ModWeigh MW93A User manual

Weight Change Instrument MW93A
Instruction Manual ALL
MW93A_IM_ALL_SV6.09f_en EMC INDUSTRIAL GROUP LTD
F ATUR S
• Flowrate measurement and control for
loss-in-weight (or gain-in-weight) sys-
tems
• Motor Speed Control Output Signal
• Flowrate Output
• Material Totaliser
• Modbus communications (independent
RS232 and RS485 ports)
• USB Host & Device (memory stick & PC)
• Field software upgrades
• 12-24Vdc power supply
• Overall accuracy better than 0.01%
MD2,MP2 INDICATOR
• IP54 Facia
• 2.8" (70mm) colour LCD
• 320 x 240 pixels
• Polyester film tactile keypad
• 4-20mA output, 1 digital input & 2 digi-
tal outputs
MO3 I/O for MP2
• 4 Digital inputs
• 4 Digital outputs
• 4-20mA input (or 0-10V)
• 4-20mA output
MD1,MP1 INDICATOR
• IP65 Facia
• 4.3" (109mm) colour LCD
• 480 x 272 pixels
• Silicone tactile keypad
MT1 TRANSMITT R
• Size 136 x 66 x 50mm
• Optional removable P-Module holds cali-
bration settings
MT3 TRANSMITT R
• Size 136 x 66 x 50mm
MR1 I/O
• Size 136 x 66 x 30mm
• 8 Digital inputs
• 8 Digital outputs
• 4-20mA input (or 0-10V)
• 4-20mA output x 2
• Pulse output
INCLUD S
• Installation
• Setting up principles
• Setup Summary
• I/O Function Table
• Operation
• Alarms
APPLI S TO
• MW93A - Weight Change -Module
• MT1,MT3 - Transmitters
• MD1,MD2 - Display
• M 1,M 2 - rocessor
• MR1 - Remote IO
• Software v6.09 onwards
MR1
MT3
MT1
MD2,M 2
MD1,M 1
BULK HO ER
loadcells
WEIGH HO ER
VSD
&
MOTOR
feed gate

MC INDUSTRIAL GROUP LTD Features
MW93A_IM_ALL_SV6.09f_en 2/59
AVAILABL DOCUM NTATION
CO YRIGHT © 2021 by EMC Industrial Group Ltd
56 Tarndale Grove, Albany, North Shore, Auckland 0632
O Box 101 444 North Shore, Auckland 0745, New Zealand
Telephone +64-9-415 5110, Facsimile +64-9-415 5115
E-mail sales@emc.co.nz Web http://www.emc.co.nz
As we are continuously improving our products, changes to this specification may occur without notice.
(Do cument Details: g0 g1 g2 g3 g4 g5 g6 g7 g8 g9 g10 g11 g12 g13 g14 g15 MT1,MT3,MD1,MD2,M 1,M 2))
PRODUCT D SCRIPTION DOCUM NTATION
MW61 Weigher Instrument Technical Information
Instruction Manual
MW64 Batch Weigher Instrument Technical Information
Instruction Manual
MW65 rocess Weigher Instrument Technical Information
Instruction Manual
MW93 Weight Change Instrument Technical Information
Instruction Manual
MW94 Impact Flowmeter Instrument Technical Information
Instruction Manual
MW95 Belt Weigher Instrument Technical Information
Instruction Manual
MW96 Weighfeeder Instrument Technical Information
Instruction Manual

MC INDUSTRIAL GROUP LTD Features
MW93A_IM_ALL_SV6.09f_en 3/59
Contents
INTRODUCTION ....................................................... 5
Features 5
Basic 5
Inputs 5
Internal Signals 5
Outputs 6
Communications & Display 6
IO Summary 7
Configurations 7
Specifications 9
Loadcell Input AI1 9
Analog Input AI2 9
Analog Outputs AO1 & AO2 9
Digital Inputs INx 10
Digital Outputs OUTx 10
Communications COM1, COM2 & COM3 10
General 10
INSTALLATION ....................................................... 10
Dimensions 10
MD2 Display 11
M 2 rocessor 11
MD1 Display 11
M 1 rocessor 11
MT1 Transmitter 11
MT3 Transmitter 11
MR1 Remote IO 11
Connections 11
Motor integration 11
Batch Weighing 12
Run/Stop/ ause Logic 13
Connection rinciples 14
Connection Diagram – M 2 15
Connection Diagram – M 1 16
Connection Diagram – MT1 17
Connection Diagram – MT3 18
Loadcell Connections 18
Multidrop Systems 19
S TTING UP ........................................................... 20
Setup 20
Description 20
Keypad 21
Displaying the Setup Menus 22
Selecting a Menu Item 22
Description of Menus 22
To Adjust A Setting 23
Macros 24
Macro Codes 24
Adjusting a Macro 26
Software Updating 27
Update with USB Drive 27
Update with a C 28
S TTING UP GUID ................................................ 28
Settings 28
Quick Keys 28
Quick Keys Reference 28
Initial Setup 29
Engineering Units 29
Measuring Range 29
Display Resolution 29
Main Calibration Sequence 29
S TUP – MW93A W IGHT CHANG .......................... 30
Basic Settings 30
Engineering units 30
Measuring range 30
Display resolution 30
Trade setup 30
Weight change constants 30
Enter hopper filling setpoints 30
Clock 31
Inputs 32
Digital inputs 32
Loadcell input (vessel weight) 32
Calibrate loadcell 32
Calibrate Using Loadcell Specifications 33
Current/Voltage input (remote flowrate setpoint) 34
Input options 34
Internal Signals 35
Weight 35
Flowrate 35
Totaliser 36
Adjust motor calibration 36
Check flowrate measurement 37
Enter flowrate disturbance hold 37
Limits 37
Events/Alarms/Faults 38
Control 38
Memory Storage 40
User data 41
Outputs 41
Analog output 1 (speed demand) 41
Analog output 2 (flowrate) 42
Digital outputs 42
Communications & Display 42
Comms port 1 - RS232 42
Comms port 2 - RS485 43
Comms port 3 - RS485 MR1 43
Interface registers 43
rinting & Macros 44
Display (MD1,MD2,M 1,M 2) 46
USB 48
Info, Resets & Final Cal 49
roduct Information 49
Reset settings 49
Reset macros 49
Final calibration 49
Run an Auto-Tune rocess 49
S TUP – DISPLAY ................................................... 50

MC INDUSTRIAL GROUP LTD Features
MW93A_IM_ALL_SV6.09f_en 4/59
Basic Settings 50
Clock 50
Communications & Display 50
Comms port 1 – RS232 50
Comms port 2 – RS485 50
Display 51
CompactCom 51
Information & Resets 51
roduct Information 51
Reset settings 51
Other display settings 52
I/O Function Table 52
OP RATING D TAILS .............................................. 55
Setpoint & Speed Demand Signals 55
Modbus Access 55
OP RATION ............................................................ 56
Display 56
Keys 57
Operator Menu 57
Actions 58
Settings 58
Alarm menu 58

MC INDUSTRIAL GROUP LTD Features
MW93A_IM_ALL_SV6.09f_en 5/59
INTRODUCTION
Features
Basic
Units & Resolution
The units for each variable type (weight etc.) can be selected from a list of metric and imperial units.
The resolution of each variable type can be adjusted, this alters the count by e.g 100kg displayed in
0.2kg increments.
OIML Design
The instrument is designed to OIML standards.
Language Support
Support is available for the following languages: English, Chinese, Korean, German, Spanish, French,
Italian and olish.
Inputs
Digital Inputs INx
The digital inputs are programmable to a range of function including ‘acquire zero’, ‘print’ etc.
Direct Calibration
Direct calibration uses the loadcell capacity and loadcell sensitivity to calibrate the weight signal. Large
capacity weighing systems can be quickly and accurately calibrated without the need for large test
weights.
Corner Adjustment (MT1 only)
The input sensitivity can be individually adjusted for up to 4 loadcells, allowing differences in loadcell
sensitivities to be corrected.
Four Loadcell Inputs (MT1 only)
Separate inputs are available for 4 loadcells allowing the signal of each to be monitored sperately. This
provide an aid for load balancing across loadcells and also for fault finding.
Flowrate Setpoint
The setpoint is the flowrate of material the operator wants the flow regulator to convey. The MW93 can
control to the local setpoint, which is set using the keypad, or it can control to the optional remote
analog setpoint signal. The second analog input AI2 is required for a remote analog setpoint.
Signal Filtering
Filtering for the weight can be adjusted to get the optimum compromise between reduction of plant vi-
bration and response speed.
Internal Signals
Limits
The high and low limits have adjustable setpoints which may be programmed to operate on any internal
signal.
Batching
The system can be used to batch out a desired weight by stopping the feeder when the batch weight
has been totalised. A pre-act is available to compensate for overrun.
vent Collection
rocess events are collected for operation with external equipment ( LCs etc.)
Loop Control
The processor compares the flowrate with the setpoint. A proportional/integral ( I) control technique
with feed forward alters the motor speed demand signal to maintain the flowrate at setpoint. Feed for-
ward allows the system to reach the desired set flowrate very quickly and also to respond to changes in
setpoint rapidly.
Volumetric Mode
Normally the controller operates gravimetrically and automatically adjusts the speed demand signal to
reach the required flowrate setpoint.
In volumetric mode, the I control is disabled, and the speed demand is estimated using the feed for-
ward settings.
This allows the system to be kept operating even in the event of a loadcell failure.
Advanced Control Settings
Feed forward settings can be adjusted and corrections for plant delays (transport delay) can be made. A
ratio setting is available to multiply the setpoint signal by a percentage for ratio control applications.
Hopper Refilling
The processor uses weight setpoints and delays to produce a material feed control signal. In a weight
loss system, the feed is opened to refill the weigh hopper from bulk storage when it nears empty. In a

MC INDUSTRIAL GROUP LTD Features
MW93A_IM_ALL_SV6.09f_en 6/59
weight gain system, the feed is opened to empty the weigh hopper when it nears full. During the filling
process, the processor is put into hold during which the flowrate reading and the motor speed demand
signal are held constant. This keeps the flow regulator speed constant during refilling when the flowrate
can not be measured.
Automatic Hold
The hopper weight is continuously monitored to automatically detect that filling is occurring or that the
hopper has been accidentally knocked. If this is detected, the flowrate signal and speed demand signal
are held constant until the weight returns to normal. This feature ensures that a constant output
flowrate is always maintained during a disturbance to the hopper.
Auto Setup
To make setting up easier, the auto setup facility allows many settings for the processor to be calcu-
lated and set automatically.
Memory Storage
Allows a group of settings to be stored or recalled from memory. This can be used for example to store
settings for different products. There are 20 memory locations with up to 4 settings in each.
Material Total
The processor incorporates a totaliser which totalises the weight of material through the system. The
totaliser can be reset to zero. A pulse output is available to operate external counters. A low flow cutout
ensures that low flows do not cause false counts. The total is retained after a power failure.
The totaliser can be set to operate with 5, 6, 7 or 8 digits.
Outputs
Speed Demand
An analog speed demand output signal is used to drive an externally connected motor controller to vary
the flow regulator speed.
Material Flowrate
An analog flowrate output signal is available for connection to other instruments.
Analog I/O Scaling
The analog output range can be adjusted over the full 0 to 20mA range. The output will drive to a slight
negative mA, allowing a live zero to be achieved when using a 0 to 20mA range. A voltage output is
easily produced by connecting a resistor to the output.
In addition the analog output signal is selectable to come from any internal signal in the instrument e.g
weight, flowrate etc.
Digital Outputs OUTx
The digital outputs are programmable to operate from any internal signal. These signals include the
digital input states, status conditions (running, paused etc) and any fault conditions that are detected.
This makes it easy connect into other systems.
Communications & Display
Comms
RS232 and RS485 ports are available. These are used to connect ModWeigh units together and also to
connect to other systems. The protocol is either ASCII output for example to drive a printer or Modbus
for interactive communications. Baud rates and node addresses are programmable.
USB host and device ports are available. This allows for example C and USB flash drive connectivity. It
can be used to update the units software, for data logging and for recording of the units settings.
Printouts & Macros
rintouts can be triggered by a key press or set up to occur at set times during the day or week. Data
may also be output continuously for data collection purposes. Data is output on the COM1 RS232 port.
The content of the printouts is fully programmable using Macros.
Macros are programs used to customise printouts, but can also be used to perform arithmetic calcula-
tions. The Macro language also contains conditional terms for more advanced programming.
Display Customisation
Locks may be set to prevent unauthorised use of the operator keys and restrict entry to the operator
menu. The keys are individually lockable and optionally a passcode can be used to allow authorised op-
erators to use the keys. Alternatively a confirmation of the key action can be requested.The operator
MENU can be customised to make additional settings or signals available to the operator.
The contents of the main display can be set to suit any condition, from a comprehensive display show-
ing all operating parameters to a simple display showing the basic signals.

MC INDUSTRIAL GROUP LTD Features
MW93A_IM_ALL_SV6.09f_en 7/59
Computer Connectivity
ModWeigh instruments can be connected to a computer withan RS232 connection. Data can be sent to
the C at a preset rate. The data sent can be set up using macros.
There is also a command line interface which allows any of the settings and data to be read or written.
IO Summary
Digital Inputs
(includes pulse input)
NAMUR pulse input option
Digital Outputs
(includes pulse output)
Isolated ulse Output
Isolated 4-20mA Inputs
Isolated 4-20mA Outputs
RS232
RS485
USB Host (Memory Stick)
USB Device ( C Cable)
Corner adjustment and bal-
ancing for 4 loadcells
Trade approvals (MW95,
MW96)
M 2 1 2 1 0 1 1 1 1 1
M 2,MO3 1+4 2+4 1 1 1+1 1 1 1 1
M 1,MR1 1+8 9 1 1 2 2 1 1 1
MD1,MT1,MR1 2+8 1+9 1 1 2 2 2 1 1
MD2,MT1,MR1 2+8 1+9 1 1 2 2 2 1 1
MD1,MT3 2 1 0 0 1 2 1 1 1
MD2,MT3 2 1 0 0 1 2 1 1 1
MD1,MT3,MR1 2+8 8 1 1 3 2 1 1 1
MD2,MT3,MR1 2+8 8 1 1 3 2 1 1 1
Configurations
There are three principle configurations for gravimetric flow measurement and control systems. These
are Weight Loss, Modified Weight Loss and Weight Gain.
All configurations have the same basic components of a flow regulator and weigh hopper.
Weight Loss
Modified Weight Loss
BULK HO E
R
control valve
loadcells
WEIGH HO ER
FLOW REGULATOR
Features
• continuous flow
• weigh hopper isolated from flow regula
tor
combined e.g. plastic extruders
BULK HO ER
control valve
loadcells
WEIGH HO ER
FLOW REGULATOR
Features
• continuous flow
• weigh hopper & flow regulator combined

MC INDUSTRIAL GROUP LTD Features
MW93A_IM_ALL_SV6.09f_en 8/59
Weight Gain
Flow Regulators
SCREW FEEDER
VIBRATOR FEEDER
ROTARY VALVE
BELT FEEDER
DRUM FEEDER
TABLE FEEDER
PUMP
RESTRICTOR VALVE
Performance
One factor which determines the performance of a system is the capacity of the loadcell weighing sys-
tem used to weight the hopper. The following graph gives an indication of the useful operating range
that may be used. The Loadcell Capacity is the sum of the capacity of all loadcells, and should take into
account any lever system if one exists.
The performance is very dependent on the weighing system repeatability. It is desirable to aim for as
high a repeatability as possible. With care, it is possible to achieve weighing repeatability of 1 part in
10,000 to 1 part in 100,000.
The flowrate is measured by calculating the change in weight over a period of time. The error in this
measurement is limited by the length of time and loadcell accuracy. Calculate the ratio of flowrate (in
kg/h) to the loadcell capacity (in kg). Using this ratio, the following graph gives an idea of the flowrate
fluctuation for different measuring intervals (the flowrate response setting) and the loadcell incremental
accuracy.
FLOWRATE
[kg/h]
10,000
1,000
100
10
1
1
10
10,000
1,000
100
LOADCELL CA ACITY
[kg]
GOOD ERFORMANCE
OOR ERFORMANCE
ACCE TABLE
BULK HO ER
control valve
loadcells
WEIGH HO ER
FLOW REGULATOR
Features
• interrupted flow
• simple installation
• ideal where bulk hopper & feeder al
ready
exist

MC INDUSTRIAL GROUP LTD Specifications
MW93A_IM_ALL_SV6.09f_en 9/59
0.10
1.00
10.00
100.00
0.01 0.1 1 10 100
RATIO (flow rate [k g/h] / loadce ll capacity[k g])
Measured Flowrate Fluctuatio [% ]
50s, 0.1%; 14s, 0.03%
50s, 0.03% ; 14s, 0.01%
50s, 0.01% ; 14s, 0.003%
50s, 0.003%
flow rate r es po s e [s],
i cr e m e tal loadce ll accuracy[%]
The loadcell incremental accuracy measures how accurately a loadcell can measure small changes in
weight. This accuracy is not normally given on loadcell datasheets, but is generally better than the
other accuracies specified.
Note that other factors may also limit the performance.
Watch flexible couplings to the weigh hopper, as these can easily reduce the achievable performance.
Good accuracy also requires repeatable results from the flow regulator system. Some materials can be
difficult to control (for example powders that fluidise)
Specifications
Loadcell Input AI1
Input Range ±4 mV/V (0-20mV)
Excitation 5 Vdc ±20 %, 250 mA maximum current
Signal processing rate 100 Hz (response time setting≤ 0.5 s)
Input sensitivity 0.5 µV/division maximum
Zero range ±3 mV/V (±15 mV)
Zero drift ±0.02 µV+0.0005 % of deadload/°C typical
Span drift ±0.0005 %/°C typical
Non-linearity ‹0.002 % of FS
Input noise 0.15 µVp-p typical
Filtering 0.04 s to 32.0 s response time adjustable
Sense voltage range 1-5 V
Analog Input AI2
4-20mA input resistance <60 Ω
0-10V input resistance ›100 kΩ
Isolation galvanically isolated to 50Vac
Analog Outputs AO1 & AO2
Output range 0 to 20 mA (-0.2 mA to 21 mA, includes standard 4-20mA)
Maximum load 1000Ω
Resolution 0.4 µA
Response time Loadcell response time setting + 20 ms
Voltage output Use an external resistor to convert mA to volts.
For example 500Ω gives 10 V at 20 mA.
Non-linearity ‹0.01 %
Drift ‹2 µA/°C.
Isolation independently galvanically isolated to 50Vac
High voltage › 8 V
Low voltage ‹ 4 V
Maximum voltage 32 V

MC INDUSTRIAL GROUP LTD Dimensions
MW93A_IM_ALL_SV6.09f_en 10/59
Input load 4 kΩ approximate
Digital Inputs INx
High voltage › 8 V
Low voltage ‹ 4 V
Maximum voltage 32 V
Input load 6 kΩapproximate
Input type N output sensors
Digital Outputs OUTx
Max output current Σ IIOx < 0.25 A
Output voltage same as supply voltage
Communications COM1, COM2 & COM3
COM1 Interface RS232
COM1 Handshake CTS can be enabled
COM2/COM3 Interface RS485
Baud rates 9600, 19200, 38400, 57600, 115200 (230400 on COM2)
Settings 8 data bits, no parity, 2 stop bits (8-N-2)
rotocol Modbus RTU (MWBUS on COM2)
General
I Rating I 20 (MD1,M 1 facia I 65) (MD2,M 2 facia I 54)
Operating temperature -10 to 45 °C
Supply voltage 10 to 28 Vdc
ower MT1 1.0 to 2.2 W + Tacho Excitation
ower MT3 1.0 to 2.2 W + Tacho Excitation
ower MR1 1.5 to 2.5 W + OUTx
ower MD1 1.8 W
ower M 1 1.8 to 3.0 W
ower MD2 1.4 W
ower M 2 1.4 to 3.1 W
ower M 2 + MO3 3.4 to 5.0 W + OUTx + Tacho Excitation
M 2 Restrictions Loadcell Excitation + AO1 + AO2 < 1.5 W
ISupply < 0.5 A
INSTALLATION
The instrumentation must be mechanically installed and then the electrical connections made. The im-
portant electrical connections are as follows.
ower supply connections: 24Vdc fused or current limited to 5A.
Communications: A shielded cable is recommended to connect units together with COM2. It can extend
up to 500m. This leaves COM1 (RS232) free for other applications. For a cable length over 50m, MAT
line terminators must be fitted at each end of the cable.
Loadcell connections: For cable runs less than 20m, a 4 wire connection should be adequate. For longer
cable lengths, a 6 wire connection is recommended.
The ‘material feed’ output to control filling of the weigh hopper.
Speed demand signal (4-20mA) wired to motor speed controller with shielded cable.
If the control feeder motor run/stop is controlled remotely (by LC etc), then the ModWeigh RUN input
must be connected. It must be ON when the weigh belt motor is running. In this case the START key
on the MD1,MD2 display should be disabled when the system is commissioned.
If the feeder motor run/stop is to be controlled by the ModWeigh instrument, the ModWeigh RUN
MOTOR output should be used to control the feeder motor.
Some additional optional connections are as follows.
A remote totaliser.
The 4-20mA measured flowrate output.
The 4-20mA flowrate setpoint input.
Dimensions
Following are the dimensions of the hardware items that make up the system.
The displays/processors are designed for panel mounting.

MC INDUSTRIAL GROUP LTD Connections
MW93A_IM_ALL_SV6.09f_en 11/59
MD2 Display
MP2 Processor
MD1 Display
MP1 Processor
MT1 Transmitter
MT3 Transmitter
MR1 Remote IO
Connections
Motor integration
The following diagrams show various methods to connect a ModWeigh to a VSD drive or motor contac-
tor.
VSD Drive, keypad run/stop
ModWeigh keypad used to start and stop the system. Can be used for batching applications.
VSD Drive, VSD run/stop
ModWeigh slaved from VSD running signal.
+
−
AO1
+
− VSD speed input
4-20mA
VSD run input
run motor [OUT3, 56]
+24V 0V
NOT stop [INx, -1]
VSD OK
136mm
66mm
20mm
8mm
optional DIN rail mount
approx. 35
0g
156mm
86mm
136mm
66mm
20mm
50mm
8mm
optional DIN rail mount
approx. 35
0g
136mm
66mm
20mm
50mm
8mm
optional DIN rail mount
approx. 35
0g
ANEL cut out
186 x 92 mm
-0.0 + 1.0 mm
FACIA
208 x 104 mm
top view
approx. 450g
104mm
30mm
8mm
208mm
ANEL cut out
138 x 67 mm
-0.0 + 1.0 mm
FACIA
144 x 72 mm
top view
approx. 400g
72mm
80mm
9mm
144mm

MC INDUSTRIAL GROUP LTD Connections
MW93A_IM_ALL_SV6.09f_en 12/59
• disable START key
• do not use start function
VSD drive, start/stop buttons
External START / STO buttons connected to ModWeigh instrument driving motor VSD.
Motor Contactor, keypad run/stop
ModWeigh keypad used to start and stop system. Contactor used to run motor.
Motor Contactor, run/stop buttons
External START / STO buttons connected to ModWeigh instrument controlling motor contactor.
• disable START key
• do not use start function
Batch Weighing
xternal Buttons for Batching – Method 1
When START is pressed, the total is reset and the motor started. ressing STO at anytime stops the
motor. If CONTINUE is pressed with the total weight below the batch weight, the motor will start with-
out resetting the total.
motor contactor (mc)
0V
run motor [OUT3, 56]
+24V
START
batch start [INx, 29]
CONTINUE
start [INx, 27]
STO
NOT stop [INx, -1]
+24V 0V
mc
START
run [IN3, 2]
STO
motor contactor (mc)
overload
mc
motor contactor
run motor
[OUT3, 56]
+24V 0V
NOT stop [INx, -1]
overload
overload
+
−
AO1
+
− VSD speed input
4-20mA
VSD run input
run motor [OUT3, 56]
+24V 0V
NOT stop [INx, -1]
VSD OK
start [INx, 27]
START
STO
+
−
AO1
+
− VSD speed input
4-20mA
run [IN3,2]
VSD running signal
+24V 0V

MC INDUSTRIAL GROUP LTD Connections
MW93A_IM_ALL_SV6.09f_en 13/59
• disable START key
xternal Buttons for Batching – Method 2
ressing START resets the total and starts the motor. ressing AUSE stops the motor. If paused, the
batch may be continued by pressing START. ressing STO stops the motor and aborts the batch.
• disable START key
xternal Buttons for Batching – Method 3
ressing START will reset the total and start the motor. If running, pressing AUSE/STO will stop the
motor and pause. ressing AUSE/STO a second time will cancel the pause and abort the batch. ress-
ing START when the controller is paused will start the motor without resetting the total.
• disable START key
Key
Run/Stop/Pause Logic
The following table describes how the status is affected by the inputs.
ModWeigh digital output
+
−
AOx
ModWeigh digital input
ModWeigh analog output
[OUTx,
output function
]
[INx, input function]
pause/stop [INx, 31]
motor contactor (mc)
0V
run motor [OUT3, 56]
+24V
START
batch start [INx, 29]
AUSE/STO
paused [OUTx, 58] AUSED
pause [INx, 30]
motor contactor (mc)
0V
run motor [OUT3, 56]
+24V
START
batch start [INx, 29]
AUSE
STO
NOT stop [INx, -1]

MC INDUSTRIAL GROUP LTD Connections
MW93A_IM_ALL_SV6.09f_en 14/59
Inputs (Control1) Outputs (Status1)
stop run pause start running paused run motor
1 X X X 0 0 0
0 1 0 X 1 0 1
0 0 0 0 * 0 0 0
0 X 1 X NC 1 0
0 0 0 1 0 1
0 0 1 1 1 0
K Y
ntry Description
0 input or output off
1 input or output on
X don’t care (either on or off)
NC no change
rising edge (input turns on)
* remains off since last stop
Connection Principles
ModWeigh instruments can be configured in many different ways to suit any given application.
The display is normally located to suit an operator. The transmitter can be located in the field to reduce
field wiring or can be located with the display for a more conventional approach.
The I/O can conveniently be situated on a DIN rail in a cabinet.

MC INDUSTRIAL GROUP LTD Connections
MW93A_IM_ALL_SV6.09f_en 15/59
Connection Diagram – MP2
D
1
D
2
D
3
D
4
D
5
Analog
+AO2
−
AO2
+VAI2
+mAAI2
−
AI2
pulse output
material feed
run motor
healthy
hold control
acquire zero
run
reset total
M 2
2
3
4
5
6
7
8
2
3
4
6
7
20
RXD
DSR
SG
DTR
CTS
RTS
RXD
TXD
CTS
DSR
SG
DTR
1
2
3
4
5
6
RTS
TXD
0V
0V
RXD
CTS
RJ12
Loadcell
Power/COM2
+EX
−
EX/0V
+
SIG
−
SIG
+
SEN
−
SEN
24V
0V
COM1
MAC
MAP
DB25M
t
o
rinter
remote setpoint input
weight
speed demand
LOADC LL
(s)
optional sense for 6 wire
connection
B LT SP D TACHO
+
0
V
output
B
1
B
2
B
3
B
4
B
5
B
6
I/O
+AO1
−
AO1
+/~ OUT0
−
/~ OUT0
OUT9
IN9
B7
0V
C
1
C
2
C
3
C
4
C
5
C
6
C
7
C
8
C
9
Digital
I/O
OUT1
OUT2
OUT3
OUT4
{MT1}
IN1
IN2
IN3
IN4
24V
C10
0V
TOTALIS R
input
0
V
flowrate
POW R SUPPLY
+24V
0
V
A1
A
2
run motor
acquire zero
MO3 OPTION
24V
TOTALIS R
input
0V
I1
I2
I3
I4
I5
I6
I7
I8
I9
I10
H1
H2
H3
V1
V2
V3
K1
K2
K3
K4
K5
O1
O2
O3
O4
O5
O6
O7
O8
O9
U1
U2
M1
M2
M3
M4
Digital Inputs
Power/COM2
Digital Outputs
Pulse Output
Analog Outputs
COM3
Analog Input 2
IN1
IN2
IN3
IN4
IN5
IN6
IN7
IN8
24V
0V
24V
0V
+
D
−
D
ADS
OUT1
OUT2
OUT3
OUT4
{MT1}
OUT5
OUT6
OUT7
OUT8
0V
+mAO2
−
mAO2
+mAO1
−
mAO1
+/~ OUT0
−
/~ OUT0
+D
−
D
0V
+VI2
+mAI2
−
AI2
pulse output
material feed
run motor
healthy
weight fault
low flow fault
not filling or discharging
alarm alert
to
C, LC
or
ModWeigh Display
MD1,MD2
remote setpoint input
weight
flowrate
speed demand
hold control
acquire zero
run
reset total
print
print total
run
pause
A
3
A
4
A
5
+
D
−
D
IN0
t
o C/ LC
TXD
MAD
DB9F
MR1
Address Select ADS
1
2
3
4
5
24V
0V
+
D
−
D
ADS
1
2
3
4
5
1
2
3
4
5
1
2
3
4
5
R
1k
2k2
4k7
10k
22k
47k
100k
4
5
6
7
8
9
10
1
2
3
Keep all wiring separated
from mains wiring
Use shielded cable where
indicated
Either the RUN input or the
RUN MOTOR output should
be used

MC INDUSTRIAL GROUP LTD Connections
MW93A_IM_ALL_SV6.09f_en 16/59
Connection Diagram – MP1
TOTALIS R
input
0V
I1
I2
I3
I4
I5
I6
I7
I8
I9
I10
H1
H2
H3
V1
V2
V3
K1
K2
K3
K4
K5
O1
O2
O3
O4
O5
O6
O7
O8
O9
U1
U2
M1
M2
M3
M4
Digital Inputs
Power/COM2
Digital Outputs
Pulse Output
Analog Outputs
COM3
Analog Input 2
IN1
IN2
IN3
IN4
IN5
IN6
IN7
IN8
24V
0V
24V
0V
+
D
−
D
ADS
OUT1
OUT2
OUT3
OUT4
{MT1}
OUT5
OUT6
OUT7
OUT8
0V
+mAO2
−
mAO2
+mAO1
−
mAO1
+/~ OUT0
−
/~ OUT0
+D
−
D
0V
+VI2
+mAI2
−
AI2
pulse output
material feed
run motor
healthy
weight fault
low flow fault
not filling or discharging
alarm alert
M 1
MR1
2
3
4
6
7
20
RXD
TXD
CTS
DSR
SG
DTR
MAC
MAP
DB25M
t
o
rinter
to
C, LC
or
ModWeigh Display
MD1,MD2
remote setpoint input
weight
flowrate
speed demand
hold control
acquire zero
run
reset total
print
print total
run
pause
LOADC LL
(s)
optional sense for 6 wire
connection
Address Select ADS
1
2
3
4
5
24V
0V
+
D
−
D
ADS
1
2
3
4
5
1
2
3
4
5
1
2
3
4
5
R
1k
2k2
4k7
10k
22k
47k
100k
4
5
6
7
8
9
10
1
2
3
B LT SP D TACHO
+
0
V
output
POW R SUPPLY
+24V
0
V
TXD
2
3
4
5
6
7
8
RXD
DSR
SG
DTR
CTS
RTS
MAD
DB9F
t
o C/ LC
1
2
3
4
5
6
A1
A
2
A
3
A
4
A
5
RTS
TXD
0V
0V
RXD
CTS
RJ12
Loadcell
Power/COM2
+EX
−
EX/0V
+
SIG
−
SIG
+
SEN
−
SEN
24V
0V
+
D
−
D
IN0
COM1
Keep all wiring separated
from mains wiring
Use shielded cable where
indicated
Either the RUN input or the
RUN MOTOR output should
be used
M 1 bus address set with
setting (Q2522).
MR1 bus address set with
ADS pin and must be same
as M 1.
Fit an MAT terminator to
each end of COM2 cable if
length exceeds 50m.

MC INDUSTRIAL GROUP LTD Connections
MW93A_IM_ALL_SV6.09f_en 17/59
Connection Diagram – MT1
B LT SP D TACHO
+
output
0
V
POW R SUPPLY
+24V
0
V
TOTALIS R
input
0V
I1
I2
I3
I4
I5
I6
I7
I8
I9
I10
H1
H2
H3
V1
V2
V3
K1
K2
K3
K4
K5
O1
O2
O3
O4
O5
O6
O7
O8
O9
U1
U2
M1
M2
M3
M4
Digital Inputs
Power/COM2
Digital Outputs
Pulse Output
Analog Outputs
COM3
Analog Input 2
IN1
IN2
IN3
IN4
IN5
IN6
IN7
IN8
24V
0V
24V
0V
+
D
−
D
ADS
OUT1
OUT2
OUT3
OUT4
{MT1}
OUT5
OUT6
OUT7
OUT8
0V
+mAO2
−
mAO2
+mAO1
−
mAO1
+/~ OUT0
−
/~ OUT0
+D
−
D
0V
+VI2
+mAI2
−
AI2
pulse output
material feed
run motor
healthy
weight fault
low flow fault
not filling or discharging
alarm alert
MD1,MD2
MT1
MR1
L1
L
2
L
3
L
4
L
5
RTS
TXD
0V
0V
RXD
CTS
RJ12
Power/COM2
24V
0V
+
D
−
D
ADS
COM1
TXD
2
3
4
5
6
7
8
2
3
4
6
7
20
RXD
DSR
SG
DTR
CTS
RTS
RXD
TXD
CTS
DSR
SG
DTR
MAC
MAD
DB9F
t
o C/ LC
MAP
DB25M
t
o
rinter
to
C, LC
or
ModWeigh Display
MD1,MD2
remote setpoint input
weight
flowrate
speed demand
hold control
acquire zero
run
reset total
print
print total
run
pause
LOADC LL
(s)
optional sense for 6 wire
connection
Address Select ADS
1
2
3
4
5
24V
0V
+
D
−
D
ADS
1
2
3
4
5
1
2
3
4
5
1
2
3
4
5
R
1k
2k2
4k7
10k
22k
47k
100k
4
5
6
7
8
9
10
1
2
3
1
2
3
4
5
6
Q1
Q2
Q3
Q4
Q5
Q6
T1
T2
T3
T4
T5
J1
J2
J
3
J
4
J
5
R1
R2
R3
R4
R5
R
6
S
1
S
2
S
3
S4
S5
S6
RTS
TXD
0V
0V
RXD
CTS
RJ1
2
Loadcell 1
Loadcell 2
Tacho (I/O)
Loadcell 4
Loadcell 3
Power/COM2
+EX
−
EX/0V
+
SIG
−
SIG
+
SEN
−
SEN
+EX
−
EX/0V
+
SIG
−
SIG
+
SEN
−
SEN
+EX
−
EX/0V
+
SIG
−
SIG
+
SEN
−
SEN
24V
0V
+
D
−
D
ADS
24V
0V
IN0
IN9
OUT9
+EX
−
EX/0V
+
SIG
−
SIG
+
SEN
−
SEN
COM1
acquire zero
run motor
Keep all wiring separated
from mains wiring.
Use shielded cable where
indicated.
Either the RUN input or the
RUN MOTOR output should
be used.
For individual loadcell sensi-
tivity adjustment, use termi-
nals , Q, R and S.
Display and transmitter can
alternatively be connected
COM1 to COM1 using an MAC
cable.
MT1 bus address set with
ADS pin or a setting.
MR1 bus address set with
ADS pin and must be same
as MT1.
Fit an MAT terminator to
each end of COM2 cable if
length exceeds 50m.

MC INDUSTRIAL GROUP LTD Connections
MW93A_IM_ALL_SV6.09f_en 18/59
Connection Diagram – MT3
Loadcell Connections
The loadcell(s) may be wired directly to the loadcell terminals or connected together in the field with a
junction box and connected to the ModWeigh unit with a single cable.
When connected to the terminals only a 4-wire connection is used, and digital corner adjustments are
possible. (MT1 only)
When connected with one cable and a junction box no corner adjustments are possible. It is preferable
to use a 6-wire connection as this eliminates voltage drop errors in long cables caused by cable resis-
tance.
B LT SP D TACHO
+
output
0
V
POW R SUPPLY
+24V
0
V
TOTALIS R
input
0V
I1
I2
I3
I4
I5
I6
I7
I8
I9
I10
H1
H2
H3
V1
V2
V3
K1
K2
K3
K4
K5
O1
O2
O3
O4
O5
O6
O7
O8
O9
U1
U2
M1
M2
M3
M4
Digital Inputs
Power/COM2
Digital Outputs
Pulse Output
Analog Outputs
COM3
Analog Input 2
IN1
IN2
IN3
IN4
IN5
IN6
IN7
IN8
24V
0V
24V
0V
+
D
−
D
ADS
OUT1
OUT2
OUT3
OUT4
{MT1}
OUT5
OUT6
OUT7
OUT8
0V
+mAO2
−
mAO2
+mAO1
−
mAO1
+/~ OUT0
−
/~ OUT0
+D
−
D
0V
+VI2
+mAI2
−
AI2
pulse output
material feed
run motor
healthy
weight fault
low flow fault
not filling or discharging
alarm alert
MD1,MD2
MR1
L1
L
2
L
3
L
4
L
5
RTS
TXD
0V
0V
RXD
CTS
RJ12
Power/COM2
24V
0V
+
D
−
D
ADS
COM1
TXD
2
3
4
5
6
7
8
2
3
4
6
7
20
RXD
DSR
SG
DTR
CTS
RTS
RXD
TXD
CTS
DSR
SG
DTR
MAC
MAD
DB9F
t
o C/ LC
MAP
DB25M
t
o
rinter
to
C, LC
or
ModWeigh Display
MD1,MD2
remote setpoint input
weight
flowrate
speed demand
hold control
acquire zero
run
reset total
print
print total
run
pause
LOADC LL
(s)
optional sense for 6 wire
connection
Address Select ADS
1
2
3
4
5
24V
0V
+
D
−
D
ADS
1
2
3
4
5
1
2
3
4
5
1
2
3
4
5
R
1k
2k2
4k7
10k
22k
47k
100k
4
5
6
7
8
9
10
1
2
3
MT3
1
2
3
4
5
6
E
1
E
2
T1
T2
T3
T4
T5
J1
J2
J
3
J
4
J
5
RTS
TXD
0V
0V
RXD
CTS
RJ1
2
Loadcell 1
Analog Output
Tacho (I/O)
Power/COM2
+EX
−
EX/0V
+
SIG
−
SIG
+
SEN
−
SEN
+AO1
−
AO1
24V
0V
+
D
−
D
ADS
24V
0V
IN0
IN9
OUT9
COM1
acquire zero
run motor
speed demand
Keep all wiring separated
from mains wiring.
Use shielded cable where
indicated.
Either the RUN input or the
RUN MOTOR output should
be used.
Display and transmitter can
alternatively be connected
COM1 to COM1 using an MAC
cable.
MT3 bus address set with
ADS pin or a setting.
MR1 bus address set with
ADS pin and must be same
as MT3.
Fit an MAT terminator to
each end of COM2 cable if
length exceeds 50m.

MC INDUSTRIAL GROUP LTD Connections
MW93A_IM_ALL_SV6.09f_en 19/59
Multidrop Systems
ModWeigh instruments can be connected using the COM2 RS485 bus. Up to 10 systems may be con-
nected on the bus. A ModWeigh display can select any one of the systems on the bus to work with.
A multidrop connection can also be used with any other Modbus master device such as a LC. If a non
ModWeigh master is used on the bus, then the ModWeigh instruments are unable to communicate with
one another. An external Modbus master can alternatively be connected to an RS232 COM1 port.
An MR1 unit cannot share the bus with a non ModWeigh master such as a LC. A LC could be con-
nected using the COM3 port on the MR1.
To connect in mutidrop use the RS485 connection COM2. The wiring should be made in a daisy-chain,
with one instrument connected to the next. If a stub connection is used to a main cable as shown in the
diagram, then make sure its length limit is adhered to.
Two MAT line terminators must be fitted, one at each end of the cable run.
The +D, -D and a 0V terminal must all be connected together through the data cable.
…
L
i
L
][
40 m
n
Li ≤ ][500 mL
≤
if D = MD1,MD2 Display, then n ≤ 10
if D = LC master, then n ≤ 32
Q1
Q2
Q3
Q4
Q5
Q6
Loadcell 2
+EX
−
EX/0V
+
SIG
−
SIG
+
SEN
−
SEN
1
2
3
4
5
6
Loadcell 1
+EX
−
EX/0V
+
SIG
−
SIG
+
SEN
−
SEN
R
1
R
2
R
3
R
4
R
5
R
6
Loadcell 3
+EX
−
EX/0V
+
SIG
−
SIG
+
SEN
−
SEN
S
1
S
2
S
3
S
4
S
5
S
6
Loadcell 4
+EX
−
EX/0V
+
SIG
−
SIG
+
SEN
−
SEN
4
3
2
1
Loadcells Wired to
Directly to Terminals
Allows corner adjustment and individual
monitoring of loadcell outputs
MT1
1
2
3
4
5
6
Loadcell 1
+EX
−
EX/0V
+
SIG
−
SIG
+
SEN
−
SEN
LOADC LL
(s)
optional sense for 6 wire
connection
1
+E
1
−
E
+S
−
S
2
+E
1
−
E
+S
−
S
3
+E
1
−
E
+S
−
S
4
+E
1
−
E
+S
−
S
Loadcells Wired to Junction Box
For best accuracy use a 6-wire connec-
tion to controller

MC INDUSTRIAL GROUP LTD Setup
MW93A_IM_ALL_SV6.09f_en 20/59
Setting the COM1 Modbus Address
Before a multidrop system will operate, the addresses in each of the ModWeigh units will need to be set
differently. This can be done by wiring a link or resistor to the ADS terminal where available. See the
table on the connection diagram. Alternatively the address setting can be changed in each unit using a
display connected to its COM1.
The following procedure is used to set a units address.
1. ress the Q key to access the setup menu.
2. Key in the quick key code 2512 to select the ‘COM1&2 modbus address’ step.
3. ress the EDIT key. (If editing is locked, key in the password 111 and press ENTER).
4. Enter the desired address (1, 2 or 3 etc.) and press ENTER.
5. ress and hold the BACK key to return to normal operation.
6. Repeat for each of the units which are to be used on the bus.
When the multidrop system is then connected and powered, the display should be able to see each of
the ModWeigh systems. This is done by pressing the SELECT key on the display.
S TTING UP
Setup
ModWeigh instruments must be calibrated for each specific application. The parameters stored are col-
lectively known as the Setup.
Description
ress the Q key to access the setup menu.
The setup is divided into sections as shown in the following diagram.
S TUP
Basic Settings
AI1 AO1
AI2 AO2
IN1 OUT1
IN2 OUT2
IN3 OUT3
IN4 OUT4
IN5 OUT5
IN6 OUT6
IN7 OUT7
IN8
Inputs
Internal Signals
Outputs
OUT8
COM1
Communications & Display
COM2
Information, Resets & Final Calibration
Setup Diagram
The Setup contains
Settings
and
Macros
which are described next.
Settings
Most of the setup for a system involves setting calibration constants which for example calibrate the
loadcell input, the 4-20mA outputs and the operation of relays etc. These settings are simple numeric
values.
Macros
Macros are used to store short programs which are used to construct text strings to output to the
printer, perform arithmetic calculations and other special control functions. Macros are a collection of
program segments which can call one another as subroutines. They have structured if/then/else state-
ments and program looping constructs.
A macro is a sequence of numbers (bytes with values of 0 to 255).
Menus
All the setup parameters are contained within a menu structure which follows the setup sections.
Basic Settings
Inputs
Internal Signals
Outputs
Communications & Display
Information, Resets & Final Calibration
Factory Settings
Loadcell
Calibration
Ma
c
ros
Table of contents
Other ModWeigh Measuring Instrument manuals
Popular Measuring Instrument manuals by other brands

Bürkert
Bürkert 8025 Series operating instructions

Hella
Hella 8PE 185 103-261 operating instructions
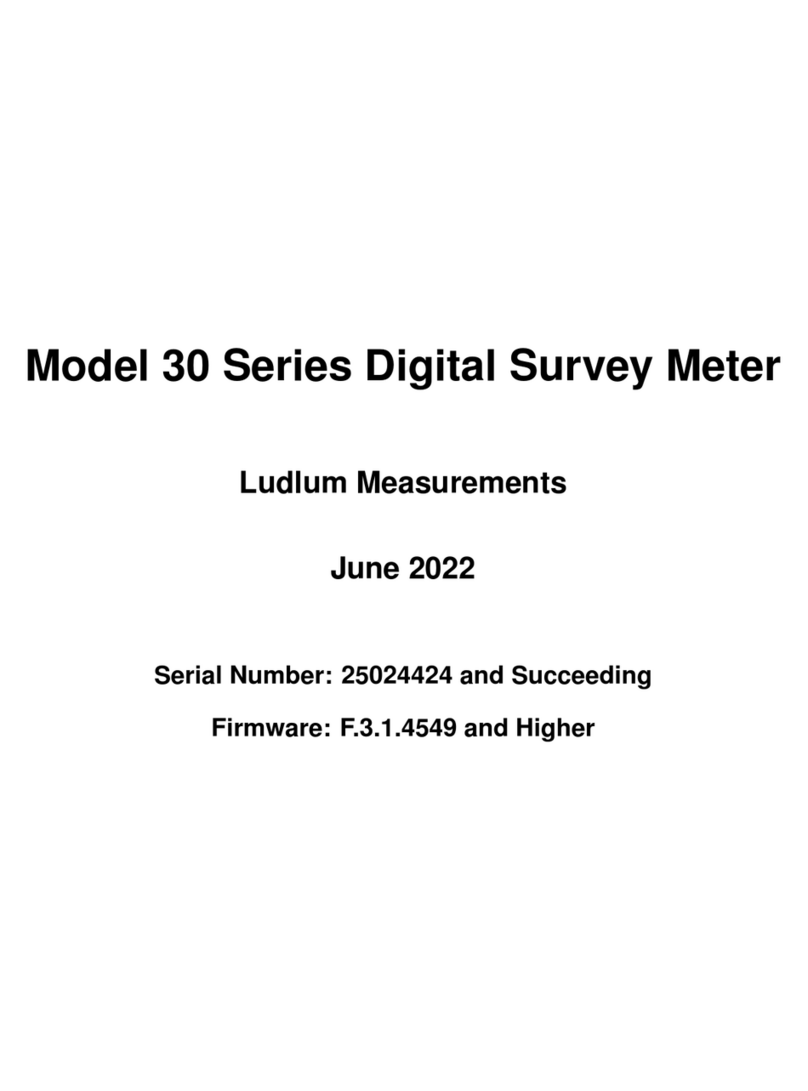
Ludlum Measurements
Ludlum Measurements 30 Series manual
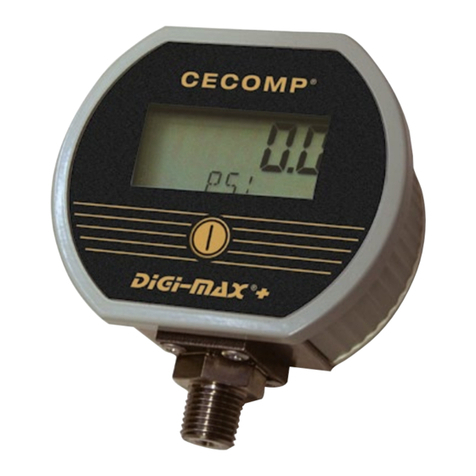
Absolute Process Instruments
Absolute Process Instruments Cecomp DPG2000B Series instructions
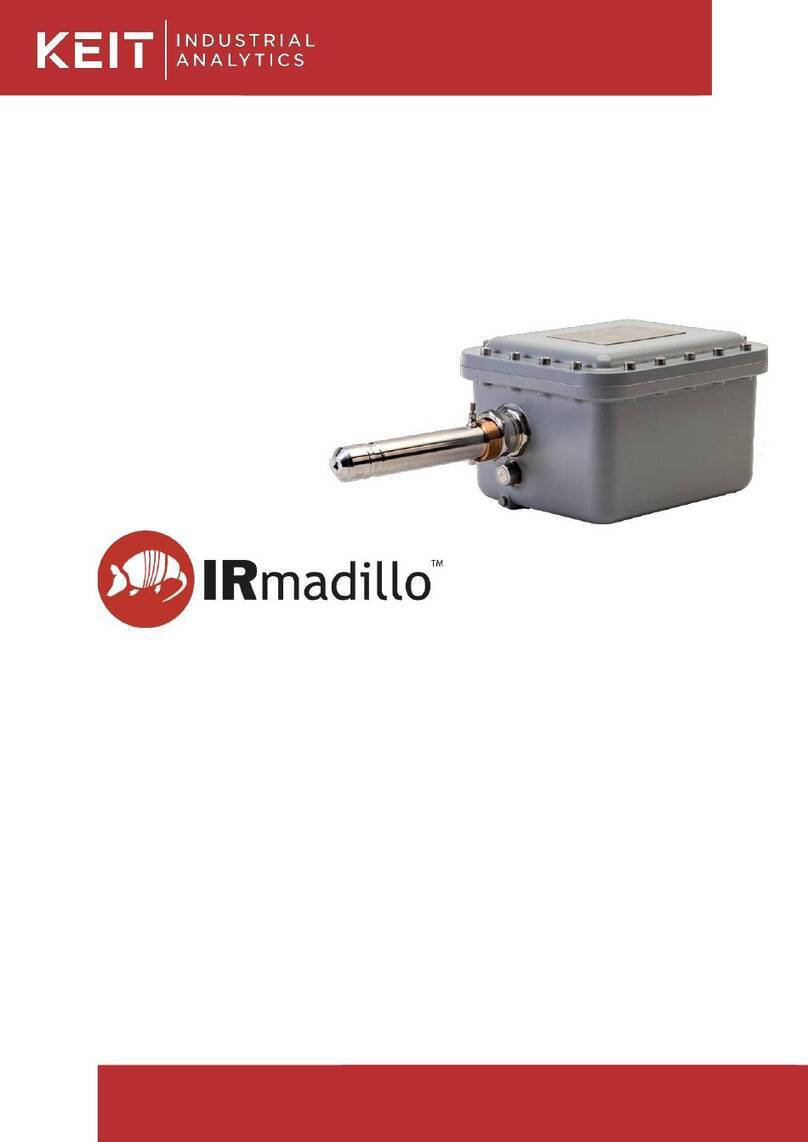
Keit
Keit IRmadillo DOC1048R user manual

Orno
Orno OR-DC-633 instruction manual