Mooney M20M Reference manual

alrg~
SUBJECI:
MOONEY
24
VOLT
AIRCRAFT
ELECTRICAL
WIRING
MODIFICATION,
1
(Revision
A
is
applicable
to
M20J
and
M20K
aircraft
only
and
is
still
in
effect
for
those
model
aircraft.
Revision
B
is
applicable
to
M20M
only--).
MODEUS/N
AFFECTED:
MOONEY
MODEL:
M20M
S/N
27-0001
THRU
27-0052
TIME
OF
COMPLIANCE:
AT
NDCT
SCHEDULED
MAINTENANCE
INTRODUCTION:
THE
24
VOLT
ELECTRICAL
SYSTEM
iS
WIRED
IN
A
MANNER
THAT
RENDERS
THE
OVERVOLTAGE
WARNING
LIGHT
IN
THE
ANNUNCIATOR
PANEL
ASSEMBLY
INOPERATIVE
SHOULD
AN
ALTERNATOR
OVERVOLTAGE
OCCUR.
THIS
S.
B.
PROVIDES
INSTRUCTIONS
TO
REWIRE
A
PORTION
OF
THE
CIRCUTT
TO
ENABLE
THIS
WARNING
LIGHT.
INSTRUCTIONS:
1.
Disconnect
voltage
regulator
(for
Altemator
#1)
iocated
under
the
instrument
panel
on
the
co-pilot’s
side.
2
Locate
existino
~Mre
number
M-PA13A18;
push
wire
out
of
pin
8
of
#1
regulator
main
harness
receptacle.
3.
Cut
pin
from
wire,
M-PA13A18;
cap
wire
end
using
AMP
324485
wire
cap
(included
in
kit).
4.
Remove
Glareshield
per
instructions
in
the
appropn’ate
S
M
manual,
Section
39-10-01.
5.
Insert
wire
number
M-PA13B18
(included
in
-1B
kit)
into
pin
8
of
voltage
regulator
receptacle
and
reconnect
regulator.
6.
Route
wire
number
M-PA13B18
along
existing
wire
bundle
to
annunciator
panel
connector
(M-WT103A).
Secure
with
lacing
cord
or
TyRaps.
7.
Locate
wire
number
M-WT02A20
connected
to
pin
1
of
annunciator
panel
connector,
M-WT103A,
and
cut
M-V1~02C\20
wire
6
inches
back
from
connector.
8.
Use
AMP
320559
wire
splice
to
re-connect
wire
number
M-WT02A20
and
tile
unconnected
end
of
new
wire
M-PA13B18
(SEE
nGUREM20-245-1B).
9.
For
No.
2
Altemator:
repeat
Steps
1
through
5
with
#2
regulator
but
on
wire
numbers
M-PA33A18
(Steps
1,
2
3)
and
M-PA33B18
(Step
5);
Route
unconnected
end
of
wire
number
M-PA33B18
to
vacuum
switch
on
back
of
Artifical
Horhon
and
connect
to
"white"
terminal.
10.
Remove
the
1
amp
Annunciator
C/B
and
replace
with
the
2
amp
C/B,
included
in
-1B
kit.
1
I.
Functionally
check
operation
of
altemator(s)
per
POH/AFM,
Section
IV,
Normal
Procedures,
Before
Takeoff
12.
Enter
compliance
note
in
aircraft
logbook
and
return
aircraft
to
service.
WARRANIY:
This
kit
should
be
ordered
from
the
Mooney
Service
Center
in
your
area.
Normal
warranty
billing
policies
will
be
in
affect
for
this
kit.
MooneyAircraft
Corporation
will
allow
up
to
2.0
hourslabor
to
accomplish
this
modification
if
a
completed
Warranty
Claim
is
received
within
180
days
from
the
date
of
this
SeM’ce
Bulletin.
REFERENCE
DATA:
N/A
PARTS
LIST:
KIT
P/N
SB-M20-245-1B
(M20M
only)
mM
P~
DESCRIPTION
.QK
1.
M-PA~3B18
WIRE
ASSEMBLY
1
2
M-PA33B18
WIRE
ASSEMBLY
1
3.
324485
WIRE
CAP
(AMP)
2
4.
320559
WIRE
SPLICE
(AMP)
1
5.
7277-2-2
C/B,
ANNUNCIATOR
(2
AMP)
1
FI
GURESI
TABLES:
SPUCE
-I
I
FIGURE
M20-24518
(M20M
only)

THIS
SERVICE
BULLETIN
IS
FAA
APPROVED
FOR
ENGINEERING
DESIGN.
SUBJECT:
MOONEY
TLS,
M20M.
INCREASED
TAKEOFF
WEIGHT
RETROFIT
MODEL
S/N
AFFECTED:
MOONEY
MODEL
M20M.
SIN
27-0001
THRU
27-0052
TIME
OF
COMPLIANCE.
AT
OWNERS
DISCRETION
BUT
MANDATORY
IF
AIRCRAFT
IS
TO
BE
FLOWN
AT
A
TAKEOFF
WEIGHT
ABOVE
3200
POUNDS.
INTRODUCTION:
Some
aircraft
owners
have
expressed
a
desire
to
increase
the
useful
load
of
the
M20M
aircraft.
Mooney
Aircraft
Corporation
is
offering
the
retrofit
procedures
of
this
Service
Bulletin
to
accomplish
this.
There
are
several
areas
that
will
be
modified
in
order
for
the
aircraft
to
be
flown
at
the
increased
takeoff
weight
of
3368
pounds.
It
is
recommended
that
the
aircraft
be
brought
back
to
Mooney
Aircraft
Corporation
for-the
retrofit.
Scheduling
of
the
retrofrt
action
will
be
co-ordinated
by
the
Product
Support
Department,
telephone
(512)
896-6000.
INSTRUCTIONS:
I.
Remove
and
replace
the
Main
Landing
retraction
truss
assembly,
P/N
520024501
(UH)
and
-502
(R/H)
per
M20M
Service
and
Maintenance
Manual
(S
M)
No.
150,
Section
32-10-00.
The
new
truss
will
be
identified
by
an
"A-2"
metal
stamp
on
the
fork
lover
center
link)
and
a
ink
stamp
"A-2"
after
paint.
2.
Check
for
proper
operation
and
rigging
of
landing
gear
retraction
system
after
replacement
of
retraction
truss
assembly
per
S
M
No.
150.
Section
32-30-00.
3.
Remove
the
8
ABS
flap
hinge
fairings.
(4
on
each
wing)
by
drilling
out
the
rivets
on
fairing
flanges
and
the
side
rivet
on
each
outboard
fairing.
The
two
inboard
fairings
have
screws
attaching
them
to
the
fuselage
belly
fairing
and
one
screw
(inboard
side)
attaching
ABS
fairing
to
the
inboard
wing
flap
hinge
arm
aluminum
fairing.
All
ABS
flap
hinge
fairings
will
be
modified
pn~or
to
re-installation.
(See
Step
4
below)
4.
Remove
flap
gap
seals,
P/N
210374-001
(1
pc)
-003
(2
pcs),
from
left
wing
and
P/N
210374-002
(1
pc)
-004
(2
pcs),
from
right
wing
by:
(1)
Dn’ll
out
the
lower
forward
row
of
rivets
holding
forward
edge
of
aluminum
gap
seal
on.
(2)
Lowerfiaps,
drill
out
row
of
rivets
holding
aluminum
channels,
P/N
210375-1
(1
pc)
and
-003
(2
pcs)
from
each
wing
(Reference
Figure
SE
M20-248-1).
Remove
the
flap
gap
seals
with
the
channels
still
attached.
5.
The
AVEX
1601-0401
rivets
being
drilled
out
will
leave
portions
of
the
rivet
inside
the
wing.
THESE
NEED
TO
BE
REMOVED.
Enlarge
the
existing
No.
30
hole
outboard
of
each
aft
rib
(rib
rivet
line
can
be
seen
on
wing
skins)
to
a
.250
hole
(8
holes
on
each
wing).
Forcefully
use
hand
or
rubber
malletto
hit
wing
skin
area
(DO
NOT
DAMAGE
SKINS)
and
a
magnet
to
move
rivet
residue
toward
.250
hole
and
remove
all
pieces,
with
magnet,
through
hole.
This
should
be
done
between
each
rib
bay.
6.
After
all
drilled
rivet
residue
is
removed.
Install
A10-80
R’Nnuts
in
each
enlarged
hole.
(16
places)
7.
Trim
ABS
flap
hinge
fairings.
P/N
210398-005
(LH)
-006
(RH)
(1
each
side)
inboard,
P/N
210379-009
(LH)
-010
(RH)
(2
each
side)
mid,
and
P/N
210379-011
-012
(1
each
side)
outboard,
per
Figures
SE
M20-248-2A
8r
28.
8.
A
new
hole
will
be
required
in
outboard
’side
wall"
of
each
middle
ABS
fairing,
now
to
be
identified
as
P/N
210379-013
(LH)(2
ea)
074
(RH)(2
ea)
to
match
tooling
hole
in
the
two
middle
wing
flap
hinge
arm
aluminum
fairings,
P/N
210106,
(L
R
wing).
Reference
Figure
SE
M20-248-3
for
basic
instructions
to
drill
holes.
1
9.
NOTE:
Outboard
hole
of
middle
8
inboard
iairings
will
require
enlarging
to.189
(No.
12
hole)
so
M835207-263
screw
can
be
used
in
the
A10-80
rivnut
to
secure
fairing
fiange.
Re-install
each
modified
fairing
using
appropriate
existing
rivet
holes
in
wing
skins
that
match
remaining
hole
in
flange
of
each
ABS
hinge
fairing
and
new
hole
to
match
tooling
hole
in
wing
flap
hinge
arm
fairings.
Use
AVM
1601-0410
(or
equivalent)
blind
rivets
and
MS35207-263
screws
to
attach
ABS
fairings.

SE
M20-248
DATE
3
20
90
Page
2
of
4
10.
Use
AVD:
1
601-0410
rivets
(59
each
row,
minus
ABS
fairing
attach
holes
and
enlarged
holes
for
rivnuts))
to
fill
remaining
holes
in
wing
skins
drilled
out
dun’ng
removal
of
gap
seals
and
channels.
Reference
Figure
SE
M20-248-1.
1
1.
install
MS35207-263
screws
in
all
other
enlarged
holes
to
seal
up
wing
skin
area.
CTotal
of
(16)
MS35207-263
screws
are
required
for
all
enlarged
holes.)
12.
Repainting
of
the
now
exposed
wing
flap
gap
area
will
be
required.
Contact
Mooney
Service
Parts
Department
for
paint
color
PIN
for
aircraft
Sen~al
Number.
13.
Remove
existing
airspeed
indicator,
P/N
820308-527,
and
replace
with
new
airspeed
indicator,
P/N
820308-531,
included
inthis
kit;
it
incoporates
new
airspeed
markings
for
the
increased
weight
performance.
14.
After
airspeed
indicator
has
been
replaced
and
all
lines
secured,
perform
pitot/static
check
for
leaks.
15.
Remove
the
OPERATING
UMITATIONS
placard
from
pilot’s
side
panel
and
replace
with
new
OPERATING
UNIITAIIONS
placard,
P/N
150080-980,
included
in
kit.
16.
Enter
compliance
note
in
AVC
log
book,
insert
AFM
Supplement
into
POH/AFM
and
return
aircraft
to
service.
WARRANTY:
Mooney
Aircraft
Corporation
will
perforn
all
retrofit
action
at
the
factory
service
facility.
Aircraft
owners
will
need
to
contact
the
Product
Support
Department,
(512)
896-6000
to
make
arrangements
for
scheduling
aircraft.
REFERENCE
DATA:
N/A
PARTS
LIST:
KITPARTNUMGER
SE
M20-248-1
ITEM
P/N
DESCRIPTION
QT/.
i.
520024-501
(A-2)
RETRACT
TRUSS
ASSY,
LH
1
2.
520024-502
(A-2)
RETRACT
TRUSS
ASSY,
RH
1
3.
820308-531
AIRSPEED
INDICATOR
1
4.
150080-980
PLACARD
1
5.
1601-0410
RIVET.
AVEX
240
6.
Al
0-80
RIVNUT
.16
7.
MS35207-263
SCREWS
.16
8.
NIA
AFM
SUPPLEMENT
SE
M20-248
1
FIGURES/
TABLES:
See
Figures
on
next
pages.

SE
M20-248
DATE3-20-90
Page
3
of
4
MS20600AD4
(67
PLCS)
REPLACE
WITH
16019410
AVEX
RIVETS
DRILL
THIS
ROW
OF
RIVETS
OUT.
240014
FLAP
ASSY
210375
CHANNELS
MS20470AD4
(61
PLCS)
~210374
DO
NOT
DRILL
THESE
RIVETS
OUT.
MS20600AD4
FLAP
GAP
SEALS
(61
PLCS)
EXTEND
FLAPS
AND
DRILL
OUT
UPPER
ROW
OF
RIVETS
REPLACE
WITH
1601-0410
AVEX
RIVETS
HOLDING
CHANNELS
ON.
DRILL
MIS
ROW
OF
RIVETS
OUT.
FIGURE
SE
M20-248-1
TRIM
EXISTING
ABS
FAIRINGS
TO
DIMENSIONS
SHOWN.
DOTrrD
LINES
INDleArr
UNTRIMMED
CONFIGURAT;IPH
3-CS
~.Z5
\.2J
I
-009
(SHOWN)
210379
FAIRINGS
’------I
-011
(SHOWN)
-olo
(092)
-012
(OPP)
t
OFa\n\NC~>
NEW
CONFKiURATION
PIK
FA\RI~G
OPP
FIGURE
SE
M20-248-2A

SE
M20-248
DATE
3
20
90
Page
4
of
4
FAIRING
Slu2-I
210398-005(SHOWN)
-006
(gpp)
t
0-~
o~c;
NEW
CONFIGURATION
PIK
FIGURE
SE
M20-248-28
i/
~VLX
160~-M\D
(J)
,*L~C
4P~C
I I
I
V
I
klS35207-263
1´•11
C.12~
DI~
~o
LY
Z1010CI
’~b
L~
Wow
hv~x
-14
OCe
16019410
Rtvrr.
-F
I
I~-ts
-I~
w
-\4´•
orr
U.L
--IcO~o
*LI
~LI-
Izcn~
COD~\huo
UP)
~De
FIGURE
SE
M20-248-3

SUBJECT:
MOONC/
M20M
ENGINE
MOUNT
HEAT
SHIELD
MODEU
SIN
AFFECTED:
27-0001
THRU
27-0129
TIME
OF
COMPLIANCE:
WITHIN
NMT
50
OPERATING
HOURS
INTRODUCTION:
There
have
been
occasions
that
the
engine
mount,
in
the
vicinity
of
the
turbocharger,
has
had
paint
scorched
or
missing
due
to
exhaust
temperatures.
The
steel
tubing
may
show
evidence
of
heat
and
in
need
of
maintenance
action.
The
heat
shidd
and
associated
components
on
this
kit
will
reduce
this
temperature
related
action.
INSTRUCTIONS:
1.
Remove
upper
and
lower
ccwling
per
M20M
S
M,
Section
71-10-00.
2
Locate
the
area
of
the
engine
mount
as
shown.
(See
Figure
SE
M20-251-1
for
location)
3.
Inspect
all
engine
mount
tubes
in
dose
proximity
to
the
for
evidence
of
heat
related
damage.
Re~iir
any
damage
per
appropriate
AC43-13
procedures
or
M20M
S
M
manual,
Chapter
51.
4.
Lightly
sand,
and
repaint
with
high
temperature
paint,
any
tubes
showing
evidence
of
heat.
5.
Install
630071-001
shield
using
two
each
630071-003
damp
assemblies
and
appropriate
attaching
hardware.
(Reference
Figure
SE
MM251-1
for
proper
location
and
orientation
on
the
engine
mount
tube.
6.
Re-install
lower
and
upper
cowling
per
M20M
S
M,
Section
71-11-00.
7.
Enter
compliance
statement
in
Aimame
log
book
and
retum
aircraft
to
service.
WARRANP~
Mooney
Aircraft
Corporation
will
allow
up
to
0.7
hours
labor
to
install
the
components
of
this
kit
The
kit
can
be
ordered
through
the
nearest
Mooney
Service
Center.
Warranty
credit
will
be
allowed
forthe
kit
if
necessary
paperwork
is
received
by
Service
Parts
within
180
days
of
the
date
of
this
Service
Bulletin
REFERENCE
DATA
N/A
PARTS
USTr
KIT
PART
NUMBER
-SB
M20-251-1
ITEM
P/N,,....
DESCRIPTION
.QTY
1.
630071-001
SHIELD
1
2
630071~03
CLAMP
ASSY
2
3.
AN3-6A
BOLT
2
4.
AN960-10
.WASHER
4
5.
MS21
042-3
NUT
4
FIGURESI
TABLES:
REFER
TO
FlGURE
SE
M20-251-1

I;
~-ci.
-T
T
SERVICE
BULLETIN
M20-251
DATE:
4-10-92
Page
2
of
2
n
i´•/´•l~
590048
ENGINE
NOUNT
CUUP
ASSY.
530071-003
(2
REOWRED)~
~t
0.00
SHIELD
MM1M2-3
HUI
AN950-10
WASHER
/-530071-001
SHIEU)
TOP
VIEW
630371-003
Ifi~
590048
PICINE
.UOUNI
~2
REaVatEO)
-~3
sylml-atn
4lmo
AN3-6A
BOLT
AN860-10
WASHER
MS21042-3
NLIF
I
SECTION
A-A
ROTATED
550
PUIEIE
OF
~GINE
LIDUNI
TUBE
ii
i
1-
ii~----_,
~iRREWW.
(RD)
630135
WL
PIPE
d
-i
~Jm
V
´•ti
SIDEVIEW
FIGURE
SE
M20-251-1

SUBJECT:
M20M
LANDING
GEAR
RIGG)NG
INSPECTION
AND
MODIFICATION.
MODEU
S/N
AFFECTED:
M20M
S/N
27-0107
THRU
27-0147
(S/N’s
27-0115,
27-0123,
27-0127,
27~131,
27-0137,
27-0142,
27-0144,
27-0150
HAVE
HAD
INSTRUCTIONS
OF
SE
ACCOMPLISHED).
TIME
OF
COMPLIANCE:
WlTHlN
NMT
25
FLIGHT
HOURS
OR
AT
NDCT
SCHEDULED
MAINTENANCE.
Some
aircraft
within
the
above
S/N
block
have
experienced
landing
gear
inner-door
malfunc-
.tions.
This
has
not
caused
difficulty
with
the
retraction/extension
cycle
in
any
of
the
cases.
Maintenance
inspec-
tions
have
found
that
some
of
the
mechanism
components
have
gone
beyond
normal
tolerance.
Replacement
of
some
ofthe
components
is
recommended.
To
eliminate
the
possibility
of
exceeding
tolerances,
a
mechani-
cal
stop
has
been
developed
to
be
installed
in
the
wheelwells.
The
instructions
of
this
Service
Bulletin
and
and
components
of
SE
Kit
wilt
allow
field
personnel
to
retrofit
applicable
aircraft.
INSTRU~TIONS:
i.
Raise
aircraft
on
jacks
per
Service
and
Maintenance
(S
h;l)
manual,
Section
71-10-00.
2
Remove
composite
belly
skins
per
S
M
manual,
Section
53-30-00.
3.
Perform
Landing
Gear
dperational
Inspection
per
S
M
manual,~Section
32-30-01,
revised
March,
1993.
4.
On
LH
RH
main
landing
gear,
replace
bearings
(B-47)
and
bushings
(914020-161)
in
bellcrank
(2).
Replace
rods
(5),
(6),
attaching
pins
and
hardware.
Inspect
press
fit
pins
on
bellcranks
2,
3
4;
replace
if
worn.
5.
Re-n’g
entire
landing
gear
system
per
S
3
M
manual,
Section
32-30-02,
revised
March,
1993
if
Operational
In-
spections
showany
discrepancies.
NOTE
Instructions
of
this
Service
Bulletin
are
to
be
used
in
conjunction
with
M20M
Service
and
Maintenance
Manual,
No.
150
Chapter
32,
revised,
March,
1993.
When
landing
gear
system
has
been
n’gged
and
preload
correctly
set,
the
inboard
landing
gear
door
is
to
have
a
mechanical
stop
incorporated
into
the
system
per
the
following
instructions:
6.
Aircraft
still
on
jacks.
Landing
gear
down
and
locked.
7.
Locate
the
two
rivets
on
LH
RH
whedwells
that
are
just
forward
of
the
inboard
gear
door
hinge
(9)
attaching
rivets
(Ref.
Fig
M20-254-1).
This
is
the
location
for
the
550075-501
stops
(7)
to
be
installed.
8.
Disconnect
Inboard
Gear
doors.
Carefully
drill
off
the
two
rivet
heads
on
LH
RH
sides;
punch
rivets
out.
NOTE
550075501
stop
(7)
has
two
#40
pilot
holes
in
flange.
In
some
instances,
doe
to
manofacturing
toleran-
ces,
the
pilot
holes
may
not
align
exactly
with
both
drilled
holes
in
wing
rib.
If
this
is
the
case,
determine
which
ofthe
two
holes
in
stop
fiange
viill
create
the
better
alignment
of
the
stop
bolt
head
(8)
with
the
bellcrank
(4)
arm.
Use
this
hole
as
the
’primary"
attachment
hole,
9.
Drill
"primary"
attachment
hole
to
size
(i5~20
dn’ll)
in
each
stop.
Cleco
stops
(7)
in
place,
at
"primary"
attach
hole
only,
so
head
of
bolt
(8)
in
stop
aligns
with
arm
of
inboard
gear
door
bellcrank
(4)
that
spring
(1)
is
attached
to.
NOTE
It
is
acceptable
to
chamfer
rear
edge
of
Range,
on
stop,
that
rests
against
wing
rib
if
bucked
heads
of
rivets
interfere
with
proper
alignment
of
stop
bolt
head
and
bellcrank
arm.
Chamfer
only
as
required
to
clearrivet.
10.
When
stop
(7)
is
decoed
in
proper
position,
drill
second
attach
hole
in
stop
Range
to
size
(#20
drill),
by
back
drilling
through
e>dsting
"non-primary"
rivet
hole.
Deburr
hole
in
Range
and
cieco
in
position.
Make
sure
head
of
bolt
(8)
in
stop
aligns
(directly
centered)
with
arm
of
bellcrank
(4).

SERVICE
BULLETIN
M20-254
DATE:
4-1-93
Page
2
of
4
lNSTRUCTIONS:
(con’t)
11.
Rivet
stops
t/),
P/N
550075-501,
in
each
wheelwell
at
the
location
descn’bed
in
steps
8
9
above
using
rivets
included
in
this
kit.
Re-attach
Inboard
Gear
doors
before
cycling
landing
gear
for
following
steps.
12
Leave
spring
(1)
attached
to
clevis
of
inboard
door
bellcrank
(4).
Bolt
head
(8)
should
be
screwed
all
the
way
in.
NOTE
Two
mechanics
(personnel)
may
be
required
for
the
next
several
steps.
One
under
the
aircraft
and
the
other
inside
the
aircraft
operating
the
landing
gear
switch.
13.
Retract
landing
gear
using
safety
by-pass
switch
(See
S
M,
Section
32-30-01,
steps
5, 6,
7)
until
inboard
gear
door
has
traveled
as
far
as
it
willgo
during
its
retraction
cycle.
In
this
position,
the
pivot
points
of
bellcrank
(3)
center
line
of
rod
-(5)
will
be
in
a
straight
line
(Reference
Figure
M20-254-2).
Components
(2),
(5)
(6)
should
now
be
in
a
loaded
condition
and
feel
very
tight.
14.
Adjust
stop
bolt
head
(8)
OUT
until
it
rests
on
bellcrank
(4)
arm.
Continue
to
adjust
bolt
head
OUT
until
rods
(5)
gr
(6)
become
loose
(no
load
felt
on
either
rod).
Bellcrank
(2)
will
also
become
loose
when
bolt
head
(8)
is
in
correct
position.
Tighten
jam
nut
on
bolt
(8)
against
tube
on
stop
(7).
15.
Repeat
installation
of
stop
(7)
(Steps
7
thru
11)
and
adjustment
procedures
(Steps
12
thru
14)
in
other
whedwdl.
16.
Cycle
landing
gear
through
five
complete
retraction/extension
cycles;
inspect
all
components
during
and
after
cycles
for
any
interference,
binding
or
improper
operation.
Reference
Operational
Inspection
in
S
M,
as
done
in
Step
No.
3.
17~
Ccmplete
lag
boole
entry
and
retum
aircraft
to
service.
WARRANP~
Mooney
Aircraft
Corporation
will
allow
3.0
hours
labor
to
comply
with
this
Service
Bulletin.
Parts
Kit
will
be
ordered
through
Mooney
Service
Centers
and
credit
will
be
issued
upon
receipt
of
warranty
forms
within
180
days
of
the
issue
date
of
this
Service
Bulletin.
REFERENCE
DATA:
N/A
PARTS
UST:
KIT
PART
NUMBER
SBM20-254-1
lTEM
.P/N
DESCRIPTION
QTY
1
~550075601
STOP
ASSY.
.2
2
.550082-503
ROD,
LOWER
.2
3
.550082-505
ROD,
UPPER
.2
4
.91
4020-1
61
BUSHING
.2
5
.8-47
BEARING
.2
6
.MS20392-2C7
PIN,
CLNIS
(PRESS
FIT:BELLCRANK
4)
.2
7
.MS20392-2C9
PIN,
CLNIS
(PRESS
FIT-BELLCRANK
i&
3)
.4
8
.MS20392-2C17
PIN,
CLEVIS
.2
9
.AN381-2-6
PIN,
COTTER
.8
10.
.AN470AD5-13
RIVET
.4
11.
M20M
S
M
Chapter
32,
kevised
3-93’
.1
At
some
later
date
the
complete
S
M
will
be
revised
and
Chapter
32,
as
revised
in
March,
1993,
will
be
available
to
the
field
and
may
not
be
included
in
this
Service
Bulletin
kit.
FlGUREl
TABLES:
SEE
NDCT
PAGES
FOR
FlGURES
SBM20-254-1
AND
SBM20-254-2

SERVICE
BULLETIN
M20-254
DATE:
4-1-93
Page
3
of
4
p’’
O
spi~P
a
dp"‘’
3~
o~
a
o
a
a,
a
I!
\~4
5~
11
I
~\o
2
--~21
I,I
II
al
II
61
0\
L.9
SBM20-25
4´•-1

SERVICE
BUU-FTIN
M20-254
DATE:
4-1-93
Page
4
of
4
NI7I1CE
THESE
PIVDT
P[71NTS
ARE
IN
ALMOST
A
STRAIGHT
LINEI
THIS
R-EPRESENTS
THE
M[7ST
EXIREME
TRAVEL
THAT
THESE
CDMP
ONENTS
SHOULD
BE,
i
o
SBM20-254-2

SERVICE
BUU~ETIN
M20-255A
I
ISSUEDATE:
Novemberl’l,
1993
SUB3ECT:
Mooney
M20M,
Retrofit,
cabin
exhaust
vents
on
fuselage
sideslcabin
ventilation
system
modifiction.
MODELSISIN
AFFECTED:
PART
1:
M20M
S/N
27-0002
THRU
27-0137
(D(CEPT
S/N
27-0094)
PART
2:
M20M
SM
27-0053
THRU
27-0167
(EXCEPT
S/N
27-0094)
I
PART
3:
M20M
SRN
27-0002
THRU
27-0052
TlME
OF
COMPLIANCE:
Within
next
25
Right
hours
or
at
next
scheduled
maintenance
action.
INTAODUCTION:
In
order
to
provide
a
continual
purge
of
the
cabin
air,
compliance
of
this
Service
Bulletin
needs
to
be
accomplished
for
serial
numbers
listed
above.
INSTRUCTIONS:
PART
ADDCABIN
D(HAUSTVENTS
(F1G.SBM20-255-1)
(S/N
27-0002
thru
27-0167,
excluding
S/N
27-0094)
I
1.
it
is
recommended,
but
not
essential,
to
remove
aft
interior
baggage
compartment
ABS
panels,
both
sides.
The
long
ABS
panels,
forward
of
the
baggage
campartment
panels,
will
need
to
be
pulled
UP
and
restrained
UP
to
provide
access
to
the
inside
skin.
These
long
ABS
panels
may
be
removed,
if
desired,
to
accomplish
the
retrofit
Caution
should
be
observed
during
cut
out
of
hole
and
drilling
of
rivet
holes
in
fuselage
skin
soas
not
to
drill
through
any
electrical
wiring,
ABS
panels
or
tubular
structure.
Z
Locate
area
of
fuselage
skin
to
be
cut
out
by
measuring
from
the
baggage
campartment/cabin
area,
vertical
skin
lap,
forward,
9.0
inches
and
dawn
16.4
inches
from
lower
edge
of
ah
window
skin
clrt-out.
The
size
of
each
cut-out
should
be
29
inches
high
and
2.26
inches
wide.
Keep
vertical
sides
of
cut-out
parallel
with
vertical
skin
lap.
Recommended
radius
on
all
comers
of
cut-out
is
.125
inches.
(Fig.
SE
M20-255-1)
3.
Deburrcut-out
4.
Cleco
640296-001
ABS
baffle
to
a
lowered
plate
for
UH
side
sub-assembly
to
verify
that
all
pilot
holes
in
baffle
and
lowered
plate
are
matched.
Drill
all
pilot
holes
out
to
#30
holes.
Repeat
for
R/H
side
sub-as-
sembly.
Ident~y
lowered
plates
as
RIH
and
UH
during
this
procedure.
NOTE:
Be
sure
that
louvers
will
have
openings
toward
the
aft
end
of
the
aircraft.
5.
After
drilling
i4~30
matching
holes
in
baffle
and
lowered
plate,
sandwich
a
640247-003,
aluminum
screen
between
UH
baffle
and
UH
lowered
plate;
punch
matching
holes
through
screen
mesh
with
an
awl.
Repeat
for
RIH
side
sub-assembly.
6.
Place
R/H
640130-000
lowered
plate
in
position,
over
RIH
cut-out
hole,
in
accordance
with
Fig.
SE
M20-255-1.The
location
of
the
lowered
plate
does
not
have
to
be
exact,
however,
a
minimum
of
.31
inr
ches
edge
distance
should
be
maintained
for
all
fasteners.
Drill
#30
holes
in
fuselage
skin
to
match
#30
holes
in
lowered
plates
(13
places
far
each
plate).
Reference
Pig.
SE
M20-255-1.
Repeat
for
UH
cut~ut
hole..
7.
install
RM
lowered
plate
(outside
of
fuselage
skin),
R/H
aluminum
screen
and
640246-002
ABS
baffle
(inside
of
fuselage
skin)
with
Avex
1691-0410-05
rivetsand
AN960-6
washers.
Sandwich
aluminun
screen
between
ABS
baffle
and
inside
surface
of
fuselage
skin
as
shown
in
Fig.
SE
M20-255-1.
Repeat
for
UH
side.
3.
Clean
up
area
and
install
ABS
interior
panels,
ii
remaved.
9.
Paint
rivets,
attaching
lowered
plates,
to
match
exterior
paint
color.
10.
Enter
compliance
note
in
log
book
and
return
aircraft
to
service.
Il.
RI
out
and
return
pre-addressed,
stamped
compliance
card.
PART
2:
REPLACE
ASSEMBLY
1N
CABrN
VENLlVITION
J-BOX
(FIG.
SE
M20-255-2)
(S/N
27-0053
THRU
27-0167
excluding
SIN
27-0094)
I
1,
Locate
cabin
ventilation
J-Box
in
forward,
RH
cabin
immediately
behind
firewall.
2.
Access
J-Box
assembly
by
loosening
QS100-M40S
clamp
at
J-Box
and
flex
tubing
connection;
replace
existing
640326-505
butterfly
assembly
with
new
640326-511
butterfly
assembly,
Fig.
SE
M20-
255-2
3.
Re-instaI(ffextubingto
J-Boxwith
QS100-M40S
clamp.
4.
Enter
compliance
note
in
log
book
and
retum
aircraft
to
service.
5.
Fill
out
and
retum
pre-addressed,
stamped
compliance
card.

SERVICE
BULLETIN
M20-255A
ISSUE
DATE:
November
17,
1993
Page
2
of
4
PART
3:
MODIRCATION
OF
SUDE
PLATE
ON
CABIN
VENTILATION
J-BOX
(FIG.
SE
M20-2553)
(S/N
27-0002
THRU
27-0052)
1.
Locate
cabin
ventilation
J-Box
in
forward,
RH
cabin
immediately
behind
firewall,
2.
Access
J-Box
slide
plate
assembly
by
loosening
QS100-M40S
clamp
on
J-Box
outlet
air
flex
tubing
connection.
Use
needle
nose
pliers
to
remove
MS16562-4
roll
pin
from
slide
plate.
Remove
cable
as-
sembly/cable
stops
from
slide
plate.
Remove
e~dsting
640010-000
slide
platetrom
J-Box.
3.
Modify
640010-000
slide
plate
by
dnlling
two
0.50
inch
diameter
holes,
in
locations
as
shown
in
FIG.
SE
M20-255-3.
Slide
Plate
must
now
be
re-identified
as
P/N
SE
M20-255-501;
use
indelible
ink
to
mark
P/N
on
body
of
slide
plate.
4.
Re-install
modified
slide
plate
into
J-Box
assembly.
Attach
cable
assembly
with
existing
cable
stops
and
hardware.
5.
Position
slide
prate
so
MS16562-4
roll
pin
can
be
inserted
into
hole
through
outlet
air
flex
tube
opening.
6.
Verify
slide
plate
operation
is
smooth
and
complete
travel
can
be
obtained
in
both
directions,
prior
to
installation
of
flex
tubing.
7.
Re-install
flextubingtoJ-Boxwith
QS100-M40S
clamp.
8.
Enter
compliance
note
in
log
book
and
retum
aircraft
to
service.
9.
Fill
outand
return
pre-addressed,
stamped
compliance
card.
Applicable
kits
should
be
ordered
from
Mooney
Service
Centers.
WARRANP~
Mooney
Aircraft
Corporation
will
allow
4.0
hours
labor
to
incorporate
applicable
portions
of
this
Service
Bulletin
on
AIC
S/N’s
27-0002
TH
RU
27-0137
and
1.0
hours
labor
on
A/C
S/N’s
27-01
38
THRU
27-0167
if
compliance
card
and
warranty
paper
work
is
received
from
Service
Center
by
Mooney
Service
Parts
Department
within
180
days
of
the
on’ginal
date
(September
29,
1993)
of
this
Service
Bulletin.
Normal
warranty
procedures
on
parts
and
kit
components
will
be
followed.
REFERENCE
DATA:
NIA
PARTS
UST:
PART
1-
Kit
Part
Number
-SB
M20-255-1
(S/N
27-0002
MRU
27-0137
U(CEPT
27-0094)
Item
..Part
Number
Descn’ption
Quantity
1.
.640130-000,..
Plate,
Louvered
(Painted)
.2
2
,640247-003
Screen,
Aluminum,
(16
mesh)
.2
3.
1691-0410-05
Rivet
(AVD()
26
4
.AN960-6
Washer
26
5.
-64029~-001
Baffle,
ABS,
LH
.1
6.
.640296-002
Baffle,
ABS,
RH
.1
7.
Paint
To
match
AIC
color
.1
8.
,Compliance
Card
To
be
retumed
to
Service
Parts
.1
NOTE
Matching
paint
will
be
shipped
with
kit.
Provide
aircraft
S/N
when
orden’ng
above
kit
part
number.
PART
2
Kit
Part
Number-
SE
M20-255-2
(S/N
27-0053
MRU
27-0167,
MCEPT
27-0094)
1.
6$0326-511
Butterfly
assembly
.1
2
.MS35206-226
Screw
.2
3.
Compliance
Card
To
be
retumed
to
Service
Paris
.1
FIGLERES/
TABLES:
See
Figures
SE
M20-255-1,
SE
M20-255-2
and
SE
M20-255-3
on
following
pages.

SERVICE
BULLETIN
M20-255A
ISSUE
DATE:
November
17,
1993
Page
3
of
4
2.26
o
o
lo\
(INSIDE)
10
~ci
2,90SKIN
BAFFLE
ALUMINUM
SCREEN
10
PLATE
1
~I
I
I
I
III´•
(CIUTSIDE)
VIEW
LOOKING
I)OWN
O
(RH
SHOWU
LH
TYPICAL)
O
O
-T~O
O
LOUVERED
PLATE
STA
-5,37
c-1
16.4
IN.
TO
TOP
SEE
j
ET~GE
OF
CUTOUT
\I
9,0
IN,
FRON
SKIN
LAP
TO
AFT
EDGE
OF
CUTOUT
(BOTH
SIDES
OF
STA
STA
100,00
53,00
FIGURE
1

Senrice
Bulletin
M20-255A
ISSUE
DATE:
November
17,
1993
Page
4
of
4
FLEX
J-BI7X
ASS
RH
VIEW
LDtlKING
INBOARD
O
O
O
BUTTERFLY
ASSY--,
LMS35206-226
SCREVS
<2>
SECURE
WITH
LOC-TITE
CV
FIGURE
2
0.50
inch
diameter
holes.
640010
SUDE
PLATE
TO
BE
RE-IDEN-
TIRED
TO
SE
M20´•255-501
AFTER
MODIRED
WITH
.625
TWO
0.50
INCH
HOLES
PER
THIS
ILLUSTRATION.
O
USE
INDEUBLE
(PERMANENT)
INK
ON
BODY
OF
?-1
.625
´•u~-
SLIDE
PLATE.
FIGURE
3

THIS
SERVICE
BULLETIN
IS
FAA
APPROVED
FOR
ENGINEERING
DESIGN
SERVICE
BULLETIN
M20-261
ISSUEDATE:
iDecember,
1996
SUBJECT:
BENDU(-MNG
SERVICE
BULLETIN
No.
SE
KT
76A-7,
JULY/96
(or
later
revision(s)),
KT
76A
ATC
TRANSPONDER
MODELSISIN
AFFECTED:
ALL
MODELS
OF
MOONC(AIRCRAFT
MANUFACTURED
SINCE
1975
(INCLUDES
M20C,
M20E,
M20F,
M20J,
M20K,
M20L,
M20M,
AND
M20FP
AND
ANY
MODEL
THAT
MAY
HAVE
HAD
A
KT
76A
TRANSPONDER
RETROFI~ED
SINCE
i
975
(INCLUDES
M20,
M20A,
M20B,
M20D,
M20G,
OR
M22)
(APPUES
TO
ALL
S/N’s)
TIME
OF
COMPLIANCE:
F~EFER
TO
BENDIX-KING
SE
KT
76A-7,
DATED
JULY/96
(or
later
revision(s)
INTFZODUCTION:
i,
Bendix-King
Service
Bulletin
No.
KT76A-7
provides
information
that
indicates
the
integrated
cir-
cuit
(IC)
of
the
KT76A,
P/N
066-1062-00/10!02,
Sn\l’s
from
93,000
to
109,000,
may
possess,
or
progress
to,
an
electronic
breakdown
within
the
IC
that
causes
either
or
both
of
the
following
malfunctions:
The
unit
may
incorrectly
interpret
the
output
of
the
encoding
attimeter.
or
2)
The
unit
may
transmit
a
code
other
than
what
is
set
land
shown)
on
the
face
of
the
t~ansponder
unit.
2
The
subject
Bendix-King
SE
provides
the
compliance,
retrofit,
warranty,
and
parts
list
information
necessary
for
the
retrofit
procedures
to
be
accomplished
by
appropriately
rated
Bendix-King
Seivice
Centers.
INSTRUCTIONS:
REFER
TO
BENDU(-KING
SE
Kr76A-7,
DATED
JULY/96
(or
later
revision(s)
WARRANPI:
I~EFERTO
BENDIX-KING
SE
KT
76A-7,
DATED
JULY/96
(or
later
revision(s)
REFERENCE
DATA:
~EFER
TO
BENDD(-KING
SE
KT
76A-7,
DATED
JULY/46
(or
later
revision(s)
PARTS
LIST:
F~EFER
TO
BENDU(-KING
SE
KT
76A-7,
DATED
JULY/96
(or
later
revision(s)
F1GURES/
TABLES:
FIEFERTO
BENDIX-MNG
SE
KT
76A-7,
DATED
JULY/96
(or
later
revision(s)

THIS
SERVICE
BULLETIN
IS
FAA
APPROVED
FOR
ENGINEERING
DESIGN
SERVICE
BULLETIN
M20-262
ISSUEDATE:
10January,
1997
SUBJECT:
TEX~RON
LYCOMING
SERVICE
BULLETIN
No.
5278,
DATED
8
OCTOBER,
1996,
(OR
SUBSEQUENT
REVISIONS),
RECALL
OF
PISTON
PIN,
P/N
LW14077
MODELS/S/N
AFFECTED:
ME
FOLLOWING
AIRCRAFT
SHOULD
BE
INSPECTED
TO
DETERMINE
1)
IF
LYCOMING
ENGINE
S/N’s
LISTED
ON
SUBJECT
LYCOMING
SERVICE
BULLETIN,
No.
5278
(OR
SUBSEQUENT
REVISION
ARE
INSTALLED.
2)
IF
CYUNDERASSEMBUES
OM-IICH
INCLUDE
PISTONS
AND
PISTON
PINS)
HAVE
BEEN
REPIJ\CED
SINCE
15
DECEMBER,
1995
3)
if
PISTON
PINS
ONLY,
HAVE
BEEN
REPLACED
SINCE
15
DECEMBER,
1995
IF
ANY
OF
1),
2)
OR
3)
ABOVE
CONDITIONS
ARE
FOUND,
COMPLIANCE
WITH
LYCOMING
SERVICE
BULLETIN
No.
5278
(OR
SUBSEQUENT
REVISIONS)
INSTRUC-
TIONS
MUST
BE
ACCOMPLISHED
IN
ACCORDANCE
WITH
ALL
PARAMETERS
OF
THE
SERVICE
BULLETIN.
M20A,M20B,
M20C,
M20D,
M20E,
M20F,
M20G
AL,
SIN’s
8
M20J
S/N’s
24-0001
THRU
243380
IF
RETROFITTED
WITH
NEW,
OVERHAULED
OR
REMANUFACTURED
ENGINES
OR
CYUNDERASSEMBLIES
(PISTONS
8
PISTON
PINS
IN
CYLINDERS)
OR
PISTON
FINS
ONLY,
SUPPLIED
BY
LYCOMING
BET~
15
DECEMBER
1995
THRU
17
SEPTEMBER,
1996.
M20J
SIN’s
24-3381
MRU
24-3389,
24-3391
AIRCRAFT
WITH
ENGINES
MANUFACT-
URED
BETWEEN
15
DECEMBER,
1995
THRU
17
SEPTEMBER,
1996
INSTALLED
DURING
PRODUCTION.
M20M
SIN
27-0001
THRU
27-0210
WITH
-AF1B
ENGINE
RETROFIT
KIT
INSTALLED
OR
IF
v\nTH
NEW,
OVERHAULED
OR
REMANUFACTURED
ENGINES
OR
Cn-
INDERASSEMBLIES
(PISTONS
8
PISTON
PINS
IN
CYLINDERS)
OR
PISTON
PINS
ONLY,
SUPPLIED
BY
LYCOMING
BETVMW
15
DECEMBER
1995
THRU
17
SEPTEMBER,
1996.
M20M
SIN
27-0212
MRU
27-0214,
27-0217
NOTE:
Aircraft
Serial
Number
effectivity
is
based
on
original
manufactun‘ng
records.
To
determine
final
applicability,
verify
engine
sen~al
number
and
consult
Textron
Lycoming
Service
Bulletin
527(8)
or
subsequent
revision
TIME
OF
COMPLIANCE
SEETDCTRON
LYCOMING
SERVICE
BULLETIN
No.
5278,
8
OCTOBER,
1996
(OR
LATER
REVISION)
INTF~ODUCTION:
SEETMTRON
LYCOMING
SERVICE
BULLETIN
No.
5278,
8
OCTOBER,
1996
(OR
LATER
REVISION)
INSTRUCTIONS:
SEETDCTRON
LYCOMING
SERVICE
BULLETIN
No.
5278,
8
OCTOBER,
1996
(OR
LATER
REVISION)
VWRRANTY:
SEETDCTRON
LYCOMING
SERVICE
BULLETIN
No.
5278,
8
OCTOBER
1996
(OR
LATER
REVISION)
REFERENCE
SEE
TEXTRON
LYCOMING
SERVICE
BULLETIN
No.
5278,
8
OCTOBER,
1996
DATA:
(OR
LATER
REVISION)
PARTS
LIST:
SEE
TDCTRON
LYCOMING
SERVICE
BULLETIN
No.
5278,
8
OCTOBER,
1996
(OR
LATER
REVISION)
FIGURESI
TABLES:
SEE
TECTRON
LYCOMING
SERVICE
BULLETIN
No.
5278,
8
OCTOBER,
1996
(OR
LATER
REVISION)

THIS
SERVICE
BULLET1N
IS
FAA
APPROVED
FOR
ENGINEERING
DESIGN
SERVICE
BULLmN
M20
-263
ISSUE
DATE:
15
August,
1997
SUBJECT
Seat
Belt
retainer
bushings
nylon
grommet
failure.
MODEYS/N
AFFECTED.
M20
Series
ALL
SIN’s
with
Non-lnertial
Reel
Shoulder
Restraints
installed
M20J
24-0001
thru
24-1685
-With
Non-lnertial
Reel
Shoulder
Restraint
Assemblies
24r1686
thru
24-TEA
With
Rear
Seat
Should
er
Restraint
Assemblies
M20K-
25-0001
thru
25-1224
With
Non-inertial
Reel
Shoulder
Restraint
Assemblies
25-1225
thru
25-TEA
Wrth
Rear
Seat
Shoulder
Restraint
Assemblies
M20L-
26-0001
thru
26-0041
Wrth
Rear
Seat
Shoulder
Restraint
Assemblies
M20M
27-0001
thru
27-iBA
\Nnh
Rear
Seat
Shoulder
Restraint
Assemblies
M20R-
29-0001
thru
29-TBA-
With
Rear
Seat
Shoulder
Restraint
Assemblies
M20J
S/N’s
24-1150
thru
24-1417
M20K
S/N’s
25-0560
thru
250780
had
Indiana
Mills
Seat
8elt
and/or
Shoulder
Restraint
Assemblies
instail~d
during
production,
however,
if
any
replacement
has
been
accomplished,
the
replacement
Seat
Belt/Restraint
Assembly
may
have
the
retainer
bushing,
nylon
grommet
configuration.
NOTE
AM-Safe
Brand
shoulder
restraint~s
incorporate
a
retainer
bushing
used
for
the
cargo
restraint
tie
down
system
for
the
rear
seats.
These
retainer
bushing’s
should
also
be
inspected
for
missing
or
defective
nylon
grommets
used
in
the
original
configuration.
TIME
OF
COMPLIANCE:
Within
the
next
25
operational
hours
or
at
next
maintenance
action.
INTRODUCTION:
Ramp
inspections
at
some
airports
have
found
the
nylon
grommets
missing
or
broken
from
shoulder
hamess
retainer
bushings
on
several
model
aircraff.
Unauthon’zed
repairs
using
ty-raps
have
been
found.
The
Ty-rap’s
locking
tab
may
prevent
the
restraint
buckle
from
properly
snapping
into
position
or
may
create
difficuit~s
in
releasing
the
restraint
buckle
in
an
emergency.
The
intent
of
this
SE
is
to
provide
information
for
inspection
and
correctly
repain~ng
any
defective
retainer
bushing
grommet
that
may
have
failed.
INSTRUCTIONS:
Figure
SE
hi120-263-1
depicts
the
conditions
that
may
be
found
on
any
seat
belt/restraint
assembly.
Refer
to
the
illustration
and
follow
the
procedures
shown
on
the
figure.
VWRRANTY:
Mooney
Aircraft
Corpoiation
will
allow
0.5
hours
laborto
inspect
and
repair
the
seat
beltl
harness
restraints
on
aircraft
still
WITHIN
WARRANTY.
The
parts
will
be
available
through
your
Mooney
Service
Center.
k~our
account
will
be
credited
in
the
normal
manner
when
properly
completed
warranty
claims
are
reiumed
to
Service
Parts
Department,
Kenviile.
TX.
REFERENCE
FAA
General
Aviation
Airworthiness
Alerts,
AC
No.
43-16,
No,
210,
January,
1996
DATA:
PARTS
UST~
Kit
Part
number
SE
M20-263-1
lTEM
P/N
DESCRIPTION
QT/
1
HRSR-1/2
GROMMET
4
Vendor
for
Grommet:
XL
Technologies
1315
So.
Park
Dr.
Kernsvitle,
NC
27284
Telephone:
(910)
966-6777
Fax:
(910)
9~6-2887
FIGURES/
TABLES:
See
Figure
SE
M20-263
-1
on
next
page.

t,
~I
;OIC!
5m
rnm
o
I
II(
--EXISTING
NYLON
BUSI-IING
IN
PLACE
oo
II
I-_11
(1I\ISPECT
FOR
DEFECTS)
IJNSAFE--NILON
F
BUSIIING
MISSING
co
RETPOFIT
PROCEDUPES
tlRSR-I/P
T~RDMMES
SLIPPED
OVER
STUD
c
2.
APPLY
NEAT
FROW
I´•IEAT
GUN
Tn
S~-IRINK
GROMMET
o,
i
3
HRSR-1/2
~ROMMET
SWRUNK
IN
PLACE
´•\,r,~
´•´•t,\ri´•\,
4
VERIFY
SIIOULDCR
RES7laAINT
SNAPS
OVER
GRUMMET
SECURELY
I
III
’Y
\i’
i.
I
i
I(´•´•i
\t\
ii:
1~

THIS
SERVICE
BULLETIN
IS
FAA
APPROVED
FOR
ENGINEERING
DESIGN
SERVICE
BULLETIN
M20-264
ISSUEDATE:
1
February,
1998
SUBJECT:
Aileron,
Center,
Control
Links
Inspection
MODELSIS~
M20B,
M20C,
M20D,
M20E,
M20F,
M20G
ALL
SERIAL
NUMBERS
AFFECTED:
M20J
S/N
24-0001
THRU
24-3359
M20K
S/N
25-0001
THRU
25-1999
N120L
ALL
SERIAL
NUMBERS
M20M
S/N
27-0001
MRU
27-0197
M20R
S/N
29-0001
THRU
29-0042
TIME
wn~in
nex~
25
hours
of
operation
and
in
accordance
wil~
NOTE
2
below.
INTRODUCTION:
There
have
been
reports
of
a
crack
adjacent
to
the
weld
area
of
the
LH
aileron,
center
control
link,
P/N
730005-1.
Since
the
LH
6
RH
are
very
similar,
a
is
requested
that
an
inspection
of
both
of
these
control
links
be
completed
in
accordance
with
the
instrudions
shown
below.
The
part
numbers
to
be
inspected
are
as
follows:
M20B,
M20C,M20D,
M20E,
M20F,
M20G,
M20J,
M20K
730005-1
(LH)
6
730006-000
(RH)
M20L,
M20M
730051-501
(LH)
6
730052-501
(RH)
INSTRUCTIONS:
I.
Remove
Iower
belly
skin
to
gain
access
to
underside
of
aircraft:
Aluminum
Belly
Skin
aircraft
lst
skin
aff
of
nose
wheel
well
Smooth
fiberglass
belly
aircraft
Forward
fiberglass
skin
NOTEQ
ff
during
a
Visual
inspection
it
is
determined
that
either
control
link
has
a
reinforcing
gusset
at
the
2nd
900angIe
joint
from
Helm
bearing,
(link
has
been
replaced),
no
further
inspection
is
required
for
that
control
link.
W
both
links
have
been
replaced,
reassemble
belly
skin
and
proceed
to
step
9
thru
11.
2.
If
a
visual
inspection
determines
that
there
are
no
reinforcing
gussets,
remove
LH
6
RH
aileron,
cen-
ter,
control
links.
Note
location
of
spacer
between
LH
RH
control
links
at
attach
bolt.
Remove
paint
from
the
area
to
be
inspected.
3.
When
paint
and/or
any
foreign
maten~al
have
been
removed
from
the
weld
area
of
the
2nd
900
angle
joint
(2nd
from
Helm
bean’ng),
conduct
a
Magnetic
Particle
Inspection
of
each
link
on
that
2nd
90"
angle
joint.
4.
Carefully
inspect
the
results
of
the
Magnetic
Particle
Inspection
to
determine
if
any
discrepancy
e~a’sts
at
the
weld
area,
either
in
the
weld
or
in
the
adjacent
tube
material.
5,
If
no
discrepancies
exist,
dean
area,
prime
and
repaint
area
(epoxy
paint
recommended).
6.
Reinstallthe
e>dsting
good
control
links.
NOTEZ
If
existing
good
control
links
are
not
replaced
at
this
time,
repetitive
inspections,
in
ac-
cordance
with
this
SE,
are
required
at
each
annual
or
100
hour
inspection
thereafter.
7.
If
discrepancies
are
found,
proceed
to
PARTS
LIST
below.
6.
Connect
attaching
bolts,
spacer,
nuts
and
washers
in
accordance
with
AC43-13
or
Mooney
Service
3
Maintenance
Manual
instructions.
Lubn’cate
Helm
bearings
withTeffon
spray
lubricant
per
S
M.
9.
Verify
aiieron
rigging
in
accordance
with
the
proper
section
of
the
applicable
model’s
S
6
M
manual.
10.
When
rigging
is
verified
to
be
correct,
reinstall
aircraft
aluminum
belly
skin
or
fiberglass
skin.
Other manuals for M20M
2
Other Mooney Tools manuals
Popular Tools manuals by other brands
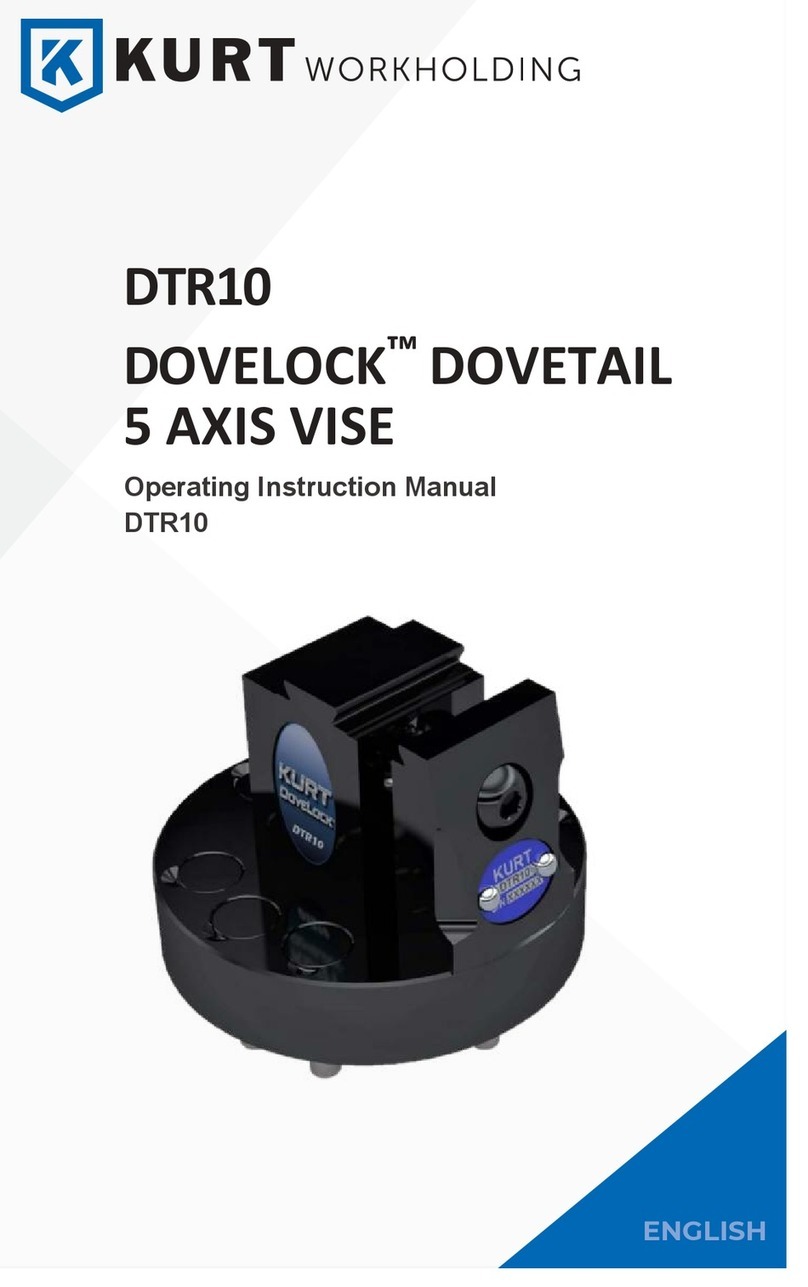
Kurt
Kurt DTR10 Operating instructions manual
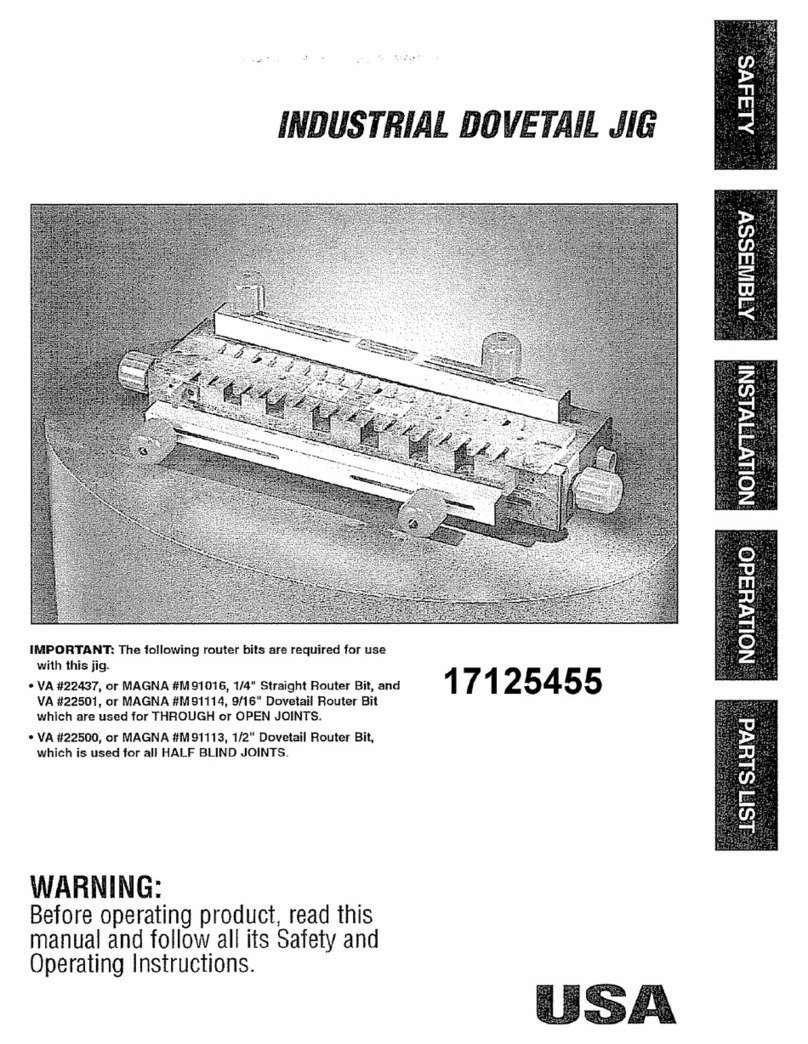
Craftsman
Craftsman 17125455 operating instructions
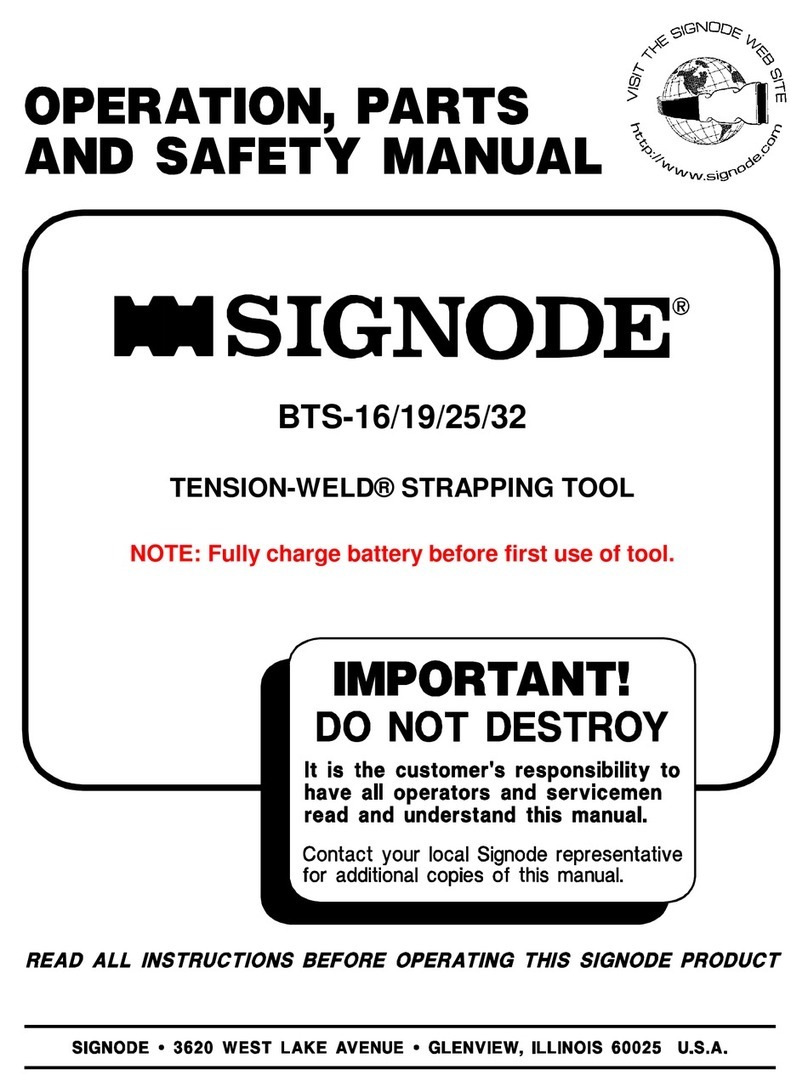
Signode
Signode Tension-Weld BTS-16 Operation, parts and safety manual
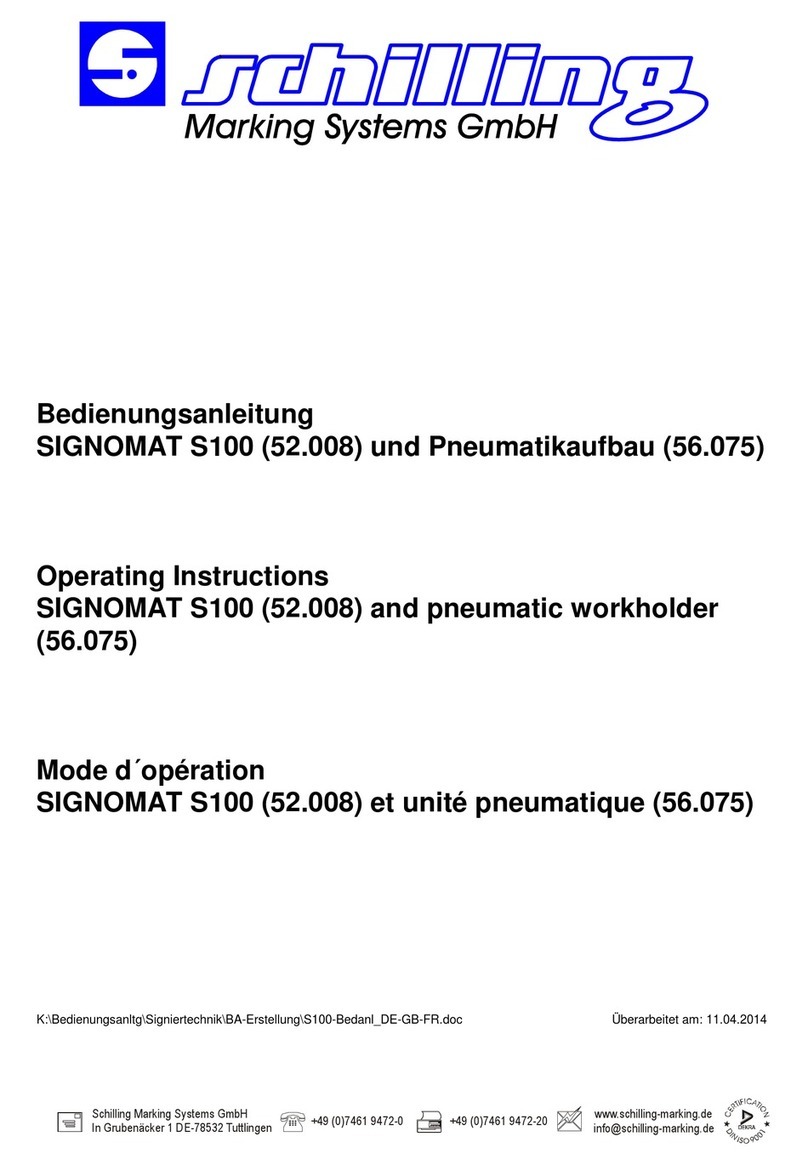
Schilling
Schilling SIGNOMAT S100 operating instructions

Framers Corner
Framers Corner T225 Operator's manual
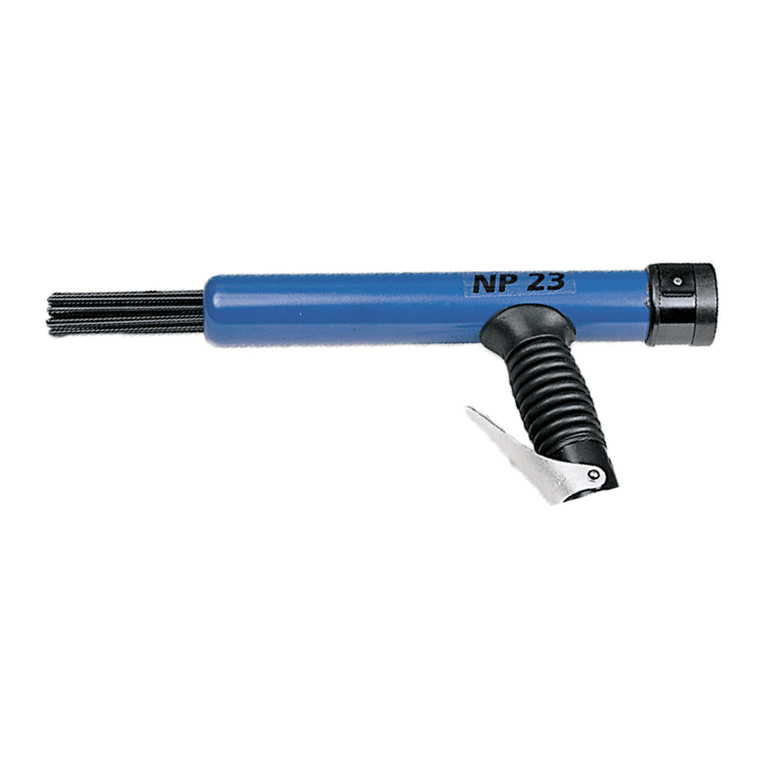
Von Arx
Von Arx NP Series operating manual