Pressure Tech THE SS-414 Series Service manual

1
THE SS-414 SERIES
Operating and Service Manual
Series includes all variants of SS-414
Issue A
March 2020

2
TABLE OF CONTENTS
1. Description.............................................................................................................................3
2. Installation .............................................................................................................................3
3. Operation...............................................................................................................................5
4. Special Conditions for Safe Use .............................................................................................6
5. Hazardous Location Usage.....................................................................................................6
6. Servicing and Maintenance....................................................................................................6
6.1. Servicing the SS-414G.............................................................................................7
6.1.1. Accessing the Main Valve Assembly ...................................................................7
6.1.2. Accessing the Sensor Assembly (NV)..................................................................9
6.1.3. Accessing the Top Works Assembly..................................................................10
6.1.4. Figure 1 –Sectional View of the SS-414G.........................................................11
7. Technical Data......................................................................................................................12
8. Warranty Statement ............................................................................................................12

3
1. Description
The SS-414 is a ‘medium flow’ piston sensed pressure reducing regulator, which incorporates
a balanced main valve to provide stable control under varying inlet pressures. The regulator
has the option of a PEEK or PCTFE seat for gas service and Tecasint or ceramic for hydraulic
service.
These regulators can operate at depths of up to 3,000 metres, either using the external
seawater pressure as a reference pressure or working within a sealed chamber to remain
completely unaffected by outside conditions.
Operating at depths of up to 3,000 metres (10,000ft), the SS414 have been designed and
manufactured specifically to produce the highest standard of results within the challenging
subsea environment and features NV or SV 1:1 ratio sensor assembly, as standard for sub-sea
applications and incorporates, the option of the following top works assemblies, dependant
of the functionality requirements:
-‘SR’ - Spring Loaded with Reference to External Sea Water Pressure. (*Ref. 6.1.4 for
Reference Port detail, circled in red)
-‘SS’ – Spring Loaded with Sealed Chamber to remain completely unaffected by the
external sea water environment conditions. (Without Reference port)
Pressure Equipment Directive (PED) 2014/68/EC Declaration
This equipment is designed and manufactured in accordance with Sound Engineering Practice
(SEP) Article 4, Paragraph 3 of the directive 2014/68/EC. As such, CE marking must not be
applied. The equipment is marked under section 3.3 of Essential Safety Requirements of the
directive.
2. Installation
Before system start-up, it is recommended that all lines should be free from any form of
contaminations, as those can affect regulator performance and functionality. all systems be
pressure tested, leak tested and purged with an inert gas such as nitrogen.
Prior to placing into service ensure that the regulator is in the fully closed position, with the
adjusting mechanism turned completely anti-clockwise.
For pre-set regulators the supply pressure should be increased gradually and also to be
mindful that downstream pressure will be present.
Check the model number reference to ensure that the pressure range complies with the
installation requirements.
Visually inspect the regulator for any signs of damage or contamination. If any foreign
materials are present and cannot be removed from the regulator, or if the threads on the
regulator appear to be damaged, please contact the office immediately to arrange for the
regulator to be returned for service.

4
The Inlet and Outlet ports are clearly marked. Select the correct size and type of connection
fittings for these ports which are indicated in the regulators part number. The connection
type options that are available on this regulator are: British Standard Pipe (BSPP) ‘B’, National
Pipe Thread (NPT) ‘N’and Medium Pressure (MP) ‘A’. Use the correct dowty or bonded seal
for BSPP connections, self-centering seals are recommended. For NPT threads, ensure that
PTFE tape is applied correctly to the fittings, applying two overlapping layers in the direction
of the thread, taking care that the tape does not come into contact with the first thread. For
MP, the correct torque values to be used as specified by fitting manufacturer.
Any gauge ports on the regulator will be 1/4” NPT unless otherwise stated. If any gauge port
is not required, ensure that the port is plugged prior to installation. The SS414 can be also
supplied as self-venting (SV), which will have additional vent port, fitted with a filter.
The media supplied to the regulator must be clean. Contamination can damage the seat which
may cause the regulator to fail. Filtration suited to the application is recommended upstream
of the regulator.
Should further assistance or information be required in relation to installation of any Pressure
Tech regulator please contact the office, giving reference to the regulators part number
and/or serial number.

5
3. Operation
The SS-414 series of regulator are fitted with a stainless-steel locking cap as standard. It is
recommended that for the pressure adjustment the locking cap is removed, and a 17mm
spanner (or adjustable) is used to control and set the outlet pressure. The locking cap should
then be secured to the adjusting screw and bonnet by tightening the respective grub screws
to prevent further adjustments.
Turning the adjusting screw clockwise compresses the load spring, which in turn opens the
main valve, and allows the inlet pressure to pass through the orifice until the outlet pressure
is equivalent to the loading forces set by the compressed spring.
The SS-414 is offered with either a sealed chamber, or a reference chamber.
A sealed chamber option ensures that the outlet pressure set at the surface will remain
unaffected by sea water pressure during its operation
A reference chamber allows the regulator to respond to the atmospheric conditions during
its descent and/or ascent* at an approx. ratio of 1:1. The subsea regulator with reference
must be ‘self-venting’ in order to respond to the external atmospheric conditions during
ascent.
Where applicable, the vent port and the reference port of the SS-414 are fitted with a debris
filter as standard.
The SS-414 can be supplied set and locked to pre-defined pressure conditions. Regulators will
be fully adjustable through a given pressure range and the maximum allowable working
pressures will be indicated on the regulator label and in the part number.
Pressure locking regulators are fitted with a locking cap which may be set (when specified) to
pre-determined requirements. It is secured in place by three M5 grub screws which lock
against the bonnet of the regulator creating an anti-tamper device to ensure the pressure
cannot be adjusted accidentally.
Pre-set pressure regulators are adjusted (factory set) to specified customer requirements
within a given pressure range.

6
4. Special Conditions for Safe Use
The SS-414 series are pressure regulators and should not be used as an isolation valve. When
adjusting Non-Venting (NV) option, the outlet pressure shall be reduced by venting
downstream of the regulator whilst simultaneously turning the adjusting mechanism anti-
clockwise. (*Ref. 6.1.3)
Sudden dynamic high-pressure inlet pressures should be avoided, and preferably be gradually
increased to protect against damage to the regulator. Any resonating within regulator may
cause the regulator to malfunction and it is not recommended to be used under these
conditions.
5. Hazardous Location Usage
This equipment has not been manufactured specifically for use in potentially explosive
atmospheres and as such an ignition hazard assessment has not been carried out on this
product. If the user should wish to use this product in such an environment where there may
be a potentially explosive atmosphere then it is the responsibility of the user to conduct an
ignition hazard assessment against 99/92/EC.
6. Servicing and Maintenance
Servicing and maintenance work on the SS-414 regulators should only be performed after
fully reading and understanding the Operating and Servicing Manual. Due to the
compressibility of gases, the operator should not endanger themselves or others by working
on this regulator without prior knowledge of the Health and Safety risks relating to handling
of technical gases. Any uncertainty should be clarified with Pressure Tech before working on
the regulator.
Pressure Tech Ltd recommends the use of the following Lubricants/Adhesives during
servicing:
-Krytox GPL 205 lubricant: For the O-rings.
-Molykote 1000 paste: For the adjusting screw.
-Loctite 638: For the hard seat and seat nut Threads.
Prior to commencing service, please ensure that:
-The equipment has been de-pressurised
-The load spring has been de-compressed by turning the adjusting mechanism fully
anti-clockwise
-Applications involving toxic, flammable or corrosive media have been fully purged and
decontaminated sufficiently for safe service.
To ensure the best possible results from servicing, when re-assembling the regulator and any
assemblies within it, ensure that all areas of the components and the regulator body are
cleaned and free from contaminants which may result in failure of the regulator.

7
We recommend that the filter should be removed and the vent port should be piped off to
safe location or drain and should not point towards the operator during service work, if using
a hazardous media through the regulator.
6.1. Servicing the SS-414G
*Note: Fig 1 should be used as a reference for the following set of instructions
6.1.1. Accessing the Main Valve Assembly
*The top works and sensor assembly must first be removed to access the main valve
assembly. Before continuing follow the steps ‘i. – X.’ shown in - ‘6.1.2. Accessing the Sensor
Assembly’.
To access the Main Valve Assembly:
i. With the flats of the regulator body (29) secured in a vice*, Unscrew** the Body
Nut (31) from the Body (29) of the regulator to access the lower section of the
main valve assembly.
*NOTE: Soft vice jaws must be used, when securing the body within the vice
against flats. Due to the position of the flats it may be necessary to angle the body
in the vice with the bottom nut upright for access.
**NOTE: That the Bottom Nut has been torqued to 30Nm.
ii. Remove and replace the ‘O’ rings (8 & 30) located on the Bottom Nut (31)
iii. Remove the Main Valve Spring (19).
iv. Secure the upper section of the Main Valve (18) with a 10mm socket and use a
7mm socket to turn the Seat Nut (17) anti-clockwise.
v. Remove the Seat Nut (17) with ‘O’ rings (8,12,30) and Soft Seat (21) from the lower
main valve assembly.
vi. The Main Valve Pin (18) should be removed* through the top of the regulator to
avoid damaging the ‘O’ ring (11) and Back Up Ring (13) located on it.
*NOTE: The Main Valve Pin (18) can only be removed this way.
vii. Remove the Hard Seat (20) from the regulator Body (29) by turning it anti-
clockwise with a 19mm socket.
*NOTE: There may be some increased resistance and good fit between socket and
hard seat must be achieved to prevent it from any potential damage on flats.
viii. Apply two drops of Loctite thread lock 638 (or equivalent) and insert a new Hard
Seat (20) into the regulator Body (29) after carefully positioning the 12 x 1mm ‘O’
ring (6) into the body.
ix. Check for any damage* on the main valve (18), replace where required.
*NOTE: for (SV) regulators, special attention must be paid to sealing face on the
cone, located on the top of the valve, replace where required.
x. Replace the ‘O’ ring (11) and Back-Up Ring (13) on the Main Valve (18) (ensuring
adequate lubrication is used) and place the main valve into position through the
top of the regulator body with the hex section facing upwards.
xi. Turn the regulator body upside down so that the lower section of the main valve
is visible and place a new Soft Seat (21) onto the Main Valve stem (18).

8
xii. Apply two drops of Loctite thread lock 638 (or equivalent) on the M6 thread within
the Seat Nut (17)
xiii. Replace the BS-610 ‘O’ ring (12) and place into the Seat Nut (17).
xiv. Screw the Seat Nut (17) on to the Main Valve (18) and tighten both parts together
using a 10mm socket (on the main valve hex) and a 7mm socket (on the seat nut
hex).
xv. Place the Valve Spring (19) into the Bottom Nut (31) and whilst holding the
regulator body (29) upright, screw both parts (19,31) into the regulator Body (29).
Tighten the bottom nut to 30Nm.
IMPORTANT: Ensure that the OR-BS028 ‘O’ ring (30) is located correctly within the
‘O’ ring groove of the Bottom Nut (31).
To ensure that the main valve assembly has been correctly and effectively installed it may be
required to perform the appropriate seat leak test as per ANSI/FCI 70-2.

9
6.1.2. Accessing the Sensor Assembly (NV)
The loading mechanism and sensor assembly for the SS-414 can be accessed from the top of
the regulator. Ensure the spring is de-compressed by rotating the Adjusting Screw fully anti-
clockwise and follow the instructions below:
To access the Sensor Assembly:
i. Remove the securing M3 Grub Screw (3) from the regulator Body (29).
ii. Unscrew the Pan Screw (2) and remove the Name Plate (23) from the Locking Cap
(25)
iii. Loosen the 3x M6 Grub Screws (4) and the 2x M6 Grub Screws (5) in the Locking
Cap (25) and lift the locking cap from the assembly
iv. With the flats of the regulator body (29) secured in a vice*, remove** the Bonnet
(27) by using a torque wrench or equivalent with 47mm open end
*NOTE: Soft vice jaws must be used, when securing the body within the vice
against flats. Due to the position of the flats it may be necessary to angle the body
in the vice with the bottom nut upright for access.
**NOTE: That the Bonnet has been torqued to 120Nm.
v. Un-screw and lift the top works from the assembly, inclusive of the Bonnet (27),
Load Spring (36), adjusting mechanism (1,7,9,10,24,28) from the body.
vi. The sensor assembly (14-16,22,33-35) can be removed from the body by using
pliers.
vii. Remove the Sensor (34) from the Sensor Holder (33), by pressing the sensor (from
the domed top) out of the sensor holder.
viii. Replace all ‘O’ rings (14-16,35) located on the Sensor (34) and Sensor Holder (33)
prior to reassembly, ensuring adequate lubrication is used.
ix. Push the Sensor (34) into the Sensor Holder (33), ensuring the sensor holder is
oriented correctly in relation to the sensor (See figure 1)
x. Place the sensor assembly (14-16,33-35) into the regulator Body (29) ensuring that
it is firmly in place. Press down on the sensor (34), ensuring that it springs back
into position to ensure all parts are engaging correctly.
xi. Screw the top works assembly, inclusive of the Bonnet (27), Load Spring (36),
adjusting mechanism (1,7,9,10,24,28) into the regulator Body (29) and using a
torque wrench, tighten to 120Nm.
xii. Tighten* the securing M3 Grub Screw (3) against the Bonnet (27).
*NOTE: Take care to not overtight as this may damage M3 hex socket.
xiii. The Locking Cap (25) can now be secured on to the Adjusting Screw (28) using the
2x M6 Grub Screws (5).
xiv. The Name Plate (23) can then be secured using the Pan Screw (2).
The regulator is ready to be set. When the desired outlet pressure has been set, use the 3x
M5 Grub Screws (4) to secure the Locking Cap (25) to prevent further adjustment.
It is recommended that all parts in the repair kits are used. Any defect parts removed during
the service should be disposed of.

10
6.1.3. Accessing the Top Works Assembly
The loading mechanism for the SS-414 can be accessed from the top of the regulator. Ensure
the spring is de-compressed by rotating the Adjusting Screw fully anti-clockwise and follow
the instructions below:
To access the Top Works Assembly:
i. Remove the securing M3 Grub Screw (3) from the regulator Body (29).
ii. Unscrew the Pan Screw (2) and remove the Name Plate (23) from the Locking Cap
(25).
iii. Loosen the 3x M6 Grub Screws (4) and the 2x M6 Grub Screws (5) in the Locking
Cap (25) and lift the locking cap from the assembly.
iv. With the regulator secured up-right in a vice, remove the Bonnet (27) by using a
torque wrench or equivalent with 47mm open end.
*NOTE: Soft vice jaws must be used, when securing the body within the vice
against flats. Due to the position of the flats it may be necessary to angle the body
in the vice with the bottom nut upright for access.
v. Un-screw and lift the top works from the assembly, inclusive of the Bonnet (27),
Load Spring (36), adjusting mechanism (1,7,9,10,24,28) from the body.
vi. Screw the Adjusting Screw (28), down into the Bonnet (27) to help push out the
remaining adjusting mechanism (1,9,10,24).
vii. The Adjusting Screw (28) can be removed by un-screwing anticlockwise until
released from the Bonnet (27).
viii. Remove/replace the ‘O’ rings (7) from around the Adjusting Screw (28) as required,
prior to reassembly, ensuring adequate lubrication is used.
ix. Lift the load spring (24), upper spring rest (29) and ball bearing (28) from the
assembly.
x. Remove/replace the ‘O’ ring (9) from around the lower spring rest (24), prior to
reassembly, ensuring adequate lubrication is used.
xi. Remove/replace the ‘O’ rings (10) from around the Bonnet (27), prior to
reassembly, ensuring adequate lubrication is used.
xii. Screw the Adjusting Screw (28) into the Bonnet (27) until each of the ‘O’ rings (7)
have entered the bore and are no longer visible.
xiii. Place the Load Spring (36) onto the Lower Spring Rest (24), then locate the upper
spring rest (29) and ball bearing (28), onto the top of the Load Spring and place the
full assembly into the Bonnet (27).
xiv. Screw the top works assembly, inclusive of the Bonnet (27), Load Spring (36),
adjusting mechanism (1,7,9,10,24,28) into the regulator Body (29) and using a
torque wrench, tighten to 120Nm.
xv. Tighten the securing M3 Grub Screw (3) against the Bonnet (27).
xvi. The Locking Cap (25) can now be secured on to the Adjusting Screw (28) using the
2x M6 Grub Screws (5).
xvii. The Name Plate (23) can then be secured using the Pan Screw (2).
The regulator is ready to be set. When the desired outlet pressure has been set, use the
3x M5 Grub Screws (4) to secure the Locking Cap (25) to prevent further adjustment.
It is recommended that all parts in the repair kits are used. Any defect parts removed during
the service should be disposed of.

11
6.1.4. Figure 1 –Sectional View of the SS-414G
© Copyright of Pressure Tech Ltd
PARTS LIST
ITEM
QTY
PART NUMBER
DESCRIPTION
1
1
BALL-010-SS-316
10MM BALL BEARING
2
1
FIT-M3-08-A4-70.0-SKT-BTN
M3 x 8mm SOCKET BUTTON SCREW
3
1
FIT-M3x4MM-SS-316-GRUBSCRW
M3 x 4mm SET SCREW
4
3
FIT-M6-08-A4-SKT-FLT-SET
M6 x 8mm SET SCREW
5
2
FIT-M6-16-A4-SKT-FLT-SET
M6 x 16mm SET SCREW
6
1
OR-0120-10
O' RING STD
7
2
OR-0130-15
O' RING STD
8
1
OR-0270-25
O' RING STD
9
1
OR-0350-20
O' RING STD
10
2
OR-0530-25
O' RING STD
11
1
ORB-PT-C-082
BACK UP O' RING
12
1
OR-BS610
O' RING STD
13
1
OR-BS4518-0066-24
O' RING STD
14
1
OR-BS4518-0246-24
O' RING STD
15
1
OR-BS4518-0416-24-NBR-70
O' RING STD
16
1
OR-BS4518-0456-24
O' RING STD
17
1
PT-300-MF-005-001
SEAT NUT
18
1
PT-305-MF-001-005
MAIN VALVE (PEEK-HP)
19
1
PT-305-MF-005
MAIN VALVE SPRING
20
1
PT-305-MF-008
SEAT
21
1
PT-C-002-015-001
PCTFE SEAT
22
1
PT-C-038
SLIDE RING
23
1
PT-C-049
NAMEPLATE
24
1
PT-C-095-001
SPRING REST - DOME
25
1
PT-C-100-004
LOCKING CAP
26
1
PT-C-125-001
UPPER SPRING REST
27
1
PT-C-126-004
SUBSEA BONNET - NO REFERENCE
28
1
PT-C-127-004
SUBSEA ADJUSTING SCREW
29
1
PT-SS-414-N-06A-SS-NV
SUBSEA BODY - N PORTING
30
1
OR-BS028
O' RING STD
31
1
PT-305-MF-011
SUB SEA BOTTOM NUT
33
1
PT-C-253
32mm SENSOR HOLDER
34
1
PT-C-252
SENSOR 32MM
35
1
OR-0290-20
O' RING STD
36
1
SPR-R40X89-002
LOAD SPRING

12
7. Technical Data
Fluid Media: All gases and liquids compatible with materials of
construction
Max Inlet Pressure: 414 bar (6,000 psi) for Ceramic/Tecasint/PEEK
300 bar (4,350 psi) for PCTFE
Outlet Pressure Range: 5-250 bar (3,625 psi)
Operating Temperature: -20°C to +80°C
Materials: Body and Trim: 316 SS
Seat Gas: PEEK® or PCTFE
Seat Hydraulic: Ceramic or Tecasint
Flow Capacity (Cv): 2.0
Leakage: Hydraulic: Zero drops of water at max inlet
Gas: Bubble tight
8. Warranty Statement
Pressure Tech Ltd guarantee all products correspond with their specification at the time of
delivery and, with exception to wear and tear, wilful damage, negligence, and abnormal
working conditions, will be free from defects for a period of 12 months from date of delivery.
Table of contents
Other Pressure Tech Controllers manuals
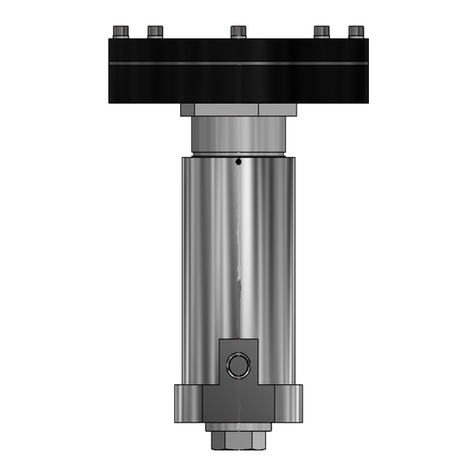
Pressure Tech
Pressure Tech LF-792 Series Service manual
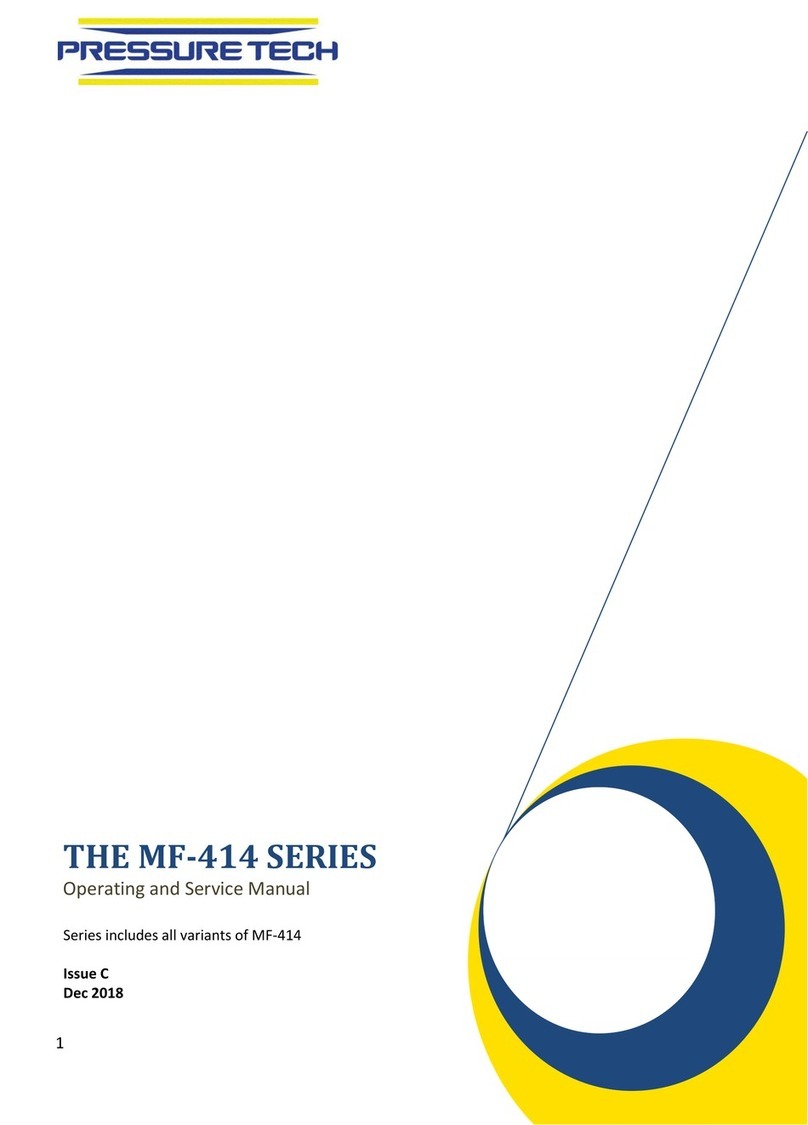
Pressure Tech
Pressure Tech MF-414 Series Service manual
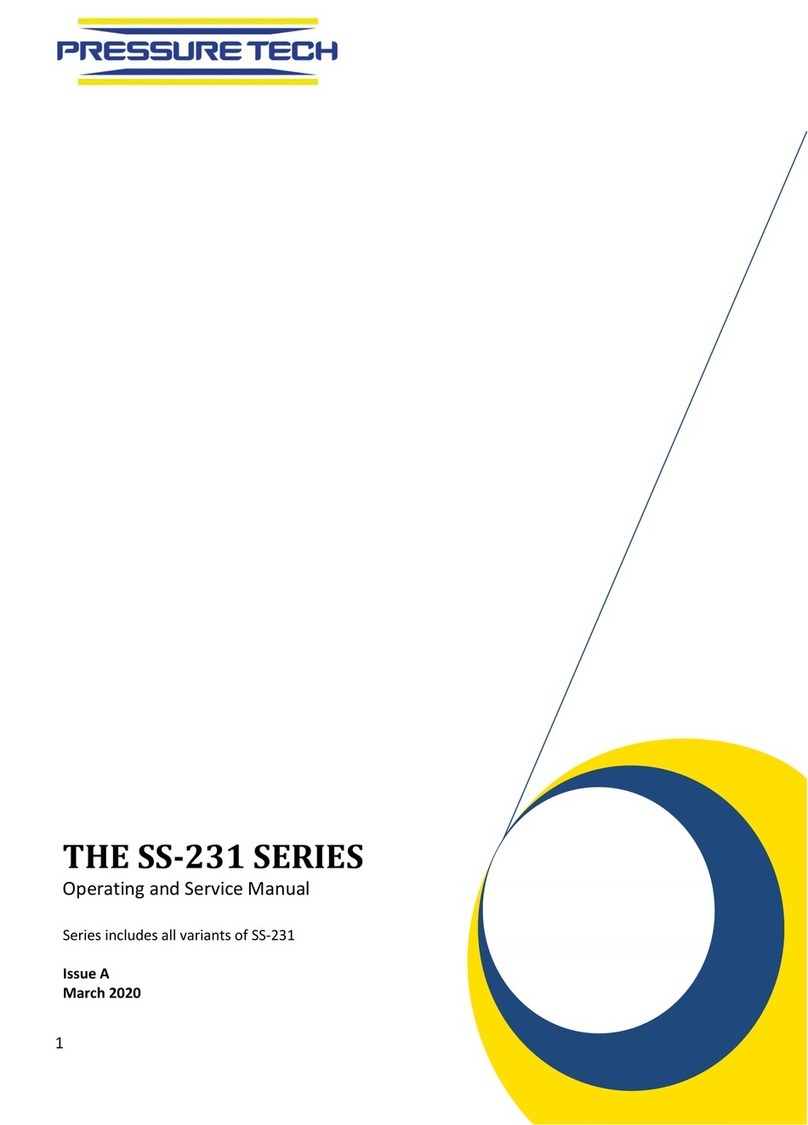
Pressure Tech
Pressure Tech SS-231 Series Service manual
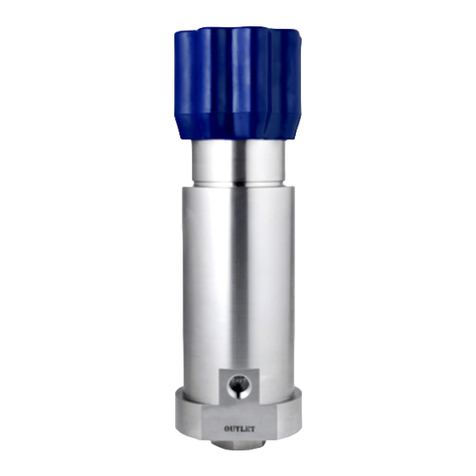
Pressure Tech
Pressure Tech LF-690 Service manual
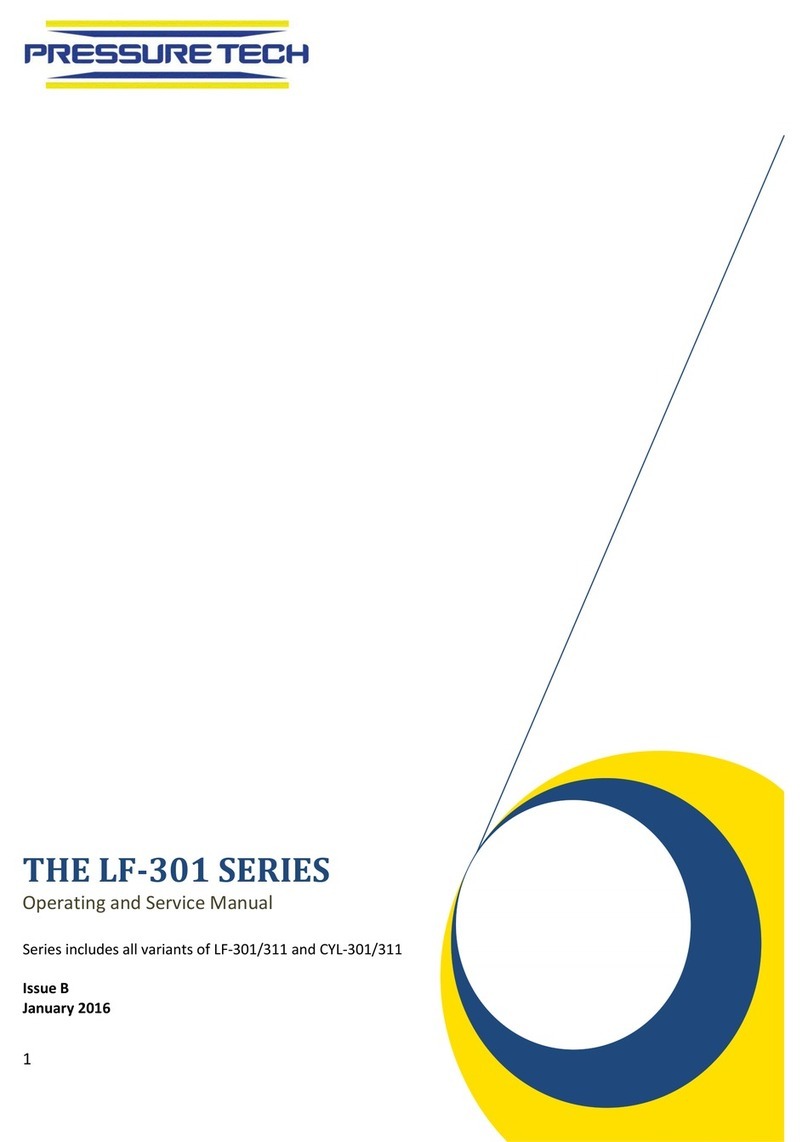
Pressure Tech
Pressure Tech LF-301 SERIES Service manual
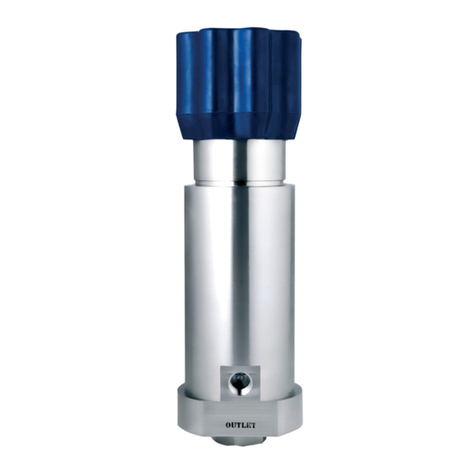
Pressure Tech
Pressure Tech LF-540 Series Service manual
Popular Controllers manuals by other brands
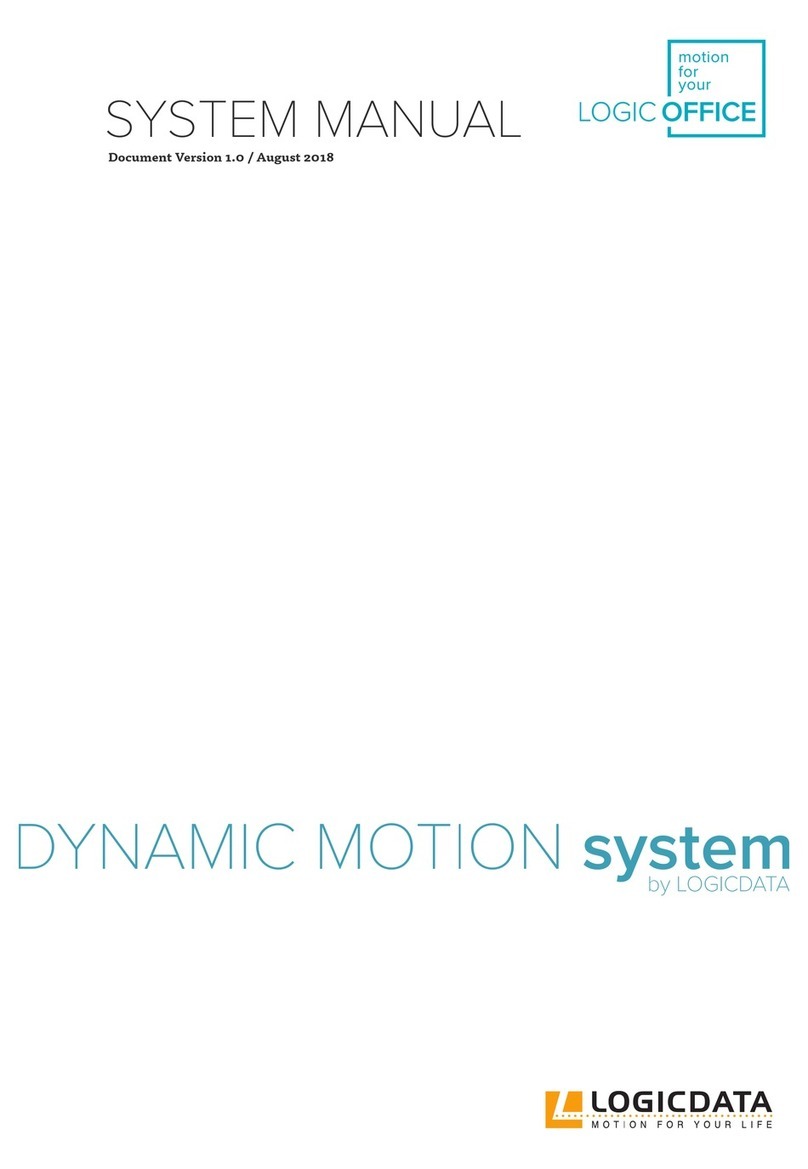
LOGICDATA
LOGICDATA DYNAMIC MOTION System manual
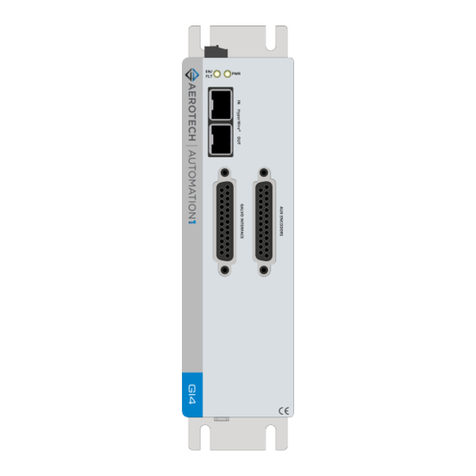
Aerotech
Aerotech Automation1 GI4 Galvo Hardware manual
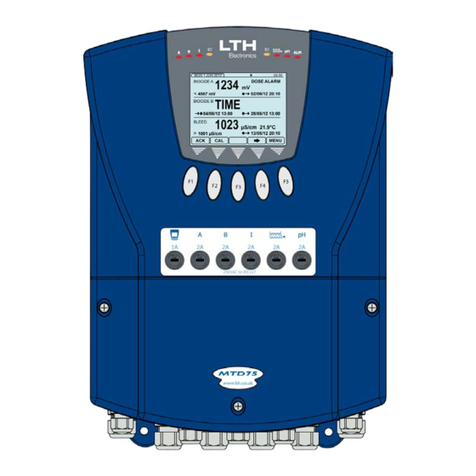
LTH Electronics
LTH Electronics MTD75 Operation guide
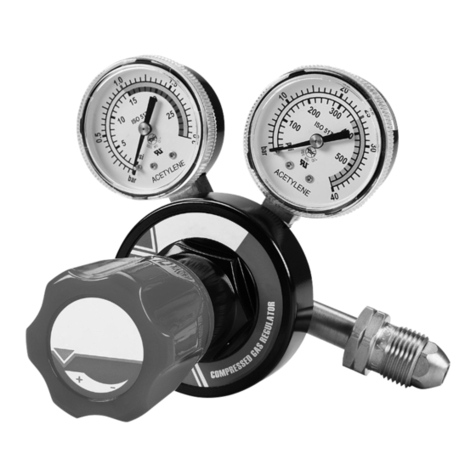
Olsen
Olsen 57574 Owner's manual & safety instructions
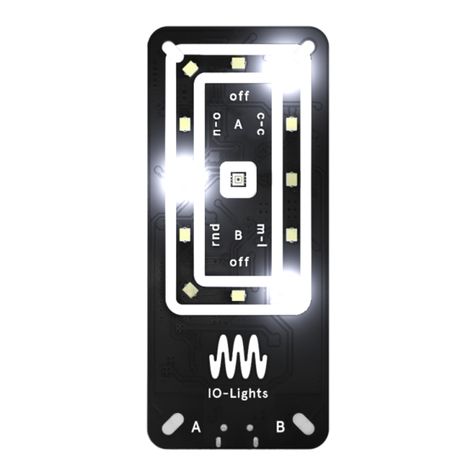
Instruments of Things
Instruments of Things IO-Lights user manual
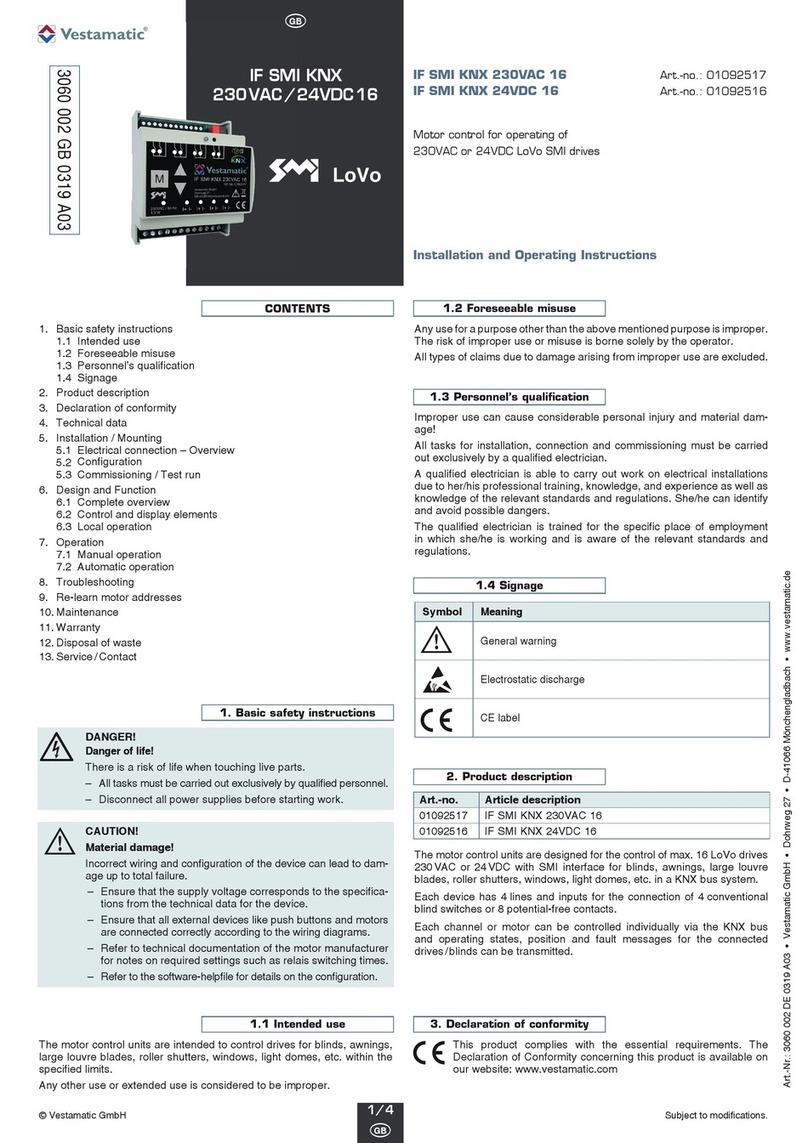
Vestamatic
Vestamatic IF SMI KNX 230VAC 16 manual