use this equipment.
1. 1 General Information
1.1.1 Symbols Used in This Manual
This symbol is intended to alert the operator to the
presence of dangerous voltages that may be of
sufficient magnitude to constitute a risk of electric
shock.
This symbol is intended to alert the operator to the
presence of important operating and maintenance
instructions.
This symbol is intended to alert the operator to the
danger of exposure to hazardous visible and invisible
laser radiation.

6
/
36
1.1.2 Some important instructions:
1325/1530 is using laser to cut. Laser light, because of its special
properties, poses safety hazards not associated with light from other
sources. The safe use of lasers requires that all laser users and
everyone near a laser be aware of the dangers involved in laser
operation.
Don' t touch any switches by wet hand in order not to get an electric
shock.
Don't touch the drive device, power supply, the fan and other
electriferous elements when power on.
Ensure that untrained personnel do not open the cover board over the
laser and the protective covering over the beam path, or focus the
cutting head and adjust the beam delivery optics.
1.2 Safety instruction about the laser
This laser is a Class 4 laser product (there are warning
labels on the laser unit and the beam path). The energy
density of the beam is high and the wavelength of the
output beam can be in the range 10.4μm to 11.2μm.
The wavelength range is invisible to the human eye,
and never look directly into the light source or
scattered laser light from reflective surfaces when
adjusting the beam delivery optics and machining.
All personnel must wear safety spectacles. If laser
radiation is exposed to the skin it can burn and cut the
flesh.
Do not cut the high reflectivity materials.
1.2.1 Optical Safety
Laser light, because of its special properties, poses safety hazards not

7
/
36
associated with light from other sources. The safe use of lasers requires that all
laser users and everyone near a laser be aware of the dangers involved in laser
operation. Only authorized personnel who have been instructed in and fully
understand the necessary safety procedures must use this laser equipment. Any
warning signs around the area where is operating must be complied with.
Direct eye contact with the output beam from the
laser will cause serious damage and may cause
blindness.
Avoiding Laser Radiancy
ensure that the beam is not directed towards reflective objects, and
that laser light cannot escape through windows. (not that personal
jewelry is a potential hazard.)
interaction of the beam with certain materials can cause potentially
harmful levels of visible radiation to be emitted. Appropriate
protective measures must be taken in this case.
All personnel in the same room as the laser or anyone who may be
exposed to the laser beam should be informed that a laser is in
operation.

8
/
36
Safety precautions
Exercise caution to protect against specular reflections since reflections at
the laser wavelength are invisible.
Eye safety is great concern when using a high-power laser. There are often
many secondary beams present at various angles near the laser. These beams
are specular reflections of the main beam from polished surfaces. While weaker
than the main beam, such beams may still be sufficiently intense to cause eye
damage. Laser beams ar also powerful enough to burn skin, clothing or paint.
They can ignite volatile substances such as alcohol, gasoline, ether, and other
solvents and can damage the light-sensitive elements in videp cameras,
photomultipliers, and photodiodes.
Use protective eyewear when operating the laser and guard against
inadvertent exposure to skin or clothing. Select eyewear which is
suitable for use with the wavelengths and radiation intensity that the
laser emits.
Do not remove the protective covering over the beam path. During
normal operation, internal reflections are confined within the laser head
and pose no safety hazard.
Never look directly into the laser output port when the power is on.
Only authorize personnel who have been instructed in and fully
understand the necessary safety procedures must use this laser.

9
/
36
Avoid operating the laser in a darkened environment.
Do not use the laser in the presence of flammables, explosives, or
volatile solvents such as alcohol, gasoline, or ether.
For additional information on laser safety, refer to the following publications:
American National Standard for the Safe Use of Lasers, Z136.1-1993, American
National Standards Institute, 1993.
Performance Standard for Laser Products. FDA. ( FR-40 ) (148): 32252-32265.
Department of Health, Education and Human Service Bureau of Radiological
Health, July 31, 1974.
Laser safety Guide, Laser Institute of American. (9th Edition). Orlando, FL 1993.
D. Sliney and M. Wolbarsht. Safety with Lasers and Other Optical Sources, Plenun
Publishing Company, New York, N.Y., 1980.
Many of these documents on Laser Safety are available through Laser Institute o
America, 13501 Ingenuity Drive,Suite 128,Orlando,CA 32826。Phone 800-345-
2737 and on their web site www.laserinstitute,org.
1.2.2 Electrical Safety
This equipment contains lethal AC and DC voltages.
These may still be present even when the power is
disconnected.
No electrical hazard exists if the system is operated normally. This
requires the PSU to be properly grounded.
1.3 Safety Requirements in Operation
1.3.1 Safety instructions before starting the machine

10
/
36
The cable that connected with power supply should be long enough and
have damage-protecting external cover.
The numerical control system of this machine has strict
requirements for the input voltage. Manostat is
strongly recommended, to ensure the voltage conform
to the requirements for the voltage.
Ensure that the range of the cooling water temperature is 15℃~30℃
and must higher than the dew point of the air (according to the
environment temperature and humidity). The environment temperature
must be 15℃~28℃ and the relative humidity is not more than 60%.
Switch on the main power supply, water cooler switch, air switch and
the start up switch of the system in order.
1.3.2 Safety instructions when the machine startup
Before power on, ensure machine to be properly
grounded. Otherwise the electrical system will be
damaged.
Check to make sure whether there are some warning indications on the
screen.
Check all the motor and moving parts, to make sure whether there are
some abnormal vibration and noise.
Ensure that the turning of each motor is correct and the wind directions
of the control cabinet and the beam delivery system are outward.
If there are some problems on the machine, you must solve the
problem in time, then begin to work.
1.3.3 Safety instructions during operating the machine

11
/
36
The water cooler system should have been running for ten minutes
before operating the cutting machine. And check the whole water
cooler system, to ensure there are no air bubble in the pipe.
Before operating the cutting machine, check each
parameter setting, to ensure there are no air bubble in the
pipe. Otherwise, Laser pipe will break.
Check to make sure that all the indicators of the laser and laser power
module are all right.
There is a yellow-lamp on the frame of machine. When laser on, the
lamp is turned on.
Simulated run the new program when the laser does not work, and
check to make sure the program logic is correct.
1.3.4 Safety instructions after the machining finished
Press the emergency " stop ", then switch off the main power supply of
the machine, finally, switch off the workshop power supply.
1.4 Safety instructions in maintenance
The maintenance of this laser cutting machine must only be carried out
by trained, professional staff.
The maintenance should be carried out on the condition of power off.
Don't change the position of the limit and the control switches.

12
/
36
Chapter Two
2.1 Introduction
2.2 Technical specification
2.3 Machine structure

13
/
36
2.General description
2.1 Introduction
MINTECH MC-1250/MC-2500 is a brand-new mixing cutting machine which
can cut thin metal, acrylic, wood and other nonmetals.
The machine can come to Chinese tube 100W/130W/ 220W/260W.
MC-1250/MC-2500 with high quality configuration: Here are industrial
standard configuration including fixed beam optical laser system, cutting
following system, Mitsubishi servo system, imported ball screw, water-cooling
system, exhaust-air system, off-computer system so as to guarantee high
precision and reliability meanwhile make the machine more cost-effective!
When cut some materials such as acrylic, some harmful gas, smoke or
powder may be produced. A purge kit (option) is recommended.
The materials for machining or its output gas may be combustible, and
the preventive methods should be adopted.
Do not cut the high reflectivity material which wavelength is 10.6μm
such as copper, gold, aluminum etc.
Do not cut PVC (polyvinyl chloride) with a laser beam. The chemical
heat reaction in combination with the humidity in the air will produce
hydrochloric acid. Hydrochloric acid is hazardous to the operator and
the laser system.

14
/
36
2.2 Technical specification
Model MC-1250
Laser power 150W CO² Sealed Glass
M2- Transverse mode quality M2≤1.1
Worktable dimension 49" x 36"
(1250mm x 900mm)
Workbtable load 330 lbs
(150 kg)
Cutting ability (Acrylic) 1-3/16 inch
(30mm)
Speed of positioning(X,Y) 65.6 ft/min
(20 m/min)
Positioning accuracy (X,Y) ±0.002"/39.4"
(±0.05mm/1000mm)
Repeatability accuracy ±0.002"
(±0.05mm)
Full current 13A
Gross Power ≤ 1500W
Pressure of accessorial gas source 0.6MPa
Operating Temperature
32℉-104℉
(0°C-40°C)
Operating Humidity 5-95%
Data Transfer Interface USB 2.0
System Environment Windows XP/2000/7/8/10
Graphic Format Supported Files CorelDraw Identify (BMP,
JPEG, AI, PLT etc.)
Cooling Type Water Cooling
Overall dimensions(L×W×H)
63" x 68.9" x 47.2"
(1600mm x 1750mm x 1200mm)
Machine net weight 880 lbs
(400kg)

15
/
36
2.3 Machine structure
Laser Cutting Machine (figure 2-1) contains of laser unit, the cutting
machine, control system, water chiller.
Figure 2-1 Laser cutting machine
2.3.1 The cutting machine
The cutting machine consists of the base, worktable, gantry frame, cutting
head and operating panel. The worktable fixed on the base, and the gantry frame

16
/
36
moves on the rails fixing on the base. The laser unit and the cutting head move
on the rails fixing on the gantry frame.
There are four casters under the base. The left is the cabinet containing all
electric components. The right near the back is the vent, connecting it to exhaust
by pipe, thus can vent exhaust gas that cutting made.
The structure of cutting head is shown on Figure 2-2
1. locknut of cutting head 2. locknut 3. lock screw
4. nozzle 5. handwheel
Figure 2-2 The Cutting Head
In order to acquire good cutting quality, we must make laser beam passing
nozzle coaxially without being curtained off, so we need carry out adjustment
of the nozzle.
Adjustment means of coaxial situation:
Rotate four handwheels(5), make the nozzle(4) moving to a right position
and insure laser beam passing nozzle coaxially without being curtained off.
Adjustment means of focus position:
Loosen four lock nuts(2), rotate the bottom of cutting head, the nozzle move
up when rotating deasil, anticlockwise move down, the screw pitch is 1 mm.
Finally lock four nuts(2).
2.3.2 The laser unit and beam delivery system
The laser unit consists of laser head, power supply. This laser can give
you excellent mode quality, fast optical rise times, and high peak power. The

17
/
36
beam delivery system includes reflecting mirror and lens. (figure 2-3)
A,B,C ,D,E are reflecting mirrors and F is lens.
Figure 2-3 The Laser Unit
Laser head was fixed in the shield.
When cutting workpiece, should prevent optics lens from being damaged
by high reflectivity material.
Check the optics lens periodically, clean up in time. If appearing
abnormity, please contacting manufacturer.
The laser units were already adjusted over before leaving
factory, the untrained people can not open laser shield, can
not adjust cutting head and optics component.
2.3.3 Water chiller
The Laser Head require water cooling. The chiller must be filled with de-
mineralised water. The cooling specification is given in section 3.4.2.
2.3.4 Accessorial cutting gas
You must use different accessorial gas to cut different materials. The gas

18
/
36
must filtrate by the clean air system, to ensure the accessorial cutting gas
conform to the purity requirements. Refer to figure 2-4.
When use the compressed air, you should provide oil mist seperator, filter
and dryer, to ensure the particles is smaller than 5μm, the content of condensate
is lower than 5mg/m3, the content of oil is lower than 0.1 mg/m3. The operator
should open the drain valve every eight hours.
The methods of adjusting the air pressure: Pull up the adjusting button of
the regulator and rotate it slowly. Observe the pointer of the gauge, and press
the button when the air pressure is correct. The proof press of all pneumatic
units is 1.0MPa.
1. gas inlet 2. pressure switch 3. regulator 4. gauge
5. air filter 6. switch valve 7. gas outlet
Figure 2-4 Clean Air System

19
/
36
Chapter Three
3.1 Hoist and transpotation
3.2 The preparing requirements of the machine
installation and adjustment
3.3 The work shop and environment requirements
3.4 Utility requirements

20
/
36
3. Installation and Utility Requirements
3.1 Hoist and transportation
It is necessary to fix the moving parts and the whole machine when packing.
Pay attention to machine net weight and the position of center of gravity while
the machine is being hoisted. The jacks should have enough carrying capacity.
It is strongly recommend that moving the machine
must be lightly, slowly and smoothly, and collision and
leaning should be avoid.
The machine net weight is 450kg, so the forklift weight load should be
more than 1000kg and the tip of the prong should exceed center of gravity of
the machine by 500 milimeters.
3.2 The preparing requirements of the machine installation and
adjustment
a. Gradienter (200mm), accuracy: 0.02mm/m
b. De-mineralised water (30L)
c. Air pump offer the compressed air and the compressed air must be oil-
free and dry. (refer to section 2.3.4)
d. Special regulator to the gas bottle and special tube(φ6mm).
e. Machine installation: ensure the machine is horizontal.
f. The connections of gas and water diagram refer to appendix figure 3,4.
*Dismantling all setscrews of conveying state.
3.3 The workshop and environment requirements
The users should complete the following requirements before the machine
entered the factory.
3.3.1 Workshop requirements
The machine floor area is 3600mm×1800mm/4500mm×2200mm , and it is
recommended that the workshop area is 5000mm×4000mm/5500mm×4500mm.
The door width is more than 2000mm/2500mm and height is more than
1500mm. Refer to figure 3-1 for the machine dimensions.
Table of contents
Popular Cutter manuals by other brands

Reliable
Reliable 2000FR instruction manual
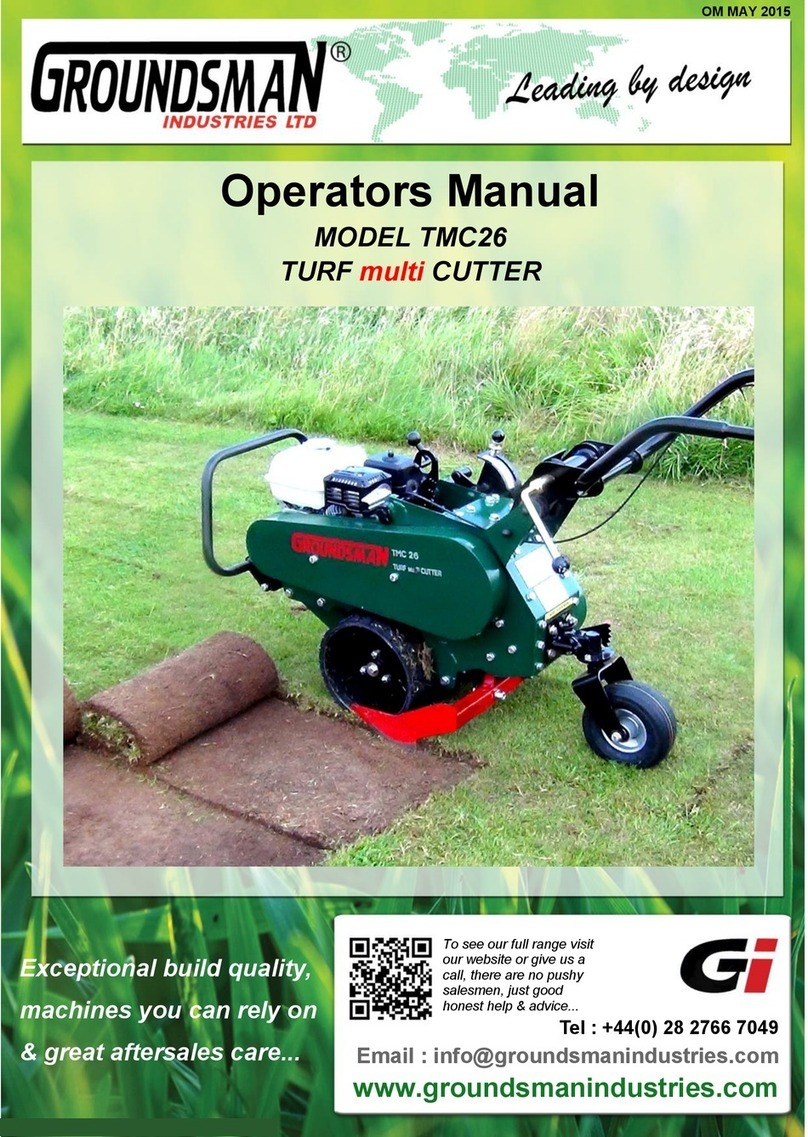
Groundsman
Groundsman TMC26 Operator's manual

Webtool
Webtool RCV190 Instructions for installation, operation, maintenance
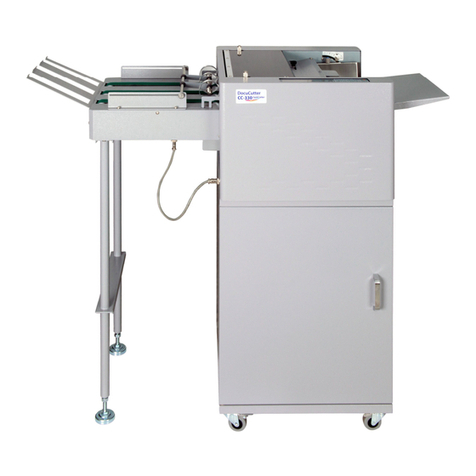
Duplo
Duplo DocuCutter CC-330 Service and parts manual
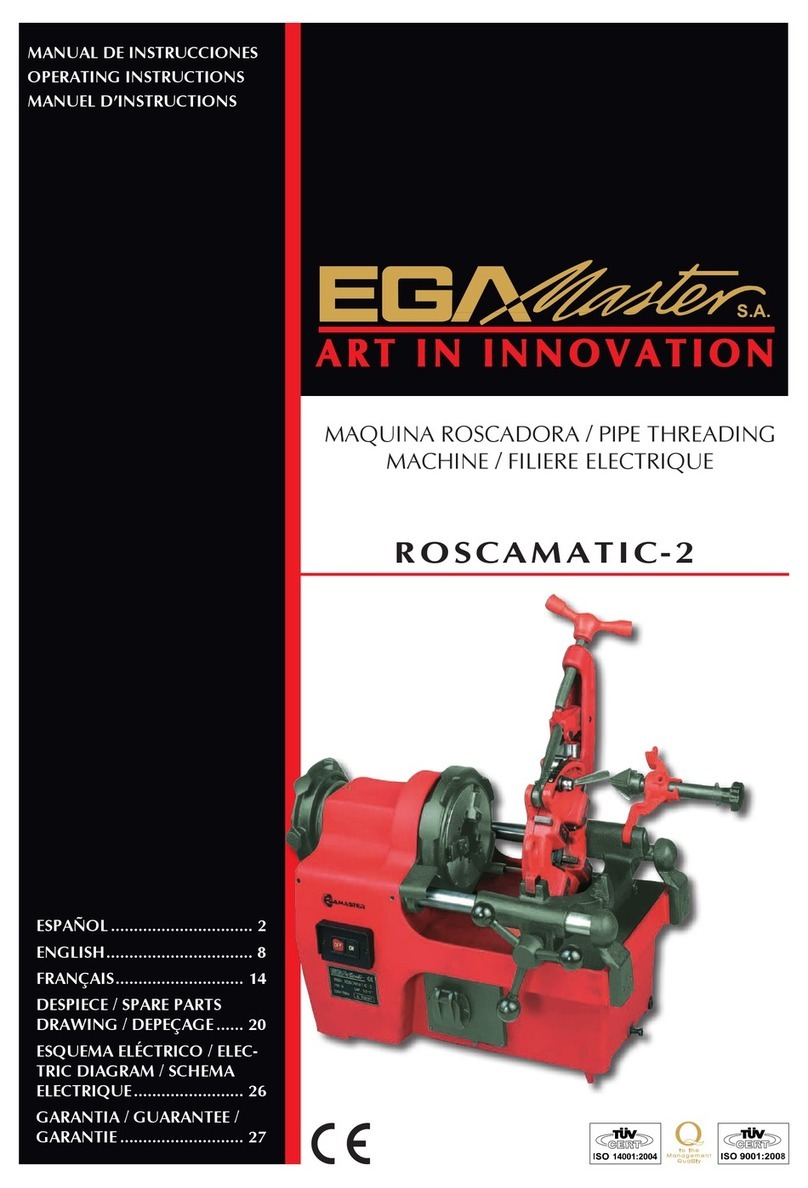
EGAmaster
EGAmaster ROSCAMATIC-2 operating instructions
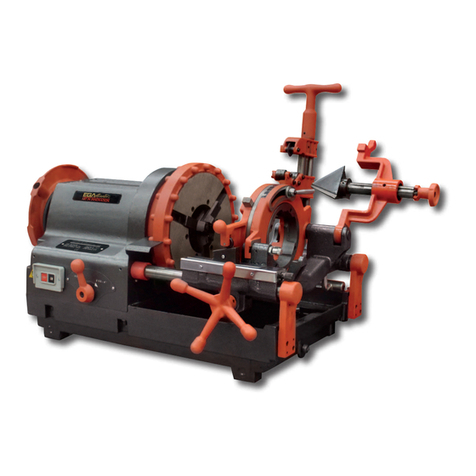
EGAmaster
EGAmaster ROSCAMATIC 100-4 operating instructions
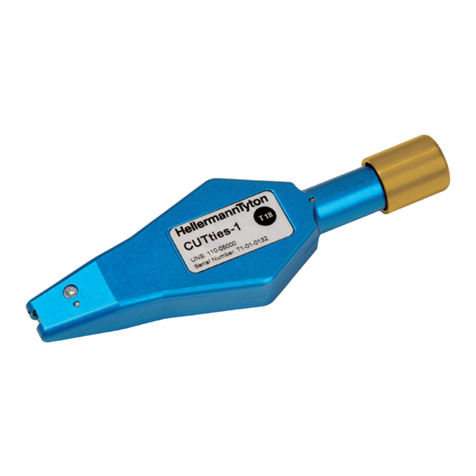
Hellermann Tyton
Hellermann Tyton CUTties-1 operating instructions

Z.I.P.P.ER MASCHINEN
Z.I.P.P.ER MASCHINEN BLADERUNNER 3 user manual

CustomCrimp
CustomCrimp CC38 Operator's manual

Master Trimmers
Master Trimmers MT Tumbler manual

KAMBO
KAMBO GD 24 instruction manual
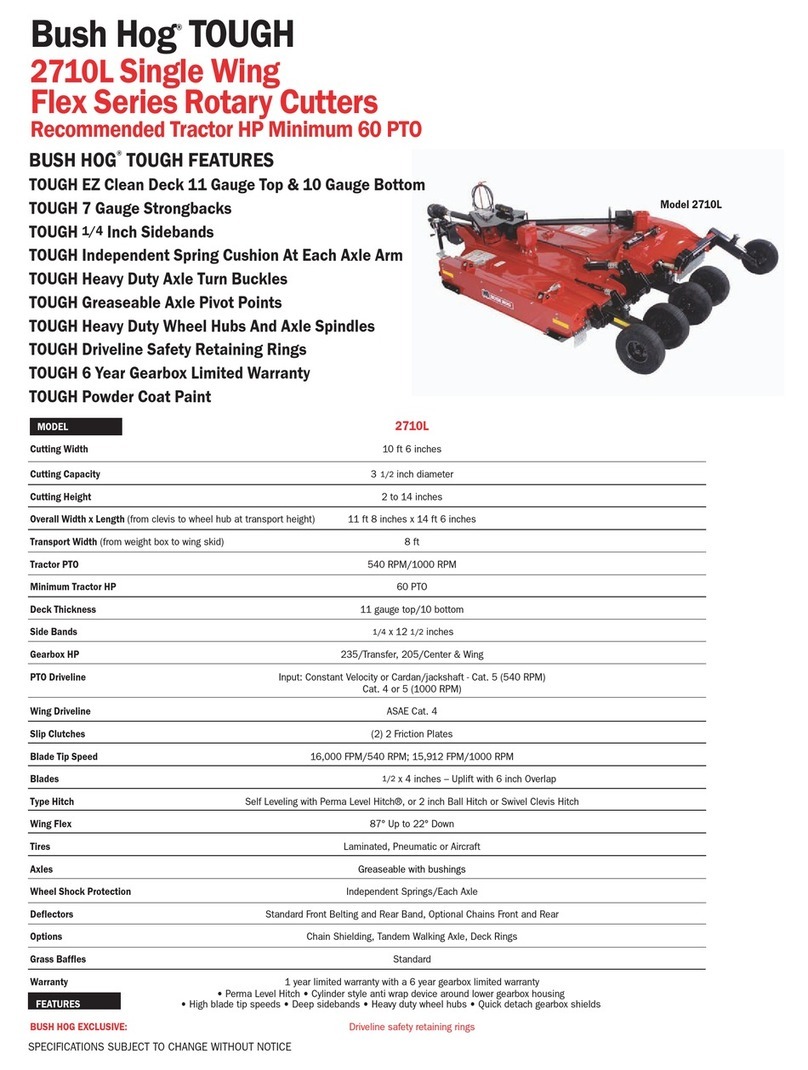
Bush Hog
Bush Hog TOUGH 2710L Specifications