Absolute Process Instruments Cecomp DPG2000B Series User manual

Cecomp®Intrinsically Safe Digital Pressure Gauges, with Min/Max Options DPG2000B D4 and M0, M1 Series
O±0.25% Test Gauge Accuracy
O316L Stainless Steel Sensor
OAll Metal Housing
Agency Approval
Factory Mutual Approved Intrinsically Safe for Hazardous Locations
USA & Canada
IS Class I, Division 1, Groups A, B, C, D
T3C Ta = –40°C to 82°C; T4 Ta = –40°C to 66°C
CL I Zone 0 AEx/Ex ia IIC
T3 Ta = –40°C to 82°C; T4 Ta = –40°C to 66°C
Ranges and Resolution
See table below. Select range and default engineering unit.
Units may be changed to any listed under the same sensor range.
Resolution is fixed and limited to available display digits.
Display
3 readings per second nominal display update rate
4 digit LCD, 0.5" H and 5 character 0.25" H alphanumeric
BL: Red LED backlight. Keypress activates backlighting for 1
minute if ambient light is insufficient.
Accuracy
Accuracy includes linearity, hysteresis, repeatability
Standard accuracy: ±0.25% of full scale ±1 least significant digit
HA accuracy option: ±0.1% FS ±1 LSD, see ranges for availability
Sensor hysteresis: ±0.015% FS, included in accuracy
Sensor repeatability: ±0.01% FS, included in accuracy
Auto Shutoff
5, 10 , 30 minutes, or on/off. User selectable 1 minute to 8 hrs
Memory Options
Min/max can be user configured to be individually enabled or dis-
abled, readings saved or cleared at power off
Std: Min/max enabled
M0: Min/max turned off in user setup
M1: Peak reading only gauge for tire pressure
Calibration
Non-interactive zero, span, and linearity, ±10% of range Internal
setup/calibration buttons, internal lockout switch.
Controls and Functions
Front button turns gauge on or off, zeros gauge reference gauges,
and cycles through min/max functions (if enabled)
Internal buttons for engineering unit selection, auto shutoff time,
min/max setup, calibration
Internal lockout switch to disable setup and calibration
Batteries
Two 1.5 V AAA Panasonic LR03 alkaline cells
B: Approx. 1000 hours
BL: Approx. 150 to 1000 hours depending on backlight usage
Low battery symbol on display when batteries need replacement
Weight
9 ounces (approx.), shipping wt. 1 pound (approx.)
Housing Materials and Circuit Board Protection
Epoxy powder coated aluminum case, rear cover, and bezel. Front
and rear rubber gaskets, polycarbonate label.
Stainless steel stiffener plate to reinforce sensor area.
Conformal coating on circuit boards for moisture resistance.
Connection and Material
1/4" NPT male fitting. All wetted parts are 316L stainless steel.
Overpressure, Burst, Vacuum
2 X pressure range for 3 psi to 2000 psi sensors
5000 psig for ranges using 3000 psig sensor
7500 psig for ranges using 5000 psig sensor
Over-range display 112.5% FS: I – – – or I –.–.–.–
Under-range display (non-vacuum sensors): –Err
Vacuum service: 15 psia, ±15 psig, 15 psig, 30 psia,
100 psig, 100 psia, 200 psig sensors
Burst: 4 X sensor pressure rating or 10,000 psi, whichever is less
Environmental
Storage temperature: –40 to 203°F (–40 to 95°C)
Operating temperature: –4 to 185°F (–20 to 85°C)
Compensated temperature: 32 to 158°F (0 to 70°C)
Sensor Ranges and Engineering Units * -HA option not available Range codes are rounded off
3 psig *Res 15 psig vac *Res 30 psia Res –15V100psig *Res 300 psig Res
3PSIG .001 100KPAVAC .1 2KGCMA .001 100PSIVAC .1 300PSIG .1
6INHGG .001 0.1MPAVAC .0001 2ATMA .001 100PSICPD .1 610INHGG .1
85INH2OG .1 1BARVAC .001 30 psig Res 200INHGVAC .1 4800ZING 1
50ZING .01 1KGCMVAC .001 30PSIG .01 2770INH2OVAC 1700FTH2O .1
210GCMG .1 1ATMVAC .001 60INHGG .01 1600ZINVAC 12000KPAG 1
150MMHGG .1 15 psig Res 850INH2OG 15200MMHGVAC 12MPAG .001
150TORRG .1 15PSIG .01 480ZING .1 5200TORRVAC 120BARG .01
200MBARG .1 30INHGG .01 2100GCMG 1700KPAVAC 120KGCMG .01
200CMH2OG .1 400INH2OG .1 1600MMHGG 10.7MPAVAC .001 20ATMG .01
2000MMH2OG 1240ZING .1 1600TORRG 17BARVAC .01 500 psig Res
7FTH2O .001 1000GCMG 12000MBARG 17KGCMVAC .01 500PSIG .1
20KPAG .01 760MMHGG .1 2100CMH2OG 17ATMVAC .01 1020INHGG 1
5 psig *Res 760TORRG .1 70FTH2O .01 100 psig Res 1150FTH2O 1
5PSIG .001 1000MBARG 1200KPAG .1 100PSIG .1 3500KPAG 1
10INHGG .01 1000CMH2OG 10.2MPAG .0001 200INHGG .1 3.5MPAG .001
140INH2OG .1 35FTH2O .01 2BARG .001 2770INH2OG 135BARG .01
80ZING .1 100KPAG .1 2KGCMG .001 1600ZING 135KGCMG .01
350GCMG .1 0.1MPAG .0001 2ATMG .001 7000GCMG 135ATMG .01
260MMHGG .1 1BARG .001 60 psig Res 5200MMHGG 11000 psig Res
260TORRG .1 1KGCMG .001 60PSIG .01 5200TORRG 11000PSIG 1
350MBARG .1 1ATMG .001 120INHGG .1 7000MBARG 12040INHGG 1
350CMH2OG .1 ±15 psig *Res 1660INH2OG 17000CMH2OG 12300FTH2O 1
3500MMH2OG 1±15PSIVAC .01 960ZING 1230FTH2O .1 7000KPAG 1
12FTH2O .01 15PSICPD .01 4200GCMG 1700KPAG .1 7MPAG .001
35KPAG .01 ±30INHGVAC .01 3100MMHGG 10.7MPAG .0001 70BARG .01
15 psia Res ±400INH2OVAC 13100TORRG 17BARG .001 70KGCMG .01
15PSIA .01 ±240ZINVAC .1 4100MBARG 17KGCMG .001 70ATMG .01
30INHGA .01 ±1000GCMVAC 14200CMH2OG 17ATMG .001 2000 psig Res
400INH2OA .1 ±760MMHGVAC 1140FTH2O .1 –15V200 psig *Res 2000PSIG 1
240ZINA .1 ±760TORRVAC 1400KPAG .1 200PSIVAC .1 4070INHGG 1
1000GCMA 1±1000MBARVAC 10.4MPAG .0001 200PSICPD .1 4600FTH2O 1
760MMHGA .1 ±1000CMH2OVAC 14BARG .001 400INHGVAC .1 14MPAG .01
760TORRA .1 ±100KPAVAC .1 4KGCMG .001 5500INH2OVAC 1140BARG .1
1000MBARA 1±0.1MPAVAC .0001 4ATMG .001 3200ZINVAC 1140KGCMG .1
1000CMH2OA 1±1BARVAC .001 100 psia Res 1400KPAVAC 1140ATMG .1
100KPAA .1 ±1KGCMVAC .001 100PSIA .1 1.4MPAVAC .001 3000 psig Res
0.1MPAA .0001 ±1ATMVAC .001 200INHGA .1 14BARVAC .01 3000PSIG 1
1BARA .001 30 psia Res 2770INH2OA 114KGCMVAC .01 6100INHGG 1
1KGCMA .001 30PSIA .01 1600ZINA 114ATMVAC .01 6900FTH2O 1
1ATMA .001 60INHGA .01 7000GCMA 1200 psig Res 20MPAG .01
15 psig vac *Res 850INH2OA 15200MMHGA 1200PSIG .1 200BARG .1
15PSIVAC .01 480ZINA .1 5200TORRA 1400INHGG .1 200KGCMG .1
30INHGVAC .01 2100GCMA 17000MBARA 15500INH2OG 1200ATMG .1
400INH2OVAC .1 1600MMHGA 17000CMH2OA 13200ZING 15000 psig Res
240ZINVAC .1 1600TORRA 1700KPAA .1 480FTH2O .1 5000PSIG 1
1000GCMVAC 12000MBARA 10.7MPAA .0001 1400KPAG 135MPAG .01
760MMHGVAC .1 2100CMH2OA 17BARA .001 1.4MPAG .001 350BARG .1
760TORRVAC .1 200KPAA .1 7KGCMA .001 14BARG .01 350KGCMG .1
1000MBARVAC 10.2MPAA .0001 7ATMA .001 14KGCMG .01 340ATMG .1
1000CMH2OVAC 12BARA .001 14ATMG .01
How to Specify Display Memory
DPG2000B range -D4-time-options - Min/max
DPG2000BBL range -D4-time options backlit Min/max
DPG2000B range -D4-M0-time-options -Min/max off
DPG2000BBL range -D4-M0-time-options backlit Min/max off
DPG2000B range -D4-M1-time-options -Peak read
DPG2000BBL range -D4-M1-time-options backlit Peak read
G = gauge reference pressure
CPD = compound; inHg vacuum, psi pressure
VAC = gauge reference vacuum
A = absolute reference
psi = PSI
inHg = INHG
oz/in2= ZIN
inH2O = INH2O
ftH2O = FTH2O
mmHg = MMHG
torr = TORR
mmH2O = MMH2O
kg/cm2= KGCM
g/cm2= GCM
kPa = KPA
MPa = MPA
mbar = MBAR
bar = BAR
cmH2O = CMH2O
atm = ATM
Range—See table at left. Select a range code for default units.
Please specify if vacuum gauge requires a minus sign.
Time—auto shutoff time
55 minutes. Default if not specified.
10 10 minutes
30 30 minutes
ON No auto shutoff. On/off via front button.
xH Custom shutoff time where x = up to 8 hours
Options—add to end of model number. See price list for details.
HA High accuracy, ±0.1% FS ±1 LSD. See range table.
PM Panel mount, 4.1" x 4.1"
TP Top port, gauge port on top of case
CD Calibration data; 5 test points and date
NC NIST traceability documentation, 5 points and date
HHHHHH
HHHHH
HHHHHH
HHHHH
HHHHHH
HHHHH
HHHHHH
HHHHH
HHHHHH
Made in USA
Quick Link
cecomp.com/is
Accessories—order separately
CON14SS
Quick connector to install or remove gauge with-
out tools. 304 stainless steel, urethane seal.
SCR14SS
Filter screen fitting keeps debris out of gauge
sensor. For food vacuum packaging applications.
303SS body, 100 micron 304SS screen.
RB
High visibility orange rubber boot protects gauge
for portable applications. Not available with NEMA
4X models.
TP
Top gauge port. Primarily used with tire pressure
applications. Not available with NEMA 4X models.
© 08-18
cecomp.com
1220 American Way Libertyville, IL 60048
800-942-0315
CECOMPDiv. of
ABSOLUTE PROCESS INSTRUMENTS

Instructions DPG2000B D4 and M0, M1 Series
¼" NPT
2.88"
3.38"
0.75"
1.65"
Types of Gauges
Gauge reference reads zero with the gauge port open.
Bipolar ranges read positive pressure and vacuum in the same
units, and zero with the gauge port open.
Compound ranges read positive pressure in psig and vacuum
in inHg, and zero with the gauge port open.
Sealed reference reads zero with the gauge port open and is
referenced to 14.7 psi. Used for 1000 psi and up.
Absolute reference reads atmospheric pressure with gauge
port open and zero at full vacuum. With the gauge port open
to atmosphere, it is normal for readings to fluctuate due to
continuously changing barometric pressure.
Dimensions
Operation
Power-Up
Press and hold the front button for approximately 1 second.
The display is tested, the full-scale range is indicated, the
display segments are briefly shown again, then the actual
pressure and units are displayed.
Power Up with Zero
This applies to gauge reference models only. Absolute refer-
ence gauges do not use the zero feature since they read
atmospheric pressure under normal conditions.
Be sure the gauge port is exposed to normal atmospheric pres-
sure and no pressure is applied. The zeroing function is only
activated at each power-up and the stored zero correction is
erased when the gauge is shut off.
Press and hold the front button.
The display is tested.
Continue to press the button until oooo is displayed.
Release the button. The gauge in now zeroed.
The full-scale range is indicated and the display segments are
briefly shown again.
The actual pressure and units are displayed.
Attempting to zero the gauge with pressure greater than
approximately 3% of full-scale pressure or vacuum applied
will result in an error condition, and the display will alternately
indicate Err 0 and the actual measured pressure. The gauge
must be powered down to reset the error condition.
Normal Operation
Following the start-up initialization, the display indicates the
pressure reading updated approximately 3 times per second.
The auto shutoff timer starts when the gauge is powered up or
whenever the button is pushed, unless the gauge shutoff time
was set to zero for on/off operation.
If excessive vacuum is applied to a pressure-only gauge, the
display will indicate -Err until the vacuum is released.
Applying vacuum to a gauge designed for pressure may
damage the pressure sensor. If excessive pressure is applied
(112.5% over range), an out-of-range indication of I – – – or
I.–.–.– will be displayed depending on model.
Shut-Down
To shut off the gauge manually at any time, press and hold
the button until the display indicates OFF (about 5 seconds)
and then release.
When an auto shutoff timer is used, the display indicates OFF
five seconds prior to auto shutoff. Pressed the button to keep
the gauge on. The auto shutoff and backlight (if equipped)
timers are reset whenever the button is pressed and released.
Operation—continued
If the gauge is set up without auto shutoff (on/off operation)
it will stay on until manually shut off or until the batteries are
depleted. Turn gauge off when not in use to conserve battery
life.
Display Backlighting (BL Option Only)
Display backlighting will operate when a button is pressed or
held provided the front light sensor detects low ambient light
levels. Display backlighting will turn on for one minute and
then shut off. Backlighting may not be apparent under some
lighting conditions.
Minimum and Maximum Readings
Minimum and maximum readings are stored continuously
whenever the gauge is on. The stored readings can be manu-
ally cleared if desired. The MIN and MAX memory can be con-
figured to save or clear the reading whenever the gauge is off.
Press and hold the button for about 1 second until MAX is
displayed alternating with the units. The maximum reading will
be continuously updated. The gauge may be left in this mode.
After MAX is displayed, press and hold the button for about 1
second until MIN is displayed alternating with the units. The
minimum reading will be continuously updated. The gauge
may be left in this mode. If excessive vacuum is applied to a
pressure-only gauge while in this mode, the display will indi-
cate -Err until the MAX/MIN readings are cleared.
After MIN is displayed, press and hold the button again for
about 1 second until * * * * is displayed. The MAX and MIN
memory is not erased and the gauge returns to normal opera-
tion with the display indicating the current reading.
Press and continue to hold the button until the display indicates
clr MX/MN (about 3 seconds total) and then release the but-
ton. Both maximum and minimum values are cleared and the
gauge returns to the normal operating mode.
M0 Models are configured with minimum and maximum func-
tions disabled. One or both can be enabled or disabled in the
User Configuration mode.
M1 Models are peak reading gauges that only display and
captures maximum readings. Press and hold the button for
about 1 second until MAX is displayed alternating with the
units. The maximum reading will be continuously updated. The
MAX memory can be configured to save or clear the reading
whenever the gauge is off.
Operation—continued
Battery ReplacementPrecautions
A low battery indication (either LOBAT or a symbol depend-
ing on the model) will be shown in the upper left-hand corner
of the display when the battery voltage falls sufficiently. The
batteries should be replaced when the indicator comes on or
unreliable readings may result.
WARNING: Replace batteries with approved type in non-
hazardous locations only. Replace batteries with two Panasonic
LR03 1.5 V AAA alkaline cells.
Replace both batteries with new ones at the same time. Do
not mix different types of batteries. Substitution of components
may impair intrinsic safety.
1. Remove the 6 Phillips
screws on the back of
the unit.
2. Remove batteries by lift-
ing up the positive end of
the battery (opposite the
spring) taking care not to
bend the spring.
3. Discard old batteries
properly, do not discard
into fire, sources of
extreme heat, or in any
hazardous manner.
4. Install batteries with correct orientation. The negative (flat)
end of each battery should be inserted first facing the bat-
tery holder spring.
5. Replace the back cover, including the rubber gasket.
Approved Locations
The DPG2000B series is approved for use in the following
Hazardous Locations.
IS Class I Div 1 Gp ABCD
T3C Ta = –40ºC to 82ºC; T4 Ta = –40ºC to 66ºC.
CL I Zone 0 AEx/Ex ia IIC
T3 Ta = –40ºC to 82ºC; T4 Ta = –40ºC to 66ºC
Installation
4Read these instructions before installing the gauge.
Configuration may be easier before the gauge is installed.
Contact the factory for assistance.
4Installation instructions must be strictly followed in compli-
ance with Intrinsic Safety National Standard NEC 504 or
ANSI/ISA RP 12.6 and the National Electrical Code.
4Outdoor or wash down applications require a NEMA 4X
gauge or installation in a NEMA 4X housing.
4Use fittings appropriate for the pressure range of the gauge.
4Due to the hardness of stainless steel, it is recommended
that a thread sealant be used to ensure leak-free operation.
4For contaminated media use an appropriate screen or filter
to keep debris out of gauge port.
4Avoid permanent sensor damage! NEVER insert objects into
gauge port or blow out with compressed air.
4Remove system pressures before removing or installing
gauge.
4Install or remove gauge using a wrench on the hex fitting
only. Do not attempt to turn by forcing the housing.
Operation
4Use within the pressure range indicated on gauge label.
4Avoid permanent sensor damage! Do not apply vacuum to
gauges not designated for vacuum operation.
4Use only with media compatible with 316L stainless steel.
Gauges are not for oxygen service. Accidental rupture of
sensor diaphragm may cause silicone oil inside sensor to
react with oxygen.
4The DPG2000B series gauges must only be operated in
specified ambient temperature ranges.
Maintenance
4The non-metallic cover of the pressure gauge is considered
to constitute an electrostatic discharge hazard. Clean only
with a damp cloth.
4Batteries must be replaced when the low battery indication
comes on to prevent unreliable readings.
4WARNING: Replace batteries with approved type in non-
hazardous locations only.
4Approved batteries are two Panasonic LR03 1.5 V AAA
alkaline cells. Replace both batteries at the same time.
p WARNING: Substitution of batteries may impair intrinsic
safety. Improper voltages will damage the gauge.
4WARNING: Substitution of components may impair intrinsic
safety. Do not modify the gauge.
4These products do not contain user-serviceable parts
except for batteries. Contact factory for repairs, service, or
refurbishment.
DS-DPG2000B rev. 12-12
Two
AAA
batteries
cecomp.com
1220 American Way Libertyville, IL 60048
800-942-0315
CECOMPDiv. of
ABSOLUTE PROCESS INSTRUMENTS
Cecomp maintains a constant effort to upgrade and improve its products.
Specifications are subject to change without notice. See cecomp.com for
latest product information. Consult factory for your specific requirements.
WARNING: This product can expose you to chemicals including
lead, nickel and chromium, which are known to the State of
California to cause cancer or birth defects or other reproductive
harm. For more information go to www.P65Warnings.ca.gov

Instructions DPG2000B D4 and M0, M1 Series
Entering User ConfigurationBasic Setup
Configuration must only be done in a non-hazardous area.
Remove the 6 Phillips screws on the back of the unit and
remove the rear cover.
Move the switch on the circuit board to the ENABLE position.
Locate the UP and DOWN buttons on the circuit board.
User Configuration Access
With the gauge off, press and hold the UP button. Then press
the front button. Release all buttons when the display indicates
CFG and the program version. Then the full-scale range is
indicated and the display is tested.
The display then indicates _ _ _ _ with the first underscore
blinking, with CFGPC (configuration pass code) on the lower
display.
Note: The gauge will automatically revert to normal operation if
no buttons are pressed for approximately 15 seconds. To can-
cel and return to normal operation, press and release the front
button without entering any pass code characters.
User Configuration Pass Code Entry
The factory default is 3510, but this may be changed by the
user under the Pass Code Configuration section. If an incorrect
pass code is entered, the gauge will return to the start of the
pass code entry sequence.
1. Use the UP or DOWN buttons to set the first digit to 3.
2. Press and release the front button to move to the next
position. The 3 will remain, and the second position will be
blinking.
3. Use the UP or DOWN buttons to select 5.
4. Press and release the front button to index to the next posi-
tion. 35 will remain, and the third position will be blinking.
5. Use the UP or DOWN buttons to select 1.
6. Press and release the front button to index to the next
position. 351 will remain, and the fourth position will be
blinking.
7. Use the UP or DOWN buttons to select 0.
8. Press and release the front center button to proceed.
Configuration must only be done in
a non-hazardous area.
Remove the 6 Phillips screws on the
back of the unit.
Remove the rear cover.
Move the switch on the circuit
board to the ENABLE position.
Locate the UP and DOWN buttons
on the circuit board.
Engineering Unit Selection
Engineering unit selection is done via internal buttons to help
prevent accidental or unauthorized changes. The selected
engineering unit is stored in non-volatile memory and will be
retained even with the gauge off or batteries removed. The
available engineering units depend on the sensor range and
display resolution.
Compound (inHg/PSIG) gauges must be changed to dis-
play single-unit vacuum/pressure readings in the Advanced
Configuration mode before different engineering units can be
selected.
The default engineering units are mathematically converted to
the newly selected engineering unit. When the gauge is pow-
ered up, the originally configured range is displayed and then
the conversion with the selected engineering unit is displayed.
With the gauge powered up, press and hold the UP button.
Release the button when the engineering units begin to flash.
Use the UP and DOWN buttons to scroll through the list of engi-
neering units available for the pressure range of the sensor.
When the desired units are displayed, press and release the
front button to save the selection and return to normal opera-
tion.
Note: The gauge will automatically revert to normal operation if
no buttons are operated for approximately 15 seconds.
If done, replace the rear cover, or proceed to the next step.
Auto Shutoff Time Selection
Auto shutoff time selection is done via internal buttons to help
prevent accidental or unauthorized changes. The selected shut
off time is stored in non-volatile memory and will be retained
even with the battery off or batteries removed.
With the gauge powered up, press and hold the DOWN button.
Release the button when the auto shutoff time is displayed on
the upper section.
The lower display will indicate AST M if the time displayed is
in minutes, and AST H if it in hours.
An auto shutoff time of 0 signifies that the auto shutoff feature
is disabled and the front button turns the gauge on and off.
Use the UP and DOWN buttons to select 0, 1, 2, 5, 10, 15, 20
or 30 minutes, or 1, 2, 4, or 8 hours.
When the desired time is displayed, press and release the front
button to save the selection and return to normal operation.
Note: The gauge will automatically revert to normal operation if
no buttons are operated for approximately 15 seconds.
Move the switch on the circuit board to the DISABLE position
and replace the rear cover including the rubber gasket.
User Configuration
Factory/User Configuration
This gives the choice of resetting the gauge features to the
factory settings or continuing with user configuration.
The upper display section will be blank, and the lower section
will display either USER_ or FCTRY.
If FCTRY is selected, the existing user configuration will be
replaced by the original factory configuration.
To select FCTRY, press and release the UP button.
With FCTRY displayed press and release the front button to
restore the factory configuration and restart the gauge.
If USER_ is selected, the user configuration can be modified
as described in the following steps.
To select USER_, press and release the DOWN button.
With USER_ displayed press and release the front center
button to continue.
The configuration parameters vary depending on the model. Go
to the appropriate section for your gauge.
M0, M2 Max/Min Configuration
Use the UP and DOWN buttons to select from the following:
MX/MN Both highest and lowest values will be captured
MX/-- Only highest value will be captured
--/MN Only lowest value will be captured
--/-- Capture feature is disabled
Press and release the front button to move to the next param-
eter.
M0, M2 Max/Min Memory
The upper display section will indicate c l r .
Use the UP and DOWN buttons to select from the following:
AUTO Automatically clear max. and min. values when the
gauge is powered off
MAN Manually clear max. and min. values
Press and release the front button to move to the next param-
eter.
M1 Peak Reading Gauge
You can select whether to retain maximum captured values
at power off.
The upper display section will indicate c l r .
Use the UP and DOWN buttons to select from the following:
AUTO Automatically clear the maximum stored value when
the gauge is powered off
MAN Save the maximum stored value when the gauge is
powered off. It must be cleared manually.
Press and release the front button to move to the next param-
eter.
Gauge Type Configuration
This will only appear with 15, 100, or 200 psig ranges that
were originally ordered as compound gauges.
Use the UP and DOWN buttons to select from the following:
-/+EU Vacuum is indicated as negative pressure in the
selected engineering units
CMPND VacuumisnegativeINHG,pressureisPSIG.Thissetting
will disable engineering unit selection.
Press and release the front button to save the user configura-
tion and restart the gauge.
This completes the configuration for this model. Move the
switch on the circuit board to the DISABLE position and replace
the rear cover including the rubber gasket.
Enable/
Disable
Switch
Internal Up/Down Buttons
cecomp.com
1220 American Way Libertyville, IL 60048
800-942-0315
CECOMPDiv. of
ABSOLUTE PROCESS INSTRUMENTS

Calibration DPG2000B D4 and M0, M1 Series
User-defined pass code configuration allows changing of the
factory 3510 pass code to new value for configuration and
calibration.
Configuration must only be done in a non-hazardous area.
Remove the rear 6 Phillips screws and remove the rear cover.
Move the switch on the circuit board to the ENABLE position.
Located the internal UP and DOWN buttons on the circuit board.
View Or Change User Configuration Pass Code
With the unit off, press and hold the UP button, then press the
front button. Release all buttons when the display indicates
CFG.
View Or Change User Calibration Pass Code
With the unit off, press and hold the DOWN button, then press
the front button. Release all buttons when CAL is shown.
Enter Access Code 1220
Before the unit enters the view or change pass code mode,
the display initially indicates _ _ _ _ with the first underscore
blinking, and with CFGPC or CALPC on the lower display.
Note: The gauge will automatically revert to normal operation if
no buttons are operated for approximately 15 seconds.
To cancel and return to normal operation, press and release
the front button without entering any pass code characters.
Use the UP, DOWN, and front buttons to enter the 1220 pass
code.
Press and release the front button to proceed.
Note: If an incorrect access code was entered, the gauge will
return to the start of the access code entry sequence.
Once the access code has been entered correctly, the display
will indicate the existing user-defined pass code with either
CFGPC or CALPC on the character display.
1. Press the UP or DOWN button to select the first character of
the new pass code.
2. When the desired first character is displayed, press and
release the front button to move to the next character.
3. Repeat above until the entire pass code is complete.
4. To exit, press and hold the front button. Release the button
when the display indicates - - - - to restart the gauge.
5. Move the switch on the circuit board to the DISABLE posi-
tion.
6. Replace the back cover, including the rubber gasket.
User Pass Code
See Calibration Preparation section. See rear label of gauge for
model identification and range.
Remove the 6 Phillips screws on the back of the unit and
remove the rear cover.
Move the switch on the circuit board to the ENABLE position.
Locate the internal UP and DOWN buttons on the circuit board.
Entering Calibration Mode
With the gauge off, press and hold the DOWN button, then
press the front button.
Release all buttons when the display indicates CAL.
The display begins by indicating the full-scale positive pressure
rating of the gauge in the engineering units as configured by
the factory, and then shows all display segments.
Before the gauge enters the calibration mode, the display ini-
tially indicates _ _ _ _ with the first underscore blinking, with
CALPC (calibration pass code) on the lower display.
Note: The gauge will automatically revert to normal operation
if no buttons are operated for approximately 15 seconds. To
cancel and return to normal operation, press and release the
front without entering any pass code characters.
Enter the pass code as described in the User Configuration
Pass Code Entry section. The default is 3510, but this is user
changeable.
Calibration Mode
The gauge remains in the calibration mode until restarted
manually or power is removed. Features not related to calibra-
tion are disabled.
The calibration may be performed in any of the available
engineering units as well as percent (PCT). Compound range
models are set for the same engineering units for pressure
and for vacuum.
For greatest calibration accuracy, use the UP and DOWN
buttons to select engineering units with highest number of
display counts.
Press and release the front button when the desired engineer-
ing units are displayed.
Calibration
Sensor Suggested units for calibration
3 PSI 3.000 PSI
5 PSI 5.000 PSI
15 PSI 775.7 MMHG (TORR)
30 PSI 69.20 FTH2O
60 PSI 60.00 PSI
100 PSI 7.031 KG/CM2
200 PSI 407.2 INHG
300 PSI 610.8 INHG
500 PSI 500.0 PSI
1000 PSI 70.31 KG/CM2
3000 PSI 6108 INHG
5000 PSI 5000 PSI
Any 100.00 PCT (percent)
The display will then indicate the currently applied pressure in
the engineering units selected for calibration.
UP and DOWN Button Operation
Each time one of the UP or DOWN buttons is pressed and
released quickly, a small change is made to the digitized pres-
sure signal. It may take more than one of these small changes
to result in a single digit change on the display.
To make larger changes, press and hold the appropriate UP or
DOWN button. After about one second, the display will begin
to change continuously. Release the button to stop. Then
make fine adjustments by pressing and quickly releasing the
appropriate button.
Gauge Reference Pressure Gauges
Apply zero pressure by venting the gauge port to atmosphere.
The character display will alternate between ZERO and CAL.
Press the UP and DOWN buttons to obtain a zero indication on
the gauge display.
Apply full-scale pressure. The character display will alternate
between +SPAN and CAL.
Press the UP and DOWN buttons to match the gauge display to
the full-scale pressure reading on the calibrator.
Apply 50% full-scale pressure. The character display will alter-
nate between +MID and CAL.
Press the UP and DOWN buttons to match the gauge display to
the 50% of full-scale pressure on the calibrator.
Gauge Reference Vacuum Gauges
Apply zero pressure by venting the gauge port to atmosphere.
The character display will alternate between ZERO and CAL.
Press the UP and DOWN buttons to obtain a zero indication on
the gauge display.
Apply full-scale vacuum. The character display will alternate
between +SPAN and CAL.
Press the UP and DOWN buttons to match the gauge display to
the full-scale vacuum indication on the calibrator.
Apply 50% full-scale vacuum. The character display will alter-
nate between +MID and CAL.
Press the UP and DOWN buttons to match the gauge display
to the 50% of full-scale vacuum indication on the calibrator.
Absolute Reference Gauges
Apply full vacuum. The character display will alternate between
ZERO and CAL.
Press the UP and DOWN buttons until the display indicates
zero.
Apply full-scale pressure. The character display will alternate
between +SPAN and CAL.
Press the UP and DOWN buttons to match the gauge display to
the full-scale pressure reading on the calibrator.
Apply 50% of full-scale pressure. The lower display will alter-
nate between +MID and CAL.
Press the UP and DOWN buttons to match the gauge display to
the 50% of full-scale reading on the calibrator.
Compound and Bipolar Gauges
In addition to the steps described above for pressure gauges,
apply full-scale vacuum. The character display will alternate
between -SPAN and CAL.
Press the UP and DOWN buttons to match the gauge display to
the full-scale vacuum reading on the calibrator.
For bipolar (±) and –30.00inHg/+15.00psig compound range
models only, apply 50% full-scale vacuum. The character
display will alternate between -MID and CAL.
Press the UP and DOWN buttons to match the gauge display to
the 50% of full-scale vacuum on the calibrator.
Save Calibration
Once the adjustments are complete, press and hold the front
button until the display indicates - - - - then release the button
to store the calibration parameters in non-volatile memory and
restart the gauge.
Verify the pressure indications at 0%, 25%, 50%, 75% and
100% of full scale.
Move the switch on the circuit board to the DISABLE position.
Replace the back cover, including the rubber gasket.
Enable/
Disable
Switch
Internal Up/Down Buttons
Calibration Preparation
Calibration must only be done in a non-hazardous area. See
Installation and Precautions.
Gauges are calibrated at the factory using equipment traceable
to NIST. There is no need to calibrate the gauge prior to use.
Calibration should only be performed by qualified individuals
using appropriate calibration standards and procedures.
Contact factory if assistance is required. Gauges can be
returned to factory for certified calibration and repairs. NIST
traceability is available.
Calibration intervals depend on your quality control program
requirements. Many customers use an annual calibration cycle.
The calibration equipment should be at least four times more
accurate than the gauge being calibrated.
The calibration system must be able to generate and measure
pressure and/or vacuum over the full range of the gauge.
A vacuum pump able to produce a vacuum of 100 microns
(0.1 torr or 100 millitorr) or lower is required for vacuum and
absolute gauges.
Warning: Never apply vacuum to gauge not designated for
vacuum service. Permanent sensor damage may result.
It is good practice to install fresh batteries before calibration.
Allow the gauge to equalize to normal room temperature (about
20 minutes minimum) before calibration.
Calibration—continued Calibration—continued
cecomp.com
1220 American Way Libertyville, IL 60048
800-942-0315
CECOMPDiv. of
ABSOLUTE PROCESS INSTRUMENTS
This manual suits for next models
6
Other Absolute Process Instruments Measuring Instrument manuals
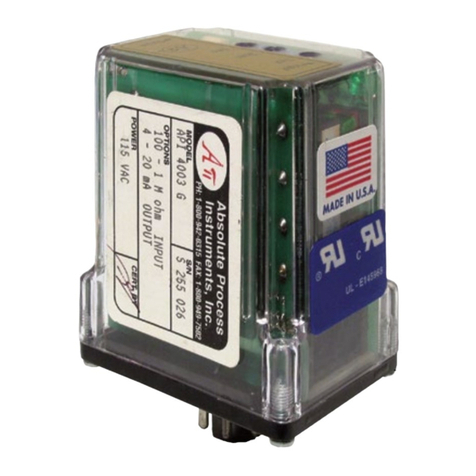
Absolute Process Instruments
Absolute Process Instruments API 4003 G I User manual
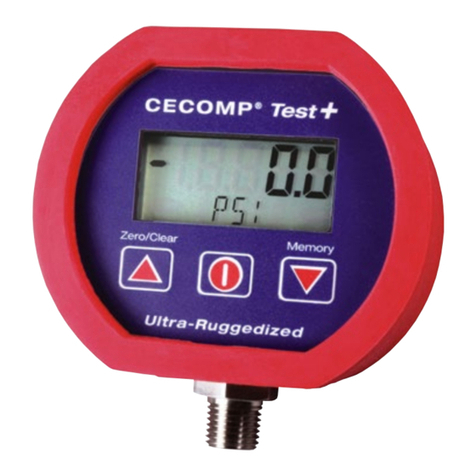
Absolute Process Instruments
Absolute Process Instruments Cecomp Test+ CTP3B User manual
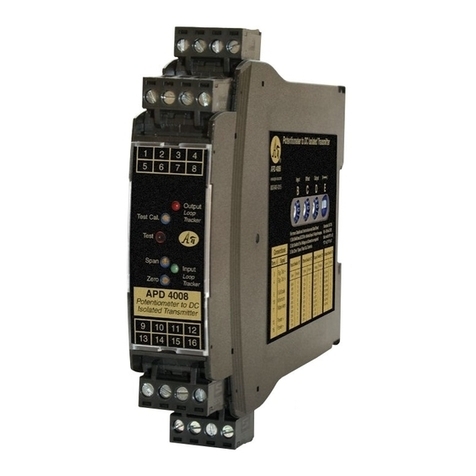
Absolute Process Instruments
Absolute Process Instruments APD 4008 User manual
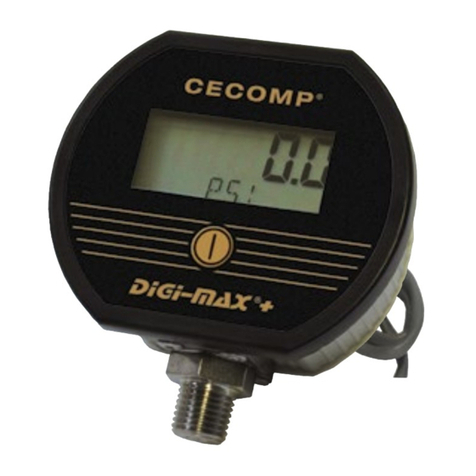
Absolute Process Instruments
Absolute Process Instruments Cecomp F16AD User manual
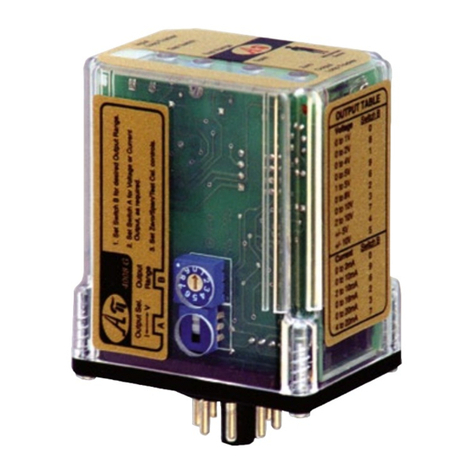
Absolute Process Instruments
Absolute Process Instruments API 4008 G User manual
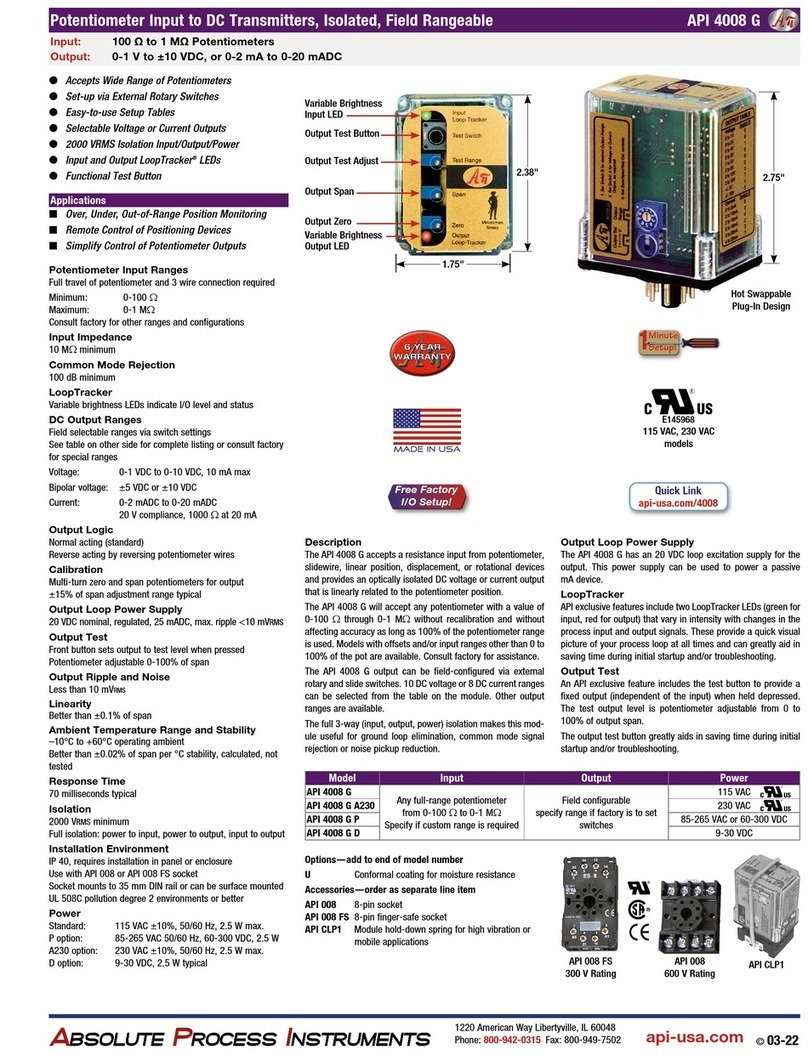
Absolute Process Instruments
Absolute Process Instruments API 4008 G User manual
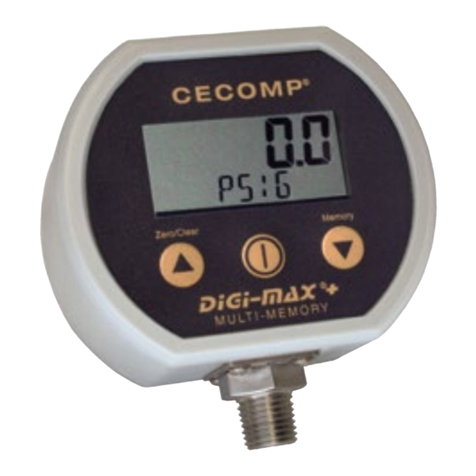
Absolute Process Instruments
Absolute Process Instruments Cecomp F20B User manual