Monitor Technologies TC-1 Owner's manual

Tilt Switch Level Monitors
Model TC-1 & TC-3
BULLETIN
634
INSTALLATION & OPE ATION
Thank you for purchasing a quality product manufactured by Monitor
Technologies C. We realize that you do have a choice of vendors
when procuring bin level monitors and we sincerely appreciate your
business!
This manual contains the information necessary to ensure a safe and
successful installation. Please read and comply with the section on page
4 of this manual pertaining to SAFETY. Doing so will ensure proper oper-
ation of the equipment and the safety of all personnel.
Before discarding shipping container, please inspect it thoroughly and
verify that all parts ordered are accounted for. Sometimes smaller parts
become stuck under carton flaps and other packaging materials.
In the event that information contained herein does not completely sat-
isfy your requirements or answer your questions, you may contact
Technical Support on our website www.monitortech.com, by telephone
at 800-766-6486 (630-365-9403), or by fax at 630-365-5646. If your tilt
switch ever requires service either in or out of warranty, please contact
us and obtain an RMA number prior to shipping the unit to us.

Using Extension Actuators (See Figure 3)
Each tilt switch has a threaded bore on the assembly’s bottom
where an extension actuator can be attached. The extension
actuator can be fabricated from pipe and steel sheet and then
screwed into the tilt switch. ength and vane size can be deter-
mined by the user as required by the application. (Optional 20”
extension actuators for TC-3 are available through Monitor - See
back page for details.) The extension actuators can improve tilt
switch operation in two ways:
1) Improve repeatability of detection angle: Material can cre-
ate a more consistent physical deflection when contacting
the vanes of an extension actuator than when contacting the
enclosure wall of the tilt switch.
2) Protection against physical wear: Extending the tilt switch
away from the initial contact with the “sensed” material will
prevent potential damage to the tilt switch.
Choosing a Location (See Figure 1)
1) Free movement: Select a location where any movement of
the tilt switch is not impeded by structural components such
as vessel braces or side walls. Insure the electrical connec-
tion does not impede the the tilting action of the tilt switch
when sensing material.
2) Material contact: Do not locate the tilt switch in the direct
flow of material as this may cause false signals or physical
damage to the enclosure or the electrical connections. Select
a hanging location where the application permits the tilt
switch to “tilt” at least 17ofrom vertical when “sensing” is to
be indicated. Consider whether extension actuators are
required. If the anticipated angle of deflection approximates
17˚ (hence very repeatable sensing is required), or if materi-
al is very coarse, thereby potentially causing physical dam-
age, attach an extension actuator to protect the tilt switch
(See Mechanical Installation).
MECH A N I C AL INS TALL ATION
P E-INS TALL ATION CONSIDE ATIONS
2
ELEC T I C A L I N STALL ATIO N
Figure 1
Figure 2
Figure 3
Suspension of Tilt Switch (See Figure 2)
ocate or fabricate a structural brace to support the full weight of
a suspended tilt switch (and extension actuator if used).
Interconnect the structural brace and the tilt switch with a rigid or
flexible hanger (e.g. wire rope, chain). Never hang tilt switch by
its electrical cable. Ensure installation permits the switch to “tilt”
at least 17˚ from vertical when “sensing” is to be indicated in a
360˚ circle. (Do not use a bolt through the eyebolt as a means of
attachment.) Shorter teathers will permit a 17˚ tilt where as long
flexible teathers may not allow the sensor to “tilt” 17˚ before the
sensor becomes buried in the material being sensed or detected.
Output Contacts (See Figure 4)
Each tilt switch has a cord connector sized to accept an electrical
cord with a diameter of 0.25-0.38in (6.4-9.6mm). Select a cord
rated for “extra hard usage” (e.g. SO or STO ratings). Guide cord
through the cord connector and tighten to insure dust-tight and
water-tight protection. If it is desirable to use conduit, remove
cord connector to expose threaded conduit entry in enclosure
body. Use at least two feet of flexible conduit. Never connect
rigid conduit directly to the tilt switch. Verify tilting action is not
impeded under normal sensing conditions. No power is required
to operate the tilt switches. Electrical installation is done directly
to the terminals of the output switch within the enclosure. The
terminals are designated with COM-common, N.C.-normally
closed, and N.O.-normally open. When the switch is “not tilted,”
the switch is opposite from normal condition (i.e. N.C. contact is
open to COM, and N.O. contact is closed to COM). However,
when the tilt switch is “tilted” the switch is in the normal condition
(i.e. N.C. contact is closed to COM, and N.O. contact is open to
COM). Connect earth ground to the terminal located on the
lower enclosure half. Be sure to comply with all electrical speci-
fications.

P OBLEM: The tilt switch does not indicate material
sensing.
CAUSE/SOLUTION:
1) Verify material is contacting the tilt switch or its exten-
sion actuator. If necessary, reposition tilt switch.
2) Verify a sufficient angle (equal or greater than 17˚ from
vertical) is achieved when material is to be sensed. If
necessary, remount per Mechanical Installation section.
3) Verify that the hanging mechanism (wire rope, chain,
etc.) and the electrical cable are not restricting the angu-
lar movement of the tilt switch body. If necessary, modify
hanging or electrical connection.
4) Verify electrical connection. When in non-material
sensed mode (not tilted) the N.O. contact is closed to
COM, and the N.C. contact is open to COM. If neces-
sary, change wiring orientation.
5) Verify that the internal steel ball deactivates the switch
when rolled off center between each set of dimples. If
necessary, adjust position of internal switch per
Maintenance section.
P OBLEM: The tilt switch always indicates material is
sensed.
CAUSE/SOLUTION:
1) Verify material falls completely away from the tilt switch
and its extension actuator. If necessary, reposition tilt
switch to assure return to vertical status.
2) Verify that the hanging mechanism (wire rope, chain,
etc.) and the electrical cable are not restricting the tilt
switch from returning to vertical status. If necessary,
modify hanging or electrical connection.
3) Verify electrical connection. When in material sensed
mode (tilted) the N.O. contact is open to COM, and the
N.C. contact is closed to COM. If necessary, change
wiring orientation.
4) Verify that the internal steel ball actuates the switch
when positioned in the center of the cage. If necessary,
adjust position of internal switch per Maintenance
section.
The tilt switches require no calibration or setup in the field. Each
tilt switch is factory set to provide indication whenever the enclo-
sure is tilted at 17˚ or greater from the vertical axis. Each unit will
actuate at the 17˚ tilt angle throughout the complete 360˚ of axial
arc. If an internal switch is replaced, see Maintenance section for
proper adjustment.
3
Figure 5
C ALIB AT IO N
T OUBLE S H O OTING
M AI N TE N AN C E
Figure 4
Switch eplacement/Positioning (See Figure 5)
1) Remove power from the wires connected to the tilt switch.
Remove tilt switch from installation.
2) Open assembly by removing screws holding upper and
lower enclosure halves. Remove switch.
3) Mount new switch using the same hardware. Position switch
so the following conditions are met:
a) Achieve distance between switch body and mounting
frame as noted in drawing below.
b) Switch should activate when steel ball is placed in the
center of the cage.
c) Switch should deactivate when steel ball rolls off center
between each set of dimples.
4) Reattach wires as required. Reassemble upper and lower
enclosure halves. Test operation to insure switch activates/
deactivates at 17˚ angle.
DIMENSIONS A E SHOWN IN INCHES WITH MILLIMETE EQUIVALENT IN B ACKETS

WA ANT Y SPEC IFIC AT IO NS
General Safety
CAUTION: It is essential that all instructions in this manual be
followed to ensure proper operation of the equipment and safety
of operating personnel. The use of this symbol is used through-
out this manual to highlight important safety issues. Please pay
particular attention to these items.
Electrical Shock Caution
All tilt switches may be configured to “switch” HIGH VO TAGE
depending on the application requirements. To avoid electrical
shock, remove power before opening enclosure. Each unit is
provided with a “protective ground” connection which shall be
terminated to earth ground potential. This terminal shall be used
to eliminate shock hazard in the unlikely event of internal insula-
tion breakdown.
S A FE T Y
Monitor Technologies C warrants each tilt switch it manufac-
tures to be free from defects in material and workmanship under
normal use and service within two (2) years from the date of pur-
chase. The purchaser must give notice of any defect to Monitor
within the warranty period, return the product intact and prepay
transportation charges. The obligation of Monitor Technologies
C under this warranty is limited to repair or replacement at its
factory. This warranty shall not apply to any product which is
repaired or altered outside of the Monitor Technologies C fac-
tory, or which has been subject to misuse, negligence, accident,
incorrect wiring by others or improper installation. Monitor
Technologies C reserves the right to change the design and/or
specifications without prior notice.
Model TC-3
Power Requirements: None
Output: SPDT, 10A @ 250 VAC max
Sensitivity: 17˚ from vertical axis
Enclosure: Cast aluminum, unpainted
Enclosure Protection: NEMA 4, IP56
Mounting Connection: Eyebolt, 3/4 in (19mm) I.D.
Wire Entry: 3/8" NPT cord connector
Cord dia 0.25-0.38 in (6.4-9.6mm)
Operating Temperature: -40˚ to 175˚F (-40˚ to 80˚C)
Weight: 3lb (1.35kg)
Approvals: CE Mark
CHINA RoHS 2
Model TC-1
Power Requirements: None
Output: SPDT, 15A @ 250 VAC max
Sensitivity 17˚ from vertical axis
Enclosure Cast iron, painted beige
Enclosure Protection NEMA 4, IP56
Mounting Connection Eyebolt, 1-3/32 in (27.7mm) I.D.
Wire Entry 1/2" NPT cord connector
Cord dia 0.25-0.38 in (6.4-9.6mm)
Operating Temperature -40˚ to 250˚F (-40˚ to 121˚C)
Weight 24lb (11.25kg)
Approvals: CE Mark
CHINA RoHS 2
MECHANICALS
BULLETIN
634
DIMENSIONS A E SHOWN IN INCHES WITH MILLIMETE EQUIVALENT IN B ACKETS
OPTIONAL ACCESSO IES (TC-3)
PA T # DESC IPTION
4-8001 TC-3 Extension actuator, 20” overall extension length,
stainless steel extension and ball float.
4-8002 TC-3 Extension actuator, 20” overall extension length,
galvanized steel extension and polypropylene ball float.
4-8001 4-8002
20.53 + .19
[522 + 5]
8.12
[206]
20.53 + .19
[522 + 5]
8.25
[210]
7.00
[ 178] 8.00
[ 203]
.75
[19]
GDR JSC AUG 05 2016 DOC-001-634A 12
DIMENSIONS A E SHOWN IN INCHES WITH MILLIMETE EQUIVALENT IN B ACKETS
This manual suits for next models
1
Popular Measuring Instrument manuals by other brands

vacuubrand
vacuubrand VACUU-VIEW Instructions for use
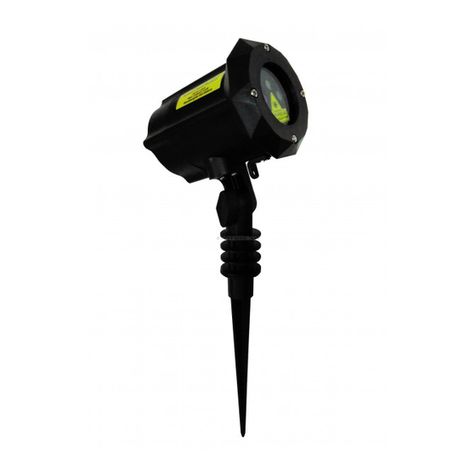
Alice's Garden
Alice's Garden ZEUS manual
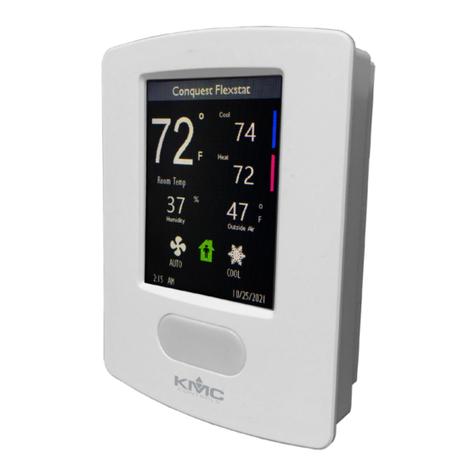
KMC Controls
KMC Controls BAC-19 FlexStat Series installation guide
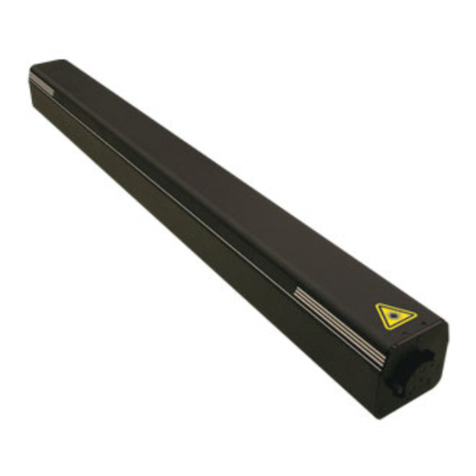
THORLABS
THORLABS HRP350 operating manual
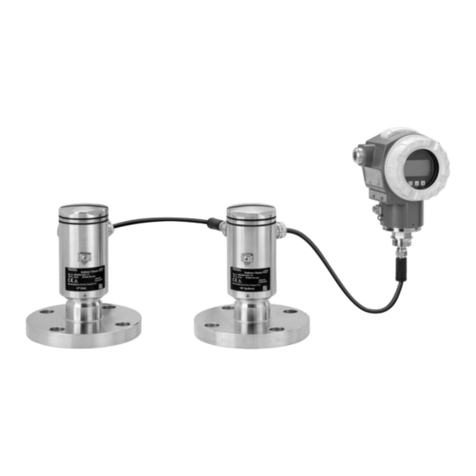
Endress+Hauser
Endress+Hauser Deltabar FMD72 operating instructions

ECD
ECD WaveRIDER Series Hardware user's guide